 |
|
Weekly Spotlight
The two companies had applied for grant support under the EU's NER 300 program, but the joint project was not among those recently approved for funding
Learn More...
|
Nearly 90 golfers enjoyed perfect weather on August 14 in DePere, Wis., USA, as Lake States TAPPI/North Central PIMA hosted their first of two annual golf outings
Learn More...
|
TAPPI's Board of Directors, Norcross, Ga., USA, this week approved the creation of two new student chapters—at Christian Brothers University in Memphis, Tenn., and Washington State University in Pullman, Wash.
Learn More...
|
NewPage Corp., Miamisburg, Ohio, USA, this week announced that it has teamed with L.L.Bean and the Wisconsin Woodland Owners Assn. (WWOA) to increase sustainably managed woodlands in six Central Wisconsin counties
Learn More...
|
Below is the latest listing of job openings in the TAPPI Career Center.
Learn More...
|
Market Roundup
Total U.S. boxboard production in July decreased by 4.1% compared with July 2011
Learn More...
|
July U.S. coated recycled board (CRB) estimated prices were flat m/m at $890-$910/ton after a $20/ton decline in June
Learn More...
|
Containerboard production in the U.S. rose 2.3% over June 2012, but fell 2.2% compared with the same month last year
Learn More...
|
Total kraft paper shipments in July were 138,000 tons, an increase of 3% compared with June 2012
Learn More...
|
U.S. producers implemented the $50/ton extensible sack kraft increase in July
Learn More...
|
In July, 30-lb newsprint East (North America) was flat at $640/metric ton
Learn More...
|
The difficult operating environment for the Finnish paper industry in the first quarter of this year continued in the second quarter
Learn More...
|
Pulp & Paper
Asia Pulp & Paper group (APP), Jakarta, Indonesia, reports that by 2015 it will source 100% of its pulpwood from plantations (tree farms), as part of its recently-launched Sustainability Roadmap for 2020 and beyond
Learn More...
|
Catalyst Paper, Richmond, B.C., Canada, this past week reached agreement with Pacifica Deep Sea Terminals Inc. on the sale of its Elk Falls site in Campbell River, Vancouver Island, B.C.
Learn More...
|
Kruger Inc., Montréal, Qué., Canada, this week announced that active and retired unionized employees at its Corner Brook Pulp and Paper mill, Corner Brook, N.L., Canada, have approved the proposal to apply funding relief measures to their pension plan's deficit
Learn More...
|
The Canadian Province of Nova Scotia this week announced a financial commitment to support the sale of the former NewPage Port Hawkesbury mill to Pacific West Commercial Corp., reportedly bringing more than 1,400 jobs and more than $11 million in annual revenue to the province
Learn More...
|
JK Paper Ltd., India, a producer of branded photo copier and cut-sized office papers, has ordered from Metso, Finland, the supply and startup of a Metso Paper Lab for automatic testing of paper properties at its Rayagada paper mill
Learn More...
|
UPM, Finland, reports that it completed the sale of its closed Papierfabrik Albbruck GmbH mill in Germany to the German Karl Group
Learn More...
|
Wausau Paper, Mosinee, Wis., USA, this week announced the certification of its coated products Manufacturing and Distribution Quality Management (MDQM) system to ISO 9001 :2008
Learn More...
|
Containerboard/Packaging
The packaging industry in Thailand registered strong growth during 2007–2011
Learn More...
|
In August, domestic OCC has dropped $20/ton to $97/ton (-$82/ton y/y)
Learn More...
|
International Paper Co., Memphis, Tenn., USA, is reportedly five months into planning to refurbish its Bogalusa, La., containerboard mill's wastewater treatment plant
Learn More...
|
|
New Products
Voith Paper, Germany, has launched NipVision, an online and real-time measurement tool using the latest roll cover technology
Learn More...
|
Energy
SCA, Stockholm, Sweden, reports that its Bollsta sawmill in the Bollstabruk, Kramfors municipality in the county of Västernorrland Sweden, has increased its capacity to produce bioenergy
Learn More...
|
People
Norske Skog, Norway, this week reported that its corporate management will be reduced from seven to three members, effective September 1
Learn More...
|
Xerium Technologies, Raleigh, N.C., USA, has appointed Harold C. Bevis its new CEO, president, and director
Learn More...
|
Travels with Larry
This past May, I visited APRIL's Rizhao pulp mill in China. This report explores the mill's history, production systems, capacity, and environmental performance, as well as APRIL's future plans globally.
Learn More...
|
TAPPI News
The U.S.Forest Service Forest Products Laboratory (FPL) celebrated the opening of its one- of-a-kind nanocellulose pilot plant in Madison, Wis., USA, late last month. TAPPI President and CEO Larry N. Montague joined industry representatives and dignitaries to celebrate the event.
Learn More...
|
The TAPPI Extrusion Coating course, to be held August 27-29 on the Michigan State University campus, provides an opportunity for critical technical training and networking that can help improve your extrusion coating operations and allow you to gain a competitive edge.
Learn More...
|
Inventory Count from August 30 - September 4 means TAPPI Press will not be processing orders until September 5. Orders received during this time will ship in the order they have been received starting on September 5.
Learn More...
|
Join us on Tuesday, August 28, at the Grand View Lodge, Preserve Course, in Pequot Lakes, Minn., USA.
Learn More...
|
The paper coating community will be converging in Atlanta, Ga., USA, Sept.10-12, 2012, for the 12th TAPPI ACFS. This biennial event attracts the world's foremost experts in coating technology, and is the preeminent symposium for leading-edge research. .
Learn More...
|
The TAPPI Biomass Supply, Demand, and Handling Subcommittee, formed in early 2011, is looking for volunteers to join and assist in working on various projects. A September 19 webinar is scheduled to update the subcommittee on efforts in these areas.
Learn More...
|
The 2012 Preventive Maintenance and Essential Care & Condition Monitoring Course shows participants how to set up a cost-effective process and provide practical exercises and techniques. This training takes place Sept. 12-13, 2012, in Raleigh, N.C., USA.
Learn More...
|
This sporting clay shoot event in Navarino, Wis., USA, is designed to help relieve work related stress through a series of team building activities, culminating in an evening of social interaction. It will get underway at 11:30 a.m. on Tuesday, September 25.
Learn More...
|
The Boiler MACT program is currently being assembled for this meeting, to be held at KBR Offices in Birmingham, Ala., USA, on September 27. More meeting detail will follow when completed.
Learn More...
|
This year's golf tournament proceeds go to the Pacific Section TAPPI scholarship fund. Come enjoy a day of fun that features all you need for your game as well as awards, prizes, and a meal afterwards. Event will be held on September 28.
Learn More...
|
New edition, expanded to include defects from processes that did not exist when the first edition was written 15 years ago, is a "must have" communications tool for suppliers and their customers to assist in the identification and elimination of roll and web defects.
Learn More...
|
Learn how at the Financial and Strategic Analysis Workshop for Pulp and Paper and Related Industries to be held Oct. 3-5, 2012, in Raleigh, N.C., USA.
Learn More...
|
Special workshop at North Carolina State University focuses on the fundamental processes and operations of today's pulp and paper mills producing a variety of paper and paperboard products.
Learn More...
|
TAPPI is partnering with North Carolina State University to present an imperative workshop for today's economic climate - the NCSU Financial and Strategic Analysis Workshop, October 3-5.
Learn More...
|
Don't miss out on your chance to attend the Fixed Equipment Maintenance Optimization System Workshop (FEMOS) - Sunday, October 14th 2012; 8:00am to 5:00pm EDT in Savannah, Georgia, USA. . This workshop teaches maintenance staff how to manage the mechanical integrity of all fixed equipment.
Learn More...
|
TAPPI members save $75 off the list price for this definitive text on the science of winding written by noted experts Dr. David Roisum and Dr. J.K. Good. This three-part book includes a supplemental CD-ROM.
Learn More...
|
Sessions in Pulping, Engineering, Environmental, Recycling, and Sustainability focus on building a sustainable future.
Learn More...
|
A first-time, unique program for the TAPPI PEERS Conference, this one-day seminar explores the latest reliability strategies today's mills are implementing to stay in-tune and competitive under progressively lean operating conditions. October 14,15,18, 2012.
Learn More...
|
On Wednesday, Thursday, and Friday, Nov. 7-9, 2012, TAPPI will conduct its Tissue Runnability Course at Neenah, Wis., USA., with a faculty of technical experts in each area of the machine from wet end operations through creping and process control.
Learn More...
|
Authors are encouraged to include the PaperCon 2013 "Innovation Generation" theme in their papers or posters. Event will include the Tissue 360 Forum, NETInc Conference, RPTA P-T Seminar, and OpEx Reliability Workshop.
Learn More...
|
Dr. Kocurek has been involved with TAPPI for nearly 50 years. A TAPPI Fellow and winner of the 1992 TAPPI Distinguished Service Award, he is recently retired from his time as head of NCSU's Dept. of Wood and Paper Science, but is still actively involved at TAPPI.
Learn More...
|
|
Find us on Facebook
Network with us on LinkedIn
Follow us on Twitter
|
Weekly Spotlight
Finland-based Stora Enso and Neste Oil will not go forward with plans to build a biodiesel plant. The two companies had applied for grant support under the EU's NER 300 program, but the joint project was not among those recently approved for funding.
"We have calculated the cost of the project very carefully and realistically. It would have represented a very significant investment and we concluded that we would not have gone ahead in any case, even if we had won public funding," according to Neste Oil President and CEO Matti Lievonen and Stora Enso CEO Jouko Karvinen.
The trials carried out by Neste Oil and Stora Enso at a pilot plant in Varkaus, Finland, between 2009 and 2011 on the entire chain needed for the planned plant—from wood biomass to biowax suitable for use as a raw material for producing renewable diesel—proved very successful, the two companies reported.
"Technically speaking, our work was a great success and we are very satisfied with what we achieved. Cooperation between the two companies has also been very smooth and will continue in the future in the area of other bio-based products," Lievonen and Karvinen noted.
Stora Enso has an annual production capacity of 4.9 million metric tons of chemical pulp, 11.8 million metric tons of paper and board, 1.3 billion sq. meters of corrugated packaging, and 6.0 million cubic meters of sawn wood products, including 3.1 million cubic meters of value-added products. The company had sales in 2011 of some EUR 11.0 billion, and it employs about 30,000 people worldwide.
Neste Oil is a refining and marketing company, with a production focus on premium-quality, lower-emission traffic fuels. The company produces a range of major petroleum products and is a global producer of renewable diesel. It had net sales of EUR 15.4 billion in 2011 and employs around 5,000 people.
Back To Top
|
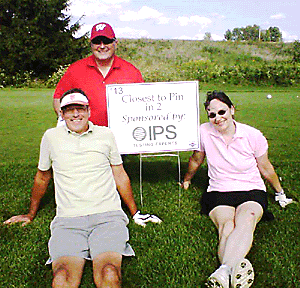 Nearly 90 golfers enjoyed perfect weather on August 14 in DePere, Wis., USA, as Lake States TAPPI/North Central PIMA hosted their first of two annual golf outings. The proceeds go to support pulp and paper industry scholarships in the area. The next outing is August 28 in Pequot Lakes, Minn. (see item in TAPPI News section below). Lake States is also planning the Thirteenth Annual "Guns of Navarino" fall clay shoot on September 25 in Navarino, Wis. See the TAPPI Event Calendar for more details.
In the photo at right are (clockwise from upper left): TAPPI members Bruce Shafer, Integrated Paper Services; Sandra Lenz, Appleton Coated; and Steve Veith, Integrated Paper Services, ready to tee off on IPS's sponsored hole.
Back To Top
|
TAPPI's Board of Directors, Norcross, Ga., USA, this week approved the creation of two new student chapters—at Christian Brothers University in Memphis, Tenn., and Washington State University in Pullman, Wash. Robert Hammond, chair of TAPPI's PLACE Division noted that "traditionally, the TAPPI Chapters have only been at paper schools. This represents a significant step for TAPPI in reaching out to all sectors of the packaging industry."
Christian Brothers University's packaging program was started in 2001 as a certificate program and now offers two new packaging programs: a BS degree in engineering management (packaging concentration) and a MS degree in engineering management (packaging concentration). Siripong Malasri, Ph.D., P.E., chair of the packaging program, said that "having a TAPPI Student Chapter will galvanize our packaging students. The packaging department at CBU became official on June 1, even though we have had packaging programs for many years. Recently CBU packaging has moved forward significantly with its ISTA certified packaging lab (2009) and healthcare packaging consortium (2010). We are now in the position to grow our packaging enrollment."
Washington State's packaging program is a graduate program within the Department of Biological Systems Engineering focused primarily on food packaging. A contingent from Washington State attended the PLACE Conference this year and won the student poster competition. The team's design entry was called "boteFlex™." The novel packaging design is an expandable or collapsible bottle designed to contain value-added food powders.
Back To Top
|
NewPage Corp., Miamisburg, Ohio, USA, this week announced that it has teamed with L.L.Bean and the Wisconsin Woodland Owners Assn. (WWOA) to increase sustainably managed woodlands in six Central Wisconsin counties. The project partners will provide forest management assistance and third-party certification using certification standards of the American Tree Farm System to woodland owners at no cost.
The initial pilot program is targeted at WWOA-member woodland owners in the Central Sands Chapter, which includes Wood, Portage, Waushara, Adams, Juneau, and Marquette counties. To date, 42 landowners owning more than 6,000 acres of forest have committed to the program.
According to Brian Kozlowski, director of sustainable development at NewPage, "This groundbreaking project reflects a shared commitment to forest stewardship. At the same time, it helps increase the availability of locally certified wood to support the growing demand from our customers, including L.L.Bean, seeking paper sourced from certified timberlands."
In 2011, 48% of the fiber purchased by NewPage came from certified sources. NewPage is the largest buyer of pulpwood in the Great Lake States. This program is designed to increase the level of certification and provide forest management resources to WWOA members.
Back To Top
|
Below is the latest listing of job openings in the TAPPI Career Center. The current listing includes job openings for a maintenance planner, chemist, sales engineer, extrusion coating specialist, lab technician, fiber line superintendent, and process control engineer. Current, specific job openings at companies and locations in the TAPPI Career Center include:
Employer |
Title |
Location |
Dept. Chem/Bio Eng, UBC |
Mercer Int. Ind. Res. Chair/Appt. at Assoc./Full Prof. |
Vancouver, B.C. |
Chevron Phillips Chemical |
Extrusion Coating Tech. Service/App. Dev. Spec. |
Oklahoma |
Rayonier |
Maintenance Planner, Mechanical |
Jesup, Ga. |
Rayonier |
Sr. Process Control Engineer |
Jesup, Ga. |
AIRTHERM Corp. |
Sales Engineer |
Longview, Wash. |
Celanese |
Chemist II – Paper Lab |
Florence, N.Y. |
Pactiv |
Principal Engineer/Scientist |
Canandaigua, N.Y. |
Georgia-Pacific. |
Fiber Line Superintendent |
Mississippi |
Albarrie Environmental Services |
Product Marketing Mgr. (Liquid Filtration Media) |
|
Applied Paper Technology |
Lab Technician |
Marietta, Ga. |
Applied Paper Technology |
Assistant Lab Mgr. |
Marietta, Ga. |
Georgia-Pacific |
Process Safety Mgr. |
Brewton, Ala. |
More information about these jobs is available online
Back To Top
|
Market Roundup
Total U.S. boxboard production in July decreased by 4.1% compared with July 2011, and decreased 0.4% from last month, according to the AF&PA (Washington, D.C., USA) July 2012 U.S. Paperboard Report released this week. Unbleached kraft folding boxboard production decreased over the same month last year but increased compared with last month.
Total solid bleached boxboard and linerboard production decreased compared with July 2011 and last month. The production of recycled folding boxboard decreased compared with July 2011 but increased compared with last month.
Back To Top
|
July U.S. coated recycled board (CRB) estimated prices were flat m/m at $890-$910/ton after a $20/ton decline in June, Mark Wilde of Deutsche Bank says. Reports, he adds, suggest producers are offering spot deals. The two key issues are soft demand and falling OCC (old corrugated container prices)— see Containerboard/Packaging section below. Trade reports suggest most CRB producers are taking downtime to maintain demand/supply balance and prevent prices from slipping. URB (uncoated recycled board) remains mixed. "Demand is OK, aided by last year's supply reductions. However, falling OCC could pressure URB prices. July prices were flat at $655-$685/ton," Wilde notes.
Solid bleached sulfate (SBS) board demand is soft and prices are under pressure, according to Wilde, and producers are taking downtime to keep the demand/supply in balance. July estimated prices were flat at $1,135/ton. Trade reports, he points out, suggest that order backlogs have declined and producers are offering spot deals. The $50-$60/ton hike on cupstock and plate stock hike in late-May/June does not appear to have gained much traction. "
Better than SBS and recycled grades. July coated unbleached kraft board estimated prices were flat at $1,000-$1,060/ton, Wilde reports. Demand is relatively stable, although not as strong as last year. Producers have done a good job of keeping demand/supply in balance, he says, adding that a $40/ton February price hike failed to gain traction.
A key issue for all boxboard grades is the prospective fall-out from a surge in Chinese capacity, Wilde continues. "With fiber costs down and Chinese demand having slowed, we could see a jump in Chinese exports.
Back To Top
|
Containerboard production in the U.S. rose 2.3% over June 2012, but fell 2.2% compared with the same month last year, according to the AF&PA (Washington, D.C., USA) July 2012 U.S. Containerboard Statistics Report published this week. The month-over-month average daily production decreased 1%.
The containerboard operating rate for July 2012 lost one point compared with June 2012, from 96.3% to 95.3%.
Back To Top
|
Total kraft paper shipments in July were 138,000 tons, an increase of 3% compared with June 2012, according to the AF&PA (Washington, D.C., USA) July 2012 Kraft Paper Sector Report released this week. Total inventory was 78,700 tons in July, AF&PA noted.
Back To Top
|
U.S. producers implemented the $50/ton extensible sack kraft increase in July (estimated level = $1,140-$1,160/ton), Mark Wilde of Deutsche Bank reports. The key drivers were tight supplies, pick-up in export demand, and strong order backlogs. Domestic demand remains sluggish (H1 sack shipments -5% y/y). Natural multiwall estimated prices were flat at $985-$995/ton in July.
Back To Top
|
In July, 30-lb newsprint East (North America) was flat at $640/metric ton, according to Mark Wilde of Deutsche Bank, who adds that in the West, prices slipped $5/metric ton m/m to $605/metric ton. Incremental capacity from the restart of White Birch's 150,000 metric tpy paper machine at Stadacona will be more than offset by permanent closure of Catalyst Papers' Snowflake mill (277,000 metric tpy) and Resolute Forest Products' Mersey mill (250,000 metric tpy), Wilde adds. The net reduction of 377,000 metric tpy implies ˜7.5% of North American newsprint capacity. "Reports suggest that the Snowflake closure could stem price declines in the West," Wilde says.
Back To Top
|
The difficult operating environment for the Finnish paper industry in the first quarter of this year continued in the second quarter, according to the Finnish Forest Industries Federation (FFIF). Finland's production of printing and writing paper fell by 12% in the first six months of the year to 3.2 million metric tons, and board manufacturing fell by 6% to 1.3 million tons.
The FFIF reports that consumption of graphic paper on the main markets in Europe remained at a low level due to the euro crisis. This was reflected in Finnish production figures, FFIC adds, noting that Finland's exports of paper and board decreased by 12% and 8.5%, respectively, compared with the first six months of last year. But prices remained on the same level.
The production of chemical pulp in Finland decreased by 2% to 3.4 million metric tons in the first half of 2012. Pulp exports, however, increased.
Back To Top
|
Pulp & Paper
Asia Pulp & Paper group (APP), Jakarta, Indonesia, reports that by 2015 it will source 100% of its pulpwood from plantations (tree farms), as part of its recently-launched Sustainability Roadmap for 2020 and beyond. APP says that being "wholly plantation-reliant by 2015" puts it "10 years ahead of the publicly-stated goals coming out of other global paper industry players."
Ian Lifshitz, North American director of sustainability and public affairs for APP, notes that "the old way of gauging a paper product's sustainability was to look at percent of recycled content, but this should not be the only barometer. Fiber age is equally if not more important. Our business aim is to be wholly reliant on tree farms in Southeast Asia, and trees from these plantations can be harvested, re-planted, re-grown, and harvested again in just six years. That is obviously in stark contrast to the process of harvesting old-growth trees in North America – a process that takes 70 to 80 years.
"There are so many misconceptions about what it takes to be environmentally conscious," Lifshitz continues. "For example, despite all of its benefits, recycling does require intense amounts of energy and chemicals for the deinking process. The important thing to remember is that trees grow back. In that regard, they should be considered a crop, and nowhere in the world do trees grow faster than in Indonesia and China."
This week's announcement follows an earlier company report that its production mills are the first in Indonesia to achieve SVLK certification, the country's new wood legality standard.
APP is a brand umbrella for paper products produced by several mills in Indonesia, including PT Indah Kiat Pulp & Paper Tbk, PT Pindo Deli Pulp & Paper Mills, PT Pabrik Kertas Tjiwi Kimia Tbk, PT Lontar Papyrus Pulp & Paper Industries, and PT Ekamas Fortuna.
Back To Top
|
Catalyst Paper, Richmond, B.C., Canada, this past week reached agreement with Pacifica Deep Sea Terminals Inc. on the sale of its Elk Falls site in Campbell River, Vancouver Island, B.C. The $8.6 million sale of the 400-acre industrial site and adjacent properties is expected to close September 5. It completes Catalyst's comprehensive bid review process that began earlier this year.
"We are very pleased to have attracted an experienced developer with the capacity and an industrial concept that will fully utilize the site's infrastructure and bring new business and jobs to the region," said Kevin J. Clarke, Catalyst president and CEO.
The former pulp and paper site was indefinitely curtailed in 2009 and closed permanently in 2010. Since then, equipment has been decommissioned and demolition work has been completed to prepare the site for sale and redevelopment to other industrial uses. The Elk Falls mill began operation in 1952, and at its peak, produced 784,000 metric tpy of pulp, paper, and kraft paper.
"The site is strategically located to serve a variety of marine, light manufacturing, clean energy, and distribution uses," said Pacifica Owner and Director Harold Jahn, "and we intend to transform it into a dynamic industrial park and port facility with the goal of creating 400 full time jobs in the Campbell River region over the next three years."
Jahn is the director and owner of numerous Canadian private firms launched in a range of industries over the past 20 years. He is currently developing three industrial parks in northern Alberta. Within the new Pacifica Industrial Park, Jahn plans to base his companies that are currently developing algae based solar cells, a lithium battery manufacturing facility, ocean wave energy equipment fabrication, and an electric vehicle assembly plant.
Catalyst Paper produces mechanical printing papers, newsprint, and pulp. Its customers include retailers, publishers, and commercial printers in North America, Latin America, the Pacific Rim, and Europe. With four mills located in British Columbia and Arizona (USA), Catalyst has a combined annual production capacity of 1.8 million metric tons.
Back To Top
|
Kruger Inc., Montréal, Qué., Canada, this week announced that active and retired unionized employees at its Corner Brook Pulp and Paper mill, Corner Brook, N.L., Canada, have approved the proposal to apply funding relief measures to their pension plan's deficit. Kruger noted that these relief measures were essential to the mill's ability to compete in the market and will enable the company to pursue its assessment of the mill's long-term viability. The next step will be for the company to present a sustainability plan to its lenders and to the Newfoundland and Labrador government within the coming weeks.
According to the final report issued last Friday by independent auditor Brian N. Hillier, the number of objections for each group of members were:
- Active members (321)—19 objections, 5.9%
- Retired members (645)—7 objections, 1.1%.
With Canadian facilities in Québec, Ontario, British Columbia, and Newfoundland and Labrador, as well as in the U.S., Kruger is a producer of publication papers, tissue, lumber, and other wood products, corrugated cartons from recycled fibers, green and renewable energy, and wines and spirits.
Back To Top
|
The Canadian Province of Nova Scotia this week announced a financial commitment to support the sale of the former NewPage Port Hawkesbury mill to Pacific West Commercial Corp., reportedly bringing more than 1,400 jobs and more than $11 million in annual revenue to the province. The provincial assistance is contingent on Pacific West's final purchase of the mill.
After NewPage, Miamisburg, Ohio, USA, indefinitely shutdown the Port Hawkesbury mill in September 2011 and filed for creditor protection in the U.S. and Canada, Pacific West, associated with Stern Partners, a Vancouver, B.C., Canada, investment firm that also owns Alberta Newsprint Co. of Whitecourt, Alberta, Canada, and Westland Paper Co., an Oregon, USA-based mill, became the successful bidder for the idled operation in January of this year. The bid amount was reported to be $33 million.
Through its Jobs Fund, the Province of Nova Scotia is providing a financial package that includes:
- A $24-million loan to support improved productivity and efficiency
- A $40-million repayable loan for working capital to help the mill become a low cost, competitive producer of supercalendered (SC) papers
- $1.5 million to train workers to operate the paper machine
- $1 million to implement a marketing plan to sell the Nova Scotia forestry sector to the world and create customer opportunities.
The province, through the Department of Natural Resources, has also agreed to invest:
- $20 million to buy 51,500 acres of land to help meet the province's commitment to increase Crown land share and ensure the resource is protected for future generations
- $3.8 million annually, for 10 years, from the forestry restructuring fund to support sustainable harvesting, forest land management, and fund programs that will allow more woodlot owners and pulpwood suppliers to become more active in the management of their woodlands
- Funding for the development of a Mi'kmaq Forestry Strategy and a Mi'kmaq forestry coordinator.
"These investments will support the most modern paper machine in the industry and the development of a new and innovative forestry sector that will give future generations the opportunity to live, work, and raise a family in Nova Scotia," said Premier Darrell Dexter.
Restarting the mill, the province notes, will bring 330 people back to work, protect 600 indirect jobs in the woodlands, sawmills, and power generation industries, and provide 500 more jobs for local communities.
Back To Top
|
JK Paper Ltd., India, a producer of branded photo copier and cut-sized office papers, has ordered from Metso, Finland, the supply and startup of a Metso Paper Lab for automatic testing of paper properties at its Rayagada paper mill. Ashish De, new products chief executive at JK Paper, noted that the advanced Paper Lab was chosen to meet challenges posed by the high machine speed, scarcity of trained manpower for routine lab testing, and the company's "ccontinuous pursuit of best technologies."
Planned startup date for the Paper Lab is this October, when JK Paper's Rayagada mill completes 50 years of operation.
The Paper Lab measures quality parameters including tensile, formation, brightness, roughness, porosity, basis weight, and caliper.
Back To Top
|
UPM, Finland, reports that it completed the sale of its closed Papierfabrik Albbruck GmbH mill in Germany to the German Karl Group. UPM permanently ceased graphic paper production at the mill situated in Baden-Württemberg this past January.
The Karl Group plans to establish new businesses on the premises of the former paper mill within the next three to five years. "Our aim was to identify development ideas and business opportunities for the site," said Hartmut Wurster, who represented UPM in the negotiations. "The sale to Karl Group opens up new economic perspectives for the whole region."
Meanwhile, more than 200 former paper mill employees have found new jobs supported by the transfer company funded by UPM.
Back To Top
|
Wausau Paper, Mosinee, Wis., USA, this week announced the certification of its coated products Manufacturing and Distribution Quality Management (MDQM) system to ISO 9001 :2008. The certification assures that the company's coated products MDQM system complies with performance standards set forth by the International Standards Organization (ISO).
"Driven by our commitment to continual improvement and to consistently produce products that meet or exceed customer expectations, we chose to pursue ISO certification utilizing BSI as our certifying body," said Sheila Widule, strategic marketing manager. "Meeting the ever-growing customer demand for the highest level of quality is vital to the future success of our coated products business."
Widule added that "this certification is the end result of the intense effort by multi-functional groups within our company dedicated to improving workflow and advancing our processes to ensure consistent top-quality products for our customers. Our decision to become ISO 9001 :2008 certified is just another demonstration of our commitment to achieve total customer satisfaction."
Wausau Paper produces and markets specialty papers for industrial, commercial, and consumer end markets as well as a complete line of away-from-home towel and tissue products.
Back To Top
|
Containerboard/Packaging
The packaging industry in Thailand registered strong growth during 2007–2011, according to a new report by MarketResearch.com, Rockville, Md., USA, titled Packaging Industry Outlook in Thailand: Market Size, Key Trends, Drivers, and Challenges to 2016. The new report also provides forecast figures for the 2012–2016 period.
The new report notes that during 2007-2011, the Thai packaging industry grew with a CAGR of 8.21%, supported by both growing food exports and the entry of major industry competitors into the domestic market. The food and beverages sector remains the key growth driver of the domestic packaging industry and is supported by export demand and easy access to raw materials.
Over the forecast period, the industry is expected to grow at a CAGR of 6.41% to reach a value of $11.1 billion in 2016. The estimated growth rate for the industry over the forecast period is significantly lower than the growth rate achieved in the review period. The slow growth in the demand for packaging products is expected to reduce revenue growth, and hence the financial performance, of Thai packaging companies.
More information is available online.
Back To Top
|
In regard to the continuing drop in OCC (old corrugated containers) demand and pricing in the U.S., Mark Wilde of Deutsche Bank asks "are we nearing a bottom?" In August, he says, domestic OCC has dropped $20/ton to $97/ton (-$82/ton y/y). Prices have slipped below $100/ton for the first time in 32 months.
"We estimate that it costs ˜$40-$45/ton just to cover pick-up and handling costs on OCC. The biggest issue is weak demand in China and falling export prices. In August, export OCC to China was down $30/ton. In the short term, falling OCC may aid margins. However, containerboard producers may find it more difficult to pass-through announced price hikes if OCC and other inputs continue to moderate," Wilde explains.
Back To Top
|
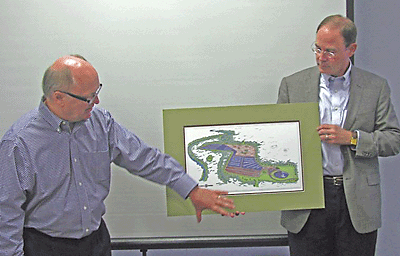 International Paper Co., Memphis, Tenn., USA, is reportedly five months into planning to refurbish its Bogalusa, La., containerboard mill's wastewater treatment plant. When finished, the refurbished plant will be IP's most efficient and state-of-the art wastewater treatment facilities, according to an article this week by the Picayune Item newspaper, Picayune, Miss.
This past May, IP, which acquired the 106-year-old mill from Temple-Inland in February, announced that it would be investing $44 million to modernize and improve the mill's competitiveness by adding new equipment and technology. The mill has 400-plus employees.
According to the Picayune Item article, the new treatment plant at the Bogalusa mill will cost IP an estimated $30 million dollars. Dr. Mike Steltenkamp (on left in photo), mill environmental, health and safety manager, stated in the article that "to say it will be one of the best in company is saying a lot because IP has plants all over the world — in Asia, Europe, and North and South America."
Steltenkamp said that when IP bought the plant from Temple-Inland, the company was handed a plan, but IP officials wanted to revise it and submit a better plan to state officials.
Steltenkamp added that IP officials got permission to revamp the plan, and now, six months later, have submitted plans to both the Louisiana and Mississippi Departments of Environmental Quality, and as soon as they get approval from both agencies, will begin construction on what will be one of a state-of-the-art, and one of the best, wastewater treatment facilities in the world.
Modifications to the mill's wastewater treatment system will be "major," Steltenkamp continued. "There is a lot of redundancy in our new plans." He said the new system will "compartmentalize" waste, mainly solids, and while one portion of the plant can be shut down, the other part will remain up and running. That was not possible under the old system, he said, noting that solids will also be removed at the "front end" of the facility.
"The benefits of this new plant will accumulate quickly, and people will actually see improvements as we get under construction with the facility," Steltenkamp explained. He added that company officials plan to meet with Louisiana and Mississippi officials in late August to get approval and begin work.
Back To Top
|
Sichuan F. Source Paper, China, has ordered from Andritz, Graz, Austria, the paper machine approach, a save-all disc filter for fiber recovery, two PrimeFlow headboxes, and a PrimeDry Hard 2 roll calender for its new testliner and corrugated medium machine. Startup is scheduled for next month (September).
With a design speed of 650 m/min and a width of 4.9 m, the new machine will have a production capacity of 150,000 metric tpy. The Andritz headbox is a compact design unit and easy to install, a critical criteria especially for rebuilds. The PrimeCal Hard calender optimizes pre-calendering and final calendering of all paper and board grades.
Back To Top
|
New Products
Voith Paper, Germany, has launched NipVision, an online and real-time measurement tool using the latest roll cover technology. It is the first system to measure nip pressure, profile, and the cover temperature while the paper machine is running.
The new tool allows actual conditions in a pressed nip to be analyzed. The NipVision glass fiber sensors are very small, non-aging, flexible, and chemically resistant. They lie inside the cover, so that the roll application and dimensions remain unchanged. The sensors are so sensitive that they can detect the presence of paper in the nip.
NipVision is the only system that can measure temperature within the cover while the paper machine is running. This is a real benefit to the customer, Voith emphasizes, given that a large number of damages result from temperature-related issues. Until now, the source of poor profiles and sheet quality, increased sheet breaks, and sudden roll cover damages have often been linked to a given press nip but, without any proof. With the help of NipVision, such problems can be detected and prevented, the company says.
Information from the sensors is transmitted to a computer that plots the profile across the width of the machine and over time. With specific software, the conditions in the nip are shown simultaneously and synchronously. The system is powered through induction, allowing NipVision to constantly transmit information 24 hr a day, while the paper machine is running.
Back To Top
|
Energy
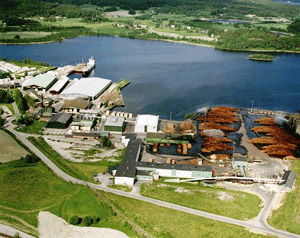 SCA, Stockholm, Sweden, reports that its Bollsta sawmill in the Bollstabruk, Kramfors municipality in the county of Västernorrland Sweden, has increased its capacity to produce bioenergy, reducing its need for fossil fuels. The mill's old boiler was replaced by two new units that are fired with bark and other residue from its wood-based fuel products operations.
The Bollsta mill says that the new boilers have cut its use of fuel oil from 3,400 cubic meters per year to practically zero. The mill has an annual saw capacity of 460,000 cubic meters and a planing capacity of 100,000 cubic meters. The mill's raw material is Nordic pine.
Back To Top
|
People
Norske Skog, Norway, this week reported that its corporate management will be reduced from seven to three members, effective September 1. The new team will consist of CEO Sven Ombudstvedt, CFO Rune Gjessing, and COO Trond Stangeby.
"I am grateful to be joined by two such highly experienced people, Rune and Trond, in the future development of the company. The challenges ahead will be to continue to adjust capacity to market needs, while at the same time adjusting our organization to the company's size and activities. I want to thank all of the retiring members of corporate management. They have for several years contributed with valuable work to improve the profitability of the group," Ombudstvedt said.
The structure of the new corporate management, Ombudstvedt explained, will be adapted to the operating model we already have implemented. "We are now taking the final step from a corporate-driven organization to a flatter organization with independent business units. The overall objectives of the changes have been to improve return on capital and cash-flow from the plants and reduce fixed costs," he said.
Gjessing is currently SVP of operations outside of Europe. He has served in corporate management since 2007 and has been employed in Norske Skog since 2002. He has held several positions within Norske Skog, including SVP of strategy and director of investor relations.
Stangeby is currently SVP of organizational development, and now becomes COO. He has broad experience from various leading positions in Norwegian industry.
SVP of Commercial Jan-H. Clasen will maintain his current role and responsibilities, and will report to Stangeby.
Back To Top
|
Xerium Technologies, Raleigh, N.C., USA, has appointed Harold C. Bevis its new CEO, president, and director. Bevis has been CEO, president, and director of Pliant Corp. and Jordan Telecommunication Products, and has held executive positions with Emerson Electric and General Cable Corp. He is a 1983 graduate of Iowa State University, receiving an Industrial Engineering degree and earned his MBA from Columbia University in 1988.
Coincident with the appointment of Bevis, James F. Wilson, currently Xerium's lead director, has been named chairman of the board. Wilson joined the Xerium Board of Directors in June 2010 and has served on the compensation and nominating committees since that time. He is a principal at Carl Marks Management Co., an investment firm that is a significant shareholder of Xerium stock.
As a result of separating the chairman and CEO roles, Xerium's board of directors will no longer have a lead director.
Back To Top
|
Travels with Larry
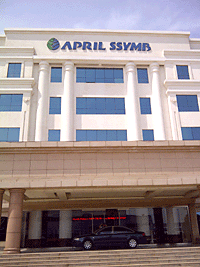 This past May 31, I had the distinct pleasure of meeting with personnel from APRIL's pulp mill in Rizhao, Shandong Province, China.
First Impressions. From the moment you walk in the corporate office building you realize that you are in the presence of greatness. The corporate story is told electronically in a wrap-around room complete with special effects that would make Walt Disney take notice.
History. According to A.J. Devanesan, president/COO, "this mill at one time was state owned. Other major paper companies had looked at the mill and actually considered buying it over a five year period. With no offers in hand, my sales director visited the mill and came back to me and told me that I should take a look at it. I asked how much money were they asking, and he said book value. My chairman said it's a deal."
After the quick decision to purchase the mill, it took 1.5 years to complete the transaction. APRIL has owned the mill since August 2005.
Capacity. The Rizhao mill currently produces nearly 1.5 million metric tons of pulp each year. On May 31, it hit its second largest production month with 125,000 metric tons. Its very best production month was 140,000 metric tons The mill has the capacity to produce 2 million metric tpy.
Equipment. The mill makes all of its bleaching chemicals on-site for its four-stage bleaching process. It has a 5,210 metric ton digester for acacia, two twin-wire pulp dryers capable of handling 2,800 metric tons each, and a 7,200 metric ton recovery boiler.
Feedstock. For the most part, the mill uses acacia and eucalyptus chips sourced from China, Thailand, Australia, Malaysia, Vietnam, and Indonesia. Cost and yield are key drivers for the mix.
The mill's current effluent COD is between 60-70 mg/l, with plans to reduce it to 50 mg/l. Keep in mind that the standard in China is 100 mg/l.
Logistics. A.J. Devanesan has a chemical engineering background and is a fellow of the Wharton Business School. APRIL has studied the Japanese and Korean port based Industries and fashioned this mill to be port-based instead of forest-based.
The chips arrive in ships and guess who owns the ships? APRIL. The company currently has 7-8 custom built ships and has 12 more in the pipeline.
Environmental. APRIL does not build to national environmental standards. It takes the best worldwide standards and beats them by 10%. The company plans ahead and allocates a very large budget on environmental protection.
Future Plans. APRIL is a very prudent company. It has faced financial crisis in the past, and so does not want to overstep its own capacity. The company may expand in pulp in the future, however. It is currently looking at downstream expansion into liquid packaging, board, and tissue as sustainable and long term product lines, in the form of a board and tissue machine. The company plans to keep building to meet requirements of outside and internal integration.
APRIL is building capacity primarily for the China market. It currently is at 45% capacity versus Chinese market pulp demand in China. It may export within a regional area or even the West Coast of the U.S. In Indonesia it is building capacity for export.
The two largest pulp mills in the world are in China. One is owned by APP and the other is owned by APRIL. Many smaller mills have been shut down in China—it looks like bigger is better, as they say. Some 85% of the world's new paper products capacity has been in China for the past several years. The average person in China uses 35-40 kilos of paper per year. Right now, China is a net exporter of paper.
Currently, the U.S. still has more natural resources than China. However, globally, more than 200 million trees are planted each year by the APRIL group. This means that those countries planting trees today will assure their own raw materials in the future.
APRIL is a firm believer in plantations. It is committed to planting trees, and believes that it will be a leader in our industry for a long time to come.
More information about April is available online.
More information about TAPPI is also available online.
There are two types of people in our industry, TAPPI members and those who should be.
Until next time............
Larry
Back To Top
|
TAPPI News
The U.S. Forest Service Forest Products Laboratory (FPL) celebrated the opening of its $1.7 million nanocellulose pilot plant in Madison, Wis., USA, late last month. TAPPI President and CEO Larry N. Montague joined industry representatives and dignitaries, including USDA Under Secretary Harris Sherman, to celebrate FPL's investment to become the country's leading producer of nanocellulose.
Nanocellulose, derived from cellulose, which is the world's most abundant natural polymer, has unique crystalline properties that can be used commercially to make lightweight, high-performance products for use in a wide range of industries. Applications include consumer products, medical devices, electronics, food packaging, coatings, composites, antimicrobial fibers, military applications, filters for blood and water, and many others. The emerging market for new wood-derived renewable materials will create jobs and contribute an estimated $600 billion to the economy by 2020.
"TAPPI and its International Nanotechnology Division commend the Forest Service for making this investment in a one of a kind pilot plant to support the growth of nanocellulose applications. Applying nanotechnology to renewable materials is a groundbreaking advancement for improving not only cellulose based products but for other renewable materials and industries." notes TAPPI's Montague. "The FPL pilot plant will play an integral role in advancing nanotechnology research and new product development by providing forest based nanocellulose to researchers and commercial application developers in a wide range of industries."
Founded in 1910, the U.S. Forest Service Forest Products Laboratory is the nation's only federally funded wood utilization research laboratory. The mission of the FPL is to identify and conduct innovative wood and fiber utilization research that contributes to conservation and productivity of the forest resource.
TAPPI's International Nanotechnology Division serves as the leading global forum for the community of individuals, organizations, and institutions seeking to collectively advance the responsible and sustainable production and use of renewable materials. The division's International Conference on Nanotechnology for Renewable Materials, which will hold its next meeting on June 24-27, 2013, in Stockholm, Sweden, is the industry's largest annual meeting.
Back To Top
|
The TAPPI Extrusion Coating Course, August 27-29, 2012, on the Michigan State University campus, will provide an opportunity for critical technical training and networking that can help you improve your extrusion coating operations and gain a competitive edge. TAPPI is one of the few training centers offering courses in a specialized area such as extrusion coating taught by experts who have worked in the industry.
The slate of instructors scheduled to lead the sessions for the course represent decades of experience and leadership. With their guidance, you'll be able to explore the best practices and equipment technologies that apply to extrusion coating applications. Attending this course is the next logical step in your efforts to more effectively troubleshoot and increase your productivity. The course offers face-to-face opportunities to accelerate learning at a faster rate than you can get by using online learning, reference books, or manuals alone.
Register now for this not-to-miss opportunity!
Back To Top
|
TAPPI will be performing its fiscal year end inventory counting starting August 30. As a result, TAPPI will not be processing TAPPI Press orders from August 30 - September 4. Orders received during this time will be shipped in the order in which they have been received starting on September 5. All normal payment processing will resume on September 5.
We apologize in advance for any inconvenience and thank you for your patience. This allows us to better serve our members.
Back To Top
|
Join us on Tuesday, August 28, at the Grand View Lodge, Preserve Course, in Pequot Lakes, Minn. A morning shotgun scramble golf outing is planned with lunch to follow.
Please remember, your participation will help fund scholarships for Lakes States TAPPI/North Central PIMA's Scholarship programs. Prizes will be awarded along with a putting contest and a raffle.
Reservation preference will be given to foursomes. Groups of two or less will be placed into foursomes pending availability. We will limit the number of participants to 128.
Entries will only be accepted with full payment. For entries received after August 16, the cost is $135.00 per person. Check-in registration will begin at 8:00 am.
If you have any questions about this event, please contact: Wfrawley@new.rr.com
Full event information and registration details are available online.
Back To Top
|
Join Worldwide Coating Experts at the
Advanced Coating Fundamentals Symposium
The paper coating community will be converging in Atlanta, Ga., USA, Sept. 10-12, 2012, for TAPPI's 12th Advanced Coating Fundamentals Symposium. This biennial event attracts the world's foremost experts in coating technology and is the preeminent symposium for leading-edge research.
Your next opportunity will not come until 2014!
As a special added bonus and for your convenience, the Advanced Coating Fundamentals Symposium (ACFS) will be co-located with the 16th International Coating Science and Technology Symposium (ISCST) providing you with insights into coating research in non-paper applications. Your TAPPI registration will allow you extended access in to any of the ISCST presentations. It will also include full printed proceedings of the TAPPI program.
The ACFS Technical Program will focus on what it takes to commercialize an innovation -- and includes more than 20 peer-reviewed papers covering novel paper coatings, mechanics of printing, new and emerging technologies, and nanotechnology in paper coating.
In addition to learning about all of the latest developments, your registration includes an evening of fun and fellowship with coating colleagues from around the world at the Advanced Coating Fundamentals dinner, scheduled at a distinctive Atlanta venue.
Click here to view the program.
Click to learn more about ACFS 2012.
Back To Top
|
A message from the leadership of the TAPPI Biomass Supply, Demand, and Handling Subcommittee
Regardless of the cellulosic biorefinery platform, the success of all cellulosic biorefineries will be dependent on a steady and sustainable supply of, and reasonable cost for, well cleaned, cellulosic biomass delivered to the biorefinery.
The TAPPI Biomass Supply, Demand & Handling Subcommittee was formed in early 2011 to focus on various aspects of the biomass supply chain. The intent of this subcommittee is to provide a venue for interested parties to have a free exchange of state-of-the-art technical ideas on these important topics.
We have identified a few subcommittee projects, and are looking for volunteers to join the subcommittee and assist in working on these or other projects. If you are interested in joining this subcommittee, please contact Mary Ann Cauthen ( mcauthen@TAPPI.org) at TAPPI.
Biomass Supply Short Course - This course would address issues in cost-effective delivery and preparation of biomass materials (wood and non-wood). Bob Hurter, Bill Fuller, and Desmond Smith are currently working on educational outcomes and identifying speakers.
Standards for Biomass Sampling and Testing Methods - We are looking for one or two individuals to head up this area, plus others who can contribute. This group would first work to identify needs and evaluate gaps between existing standards and identified needs. A survey of needs has been suggested as a first step. If you are interested in this area, or know someone who would be, please encourage them to contact Mary Anne Cauthen ( mcauthen@TAPPI.org) and 1) join this subcommittee if not currently a member, and 2) indicate interest to work on this project.
LinkedIn Group - We are also investigating the use of a TAPPI LinkedIn group for biomass supply, demand, and handling issues. If you are interested in helping on this project, please let Mary Ann Cauthen ( mcauthen@TAPPI.org) know.
September 19 Subcommittee Webinar - We are scheduling a webinar to update the subcommittee on efforts in these areas. Please plan to attend on Wednesday, September 19, from 1:00-2:00 p.m.
Subcommittee Chair - Bob Hurter, HurterConsult
Subcommittee Co-Chair - Bill Fuller, FRM Consulting
Back To Top
|
Every mill is capable of improving its reliability and maintenance practices. This is a critical function in mill operation that affects the bottom line. Training to keep up with changing technology and new procedures is absolutely essential for maintaining profitability and productivity.
The 2012 Preventive Maintenance and Essential Care & Condition Monitoring Course
shows participants how to set up a cost-effective process and provide practical exercises and techniques. This training takes place September 12-13, 2012, in Raleigh, N.C., USA.
IDCON's Root Cause Problem Elimination Seminar focuses on eradicating problems. You will learn how to tie cause and effect together while applying logical thought processes to arrive at the problem's core.
You stand to benefit from this training if you:
- Plan preventive maintenance work
- Execute preventive maintenance tasks (operations and maintenance)
- Manage preventive maintenance
- Work with reliability improvements
- Manage and/or supervise maintenance personnel
- Work with a computerized maintenance management system
- Work as a maintenance or reliability engineer
- Coordinate PM tasks between E/I, mechanical and operations
- Manage operator essential care and inspections.
TAPPI and IDCON are pleased to partner for this course so that you and your maintenance teams can get expert advice from the industry's leaders in reliability and maintenance.
Click Here to Register.
Remember, seats will fill quickly for this essential training program!
Back To Top
|
Lake States TAPPI/North Central PIMA will host the 13th Annual "Guns of Navarino" on Tuesday, September 25, at J&H Game Farm in Navarino, Wis., USA. This event is designed to help relieve work related stress through a series of team building activities culminating in an evening of social interaction. Sounds good, doesn't it? Just ask anyone who has been to one of our past outings.
This event will begin at 11:30 a.m. on September 25, and the actual tournament gets underway as soon as teams assemble, at approximately 12:30 p.m. The format will be five-person teams. Individual shooters and teams of less than five are also welcome. We will make every effort to have complete teams of five for the competition. Registration is limited to the first 30 teams (150 shooters). The cost for the event will be $120.00 per person ($600.00 per team). Registration includes the following:
- Sporting clays, five-stand, wobble events
- Ammunition for both shooting events
- Dinner (picnic/tailgate style)
- Cash prizes for top team and Individual
- Raffle prizes
- Shotgun Raffle.
Lunch will be provided before the shoot, starting at 11:30 a.m. There will be a cash bar available after the shooting portion of the program concludes. No alcohol will be served until you have completed the shooting portion of the outing. Prizes will be awarded following the completion of the day's shoot.
Don't Delay. Assemble your Teams Today!
Event information is available here.
Registration Information is available here.
Back To Top
|
The Gulf Coat TAPPI Local Secton announced that its Fall 2012 Meeting topic will be "New Boiler Mact Rule Considerations." The meeting will be held at the KBR offices in Birmingham, Ala., USA, on Thursday, September 27, 2012.
Please mark your calendar and advise others who may have an interest in this subject.
The program is currently being assembled, and meeting details will follow as soon as they are completed. We expect 10-12 presentations covering this topic.
If you wish to participate in this program, please contact Jeff Smith via email at jeff.smith@btg.com.
Back To Top
|
You're invited to the 7th Annual Pacific Section Golf Tournament! This event will be held on September 28, 2012 (Friday). Start time is 1:00 p.m. at the Lewis River Golf Course.
The tournament format is a Modified Shotgun Start, four-person scramble with 144 spots open - First Come/First Serve. The entry fee is $125/person, which includes green fees, cart, two beverage tickets, prizes, a meal afterwards, and most of all... lots of fun!
Awards: 1st Place Team, 2nd Place Team, 3rd Place Team, M/W Longest Drive, KP, Longest Putt. Also enjoy door prizes and a raffle!
Proceeds go to the Pacific Section TAPPI scholarship fund!
Questions? Contact Vince Hochanadel via phone (360) 901-1680 or via email: vince.hochanadel@gmail.com.
Additional details and the registration form can be found here on the TAPPI website.
Back To Top
|
Roll and Web defect Terminology, Second Edition by R. Duane Smith describes defects commonly found in paper, film, nonwoven webs, and wound rolls. This edition has been expanded to include defects from processes that did not exist when the first edition was written 15 years ago. This book is a "must have" communications tool for suppliers and their customers to assist in the identification and elimination of roll and web defects.
This industry resource was written and edited by 22 Industry Experts with more than 500 years of web handling and winding experience along with 16 contributing editors. Each of the 224 defects has concise information that provides:
- A description of the defect
- An illustration of the defect
- The synonyms or also-known-as terms commonly used
- Cross references for these synonyms in index
- Common causes of the defect
- Common remedies of the defect
- Other sources of information published on the defect.
Roll and Web Defect Terminology, Second Edition has already been recognized by web producing and converting industry experts as the most comprehensive reference guide available for addressing roll and web defects.
View the Table of Contents.
Product code: 0101R318
TAPPI Member Price: $139.00
Non-Member Price: $210.00
Back To Top
|
Learn with expert guidance from instructors with decades of leadership in business operations specifically in the pulp and paper industry.
The Financial and Strategic Analysis Workshop for Pulp & Paper and Related Industries is designed to teach important business skills for the challenges mills are facing today. This workshop is scheduled for October 3-5, 2012 in Raleigh, N.C., USA.
You'll also learn how to market your ideas, products, and services with sound financial backing.
North Carolina State University and TAPPI have partnered to offer basic as well as sophisticated tools to help you analyze and manage important financial information with more confidence. This workshop will help you:
- Understand the crtical role of reinvesting in pulp and paper mill assets to ensure long term survival and prosperity
- Learn the basics of capital budgeting, cost of capital (cost of debt and cost of equity) and financial indicators to allow you to use these tools to build financial analyses and sell your ideas, products, and serives
- Understand the importance of cost structure and how you can increase your competitive advantage by managing your costs
- Appreciate, in financial terms, the impact of your operation, research, new technique or new product
- Build an entire financial analysis from the ground up
- Learn the basis for strategic planning and decision-making.
Learn more about the instructors and curriculum.
Back To Top
|
Are you someone who could benefit from an overview of the entire pulping and paper-making process?
If so, The 2012 TAPPI Hands-On Workshop for Pulp and Paper Basics might be the perfect course for you to learn about the fundamental processes and operations of the pulping and paper-making industry. This year's workshop runs from October 1-5 at North Carolina State University in Raleigh, North Carolina, USA. Reserve your place now so that you can:
- Find out how different processes affect paper properties
- Perform hands-on laboratory experiments to support your understanding of the process
- Run a pilot plant paper machine
- Solidify your knowledge from close interaction with professors in small, interactive groups
Be among the first 32 people to register for this five-day workshop, and you will gain an invaluable overview of pulping, bleaching, chemical recovery, recycling, paper-making and converting. You'll receive course notes, an accompanying CD-ROM, and your own polo shirt. You will also have the opportunity to earn 3.7 CEUs.
This workshop is ideal for new process engineers, manufacturing operators and technicians, sales and service personnel, machine operators, and maintenance personnel. Everyone who wants a better understanding of the basic operation of the pulp and paper business will benefit from this course.
This course typically fills quickly, so don't wait long.
We look forward to seeing you in Raleigh this October!
Back To Top
|
The NCSU Financial and Strategic Analysis Workshop, October 3-5, 2012, Raleigh, N.C., USA
You will learn basic and sophisticated tools to analyze business operations, estimate financial outcomes, and support decision making. In this workshop, you will also discover how to:
- Understand the critical role of reinvesting in pulp and paper mill assets to ensure long term survival and prosperity
- Study basics of capital budgeting, cost of capital (cost of debt and cost of equity), and financial indicators to allow you to use these tools to build financial analyses and sell your ideas, products and services
- Appreciate the importance of cost structure and how you can increase your competitive advantage by managing your costs
- Explain in financial terms the impact of your operation, research, new technique, or new product
- Build an entire financial analysis from scratch with the assistance of recognized Business Operation Instructors with decades of experience in business operations in the pulp and paper industry
- Learn the basis for strategic planning and decision-making.
Who Should Attend?
This workshop is especially beneficial for:
- Managers at pulp and paper mills and business units responsible for strategic planning
- Engineering consultants who provide strategic studies to pulp and paper mill clients
- Sales and service personnel who want to sell their ideas to customers and upper level management
- Superintendents and engineers who want to understand how to measure profitability and costs in their operations
- Managers who want to understand the financial outcomes of process improvements and capital projects
- Research and development engineers and scientists looking to calculate the potential financial impact of their research
- Engineers who are new to the pulp, paper and related industries Register today to apply your new skills in business and financial analysis and take your job performance to the next level.
Register today to apply your new skills in business and financial analysis and take your job performance to the next level.
Back To Top
|
Pulp and Paper mills often find themselves spending millions of dollars inspecting, repairing, and recovering from unexpected leaks in their boiler tubes, tanks, pressure vessels, exposed and buried pipeline, stacks, bleach towers, etc...
Here's your chance to learn how to substantially reduce these costs! Corrosion probe Inc.'s FEMOS Workshop training shows maintenance staff how to rationally manage the mechanical (containment) intregrity of all types of fixed eqpment with a simple, rigorous system utilizing disciplines and procedures by vendors who specialize in the maintenance of rotating equipment.
What do you gain from attending?
This workshop to be held October 14, 2012, 8 am - 5 pm EDT in Savannah, Ga., USA, will teach attendees how to implement a mill-specific program by using a transparent and disciplined process to systematically design the right inspection plan for each major piece of fixed equipment based on its' materials of construction, present condition, and service conditions. The basic concept employs proven, high-value practices from refining and petrochemical industries for risk based inspection, customizing inspection plans to possible damage mechanism and using fitness-for-service engineering assessments to define damage limits.
Who is leading the workshop?
Corrosion Probe Inc.'s workshop will employ experienced and renowned TAPPI participants Dave Bennett, David Browe, and Doug Sherman. They will train up to 20 people in a 1-day (6-Hour) workshop. Training is presented so attendees can use their new knowledge to immediately implement FEMOS at their mill. Many working examples are provided and students are invited to bring their mill's costliest fixed equipment inspection and maintenance concerns for case analysis.
The FEMOS workshop takes place just before the 2012 TAPPI PEERS Conference and the 2012 IBBC conference. Those attending the FEMOS Workshop can also attend these important events.
Back To Top
|
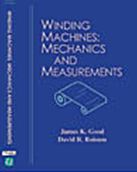
Winding Machines: Mechanics and Measurements
By: Dr. David Roisum and Dr. J.K. Good
Winding Machines: Mechanics and Measurements is the definitive book on the science of winding written by noted experts Dr. David Roisum and Dr. J.K. Good. This three-part book (with supplemental CD-ROM) describes the various classes and arrangements of winding machinery commonly found in the web industries, including a discussion of controls and defects, how roll stresses and roll defects can be predicted by mathematical models and what factors are important, and almost every method for measuring and evaluating wound roll quality.
The book describes how and why many wound roll defects occur. In more than a few cases, it even describes when defects occur based on winding models that have matured to the point of trustworthy application. In these cases, we have science at its best, a predictive tool. A CD with an easy-to-run winding model is included with every book.
However, one need not be a scientist to appreciate and use this text. Much of it is written in everyday language describing the machines we work with, the defects we see, and the many measures of roll quality. It is a book that most plants with a winding department would want to have.
View the Table of Contents
Preview Pages
Product code: 0102B068
TAPPI Member Price: $154.00
Non-member Price: $229.00
Back To Top
|
The 2012 TAPPI PEERS Conference, October 14-17 in Savannah, Ga., USA, has announced a detailed technical program. Five programming tracks of peer-reviewed sessions, Pulping, Engineering, Environmental, Recycling, and Sustainability, will answer the most pressing business and technical questions faced by pulp and paper companies as they manage raw materials, assets, regulatory requirements, and production assets.
Register now and save.
In addition to the in-depth, peer-reviewed technical program, Keynote Speaker Don Roberts, vice chairman of CIBC World Markets, will present " A Whirlwind Tour of Investment Trends and Issues in the Global Bio-Energy Space." PEERS will also offer exclusive networking opportunities and insight into new technologies that can help you optimize your mill operations.
The TAPPI PEERS Conference will be co-located with the International Bioenergy and Bioproducts Conference, creating a value-added opportunity for you to expand your learning, networking, and resources by attending both events. See you in Savannah!
Back To Top
|
Operating Excellence (OpEx) Maintenance and Reliability Seminar at PEERS
This is a first-time program for the 2012 TAPPI PEERS Conference.
Maintenance and reliability continue to be critical to the efficient operation of pulp and paper mills worldwide, just behind fiber and labor as top production cost factors.
This one-day seminar explores the latest reliability strategies today's mills are implementing to stay in-tune and competitive under progressively lean operating conditions.
The OpEx Maintenance and Reliability Track, included in your PEERS registration at no extra cost, is part of the Engineering Program.
If you are only interested in attending the OpEx Track, select the Single Day PEERS Registration for Thursday, October 18. This year's PEERS Conference includes a full program of educational opportunities for maintenance and reliability personnel, including:
- Sunday, Oct. 14: Fixed Equipment Maintenance Optimization System Course (Additional Fee)
- Monday, Oct. 15 - Wednesday, Oct. 17: Corrosion & Materials Engineering Track
- Thursday, Oct. 18: OpEx Maintenance and Reliability Track.
In addition, 2012 TAPPI PEERS Conference, October 14-17 in Savannah, Ga., features a detailed technical program. Five programming tracks of peer-reviewed sessions, Pulping, Engineering, Environmental, Recycling and Sustainability, will answer the most pressing business and technical questions faced by pulp and paper companies as they manage raw materials, assets, regulatory requirements and production assets.
Register now and save.
The 2012 TAPPI PEERS Conference will be co-located with the 2012 International Bioenergy and Bioproducts Conference, creating a value-added opportunity for you to expand your learning, networking, and resources by attending both events.
See you in Savannah!
Back To Top
|
On Nov. 7-9, 2012, TAPPI will conduct its Tissue Runnability Course in Neenah, Wi., USA.
This special course is being taught by technical experts in each area of the machine from wet end operations through creping and process control. The experienced, highly qualified faculty for this course will provide a thorough understanding of the entire tissue making process and current best practices in each area.
Wednesday's (November 7) classes will focus on stock preparation and wet end operations, while Tuesday's (November 8) classes cover pressing, drying, and doctoring. Wednesday (November 9) classes examine technologies and latest developments in hoods, TAD (through-air drying), and other dynamics of the tissue machine dry end,
The 2012 TAPPI Tissue Runnability Course is designed for process engineers, machine supervisors, and reliability professionals who have to maximize uptime and saleable production. It is also an excellent tutorial for suppliers who support tissue making customers. It will help attendees:
- Improve tissue quality and consistency
- Understand contributors to waste and downtime
- Learn reliability and maintenance best practices
- Diagnose and troubleshoot problems quickly.
After successfully completing this course, attendees will specifically be able to:
- Diagnose the impact of recycled furnishes on tissue properties
- Make changes to wet-end chemistry to improve machine operations
- Improve cleaning and conditioning of fabrics
- Troubleshoot runnability problems in the press, Yankee, and creping systems
- Identify improvement opportunities on the dry end
- Pinpoint productivity opportunities in Yankee steam, coating, and hood systems.
TAPPI will award CEU credits to participants who attend at least 80% of the educational sessions and complete a final program evaluation.
The 2012 Tissue Runnabilitry Course includes advanced process instruction. If you are looking for an introductory-intermediate tissue course, consider the upcoming 2012 Tissue Properties and Manufacturing Course at TAPPI Headquarters in Norcross, Ga., USA, on August 15-16.
Attendance for the 2012 TAPPI Tissue Runnability Course is limited, so please register today at the course website.
Back To Top
|
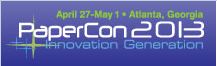
A Call for Papers has been issued for PaperCon 2013. Theme is "Innovation Generation."
After record attendance in 2012, PaperCon will again bring together CEOs, mill managers, superintendents, scientists, process engineers, and suppliers for the largest pulp and paper technical program in the world. The event will take place April 27 to May 1 in Atlanta, Ga., USA. Learn more about PaperCon 2013.
For 2013, PaperCon is pleased to welcome the Tissue360 Forum, NETInc (Innovative Nonwovens Conference), RPTA (Recycled Paperboard Technical Association) P-T Seminar and the OpEx Reliability Workshop. Each of these events is open to full PaperCon registrants and papers in these areas are welcome.
Calls for Papers and Posters have been issued. The conference theme is Innovation Generation, and authors are encouraged to include this within their papers. Topics under consideration include mill management, papermaking, coating, tissue, nonwovens, and recycled paperboard. Paper company personnel, suppliers, academics, and students are strongly encouraged to submit their ideas for papers, posters, or roundtable discussions.
Papermakers Program:
The Papermakers Program encourages topics on paper machine performance evaluations, papermaking fundamentals, product/process optimization, recycled paperboard, tissue making (Tissue360 Forum), and the RPTA P-T Seminar. The deadline for submission of abstracts is November 20, 2012. Abstracts for panel discussions and roundtables are welcome. See Papermakers Program Call for Papers.
Coating and Graphic Arts Program:
The Coating and Graphic Arts Program will focus on The Future of Print and its Demands on Paper and Coatings. The deadline for extended abstracts for this program is Oct. 16, 2012. See the Coating and Graphic Arts Program Call for Papers.
All abstracts must be submitted using TAPPI's Speaker Management System for consideration by the TAPPI and RPTA program committees.
Back To Top
|

Named a TAPPI Fellow in 1985, member Michael Kocurek, Ph.D., has been an extremely active participant in TAPPI for nearly 50 amazing years. In 1992, that dedication was recognized with TAPPI's Distinguished Service Award, the second highest honor bestowed on members.
Recently retired as a professor and former head of North Carolina State University's Department of Wood and Paper Science, Dr. Kocurek spent his entire career dedicated to the P&P industry, educating its future ranks and preparing them to serve as the next generation of leaders. Still actively involved in TAPPI, he continues to teach some of TAPPI's perennially favored courses, including Introduction to Pulp and Paper, which he has been doing continuously since 1974, Introduction to Kraft Pulping and Bleaching, Linerboard and Medium Manufacturing, and Tissue Properties and Manufacturing . Find out more by reading this month's Member Spotlight.
Spotlight participants are recommended by fellow members and staff. If you would like to nominate a member just send name (or names) to MemberSpotlight@tappi.org. We will forward a Spotlight Questionnaire to fill out and return.
We look forward to seeing you in the Spotlight!
Back To Top
|
|
|
TAPPI Over the Wire | 15 Technology Pkwy. S. | Norcross, GA 30092 USA | Voice: 770.446.1400 | Fax: 770.446.6947
|
 |