 |
|
Weekly Spotlight
In line with a resolution by its board of directors, and after having received all required legal and regulatory approvals, Paper Packaging Canada, Brampton, Ont., Canada, has changed its name to Canadian Corrugated & Containerboard Association
Learn More...
|
SP Fiber Technologies LLC (SPFT) announced this past week that it has acquired substantially all of the assets and certain liabilities of SP Newsprint, Dublin, Ga., USA, and its subsidiaries in a court-approved sale
Learn More...
|
Catalyst Paper, Richmond, B.C., Canada, this week announced that it has begun a sale process for its Snowflake mill and associated assets in Arizona, USA, in accordance with the U.S. Court-approved sale and investor solicitation procedures (SISP)
Learn More...
|
Kimberly-Clark Corp., Dallas, Texas, USA, has received an A+ rating from Global Reporting Initiative (GRI) on its 2011 Corporate Sustainability Report, Full Circle, which highlights the company's progress towards its Sustainability 2015 goals
Learn More...
|
Western Michigan University's Pulp and Paper Program, Kalamazoo, Mich., USA, has donated pulp that will keep the Paperworks Goodwill Program in business for the next year
Learn More...
|
SCA, Philadelphia, Pa., USA, this week announced that its Tork napkin brand has launched a new program in support of its sponsorship of Share Our Strength's No Kid Hungry® campaign to end childhood hunger in America
Learn More...
|
Sappi Fine Paper North America (SFPNA), Boston, Mass., USA, has announced the eighth episode of its humorous online video series, Off Register™ on The Flo Channel, titled "Kevin Picks the President," an election-inspired episode that makes fun of the sometimes difficult client approval process
Learn More...
|
Below is the latest listing of job openings in the TAPPI Career Center.
Learn More...
|
Market Roundup
Prices for wood chips and pulp logs in both local currencies and in U.S. dollars fell in most of the 17 regions tracked
Learn More...
|
Pulp & Paper
The Bank Note Paper Mill has ordered from Voith (Germany) two banknote paper machines for its mill in Mysore, India
Learn More...
|
Completion of the acquisition represents the successful culmination of a nearly three-year restructuring process
Learn More...
|
Cascades Inc., Kingsey Falls, Que., Canada, has established a Small Shareholder Program for registered shareholders and beneficial owners of 99 or fewer of the company's common shares as of September 17
Learn More...
|
Catalyst Paper, Richmond, B.C., Canada, a producer of specialty mechanical printing papers, newsprint, and pulp, this past week reported the completion of its previously announced reorganization under the Companies' Creditors Arrangement Act of Canada
Learn More...
|
Domtar, Montreal, Que., Canada, is joining businesses and individuals around the globe to participate in the Rainforest Alliance's second annual Follow the Frog Week that kicked off Monday of this week (September 17) and runs through this Saturday (September 23)
Learn More...
|
Orchids Paper Products Co., Pryor, Okla., USA, was recently awarded Dollar General's 2012 Pride Award - Private Label Vendor of the Year
Learn More...
|
The company said that it expects to make further announcements about additional appointments to the board
Learn More...
|
Dry weather conditions resulting in extreme forest fire danger have caused Rayonier, Jacksonville, Fla., USA, to close its Western Washington State lands to all general public access, effective immediately
Learn More...
|
SCA, Sweden, reportedly has informed employees at its tissue mill in Jönköping, central Sweden, that the plant likely will shut down by year-end
Learn More...
|
SCA, Stockholm, Sweden, has again been included in the Dow Jones Sustainability Europe Index, one the world's most prestigious sustainability indexes
Learn More...
|
The group's strategic production model is designed to bring capacity into line with demand and reduce its cost structure
Learn More...
|
UPM, Finland, has been selected both as a Supersector Leader in Basic Resources sector and Forestry and Paper Sector Leader for 2012-2013 in the Dow Jones Sustainability Index
Learn More...
|
Weyerhaeuser was one of only three forest products companies included in the World Index and one of only two North American companies
Learn More...
|
Weyerhaeuser Co., Federal Way, Wash. USA, also has closed its Western Timberlands operations in Washington and Oregon to public access due to the current, extreme forest fire danger, effective immediately
Learn More...
|
Containerboard/Packaging
Mayr-Melnhof (MM) Packaging, Austria, has acquired Plegacol, a Colombian folding carton producer located in Santiago de Cali
Learn More...
|
Mondi Group, South Africa, this week signed an agreement with Duropack GmbH, Germany, for the acquisition of Duropack's operations in Germany and the Czech Republic, which consist of two corrugated box plants and one recycled containerboard mill
Learn More...
|
MeadWestvaco Corp., Richmond, Va., USA, has been featured in the Carbon Disclosure Project's (U.K.) Carbon Disclosure Leadership Index for 2012
Learn More...
|
Sonoco, Hartsville, S.C., USA, has been selected as sector leader in the U.S. Container & Packaging category of the Dow Jones Sustainability World Index (DJSI World) for 2012-2013
Learn More...
|
Stora Enso, Finland, and Packages Ltd. of Pakistan have established a joint venture called Bulleh Shah Packaging
Learn More...
|
|
New Products
NewPage Corp., Miamisburg, Ohio, USA, has introduced OmniPoint™, a new 60 lb. (89 gsm) heavyweight wet strength label paper designed for large glass and plastic containers used in food, beverage, and condiment applications
Learn More...
|
Twin Rivers Paper Co., South Portland, Maine, USA, a producer of lightweight specialty packaging, label, and publishing papers, has launched a new mold-resistant label paper known as Alliance® WS AM
Learn More...
|
Verso Paper Corp., Memphis, Tenn., USA, has introduced Aspect™ SCK Release Papers, a new addition to its Aspect line of label and release papers
Learn More...
|
Voith, Germany, has launched its newly-developed Revolution press felt for board and packaging paper machines
Learn More...
|
Energy
Nexterra Systems Corp. Vancouver, B.C., Canada, the University of British Columbia, and GE this past week celebrated the successful completion of an energy-from-renewable-waste combined heat and power (CHP) system located at UBC's Vancouver campus
Learn More...
|
People
Packaging paper producer Billerud AB, Stockholm, Sweden, has set the number of its board members to a total of eight, with no deputies
Learn More...
|
McLarty will oversee Finch Forest Management and its staff of professional foresters, as well as lead the wood sourcing team
Learn More...
|
Travels with Larry
This past August 16, 2012, Eric Fletty and I had the pleasure of visiting another leader in its chosen field—NALCO, a newly acquired Ecolab Company.
Learn More...
|
TAPPI News
SuperCorrExpo, October 1-4 in Atlanta, Ga., USA, is your one-stop shop for all things corrugated, with nearly 300 exhibitors on the floor in addition to special workshops and presentations. There will be a Welcome Reception at 200 Peachtree on Sept. 30.
Learn More...
|
Register by September 21 for Discounted Rates. Discounted Hotel Rooms at Savannah Marriott Riverside also available through September 21.
Learn More...
|
If you've ever wanted to feel more confident in working with important financial information at your mill, understanding the costs of running operations, or putting the financial structure behind an idea, then the Financial and Strategic Analysis Workshop for Pulp & Paper and Related Industries may be for you. This course is scheduled for October 3-5 in Raleigh, N.C., USA.
Learn More...
|
This comprehensive textbook describes the entire process of manufacturing corrugated containers. In addition to detailed explanations, the book also features practical troubleshooting tips, and a discussion of common problems and solutions within each major section. TAPPI members can pick this up for just $37 compared to the list-price of $185.
Learn More...
|
Join us on October 22 at this new, lovely golf center near Memphis, Tenn., USA, to hit a bucket of balls and enjoy food and fellowship. Proceeds will support scholarships at Christian Brothers University Packaging Program.
Learn More...
|
This year's golf tournament proceeds go to the Pacific Section TAPPI scholarship fund. Come enjoy a day of fun that features all you need for your game as well as awards, prizes, and a meal afterwards. Event will be held on September 28.
Learn More...
|
This sporting clay shoot event in Navarino, Wis., USA, is designed to help relieve work related stress through a series of team building activities, culminating in an evening of social interaction. It will get underway at 11:30 a.m. on Tuesday, September 25.
Learn More...
|
Special workshop at North Carolina State University focuses on the fundamental processes and operations of today's pulp and paper mills producing a variety of paper and paperboard products.
Learn More...
|
Webinar on October 9 will provide a unique, in-depth look into the current state of biomass production and it's commercial viability.
Learn More...
|
IBBC 2012 will focus on advancements and commercialization of bioconversion technologies that leverage forest products manufacturing infrastructure.
Learn More...
|
What role can government policies play in development of bioenergy in the forest products industry? Panel Themes and special sessions at the 2012 TAPPI IBBC conference will answer those questions and more.
Learn More...
|
Back by demand, this one-day workshop focuses on improving operations and quality in the kraft pulping process. The workshop will make it's encore on Saturday, October 13, in conjunction with PEERS 2012, October 14-17, in Savannah, Ga., USA.
Learn More...
|
A first-time, unique program for the TAPPI PEERS Conference, this one-day seminar explores the latest reliability strategies today's mills are implementing to stay in-tune and competitive under progressively lean operating conditions. October 14,15,18, 2012.
Learn More...
|
The FEMOS Workshop shows maintenance staff how to rationally manage the mechanical integrity of all fixed equipment. The workshop takes place Sunday, October 14 from 8 a.m.-5 p.m. The workshop takes place just before TAPPI PEERS and IBBC conferences, so those going can also attend these important events.
Learn More...
|
On Wednesday, Thursday, and Friday, Nov. 7-9, 2012, TAPPI will conduct its Tissue Runnability Course at Neenah, Wis., USA., with a faculty of technical experts in each area of the machine from wet end operations through creping and process control.
Learn More...
|
Authors are encouraged to include the PaperCon 2013 "Innovation Generation" theme in their papers or posters. Event will include the Tissue 360 Forum, NETInc Conference, RPTA P-T Seminar, and OpEx Reliability Workshop.
Learn More...
|
Well-known author and expert will focus on "Innovation and the Future of Print" in his keynote at PaperCon 2013, April 27 - May 1 in Atlanta, Ga., USA.
Learn More...
|
This 20-volume set covers the entire papermaking process from wood fiber to end product, providing a basis for university-level education, for updating training courses, and as handbooks for the industry.
Learn More...
|
Jay Kaplan shares his story of how TAPPI's member resources can be extremely valuable tools to build and sustain a vibrant career in the industry.
Learn More...
|
The 2013 TAPPI International Conference on Nanotechnology for Renewable Materials will be held July 24-27, 2013, on the KTH Royal Institute of Technology campus in Stockholm, Sweden. The technical program committee has issued a Call for Papers, with abstracts due by December 3.
Learn More...
|
Calls for Papers have been issued for the 14th TAPPI European Place Conference to be held May 6-8, 2013, in Dresden, Germany.
Learn More...
|
|
Find us on Facebook
Network with us on LinkedIn
Follow us on Twitter
|
Weekly Spotlight
In line with a resolution by its board of directors, and after having received all required legal and regulatory approvals, Paper Packaging Canada, Brampton, Ont., Canada, has changed its name to Canadian Corrugated & Containerboard Association (French: Association canadienne du cartonnage ondulé et du carton-caisse). David Andrews, executive director of the association, explained that the new name was chosen to more precisely describe the business areas of its member companies.
Andrews noted that the new name "will more accurately reflect the nature and scope of our members' business interests while supporting the focus of the organization's mandate and mission."
More information is available online.
Back To Top
|
SP Fiber Technologies LLC (SPFT) announced this past week that it has acquired substantially all of the assets and certain liabilities of SP Newsprint, Dublin, Ga., USA, and its subsidiaries in a court-approved sale. SPFT will relocate the company's corporate headquarters to its facility in Dublin, from where it will operate the mills in Newberg, Ore., and Dublin, as well as its wholly-owned subsidiaries SP Recycling Southeast LLC (SPRS) and SP Recycling Northwest LLC (SPRN).
Based in Atlanta, Ga., SPRS and SPRN are recyclers of recovered paper and other recovered commodities in the Southeast and the Pacific Northwest. The two recycling companies collect, process, and ship high quality material from 21 processing facilities in nine states.
Jay Gurandiano will serve as chairman of the board, president, and CEO. He has held senior management positions at Smurfit-Stone Container Corp. and founded St. Laurent Paperboard, a specialty packaging paperboard and converting company. Gurandiano, who will also oversee SPFT's recycling businesses, has put together a senior management team made up of seasoned industry managers to lead the new company.
"We are excited about the future of SPFT and all of its businesses," said Gurandiano. "SPFT is a well capitalized company with committed and knowledgeable shareholders and an exciting strategic plan to strengthen its place in the newsprint and packaging markets. It has a strong and experienced workforce and a solid customer base to build upon. The new management team is committed to improve product and service, boost product innovation, and a build an engaged workforce with an enhanced customer focused culture. "
Gurandiano added that "while newsprint will remain the foundation of the business for the foreseeable future, the company is looking forward to aggressively developing an innovative value-added packaging component to service the paperboard, containerboard, and converting marketplaces. SPFT will focus on customer service, environmental stewardship, and technological innovation."
SPFT newsprint and paperboard mills in Dublin and Newberg produce more than one million tons, of which at least half is made from recycled fiber. Wholly-owned subsidiaries SPRS and SPRN collect, process, and ship materials from 21 processing facilities in nine states.
Back To Top
|
Catalyst Paper, Richmond, B.C., Canada, this week announced that it has begun a sale process for its Snowflake mill and associated assets in Arizona, USA, in accordance with the U.S. Court-approved sale and investor solicitation procedures (SISP). The Snowflake facility is located in the foothills of the White Mountains in northeastern Arizona. The assets for sale include the equipment and other properties associated with the paper mill, approximately 19,000 acres of land, and The Apache Railway Co.
The steps and timeline for soliciting bids to purchase the Snowflake mill and associated assets will be/are being implemented as follows:
- An initial offering summary and confidentiality agreement was distributed to known potential bidders this past Monday (September 17)
- Potential bidders are to submit certain information and an executed confidentiality agreement no later than 5:00 p.m. (Vancouver, B.C., time) on October 1
- Qualified bidders will be determined within three business days after such potential bidders have delivered their materials
- Qualified bidders are to submit a non-binding indication of interest no later than 5:00 p.m. (Vancouver time) on November 1 (the Phase 1 Bid Deadline)
- The non-binding indication of interest will be assessed within three business days after the Phase 1 Bid Deadline
- Once the non-binding indication of interest has been determined to likely be consummated, the bidder will submit a purchase bid or investment bid no later than 5:00 p.m. (Vancouver time) 30 calendar days from being advised by Catalyst to do so (the Phase 2 Bid Deadline)
- The purchase bid or investment bid will be assessed within the three business days following the Phase 2 Bid Deadline
- In the event that Catalyst determines there is more than one qualified purchase bid or investment bid, an auction will be conducted on a date and at a time and location to be advised by Catalyst to such qualified bidders.
Potential bidders who have questions about the recapitalization may contact Nancy Turner of Perella Weinberg Partners, the financial advisor for Catalyst Paper, at 415-671-4550.
Back To Top
|
Kimberly-Clark Corp., Dallas, Texas, USA, has received an A+ rating from Global Reporting Initiative (GRI) on its 2011 Corporate Sustainability Report, Full Circle, which highlights the company's progress towards its Sustainability 2015 goals. GRI is a non-profit organization promoting economic, environmental, and social sustainability by providing organizations with a comprehensive sustainability reporting framework used worldwide.
"Receiving the A+ GRI rating is a testament to the commitment that our leaders and our employees have to sustainability across our entire value chain involving every function, brand, and business at K-C," said Peggy Ward, director, Sustainability Strategy at K-C. "While we are proud of our 2011 progress and the quality level of our sustainability report, we recognize that sustainability is a journey that we will never complete."
The 2011 Sustainability Report was released in May 2012 and is K-C's ninth such annual report. It is structured around the company's Sustainability 2015 strategy framework of People, Planet, and Products introduced last year. The new framework represents K-C's most ambitious and comprehensive sustainability strategy to date, and embodies the company's commitment to weaving a sustainable business practice and mindset into every facet of the organization and as an integral part of its Global Business Plan.
To secure the A+ rating, K-C fulfilled all 79 indicators established by GRI under the headings of Economic Performance, Labor Practices, Human Rights, Environmental Practices, Society Performance, and Product Responsibilities. Some of the key highlights of K-C's activities captured in the report include:
- Sourced 99.9% of its fiber from suppliers certified by sustainable forestry practices.
- Generated 13% of 2011 net sales from environmentally innovative products
- Accomplished its goal of zero workplace fatalities
- Communicated to all of its key suppliers its Supplier Social Compliance Standards that encourage suppliers to align their operations with K-C's Code of Conduct practices and internationally accepted standards for corporate social responsibility and human rights
- Achieved zero manufacturing waste-to-landfill from all of its European Personal Care business facilities
- Extended the Huggies brand "Every Little Bottom" campaign in the U.S. to assist moms who struggle to provide their babies clean disposable diapers
- Expanded the Huggies diaper composting initiatives by opening a second K-C-sponsored recycling plant in New Zealand
- Kleenex brand became the first U.S. consumer tissue to offer Forest Stewardship Council (FSC) certified tissue products and extended its Kimberly-Clark Professional business' FSC certification to more than 95% of its tissue and towel lines in North America
- Initiated water-replenishment projects in India, Israel, Colombia, and Spain, anticipating an annualized return of 205 million gal of water to surrounding communities
- Conducted social initiatives in 23 countries, providing cash and product donations totaling more than $32 million.
More information about the report is available online.
Back To Top
|
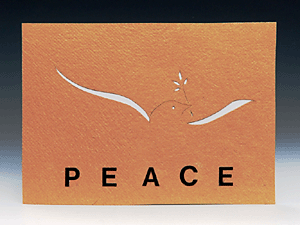 Western Michigan University's Pulp and Paper Program, Kalamazoo, Mich., USA, has donated pulp that will keep the Paperworks Goodwill Program in business for the next year. The Paperworks Goodwill Program employs people with physical and mental handicaps to make Christmas cards used by corporations and organizations, including TAPPI.
"Paperworks is simply a wonderful program that supports people with physical and mental disabilities by providing them an opportunity for employment and training. We commend Western Michigan University's Pulp and Paper program for donating the pulp used to manufacture the cards," notes David Bell, TAPPI's V.P. of Corporate Relations.
Paperworks Studio, a program of Goodwill Industries of Northern Michigan, located in Traverse City, is a community-based organization offering employment and training for people with special needs. It makes high quality handmade recycled greeting cards one-at-a-time with a talented and inspirational team of artists with disabilities and disadvantages. The program's goal is to build self-esteem and confidence and to produce beautiful cards that lift spirits, reassure someone they are loved, and strengthen the bonds of human relationships. .
The cards are made with recycled material such as blue jeans, wool, coffee, and cotton. Products include holiday, birthday, and thank you cards as well as custom corporate cards used by companies and individuals from around the country.
Back To Top
|
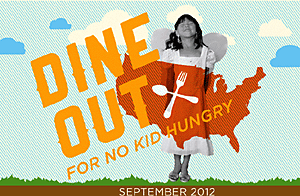 SCA, Philadelphia, Pa., USA, this week announced that its Tork napkin brand has launched a new program in support of its sponsorship of Share Our Strength's No Kid Hungry® campaign to end childhood hunger in America. Tork, which makes the Xpressnap® line of napkins and dispensers for the Foodservice Industry, will donate $1 to the No Kid Hungry campaign for each Xpressnap Signature Tabletop dispenser sold starting this month, to kick off Share Our Strength's Dine Out for No Kid Hungry fundraising program. SCA has donated $150,000 to date to the No Kid Hungry campaign.
To celebrate its sponsorship, Tork will offer this promotion through the end of 2012. Additionally, Tork will supply custom AD-a-Glance advertisements for Xpressnap dispenser systems to restaurants to help promote the cause. The AD-a-Glance inserts highlight the issue of childhood hunger in America and include a QR code to encourage consumers to donate right from their table.
In America, one in five children – more than 16 million – struggle with hunger, SCA notes. The problem of childhood hunger is not due to a lack of food; rather, the problem is getting the food to where the hungry mouths are—in schools, struggling neighborhoods, parks, and community centers, among other places, it adds.
"SCA's Tork brand is behind the No Kid Hungry campaign because we believe in its goal and its strategy for accomplishing that goal," said Suzanne Cohen, foodservice marketing director for SCA Professional Hygiene. "Many of our customers in the restaurant industry also support No Kid Hungry and have raised millions of dollars to get food where it is needed most. We are proud to be a part of this ambitious yet realistic program to connect America's kids to the healthy food they need, every day."
Dine Out for No Kid Hunger runs from September 16 – 22, with many restaurants promoting the campaign all month, and encourages people to visit the thousands of participating restaurants. In 2011, funds raised through the program were invested in 18 No Kid Hunger state and city partnerships, and community organizations in all 50 states to help connect more at-risk kids to programs like school breakfast and summer meals. The No Kid Hungry campaign focuses on public nutrition programs that effectively keep children and their families from going hungry, yet require additional support to reach everyone who is eligible for them.
"Share Our Strength relies on its partners to help generate needed funds and awareness, and SCA's commitment to the No Kid Hungry campaign takes this partnership to the next level," said Debbie Shore, co-founder of Share Our Strength. "Tork dispensers are found in restaurants and food courts across the country, and the innovative AD-a-Glance displays will bring high visibility to No Kid Hungry. We know that this program is good for business and the community, and SCA will help us share that message with so many people – from the businesses that proudly use Tork dispensers to the countless consumers that see them in restaurants."
Back To Top
|
Sappi Fine Paper North America (SFPNA), Boston, Mass., USA, has announced the eighth episode of its humorous online video series, Off Register™ on The Flo Channel, titled "Kevin Picks the President," an election-inspired episode that makes fun of the sometimes difficult client approval process. Off Register is based on real-life experiences of printers and captures some of the more absurd, yet entertaining aspects of being on press. The new video is available online.
In "Kevin Picks the President," actors from Second City Improv deliver another satirical episode, as they labor over designing the official poster for the next presidential candidate through endless rounds of proofs from the disapproving color dog, Kevin.
"Sappi takes great pride in the role of paper in politics – from posters to direct mail pieces – paper's role in politics is prominent," says Patti Groh, director, marketing communications, SFPNA. "With that being said, we could not help but find a way to bring humor to the current election season by introducing designer dog, Kevin. As the Off Register series continues to be a success with our customers, we're planning to build upon these humorous printing installments with more episodes slated for the future."
Sappi's Off Register not only shares hilarious stories of printing, it also invites the public to share in the fun. The series celebrates the quirks of print production, the personalities people must contend with in the process, and the desire to produce good work despite uncontrollable variables. Sappi continues to invite printers to share their own "'war stories" for future episodes. Story ideas can also be submitted by email.
Back To Top
|
Below is the latest listing of job openings in the TAPPI Career Center. The current listing includes job openings for a variety of pulp and paper manufacturing positions, product marketing manager, shift supervisor, stock prep manager, chemist, sales engineer, director of production planning, and customer service representative. Current, specific job openings at companies and locations in the TAPPI Career Center include:
Employer |
Title |
Location |
AIRTHERM Corp. |
Sales Engineer |
Longview, Wash. |
Albarrie Environ. Serv. |
Product Mktg. Mgr. (Liquid Filt. Media) |
Canada |
Armstrong World Ind. |
Maintenance Mgr. |
Pennsylvania |
Boise Inc. |
Sr. Scientist-Fiber |
Wallula, Wash. |
Celanese |
Chemist II-Paper Lab |
Florence, Ky. |
Confidential |
Pulp & Paper Manufacturing Openings |
Fernandina Beach |
Confidential |
Pulp & Paper Manufacturing Openings |
Hopewell, Va. |
Confidential |
Pulp & Paper Manufacturing Openings |
West Point, Va. |
Confidential |
Pulp & Paper Manufacturing Openings |
Florence, S.C. |
Confidential |
Technical Services Manager |
Columbus, Ohio |
Confidential |
Coatings Scientist |
Columbus, Ohio |
First Quality Enterprises |
Director of Operations |
Lock Haven, Pa. |
Georgia-Pacific |
Mgr.-Process Safety |
Atlanta, Ga. |
GL&V USA |
Sr. Process Engineer- Fiberline Specialist |
Nashua, N.H. |
Longview Fibre |
Dir. Production Planning/Order Fulfillment |
Longview, Wash. |
New-Indy Containerboard |
Shift Supervisor |
Ontario, Calif. |
New-Indy Containerboard |
Stock Prep Mgr. |
Ontario, Calif. |
UPM Kymmene |
Customer Service Representative |
Westmont, Ill. |
More information about these jobs is available online
Back To Top
|
Market Roundup
Wood fiber costs for the world's pulp mills were down again in the 2Q/2012, according to Wood Resource Quarterly (WRQ), Seattle, Wash., USA. Prices for wood chips and pulp logs in both local currencies and in U.S. dollars fell in most of the 17 regions tracked by the WRQ.
Uncertainty in demand for pulp, lower pulp and paper prices, reduced market pulp production, and a healthy supply of sawmill residuals were all factors that put downward pressure on wood fiber prices this spring and early summer. The Softwood Wood Fiber Price Index (SFPI) fell by 4.1% from the 1Q/12 to $100.54 per oven-dry metric ton (odmt). This was the biggest quarter-to-quarter drop since 2008. The biggest price declines for hardwood fiber from the 1Q/12 to 2Q/12 occurred in Brazil, the U.S. Northwest, Australia, and Eastern Canada.
Hardwood fiber prices have fallen even more than softwood fiber prices this year. The Hardwood Wood Fiber Price Index (HFPI) was down 4.4% to $104.88/odmt from the previous quarter. The HFPI has now fallen for three consecutive quarters since the all-time high in the 3Q/11, and in the 2Q/12 was at the lowest level in two years. The largest price reductions from the 1Q/12 occurred in Brazil, Russia, and Australia.
Although Brazilian pulp log prices have not changed much in the local currency, they have fallen dramatically in U.S. dollar terms as the Brazilian real has weakened over the past year. Eucalyptus pulp log prices in the 2Q/12 were down 28% from the same quarter in 2011, while pine pulp log prices declined 26% from a year ago. The recent dramatic price reductions of pulp logs have resulted in Brazilian pulp mills enjoying among the lowest wood costs of all regions tracked by the WRQ, despite being above the global average as recent as 12 months ago.
Wood fiber costs were also down throughout Europe in the 2Q, with the smallest declines (in U.S. dollars) in Finland (-1.3%) and Norway (-3.6%) and the biggest reductions in Spain (-15%) and France (-7.7%). In most markets, wood fiber prices have come back down to where they were in 2010.
More information is available online.
Back To Top
|
North American NBSK (northern bleached softwood kraft) pulp prices averaged $850/ metric ton in August, which was -$30/metric ton compared with July, according to Mark Wilde with Deutsche Bank. August prices ranged between $600/metric ton and $1,100/metric ton, Wilde noted.
Back To Top
|
Newsprint prices in North America averaged $640/metric ton in August, according to Mark Wilde of Deutsche Bank, which was flat compared with July. Prices for newsprint last month ranged between $415/metric ton and $800/metric ton, Wilde reported.
Back To Top
|
Pulp & Paper
The Bank Note Paper Mill has ordered from Voith (Germany) two banknote paper machines for its mill in Mysore, India. The project involves two complete production lines, including all machine clothing. Each of the machines has an annual production capacity of 6,000 metric tons of high-quality banknote paper.
In 2010, Voith had already received an order for the delivery of a complete banknote paper machine from the Indian banknote paper manufacturer SPMCIL in Hoshangabad. Together with the two production lines just ordered, the three machines will be able to cover the current demand for banknotes in India.
Banknote paper machines, Voith explains, have to meet high quality requirements. The paper must be robust, dirt resistant, and moisture repellent. In addition, there are also high security standards regarding the quality and the production of this special material. Banknote paper contains about 200 different security features, such as water marks, fluorescent fibers, or a security thread made of aluminum, which is inserted by the machine during the production process. For this reason, banknote paper machines are usually custom-built items, adapted to the individual requirements and specific conditions of the country where they are operating.
Back To Top
|
BD White Birch Investment LLC, Quebec City, Que., Canada, has completed the acquisition of White Birch Paper Co. Completion of the acquisition represents the successful culmination of a nearly three-year restructuring process, resulting in the formation of a newly revitalized and competitive enterprise.
BD White Birch Investment LLC and its affiliates are producers of newsprint, directory paper, and paperboard, with mills located in Canada and the U.S. It is the second largest newsprint producer in North America.
Commenting on the announcement, Peter Brant, CEO of the new White Birch, said "I am pleased that the conclusion of the restructuring process, together with significant new investment by the Brant Family and the Black Diamond-led investment group, has resulted in a healthier, better capitalized company. The process of turning this company around would not have been possible without the support of our management team, new investors, and the strong belief by all of our employees that this is a vital business that is well positioned to succeed in the global paper market for years to come. "
Christopher Brant, president of the new White Birch, added that "without the contributions of our dedicated employees, our loyal customers and suppliers, our partners at Black Diamond, and the support of the Quebec government, the new White Birch's future would not be nearly as bright as it is today. I would like to thank them all for their tremendous efforts throughout this long and arduous process. As the new White Birch moves forward with our current product portfolio, I am excited about the opportunities we have to develop our operations in new products and modernized platforms. Working together with our superb management team and all of the company's stakeholders, I am optimistic about the future and the long-term viability of the new White Birch."
Back To Top
|
Cascades Inc., Kingsey Falls, Que., Canada, has established a Small Shareholder Program for registered shareholders and beneficial owners of 99 or fewer of the company's common shares as of September 17. The voluntary program allows eligible shareholders to sell their shares without paying a brokerage commission. Shareholders who purchased common shares through the Cascades Employee Share Purchase Plan and who are also currently employed by Cascades are not eligible to participate in the program.
The new program begins September 21 and will expire at 4:00 p.m. Toronto time (EST) on December 17, unless extended. Information about the program and participation documents will be mailed to eligible shareholders.
Back To Top
|
Catalyst Paper, Richmond, B.C., Canada, a producer of specialty mechanical printing papers, newsprint, and pulp, this past week reported the completion of its previously announced reorganization under the Companies' Creditors Arrangement Act of Canada. As a result of the reorganization and related transactions, Catalyst reduced its debt by $390 million, eliminated $80 million of accrued interest, and reduced annual interest expense and other cash costs by approximately $70 million, Kevin J. Clarke, president and CEO, noted.
As part of the reorganization, the company has also entered into the previously announced new asset backed loan (ABL) facility and exit financing facility. Approximately $35 million was drawn under the exit facility upon implementation of the amended plan of reorganization. .
The company's new board of directors as of September 13, in addition to Clarke, is comprised of John Brecker, Giorgio Caputo, John Charles, Todd Dillabough, Walter Jones, and Leslie Lederer.
"As we emerge from creditor protection, I want to acknowledge our former board chairman Jeffrey Marshall and directors Thomas Chambers, William Dickson, Douglas Hayhurst, Alan Miller, Geoffrey Plant, and Dallas Ross for their service to Catalyst Paper," said. Clarke.
Speaking on behalf of the former board, Chairman Jeffrey Marshall commended "the dedication, contributions and unwavering support of Catalyst's employees and management team, unions, customers, suppliers, retirees, and pensioners, as well as the support of the communities where its mills and other facilities are located."
Additional information regarding the amended plan and the company is contained on the Monitor's website and in Catalyst's information circular dated March 23, 2012, also available on the SEDAR website, and Catalyst's web page.
Back To Top
|
Domtar, Montreal, Que., Canada, is joining businesses and individuals around the globe to participate in the Rainforest Alliance's second annual Follow the Frog Week that kicked off Monday of this week (September 17) and runs through this Saturday (September 23). Follow the Frog Week is an international social media campaign that encourages shoppers to help create a healthier planet by choosing products that feature the Rainforest Alliance Certified green frog seal.
The green frog "trustmark," found on coffee, tea, chocolate, fruit, furniture, and paper, is recognized by consumers globally as a symbol of sustainability, Domtar notes. Products featuring the seal come from farms and forests that meet a rigorous set of criteria that protect wildlife, soils, and waterways and the well-being of workers, families, and communities.
"We strive to be the preferred supplier of environmentally sound forest products to our customers, while leaving the smallest environmental footprint and helping them reduce theirs," says Lewis Fix, VP of Sustainable Business and Brand Management. "And, we're happy to participate in this campaign to promote Rainforest Alliance Certified products."
Domtar has worked together with the Rainforest Alliance for many years on responsible paper production and fiber sourcing. In 2005, Domtar and the Rainforest Alliance signed a collaborative agreement when the EarthChoice product line was launched, later renewing the agreement in 2009. Rainforest Alliance applauds the forest management practices that support the Domtar EarthChoice product family. All Forest Stewardship Council (FSC) certified Domtar EarthChoice products proudly bear the Rainforest Alliance Certified seal.
More information about Domtar's sustainability commitment and strategy is available online.
Back To Top
|
Orchids Paper Products Co., Pryor, Okla., USA, was recently awarded Dollar General's 2012 Pride Award - Private Label Vendor of the Year. Orchids received the award at Dollar General's recent Annual Vendor Summit in recognition of its innovation, dependability, and excellence in its partnership with Dollar General.
"We are very proud and honored to have earned this recognition from such a valued customer and partner as Dollar General. Dollar General is a leader in its field and we are honored to be a long-term supplier to their organization," said Robert Snyder, president and CEO. "The award is a testament to the dedication of our team in achieving world class service and innovation to our customers."
Dollar General is the largest value retailer in the U.S. with annual revenue in 2011 of $14.8 billion. It currently has more than 10,000 stores in 40 states.
Orchids Paper Products is an integrated manufacturer of tissue paper products, serving the at-home private label consumer market. From its operations in northeast Oklahoma, the company produces a full line of tissue products, including paper towels, bathroom tissue, and paper napkins, to serve the value through premium quality market segments. The company provides these products to retail chains throughout the U.S.
Back To Top
|
PaperlinX Ltd., Australia, yesterday (September 19), announced that Harry Boon (chairman and non-executive director), Lyndsey Cattermole (non-executive director), and Anthony Clarke (non-executive director) have resigned from the company's board of directors, effective at the close of business on September 28.
The company said that it expects to make further announcements about additional appointments to the board prior to the effective date of the above resignations.
Back To Top
|
Dry weather conditions resulting in extreme forest fire danger have caused Rayonier, Jacksonville, Fla., USA, to close its Western Washington State lands to all general public access, effective immediately. Rayonier owns 390,000 acres of timberlands in Grays Harbor, Pacific, Wahkiakum, Jefferson, Lewis, and Clallam counties in Washington.
"We regret this closure during hunting season, but it is necessary to protect forest lands and the long term economic and environmental benefits dependent on them," said Eduardo Hernandez, Rayonier's Pacific Resource Unit Leader. "We hope the public will recognize the seriousness of the situation and comply with the restrictions."
Rayonier lands will remain closed to general public entry until a substantial amount of rainfall occurs and an announcement is made that the lands have reopened.
Rayonier operates in three core business sectors: Forest Resources, Real Estate, and Performance Fibers. The company owns, leases, or manages 2.7 million acres of timber and land in the U.S. and New Zealand. The company's holdings include approximately 200,000 acres with residential and commercial development potential along the Interstate 95 corridor between Savannah, Ga., and Daytona Beach, Fla. Its Performance Fibers business is one of the world's leading producers of high-value specialty cellulose fibers used in products such as filters, pharmaceuticals, and LCD screens.
Back To Top
|
SCA, Sweden, reportedly has informed employees at its tissue mill in Jönköping, central Sweden, that the plant likely will shut down by year-end. According to a report by papernet.se, all 42 employees at the mill in Jönköping were informed earlier this week that SCA intends to close down the plant. Negotiations with the local unions have already started.
The papernet.se report noted that, according to local media, the mill might be closed before year-end, but that SCA has not revealed an actual shutdown schedule.
The Jönköping mill produces some 25,000 metric tpy of tissue, but does not have converting facilities. It is assumed that SCA wants to concentrate production at the Lilla Edet facility, north of Gothenburg, with a capacity of 110,000 metric tpy. That facility includes a converting plant.
Back To Top
|
SCA, Stockholm, Sweden, has again been included in the Dow Jones Sustainability Europe Index, one the world's most prestigious sustainability indexes. This is the fifth time SCA has been in the index since 2004.
"We are pleased that our sustainability work is being recognized in this way. We are proud to have been included in the index five times during the past eight years. Our sustainability work is an essential part of our strategy for growth and value creation for our business and also for people and nature," said Kersti Strandqvist, SVP Corporate Sustainability at SCA.
SCA is a global hygiene and forest company that develops and produces personal care products, tissue, publication papers, and solid-wood products. Sales in 2011 totaled SEK 106 billion (EUR 11.7 billion). SCA has approximately 37,000 employees.
Back To Top
|
Sequana, France, reports that as part of its strategic plan announced this past July along with a EUR 150 million capital increase, Arjowiggins has presented plans to close the Dalum Papir A/S plant in Denmark (graphic papers), the Ivybridge plant in the U.K. (papers used for security documents, creative papers), and the Witcel plant in Argentina (creative papers). The group's strategic production model is designed to bring capacity into line with demand and reduce its cost structure, and to pursue development in emerging economies and growth markets on the distribution side of the business.
Sequana is a major player in the paper industry with two businesses:
- Antalis, a European leader in the distribution of paper and packaging products, present in 44 countries, with more than 6,000 employees
- Arjowiggins, a world leader in creative and technical papers, with more than 5,200 employees.
The company notes that the particularly tough conditions the paper industry has faced since 2008 have accelerated the fall in demand for graphic papers, with the market contracting by approximately 6% every year. Given the structural decline and overcapacity on the market, Sequana adds, and following the shutting down of a machine at the Chartham plant (creative papers) in the U.K. last month (August), Arjowiggins has decided to continue to adjust its capacity in line with demand and to close the Dalum Papir A/S, Ivybridge, and Witcel operations.
These capacity reductions represent a total of 126,000 metric tpy (including 103,000 metric tpy for Dalum Papir A/S), or around 10% of the group's total production capacity. Thanks to the flexibility of Arjowiggins' production model, all product ranges concerned will be transferred and manufactured at other group plants in France, the U.K., and Brazil, according to Sequana. The closure of the Dalum Papir A/S and Witcel plants should be effective by the end of 2012, and the closure of the Ivybridge plant in the first quarter of 2014. Around 430 employees are affected.
Approximately EUR 25 million will be booked in the third quarter of 2012 to reflect these restructuring operations. Around EUR 8 million of this amount will be disbursed in the last three months of 2012 and most of the remaining balance in 2013. The restructuring measures will result in full-year net cost savings of around EUR 17 million, the bulk of which will be generated beginning in 2013.
Additionally, in line with its development strategy focusing on fast-growing market segments and geographical regions, Antalis has finalized two acquisitions of packaging product distributors, in Chile (Abitek) and in the Czech Republic (Branopac). These acquisitions were carried out for an enterprise value of EUR 17 million and will contribute additional full-year sales of around EUR 15 million.
These operations follow Antalis' early-2012 acquisitions of Ambassador in the U.K. and Pack 2000 in Germany in the same sector, helping it to continue building its presence in packaging distribution, a fragmented market currently growing at more than 5% annually. All of these acquisitions will provide Antalis with additional expertise and a strong platform for launching its packaging business development program in Latin America (it is now No. 2 in Chile) and in Eastern Europe in line with its strategy of expanding in emerging economies.
Sequana reported sales of EUR 3.9 billion in 2011, and employed some 11,000 people worldwide.
Back To Top
|
UPM, Finland, has been selected both as a Supersector Leader in Basic Resources sector and Forestry and Paper Sector Leader for 2012-2013 in the Dow Jones Sustainability Index.
"We are very happy that our work on corporate responsibility is recognized externally in the Dow Jones Sustainability Index. Continuous improvement in our environmental, social,l and financial performance is a fundamental part of UPM's Biofore strategy. During the past year we have focused especially on material and resource efficiency – creating more with less is a key driver for us. I would also like to highlight our company-wide safety initiative that has been a top leadership priority," said Jussi Pesonen, CEO of UPM.
UPM is comprised of three Business Groups: Energy and pulp, Paper, and Engineered materials. The company has production units in 17 countries and employs some 24,000 people worldwide. Its 2011 sales exceeded EUR 10 billion.
Back To Top
|
Weyerhaeuser Co., Federal Way, Wash., USA, again has been included in the Dow Jones Sustainability World Index. Weyerhaeuser was one of only three forest products companies (see SCA and UPM articles above) included in the World Index and one of only two North American companies. Weyerhaeuser also continues to be a member of the Dow Jones North America Index, as it has every year since its inception in 2005.
"We're thrilled the Dow Jones Sustainability Index has once again recognized Weyerhaeuser for our ongoing work to meet important performance, people, and planet goals," said Dan Fulton, president and CEO. "In discussions with our shareholders and key global customers, we've identified the Dow Jones Sustainability Index as the most important third-party validation that we receive. It is our objective to perform within the top quartile among our competitors, and in this case, we are honored to be recognized as being among the top 10 percent of sustainability performers in the world."
The Dow Jones Sustainability Index follows a best-in-class approach and includes sustainability leaders from each industry on a global` and regional level. The annual review is based on an assessment of corporate economic, environmental, and social performance, covering issues such as corporate governance, risk management, customer relationships, climate change strategy, and labor practices.
Back To Top
|
Weyerhaeuser Co., Federal Way, Wash. USA, also has closed its Western Timberlands operations in Washington and Oregon to public access due to the current, extreme forest fire danger, effective immediately. The closure will remain in effect until the operating areas receive adequate rainfall and the temperatures improve.
In Washington, tree farms in the Vail, Aberdeen, Raymond, and St. Helens operating areas will be indefinitely closed to public recreational access. The tree farms in Aberdeen and Raymond will have limited access to walk-in traffic only, but no motorized vehicles.
In Oregon, tree farms in the North Coast, North Willamette Valley, South Willamette Valley, Springfield, and Coos Bay operating areas will be indefinitely closed to public recreational access.
Visitors planning a trip to Weyerhaeuser timberlands in Oregon and Washington are reminded to call the company's statewide, toll-free telephone numbers before heading out to the woods. The Weyerhaeuser Hunter and Recreational Use Hotline numbers are: Oregon—888-741-5403; Washington—866-636-6531.
Weyerhaeuser, one of the world's largest forest products companies, grows and harvest trees, builds homes, and makes a range of forest products. It employs some 12,800 people in 11 countries, and generated $6.2 billion in sales in 2011.
Back To Top
|
Containerboard/Packaging
Mayr-Melnhof (MM) Packaging, Austria, has acquired Plegacol, a Colombian folding carton producer located in Santiago de Cali. Plegacol generates annual sales of approximately EUR 15 million.
The transaction will "concentrate" Plegacol and Gráficas Los Andes S.A., Cali, the largest Colombian folding carton manufacturer, in which MM Packaging already holds a 20% share and an option right to 100%, to form a new Colombian market leader in folding cartons. The entity will generate sales of about EUR 30 million with around 400 employees and convert approximately 16,000 metric tons of cartonboard.
For MM Packaging, the acquisition of Plegacol represents a third step into Latin America subsequent to the acquisition of the Chilean market leader Marinetti in 2010 and the 20% interest in Gráficas Los Andes S.A earlier this year.
"Our goal is to follow our customers into future markets and to create a Latin American network of highly efficient folding carton plants, which we will develop according to best practice of the MM Group," said CEO Wilhelm Hoermanseder about his company's long term strategy.
Back To Top
|
Mondi Group, South Africa, this week signed an agreement with Duropack GmbH, Germany, for the acquisition of Duropack's operations in Germany and the Czech Republic, which consist of two corrugated box plants and one recycled containerboard mill. The two corrugated box plants consume approximately 130,000 metric tpy of containerboard, while the recycled containerboard mill is capable of producing 105,000 metric tpy.
The amount to be paid for 100% of the operations totals EUR 125 million and will be paid in cash at completion. Mondi Group will assume approximately EUR 5 million net cash as of the same date, implying an enterprise value of EUR 120 million. In 2011, the Duropack operations generated unaudited pro forma consolidated revenues of EUR 160 million and unaudited pro forma consolidated adjusted EBITDA of EUR 23 million.
The acquisition is in line with Mondi Group's strategy to strengthen its market position in corrugated packaging in central and eastern Europe. Completion of the deal is conditional on approval by relevant competition authorities and other customary closing conditions.
Mondi is an international paper and packaging group, with production operations in 28 countries and revenues of EUR 5.7 billion in 2011. The group's key operations are located in central Europe, Russia, and South Africa. At the end of 2011, Mondi employed 23,400 people.
Back To Top
|
MeadWestvaco Corp., Richmond, Va., USA, has been featured in the Carbon Disclosure Project's (U.K.) Carbon Disclosure Leadership Index for 2012. The index highlights companies scoring in the top 10% of the S&P 500 based on commitment to climate change disclosures and understanding of the impact of climate change-related issues. MWV scored 93 out of 100, one of only five companies in the materials sector to score this high and the only company in the containers and packaging category to earn a place on the index. The average score for the S&P 500 was 70.
MWV has made a commitment to reduce carbon dioxide emissions 25% by 2015 (versus a 2010 baseline), and currently is on target to achieve that goal. The company is installing a new, state-of-the-art biomass boiler that will burn renewable biomass such as tree bark, wood residues, and waste water residuals at its Covington paperboard facility. The new boiler will replace a coal-fired boiler and further reduce the company's carbon footprint, cutting plant emissions by ˜30%.
"We are taking steps every day to make our operations more efficient and our business more sustainable," said Dirk Krouskop, MWV's VP for safety, health, and environment. "And we're not only letting our customers, investors, suppliers, and communities know what we're up to, we're working to achieve specific targets in partnership with all of these stakeholders. It's an honor to be named on the CDP Leadership Index. It recognizes the work we've done in so many areas to proactively reduce carbon emissions as cost effectively as possible."
Back To Top
|
Sonoco, Hartsville, S.C., USA, has been selected as sector leader in the U.S. Container & Packaging category of the Dow Jones Sustainability World Index (DJSI World) for 2012-2013. DJSI World is comprised of the top 10% best-in-class economic, environmental, and social performers among the world's 2,500 largest companies in 58 different sectors.
"Sonoco strives to be an industry leader in sustainability, so it's gratifying that we have been selected as our industry's leader for the second year in a row," said Harris E. DeLoach Jr., chairman and CEO. "One of the ways in which we measure our sustainability efforts is through the annual review and listing of DJSI World. Sonoco has been listed on the index for four consecutive years, which we believe confirms that we are on the right track in the way we develop products for our customers and in adopting sustainable business practices."
DeLoach also pointed out that Sonoco's overall score for the 2012/2013 index was 36% higher than its comparative industry sector's average score. The company received top scores in its sector for corporate governance—including its anti-trust policy and codes of conduct—and for its customer relationship management and risk and crisis management efforts.
This year's DJSI World includes 41 new companies, while 41 firms will be deleted, resulting in a total of 340 index components. All changes will become effective with the opening of stock markets on September 24. DJSI was the first global index tracking the financial performance of the leading sustainability-driven companies worldwide. Today, the index family has approximately $6 billion in assets under management in a variety of financial products in 15 countries.
Back To Top
|
Stora Enso, Finland, and Packages Ltd. of Pakistan have established a joint venture called Bulleh Shah Packaging. Stora Enso's initial shareholding will be 35% with a commitment to increase the shareholding at the agreed value to 50% at a later stage subject to certain conditions being met. The joint venture will include the operations of the Kasur mill and Karachi plant in Pakistan currently owned by Packages Ltd.
The joint venture will provide packaging products to key local and international customers in the fast-growing Pakistani market. The joint venture will employ about 950 people and its sales are forecast to be $130 million (EUR 99 million) in 2012.
The agreed value for 100% of the joint-venture company is approximately $108 million (EUR 83 million) on a cash and debt-free basis. The total consideration can be up to $125 million (EUR 96 million), including an additional maximum performance compensation based on the financial results of the second half of 2012 and the first half of 2013. As part of the agreement, both parties are committed to a substantial $135 million (EUR 103 million) investment program during 2013 and 2014 to develop the business further.
"This is an example of Stora Enso's investments in value-creating growth markets. The Pakistani market, with growing demand for packaging products and paperboard, offers an attractive growth opportunity for us and the joint venture will enable us to increase our capability to serve our key customers," said Mats Nordlander, EVP, Renewable Packaging Business Area.
The joint-venture transaction is expected to be completed during the first quarter of 2013, subject to competition and regulatory approval and other customary transaction conditions.
Back To Top
|
New Products
NewPage Corp., Miamisburg, Ohio, USA, has introduced OmniPoint™, a new 60 lb. (89 gsm) heavyweight wet strength label paper designed for large glass and plastic containers used in food, beverage, and condiment applications. OmniPoint joins the broader range of label papers from NewPage that includes DuraPoint™, ProPoint™, LithoPoint™ and EcoPoint™ product brands.
With specific expertise and technological capabilities in manufacturing wet strength label papers for the food and beverage market, NewPage said that its product development team set its sights on developing a new heavyweight label paper that maintains a premium appearance, and consistently performs well in all aspects of production, from label printing to die cutting and high speed label application.
"We worked closely with our customers to develop a heavyweight label paper solution that meets their needs for consistent quality, durability, and label converting performance, while allowing them to deliver the best possible label graphics for their food and beverage brand owner customers," said David Diekelman, executive director of sales and marketing for specialty papers. "OmniPoint achieves these critical objectives."
OmniPoint is available with third-party chain-of-custody certifications to the Forest Stewardship Council (FSC), the Sustainable Forestry Initiative® (SFI), and the Programme for the Endorsement of Forest Certification (PEFC™).
NewPage is a producer of printing and specialty papers in North America with $3.5 billion in net sales for 2011. The company owns paper mills in Kentucky, Maine, Maryland, Michigan, Minnesota, and Wisconsin. These mills have a total annual production capacity of approximately 3.5 million tons of paper. The company's product portfolio is the broadest in North America and includes coated, specialty, supercalendered, and uncoated papers.
Back To Top
|
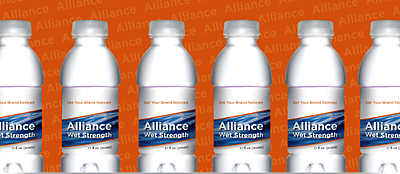 Twin Rivers Paper Co., South Portland, Maine, USA, a producer of lightweight specialty packaging, label, and publishing papers, has launched a new mold-resistant label paper known as Alliance® WS AM. The highly-engineered wet-strength label papers are formulated to meet stringent customer requirements for mold-resistant products. Offered in a broad range of basis weights (44, 47, 51, and 60 lb.), the new papers provide optimized wet-strength chemistry to perform throughout the rigors of the supply chain.
"By leveraging our advanced coating expertise, we have developed Alliance® WS AM, a label paper that offers superior mold protection in high humidity climates while maintaining the same high quality standards people have come to expect from our wet-strength label papers," says Dave Deger, director of business development and marketing.
Back To Top
|
Verso Paper Corp., Memphis, Tenn., USA, has introduced Aspect™ SCK Release Papers, a new addition to its Aspect line of label and release papers. Now comprised of cut and stack labels, pressure sensitive face sheets, and SCK release liners, Verso's Aspect Label and Release Papers deliver the aesthetics, strength, and performance required for quality and efficient label production, the company notes.
"Our premium SCK Release Liner is a high performing, extremely efficient, and cost effective liner, allowing lower silicone coat weight and reduced adhesive usage due to better, more consistent profiles," says Mike Weinhold, Verso's SVP of sales, marketing, and product development. "With a perfect balance between desired optical properties, performance requirements, and cost effectiveness, our Aspect SCK Release Liner is sure to become the industry standard."
Aspect™ SCK Release Liner has high strength, superb apparent density, low dirt count and opacity, exceptional die-cutting performance, excellent cure and holdout, and smooth surface characteristics.
The Aspect product line will be produced on the No. 4 paper machine at Verso's mill in Androscoggin, Maine. "Androscoggin's No. 4 paper machine is a well-positioned asset, with relative machine scale and an integrated pulp supply," Weinhold explains. "Androscoggin, like all of our mills, has a strong manufacturing focus on producing consistent, quality products, and our Aspect line of label and release papers is no exception. We understand our customers want a product and a supplier they can rely on, and Verso delivers on both of those needs," he says.
Back To Top
|
Voith, Germany, has launched its newly-developed Revolution press felt for board and packaging paper machines. Along with increased drying performance, Voith notes that Revolution ensures shorter startup phases, energy savings, and consistent quality characteristics over its entire service life.
The key innovation of Revolution is its structure, which has a special polymer layer, according to Voith. The felt can thus control the flow of water before, during, and after passage through the nip. This allows it to dewater better and contaminate less. The dry content is higher by up to 2% than with a conventional felt. The self-cleaning effect also helps to ensure that felt performance remains the same over its entire service life.
Voith further points out that paper produced with the aid of Revolution has especially good surface characteristics due to the larger contact surface with the paper or board web, adding that practical testing confirmed that the new felt allows substantially shorter startup times. From the beginning, it says, the level of nip dewatering is very high. Revolution thus has a positive effect on energy balance.
Back To Top
|
Energy
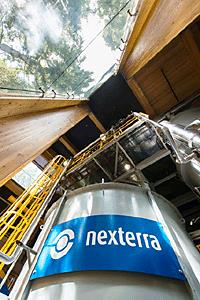 Nexterra Systems Corp. Vancouver, B.C., Canada, the University of British Columbia, and GE this past week celebrated the successful completion of an energy-from-renewable-waste combined heat and power (CHP) system located at UBC's Vancouver campus. This is North America's first commercial demonstration of a transformative system that combines Nexterra's gasification and syngas conditioning technologies with one of GE's high-efficient Jenbacher internal combustion engines.
GE's Jenbacher gas engine will produce 2 MW of clean, renewable electricity that will offset UBC's existing power consumption, enough to power approximately 1,500 homes. The Nexterra system will also generate 3 MW of thermal energy, enough steam to displace up to 12% of UBC's natural gas consumption. This will reduce UBC's greenhouse gas emissions by up to 5,000 metric tpy, the equivalent of taking more than 1,000 cars off the road.
The successful startup of the project at UBC, officially named the Bioenergy Research and Demonstration Facility (BRDF), represents an important milestone in Nexterra's quest to reliably convert low-value waste feedstocks into higher value renewable fuels and chemicals. The system has completed a comprehensive testing program for reliability, capacity, and emissions, and has successfully connected to the grid.
Using Nexterra's proven gasification technology platform and innovative gas cleanup and thermal cracking solution, the system converts locally-sourced waste wood into a clean, reliable gas that is suitable for use in a high-efficiency, industrial-scale gas engine to produce heat and power. The system will deliver global electrical efficiencies that are 25% higher than traditional methods for producing biomass-based electricity at this scale.
Startup of the system represents the culmination of more than four years of product development work and collaboration with GE's Gas Engines business. Prior to installing the gas engine at UBC, Nexterra successfully completed more than 5,000 hr of trials at its Product Development Center in Kamloops, B.C.
Designed by McFarland Marceau Architects, UBC's CHP bioenergy system is housed in a building that was constructed using cross-laminate timber (CLT), a new solid wood building material that can be used as a low carbon, renewable alternative to steel frame construction. This will be one of the first CLT buildings in North America and will demonstrate its market potential for the forest industry.
Funding support for this project was provided by: the Government of Canada (Natural Resources Canada and Western Economic Diversification Canada); the Province of British Columbia (B.C. Innovative Clean Energy Fund and the Ministry of Forests, Mines, and Lands); Sustainable Development Technologies Canada (SDTC); the BC Bioenergy Network; and FP Innovations.
Back To Top
|
People
Packaging paper producer Billerud AB, Stockholm, Sweden, has set the number of its board members to a total of eight, with no deputies. The company subsequently elected Hannu Ryöppönen, Mia Brunell Livfors, Wilhelm Klingspor, and Mikael Larsson as new members of the board.
Current board members, except Jan Homan, Lennart Holm, Gunilla Jönson, and Michael M.F. Kaufmann, have said they will resign once the appointment of the new board members takes effect. The company elected Ryöppönen as chairman of the board.
Changes to the board of directors becomes effective when Billerud closes its acquisition of Korsnäs, as announced this past June. Once the resolution becomes effective and until the close of the next Annual General Meeting, the board will consist of Ryöppönen (chairman), Livfors, Klingspor, Larsson, Homan, Holm, Jönson, and Kaufmann.
Back To Top
|
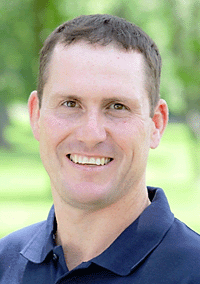 Finch Paper LLC, Glens Falls, N.Y., USA, has appointed Michael McLarty VP of Forest Management and Wood Procurement. In this role, McLarty will oversee Finch Forest Management and its staff of professional foresters, as well as lead the wood sourcing team to secure and sustain timber sourced from local, Northeastern forests.
McLarty is a registered professional forester from Northwestern Ontario with more than 15 years of experience in the forest industry. He was most recently the timberlands manager for Northern Pulp Nova Scotia Corp., where he managed fiber procurement and forestland and the company's forest seedling nursery. Prior to moving to Nova Scotia, he was employed with Kimberly-Clark, Neenah Paper, and with Buchanan Forest Products, where he was responsible for forest management activities on both the Ogoki and Kenogami Forests. McLarty is also experienced in strategic, long-term timber harvest planning, regeneration, and silviculture programs.
McLarty succeeds Roger Dziengeleski, who recently retired from Finch Paper after 33 years of service. During his tenure, Finch became a leader in sustainable forestry standards and launched the innovative Finch Forest Management division, which provides consulting forestry services to landowners across the Northeast.
Finch Paper President and CEO Joseph F. Raccuia said the addition of McLarty to Finch's senior leadership team will help drive the company's sustainability initiatives and further establish Finch Forest Management as an ever-growing, profitable segment of Finch Paper.
"Finch was the first integrated paper mill in the U.S. to receive both Forest Management and Chain-of-Custody certifications from the Forest Stewardship Council and is one of only a few paper companies with an active forestry staff. I'm happy to have Mike continue our industry leading forestry efforts," Raccuia said, adding that with its new Family Forest Owner program, Finch is again leading the way in helping small landowners meet certification standards and obtain premium market value from their wood.
Finch Paper operates a single, fully-integrated pulp and paper manufacturing facility in Glens Falls, at which it produces more than 255,000 tpy of uncoated printing papers for marketing, book publishing, and business office purposes.
Back To Top
|
Travels with Larry
The date of August 16th has a special meaning to me. This date happens to be the day, in different years, when the Sultan of Swat, Babe Ruth, and the King of Rock-N-Roll, Elvis Presley passed away. Both of these men were leaders in their chosen profession. Although many have tried to mimic them over the decades, they both represent the gold standard in their chosen fields.
This past August 16, 2012, Eric Fletty and I had the pleasure of visiting another leader in its chosen field—NALCO, a newly acquired Ecolab Company. Ecolab realized that a very good way to increase its business was to expand outside of its historic markets, in this case the pulp and paper industry.
We actually received two separate invitations—by TAPPI members Steve Govoni and Garnet Bremner—to visit NALCO's headquarters in Naperville, Ill.
Nalco has been a staple within TAPPI and our industry for years. It has been a TAPPI Sustaining Member Company since 1949. The company's tag line is Essential Expertise for Pulp and Paper. NALCO's longest tenured TAPPI Member is Ollie O'Neal. Ollie has been a member since January 1, 1981.
Steve Govoni was kind enough to assemble a group of approximately 20 employees who wanted to hear an update on how best to utilize their memberships in TAPPI. During this meeting, we heard some great testimonies on what they liked best over the years with TAPPI as well as several recommendations on how we might improve TAPPI. These types of meetings have impacted how we run TAPPI and have played a big role in TAPPI being in the black for five years in a row.
NALCO approaches its business demonstrating cost improvement opportunities in the areas of Raw Material, Water and Energy, Chemicals, and Efficiency. The company has several case studies available that demonstrate numerous ways it delivered in each of these areas.
Steve was kind enough to take us on a tour of Nalco's offices and research labs. It was apparent from the start they are looking to invent delivery systems that work in conjunction with their chemicals that will enhance machine efficiencies in the mills.
One of Nalco's latest innovations is OxiPRO™ Technology for Deposit Control. It combines NALCO's proprietary and proactive monitoring tools, individually tailored chemistry strategies, and local application expertise to improve machine efficiency.
NALCO was clear that it does not just sell chemicals. It sells an innovative, integrated solution approach to its customer base. This statement was explained with Nalco's PARETO Mixing Technology that has been specifically designed to reduce the inefficiencies and challenges inherent in traditional papermaking methods.
Our thanks to all of the TAPPI members who were able to join us and to NALCO for allowing us the time for this visit and for being a TAPPI Sustaining Member Company for 63 years.
In the photo below are (l-r) Brett Brotherson, Ollie O'Neal, Paul Richardson, Linda Strysik, Ross Gray, Steve Govoni, Larry Montague, Dorota Smoron, William Johnson, Shawnee Wilson, Chris Kaley, Zhiyi (Jerry) Zhang, Jane Wong Shing, Laura Rice, Ray Miller, and Liliya Lund. Not pictured is Eric Fletty, who served as our camera man.
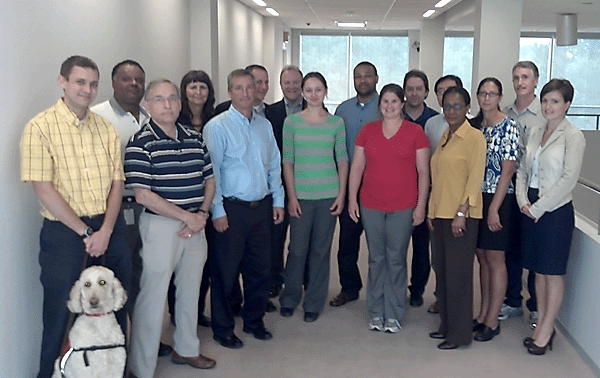
More information about NALCO is available online.
More information about TAPPI or how your company can become a TAPPI sustaining member is also available online.
Remember, there are two types of people in our industry—TAPPI members and those who should be.
Until next time.......................
Larry
Back To Top
|
TAPPI News
SuperCorrExpo, Oct.1-4, 2012, in Atlanta, Ga., USA, is your one-stop shop for all things corrugated. In addition to the nearly 300 exhibitors on the show floor, you can also take advantage of the pre-conference workshops, the joint TAPPI/AICC conference program featuring six keynote presentations and eight multi-track workshops, as well as countless networking opportunities like the Welcome Reception at 200 Peachtree on Sunday, September 30.
And, just added to the jam-packed program, there is now a Folding Carton Workshop sponsored by PIRA. Join Strategic Consultant Dr. Graham Moore on Thursday, October 4, as he provides an overview of the carton board sector and insight into the value added innovations that are attracting attention in the carton board market and increasing the functionality of the products. A separate registration is required for this workshop.
See for yourself why SuperCorrExpo is One Week. One Conference. One Can't Miss Event!
Register today!
Back To Top
|
Discounted Registration for PEERS and IBBC has been extended to September 21. In addition, discounted hotel rooms at the host hotel, the Savannah Marriott Riverside, are available on a first-come, first-serve basis through September 21.
New Program Addition: Safety Training Session (Session 13 led by Matthew Kanneberg, RockTenn) an interactive training session sponsored by the Pulp and Paper Safety Association exploring the four (4) stages of safety learning and help participants identify their current organizational safety level. This analysis will identify actions needed to support an injury free team from planning through implementation to delivering safe solutions throughout the organization.
PEERS is a "must attend" event for anyone seeking to make their mill run more efficiently. The Pulping Program focuses on ways to improve kraft pulping to afford pulps that are more uniform in quality and to afford higher pulp yields. The Engineering Program has added a focused one-day session focusing on OpEx Maintenance and Reliability. The Environmental Program will address the challenges and costs involved in keeping up with the regulations of the U.S. paper industry. The Recycling Program brings together experts from around the world to present new technological breakthroughs related to fractional pulping, absorption deinking and electrostatic deinking. Keynote Speaker Don Roberts will discuss why the pulp and paper industry should be open to change by presenting a case study in commercializing an emerging bio-energy technology and the key success factors as part of the Sustainability Program.
PEERS is co-located with IBBC, the only conference that is dedicated to examining applications of biorefineries in the pulp and paper industry - offering you a deeper analysis of technology and economics in commercializing biorefineries. See the Full Program.
Back To Top
|
If you've ever wanted to feel more confident in working with important financial information at your mill, understanding the costs of running operations, or perhaps in putting the financial structure behind an idea, this course is for you.
The Financial and Strategic Analysis Workshop for Pulp & Paper and Related Industries is taught by instructors with decades of leadership in the business operations of the pulp and paper industry.
North Carolina State University and TAPPI have partnered to offer this exceptional course scheduled for October 3-5, 2012, in Raleigh, N.C., USA.
You'll learn both basic and sophisticated tools to help you analyze and manage important financial information with more confidence.
Understand the critical role of reinvesting in pulp and paper mill assets to ensure long-term survival and prosperity
- Study basics of capital budgeting, cost of capital (cost of debt and cost of equity), and financial indicators to allow you to use these tools to build financial analyses and sell your ideas, products, and services
- Appreciate the importance of cost structure and how you can increase your competitive advantage by managing your costs
- Explain in financial terms the impact of your operation, research, new technique, or new product
- Build an entire financial analysis from the ground up
- Learn the basics for strategic planning and decision making.
Learn more about the instructors and curriculum with this printable schedule.
Back To Top
|
The Corrugated Containers Manufacturing Process
Authors: Jody A. Brittain, Stephen R. Perkins, and Philip G. Schnell
This comprehensive textbook describes the entire process of manufacturing corrugated containers. In addition to detailed explanations, the book also features practical troubleshooting tips and a discussion of common problems and solutions within each major section. Seven detailed chapters cover the following topics:
- Paper and the Papermaking Process
- Steam
- Corrugating Adhesives
- Singleface Operations
- Doublebacker Process
- Combined Board
- Converting.
This textbook is designed to provide in-depth explanations and information for professionals working in all areas of the corrugated containers industry.
Product Code: 0101R281
Member Price: $37.00
Non-Member Price: $185.00
Back To Top
|
Join us at this new lovely golf center near Memphis, Tenn., USA to hit a bucket of balls and enjoy food and fellowship at our Driving Range Fundraiser. Proceeds will support scholarships at Christian Brothers University Packaging Program.
The event will be held in Cordova, Tennessee on October 22 from 5:30 - 9:30pm.
Prizes all for a great cause!
- Team & Individual Events
- Longest Drive
- Nearest the pin
- Silent Auction
- Golf Trivia
- And much, much more...
Visit www.tappi.org/CBUFundraiser for more information and to learn about sponsorship opportunities.
Back To Top
|
You're invited to the 7th Annual Pacific Section Golf Tournament! This event will be held on September 28, 2012 (Friday). Start time is 1:00 p.m. at the Lewis River Golf Course.
The tournament format is a Modified Shotgun Start, four-person scramble with 144 spots open - First Come/First Serve. The entry fee is $125/person, which includes green fees, cart, two beverage tickets, prizes, a meal afterwards, and most of all... lots of fun!
Awards: 1st Place Team, 2nd Place Team, 3rd Place Team, M/W Longest Drive, KP, Longest Putt. Also enjoy door prizes and a raffle!
Proceeds go to the Pacific Section TAPPI scholarship fund!
Questions? Contact Vince Hochanadel via phone (360) 901-1680 or via email: vince.hochanadel@gmail.com.
Additional details and the registration form can be found here on the TAPPI website.
Back To Top
|
Lake States TAPPI/North Central PIMA will host the 13th Annual "Guns of Navarino" on Tuesday, September 25, at J&H Game Farm in Navarino, Wis., USA. This event is designed to help relieve work related stress through a series of team building activities culminating in an evening of social interaction. Sounds good, doesn't it? Just ask anyone who has been to one of our past outings.
This event will begin at 11:30 a.m. on September 25, and the actual tournament gets underway as soon as teams assemble, at approximately 12:30 p.m. The format will be five-person teams. Individual shooters and teams of less than five are also welcome. We will make every effort to have complete teams of five for the competition. Registration is limited to the first 30 teams (150 shooters). The cost for the event will be $120.00 per person ($600.00 per team). Registration includes the following:
- Sporting clays, five-stand, wobble events
- Ammunition for both shooting events
- Dinner (picnic/tailgate style)
- Cash prizes for top team and Individual
- Raffle prizes
- Shotgun Raffle.
Lunch will be provided before the shoot, starting at 11:30 a.m. There will be a cash bar available after the shooting portion of the program concludes. No alcohol will be served until you have completed the shooting portion of the outing. Prizes will be awarded following the completion of the day's shoot.
Don't Delay. Assemble your Teams Today!
Event information is available here.
Registration Information is available here.
Back To Top
|
Are you someone who could benefit from an overview of the entire pulping and paper-making process?
If so, The 2012 TAPPI Hands-On Workshop for Pulp and Paper Basics might be the perfect course for you to learn about the fundamental processes and operations of the pulping and paper-making industry. This year's workshop runs from October 1-5 at North Carolina State University in Raleigh, North Carolina, USA. Reserve your place now so that you can:
- Find out how different processes affect paper properties
- Perform hands-on laboratory experiments to support your understanding of the process
- Run a pilot plant paper machine
- Solidify your knowledge from close interaction with professors in small, interactive groups
Be among the first 32 people to register for this five-day workshop, and you will gain an invaluable overview of pulping, bleaching, chemical recovery, recycling, paper-making and converting. You'll receive course notes, an accompanying CD-ROM, and your own polo shirt. You will also have the opportunity to earn 3.7 CEUs.
This workshop is ideal for new process engineers, manufacturing operators and technicians, sales and service personnel, machine operators, and maintenance personnel. Everyone who wants a better understanding of the basic operation of the pulp and paper business will benefit from this course.
This course typically fills quickly, so don't wait long.
We look forward to seeing you in Raleigh this October!
Back To Top
|
Biomass Subcommittee Hosts Webinar Featuring Biomass Modeling Tool
As the competition for biomass increases, there is a growing need to more rigorously understand and predict supply availability, sustainability, and economic feasibility of biomass sources. This is true for existing pulp mills as well as new biorefineries.
TAPPI's Biomass Supply, Handling & Handling Subcommittee is hosting a webinar for their next subcommittee meeting featuring a new modeling tool available from Enegis: Biomass Energy Analytical Model (BEAM). BEAM can assess biomass energy availability, including transport options and delivery costs, modeling resources from field/forest, through processing, to determining demand - providing a geographic quantification, storage, and densification options as well as transportation analysis.
The model has a 30 meters resolution for the lower 48 states, and currently carries about 50 species and commodities as it performs analysis with costs of net energy and net carbon carried forward at all modeling steps. BEAM can conduct assessments on a site-specific, regional, or national-scale. Focus on residuals, consistent with the American Council on Renewable Energy (ACORE) proposed definition of biomass, has been run in a number of cases including mark to market. BEAM was originally developed for the Federal Energy Management Program.
Please come join us for the next subcommittee meeting and this presentation on Tuesday, October 9th from 1:00-2:00 PM.Subcommittee Chair Bob Hurter and Vice-Chair Bill Fuller will provide an update on subcommittee activities.
Webinar Registration
- This webinar is free to all TAPPI members. Click here to register for this one-of-a-kind opportunity to learn about cutting-edge technology and commercial strategies as it relates to new business opportunities in the biomass sector.
Back To Top
|
TAPPI's International Bioenergy and BioProducts Conference, October 17-19, 2012 in Savannah, Ga., USA will focus on advancements and commercialization of bioconversions that leverage the forest products manufacturing infrastructure, providing you with a deeper analysis of the technology and economics involved in commercializing biorefineries. Click here to learn more about the IBBC full technical program.
Keynote Speakers:
- Paul Spindler, VP of Technology at Catchlight
- John B. Crowe, Chairman and CEO, Buckeye Technologies, Inc.
In addition, IBBC will include technical presentations, expert panels, case studies, and reports from projects that address:
- Feedstock and harvesting improvements to increase yield and quality of biomass
- Bioconversion technologies for wood and biomass
- Production of chemicals and transportation fuels from wood and biomass
- Commercial bioenergy products using woody biomass
- Tools for evaluating bioenergy projects.
IBBC will be co-located with the TAPPI PEERS Conference, creating a value-added opportunity for participants to expand their learning, networking, and resources by attending both events.
Exhibit and Sponsorship opportunities are available. Contact Shane Holt via e-mail or at 800.369.6220, ext. 3345 for more information.
Back To Top
|
The 2012 TAPPI Internatioal Bioenergy & Bioproducts Conference, taking place October 17-19 in Savannah, Ga., USA, offers you a deeper analysis of technology and economics in commercializing biorefineries. IBBC is the only event dedicated to advancing biorefineries in the forest products industry. Hear the latest on biomass development, as well as the thermochemical and biochemical-based technologies that can be profitably integrated into pulp mills.
Please note that discounted registration for IBBC has been extended to September 21. In addition, discounted hotel rooms at the host hotel, the Savannah Marriott Riverside, are available on a first-come, first-serve basis through September 21.
Program Highlights:
Session 4: Bioenergy Policy: Three Perspectives
Panel Moderator: Steve Betzler - Paper Segment Leader, Minnesota Power
Wednesday, October 17, 2012 - 4:00-5:30pm
Panel Themes: What role can government policies play in the development of bioenergy in the forest products industry in North America? Come and hear three policy experts assess recent bioenergy policy impacts and discuss future priorities for Canadian and US policies. Panelists include representatives of two forest industry public policy organizations (FPAC and AF&PA) and a representative of a major industrial forestland owner. A timely topic for the election seasons in North America...
Panelists:
Catherine Cobden - Executive VP, Forest Products Association of Canada
Mike Jostrom - Director Renewable Resources, Plum Creek
Paul Noe - Vice President for Public Policy, American Forest & Paper Association
Learn more about IBBC.
Click here to see the entire program.
Back To Top
|
Gain a better understanding of kraft pulping operations and the effect of process on quality.
An encore, one-day presentation of the popular Intro to Kraft Pulping Workshop will be held in conjunction with the 2012 TAPPI PEERS Conference, October 14-17 in Savannah, Ga., USA. This workshop, held on Saturday, October 13, will be lead by Dr. Michael J. Kocurek, Professor Emeritus of Paper Science and Engineering at North Carolina State University.
The Intro to Kraft Pulping Workshop is a condensed version of the pulping portion of the full course. The overall course objective is to give participants increased understanding of kraft pulping operations, awareness of how one part of the process affects other operations, and the effect of processes on kraft pulp quality.
Learn more about this workshop.
Pulp and Paper Companies Get Discounted Registration!
TAPPI offers a discounted registration to pulp and paper mills and their corporate offices to attend the PEERS Conference. Bring an unlimited number from your mill or office to visit for one day, one hour, or just to drop in and see the Trade Fair! Learn more.
Register Now for PEERS and Save!
The 2012 TAPPI PEERS Conference will be co-located with the International Bioenergy and Bioproducts Conference, creating a value-added opportunity for you to expand your learning, networking and resources by attending both events.
See you in Savannah!
Back To Top
|
Operating Excellence (OpEx) Maintenance and Reliability Seminar at PEERS
This is a first-time program for the 2012 TAPPI PEERS Conference.
Maintenance and reliability continue to be critical to the efficient operation of pulp and paper mills worldwide, just behind fiber and labor as top production cost factors.
This one-day seminar explores the latest reliability strategies today's mills are implementing to stay in-tune and competitive under progressively lean operating conditions.
The OpEx Maintenance and Reliability Track, included in your PEERS registration at no extra cost, is part of the Engineering Program.
If you are only interested in attending the OpEx Track, select the Single Day PEERS Registration for Thursday, October 18. This year's PEERS Conference includes a full program of educational opportunities for maintenance and reliability personnel, including:
- Sunday, Oct. 14: Fixed Equipment Maintenance Optimization System Course (Additional Fee)
- Monday, Oct. 15 - Wednesday, Oct. 17: Corrosion & Materials Engineering Track
- Thursday, Oct. 18: OpEx Maintenance and Reliability Track.
In addition, 2012 TAPPI PEERS Conference, October 14-17 in Savannah, Ga., features a detailed technical program. Five programming tracks of peer-reviewed sessions, Pulping, Engineering, Environmental, Recycling and Sustainability, will answer the most pressing business and technical questions faced by pulp and paper companies as they manage raw materials, assets, regulatory requirements and production assets.
Register now and save.
The 2012 TAPPI PEERS Conference will be co-located with the 2012 International Bioenergy and Bioproducts Conference, creating a value-added opportunity for you to expand your learning, networking, and resources by attending both events.
See you in Savannah!
Back To Top
|
Attend the Fixed Equipment Maintenance Optimization System Workshop (FEMOS)
Sunday, October 14, 2012; 8:00 a.m. - 5:00 p.m.
Mills annually spend millions of dollars inspecting, repairing, and recovering from unexpected leaks in boiler tubes, tanks, pressure vessels, exposed and buried pipes, stacks, bleach towers, etc. – learn how to substantially reduce those costs! Corrosion Probe Inc.'s FEMOS Workshop training shows maintenance staff how to rationally manage the mechanical (containment) integrity of all types of fixed equipment with a simple, rigorous system utilizing comparable disciplines and procedures promoted by vendors specializing in maintenance of rotating equipment.
What will you learn?
The workshop teaches attendees how to implement a mill-specific program by using a transparent and disciplined process to systematically design the right inspection plan for each major piece of fixed equipment based on its materials of construction, present condition and service conditions. The basic concept employs proven, high-value practices from refining and petrochemical industries for risk-based inspection, customizing inspection plans to possible damage mechanisms and using fitness-for-service engineering assessments to define damage limits.
Who is leading the workshop?
Corrosion Probe Inc.'s experienced and renowned TAPPI participants Dave Bennett, David Crowe, and Doug Sherman, will train up to 20 people in a one-day (6-hour) workshop. Training is presented so attendees can use their new knowledge to immediately implement FEMOS at their mill. Many working examples are provided and students are invited to bring their mill's costliest fixed equipment inspection/ maintenance concern for case analysis.
The workshop takes place just before the TAPPI PEERS and IBBC conferences so those attending the FEMOS workshop can also attend these important events.
Learn more about PEERS 2012...
Back To Top
|
On Nov. 7-9, 2012, TAPPI will conduct its Tissue Runnability Course in Neenah, Wi., USA.
This special course is being taught by technical experts in each area of the machine from wet end operations through creping and process control. The experienced, highly qualified faculty for this course will provide a thorough understanding of the entire tissue making process and current best practices in each area.
Wednesday's (November 7) classes will focus on stock preparation and wet end operations, while Tuesday's (November 8) classes cover pressing, drying, and doctoring. Wednesday (November 9) classes examine technologies and latest developments in hoods, TAD (through-air drying), and other dynamics of the tissue machine dry end,
The 2012 TAPPI Tissue Runnability Course is designed for process engineers, machine supervisors, and reliability professionals who have to maximize uptime and saleable production. It is also an excellent tutorial for suppliers who support tissue making customers. It will help attendees:
- Improve tissue quality and consistency
- Understand contributors to waste and downtime
- Learn reliability and maintenance best practices
- Diagnose and troubleshoot problems quickly.
After successfully completing this course, attendees will specifically be able to:
- Diagnose the impact of recycled furnishes on tissue properties
- Make changes to wet-end chemistry to improve machine operations
- Improve cleaning and conditioning of fabrics
- Troubleshoot runnability problems in the press, Yankee, and creping systems
- Identify improvement opportunities on the dry end
- Pinpoint productivity opportunities in Yankee steam, coating, and hood systems.
TAPPI will award CEU credits to participants who attend at least 80% of the educational sessions and complete a final program evaluation.
The 2012 Tissue Runnabilitry Course includes advanced process instruction. If you are looking for an introductory-intermediate tissue course, consider the upcoming 2012 Tissue Properties and Manufacturing Course at TAPPI Headquarters in Norcross, Ga., USA, on August 15-16.
Attendance for the 2012 TAPPI Tissue Runnability Course is limited, so please register today at the course website.
Back To Top
|
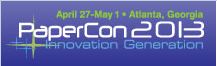
A Call for Papers has been issued for PaperCon 2013. Theme is "Innovation Generation."
After record attendance in 2012, PaperCon will again bring together CEOs, mill managers, superintendents, scientists, process engineers, and suppliers for the largest pulp and paper technical program in the world. The event will take place April 27 to May 1 in Atlanta, Ga., USA. Learn more about PaperCon 2013.
For 2013, PaperCon is pleased to welcome the Tissue360 Forum, NETInc (Innovative Nonwovens Conference), RPTA (Recycled Paperboard Technical Association) P-T Seminar and the OpEx Reliability Workshop. Each of these events is open to full PaperCon registrants and papers in these areas are welcome.
Calls for Papers and Posters have been issued. The conference theme is Innovation Generation, and authors are encouraged to include this within their papers. Topics under consideration include mill management, papermaking, coating, tissue, nonwovens, and recycled paperboard. Paper company personnel, suppliers, academics, and students are strongly encouraged to submit their ideas for papers, posters, or roundtable discussions.
Papermakers Program:
The Papermakers Program encourages topics on paper machine performance evaluations, papermaking fundamentals, product/process optimization, recycled paperboard, tissue making (Tissue360 Forum), and the RPTA P-T Seminar. The deadline for submission of abstracts is November 20, 2012. Abstracts for panel discussions and roundtables are welcome. See Papermakers Program Call for Papers.
Coating and Graphic Arts Program:
The Coating and Graphic Arts Program will focus on The Future of Print and its Demands on Paper and Coatings. The deadline for extended abstracts for this program is Oct. 16, 2012. See the Coating and Graphic Arts Program Call for Papers.
All abstracts must be submitted using TAPPI's Speaker Management System for consideration by the TAPPI and RPTA program committees.
Back To Top
|
Frank Romano to Keynote at PaperCon 2013
Frank Romano, Professor Emeritus, Rochester Institute of Technology, will Keynote at Papercon 2013 on Sunday, April 21. Focusing on "Innovation and the Future of Print," Romano will kick-off PaperCon's Coating and Graphic Arts Program.
Romano's career has spanned an impressive 53 years in the printing and publishing industries. Many know him as the editor of the International Paper "Pocket Pal" for 30 years, or have read one of the thousands of articles he has written. He is the author of 52 books, including the 10,000-term Encyclopedia of Graphic Communications (with Richard Romano), the standard reference in the field.
Learn more about Romano.
PaperCon 2013 will take place April 27 through May 1 in Atlanta, Ga., USA. Designed by industry professionals, PaperCon brings together CEOs, mill managers, superintendents, scientists, process engineers and suppliers for the largest pulp and paper technical program in the world. No other event provides such a comprehensive program, networking opportunities, and trade fair among such a distinguished group of industry leaders.
Learn more about PaperCon 2013.
Registration information, including special mill reservation deals, are now available at the PaperCon website.
Back To Top
|
The 20 volumes of Papermaking Science and Technology bookseries cover the entire paper manufacturing process from wood raw material to end product, providing a basis for university-level education, for updating training courses, and as handbooks for the industry. The bookseries has been updated and second editions are now available. TAPPI members can place an order by contacting The Finnish Paper Engineers' Association. Please contact Mary Anne Cauthen, Member Group Coordinator, at +1.770.209.7352 or by e-mail at MCauthen@TAPPI.org
These books can be purchased individually or as a set.
This 20 volume set includes:
- Volume 1 - Economics of the Pulp and Paper Industry
- Volume 2 - Forest Resources and Sustainable Management
- Volume 3 - Forest Products Chemistry
- Volume 4 - Papermaking Chemistry
- Volume 5 - Mechanical Pulping
- Volume 6, part 1 - Chemical Pulping Part 1, Fiber Chemistry and Technology
- Volume 6, part 2 - Chemical Pulping Part 2, Recovery of Chemicals and Energy
- Volume 7 - Recycled Fiber and Deinking
- Volume 8 - Papermaking Part 1, Stock Preparation and Wet End
- Volume 9 - Papermaking Part 2, Drying
- Volume 10 - Papermaking Part 3, Finishing
- Volume 11 - Pigment Coating and Surface Sizing of Paper
- Volume 12 - Paper and Paperboard Converting
- Volume 13 - Print Media - Principles, Processes, and Quality
- Volume 14 - Process and Maintenance Management
- Volume 15 - Materials, Corrosion Prevention and Maintenance
- Volume 16 - Paper Physics
- Volume 17 - Pulp and Paper Testing
- Volume 18 - Paper and Board Grades
- Volume 19 - Environmental Management and Control
- Volume 20 - Biorefining of Forest Resources
Back To Top
|
 Member Jay Kaplan has been associated with TAPPI since 1994 when he was living in the Chicago area working for Stone Container. But it wasn't until years later that he finally took full personal advantage of all the benefits inherent in TAPPI membership, "the industry's best resource for technical support and information on emerging technologies and cutting edge science."
Having been mentored early in his career by serveral long-time TAPPI members, Jay says their influence set the groundwork for his future involvement. Through the years he has practiced in numerous meetings and shows at both the local and national level, and is now very involved in SuperCorrExpo, the largest tradeshow in the western hemisphere catering to the corrugated industry. "It's through events like these that you form and nurture professional relationships that help drive sustainable business improvements that may not have been achieved as quickly or at all without the common ground and opportunity that TAPPI provides."
Jay also believes this exposure to emerging technologies, technical expertise, and experts from outside his own company have played an integral role in his professional growth. Now serving as the Manager for Learning an Organizational Development for Corrugated Packaging at RockTenn, he says that use of TAPPI's website, the eLibrary, technical support, and industry news are all important elements to stay on the cutting edge of your career. And, furthermore, Jay puts his actions where his words are. Not content to just tell his peers and fellow employees about the benefits of membership, he recently brought a new group of new and future production managers to TAPPI's headquarters in Norcross, Ga., USA, for a tour and afternoon of learning. "I believe they left feeling a lot more informed about what our industry has to offer," he said.
To read more about Jay's professional accomplishments and personal interests, be sure to visit this month's Member Spotlight page.
Back To Top
|
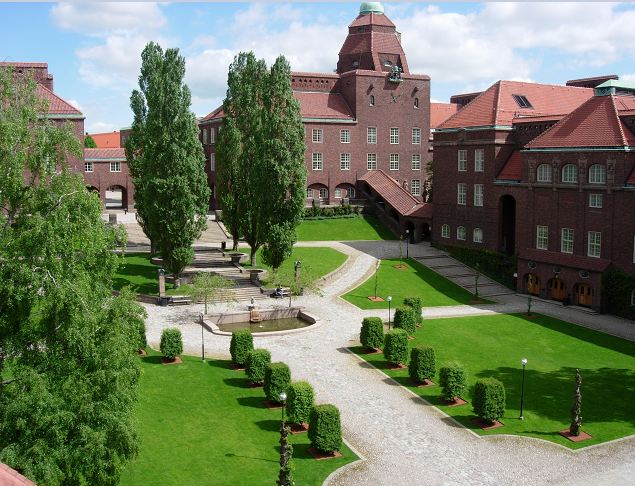 The 2013 TAPPI International Conference on Nanotechnology for Renewable Materials will be held July 24-27, 2013, on the KTH Royal Institute of Technology campus in Stockholm, Sweden. Industry experts, scientists, health and safety specialists, legal and government policy makers, as well as the field's leading researchers will discuss the latest in nanotechnology research and development.
The 2013 Technical Program Committee has issued a Call for Papers inviting contributions from participants working in research, development, and deployment of renewable nanomaterials.
Abstracts are due by December 3, 2012.
Back To Top
|
Make your plans now to join a host of professionals from industry, universities and research institutes at the 14th TAPPI European PLACE Conference, which will be held May 6-8, 2013, at the Swissotel in Dresden, Germany.
The Call for Papers is now officially open. Submit your abstract and take an active role in this not-to-miss event!
Back To Top
|
|
|
TAPPI Over the Wire | 15 Technology Pkwy. S. | Norcross, GA 30092 USA | Voice: 770.446.1400 | Fax: 770.446.6947
|
 |