 |
|
Weekly Spotlight
Appleton, Appleton, Wis., USA, and Domtar Corp., Montreal, Qué., Canada, this week announced a tentative agreement by which Domtar would supply Appleton with most of the uncoated base paper the company needs to produce its thermal, carbonless, and other specialty paper products
Learn More...
|
U.S. Representative Reid Ribble (R) of Wisconsin's 8th District held a Paper Industry Roundtable discussion with several industry representatives in Appleton, Wis., USA, on February 22
Learn More...
|
Two opening keynote speakers at TAPPI's PaperCon 2012 event, April 22 - 25, in New Orleans, La., USA, are highly accomplished authors and well-know movers and shakers in their respective business arenas
Learn More...
|
Sappi Fine Paper North America (SFPNA), Boston, Mass., USA, has released The Standard Volume 5, a guide to designing for print
Learn More...
|
During a visit to the University of Miami to highlight his administration's all-out, all-of-the-above approach to American energy, U.S. President Obama this past week touted the Energy Department's cost-cutting Industrial Assessment Program
Learn More...
|
China's imports of logs, lumber, woodchips, and pulp hit record levels in 2011, when its timber supply deficit surged more than 30% to an estimated 152 million cubic meters, according to the new edition of Global Tree Farm Economics Review published this week by RISI, Brussels, Belgium
Learn More...
|
WWF, Gland, Switzerland, is launching its second Environmental Paper Company Index, a rating of paper producers in regard to their global ecological footprint
Learn More...
|
Below is the latest listing of job openings in the TAPPI Career Center.
Learn More...
|
Market Roundup
Total U.S. kraft paper shipments were 118,700 tons, a decrease of 14.2% compared with January 2011
Learn More...
|
Total U.S. printing and writing (P&W) paper shipments decreased 3% in January compared with January 2011, according to the AF&PA's (Washington, D.C., USA) recently released January 2012 Printing-Writing Paper Report
Learn More...
|
Sawlog prices in the fourth quarter of 2011 were down both in U.S. dollar terms and in local currencies in most of the 20 regions covered by the Wood Resource Quarterly (WRQ), Seattle, Wash., USA, compared with the previous quarter.
Learn More...
|
Pulp & Paper
Hengan Group Chongqing, China, reports to have successfully started up its new PM 11 tissue paper machine supplied by International technology Group Andritz, Graz, Austria
Learn More...
|
M-real Corp., Finland, part of the Metsä Group, this week reported that it has concluded an "information and consultation process" to discontinue uncoated fine paper and "unprofitable" specialty paper production at its Gohrsmühle mill in Germany
Learn More...
|
SCA, Stockholm, Sweden, has made a binding offer to acquire the Taiwan-based hygiene products company Everbeauty
Learn More...
|
Sipat S.A, Moroco, has awarded a contract to Toscotec, Italy, for the rebuild its PM 2 tissue machine at Meknes, Morocco
Learn More...
|
Sonoco Recycling Inc., a wholly-owned subsidiary of Sonoco, Hartsville, S.C., USA, and one of the largest packaging recyclers in North America, this week announced that Sonoco's Chicago-Dupage rigid paper facility has received a gold-tier Sonoco Sustainability Star Award for going landfill free
Learn More...
|
Containerboard/Packaging
Cascades Inc., Kingsey Falls Qué., Canada, reported this past week that the company is continuing to consolidate its operations, and at the same time announced the permanent closure of its Enviropac unit, located in Toronto, Ont., Canada
Learn More...
|
International Paper Co., Memphis, Tenn., USA, reports that it plans to build a new corrugated packaging plant in Villalbilla, Spain, to "build out" its position in that country, the fourth largest corrugated packaging market in Europe
Learn More...
|
RockTenn, Norcross, Ga., USA, yesterday (February 29) announced the permanent closure of its Matane, Que., Canada, containerboard mill
Learn More...
|
Tetra Pak, Switzerland, this week reported the startup of its second production line in the company's Hohhot, China, packaging material plant
Learn More...
|
|
New Products
Twin Rivers Paper Co., South Portland, Maine, USA, a producer of lightweight specialty publishing, packaging, and label papers, has added 22 lb and 24 lb to its Border Brite grade line
Learn More...
|
Published Pricing
BASF reports that it will increase prices in Europe, Middle East, and Africa for resins and dispersions for the coatings, printing, and packaging industries by 3% to 12%, effective March 1, as existing contracts allow
Learn More...
|
Mitsubishi HiTec Paper Europe, Bielefeld, Germany, this week reported that it will increase prices for its thermoscript POS thermal paper globally by 5%, effective with deliveries beginning April 15
Learn More...
|
People
MeadWestvaco Corp., Richmond, Va., USA, has elected Gracia C. Martore a director of the company
Learn More...
|
TAPPI News
Curiosity may have killed a cat or two, but for TAPPI member Al Button it has led to a highly satisfying career in the paper and pulp science industry.
Learn More...
|
March 5-9, 2012 workshop at North Carolina State University in Raleigh, North Carolina, provides comprehensive overview of pulp and paper mill operations.
Learn More...
|
Learn new ways to avoid roll damage and improve your bottom line at SRW Workshop in April.
Learn More...
|
International Bioenergy and Bioproducts Conference to focus on advancements and commercialization of bioconversion technologies.
Learn More...
|
The industry's most important event taking place April 22-25 in New Orleans.
Learn More...
|
Designed for professionals involved in the procurement of materials and services in the manufacture of paper and packaging materials.
Learn More...
|
Learn effective tools and techniques needed to build a customer-centered, fact-based cost reduction strategy at April 21, 2012 workshop.
Learn More...
|
New training standard provides guidelines for skills and knowledge required for this important position in the mill.
Learn More...
|
|
Find us on Facebook
Network with us on LinkedIn
Follow us on Twitter
|
Weekly Spotlight
Appleton, Appleton, Wis., USA, and Domtar Corp., Montreal, Qué., Canada, this week announced a tentative agreement by which Domtar would supply Appleton with most of the uncoated base paper the company needs to produce its thermal, carbonless, and other specialty paper products. The historic 15-year supply deal is valued at more than $3 billion over the life of the agreement. The deal would bring together Appleton, one of the world's leading specialty coaters, and Domtar, the largest integrated manufacturer of uncoated paper in North America.
The proposed supply agreement would provide Appleton with reliable access to competitively-priced, high-quality base paper for all of its paper segments and reduce the company's exposure to unpredictable market costs for pulp and wastepape, and Appleton would become more competitive with integrated paper companies. The proposed agreement would also enable Appleton to place greater focus on its core capabilities of coating formulations and applications. Domtar would gain significant and predictable volume for its base paper business driven by demand in Appleton's growing global thermal paper business.
"We operate in a capital and resource-intensive industry," said Mark Richards, Appleton's chairman, president and CEO. "Successful companies will be ones who find more efficient ways to operate and deliver value to their customers. For some that means greater and more efficient use of their assets; for others it may involve closing operations that limit efficiency. The proposed supply agreement with Domtar involves both, and Appleton stands to gain significant operating efficiencies. We believe the proposal also demonstrates Appleton's deep commitment to our customers and to the future of the specialty paper business."
John D. Williams, Domtar's president and CEO, said that "this proposed agreement provides us with an opportunity to repurpose and replace high volume communication paper capacity to specialty paper grades, while securing a growing business long-term. This innovative agreement is consistent with our strategic plan that aims to bring growth into our revenue stream, capitalizing on our core competencies. We appreciate the trust and support of Appleton and their interest in further deepening our long standing business relationship."
Appleton currently produces base paper at mills in West Carrollton, Ohio, and Roaring Spring, Pa. The company purchases any additional base paper it needs from other paper producers including Domtar. Appleton also buys a large amount of wastepaper and pulp, primarily for its West Carrollton mill, both of which are susceptible to significant price volatility.
By purchasing the majority of its base paper supply from Domtar, Appleton would stabilize a significant expenditure and enable the company to shed old, high-cost, non-integrated papermaking assets. Appleton is proposing to cease recycled fiber processing and paper production at its West Carrollton mill. The company would continue to operate the world-class thermal paper coating operations installed there in 2008.
The proposed supply agreement would result in a reduction of approximately 330 jobs at the West Carrollton mill. Assuming the plan is finalized, approximately 100 employees would be retained to continue to operate the thermal paper coating facility. Carbonless paper coating currently conducted at West Carrollton would be shifted to the company's converting plant in Appleton, and result in an increase of approximately 50 jobs at that facility. Employment and operations at Appleton's integrated pulp and paper mill in Roaring Spring would be unaffected by the agreement.
The agreement is pending discussions with representatives of West Carrollton's Local 266 of the United Steelworkers regarding the reasons the company chose to pursue the agreement.
"We believe our proposal to discontinue papermaking operations at West Carrollton is a competitive necessity and not a reflection of the talent or commitment of our mill employees," Richards said. "Our employees have never wavered in their dedication to excellence and to serving our customers. What has changed is the economics of the industry in which we compete."
Richards added that non-integrated paper mills, those not capable of producing pulp from logs or wood chips, are distinctly disadvantaged and no longer competitive. Worldwide demand for pulp has driven its market price to historic highs, he noted.
"Because we buy pulp on the open market, it costs Appleton considerably more to make base paper than it costs a producer like Domtar, which can supply its own pulp. Our proposed operational changes, as difficult as they may be for many of our employees in West Carrollton, are needed for our company to remain competitive," Richards said.
The West Carrollton mill was built in 1948 by the American Envelope Company. Appleton purchased the mill in 1984 and has made substantial investments to improve its capabilities and productivity. The most significant investment occurred in 2008 when the company completed a $100-million expansion that included the installation of a state-of-the-art coater to produce thermal paper and construction of related facilities.
Richards said the company will continue thermal paper coating operations at the mill and that the new coater remains the foundation on which Appleton will expand its leadership in the growing, global thermal paper business.
Back To Top
|
U.S. Representative Reid Ribble (R) of Wisconsin's 8th District held a Paper Industry Roundtable discussion with several industry representatives in Appleton, Wis., USA, on February 22. The largely open discussion covered several topics of interest to mills, including Boiler MACT, the pending highway bill, and general state of business.
Boiler MACT was of most concern to the attendees and Rep. Ribble stated that a moratorium bill currently pending in the Senate would likely pass this year if brought to a floor vote. Companies represented at the roundtable were Green Bay Packaging, Domtar, Neenah Paper, Fox River Fiber, Appleton Coated, Georgia-Pacific, and Thilmany. Industry associations Wisconsin Paper Council, Pulp and Paper Manufacturers Association (PPMA), and TAPPI were also in attendance.
In the photo below are: (l-r) Scott Springmier, TAPPI; U.S. Representative Reid Ribble; and Dick Kendal, PPMA.
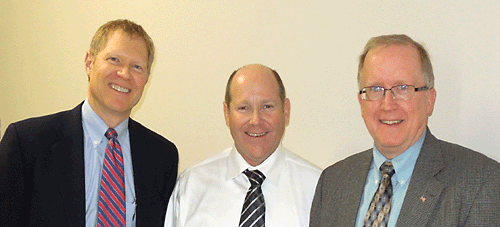
Back To Top
|
Two opening keynote speakers at TAPPI's PaperCon 2012 event, April 22 - 25, in New Orleans, La., USA, are highly accomplished authors and well-know movers and shakers in their respective business arenas. During the PaperCon opening session on Monday morning, April 23, Jeffrey Hayzlett, a bestselling author, global business celebrity, and "sometime cowboy," will discuss how the paper industry can drive and deliver change and avoid the pitfalls that beset other industries. Following the PaperCon opening session, Dr. Howard W. Penrose, an active reliability consultant, publisher, and writer, gets TAPPI's co-located OpEx Reliability Seminar underway with his keynote look at physical asset management "futureshock" and how our industry's past affects its future.
Hayzlett is author of the business book The Mirror Test, which received acclaim on numerous bestseller lists including Inc's 800CEORead and USA Today. His second book, Running the Gauntlet, released in January 2012, answers the question: How do I change my business in a way that instills enthusiasm and increases profits? Providing the inspiration and tools for spearheading dramatic change, Hayzlett helps readers tackle their biggest obstacles to making changes necessary for business success—fear, apathy, and failure to take personal responsibility. In his trademark fast-paced, brash, humorous style, he provides a realistic approach to competing effectively in an increasingly competitive business environment.
With years of international marketing, sales, and customer relations management experience, Hayzlett is a well-traveled public speaker, author, celebrity editor to one of the largest-circulation business publications, and one of the most compelling figures in global business. Dubbed "a born leader" by Mark Burnett, he has successfully leveraged multiple media appearances on programs such as Fox Business News, MSNBC's Your Business, and NBC's Celebrity Apprentice with Donald Trump.
Dr. Penrose, VP of Dreisilker Electric Motors Inc., received the 2008 Axiom Business Book Award for Physical Asset Management for the Executive: Caution – Do Not Read this on an Airplane, and 2008 Foreword Book of the Year for Electrical Motor Diagnostics: 2nd Edition. He currently is webmaster and social media specialist for the Institute of Electrical and Electronics Engineers (IEEE) and the Dielectrics and Electrical Insulation Society (DEIS), and also serves as outreach director for the Society for Maintenance and Reliability Professionals (SMRP).
Dr. Penrose's research in reliability, maintenance, time to failure estimation, hybrid vehicles, bio-engineering, and the environment are well published in technical conferences and magazines as is his work with causes such as autism. He is a Certified Maintenance and Reliability Professional and a NAVAIR and NAVSEA RCM specialist. He received five consecutive UAW and GM "People Make Quality Happen" awards from 2005 through 2009 in relation to reliability, maintenance, and energy projects within General Motors.
More details about the PaperCon 2012 program, exhibition, workshops and seminars, including the OpEx (Operating Excellence) Seminar, special events, and registration are available online, along with information about travel and accommodations.
Back To Top
|
Sappi Fine Paper North America (SFPNA), Boston, Mass., USA, has released The Standard Volume 5, a guide to designing for print. The latest volume focuses on how Special Effects can make the printed page offer a more dimensional, tactile, and interactive experience for audiences. It demonstrates how using printing techniques can serve as a creative tool to make images and editorial messages more powerful and impactful.
A virtual encyclopedia of special printing effects, The Standard 5 showcases a wide range of foils, emboss/deboss, engraving and thermography, a variety of coating and varnish techniques, strike-through, laser die-cuts, thermochromagraphy, lenticular, flocking, microencapsulated scents, phosphorescent UV coating, QR codes, and augmented reality. Although the techniques may look like magic, many are straightforward methods for designers to incorporate and can be done inline on a conventional press, SFPNA explains.
"The techniques demonstrated in Standard 5 show the innovative ways that designers can make printing on paper a multisensory experience," says Patti Groh, marketing director, SFPNA. "Print communication offers unique advantages that are not achievable with digital. Print and digital each has its strengths but are increasingly becoming intertwined and mutually supportive."
To illustrate that point, The Standard provides a dazzling example of augmented reality (AR) technology. Produced by Metaio software developer, the AR technology turns a printed character named Super Dude into an animated superhero when viewed on a mobile device or online.
As with the rest of The Standard series, Special Effects was conceived and designed by Kit Hinrichs of Studio Hinrichs, and done with the cooperation of 826 National, a nonprofit network of tutoring, writing, and publishing centers across the U.S. Co-founded by best-selling author Dave Eggers, 826 National serves under-resourced students, ages 6-18, by encouraging them to nurture their creativity through writing. In keeping with this mission, all 826 learning centers are fronted by a fantasy retail store. Examples are the Greater Boston Bigfoot Research Institute, The Pirate Supply Store of San Francisco, The Brooklyn Superhero Supply Co., and the Museum of Unnatural History of Washington D.C. The zany 826 retail concepts inspired the visuals for Volume 5 and made it possible to depict everything from a flocked Abominable Snowman to a glow-in-the-dark solar system to a jar full of fake eyeballs that "move."
"826 National and our nonprofit network of chapters are dedicated to inspiring young people to embrace imagination," said Gerald Richards, 826 National CEO. "Sappi Fine Paper North America shares our passion for inspiring creativity, and, taking this mission to heart, The Standard Vol. 5 showcases the intriguing concepts of the 826 stores with visually enticing special effects. Through their incredible design and printing techniques, Sappi was able to make the imaginative spark behind each of our locations come to life on paper."
This spring SFPNA is hosting a national road show to launch The Standard 5. The first event was held last Thursday, February 23, in San Francisco, also home to 826 National headquarters. Events will be held in nine other cities in the U.S. and Canada. A $10 admission fee will go to support 826 educational programs. The entire schedule and registration details are available online.
Back To Top
|
During a visit to the University of Miami to highlight his administration's all-out, all-of-the-above approach to American energy, U.S. President Obama this past week touted the Energy Department's cost-cutting Industrial Assessment Program. The program supports university-based Industrial Assessment Centers (IACs) across the country, which provide students with critical skills and training to conduct energy assessments in a broad range of facilities, while producing real cost savings for small to mid-size manufacturers. To date, these assessments reportedly have helped save more than 530 trillion BTUs of energy—enough to meet the energy needs of 5.5 million American homes—and have helped participating manufacturers save more than $5.6 billion in energy costs.
"As President Obama made clear, an American economy built to last will depend on American manufacturing, American energy, and skills for American workers," said U.S. Energy Secretary Steven Chu. "This is why the Energy Department invests in innovative initiatives like the Industrial Assessment Centers that help to train the clean energy workforce of tomorrow, while cutting energy waste for American businesses and making our manufacturing companies more competitive."
Through Industrial Assessment Centers at universities throughout the U.S., engineering students receive practical training in industrial processes, energy assessment procedures, and energy management principles, and gain real-world experience by working directly with small- and medium-sized industrial and manufacturing facilities in their communities.
For more than 30 years, the Industrial Assessment Program has provided training and experience for students, while saving money for manufacturing plants. Since the program began in 1976, the university teams have conducted more than 15,000 energy assessments at U.S. manufacturing plants nationwide. To date, more than 3,000 students have graduated from the Industrial Assessment Center program, with more than 60% going on to careers in the energy industry.
More information and a full list of Industrial Assessment Centers across the U.S. are available online.
Back To Top
|
China's imports of logs, lumber, woodchips, and pulp hit record levels in 2011, when its timber supply deficit surged more than 30% to an estimated 152 million cubic meters, according to the new edition of Global Tree Farm Economics Review published this week by RISI, Brussels, Belgium. Similarly, demand for timber in other wood deficit countries (such as India) is also on the rise, the report notes, adding that while some countries clamber for wood resources, concerns about deforestation have caused an increasing share of the world's native forests to be set aside for conservation.
These global trends are increasing the market's dependence on man-made forest plantations (tree farms), according to RISI. Not surprisingly, an increasing number of players in the timber industry are interested in developing tree farms—often in new regions and with relatively unproven species. This type of investment requires analysis that incorporates political and economic factors as well as direct costs and biological growth rates, RISI adds.
"The study is a very useful reference tool to evaluate not just forest investments, but also to identify where investment is occurring, where it is likely to expand (based on which countries/species offer the best financial returns), and thus where wood fiber supply will be available in the future. The Review is specific enough to be useful, but broad enough to cover the very wide range of geographic and product variations in type of timber investment projects," explains Robert Flynn, director of International Timber at RISI and Study co-author.
More information about Global Tree Farm Economics Review is available online.
Back To Top
|
WWF, Gland, Switzerland, is launching its second Environmental Paper Company Index, a rating of paper producers in regard to their global ecological footprint. In this round of the Index, 19 global producers of fine paper, tissue, and packaging allowed WWF to scrutinize their global paper production on key environmental criteria, such as fiber coming from well-managed forests, clean production, and public reporting.
Producers participating in this year's Index are:
- Fine paper category: Arjowiggins Graphic, Burgo, Cascades, Domtar, Fedrigoni, Mondi, M-real, Stora Enso, Suzano, UPM
- Packaging category: Cascades, Korsnäs, Mondi, SCA Containerboard
- Tissue paper category: Arjowiggins Graphic, Metsä Tissue, Renova, SCA Tissue, Sofidel.
The best scores on environmental footprint overall were achieved by companies in the packaging sector--SCA Containerboard with 85.55% and Mondi with 75.45% of achievable scores. In the Fine Paper category, the best scores were achieved by Arjowiggins Graphic with 73.86%, and in the Tissue category by SCA Tissue with 65.13% of achievable scores.
More scores for the best performing producers reaching at least 60% of achievable scores can be found online.
"At SCA Containerboard we are extremely proud to be named among the best scoring companies in the Environmental Paper Index of WWF International. For a long time we have devoted relentless energies to offering environmentally-sound products. This achievement will generate additional enthusiasm to fuel our environmental performance," said Stefano Rossi, VP and managing director, SCA Containerboard.
"Arjowiggins Graphic class leading score in the WWF Environmental Paper Company Index - Fine paper category, confirms the importance of leadership in the usage of recycled fiber, for graphic papers, as part of an economically successful sustainability strategy," said Jean Charles Monange, sales and marketing director, Arjowiggins Graphic.
"The willingness of companies to participate in WWF's Environmental Paper Company Index is a positive reflection on our industry and Mondi is delighted to once again be recognized as one of the top performing paper and packaging companies. Our approach to product responsibility incorporates transparent disclosure of our environmental footprint and allows responsible buyers to choose our products," said John Lindahl, group technical director, Mondi.
Back To Top
|
Below is the latest listing of job openings in the TAPPI Career Center. The current listing includes a variety of technical sales/specialists, maintenance, and production manager positions available in the U.S. pulp and paper industry. Current, specific job openings at companies and locations in the TAPPI Career Center include:
Employer |
Title |
Location |
Filcon America |
Technical Sales Rep |
Southeastern U.S. |
BASF, The Chemical Co. |
Tech. Specialist (Paper- Wet End) |
Appleton, Wis. |
NCR Corp |
Creative Chemist |
Atlanta, Ga. |
BASF, The Chemical Co. |
Technical Sales Rep, Senior II |
Washington State |
Orange County Container Group |
Maintenance—Paper Mill |
East of Dallas, Texas |
RockTenn |
Division Safety Manager |
Duluth, Ga. |
Southworth Co. |
Paper Mill Manager |
Western Mass. |
BASF, The Chemical Co. |
Develop. Scientist (Paper Chem.) |
Charlotte, N.C. |
Longview Fibre |
Quality Team Leader(s) |
Yakima, Wash./Twin Falls, Id. |
Longview Fibre |
Maintenance Engineer |
Longview, Wash. |
More information http://careers.tappi.org/ about these jobs is available online.
Back To Top
|
Market Roundup
Total U.S. kraft paper shipments were 118,700 tons, a decrease of 14.2% compared with January 2011, according to the AF&PA's (Washington, D.C., USA, January 2012 Kraft Paper Sector Report released this past week. Total inventory was 83,300 tons in January 2012.
Additional key findings from the report include:
- Total unbleached kraft shipments decreased compared with January 2011
- Total bleached kraft shipments stayed constant compared with last January but increased from last month.
Back To Top
|
Total U.S. printing and writing (P&W) paper shipments decreased 3% in January compared with January 2011, according to the AF&PA's (Washington, D.C., USA) recently released January 2012 Printing-Writing Paper Report. All four major P&W paper grades posted decreases compared with last January. U.S. purchases (shipments + imports – exports) of P&W papers decreased 8% in January. Total P&W paper inventory levels increased 1% compared with December 2011.
According to AF&PA, the pace of growth of the U.S. economy accelerated as we progressed through 2011, with each quarter posting ever higher growth rates (0.4%, 1.3%, 1.8%, and 3.3%, respectively) – and GDP is forecast to be 1.7% for the year. While the unemployment rate did not follow this exact pattern, the end result was the same, beginning at 8.9% for Q1, rising to 9.1% for Q2 and Q3, but then decreasing to 8.7% for Q4. The overall effect on total non-farm employment was positive for the four quarters of 2011, increasing 1.3%, 1.4%, 0.9%, and 1.3%, respectively. In spite of these positive developments, P&W paper shipments decreased in all four quarters for the year and, except for a slightly less negative quarter to end the year, slowed at a progressively declining rate—down 1.6%, 6.4%, 7.0%, and 4.9%, respectively.
Back To Top
|
Sawlog prices in the fourth quarter of 2011 were down both in U.S. dollar terms and in local currencies in most of the 20 regions covered by the Wood Resource Quarterly ( WRQ), Seattle, Wash., USA, compared with the previous quarter. The Global Sawlog Price Index ( GSPI) declined for the second straight quarter to $87.28/cubic meter in the fourth quarter. The Index was down 6% from the all-time high in the second quarter of 2011. In U.S. dollar terms, the biggest declines from the third quarter 2011 occurred in the Nordic countries and Oceania.
In the fourth quarter, the U.S dollar continued to strengthen against the currencies of all of the countries covered by the WRQ except Japan. This development, together with a downward price pressure on pulp log and wood chips in local currencies because of weakening pulp demand, resulted in a decline of both of the global wood fiber indices.
The Softwood Wood Fiber Price Index fell for the second straight quarter to $105.30/ovendry metric ton (odmt) in the fourth quarter of 2011. This was down 3.3% from the previous quarter, but 1.6% higher than the fourth quarter of 2010. The biggest price declines from the third quarter took place in Western Canada, Brazil, Spain, Germany, and Finland.
The Hardwood Wood Fiber Price Index fell 3.6% from the third quarter to the fourth quarter of 2011, when it averaged $113.69/odmt. Despite this drop, this was still 5.0% higher than in the fourth quarter of 2010 and the third highest level ever recorded. The biggest price reductions from the third to the fourth quarter occurred in Spain, Finland, Brazil, and Chile.
Production of market pulp on a worldwide basis was up 4% from October to November, and operating rates reached 91% for 20 of the world's largest producing countries. For the first 11 months of 2011, world production was 3.7 % higher than the same period in 2010, with production going up the most in Latin America and W. Europe. Prices for bleached hardwood kraft pulp (BHKP) fell more than those for northern bleached softwood kraft (NBSK) pulp last fall, but they seemed to reach a bottom in early January and have been slowly climbing during late January and early February.
More information is available online.
Back To Top
|
Pulp & Paper
Hengan Group Chongqing, China, reports to have successfully started up its new PM 11 tissue paper machine supplied by International technology Group Andritz, Graz, Austria. Hengan Group now has six Andritz PrimeLine machines in operation. Three more machines will be started up during this year, two of them equipped with the world's first wide steel yankees (5-meter dia.) for high-speed machines.
PM 11 (type PrimeLine TM W8) started up in a record time of only three-and-a-half months after the beginning of erection. It has a design speed of 2,100 m/min, a width of 5.6 meters, and is equipped with energy-saving components such as steel yankee head insulation and a re-evaporation system. Andritz's scope of supply also included the complete stock preparation and automation system.
Back To Top
|
M-real Corp., Finland, part of the Metsä Group, this week reported that it has concluded an "information and consultation process" to discontinue uncoated fine paper and "unprofitable" specialty paper production at its Gohrsmühle mill in Germany. To eliminate "severe losses" at the mill, M-real began negotiations with worker representatives this past October.
M-real's annual uncoated fine paper capacity at the Gohrsmühle mill will be reduced by approximately 120,000 metric tons and specialty paper capacity by 70,000 metric tons. The related personnel reduction of a maximum of 260 people will be implemented by the end of the second quarter this year. The level of redundancy costs is in line with the cost provisions made in the last quarter of 2011.
M-real will continue the Chromolux business and says it is currently investigating possibilities to startup folding boxboard sheeting operations at the Gohrsmühle site.
M-real noted that its efforts to establish a business park in Gohrsmühle are continuing, together with workers' representatives and local authorities, with the goal of creating new jobs at the site. One of the alternatives is to find partners to use existing paper production and converting equipment as well as other site infrastructure. M-real points to its Reflex mill as an example of the successful implementation of the business park concept, where the company was able to divest business units to different companies, saving more than 200 jobs. Divestment of M-real's last operations at the Reflex mill, the Premium Paper business, was finalized last month.
"We have reached a very important step in our work to eliminate losses of our paper business. Opportunities to establish a business park in Gohrsmühle are good," M-real's CEO Mikko Helander said.
Back To Top
|
SCA, Stockholm, Sweden, has made a binding offer to acquire the Taiwan-based hygiene products company Everbeauty. The purchase price for the deal amounts to approximately SEK 1.9 billion ($290 million) on a debt-free basis. If the deal is completed, SCA's positions in Asia, one of the Group's prioritized growth markets, will be substantially strengthened.
Everbeauty is an Asian personal care products company with sales in China, Taiwan, and Southeast Asia. The company produces and markets baby diapers and incontinence care products. Within incontinence care products, the company holds a No. 2 position in China and a No. 1 position in Taiwan. Within baby diapers, the company holds a No. 5 position in China and Taiwan. Everbeauty had sales of SEK 1.6 billion in 2010. Some 60% of sales are related to baby diapers and 40% comes from incontinence care products. The company has about 900 employees.
The transaction is expected to give SCA access to an extensive distribution network and a strong sales organization as well as production facilities in China and Taiwan.
The offer is subject to Everbeauty being privatized under Taiwanese law. Completion of the transaction remains subject to certain conditions, including approvals and clearances by relevant authorities in Taiwan. Closing of the deal is expected to take place in this summer.
"Asia is expected to account for 60% of the global growth within hygiene products. The acquisition of Everbeauty would create good growth opportunities in a strategic growth market, and with this acquisition, SCA would be the market leader in incontinence care products in Asia, excluding Japan. The acquisition would also strengthen SCA's market position and geographical reach within baby diapers in Asia," says Jan Johansson, SCA's president and CEO.
Today, SCA is present in Asia with personal care and tissue products and in some markets holds leading positions. SCA also holds an 18% ownership in Vinda International, a major tissue producer in China.
Back To Top
|
Sipat S.A, Moroco, has awarded a contract to Toscotec, Italy, for the rebuild its PM 2 tissue machine at Meknes, Morocco. Startup of the rebuilt machine is scheduled for the fourth quarter of this year. The project goal is to meet growing market demands in terms of product quality and production capacity, as well as to reduce energy consumption.
Sipat S.A.—Societé Industrielle Des Papiers Tissues—established in 1978, is owned by the El Kendouci family. With a production capacity of 16.000 metric tpy, the company is able to supply the Moroccan market, which absorbs 70% of its capacity, with the remainder exported to Senegal and Tunisia. The company produces mainly facial tissue, followed by toilet rolls, napkins, and kitchen towels.
Toscotec 's delivery includes a major rebuild of the original Toschi sloped wire forming section, which will be replaced with a Modulo Plus type crescent former with TT Headbox SL-T, a rebuild of the existing approach system and the felt run, as well as YD doctoring system. Electrification and a new machine control system will complete the package. The project will be handled on a turnkey basis, including dismantling of the existing equipment, installation of the new machinery, startup assistance, and training services. The new machine parts will be designed for an operating speed up to 1,300 m/min, with a reel width of 2,750 mm.
In 2009 Toscotec modified the dry end of the same machine with the installation of a new steel dryer TT SYD (2,500 mm) and relevant accessories. The project significantly improved Sipat's energy savings and boosted production by 30%.
According to Managing Director Driss El Kendouci, Sipat‘s growth in the tissue sector will be between 8% and 10%, and the new investment will have a fast pay-back. "There has been an evolution," he says. "In Africa, there has been more demand for quality, whether from Westerners driving the need, or from more and more people moving from the countryside into cities."
Back To Top
|
Sonoco Recycling Inc., a wholly-owned subsidiary of Sonoco, Hartsville, S.C., USA, and one of the largest packaging recyclers in North America, this week announced that Sonoco's Chicago-Dupage rigid paper facility has received a gold-tier Sonoco Sustainability Star Award for going landfill free. The facility has actually been landfill free since October 2011, according to Ron Camp, plant manager, who noted that "we've maintained 100% landfill diversion since then and are very excited to receive this prestigious sustainability award."
Ray Howard, GM, Sonoco Recycling, said that "in 2011, we committed to taking 10% of our plants landfill free by 2015. The Chicago-Dupage facility is the next step towards achieving our goal, and we applaud them for their efforts."
While the Chicago plant had been recycling for many years, employees worked with Sonoco Sustainability Solutions (S3) to achieve landfill-free status. All plant waste streams were audited and evaluated for potential opportunities, using reduction, reuse, recycling, and recovery to determine the best solution for diversion of all landfill waste. The facility created a team focused on reaching 100% landfill diversion while remaining cost neutral, or better than its existing cost of disposal.
Together with S3, the facility developed a thorough plant recycling program that includes all paper, corrugate, wood pallets, metal, stretch film, plastic banding, aluminum cans and plastic bottles. All other waste is sent to an alternative waste-to-energy (WTE) facility, and all material is compacted, sorted, shredded, and baled.
Created to recognize customer and Sonoco facilities for achieving significant milestones in landfill diversion and waste stream reduction, the program is composed of three tiers:
- Gold Star Awards that recognize facilities achieving 99% landfill diversion
- Silver Star Recognition awarded to facilities achieving 95% landfill diversion
Bronze Awards that recognize facilities achieving significant waste reduction.
Back To Top
|
Containerboard/Packaging
Cascades Inc., Kingsey Falls Qué., Canada, reported this past week that the company is continuing to consolidate its operations, and at the same time announced the permanent closure of its Enviropac unit, located in Toronto, Ont., Canada. Production at this unit, specialized in the manufacturing of Technicomb honeycomb packaging intended primarily for the furniture packaging industry, will progressively be redirected towards the Cascades Enviropac Berthierville, Qué., and the Grand Rapids, Mich., USA, plants. Approximately 36 employees will be affected by the closure, which becomes effective June 1.
"The decision to cease operations at the Toronto plant is due to a significant reduction in business volume. This decision was taken to secure the group's profitability and to improve its position as leader in the industrial packaging sector. Demand in the honeycomb packaging industry has been affected by challenging economic conditions over the past few years and it is imperative we adjust our operations based on this new economic environment. This initiative will enable us to maximize operations at our Grand Rapids and Berthierville, mills while continuing to offer a first-class product and service to our customers," Luc Langevin, president and COO of Cascades Specialty Products Group, said.
Cascades notes that it has taken necessary measures to help employees affected by this closure relocate to other manufacturing units and provide them with assistance in their search for work.
Cascades employs some 11,000 employees who work in more than 100 units in North America and Europe. Cascades Specialty Products Group has 50 business units in North America and Europe and employs more than 2,500 people.
Back To Top
|
International Paper Co., Memphis, Tenn., USA, reports that it plans to build a new corrugated packaging plant in Villalbilla, Spain, to "build out" its position in that country, the fourth largest corrugated packaging market in Europe. The new plant will replace IP's leased box plant in Alcala and take over its volumes, while also enhancing its capabilities. The new plant is the company's first greenfield box plant in almost two decades in the Europe, Middle East, and Africa region (EMEA).
"This multi-year project is a substantial investment and reinforces International Paper's commitment to Spain and the EMEA corrugated packaging market," Greg Gibson, VP and GM of IP's corrugated packaging business in EMEA, said. "Building a new plant in Alcala will allow us to sustain our market position in central Spain following the lease expiration of our current box plant there, while also enhancing our capabilities and serving as a platform to grow in new profitable markets and segments."
Back To Top
|
RockTenn, Norcross, Ga., USA, yesterday (February 29) announced the permanent closure of its Matane, Que., Canada, containerboard mill. The Matane mill, which RockTenn acquired in May 2011 as part of the Smurfit-Stone acquisition, had 176,000 tpy of recycled corrugated medium production capacity. RockTenn ceased production at the mill in late January 2012. The company notes that it took this action to balance its overall containerboard mill system capacity to match system demand, in light of major steps RockTenn is taking to realign system capacity and lower average system costs.
The Matane mill was the highest cost mill in the RockTenn containerboard mill system after accounting for all costs, including freight and overhead. RockTenn intends to work with the City of Matane and other interested parties to determine the best alternative use for the site. The company expects to incur pre-tax charges currently estimated at $29 million, including an estimated $12 million pre-tax for non-cash inventory and property, plant, and equipment write-downs.
RockTenn expects to record approximately $23 million of the charges in the second fiscal quarter ending March 2012. The remaining charges to decommission and dispose of the facility will be expensed as incurred. The amount and timing of expense incurred may vary depending upon, among other things, the duration and method of disposal. RockTenn believes that the containerboard system cost savings from the closure of the Matane mill will be approximately $16 million per year.
Back To Top
|
Tetra Pak, Switzerland, this week reported the startup of its second production line in the company's Hohhot, China, packaging material plant. The new world-class line will increase production capacity at the plant by 10 billion cartons per year to a total of 20 billion cartons per year.
China's booming economy, rising middle-class, and the trend toward urbanization puts it on track to become one of the fastest growing markets for liquid dairy consumption globally. According to Tetra Pak's 2011 Dairy Index, China's demand for liquid dairy products will surge by 40%, from 25 billion liters in 2009 to 35 billion liters in 2013.
"Tetra Pak's Hohhot converting plant has become one of the most technologically advanced and productive Tetra Pak production facilities both in China and globally," said Tetra Pak China President Steve Yin. "By investing at Hohhot, we aim to deliver maximum value as customers seek to identify and respond to new liquid dairy opportunities in this booming market."
In March 2011, the Hohhot converting plant won the TPM "Excellence Award" after having been in operation for less than two years, creating a record for Tetra Pak in World Class Manufacturing. The plant was also named "2011 Best Plant" by Tetra Pak Global for outstanding performance.
Back To Top
|
New Products
Twin Rivers Paper Co., South Portland, Maine, USA, a producer of lightweight specialty publishing, packaging, and label papers, has added 22 lb and 24 lb to its Border Brite grade line. The company notes that, with the brightness of a freesheet, Border Brite is ideal for reference books, bibles, catalogs, manuals, and financial printing.
Launched in 2011, Border Brite was engineered to bridge the gap between groundwood and freesheet papers since they provide a cost-effective alternative to freesheet. The addition of 22 lb and 24 lb broadens the basis weight range, creating more options for the customer.
Twin Rivers Paper Co. has operations in New Brunswick, and Québec in Canada, and Maine in the U.S.
Back To Top
|
Published Pricing
BASF reports that it will increase prices in Europe, Middle East, and Africa for resins and dispersions for the coatings, printing, and packaging industries by 3% to 12%, effective March 1, as existing contracts allow. The price increase affects, but is not limited to, the fJoncryl®, Luhydran®, and Acronal®. product ranges. BASF notes that the price increases are necessary mainly due to significantly increased costs of key raw materials.
Back To Top
|
Mitsubishi HiTec Paper Europe, Bielefeld, Germany, this week reported that it will increase prices for its thermoscript POS thermal paper globally by 5%, effective with deliveries beginning April 15. The company noted that the increase is in response to increasing costs as well as continued strong demand.
Mitsubishi HiTec Paper Europe is a German subsidiary of Mitsubishi Paper Mills Ltd. of Japan. It has some 700 employees, producing thermal papers (thermoscript), digital imaging papers (jetscript), and carbonless papers (giroform) at the Bielefeld and Flensburg mills in Germany.
Back To Top
|
Södra Cell, Sweden, has announced a new price for its NBSK (northern bleached softwood kraft) pulp in Europe of $850/metric ton. The new price becomes effective March 1, and is valid until further notice, the company said.
Back To Top
|
Billerud, Sweden, reportedly will raise its price for NBSK (northern bleached softwood kraft) pulp by $20/ metric ton, to $850/metric ton, with shipments beginning March 1. Billerud produces some 355,000 metric tpy of market pulp at its Gruvön, Karlsborg, and Skärblacka mills in Sweden.
Back To Top
|
People
MeadWestvaco Corp., Richmond, Va., USA, has elected Gracia C. Martore a director of the company. Martore brings financial and management experience, media and marketing expertise, and unique consumer insight to MWV's board of directors, which the company says will help guide its global packaging business.
Martore is president and CEO of Gannett Co., a media and marketing company with a diverse portfolio of broadcast, digital, mobile, and publishing companies. She joined Gannett in 1985 as assistant treasurer, becoming a VP in the treasury group in 1993, and investor relations duties being added in 1995. Martore was named treasurer and VP of investor relations in 1998. She was promoted to SVP of finance in addition to her treasurer's responsibilities in 2001. In 2003, she became SVP and CFO and was appointed to Gannett's management committee. In 2005, she became EVP and CFO, and in 2010 was named president and COO. Prior to joining Gannett, she worked for 12 years in the banking industry.
As a member of the MWV Board of Directors, Martore's duties will include her participation on the audit committee and the finance committee. She serves on the Board of Directors of Gannett Co. Inc. and FM Global and the advisory board of Florence Crittendon.
Back To Top
|
TAPPI News
As most industry professionals can tell you, TAPPI JOURNAL (TJ) has been an invaluable scientific resource for many years. But for 42-year TAPPI member Al Button, Ph.D., it actually served as the catalyst for a successful pulp and paper career devoted to research and discovery.
Fueled by his TJ findings, and subsequent TAPPI membership, Al went on to develop a seemingly insatiable appetite for learning and knowledge-sharing throughout his long and successful career. To this day, he says he is still amazed at the number of contacts he has made through the years and how readily accessible they remain. Find out more by reading this month's Member Spotlight.
Spotlight participants are recommended by fellow members and staff. If you would like to nominate a member just send their name (or names) to MemberSpotlight@tappi.org. We will forward a Spotlight Questionnaire to fill out and return. We look forward to seeing you in the Spotlight!
Back To Top
|
A Few Seats Open for Pulp and Paper Basics Workshop
The 2012 Hands-On Workshop for Pulp and Paper Basics typically sells out weeks in advance, yet a few seats remain open, which offers anyone still undecided the opportunity to take full advantage of the March 5-9 workshop being held at the North Carolina State University in Raleigh, North Carolina, USA.
Register for the Hands-On Workshop for Pulp and Paper Basics presented by TAPPI and North Carolina State University to gain this comprehensive, laboratory-based experience.
This hands-on workshop provides a broad overview of Pulping, Bleaching, Chemical Recovery, Recycling, Papermaking and Converting. The 5-day program offers presentations in the morning and hands-on laboratory and pilot-plant exercises in the afternoon. Students receive a course notebook and CD with approximately 400 pages of reference materials. This workshop sponsored by TAPPI and North Carolina State University balances lectures and laboratories at NC State's beautiful educational setting in Raleigh, North Carolina.
This introductory-level workshop is ideal for technical and non-technical employees with a desire for lab-focused instruction that will help them understand and appreciate the basics of pulping, bleaching, recovery, recycling, papermaking and converting operations.
Stock up on 3.7 CEUs and join others March 5-9, 2012 in Raleigh, NC.
Back To Top
|
Attend the Shipping, Receiving and Warehousing Workshop, in Nashville, April 2-4, 2012, and learn new ways to avoid expensive roll damage and improve your bottom line. Be a part of this dedicated group of mills, carriers, warehouses and printers as they collaborate to reduce in-transit damage to rolls of paper at this premier forum for industry leading paper shippers.
This is truly a practical, interactive and collaborative shipping and receiving workshop put on by industry professionals, for industry professionals - all parties of the supply chain - to address common issues and concerns relating to damage and damage prevention in the paper industry. It's an excellent networking opportunity - paper buyers, paper companies, carriers, securing / damage prevention specialists, block and bracing manufacturers, safety experts all under one roof. Learn more about TAPPI's Shipping, Receiving and Warehousing Workshop.
Back To Top
|
An Invitation to Present has been announced for TAPPI's 2012 International Bioenergy and Bioproducts Conference (IBBC), October 17-19, 2012 in Savannah, Georgia.
IBBC will focus on technical advancements and commercialization of bioconversion technologies that leverage the forest products manufacturing infrastructure and will include technical presentations, expert panels, case studies, and reports from projects that address:
- Feedstock and harvesting improvements to increase yield and quality of biomass
- Bioelectricity using combined heat and power (CHP)
- Bioconversion technologies for wood and biomass
- Production of chemicals and transportation fuels from wood and biomass
- Policies and incentives for bioconversion projects
Presentations are sought in the following areas:
Advances in Technology: strong technical papers with a focus on presenting new findings
- Biomass Supply & Demand
- Advances in Conversion Pathways ·
- Biomass Harvesting & Preparation
- Advances in Bioproducts
Commercialization Activities: case studies and updates from pilot scale, commercial, and pre-commercial operations
- Biorefineries
- Repurposing the Traditional Pulp and Paper Mill
- Harvesting and Preparation · Technical Economic Analyses
- Commercial Collaborations for Enabling Technologies
- Project Deployment Issues
Impacts of Policies and Incentives: analysis of existing or proposed bioconversion policies at State, Provincial or Federal levels
- Public policy proposals
- Pulp/paper incentives that support bioconversion progress
- Assessing common ground between pulp/paper and agricultural bioconversion policies
Limited space is available for poster presentations.
Abstract Submission Information:
Authors interesting in presenting a paper should upload their abstract to the TAPPI's Speaker Management System
Abstract Requirements: Abstracts should be no more than 200 words.
Submission Deadline: March 9, 2012
Presentations Deadline: September 17, 2012 Authors will be notified of acceptance by April 20, 2012.
Back To Top
|
With the industry's largest technical program, PaperCon is where CEOs, mill managers, superintendents, scientists, process engineers and suppliers gather to learn and network. PaperCon 2012 is about "Growing the Future": leveraging resources and people to ensure value for your customers, long-term success. Located in the heart of the Southern USA pulp and papermaking region, PaperCon sessions will highlight today's dynamic packaging sector.
Program tracks include Papermakers, Coating and Graphic Arts and PIMA Management. The PaperCon program also features: Inside and outside the box: Optimizing paperboard grades , the Sustainability Forum , an Executive Panel Discussion , a Young Professional Program , Coating 101 Course and other practical workshops and seminars and features the largest PaperCon exhibit ever. Bonus Sessions (open to all PaperCon registrants) Control Systems 2012: The first USA appearance for this highly-rated biannual conference. RPTA Production-Technical Seminar , the OpEx Reliability Seminar .
Take a moment to register and reserve your hotel room for this year's "must attend" event.
Back To Top
|
PaperCon's Procurement and Sourcing Forum taking place Monday, April 23, 2012, is an opportunity for professionals involved in the procurement of materials and services in the manufacturer of paper and packaging materials to identify best-in-class procurement strategies, highlight better ways to manage data, discuss mechanisms and approaches to increase value, learn about relevant industry-wide issues and concerns, and meet and network with industry peers Topics will address best practices and emerging trends in procuring consumables, chemicals, energy, mechanical parts, but not capital equipment.
Designed by industry professionals, PaperCon 2012 will bring together CEOs, mill managers, superintendents, scientists, process engineers and suppliers for the largest pulp and paper technical program in the world, April 22-25 in New Orleans.
Located in the heart of the Southern USA pulp and papermaking region, PaperCon 2012 will focus on "Growing the Future"; leveraging renewable, recyclable raw materials to ensure value for customers and long-term sustainability for shareholders. It's an event you can't afford to miss.
Learn more about the Procurement and Sourcing Forum and PaperCon.
Back To Top
|
Eliminating Cost while Enhancing Customer Value Workshop
Taking place at PaperCon, this one-day workshop on Sunday, April 21 will help you learn and identify effective tools and techniques needed to build a customer-centered, fact-based cost reduction strategy
Lead by Christopher W. Miller, PhD, NPDP, President Innovation Focus, Inc., this workshop features a customer-centered and creative approach to value analysis (the Unilever approach). Attend and learn how to unleash the power of your organization; design a customer-centered cost reduction project; facilitate an effective cost reduction effort; and how to select tools and techniques that will help you and your team be more customer-centered.
During this workshop, you'll learn how to design a customer-centered cost reduction project, facilitate an effective cost reduction effort, select tools and techniques that will help their team be more customer centered and build a customer centered, fact based cost reduction strategy
Process engineers and mid-to-upper level manufacturing managers within the paper manufacturing industry with an interest in cost management and reduction will find this course beneficial. Experience in cost reduction and related activities would be helpful.
Learn more about Eliminating Cost while Enhancing Customer Value Workshop and PaperCon.
The cost for this course is only 500 USD, which includes lunch and course materials. This special rate is being offered to TAPPI for this one-time workshop. Register now.
Back To Top
|
Training Standard for Paper Machine Tender, Standard Guideline T 1501 sg-11
New training standard for paper machine tenders
A technical committee of TAPPI members working with NPT2, the National Network for Pulp and Paper Technology Training, has developed a training standard for paper machine tenders―T-1501. This new standard provides guidelines for the skills and knowledge needed by a paper machine tender—often referred to as the paper machine first hand. Training standard for paper machine tender, Standard Guideline T 1501 sg-11
This standard will also be useful as a measure of the capabilities and understanding that a person must have to successfully perform the machine tender function. As the first standard of this type based on the information sources referenced, this particular standard may serve as a model to see if similar standards would be useful for other pulp and paper mill job classifications.
Back To Top
|
|
|
TAPPI Over the Wire | 15 Technology Pkwy. S. | Norcross, GA 30092 USA | Voice: 770.446.1400 | Fax: 770.446.6947
|
 |