Furniture and Accessory Fabrication (Non-Forged)
In order to be placed in this category, metal fabrication including custom castings and cold forged elements should have less than 5% custom hand forgings. This category includes items such as lighting, tables, chairs, fire screens, fire tools, baker's racks, and window and door grills.
Gold Winner:
Finelli Architectural Iron & Stairs
Solon, Ohio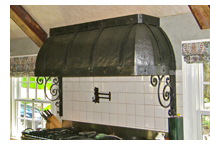
The design of this custom range hood was done by an Architect and was made for a long standing customer of Finelli Architectural Iron & Stairs. The basic frame construction consisted of flat stock with dimples which were created by hitting a ball peen hammer with a sledge hammer to get the desired texture. All of the sheet metal was also peened using the same, old style technique, cut to size, and then welded into place within the frame. The difficulty grew in acquiring the correct radius and angle on the corner pieces of the curved range hood. The Finelli team was able to overcome this obstacle by experimenting with 3D CAD and geometric equations. The 48 rivets were added to the hood and a hammered bar was used for scrollwork as support brackets on each end of the hood. The entire project was wire brushed clean and finished with a clear lacquer.
This project took approximately 85 hours.
Silver Winner:
MDO Welding & Fab. Inc.
Wheaton, Illinois
The design of this table was done by the fabricator. The base of the table is 2"x4" stainless steel rectangular tube with a brushed finish. The top of the table is a formed cold rolled steel top with a wood core finished with a black patina. The fabrication of the table top was straight forward. The table was formed with cold rolled steel 16 ga sheet on the press brake to fit around a solid wood core. Table top is 44"W x 108"L x 2" thick. The table base was where the challenge came from. The team fabricated the hollow diamond shaped center of the table from thick plate stainless steel, which sets the angles for the eight legs and is the core to which all of the weight of the table is centered on. Getting the angles perfect so that they could have a tight TIG weld to hold everything together was time consuming because each of the eight legs has compound angle cuts going in three directions to off set from the center line, fit the diamond, and rise or fall to meet the top or floor. The finish: Steel top is finished with black patina and an automotive satin clear coat to seal the metal. The base for table is brushed stainless steel.
This project took approximately 50 hours.
Bronze Winner:
The Heirloom Companies
Campobello, South Carolina
This project was a very unique piece that proved to be more of challenge than the team first realized. The stone seating had already been previously installed, and the team working on this project was asked to provide some kind of back rest to bring it all together. They used flat bar which was heated and bent around a form, but given how close the slates were together, in order to get them all to match perfectly caused a bit of frustration. Seven individual stanchions were created for support. This involved cutting the shape out of plate and then bending both an inside and outside piece in order to frame it and give it strength. Attaching the backing they created to the concrete floor and the back of the seat provided exceptional rigidity. A powder coating was used as a finish.
This project took approximately 170 hours.