 |
|
Weekly Spotlight
In a move signaling a new, innovative approach to multidisciplinary research with university partners, North Carolina State University, Raleigh, N.C., USA, has entered into a multiyear agreement with Eastman Chemical Co. to conduct joint cutting-edge research in chemistry, materials science, and other scientific disciplines
Learn More...
|
Domtar Corp., Montreal, Qué., Canada, is teaming up with the Washington, D.C., USA-based non-profit organization First Book to put more than 20,000 new books in the hands of children in need
Learn More...
|
According to Ford Motor Co., Dearborn, Mich., USA, cellulose joins the growing list of sustainable materials originating from unlikely sources that could soon be used in Ford vehicle components and help further reduce the automaker's reliance on traditional content such as fiberglass and petroleum
Learn More...
|
Fisher International, South Norwalk, Conn., USA, has conducted a study of water use in the pulp and paper industry, and published its findings in a study titled The 2012 Global PPI Water Benchmark Report
Learn More...
|
MeadWestvaco Corp. (MWV), Richmond, Va., USA, reports that for the ninth consecutive year it has been listed on the 2012 Dow Jones Sustainability World Index
Learn More...
|
Yankee drying experts from around the world are planning their fall meeting for November 5-6 in the heart of North American tissue making, Neenah, Wis., USA.
Learn More...
|
TAPPI's 2012 Nominating Committee presents a slate of candidates for two officer and three director positions on the TAPPI Board
Learn More...
|
Below is the latest listing of job openings in the TAPPI Career Center
Learn More...
|
Market Roundup
China will continue to see rising wood pulp production along with rising imports of wood chips to make that pulp
Learn More...
|
Governments in Japan and South Korea have announced definite plans to increase their usage of green and low carbon energy alternatives
Learn More...
|
Total U.S. paper industry consumption of recovered paper in August was 2.56 million tons, 6% higher than July 2012
Learn More...
|
Pulp & Paper
Cascades Tissue Group, Waterford, N.Y., USA, this week launched a new antibacterial paper towel, which it says redefines the hand towel's role in enhancing hygiene
Learn More...
|
C&S Paper, China, has ordered from Toscotec, Italy, two new tissue machines with a combined capacity of 58,000 metric tpy to be installed at its mills in China
Learn More...
|
Fortress Paper, Vancouver, B.C., Canada, has signed, through its wholly-owned subsidiary, Fortress Global Cellulose Ltd., an electricity supply agreement with Hydro Québec for the sale of green electricity to be produced at the Fortress Global Cellulose Mill's cogeneration facility upon its restart
Learn More...
|
The Hengan Group, China, and Andritz, Graz, Austria, have successfully completed a total of four tissue machine startups planned for this year
Learn More...
|
FutureMark Paper Group (FMPG), Westport, Conn., USA, was launched this past week as the umbrella group for two recycled paper producers previously operating as Manistique Papers, Manistique, Mich., and FutureMark Paper Co., Alsip, Ill.
Learn More...
|
Chenming Jilin, part of Shandong Chenming Paper Holdings Ltd., China, has contracted Metso, Finland, to relocate and rebuild a paper machine for the company's new mill site in Jilin Province, China
Learn More...
|
Södra, Sweden, reported this week that it will be making 260 people "redundant" as part of its drive to reduce the group's costs
Learn More...
|
UPM, Helsinki, Finland, has positioned itself as a frontrunner in the sustainable transformation of the paper industry by obtaining the first EU Ecolabel for newsprint
Learn More...
|
The United Steelworkers (USW) Local 2688 "Union Committee to Re-open Snowflake Paper" this past week issued a statement about the October 5 shutdown, urging Catalyst Paper Co. to cooperate with its workers in seeking a buyer for that company's Snowflake, Ariz., USA, facility
Learn More...
|
Verso Paper Corp., Memphis, Tenn., USA, reports that the Sustainable Resources Institute (SRI) will be the first recipient of a Verso Forest Certification Grant
Learn More...
|
Containerboard/Packaging
Holmen AB, Stockholm, Sweden, report that its paperboard mill in Iggesund, Sweden, will make its operations more efficient, with employee numbers being cut from 900 to 800
Learn More...
|
At the end of September, Iggesund Paperboard inaugurated the new recovery boiler at its Iggesund Mill in Sweden
Learn More...
|
Sonoco Recycling, a unit of Sonoco, Hartsville, S.C., USA, and one of the largest packaging recyclers in North America, has completed a $2 million upgrade at its Onslow County, N.C., materials recovery facility (MRF)
Learn More...
|
Tetra Pak, Lausanne, Switzerland, marking its fortieth year of operations in Turkey, has inaugurated a new laminator at its packaging material factory in Izmir, Turkey
Learn More...
|
|
New Products
Stora Enso, Finland, reports that its Tambrite board has been upgraded in quality as a result of an investment program completed at the Ingerois Mill in Finland
Learn More...
|
Weyerhaeuser Co., Federal Way, Wash., USA, reports that it has launched a proprietary, patent-pending form of thermoplastic composite that uses sustainably sourced cellulose fiber as a reinforcement additive
Learn More...
|
Published Pricing
Fibria, Brazil, the world's biggest producer of bleached eucalyptus kraft (BEK) pulp, has begun informing customers that it will increase its price for BEK in Europe to $780/metric ton
Learn More...
|
TAPPI News
TAPPI Member Garnet Bremner describes TAPPI as a "mosaic" of individuals whose depth of experience and knowledge creates a wonderful atmosphere for finding outstanding mentors. Brenner began as a P&P engineer, working eventually into management and more. Learn more about this month's featured TAPPI member who's "In the Spotlight"...
Learn More...
|
See who all will be attending PEERS and IBBC this year. These conferences, being held Oct. 14-18, in Savannah, Ga., USA are going to be hot-spots for learning, networking, and growing careers in the industry.
Learn More...
|
Candidates have been nominated for two officer and three director positions, and voting is scheduled to begin December 1.
Learn More...
|
Free Webinar courtesy of TAPPI, on Oct. 10, will show you how to employ new tools to break or eliminate loop interactions and the effects of disturbances.
Learn More...
|
This comprehensive textbook describes the entire process of manufacturing corrugated containers. In addition to detailed explanations, the book also features practical troubleshooting tips, and a discussion of common problems and solutions within each major section. TAPPI members can pick this up for just $37 compared to the list-price of $185.
Learn More...
|
Join us on October 22 at this new, lovely golf center near Memphis, Tenn., USA, to hit a bucket of balls and enjoy food and fellowship. Proceeds will support scholarships at Christian Brothers University Packaging Program.
Learn More...
|
This text covers fundamentals and processes from chemical composition of pulp to technology, production, and the environmental impact of bleaching. TAPPI members are eligible to receive a special $62 discount on this text's list price.
Learn More...
|
Global yankee drying experts will meet at the YDS&R fall meeting November 5-6 in Neenah, Wis., USA, to explore the development of standard practices and hear presentations on doctor setup/profiling and metalizing yankee dryers.
Learn More...
|
This Webinar on October 9 will provide a unique, in-depth look into the current state of biomass production and it's commercial viability. This insightful, educational Webinar is being offered free of charge to anyone in the pulp, paper, or any related industries who are interested. Don't miss out on this opportunity - register today!
Learn More...
|
IBBC 2012 will focus on advancements and commercialization of bioconversion technologies that leverage forest products manufacturing infrastructure.
Learn More...
|
What role can government policies play in development of bioenergy in the forest products industry? Panel Themes and special sessions at the 2012 TAPPI IBBC conference will answer those questions and more.
Learn More...
|
Back by demand, this one-day workshop focuses on improving operations and quality in the kraft pulping process. The workshop will make it's encore on Saturday, October 13, in conjunction with PEERS 2012, October 14-17, in Savannah, Ga., USA.
Learn More...
|
A first-time, unique program for the TAPPI PEERS Conference, this one-day seminar explores the latest reliability strategies today's mills are implementing to stay in-tune and competitive under progressively lean operating conditions. October 14,15,18, 2012.
Learn More...
|
The FEMOS Workshop shows maintenance staff how to rationally manage the mechanical integrity of all fixed equipment. The workshop takes place Sunday, October 14 from 8 a.m.-5 p.m. The workshop takes place just before TAPPI PEERS and IBBC conferences, so those going can also attend these important events.
Learn More...
|
This free webinar from TAPPI addresses why whitewater filtration systems are often problematic, while also offering solutions to improve the reliability of the process.
Learn More...
|
On Wednesday, Thursday, and Friday, Nov. 7-9, 2012, TAPPI will conduct its Tissue Runnability Course at Neenah, Wis., USA., with a faculty of technical experts in each area of the machine from wet end operations through creping and process control.
Learn More...
|
Deadline for Coating Program Submissions October 16; Deadline for Papermakers Program submissions November 20. Topics under consideration include mill management, papermaking, coating, tissue, nonwovens, and recycled paperboard. Paper company personnel, suppliers, academics, and students are strongly encouraged to submit their ideas for papers, posters, or roundtable discussions.
Learn More...
|
This 20-volume set covers the entire papermaking process from wood fiber to end product, providing a basis for university-level education, for updating training courses, and as handbooks for the industry.
Learn More...
|
The 2013 TAPPI International Conference on Nanotechnology for Renewable Materials will be held July 24-27, 2013, on the KTH Royal Institute of Technology campus in Stockholm, Sweden. The technical program committee has issued a Call for Papers, with abstracts due by December 3.
Learn More...
|
Calls for Papers have been issued for the 14th TAPPI European Place Conference to be held May 6-8, 2013, in Dresden, Germany.
Learn More...
|
|
Find us on Facebook
Network with us on LinkedIn
Follow us on Twitter
|
Weekly Spotlight
In a move signaling a new, innovative approach to multidisciplinary research with university partners, North Carolina State University, Raleigh, N.C., USA, has entered into a multiyear agreement with Eastman Chemical Co. to conduct joint cutting-edge research in chemistry, materials science, and other scientific disciplines. As part of the agreement, Eastman will provide $10 million over six years in support of the Eastman Chemical Co. Center of Excellence (ECCE) partnership. It also establishes the Eastman Innovation Center (EIC) laboratory. The lab will be located on Centennial Campus, NC State's nationally recognized research campus.
"This agreement demonstrates NC State's commitment to be a leader in public-private research partnerships," says NC State Chancellor Randy Woodson. "Our work with Eastman Chemical Co. provides NC State researchers and students many exciting opportunities to address real-world problems in chemistry and material sciences, and will reduce the time required to take innovative solutions to market."
Dr. Greg Nelson, SVP and CTO at Eastman Chemical Co., added that "we're excited about the possibilities the Eastman Innovation Center being established at NC State brings. Our partnership launches a world-class, open innovation collaboration with a leading university. That relationship will help us bring differentiated new ideas, technologies, and materials from early stage research to the market more quickly than traditional approaches."
The developing research agreement with Eastman should ease the collaborative process, says Dr. Terri Lomax, NC State vice chancellor for research, innovation and economic development. "In addition to a unique intellectual property agreement, the university has created one central point of contact for Eastman to coordinate activities with both academic and administrative units," Lomax says. "From the very beginning, we want to demonstrate that collaborating with NC State is unlike working with any other university."
At least six colleges across the university will participate in the joint research projects, which will be selected by the research steering team comprised of an equal number of company and university researchers. Departments involved in initial research interactions include: chemistry; chemical and biomolecular engineering; materials science and engineering; textile engineering, chemistry, and science; forest biomaterials; and graphic design and industrial design, as well as NC State's Center for Innovation Management Studies.
The agreement also allows visiting Eastman scientists to work in NC State labs and allows NC State researchers to do the same at Eastman sites. NC State students are also expected to participate in the research projects.
The Eastman Innovation Center lab will be located in 2,000 square feet of lab space on Centennial Campus. The company is expected to move into the space in early 2013.
Back To Top
|
Domtar Corp., Montreal, Qué., Canada, is teaming up with the Washington, D.C., USA-based non-profit organization First Book to put more than 20,000 new books in the hands of children in need. Domtar will provide a total of $25,000 in grants among 10 schools and community programs located near Domtar facilities across the U.S. The communities include Addison, Ill.; Ashdown, Ark.; Owensboro, Ky.; Plymouth, N.C.; and Rock Hill, S.C. These schools and programs can use their Domtar grants at the First Book Marketplace, a website that provides high-quality, age-appropriate children's books and educational materials at prices 50% - 90% below retail.
"We invest in projects like First Book that promote education and emphasize literacy as part of our company commitment to supporting the sustainable development of our communities," noted Domtar President and CEO John D. Williams. "The fact that we are partnering with an organization like First Book means that the right books go to the right children in the right place."
In addition to the grants, Domtar will sponsor 5,000 copies of the book Recycle This Book: 100 Top Children's Book Authors Tell You How to Go Green, edited by Dan Gutman and published by Yearling Books, to be added to the First Book Marketplace website and distributed throughout First Book's network of schools and community programs. This book gives students 100 ideas on how they can help change the world.
"We're excited about this partnership with Domtar, and thrilled that they've stepped up to help children in need across the country get the books and resources they need to succeed," said Kyle Zimmer, president and CEO of First Book.
More information is available online.
Back To Top
|
According to Ford Motor Co., Dearborn, Mich., USA, cellulose joins the growing list of sustainable materials originating from unlikely sources that could soon be used in Ford vehicle components and help further reduce the automaker's reliance on traditional content such as fiberglass and petroleum. The Ford biomaterials research team has been working with Weyerhaeuser, Federal Way, Wash., to investigate the use of a plastic composite material utilizing cellulose fibers from trees in place of fiberglass or mineral reinforcements (also see Weyerhaeuser article in the New Products section below).
Because the cellulose fibers in this new composite come from sustainably grown and harvested trees and related byproducts, such as chips, the environmental impact of building cars could be lessened, the two companies emphasize. Specifically, replacing fiberglass, minerals, and/or petroleum with a natural, plant-based material can sequester carbon dioxide and ultimately lead to a smaller carbon footprint, among other benefits.
"Our responsibility to the customer is to increase our use of more sustainable materials in the right applications that benefit both the environment and product performance," said John Viera, Ford global director of sustainability and environmental matters.
Ford's research has found that Weyerhaeuser's cellulose-based plastic composite materials meet the automaker's stringent requirements for stiffness, durability, and temperature resistance. Further, components weigh about 10% less and can be produced 20% - 40% faster and with less energy when made with cellulose-based materials compared with fiberglass-based materials. These weight and process savings can enable equivalent or reduced component costs.
And like other less-than-obvious candidates for use in vehicle components, such as retired and shredded paper currency, the cellulose-based plastic composite material could be as important to Ford as soybeans have become. Ford uses soybean-based cushions in all of its North American vehicles such as the all-new Fusion, saving about 5 million lb. of petroleum annually.
Ford began working with Weyerhaeuser about three years ago to evaluate the use of a cellulose-based plastic composite material for potential use in vehicle components. Several prototype vehicle components were created from the cellulose-based material and put through a battery of tests by a team led by Dr. Ellen Lee, Ford's plastic research technical expert.
"We found that working collaboratively at an early stage has accelerated the development of a material that has a high thermal stability, doesn't discolor, and doesn't have an odor," said Lee. "That's important because it opens the door for use of the material in a wide range of applications that could eventually add up to significant environmental benefits across our product line." For example, prototype armrests were tested as potential components that could feature the cellulose-based material.
Not only can the cellulose material be used in interior applications, but the high level of performance provided by the cellulose fibers also makes it a good candidate for exterior and under-the-hood applications as well. "Cellulose fiber is a great renewable resource that already has established infrastructure around the world, making it an ideal material for Ford's global products," said Lee.
Weyerhaeuser oversees more than 20 million acres of sustainably managed and third-party certified forestland around the world and plants more trees than they harvest.
Back To Top
|
Fisher International, South Norwalk, Conn., USA, has conducted a study of water use in the pulp and paper industry, and published its findings in a study titled The 2012 Global PPI Water Benchmark Report. The report is intended to help environmental managers understand how water issues are affecting pulp and paper mills around the world as they benchmark their own positions and evaluate their policies.
The study finds that many mills expect that their access to water will be threatened in the next five years. Even more mills – a majority worldwide – expect to make changes to their water usage goals in the next five years, particularly in developing countries.
Worldwide, the range of water usage per ton of paper produced was found to be quite broad, from under 250 gal/short ton of paper produced up to 70,000 gal/short ton of paper produced. Similarly, sludge production was found to range from almost nothing to just over 0.4 short tons of sludge/short ton of pulp or paper produced. Nevertheless, attitudes about the seriousness of potential threats to water availability are similar across types of mills and regardless of how mills handle effluent treatment.
The report is free to mills that take part in Fisher International's water survey. It is also available for purchase. To take the survey, obtain a copy of the report, or receive additional information, please email Fisher or call +1 203.854.5390.
Back To Top
|
MeadWestvaco Corp. (MWV), Richmond, Va., USA, reports that for the ninth consecutive year it has been listed on the 2012 Dow Jones Sustainability World Index. The Index recognizes leading global companies in the areas of economic, environmental, and social performance, and evaluates organizations based on their commitment to and success in integrating sustainability into core business objectives and performance.
In addition to being among the 340 companies listed on the Index, MWV was the only company in the Containers & Packaging sector to be listed on the North American index.
"Our drive to find sustainable solutions is embedded in our core and reflects the way we run our business every day," said John A. Luke Jr., chairman and CEO of MWV. "As a global leader in packaging solutions, serving the world's most recognized brands, we find inspiration from working with others – partnering with customers to create valuable solutions that satisfy their needs and move us toward the goals we share in business and for our environment."
In the past year, MWV has launched a comprehensive Sustainability Strategy for its business and released measurable targets to monitor progress toward energy efficiency, carbon emissions and water use reductions, certified fiber sourcing, beneficial reuse of waste, and supplier conduct. On this year's index, the company increased its overall score in the Operational Eco-Efficiency, Labor Practices and Human Rights, and Social Reporting sectors. MWV maintained its high score for the social criteria based on its programs to engage stakeholders and its industry-leading Code of Conduct for employees, and also scored above its peers for environmental policies and management systems.
Back To Top
|
Yankee drying experts from around the world are planning their fall meeting for November 5-6 in the heart of North American tissue making, Neenah, Wis., USA. The committee meets twice per year to share knowledge and best practices to increase safety and reduce delay that negatively impacts dryer operations and overall productivity. The fall meeting will include the development of standard practices and presentations on doctor setup/profiling and metalizing yankee dryers. More information and registration details are available online.
The meeting will be held in conjunction with the Lake States TAPPI/North Central PIMA Energy Forum and is open to all TAPPI members and visitors (one time only). To attend as a visitor, please contact Scott Springmier.
Immediately following the biannual Yankee Dryer Safety and Reliability Meeting, TAPPI will hold the popular Tissue Runnability Course November 7-9 at Miron Construction in Neenah. The course will provide an excellent knowledge base for process engineers, machine supervisors, reliability professionals, and suppliers responsible for maximizing uptime and saleable tissue production. Attendees will learn to:
- Improve tissue quality and consistency
- Understand contributors to waste and downtime
- Learn reliability and maintenance best practices
- Diagnose and troubleshoot problems quickly
The course includes two and one-half days of focused instruction from a dozen globally recognized tissue making experts. More information is available online. A registration discount is offered to TAPPI members.
Back To Top
|
The candidates are: chair, Thomas J. Garland; vice chair, Chris Luettgen, Kimberly-Clark; and directors, Daniel D. Cappell (AstenJohnson), Kirt J. Cuevas (International Paper), and Robert A. Feeser (MeadWestvaco Corp.). Voting begins December 1. Per the TAPPI Bylaws, members of the organization have until November 1 to review the slate.
More information about the slate and election process is available online
Back To Top
|
Below is the latest listing of job openings in the TAPPI Career Center. http://careers.tappi.org/ The current listing includes job openings for a variety of positions, including product marketing manager, maintenance manager, fiber scientist, technical services manager, director of operations, coating scientist, process engineer, electrical engineer, fiberline specialist, and customer service representative. Current, specific job openings at companies and locations in the TAPPI Career Center include:
Employer |
Title |
Location |
Albarrie Environ. Services |
Product Mkt. Mgr. (Liq. Filtration Media) |
|
Armstrong World Industries |
Maintenance Manager |
Pennsylvania |
Boise Inc. |
Sr. Scientist- Fiber |
Wallula, Wash. |
Catalyst Paper |
Manager, Technical Services |
Powell River, B.C. |
Confidential |
Technical Services Manager |
Columbus, Ohio |
Confidential |
Coatings Scientist |
Columbus, Ohio |
First Quality Enterprises |
Director of Operations |
Lock Haven, Pa. |
GL&V USA |
Sr. Process Eng.- Fiberline Specialist |
Nashua, N.H. |
New-Indy Containerboard |
Process Engineer |
Ontario, Calif. |
SCA Americas |
Electrical Engineer |
|
SCA Americas |
Process Optimization Manager |
|
UPM Kymmene |
Customer Service Representative |
Westmont, Ill. |
More information about these jobs is available online.
Back To Top
|
Market Roundup
China will continue to see rising wood pulp production along with rising imports of wood chips to make that pulp, according to a new report by RISI, Boston, Mass., USA, titled 2012 The China Pulp Market: A Comprehensive Analysis and Outlook. The study also concludes that large-scale paper grade market pulp production in China is not a sustainable business over time.
A steady upward trend in wood growing costs in southern China will keep China's pulp producers purchasing ever-increasing volumes of wood chips from greater distances, including North and South America, at very high costs, the report notes.
"Wood costs in China are already almost the highest in the world, and account for as much as 70% of cash costs for bleached hardwood kraft (BHK) market pulp producers in China. Market BHK producers in China have some of the newest and largest pulp lines in the world, and yet are still the high cost producers, even in their own market," said Kurt Schafer, VP of Pulp & Recovered Paper at RISI. "Our research indicates that wood growing costs in southern China will probably outpace growing costs in Brazil by a wide margin over the next decade, and this suggests that large-scale paper grade market pulp production in China is not a sustainable business over time."
Back To Top
|
Asia will consume more wood pellets and energy wood chips in the future, according to a report this past week by Wood Resource Quarterly ( WRQ) , Seattle, Wash. USA. Governments in Japan and South Korea have announced definite plans to increase their usage of green and low carbon energy alternatives.
South Korea is taking steps to reduce its dependence on imported fossil fuels and instead invest in domestic renewable energy technology, including wind, solar, hydropower, and biomass. The long-term plan is to increase the renewable energy share from less than 4% in 2011 to 6.1% in 2020, and then to 11.5% in 2030. As part of this effort, the government has initiated a program that included building eight new pellet plants as well as exploring opportunities to import large volumes of pellets in the future. The goal is to consume 5 million metric tons of pellets by 2020, a huge increase from the less than a few hundred thousand metric tons used in 2011.
South Korea has access to wood residues from the domestic sawmilling industry, which could be used for the manufacturing of pellets. This domestic supply, however, will not be sufficient, so South Korea will need to increase pellet imports to meet the ambitious 6.1% goal only eight years from now. The government estimates that by 2020, 75% - 80% of pellets consumed in the country will need to be imported. Some of the major energy companies in South Korea have reportedly been exploring the opportunities to import pellets from Australia, Vietnam, Indonesia, the Philippines, Canada, and the U.S.
Japan is another Asian country expected to increase importation of energy chips and wood pellets, due in part to the nuclear power plant accident in Fukushima last year. Following the disaster, the Japanese government decided to close down all nuclear plants, at least temporarily. Even if a few plants eventually reopen, nuclear energy will never again be as important for energy production as it once was.
In the future, Japan will increasingly rely on renewable energy sources, with biomass likely to be one important supply source. Up until this year, Japan has imported only very limited volumes of wood pellet, primarily from Canada, but it is likely that import volumes of both pellets and energy chips will increase in the coming years.
More information is available online.
Back To Top
|
Total U.S. paper industry consumption of recovered paper in August was 2.56 million tons, 6% higher than July 2012, AF&PA, Washington, D.C., USA, reported in its August 2012 U.S. Recovered Fiber Monthly Report. Year-to-date total consumption in 2012 is 4% lower than during the same period last year.
U.S. exports of recovered paper, as reported by the U.S. Census Bureau, increased 5% in July compared with June, led by a 14% increase in mixed papers exports. Year-to-date exports of recovered paper in 2012 are 6% lower than during the same period in 2011.
Back To Top
|
Pulp & Paper
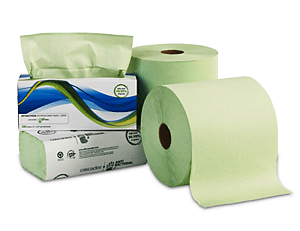 Cascades Tissue Group, Waterford, N.Y., USA, this week launched a new antibacterial paper towel, which it says redefines the hand towel's role in enhancing hygiene. The Cascades Antibacterial Paper Towel reportedly minimizes hand contamination by killing 99.99% of harmful bacteria almost instantly, unlike ordinary paper towels.
Since 80% of all infections are transmitted by hand, the lack of proper hand hygiene, in particular inadequate hand washing and drying practices, continues to be a consistent, if not deadly, problem, Cascades notes. The green-colored Cascades antibacterial towel can "fit anywhere, doesn't require additional steps, and compensates for people's imperfect hygiene habits without changing the way they wash or dry their hands," the company explains. The towel releases benzalkonium chloride when in contact with wet hands. This active ingredient has been around since 1935 and is safely used in common products, including gel sanitizers, baby wipes, and antiseptic skin solutions.
First cleared by Health Canada, the new Cascades' product now complies with the regulation and policies of the U.S. Food and Drug Administration.
"It's a first-of-a-kind product that eliminates residual bacteria almost instantly. Now everyone can help control the spread of bacteria," said Suzanne Blanchet, CEO of Cascades Tissue Group and product champion. "While this is a groundbreaking innovation, the Antibacterial Paper Towel makes good common sense as it relates to human health. We believe the product will revolutionize the paper towel's role in proper hygiene because of its efficacy and because it doesn't require a change of habits."
Cascades has performed several third-party laboratory tests to ensure the safety and efficacy on the new towel. Microbiologists also note that using the antibacterial towel in conjunction with washing hands with soap and water provides a more hygienic result than using alcohol-based gels and other hand sanitizers. While these products kill bacteria and are useful when there is no water and soap available, they don't remove the organic matter (grease, dirt, blood, fecal matter) often found on hands.
The Antibacterial Paper Towel contains 100% recycled fiber, and is made using five times less water than the North American paper industry average, according to Cascades Tissue Group. More information is available online.
Back To Top
|
C&S Paper, China, has ordered from Toscotec, Italy, two new tissue machines with a combined capacity of 58,000 metric tpy to be installed at its mills in China. The order was placed after C&S Paper brought another Toscotec tissue machine online this summer at its Tangshan City mill, the third one supplied by Toscotec in the past two years. The two new machines are scheduled to come online in the second half of 2013.
The new Toscotec machines will be installed at the Chengdu mill at Sichuan. One of the machines (AHEAD-1.5M) will have a trim width of 3,550 mm, a speed of 1,650 meters/min, a steam heated hood, a steel yankee dryer TT SYD-16FT, and a production capacity of some 32,000 metric tpy. The second machine (AHEAD-1.5S) will have a trim width of 2,850 mm, a speed of 1,700 meters/min, a gas fired hood, a steel yankee dryer TT SYD-12FT, and a production capacity of some 27,000 metric tpy.
Toscotec's scope of supply for both machines includes a crescent former TM, machine auxiliaries, the hood, and dust removal system (provided by Toscotec associated Milltech), electrification, and the control system.
C&S Paper owns six mills in China operating 80 machines, including the new Toscotec units at the Jiangmen and Tangshan sites with a total tissue capacity of approximately 350,000 metric tpy at the end of 2012. Three more Toscotec units will come on-stream in the next months.
Back To Top
|
Fortress Paper, Vancouver, B.C., Canada, has signed, through its wholly-owned subsidiary, Fortress Global Cellulose Ltd., an electricity supply agreement with Hydro Québec for the sale of green electricity to be produced at the Fortress Global Cellulose Mill's cogeneration facility upon its restart. The agreement is in connection with Hydro Québec Distribution's Power Purchase Program for electricity derived from forest biomass, which was launched on December 20, 2011.
Under the terms of the agreement, Fortress Global will provide up to 34 MW of green power to Hydro Québec, commencing no later than June 1, 2014, at a price of $106 per MW hour, indexed to the consumer price index over a 25-year term.
Chadwick Wasilenkoff, CEO of Fortress Paper, noted that "the signing of the electricity supply agreement represents a key component in achieving our business plan at the Fortress Global Cellulose Mill, which includes the restart of the cogeneration facility to produce green electricity that in turn will reduce production costs. Generating green energy exemplifies our commitment to sustainable development and we believe that the results of this partnership with Hydro Québec will be beneficial to the environment and the community, as well as to Fortress Paper."
Fortress Paper operates internationally in three distinct business segments: dissolving pulp, specialty papers, and security paper products. The company operates its dissolving pulp business at the Fortress Specialty Cellulose Mill located in Canada, which is also in the process of expanding into the renewable energy generation sector with the construction of a cogeneration facility. The company is also seeking to expand its dissolving pulp capacity with the recent acquisition of the Fortress Global Cellulose Mill located at Lebel-sur-Quévillon, Québec, which the company intends to convert into a dissolving pulp mill and where it intends to restart the cogeneration facility.
The company operates its specialty papers business at the Dresden Mill in Germany, where it produces specialty non-woven wallpaper base products. Its security paper products are made at the Landqart Mill in Switzerland, where it produces banknote, passport, visa, and other brand protection and security papers, and at its Fortress Optical Facility in Canada, where it manufacturers optically variable thin film material.
Back To Top
|
The Hengan Group, China, and Andritz, Graz, Austria, have successfully completed a total of four tissue machine startups planned for this year. The Hengan Group is thus running nine Andritz tissue machines, two of which are fitted with the largest steel yankees in operation worldwide.
From January to September of this year, two PrimeLine W8 tissue machines were started up at the Chongqing mill and two PrimeLine TM W6 tissue machines at the Jinjiang mill, all ahead of the time schedule. All four orders included supply of the complete stock preparation and machine control systems. The steel yankees of PM 15 and PM 16 are the largest for tissue operating anywhere in the world, with a diameter of 4.9 meters and a shell length of 6.2 meters.
Back To Top
|
FutureMark Paper Group (FMPG), Westport, Conn., USA, was launched this past week as the umbrella group for two recycled paper producers previously operating as Manistique Papers, Manistique, Mich., and FutureMark Paper Co., Alsip, Ill. FutureMark Paper Group aligns the executive management, business development, marketing, and operational functions of Manistique (uncoated recycled papers) and FutureMark Alsip (coated recycled papers). Industry veteran Steve Silver will serve as FMPG's president and CEO, overseeing both manufacturing facilities.
"In addition to sharing a senior management team and board of advisors, our two recycled mills share a strong history of innovation," Silver notes. "Combining the unique production capabilities of these two mills creates a platform for faster growth and enables us to achieve operational synergies that otherwise wouldn't be possible. We're joining forces at a great time in the market to take advantage of the momentum behind environmental paper."
FMPG says that strategic alignment of the two operations will promote and accelerate:
- Process innovation and product development. By cross-pollinating best practices in operations, predictive maintenance, and new technology between the two mills, FMPG will be able to accelerate development of high-quality products and lower the environmental impact of its manufacturing activities.
- Sales and marketing integration. Sales and marketing resources are now realigned to better serve the group's green customer base with a unified brand and complementary products.
- Transportation optimization. The group is optimizing paper transportation routes between its two manufacturing facilities and their suppliers and customers to speed delivery and decrease its transportation footprint.
While FutureMark Paper Group's Alsip and Manistique facilities will work closely in the marketplace to achieve synergies and bring new value to customers, each operation is financially and legally independent, owned by separate investment funds.
FMPG's 100% recycled uncoated papers, formerly sold under Manistique Papers' product names, will now be sold under the brand Future Mystique™. Book papers will be marketed under the Future Book™ UC brand. Printing papers for the converter market will be bundled under the Future Office™ product family, and recycled packaging and bag papers will be sold as Future Pack™ and Future Bag™, respectively.
Product names for the group's recycled coated publication papers, previously sold by FutureMark Paper Co., will remain unchanged as Future Book™, Future Choice®, and Future Connection®. Future ReMark®, a C1S label paper, will be renamed Future Label™.
Back To Top
|
Chenming Jilin, part of Shandong Chenming Paper Holdings Ltd., China, has contracted Metso, Finland, to relocate and rebuild a paper machine for the company's new mill site in Jilin Province, China. The value of the order will not be disclosed. However, a typical market value of this type of a relocation and rebuild project ranges from EUR 10 to 20 million, Metso notes.
"The main target of the project is to increase production by improving the efficiency of the papermaking line and by increasing the drying capacity of the paper machine," says Jukka Vuorela, Metso's sales manager.
The PM 12 paper machine to be relocated to the company's new mill site in Jilin City is currently at its Chenming Jilin mill site. Metso will supervise the dismantling and packing of the paper machine line and supervise the installation and startup of the relocated equipment. Metso's will also rebuild the relocated PM 12. Startup of the relocated and rebuilt machine is scheduled for the second half of 2013.
PM 12 is a 6.95-meter-wide (wire) machine. The modernization will include forming and drying section modifications and a press section rebuild with a new SymBelt shoe press. Originally PM 12 produced coated wood-containing LWC (lightweight coated) paper grades and after the rebuild will produce other paper grades as well..
Chenming Jilin is part of Shandong Chenming Paper Holdings Limited, one of the biggest paper producers in China. In 2010, the company's paper production capacity was more than 4 million metric tpy. It had a turnover of EUR 2 billion and employed some 17,000 people.
Back To Top
|
Södra, Sweden, reported this week that it will be making 260 people "redundant" as part of its drive to reduce the group's costs. The move is being taken, Södra says, "to face up to international competition at a time when the economic situation is poor and significant fluctuations in currency exchange rates have exacerbated the situation."
This measure will affect all Swedish business areas, and staff at all levels, the company notes, adding that trade union negotiations will begin immediately.
"Södra operates in an international market. Just like other companies, Södra is affected by the prevailing economic situation and trading conditions. The outlook for our main markets remains uncertain. To be able to face up to international competition, we have to undertake measures to reduce our costs," said Gunilla Saltin, acting CEO.
Back To Top
|
UPM, Helsinki, Finland, has positioned itself as a frontrunner in the sustainable transformation of the paper industry by obtaining the first EU Ecolabel for newsprint. UPM News and UPM EcoBasic have obtained the EU Ecolabel after fulfilling strict criteria that include requirements related to energy and chemical use, forest sustainability (origin of wood), and production-related emissions to water and air.
UPM News and UPM EcoBasic are the first newsprints in Europe to receive the EU Ecolabel since the criteria were approved in July 2012. They are produced with at least 70% recovered fibers with the balance of fibers from PEFC or FSC certified sources. The EU Ecolabel for newsprint further certifies that the energy use, chemicals used, as well as emissions and waste management comply with strict benchmark standards.
"UPM aspires to deliver products that have minimal environmental impact. The EU Ecolabels help our customers to choose the most environmentally responsible products available on the market. The label also shows that UPM is committed to its European customers," said Wolfgang Bucher, VP of Newspaper Publishers, UPM Paper.
UPM's EU Ecolabel newsprint paper is produced in seven different paper mills: Kaipola (Finland); Ettringen, Schongau, and Schwedt (Germany); Steyrermühl (Austria); Shotton (UK); and Chapelle (France).
Back To Top
|
The United Steelworkers (USW) Local 2688 "Union Committee to Re-open Snowflake Paper" this past week issued a statement about the October 5 shutdown, urging Catalyst Paper Co. to cooperate with its workers in seeking a buyer for that company's Snowflake, Ariz., USA, facility.
USW Local 2688 President Mike Popovich, representing the 200 production workers who are losing their jobs at Snowflake paper, has urged owners of the facility to utilize the court-approved sale process to search for potential buyers that will want to run the mill. The sale of the paper mill reportedly will play out over the next several months.
"It's very early in the sale process Catalyst has laid out," Popovich said. "There is time for the company to work with its employees and the communities to find a buyer that is committed to making paper at Snowflake." Popovich announced the newly-named "Union Committee to Re-open Snowflake Paper," explaining he is confident that alternative paper products can be made by the mill.
"There is still a strong domestic market for paper products including brown bag paper, corrugating medium, and linerboard that are viable only if the infrastructure is retained for the paper machines," Popovich said. "We seek a public commitment from Catalyst Paper to do so."
According to the USW committee that negotiated a September 20 agreement addressing the effects of the shutdown, about 65 USW-represented workers at the Snowflake paper mill will be eligible to retire. A benefit package will be distributed to all of the union members that have severance pay for years of service, plus pay for unused vacation and earned holidays. Health care benefits will be provided by the company until the end of the month from when an employee is terminated.
The agreement also addresses recall rights plus retention and incentive pay for new hires with less than one-year of seniority. In addition, existing successorship protections for the USW in connection with a potential sale were preserved.
Popovich said the final day of work for the majority of maintenance and production workers at the paper mill is October 5, but there is a small group of maintenance employees that is scheduled to do wind down work until January 31, 2013. Production for large contract orders will run until late night shift on September 30. He said 100 salaried workers at Snowflake paper will also be affected by the mill shutdown.
According to Bob LaVenture, director for the eleven-state USW District 12 that represents the Arizona paper mill, the union has engaged a financial consultant to reach out to paper companies and other investors to encourage them to pursue an acquisition that will sustain the family-supportive and skilled jobs at the mill.
The Snowflake facility is located in the foothills of the White Mountains in northeastern Arizona. The sale includes the equipment and other assets associated with the paper mill, approximately 19,000 acres of land, and The Apache Railway Co.
Back To Top
|
Verso Paper Corp., Memphis, Tenn., USA, reports that the Sustainable Resources Institute (SRI) will be the first recipient of a Verso Forest Certification Grant. The two-year grant will enable SRI to target the owners of small, private, non-industrial properties (2,400 acres or less) in Michigan and help them achieve certification at an affordable cost.
Third-party certification to credible forest management standards advances responsible management practices that keep U.S. forests vibrant and healthy. SRI's first-year goal to certify an additional 15,000 acres has the potential to add up to 35,000 tons of certified fiber in the marketplace, Verso notes.
"We launched the Verso Forest Certification Grant program to increase certified fiber and certified acreage on lands near Verso's three paper mills," said Verso SVP of Manufacturing and Energy Lyle Fellows. "SRI's grant proposal demonstrated not only a solid plan to help us advance this goal, but also strong partnerships with the Michigan Master Logger Certification program, the Michigan Association of Timbermen, and others that provide a strong foundation for success."
SRI Executive Director Don Peterson added that "startup funds provided by the Verso Forest Certification Grant will help us reach out to landowners who already have responsible forest management plans and offer them a more accessible path to affordable certification. We're anxious to get underway and are committed to seeking additional funding from other sources to make sure we're able to continue the terrific certification opportunities that Verso's initial two-year funding provides."
For more information about the Verso Forest Certification Grant Program, contact Greg Barrows at Verso's Bucksport, Maine, mill.
Back To Top
|
Containerboard/Packaging
Holmen AB, Stockholm, Sweden, report that its paperboard mill in Iggesund, Sweden, will make its operations more efficient, with employee numbers being cut from 900 to 800. The mill intends to make the cuts through normal personnel turnover-attrition (basically retirement) over a two-year period.
"We are active in a market that is subject to fierce competition and that is under immense cost pressure. High-quality products and high productivity are our competitive weapons, but we also need to constantly review our costs," said Björn Kvick, president of Iggesund Paperboard.
The cuts will be made through various initiatives such as reviewing the sheeting and wood chipping operations. SEK 2.3 billion has recently been invested at the mill in a new recovery boiler, laying the foundations for maintaining the company's competitive edge in the future.
Back To Top
|
At the end of September, Iggesund Paperboard inaugurated the new recovery boiler at its Iggesund Mill in Sweden. The ceremony was conducted by Lars G Sundblad, who was managing director of the company at the end of the 1950s, when the decision was made to begin manufacturing paperboard.
The new recovery boiler makes it possible for Iggesund to increase production of its paperboard Invercote, and also enables the mill to operate on 100% biofuel and be self-sufficient in energy, both thermal and electric. Construction of the recovery boiler took two years and cost SEK 2.3 billion (EUR 240 million).
The company is also building a biofuel boiler at its mill in Workington, England. That investment, for the production of the paperboard Incada, will cost SEK 1.1 billion (EUR 123 million) and involves a radical change of energy source from today's fossil natural gas to bioenergy. The new biofuel boiler at Workington is scheduled for completion in the spring of 2013.
Back To Top
|
Sonoco Recycling, a unit of Sonoco, Hartsville, S.C., USA, and one of the largest packaging recyclers in North America, has completed a $2 million upgrade at its Onslow County, N.C., materials recovery facility (MRF). The upgrades will allow the MRF to process a higher volume of recyclables.
With locations and expertise worldwide, Sonoco Recycling annually collects more than 3 million tons of old corrugated containers, various grades of paper, metals, and plastics. Currently, Sonoco Recycling operates six MRFs and serves more than 125 communities in which curbside-collected residential and commercial materials are processed. The company also provides recycling programs that identify waste reduction opportunities for many of the largest consumer product companies in the U.S.
"Onslow County is one of the premier coastal counties of North Carolina and environmental stewardship has always been of the utmost importance," said Scott Bost, solid waste director, Onslow County. "With that in mind, we are extremely pleased to partner with Sonoco Recycling to provide long-term recycling capabilities to the citizens of the Onslow County area. Sonoco Recycling's expertise and many years of experience in the recycling industry will continue to move the county forward with efficient and sustainable waste management."
Ray Howard, GM, Sonoco Recycling, agrees. "In the year that we've been here, we've found the Onslow community to be very progressive in the areas of sustainability and recycling. We are excited to provide them with expanded recycling capabilities and help the county continue to move forward in these areas."
In addition to new equipment, the company also added an education room, and has been providing tours to approximately three classes of students per week. Currently, the tours are open to students of all ages, including first grade through high school seniors."
Back To Top
|
Tetra Pak, Lausanne, Switzerland, marking its fortieth year of operations in Turkey, has inaugurated a new laminator at its packaging material factory in Izmir, Turkey. The VT laminator will increase production capacity by 20%, delivering innovative packages with shorter lead time to customers in the Turkey and Caucasus, and enabling export to the region.
The new laminator, which begins production in January 2013, will boost production capacity from 5 billion packs to approximately 6 billion. It is capable of laminating all types and sizes of Tetra Pak packages.
Tetra Pak Turkey & Caucasus Managing Director Francis Goodenday said that "in an increasingly competitive world, Tetra Pak recognizes the need to offer our customers the very best products, technology, and service. This investment will enable us to meet our customers' needs in a continuously growing, dynamic market by providing them with faster lead times, innovative packages, and all the advantages of local supply and support."
Back To Top
|
New Products
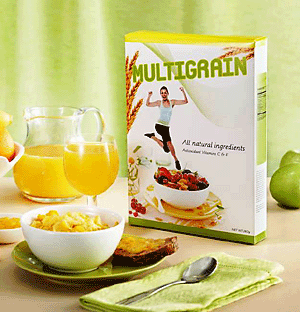 Stora Enso, Finland, reports that its Tambrite board has been upgraded in quality as a result of an investment program completed at the Ingerois Mill in Finland. Tambrite is a fully coated folding boxboard with a cream reverse, offering high performance in dry and frozen foods as well as confectionery and pharmaceutical packaging solutions. Its stiffness, smoothness, and printability are complemented by a high yield.
The company notes that Tambrite is especially designed for applications where laser or inkjet coding and Braille embossing are required. Its most important technical improvement, the company adds, is increased cross direction stiffness and visual appearance.
In pharmaceutical packaging, reliability and performance of cartonboard in all required processes is of utmost importance, Stora Enso continues, pointing out that Tambrite has a good visual appearance and is performing well in printing and converting processes including digital printing. In food packaging, where robustness of the package plays an important role, Tambrite also performs very well.
According to the recent Cartonboard Brand Tracking Survey 2012 by the research agency Opticom International Research AB, Finland, Tambrite is the most acknowledged virgin fiber cartonboard product brand among converters in Central European markets. The survey also revealed that Tambrite is the best-selling brand in Germany, Benelux, Italy, and Spain.
Back To Top
|
Weyerhaeuser Co., Federal Way, Wash., USA, reports that it has launched a proprietary, patent-pending form of thermoplastic composite that uses sustainably sourced cellulose fiber as a reinforcement additive. Called THRIVE™ composites, the product will initially be used in household goods and automotive parts (also see Ford Motor article in the Weekly Spotlight section above). In addition, THRIVE can be used in a variety of composite plastic applications, including office furniture, kitchenware, small and large consumer appliances, and other industrial goods.
Weyerhaeuser notes that THRIVE composites offer several advantages over materials reinforced with short glass fibers or natural fibers such as sisal, hemp, and kenaf. The product is available in master batch form for custom compounders and ready-to-mold thermoplastic pellets for molders.
"THRIVE composites are economical and widely available, and they are low mass yet demonstrate excellent tensile strength and flexural properties," said Don Atkinson, VP, marketing and new products for Weyerhaeuser's Cellulose Fibers business. "These composites can improve molding cycle times up to 40%. Products made with THRIVE require less energy to produce and can reduce wear and tear on processing equipment when compared with those containing abrasive short glass fibers. These substantial benefits create significant advantages for companies looking to reduce their carbon footprints while enhancing performance and productivity."
THRIVE composites are currently available as cellulose blended with polypropylene with both high and low melt flow indices. Because cellulose fibers are compatible with various "workhorse" polymers, Weyerhaeuser plans to expand the THRIVE line of products beyond polypropylene to a range of hydrocarbon and nonhydrocarbon polymers.
"THRIVE products readily absorb dyes and offer excellent flowability and thin-section fill, providing manufacturers with considerable design flexibility," Atkinson said. "In addition, THRIVE composites are produced using a proprietary process that allows control of the dispersion of cellulose fibers within the polymer matrix. This allows for a smooth surface finish, which opens up new opportunities for the use of natural fibers in composite plastics. Conversely, if manufacturers prefer the fibers to be visible, they have that option as well."
In addition to enhanced design aesthetics, Weyerhaeuser adds that THRIVE products demonstrate consistent performance characteristics from batch to batch, "which isn't always the case with other natural fibers." Also, the cellulose fiber in THRIVE composites is sourced in part from some of the 20 million acres of forestland that Weyerhaeuser manages to third-party sustainability standards, ensuring a readily available global supply from a trustworthy source, the company points out.
Back To Top
|
Published Pricing
Fibria, Brazil, the world's biggest producer of bleached eucalyptus kraft (BEK) pulp, has begun informing customers that it will increase its price for BEK in Europe to $780/metric ton, according to RISI, Brussels. Belgium. The price increase becomes effective October 1.
The company operates three pulp mills in Brazil (Aracruz, Jacarei, and Três Lagoas) with a combined annual production capacity of 5.25 million metric tons of pulp. It also has a 50% stake in Veracel (a joint-venture with Stora Enso of Finland) in Bahia. Located in Barra do Riacho, Espírito Santo, 70 km from Vitória, the Aracruz mill has three fiber lines (Mills A, B, and C), with a total annual capacity of 2.3 million metric tons of bleached pulp. The Jacarei mill is in São Paulo State and has a production capacity of 1.1 million metric tons of bleached pulp per year, 91% of which is exported. The Três Lagoas mill is in Mato Grosso do Sul State and has a production capacity of 1.3 million metric tons of pulp per year. Veracel, opened in 2005, produces about 1.1 million metric tons of bleached pulp per year.
Back To Top
|
People
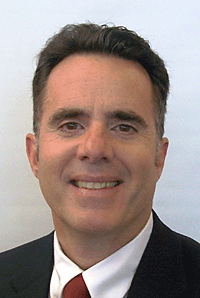 The Herty Advanced Materials Development Center, Savannah, Ga., USA, has named Alexander Koukoulas, Ph.D., its president and CEO. Koukoulas, a well-known scientist and entrepreneur, previously served as managing director of ANL Consultants, a private consulting firm supporting the pulp and paper, biomaterials, and bioenergy industries. Koukoulas will begin his new role on November 1.
Herty's clients, which include global corporations as well as numerous Fortune 500 companies, are currently focused in the transportation, forest and paper related products, building materials, energy and the environment, and bio-products industries. In April 2012, Georgia Governor Nathan Deal transferred management of the Herty Advanced Materials Development Center to Georgia Southern University with a goal of enhancing economic and business development in the state of Georgia.
Prior to his role at ANL Consultants, Koukoulas served as VP and executive director of research and development at Albany International. Earlier in his career, he served in increasingly responsible leadership positions at International Paper, including chief scientist, where he directed research and was responsible for new product development and R&D supporting the company's pulp, paper, and packaging business units.
One of Koukoulas' primary goals will be to enable Herty's clients to achieve their R&D and financial goals while working to create an environment that cultivates opportunity for businesses to relocate or stay within Georgia. The result, according to Charles Patterson, Ph.D., VP for research and economic development at Georgia Southern University, and officials at Georgia Southern, will be more jobs and an expanded national reputation helping put Savannah on the map as a center for advanced materials innovation.
Koukoulas received his Bachelor of Science and Ph.D. degrees in Chemistry from McGill University. He is currently pursuing an Executive Certificate from the Sloan School of Management at M.I.T. He has published numerous presentations and publications and holds numerous U.S. patents. He is a scientific advisor and bioenergy expert.
Back To Top
|
PaperlinX, Australia, this past week reported several changes to its board of directors. Michael Barker has been named chairman and a non-executive director, effective immediately, ensuring an ongoing quorum. As a result of this appointment, the three previously announced resignations of Harry Boon, Lyndsey Cattermole, and Anthony Clarke have been brought forward to be immediately effective.
Subsequently, Robert Kaye was appointed to the board as a non-executive director, effectively immediately, and Michael McConnell resigned from the board, effective beginning at 5 p.m. the night prior to the next general meeting of shareholders.
Barker is an actuary with a career background in institutional investment management and has held a number of senior executive positions including with NatWest Investment Management, County NatWest Investment Management, and Aetna Life and Casualty. He has served as a non-executive director on a number of boards in the financial and property sectors and is currently a director of Metlife Insurance Ltd.
Kaye is a senior counsel in NSW who has given legal and strategic advice and acted for many public and private financial institutions and commercial enterprises. He has had significant mediation experience and has been involved in the successful resolution of complex disputes in an array of commercial matters both advisory and litigious in nature.
Barker noted that "as the newly elected chairman, I am committed to working with the other directors and management to build rapidly and efficiently on the restructuring and diversification plans already announced and restore value to our shareholders. We are very conscious of the interests of the hybrid holders and other stakeholders, and plan to return the company to profitability
"The industries in which we operate have been facing challenging times, particularly in Europe, and major efforts are being devoted to our European operations to bring their results in line with the better performing operations in Australia, New Zealand, Asia, and Canada. We have a significant presence in many of the countries in which we operate, and we intend to leverage on our global position in coming months," Barker concluded.
Back To Top
|
TAPPI News
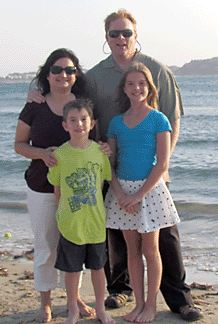
TAPPI Member Garnet Bremner describes TAPPI as a "mosaic" of individuals whose depth of experience and knowledge creates a wonderful atmosphere for finding outstanding mentors.
Bremner now works as an industry consultant for an air, water, & energy solutions and services provider. He began his pulp and paper industry career in a mill engineering role in Canada. Eventually, he successfully worked into deinking supervisory positions, also working to rebuild recycling mills, and then finally serving as a mill manager himself. Bremner has been an active TAPPI member, participating in officer roles on various committees and as a program chairman. Currently, he is serving as the PMD program chair for the PEERS 2012 conference being held October 14-18 at the Marriott Riverfront in Savannah, Ga., USA.
Learn more about the upcoming PEERS Conference.
Bremner says that having a short list of contacts from mill operations, academics, R&D fields, equipment vendors, chemical vendors, automation vendors, and consultants of all types of expertise provided him with a support group to help with challenges.
Find out more by reading this month's Member Spotlight.
Spotlight participants are recommended by fellow members and staff. If you would like to nominate a member, just send name (or names) to MemberSpotlight@tappi.org. We will forward a Spotlight Questionnaire ( click here) for you to fill out and return.
We look forward to seeing you "In the Spotlight!"
Back To Top
|
See who all is attending the upcoming PEERS and IBBC conferences in Savannah, Ga., USA:
About PEERS:
PEERS is a "must attend" event for anyone seeking to make their mill run more efficiently. The Pulping Program focuses on ways to improve kraft pulping to afford pulps that are more uniform in quality and to afford higher pulp yields. The Engineering Program has added a focused one-day session focusing on OpEx Maintenance and Reliability. The Environmental Program will address the challenges and costs involved in keeping up with the regulations of the U.S. paper industry. The Recycling Program brings together experts from around the world to present new technological breakthroughs related to fractional pulping, absorption deinking and electrostatic deinking. Keynote Speaker Don Roberts will discuss why the pulp and paper industry should be open to change by presenting a case study in commercializing an emerging bio-energy technology and the key success factors as part of the Sustainability Program.
Your investment of time and money will go far with the full program of both educational and career networking opportunities presented at PEERS 2012.
PEERS will be co-located with IBBC 2012, the only conference that is dedicated to examining applications of biorefineries in the pulp and paper industry - offering you a deeper analysis of technology and economics in commercializing biorefineries. See the Full Program.
IBBC Keynote Speakers:
- Paul Spindler, VP of Technology at Catchlight
- John B. Crowe, Chairman and CEO, Buckeye Technologies, Inc.
In addition, IBBC will include technical presentations, expert panels, case studies, and reports from projects that address:
- Feedstock and harvesting improvements to increase yield and quality of biomass
- Bioconversion technologies for wood and biomass
- Production of chemicals and transportation fuels from wood and biomass
- Commercial bioenergy products using woody biomass
- Tools for evaluating bioenergy projects.
We look forward to seeing you soon, October 14-18th, for these two great conferences happening in Savannah!
Back To Top
|
TAPPI's 2012 Nominating Committee presents a slate of candidates for two officer and three director positions on the TAPPI Board. The candidates are: chair, Thomas J. Garland; vice chair, Chris Luettgen, Kimberly-Clark; and directors, Daniel D. Cappell (AstenJohnson), Kirt J. Cuevas (International Paper), and Robert A. Feeser (MeadWestvaco Corp.).
Voting begins December 1.
Per the TAPPI Bylaws, members of the organization have until November 1 to review the slate.
More information about the slate and election process is available online.
Back To Top
|
Attend this FREE TAPPI Webinar!
Process Control: Combat Process Disturbances and Interactions
Time: 12:00 p.m. to 1:00 p.m. EST
Monday, October 10, 2012
Learn how to employ new tools to easily assess the effects of interactions and disturbances on your process (the models) and how to use these to break or eliminate loop interactions and the effects of disturbances. Appropriate for managers, process engineers, and process control engineers.
Register to attend
This webinar is presented by TAPPI's Process Control Division and was selected as the best Process Control Paper at PaperCon 2011.
Participants will receive a 25% discount on Paper Machine Quality Control Systems - Volume 1: Measurement Systems and Product Variability by the Quality Control Systems Education Common Interest Group of the Process Control Division.
Back To Top
|
The Corrugated Containers Manufacturing Process
Authors: Jody A. Brittain, Stephen R. Perkins, and Philip G. Schnell
This comprehensive textbook describes the entire process of manufacturing corrugated containers. In addition to detailed explanations, the book also features practical troubleshooting tips and a discussion of common problems and solutions within each major section. Seven detailed chapters cover the following topics:
- Paper and the Papermaking Process
- Steam
- Corrugating Adhesives
- Singleface Operations
- Doublebacker Process
- Combined Board
- Converting.
This textbook is designed to provide in-depth explanations and information for professionals working in all areas of the corrugated containers industry.
Product Code: 0101R281
Member Price: $37.00
Non-Member Price: $185.00
Back To Top
|
Join us at this new lovely golf center near Memphis, Tenn., USA to hit a bucket of balls and enjoy food and fellowship at our Driving Range Fundraiser. Proceeds will support scholarships at Christian Brothers University Packaging Program.
The event will be held in Cordova, Tennessee on October 22 from 5:30 - 9:30pm.
Prizes all for a great cause!
- Team & Individual Events
- Longest Drive
- Nearest the pin
- Silent Auction
- Golf Trivia
- And much, much more...
Visit www.tappi.org/CBUFundraiser for more information and to learn about sponsorship opportunities.
Back To Top
|
This text, edited by Carlton W. Dence and Douglas W. Reeve, covers fundamentals and processes from the chemical composition of pulp to the technology, production, and the environmental impact of bleaching. Designed as both a textbook and a reference book, Pulp Bleaching: Principles and Practice explains what bleaching is, why pulp is bleached, and how bleaching is done.
The book also features discussions on several "hot topics" in pulp bleaching, including elemental chlorine free bleaching, totally chlorine free bleaching, enzyme assisted bleaching, and bleaching of recycled fiber. In addition, the book is key-word indexed and each chapter contains extensive references.
Pulp Bleaching: Principles and Practice
Product code: 0102B061
Member Price: $124.00
Non-Member Price: $186.00
Back To Top
|
Yankee drying experts from around the world are planning their fall meeting for November 5-6 in the heart of North American tissue making, Neenah, Wis., USA. The committee meets twice per year to share knowledge and best practices to increase safety and reduce delay that negatively impacts dryer operations and overall productivity. The fall meeting will include the development of standard practices and presentations on doctor setup/profiling and metalizing yankee dryers.
More information and registration details are available online.
The meeting will be held in conjunction with the Lake States TAPPI/North Central PIMA Energy Forum and is open to all TAPPI members and visitors (one time only). To attend as a visitor, please contact Scott Springmier.
Immediately following the biannual Yankee Dryer Safety and Reliability Meeting, TAPPI will hold the popular Tissue Runnability Course November 7-9 at Miron Construction in Neenah. The course will provide an excellent knowledge base for process engineers, machine supervisors, reliability professionals, and suppliers responsible for maximizing uptime and saleable tissue production. Attendees will learn to:
- Improve tissue quality and consistency
- Understand contributors to waste and downtime
- Learn reliability and maintenance best practices
- Diagnose and troubleshoot problems quickly.
The course includes two and one-half days of focused instruction from a dozen globally recognized tissue making experts.
More information is available online. A registration discount is offered to TAPPI members.
Back To Top
|
Biomass Subcommittee Hosts Webinar Featuring Biomass Modeling Tool
As the competition for biomass increases, there is a growing need to more rigorously understand and predict supply availability, sustainability, and economic feasibility of biomass sources. This is true for existing pulp mills as well as new biorefineries.
TAPPI's Biomass Supply, Handling & Handling Subcommittee is hosting a webinar for their next subcommittee meeting featuring a new modeling tool available from Enegis: Biomass Energy Analytical Model (BEAM). BEAM can assess biomass energy availability, including transport options and delivery costs, modeling resources from field/forest, through processing, to determining demand - providing a geographic quantification, storage, and densification options as well as transportation analysis.
The model has a 30 meters resolution for the lower 48 states, and currently carries about 50 species and commodities as it performs analysis with costs of net energy and net carbon carried forward at all modeling steps. BEAM can conduct assessments on a site-specific, regional, or national-scale. Focus on residuals, consistent with the American Council on Renewable Energy (ACORE) proposed definition of biomass, has been run in a number of cases including mark to market. BEAM was originally developed for the Federal Energy Management Program.
Please come join us for the next subcommittee meeting and this presentation on Tuesday, October 9th from 1:00-2:00 PM.Subcommittee Chair Bob Hurter and Vice-Chair Bill Fuller will provide an update on subcommittee activities.
Webinar Registration
- This webinar is free to all who are interested!. Click here to register for this one-of-a-kind opportunity to learn about cutting-edge technology and commercial strategies as it relates to new business opportunities in the biomass sector.
Back To Top
|
TAPPI's International Bioenergy and BioProducts Conference, October 17-19, in Savannah, Ga., USA will focus on advancements and commercialization of bioconversions that leverage the forest products manufacturing infrastructure, providing you with a deeper analysis of the technology and economics involved in commercializing biorefineries. Click here to learn more about the IBBC full technical program.
Keynote Speakers:
- Paul Spindler, VP of Technology at Catchlight
- John B. Crowe, Chairman and CEO, Buckeye Technologies, Inc.
In addition, IBBC will include technical presentations, expert panels, case studies, and reports from projects that address:
- Feedstock and harvesting improvements to increase yield and quality of biomass
- Bioconversion technologies for wood and biomass
- Production of chemicals and transportation fuels from wood and biomass
- Commercial bioenergy products using woody biomass
- Tools for evaluating bioenergy projects.
IBBC will be co-located with the TAPPI PEERS Conference, creating a value-added opportunity for participants to expand their learning, networking, and resources by attending both events.
Exhibit and Sponsorship opportunities are available. Contact Shane Holt via e-mail or at 800.369.6220, ext. 3345 for more information.
Back To Top
|
The 2012 TAPPI Internatioal Bioenergy & Bioproducts Conference, taking place October 17-19 in Savannah, Ga., USA, offers you a deeper analysis of technology and economics in commercializing biorefineries. IBBC is the only event dedicated to advancing biorefineries in the forest products industry. Hear the latest on biomass development, as well as the thermochemical and biochemical-based technologies that can be profitably integrated into pulp mills.
Program Highlights:
Session 4: Bioenergy Policy: Three Perspectives
Panel Moderator: Steve Betzler - Paper Segment Leader, Minnesota Power
Wednesday, October 17, 2012 - 4:00-5:30pm
Panel Themes: What role can government policies play in the development of bioenergy in the forest products industry in North America? Come and hear three policy experts assess recent bioenergy policy impacts and discuss future priorities for Canadian and US policies. Panelists include representatives of two forest industry public policy organizations (FPAC and AF&PA) and a representative of a major industrial forestland owner. A timely topic for the election seasons in North America...
Panelists:
Catherine Cobden - Executive VP, Forest Products Association of Canada
Mike Jostrom - Director Renewable Resources, Plum Creek
Paul Noe - Vice President for Public Policy, American Forest & Paper Association
Learn more about IBBC.
Click here to see the entire program.
Back To Top
|
Gain a better understanding of kraft pulping operations and the effect of process on quality.
An encore, one-day presentation of the popular Intro to Kraft Pulping Workshop will be held in conjunction with the 2012 TAPPI PEERS Conference, October 14-17 in Savannah, Ga., USA. This workshop, held on Saturday, October 13, will be lead by Dr. Michael J. Kocurek, Professor Emeritus of Paper Science and Engineering at North Carolina State University.
The Intro to Kraft Pulping Workshop is a condensed version of the pulping portion of the full course. The overall course objective is to give participants increased understanding of kraft pulping operations, awareness of how one part of the process affects other operations, and the effect of processes on kraft pulp quality.
Learn more about this workshop.
Pulp and Paper Companies Get Discounted Registration!
TAPPI offers a discounted registration to pulp and paper mills and their corporate offices to attend the PEERS Conference. Bring an unlimited number from your mill or office to visit for one day, one hour, or just to drop in and see the Trade Fair! Learn more.
Register Now for PEERS and Save!
The 2012 TAPPI PEERS Conference will be co-located with the International Bioenergy and Bioproducts Conference, creating a value-added opportunity for you to expand your learning, networking and resources by attending both events.
See you in Savannah!
Back To Top
|
Don't miss out on the new Operating Excellence (OpEx) Maintenance and Reliability Seminar at PEERS 2012!
This is a first-time program for the 2012 TAPPI PEERS Conference.
Maintenance and reliability continue to be critical to the efficient operation of pulp and paper mills worldwide, just behind fiber and labor as top production cost factors.
This one-day seminar explores the latest reliability strategies today's mills are implementing to stay in-tune and competitive under progressively lean operating conditions.
The OpEx Maintenance and Reliability Track, included in your PEERS registration at no extra cost, is part of the Engineering Program.
If you are only interested in attending the OpEx Track, select the Single Day PEERS Registration for Thursday, October 18. This year's PEERS Conference includes a full program of educational opportunities for maintenance and reliability personnel, including:
- Sunday, Oct. 14: Fixed Equipment Maintenance Optimization System Course (Additional Fee)
- Monday, Oct. 15 - Wednesday, Oct. 17: Corrosion & Materials Engineering Track
- Thursday, Oct. 18: OpEx Maintenance and Reliability Track.
2012 TAPPI PEERS Conference, October 14-17 in Savannah, Ga., features a detailed technical program. Five programming tracks of peer-reviewed sessions, Pulping, Engineering, Environmental, Recycling and Sustainability, will answer the most pressing business and technical questions faced by pulp and paper companies as they manage raw materials, assets, regulatory requirements and production assets.
Register now and save.
The 2012 TAPPI PEERS Conference will be co-located with the 2012 International Bioenergy and Bioproducts Conference, creating a value-added opportunity for you to expand your learning, networking, and resources by attending both events.
See you in Savannah!
Back To Top
|
Attend the Fixed Equipment Maintenance Optimization System Workshop (FEMOS)
Sunday, October 14, 2012; 8:00 a.m. - 5:00 p.m.
Mills annually spend millions of dollars inspecting, repairing, and recovering from unexpected leaks in boiler tubes, tanks, pressure vessels, exposed and buried pipes, stacks, bleach towers, etc. – learn how to substantially reduce those costs! Corrosion Probe Inc.'s FEMOS Workshop training shows maintenance staff how to rationally manage the mechanical (containment) integrity of all types of fixed equipment with a simple, rigorous system utilizing comparable disciplines and procedures promoted by vendors specializing in maintenance of rotating equipment.
What will you learn?
The workshop teaches attendees how to implement a mill-specific program by using a transparent and disciplined process to systematically design the right inspection plan for each major piece of fixed equipment based on its materials of construction, present condition and service conditions. The basic concept employs proven, high-value practices from refining and petrochemical industries for risk-based inspection, customizing inspection plans to possible damage mechanisms and using fitness-for-service engineering assessments to define damage limits.
Who is leading the workshop?
Corrosion Probe Inc.'s experienced and renowned TAPPI participants Dave Bennett, David Crowe, and Doug Sherman, will train up to 20 people in a one-day (6-hour) workshop. Training is presented so attendees can use their new knowledge to immediately implement FEMOS at their mill. Many working examples are provided and students are invited to bring their mill's costliest fixed equipment inspection/ maintenance concern for case analysis.
The workshop takes place just before the TAPPI PEERS and IBBC conferences so those attending the FEMOS workshop can also attend these important events.
Learn more about PEERS 2012...
Back To Top
|
Why Whitewater Filtration Systems Fail
Time: 12:00 p.m. to 1:00 p.m. EST
Wednesday, November 14, 2012
This free webinar from TAPPI addresses why whitewater filtration systems are often problematic and in some instances fail completely. The presentation will explain why filtration systems fail under certain conditions and offers the best solutions to improve the overall reliability of the process.
Attendees will learn:
- Significance of process variation on equipment performance
- The negative cost impact associated with poor system performance
- New sensor technology that is making the system "visible"
- Cutting-edge strategies to manage the process variation
- How to develop a "roadmap' for system optimization.
Learn more and register
Back To Top
|
Nov. 7-9, 2012 - TAPPI will conduct it's Tissue Runnability Course in Neenah, Wi., USA.
This special course is being taught by technical experts in each area of the machine from wet end operations through creping and process control. The experienced, highly qualified faculty for this course will provide a thorough understanding of the entire tissue making process and current best practices in each area.
Wednesday's (November 7) classes will focus on stock preparation and wet end operations, while Tuesday's (November 8) classes cover pressing, drying, and doctoring. Wednesday (November 9) classes examine technologies and latest developments in hoods, TAD (through-air drying), and other dynamics of the tissue machine dry end,
The 2012 TAPPI Tissue Runnability Course is designed for process engineers, machine supervisors, and reliability professionals who have to maximize uptime and saleable production. It is also an excellent tutorial for suppliers who support tissue making customers. It will help attendees:
- Improve tissue quality and consistency
- Understand contributors to waste and downtime
- Learn reliability and maintenance best practices
- Diagnose and troubleshoot problems quickly.
After successfully completing this course, attendees will specifically be able to:
- Diagnose the impact of recycled furnishes on tissue properties
- Make changes to wet-end chemistry to improve machine operations
- Improve cleaning and conditioning of fabrics
- Troubleshoot runnability problems in the press, Yankee, and creping systems
- Identify improvement opportunities on the dry end
- Pinpoint productivity opportunities in Yankee steam, coating, and hood systems.
TAPPI will award CEU credits to participants who attend at least 80% of the educational sessions and complete a final program evaluation.
The 2012 Tissue Runnabilitry Course includes advanced process instruction. If you are looking for an introductory-intermediate tissue course, consider the upcoming 2012 Tissue Properties and Manufacturing Course at TAPPI Headquarters in Norcross, Ga., USA, on August 15-16.
Attendance for the 2012 TAPPI Tissue Runnability Course is limited, so please register today at the course website.
Back To Top
|
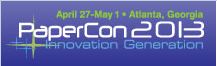
Deadlines for the PaperCon Call for Papers and Posters are fast approaching!
- The Deadline for Coating Program Submissions is October 16.
- The Deadline for Papermakers Program submissions is November 20.
A Call for Papers has been issued for PaperCon 2013. This year's theme is "Innovation Generation."
After record attendance in 2012, PaperCon will again bring together CEOs, mill managers, superintendents, scientists, process engineers, and suppliers for the largest pulp and paper technical program in the world. The event will take place April 27 - May 1, 2013 in Atlanta, Ga., USA. Learn more about PaperCon 2013.
For 2013, PaperCon is pleased to welcome the Tissue360 Forum, NETInc (Innovative Nonwovens Conference), RPTA (Recycled Paperboard Technical Association) P-T Seminar and the OpEx Reliability Workshop. Each of these events is open to full PaperCon registrants and papers in these areas are welcome.
Calls for Papers and Posters have been issued. The conference theme is Innovation Generation, and authors are encouraged to include this within their papers. Topics under consideration include mill management, papermaking, coating, tissue, nonwovens, and recycled paperboard. Paper company personnel, suppliers, academics, and students are strongly encouraged to submit their ideas for papers, posters, or roundtable discussions.
Coating and Graphic Arts Program:
The Coating and Graphic Arts Program will focus on The Future of Print and its Demands on Paper and Coatings. The deadline for extended abstracts for this program is Oct. 16, 2012.
See the Coating and Graphic Arts Program Call for Papers.
Papermakers Program:
The Papermakers Program encourages topics on paper machine performance evaluations, papermaking fundamentals, product/process optimization, recycled paperboard, tissue making (Tissue360 Forum), and the RPTA P-T Seminar.
The deadline for submission of this program's abstracts will be November 20, 2012.
See Papermakers Program Call for Papers.
Abstracts for panel discussions and roundtables are welcome. All abstracts must be submitted using TAPPI's Speaker Management System for consideration by the TAPPI and RPTA program committees.
Back To Top
|
The 20 volumes of Papermaking Science and Technology bookseries cover the entire paper manufacturing process from wood raw material to end product, providing a basis for university-level education, for updating training courses, and as handbooks for the industry. The bookseries has been updated and second editions are now available. TAPPI members can place an order by contacting The Finnish Paper Engineers' Association. Please contact Mary Anne Cauthen, Member Group Coordinator, at +1.770.209.7352 or by e-mail at MCauthen@TAPPI.org
These books can be purchased individually or as a set.
This 20 volume set includes:
- Volume 1 - Economics of the Pulp and Paper Industry
- Volume 2 - Forest Resources and Sustainable Management
- Volume 3 - Forest Products Chemistry
- Volume 4 - Papermaking Chemistry
- Volume 5 - Mechanical Pulping
- Volume 6, part 1 - Chemical Pulping Part 1, Fiber Chemistry and Technology
- Volume 6, part 2 - Chemical Pulping Part 2, Recovery of Chemicals and Energy
- Volume 7 - Recycled Fiber and Deinking
- Volume 8 - Papermaking Part 1, Stock Preparation and Wet End
- Volume 9 - Papermaking Part 2, Drying
- Volume 10 - Papermaking Part 3, Finishing
- Volume 11 - Pigment Coating and Surface Sizing of Paper
- Volume 12 - Paper and Paperboard Converting
- Volume 13 - Print Media - Principles, Processes, and Quality
- Volume 14 - Process and Maintenance Management
- Volume 15 - Materials, Corrosion Prevention and Maintenance
- Volume 16 - Paper Physics
- Volume 17 - Pulp and Paper Testing
- Volume 18 - Paper and Board Grades
- Volume 19 - Environmental Management and Control
- Volume 20 - Biorefining of Forest Resources
Back To Top
|
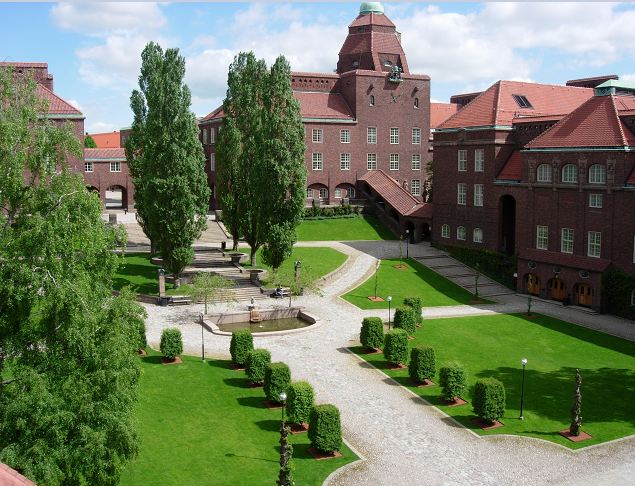 The 2013 TAPPI International Conference on Nanotechnology for Renewable Materials will be held July 24-27, 2013, on the KTH Royal Institute of Technology campus in Stockholm, Sweden. Industry experts, scientists, health and safety specialists, legal and government policy makers, as well as the field's leading researchers will discuss the latest in nanotechnology research and development.
The 2013 Technical Program Committee has issued a Call for Papers inviting contributions from participants working in research, development, and deployment of renewable nanomaterials.
Abstracts are due by December 3, 2012.
Back To Top
|
Make your plans now to join a host of professionals from industry, universities and research institutes at the 14th TAPPI European PLACE Conference, which will be held May 6-8, 2013, at the Swissotel in Dresden, Germany.
The Call for Papers is now officially open. Submit your abstract and take an active role in this not-to-miss event!
Back To Top
|
|
|
TAPPI Over the Wire | 15 Technology Pkwy. S. | Norcross, GA 30092 USA | Voice: 770.446.1400 | Fax: 770.446.6947
|
 |