Bosh Introduces Integrated Topload Cartoner
Print this Article | Send to Colleague
Increasing the convenience it offers to customers, Bosch Packaging Technology, Germany, in partnership with recently acquired Kliklok-Woodman Corp., Decatur, Ga., USA, is introducing the Kliklok ITC This integrated topload carton forming, loading, and closing solution complements Bosch's current packaging portfolio, and enables it to offer its food customers complete system solutions for primary, secondary, and tertiary packaging. The new development boasts one of the highest speeds available for a solution with such a small footprint, and has a large carton size range. This allows manufacturers to save production space and increase product output without compromising quality.
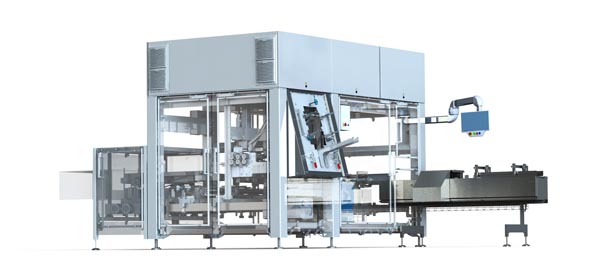
Targeting producers of confectionery, cereal bars, bakery products, biscuits, and cookies, the ITC's principal function is to form topload style cartons or trays and automatically load wrapped products into them, before closing, if required. Comprised of a single fully integrated solution with three functions—carton forming, loading, and closing—the machine helps to reduce customer footprint with an ergonomic design, avoiding the need to source three separate pieces of equipment, to interlink and integrate them.
Another benefit of the ITC is the need for only one operator and one human machine interface (HMI), which enables the productivity rate to be improved. Increasing labur costs and availability of qualified resources has driven the demand for this complete, easy-to-operate integrated topload cartoner.
Neil Fowell, GM, Kliklok International Ltd., said that "innovation is at the heart of everything we do and it is imperative for Bosch to adapt to consumer demands as we focus on becoming the single-source solutions provider within the market."
The ITC offers food customers the flexibility to change formats and run a variety of carton styles, and is designed for flow wraps, roll wraps, compartment trays, or multi-packs. Cartons are fed using a reciprocating carton feeder, and are formed using a motion profiled vertical plunger. Either lock or glue cartons can be formed on the ITC, and four possible carton styles can be incorporated within a single or twin infeed model: three-flap carton with full flaps, three-flap carton with economy flaps, a single-flap carton or a tray.
Once the carton is formed, an intelligent transport system is used to carry it independently through the machine loading and closing module. This system provides flexible and variable configurable control of the carton to suit both loading and closing requirements, and is also comprised of minimal parts, reducing maintenance and increasing overall equipment effectiveness (OEE).
The next step is the automatic loading of products, integrated into the machine using Bosch's Delta robot. The appearance of a Delta robot is similar to an inverted three-legged tripod. The three segments or "arms" move independently of one another but share a common connection—the "robot hand." This is moved by either extending or retracting one of the segments and enables Delta robots to reach every point within their range at the same speed at high accuracy.
In contrast with conventional robots, Delta robots do not need to struggle against gravitational and inertial forces and are therefore capable of extremely high speeds. In addition, the Delta robot is able to track the carton transport system and load products "on the move"—an advantage over two-axis robots, which can only load stationary cartons. Bosch has installed in excess of 3,000 Delta robots globally.
For the carton closing operation, a simplified lug-less design eliminates carton carrying lugs, driven chains, mechanical transfers, and timing flaps. Instead, the closing section uses easily replaceable high-friction belts to quietly convey cartons out of the machine, effectively reducing any carton marking and product damage.
Responding to customer demand for efficient and fast production while maintaining premium product quality, the ITC offers reduced changeover times and improved performance levels. Developed with the new HMI 4.0 touch screen, the next generation of intelligent human machine interfaces, it offers users an enhanced experience, guiding the operator through each step of the production process. With a clearly structured menu, operators are immediately aware of the machine status. With trouble-shooting support, the HMI significantly reduces the risk of unscheduled downtime and allows employees to minimize planned maintenance time. The ability to optimize production schedules for greater efficiency leads to a faster return on investment (ROI) and lowers overall total cost of ownership (TCO).
More information is available online.