 |
|
Weekly Spotlight
Stora Enso, Helsinki, Finland, this week reported that it plans to build plantation-based integrated board and pulp mills at Beihai city in Guangxi, southern China
Learn More...
|
International Paper, Memphis, Tenn., USA, and SCA, Stockholm, Sweden, have again been named among the world's most ethical companies by the American Ethisphere Institute, New York, N.Y., USA
Learn More...
|
At TAPPI's PaperCon 2012 event, April 22 - 25, in New Orleans, La., USA, two leaders from Longview Fiber Paper and Packaging, Longview, Wash., will be sharing the story of Longview's transformation from the time it was acquired by Brookfield Asset Management in 2007 until today
Learn More...
|
TAPPI's two-day (April 23 - 24) OpEx Reliability Seminar being co-located with PaperCon 2012, April 22 - 25, in New Orleans, La., USA, features a special workshop on Fixed Maintenance Optimization (FEMOS) and a customized course on maintenance and reliability training
Learn More...
|
Appleton Papers, Inc. (API), Appleton, Wis., USA, citing "numerous instances in which federal officials have ignored environmental laws, regulations, and rules of procedure, improperly driven up the cost of the Lower Fox River cleanup, and generally prevented the company from having its day in court," this week sought a new approach for resolving enforcement litigation involving the Lower Fox River remediation effort.
Learn More...
|
Domtar Corp., Montreal, Que., Canada, this week announced that, with Newsweek planning a retro edition to promote the new season of "Mad Men," Domtar will run a 1960s-style ad that shows while we live in a more digital age, people still read faster on paper
Learn More...
|
Market Roundup
Total U.S. printing and writing (P&W) paper shipments increased 2% in February compared with February 2011
Learn More...
|
Total February U.S. kraft paper shipments were 121,000 tons, a decrease of 8.4% compared with February 2011
Learn More...
|
Eucalyptus log prices in Brazil reached a peak in the third quarter of last year, but fell back almost 8% in the fourth quarter in U.S. dollar terms because of the strengthening dollar
Learn More...
|
Pulp & Paper
Catalyst Paper, Richmond, B.C., Canada, reports that it has reached new labor agreements with unions representing more than 1,000 paper and pulp workers at the company's Crofton, Port Alberni, and Powell River mills
Learn More...
|
Mohawk Fine Papers, Cohoes, N.Y., USA, has transitioned its sourcing of cast coated products from the Kromekote brand to Chromolux, manufactured by M-real. Mohawk expects to begin accepting orders in August
Learn More...
|
PaperlinX, Victoria, Australia, reports that it has agreed to sell its Italian business, Polyedra, to Lecta, a European paper manufacturer for EUR 45 million
Learn More...
|
Stora Enso, Helsinki, Finland, reports that it is appointing three new members to its Group Executive Team
Learn More...
|
Tembec, Montreal, Qué., Canada, this week announced a $190 million capital investment to upgrade its specialty cellulose manufacturing facility at Temiscaming, Qué
Learn More...
|
UPM, Finland, this week said that it will begin a large construction project to rebuild the effluent treatment plant at its Pietarsaari pulp mill in Finland
Learn More...
|
UPM Nordland Papier, Dörpen Lower Saxony, Germany, has started up a new Solaronics Bekaert (Armentières, France), infrared/air drying system as part of the rebuild of its Coater 1
Learn More...
|
Containerboard/Packaging
U.S. containerboard production increased 6.0% over the same month last year
Learn More...
|
Total U.S. boxboard production in February increased by 2.0% over February 2011, but decreased 2.5% from January 2012
Learn More...
|
Smurfit Kappa, Dublin, Ireland, has announced a three-year £98 Million investment plan for its Townsend Hook, Kent, U.K., papermaking facility
Learn More...
|
|
New Products
NewPage Corp., Miamisburg, Ohio, this week introduced its 40 lb. (65 gsm) EcoPoint™, a new wet strength label paper offering environmental and performance advantages for the bottled water, juice, and soft drink industries
Learn More...
|
Cristini Diagnostic Systems (CDS), Italy, has introduced its new FiberScanFIX™, an on-line version of the company's well known microwave consistency meter
Learn More...
|
Published Pricing
The price increase becomes effective with shipments beginning April 1.
Learn More...
|
The Newark BCI Division of The Newark Group, Cranford, N.J., USA, has announced an 8% price increase on all sheets, cut-to-size panels, loose-leaf panels, and spines
Learn More...
|
Tronox Inc., Oklahoma City, Okla., USA, on behalf of its subsidiary companies, this week announced a $250 per metric ton price increase for all TRONOX® titanium dioxide grades sold in Latin America
Learn More...
|
People
The Forest Products Association of Canada (FPAC), Ottawa, Ont., Canada, this week announced that Avrim Lazar will be retiring as its president and CEO at the end of this month
Learn More...
|
Louisiana-Pacific Corp., Nashville, Tenn., USA, has named Curt Stevens to succeed Rick Frost as CEO, effective May 4
Learn More...
|
TAPPI News
Learn new ways to avoid roll damage at SRW Workshop in April Body
Learn More...
|
Make the most out of your time at PaperCon by attending one or more of these workshops or seminars
Learn More...
|
Register now and don't miss the opportunity to network with this unique group in the "Big Easy"
Learn More...
|
Learn effective tools and techniques needed to build a customer-centered, fact-based cost reduction strategy at April 21, 2012 workshop.
Learn More...
|
New product development seminar April 17-18 in Alexandria, Virginia, uses Stage-Gate process and is focused on increasing success rate.
Learn More...
|
Major awards that may be presented include Gunnar Nicholson Gold Medal for preeminent scientific achievement, TAPPI Fellows, Distinguished Service Award and Oustanding Local Section Member Award.
Learn More...
|
Eight detailed chapters provide an excellent review of coating coating fundamentals and practical applications for this key papermaking and converting process.
Learn More...
|
Two important Keynote Speakers to address PaperCon as the industry gathers April 22-25 in New Orleans.
Learn More...
|
Through their dues, Sustaining Members support TAPPI's extensive educational efforts as well as facilitate the work of the TAPPI Foundation, a significant source of funding for the vital scholarship programs we offer to next-generation superstars.
Learn More...
|
Spring Golf Outing will be May 17, 2012 in Lake George, NY and the technical conference will be on June 21 in Glens Falls, NY.
Learn More...
|
April 4-5, 2012 event in Orono, Maine features panel of expert speakers who will focus on "The Paper Industry from a Global Perspective."
Learn More...
|
|
Find us on Facebook
Network with us on LinkedIn
Follow us on Twitter
|
Weekly Spotlight
Stora Enso, Helsinki, Finland, this week reported that it plans to build plantation-based integrated board and pulp mills at Beihai city in Guangxi, southern China. The mill site will initially include a 450 000 metric tpy, state-of-the-art paperboard machine and pulp capacity of 900 000 metric tpy, including necessary energy plant and auxiliary facilities. In a unique set-up, the board and pulp mills will be self-sufficient.
The company's ultimate target is to expand the paperboard capacity to 900 000 metric tpy at a later stage. The operations will be managed by an equity joint-venture company established by Stora Enso (85%) and the Guangxi Forestry Group (15%), a state-owned company under the Guangxi provincial government. The joint venture will serve the fast-growing market for liquid packaging board and other premium consumer board grades.
The project investment will be approximately EUR 1.6 billion. Construction at the industrial site will commence when specific preconditions have been fulfilled, which is expected to be in the second half of 2012. Production is scheduled to start in the fourth quarter of 2014. The investment will significantly support Stora Enso moving towards its 13% ROCE target.
The project will be financed through a combination of debt and equity on an approximately 60/40 basis. The debt financing is expected to be a mix of export credit agency, multilateral, and commercial bank debt.
"Today we are taking another significant step in transforming Stora Enso into a global renewable materials company. We already have a globally leading position in renewable fiber-based packaging boards. We will now invest in a world-class integrated mill based on locally grown renewable materials for the benefit of local Chinese consumers in the fastest-growing market. Everything we do will be based on best-in-class technologies, environmental standards, and sustainability practices, together with the local partners and communities," Stora Enso CEO Jouko Karvinen said.
"Generating sustainable returns from any business requires a unique offering to the customers, be it product or process benefits, in a cost-efficient way, or something that is very difficult for the competitors to copy, like integrating the operation from the plantations to the technically advanced product. This is exactly why we have chosen to differentiate ourselves through a range of specialized world-class board products and end-to-end integration—with the most cost-efficient solution for the Chinese market and at a globally competitive total cost," Stora Enso EVP for Renewable Packaging Mats Nordlander noted.
The investment is subject to regulatory approvals, the signing of final documentation, and other customary conditions precedent.
Stora Enso has been establishing plantations in Guangxi since 2002. The company currently holds approximately 90 000 hectares, and is to establish sustainable eucalyptus plantations with an effective fiber base of 120 000 hectares to support the new pulp mill in Guangxi. Its other operations in China include a 245,000 metric tpy coated fine paper mill in Suzhou, a 170,000 metric tpy uncoated magazine paper mill at Dawang, two core factories, five sales offices, and the newly acquired majority shareholding in Inpac International, a packaging company with production operations in China and India, and service operations in Korea. The total number of employees in China is currently about 4 500.
Back To Top
|
International Paper, Memphis, Tenn., USA, and SCA, Stockholm, Sweden, have again been named among the world's most ethical companies by the American Ethisphere Institute, New York, N.Y., USA. Kimberly-Clark, Dallas, Texas, was also on this year's list. Ethisphere recognizes companies that go beyond the ordinary and demonstrate that business ethics are decisive for a company's brand and profitability.
This is IP's sixth year in a row to be on the list, and the fifth straight year for SCA. Ethisphere has published the WME rankings for six consecutive years.
This year, several thousand companies were evaluated from more than 40 industries. The list of nominees for 2012 included a record of 145 companies that outperform their peer competitors in ethical business practices. A total of 40 companies are headquartered outside of the U.S.
The methodology used to develop WME rankings includes reviewing codes of ethics, litigation, and regulatory infraction histories, evaluating the investment in innovation and sustainable business practices, looking at activities designed to improve corporate citizenship, and studying nominations from senior executives, industry peers, suppliers, and customers.
"In all of our endeavors around the globe, from safety performance to environmental stewardship to running our businesses, our actions come down to one simple principle—doing the right things for the right reason. International Paper is proud to be recognized as one of the World's Most Ethical Companies for the sixth straight year," said John Faraci, chairman and CEO of International Paper.
Jan Johansson, president and CEO of SCA, said that "SCA's track record in ethical business practices and sustainability work is a business differentiator that strengthens our competitive advantage. Our ambitious work in this area makes us more attractive for customers, consumers, and investors, and also generates considerable savings. SCA puts sustainability on top of the agenda, and we are honored by Ethisphere's recognition of our achievements."
Tom Falk, chairman and CEO of Kimberly-Clark, said that "we are honored to be recognized for our ethical business practices. Creating a culture where our employees are committed to driving business results ethically and doing the right thing for our customers, our communities, and the environment contributes directly to the success of our company."
More information about the award is available online.
Back To Top
|
At TAPPI's PaperCon 2012 event, April 22 - 25, in New Orleans, La., USA, two leaders from Longview Fiber Paper and Packaging, Longview, Wash., will be sharing the story of Longview's transformation from the time it was acquired by Brookfield Asset Management in 2007 until today. The company, while maintaining its steadfast focus on the manufacture of kraft paper products, has essentially become a new company culturally, operationally, and financially.
During Monday's (April 23) PB1 track session, Paul Duncan, mill manager, will lay the groundwork for the presentation by sharing information about some of the overall improvements that were made. Among other things, he'll describe how Longview:
- Shutdown four paper machines, and at the same time, managed to improve productivity by 52%
- Decreased the safety incident rate by 82%
- Achieved a 23% reduction in energy conservation
- Continues to make significant investments in capital to grow the future.
Brian Peterson, containerboard team lead, will delve into some of the details of what the mill did to support the transformation. He will provide details in a range of areas, including:
- How performance on Longview's five machines was improved
- How the management of people was handled and how that affected the results
- How their approach to production guided them to make appropriate decisions
- How their approach to investing capital kept them focused on doing those things that were essential to achieving the results needed,
In a separate but related presentation, Bruce Warrick, operations training manager for Longview, will be sharing the role that operator training played in the transformation at Longview.
Longview Fibre Paper and Packaging produces lightweight, high-performance multiwall and complementary specialty kraft papers for an established domestic and global customer base. The company also produces containerboard and corrugated boxes. Longview operates a pulp and paper mill at Longview, Wash., and a network of seven converting plants in the western U.S.
More details about the PaperCon 2012 program, exhibition, workshops and seminars, special events, and registration are available online, along with information about travel and accommodations.
Back To Top
|
TAPPI's two-day (April 23 - 24) OpEx Reliability Seminar being co-located with PaperCon 2012, April 22 - 25, in New Orleans, La., USA, features a special workshop on Fixed Maintenance Optimization (FEMOS) and a customized course on maintenance and reliability training. Both of these sessions are scheduled for day two, Tuesday, April 24, of the OpEx event.
The FEMOS workshop, from 8:30 a.m. – 10:30 a.m., focuses on use of the Systematic Inspection Design (SID) inspection planning process and the API 579-1/ASME FFS-1, Fitness for Service post-construction code and WRB 488. It is being conducted by David C. Bennett of Corrosion Probe Inc.
The Maintenance and Reliability Training course, at 1:30 p.m. – 3:30 p.m., is being instructed by Jeff Shiver, CMRP, of Managing Principal, People and Resources Inc. The special course will be in two parts. Part 1 is focused on "Learning the Editorial Steps to Create Your Reliability Centered Culture." Part 2 covers "How to Succeed with Your Equipment Reliability Efforts, Starting with Education."
More details about the PaperCon 2012 program, exhibition, workshops and seminars, including the OpEx (Operating Excellence) Seminar, special events, and registration are available online, along with information about travel and accommodations.
Back To Top
|
Appleton Papers, Inc. (API), Appleton, Wis., USA, citing "numerous instances in which federal officials have ignored environmental laws, regulations, and rules of procedure, improperly driven up the cost of the Lower Fox River cleanup, and generally prevented the company from having its day in court," this week sought a new approach for resolving enforcement litigation involving the Lower Fox River remediation effort.
In a letter to the U.S. Department of Justice, lawyers for Appleton said that a year-and-a-half into the EPA's enforcement action to clean up the river "the government has taken no steps to establish the most basic element of its case against API—that API is liable under the Comprehensive Environmental Response, Compensation, and Liability Act (CERCLA)."
David R. Erickson, a lawyer for the company, wrote that "the litigation history demonstrates that by design, or in effect, the government in doing everything it can to avoid justice, increase the costs of this litigation, and delay any resolution on the merits."
The letter was written in response to the government's demand that API agree to dredge 680,000 cubic yards of the Lower Fox River during the 2012 dredging season at an estimated cost of $75 million. The demand, Erickson said, is premised on a "new and unjustifiable interpretation" of a 2007 EPA Record of Decision that does not comport with proper Federal procedures.
The demand, API contends, is just the latest in a series of actions that has violated standard procedures and placed the company in "a due process-defective vise of the government's making." For example, the letter stated:
- The government has refused to ask the Federal Court to schedule a trial so the government can prove its case, instead selectively enforcing a Unilateral Administrative Order against only two of the companies (NCR and API) named as Potentially Responsible Parties (PRPs) for polluting the river
- Using potential economic penalties for failing to comply with the UAO as a threat, in 2007 the EPA insisted that dredging begin prior to completion of the remedial action's design, an inefficient approach that created huge and unnecessary expenses for NCR and API and was therefore an abuse of the agency's authority
- When it learned two years ago that it had underestimated the cost of the cleanup by $265 million, or 62%, the EPA decided not to amend its Record of Decision—which would have triggered a formal review by a special EPA board—and instead side-stepped the scrutiny by issuing an "Explanation of Significant Difference."
"API has accommodated the government the past 3-plus years, expecting it would have a meaningful chance to be heard," Erickson said in his letter. "That cooperation has been rewarded by unreasonable and what API believes are unlawful remedial demands."
The company has an obligation to its employees, the communities in which it operates, and its shareholders "to operate its business, including its handling of litigation, in a sustainable manner," the letter said. "The status quo is not sustainable."
In place of the "current inconclusive and patently unfair process," API proposed that the parties to the dispute agree to resolve the litigation on an accelerated schedule. This proposal would be accompanied either by a temporary suspension of remediation efforts during the 2012 dredging season or a "measured but significant amount" of remediation work while the matter is resolved in court.
If the government's allegations are proven at trial, questions about which company is liable will end, the lawyers note. "But if the government's allegations cannot win on the merits, they add, "the government will avoid being directly responsible for a potential miscarriage of justice that jeopardizes the jobs of 885 Wisconsin residents—and about 1,000 others—who work for a company that was not even in existence when PCBs were released into the Lower Fox River."
The proposal, Erickson said, "will ensure fairness both to EPA to test its conduct in this matter...and to API to test API's claim of nonliability or, if needed, API's defenses."
As it has repeatedly noted in the past, API reminded the government that it could also direct the remediation order it has issued, but never enforced, against the other named PRPs.
Back To Top
|
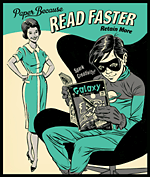 Domtar Corp., Montreal, Que., Canada, this week announced that, with Newsweek planning a retro edition to promote the new season of "Mad Men," Domtar will run a 1960s-style ad that shows while we live in a more digital age, people still read faster on paper.
"We've seen studies that show whether you're an executive or a millennial, people prefer to read on paper, and it's faster to read on paper," said Lewis Fix, Domtar's VP of Sustainable Business and Brand Management. "Whether you are learning or sharing important information, there are good reasons to make sure people still read the material on paper."
The Domtar ad, part of its award-winning Paperbecause campaign, will run in Newsweek's March 19 issue. It shows a boy dressed as a superhero and reading a comic book, while his mother proudly watches. The message: while entertainment options may have changed, people still enjoy reading on paper.
"A lot has changed since the 1960s, but we wanted to use this retro theme to make a serious point," Fix said. "There are several studies that prove there's a value in reading on paper that helps people learn and communicate."
Fix highlighted four studies, in particular:
- A 2011 survey of "millennials" (people born after 1985) showed that 65% think it's easier to view or read something on paper. About the same percentage of senior executives agree, according to a 2007 Study. It showed that 59% trust printed material more than online sources, and that 60% prefer printed information when they need to do an in-depth analysis.
- A 2009 study revealed that 64% of workers prefer ink on paper rather than a screen when it comes to reading. The rate was even higher (70%) among employees of technology companies. Further research conducted at Wayne State University found that reading on paper is actually 10% to 30% faster than reading online, partly because it is easier to track where you are on the page.
Starting March 19, readers can view the Mad Men issue of Newsweek online. Readers can also vote online for their favorite ad in the issue.
Back To Top
|
Market Roundup
Total U.S. printing and writing (P&W) paper shipments increased 2% in February compared with February 2011, according to AF&PA's (Washington, D.C., USA) February 2012 Printing-Writing Preliminary Shipments Report released this past week. Three of the four major P&W grades posted increases compared with last February, although tone grade, uncoated mechanical, decreased 10%.
Free sheet paper shipments were up 3% compared with February 2011, and are up by 1% year-to-date. Uncoated free sheet (UFS) shipments posted a 3% increase over February 2011, which more than offset the small decline in January, bringing year-to-date UFS shipments up 1%. Coated free sheet (CFS) shipments also increased 3%. Combined with the slight increase in January, year-to-date shipments are up nearly 1.5%.
Mechanical paper shipments decreased by 1% compared with February 2011, and for the year are down 4%. The culprit is uncoated mechanical (UM) paper shipments, AF&PA notes, which are down 10% year-over-year. Since this decrease matches the decrease in January, year-to-date shipments are also down 10%.
On the other hand, coated mechanical (CM) paper shipments increased the most out of the four grades, up 4% compared with February 2011. This strong growth was not quite enough to offset the 5% decrease in January, so year-to-date shipments are down 1%.
Back To Top
|
Total February U.S. kraft paper shipments were 121,000 tons, a decrease of 8.4% compared with February 2011, as the AF&PA reported in its February 2012 Kraft Paper Sector Report issued this past week. Total inventory was 82,800 tons.
Additional key findings from the report include:
- Total unbleached kraft shipments decreased compared with February 2011, but increased compared with last month
- Total bleached kraft shipments stayed constant compared with February 2011.
Back To Top
|
Eucalyptus log prices in Brazil reached a peak in the third quarter of last year, but fell back almost 8% in the fourth quarter in U.S. dollar terms because of the strengthening dollar, according to the Wood Resource Quarterly ( WRQ), Seattle, Wash., USA. Current price levels are still among the highest since the WRQ started tracking Brazilian wood prices in 1990.
Prices for Eucalyptus pulpwood traded in the open market are high not only from a historical perspective, but also compared with many other regions around the world, WRQ notes. Only pulp mills in Europe and Australia had higher hardwood fiber costs than Brazil in late 2011, while North America, Chile, Russia, and Indonesia all had lower hardwood log prices than the world's largest market pulp exporter.
Wood fiber cost is by far the most important cost component for Brazilian pulp mills, more so than for most other pulp mills in the world, WRQ says. In the fourth quarter, wood costs accounted for as much as 72% of the total cash costs in Brazil, according to Fisher International. This is substantially higher than the global average of 61%.
For the sawmilling industry in Brazil, 2011 was a better year than the previous year, with higher demand both from their domestic market and from abroad. Lumber exports in 2011 were up 6% to their highest levels in three years, with shipments to China, Saudi Arabia, Mexico, and Morocco increasing the most. As a result of the higher lumber production, sawlog prices have trended upward for almost three years, reaching an all-time high in the 2Q/11, according to WRQ.
During the second half of 2011, log prices fell in U.S. dollar terms, while there were only small price adjustments in the Brazilian Real terms. Domestic demand for lumber is expected to continue to improve in 2012 with the construction sector gearing up for the World Cup in soccer (2014) and the Olympic Games (2016). If the U.S. dollar continues to strengthen against the Brazilian Real, exports may also contribute to a better year for the Brazilian lumber industry than that of the past two years. This development is likely to put upward pressure on sawlog prices in the coming year, WRQ advises.
More information is available online.
Back To Top
|
Pulp & Paper
Catalyst Paper, Richmond, B.C., Canada, reports that it has reached new labor agreements with unions representing more than 1,000 paper and pulp workers at the company's Crofton, Port Alberni, and Powell River mills.The new contracts will go into effect at the expiry of the current contract on April 30.
"Approval of the new labor agreements lets everyone know that the people who make up Catalyst are taking the actions necessary to save jobs and ensure we have a viable and competitive business for the future," said Kevin J. Clarke, president and CEO. "We appreciate there is still an enormous amount of work to do to complete the restructuring plan that will enable the company to exit creditor protection on solid footing going forward."
The agreements, effective from May 1, 2012, to April 30, 2017, include a 10% reduction in hourly rates along with various adjustments to vacation, health benefits, and work rules necessary to provide Catalyst with a competitive labor cost structure. The agreements also maintain hourly retiree health benefits. Annual savings in the range of $18 to $20 million are expected.
The Communications, Energy, and Paperworkers Union of Canada (CEP) locals 1, 76, 592, 686, and 1132 represent 700 employees at the three mills; the Pulp, Paper and Woodworkers Union of Canada (PPWC) local 2 represents approximately 380 employees at the Crofton pulp mill.
Catalyst Paper produces specialty mechanical printing papers, newsprint, and pulp, with four mills located in British Columbia and Arizona, The company has a combined annual production capacity of 1.8 million metric tons.
Back To Top
|
Mohawk Fine Papers, Cohoes, N.Y., USA, has transitioned its sourcing of cast coated products from the Kromekote brand to Chromolux, manufactured by M-real. Mohawk expects to begin accepting orders in August. During the transition period, Mohawk will continue to support sales of Kromekote until current inventories are depleted.
Mohawk will offer Chromolux for traditional commercial printing, and will launch new Chromolux digital papers to complement its industry leading product and service offering in the rapidly growing digital printing market.
"Cast coated papers play a key role in our product offering and we intend to create a world-class line up for every leading print platform," said Thomas D. O'Connor Jr., chairman and CEO, Mohawk Fine Papers. "We are happy to announce this partnership with a globally recognized brand and to be working with the M-real organization. This partnership is strategic to our growth plan."
Mohawk notes that the broad portfolio of papers and boards for label, packaging, and graphic applications available from Chromolux "combined with Mohawk's know-how and extensive distribution network will realize a much deeper resource for the industry in the coated paper segment, and is expected to create new opportunities for both partners."
This is the second partnership Mohawk has formally announced this year. In January, Mohawk revealed a partnership with MOO.com to create a custom paper application for Luxe business cards.
Back To Top
|
PaperlinX, Victoria, Australia, reports that it has agreed to sell its Italian business, Polyedra, to Lecta, a European paper manufacturer for EUR 45 million. The purchase price represents more than 90% of book value and, after transaction costs and repayment of related debt in Italy, is expected to release approximately EUR 13 million in net proceeds. Polyedra contributed EBITDA of EUR 4 million in the 12-month period ending December 2011. The sale is expected to close within 90 days, subject to regulatory approvals and a final value audit.
PaperlinX CEO Toby Marchant noted that "we achieved fair value in today's market from a strategic investor and, importantly, generated a substantial portion of the A$20 million cash required to immediately implement the restructuring of Continental Europe and Corporate Head Office."
The multi phase restructuring of PaperlinX's business was a headline issue in the company's Interim Results announcement on February 23. The company expects savings of A$61 million by FY2014 from the ongoing restructuring program.
"Given the continued uncertainty of world paper markets, aggressive cost reduction is our most important initiative for the next two years. Every 1% reduction in our cost to sales ratio represents some A$40 million. We are aiming for a 3% total cost reduction, half of which will be generated from the current plans by FY2014," Marchant said.
Back To Top
|
Stora Enso, Helsinki, Finland, reports that it is appointing three new members to its Group Executive Team. At the same time, three current members will leave the team to take new positions inside and outside of the company.
Karl-Henrik Sundstrom has been appointed CFO, effective August 1. He joins Stora Enso from the Dutch semiconductor company NXP, the former Philips semiconductors business located in Eindhoven. Sundstrom has spent most of his career with the Swedish telecommunications company Ericsson, building his career from Latin America and managing the company's business in Australia to finally first becoming head of Global Services and later EVP and CFO of Ericsson AB.
"In his last two roles, as CFO of one of Sweden's largest companies for almost five years, and currently as CFO of NXP, Karl-Henrik Sundstrom has proved to be a world-class CFO. His additional experience of running a business will greatly contribute to our efforts to renew Stora Enso. We all warmly welcome Karl-Henrik to our team with high expectations," said Stora Enso CEO Jouko Karvinen.
Head of Stora Enso Global Identity Lauri Peltola (right), and General Counsel Per Lyrvall (below) are also appointed as new members of the Group Executive Team, effective March 19. The new Group Executive Team is as follows:
- Jouko Karvinen, CEO
- Juan Bueno, EVP, Biomaterials Business Area
- Lars Haggstrom, EVP, Global People and Organization
- Hannu Kasurinen, EVP, Building and Living Business Area
- Per Lyrvall, EVP, Global Ethics and Compliance, general counsel
- Mats Nordlander, EVP, Renewable Packaging Business Area
- Lauri Peltola, EVP, Global Identity
- Karl-Henrik Sundstrom, EVP, CFO (as of August 1)
- Juha Vanhainen, EVP, Printing and Reading Business Area.
The following three members are leaving the Group Executive Team: Hannu Alalauri, formerly head of the Fine Paper Business Area, has been appointed as the head of the Packaging Solutions Business Unit and joins the Renewable Packaging Management Team. Bernd Rettig, currently responsible for energy, logistics, R&D, and capital investments, will continue with R&D and capital investments, but will also increase his focus on managing Stora Enso's large capital investment projects. He continues to report to the CEO. The current CFO, Markus Rauramo, has been appointed as CFO of Fortum Corp. He will remain with Stora Enso and in the Group Executive Team until Karl-Henrik Sundstrom joins the company.
Back To Top
|
Tembec, Montreal, Qué., Canada, this week announced a $190 million capital investment to upgrade its specialty cellulose manufacturing facility at Temiscaming, Qué. The investment will increase annual production of green electricity by up to 40 MW, reduce sulfur dioxide emissions by 70%, increase Temiscaming's annual production capacity of specialty cellulose by 5,000 metric ton, and make Temiscaming one of the world's lowest-cost specialty cellulose manufacturing facilities.
The project is the first phase of a two-phase investment plan for the facility. It will involve the replacement of three old boilers with a new high-pressure boiler designed to burn waste sulfite liquor, a co-product of the specialty cellulose manufacturing process, producing green steam for use at the facility. The project also calls for the installation of a new electricity turbine that will be driven by this steam. The turbine will increase the Temiscaming facility's green electricity production capacity from its current 10 MW to, eventually, 60 MW. The boiler is scheduled to startup in December 2013, followed by the turbine, in May 2014.
Hydro-Québec will offtake the additional green electricity produced by this turbine under a 25-year contract at $106 MW/hr, indexed with CPI, which will strengthen and stabilize Tembec's revenues through the economic cycle.
The $190 million investment in Phase 1 will be financed with $105 million of new debt, which includes a $75 million loan from Investissement Québec; the balance of $85 million will come from free cash flow from Tembec operations.
"This game-changing project for Tembec will make Temiscaming one of the most competitive mills in the global pulp and paper market. I want to acknowledge the critical support of the Québec Government, through Investissement Québec, and the continuing commitment of our employees to remaining competitive," said James Lopez, Tembec's president and CEO.
"This exciting project shows Québec's commitment to supporting its regional resource-based industries, and helping them compete on the world stage. By working together proactively with local governments and Investissement Québec, we are pleased to reinforce Tembec's leadership position in specialty cellulose, a growing and sustainable industry," stated Québec Premier Jean Charest.
Once the new equipment is in operation, Tembec expects a four-year return on investment, through new revenues from green electricity, the additional production of 5,000 metric tons of specialty cellulose, and lower costs. Tembec's management expects the project will reach an annual run-rate EBITDA (earnings before interest, taxes, depreciation and amortization) contribution of approximately $40 - $45 million by fiscal year 2015, assuming implementation as scheduled and planned.
The new boiler, turbine, and emission control equipment will be sized to accommodate Phase 2 of the project, a follow-on investment of $120 million which is currently projected for 2014 – 2015. Phase 2 would increase Temiscaming's annual specialty cellulose production capacity by 30,000 metric tons, boost green electricity generation by 10 MW to attain full turbine capacity, and further reduce operating costs.
Tembec's combined investment of $310 million in the Temiscaming specialty cellulose facility—$190 million in Phase 1 and $120 million in Phase 2—will be one of the largest in the forest products industry in many years. It will further reinforce Tembec's position as the world's second leading producer of specialty cellulose. The overall project will increase Tembec's annual production capacity of specialty cellulose from the current 310,000 metric tons to 345,000 metric tons.
The Temiscaming facility's production capacity will increase from the current 160,000 metric tons to 195,000 metric tons. Tembec's Tartas, France, specialty cellulose facility has a current production capacity of 150,000 metric tpy.
Back To Top
|
UPM, Finland, this week said that it will begin a large construction project to rebuild the effluent treatment plant at its Pietarsaari pulp mill in Finland, The approximate EUR 30 million investment will cover the rebuild of all of the main phases of wastewater treatment. The work will start immediately and is to be completed at the end of 2013.
"With the rebuild of the effluent treatment plant, we will improve the pulp mill's production efficiency and reduce its environmental impact. The rebuild will also enable further development of the mill in the future," the mill's GM, Kenneth Winberg, said.
The construction includes a new preliminary clarifier for fibers and an aeration basin, created mainly by excavating rock. The pumping station and compressor house will be completely new constructions.
UPM is currently reviewing water management and efficiency in material use at several mills. By 2020, the company aims to have reduced wastewater volume by 15% in pulp and paper production, compared with levels in 2008.
UPM treats all wastewater in primary and secondary effluent treatment plants before it is released into watercourses. The company explained that the biological treatment stage is an efficient way to remove dissolved organic contaminants and nutrients from wastewater. The emission level of wastewater, it added, is regularly measured and monitored according to valid monitoring plans.
UPM's Pietarsaari pulp mill is the biggest pulp mill in Europe with an annual production capacity of some 800,000 metric tons. of softwood and hardwood pulp. The pulp mill employs about 300 people. Pulp is sold mainly to global markets, where it is used in the production of tissue, packaging, label, and office and writing papers. The Pietarsaari mill site also includes a packaging paper mill.
Back To Top
|
UPM Nordland Papier, Dörpen Lower Saxony, Germany, has started up a new Solaronics Bekaert (Armentières, France), infrared/air drying system as part of the rebuild of its Coater 1. The turnkey rebuild involved replacement of the existing electrical infrared and air drying systems supplied in 1988.
The new configuration consists of UniDryer® V2 units combined with new air dryers for the non contact drying of the coated paper. After each coating head, there is a new UniDryer V2 followed by a high performance air dryer that are linked by a Solaronics Bekaert energy recovery system. The objective of the project was to maintain the existing quality of coated wood free grades while reducing energy consumption.
This new configuration has significantly reduced installed power due to the replacement of electricity by gas and due to the high efficiency achieved with the high performance air dryers and Solaronics Bekaert energy recovery system link.
UPM consists of three Business Groups: Energy and Pulp, Paper, and Engineered materials. The company employs some 24,000 people and has production facilities in 16 countries. Its annual sales exceed EUR 10 billion.
UPM Nordland Papier in Dörpen is one of the world's largest producers of uncoated and coated woodfree fine paper, with an annual capacity of 1.4 million metric tons.
Back To Top
|
Containerboard/Packaging
U.S. containerboard production increased 6.0% over the same month last year, according to AF&PA's February 2012 U. S. Containerboard Statistics Report released this past week. Production was down, losing 5.5% compared with January 2012. However, the month-over-month average daily production increased by 1.1%. The containerboard operating rate for February 2012 gained 1.0% over January 2012, increasing from 95.2% to 96.2%.
Additional key findings from the report include:
- Linerboard production was up 6.5%
- Corrugating medium production also saw an increase.
Back To Top
|
Total U.S. boxboard production in February increased by 2.0% over February 2011, but decreased 2.5% from January 2012, AF&PA reported in February 2012 U.S. Paperboard Report issued this past week. Highlights of the report include:
- Unbleached kraft folding production increased over the same month last year, and increased compared with last month
- Total solid bleached boxboard and linerboard production increased compared with February 2011, but decreased compared with last month
- Production of recycled folding decreased compared with February 2011, and decreased compared with January 2012
Inventory of solid bleached kraft paperboard decreased from a year ago.
Back To Top
|
Smurfit Kappa, Dublin, Ireland, has announced a three-year £98 Million investment plan for its Townsend Hook, Kent, U.K., papermaking facility. The installation and commissioning of a custom designed, 5-m, lightweight recycled containerboard machine is due to be completed and operational by the end of 2014. This will secure the supply of paper for all of Smurfit Kappa's packaging operations in the U.K. and Ireland.
The new machine will produce lightweight corrugated papers, for use in Smurfit Kappa integrated plants meeting market requirements for high efficiency and sustainable, recycled papermaking. The cost associated with the project will be phased over three years and will be within the scope of SKG's stated annual capital expenditure guidance. The outlay represents one of the largest investments by an established U.K. paper producer, the company notes.
The equipment sourced from Cartiera di Cadidavid will replace two existing containerboard machines, increasing Townsend Hook's annual capacity of FSC certified, recycled paper by more than 8%, from 240,000 metric tpy to 260,000 metric tpy.
Together with Smurfit Kappa's SSK mill in Birmingham, the company will offer the widest portfolio of corrugated paper available in the U.K. Accredited with FSC certification and Carbon Trust Standard, the new paper mill will offer the most sustainable approach to packaging in the U.K.
Chris Allen, CEO, Smurfit Kappa Paper U.K., said that "this investment in the current financial climate shows Smurfit Kappa's commitment to the U.K., Ireland, and Pan-European customers of our Corrugated and Paper divisions. The design of the new machine features state-of-the-art technology that will produce a superior lightweight paper, enhancing our position and confirming us as a leading player in the U.K. and Ireland. Smurfit Kappa's two U.K. mills will now specialize in producing all of the recycled brown corrugated case material for its U.K. and Irish corrugated business, while maintaining its presence in the market."
The investment continues the 150-year history of papermaking at Townsend Hook. Smurfit Kappa's position in Europe as a leading paper manufacturer, producing 4.7 million metric tpy, will ensure that the supply of paper to its customer base is uninterrupted during the complex installation and commissioning of the new equipment.
Back To Top
|
New Products
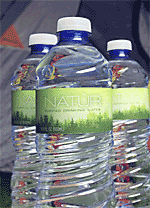 NewPage Corp., Miamisburg, Ohio, this week introduced its 40 lb. (65 gsm) EcoPoint™, a new wet strength label paper offering environmental and performance advantages for the bottled water, juice, and soft drink industries. NewPage notes that EcoPoint 40 lb. offers a notable source reduction advantage to beverage producers, with up to a 7% reduction in label paper usage compared with traditional 43 lb. (70 gsm) bottle label papers, and is designed for optimal performance in continuous roll fed labeling operations as well as cut-and-stack labeling machines. EcoPoint is available with third-party chain-of-custody certifications to the Forest Stewardship Council.
EcoPoint 40 lb. joins the broader range of label papers from NewPage for beverage markets which includes DuraPoint™, ProPoint™, and LithoPoint™ product brands. In addition, NewPage manufactures specialty papers used in flexible packaging, technical and pressure-sensitive labeling applications.
Back To Top
|
Cristini Diagnostic Systems (CDS), Italy, has introduced its new FiberScanFIX™, an on-line version of the company's well known microwave consistency meter. The system is engineered to be connected to multiple sensors and to be installed in various positions of the forming section. The connection is made via a high speed Ethernet network.
CDS explains that key parameters such as water weight and consistency in critical points of the forming section are normally measured by use of hand held devices, but their value changes constantly (vacuum, stock conditions, etc.). Only real-time monitoring, it says, allows superior optimization of dewatering and consistency, and also allows closed loop controls.
Important optimizations such as ply bonding, vacuum control and optimization, and refining can be easily achieved with FiberScanFIX, CDS points out, adding that faster startup and threading are also possible, thanks to optimization and the shortening of time to reach optimal machine parameters.
The FiberScanFIX system employs microwaves, so it is not necessary to obtain permission to use, store, or transport it, as with traditional gamma gauges, the company says. The sensors, CDS continues, allow a unique and impressive reading range, up to 44.000 gsm, with a precision of 0.01%. The patented microwave technology is extremely accurate, compared with old meters (infrared or radiofrequency technologies), the company emphasizes.
More information is available online.
Back To Top
|
Published Pricing
Domtar, Montreal, Que., Canada, reportedly will raise the price of its uncoated freesheet offset rolls by $60 per ton. The price increase becomes effective with shipments beginning April 1.
Back To Top
|
The Newark BCI Division of The Newark Group, Cranford, N.J., USA, has announced an 8% price increase on all sheets, cut-to-size panels, loose-leaf panels, and spines. The increase for these specialty products will be 5% and will apply to all of the division's foam-padded products, unitized covers, and various lines of industrial packaging products. It will become effective with all orders shipped on or after April 9.
Newark BCI serves the global coverboard, file, puzzle, game, and associated markets, with converting plants in Chicago, Ill; Franklin, Ohio; and Los Angeles, Calif. With the invention of multi-ply laminating of completed book covers (two panels and a spine joined together in a continuous manufacturing process), The Newark Group began serving the book manufacturer market with this new "unitizing" capability. Initially known as Book Covers Inc., and later BCI, this business is now a part of Newark BCI.
Back To Top
|
Tronox Inc., Oklahoma City, Okla., USA, on behalf of its subsidiary companies, this week announced a $250 per metric ton price increase for all TRONOX® titanium dioxide grades sold in Latin America. The price increase becomes effective April 1, or as contracts allow.
This increase is in addition to those previously announced. Other increases may be announced locally within each region, Tronox noted.
Tronox is one of the five largest producers and marketers of titanium dioxide pigment used in paint, coatings, plastics, paper, and many other products. The company's pigment plants, located in the U.S., Australia, and the Netherlands, supply products to approximately 1,100 customers in 100 countries. In addition, the company produces electrolytic products, including sodium chlorate, electrolytic manganese dioxide, boron trichloride, elemental boron, and lithium manganese oxide.
Back To Top
|
People
The Forest Products Association of Canada (FPAC), Ottawa, Ont., Canada, this week announced that Avrim Lazar will be retiring as its president and CEO at the end of this month. He will be replaced on an interim basis by Catherine Cobden, currently SVP of FPAC. Cobden has managed the association's economic files and led the landmark Biopathways study into how to best transform the forest sector through innovation. A permanent replacement will be in place in September.
"Avrim has been an extraordinary industry leader who has made giant strides in improving the environmental credentials of Canada's forest products industry and who was pivotal in working with government to lay the groundwork for the sector's transformation," said Jim Lopez, chairman of the board at FPAC. "They will be big shoes to fill, but Catherine has been an essential player in the success of FPAC and I know she will do a top-notch job over the next six months."
The association is the voice of Canada's wood, pulp, and paper producers nationally and internationally in government, trade, and environmental affairs. The $57-billion-a-year forest products industry represents 2% of Canada's GDP and is one of Canada's largest employers, operating in 200 forest-dependent communities from coast to coast and providing 240,000 direct jobs across the country.
Lazar is known for his leadership role in bringing together industry and environmental groups in the landmark Canadian Boreal Forest agreement, signed in 2010. During an often challenging decade, he also helped the industry develop new markets, new products, new partnerships, and new positioning as a player in the emerging bio-economy.
FPAC said that it will be announcing a new vision and new challenge for the sector later this spring to build on the industry's recent success.
Back To Top
|
Louisiana-Pacific Corp., Nashville, Tenn., USA, has named Curt Stevens to succeed Rick Frost as CEO, effective May 4. Frost, who has served as CEO since 2004, will retire from LP May 31. During the period from May 4 through May 31, Frost will remain with Louisiana-Pacific to aid in the transition.
LP Chairman Gary Cook said that "the board of directors is very pleased to announce the appointment of Curt Stevens as our new CEO. Curt is a leader of exceptional integrity and ability. His long experience and deep familiarity with LP along with his expansive knowledge of financial and operational matters make him well suited to lead LP into a promising future.
"Rick Frost has served LP with distinction and we have been very fortunate to have enjoyed his steady and inspirational leadership during turbulent times. This transition has been well planned and will be seamless," Cook added.
Stevens joined LP in 1997 and has held senior management positions throughout his career at the company. He was appointed to the interim position of EVP, COO in December 2011. Previously, he served as EVP, administration and CFO from May 2002 to December 2011. From September 1997 to April 2002, Stevens served as VP, treasurer and CFO. Before joining LP, he spent 13 years in executive positions at Planar Systems Inc., a manufacturer and supplier of flat panel displays. He is also a member of the board of directors of Quanex Building Products.
Back To Top
|
TAPPI News
Roll Damage a Problem?
Attend the Shipping, Receiving and Warehousing Workshop, in Nashville, April 2-4, 2012, and learn new ways to avoid expensive roll damage and improve your bottom line.
Discounted Registration Ends March 23
Be a part of this dedicated group of mills, carriers, warehouses and printers as they collaborate to reduce in-transit damage to rolls of paper at this premier forum for industry leading paper shippers.
Keynote addresses will be presented by Michele Donahue, Executive Director of Paper Supply Chain with Conde Nast publishers, and Colin Barrett, Consultant, Author and Educator.
This is truly a practical, interactive and collaborative shipping and receiving workshop put on by industry professionals, for industry professionals - all parties of the supply chain - to address common issues and concerns relating to damage and damage prevention in the paper industry. It's an excellent networking opportunity - paper buyers, paper companies, carriers, securing / damage prevention specialists, block and bracing manufacturers, safety experts all under one roof. Learn more about TAPPI's Shipping, Receiving and Warehousing Workshop.
Back To Top
|
Make the most out of your time at PaperCon by attending one or more of these workshops or seminars. Additional registration is required for each.
Essentials of Market Pulp Course
Wednesday, April 25
Instructor: Alan F. Button, PhD, World of Market Pulp
Gain a broad understanding of current pulp trends in the global marketplace, understand the unique nature of pulps through the study of a large cross-section of samples from all over the world, and initiate a simple, efficient evaluation process for smart pulp selection. Learn more.
Coating 101 Course
Saturday and Sunday, April 21-22
Taught by TAPPI coating experts from both the supplier and manufacturing backgrounds, this course is designed for commercial professionals needing a technical knowledge base, professionals new to the paper industry, young professionals that are recent graduates or new to coating, or professionals new to coating who've spent their career in other parts of the paper industry. Learn more.
Eliminating Cost while Enhancing Customer Value
Sunday, April 21
Instructor: Christopher W. Miller, PhD, NPDP, President, Innovation Focus, Inc.
A customer-centered and creative approach to value analysis (the Unilever approach), this one-day workshop will help you unleash the power of your organization. Learn to design a customer-centered cost reduction project; facilitate an effective cost reduction effort; and how to select tools and techniques that will help you and your team be more customer-centered. Learn more.
Stickies Workshop Sunday
April 21
Instructor: Dr. Mahendra Doshi, Editor, TAPPI Journal and Progress in Paper Recycling Designed for engineers, scientists and technicians who want to a better understanding of stickies and related issues, anyone working in recycling mills, using recycled pulp or supplying equipment, chemicals or recovered paper to recycled mills will greatly benefit from attending. Learn more.
Back To Top
|
Join the World's Process Control Experts in New Orleans
The 15th Control Systems Conference will bring together the world's preeminent experts in pulp and paper process measurement, control and systems engineering. The exceptional program emphasizes both practical implementation and leading research.
Control Systems 2012 will be held April 22-25 in conjunction with TAPPI's PaperCon 2012, the largest pulp and paper technical program in the world and Control Systems 2012 attendees have access to the PaperCon Sessions and Trade Fair. Discounted registration is available through March 30.
Keynote Address: "What's Hidden in your Data? Sensor-Fusion and Signal Processing for Process and Performance Monitoring" - Sirish L. Shah, Department of Chemical and Materials Engineering, University of Alberta
Topics include:
- Web Imaging and Inspections ·
- Millwide Applications
- Paper Machine Optimization and Grade Change
- Paper Machine CD Applications
- Sheet Quality Measurement
- Pulp Mill Sensors
- Pulp Mill Controls
- Diagnostics and Analysis
- Process Control New Technology Showcase
Learn more about the Control Systems 2012 program.
Back To Top
|
Eliminating Cost while Enhancing Customer Value Workshop
Taking place at PaperCon, this one-day workshop on Sunday, April 21 will help you learn and identify effective tools and techniques needed to build a customer-centered, fact-based cost reduction strategy
Lead by Christopher W. Miller, PhD, NPDP, President Innovation Focus, Inc., this workshop features a customer-centered and creative approach to value analysis (the Unilever approach). Attend and learn how to unleash the power of your organization; design a customer-centered cost reduction project; facilitate an effective cost reduction effort; and how to select tools and techniques that will help you and your team be more customer-centered.
During this workshop, you'll learn how to design a customer-centered cost reduction project, facilitate an effective cost reduction effort, select tools and techniques that will help their team be more customer centered and build a customer centered, fact based cost reduction strategy
Process engineers and mid-to-upper level manufacturing managers within the paper manufacturing industry with an interest in cost management and reduction will find this course beneficial. Experience in cost reduction and related activities would be helpful.
Learn more about Eliminating Cost while Enhancing Customer Value Workshop and PaperCon.
The cost for this course is only 500 USD, which includes lunch and course materials. This special rate is being offered to TAPPI for this one-time workshop. Register now.
Back To Top
|
Winning at New Products: Proven Roadmap to Success
Contrary to popular belief new product ideas often are not the biggest problem companies face. It's figuring out which ones are most likely to succeed – and then taking them through to development and launch. Join Stage-Gate International April 17-18 in Alexandria, VA, to learn how the top global competitors get it done!
The two-day seminar will help attendees improve their ability to conceive and develop winning new products and launch products faster than ever before. Why attend? Because research shows that a high-quality product development process increases new product success by almost 40%.
The seminar is led by the creator of the Stage-Gate process, Dr. Robert Cooper, an internationally recognized forest products innovation thought-leader who has helped companies develop new products for more than 25 years. The seminar will teach attendees how to:
- Tap customer knowledge and needs to identify the right products to develop
- Pinpoint the factors that will help, or hinder, product success
- Structure a cross-functional approach to speed development
- Engage company leadership to champion the right development projects
After two days packed with lectures, self assessments, problem solving sessions and case studies, you'll leave ready to take your team and company to the next level of new product success.
Learn more
Plan to attend "Winning at New Products: Proven Roadmap for Success" and the May 15-16 seminar "Successfully Implementing and Sustaining Your Idea-to-Launch Innovation Process" – AND SAVE! Contact Valerie Sather for promotion information – valerie.sather@stage-gate.com
Remember to use the code TAP11 to receive the TAPPI member discount!
Back To Top
|
Nominations for the major TAPPI 2013 awards are due by August 1, 2012.
The awards that may be presented in the upcoming year are:
Gunnar Nicholson Gold Medal Award - The Association's highest technical honor may be presented annually to recognize an individual or individuals for preeminent scientific and engineering achievements of proven commercial benefit to the world's pulp, paper, board, and forest products industries and the other industries that TAPPI serves.
Herman L. Joachim Distinguished Service Award - The Association's highest award for service, may be presented annually to recognize leadership and service which have significantly and demonstrably contributed to the advancement of the Association.
Paul W. Magnabosco Outstanding Local Section Member Award – The highest honor for Local Sections may be presented annually to recognize an individual for outstanding leadership and exceptional service to one or more Local Sections, which have resulted in significant and demonstrable benefits to the Local Section members.
TAPPI Fellow - TAPPI Fellows are Individuals who have been members of TAPPI for not less than 10 years prior to the nomination, and who have contributed meritorious service to the Association and/or the paper and related industries. Retiring members of the TAPPI Board of Directors become Fellows automatically at the end of their term.
The TAPPI Awards and Honors page has links to these awards which will show the qualifications required and links to the nomination forms that must be completed. You may submit all nomination forms by email to standards@tappi.org, or you may fax them to the attention of the awards department at +1-770-446-6947, or send by mail to TAPPI, Awards Department, 15 Technology Parkway South, Norcross, GA 30092, USA.
Back To Top
|
The Coating Process
Edited by: Jan C. Walter
This book covers fundamentals and practical applications of paper coating. The book is divided into eight chapters that outline the process of making coated paper, the preparation, application and drying, and treatment of the dried coated surface. Each chapter is written by an expert in the particular subject area covered. This book is an excellent resource for both businesses and universities. The Coating Process.
View the Table of Contents
Product code: 0102B057
Member Price: $103.00
Non-Member Price: $155.00
Back To Top
|
PaperCon 2012 will feature two Keynote Speakers as the industry gathers April 22-25 in New Orleans. Jeffrey Hayzlett , Bestselling Author, Global Business Celebrity and Sometime Cowboy will address the crowd on Monday, April 23 in the Opening Session and Lisa Bauer Lotto, M.S., Director, Environmental and Sustainability Programs, Green Bay Packaging Inc., will kick-off the Coating program during a special session on Sunday, April 22. Learn more about PaperCon and these speakers.
PaperCon is where CEOs, mill managers, superintendents, scientists, process engineers and suppliers gather to learn and network. Program tracks include Papermakers, Coating and Graphic Arts and PIMA Management. The PaperCon program also features: Inside and outside the box: Optimizing paperboard grades , the Sustainability Forum , an Executive Panel Discussion , a Young Professional Program , Coating 101 Course and other practical workshops and seminars and features the largest PaperCon exhibit ever. Bonus Sessions (open to all PaperCon registrants) Control Systems 2012: The first USA appearance for this highly-rated biannual conference. RPTA Production-Technical Seminar , the OpEx Reliability Seminar .
Take a moment to register and reserve your hotel room for this year's "must attend" event.
Back To Top
|
Each year, TAPPI is generously supported by companies who join, or renew, as Sustaining Members. Through their dues, these companies support TAPPI's extensive educational efforts as well as facilitate the work of the TAPPI Foundation, a significant source of funding for the vital scholarship programs we offer to next-generation superstars. We are proud to list these visionary leaders as dedicated participants in sustaining, and growing the future of the paper, pulp and converting industries.
If you, or your company, are not currently members of this select group, we invite you to join today. To see if your company is a Sustaining Member, click here. To learn more about the many benefits inherent in becoming a Sustaining Member, please click here, or call Sustaining Member Concierge Piper James at 770-209-7225.
Back To Top
|
GOLF!
The 2012 EMPIRE STATE TAPPI - New York/ Canadian Pima Spring Golf Outing will be held Thursday, May 17, 2012 at the Queensbury Country Club, Lake George, New York. This event has an 11:00AM Start and is a 4- man scramble. This event is limited to 72 players, so register early! There will be hot dogs and beverages at the turn, an open bar 4:00 to 5:30 pm, a steak dinner, golf awards and prizes after dinner. Dinner tickets may be purchased in advance or at door. Cash or check made out to Empire State TAPPI/PIMA, or use credit card @ registration. No refunds after May 11th.
Help support this year's event by sponsoring a hole. A $100 Sponsorship will give you a prominently displayed sign on a tee letting everyone know you are a TAPPI/PIMA "booster." All proceeds will go towards scholarships. All sponsorship information and the exact company name is needed by May 6th.
MARK YOUR CALENDARS! "Transformational Technologies Conference" on June 21, 2012 at the Queensbury Hotel in Glens Falls, New York. Presentations are currently being established and more details will follow.
For ALL of the latest Empire State TAPPI - New York/Canadian PIMA information, please visit the March 2012 Empire State TAPPI - New York/Canadian PIMA Newsletter.
Back To Top
|
You are invited to attend the 62nd annual Maine PAPER DAYS Event at the University of Maine, Wells Conference Center, April 4-5, 2012 in Orono, Maine. This year we have a terrific line up of speakers and panels who will focus on The Paper Industry from a Global Perspective.
Speakers include Mark Cross, Senior Vice President of MeadWestvaco; Deece Hannigan, Vice President Sappi Fine Paper; and Terrance Gallagher, Senior Division Vice President, Nalco Company. On Wednesday afternoon we will have a talk by Brendan Lowney, President of Forest Economic Advisors, with a student panel moderated by R. James Alexy, Senior Partner Brimstone Consulting.
At breakfast on Thursday morning we will have a student panel moderated by Mike Luciano, HR Manager of Verso Paper with a topic of Expanding Students Global Perspective. The morning session on Thursday will address the "Challenges of the Global Economy" with a panel consisting of Al Blanchard of, Sappi Fine Paper, Robin McCann of OMNOVA Solutions, Keith Meyer of Andritz, Zeynep Turk of The Maine International Trade Center, and Mark Mosher of Irving Paper Ltd.
In addition we expect the Honorable Governor Paul LePage to address the group at 10:00 am on Thursday.
Please see the attached brochure, which includes a schedule of events and registration information. There is also a separate registration form, for your convenience.
Back To Top
|
|
|
TAPPI Over the Wire | 15 Technology Pkwy. S. | Norcross, GA 30092 USA | Voice: 770.446.1400 | Fax: 770.446.6947
|
 |