L.C. Paper Starts up Rebuilt PM 2 Tissue Machine in Spain
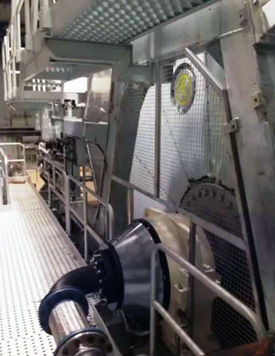
L.C. Paper, Spain, has started up No. 2 tissue machine at its Besalu, (Catalunya, Spain) mill after a major dry end rebuild by Toscotec (Italy) and its associate Milltech. The rebuild was conducted mainly to reduce PM 2 energy costs and improve paper machine efficiency, as well as increase production with higher quality tissue grades, thanks to the application of TT DOES (Drying Optimization for Energy Saving) package.
LC Paper was formed in 1881 and is now known for its production of niche tissue products made on two tissue machines (PM 2 and PM 3), annually producing 65,000 metric tons of tissue for the AfH (Away-from-Home) market. The mill has a primary focus on energy savings, and thus for many years has been advancing cogeneration applications.
In 1993, LC Paper installed the mill’s first cogeneration plant. It was the first plant having a diesel engine with 6.5 MW of capacity in Spain, and was expanded in 1999 with a second 6 MW engine.
In 2009, LC Paper launched PM 3 with a patented process that takes gas from the cogeneration plant to dry the tissue paper via an innovative hood provided by Milltech. In 2011, the first diesel engine was sold and in 2012 the company installed a new gas powered engine. Some 6 MW of that energy is now used to feed the new Milltech hood on PM 2, providing an additional decrease in energy consumption.
The Toscotec/Milltech combined scope of supply included a new double press configuration with a rebuild of the felt run, a new TT SYD-15FT with doctoring system, and a Duo-system yankee hood, SMART eMT type from Milltech. The wet end hood is a burner feeding type while the dry end hood could be fed either by cogeneration gases or by a conventional burner.
Exhaust gases coming from a gas engine are used to generate two stages of steam (high and low pressure) through steam generators, in addition to the heat recovery to pre-heat the make-up and combustion air for the hood.
Maximum drying production with a machine trim width at the reel of 3,050 mm will be 130 metric tpd.
With this new intervention, the PM 2 thermal consumption will be lowered to 1,350 kWh/t.
TAPPI
http://www.tappi.org/