Structures
In order to be placed in this category, the structural fabrications should include (but not be limited to) structural steel, bridges, canopies, gazebos, trellises, entry arches, sunshades, and cladding.
Gold Winner:
Migala Metal Designs
Harvard, Illinois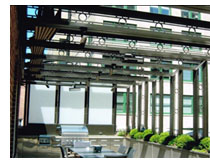
This job was designed by the architecture firm and was part of a complete rebuild of an 11th floor penthouse apartment. It involved creating 22 custom I-beams located on both sides of the exterior terrace. The longest are 13-1/2' and weigh about 280 lbs. The shorter verticals are about 8' long. Each I-beam contained a 1/2" wide waterjet pattern sandwiched between four pieces of 3" angle iron. C-channel was bolted to the wall and the beams were bolted and welded to it. The finish is powder coated Statuary Bronze. Some of the challenges included getting the beams to the jobsite and bringing them up the freight elevator - one at a time. Much planning was involved to assemble the pieces on the edge of the 11th floor. The vertical beams had to be raised in space and secured while leaning against the short wall. A pallet jack was used to hoist the verticals in place, and lots of safety equipment was involved in the process.
Silver Winner:
MDO Welding & Fab. Inc.
Wheaton, Illinois
This canopy structure was designed by the architect in collaboration with the MDO Welding & Fab. Inc. shop and was modeled after early 1900s French metro station canopies. The canopy is fabricated out of steel and measures just under 12’ height, with a 12’ wingspan, and is over 16’ long. All of the scroll work was completely hand forged/scrolled, and the base shoes were hand made from plate steel with a layered panel design. The structure was finished in oil-rubbed, bronze, textured powdercoat. The biggest challenge was that the wings of the canopy are not only curved, but they also have a setback of about 14" to give the canvas a bigger shadow profile and more appealing shape since it was designed to shade the bar and grill, given where the sun travels in relation to their house and canopy. It was a challenge to make sure each wing had the perfect angle to then fit the canopy canvas tight and without wrinkles. Install was done by the MDO Welding & Fab. Inc. shop.
It took approximately 100 hours to complete this project.
Bronze Winner:
Big D Metalworks
Dallas, Texas
Big D Metalworks created a Trellis structure with custom triangular stainless steel supports with 1/2" diameter curved stainless steel rods. This project was an existing Arboretum that added 8 acres of new property to its existing facilities. Big D Metalworks' scope of work included 214 lineal feet of continuous stainless steel trellis with six different raddi. All of the triangular supports were fabricated from 1/2" thick 316 alloy stainless steel plate. The 53 triangle supports all vary in size with no two supports being the same. Each support is projecting off of the face of the building at a different angle. The 3/4" diameter rods were pre-rolled and finished in the shop and sent to the field where they were welded on to the top of the triangle supports. The final structure was finished with an angel hair (nondirectional) finish.
It took approximately 959 hours of labor time to complete the work (200 hours fabrication, 217 hours finishing, 542 hours installation).