 |
|
Weekly Spotlight
Fortress Paper, Vancouver, B.C., Canada, a producer of security and specialty papers, in a major strategic move this week, announced the acquisition of the Fraser Paper Thurso, Que., northern bleached hardwood kraft (NBHK) mill, with the intention to convert it into a "world class, low cost" specialty cellulose (dissolving pulp) operation
Learn More...
|
TAPPI's Papermakers Committee has organized a strong program of peer-reviewed papers for PaperCon 2010, May 2 - 4 in Atlanta, Ga., USA
Learn More...
|
The Twenty-Third Process Industry Reliability & Maintenance (PIRM) Conference being co-located with PaperCon 2010 at the Hyatt Regency Atlanta, Atlanta, Ga., USA, May 2-5, covers the maintenance function from several critical perspectives while focusing on basics and methodologies that have developed and evolved over more than a century
Learn More...
|
Market Roundup
The American Forest & Paper Association (AF&PA), Washington, D.C., USA, this week released its 50th Annual Survey of Paper, Paperboard, and Pulp Capacity, which reported that U.S. paper and paperboard capacity declined 2.5% in 2009 to 93.9 million tons
Learn More...
|
AF&PA also announced this week that a record-high 63.4% of paper consumed in the U.S. was recovered for recycling in 2009, noting that "this is great news for the industry and the environment, and exceeds the industry's 60% recovery goal three years ahead of schedule
Learn More...
|
Pulp & Paper
Atlantic Packaging Products, Toronto, Ont., Canada, this week announced that it has closed its Whitby Newsprint mill, following effort to reduce operating costs and improve performance results
Learn More...
|
Chile's CMPC reported earlier this week that it expects in April to gradually recover a "substantial" part of pulp output capacity in four plants shutdown after the February 27 earthquake
Learn More...
|
Kruger Inc., Montréal, Qué., Canada, will extend the shutdown of No. 3 paper machine at its Wayagamack Mill in Trois-Rivières, Qué, for a period of one month, starting March 31
Learn More...
|
(USCAP), Washington, D.C., USA, announced last week that Weyerhaeuser, Federal Way, Wash., has joined the coalition of business and environmental groups pushing for climate and energy legislation
Learn More...
|
Containerboard/Packaging
Total U.S. containerboard paper production again rose sharply in February compared with February 2009, according to the American Forest & Paper Association's (Washington, D.C., USA) February 2010 U.S. Containerboard Statistics Report released this week
Learn More...
|
Cheng Loong Corp. will install a new containerboard production line at its Hou-Li paper mill in Taiwan, to be supplied by Metso, Finland
Learn More...
|
MeadWestvaco Corp., Richmond, Va., USA, this week announced that its Brazilian subsidiary, Rigesa, is undertaking a formal study to assess the feasibility of expanding its paper production through a new linerboard machine at the Três Barras facility, located in Santa Catarina State, Brazil
Learn More...
|
MeadWestvaco Corp., Richmond, Va., USA, this week reported that its MWare food service paperboard has been certified by the Biodegradable Products Institute (BPI)
Learn More...
|
Iggesund Paperboard AB, Sweden, reports that its newly published Graphics Handbook gives examples of many different paperboard graphic design techniques and describes how to achieve them
Learn More...
|
Smurfit Kappa Completes Mill Modernization, Integration in the Netherlands Smurfit Kappa Group, Ireland, reports that the modernization of its mill in Etten-Leur, the Netherlands, and its integration with the company's nearby Oudenbosch facility, is now complete
Learn More...
|
Work is underway to transition Sonoco Recycling, Inc.'s Charlotte, N.C., USA, Recycling Center into a full-scale material recovery facility (MRF) by early summer
Learn More...
|
Saica Containerboard U.K., at Partington Wharfside, in Trafford, near Manchester in the U.K., will install a new lightweight linerboard production line, to be supplied by Metso, Finland
Learn More...
|
|
New Products
West Linn Paper Co., West Linn, Ore., USA, announced this week that the Capistrano product line is now available with FSC certification
Learn More...
|
Published Pricing
RockTenn, Norcross, Ga., USA, has announced a price increase on its CartonMate bleached paperboard products
Learn More...
|
SCA Containerboard, Sweden, this past week announced a price increase of EUR 60 per metric tons on in its recycled containerboard grades in all European markets, effective April 1
Learn More...
|
People
Appleton, Appleton, Wis., USA, has named Jeff Fletcher VP of financial operations
Learn More...
|
Neenah Paper, Alpharetta, Ga., USA, this week announced that John P. O'Donnell has been named COO, reporting to Sean Erwin, chairman and CEO, effective June 1
Learn More...
|
Travels with Larry
Corrugated box maker thrives on history of strong customer service and detailed analysis of customer needs.
Learn More...
|
TAPPI News
Popular program moves to larger hotel venue so participants can lodge where they learn, April 19-21, in Norcross, Ga.
Learn More...
|
Early bird rates available until April 16 for the June 1-3 event.
Learn More...
|
TAPPI visits the Ohio Local Section, which shares details about April 9th meeting at Miami University in Oxford.
Learn More...
|
Unique event to focus on practical ways for converting a broad range of biomass resources to renewable energy.
Learn More...
|
Technology and Deployment presentations sought for annual bioproducts and bioenergy event.
Learn More...
|
Dates announced for upcoming meetings in Atlanta, GA.
Learn More...
|
The TAPPI International Conference on Nanotechnology for the Forest Products Industry solicits program info for 2010.
Learn More...
|
"Nothing is more difficult, and therefore more precious ... "
Learn More...
|
|
Find us on Facebook
Network with us on LinkedIn
Follow us on Twitter
|
Weekly Spotlight
Fortress Paper, Vancouver, B.C., Canada, a producer of security and specialty papers, in a major strategic move this week, announced the acquisition of the Fraser Paper Thurso, Que., northern bleached hardwood kraft (NBHK) mill, with the intention to convert it into a "world class, low cost" specialty cellulose (dissolving pulp) operation. Concurrently, Fortress Paper intends to build a biomass-based cogeneration plant at the Thurso Mill that will produce green electricity, resulting in material net energy savings (income).
On closing of the acquisition of the Thurso mill, which will be completed through Fortress's wholly-owned subsidiary Fortress Specialty Cellulose Inc., the company intends to incur capital expenditures of approximately $153 million to convert the non-operating NBHK mill into a high quality specialty cellulose mill and to construct a new cogeneration facility. In connection with the proposed capital expenditures, Fortress announced that it has pre-arranged specific financing initiatives to fund the conversion and cogeneration projects.
The specialty cellulose mill is planned to have an annual production capacity of more than 200,000 air dried metric tpy and is expected to be completed in mid-2011. In entering into the specialty cellulose sector, Fortress Specialty will focus on producing dissolving grade cellulose for the textile industry, primarily targeting viscose fiber (rayon) products that have shown strong growth of approximately 10% in China and 7% worldwide over the past five years.
The25 MW cogeneration facility will service a net 18.8 MW power supply agreement over a 15-year term. The location of the cogeneration facility provides it with access to on-site generation of biomass and an extensive local network of chip and other biomass suppliers. The cogeneration facility is expected to be supplying electricity in the fourth quarter of 2012.
Chad Wasilenkoff, CEO of Fortress Paper, said that "we are very pleased to announce this new acquisition, which we believe will add significant shareholder value in the years to come. Both the board of directors and management of Fortress Paper feel that this new opportunity warrants the diversification of the corporation into other specialty sectors as it has the potential to materially enhance shareholder value. Once the conversion and cogeneration projects are complete, we will be entering a new product segment that offers long-term growth prospects and attractive margins. During the interim period, we will capitalize on the current strength of the NBHK pulp market. We feel it is important to emphasize that this is not an acquisition to enter into the pulp industry, but rather the opportunity to acquire assets that are ideally suited to be converted into a bio-refinery and produce high value-added products. We intend to strategically enter this sector at a time when demand exceeds current capacity. We believe this trend will continue over the next several years given the limited announced new capacity."
Fortress Paper will pay Fraser $3 million in cash at closing, subject to certain adjustments. Included in the assets being purchased from Fraser is approximately $9.9 million in credits (black liquor credits) granted under the Canadian government's Pulp and Paper Green Transformation Program (GTP).
Back To Top
|
TAPPI's Papermakers Committee has organized a strong program of peer-reviewed papers for PaperCon 2010, May 2 - 4 in Atlanta, Ga., USA. The latest additives for improving strength, bulk, and biological control are discussed in the Papermaking Chemistry and Microbiology Track kicking off on Monday, May 3. Speakers from the following organizations are featured:
- Auburn University
- Ashland Hercules Water Technologies
- BASF
- Buckman
- Dow
- Guangxi University
- Kemira
- Omya
- Seoul National University
- VTT Technical Research Centre of Finland.
Process Control Innovations are also highlighted in a peer-reviewed program that reveals how the latest sensors, cameras, and controls can help reduce drying energy, control sheet quality, and help you make better production decisions. Papermakers, process engineers, and anyone yearning to learn more about paper machine process control can attend a "Paper Machine Sensors Tutorial" on Monday, May 3, covering the foundations.
The full program and speakers for PaperCon 2010 are available on the event website. The registration deadline is April 5, with substantial discount available to mills sending three or more people.
Back To Top
|
The Twenty-Third Process Industry Reliability & Maintenance (PIRM) Conference being co-located with PaperCon 2010 at the Hyatt Regency Atlanta, Atlanta, Ga., USA, May 2-5, covers the maintenance function from several critical perspectives while focusing on basics and methodologies that have developed and evolved over more than a century. Some of business and industry's top reliability and maintenance experts examine safety, training, the future workforce, vibration analysis and control, lean manufacturing, and spares and parts management, along with other key R&M issues common to a broad spectrum of manufacturing based industries.
Several case study reports during PIRM explore how mills and plants are going "back to the future' to rediscover time-proven effectiveness and efficiencies of certain maintenance basics. A session on Tuesday morning, May 4, debunks some of the myths and stereotypes surrounding the maintenance operation.
A series of workshops woven through the conference go deep into the how-to sides of reliability and maintenance. Four of these workshop on Wednesday, May 5, look at early detection and prevention of equipment failures, basics of hydraulic systems reliability and maintenance, seven steps to optimize a lubrication program, and using vibration analysis as a trending tool.
The Early Bird registration deadline for PIRM is Monday, April 5. Contact information about sponsorship/exhibit opportunities is also available on the event's website. Attend the entire conference and receive 1.8 Continuing Education Units.
Back To Top
|
Market Roundup
The American Forest & Paper Association (AF&PA), Washington, D.C., USA, this week released its 50th Annual Survey of Paper, Paperboard, and Pulp Capacity, which reported that U.S. paper and paperboard capacity declined 2.5% in 2009 to 93.9 million tons. The decline took place against a backdrop of a severe global economic recession. Paper and paperboard production is rebounding from the recession-induced lows reached in early 2009.
The survey also reported that 14 U.S. mills were permanently closed in 2009, shutting down 16 paper and paperboard machines, and an additional 11 machines were permanently shutdown at other mills. Furthermore, several mills and machines have been indefinitely idled in response to weak market conditions, but have not been removed from the survey base because they may be restarted at some future date.
According to data reported to the survey, total paper and paperboard capacity is expected to decline 3.4% in 2010 and then remain essentially stable in 2011 and 2012.
The survey reports U.S. industry capacity data for the years 2009 through 2012 for all major grades of paper, paperboard, and pulp, based on a comprehensive survey of all U.S. pulp and paper mills. Survey respondents represent about 90% of the U.S. industry capacity.
The complete survey with detailed tables can be purchased for $1,650 by contacting Michelle Gaskins at AF&PA (202-463-5162).
Back To Top
|
AF&PA also announced this week that a record-high 63.4% of paper consumed in the U.S. was recovered for recycling in 2009, noting that "this is great news for the industry and the environment, and exceeds the industry's 60% recovery goal three years ahead of schedule. To balance growing global demand for recovered fiber and decreased paper consumption, increasing recovery nationwide remains a priority."
AF&PA President and CEO Donna Harman said that "recycling is one of America's great environmental success stories and the paper industry is proud of our ongoing leadership role in this arena. Today's announcement is a testament to the work of the industry and the commitment of millions of Americans who recycle at home, school, and work on a daily basis."
Back To Top
|
Pulp & Paper
Atlantic Packaging Products, Toronto, Ont., Canada, this week announced that it has closed its Whitby Newsprint mill, following effort to reduce operating costs and improve performance results. The closure became effective March 19.
The Whitby facility has been in operation since 1990 and employs 151 salaried and hourly staff. Canada's first 100% recycled newsprint mill is located in the Ontario lakeside community of Whitby on the eastern edge of Greater Toronto. Opened by Atlantic Newsprint in 1991, the plant recycles more than 200,000 metric tons of used newspapers and magazines annually, converting them into newsprint. Among its customers are some of North America's largest daily newspapers.
The company attributes the closure to a combination of factors including a drastic decline in North American newsprint demand, the rising value of the Canadian dollar, increased costs for raw material, and an overcapacity in the newsprint manufacturing sector.
John Cherry, president of Atlantic Packaging Products, noted that "we are disappointed that this step is necessary and deeply regret the impact it will have on our employees, their families and the community. We will continue to treat those affected with respect and fairness. Unfortunately discussions with various government levels and the union were not enough to offset the negative impact of the market conditions affecting the newsprint industry."
Back To Top
|
Chile's CMPC reported earlier this week that it expects in April to gradually recover a "substantial" part of pulp output capacity in four plants shutdown after the February 27 earthquake, according to a Reuters news report. The factories Laja, Pacifico, Sante Fe I, and Santa Fe II are still down but the damage is not irreparable and is covered by insurance, CMPC said. Much of the rest of its operations came back online as its posterboard, wrapping paper, sawmill, and plywood businesses re-established normal activity. However, the newsprint mill of Inforsa en Nacimiento will not be operational until the first half of April, the company said.
Chilean rival Arauco, the forestry unit of conglomerate Empresas Copec, reported its Valdivia pulp plant came back on line but said the company was still evaluating damage to other operations from the earthquake zone in south-central Chile, the Reuters report noted. Valdivia has an annual production capacity of 550,000 metric tons.
Back To Top
|
Kruger Inc., Montréal, Qué., Canada, will extend the shutdown of No. 3 paper machine at its Wayagamack Mill in Trois-Rivières, Qué, for a period of one month, starting March 31. The company says it came to this decision due to ongoing weak market conditions, such as the high value of the Canadian dollar and low demand for directory paper.
PM 3 was shutdown on December 31, 2009, and was planned to restart on March 31. Production is now planned to resume on May 1.
Kruger Inc. is a producer of publication papers, tissue, lumber and other wood products, corrugated cartons from recycled fibers, green and renewable energy, and wines and spirits. The company operates paper and paperboard facilities in Quebec, Ontario, Alberta, British Columbia, Newfoundland and Labrador, and the U.S. It has 9,000 employees.
Back To Top
|
(USCAP), Washington, D.C., USA, announced last week that Weyerhaeuser, Federal Way, Wash., has joined the coalition of business and environmental groups pushing for climate and energy legislation. USCAP noted that Weyerhaeuser is a major force for sustainable business practices and understands the need for sensible, clear legislation that "puts the U.S. on the pathway to creating new energy technologies that will fuel our economy. Weyerhaeuser is joining at a critical time and will play a vital role in advancing the objectives of all USCAP members."
Weyerhaeuser owns or manages 21 million acres of timberland and has offices or operations in 10 countries. A coalition of corporations and environmental NGOs representing a broad spectrum of the U.S. economy, USCAP is dedicated to enacting bipartisan energy and climate legislation that will create American jobs, enhance energy security, and put the U.S. on a path to lower greenhouse gas emissions.
"The forest products industry will play a leading role in reducing dependence on fossil fuels and reducing emissions of carbon dioxide using biomass from forests, a sustainable resource and one of the best at sequestering carbon," said Weyerhaeuser CEO Dan Fulton. "The role of forest fiber in a low carbon economy will depend on the public policy concepts under debate in Washington, D.C. USCAP has successfully integrated the expertise of numerous stakeholders and we believe our membership will help positively position sustainable forestry, biomass, and forest products in these important policy discussions."
Back To Top
|
Containerboard/Packaging
Total U.S. containerboard paper production again rose sharply in February compared with February 2009, according to the American Forest & Paper Association's (Washington, D.C., USA) February 2010 U.S. Containerboard Statistics Report released this week. Total production saw an increase of 208,400 tons or 8.9% over the same month last year. For the two months of 2010 production was 13.9% over 2009.
Additional key findings from the report include: linerboard production was up from last year, corrugating medium production follows the trend and increased over February 2009, and operating rates also reflected the year-over- year increase.
Back To Top
|
Cheng Loong Corp. will install a new containerboard production line at its Hou-Li paper mill in Taiwan, to be supplied by Metso, Finland. The production line is scheduled to startup in the second quarter of 2011. The value of the order exceeds EUR 20 million.
Metso's delivery will include three headboxes for the three-ply liner machine with a dilution profiling system for the back ply, a press section, and a film size press. The dryer section will be equipped with a moisturizing unit for web moisture profile control.
Established in 1959, Cheng Loong Corp. has four paper mills and five paper box plants in Taiwan. The company's annual production capacity of paper and paperboard is approximately 1.8 million metric tons.
Back To Top
|
MeadWestvaco Corp., Richmond, Va., USA, this week announced that its Brazilian subsidiary, Rigesa, is undertaking a formal study to assess the feasibility of expanding its paper production through a new linerboard machine at the Três Barras facility, located in Santa Catarina State, Brazil. The analysis, which is currently in its initial phase, is part of the company's strategy to grow its operations in emerging markets.
Rigesa, a wholly-owned subsidiary of MWV, supplies packaging solutions in the food, cleaning, cosmetics, health, chemicals, and electronic markets. It operates two paper mills, four corrugated packaging plants, one consumer packaging plant, and owns 54 thousand hectares of forestry certified by Cerflor – Brazilian Program of Forestry Certification in Brazil.
Back To Top
|
MeadWestvaco Corp., Richmond, Va., USA, this week reported that its MWare food service paperboard has been certified by the Biodegradable Products Institute (BPI). Cups, plates, and other disposable containers made from MWare PLA-coated and uncoated bleached paperboard can be commercially composted with food waste and can feature BPI's compostable label.
All MWare paperboard materials are made from Sustainable Forestry Initiative (SFI) certified, sustainably sourced paperboard and can be made with up to 30% post consumer recycled fiber. MWare Balance coated cup stock is made with PLA (polylactic acid), a bio-based resin that offers the functional performance of non renewable coatings but is made with annually renewable resources.
"Consumers are increasingly concerned about how their habits impact the planet, including their use of disposable cups and plates," said Dobbie Newman, director of Food Service Marketing, MWV. "Providing certified compostable solutions that can be diverted from the landfill waste stream and are made from renewable resources gives our customers additional options for meeting their food service packaging needs. While we recognize that commercial composting facilities for these products are limited, we view composting as an important end-of-life option for organic materials and believe that commercial composting capacity will continue to grow. This achievement is also an important element of enabling MWV to meet its own sustainability goals."
Back To Top
|
Iggesund Paperboard AB, Sweden, reports that its newly published Graphics Handbook gives examples of many different paperboard graphic design techniques and describes how to achieve them. "Many graphic designers are unsure of how they can benefit and what they can achieve by using paperboard instead of paper," explains Jonas Adler, applications specialist at Iggesund and one of the book's authors. "In this handbook we have collected examples of paperboard techniques that are especially relevant to anyone who wants to develop their creativity to new and exciting levels." He emphasizes, though, that the book is not just aimed at designers. It also contains a more technical section which advises printers on the best ways to achieve success with paperboard.
"Throughout much of the graphics industry there is uncertainty about paperboard as a material," Adler says. "People would rather use a thick grade of a brand of paper that they know, even if they thereby lose out on the many advantages paperboard would have given them."
The Graphics Handbook is part of Iggesund's "Iggesund Anchor" reference material. The material also includes The Paperboard Reference Manual, which is used as a standard reference work in many packaging and design courses. The Graphics Handbook has 90 pages and is richly illustrated. It is currently available only in English but additional language versions are planned.
An extract of the Graphics Handbook can be seen at Iggesund's website, where it can be ordered at a cost of 25 Euro including postage.
Back To Top
|
Smurfit Kappa Completes Mill Modernization, Integration in the Netherlands Smurfit Kappa Group, Ireland, reports that the modernization of its mill in Etten-Leur, the Netherlands, and its integration with the company's nearby Oudenbosch facility, is now complete. There is now a single plant named Smurfit Kappa ELCORR (formerly known as Smurfit Kappa Oudenbosch Golfkarton), which manufactures corrugated board packaging throughout the Benelux. A single corrugator at the ELCORR factory will produce 150 million square meters of packaging annually, made possible by the facility's combination of an advanced level of automation, its unique scale, and a highly skilled workforce, Smurfit Kappa says.
Back To Top
|
Work is underway to transition Sonoco Recycling, Inc.'s Charlotte, N.C., USA, Recycling Center into a full-scale material recovery facility (MRF) by early summer. The $2.6 million project will result in the Charlotte center, located at 3901 Barringer Drive, becoming the third MRF owned and operated by the company in the Southeast. The others are located in Raleigh, N.C., and Columbia, S.C.
In November 2009, Sonoco Recycling completed a $2 million expansion project at the Charlotte center. The project expanded the facility's footprint by 23,500 square feet and included the installation of new commercial sorting and baling equipment. In addition, the facility's outside space was redesigned to improve traffic flow. The Charlotte center accepts and processes corrugated boxes and other grades of paper as well as plastic and other materials. It accepts curbside material delivered by the public and offers flatbed pick up of baled material, and van pick up for loose, palletized, or baled material. Sonoco, which processes and uses many of these recycled materials to produce recycled paperboard at its paper mills in the Southeast, then uses that paperboard to produce new consumer and industrial packaging, making Sonoco one of the few closed loop suppliers of packaging in the industry.
Marcy Thompson, VP and GM, Sonoco Recycling, noted that "at Charlotte we're adding high-tech equipment that will allow us to further grow our capacity and more effectively sort residential single-stream waste. Additions will include new sorting screens, separators, high-speed conveyors, steel disks, and other state-of-the-art equipment. While Mecklenburg County is already served by a materials recovery facility, the area needs a second MRF because of the tremendous growth throughout the region. These upgrades, along with the upgrades we completed last fall, better position us to meet the recycling needs of this growing market."
Back To Top
|
Saica Containerboard U.K., at Partington Wharfside, in Trafford, near Manchester in the U.K., will install a new lightweight linerboard production line, to be supplied by Metso, Finland. Startup of the new line is scheduled for the first quarter of 2012. Total value of the order is approximately EUR 60 million.
Metso's delivery will include a complete paper machine, including an approach flow system, pulpers, and air systems. A comprehensive Metso automation package will comprise process, machine, and quality controls. A Metso process control system will also be supplied for the new combined heat and power station at the Partington mill.
Annual production capacity of the machine will be approximately 400,000 metric tons of testliner and fluting out of 100 % recycled furnish.
Saica Containerboard is a subsidiary of SAICA, a family owned Spanish company and a global producer of lightweight corrugated containerboard from recovered paper. The company currently employs more than 8,000 people in Spain, France, Portugal, Italy, Ireland, and the UK. SAICA has an annual turnover of EUR 2.2 billion.
Back To Top
|
New Products
West Linn Paper Co., West Linn, Ore., USA, announced this week that the Capistrano product line is now available with FSC certification. This new product offering has the same product qualities and specifications as the company's standard No. 2 coated freesheet. Capistrano grades but can be purchased with the option to include the use of FSC-certified pulp, which is tracked through the chain-of-custody process to ensure that it is acquired from forests that are managed in accordance with the FSC's principles and criteria.
Capistrano FSC-certified products will be available in gloss, matte, and dull finishes in 60 lb to 100 lb text weights, 60 lb, 65 lb, and 80 lb cover as well as 7 pt. and 9 pt. reply card. In addition, West Linn Paper offers an equivalent recycled version (Nature Plus) with up to 30% post consumer waste content and FSC certification.
West Linn Paper Co. is an independent manufacturer of coated free-sheet web paper and is the oldest active paper mill and the only coated free-sheet manufacturer in the western U.S.
Back To Top
|
Published Pricing
RockTenn, Norcross, Ga., USA, has announced a price increase on its CartonMate bleached paperboard products. The increase will be $50 per ton for these packaging grades, effective April 21.
Back To Top
|
SCA Containerboard, Sweden, this past week announced a price increase of EUR 60 per metric tons on in its recycled containerboard grades in all European markets, effective April 1. The company attributed the increase to the "enormous pressure of increasing input costs, particularly raw material including related availability," and the fact that market conditions are "currently good."
Back To Top
|
People
Appleton, Appleton, Wis., USA, has named Jeff Fletcher VP of financial operations. In this new position, Fletcher assumes executive oversight of the finance functions of Appleton's paper manufacturing operations and its Encapsys business. He will also have oversight of the company's information and technology department, and the procurement, tax, risk, and insurance functions. He has served as Appleton's controller since joining the company in 2007.
Pat Jermain has been named company controller. Jermain will serve as the principal accounting officer and have responsibility for company reporting to the Securities and Exchange Commission, corporate budgeting, forecasting and financial planning, cash management, and accounts payable. Jermain joined Appleton in 2006 has been serving as director of enterprise risk management.
Back To Top
|
Neenah Paper, Alpharetta, Ga., USA, this week announced that John P. O'Donnell has been named COO, reporting to Sean Erwin, chairman and CEO, effective June 1. O'Donnell has been president of Neenah's Fine Paper business since he joined the company in November 2007. Prior to joining Neenah Paper, O'Donnell held positions at Georgia-Pacific Corp., including president of its North America Retail Business and president of its Commercial Tissue Business. He has extensive knowledge of the paper and tissue industry and in his new role will have direct responsibility for both the Fine Paper and Technical Products businesses, providing leadership over innovation, sales, marketing, manufacturing, and distribution activities.
In addition, Armin Schwinn has been named senior VP and managing director, Neenah Germany effective April 1. Schwinn succeeds Dr. Walter Haegler, who will retire after 20 years as managing director during which he led the substantial growth and development of these businesses. Schwinn has been part of Neenah Germany since 1995 and was most recently VP, Finance, responsible for financial, purchasing, and administrative functions. Prior to that, he served in various leadership positions in other German manufacturing and service companies.
Back To Top
|
Travels with Larry
In 1966, the St. Louis Cardinals were preparing for a new era of baseball in a space age designed ballpark -- Busch Memorial Stadium. That same year, an upstart corrugated sheet plant -- Buckeye Boxes Inc. -- was founded in Columbus, Ohio, during this magic age of space travel. While the two events are unrelated except for their timing, the baseball reference reminds me that I love this Spring Training time of year, because it's the point when everyone has a perfect record. The true, sustainable winners won't step forward for some time to come.
Earlier this month, Eric Fletty and I had the opportunity to visit with one of the long time supporters of TAPPI's Corrugated Packaging Division, Craig Hoyt, who is a current member of TAPPI's Corrugated Packaging Council. Craig's father and three others, with an average of 15 years experience in corrugated, founded Buckeye in 1966. But why in Columbus? Back in 1966, there was only one sheet plant in the city.
Buckeye was quickly recognized for its quick service and adherence to the Buckeye Mission: We must improve our customer's bottom line by solving the customer's problems, especially ones they don't know they have.
"We baby our customers; we are just weird that way," Craig told us. And Buckeye doesn't just talk about doing so; they actually measure quantifiable and qualifiable improvements. One of Buckeye's slogans is the "Corrugated Solutions ROUND 2 IT: Bottom line, we get you around 2 more Profit."
ISO 9001 Certified since 1997, Buckeye practices a process of Customer Value Analysis (CVA). This team-selling approach examines both the customer's entire packaging system, as well as how that system can improve its customer's supply chain. Using Lean Enterprise applications, Buckeye discovers opportunities, creates solutions, and captures savings that sell its customized value propositions.
Craig began his immersion in the corrugated industry by working five of his high school and college summers in the Buckeye box plant. After graduating from college, he spent three years with Continental Can.
"I learned what products fit an integrated plant and what fits in an independent sheet plant," Craig explained, "I sold out of both types during that time of my career."
Craig also learned how capital expenditures are handled in some large corporations. He discovered that, in many cases, capital was spent to get boxes to fit a certain machine rather than to fit the customer's wants. Craig feels that his competitors come from independents rather than the integrated plants. Buckeye has some employees and customers who have been with it for 40 years. The company's design lab and maintenance shop allows Buckeye to customize its equipment to meet a customer's needs. "In short, we just service our customers better than our competition," Craig explained.
Craig's take on TAPPI is that we are going in the right direction. He suggested that we somehow try to bridge the "disconnect" between the mills and the converter side of the business. The end customer should dominate the decisions made at the mill level, and he feels that TAPPI needs to be the LINK between the two.
Craig also recommends that TAPPI take more of a leading role in bringing information on new innovation and technologies into the converting side of the business.
"Independents need to find more value in their TAPPI memberships and understand how TAPPI's strategic plan includes their interests. Production professionals need to know what's in it for them," Craig said.
To that end Craig will help TAPPI's Corrugated Packaging Division update its strategic plan, and TAPPI will spread the word of its overall strategic plan to our entire membership. Going back to the baseball theme, Buckeye has and will continue to show how a true, sustainable winner steps forward.
My thanks to Craig Hoyt, president and CEO; Ken Churchill, vice president of Sales; and Chris Pieroni, assistant general manager, for making us feel welcome at Buckeye Boxes.
For more information on Buckeye Boxes Inc., contact Ken Churchill at kenchurchill@buckeyeboxes.com.
For more information on TAPPI, please go to www.tappi.org.
There are two types of people in our industry, TAPPI members, and those who should be.
Until next time -- Larry
Back To Top
|
TAPPI News
Offered for the first time in years, TAPPI is pleased to unroll the Tissue Runnability Course, April 19-21, 2010 – an essential program for paper professionals at TAPPI's Atlanta headquarters. This course offers a comprehensive understanding of the tissue making process at many levels that can be applied immediately on the job. Instructional topics are focused on helping attendees improve the quality of their products, diminish waste and poor output and reduce frustrating down-time. The course material is designed with the objective of helping participants thrust production into high gear.
The Tissue Runnability Course is designed expressly for engineers, machine supervisors, technical resources, lead operators and technical personnel in tissue and towel mills. The three-day event covers the impact of recycled furnishes on paper characteristics, the principles of wet-end chemistry with machine operation, cleaning and conditioning of felts and wires, causes of tissue runnability problems in the press/Yankee/hood drying systems, identifying improvement opportunities on the dry-end of the paper machine, and pinpointing problems with the Yankee dryer steam, coating, and hood systems to increase machine productivity. The course schedule is led by industry-recognized instructors.
Registration for this course has been so robust, the training room has moved to a larger venue – the Hilton Atlanta Northeast in Norcross, Ga. This means, you can stay in the same location as the training sessions for even more convenience. Lodge Where You Learn!
Hilton Atlanta Northeast
5993 Peachtree Industrial Blvd
Norcross, GA 30092
Telephone: +1.770.447.4747
Tissue Runnability is still open, but prompt registration is still encouraged for this course!
Back To Top
|
Event: PulPaper 2010
Date: June 1-3, 2010
Location: Helsinki,Finland
For the seventh time, the global pulp, paper, board, and converting industry will meet in Helsinki for the PulPaper exhibition and conference. The event, organized by Adforum in cooperation with the Paper Engineers' Association, AEL and The Finnish Fair Corporation, will be the largest show for the pulp, paper, board and converting industry worldwide in 2010. Exhibitors and visitors travel from all over the world to take part in this international event. The last PulPaper show in 2007 attracted more than 16,000 visitors from 78 countries. TAPPI is co-sponsoring the nanotechnology session.
Along with the exhibition, there will be a conference with the theme of "Implementing the new rise." The theme will cover topics that the forest products industry must address to maintain its position and improve results in a changing environment.
Registration is now open and early bird fees are valid until April 16.
Back To Top
|
Nominations are being accepted for induction into the Paper Industry International Hall of Fame. The deadline for nominations to be considered for 2010 is March 31st. The 16th induction ceremony will be held September 23rd in Appleton, Wisconsin.
Any individual, living or deceased, who has pioneered and/or uniquely helped the world's paper industry flourish, is eligible for induction into the Paper Industry International Hall of Fame. Recognition will be based on contributions in the following categories: Academics; Economics; Entrepreneur; Founder; Leadership; Marketing/Sales; Research and Development; Service; and Technology.
The 2010 nomination form is available at www.paperhall.org. Contact Dave Lee, executive director, for further information at 920-380-7491 or dave@paperdiscoverycenter.org.
Back To Top
|
What's high in the middle and round on the ends? Well, Ohio of course, and TAPPI's Ohio Local Section is high on planning for their next meeting (April 9, 2010 at Miami University, Oxford, Ohio). Ok, bad joke – but no where near a bad meeting!
Recently, Larry Montague and Eric Fletty had the pleasure of visiting Appleton's West Carrollton Mill and not only saw TAPPI members (from both Appleton and Ashland – Hercules) in action but discussed plans for the upcoming Ohio TAPPI Local Section Meeting. The Local Section has undergone a reinvention of itself and has a great event planned. For just $10, (register by March 26th for this early bird rate) you get:
- 9:00 AM - Upgrades and modernization of stock prep systems - J. Kerr, ANDRITZ
- 10:00 AM - Doctor blade setting - S. Cockerham, KADANT
- 11:00 AM - Paper machine water management for the Fourdrinier -S. Stewart, JOHNSON FOILS
- Lunch (provided)
- 2:00 PM - Automation: Color control & air systems, air dryers, heat recovery -T. Betteridge & M. Harrison, METSO
- 3:00 PM - How CD moisture actuators can save energy - J. Spachman, ABB
Registration couldn't be easier – just e-mail Prof. Doug Coffin at Prof. Doug Coffin at coffindw@muohio.edu. Additional information can be found at this link.
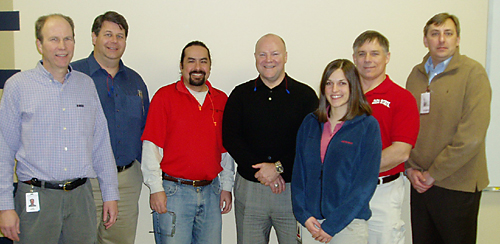
Pictured (Left to Right): Tom Maleike, Manager – Utilities, Process Control, Technical, Appleton
Jim Fuller, Quality Manager, Appleton
Bill Levenderis, Process Control Engineer, Appleton
Larry N. Montague, President & CEO, TAPPI
Nicole Hartley, Technical Sales Representative, Ashland-Hercules
Philip B. Keegan, Sales Team Leader, Ashland-Hercules
Eric Fletty, Vice President Operations, TAPPI
Back To Top
|
Early discounted registration is now open for the 2010 BioPro Expo™ and Conference, slated for August 24-26 at the Cobb Galleria Centre in Atlanta. Providing program content and comprehensive exhibits created with multiple industries in mind, BioPro Expo™ explores practical methods for transitioning a variety of biomass feedstocks into energy and biofuel. This unique event will bring together diverse communities ranging from forest, agriculture, and biorefinery operations to power companies and technology suppliers – offering the Southeast's most powerful educational and professional networking experience in the bioenergy arena.
BioPro Expo will include in-depth case studies and technical sessions from experts in a variety of industries. In addition, there will be a comprehensive tradeshow and hands-on technology interaction. Additional input from governmental agencies will supplement this experience with perspective on the rapidly changing regulatory and funding environment impacting renewable energy efforts.
Registration fees are $485 for TAPPI members and $746 for non-members, if confirmed by July 2, 2010. Onsite registration is $735 for TAPPI members and $1,125 for non-members. Registration information is available at www.bioproexpo.org.
Back To Top
|
The 2010 International Bioenergy and Bioproducts Conference (IBBC) is now an important conference component of BioProExpo™. IBBC will include technical presentations, expert panels, case studies, and reports from projects that address the production of biofuels and bioproducts through: the use of forest and agricultural biomass resources; biorefining technology; feedstock and harvesting improvements to increase yield and quality of biomass; and leveraging forest products manufacturing infrastructure.
Presentations are being sought in the following topic areas:
Technology Track: Seeking strong technical papers with a focus on presenting new findings in Biomass Supply & Demand, Biomass Harvesting & Preparation, Advances in Conversion Pathways and Advances in Bioproducts.
Deployment Track: Seeking case studies and updates from pilot scale, commercial, and pre-commercial operations in Biorefineries, Repurposing the Traditional Pulp and Paper Mill, Harvesting and Preparation, Technical Economic Analyses, Commercial Collaborations for Enabling Technologies and Project Deployment Issues.
For more information on the IBBC Call for Papers, visit http://www.bioproexpo.org/ibbc_call.asp.
Abstract Requirements: Abstracts should be no more than 200 words.
Submission Deadline: March 22, 2010
Presentations Deadline: August 2, 2010
Submit Abstracts to: IBBC@tappi.org
Event Website: www.bioproexpo.org
Back To Top
|
Date(s):
Spring 2010 -- April 12-14
Fall 2010 -- October 4-6
Spring 2011 -- April 4-6
Fall 2011 -- October 3-5
Location:
Crowne Plaza Hotel at the Atlanta Hartsfield-Jackson Airport
The Black Liquor Recovery Boiler Advisory Committee (BLRBAC) guides the safe installation and operation of recovery boilers at kraft paper mills. Their meetings draw attendees from all over the world, from the operating mills, the manufacturers of recovery boilers and associated equipment, to engineers from the insuring companies. Many members of BLRBAC are also TAPPI members that serve on the Steam and Power Committee.
Visit www.blrbac.org for registration information and additional details or contact David Parrish at david.parrish@fmglobal.com.
Back To Top
|
A Call for Presentations/Posters has been issued for the 2010 TAPPI International Conference on Nanotechnology for the Forest Products Industry, 27-29 September, 2010, in Espoo, Finland. This annual, internationally recognized event brings together leading researchers, industry experts, government representatives, and other stakeholders to share advances and perspectives on nanotechnology-based products for the forest products and related industries.
To leverage research advances and offer participants new opportunities for knowledge sharing, the 2010 Technical Program Committee invites contributions from participants working with nano-enabled bio-materials, products, and their processing. Analysis of challenges and trends in emerging markets for forest products that are based on nanotechnology are sought to provide a foundation for new research and industrial activities. The organizers also encourage submissions on other aspects of nanotech products including law, policy, economics and environmental health and safety. View the Call for Papers.
Back To Top
|
"Nothing is more difficult, and therefore more precious, than to be able to decide."
-- Napoleon Bonaparte (1769 – 1821), French military and political leader
This quote was submitted by Michael Webber, senior process specialist, NewPage Research.
Share YOUR favorite advice or interesting ideas -- about life, business, the industry, work or leadership -- by sending in a quote to share with other Over the Wire readers. Email your quote suggestions, along with your name and company information, to mshaw@tappi.org. We value the input of our OTW readers.
Back To Top
|
|
|
TAPPI Over the Wire | 15 Technology Pkwy. S. | Norcross, GA 30092 USA | Voice: 770.446.1400 | Fax: 770.446.6947
|
 |