Honda's "Pulpahol" Experiment: History's Near-Forgotten Turpentine Powered Motorbike
Pulp Energy: Honda’s Original High-Octane Turpentine
Woody biomass can be made into two very valuable types of fuel that together are used in the vast majority of internal combustion engines. Ethanol can blend into bio gasoline mixtures that easily drop into gasoline engines with very little modification up to 85% or even higher. Wood can also be processed into biodiesel to effectively directly replace petrol based diesel and power large trucks and tractors vital to economies. Wood fiber processing may represent one of the most crucial aspects of developing new energy solutions in the fight to create a vibrant, healthy, and sustainable 21st century economy of both financial and environmental prosperity. Biomass is carbon neutral, while the actual combustion process releases carbon, the global management protocols effectively in place assure that renewal of the natural resource of the fuel (trees) unlike fossil oil reserves, will "resink" the carbon.
The first stage of creating most woody biomass fuel is fermenting a mixture of raw material so as to get sugar molecules involved to react and produce alcohol. In the case of wood fiber or pulp, this first stage of initial processing fermentation will produce what is known as turpentine, which comes primarily from what we see, smell, and feel (its very sticky) as the potent, relatively energy rich "resin" component within a tree – in layman’s terms, it’s "tree blood" among many other vital components mixed together essential to the living energy of the tree itself to bud, perform photosynthesis, and grow.
When producing chemical wood pulp from pines or other coniferous trees, sulfate turpentine may be condensed from the gas generated in Kraft process pulp digesters. The average yield of crude sulfate turpentine is 5–10 kg/t pulp. Unless burned at the mill for energy production, sulfate turpentine may require additional treatment measures to remove traces of sulfur compounds.
Turpentine oil can be differentially separated as Volatile Turpentine and Nonvolatile. Volatile Turpentine is an ideal additive to Biodiesel, sine it enhances combustion efficiency and leaves less residue, Marginal increase in Nitric oxide pollution is more than off-set by reduction in Carbon Monoxide emission.
The theory of creating ethanol or alcohol fuel from wood by the process of fermentation into majority turpentine* and beyond is actually nothing new. There have been numerous methods successfully devised to distil and post-process wood fiber into the equivalent of at least pure ethanol as biogasoline. Obviously, because of their value, these have given rise to the issuance of many patents. Yet they have not been fully implemented, most likely because as a stand-alone operation in dealing with wood fiber sources, it is not a profitable model. But perhaps there is promise in its positive potential as a cooperative venture with other pulp product production:
"It does not seem possible for wood alcohol production industry to exist outside of enormous forestry centers such as exist in America, capable of furnishing large quantities of sawmill waste and/or woody bioresidue from pulping related operations throughout the year." - E. Boullanger: Distillerie Agricole et Industrielle
Alcohols, being liquid fuel, can be used in a high-proportion in internal combustion engines. Most accept at least 15% percent but can run on as high as 20-25% if need be, while many fleet cars with very little modification have run for many years as E85 or 85% blended with petrol (but turpentine, without further conversion and/or refinement, is far from for this application in today’s engines...)
Yet doesn’t mean that "treethanol" from kraft pulp mills didn’t once power motorcycles...
Beginning in 1910, Tomlinson implemented on a large scale, in America, the manufacture of turpentine oil (crude fuel grade; steps 1-3) followed by a second-step alcohol from sawdust:
1.pine sawdust is placed in rotatory digesters made of sheet steel lined with ceramic tiles, along with dilute suphuric acid.
2. Inject direct steam injection for approx. 1 hour to achieve heat.
3. Exhaust steam to achieve partially condensed turpentine. The total yield will be approx. 200-300 grams per metric ton of the dried wood dust.
Stage 3 product was typically only for certain lamps. For "High Grade Turpentine" as it was sometimes traded, the sawdust was then extracted in a diffusion battery, pressed, and then used as fuel. Once more, the juice obtained was partly neutralized, filtered, cooled and sent on for fermentation. In France, according to officially unverified citation quotation posted to Wikipedia, alcohol manufacture from sawdust was reportedly studied and implemented industrially in a distillery in the Ardèche region, before 1914.
During the war, the question of wood-alcohol manufacture was again taken up in the light of the need for alcohol for national defense.
In Germany, production of wood alcohol was accomplished during the 1914-1918 war with either the Classen or the Windesheim-ten-Doornkaat process. In the Classen process, the process underwent a few modifications which make it a little different from the one described above. The heating of the sawdust is carried out for 40 minutes in rotatory autoclaves, with suphurous acid, at a pressure of 7 kilograms (165 deg). The steam is then expanded as rapidly as possible and the mass is emptied into diffusers. The ‘juice’ that is obtained is neutralized, nutritive salts are added and fermentation is started with pressed yeast. Yield is from 8 to 11 liters of "mid-grade" crude fuel oil (clear, low viscosity) per 100 kilograms of dry matter. This type of slightly expanded / extended process or modifications in this style likely were required at minimum to yield turpentine engine oil in post WWII Japan; the Tomlinson method, however, produced a turpentine fuel that became popular in lamps at one point in the early 20th century.
In the Windesheim-ten-Doornkaat process, the sawdust is heated with dilute hydrochloric acid in the presence of catalysts (metallic salts), in rotatory autoclaves, at 7 to 8 atmospheres for 20 to 30 minutes. Yield is 6 liters of alcohol per 100 kilograms of dry matter, but it is surely possible to improve this.
Powering History
These early methods slowly improving production would lead to the odd-fuel choice becoming the source of power in the very first vehicles produced by what would soon become the now world renowned Honda Motor Company. Soichiro Honda’s dream began taking shape amidst the ruins of a ravaged postwar Japan. Following World War II, the entire nation entered the long and difficult process of rebuilding, and along with it came a huge demand for inexpensive transportation. Honda began by purchasing a batch of small-displacement army-surplus engines formerly used to power radio transmitters, which he attached to bicycles to power the rear wheel by a drive belt. This proved to be a profitable business venture, but the meager supply of engines was soon exhausted, prompting Honda to design his first gas powerplant in 1947—the A-type engine.
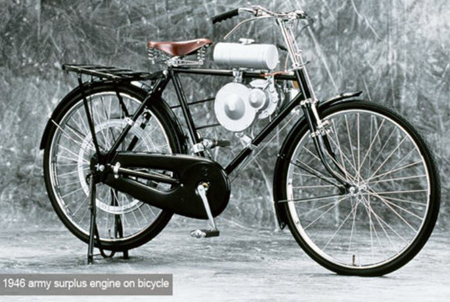
Honda associates quickly gave a nickname to this 1-horsepower, rotary-valve 50cc two-stroke engine. They called it the "chimney" thanks to its tall single cylinder, but also because it smoked ferociously when fed the engineering team’s collection of tree pulp malt sprouts in the saccharine juice. After development, supplies of yeast was used for inoculating the saccharine juice in more formal fermentation vats. Industrial yields, under normal conditions, reached 7.3 liters of 100-degree alcohol per 100 kilograms of dry wood, and the factory's annual production was 20,000 hectoliters of this early equivalent of a biofuel made from wood fiber.
It wouldn’t be until more than a half century later that the pulp industry would begin to produce lines of biofuel for commercial use again, lead primary by Scandinavian forest product companies.
Sparking A Small Yield – Worth it for A Small Price
Alcohol yields are very low when compared to distilled natural alcohols such as the common simple distillation staple grain alcohol. Due to the complexity of cellulose in the traditional process of wood fermentation, the alcohol yield of wood by hydrolysis is minimal compared with the quantity of cellulose that it contains. For the pulp and paper industry, however, this aspect may just be to their benefit. Because of the generous amount of excess wood scrap produced at a pulping mill’s wood yard, the operation, unless modernized in a special type of co-generation or bioproduct production already utilizing biomass surplus from logs, essentially has a lot of "free" excess woody biomass being generated – certain scraps and dust are inevitably left over from the entire chain from harvest to chipping, cooking, etc. at mills.
If collected cost-effectively beyond the needs of the mill, it could represent an energy net positive source of liquid fuels that would be carbon neutral due to the renewable nature of their source material (trees). Many alternative energy plans today predict a reliance on a diverse strategy of renewable fuels. Though waste biomass from the pulping industries alone is not sufficient to solve all of the energy needs in a large nation like the U.S., it nevertheless represents a valuable source of energy when measured as a potential source on a global scale, and even more valuable because of its ability to be processed, even in the most basic preparations, into a type of fuel able to light lamps, heat water, and even power Honda’s first motorcycles.
The challenge would be to do it anywhere near cost effective ...do things like route construction debris that unfortunately currently rots in way to the landfill (or soon after – which is actually better than not biodegrading). But that still releases the CO2 without even using the energy. So it should not, theoretically, be considered at all environmentally negative to burn this wood waste for energy – wood will inevitably decay in the atmosphere irrespective of being subject to combustion. But a real challenge would be recovering woody biomass on site – so very many sites! Not to mention, relatively fast acting in terms of global recovery time, air and moisture alone, which are present all over the globe, essentially act upon and "waste" the energy potential of the wood fiber that’s inevitably lost before we could recover it, and in doing, so releases carbon that can only be negated by replacing it with another tree – which can and is being established, led by the paper and forest related industries.
Eventually, perhaps it might just make sense, assuming some fashion of carbon financial crediting or taxing were to be implemented, for the markets to route more wood waste to pulp mills currently making the old fashioned, basic turpentine that’s firing their internal boilers could exit the confines of the mill as an export product... All depending on many things, though, such as on the amount of energy sources used as well the overall amount of diversification of sources "plugged in" to the overall "smart" grid from in future decades. The grid is supposed to be smart because of its ability – with programming – to understand how to accommodate for changes in power stability whether it be losses or surges in areas that can be an enigma to account for by even well trained power room control personnel. So it might make sense to use a certain percentage of kraft mill sourced wood alcohols / "turpentines" outside mills, but this likely wouldn’t make more sense than heating small villages in extreme northern or southern hemispheres, near polar climate towns that happen to have a pulp mill to generate significant energy. And in most of these areas, especially in countries like Sweden and Finland with globally leading paper companies on the cutting-edge of production, including co-generation, this is not a problem. They already have advanced systems that are only partially based on the inputs to the recovery boiler of the kraft pulping operation.
But if, and only if, we were to use truly waste wood biomass... what otherwise would for sure rot in yards, woods, or end up in a landfill in modern times, should we go out of the way to make wood alcohol for export directly at existing or even new mills (unless, suppose, an efficient catalyzing process beyond anything except the imagination were to turn kraft cooked wood alcohols / turpentine into petroleum in the not too distant future).
Nevertheless, beyond the 21st century's use for simple wood lamp fuels, woody biomass should not become biowaste needlessly even though it is biodegradable if the energy potential is to be considered. That consideration on the end may be arguably on the borderline but also arguably on the usable side of "borderline" as a resource... primarily due to the sheer abundance of trees - beyond furniture and paper - turpentine for lamp oil to see things lit up by it would be very much more important in a world of 6 billion people without electricity.
Though crude by today’s standards, wood alcohols and turpentine are material examples of the energy that is lost when wood is left to decay and literally disintegrate into the wind. If not utilized directly in our industry, it should be always be processed, globally (including in developing countries) even into bio-pellets for export to Europe for a relatively low cost for those countries to pay that can translate to a profit, even for the U.S. when traded for the dollar at equal valued wages, where the production of these are common for shipment across the Atlantic to meet EU regulations on CO2 emitting heating fuels.
In conclusion, if the cooking of pulp by conventional means (such as at paper mills) the only potential for deliberately "rerouted wood waste" would seem to be into low-grade pulp products hybridized with wood alcohol production for running farm equipment because of the low yield and possible issues with quality. And that hypothetical farm equipment would probably need to be less oily and smoky than those original Honda motorcycles...
There are also some additional proposed ways to, in the correct conditions (not covered here), possibly more efficiently and better process wood fiber such as boiling under the pressure of calcium sulphite. This creates a strong discharge of sulfite liquor.
*The standard industrial handling processes used today to make wood alcohol post-generation of either the kraft pulp mill excess turpentine or the synthetic independent facility turpentine generally refines or "keep" pure turpentine as well as methanol, each separately. Often times natural methanol is separated from turpentine and sold as "wood alcohol" due to crude turpentine not technically being an alcohol in the sense of ethanol, the most common solvent.
In principle, crude turpentine is recovered from the digester relief condensates and purified in the distillation process. However, batch digester recovery systems differ substantially from continuous digester recovery systems in the methods by which the relief vapors are captured. The average yield of crude turpentine from pine species is 5–10 kg/ton of pulp and is somewhat lower for spruce species.
More information about the conventional use of turpentine fuel,
burned on a kraft pulp mill site (where it’s maximally cost effective) collected via a special recovery system that is routed to power a boiler for heat / electric energy co-generation.
View a YouTube presentation demonstrating how to produce a sample of turpentine and resin from pine tree sap. The semi-clear liquid is visible at 11:18.
Report by Dylan Patrick
TAPPI
http://www.tappi.org/