Save the Dates: Upper Midwest Chapter
Fall Meeting
(Visit http://bit.ly/2dINeWw for a list of full details on the Fall Meeting)
When: Saturday, October 29, 2016
Time: 10 a.m. to 1 p.m.
Where: Migala Metals, Harvard, Illinois
*Note*: There will be a Friday evening social
PROGRAM:
- Explosion welding and rigging presented by Matt Olseng
- Shop tour of Migala Metal Designs
- Vendor Demonstrations/Displays (Wagner, Scotchman Demo Truck)
- Optional Art Event on Friday (4th Fridays)
**Please RSVP Rob Rolves at rrolves@foremanfab.com, or contact any NOMMA officer with questions.
Winter Meeting
When: December 10, 2016
Where: MDO Welding & Fab, West Chicago, Illinois
Note: Work on auction items
Note: Elections are coming up. Rise to the challenge and become a leader of this great chapter.
|
You Still Have Time to Apply for the Todd Kinnikin Scholarship
By submitting ONE referral to our committee, you can become a member of the Rust Free Club, see your name in an upcoming O&MM Fabricator magazine, qualify to win a NOMMA Shop Banner, and get recognition at METALfab in February.
NOMMA's current membership campaign, Member Get A Member, has been very successful. All you have to do is think of one or more fellow fabricators or suppliers and provide NOMMA with their contact information. A dedicated member of NOMMA's team will taken it from there.
Share NOMMA's great benefits with others and actively make NOMMA stronger by sharing your experience with potential new members.
Please send your referral forms by November 17 (or sooner) to either Todd Daniel at todd@nomma.org or to David Busarello at info@bridgetondrafting.com.
|
Preview for METALfab/FENCETECH
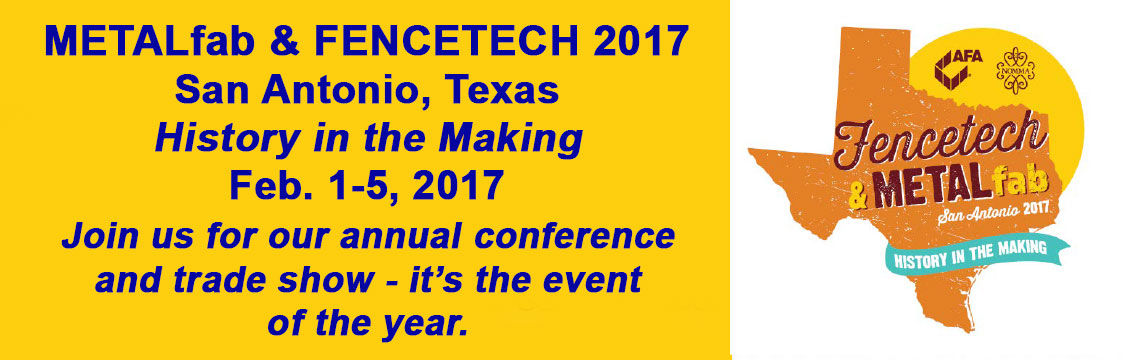
Whether you’re an exhibitor or attendee, the upcoming FENCETECH & METALfab 2017 conference has something for everyone. Join your peers from across the country in the largest gathering of the fence and ornamental and miscellaneous metals industries for 5 full days of industry expertise.
Here’s what’s in store:
• Education related to today’s technology
• Business tools, sales tips and training
• Certification and networking opportunities
• Expected attendance of 4,800
• Over 300 booths on the exhibit floor
• History in the Making Opening Party
• Annual Meeting/General Session
Schedule of events:
NOMMA’s METALfab: click here
AFA’s FENCETECH: click here
|
On October 15, Stan Lawler was presented with an award like no other at Octoberfest. In honor of Mr. Lawler's many years of selfless dedication to the ornamental industry, an award was created in his name - the Stanley G. Lawler Lifetime Achievement Award.
Mr. Lawler has been a mentor to a number of people in the industry, encouraging many men and women to stay in business despite their hardships. He has also served his community by working at a food bank for his church; contributed to the Metal Museum by donating equipment for educational purposes; pledged $100,000 to the NOMMA Education Foundation (NEF), donated and purchased auction items from NEF, making it possible for others to gain access to education in the field; and has built lasting, family-like relationships with various men and women in the ornamental metal industry.
The actual award itself was specifically designed and created with Mr. Lawler in mind. The casting is from Lawler Foundry's very own catalog, and the marble used is from Alabama. NOMMA member, Roger Carlsen of Ephraim Forge, Inc., did the prep work for the award, polished it, and created the hammered base. The bronze plate was cast by the Metal Museum.
This multi-faceted award is not likely to be awarded annually. It will be awarded to those who have made a big impact in the industry over an extended period of time. Congratulations to Mr. Lawler on receiving this prestigious award!
|
Art/Sculpture
Objects specifically designed as art or sculpture, to include fountains, statues, etc.
Gold Winner:
Medwedeff Forge & Design
Murphysboro, Illinois
This 26.5' tall and 19' x 9' sculpture was designed by the fabricator and was commissioned by a real estate developer for a commercial and retail development near the State Capital. The artwork and construction methodology was realized by working through a series of scale models, prior to full scale fabrication. All of the patterns were digitalized and scaled accordingly, then laser and plasma cut from 3/16", 3/8", 1/2", and 1 1/2" thick steel. Most of the forming was done in a 10' wide pyramid roll. All components of the forms were assembled into larger sections that could then be hoisted into position for final welding as the sculpture was vertically constructed within a custom designed scaffolding system. The surface was sanded smooth and rusted, then clear coated. Loading, shipping, and installation in one fabricated piece, less the base, required tremendous effort of planning and logistics. The installation, which was completed in two hours, went as planned.
Full scale construction took approximately 1,600 hours.
Silver Winner:
Compass Ironworks
Gap, Pennsylvania
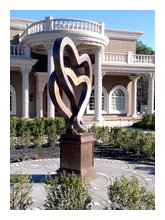
A past client wanted a heart sculpture for a photo op for the bride and groom at a wedding facility. The design team selected this intertwining heart sculpture. The Compass Ironworks team proposed everything to be in aluminum. They also wanted a brushed bronze finish. Everything was drawn in CAD and presented to the client for approval. The fabrication was somewhat complex with the sculpture being different widths and various helixes. The Compass Ironworks team had their biggest fabrication challenge with the difficult knot at the bottom, but that challenge was mild once the team got into finishing. The paint company stated "We don’t know what the sculpture is like, but the finish will be every bit a piece of art as the sculpture itself." The Compass Ironworks team considered this project to be a serious ordeal. It was an eight-step process with plenty of trial and error for three weeks. In the end, the client was overjoyed.
This project took 326 hours, including 103 in finishing.
Bronze Winner:
Custom Metals Inc.
Madison, Wisconsin
This sculpture was fabricated using nickel silver on a stainless steel support structure with hand-blown glass elements. Custom Metals Inc. received the unusual request to mimic a kelp bed; organic shapes with bubbles and bits of flotsam, as seen to the right. The architect had a clear idea of what was wanted, but not quite how to get there. After reviewing a number of paper mock-ups, the parameters were set. Each piece of "kelp" was hand-cut, formed into a shallow, flowing dish and curved back on itself. The textures are mirror polished or non-directional satin over the planished faces.
The Custom Metals Inc. team faced a challenge. They had to mount these irregular pieces to the structural grid without losing the "natural" form or letting the structural members be seen. If that wasn't a significant challenge in itself, they also had to install anchors in the unfinished, waving, pitched ceiling, such that the stainless cables would hang dead plumb. No turnbuckles were used.
This project took approximately 600 man hours.
|
Collaboration between architect and contractor from the very beginning of a project — where is the harm in that? That's the goal of the design-build project delivery method, which proponents say allows for collaboration by all stakeholders from the outset of a project, improving communication to the point that the need for change orders during the course of a job is greatly reduced.
In fact, design-build projects have proven themselves schedule-and budget-friendly. According to a 1999 Penn State study, design-build's production schedule was 33% faster than the traditional design-bid-build. When researchers compared costs, they discovered that design-build came in 6% cheaper than design-bid-build as well.
|
Stainless steel is widely used in the food and medical industries because it is easily cleaned and sanitized. Strength and corrosion resistance often make it the material of choice in transportation and processing equipment, engine parts, and firearms. And sometimes, designers specify stainless simply for its appearance, not for its structural properties. However, its benefits don’t fit every application.
|
|
The company, which in 1907 began as United Parcel Service and grew so familiar that people called it "Brown" because of the color of its delivery trucks, now universally uses the tagline "United Problem Solvers." One aspect of the firm’s work over the last two years to which that tagline speaks is the setting up of 3D printing services in more than 60 stores in major population centers around the US, Charlie Chung, marketing manager for UPS’s industrial manufacturing segment, said last week in an address at Purdue University’s Smart, Lean Ecosystems conference.
|
Engineers often specify steel when designing axles, bearings, shafts, gears, and a host of other components essential to the dependability and safety of both consumer and industrial products. But many of these engineers overlook specification practices that can lower the cost of steel parts.
This article provides an overview of the following eight tips which can lead to stronger, lighter, and less expensive parts and products:
• Specify Cold Finishing
• Consider HSLA
• Add Surface Carbon
• Use Mill Pretreatments
• Specify Special-Quality Steel Bars
• Shape it Hot and Fast...or Shape it Cold
• Be Smart When Buying
|
|
Staying informed about new technology helps companies keep up with the competition. Whether you’re a machinist wondering about 3D printing or a production manager in need of finding automation equipment, exhibitions at this year’s IMTS presented a range of possible solutions in the manufacturing arena.
|
|
|
|