Midwest Paper, Formerly Appleton Coated, Reaches Milestone in Comeback
Print this Article | Send to Colleague
According to an article published this week in the Post-Crescent (Appleton, Wis., USA), the former Appleton Coated mill, now called Midwest Paper Group, has reached a milestone that 10 months ago seemed virtually impossible.
The mill is now running all three of its paper machines around the clock, every day of the week. The machines will operate continuously from now on, only silent for maintenance periods. Anyone who sat through Appleton Coated’s courtroom receivership hearings last fall wouldn’t imagine this is the way it would turn out. Appleton Coated shut down in September, putting most of its 600 employees out of work.
In October, the mill was sold for $21 million to just one bidder, the combined Industrial Assets Corp. and Maynards Industries USA, two businesses that primarily buy and sell used machinery and conduct liquidations and auctions. It appeared that Appleton Coated was destined to be scrapped.
But when the new buyers learned the mill could be valuable as an ongoing manufacturing plant, they invested many millions more to upgrade the facility. Machines restarted one by one beginning in December. About 310 employees were recalled.
Midwest Paper president Kyle Putzstuck declined to pin down the exact dollar amount of the additional investment by the new owners, other than to say "they’re doubling down." It was apparently a bet that paid off.
The company is now near capacity, even while on its startup curve with a new OCC pulping system put into operation July 2. The system essentially recycles old corrugated cardboard boxes to make material for new corrugated boxes.
"It’s taken less than six months from concept to startup of our OCC recycling process that is now supplying the majority of fiber to our machines," said Managing Director Doug Osterberg.
"I’m not aware of anyone anywhere building a similar pulping system in this short timeframe," Osterberg said. "This doesn’t happen in six months. Usually putting in a system like this would take 18 months," said John Mazuroski, head of sales and marketing. "It was essentially a ballet of moving the equipment in while the mill was operating, while we were producing paper and selling it to customers."
Midwest Paper gets its post-consumer waste boxes from grocery stores, department stores, and other recycling sources in Wisconsin and the upper Midwest. Two-thirds of the company’s production now is in brown paper used for containerboard grades for packaging, which are in high demand.
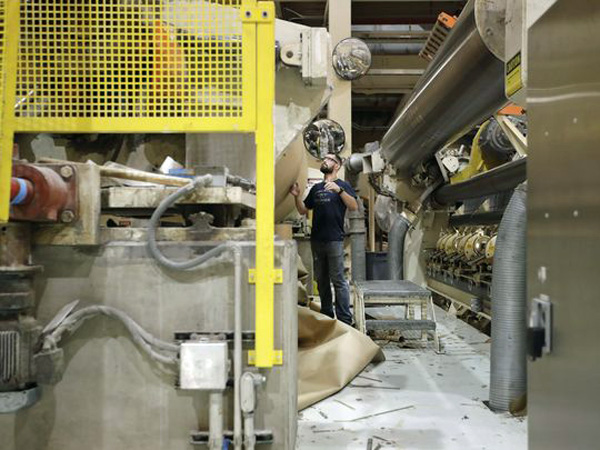
Kyle Quaintance, a third hand with Midwest Paper Group, prepares the master roll on PM 7 for a slitter change, which will take the master roll and slit it down into smaller rolls. (Photo: Danny Damiani/USA TODAY NETWORK-Wisconsin)
Before going into receivership, which is an alternative to bankruptcy, the company made mostly printing grades of white paper used in advertising, fliers and direct mail — categories in declining demand — and had only begun to test brown paper. The new owners didn't waste time putting in the waste-recovery system to cut down the escalating cost of new pulp. Production has rampped up to 1,200 tpd, putting the mill within reach of its 400,000-tpy capacity.
"We’re doing exceptionally well here," Putzstuck said. "Industrial Assets is thrilled with the progress."
The new owners’ concerns have eased over the riskiness of the investment, he noted.
"It’s only with significant investment that you pull this off. There are no limitations. We have the equipment, the employees, and the customers. There’s no more ‘if we had this, we’d have that.’ We’ve removed all the capital constraints," he said.
Osterberg said local firms were key in helping refurbish, convert, and install equipment, including Poyry Appleton, BKB Construction, Pieper Electric, Piping Services, and Voith. Poyry Appleton, for example, did engineering design for the pulping system. Poyry’s EVP, Roger Marsicek, lives near the mill and said while the accelerated speed of the installation was stressful, he was like many in the village who were rooting for the mill to come back to life.
"People still remember the Kimberly mill and that being torn down," he said. "The community here is excited to see the mill start up again and get people back to work."
Pieper Electric of Neenah was another firm eager to help with the mill's rebirth.
"This plant has kept many of our local electricians employed for 20-plus years," said Jamie Darkow, department supervisor. "We are grateful for the opportunity to be able to help Midwest Paper Group and the community of Combined Locks."