No Delays, No Surprises: 3D Laser Scanning Keeps Projects on Schedule and Identifies Unknown Issues
Print this Article | Send to Colleague
BY BRIAN LAIRD, PRINCIPAL PROJECT MANAGER, RICK ENGINEERING COMPANY
PATRICK EARLY, ESTIMATOR/PROJECT MANAGER, ALLGIRE GENERAL CONTRACTORS
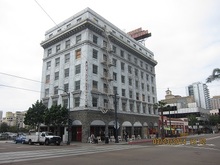
With the building already gutted the previous summer, Hotel Churchill’s renovations under Allgire’s scope included historic restoration, seismic upgrades, and a complete multi-family buildout on this 20.5 million dollar project.
At project initiation, Allgire’s Steve Brown, project superintendent, and Patrick Early, project manager, spent hours in intensive closed-door brainstorming sessions developing a detailed plan and schedule for this project, aware that the unique construction of the century-old, concrete building would come with its set of complications. The framing and layout was slated for November 2015, and it was imperative that walls, penetrations, tubs, water closets be laid out to identify as many potential conflicts in advance as possible.
From experience, Brown knew that no matter how perfect plans are on paper, when the first piece of framing hits the floor, there are conflicts no one can prepare for.
This was particularly true of the Hotel Churchill.
THE VALUE PROPOSITION
To detect unforeseen conflicts, the project team reached out to Rick Engineering Company (RICK), a San Diego Chapter member, to provide a quote for 3D laser scanning services. The initial proposal was quickly discounted due to budgetary concerns.
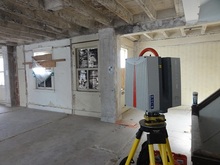
RICK’s team scanned the basement and first floor in a single day and presented the results a week later. Allgire invited the architect (Josh Hoffman, Studio E Architects) and owner’s representative (Tom Delaney, Springline) to join the project meeting as the results were likely going to impact the project as a whole.
In just two floors, Laird and his team had identified more than 30 conflicts using the 3D scanning technology. Early’s first response was simple and straightforward: "Where do I sign?"
THE VALUE IN ACTION
Within the next few days, RICK scanned the rest of the building interior. The joist locations, as they relate to the floor above, were deemed the most critical as the tubs, toilets, and penetrations were going to have major conflicts with the existing concrete joists. 3D laser scanning unveiled extensive hidden conditions that would have dramatically impacted the project plan and schedule.
Traditional methods would not have found these same conflicts until November during the framing and layout. At that time, construction would have ground to a halt, and the architects would have been back to the drawing board with only field dimensions to guide them. This Hotel Churchill project was being held to a 365-day schedule. With laser scanning, every framing conflict was known within the first three weeks while still in the demolition phase. Resolving these conflicts early in the schedule meant construction could proceed without delay.
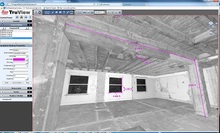
Furthermore, some of the steel was made out of grades that exceed welding confines and tolerances that can’t fluctuate. Precision work against concrete poured by brute strength a hundred years ago was going to be challenging at best, and without laser scanning, this would have been disastrous on the schedule.
The method for installing the large steel frames into the first floor was risky. Because the first floor was constructed out of an archaic assembly and rested on unreinforced columns, the idea of bringing a machine into that space to set 7,000 lbs. beams was inconceivable.
Subsequently, shoring, plating, and engineering were included in the proposal. Once the project was awarded, analysis of this method began to take its course through evaluation and vetting. 3D laser scanning produced accurate as-built drawings of the joists at the basement. Allgire was able to simply deliver that floor plan to a structural engineer, who quickly put together a shoring plan and subsequent plating plan (to spread the load on top) utilizing as-built conditions in a virtual environment.
Because of the amount of steel being installed at this level (nearly 150,000 lbs.), the shoring and load distribution had to be exact due to the constant loading from the machinery and picks. Because the team had precise drawings to work with, they were able to engineer the shoring at every other joist and employ a point loading scenario on top of the slab that loaded the joist inside and directly in line without adding intolerable loads to the unsupported slab between.
RICK took the CADD drawings from the structural engineer and, with survey total stations, marked each location where a post shore was to be installed. This enabled the team to receive the most productive price from the shoring contractor, who could remove analysis and layout from their scope and plan, as they only had to connect the dots with post shores. The biggest worry on the top of the slab was that someone might inadvertently point load something an inch or so off of the joist below, which is completely unavoidable without precise measurements. Again, RICK transferred the points from the basement to the main floor with survey total stations and the shoring/load distribution operation was complete within one week – putting steel installation five days ahead of schedule.
One of the last-minute team decisions made during and after the presentation by Rick was an option for topographical maps of each floor. This would help analyze the toppings being applied to each floor, but it was unknown how that decision would impact the job later. Numerous renovations, penetrations, and scarring over the years had left the 100-year-old floors unsuitable for any floor application. The structural capacities of the floor assemblies restricted the use of the topping and disallowed anything exceeding a 5/8 inch average. A few days after an analysis of the topographical maps was complete, it was determined that the original plan would not be feasible. Using the traditional construction methodology to zero the floor at predetermine elevations would put the framing far back in the schedule, which put subsequent back end pressure on the job. While the critical path of the schedule ran through the basement infrastructure, back-end pressure was not desired but seemed necessary considering the constraints on the final product. At the end of an analysis to determine the best alternative, RICK found the addressing for each scar/hole using the results of scanning and the floor survey, which allowed the project to move forward immediately. This application resulted in an immediate cost savings of nearly $50,000.00 to the project.
It was well known during the bid process and during many of the bid walks that the existing joists were dilapidated. With CADD drawings of each floor’s joists, Allgire was able to identify every hole, chip, scar, or problem and provided pinpoint accuracy to the corresponding location. The bid documents defined the number of holes and repairs necessary, and allowances were included in the prime contract for the corresponding counts and conditions. Upon review and subsequent mapping onto the 3D laser scanning results, the team found that the initial 170 locations as allowed were actually more than 700 locations. Because of this detail, the team was able to put in the analysis and location of each location, and the structural engineer was able to reduce the number by more than 200 – subsequently saving the owner tens of thousands of dollars in the process.
FROM THE CONTRACTOR’S PERSPECTIVE
Without laser scanning, the potential conflicts and issues arising from the existing conditions of the building would not have been identified or defined well enough for resolution until many months into the project (based on the original schedule). With 3D laser scanning, the team gained three months on the project schedule and obtained invaluable insight to avoid prolonged delays and large cost overruns.
One of the challenges with 3D laser scanning is to determine the actual value it brings to a project. However, 15 weeks into this project, the team was within days of the original schedule on the critical path and three months ahead on five of the eight floors. Without 3D laser scanning, this project would be far behind schedule and over budget, and no one would even know it – at least not yet.