 |
|
Weekly Spotlight
Resolute Forest Products Inc., Montreal, Que., Canada, this week celebrated the planting of one billion trees at its forestry operations in northern Ontario
Learn More...
|
Executives from Weyerhaeuser (Federal Way, Wash., USA), Nippon Paper Industries (Japan), Cowlitz County Public Utility District (Longview, Wash.), and the Bonneville Power Administration (BPA) in Portland, Ore., gathered last week at the North Pacific Paper Corp. (NORPAC) facility (a joint venture between Weyerhaeuser and Nippon) to celebrate the largest industrial energy efficiency project in BPA history.
Learn More...
|
NewPage Corp., Miamisburg, Ohio, USA, has been named by the Dayton Business Journal (Dayton, Ohio) as one of several local companies to win Dayton's "Healthiest Employers Award."
Learn More...
|
The new grade is made with 80% straw from "leftover by-product" of harvested wheat crops
Learn More...
|
The TAPPI Yankee Dryer Safety and Reliability (YDS&R) Committee will meet November 5-6 in Neenah, Wis., USA, at the Miron Construction facilities
Learn More...
|
Below is the latest listing of job openings in the TAPPI Career Center.
Learn More...
|
Market Roundup
India is quickly becoming an attractive new market for the U.S. pulp and paper industry, according to Turning the page on India's paper industry: A new chapter in investment potential and growth, a new report from Deloitte, New York, N.Y., USA.
Learn More...
|
China's phenomenal GDP growth of between 9% and 14% annually during the past decade slowed down last year and is forecasted by International Monetary Fund (IMF) to be "only" 8.25% in 2012
Learn More...
|
Global pulp demand remains weak and softwood prices remain under pressure
Learn More...
|
Estimated prices on No. 5, 40-lb offset rolls in the U.S. were down $25/ton to $835 - $875/ton in July
Learn More...
|
June cut-size shipments were -9.7% y/y and offset was -4.0% y/y
Learn More...
|
Pulp & Paper
Alberta Newsprint Co. (ANC) this past week reported that its ownership has approved construction of a power generation plant at its newsprint mill in Whitecourt, Alb., Canada
Learn More...
|
Cascades Inc., Kingsey Falls, Que., Canada, reports the permanent closure of its Cascades Tissue Group plant located in Scarborough (McNicoll Street),Toronto
Learn More...
|
Great Northern Paper Co. reports that it will re-start PM 5 at its East Millinocket, Maine, USA, mill, restoring 37 jobs. No 5, to begin production by the first week of September, will be the second machine operating at the mill since it reopened last October
Learn More...
|
Hebei Yihuocheng Commodity Co., China, has ordered from Andritz, Graz, Austria, a PrimeLineCOMPACT II tissue machine with a steel Yankee
Learn More...
|
Kruger Inc., Montréal, Qué., Canada, this week announced that the Woodland Operations at its Corner Brook, N.L., Canada, mill has achieved certification under the Forest Stewardship Council® (FSC) National Boreal Standard
Learn More...
|
NewPage Corp., this week filed a Joint Chapter 11 Plan with the U.S. Bankruptcy Court for the District of Delaware
Learn More...
|
Catalyst Paper, Richmond, B.C., Canada, and the City of Port Alberni on Vancouver Island, B.C., are moving forward with key strategic initiatives after reaching an agreement-in-principle for the purchase of the company's wastewater treatment facility and additional lands
Learn More...
|
Sappi Ltd., South Africa, reportedly has agreed to sell its entire 34% shareholding in the Jiangxi Chenming Paper Co. in Nanchang City, Jiangxi Province, China, for $41.58 million to the Shandong Chenming Paper Holding Co.
Learn More...
|
The sites proposed for sale were made public during SCA's recent conference call for its H1 results.
Learn More...
|
UPM permanently ceased graphic paper production at the mill situated in Baden-Württemberg this past January
Learn More...
|
Containerboard/Packaging
Corrugated retail ready packaging (RRP) is becoming an increasing necessity for the U.K. food and beverage manufacturing industry, according to a recent survey commissioned by the U.K.-based Confederation of Paper Industries (CPI) Corrugated Sector
Learn More...
|
Unisource Worldwide Inc., Norcross, Ga., USA, reports that its Unisource Global Solutions (UGS) division has completed the asset acquisition of Pakit Sweden AB, an international producer of molded fiber packaging
Learn More...
|
|
New Products
Metsä Tissue, a part of Finland-based Metsä Group, has "renewed" the product range of its Serla brand with new product quality and packaging, referring to improvements in both household towel and toilet paper qualities
Learn More...
|
Voith Paper, Germany, has launched NipVision, an online and real-time measurement tool using the latest roll cover technology
Learn More...
|
People
Longview Fibre Paper and Packaging, Longview, Wash., USA, has appointed Gary Parafinczuk its new human resources director
Learn More...
|
TAPPI News
TAPPI has conducted four key pulp and paper industry courses so far this month, with two more yet to come. These courses will keep employee skills strong and honed with the latest training approaches and technology applications in the containerboard, pulping-bleaching, tissue, and extrusion coating arenas.
Learn More...
|
This year's course, August 21-23 at TAPPI headquarters, will teach expanded energy reduction strategies.
Learn More...
|
The TAPPI Extrusion Coating course, to be held August 27-29 on the Michigan State University campus, provides an opportunity for critical technical training and networking that can help improve your extrusion coating operations and allow you to gain a competitive edge.
Learn More...
|
The TAPPI Biomass Supply, Demand, and Handling Subcommittee, formed in early 2011, is looking for volunteers to join and assist in working on various projects. A September 19 webinar is scheduled to update the subcommittee on efforts in these areas.
Learn More...
|
Inventory Count from August 30 - September 4 means TAPPI Press will not be processing orders until September 5. Orders received during this time will ship in the order they have been received starting on September 5.
Learn More...
|
Join us on Tuesday, August 28, at the Grand View Lodge, Preserve Course, in Pequot Lakes, Minn., USA.
Learn More...
|
The paper coating community will be converging in Atlanta, Ga., USA, Sept.10-12, 2012, for the 12th TAPPI ACFS. This biennial event attracts the world's foremost experts in coating technology, and is the preeminent symposium for leading-edge research. .
Learn More...
|
The 2012 Preventive Maintenance and Essential Care & Condition Monitoring Course shows participants how to set up a cost-effective process and provide practical exercises and techniques. This training takes place Sept. 12-13, 2012, in Raleigh, N.C., USA.
Learn More...
|
The Boiler MACT program is currently being assembled for this meeting, to be held at KBR Offices in Birmingham, Ala., USA, on September 27. More meeting detail will follow when completed.
Learn More...
|
This year's golf tournament proceeds go to the Pacific Section TAPPI scholarship fund. Come enjoy a day of fun that features all you need for your game as well as awards, prizes, and a meal afterwards. Event will be held on September 28.
Learn More...
|
Learn how at the Financial and Strategic Analysis Workshop for Pulp and Paper and Related Industries to be held Oct. 3-5, 2012, in Raleigh, N.C., USA.
Learn More...
|
Special workshop at North Carolina State University focuses on the fundamental processes and operations of today's pulp and paper mills producing a variety of paper and paperboard products.
Learn More...
|
TAPPI is partnering with North Carolina State University to present an imperative workshop for today's economic climate - the NCSU Financial and Strategic Analysis Workshop, October 3-5.
Learn More...
|
Don't miss out on your chance to attend the Fixed Equipment Maintenance Optimization System Workshop (FEMOS) - Sunday, October 14th 2012; 8:00am to 5:00pm EDT in Savannah, Georgia, USA. . This workshop teaches maintenance staff how to manage the mechanical integrity of all fixed equipment.
Learn More...
|
TAPPI Press presents Kraft Pulping. Edited by A. Mimms, M.J. Kocurek, J.A.Pyatte, and E.E. Wright. TAPPI Members receive a $29 discount off of the list price of $87.00.
Learn More...
|
TAPPI members save $75 off the list price for this definitive text on the science of winding written by noted experts Dr. David Roisum and Dr. J.K. Good. This three-part book includes a supplemental CD-ROM.
Learn More...
|
Sessions in Pulping, Engineering, Environmental, Recycling, and Sustainability focus on building a sustainable future.
Learn More...
|
A first-time, unique program for the TAPPI PEERS Conference, this one-day seminar explores the latest reliability strategies today's mills are implementing to stay in-tune and competitive under progressively lean operating conditions. October 14,15,18, 2012.
Learn More...
|
On Wednesday, Thursday, and Friday, Nov. 7-9, 2012, TAPPI will conduct its Tissue Runnability Course at Neenah, Wis., USA., with a faculty of technical experts in each area of the machine from wet end operations through creping and process control.
Learn More...
|
Dr. Kocurek has been involved with TAPPI for nearly 50 years. A TAPPI Fellow and winner of the 1992 TAPPI Distinguished Service Award, he is recently retired from his time as head of NCSU's Dept. of Wood and Paper Science, but is still actively involved at TAPPI.
Learn More...
|
|
Find us on Facebook
Network with us on LinkedIn
Follow us on Twitter
|
Weekly Spotlight
Resolute Forest Products Inc., Montreal, Que., Canada, this week celebrated the planting of one billion trees at its forestry operations in northern Ontario. This achievement is the result of collective efforts made over the past 30 years by the company, its employees, numerous contractors and suppliers, and the Ontario Ministry of Natural Resources.
To mark the occasion, two-meter-tall white spruce trees were planted simultaneously near three of the company's mill sites in the province—at Fort Frances, Iroquois Falls, and Thunder Bay. Ontario's Minister of Natural Resources, the Honorable Michael Gravelle, and Member of Provincial Parliament Bill Mauro were present at the Thunder Bay site. Many community and Aboriginal leaders also attended each of the ceremonies.
"This planting ceremony speaks to our long, successful, and proud company history in northern Ontario and our unwavering commitment to forest renewal and sustainable forestry," said Richard Garneau, president and CEO of Resolute. "Forests are among the world's only renewable resources. We are fortunate to be involved in an industry that is truly sustainable."
The planting of one billion trees represents more than five million hours of actual planting, and does not include the countless hours spent by cone collectors, nursery workers, transportation companies, site preparation operators, and resource professionals, all of whose skills are invaluable throughout the process, Resolute noted.
"I would like to extend my congratulations to Resolute Forest Products and all parties involved in this accomplishment," Minister Gravelle said. "Milestones such as these are a testament to the partnerships we have forged in our working forests and our commitment to the sustainability of the natural resources in our care."
Although forests can regenerate themselves through natural processes, tree planting and other techniques such as aerial seeding are an important part of a successful forest management program and ensure the renewal of the softwood forests so critical to the lumber, pulp, and paper businesses.
Resolute manages approximately 4.5 million hectares of Crown and private lands in Ontario. All (100%) of the lands managed by Resolute in Canada are certified to internationally-recognized sustainable forest management (SFM) standards, with 51% also now certified under Forest Stewardship Council® (FSC) standards.
In June of this year, Resolute became the largest manager of FSC-certified forests in the world. "For Resolute, attaining this level of certification to the rigorous FSC standards is an integral part of both our commitment to sustainable forestry and to meeting the commercial needs of our customers who are increasingly requesting such certification," Garneau added.
Back To Top
|
Executives from Weyerhaeuser (Federal Way, Wash., USA), Nippon Paper Industries (Japan), Cowlitz County Public Utility District (Longview, Wash.), and the Bonneville Power Administration (BPA) in Portland, Ore., gathered last week at the North Pacific Paper Corp. (NORPAC) facility (a joint venture between Weyerhaeuser and Nippon) to celebrate the largest industrial energy efficiency project in BPA history. The project is also one of the largest energy efficiency projects in the U.S. to date.
When complete, the project is expected to save 100,000,000 kwh per year. The energy savings from the completed project will save enough energy to serve approximately 8,000 Northwest U.S. homes. The first phase of the project was completed in June 2011 and the second and final phase is expected to be completed in the first quarter of 2013.
The project, referred to as a "Chip Pre-Treatment Interstage Screen Project," adds two new components to the NORPAC facility. The first change to the mill is the addition of the chip pre-treatment equipment. This equipment treats wood chips with steam and chemicals prior to refining the chips into pulp, resulting in reduced pulp bleaching and brightening costs.
The second feature of the project is the inter-stage screening. Prior to the new screening process, wood chips were ground through two stages of refining. These refining machines are driven by numerous electric motors that require thousands of connected horsepower, which makes the refining process very energy intensive. The inter-stage screening process now allows paper-ready fibers (wood fibers that do not require additional refining) to bypass the second stage of refining, which results in significant electrical energy savings.
"Energy efficiency is the first-choice, least-cost alternative for meeting increasing demand for electricity in the Pacific Northwest," says BPA Administrator Steve Wright. "This project serves to meet our twin goals of promoting a healthy economy and a healthy environment in the Northwest."
NORPAC purchases power for its industrial operation through Cowlitz County PUD. Working through Cowlitz, BPA will fund installation of screening equipment between refiners at the paper mill. The new processes will reduce electricity and chemicals used in the refining process, reducing the environmental impact.
BPA will fund about $21 million and Cowlitz County PUD will contribute up to an additional $3.9 million towards the project. The money contributed by both BPA and Cowlitz comes from their respective conservation funds, which provide financial incentives to their customers for the development and installation of electrical energy savings projects. NORPAC is funding the remaining $35 million of the $60 million project.
"This project is a win-win," said Dan Fulton, president and CEO of Weyerhaeuser. "NORPAC's energy-efficiency project will allow this mill to remain competitive in an increasingly challenging global economic market by significantly reducing the mill's energy costs and decreasing its environmental impact through reduction of energy consumption and chemical use onsite. We are thankful BPA and Cowlitz PUD have partnered successfully with us to make this remarkable energy-efficiency project a reality."
In addition to significant energy and chemical use savings, the project created a surprise benefit. It allows NORPAC to produce a 92 bright groundwood sheet, a new product. This allows NORPAC to continue to diversify and expand the mill's portfolio of products. The mill's marketing effort for the new product, Norbrite 92, started in June of this year.
"NORPAC produces newsprint and high brightness publication papers. The facility operates three machines that manufacture more than 750,000 tons annually and is the largest newsprint and uncoated groundwood printing papers facility in North America.
Back To Top
|
NewPage Corp., Miamisburg, Ohio, USA, has been named by the Dayton Business Journal (Dayton, Ohio) as one of several local companies to win Dayton's "Healthiest Employers Award." This is the second year for the contest, and second award for NewPage.
NewPage has confirmed its commitment to employee wellness by making it one of the corporation's overall goals. The company's wellness activities are aimed at reducing the incidence of the most prevalent diseases and disorders experienced by NewPage employees.
NewPage has a committee dedicated to employee wellness and offers a variety of programs to support employees including:
- Focused disease management and education programs
- Preventative care services
- Health fairs
- Wellness competitions
- Newsletters and updates to the company's intranet highlighting employee successes
- On-site fitness classes and walking trails.
"One of the things I am most proud of is how our wellness programs have brought employees together by encouraging, motivating, and supporting each other. In just a couple of years, wellness is quickly becoming a part of our culture at NewPage," said George Martin, president and CEO of NewPage. "We realize that our employees are a huge asset and by offering these programs we can help them become healthier and happier."
The Dayton Business Journal engaged Healthiest Employers, an independent organization dedicated to promoting wellness in business, education, and non-profits, to review the nominations and choose the winners.
George Martin accepted the award on behalf of NewPage from the Dayton Business Journal at a breakfast honoring winners at the Crowne Plaza in Dayton.
Back To Top
|
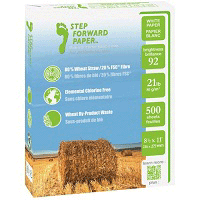 Prairie Pulp & Paper Inc., Winnipeg, Mb, Canada, has announced the production of straw-based copy paper. The new grade is made with 80% straw from "leftover by-product" of harvested wheat crops and 20% Forest Stewardship Council certified wood fiber. It is being marketed under the brand name Step Forward Paper.
The paper is being sold exclusively through Staples stores across Canada and online at Staples.ca, supported by Canadian national distributor Unisource Canada, which teamed up with Staples Canada to supply the new product. "Paper made from leftover straw produces high quality and performance that compares with other copy and printer papers," said Pete Gibel, VP of Merchandising at Staples Canada.
Step Forward Paper is currently being made at a paper mill in India. "Our goal is to establish a market that will support our plans to build a new state-of-the-art facility in the Canadian prairies in Manitoba, which will in turn enable us to produce this straw paper with an even smaller footprint," Jeff Golfman, Prairie Pulp & Paper president, explained.
As Golfman and Prairie Chairman Clayton Manness explain, phase one for the company is the manufacturing and importing of Step Forward Paper. Phase two will include constructing a state-of-the-art eco-mill in the Canadian prairies, where millions of tons of leftover straw are readily available.
Back To Top
|
The TAPPI Yankee Dryer Safety and Reliability (YDS&R) Committee will meet November 5-6 in Neenah, Wis., USA, at the Miron Construction facilities, 1471 McMahon Dr. The fall meeting is open to all TAPPI members and visitors (one time only). To attend as a visitor, please contact Scott Springmier .
The fall 2012 YDS&R Committee meeting will be held in conjunction with Lake States TAPPI's Fall Energy Forum. The meeting agenda is as follows: ·
- Monday, November 5 (subcommittee meetings), Noon - 4:30 p.m.
- Tuesday, November 6 (full committee meeting), 8:00 a.m. - 4:30 p.m.
The YDS&R Committee is an active group of Yankee dryer owners/users and service providers focused on reducing delay that causes low productivity and negatively impacts dryer safety and overall business results. The committee's goal is to develop standard practices and visual standards for problems that cause drying system delay and compromise safety across the tissue industry. More information about this committee is available online.
Back To Top
|
Below is the latest listing of job openings in the TAPPI Career Center. The current listing includes job openings for a maintenance planner, chemist, sales engineer, extrusion coating specialist, lab technician, fiber line superintendent, and process control engineer. Current, specific job openings at companies and locations in the TAPPI Career Center include:
Employer |
Title |
Location |
Dept. Chem/Bio Eng, UBC |
Mercer Int. Ind. Res. Chair/Appt. at Assoc./Full Prof. |
Vancouver, B.C. |
Chevron Phillips Chemical |
Extrusion Coating Tech. Service/App. Dev. Spec. |
Oklahoma |
Rayonier |
Maintenance Planner, Mechanical |
Jesup, Ga. |
Rayonier |
Sr. Process Control Engineer |
Jesup, Ga. |
AIRTHERM Corp. |
Sales Engineer |
Longview, Wash. |
Celanese |
Chemist II – Paper Lab |
Florence, N.Y. |
Pactiv |
Principal Engineer/Scientist |
Canandaigua, N.Y. |
Georgia-Pacific. |
Fiber Line Superintendent |
Mississippi |
Albarrie Environmental Services |
Product Marketing Mgr. (Liquid Filtration Media) |
|
Applied Paper Technology |
Lab Technician |
Marietta, Ga. |
Applied Paper Technology |
Assistant Lab Mgr. |
Marietta, Ga. |
Georgia-Pacific |
Process Safety Mgr. |
Brewton, Ala. |
More information about these jobs is available online
Back To Top
|
Market Roundup
India is quickly becoming an attractive new market for the U.S. pulp and paper industry, according to Turning the page on India's paper industry: A new chapter in investment potential and growth, a new report from Deloitte, New York, N.Y., USA. Growth in the Indian market is tied to a significant increase in demand, fueled by a burgeoning middle class and a growing workforce waiting to be added to the worldwide employment rolls.
According to the report, the U.S.-based International Paper (Memphis, Tenn.) acquisition of a 53.5% stake in Andhra Pradesh Paper Mills (APPM) in March 2011 stirred widespread interest in the Indian market. Prior to that, the paper industry in India did not appear to be on the radar of many multinational companies.
"India's paper industry is expected to grow at 6% to 7% year-over-year, with the packaging industry poised to grow at 22% to 25% annually," said John Dixon, principal, Deloitte Consulting. "India has 15% of the world's population, but consumes less than 2% of the world's paper. Meeting the growing demand will likely require a correspondingly significant investment in both new machines and upgrading of existing facilities."
The report analyzes the challenges to investing in India, which include inadequate investment in infrastructure, limitations on raw materials, lack of a coordinated and updated manufacturing policy, outdated labor policies, and lack of a broad power supply that has created a situation where only about 60% of papermaking capacity is being used.
Companies considering entrance into the Indian market should do so strategically and should consider location, the study advises. For example, states such as Andhra Pradesh, Maharashtra, and Gujarat may be preferred locations for consideration because they may be investor friendly and closer to raw materials.
"Paperboard and printing, along with specialty papers, are likely the segments with greater ease of entry and long-term growth," explained Dixon. "Acquisition of or a controlling stake in a joint venture with an existing player with sizable assets can offer an attractive option for entry," added Dixon. "India also allows 100% foreign direct investment (FDI) in this sector, making it an attractive landscape for foreign investment—one of the keys to growing the paper industry."
The full report is available online.
Back To Top
|
China's phenomenal GDP growth of between 9% and 14% annually during the past decade slowed down last year and is forecasted by International Monetary Fund (IMF) to be "only" 8.25% in 2012. Reduced investments in public projects and a cooling residential property market have resulted in a decline in the importation of saw logs during the first six months of 2012, according to the Wood Resource Quarterly (WRQ), Seattle, Wash., USA.
Softwood log imports to China in the first and second quarter this year were 6.2 million cubic meters and 6.6 million cubic meters, respectively, down from the all-time high of 8.6 million cubic meters seen in the 3Q/11, WRQ reports. Total imports for the first half of 2012 were 15% lower than during the same period last year, with the biggest declines occurring in shipments from Russia, the U.S., and Australia. Western Canada is the only major supplier that has increased shipments so far this year. Its annual shipments may reach more than 2.5 million cubic meters, which would be a record high.
The reduced demand for logs in China has not only impacted import volumes, but also prices for domestic and imported logs. The average price for imported softwood logs is down 14% from 2Q/11 to 2Q/12. Prices for New Zealand radiata pine logs dropped the most, while red pine logs from Russia showed the smallest price drops compared with other species of imported softwood logs.
Domestic log prices in China have also fallen over the past year, with Chinese-fir prices being down 6% year-over-year in the 2Q/12, according to the WRQ. Mongolian pine and larch prices were also lower by 8% and 16%, respectively.
Contrary to the recent downward price trend for softwood logs, prices for domestic hardwood logs, including Eucalyptus, birch, and poplar, have gone up this year and were close to or at record-high levels in the 2Q/12.
Much uncertainty surrounds investment activities in the Chinese construction sector, private consumption in the country, and the demand for Chinese forest products in North America and Europe. If the Chinese domestic consumption and private investments improve somewhat in the 2H/12, as IMF forecasts, both softwood and hardwood log prices are likely to stop falling and instead increase slightly in the second half of 2012.
More information is available online.
Back To Top
|
Global pulp demand remains weak and softwood prices remain under pressure, Deutsche Bank analyst Mark Wilde reports. All major North American producers have announced August NBSK (northern bleached softwood kraft) pulp at $850/metric ton, -$30/metric ton m/m, he says. Spot NBSK prices are much lower at ˜$630 - $670/metric ton, 26% below July's list price of $880/metric ton. Softwood inventories remain relatively balanced at 29 days of supply.
Weakness in softwood appears to be spreading to the hardwood grades, Wilde continues, adding that June inventories rose by four days' supply to 40 days. "Spot BHK prices are under pressure," he says. "We expect market pulp prices to be dampened over the next 9 -12 months. Key issues in market pulp include slower demand in China and Europe, a weak euro, and mill startups/restarts."
Back To Top
|
Estimated prices on No. 5, 40-lb offset rolls in the U.S. were down $25/ton to $835 - $875/ton in July, Mark Wilde of Deutsche Bank reports. Domestic demand remains soft (June shipments were -2.2% y/y). However, recent capacity reductions (Verso's 18,000 tpy Sartell PM 3 and Resolute's 150,000 SC machine No.1 at Catawba) will reduce North American coated groundwood capacity by ˜12% and tighten the demand/supply balance. These supply reductions have created some optimism on the $40 - $60/ton price hike announced by most producers for May/June, Wilde notes.
In June, No. 3 60-lb coated free sheet (CFS) prices were flat m/m, for the fifth straight month, at $965 -$985/ton, Wilde says, pointing out that producers failed to implement a $30/ton May price increase. Demand also remains weak, he reports, noting that, according to PPPC, June shipments were down 13.6% y/y. Operating rates were 86%, down from 99% in June 2011. "Globally, one of the biggest issues is the tremendous increase in Asian CFS capacity over the past two to three years," he advises.
Back To Top
|
U.S. uncoated free sheet (UFS) demand is sluggish, Mark Wilde of Deutsche Bank says. June cut-size shipments were -9.7% y/y and offset was -4.0% y/y. A $40/ton cut-size price hike for late-May/early-June and $60/ton on offset grades has not gained much traction, he adds. Producers have been able to implement partial hikes on envelope paper (+$20/ton), MOCR (+$30), and forms bond (+$30). Weak demand in Europe and a weaker euro have raised the risk of more European imports. July 20-lb repro-bond prices were flat at $1,035 - $1,085/ton, and 50-lb offset was flat m/m at $910 - $930/ton.
The uncoated mechanical paper market also remains anemic, Wilde continues. Second quarter shipments were down 15.7% y/y, while 35-lb estimated offset prices slipped $5/ton m/m in July.
Back To Top
|
Pulp & Paper
Alberta Newsprint Co. (ANC) this past week reported that its ownership has approved construction of a power generation plant at its newsprint mill in Whitecourt, Alb., Canada. ANC is a joint venture of West Fraser and Whitecourt Newsprint Co. Partnership.
The approximately 65 MW power plant will produce electricity fueled by natural gas. Electricity generated by the plant will be consumed by ANC and sold into the Alberta power grid.
"ANC is committed to being a competitive, reliable, and long-term supplier of newsprint to our customers," says ANC President Ron Stern. "This significant investment will further enhance our ability to deliver a high-quality product to the market."
ANC is in the final stages of selecting the equipment supplier for the project. It expects to begin construction of the project this fall, with anticipated startup in late 2013. Construction of the power plant will not disrupt newsprint production operations.
The Whitecourt mill produces standard newsprint as well as rotogravure paper for the North American market.
Back To Top
|
Cascades Inc., Kingsey Falls, Que., Canada, reports the permanent closure of its Cascades Tissue Group plant located in Scarborough (McNicoll Street),Toronto. This unit specialized in paper napkins for the away-from-home market, mainly for quick service restaurants. Its production will be redirected to the company's Laval, Que., and Waterford, N.Y., USA, plants, also specialized in that market.
Approximately 30 employees will be affected by the closure, which was effective August 13. This closure does not impact activities at Cascades' Milliken Street plant, also located in Scarborough.
"In line with our restructuring actions to increase our operations' efficiency, this decision was taken to secure our position as leader in the away-from-home tissue paper sector. This initiative will enable us to maximize the production at Laval and Waterford plants, while continuing to offer a first-class product and service to our customers," said Suzanne Blanchet, president and CEO of Cascades Tissue Group.
Cascades noted that it has taken necessary measures to provide support to employees affected by the closure.
Back To Top
|
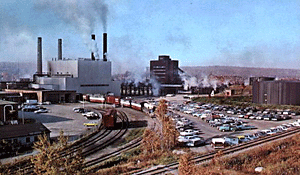 Great Northern Paper Co. reports that it will re-start PM 5 at its East Millinocket, Maine, USA, mill, restoring 37 jobs. No 5, to begin production by the first week of September, will be the second machine operating at the mill since it reopened last October.
The company, owned by Cate Street Capital, Portsmouth, N.H. (purchased from Brookfield Asset Management of Toronto, Ont., Canada in September 2011), is already advertising for experienced pulp and paper workers, President and CEO Richard Cyr told the local Bangor Daily News. Among the positions available are eight salaried management-level posts, four jobs in the wood room, four in the grinding room, three in the warehouse, six maintenance jobs, and 12 positions to staff the paper machine.
When the mill resumed operations last October, PM 5 began producing virgin newsprint, but operations were shifted to PM 6 because it allowed the mill to increase production, and PM 5 was shutdown again, according to Cyr. The restart of PM 5 by early September will add some 12,000 – 14,000 tons of newsprint production to the 150,000 produced by PM 6 in 2012. In 2013, plans are to produce 50,000 tons on PM 5.
The two East Millinocket machines produce a variety of grades from newsprint and telephone directory to book papers.
Brookfield Asset Management had closed Great Northern's nearby Millinocket, Maine mill in 2008, followed by closure of the East Millinocket mill's doors in April 2011. When Cate Street Capital restarted the East Millinocket mill in October 2011, 215 employees were put back to work. Since then, Great Northern has hired an additional 20 workers.
Cate Street Capital's Thermogen Industries subsidiary is planning a wood pellet production facility at the Millinocket mill. Beginning in the summer of 2013, the company plans to produce some 110,000 tpy of wood pellets for sale in Europe, according to the Bangor Daily News report.
Back To Top
|
Hebei Yihuocheng Commodity Co., China, has ordered from Andritz, Graz, Austria, a PrimeLineCOMPACT II tissue machine with a steel Yankee. Startup is scheduled for the end of 2013. The tissue machine will have a design speed of 1,650 m/min and a width of 2.85 m. The steel yankee has a diameter of 3.65 m.
The scope of supply also includes the complete stock preparation plant, automation, and drives. The machine and equipment will be manufactured at Andritz's sites in Europe and China.
Back To Top
|
Kruger Inc., Montréal, Qué., Canada, this week announced that the Woodland Operations at its Corner Brook, N.L., Canada, mill has achieved certification under the Forest Stewardship Council® (FSC) National Boreal Standard. Issued by QMI-SAI Canada Ltd., an FSC-accredited organization, the certificate recognizes that all woodland operations comply with FSC requirements, including management planning, road construction and maintenance, harvesting operations, fiber transportation, silviculture, and support activities.
Kruger's Corner Brook Mill obtained this certification after a rigorous auditing process, building on its existing certifications to the ISO Environmental Management and CSA Sustainable Forest Management Standards. The new certificate covers forest management districts nos. 5, 6, 9, 14, 15, and 16.
In recent years, Kruger has achieved several FSC certifications, including FSC Chain of Custody (CoC) certification for its Québec paper mills and sawmills and for the five Kruger Products tissue mills, as well as FSC certification for its forest management practices in Québec.
Back To Top
|
NewPage Corp., this week filed a Joint Chapter 11 Plan with the U.S. Bankruptcy Court for the District of Delaware. The company also requested an extension of time to file the disclosure statement related to the plan.
"The filing of our plan of reorganization is an important and positive step forward to a successful completion of our financial reorganization," said George F. Martin, president and CEO. "Discussions with and among our major creditor groups regarding the plan are ongoing. We are hopeful that these discussions will lead to broad support for our plan."
The plan is available online
NewPage, a producer of printing and specialty papers with $3.5 billion in 2011 net sales, owns paper mills in Kentucky, Maine, Maryland, Michigan, Minnesota, and Wisconsin. These mills have a total annual production capacity of approximately 3.5 million tons of paper.
Back To Top
|
Catalyst Paper, Richmond, B.C., Canada, and the City of Port Alberni on Vancouver Island, B.C., are moving forward with key strategic initiatives after reaching an agreement-in-principle for the purchase of the company's wastewater treatment facility and additional lands. The agreement, valued at $5.75 million, consists of two parts—acquisition of the 13.4-hectare wastewater treatment facility located across the Alberni Inlet and, secondly, the purchase of 3.9 hectares of land combined with a road dedication (part of the Redford Street extension arrangement) to facilitate the development of an industrial truck route along the waterfront.
"This agreement with Catalyst Paper represents an investment in the long-term prosperity of our community," Mayor John Douglas said. "This sewage treatment facility will become an integral piece of our city's infrastructure, allowing us to meet the strict new federal and provincial wastewater regulations and accommodate the continued growth of the city."
Due to mill upgrades, Catalyst's wastewater treatment facility is no longer required to support operations. The city's acquisition and planned upgrade of the facility will bring it into compliance with new federal environmental regulations at a considerable cost savings compared with building a new facility.
"We are pleased to have reached an agreement that benefits the community of Port Alberni and our company," said Kevin J. Clarke, Catalyst Paper president and CEO. "This initiative allows the city to address a vital infrastructure requirement and it enables our business to focus on core operations as we exit creditor protection in the near term."
With the agreement in place, the city will now finalize and be eligible to draw on the $11.2 million grant provided by the federal government in January to make the necessary renovations and improvements to the lagoons. Once completed, the system will provide increased capacity and improved water quality in the Alberni Harbor and Somass Estuary.
Back To Top
|
Sappi Ltd., South Africa, reportedly has agreed to sell its entire 34% shareholding in the Jiangxi Chenming Paper Co. in Nanchang City, Jiangxi Province, China, for $41.58 million to the Shandong Chenming Paper Holding Co.
In 2004 Sappi became part of a joint venture (JV) with Shandong Chenming and other partners to explore fine paper opportunities in China. A change in strategic focus by Sappi caused this investment to be reviewed and led to discussions with Shandong Chenming, the majority shareholder and co-founding partner of the JV. The parties have been able to reach an amicable agreement that will allow Sappi to concentrate on its strategy of investing in high growth businesses, disposing of non-core assets and reducing its debt.
Sappi CEO Ralph Boettger noted that "our joint venture in China has been of tremendous value to Sappi. We have gained a better understanding of the Chinese market as well as of manufacturing in China. We have built strong relationships with our Chinese partners and look forward to again working with them in the future. Sappi will remain active in China in particular through its release paper and chemical cellulose businesses."
The implementation of the transaction is subject to various Chinese regulatory approvals, which is expected to be achieved before Sappi's financial year end on September 30.
Sappi is a global company focused on producing chemical cellulose (dissolving pulp), paper pulp, and paper based products to its direct and indirect customer base across more than 100 countries
Back To Top
|
As part of the EC clearance requirements for takeover of Georgia Pacific's EMEA tissue business, RISI, Brussels, Belgium, reports that SCA, Stockholm, Sweden, will divest the 55,000 metric tpy Llangynwyd Mill in Bridgend, U.K., the 22,000 metric tpy Drammen mill in Norway, and the tissue converting plant in Horwich, Lancashire, U.K The sites proposed for sale were made public during SCA's recent conference call for its H1 results.
RISI noted that according to Jan Johansson, chief executive, SCA intends to complete the divestments within a six-month timeframe following the G-P deal's closure, as required by the EC.
Back To Top
|
UPM, Finland, reports that it completed the sale of its closed Papierfabrik Albbruck GmbH mill in Germany to the German Karl Group. UPM permanently ceased graphic paper production at the mill situated in Baden-Württemberg this past January.
The Karl Group plans to establish new businesses on the premises of the former paper mill within the next three to five years. "Our aim was to identify development ideas and business opportunities for the site," said Hartmut Wurster, who represented UPM in the negotiations. "The sale to Karl Group opens up new economic perspectives for the whole region."
Meanwhile, more than 200 former paper mill employees have found new jobs supported by the transfer company funded by UPM.
Back To Top
|
Containerboard/Packaging
Corrugated retail ready packaging (RRP) is becoming an increasing necessity for the U.K. food and beverage manufacturing industry, according to a recent survey commissioned by the U.K.-based Confederation of Paper Industries (CPI) Corrugated Sector. As the demand for attractive and environmentally friendly packaging solutions grow, the results from the survey found that corrugated packaging is leading the way as a tool for optimizing the appearance and performance of a variety of branded products.
A poll of 100 companies found that 79% of respondents rated corrugated RRP as their first choice packaging material and 83% agreed with the statement that ‘corrugated RRP helps promote product or brand in-store. Green issues also came to the fore in the survey, which revealed that the majority of those contacted believe that corrugated RRP is either very or extremely helpful in meeting corporate or government targets on environmental issues.
CPI believes that these statistics confirm corrugated cardboard as the complete solution for transit and point of sale packaging, making it the ideal and most sustainable material for fulfilling logistics expectations throughout the food and drinks supply chain.
CPI Director of Packaging Affairs Andy Barnetson said that "protection of goods and cost also score highly in the CPI survey as key advantages for using corrugated packaging. This clearly demonstrates the need for the U.K. Corrugated Industry to remain at the forefront of innovation by continuing to produce sustainable, RRP with quality printing that makes products eye-catching at the point of sale.
"To meet the expectations of the food and drinks industry, the corrugated packaging sector in the U.K. is pioneering packaging solutions that bring increased sustainability to the supply chain as well as investing significantly in new equipment," Barnetson noted.
CPI also pointed out that in addition to its high quality presentational characteristics and the protection corrugated offers for goods in transit, the industry boasts the best packaging recycling record in the country and is proud to use and promote a sustainable and renewable material, more than 80% of which is recycled.
According to CPI, UK's corrugated sector has led the way with packaging that is always ‘rightweight,' not necessarily lightweight. It brings innovative design for shelf ready packaging and space efficiency in trucks, meaning fewer lorries on the road. It has always offered protection without loss of flexibility.
For more information about this survey, email Andy Barnetson.
Back To Top
|
Sichuan F. Source Paper, China, has ordered from Andritz, Graz, Austria, the paper machine approach, a save-all disc filter for fiber recovery, two PrimeFlow headboxes, and a PrimeDry Hard 2 roll calender for its new testliner and corrugated medium machine. Startup is scheduled for next month (September).
With a design speed of 650 m/min and a width of 4.9 m, the new machine will have a production capacity of 150,000 metric tpy. The Andritz headbox is a compact design unit and easy to install, a critical criteria especially for rebuilds. The PrimeCal Hard calender optimizes pre-calendering and final calendering of all paper and board grades.
Back To Top
|
Unisource Worldwide Inc., Norcross, Ga., USA, reports that its Unisource Global Solutions (UGS) division has completed the asset acquisition of Pakit Sweden AB, an international producer of molded fiber packaging. The acquisition includes the purchase of equipment that uses cellulose fibers to produce molded fiber packaging, replacing the use of plastic trays, bottles, containers, carriers, and other conventional petroleum-based packaging. The equipment also uses considerably less energy than current packaging processes and reduces the use of water and emissions, Unisource notes.
"This acquisition builds upon our commitment to be a world leader in providing cutting-edge design, technology, research, manufacturing, and ongoing innovation to the packaging industry," said Al Dragone, CEO of Unisource Worldwide. "It also improves Unisource's capability to be more responsive to our customer needs in the sustainable packaging area."
Gary Miller, president of UGS, noted that "the molded fiber manufacturing equipment we have acquired will expand UGS' production resources to drive the next generation of packaging solutions to meet the industry's growing interest in sustainable packaging on a global basis."
Back To Top
|
New Products
Metsä Tissue, a part of Finland-based Metsä Group, has "renewed" the product range of its Serla brand with new product quality and packaging, referring to improvements in both household towel and toilet paper qualities. The company noted that the Serla household towel is now "softer and more absorbent than before, thanks to both raw material and new embossing."
The Serla brand white toilet paper has also been completely renewed in Finland, Metsä added, with more fresh fiber in the paper and the recycled material has been changed to a whiter grade. "The new toilet paper is softer yet sustainably produced – just as it was before," the company said.
"We wanted to create a new generation Serla to better meet the needs of today's consumers. We have recognized a greater demand for products that are convenient to use and soft—both for the user and the environment. Consumers want high-quality products but do not want to give up their sustainable values. This gave us the direction for New Serla," said Brand Director Mia Ropponen.
"By changing the fiber mix of the product," Ropponen explained, "we were looking for higher quality without compromising our high environment standards. As mobile and digital habits are changing the way we use paper products, recycled fibers are becoming rare and are being shipped longer and longer distances. Therefore fresh fibers can sometimes be the most sustainable option."
In addition to the new household towel, Serla's logo and package design have been updated in all markets. The new package includes an easy-to-open mechanism—the top tears away cleanly while the rest of the package remains intact, keeping the rolls in place. "New packaging design is easy to navigate in the fairly cluttered tissue shelves. Easy opening is a simple but effective novelty that makes your life a little easier," Ropponen noted.
The packaging material has also changed for many Serla products. TrioGreen—made from sugar cane—is a renewable material and is thus ideal for packaging sustainably-produced tissue products.
Back To Top
|
Voith Paper, Germany, has launched NipVision, an online and real-time measurement tool using the latest roll cover technology. It is the first system to measure nip pressure, profile, and the cover temperature while the paper machine is running.
The new tool allows actual conditions in a pressed nip to be analyzed. The NipVision glass fiber sensors are very small, non-aging, flexible, and chemically resistant. They lie inside the cover, so that the roll application and dimensions remain unchanged. The sensors are so sensitive that they can detect the presence of paper in the nip.
NipVision is the only system that can measure temperature within the cover while the paper machine is running. This is a real benefit to the customer, Voith emphasizes, given that a large number of damages result from temperature-related issues. Until now, the source of poor profiles and sheet quality, increased sheet breaks, and sudden roll cover damages have often been linked to a given press nip but, without any proof. With the help of NipVision, such problems can be detected and prevented, the company says.
Information from the sensors is transmitted to a computer that plots the profile across the width of the machine and over time. With specific software, the conditions in the nip are shown simultaneously and synchronously. The system is powered through induction, allowing NipVision to constantly transmit information 24 hr a day, while the paper machine is running.
Back To Top
|
People
Longview Fibre Paper and Packaging, Longview, Wash., USA, has appointed Gary Parafinczuk its new human resources director. Parafinczuk most recently worked as the VP of HR with RockTenn in Norcross, Ga.
"We are pleased that Gary joins Longview, bringing HR executive experience and industry experience in our current product offerings," company President Randy Nebel said. "We look forward to Gary's leadership of our HR Team."
Longview Fibre Paper and Packaging produces lightweight, high-performance multiwall and complementary specialty kraft papers for an established domestic and global customer base. The company also produces containerboard and corrugated boxes. It operates a pulp and paper mill at Longview, Wash., and a network of seven converting plants in the western U.S.
Back To Top
|
TAPPI News

If you manage anyone at your facility, you bear a significant role in maintaining a competitive edge in the industry. Workforce training is a big responsibility, especially facing an ever-changing workforce, emerging technologies and tighter budgets.
Your employees are the backbone of the business and only as viable as their abilities and knowledge. Keep their skills strong this summer.
Happening this month...
August has been a busy month for TAPPI training courses covering almost every facet of the industry for both beginner- and advanced-level employees - and there's more to come this month and during the remainder of the year. These courses provide some of the best instruction on pulping and papermaking processes available anywhere in the world, with curriculum developed by industry professionals having years of experience, credentials, and recognition. Presentations are never "canned" and are specific to the attendees' work.
Click here for a complete list of events in 2012
Remaining August events:
TAPPI courses are better on the budget!
TAPPI offers group discounts where your facility can save on course fees per person by registering three or more employees from the same location. Since 1915, the industry's leaders have turned to TAPPI to train and educate their facility's workforce. Why? Because TAPPI consistently delivers the most highly regarded resources for superior education and training for the pulp, paper, packaging, and converting industry.
Back To Top
|
TAPPI Headquarters in Norcross, Ga., USA, will host the annual Improving Paper Machine Performance Course August 21-23. This course provides students the tools needed to evaluate the performance of their paper machines against industry standards and evaluate ways to improve performance and optimize efficiencies. This year the course schedule has been expanded to include an important area of operation- evaluating energy savings.
Dick Reese of Dick Reese and Associates will help attendees learn how to evaluate energy consumption. Reese has completed energy evaluations on more than 125 paper and pulp machines in 56 mills. Several mills have reduced annual energy cost by $1 million-plus by implementing recommendations from the energy evaluations.
After successfully completing this course, participants should be able to:
- Explain how to establish a paper machine performance audit
- Improve performance and optimize energy conservation and efficiency of your paper machine
- Determine the tools needed to benchmark paper machine operations
- Identify areas of PM performance that are sub-standard.
The educational material has been designed as an intermediate or advanced course for process engineers and mid- to upper-level manufacturing managers. Service technicians, sales personnel, and engineers within the chemical and equipment categories will also benefit by attending this course.
A degree in engineering or other technical field is suggested, but not required. A good working knowledge of the paper machine is recommended (this is not an introductory course). Please bring your laptop computer for this working course. If you don't have one you may share with another course participant.
There is only room for 25 course participants, so please register today.
For more information, please visit the course website.
Early registration, travel, and lodging discounts are available.
Back To Top
|
The TAPPI Extrusion Coating Course, August 27-29, 2012, on the Michigan State University campus, will provide an opportunity for critical technical training and networking that can help you improve your extrusion coating operations and gain a competitive edge. TAPPI is one of the few training centers offering courses in a specialized area such as extrusion coating taught by experts who have worked in the industry.
The slate of instructors scheduled to lead the sessions for the course represent decades of experience and leadership. With their guidance, you'll be able to explore the best practices and equipment technologies that apply to extrusion coating applications. Attending this course is the next logical step in your efforts to more effectively troubleshoot and increase your productivity. The course offers face-to-face opportunities to accelerate learning at a faster rate than you can get by using online learning, reference books, or manuals alone.
Register now for this not-to-miss opportunity!
Back To Top
|
A message from the leadership of the TAPPI Biomass Supply, Demand, and Handling Subcommittee
Regardless of the cellulosic biorefinery platform, the success of all cellulosic biorefineries will be dependent on a steady and sustainable supply of, and reasonable cost for, well cleaned, cellulosic biomass delivered to the biorefinery.
The TAPPI Biomass Supply, Demand & Handling Subcommittee was formed in early 2011 to focus on various aspects of the biomass supply chain. The intent of this subcommittee is to provide a venue for interested parties to have a free exchange of state-of-the-art technical ideas on these important topics.
We have identified a few subcommittee projects, and are looking for volunteers to join the subcommittee and assist in working on these or other projects. If you are interested in joining this subcommittee, please contact Mary Ann Cauthen ( mcauthen@TAPPI.org) at TAPPI.
Biomass Supply Short Course - This course would address issues in cost-effective delivery and preparation of biomass materials (wood and non-wood). Bob Hurter, Bill Fuller, and Desmond Smith are currently working on educational outcomes and identifying speakers.
Standards for Biomass Sampling and Testing Methods - We are looking for one or two individuals to head up this area, plus others who can contribute. This group would first work to identify needs and evaluate gaps between existing standards and identified needs. A survey of needs has been suggested as a first step. If you are interested in this area, or know someone who would be, please encourage them to contact Mary Anne Cauthen ( mcauthen@TAPPI.org) and 1) join this subcommittee if not currently a member, and 2) indicate interest to work on this project.
LinkedIn Group - We are also investigating the use of a TAPPI LinkedIn group for biomass supply, demand, and handling issues. If you are interested in helping on this project, please let Mary Ann Cauthen ( mcauthen@TAPPI.org) know.
September 19 Subcommittee Webinar - We are scheduling a webinar to update the subcommittee on efforts in these areas. Please plan to attend on Wednesday, September 19, from 1:00-2:00 p.m.
Subcommittee Chair - Bob Hurter, HurterConsult
Subcommittee Co-Chair - Bill Fuller, FRM Consulting
Back To Top
|
TAPPI will be performing its fiscal year end inventory counting starting August 30. As a result, TAPPI will not be processing TAPPI Press orders from August 30 - September 4. Orders received during this time will be shipped in the order in which they have been received starting on September 5. All normal payment processing will resume on September 5.
We apologize in advance for any inconvenience and thank you for your patience. This allows us to better serve our members.
Back To Top
|
Join us on Tuesday, August 28, at the Grand View Lodge, Preserve Course, in Pequot Lakes, Minn. A morning shotgun scramble golf outing is planned with lunch to follow.
Please remember, your participation will help fund scholarships for Lakes States TAPPI/North Central PIMA's Scholarship programs. Prizes will be awarded along with a putting contest and a raffle.
Reservation preference will be given to foursomes. Groups of two or less will be placed into foursomes pending availability. We will limit the number of participants to 128.
Entries will only be accepted with full payment. For entries received after August 16, the cost is $135.00 per person. Check-in registration will begin at 8:00 am.
If you have any questions about this event, please contact: Wfrawley@new.rr.com
Full event information and registration details are available online.
Back To Top
|
Join Worldwide Coating Experts at the
Advanced Coating Fundamentals Symposium
The paper coating community will be converging in Atlanta, Ga., USA, Sept. 10-12, 2012, for TAPPI's 12th Advanced Coating Fundamentals Symposium. This biennial event attracts the world's foremost experts in coating technology and is the preeminent symposium for leading-edge research.
Your next opportunity will not come until 2014!
As a special added bonus and for your convenience, the Advanced Coating Fundamentals Symposium (ACFS) will be co-located with the 16th International Coating Science and Technology Symposium (ISCST) providing you with insights into coating research in non-paper applications. Your TAPPI registration will allow you extended access in to any of the ISCST presentations. It will also include full printed proceedings of the TAPPI program.
The ACFS Technical Program will focus on what it takes to commercialize an innovation -- and includes more than 20 peer-reviewed papers covering novel paper coatings, mechanics of printing, new and emerging technologies, and nanotechnology in paper coating.
In addition to learning about all of the latest developments, your registration includes an evening of fun and fellowship with coating colleagues from around the world at the Advanced Coating Fundamentals dinner, scheduled at a distinctive Atlanta venue.
Click here to view the program.
Click to learn more about ACFS 2012.
Back To Top
|
Every mill is capable of improving its reliability and maintenance practices. This is a critical function in mill operation that affects the bottom line. Training to keep up with changing technology and new procedures is absolutely essential for maintaining profitability and productivity.
The 2012 Preventive Maintenance and Essential Care & Condition Monitoring Course
shows participants how to set up a cost-effective process and provide practical exercises and techniques. This training takes place September 12-13, 2012, in Raleigh, N.C., USA.
IDCON's Root Cause Problem Elimination Seminar focuses on eradicating problems. You will learn how to tie cause and effect together while applying logical thought processes to arrive at the problem's core.
You stand to benefit from this training if you:
- Plan preventive maintenance work
- Execute preventive maintenance tasks (operations and maintenance)
- Manage preventive maintenance
- Work with reliability improvements
- Manage and/or supervise maintenance personnel
- Work with a computerized maintenance management system
- Work as a maintenance or reliability engineer
- Coordinate PM tasks between E/I, mechanical and operations
- Manage operator essential care and inspections.
TAPPI and IDCON are pleased to partner for this course so that you and your maintenance teams can get expert advice from the industry's leaders in reliability and maintenance.
Click Here to Register.
Remember, seats will fill quickly for this essential training program!
Back To Top
|
The Gulf Coat TAPPI Local Secton announced that its Fall 2012 Meeting topic will be "New Boiler Mact Rule Considerations." The meeting will be held at the KBR offices in Birmingham, Ala., USA, on Thursday, September 27, 2012.
Please mark your calendar and advise others who may have an interest in this subject.
The program is currently being assembled, and meeting details will follow as soon as they are completed. We expect 10-12 presentations covering this topic.
If you wish to participate in this program, please contact Jeff Smith via email at jeff.smith@btg.com.
Back To Top
|
You're invited to the 7th Annual Pacific Section Golf Tournament! This event will be held on September 28, 2012 (Friday). Start time is 1:00 p.m. at the Lewis River Golf Course.
The tournament format is a Modified Shotgun Start, four-person scramble with 144 spots open - First Come/First Serve. The entry fee is $125/person, which includes green fees, cart, two beverage tickets, prizes, a meal afterwards, and most of all... lots of fun!
Awards: 1st Place Team, 2nd Place Team, 3rd Place Team, M/W Longest Drive, KP, Longest Putt. Also enjoy door prizes and a raffle!
Proceeds go to the Pacific Section TAPPI scholarship fund!
Questions? Contact Vince Hochanadel via phone (360) 901-1680 or via email: vince.hochanadel@gmail.com.
Additional details and the registration form can be found here on the TAPPI website.
Back To Top
|
Learn with expert guidance from instructors with decades of leadership in business operations specifically in the pulp and paper industry.
The Financial and Strategic Analysis Workshop for Pulp & Paper and Related Industries is designed to teach important business skills for the challenges mills are facing today. This workshop is scheduled for October 3-5, 2012 in Raleigh, N.C., USA.
You'll also learn how to market your ideas, products, and services with sound financial backing.
North Carolina State University and TAPPI have partnered to offer basic as well as sophisticated tools to help you analyze and manage important financial information with more confidence. This workshop will help you:
- Understand the crtical role of reinvesting in pulp and paper mill assets to ensure long term survival and prosperity
- Learn the basics of capital budgeting, cost of capital (cost of debt and cost of equity) and financial indicators to allow you to use these tools to build financial analyses and sell your ideas, products, and serives
- Understand the importance of cost structure and how you can increase your competitive advantage by managing your costs
- Appreciate, in financial terms, the impact of your operation, research, new technique or new product
- Build an entire financial analysis from the ground up
- Learn the basis for strategic planning and decision-making.
Learn more about the instructors and curriculum.
Back To Top
|
Are you someone who could benefit from an overview of the entire pulping and paper-making process?
If so, The 2012 TAPPI Hands-On Workshop for Pulp and Paper Basics might be the perfect course for you to learn about the fundamental processes and operations of the pulping and paper-making industry. This year's workshop runs from October 1-5 at North Carolina State University in Raleigh, North Carolina, USA. Reserve your place now so that you can:
- Find out how different processes affect paper properties
- Perform hands-on laboratory experiments to support your understanding of the process
- Run a pilot plant paper machine
- Solidify your knowledge from close interaction with professors in small, interactive groups
Be among the first 32 people to register for this five-day workshop, and you will gain an invaluable overview of pulping, bleaching, chemical recovery, recycling, paper-making and converting. You'll receive course notes, an accompanying CD-ROM, and your own polo shirt. You will also have the opportunity to earn 3.7 CEUs.
This workshop is ideal for new process engineers, manufacturing operators and technicians, sales and service personnel, machine operators, and maintenance personnel. Everyone who wants a better understanding of the basic operation of the pulp and paper business will benefit from this course.
This course typically fills quickly, so don't wait long.
We look forward to seeing you in Raleigh this October!
Back To Top
|
The NCSU Financial and Strategic Analysis Workshop, October 3-5, 2012, Raleigh, N.C., USA
You will learn basic and sophisticated tools to analyze business operations, estimate financial outcomes, and support decision making. In this workshop, you will also discover how to:
- Understand the critical role of reinvesting in pulp and paper mill assets to ensure long term survival and prosperity
- Study basics of capital budgeting, cost of capital (cost of debt and cost of equity), and financial indicators to allow you to use these tools to build financial analyses and sell your ideas, products and services
- Appreciate the importance of cost structure and how you can increase your competitive advantage by managing your costs
- Explain in financial terms the impact of your operation, research, new technique, or new product
- Build an entire financial analysis from scratch with the assistance of recognized Business Operation Instructors with decades of experience in business operations in the pulp and paper industry
- Learn the basis for strategic planning and decision-making.
Who Should Attend?
This workshop is especially beneficial for:
- Managers at pulp and paper mills and business units responsible for strategic planning
- Engineering consultants who provide strategic studies to pulp and paper mill clients
- Sales and service personnel who want to sell their ideas to customers and upper level management
- Superintendents and engineers who want to understand how to measure profitability and costs in their operations
- Managers who want to understand the financial outcomes of process improvements and capital projects
- Research and development engineers and scientists looking to calculate the potential financial impact of their research
- Engineers who are new to the pulp, paper and related industries Register today to apply your new skills in business and financial analysis and take your job performance to the next level.
Register today to apply your new skills in business and financial analysis and take your job performance to the next level.
Back To Top
|
Pulp and Paper mills often find themselves spending millions of dollars inspecting, repairing, and recovering from unexpected leaks in their boiler tubes, tanks, pressure vessels, exposed and buried pipeline, stacks, bleach towers, etc...
Here's your chance to learn how to substantially reduce these costs! Corrosion probe Inc.'s FEMOS Workshop training shows maintenance staff how to rationally manage the mechanical (containment) intregrity of all types of fixed eqpment with a simple, rigorous system utilizing disciplines and procedures by vendors who specialize in the maintenance of rotating equipment.
What do you gain from attending?
This workshop to be held October 14, 2012, 8 am - 5 pm EDT in Savannah, Ga., USA, will teach attendees how to implement a mill-specific program by using a transparent and disciplined process to systematically design the right inspection plan for each major piece of fixed equipment based on its' materials of construction, present condition, and service conditions. The basic concept employs proven, high-value practices from refining and petrochemical industries for risk based inspection, customizing inspection plans to possible damage mechanism and using fitness-for-service engineering assessments to define damage limits.
Who is leading the workshop?
Corrosion Probe Inc.'s workshop will employ experienced and renowned TAPPI participants Dave Bennett, David Browe, and Doug Sherman. They will train up to 20 people in a 1-day (6-Hour) workshop. Training is presented so attendees can use their new knowledge to immediately implement FEMOS at their mill. Many working examples are provided and students are invited to bring their mill's costliest fixed equipment inspection and maintenance concerns for case analysis.
The FEMOS workshop takes place just before the 2012 TAPPI PEERS Conference and the 2012 IBBC conference. Those attending the FEMOS Workshop can also attend these important events.
Back To Top
|
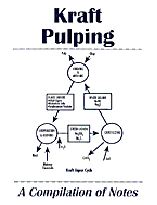
Edited by: A. Mimms, M.J. Kocurek, J.A. Pyatte, and E.E. Wright
Liberally illustrated with over 130 diagrams and photographs, this book includes basic formulas and diagrams to explain the structure of wood, variables affecting the quality and handling of wood chips, pulping chemistry and equipment, the pulping process, and black liquor recovery. Includes a glossary of frequently used terms.
View the Table of Contents.
Preview Sample Pages.
Product Code: 0101R171
TAPPI Member Price: $58.00
Non-Member Price: $87.00
Back To Top
|
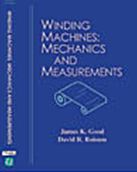
Winding Machines: Mechanics and Measurements
By: Dr. David Roisum and Dr. J.K. Good
Winding Machines: Mechanics and Measurements is the definitive book on the science of winding written by noted experts Dr. David Roisum and Dr. J.K. Good. This three-part book (with supplemental CD-ROM) describes the various classes and arrangements of winding machinery commonly found in the web industries, including a discussion of controls and defects, how roll stresses and roll defects can be predicted by mathematical models and what factors are important, and almost every method for measuring and evaluating wound roll quality.
The book describes how and why many wound roll defects occur. In more than a few cases, it even describes when defects occur based on winding models that have matured to the point of trustworthy application. In these cases, we have science at its best, a predictive tool. A CD with an easy-to-run winding model is included with every book.
However, one need not be a scientist to appreciate and use this text. Much of it is written in everyday language describing the machines we work with, the defects we see, and the many measures of roll quality. It is a book that most plants with a winding department would want to have.
View the Table of Contents
Preview Pages
Product code: 0102B068
TAPPI Member Price: $154.00
Non-member Price: $229.00
Back To Top
|
The 2012 TAPPI PEERS Conference, October 14-17 in Savannah, Ga., USA, has announced a detailed technical program. Five programming tracks of peer-reviewed sessions, Pulping, Engineering, Environmental, Recycling, and Sustainability, will answer the most pressing business and technical questions faced by pulp and paper companies as they manage raw materials, assets, regulatory requirements, and production assets.
Register now and save.
In addition to the in-depth, peer-reviewed technical program, Keynote Speaker Don Roberts, vice chairman of CIBC World Markets, will present " A Whirlwind Tour of Investment Trends and Issues in the Global Bio-Energy Space." PEERS will also offer exclusive networking opportunities and insight into new technologies that can help you optimize your mill operations.
The TAPPI PEERS Conference will be co-located with the International Bioenergy and Bioproducts Conference, creating a value-added opportunity for you to expand your learning, networking, and resources by attending both events. See you in Savannah!
Back To Top
|
Operating Excellence (OpEx) Maintenance and Reliability Seminar at PEERS
This is a first-time program for the 2012 TAPPI PEERS Conference.
Maintenance and reliability continue to be critical to the efficient operation of pulp and paper mills worldwide, just behind fiber and labor as top production cost factors.
This one-day seminar explores the latest reliability strategies today's mills are implementing to stay in-tune and competitive under progressively lean operating conditions.
The OpEx Maintenance and Reliability Track, included in your PEERS registration at no extra cost, is part of the Engineering Program.
If you are only interested in attending the OpEx Track, select the Single Day PEERS Registration for Thursday, October 18. This year's PEERS Conference includes a full program of educational opportunities for maintenance and reliability personnel, including:
- Sunday, Oct. 14: Fixed Equipment Maintenance Optimization System Course (Additional Fee)
- Monday, Oct. 15 - Wednesday, Oct. 17: Corrosion & Materials Engineering Track
- Thursday, Oct. 18: OpEx Maintenance and Reliability Track.
In addition, 2012 TAPPI PEERS Conference, October 14-17 in Savannah, Ga., features a detailed technical program. Five programming tracks of peer-reviewed sessions, Pulping, Engineering, Environmental, Recycling and Sustainability, will answer the most pressing business and technical questions faced by pulp and paper companies as they manage raw materials, assets, regulatory requirements and production assets.
Register now and save.
The 2012 TAPPI PEERS Conference will be co-located with the 2012 International Bioenergy and Bioproducts Conference, creating a value-added opportunity for you to expand your learning, networking, and resources by attending both events.
See you in Savannah!
Back To Top
|
On Nov. 7-9, 2012, TAPPI will conduct its Tissue Runnability Course in Neenah, Wi., USA.
This special course is being taught by technical experts in each area of the machine from wet end operations through creping and process control. The experienced, highly qualified faculty for this course will provide a thorough understanding of the entire tissue making process and current best practices in each area.
Wednesday's (November 7) classes will focus on stock preparation and wet end operations, while Tuesday's (November 8) classes cover pressing, drying, and doctoring. Wednesday (November 9) classes examine technologies and latest developments in hoods, TAD (through-air drying), and other dynamics of the tissue machine dry end,
The 2012 TAPPI Tissue Runnability Course is designed for process engineers, machine supervisors, and reliability professionals who have to maximize uptime and saleable production. It is also an excellent tutorial for suppliers who support tissue making customers. It will help attendees:
- Improve tissue quality and consistency
- Understand contributors to waste and downtime
- Learn reliability and maintenance best practices
- Diagnose and troubleshoot problems quickly.
After successfully completing this course, attendees will specifically be able to:
- Diagnose the impact of recycled furnishes on tissue properties
- Make changes to wet-end chemistry to improve machine operations
- Improve cleaning and conditioning of fabrics
- Troubleshoot runnability problems in the press, Yankee, and creping systems
- Identify improvement opportunities on the dry end
- Pinpoint productivity opportunities in Yankee steam, coating, and hood systems.
TAPPI will award CEU credits to participants who attend at least 80% of the educational sessions and complete a final program evaluation.
The 2012 Tissue Runnabilitry Course includes advanced process instruction. If you are looking for an introductory-intermediate tissue course, consider the upcoming 2012 Tissue Properties and Manufacturing Course at TAPPI Headquarters in Norcross, Ga., USA, on August 15-16.
Attendance for the 2012 TAPPI Tissue Runnability Course is limited, so please register today at the course website.
Back To Top
|

Named a TAPPI Fellow in 1985, member Michael Kocurek, Ph.D., has been an extremely active participant in TAPPI for nearly 50 amazing years. In 1992, that dedication was recognized with TAPPI's Distinguished Service Award, the second highest honor bestowed on members.
Recently retired as a professor and former head of North Carolina State University's Department of Wood and Paper Science, Dr. Kocurek spent his entire career dedicated to the P&P industry, educating its future ranks and preparing them to serve as the next generation of leaders. Still actively involved in TAPPI, he continues to teach some of TAPPI's perennially favored courses, including Introduction to Pulp and Paper, which he has been doing continuously since 1974, Introduction to Kraft Pulping and Bleaching, Linerboard and Medium Manufacturing, and Tissue Properties and Manufacturing . Find out more by reading this month's Member Spotlight.
Spotlight participants are recommended by fellow members and staff. If you would like to nominate a member just send name (or names) to MemberSpotlight@tappi.org. We will forward a Spotlight Questionnaire to fill out and return.
We look forward to seeing you in the Spotlight!
Back To Top
|
|
|
TAPPI Over the Wire | 15 Technology Pkwy. S. | Norcross, GA 30092 USA | Voice: 770.446.1400 | Fax: 770.446.6947
|
 |