 |
|
Weekly Spotlight
Appleton Papers Inc., Appleton, Wis., USA, and Hicks Acquisition Co. II, Dallas, Texas, today announced that they have agreed to a business combination valued at $675 million
Learn More...
|
Apprenticeships and regulated occupations are vital to the continuing health and long-term success of the Canadian forest products sector
Learn More...
|
AbitibiBowater Inc., Montreal, Que., Canada, doing business as Resolute Forest Products, reports that it and Montreal-based Fibrek Inc. are cooperating on an orderly transition to Resolute's effective control
Learn More...
|
Nominations for TAPPI's 2013 Gunnar Nicholson, Herman L. Joachim, Paul W. Magnabasco, and TAPPI Fellow awards must be submitted by this August 1.
Learn More...
|
Domtar Corp., Montreal, Que., Canada, this week announced that its SVP and CFO Daniel Buron, has won the "Aces of Finance" award in the Public Corporation category
Learn More...
|
Weyerhaeuser Co., Federal Way, Wash., USA, has announced the 2012 hours of operation for its Charles W. Bingham Forest Learning Center at Mount St. Helens, Wash.
Learn More...
|
The Indonesian TAPPI (Ina-TAPPI) and Indonesian Pulp and Paper Association (IPPA) this week announced they will host the 2012 Pan Pacific Conference (PPC) November 22 – 24, 2012, in Bandung, West Java, Indonesia
Learn More...
|
To help celebrate 25 years of the Rainforest Alliance's achievements, Domtar Corp., Montreal, Que., Canada, co-sponsored the sustainability organization's 25th anniversary gala yesterday, May 16, in New York, N.Y., USA
Learn More...
|
Below is the latest listing of job openings in the TAPPI Career Center.
Learn More...
|
Market Roundup
Finland produced 2.6 million metric tons of paper and paperboard in January - March 2012, down 12% from the corresponding period in 2011
Learn More...
|
Recovered paper prices declined by $5 - $10 at U.S. mills for old corrugated containers (OCC), mixed paper, and coated groundwood materials, while holding flat on high grades and pulp substitutes
Learn More...
|
Pulp & Paper
Uni Core Holdings Corp (UCHC), Hong Kong, announced this week that APT Paper Group (APT), Shenzhen, Guangdong, China, one of UCHC's subsidiaries, has integrated its operation resources to expand market share
Learn More...
|
Catalyst Paper, Richmond, B.C., Canada, has again rescheduled meetings of its secured and unsecured creditors to consider the plan of arrangement under the Companies' Creditors Arrangement Act of Canada
Learn More...
|
Doh-Ei Paper, Japan, has started up an Andritz (Graz, Austria) PrimeDry Steel Yankee (3.7 m dia. and 4.3 m shell length) at its Hokkaido mill in Japan
Learn More...
|
Domtar Corp., Montreal, Que., Canada, has acquired EAM Cor. a privately-held manufacturer of absorbent composite solutions, from Kinderhook Industries for $61 million
Learn More...
|
Florelle Tissue Corp., Brownville, N.Y., USA, has begun production following a four month conversion of a specialty paper mill formerly known as Brownville Specialty Paper Products Inc.
Learn More...
|
The new machine will cost some EUR 115 million and will take about 18 months to erect
Learn More...
|
Ilim Group, Russia, reports that during the first three months of this year, its Koryazhma mill in Arkhangelsk Oblast, Russia, manufactured 273,000 metric tons of pulp and paper products, which is 2% more than in the first quarter of 2011
Learn More...
|
Logística y Transporte Sociedad de Responsabilidad Limitada, Argentina, has restarted a pulp mill it purchased in Puerto Piray, Argentina, in December 2011
Learn More...
|
Containerboard/Packaging
Metsä Board, Finland, a producer of folding boxboard, reports that it has completed the rebuild of a board machine at its Ӓänekoski mill in Finland, increasing its folding boxboard capacity by 30,000 metric tpy, to 240,000 metric tpy
Learn More...
|
Sonoco Recycling LLC, a unit of Sonoco (Hartsville, S.C., USA) and one of the largest packaging recyclers in North America, reports that Sonoco Conflex's Rural Hall, N.C., facility has successfully diverted more than 95% of its waste from landfill
Learn More...
|
|
New Products
International Paper, Memphis, Tenn., USA, has launched a 100% recycled paper, Hammermill Great White 100, to North American customers
Learn More...
|
Published Pricing
Ahlstrom, Finland, has raised the price of its specialty paper materials produced by the Label and Processing business area, due to recent increases in raw material and energy costs
Learn More...
|
Billerud, Sweden, reportedly will raise prices for its semi-chemical fluting by £25 per metric ton in the U.K.
Learn More...
|
People
The board of directors at Södra, Sweden, this week said that it has decided to start searching for a new CEO and group president, noting that it and CEO Leif Brodén have "differing views" regarding the ongoing development of the company and what is required in the form of leadership and clarity
Learn More...
|
National Envelope, Frisco, Texas, USA, this week announced the addition of Anthony Rizzo as SVP of Sales and Marketing
Learn More...
|
Travels with Larry
Recently a politician made a statement during a campaign speech: "Corporations are not people, people are people." I wish to respectively submit that this person is incorrect in his assessment of the business world. People make up corporations
Learn More...
|
TAPPI News
The October 2012 PEERS Conference will focus on sustainability, practical operations, and new technology.
Learn More...
|
This year's IBBC will focus on advancements and commercialization of bioconversion technologies that leverage forest products manufacturing infrastructure.
Learn More...
|
Get an overview of the entire pulping and papermaking process and run a pilot plant paper machine at the TAPPI Hands-on Workshop for Pulp and Paper Basics.
Learn More...
|
The 16th Annual Northeast PIMA/TAPPI Scholarship Tournament will be held on June 8, 2012, in Auburn, Maine.
Learn More...
|
TAPPI President and CEO Larry N. Montague has announced the launch of Tissue360º, a new TAPPI magazine available in both print and online formats that will cover the latest business and technology developments in the global tissue and towel industry.
Learn More...
|
The Nonwovens Engineers and Technologists Division (NET) of TAPPI will co-locate its annual Innovative Nonwovens Conference (NETInc) next year with PaperCon 2013, April 28 - May 1 in Atlanta, Ga., USA.
Learn More...
|
Even as far back as 1967, in an article by then VP of R&D for Union Camp William Aiken, he said that "the money donated by our companies to educational institutions, the efforts of our recruiters at schools, and the programs of our industrial relations and public relations departments have been inadequate to supply the technical manpower which our industry needs."
Learn More...
|
The Extrusion Coating Manual, Fourth Edition, is a valuable training tool for new employees and a useful reference for everyone involved in extrusion coating.
Learn More...
|
This volume provides a thorough study of the longitudinal dynamics and tension control of web handling systems.
Learn More...
|
This handbook provides cost-saving strategies associated with the use of chemical additives during the manufacture of paper.
Learn More...
|
|
Find us on Facebook
Network with us on LinkedIn
Follow us on Twitter
|
Weekly Spotlight
Appleton Papers Inc., Appleton, Wis., USA, and Hicks Acquisition Co. II, Dallas, Texas, today announced that they have agreed to a business combination valued at $675 million. The combined company will be listed on the Nasdaq exchange, and according to Appleton, will position the company for long-term growth and profitability with an improved balance sheet and greater access to capital.
Appleton is a producer of specialty coated paper products and a provider of encapsulation applications. Hicks Acquisition is a special purpose acquisition company founded and headed by Thomas O. Hicks, with approximately $149.3 million of cash in trust.
When the transaction closes, Appleton will change its corporate name to Appvion. The new name combines the words "applied" and "innovation," reflecting the company's transformation from a paper company to a business focused on coating formulations and applications, and specialty chemicals.
With 2011 sales of nearly $860 million, Appleton operates in three business segments: direct thermal, in which it holds the leading position in North America and is considered to be the market leader in innovation; carbonless/security, in which, under its NCR PAPER and Appleton brands, the company holds the number one position worldwide; and Encapsys®, a rapidly growing specialty chemical operation that is a leader in microencapsulation for use in branded consumer products. The company employs approximately 1,800 people and has been 100% employee-owned since Nov. 9, 2001.
Members of the Appleton management team will continue in their current positions under the new ownership structure.
"This transaction will be the latest milestone in Appleton's transformation from a paper producer to a company focused on coating formulations and applications, and specialty chemicals," said Mark Richards, Appleton's chairman, president, and CEO. "The combination with Hicks Acquisition provides the company with capital to further strengthen our balance sheet, support our businesses, and pursue attractive growth opportunities in our markets."
Completion of the transaction, which is expected during July, is subject to expiration or early termination of any applicable Hart-Scott-Rodino waiting period, approval of the transaction by Hicks Acquisition's stockholders, approval by State Street Bank and Trust Co., the trustee representing participants in the Appleton ESOP, and certain other closing conditions.
Back To Top
|
Apprenticeships and regulated occupations are vital to the continuing health and long-term success of the Canadian forest products sector, according to a new report from the Forest Products Sector Council released at the 25th PwC Annual Forest and Paper Industry Conference in Vancouver, B.C., Canada. The report, Linking Innovation with Skills: Apprenticeship, regulated occupations and workforce development in Canada's forest products sector suggests current apprenticeship and training practices need to change to keep up with a coming skilled worker shortage.
According to the report, employers and workers both agree on the benefits of apprenticeship—a higher quality of work, safer work environments, higher wages and higher productivity, and increased employee satisfaction. But with only 40% of the forest products sector employers continuing to invest in apprenticeship training, the rates of participation may be lower than needed to replace retiring workers.
At the professional level, the report highlights the declining enrollment in university forestry programs leading to a professional forestry designation and suggests key HR shortages will exist if this trend continues.
The reports also notes that "with collective will—and through determined collaboration with stakeholders such as educators and governments—apprenticeship training and regulated occupations can continue as strong contributors to the success of Canada's forest products sector."
The Forest Products Sector Council (FPSC-CSPF) is an independent, not-for-profit organization, funded by the Government of Canada's Sector Council Program. Established in 2008, FPSC-CSPF provides national collaborative leadership in developing strategic responses and interventions addressing current and emerging human resource and labor market issues in the Canadian forest products sector.
Back To Top
|
AbitibiBowater Inc., Montreal, Que., Canada, doing business as Resolute Forest Products, reports that it and Montreal-based Fibrek Inc. are cooperating on an orderly transition to Resolute's effective control. The goal for both parties is to minimize any disruption to Fibrek's key relationships, including its employees, customers, suppliers, and other partners.
Following the filing of Fibrek's first quarter 2012 consolidated interim financial statements with the Canadian securities authorities, it announced that each member of the board had stepped down, effective immediately. Resolute subsequently announced that the principal members of Fibrek's outgoing management team, including Pierre Gabriel Côté, CEO, and Patsie Ducharme, CFO, have agreed to assist in the transition process as special advisors until May 31.
"We're delighted to mark this important step in the integration of Fibrek within the Resolute family," said Richard Garneau, president and CEO. "While there remains work to be done, the spirit of cooperation we've announced today means business as usual for Fibrek's operations, customers, suppliers, and other business partners."
The departing members of Fibrek's board were replaced by the following Resolute nominees: Michel Desbiens, Michel Gagnon, and Daniel Filion, each of whom will serve as outside director, and Richard Garneau (chair), Jo-Ann Longworth, and Jacques P. Vachon. Longworth is Resolute's SVP and CFO, and Vachon is its SVP for corporate affairs and chief legal officer.
This new Fibrek board appointed Garneau president and CEO, Alain Boivin, VP of operations, Longworth VP and CFO, and Vachon VP for legal affairs and corporate secretary. Boivin, Garneau, Vachon, and Longworth are not entitled to additional compensation for serving as either Fibrek officers or directors.
Garneau added that "we've consistently said that we would remain true to the three themes that underlie Resolute's strategy: cost-effective operational excellence, disciplined use of capital, and strategic development. Increasing our capacity in the growing global pulp market by adding these assets is consistent with our strategy. Resolute is uniquely positioned to generate additional value from these assets by completing their integration."
Having acquired approximately 70.9% of the currently outstanding shares of Fibrek as of this past Monday, May 14, Resolute also announced that its offer to acquire the remaining shares of Fibrek will not be further extended and will expire definitively at 5 p.m. EDT today, May 17. As further described in the offer circular and other ancillary documentation related to the offer (as amended), Resolute intends to carry out a second step transaction to acquire the Fibrek shares not deposited in the offer.
Back To Top
|
Nominations for major TAPPI 2013 awards are due by August 1, 2012. The awards that may be presented next year are:
- Gunnar Nicholson Gold Medal Award. The Association's highest technical honor may be presented annually to recognize an individual or individuals for preeminent scientific and engineering achievements of proven commercial benefit to the world's pulp, paper, board, and forest products industries and the other industries that TAPPI serves.
- Herman L. Joachim Distinguished Service Award. The Association's highest award for service, may be presented annually to recognize leadership and service that have significantly and demonstrably contributed to the advancement of the Association.
- Paul W. Magnabosco Outstanding Local Section Member Award. The highest honor for local sections may be presented annually to recognize an individual for outstanding leadership and exceptional service to one or more local sections, resulting in significant and demonstrable benefits to Local Section members.
- TAPPI Fellow. TAPPI Fellows are Individuals who have been members of TAPPI for not less than 10 years prior to the nomination, and who have contributed meritorious service to the Association and/or the paper and related industries. Retiring members of the TAPPI Board of Directors become Fellows automatically at the end of their term.
The TAPPI Awards and Honors page has links to these awards and shows the qualifications required and links to the nomination forms that must be completed. All nomination forms can be submitted by email to standards@tappi.org, or faxed to the attention of the Awards Department at +1-770-446-6947, or send by mail to TAPPI, Awards Department, 15 Technology Parkway South, Suite 115, Norcross, GA 30092, USA.
Back To Top
|
Domtar Corp., Montreal, Que., Canada, this week announced that its SVP and CFO Daniel Buron, has won the "Aces of Finance" award in the Public Corporation category. Organized by the Quebec chapter of Finance Executives International Canada (FEI Canada), this recognition is awarded annually to recognize professional accomplishments of exceptional financial executives.
"Daniel is a pivotal member of Domtar's Management Team who continues to show strong leadership as well as being a great team player in our Management Committee," said John D. Williams, president and CEO. "He richly deserves this award and on behalf of everyone at Domtar, we would like to thank him for his outstanding contribution and for representing our three core values of Agility, Caring, and Innovation."
Buron is a chartered accountant and graduate from Université Laval. He began his career at Domtar in 1999 and has been CFO since May 2004. He has responsibilities for all finance functions: financial disclosure, financial risk and debt management, treasury operations, tax administration, investor relations, and information technology. In 2009, he received the ICD.D designation from the Institute of Corporate Directors.
Back To Top
|
Weyerhaeuser Co., Federal Way, Wash., USA, has announced the 2012 hours of operation for its Charles W. Bingham Forest Learning Center at Mount St. Helens, Wash. The center opened its doors for the 2012 season this past Friday, May 11, with hours of operation from 10 a.m. - 4 p.m. on the days the Visitor Center is open. Admission is free to the general public. More specifically:
- During the opening month (May 11 - June 10), the center will only be open Friday - Sunday
- Starting with the weekend of June 15 through Labor Day, September 3, the center will be open Friday - Monday
- The indoor exhibits also will be available on Memorial Day, Monday, May 28, and Wednesday, July 4.
In addition, the gift shop, restrooms, and center's outdoor facilities will be open seven days a week from 10 a.m.- 6 p.m. The Washington State Department of Transportation rest area hours will mirror the hours of operation for the gift shop.
The Charles W. Bingham Forest Learning Center is located inside of the blast zone of the May 18, 1980 eruption of Mount St. Helens on state Route 504. It is a partnership between Weyerhaeuser, Washington State Department of Transportation, and the Rocky Mountain Elk Foundation.
Back To Top
|
The Indonesian TAPPI (Ina-TAPPI) and Indonesian Pulp and Paper Association (IPPA) this week announced they will host the 2012 Pan Pacific Conference (PPC) November 22 – 24, 2012, in Bandung, West Java, Indonesia. The PPC will be held in conjunction with the First Resource Efficiency in Pulp and Paper Technology (REPTech) International Symposium and Exhibition carried out by the Center for Pulp and Paper (CPP), Ministry of Industry, Republic of Indonesia..
The Symposium will attempt to answer some of the questions raised by speakers and delegates at the 2010 APPITA Symposium in Sydney, Australia, as a review of the current international situation of the pulp and paper and related industry, and will feature invited papers and presentations over two full days on:
- Non-wood fiber source and technology
- Recycled fibers and technology
- Lignocellulosic materials and the future of other raw fiber materials for the paper industry
- Wood supply and sustainable forest management system
- Sustainable production system for the pulp and paper industry
- Process control and instrumentation
- Developing, implementing, and maintaining an energy efficiency program
- Renewable energy resources and alternatives
- Best available technology in the pulp and paper industry
- Other related topics.
REPTech's announcement and call for papers, including symposium program details, is available online. Questions should be emailed to Ina-TAPPI Secretariat Andri T. Rizaluddin at inatappi@gmail.com, or andritr3@yahoo.com, or by phone at 62 22 5202980 ext 426.
The conference, symposium, and exhibition of REPTech and PPC will be held in the Hotel Horison, Jl. Pelajar Pejuang No. 45, Bandung, 40264, West Java, Indonesia. When booking rooms, please indicate that you are attending 2012 PPC Indonesia.
Back To Top
|
To help celebrate 25 years of the Rainforest Alliance's achievements, Domtar Corp., Montreal, Que., Canada, co-sponsored the sustainability organization's 25th anniversary gala yesterday, May 16, in New York, N.Y., USA. The annual dinner and award ceremony commemorated some of the Rainforest Alliance's biggest triumphs since pioneering the concept of responsible forestry certification. Those include:
- Conserving more than 170 million acres of forest and farmlands in 100-plus countries
- mproving lives of more than 9.5 million people worldwide, including farmers, forest managers, workers, and their families
- Engaging with more than 490,000 agriculture, forestry, and tourism operations
- Introducing countless consumers to Rainforest Alliance Certified products (includes extensive work with Domtar, whose papers have set the industry standard for displaying the Forest Stewardship Council (FSC) label and the Rainforest Alliance Certified seal.
Domtar has worked with the Rainforest Alliance to ensure that 28 of the company's pulp and paper mills and converting and distribution facilities now meet FSC standards. Nearly 20% of Domtar's paper products have been FSC-certified while, across America, the FSC estimates that only 4% to 6% of paper products earn that distinction.
"After all of our hard work over the past 25 years, it's important for us to recognize companies for their demonstrated commitments to sustainability, and that list includes Domtar," said Tensie Whelan, president of the Rainforest Alliance. "We've worked with Domtar for more than a decade, and we're proud of how they have raised the bar for the paper industry and set an example for encouraging environmental responsibility."
Proceeds from the gala will benefit the Rainforest Alliance's comprehensive sustainability initiatives, which help ensure sustainable livelihoods and conserve biodiversity. This marks the seventh year Domtar has sponsored the gala, one of the ways Domtar has teamed up with the Rainforest Alliance to encourage responsible paper production and fiber sourcing.
"We're proud to be at the forefront of the responsible production and use of forest products, and we're excited for both the gala as well as a workshop beforehand that will bring together leaders in sustainable business," said Lewis Fix, Domtar VP of Sustainable Business and Brand Management. "We're looking forward to saluting some of this year's remarkable achievements, and we also salute the Rainforest Alliance for 25 years of accomplishments."
Back To Top
|
Below is the latest listing of job openings in the TAPPI Career Center. The current listing includes a variety of engineering, technical, marketing, reliability, and management positions, as well as product development and purchasing opportunities in the U.S. pulp and paper industry. Current, specific job openings at companies and locations in the TAPPI Career Center include:
Employer |
Title |
City |
BASF, The Chemical Co. |
Paper Applications Engineer |
Charlotte, N.C. |
BASF, The Chemical Co. |
Mgr., Process & Product Dev. |
Gordon, Ga. |
Catalyst Paper |
Reliability Engineers |
Powell River/Crofton, B.C. |
Herty Adv. Materials Dev. Ctr. |
President and CEO |
Savannah, Ga. |
IMERYS Pigments |
Technical Manager |
Sandersville, Ga. |
IMERYS Pigments |
Purchasing Category Manager |
Sandersville, GA |
Intertape Polymer Group |
Dir. of Mktg, Carton Closure Prod. |
Bradenton, Fla. |
Orange Co. Container Group |
Maintenance - Paper Mill |
Forney, Texas |
RockTenn - West Point, Va. |
Air Compliance– Env. Eng. |
West Point, Va. |
SCA Americas |
Shift Electrician |
South Glens Falls, N.Y. |
More information about these jobs is available online.
Back To Top
|
Market Roundup
Finland produced 2.6 million metric tons of paper and paperboard in January - March 2012, down 12% from the corresponding period in 2011, according to a report by the Finnish Forest Industries Federation. Consumption of graphic paper grades, it adds, remained on a low level in Europe, the main market area, which had an impact on Finnish production volumes. On the other hand, production of fine paper improved toward the end of the quarter. Prices for paper and paperboard products remained stable, compared with the corresponding period of 2011.
Finland produced 1.7 million metric tons of pulp in January - March 2012, according to the report, about the same amount as in the corresponding period of 2011. First-quarter pulp exports grew to 720,000 metric tons, up 28% from 2011.
"Rapid action is needed to improve the cost-competitiveness of the forest industry in Finland. Finnish production units need to retain their vitality in an intensely competitive international market," said Timo Jaatinen, director general of the Finnish Forest Industries Federation.
"New investments are needed to alter the situation, but they cannot be realized unless domestic production factors such as raw material, energy, logistics, and labor costs, become competitive with our key rival countries," Jaatinen added.
Timber sales activity was brisk in the first quarter. The forest industry purchased 6.2 million cubic meters of wood in January - March, more than double the amount procured in the first quarter of 2011. Pulpwood procurements came to 3.2 million cubic meters. Damage from storms around the turn of the year spurred timber sales, especially in January. The high price of timber also boosted sales activity.
Back To Top
|
North American printing and writing (P&W) paper volumes remain sluggish, according to Mark Wilde, senior analyst with Deutsche Bank. Preliminary April shipments, he notes, fell 5.5% y/y. Uncoated free sheet was down 4.7% y/y (YTD -2.2%), he adds, while coated papers were down 2.2% y/y (YTD -4.7% y/y).
Back To Top
|
Recovered paper prices declined by $5 - $10 at U.S. mills for old corrugated containers (OCC), mixed paper, and coated groundwood materials, while holding flat on high grades and pulp substitutes, according to PPI Pulp & Paper Week prices published May 10 versus April 10 levels. The declines on a sequential basis stemmed from slower export demand especially in the U.S. South and Midwest to China and Mexico, as well as a variety of mill shutdowns at OCC- and groundwood-consuming mills.
Pulp & Paper Week noted that the declines, although slight sequentially, were big (about 25%), compared with 2011 average prices, which on most major grades were the highest ever, unadjusted for inflation. Compared with May 2011 pricing, OCC was down $25 this month, mixed paper was off almost $30, special news deink quality old newspapers (ONP) No. 8 was down $40, and office paper (OP) was off $100. OP this month was $70 under its 2011 average and OCC was $30 under, Pulp & Paper Week reported.
Back To Top
|
Pulp & Paper
Uni Core Holdings Corp (UCHC), Hong Kong, announced this week that APT Paper Group (APT), Shenzhen, Guangdong, China, one of UCHC's subsidiaries, has integrated its operation resources to expand market share. APT owns and operates three major production sites in China—Shenzhen, Qingdao, and Suzhou—providing APT with a large customer base and wide distribution. APT has designed a system to share APT's resources through integration of the three regional businesses.
By integrating customer resources of the three major production sites, the market share of APT products is effectively improved, UCHC notes. A great success example, it adds, includes the recent supply of honeycomb-packaging products by the Shenzhen Factory to Haier Industrial Park located at Shunde of Guangdong Province. Historically, APT has been supplying honeycomb-packaging products to Haier Group in Qingdao. Haier Group, after having repeated communication with APT and attending site visits, was very satisfied with the production capacity and technology of the Shenzhen Factory that facilitated the extended patronage of APT products in Haier Group's business at Shunde, UCHC reports.
Thomas Lee, COO of UCHC, said that "APT is persistent about the high quality of product, technology innovation, and new product development. Under the premise of high standards in areas of product quality and after-sales service, the resources of the three factories are integrated and leveraged, allowing for gradual rise in both market share and sales volume."
Through its subsidiaries, Uni Core develops, manufactures, and distributes "environmentally friendly" paper and agricultural products. The company was founded in 1998, and two years later was acquired by APT Paper Group.
Back To Top
|
Catalyst Paper, Richmond, B.C., Canada, has again rescheduled meetings of its secured and unsecured creditors to consider the plan of arrangement under the Companies' Creditors Arrangement Act of Canada. The meetings have been rescheduled from May 18 to May 23.
"Our discussions are continuing towards the possibility of amending the current plan of arrangement that would better enable Catalyst to emerge from creditor protection on a stronger financial footing, said Kevin J. Clarke, president and CEO. "The additional time is intended to permit these discussions to be successfully completed."
The rescheduled meetings will be held at a new location, the Westin Wall Centre, Vancouver Airport, 3099 Corvette Way, Richmond, B.C., at 10:00 a.m. for unsecured creditors and 11:00 a.m. for the First Lien Noteholders.
It is anticipated that the court date to sanction and approve the plan of arrangement will be rescheduled to May 25.
Catalyst Paper produces specialty mechanical printing papers, newsprint, and pulp with four mills located in British Columbia and Arizona, USA. The company has a combined annual production capacity of 1.8 million metric tons.
Back To Top
|
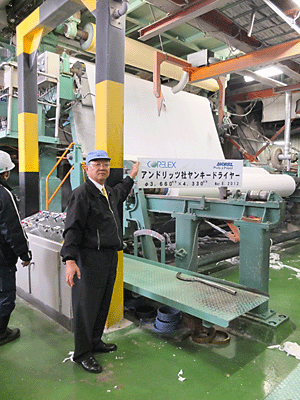 Doh-Ei Paper, Japan, has started up an Andritz (Graz, Austria) PrimeDry Steel Yankee (3.7 m dia. and 4.3 m shell length) at its Hokkaido mill in Japan. The successful startup is the first for a Steel Yankee in Japan.
Doh-Ei produces 4,500 metric of facial tissue and 14,500 metric tpy of toilet tissue from 100% recycled paper.
In June 2011, Doh-Ei commissioned Andritz to upgrade its drying line. In addition to increasing production and improving runnability of the tissue machine, the investment also was made to reduce energy costs, a particularly important criterion due to the sharp rise in oil and gas prices.
"Steel is a highly heat-conductive material. Following the installation of the Anditz PrimeDry Steel Yankee, the energy efficiency and production output of our mill will be very high," said Masashi Kobayashi, president of Doh-Ei (photo on right).
Back To Top
|
Domtar Corp., Montreal, Que., Canada, has acquired EAM Cor. a privately-held manufacturer of absorbent composite solutions, from Kinderhook Industries for $61 million. EAM Corp. produces airlaid and ultrathin laminated absorbent cores with brands such as NovaThin® and NovaZorb® used in feminine hygiene, adult incontinence, baby diapers, and other medical, healthcare, and performance packaging solutions.
EAM serves a diversified customer base and has long-standing relationships including well-known branded and private label consumer products manufacturers throughout North America and abroad. The company operates a 71,000 sq ft facility with state-of-the-art research campus and production lines in Jesup, Ga., USA, It has annual sales of approximately $45 million in more than 50 countries and a total of 53 employees.
"The acquisition of EAM Corporation will give us long term research capabilities to further differentiate our full line of adult incontinence products while integrating the best available technology to grow our existing businesses," said John D. Williams, president and CEO. "EAM's patented airlaid manufacturing process provides the performance, quality, and cost competitiveness that we believe to be keys to success in the personal care market."
Back To Top
|
Florelle Tissue Corp., Brownville, N.Y., USA, has begun production following a four month conversion of a specialty paper mill formerly known as Brownville Specialty Paper Products Inc. According to a report this past week in the Watertown Daily News, Watertown, N.Y., 15 production employees are now working at the plant, operating a napkin machine that started up early last week. Soon, the article notes, packages of napkins produced at the plant will be shipped to customers in Canada, Pennsylvania, and Ohio.
The mill, which has been closed for three years, has a total of 94,000 sq ft. President Harry Minas explained in the newspaper article that for the past two years, Florelle had been busy securing funding and making plans to outfit the mill. He noted that the mill will have a second machine up and running within a few more days, and that it will add a second 12-hr production shift this month. "The napkins have already been sold, and we have clients across Canada that are waiting for the product."
To be ready this month, three more converting machines are being installed that will produce paper towels and bathroom tissue, Minas said. The plant will hire an additional 15 to 20 production workers to operate that equipment. "It'll probably be a couple of weeks before we're ready to hire, but it should happen by the end of May or beginning of June," Minas added.
Minas said the plant will continue installing converting equipment throughout the summer. A paper machine that will use virgin pulp is being installed, which will be completed by August. More converting machines will be installed in June. By the end of the year, the mill will operate 24 hr a day, seven days a week. Employees will work on two 12-hour shifts every day.
"I foresee the machines being installed by late summer," he said. "We hope to be hitting our target of 70 to 75 employees" by the end of the year, Minas said in the article.
Reported to cost more than $4 million, the project received funding from several local sources, including a $350,000 loan from the Jefferson County, N.Y., Industrial Development Agency, a $250,000 loan from the Development Authority of the North Country, a $125,000 loan from the North Country Alliance, and a $100,000 grant from the Jefferson County Local Development Corp.
Back To Top
|
The Heinzel Group, Vienna, Austria, will install a new paper machine at its Pöls, Austria, mill. The new machine will cost some EUR 115 million and will take about 18 months to erect. Construction will begin this summer and the new, 5.4 m-wide bleached kraft papers machine will startup in late 2013.
"With construction of the new paper machine, we are primarily reacting to the increasing quality demands of the market while strengthening the Pöls site at the same time," said Alfred Heinzel, CEO of Heinzel Group.
Zellstoff Pols AG, a subsidiary of the Heinzel Group, is the largest producer of premium grade bleached long-fiber sulfate pulp in Central and South-Eastern Europe. In addition to pulp, Pöls also produces premium grade bleached kraft paper under the Starkraft name. With the new paper machine, the mill will increase its capacity to 80,000 metric tpy.
Back To Top
|
Ilim Group, Russia, reports that during the first three months of this year, its Koryazhma mill in Arkhangelsk Oblast, Russia, manufactured 273,000 metric tons of pulp and paper products, which is 2% more than in the first quarter of 2011.This includes some 91,000 metric tons of market pulp, a 1% increase compared with the same period of the previous year.
Paper production increased by 15%, to 59,000 metric tons, including 22,000 metric tons of sack paper, 30,000 metric tons of offset paper, and 7,000 metric tons of wallpaper. Board production during the first quarter of 2012 was 124,000 metric tons, decreasing 2.5% compared with the same period in 2011.The slight reduction in board output has been triggered by the changing ratio of sack paper and board output with more sack paper to satisfy the market demand. Pulp production grew by 3%, totaling 288,000 metric tons in the first quarter.
The company's OAO corrugated box business in the Leningrad Oblast increased production by more than 4%, producing 29,400,000 sq meters of corrugated products in the first quarter of 2012.
In the first quarter, Ilim Group's Bratsk and Ust-Ilimsk mills in Irkutsk Oblast, Russia, produced 363,000 metric tons of pulp and paper products, approximately equaling output in the first quarter of 2011. This includes 314,000 metric tons of market pulp, a 2% increase from the same period in 2011.
Board production at Bratsk and Ust-Ilimsk totaled 48,500 metric tons, a decrease of 16% compared with output in the first quarter of 2011. Improved corrugating technologies have boosted demand for thinner board, the company notes, resulting in lower tonnages but almost the same number of sq meters produced.
Back To Top
|
Logística y Transporte Sociedad de Responsabilidad Limitada, Argentina, has restarted a pulp mill it purchased in Puerto Piray, Argentina, in December 2011, according to a report by Industrial Info Resources (IIR), Sugar Land, Texas, USA. The mill had belonged to Benfide Sociedad Anonima, Misiones, Argentina, which went bankrupt in August 2009 and sold the operations to its employees.
The mill's employees formed a cooperative, Trabajo e Industria de Puerto Piray Ltda, to operate the facility. With financial help from the local government, the cooperative ran the mill for about two years. In mid-2011, market conditions in the country forced the mill to close in September. After several attempts to reopen it, the facility was finally bought in December 2011 by two brothers from Taiwan, the IIR report explains.
IIR further notes that originally started up in 1974, the pulp mill currently operates 20 days per month and shuts down for the last 10 days for maintenance and upgrade work. Company officials stated that they want to invest some $3.7 million to double the mill's production capacity from 80 metric tpd to 150 metric tpd. This expansion project includes the replacement, addition, and modifications of equipment such as burners, pumps, motors, drives, washer tanks, etc., and is expected to begin around the middle of this year. Approximately 55 people work at the facility.
Back To Top
|
Containerboard/Packaging
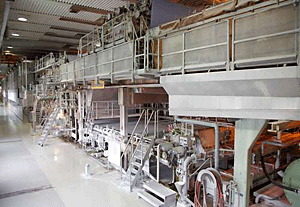 Metsä Board, Finland, a producer of folding boxboard, reports that it has completed the rebuild of a board machine at its Ӓänekoski mill in Finland, increasing its folding boxboard capacity by 30,000 metric tpy, to 240,000 metric tpy. Normal production restarted in early May for the company's Carta Integra and Carta Solida products.
"Demand for sustainable packaging made from fresh forest fibers continues to be strong, and we have responded by increasing the availability of our cartonboards," says Olli Mäki, VP Cartonboard Sales, Metsä Board. "Their purity and excellent sensory properties make them ideal for confectionery, pharmaceuticals, cosmetics, and beautycare products, and their superior printing surface allows perfect reproduction for high quality packaging. Their light weight, compared with boards of similar strength, means less impact on the environment."
An additional project to increase cartonboard sheeting capability is also underway at Ӓänekoski, converting the facility released by closure of the paper machine at the site. This will be finalized in the autumn.
The Ӓänekoski board machine rebuild is part of Metsä Board's paperboard investment program 2011 - 2012, aimed at improving availability and service. Under this program, the Simpele mill rebuild was successfully finalized in June 2011 and the Kyro mill was rebuilt in December 2011. The program also included improvement of the Kemi linerboard mill's coating operations. Further investment continues with the building of a new biopower plant next to the Kyro mill, for completion in autumn 2012, to replace fossil natural gas with carbon neutral bioenergy.
Back To Top
|
Sonoco Recycling LLC, a unit of Sonoco (Hartsville, S.C., USA) and one of the largest packaging recyclers in North America, reports that Sonoco Conflex's Rural Hall, N.C., facility has successfully diverted more than 95% of its waste from landfill. The plant is the second CorrFlex facility to receive a silver-tier Star Award.
In September 2011, employees at the Rural Hall fulfillment facility formed Team Green, focused on achieving landfill-free status in two years. Since the plant is a fulfillment facility, its materials mix frequently changes based on the current customer and project. One of the major challenges for the team was staying on top of the flux of materials and determining the best outlet for each. To better understand their current program, the team began tracking landfill and recycling tonnage. Dumpster contents were monitored, assessing those areas that needed work to reduce the plant's landfill tonnage. Common recycling areas were set up in production and office areas, and employees were encouraged to bring in their recyclables from home.
The constant change within the temporary work force at Rural Hall posed another challenge for Team Green when implementing a shift in the plant's recycling culture, as the personnel within the work force changes daily and many are non-English speakers. By working closely with the plant's temporary staffing agency and using bilingual labeling, Team Green was able to overcome many recycling issues.
"In just eight months, Team Green was able to divert more than 95% of Rural Hall's waste through a mix of recycling, reuse, and waste-to-energy," said Harris DeLoach III, Sonoco Recycling representative for the Rural Hall facility.
A strong component of Rural Hall's recycling program is the initiative to reuse articles that aren't recyclable, or are difficult to recycle. Many old inventory items such as bags or boxes, previously slated as waste, are now distributed among employees. This initiative also includes items that can be reused by local non-profit organizations. Used work gloves, scrap bubble wrap, and other items that were once thrown away now benefit non-profit educational programs within the community. Used computers, printers, and other inventory items are donated to public schools in need of supplies for art or learning.
Additionally, management agreed to set up an Employee Recycling Account to collect funds from the new programs. The account is split at the end of the year among all permanent employees.
Created to recognize customer and Sonoco facilities for achieving significant milestones in landfill diversion and waste stream reduction, the Sonoco Sustainability Star Award program is comprised of three tiers:
- Gold Star Awards that recognize facilities having achieved 99% landfill diversion
- Silver Star Awards that are given to facilities achieving 95% landfill diversion
- Bronze Awards that recognize facilities having made significant waste reduction achievements.
With 50 locations worldwide, Sonoco Recycling annually collects approximately 3 million tons of old corrugated containers, various grades of paper, metals, and plastics. Currently, it operates six material recovery facilities (MRFs) and serves nearly 150 communities in which curbside-collected residential and commercial materials are processed.
Back To Top
|
New Products
International Paper, Memphis, Tenn., USA, has launched a 100% recycled paper, Hammermill Great White 100, to North American customers. The paper is the newest product to join the Hammermill Great White line of recycled products.
"Consumers are interested in recycled paper products, but they also want confidence in the quality and how the product performs. Hammermill Great White 100 is the best of both worlds and offers a dependable 99.99% Jam-Free Guarantee paper that has a 92 brightness. It's a great paper that runs smoothly, looks sharp, and contains 100% post consumer fiber," said Jon Ernst, IP's VP for Imaging Papers.
The new product is produced at IP's Riverdale, Ala., mill and comes after a multi-million dollar investment in the company's recycled product capabilities. Hammermill Great White 100 joins IP's 30% and 50% recycled paper offerings already available and carries Forest Stewardship Council® certification.
The product launch coincides with the celebration of Hammermill brand's 100th anniversary. "Hammermill is one of oldest brands in the industry because of its ability to continually evolve to meet customer needs, and this product is our latest example of meeting consumers where they are in the marketplace," added Ernst.
Back To Top
|
Published Pricing
Ahlstrom, Finland, has raised the price of its specialty paper materials produced by the Label and Processing business area, due to recent increases in raw material and energy costs. The price hike will affect all Label and Processing products worldwide and will be effective with shipments beginning June 1. The exact increase will vary depending on the products and markets. Specific details will be discussed with each customer individually.
Products manufactured by Ahlstrom's Label and Processing Business Area include graphic, packaging, processing, release, and label papers. Their main end-use applications are release liners, self-adhesive labels, metalized wet glue labels, flexible packaging, and repositionable notes. They also are used for the production of posters, abrasive materials, and furniture foils.
Back To Top
|
Billerud, Sweden, reportedly will raise prices for its semi-chemical fluting by £25 per metric ton in the U.K. The increase is expected to begin with shipments on June 1. According to a RISI (Brussels, Belgium) report, Billerud is raising prices for the grade to increase profitability and to improve unsatisfactory returns from the U.K. market.
Back To Top
|
People
The board of directors at Södra, Sweden, this week said that it has decided to start searching for a new CEO and group president, noting that it and CEO Leif Brodén have "differing views" regarding the ongoing development of the company and what is required in the form of leadership and clarity. The board said it is terminating the employment of Brodén immediately.
At the same time, the board decided to temporarily extend responsibilities of the president of Södra Cell, Gunilla Saltin, to also include the role of CEO for the entire Södra group. Recruitment of a new CEO will begin immediately. Until a new CEO is appointed, Board Chairman Christer Segerstéen will extend his involvement in the company and take over as acting chairman. In this role, he will mainly assist the acting CEO with ownership and industry issues.
Brodén has been employed by Södra since 1999, initially to head Södra Cell, Södra's biggest subsidiary, and then as CEO and group president. Saltin has been president of Södra Cell since 2008. She joined Södra in 2000, and previously held the position of plant manager at Södra Cell Värö.
"Business at Södra subsidiaries Södra Cell, Södra Timber, Södra Interiör, and Södra Skog is successful in their respective areas. This guarantees that Södra will not suffer any adverse effects in the limited time estimated to find a new CEO," Segerstéen said.
Back To Top
|
National Envelope, Frisco, Texas, USA, this week announced the addition of Anthony Rizzo as SVP of Sales and Marketing, Rizzo joins National Envelope from Positive Promotions where he was COO for the largest printed paper and plastic products manufacturer in North America. He also has held senior positions with Hilex Poly LLC and Alcan Packaging.
Back To Top
|
Travels with Larry
Recently a politician made a statement during a campaign speech: "Corporations are not people, people are people." I wish to respectively submit that this person is incorrect in his assessment of the business world. People make up corporations. The success of corporations depends on the quality of people they employ.
A few weeks ago I was on my way to New Orleans looking forward to PaperCon2012. I was wondering if all the hard work of TAPPI's volunteers and staff would again pay off for our industry. I had great expectations. I am proud to say that yes, PaperCon2012 was a success. We had nearly 1,500 people registered for this years' conference. This number represented a 7% increase over 2011. Our post conference surveys showed very high approval ratings with a combined score of 84%. With all the anticipation and success, my mind kept going back to a letter I received on Friday April 20, 2012 from Mike Jackson. I have included this letter below.
During my 5-1/2 years with TAPPI, I have had the opportunity to spend some one on one time with many of our industry's greatest leaders and their employees. Mike Jackson and the rest of the VERSO team rank right at the top of the list of outstanding individuals. They represent a lot of what is right with our industry.
On May 14, 2012 Mike Jackson will retire as President & CEO of Verso Paper Company. He is truly one of a kind leader and gentleman. I have come to know, appreciate and respect Mike over the past several years. His style and humbleness have permeated the entire Verso organization.
He has the unique style, missing from so many, that commands the attention and loyalty of those he comes in contact with. He practices what I call the Platinum Rule: "treat others like they want to be treated."
Mike encourages his suppliers to not only tell us what we are doing right in our mills but also let us know one thing what we can do better.
David Patterson will take over the reins from Mike. He will have some big shoes to fill and I wish him well. He has a great team behind him.
With Mike's permission, I have included his letter to the employees of Verso Paper Corporation.
Mike, I and thousands of others wish you and your family the best that life has to offer.
You will be missed.
Sincerely,
Larry
Verso Paper Corp.
Headquarters
6775 Lenox Center Ct.
Suite 400
Memphis, TN 38115
Mike Jackson
President and CEO
T 901-369-4231
F 901-369-4228
www.versopaper.com
April 20, 2012
Dear Verso Employees,
My FIRST comment in this monthly letter will not surprise you as it is about safety. The SECOND comment may be a bit more of a surprise, but hopefully not.
Our safety record through today is fantastic! That means before there was a Verso and after the sale of the coated paper business to Apollo. Pick a time, any time. This result is the best ever for the first third of any year. Our total incident rate is .74 and our lost workday rate is 0. That is terrific and you should feel so proud of that performance. I know I am! Those numbers happen because more and more people are engaged and care about what happens to their peers. This is your performance.
Now for the second comment. Sometime ago I spoke with our Board of Directors that my intention was to retire within a certain amount of time and that succession planning, which of course is always part of the Board's duty, would be an important element of continuing the progress that Verso has made over the past number of challenging years. At my age, this notice to the Board may not be a surprise to you!
Verso and you and your respective teams have done an incredible job against great odds, including surviving the worst depression in 80 years. I have been so proud of all of you, including my Lead Team, who have faced so many obstacles but never flinched. We have lived the Verso Foundation Document that we developed, taken the company public, improved and refined our core product strategy, introduced a significant amount of new products, developed a name called Verso that has high recognition and respect in the halls of federal, state and local government, and developed and executed an energy strategy that few in the coated paper business could have executed and that will have a lasting positive impact on our company. To me it was always about your ability to execute. While many in the coated paper business have raised the white flag, we have moved forward.
Recently, many segments of our financial balance sheet have been addressed, which include a new revolver and an improving debt maturity schedule, and that is all good. Verso is now poised to go to another level. This will take time and effort and will be beyond my personal commitment. Trust me that my replacement will have both the ability and experience to take us to the next level.
I have loved this challenge and have so much appreciated all the wonderful work you have done and all the friendships I have gained over these past years. This is the correct time for my wife of 42 years and me to go to that next chapter in our lives. It also takes our company to a new chapter.
My last official duty will be on May 14th at our quarterly earnings call. Thank you for all you have done and, as importantly, my thanks to your families and partners that have put up with all the hours you have worked. Until we meet again.
Back To Top
|
TAPPI News
The 2012 TAPPI PEERS Conference, October 14 - 17 in Savannah, Ga., USA, is designed to answer the most pressing business and technical questions faced by pulp and paper companies as they manage raw materials, assets, regulatory requirements, and production assets.
In addition to keynote speaker Don Roberts, vice chairman of CIBC World Markets, the TAPPI PEERS Conference will feature peer-reviewed technical presentations, expert speakers, exclusive networking opportunities, and new technologies that can help mills optimize operations.
The TAPPI PEERS Conference will be co-located with the International Bioenergy and Bioproducts Conference, creating a value-added opportunity for participants to expand their learning, networking, and resources by attending both events.
Additional PEERS program and conference details will be announced soon.
Up-to-date information is available online.
Exhibit and Sponsorship opportunities also are available. Contact Shane Holt by email at TAPPIPEERS@naylor.com or by phone at 800.369.6220, ext. 3345.
Back To Top
|
TAPPI's International Bioenergy and Bioproducts Conference (IBBC), October 17 - 19, 2012, in Savannah, Ga,, USA, will focus on technical advancements and commercialization of bioconversion technologies that leverage the forest products manufacturing infrastructure.
Keynote speakers for 2012 IBBC are:
- Paul Spindler, VP of Technology at Catchlight
- John B. Crowe, chairman and CEO, Buckeye Technologies Inc.
In addition, IBBC will include technical presentations, expert panels, case studies, and reports from projects that address:
- Feedstock and harvesting improvements to increase yield and quality of biomass
- Bioelectricity using combined heat and power (CHP)
- Bioconversion technologies for wood and biomass
- Production of chemicals and transportation fuels from wood and biomass
- Policies and incentives for bioconversion projects.
IBBC will be co-located with the TAPPI PEERS Conference, creating a value-added opportunity for participants to expand their learning, networking, and resources by attending both events. Additional IBBC program and conference details will be announced soon.
Up-to-date information is available online. Exhibit and Sponsorship opportunities also are available. Contact Shane Holt by email at TAPPIPEERS@naylor.com or by phone at 800.369.6220, ext. 3345.
Back To Top
|
Get an overview of the entire pulping and papermaking process and run a pilot plant paper machine! It's all a first-hand experience at the TAPPI Hands-on Workshop for Pulp and Paper Basics. This course is coming up soon, June 4 - 8, 2012, at North Carolina State University in Raleigh, N.C., USA.
Register to reserve your seat.
The number of students in the course will be limited in size to ensure the best interaction among attendees and instructors during the workshop.
If you're wondering whether this course is right for you, it probably is! It's an essential course that teaches the basic concepts in pulp and paper manufacturing and is designed for anyone wanting to improve their role in operations.
Learn more.
Participants will receive a course notebook and CD with approximately 400 pg of reference materials.
Earn CEUs: You'll earn 3.7 continuing education credits at the completion of this June 4 - 8 course. It's a lovely time to be in North Carolina.
Back To Top
|
Mark your calendars! The date has been set for the 16th Annual Northeast PIMA/TAPPI Scholarship Tournament. The event will be held on Friday, June 8, 2012, at the Fox Ridge Golf Club in Auburn, Maine, USA.
Please see the event flyer for additional information.
Registration is now open for this event.
If you have any questions or need additional information, please contact Micki.Meggison@sappi.com.
Back To Top
|
TAPPI President and CEO Larry N. Montague has announced the launch of Tissue360º, a new TAPPI magazine available in both print and online formats that will cover the latest business and technology developments in the global tissue and towel industry. Initially, in 2012, Tissue360º will be published semiannually and cover the global tissue business including tissue manufacturing equipment and sytems, chemicals and applications, pulp/fiber, mill and plant operations, packaging and wrapping, and converting operations.
"Tissue manufacturing is one of the most technically innovative, dynamic, and rapidly growing segments of the global pulp and paper business, and Tissue360º will provide cutting edge editorial content on this key sector," Montague notes. "The tissue industry encompasses a wide range of common products that consumers and businesses around the world use every day. Tissue360º will keep readers up to date on new and emerging process technology developments, equipment and systems applications, and advances in the use of chemicals, all from the operating floor perspective."
Top professionals in North America will receive print and electronic versions with digital distribution to more than 5,000 international readers.
Tissue includes a broad array of paper products used in both consumer (at-home) and commercial/industrial (away-from-home) markets. Common products include bath or toilet tissue, towels, napkins, and facial tissue. Tissue products are manufactured around the world with the developed economies of North America and Europe traditionally accounting for a majority of output and consumption. However, in recent years tissue manufacturing and demand have been growing rapidly in developing economies, including major growth in China, which is now the world's second largest consumer.
Back To Top
|
The Nonwovens Engineers and Technologists Division (NET) of TAPPI will co-locate its annual Innovative Nonwovens Conference (NETInc) next year with PaperCon 2013, April 28 - May 1 in Atlanta, Ga., USA.. The NETInc technical conference is a unique event developed by engineers and technologists to cover the latest market and technical developments and innovations in the global nonwovens industry.
"Co-location of the NETInc Conference at PaperCon 2013, the pulp and paper industry's largest event and most comprehensive technical conference, will provide attendees an expanded range of options to network and learn the latest cutting edge technical content," notes TAPPI President and CEO Larry N. Montague. "The nonwovens industry is a dynamic, rapidly growing segment of our industry that encompasses a wide range of raw materials, applications, and market segments, and it employs some of the most innovative technology in the industry. We're excited about the synergy provided by having these two industry leading events located in one venue."
NETInc offers peer reviewed papers, expert speakers, and exclusive networking opportunities. A comprehensive technical program covers a wide range of products, innovative technologies, and topics including market trends, raw materials, fibers, and processing used in an array of applications including absorbent products, medical applications, building science, and many others.
TAPPI's NET Division covers the global nonwovens business and includes members and nonwovens experts from diverse markets and disciplines. It covers materials, equipment, and processes for the manufacture and use of nonwovens. The division's technical committees sponsor courses, conference sessions, roundtables, and TAPPI PRESS products, as well as networking and problem-solving opportunities.
Back To Top
|
Even as far back as 1967, in an article by then VP of R&D for Union Camp William Aiken, he said that "the money donated by our companies to educational institutions, the efforts of our recruiters at schools, and the programs of our industrial relations and public relations departments have been inadequate to supply the technical manpower which our industry needs." Today, the paper industry continues to have a shortage of technically trained employees.
The reasons for this shortage are the overall shortage of scientists and engineers and the tremendous amount of baby-boomer retirements. TIME magazine recently reported that the pulp and paper industry will hire 24,000 people in the next four years in North America alone. Throughout the country, an estimated 600,000 manufacturing jobs are going unfilled because employers can't find people with the right skills.
If you are in the pulp, paper, or packaging industry, it is a safe bet that your education was funded in part or in whole by individuals, companies, and/or school foundations. It has always been the case that to attract young engineers and scientists to a specialized program like ours, there needed to be some type of scholarships. Committing to not only a major but an industry when you are a freshman in College can be a pretty scary undertaking.
So today, what we are asking is for you to "pay it forward." Others were there for you; please give whatever you can to the future of our industry. The need is great. We would love for you to give a gift to the TAPPI Foundation, but if not to the TAPPI Foundation, please give to one of the foundations at the paper or packaging schools.
Back To Top
|
The Extrusion Coating Manual, Fourth Edition is now available through TAPPI Press.
Edited by: Thomas Bezigian
This comprehensive volume details all aspects of extrusion coating. The book will be a valuable training tool for new employees and a useful reference for everyone involved in extrusion coating. It includes information on classic materials and troubleshooting techniques as well as the latest materials and machine designs available anywhere in the world today.
Completely revised and updated, the fourth edition contains the work of more than 30 well-known industry experts.
View the Table of Contents
Product code: 0102B065
Member Price: $93.00
Non-Member Price: $140.00
Back To Top
|
Tension Control
Kee-Huyn Shinn, Ph.D.
This volume provides a thorough study of the longitudinal dynamics and tension control of web handling systems. Critical web handling problems that can be related to improper tension control include wrinkle, slack, breakage, lateral movement, and poor roll quality. This valuable text is the only reference currently available devoted entirely to tension control.
Tension Control
View the Table of Contents
Product code: 0101R275
Member Price: $50.00
Non-Member Price: $75.00
Back To Top
|
Martin A. Hubbe and Kasy King
This handbook provides cost-saving strategies associated with the use of chemical additives during the manufacture of paper. Topics include:
- Loss of materials (i.e. "yield" of the papermaking process)
- Production rate issues
- Downtime
- Inefficient use of functional additives
- Process-enhancing additives and their control
- Strategies to reduce the amount of fibers required to make a paper product
- Strategies to reduce the amount of energy to make paper.
A glossary of terms and a brief introduction to selected principles of capital budgeting are provided as appendices.
This book is ideal for paper machine process engineers/scientists, paper machine superintendents, paper mill management, chemical supplier technical staff, product development engineers, paper mill consultants, and technical staff from allied industries, e.g. process control equipment, papermaking machinery, and environmental services.
Cost Saving Strategies in Papermaking Chemistry
View the Forward and Table of Contents
Product code: 0101R325
Member Price: $150.00
Non-Member Price: $215.00
Back To Top
|
|
|
TAPPI Over the Wire | 15 Technology Pkwy. S. | Norcross, GA 30092 USA | Voice: 770.446.1400 | Fax: 770.446.6947
|
 |