Alfa Laval Helps ITC Attain Zero Liquid Discharge, Make Better Paper
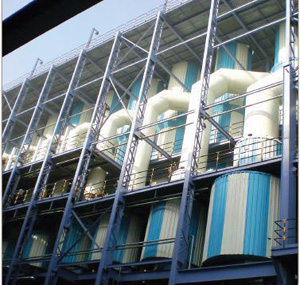
ITC Ltd, a leading pulp, paper, and paperboard company in India, wanted to start in-house production of bleached chemi-thermomechanical Pulp (BCTMP). It turned to Alfa Laval, Pune, India, to help implement an evaporator system for the new BCTMP black liquor evaporator process—and to make sure they could do it in a way that was in keeping with the zero liquid discharge statutory directive.
"This will be the first plant of its kind in India, and it's clearly the way to go for manufacturing quality packaging board," said A.V. Rao, EVP, ITC Ltd. "After finalizing the required specifications for the new evaporator plant with the BCTMP plant vendor, we discussed the technical details of the plant with Alfa Laval."
ITC explained clearly how they wanted to integrate the new evaporator with the new BCTMP pulp mill and their vision of zero liquid discharge. After the discussions, Alfa Laval came up with a new system of an evaporator with an integrated stripper.
BCTMP is mechanical pulp produced through a chemi-mechanical pulping process where wood chips are first treated thermally and refined mechanically in a refiner, followed by bleaching and washing stages. BCTMP pulp results in strong, high-bulk board.
Alfa Laval had previously supplied ITC with a black liquor evaporator plant in 2001, and by 2012 one more new plant was commissioned. Subsequently, ITC added further capacity to these evaporators through two expansion projects. So it was natural for ITC to turn to Alfa Laval again in 2015 for the new plant. Because BCTMP was a new process for ITC, they took extra care in choosing the supplier.
"We did a lot of research," said Rao. "Our team traveled to plants outside of India that used similar processes and talked to a number of suppliers. In the end, we chose Alfa Laval again because we were convinced by their analysis and because we know them and we trust them."
Not only did ITC want to build the first BCTMP mill in India, they were also determined to make it a zero liquid discharge plant. The process is designed in such a way that all of the water used for chip washing is treated internally and then re-circulated, creating a closed loop.
For the balance of spent liquor, Alfa Laval is supplying ITC with a seven-effect falling film evaporator along with an integrated stripping system. The stripping system allows the condensate from the evaporator to be reused to reduce the consumption of fresh water and help create a zero liquid discharge process.
Prasanna Upadhyay, Alfa Laval's business manager for dryers and evaporators, explained that "during the evaporation process, some of the volatile organics present in the liquor are carried over to the condensate, resulting in an increased Chemical Oxygen Demand (COD). The condensate stripper section reduces the COD level. The stripped gases are removed and burned."
The design enables reuse of 2800 cubic meters per day of treated condensate in the pulping process. The concentrated liquor from the evaporator will be fed to a boiler to recover chemicals and generate steam.
ITC - Paperboards and Specialty Papers Division (ITC-PSPD) has the largest single location paper and paperboards mill in India (550,000 metric tpy) at Bhadrachalam, Telangana. The company is the leading supplier of paperboard for value-added packaging applications. ITC is the first mill in India to produce elemental chlorine free (ECF) papers and paperboards.
TAPPI
http://www.tappi.org/