SCA Neuss Mill in Germany Heated without Fossil Fuels
Print this Article | Send to Colleague
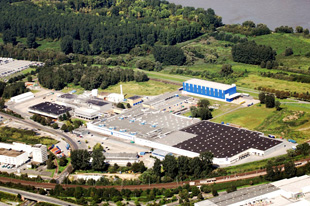
Continuously optimizing production processes to reduce energy consumption has the highest priority for SCA. Therefore, the SCA plant in Neuss is investing in heat recovery. Since October 2014, all heating and sanitary systems at the plant are operated with the waste heat that arises from the paper production.
The project started in the autumn of 2011. An expert group at the factory investigated how to make good use of the waste heat from the tissue production. The group concluded that the exhaust air to the drying hoods of the tissue machines was sufficient to operate the plant’s complete heating and hot water system.
Bernd Bichbeimer, plant manager in Neuss, said that "we have integrated as many employees as possible in the planning and implementation of this project. We were able to implement the last two phases with the existing knowledge in the factory without involving an external engineering office. This is strong evidence that SCA incorporates and appreciates employees’ knowledge and skills."
To start with, the project group installed a heat recovery system in the exhaust ducts. In the first step, the district heating system only heated the intermediate ceiling of the paper mill. Subsequently, the supply was expanded to include all buildings as well as the heating of the hot water and sanitary systems.
The most important success factor for the project was the safe operation. "We installed a pipeline on the outside walls of the buildings and built pipeline bridges over the roads that separate the buildings. Most of the installations were carried out with the help of cranes and work platforms. We built in stages to reduce the carbon dioxide emissions as fast as possible," said Martin Marx, project manager and energy and technical site support leader at the Neuss facility. "In the next step, we transferred the hot water supply for all employees to the new heat recovery system. We pressed the pipes to significantly reduce the fire load," Marx continued.
With the completion of the heat recovery project, the energy-saving measures in Neuss are by no means finished. In the next step, the mill plans to use more waste heat for frost protection of water pipes.
Other areas can also benefit from energy-saving measures. In addition to improvements in tissue production, the Neuss factory drives a project to convert the complete lighting of the plant to LED technology. With well-established projects, such as the Energy Efficiency Day, SCA strengthens employees’ self initiative and motivates them to foster the company's success.
"It's nice to see that employees actively live SCA’s values of sustainability and commitment in their work," Bichbeimer says.
SCA’s Neuss mill operates two tissue machines. The plant makes Tempo handkerchiefs and toilet paper at the tissue mill, with 455 employees.