 |
|
Weekly Spotlight
The U.S. Environmental Protection Agency (EPA), Washington, D.C., USA, this past week issued the final Clean Air Act standards for boilers and certain incinerators (Boiler MACT) that purportedly cuts the cost of implementation by about 50% from an earlier version of the proposal issued last year
Learn More...
|
Economic activity in the U.S. manufacturing sector expanded in February for the nineteenth consecutive month, and the overall economy grew for the twenty-first consecutive month, the nation's supply executives report in the latest Manufacturing ISM Report on Business
Learn More...
|
The Eighth Biennial Johan Gullichsen Colloquium, set for Nov. 22, 2011, in Espoo Finland, has issued a call for papers in three areas
Learn More...
|
Dr. Wolfgang Palm, president of the German Pulp and Paper Association, Frankfurt, Germany, noted at the association's annual press conference this past week that production and sales had risen over the year by more than 10% to 23.2 million metric tons
Learn More...
|
The listing of job openings in the TAPPI Career Center continues to increase as the U.S. and global pulp, paper, and forest products recovery progresses
Learn More...
|
A breaking-news session added to the TAPPI BioPro Expo technical program www.bioproexpo.org focuses on latest analyses showing that ethanol-based biofuels cannot be the functional pathway of choice to meet U.S. Renewable Fuels Mandates in coming years
Learn More...
|
Market Roundup
The global demand for dissolving pulp has increased sharply during the past decade, reaching 4.5 million metric tpy in 2010
Learn More...
|
Wipes will continue to benefit from features such as ease-of-use, disposability, portability, and reduced risk of cross-contamination
Learn More...
|
Global pulp production in the second half of 2010 was higher than many people anticipated, and pulp markets were better than they had been the first six months of the year
Learn More...
|
Pulp & Paper
The Australian Federal Court has handed down $4.2 million in penalties to two foreign companies that ran a purported price fixing "club" in Asia
Learn More...
|
Bel Papyrus Ltd, a member of the Lebanese Boulos Group of Companies, Lagos,Nigeria, this past week reported that it concluded the purchase of a state-of-the-art tissue production line with an average production of 65 tpd from Toscotec, Italy
Learn More...
|
Blue Heron Paper Co., Oregon City, Ore., USA, this past week announced that it is permanently curtailing operations at its Oregon City specialty paper mill and issuing WARN notices to its employees related to permanent closure of the facility
Learn More...
|
Catalyst Paper, Richmond, B.C., Canada, this week announced $13.3 million in federal funding approval for a new green-energy project at its Powell River mill that will produce low-carbon electricity and be one of the cleanest waste wood co-generation projects anywhere in Canada
Learn More...
|
Central National-Gottesman Inc., Purchase, N.Y., USA, reports that its Lindenmeyr Munroe division this week acquired the assets and business of Hudson Valley Paper Co., one of upstate New York and New England's oldest fine paper merchants
Learn More...
|
Domtar, Montreal, Que., Canada, announced this week that its Domtar Distribution Group, Covington, Ky., USA, a network of strategically located paper distribution facilities, has been rebranded under the name Ariva
Learn More...
|
Domtar Corp., Montreal, Que., Canada, is conducting a special dedication ceremony tomorrow, (Friday, March 4), celebrating the startup of a new fluff pulp machine at its Plymouth, N.C., USA, pulp mill
Learn More...
|
Eka Chemicals, Marietta, Ga., USA, the AkzoNobel Pulp and Paper Chemicals business, this week announced that it has been granted permission by the Canadian Pest Management Regulatory Agency to use its Purate® technology to produce chlorine dioxide for applications to control microorganism contamination in pulp and paper mill process water
Learn More...
|
Neenah Paper Technical Products, Alpharetta, Ga., USA, this week announced the direct sales and distribution of its heat transfer papers throughout Europe via its Neenah Paper Lahnstein, Germany, location
Learn More...
|
NewPage Corp., Miamisburg, Ohio, USA, this week announced the upload of a new On Paper sustainability series podcast featuring Lisa Quezada, sustainable development policy manager for MillerCoors
Learn More...
|
Suzano Papel e Celulose S.A. Brazil, and Metso, Finland, reportedly are in advanced negotiations towards concluding a contract for the supply of all main pulp making technology for the 1.5 million metric tpy, greenfield pulp mill to be built in the state of Maranhão in the northeastern part of Brazil
Learn More...
|
ABB, Vasteras, Sweden, reported this week that its System 800xA Extended Automation controller has received KEMA certification for its IEC 61850 electrical integration interface
Learn More...
|
AirTrim designs and supplies a full range of components and systems for conveying and disposing of trim from paper and tissue machines, rereelers, winders, sheeters, and converting equipment
Learn More...
|
Containerboard/Packaging
Dev Priya Industries, India, has commissioned Voith Paper Automation, Germany, to handle the stepwise upgrade of its PM 2 at Meerut, 70 km northeast of New Delhi
Learn More...
|
Fujian Liansheng Paper Co., Zhangzhou City, Fujian Province, China, has successfully started up its Metso (Finland) supplied containerboard machine, PM 3, which produces fluting within the basis weight range of 80 – 120 gsm
Learn More...
|
Graphic Packaging International (GPI), Marietta, Ga., USA, has announced plans to close its Jacksonville, Ark., multiwall bag facility
Learn More...
|
Platinum Equity, Los Angeles, Calif., USA, reports that has completed the acquisition of Nampak Cartons and Nampak Healthcare from South Africa-based Nampak Limited
Learn More...
|
|
Published Pricing
DuPont Titanium Technologies, Wilmington, Del., USA, is increasing prices for all of its TiPure® titanium dioxide grades sold in North America
Learn More...
|
RockTenn, Norcross, Ga., USA, this week announced a $45 per ton price increase on its Millennium grades of high strength, 100% recycled paperboard
Learn More...
|
Energy
On June 1, Dr. Harry Cullinan will assume the position of Director of Technology Deployment at Auburn University's Alabama Center for Paper and Bioresource Engineering, Auburn, Ala., USA
Learn More...
|
Travels with Larry
Anyone who has seen It's a Wonderful Life remembers that famous line "Every time a bell rings an angel gets his wings." At TAPPI headquarters, every time the President's Bell rings, we welcome a new TAPPI member!
Learn More...
|
TAPPI News
TAPPI member Ian Journeaux has spent the majority of nearly 25 years of active membership investing in the future generation of pulp and paper engineers.
Learn More...
|
TAPPI is holding its popular TAPPI Essentials of Market Pulp course on April 30 this year -- just before the opening of the PaperCon 2011 convention May 1-4, 2011.
Learn More...
|
Join your colleagues one day prior to the start of the ICE SHOW for the 2011 TAPPI PLACE Flexible Packaging Symposium, April 5.
Learn More...
|
Jack McAneny, Associate Director Global Sustainability for Procter & Gamble Co. (P&G), will give the keynote address at the welcome session for TAPPI's annual PaperCon Conference on Sunday, May 1, 2011, at 5 p.m.
Learn More...
|
The deadline to submit an extended abstract for the 2011 International Pulp Bleaching Conference has been extended.
Learn More...
|
This is your chance to improve your Linerboard/Medium and Corrugated Box Manufacturing skills - in just two days of your time.
Learn More...
|
Get some relief at the Shipping, Receiving and Warehousing Workshop and learn ways to improve your bottom line.
Learn More...
|
|
Find us on Facebook
Network with us on LinkedIn
Follow us on Twitter
|
Weekly Spotlight
The U.S. Environmental Protection Agency (EPA), Washington, D.C., USA, this past week issued the final Clean Air Act standards for boilers and certain incinerators (Boiler MACT) that purportedly cuts the cost of implementation by about 50% from an earlier version of the proposal issued last year.
In response to a September 2009 court order, EPA first issued the proposed rules in April 2010. Then in December 2010, it requested additional time to review and assess public input the proposal generated and accordingly revise it. The court granted a 30-day extension, resulting in this past week's issuance.
EPA reports that it received more than 4,800 comments from businesses and communities across the country in response to the proposed rules, adding that "public input included a significant amount of information that industry had not provided prior to the proposal." Based on this feedback, and in keeping with President Obama's executive order on regulatory review, EPA notes that it revised the draft standards "to provide additional flexibility and cost-effective techniques – achieving significant pollution reduction and important health benefits, while lowering the cost of pollution control installation and maintenance by about 50%, or $1.8 billion.
Because the final standards differ significantly from the proposals, EPA says it believes further public review is required. Thus it will reconsider the final standards under a Clean Air Act process that allows additional public review and comment "to ensure full transparency." The reconsideration will cover emissions standards for large and small boilers and for solid waste incinerators. EPA says it will release additional details on the reconsideration process in the near future "to ensure the public, industry, and stakeholders have an opportunity to participate."
About 200,000 boilers are located at small and large sources of air toxic emissions across the U.S. The final standards require many types of boilers to follow practical, cost-effective work practice standards to reduce emissions. To ensure smooth implementation, EPA is working with the U.S. Department of Energy (DOE) and the U.S. Department of Agriculture (USDA) to provide technical assistance to these facilities. DOE will work with large coal and oil-burning sources to help them identify clean energy strategies, while USDA will reach out to small sources to help owners and operators better understand and comply with the standards.
The types of boilers and incinerators covered by these updated standards include:
- Boilers at large sources of air toxics emissions. There are about 13,800 boilers located at large sources of air pollutants, such as refineries, chemical plants, and other industrial facilities (including pulp and paper). These standards will reduce emissions of pollutants including mercury, organic air toxics, and dioxins. EPA estimates that the costs of implementation have been reduced by $1.5 billion from the proposed standard.
- Boilers located at small sources of air toxics emissions. There are about 187,000 boilers located at small sources of air pollutants, including universities, hospitals, hotels, and commercial buildings that may be covered by these standards. EPA has limited the impact of the final rule making on these entities considering their small amount of emissions. The original standards for these have been updated to ensure maximum flexibility, including for some sources, revising the requirement from maximum achievable control technology to generally available control technology. The cost reduction from the proposed standard to the final is estimated to be $209 million.
- Solid waste incinerators. There are 88 solid waste incinerators that burn waste at a commercial or an industrial facility, including cement manufacturing facilities. These standards, which facilities will need to meet by 2016 at the latest, will reduce emissions of pollutants including mercury, lead, cadmium, nitrogen dioxide, and particle pollution. The cost reduction from the proposed standard to the final is estimated to be $12 million.
EPA has also identified which non-hazardous secondary materials are considered solid waste when burned in combustion units. This distinction determines which Clean Air Act standard is applied when the material is burned. The non-hazardous secondary materials that can be burned as non-waste fuel include scrap tires managed under established tire collection programs. This step simplifies the rules and provides additional clarity and direction for facilities. To determine that materials are non-hazardous secondary materials when burned under the updated rules, materials must not have been discarded and must be legitimately used as a fuel.
Back To Top
|
Economic activity in the U.S. manufacturing sector expanded in February for the nineteenth consecutive month, and the overall economy grew for the twenty-first consecutive month, the nation's supply executives report in the latest Manufacturing ISM Report on Business. The report was issued this week by Norbert J. Ore,, chair of the Institute for Supply Management Manufacturing Business Survey Committee, Tempe, Ariz., USA.
"February's report from the manufacturing sector indicates continuing strong performance as the PMI registered 61.4%, a level last achieved in May 2004. New orders and production, driven by strength in exports in particular, continue to drive the composite index (PMI). New orders are growing significantly faster than inventories, and the Customers' Inventories Index indicates supply chain inventories will require continuing replenishment. The Employment Index is above 60% for only the third time in the past decade," Ore notes.
Of the 18 manufacturing industries, 14 reported growth in February, in the following order: Apparel, Leather & Allied Products; Petroleum & Coal Products; Transportation Equipment; Electrical Equipment, Appliances & Components; Machinery; Chemical Products; Fabricated Metal Products; Computer & Electronic Products; Textile Mills; Food, Beverage & Tobacco Products; Printing & Related Support Activities; Paper Products; Wood Products; and Miscellaneous Manufacturing. The four industries reporting contraction in February were Plastics & Rubber Products, Primary Metals, Nonmetallic Mineral Products, and Furniture & Related Products.
The full text version of the Manufacturing ISM Report on Business is posted on ISM's web site.
Back To Top
|
The Eighth Biennial Johan Gullichsen Colloquium, set for Nov. 22, 2011, in Espoo Finland, has issued a call for papers in three areas:
- Resources and Infrastructure—where and what biomass is, how accessible it is, how much and what we can have in the future vs. measures to be taken, investments, infrastructure, value chain profitability, and centralization vs. distribution of production units
- Product Diversity – a Necessity—product mix, compatibility, market segments, process integration, co-production of energy and fuels, and the role of wood products
- Totally New Products—be it nano, micro, macro, liquid or solid, you name it, but it must be something totally new.
The deadline for one-page abstracts is April 30, 2011. Submissions should be sent to marja.maunu@papereng.fi. The best presentation will receive the Johan Gullichsen Award (EUR 2000).
Arranged by the Paper Engineers' Association (Helsinki, Finland), and held in conjunction with that agency's Autumn Meeting, the international Johan Gullichsen Colloquium especially encourages and promotes young engineers and scientists. The theme of this year's colloquium is New Wood Based Value Chains--Technical and Economical Feasibility, covering global forest resources, the manufacture and use of a diverse palette of mechanical, chemical, and energy forest products. The intent is to outline a broad view of how forest based industries adapt to and survive in a world short of fossil resources but an abundance of renewable raw materials.
Back To Top
|
Dr. Wolfgang Palm, president of the German Pulp and Paper Association, Frankfurt, Germany, noted at the association's annual press conference this past week that production and sales had risen over the year by more than 10% to 23.2 million metric tons. This means that the industry had already surpassed the pre-crisis performance in 2008, he added. Sales rose in 2010 by 17% to EUR 14.4 billion, although company profits were considerably encumbered by soaring raw material costs, which rose on average in 2010 by more than 80% for recovered paper and almost 70% for pulp compared with the 2009 figures. "This development was bound to have an impact on the market and many companies announced that they would be following other industrial sectors and increasing their prices," Palm said.
Packaging papers saw a marked increase in volume. Production in 2010 was 13% higher than in 2009 and also 9% higher than in 2008. Graphic paper production also improved by10%, although it was still 5% down on the 2008 level. The manufacturers of hygiene papers registered 6% growth over 2009 while technical and specialty papers experienced a marked recovery with a 15% improvement in 2010 after the heavy decline in 2009.
The driving force within the paper industry in 2010 was foreign sales, Palm explained, which performed better than domestic sales, improving by 15% compared with just 6% within Germany. Western Europe remained the largest foreign market. The industry is hoping this year for greater stimulus from the domestic economy.
Back To Top
|
The listing of job openings in the TAPPI Career Center continues to increase as the U.S. and global pulp, paper, and forest products recovery progresses. Current job openings in the TAPPI Career Center include:
Dart Container Corporation |
Senior Materials Engineer #270 |
Georgia Pacific |
Project Manager - ETMS |
SCA Americas |
Paper Manufacturing Asset Manager |
Evonik Goldschmidt Corporation |
Sr/Technical Service Representative- Tissue & Plastics |
Knowlton Technologies, LLC |
Technical Service Manager |
Signature Search |
Director, Quality & Continuous Improvement |
S. Walter Packaging |
Sr. Buyer- Paper Products |
Wadpack Private Limited |
Corrugation Specialist |
Georgia Pacific |
Optimizer, Pulp Mill |
More information about these jobs is available online.
Back To Top
|
A breaking-news session added to the TAPPI BioPro Expo technical program focuses on latest analyses showing that ethanol-based biofuels cannot be the functional pathway of choice to meet U.S. Renewable Fuels Mandates in coming years. Prompted by a new Purdue University study showing that the U.S. simply doesn't have the infrastructure to meet the federal mandate for renewable fuel use with ethanol, the new session explores alternative pathways including cellulosic and next-generation biofuels,
A speaker at this new session, titled "At the Blending Wall: The U.S. Ethanol Quandary," Prof. Frank J. Dooley at Purdue notes that the new study uses DOE and EPA data to determine that the U.S. is at the "blending wall" or the saturation point for ethanol use. Without new technology or a significant increase in infrastructure, he predicts that the country will not be able to consume more ethanol than is being currently produced.
"We can't get there with ethanol," the study's authors insist, pointing out that there just aren't enough flex-fuel vehicles that use an 85% ethanol blend, or E85 stations to distribute more biofuels. According to EPA estimates, they explain, flex-fuel vehicles make up 7.3 million of the 240 million vehicles on the nation's roads. Of those, about 3 million of flex-fuel vehicle owners aren't even aware they can use E85 fuel. There are only about 2,000 E85 fuel pumps in the U.S., and it took more than 20 years to install them.
"Even if you could produce a whole bunch of E85, there is no way to distribute it," Prof. Dooley and the other study authors explain. "We would need to install about 2,000 pumps per year through 2022 to do it. You're not going to go from 100 per year to 2,000 per year overnight. It's just not going to happen."
And even if the fuel could be distributed, E85 would have to be substantially cheaper than gasoline to entice consumers to use it because E85 gets lower mileage, the authors say. If gasoline is, say, $3 per gal, E85 would have to be $2.34 per gallon to break even on mileage.
The EPA just recently increased the maximum amount of ethanol that can be blended with gasoline for regular vehicles from 10% to 15%. But Dooley and the other authors say that even with rapid, total implementation in all states, the blending wall would be reached again in about four years.
Dooley says that advances in the production of thermochemical biofuels will be necessary to meet the Renewable Fuel Standard. He said those fuels would be similar enough to gasoline to allow unlimited blending and would increase the amount of biofuel that could be used.
"Producing the hydrocarbons directly doesn't have the infrastructure problems of ethanol, and there is no blend wall because you're producing gasoline or other drop-in fuels," he notes. "If that comes on and works, then we get there. There is significant potential to produce drop-in hydrocarbons from cellulosic feedstocks."
The new Session 17 is set for Tuesday morning, March 15, at 9:00 a.m. – 10:30 a.m. Joining Prof. Dooley and other speakers on alternative pathways for fulfilling the RFS mandate, Prof. David Bransby at Auburn University will provide "A Review of Cellulosic Hydrocarbon, Drop-in Replacement, and Infrastructure Compatible Fuel Technologies."
More information on the BioPro Expo program is available online, as is information on the co-located International Bioenergy and Bioproducts Conference (IBBC).
Back To Top
|
Market Roundup
The global demand for dissolving pulp has increased sharply during the past decade, reaching 4.5 million metric tpy in 2010, according to a new study by RISI, Boston, Mass., USA, titled Outlook for Global Dissolving Pulp Market. As detailed in the report, annual demand for dissolving pulp reached its peak in 1975 at 5.3 million metric tons. It decreased over the next three decades, with a dramatic decline in the early 1990s due to the collapse of Communism in Eastern Europe. Demand reached its lowest point in 2000 at 3.2 million metric tons, but has increased dramatically over the past decade. Last year, demand for dissolving pulp again reached its pre-crisis level from 1990 of 4.5 million metric tons.
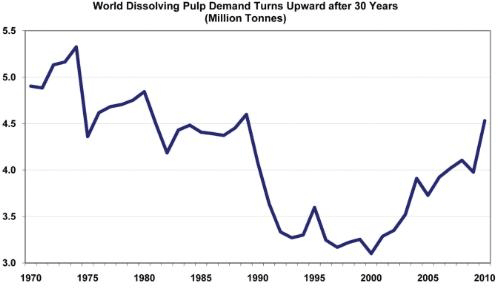
The big turnaround in dissolving pulp demand has been led by the viscose fiber market where the popularity of rayon, mainly for garment production, has been boosted by limited supplies and surging prices of cotton, the report notes. China, where dissolving pulp consumption for garment production has tripled over the past 10 years, accounts for all demand growth in the past decade.
Such strong demand and high prices have attracted pulp producers in the southern hemisphere to start new dissolving pulp lines, while in the northern hemisphere paper grade mills are converting to dissolving pulp.
"We're looking at getting a 10% addition to capacity in just one year -- an indication of how excited people are getting about this market," said Rod Young, chief economic advisor to RISI, and author of the study. "A big concern is that capacity keeps growing rapidly and we get into an overcapacity situation."
The main end uses of dissolving pulp are:
- Viscose fiber or rayon used in clothing
- Acetate tow and fibers used in cigarette filters
Ethers and microcrystalline cellulose (MCC) used in pharmaceuticals and as a food additive.
Back To Top
|
U.S. Demand for wipes, both consumer and industrial, is forecast to increase 4.5% annually to $2.3 billion in 2014. Wipes will continue to benefit from features such as ease-of-use, disposability, portability, and reduced risk of cross-contamination, according to a new Freedonia Group report titled Wipes, which MarketResearch.com, Rockville, Md., USA, has added to its collection of House & Home market reports. Nevertheless, growth will decelerate from rates achieved during the 2004 to 2009 period due to increasing market maturity and a shift in preferences to more environmentally friendly consumer goods and cleaning methods. In response to the "green" trend, wipes manufacturers will continue to develop more environmentally friendly products, such as those that are biodegradable, the report notes.
Convenience, consumer acceptance and innovation will remain driving forces in the consumer market, with household cleaning, hand and body, and a number of other, small volume consumer wipes projected to register the strongest gains. Growth in household care wipes, such as general purpose disinfectant wipes, will be propelled by the appeal of one-step, disposable wipes that provide a quick and convenient format for household cleaning chores. These wipes also offer a fast and easy cleaning alternative for consumers with little free time.
Hand and body wipes, such as bathroom hygiene and general purpose bathing, will enjoy increased market penetration. For example, the concept of wet bathroom tissue as part of a standard bathroom routine is gaining acceptance. General purpose bathing wipes are also gaining acceptance among individuals who are bedridden or find it difficult to enter and exit a bathtub. Nevertheless, baby wipes will remain the top selling type of consumer wipe. Demand for baby wipes will continue to suffer due to market maturity, as well as continued replacement by newer, task-specific wipes in non-diaper applications, where baby wipes once enjoyed considerable popularity.
After suffering from slower sales during the recession that began in December 2007, the industrial wipes market will benefit from a rebound in manufacturing activity through 2014, the new report continues. As such, wipes geared towards the manufacturing market are projected to achieve the most rapid gains through the forecast period. In addition to a more favorable economic climate, demand for industrial wipes will benefit from new product innovations and expanding applications. Among industrial wipes, manufacturing and health care types will remain the largest segments, with special purpose products such as clean room and surface preparation.
Back To Top
|
Global pulp production in the second half of 2010 was higher than many people anticipated, and pulp markets were better than they had been the first six months of the year, reports the Wood Resource Quarterly ( WRQ), Seattle, Wash, USA. Total production of chemical market pulp last year reached an estimated 45 million tons, which was about 7% more than was produced in 2009. North America and Western Europe increased production by 10% and 12%, respectively, while Latin America reduced production slightly. Other regions including Asia, Africa, and Russia also raised production in 2010, WRQ notes.
High demand for wood raw-material by the pulp industry pushed the costs for wood fiber upward in the second half 2010, WRQ continues. Softwood chips and softwood pulp log prices were higher in most key markets around the world in the fourth quarter of 2010. As a consequence, WRQ's Softwood Wood Fiber Price Index (SFPI) increased for the third consecutive quarter. The Index reached $103.60/o.d. metric ton, which was the highest level since the beginning of the financial crisis, and the SFPI is now 16% above the first quarter 2009 price. The biggest price increases in the fourth quarter of 2010 occurred in the U.S. Northwest, Sweden, Spain, and Brazil.
The Hardwood Wood Fiber Price Index (HFPI) has gone up faster than the SFPI since early 2009. The fourth quarter 2010 Index was $108.28, which was up 3.4% from the previous quarter and almost 18% higher than in the first quarter of 2009. The HFPI has only been higher twice since its inception more than 20 years ago, WRQ points out. Pulp mills in Germany, Spain, France, and Brazil all had to pay more for hardwood logs in their local currencies. In addition, the U.S. dollar weakened against most currencies and therefore contributed to a higher Price Index
One of the few regions that experienced reductions in wood fiber costs in 2010 was the U.S. South, with fourth quarter prices being about 10% lower than in the first quarter. Wood prices in the South were the lowest in all of North America in the fourth quarter of 2010, and pulp mills in this region have benefited from some of the lowest wood fiber costs in the world, according to WRQ.
More information is available online.
Back To Top
|
Pulp & Paper
The Australian Federal Court has handed down $4.2 million in penalties to two foreign companies that ran a purported price fixing "club" in Asia, according to a report this week by Melbourne-based Smart Company. Federal Court Justice Annabelle Bennett found Singaporean company Asia Pulp & Paper Co. and Indonesia's PT Indah Kiat Pulp and Paper were part of a group of competitors called the "Triple A Club," which reportedly held meetings to fix the prices of paper across the region, including Australia.
Bennett found the "AAA Club meetings involved systematic, sophisticated, and long-running cartel arrangements between the participants" and said "the cartel participants were seeking to achieve stability in pricing by avoiding competition among themselves." She ordered the Singaporean company to pay a penalty of $3.4 million, with the Indonesian firm, Indah Kiat, was ordered to pay $800,000, Smart Company reported.
In January 2010, the Federal Court ordered another Singaporean company, APRIL Fine Paper Trading Pte, and its Australian marketing arm, to pay $4 million in penalties for their involvement in the AAA Club and $250,000 toward court costs. Asia Pulp & Paper and Indah Kiat were also ordered to pay $300,000 toward court costs.
Back To Top
|
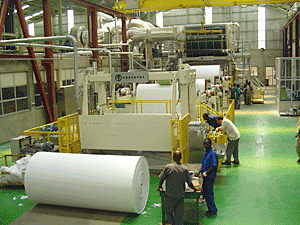 Bel Papyrus Ltd, a member of the Lebanese Boulos Group of Companies, Lagos,Nigeria, this past week reported that it concluded the purchase of a state-of-the-art tissue production line with an average production of 65 tpd from Toscotec, Italy. The new line will consolidate the company's position in the West African tissue market, raising total production capacity above 120 metric tpd. The new line integrates a new deinked pulp plant, also supplied by Toscotec, expected to come on-stream at the end of this year. With the new PM 3 line, installed within the Ogba compound, the company will become one of the largest and most advanced tissue producers in Africa.
Total cost of the project is financed by a combination of capital injection of $15 million from the shareholders and a $20 million term loan secured by Citibank. The loan to the company is guaranteed by the Overseas Private investment Corp. (OPIC) from the U.S. Government.
The Boulos group was established in 1936 by George Boulos and his sons Antoine and Gabriel, and by 1980 established a large capacity manufacturing plant for Suzuki motorcycles. In 1986, the group established Bel Papyrus and bought its first paper recycling and tissue paper production from Toscotec. In 2004 Bel Papyrus bought a Toscotec Modulo line and increased capacity to 50 metric tpd. At the same time, the group established a tissue paper converting factory, Bel Impex, to produce a large array of tissue paper products utilizing European machinery.
With a current tissue converting capacity of 22.000 metric tpy coming from Toscotec machines, Bel Papyrus produces and distributes several products and brands of tissue papers. The range includes toilet, facial, pocket handkerchiefs, table napkins, and kitchen towels. The company also has launched its third-generation baby diaper "Rose Tenders," and is planning to start production of aluminum foil, cling film, wet wipes, and sanitary napkins in the near future.
The new Toscotec line includes an AHEAD 1.5S crescent former tissue machine with single-layer headbox, single press configuration, a steel yankee dryer (TT SYD 12FT), machine auxiliaries, stock preparation plant for virgin pulp and for recycled paper including deinking cells, two-loop washer system, a hot dispersion system, and the electrification starting from medium voltage cabinets and control system.
The supply contract also includes: a steam generator, air compressors, a three-unwind-stand tissue slitter rewinder (TT WIND-P) with calendering station, and a jumbo reel wrapping machine. The machine design speed is 1,800 m/min, with a net web width of 2,850 mm. The project will be managed by Toscotec on an EPC basis.
Back To Top
|
Blue Heron Paper Co., Oregon City, Ore., USA, this past week announced that it is permanently curtailing operations at its Oregon City specialty paper mill and issuing WARN notices to its employees related to permanent closure of the facility. On Dec. 31, 2009, Blue Heron filed for bankruptcy protection and has been operating for the last 14 months under the Chapter 11 protective umbrella as it has refined its reorganization plan and tried to emerge.
Immediately after filing, the company went through a downsizing in which it cut about 3,000 tons per month of newsprint production, reduced headcount, increased worker flexibility with the support of its union employees, and began a focused effort to grow a new product line of environmentally friendly commercial toweling grades.
"The initial plan was successful in restoring profitability and the company received meaningful support from its suppliers and other creditors", said President Mike Siebers, "but lately those profits began to erode due to escalating waste paper prices and limited availability of that raw material. All of the paper products we manufacture use a high percentage of recycled fiber in them. Mills like Blue Heron are where the actual recycling of the collected waste paper you set out at the curb takes place. But China and other far-East countries have developed an insatiable appetite for recycled fiber to support their own paper plants which are then subsidized by their parent countries in other ways to maintain their jobs. This allows them to drive up the price for waste paper to unsustainable high levels for periods of time, giving them an unfair advantage over companies like ours."
Concurrent with refining its reorganization plan, Blue Heron lately also actively sought an investment partner or buyer who could provide additional capital standing to secure trade credit and strategic or operating synergies with the company. So far it has been unable to identify an investor willing to proceed at an appropriate value.
"Unfortunately things have come to a quick head due to an unforeseeable and dramatic increase in waste paper cost in February," said Siebers. "In this month alone, our delivered cost for recycled paper has increased by $24 per ton, adding around $240,000 to our monthly cost of production and basically wiping out any potential for profit in the near-term future. Our waste paper suppliers have told us to either meet the market price or they will not deliver. This has left the company with no other choice other than to curtail operations and announce the closure. The Oregon City mill is expected to only operate for a few more days as it runs out its supplies. Beyond that, it is unclear if the operation will ever be re-started."
Blue Heron is a 100% employee-owned company that has been in business since 2000. Currently, it employs about 175 union and non-union workers. The mill is an integrated producer of newsprint, high brights, bag, towel, and specialty papers, all made with a high recycled content.
Back To Top
|
Catalyst Paper, Richmond, B.C., Canada, this week announced $13.3 million in federal funding approval for a new green-energy project at its Powell River mill that will produce low-carbon electricity and be one of the cleanest waste wood co-generation projects anywhere in Canada. The project is funded entirely by the Pulp and Paper Green Transformation Program (PPGTP) credits, earned through production of black liquor at the company's Crofton pulp operation in 2009. The electricity will be certified under the federal EcoLogo program.
The project will involve new waste-wood handling equipment, a sand recycling system and other upgrades to an existing power boiler (PB19), and installation of a steam condenser on the generator (G12). Work is underway and expected to be completed within approximately 12 months.
"One of the great strengths at the Powell River operation is our clean-burning power boiler. Emissions and air-quality monitoring demonstrate that," said Bob Lindstrom, VP, supply chain, energy and information technology. "Factor in our marine access to waste-wood supplies, and our Powell River mill becomes one of the most logical and low-impact places in Canada to generate green energy from biomass."
The project is supported by the Sliammon First Nation, which has signed a memorandum-of-understanding (MOU) with Catalyst in connection with it. The MOU includes a provision for a Sliammon-Catalyst Development Fund, commits Catalyst to informing the Sliammon regarding fiber-supply opportunities, and envisions longer-term collaboration relating to skills development.
Waste wood, mostly tree bark, is burned in PB19 to create steam for both papermaking and electricity generation. Manufacturing-related steam requirements were reduced when kraft pulp production ended at Powell River in 2001. The new steam condenser will allow PB19 to once again be operated at capacity, and G12 electricity generation to double from 14 - 18 MW to a range of 32 - 36 MW.
Waste wood or biomass is classified as a carbon-neutral fuel under international carbon accounting protocols and widely accepted standards, and the project will therefore help achieve British Columbia's carbon-reduction and energy self-sufficiency goals. The same amount of fossil fuel-generated electricity would typically create nearly 100,000 metric tons of greenhouse gas emissions each year, equivalent to the operation of 25,000 cars.
"Green-energy generation has enabled us to reduce the carbon footprint of our Canadian mills by more than 80% since 1990," said Lindstrom. "We are keen to leverage that expertise more broadly. This project creates a supplemental energy product line, and that could translate into significant competitive advantage in an industry that's under pretty severe pressure."
The project's impact on the mill's environmental performance has been modeled and assessed, as required by the Canadian Environmental Assessment Act. Electricity from this project will displace natural gas generated electricity for a net annual reduction of 96,500 metric tons of carbon emissions. Mill air emissions are expected to remain within applicable permit levels and the mill's carbon footprint will remain at an industry-leading level of approximately 88 kg of CO2e/adt of production.
Installation of a recycling system will improve the use of sand that is fed into the boiler bed to ensure combustion efficiency. Rather than being trucked away for screening, as is now done, sand will be screened and recycled on-site, reducing the total volume of sand required.
The PPGTP is a federal program designed to support innovative projects with environmental and energy benefits in the Canadian paper industry. Catalyst qualified for $18 million in PPGTP credits.
Back To Top
|
Central National-Gottesman Inc., Purchase, N.Y., USA, reports that its Lindenmeyr Munroe division this week acquired the assets and business of Hudson Valley Paper Co., one of upstate New York and New England's oldest fine paper merchants. Hudson Valley is headquartered in Albany, where it maintains its principal warehouse and administrative offices. The company also operates warehouses and sales offices in Rochester, N.Y.; Burlington, Vt., and Hartford, Conn.
"Hudson Valley was founded in 1875 and is one of the leading fine paper distributors in the Northeast," said Ken Wallach, chairman and CEO of Central National-Gottesman. "Hudson Valley is managed by members of the fourth and fifth generation of the founding family and maintains the pride, integrity, and professionalism embodied in its long and distinguished history. We look forward to adding the accomplished professionals at Hudson Valley to our existing New England sales and support team. This acquisition enables us to offer our customers and suppliers an unrivaled level of service while strengthening our leading position in the important Northeast market."
This transaction is Lindenmeyr Munroe's fourth acquisition of a paper merchant in the past 15 months, including three in the U.S. and one overseas. Founded in 1886, Central National-Gottesman has sales offices in 28 U.S. cities and 23 countries worldwide. It operates several divisions, including Central National, a global provider of pulp, paper, and packaging, and Lindenmeyr, the largest independent paper merchant in the U.S.
Back To Top
|
Domtar, Montreal, Que., Canada, announced this week that its Domtar Distribution Group, Covington, Ky., USA, a network of strategically located paper distribution facilities, has been rebranded under the name Ariva. The Ariva name and brand replaces all of the company's legacy brands: RIS the paper house in the U.S. and Buntin Reid, JBR La Maison du Papier, and The Paper House in Canada.
"Our customers' businesses and needs are changing in ways no one could imagine a decade ago," said Mark Ushpol, SVP of Ariva. "Our new identity reflects our recognition of these fundamental changes and our commitment to work as a unified team to deliver new products and solutions to give our customers a competitive edge."
Ushpol said the Ariva brand provides a strong, unified identity for the company in all of the markets where it operates, including the U.S., Canada, Mexico, the Caribbean, and Latin America. "Ariva is focused on new opportunities and partnerships globally, while building on the proud legacy of our predecessor companies," he added.
Back To Top
|
Domtar Corp., Montreal, Que., Canada, is conducting a special dedication ceremony tomorrow, (Friday, March 4), celebrating the startup of a new fluff pulp machine at its Plymouth, N.C., USA, pulp mill. Ceremonies begin at 9 a.m. EST at the mill site on Highway 149 in Plymouth. Persons interested in attending should contact Stefan Nowicki, manager, Communications and Government Relations, at 803-325-559,
Domtar is the largest integrated manufacturer and marketer of uncoated free sheet paper in North America and the second largest in the world based on production capacity. The company has 10 pulp and paper mills in operation (eight in the U.S. and two in Canada) with an annual paper production capacity of approximately 3.9 million tons of uncoated free sheet paper, after converting the Plymouth facility to 100% fluff pulp production. The Plymouth mill currently operates two fiberlines, including the new fluff pulp machine, with a total capacity of 444,000 metric tpy.
Back To Top
|
Eka Chemicals, Marietta, Ga., USA, the AkzoNobel Pulp and Paper Chemicals business, this week announced that it has been granted permission by the Canadian Pest Management Regulatory Agency to use its Purate® technology to produce chlorine dioxide for applications to control microorganism contamination in pulp and paper mill process water.
"For more than 40 years, Eka Chemicals has been designing, building, and operating chlorine dioxide systems for applications ranging from pulp bleaching to water disinfection for drinking and food processing," Mario Houde, president, Eka Chemicals, said. "Purate is proven technology with more than 300 on-site chlorine dioxide production units around the world. We are really excited to be able to offer this technology to the Canadian Pulp and Paper Industry as it is the most cost effective chemistry to control biofilm in the papermaking process."
Back To Top
|
Neenah Paper Technical Products, Alpharetta, Ga., USA, this week announced the direct sales and distribution of its heat transfer papers throughout Europe via its Neenah Paper Lahnstein, Germany, location. The new warehouse arrangement results in heat transfer paper ready to ship from Germany rather than the U.S. to anywhere in the European Union. In addition to quicker delivery and less expensive transportation, Neenah Paper's web site will allow ordering directly from the manufacturer in quantities from 100 sheets up to multiple carton orders.
The webshop offers the majority of Neenah's Heat Transfer Papers in A4 and A3 sizes, including some 12 in. x 18 in. sizes for larger digital printing machines. Information on Neenah's heat transfer papers and multilingual instructions also are available on the site.
Back To Top
|
NewPage Corp., Miamisburg, Ohio, USA, this week announced the upload of a new On Paper sustainability series podcast featuring Lisa Quezada, sustainable development policy manager for MillerCoors. The focus of the podcast is on the company's water stewardship efforts and its achievements around reducing waste to landfill.
MillerCoors mission is to create America's best beer company by focusing on five key responsibilities with set goals for 2015—alcohol responsibility, environmental sustainability, people and communities, sustainable supply chain and ethics, and transparency.
"Water is an essential ingredient in the brewing process, from growing barley to cleaning brew kettles to brewing beer," says Quezada. Conserving water is a main focus for MillerCoors and the company's 2015 water goal is to reduce water usage by 15% across its eight breweries nationwide. MillerCoors currently reports a water-to-beer ratio of 4.11 barrels of water to one barrel of beer, and some brewery locations are significantly below the average.
Though water stewardship continues to be the most pressing area, MillerCoors is also focused on reducing its waste sent to landfill. "We achieved our 2015 waste reduction goal ahead of schedule, and reduced the amount of waste sent to landfill by more than 20% in 2009," Quezada notes. MillerCoors has achieved this goal by finding innovative re-uses for its waste, such as selling leftover barley to local farmers for animal feed or using brewery by-products to fertilize on-site hay fields.
This podcast can be downloaded and 30 previous episodes on a broad range of topics can be accessed from the On Paper web site. The series is an ongoing solutions-based dialogue that provides a platform for professionals to share how their organizations implement sustainable practices. With dozens of episodes featuring representatives from the most innovative of corporate America, across a variety of industries, On Paper has garnered more than one million downloads.
NewPage is the largest coated paper manufacturer in North America, based on production capacity, with $3.6 billion in 2010 net sales. The company operates paper mills in Kentucky, Maine, Maryland, Michigan, Minnesota, Wisconsin, and Nova Scotia, Canada. These mills have a total annual production capacity of approximately 4.4 million tons of paper, including 3.1 million tons of coated paper, 1.1 million tons of uncoated paper, and 200,000 tons of specialty paper.
Back To Top
|
Suzano Papel e Celulose S.A. Brazil, and Metso, Finland, reportedly are in advanced negotiations towards concluding a contract for the supply of all main pulp making technology for the 1.5 million metric tpy, greenfield pulp mill to be built in the state of Maranhão in the northeastern part of Brazil. Startup is scheduled for the first half of 2013. At this point in the negotiations, the value of the delivery is not disclosed.
Suzano Papel e Celulose is a forestry-based company and one of the largest vertically integrated producers of pulp and paper in Latin America. The company's main products, sold on the domestic and international markets, are eucalyptus pulp, printing and writing paper, and paperboard.
Back To Top
|
ABB, Vasteras, Sweden, reported this week that its System 800xA Extended Automation controller has received KEMA certification for its IEC 61850 electrical integration interface. IEC 61850 is the global communication standard for Power Distribution and Substation Automation. System 800xA's unique ability to integrate a wide variety of intelligent electronic devices provides a single platform for process and electrical systems, resulting in operational and energy efficiency benefits.
Founded in 1927, KEMA is a global provider of business and technical consulting, operational support, measurement and inspection, testing, and certification for the energy and utility industry. KEMA's Protocol Competence and Test Center is the certification organization for IEC protocols, and is the first independent test organization authorized by UCA (Utility Communications Architecture) International Users Group to perform the official IEC 61850 conformance tests and issue certificates.
The IEC 61850 standard, along with other emerging technologies, has lowered the investment barrier for customers to integrate the process and power devices on their plant floors. The demand for integrated process and power automation is growing in traditional markets that are heavy energy users, such as pulp and paper, oil and gas, power generation, minerals and metals industries.
Back To Top
|
Spinnaker Corp. International, Green Bay, Wis., USA, has been appointed Midwest distributor and service facility for AirTrim Inc., Springfield Ohio. AirTrim designs and supplies a full range of components and systems for conveying and disposing of trim from paper and tissue machines, rereelers, winders, sheeters, and converting equipment. AirTrim also supplies components and systems for dust control and disposal.
Operating from its Green Bay offices, Spinnaker will provide applications, sales, installation, field service and spare parts to mills in Wisconsin, Minnesota, and the Upper Peninsula of Michigan. Spinnaker manufactures/provides chilled cast iron plain and temperature controlled calendar rolls, headboxes, fourdriniers, presses, slice and apron lips, refiners, deflakers, plates and tackle, suction rolls and rebuilds, reelspools, roll repairing/grinding/rebuilding, rope and pneumatic threading systems and parts, winder trim systems, and metal and nylon dryer gears.
Back To Top
|
Containerboard/Packaging
Dev Priya Industries, India, has commissioned Voith Paper Automation, Germany, to handle the stepwise upgrade of its PM 2 at Meerut, 70 km northeast of New Delhi. The Indian family-owned business has invested in an OnQ quality control system for the PM 2 test liner and fluting machine, which produces 250 metric tpd of corrugated cardboard with a wire width of 4,400 mm. A MD color control as well as a local service contract for the OnQ quality control system also are part of the scope of supply.
The goal of the upgrade is to achieve high quality finished products, increased productivity, and minimization of web breaks. PM 2 is equipped with an OnQ quality control system that includes a scanner directly before the reel. The scanner is equipped with sensors to measure moisture, basis weight, and color. Additionally, to achieve consistently high paper quality in the machine direction, MD control for moisture and basis weight were previously installed.
Dev Priya Industries was founded in 1992 and produces testliner, recycled kraft linerboard, and fluting on two machines with a capacity of 400 metric tpd. The company is part of the Dev Priya Group, which is also family-owned. Moreover, the group produces duplex board and absorbent kraft grades, with a capacity of 1,000 metric tpd.
Back To Top
|
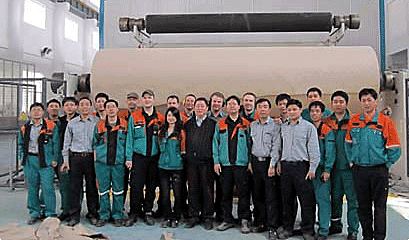 Fujian Liansheng Paper Co., Zhangzhou City, Fujian Province, China, has successfully started up its Metso (Finland) supplied containerboard machine, PM 3, which produces fluting within the basis weight range of 80 – 120 gsm. The annual production capacity of the 6.4-m-wide (wire) machine is around 300,000 metric tons and the design speed is 1,100 m/min. The production line was started up with a Metso wet end machine clothing package.
Fujian Liansheng Paper started paper production in 1999. The company established the Zhangzhou mill site in 2006. In 2010, Liansheng Paper Industry (Longhai) Co., a subsidiary of Fujian Liansheng Paper, ordered two 7.25-m-wide containerboard machines from Metso for its mill in Longhai City, Fujian Province in China.
Back To Top
|
Graphic Packaging International (GPI), Marietta, Ga., USA, has announced plans to close its Jacksonville, Ark., multiwall bag facility. The company will transition business and equipment from Jacksonville to other U.S. operating locations.
"As always, GPI deploys business to our most cost effective plants," said David Scheible, president and CEO. "We continually evaluate all of our business operations to ensure we are serving our markets as efficiently as possible. Simply put, this is a difficult business decision."
The Jacksonville multiwall bag facility will continue to operate and support customers while its business is transitioned to other company facilities in the U.S. over the next several months. The company has notified its Jacksonville employees, and will provide appropriate assistance to those affected.
Back To Top
|
Platinum Equity, Los Angeles, Calif., USA, reports that has completed the acquisition of Nampak Cartons and Nampak Healthcare from South Africa-based Nampak Limited. Nampak produces cartons for the food and beverage sectors from two sites in the U.K. and one in Holland. Nampak Healthcare manufactures cartons, leaflets, labels, and blister pack foils for the pharmaceutical industry from 11 sites across Europe.
"These are sound businesses with great people and a lot of potential," said Brian Wall, partner at Platinum who led the team pursuing the acquisition. "We see real opportunity as a standalone enterprise for growth and value creation through operational improvement and strategic acquisitions."
Last week the healthcare business announced plans to invest in a new facility that would replace and provide an upgrade to the company's current factory in Portsmouth, England. All current Portsmouth staff would be retained and transfer to the new site in nearby Segensworth, which is scheduled to be fully functional by the end of this year.
Back To Top
|
Published Pricing
DuPont Titanium Technologies, Wilmington, Del., USA, is increasing prices for all of its TiPure® titanium dioxide grades sold in North America (U.S. and Canada).by $0.15 per pound, or as permitted by contract,
DuPont Titanium Technologies is the world's largest manufacturer of titanium dioxide. The company operates U.S. plants at DeLisle, Miss.; New Johnsonville, Tenn.; and Edge Moor, Del.; as well as Altamira, Mexico; and Kuan Yin, Taiwan, all of which use the chloride manufacturing process. The company also operates a mine in Starke, Fla.
Back To Top
|
RockTenn, Norcross, Ga., USA, this week announced a $45 per ton price increase on its Millennium grades of high strength, 100% recycled paperboard. The price increases are effective with shipments beginning April 1.
RockTenn produces paperboard, containerboard, and consumer and corrugated packaging, with annual net sales of $3 billion. The company has operations in the U.S., Canada, Mexico, Chile, and Argentina. It employs some 10,400 people.
Back To Top
|
Energy
On June 1, Dr. Harry Cullinan will assume the position of Director of Technology Deployment at Auburn University's Alabama Center for Paper and Bioresource Engineering, Auburn, Ala., USA. In this new role, Dr. Cullinan will focus on the commercialization of several biorefining technologies currently under development at Auburn.
The technologies of interest are variations of the thermochemical and biochemical platforms for the production of renewable fuels and chemicals in addition to the current pulp and paper outputs from existing mill operations. The emphasis is on utilization of waste materials as feedstock to produce additional revenue streams.
Targeted feedstock material includes waste wood and bark, paper mill sludges, and forest residue. Product choices include biogas, ethanol, butanol, FT liquids, waxes, and advanced "drop-in" fuels. Process options range from pre-treatment, hydrolysis, fermentation, and concentration to gasification, gas cleaning, gas phase, and liquid phase catalysis. Supercritical water processing is also being developed.
These technologies have been under development at Auburn for a number of years and are now ready to be commercialized. Dr. Cullinan's responsibilities involve technology transfer and the formation of partnerships leading to pilot and mill scale demonstrations, then ultimate, full commercialization.
"While we firmly believe that the best use of pulp wood is wood pulp, we see great opportunities for additional value creation, in the form of renewable fuels and chemicals, from materials currently considered as waste," Cullinan said. "I look forward to concentrating on realizing this enormous potential."
Back To Top
|
Travels with Larry
Anyone who has seen It's a Wonderful Life remembers that famous line "Every time a bell rings an angel gets his wings." At TAPPI headquarters, every time the President's Bell rings, we welcome a new TAPPI member! Tim Leopold and Warren Shoemaker are the newest members to join the TAPPI community.
Tim Leopold is the Eastern Regional Manager with Western Polymer Corporation of Moses Lake, Washington. They are the largest coating, wet-end cationic potato starch and specialty starch supplier to the paper industry in the Northwest. In addition, WPC supplies and services paper mills throughout the United States. When Tim was asked about his TAPPI experience, he said "I used to be a member of TAPPI but dropped my membership a few years ago. I have seen tremendous improvements in TAPPI from a couple years ago and am proud to join again!"
Warren Shoemaker is in the Business Development unit at Cobalt Technologies. They are a leading developer of innovative technologies that enable the next generation of biofuels. By bringing together leaders in microbial physiology, strain improvement, fermentation and separation technologies, Cobalt is pioneering science that makes possible a new generation of fuels that burn cleaner, are more cost-effective, and have a smaller environmental impact. Warren told us, "I've been looking to get connected with the pulp & paper industry and TAPPI has been incredibly helpful and effective with introductions and insights. Membership has already been well worth the investment."
Please join us in welcoming Warren and Tim (back) to TAPPI! You can connect with them at tleopold@westernpolymer.com and warren.shoemaker@cobalttech.com. To learn more about Western Polymer visit www.westernpolymer.com. For more details on Cobalt Technologies, please visit www.cobalttech.com.
We get a kick out of seeing our members, so if you're in the Norcross, Georgia area, please stop by and ring the bell and you could be featured in the next Over the Wire issue.
And remember there are two types of people: TAPPI members and those who should be!
Until next time,
Larry N. Montague
TAPPI President & CEO
Back To Top
|
TAPPI News
Recognizing all that he had received from the members who joined before him, Ian Journeaux, Ph.D., became a TAPPI member nearly 25 years ago to help "pay it forward." He says it was the ease of seeking out and engaging colleagues and peers that convinced him of the value of TAPPI membership, and what it might mean to a new generation of engineering stars.
Currently a Process Technology Manager with NewPage Corporation, he oversees process optimization, process troubleshooting and new technology evaluation. Ian says that TAPPI members were always a go-to resource when there were pressing problems to solve, and remain so to this day. He considers membership one of the most important investments that industry professionals can make in their careers – no matter what stage they are in. Find out the reasons why by reading this month's Member Spotlight.
Spotlight participants are recommended by fellow members and staff. If you would like to nominate a member (or even yourself!) just send their name (or names) to MemberSpotlight@tappi.org. We will forward a Spotlight Questionnaire to fill out and return.
We look forward to seeing you in the Spotlight!
Back To Top
|
TAPPI is holding its popular
TAPPI Essentials of Market Pulp course on
April 30 this year -- just before the opening of the PaperCon 2011 convention May 1-4, 2011. There's no reason to miss it!
This course offers the most comprehensive overview available of today's market pulps worldwide. It is designed expressly to prime your knowledge of pulp markets in preparation for the convention, by helping you:
- Gain a broad understanding of current pulp trends in the global marketplace
- Understand the unique nature of pulps through study of a large cross-section of samples from all over the world - Initiate a simple, efficient evaluation process for smart pulp selection
- Network with others and discuss issues one-on-one with experienced instructors
You also will receive with your registration your own copy of the World Market Pulp CD Book - a $295 value - supplemented with new marketplace data and analytical insights. The World of Market Pulp books are sold around the world and are key reference materials in many libraries, laboratories and companies. (See a sample) [http://www.tappi.org/content/press/womp.pdf] of this valuable book online.
Be sure to register by April 1 to receive the discounted early-bird rate for this one-day course!
Back To Top
|
Join your colleagues one day prior to the start of the ICE SHOW for the 2011 TAPPI PLACE Flexible Packaging Symposium, April 5, 2011 at the Orange County Convention Center in Orlando, Florida USA.
Attend this Symposium for a comprehensive, state-of-the-art overview of the latest biopolymer materials, additives, processing technology, applications, environmental aspects and market trends. This is your opportunity to experience a real-time dialogue with industry experts and colleagues about the collective sustainability challenge.
By participating in this Symposium, you will learn:
• how to integrate sustainable practices throughout your manufacturing process
• best practices for successfully and cost-effectively extruding biopolymers
• how to progressively achieve your sustainability goals.
At the end of this symposium you will understand the latest developments in renewable source resins, films and structures, and be able to employ sustainable flexible packaging practices for resource efficiency.
View the complete schedule for this not-to-miss event!
Register now or download the faxable registration form.
Back To Top
|
Jack McAneny, Associate Director Global Sustainability for Procter & Gamble Co. (P&G), will give the keynote address at the welcome session for TAPPI's annual PaperCon Conference on Sunday, May 1, 2011, at 5 p.m. PaperCon will take place May 1-4 in Covington, KY at the Northern Kentucky Convention Center, located across the river from Cincinnati, Ohio. The welcome session is hosted by the TAPPI Coating and Graphics Arts Division.
"P&G has developed many Sustainable Innovation Products that have a significantly reduced environmental footprint without tradeoffs in price or performance," according to McAneny. "We recently announced a new long-term sustainability vision that includes increasing our efforts to develop products that have an improved environmental profile. This vision also includes a goal of using 100% renewable or recycled materials for all products."
McAneny helps to coordinate the implementation of P&G's sustainability strategy and leads several cross-functional and cross-business unit teams that focus on key sustainability issues. Procter & Gamble is the largest consumer products company in the world and has had formal sustainability programs in place for over a decade. As P&G's efforts have evolved, they have come to recognize sustainability as both a responsibility and an opportunity, with their current programs closely linked to their Purpose-inspired Growth Strategy. This session will provide an overview of P&G's current sustainability efforts, their long term sustainability vision, and highlight issues that may be particularly relevant for the pulp and paper industry.
Prior to joining P&G, McAneny worked for the Federal Occupational Safety & Health Administration as an Industrial Hygiene Compliance Officer. He holds a B.S. in Biology from Duke University and a master's degree from the University of North Carolina School of Public Health, Department of Environmental Sciences and Engineering.
"Sustainability is a very important issue for TAPPI, our industry and its customers," notes James P. (Jim) Niemiec, PaperCon 2011 Conference Co-Chairman and Senior Manager, Product Development for NewPage Corporation. "Sustainability continues to expand as more and more companies realize that being a profitable and efficient business goes hand-in-hand with being a good steward to the environment."
The annual PaperCon Conference is the largest conference of its kind in the world. It is the annual conference for three major groups in TAPPI (Technical Association of the Pulp and Paper Industry): PIMA (Paper Industry Management Association), TAPPI Papermakers Division and TAPPI Coating and Graphic Arts Division. The theme for the 2011 event is "Rethink Paper: Lean and Green." The conference will also feature a Sustainability Forum and Tissue Forum. The Recycled Paperboard Technical Association has also joined the conference this year with their Production-Technical seminar running concurrently. More is available at the website.
Back To Top
|
The deadline to submit an extended abstract for the 2011 International Pulp Bleaching Conference has been extended. Authors interested in presenting a paper should upload their extended abstract to TAPPI's Speaker Management System by April 15, 2011. Abstracts should be 1-2 pages in length.
Authors will be notified of acceptance by April 29, 2011 and must provide a full text manuscript by July 15, 2011. This event provides you with a unique opportunity to hear from researchers and operations specialists from around the world. Unlike other conferences with multiple tracts, this conference is very focused, and there are no competing sessions. Adequate time is allocated for questions and the exchange of further information. The format allows ample networking opportunities for attendees to have one-on-one exchanges with the presenters and other conference attendees in a relaxed atmosphere.
Back To Top
|
This is your chance to improve your Linerboard/Medium and Corrugated Box Manufacturing skills - in just two days of your time. A new course - T
APPI Linerboard Medium and Corrugated Box Manufacture Course - will be held
April 6-7, 2011 in Green Bay, Wisconsin, USA.
How You'll Benefit
This course will help strengthen your understanding of the corrugating process, and linerboard and medium performance properties and manufacture. The course content is intended to help improve overall corrugating box performance and runnability. It is ideal for both corrugators and pulp and paper mill employees.
What You'll Learn
After completing this course, you'll earn 1.4 CEUs and be able to:
- Explain how linerboard and medium properties and tests relate to the final box performance
- Identify and describe what happens in the corrugator, and some variables that affect the final product
- Increase recognition of - on a mill wide basis - the effects of fiber raw materials, pulp mill and recycling processes, stock preparation, chemical additives, headbox and wet end operations, pressing and drying, calendering and size press operations on performance tests and properties.
Register before
March 4 in order to save on course fees. Be sure not to hesitate long because this course will sell out at only 25 registrants.
Back To Top
|
Get some relief at the Shipping, Receiving and Warehousing Workshop and learn ways to improve your bottom line.
Be a part of this dedicated group of mills, carriers, warehouses and printers as they establish standards to reduce in-transit damage to rolls of paper. You can't learn by sitting in your office! Attend the Shipping, Receiving and Warehousing Workshop, in Nashville, April 12-13, 2011, and learn new ways to improve your bottom line.
Program Highlights:
• Results from the qMetrixTM pilot project, providing real-time roll damage reports to printers, carriers and paper mills.
• Review of claims processing procedures to assure fast processing and prevention of future damage.
• Workshop on warehouse operations, covering best practice product handling and loading of rail cars and trailers.
• Hear how Verso Paper has achieved a dramatic reduction in damage claims.
• Membership Special - register for SRW and join TAPPI at a 60% savings!
Registration for this information-packed event is only $265. And for an additional $65 (total of $330) you can become a member of TAPPI - normally $174. TAPPI Membership entitles you to news, publications, conference discounts and a directory of members - the most influential people in the pulp, paper, converting and allied industries.
Learn more about TAPPI's Shipping, Receiving and Warehousing Workshop.
Back To Top
|
"Ability is what you're capable of doing. Motivation determines what you do. Attitude determines how well you do it." – Raymond Chandler
Back To Top
|
|
TAPPI Over the Wire | 15 Technology Pkwy. S. | Norcross, GA 30092 USA | Voice: 770.446.1400 | Fax: 770.446.6947
|
 |