 |
|
Weekly Spotlight
Wausau Paper, Mosinee, Wis., USA, this week announced the closure of its technical specialty paper mill in Brainerd, Minn., to occur early in the second quarter of this year
Learn More...
|
Life-style changes and the need for product differentiation have put pressure on the quality and sales appeal of food packaging
Learn More...
|
The Institute of Paper Science and Technology (IPST) at Georgia Tech, Atlanta, Ga., USA, has awarded three prizes totaling $20,000 to students competing in the 2013 Georgia Tech Research and Innovation Conference (GTRIC)
Learn More...
|
Earlier this week, the Boston Globe ran a feature article on current operations and outlook for the East Millinocket, Maine, USA, mill that was acquired by New Hampshire-based Cate Street Capital in August 2011, along with its sister mill in nearby Millinocket, Maine
Learn More...
|
Third-grader Sarah Shreve's teachers had never heard her speak—until recently, when the student at Lone Oak Elementary School in Loan Oak, Texas, USA, wrapped up the voting in a national video contest she had entered with a comment about her effort
Learn More...
|
Domtar Corp., Montreal, Que., Canada, has announced the latest additions to its award-winning site, The Paper Trail.
Learn More...
|
The OpEx Maintenance and Reliability Workshop at TAPPI PaperCon 2013 in Atlanta, Ga., USA, on April 30, will include a special joint session with the Recycled Paper Trade Association (RPTA) that explores Operator Driven Reliability (ODR) from an up-close, mill case-study perspective
Learn More...
|
An Institute of Paper Science and Technology (IPST), Atlanta, Ga., USA, February workshop developed potential forest bioproducts industry scenarios for 2035 that consider constrained resources, changed production processes, new mill concepts, and a greatly expanded world population with different markets and market expectations
Learn More...
|
TAPPI's 2013 Tissue Properties and Manufacturing Course, to be held in conjunction with PaperCon 2013, covers the fundamentals of manufacturing and provides an excellent overview of this dynamic market segment
Learn More...
|
Below is the latest listing of job openings in the TAPPI Career Center.
Learn More...
|
Market Roundup
U.S. Containerboard production in January rose 1.7% over December 2012 and 3.5% over the same month last year
Learn More...
|
CEPI (Confederation of European Paper Industries), Brussels, Belgium, reports that paper and board production by CEPI member countries fell by in the region of 1.7% in 2012
Learn More...
|
Total U.S. boxboard production increased by 0.9% in January compared with January 2012 and increased 1.7% from last month
Learn More...
|
Demand growth for white top liners has increased significantly higher than the overall growth in corrugated packaging during the past year, according to a new report released this week by RISI, Boston, Mass., USA
Learn More...
|
Total U.S. kraft paper shipments in January were 140,500 tons, an increase of 19% compared with the prior month
Learn More...
|
Pulp & Paper
Catalyst Paper, Richmond, B.C., Canada, is taking a major step forward in its Latin American market development strategy with the launch of Marathon Lite, a high-performing newsprint grade with a basis weight of only 40 gsm
Learn More...
|
Clearwater Paper, Spokane, Wash., USA, successfully started up its new Metso (Finland)-supplied Advantage THRU-AIR (TAD) tissue machine at Shelby, N.C., in mid-December, and the startup curve has proceeded as scheduled
Learn More...
|
Domtar Corp., Montreal, Que., Canada, reports that it was a premier sponsor of the GreenBiz Forum 2013 in New York City, February 19-21
Learn More...
|
Grigiškes AB, Lithuania, plans to increase its tissue production capacity, reporting that it has secured a EUR 10 million loan from Skandinaviska Enskilda Bankens (SEB) and will invest the money in a new tissue machine
Learn More...
|
KP Tissue Inc. (KPT), Montreal, Que., Canada, which owns approximately 16.9% in Kruger Products L.P. (KPLP), announced that KPLP has successfully finished the construction phase of its TAD (Through-Air-Dried) tissue project at its Memphis, Tenn., mill
Learn More...
|
ST Tissue LLC, Oconto Falls, Wis., USA, has started up its new PMT Italia (Italy) yankee dryer on the converted PM 6 at Franklin, Va., USA (photo).
Learn More...
|
Containerboard/Packaging
Amcor, Australia, will acquire select printing assets of AGI-Shorewood's Tobacco Packaging and Specialty Folding Carton Operations for $114.8 million
Learn More...
|
The Europac Group, Madrid, Spain, has acquired a corrugated board factory in Caradec, France, for EUR 21.7 million, expected to become effective March 1
Learn More...
|
Through collaboration with the Paperboard Packing Council (PPC), Springfield, Mass., USA, the Arbor Day Foundation will once again provide discounted tree saplings to companies throughout the U.S. and Canada, as a way to honor Earth Day on April 22, and National Paperboard Packaging Week, April 22-26
Learn More...
|
Rigid Containers Ltd., U.K., part of the VPK Group, this past week reported that it will open a new corrugated packaging facility in England, its third one in that country
Learn More...
|
|
New Products
Fruitapeel, a U.K.-based manufacturer of own-label and branded juices and smoothies, has partnered with Elopak to launch the U.K.'s first gable top carton aseptic filling line for Juice.
Learn More...
|
Tetra Pak, Lausanne, Switzerland, this week announced new developments to its packaging solutions portfolio
Learn More...
|
Published Pricing
Metsä Fibre, Finland, has announced a new price for its Botnia Nordic Pine (Northern Bleached Softwood Kraft) in Europe, effective March 1, until further notice
Learn More...
|
PaperWorks Industries Inc. (PWI), Philadelphia, Pa., USA, this week announced price increase of $40 per ton for all MasterWorks grades of coated recycled boxboard, and $25 per ton for MasterWorks URB+ uncoated recycled boxboard
Learn More...
|
Sappi Fine Paper Europe, Brussels, Belgium, will increase its prices for all coated fine paper sheets and reels by 5% - 7%, effective April 1
Learn More...
|
People
Western Forest Products Inc., Vancouver, B.C., Canada, has appointed Don Demens president and CEO, effective immediately
Learn More...
|
Travels with Larry
Our visit was in response to an invitation by a 30-year TAPPI member who has served on at least seven committees, and is also the recipient of at least five TAPPI awards—Senior Group Leader for Ashland Water Technologies, Frank Sutman
Learn More...
|
TAPPI News
TAPPI has elected three new members to the Board of Directors. They will begin their three year terms starting in March 2013.
Learn More...
|
TAPPI's Annual Business Meeting will be held on March 12 via teleconference.
Learn More...
|
Webinar set for Match 13 is focued on Increasing Paper Machine Agility with a Novel Grade Change Concept.
Learn More...
|
Introductory level webinar offers overview of tissue manufacturing for softness and bulk.
Learn More...
|
TAPPI has partnered with PPSA to bring you the best safety practices in the industry.
Learn More...
|
Organized by tissue experts, this comprehensive technical forum will cover all aspects of tissuemaking.
Learn More...
|
The TAPPI Tissue Properties & Manufacturing Course will be held on April 27-28, 2013, in Atlanta, Ga., USA, co-located with PaperCon 2013 and the Tissue Forum.
Learn More...
|
The TAPPI International Best practices on the Corrugator Seminar will be held April 9-11 in conjunction with SinoCorrugated 2013 in Shanghai, China.
Learn More...
|
NETInc Innovative Nonwovens Conference in April to focus on innovation.
Learn More...
|
TAPPI's Shipping, Receiving and Warehousing Workshop Focuses on Reducing Roll Damage
Learn More...
|
David Schirmer, Vice President and General Manager, Hearst Enterprises, will Keynote SRW Workshop this April.
Learn More...
|
Strengthen your understanding of the corrugating process and linerboard and medium performance properties and manufacture with TAPPI's Linerboard Medium & Corrugated Box Manufacture Course, April 15-16, at the Holiday Inn in Neenah, Wis., USA.
Learn More...
|
April 16-18, 2013 - Join industry veteran Dick Target, founder of On Target Consultants, as he helps attendees identify and address downtime issues and develop a better understanding of machine calibration and how to maintain proper board caliper during the converting process.
Learn More...
|
TAPPI and NCSU are partnered again for the first of three introductory level courses for industry professionals that cover the entire pulping and papermaking process.
Learn More...
|
PaperCon will feature Executive Panel with leaders from International Paper, NewPage, Verso, and Soundview.
Learn More...
|
PaperCon 2013 to feature session focusing on effective labor/management teams that yield positive business results.
Learn More...
|
Expand your knowledge, improve your personal network, and learn ways to generate innovation at PaperCon.
Learn More...
|
Highly regarded industry leaders to speak on April 29 at Papercon '13 in Atlanta, Ga., USA.
Learn More...
|
Introductory course on printing methods and applications is designed for those who need to understand print quality, attend print trials, trouble shoot print problems, or are generally new to printing operations.
Learn More...
|
One of TAPPI's most exciting new products, the laminated and wall-sized 2013 Pulp & Paper "Mills of the World" Map, is now available through TAPPI Press with a twenty dollar discount for members.
Learn More...
|
Register now for the class where you will learn to understand OSHA, avoiding citations that could cost millions of dollars. Teach your company how to lower fatalities and near-misses.
Learn More...
|
Advance your career by presenting! Call for Papers underway for three of TAPPI's most important fall events.
Learn More...
|
This book takes the reader through the process of making paper, pointing out where interruptions can occur and where elements added to the system can cause problems in that part or subsequent parts of the papermaking process.
Learn More...
|
|
Find us on Facebook
Network with us on LinkedIn
Follow us on Twitter
|
Weekly Spotlight
Wausau Paper, Mosinee, Wis., USA, this week announced the closure of its technical specialty paper mill in Brainerd, Minn., to occur early in the second quarter of this year. The closure will affect approximately 130 employees.
Pre-tax closure charges are estimated to be $47 million, with non-cash charges, primarily related to the write-down of long-lived assets, accounting for approximately $44 million of the total. First quarter, pre-tax closure charges of approximately $36 million are expected with the remaining charges occurring over the balance of 2013. After considering income tax liabilities and the anticipated reduction in working capital, the cash impact of the closure is expected to be neutral on a cumulative basis.
Wausau recently announced its intent to strategically reposition the company to focus on its Tissue business, and a range of alternatives for the divestiture of the technical specialty business have been explored. The company noted that "it has become clear that Brainerd will not contribute to those alternatives, and the closure will significantly improve the continuing Paper segment operating results."
Hank Newell, president and CEO, said that "a number of factors, including our accelerated exit from the print business, protracted global economic weakness, and recent competitive paper capacity additions in Asia, have impacted the viability of the Brainerd operations and created operational losses from the mill that were unsustainable. Our employees and the community of Brainerd have done all we have asked in our efforts to create a long-term viable operation and we thank them for their support."
Wausau Paper produces and markets a complete line of away-from-home towel and tissue products and technical specialty papers for industrial, commercial, and consumer end markets.
Back To Top
|
Life-style changes and the need for product differentiation have put pressure on the quality and sales appeal of food packaging. This has increased the amount of packaging material. At the moment, most food packaging material is of non-renewable, oil-based origin. According to EUROSTAT, domestic plastic packaging waste in Europe amounts to more than 15 million metric tpy, of which 40% is disposed of and not recovered or recycled.
To increase the amount of bio-based food packaging materials, the European ADCELLPACK consortium is developing a thermoplastic wood-fiber-based packaging material for trays used primarily in packages of sliced cheese.
The new material will be designed to suit Modified Atmosphere Packaging (MAP). The MAP technique is widely used for the preservation of fresh foods because it offers the product an increased shelf life. In this packaging technique, atmospheric air inside the package is replaced with the desired gas mixture. Common MAP packaging structures are based on non-renewable multilayer materials, which are difficult to recycle.
The use of bio-based materials is a promising alternative in the packaging industry for reducing the environmental impact and the use of non-renewable resources. Materials based on cellulose can be an outstanding alternative to substitute materials currently used in MAP, ADCELLPACK notes, adding that a fully sustainable solution will be developed that will maintain the freshness of the product and assure its food contact safety. The solution will provide actual or improved shelf life through the use of cellulosic materials and biodegradable polymers, with simplified production. There will be broad opportunity for use of the solution in several food products currently packaged using MAP.
ADCELLPACK is a two-year project that started at the beginning of November 2012. Its budget is EUR 1.4 million, and the project is financed by the EU (FP7-SME-2012 Research for the benefit of specific groups).
The consortium is based on a group of four SMEs – Distribuciones Juan Luna, S.L.U. (Spain), Papelera de Brandia, S.A. (Spain), Elastopoli Oy (Finland), and Skymark Packaging International Limited (UK); one large enterprise – Centros Comerciales Carrefour (Spain); and two relevant research centers – VTT Technical Research Centre of Finland and ITENE Packaging, Transport, and Logistics Research Center (Spain), the latter as coordinator of this initiative. All have expertise in paper production, bioplastics processing, conversion of packaging materials, and cheese production. The research has received funding from the European Union's Seventh Framework Programme managed by REA-Research Executive Agency under grant agreement number 315688.
As depicted in the graphic below, ADCELLPACK's new solution will provide a readily thermoformable tray mainly composed of cellulose (up to 90% in weight), with improved properties using modified pulp fine fraction.
More information is available online.
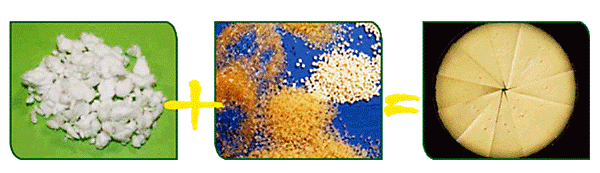
Back To Top
|
The Institute of Paper Science and Technology (IPST) at Georgia Tech, Atlanta, Ga., USA, has awarded three prizes totaling $20,000 to students competing in the 2013 Georgia Tech Research and Innovation Conference (GTRIC). All three winning students are PhD candidates in the Georgia Tech Paper Science and Engineering graduate program.
Qining Sun received the $10,000 Institute of Paper Chemistry Foundation (IPCF) Award as a participant in the Innovation Competition. The IPCF Award is given to the top student in the Innovation Competition whose research project advances horizons of the forest bioeconomy. His project is titled Comparison of Changes in Cellulose Ultrastructure During Different Pretreatments of Poplar. Qining's advisor is Professor Art Ragauskas, Chemistry and Biochemistry. More information about Qining and his research is available on the IPST website.
Two George W. Mead Awards of $5,000 each were presented to Lester Li and Jie Wu for their entries in the GTRIC poster competition, which had more than 300 graduate student competitors this year. Lester and Jie were selected based on work that represents innovations in forest bioproducts research. Lester's project is titled Superoleophobic and Superhydrophobic Surfaces on Paper. His advisor is Associate Professor Victor Breedveld, Chemical and Biomolecular Engineering. Jie's project is titled Chitin-based Bio-Inspired Optical Coating Materials for Sustainable Paper and Paint Industry. His advisor is Associate Professor Carson Meredith, Chemical and Biomolecular Engineering.
IPST's involvement in the competition is designed to stimulate innovations in forest bioproducts, including advances in manufacturing technologies. The topic areas include innovations in biomaterials, biofuels, and chemicals that advance the horizons of the forest bioeconomy.
"Congratulations to all three winners for their fine research toward advancing the forest bioeconomy," said Norman Marsolan, IPST director. "We also thank the IPC Foundation and George Mead for providing funding to stimulate research that serves the goals of our industry and IPST."
Back To Top
|
Earlier this week, the Boston Globe ran a feature article on current operations and outlook for the East Millinocket, Maine, USA, mill that was acquired by New Hampshire-based Cate Street Capital in August 2011, along with its sister mill in nearby Millinocket, Maine. Only two months after acquiring the two shuttered Katahdin paper mills through its resurrected subsidiary Great Northern Paper (GNP), Cate Street Capital restarted East Millinocket (which had been closed since April 2011), putting 225 employees back to work and re-launching the historic Great Northern Paper brand. The printing and writing papers mill launched an aggressive sales and marketing campaign and quickly built a 35-40 day backlog of orders and were sold out entering 2013.
The company has been restructuring the Millinocket site (which shutdown in September 2008) into a torrefied wood production facility that will startup this year as Thermogen Industries LLC. The plant will hire 25 full-time employees and produce 110,000 tons of torrefied wood per year for overseas, coal-fired power plants that will reduce dangerous emissions by adding torrefied wood to their fuel mix.
The East Millinocket mill has now started both paper machines. Some of the product line at East Millinocket includes newsprint, directory paper, and Baxter Brite used for inserts, flyers, books, and financial publications. The mill was recently in the news for producing more than 3,000 tons of paper for the popular Fifty Shades trilogy of books on its Baxter Brite grade. GNP's responsiveness, service, and the paper's consistent performance made Baxter Brite a reliable choice for Fifty Shades paper merchant Midland Paper and the books' publisher, Vintage, an imprint of Random House, Inc.
Today, as the Boston Globe articles describes, the mill is continuing to perform well but there are growing concerns within the East Millinocket community over finding and training younger replacements for many of the retirement-age employees who formerly worked at the mill before it went down under continuing growth of digital communications and a declining demand for P&W papers. There is also concern about the mill's reduced tax structure and the need for more city and county revenues to keep schools, parks, and roads repaired and in decent operating condition.
The full Boston Globe article is available online.
Back To Top
|
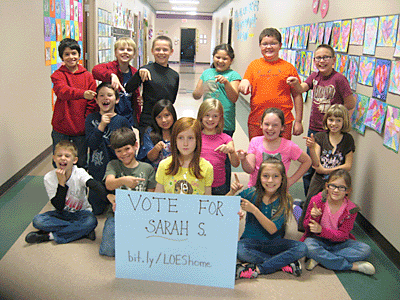 Third-grader Sarah Shreve's teachers had never heard her speak—until recently, when the student at Lone Oak Elementary School in Loan Oak, Texas, USA, wrapped up the voting in a national video contest she had entered with a comment about her effort. Sarah suffers from a severe anxiety disorder called "selective mutism," but when she entered the Scotties Facial National "Trees Rock" Video Contest, things began to change, says her mom, Melissa. The contest is sponsored by Irving Tissue Inc., Burlington, Mass., USA, which manufactures Scotties tissue products in the U.S. under license from Kimberly-Clark.
"This was a contest that Sarah felt passionate about. When we got the call this week about the judging, Sarah marched over to the phone and spoke into it, saying 'We have an update for Team Sarah -- WE WON!'" (One of the tools Sarah uses for therapy is a phone, which she speaks into without anyone on the other end). But this call was different. Scotties was calling to tell her that, after a month of online voting and nearly 100,000 votes from the public, Sarah Shreve had won $10,000 for her school and $5,000 for herself.
Sarah's mom, Melissa credits this breakthrough to the confidence Sarah has gained through the "Trees Rock" video contest, in which 3rd, 4th, and 5th graders were challenged to create a short video about the importance of trees in our lives. During the voting period, it truly was a "Team Sarah" mentality in Lone Oak, 60 miles east of Dallas. As the smallest market out of all the top 12 finalists, Lone Oak came together with a "don't mess with Texas" attitude as Principal Judy Steadham recalls. "There is a real alliance between the school and the community in Lone Oak. We had students who graduated 20 years ago voting for her."
The prize money will be used to upgrade the technology at Lone Oak Elementary. A school with very few resources will now have the ability to provide students with laptops and tablets.
A panel of judges narrowed entries down to the 12 most compelling in the categories of clarity of message, relativity to theme, and creativity. The winner was then decided by a national vote.
Scotties notes that it is committed to being a sustainable company, and in addition to creating this educational program, in cooperation with American Forests, they plant three trees for every one they use – amounting to 877 million in North America over the past 50-plus years.
More information about the Trees Rock video contest is available online, including videos by Sarah and the other contest winners.
Back To Top
|
Domtar Corp., Montreal, Que., Canada, has announced the latest additions to its award-winning site, The Paper Trail. As the fourth update to the site, The Paper Trail will now include:
- Three additional products—EarthChoice®30 Recycled Office Paper, EarthChoice®50 Recycled Office Paper, and EarthChoice® Opaque Offset 30%—all part of the Domtar EarthChoice® family of environmentally and socially responsible papers.
- A site history, picture gallery, and local stories from the company's Kingsport, Tenn., mill.
The Paper Trail, launched in June 2011, was named a Top Innovative Corporate Social Responsibility Initiative of 2012 by Brave One Agency, joining companies such as Unilever and The North Face in raising the environmental transparency bar for business. With this latest update of The Paper Trail, Domtar is again voluntarily releasing product and mill data that helps its customers learn about the environmental and social impacts of their paper purchases.
"Expanding the offerings of The Paper Trail," said Paige Goff, VP of Sustainable Business and Brand Management, "indicates Domtar's willingness to continue to push the transparency envelope, while helping our customers make informed purchasing decisions."
The Paper Trail develops personalized reports that measure Domtar products across five categories: water usage, the distance its fiber travels to a paper mill, greenhouse gas (GHG) emissions, waste sent to landfills, and renewable energy usage. The Paper Trail also illustrates how Domtar compares with the industry in these categories. In cases where the environmental impact can be improved, Domtar voluntarily discloses the information, as well as the efforts underway to make improvements.
Domtar produces a variety of fiber-based products including communication papers, specialty and packaging papers, and adult incontinence products. It also produces paper grade, fluff, and specialty pulps. The majority of its pulp production is consumed internally to produce paper and consumer products. Domtar is the largest integrated producer of uncoated freesheet paper in North America.
Back To Top
|
The OpEx Maintenance and Reliability Workshop at TAPPI PaperCon 2013 in Atlanta, Ga., USA, on April 30, will include a special joint session with the Recycled Paper Trade Association (RPTA) that explores Operator Driven Reliability (ODR) from an up-close, mill case-study perspective. During this session, Christer Idhammar with IDCON examines what has been tried with ODR, who's succeeded, what's failed, and why—all based on mill case study results.
Also during the joint session, Tony Kenneson-Adams of RockTenn will look in-depth at how his Solvay recycled containerboard mill in Syracuse, N.Y., set up its ODR program and the pitfalls they experienced along the way. Rounding out the joint OpEx/RPTA session, Jim Davis of Performance Consultants Associates illustrates how to effectively support ODR programs by building "The Perfect Maintenance Storeroom."
More information about PaperCon 2013 and the OpEx Maintenance and Reliability Workshop, including registration procedures, is available online. Also available online is the 2013 OpEx Workshop program.
Back To Top
|
An Institute of Paper Science and Technology (IPST), Atlanta, Ga., USA, February workshop developed potential forest bioproducts industry scenarios for 2035 that consider constrained resources, changed production processes, new mill concepts, and a greatly expanded world population with different markets and market expectations. The scenarios will influence the upcoming research program at IPST, and serve as the starting point for the Institute's April Executive Conference. About 25 company, government, and affiliate representatives met to consider possible economic, cultural, and social drivers that could significantly impact industry opportunities 20 years into the future.
Scenarios developed at the workshop, titled A 20-Year Outlook for the Forest Bioproducts Industry: Implications, Challenges, Opportunities, were imagined for the purpose of identifying key cross-cutting areas of research that could prepare the industry for a changing world. The annual IPST conference April 18-19 will consider the implications for the industry and the resulting priorities for further exploration and research.
Sten Nilsson, CEO of Forest Sector Insights, from Sweden, delved into the need for forest industry transformation, the obstacles impeding it, and the opportunities in accomplishing it. Agenda 2020 Technology Alliance President Ron Brown presented a review of dozens of existing forest products industry and business forecasts published by governments, business organizations, and NGOs. Ted Wegner, assistant director of the USDA Forest Service, Forest Products Lab, also presented an assessment of the future of forests and rangelands prepared under the 2010 Resource Planning Act.
A Georgia Tech faculty panel introduced participants to technology-enabled opportunities ahead in several key fields. "Possible multiple product streams from mill sites, different concepts about mills in the future, and the future of raw materials were among the important factors discussed," said one participant. "The industry must prepare for a future with very different assumptions about the cultural environment."
Back To Top
|
TAPPI's 2013 Tissue Properties and Manufacturing Course, to be held in conjunction with PaperCon 2013, covers the fundamentals of manufacturing and provides an excellent overview of this dynamic market segment. The two-day course will be held on April 27-28, 2013 in Atlanta, Ga., USA, and precedes PaperCon and the Tissue360° Forum.
"Tissue manufacturing is technically innovative and rapidly growing and the Tissue Course provides an excellent overview of manufacturing operations, equipment, and tissue sheet properties," notes Larry N. Montague, TAPPI president and CEO. "Course participants will be able to also take advantage of the Tissue360° Forum and all of the networking opportunities available during PaperCon."
This course is designed for those who desire an introductory-to-intermediate level, comprehensive, and structured course on tissue properties, and the effect of manufacturing processes on them. It provides an excellent educational compliment to the Tissue360° Forum sessions. Attendees will learn about a wide range of key topics including: tissue properties and tests; stock prep and refining; chemicals (wet end and yankee); wet end operations; TAD and yankee drying; creping; calendaring; and converting. A no-charge webinar featuring some of the course content will be held on March 6, "Tissue Manufacturing for Softness." More information about this course is available online.
The Tissue360° Forum and PaperCon 2013 feature the industry's largest technical program in addition to a number of special events, seminars, and tracks on a wide range of topics and industry segments, numerous networking opportunities, keynote presentations, and a trade show exhibit.
Back To Top
|
Below is the latest listing of job openings in the TAPPI Career Center. The current listing includes job openings for a variety of positions including sales and service engineers, maintenance managers, chief engineer, sales and service engineers, sales manager, production manager, mill manager, executive director of a pulp and paper foundation, engineering intern, and R&D manager. Current, specific job openings at companies and locations in the TAPPI Career Center include:
Employer |
Title |
Location |
Albany International |
Application Eng. Forming Americas |
Wisconsin |
Albany International |
Sales & Service Eng. /Mid-Atlantic |
Florida |
Albany International |
Sales & Service Eng. /W. Coast |
NW Ore./SW Wash. |
Albany International |
Sales & Service Eng./Canada W. Coast |
B.C., Canada |
BASF |
Process Eng.-Kaolin-Mid Georgia |
Mcintyre, N.J. |
Boise Inc. |
Process Improvement Manager |
Georgia |
Boise Inc. |
R & D Technical Leader |
Idaho |
Boise Inc. |
Sales Manager |
Atlanta, Ga. |
Boise Inc. |
Maintenance Manager |
Salt Lake City, Utah |
Burrows Paper Corp. |
VP of Human Resources |
Little Falls, N.Y. |
Confidential |
R&D Manager |
Albany, N.Y. |
Fajar Paper |
Mill Manager |
Cikarang, Indonesia |
Fajar Paper |
Production Manager |
Cikarang, Indonesia |
Fajar Paper |
Chief Engineer |
Cikarang, Indonesia |
Longview Fibre |
Project Engineering Mgr. |
Longview, Wash. |
MeadWestvaco |
Human Resources Mgr.-Mill Ops. |
Cottonton, Ala. |
Michelman |
Global Tech. Mgr.-Paper Ctgs. |
Cincinnati, Ohio |
Michelman |
Regional Sales Mgr.-Paper Ctgs. |
Cincinnati, Ohio |
Nalco |
Technical Sales Rep. |
Owensboro, Ky. |
NCR Corp. |
Chemical Eng./P&P-Paper/Ctgs. |
Georgia |
Norpac-Weyerhaeuser |
Engineering Internship |
Longview, Wash. |
Total Lubri. Mgt./Colfax Fluid Hand. |
Territory Sales Manager |
USA |
Washington P&P Found. |
Executive Director |
Seattle, Wash. |
Wisconsin Inst. for Sust. Tech. |
Lab Director |
Stevens Point, Wis. |
Wisconsin Inst. for Sust. Tech. |
PM and Allied Lab Specialist |
Stevens Point, Wis. |
More information about these jobs is available online.
Back To Top
|
Market Roundup
U.S. Containerboard production in January rose 1.7% over December 2012 and 3.5% over the same month last year, according to the AF&PA (Washington, D.C., USA) January 2013 U.S. Containerboard Statistics Report released this week. The month-over-month average daily production increased 1.7%.
The containerboard operating rate for January gained 1.3 points over December 2012, from 95.8% to 97.1%.
Back To Top
|
CEPI (Confederation of European Paper Industries), Brussels, Belgium, reports that paper and board production by CEPI member countries fell by in the region of 1.7% in 2012. CEPI estimates that its member countries produced around 92 million metric tons of paper and board in 2012, resulting from some adjustments in production capacities with closures amounting to 2 million metric tpy and new capacities or upgrading of existing ones accounting for close to 1 million metric tpy.
CEPI estimates that the production of pulp (integrated + market) has decreased by up to 1% when compared with the previous year, with total output of approximately 38 million metric tons. It further estimates that output of market pulp increased by between 4% and 4.5%, while integrated pulp output decreased by 3% in 2012 when compared with 2011.
Consumption of paper for recycling by CEPI members fell by between 1% and 1.5%, CEPI estimates. Based on cumulative data up to the end of the third quarter of 2012, it is expected that total paper and board deliveries for the year will have fallen by more than 2% when compared with 2011.
It appears, CEPI says, that the overall consumption of paper and board in CEPI countries in 2012 decreased by between 4% and 5% when compared with 2011.
Back To Top
|
Total U.S. boxboard production increased by 0.9% in January compared with January 2012 and increased 1.7% from last month, according to the January 2013 U.S. Paperboard Report published this week by AF&PA, Washington, D.C., USA. Unbleached kraft boxboard production increased over the same month last year and increased compared with last month.
Total solid bleached boxboard and liner production decreased compared with January 2012 and decreased compared with last month. The production of recycled boxboard increased compared with January 2012 and increased when compared with last month.
Back To Top
|
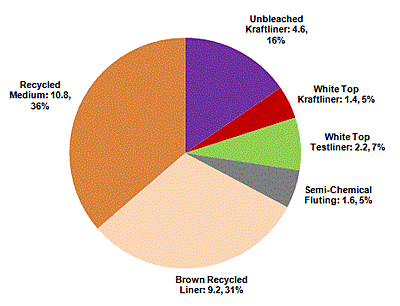 Demand growth for white top liners has increased significantly higher than the overall growth in corrugated packaging during the past year, according to a new report released this week by RISI, Boston, Mass., USA. According to the study, white top liner segments will likely post better profit margins over their brown counterparts as demand for white top liner in Europe continues to grow.
2012 Outlook for European White Top Containerboard Markets with 2013 Update examines and forecasts market developments, providing historical analysis of the white top containerboard market from 2002 – 2012 and covering supply and demand trends by country, trade, production costs, pricing, and profitability until 2016.
During the past decade, the European containerboard market has already grown by close to 5 million metric tons, and white top containerboard accounts for 20% of this growth. Although white top liners (both white top testliner and white top kraftliner) only make up a 12% share (3.6 million metric tons) of total European containerboard demand, demand for white top liners is being driven upward by printing quality requirements on the part of end-users and brand owners for retail-ready packaging, according to Orifjon Abidov, senior economist for European Paper Packaging at RISI.
Back To Top
|
Total U.S. kraft paper shipments in January were 140,500 tons, an increase of 19% compared with the prior month, AF&PA, Washington, D.C., USA, reports in its January 2013 Kraft Paper Report issued this week. Bleached kraft paper shipments increased year-over-year 17%, and unbleached kraft paper shipments increased 7% year-over-year.
As a result, total kraft paper shipments begin the year 9% higher than 2012. Total month-end inventory decreased 14% to 73,500 tons this month compared with December 2012 month-end inventories.
Back To Top
|
Pulp & Paper
Catalyst Paper, Richmond, B.C., Canada, is taking a major step forward in its Latin American market development strategy with the launch of Marathon Lite, a high-performing newsprint grade with a basis weight of only 40 gsm. Growing Catalyst's long-standing presence in Latin America is a focus of its emerging markets strategy and leverages freight-logical proximity to serve this market from its Pacific coast manufacturing facilities.
"Latin America is a market of 500 million people, which makes it very attractive. We have long-standing relationships with major publishers in the region and the demand for reliable supply of high quality papers is trending up," said Catalyst president and CEO Kevin J. Clarke who will be meeting with several key customers in the region in April, including publishers in Peru and Colombia.
With a growing middle class and less high-speed Internet penetration than Canada and the U.S., Central and South American newspapers are still the most popular vehicle for information. Growth in middle-class disposable income also means advertisers want space in those popular papers.
"This reinforces our focus on innovation in every part of our business including in newsprint, a product that we've been manufacturing for 100 years," said Clarke, "while we continue to march up the value curve offering the broadest range of specialty paper products available from a single supplier in Western North America ."
In launching Marathon Lite, Catalyst will benefit from established market acceptance of its products in the region. Besides Peru, readers in El Salvador, Panamá, Colombia, Guatemala, Nicaragua, and Venezuela already use British Columbia-made paper on a daily basis.
Hugo Holmann, owner of the Nicaraguan publisher La Prensa, said that "we are pleased that our readers and advertisers have noticed a tremendous improvement in the printing quality of our newspaper since we changed to Catalyst. We also see a great opportunity of improvement with the 40-gsm sheet. This brings more efficiency to our distribution chain all the way to the very end, allowing our street vendors to carry less weight, without affecting our production efficiency."
Lighter basis weight papers use less fiber to make the same printable area. Not only is Marathon Lite more thrifty in its fiber use, it's made with more than 85% renewable energy and certified to Programme for the Endorsement of Forest Certification (PEFC) standards.
Catalyst Paper produces diverse specialty mechanical printing papers, newsprint, and pulp. With three mills in British Columbia, Catalyst has a combined annual production capacity of 1.5 million metric tons.
Back To Top
|
Clearwater Paper, Spokane, Wash., USA, successfully started up its new Metso (Finland)-supplied Advantage THRU-AIR (TAD) tissue machine at Shelby, N.C., in mid-December, and the startup curve has proceeded as scheduled. The completion of the flagship facility in Shelby fulfills one of Clearwater Paper's primary business strategies—to focus on growing the consumer segment of the company.
"Metso TAD technology coupled with its strong project team and process integration capabilities were integral to the success of this project," said Brian Hoaglund, Clearwater Paper's expansion project leader. "Metso was a solid partner in delivering equipment that met our performance requirements and will allow Clearwater Paper to deliver ultra quality tissue products to our customers."
Soren Eriksson, account sales manager, Metso, said that "we are very impressed by Clearwater Paper's determination and dedication of building a first class tissue manufacturing facility in Shelby. It has been a pleasure for the Metso team to work with them during the definition and execution phase in a well integrated delivery team. The result paid off with an excellent startup."
Metso's delivery included a complete production line with stock preparation equipment and an Advantage THRU-AIR 200 TAD machine with a Metso Yankee cylinder, THRU-AIR dryers, and an Advantage WetDust dust management system. The delivery also included an extensive automation package with Metso DNA machine and process controls and a Metso IQ quality control system with Metso IQ Scanners and Metso IQ Profilers.
The new production line will produce 70,000 tons a year of Ultra Premium high-quality tissue grades. The raw material for the new line will be virgin pulp.
Clearwater Paper produces quality consumer tissue, away-from-home tissue, parent roll tissue, machine glazed tissue, bleached paperboard, and pulp at 15 manufacturing locations in the U.S. and Canada. The company is a supplier of private label tissue to major retailers and wholesale distributors. This includes grocery, drug, mass merchants, and discount stores. The company also produces bleached paperboard.
Back To Top
|
Domtar Corp., Montreal, Que., Canada, reports that it was a premier sponsor of the GreenBiz Forum 2013 in New York City, February 19-21. GreenBiz gatherings take place twice annually in cities around the U.S. The events bring together thought leaders from across sectors and industries to share best practices and engage in cutting-edge discussions about the key sustainability challenges and opportunities facing business today.
As part of the GreenBiz program, Domtar's VP of Sustainability, David Struhs, took part in a keynote live interview with Senior GreenBiz writer Marc Gunther.
"I'm a big fan of getting behind the press release aspect of sustainable business performance and looking at the underlying trade-offs around economics, the environment and society," noted Struhs. "The connective tissue of these decision points is not something that gets a lot of airtime, generally, so it's an area I'm pleased that Marc and I had a chance to explore in this unique conference setting."
Back To Top
|
Grigiškes AB, Lithuania, plans to increase its tissue production capacity, reporting that it has secured a EUR 10 million loan from Skandinaviska Enskilda Bankens (SEB) and will invest the money in a new tissue machine. As reported by EUWID Pulp and Paper, Germany, the company is currently negotiating with major European machine suppliers on the delivery of the new 25,000 metric tpy machine, but has not made a final choice yet.
Grigiškes employs 270 people and runs three machines with a maximum installed capacity of approximately 25,000 metric tpy of tissue. The new tissue machine is expected to come online by the end of next year and will reportedly replace the two smaller machines TM 2 and TM 3 with a total maximum capacity of 9,000 metric tpy.
Investing in additional tissue capacities should allow Grigiškes to keep pace with the growth in tissue and hygiene products demand in the region, the EUWID report noted. Growth potential in the Baltic countries and in adjacent regions is big given that the annual per capita consumption is up to five times lower than in mature European markets, Grigiškes said. Apart from Lithuania, the main sales markets for Grigiškes's tissue products are Latvia, Estonia, and Denmark.
Back To Top
|
KP Tissue Inc. (KPT), Montreal, Que., Canada, which owns approximately 16.9% in Kruger Products L.P. (KPLP), announced that KPLP has successfully finished the construction phase of its TAD (Through-Air-Dried) tissue project at its Memphis, Tenn., mill. KPLP began construction of the new TAD machine and related infrastructure in the fall of 2011 at an estimated cost of $322 million. When fully optimized, the new TAD tissue machine is expected to increase the company's production capacity by approximately 20%, or 60,000 metric tpy.
"We are especially pleased to have completed this phase of the project on time and on budget. The startup phase has commenced and we are already shipping products to our customers. The TAD project is a key component of KPLP's North American growth strategy," said Mario Gosselin, CEO of KPLP and KPT.
KP Tissue Inc. was created to acquire, and its business is limited to holding, a limited partnership interest in KPLP. It currently holds a 16.9% interest in KPLP.
Back To Top
|
ST Tissue LLC, Oconto Falls, Wis., USA, has started up its new PMT Italia (Italy) yankee dryer on the converted PM 6 at Franklin, Va., USA (photo). The yankee dryer is the world's widest with more than 8.3 meters (327 in.) of shell face. It was installed as part of the conversion of PM 6 to a 70,000 tpy recycled tissue machine at the former International Paper (Memphis, Tenn.) uncoated freesheet paper mill in Franklin.
The scope of the PMT rebuild included the new cast iron yankee dryer, complete with head insulation, mechanical drives, and dryer doctors. PMT also supplied erection supervision and startup services.
PM 6 at Franklin machine will produce parent reels for a variety of semi-crepe tissue grades from napkin to towels, and bleached to kraft products. The mill has some 80 employees.
ST Tissue, owned and operated by Tak Investments, Gaithersburg, Md., is said to have North America's largest tissue machine at Franklin, with a usable web width of 310 in. The width of the machine will allow the company to offer a variety of trim sizes and its onsite recycled fiber plant will allow it the flexibility to transform waste paper into different grades of recycled pulp.
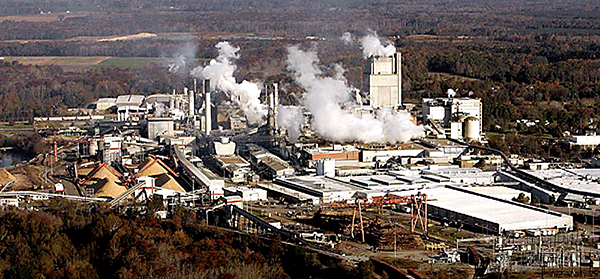
Back To Top
|
Containerboard/Packaging
Amcor, Australia, will acquire select printing assets of AGI-Shorewood's Tobacco Packaging and Specialty Folding Carton Operations for $114.8 million. The acquired business has plants or assets in South Korea, USA, Mexico, and China. The acquisition excludes the AGI-Shorewood plant in Smiths Falls, Canada. The acquisition expands Amcor's business in the higher growth regions of Asia and Latin America and includes specialty folding carton production assets in the U.S. The assets had 2012 sales of $126 million and EBITDA of $22 million. The EBITDA purchase multiple is 5.2 times based on the last 12 months of earnings.
Net synergy benefits are anticipated to be approximately $13 million and the net cash cost to achieve these synergies is expected to be approximately $20 million. The acquisition is expected to deliver a return on investment of more than 20% by the end of year three.
In South Korea, the business has approximately 30% share of this high value add market and supplies major international customers. The plant, built in 2004, is well capitalized and has a strong technology and product innovation focus.
Amcor's Managing Director and CEO Ken MacKenzie, said that "this acquisition is aligned with our strategic objective of expanding our position in emerging markets. The attractive purchase multiple and substantial operational cost synergies ensure the acquisition will generate very attractive returns for shareholders."
Amcor also announced during its six month report for business ended December 31 that the company will close its cartonboard mill in Petrie, Queensland, Australia, impacting some 300 jobs. Petrie, the only recycled cartonboard mill in Australia, produces 140,000 metric tpy of grayback and whiteback duplex board, supplying folding carton manufacturers across Australia and New Zealand. Amcor attributes the closure to "several structural changes in the competitive environment" and the fact that "the mill is no longer covering its cash costs." The mill is expected to close by the end of this year.
Back To Top
|
The Europac Group, Madrid, Spain, has acquired a corrugated board factory in Caradec, France, for EUR 21.7 million, expected to become effective March 1. The facility produces 100 million cubic meters of recycled corrugated board per year and consumes 60,000 metric tpy of paper. The deal will enable the Europac group to step up board production in France by 28% and to increase its vertical integration. With this acquisition, the degree of integration between paper and board in the French market will rise from 67% to 88%.
José Miguel Isidro, chairman of the Europac Group, said that "this acquisition falls under the umbrella of the Group's strategic targets for the French market, where we command a share of the packaging segment of 7.4%".
The factory is located in Brittany and its integration into the Europac Group's organizational structure will consolidate the company's position in Western France, which represents one-third of the French packaging market.
This transaction follows the acquisition of SCA Packaging by DS Smith, which the European anti-trust authorities had made conditional upon the sale of the Caradec corrugated board factory in Western France, among others.
The integration of this facility into the Europac Group will enable the company to consolidate its position as a benchmark supplier to the France market, Europe's third-largest market by sales volumes and Europac's largest. The deal will extend the company's sales reach in Brittany and boost cooperation with French and international customers.
The Europac Group entered the French market in 2008. It currently produces 280,000 metric tons of recycled paper and 360 million cubic meters of corrugated board annually. Accordingly, the addition of this new facility will boost board production to 460 million cubic meters per year, making Europac the fourth-largest packaging producer in France.
Back To Top
|
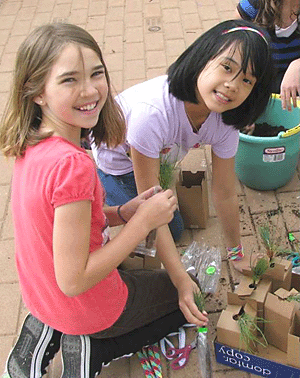 Through collaboration with the Paperboard Packing Council (PPC), Springfield, Mass., USA, the Arbor Day Foundation will once again provide discounted tree saplings to companies throughout the U.S. and Canada, as a way to honor Earth Day on April 22, and National Paperboard Packaging Week, April 22-26. Companies are encouraged to distribute the saplings free of charge to students, teachers, or even the local community, through the annual TICCIT program, an outreach and educational initiative geared towards elementary school children that highlights the renewability and sustainability of paperboard packaging and the enormous value of trees to the environment.
As part of TICCIT ("Trees into Cartons, Cartons into Trees"), students are taught how to plant saplings in paperboard cartons. The children are then instructed on how to plant the saplings—and the biodegradable cartons—in local neighborhoods or in their backyards. Once grown, the trees help restore flora that has been damaged by fire or disease, provide a natural way to cool homes, schools, or workplaces in the summer, and keep icy winds at bay in the winter.
"Because of PPC's relationship with the Arbor Day Foundation, we're able to provide schoolchildren with valuable recycling education and saplings to plant," said Ben Markens, president of PPC. "Year after year, this remains our favorite event, as it gives us the opportunity to contribute to sustainable forestry and teach our communities about recyclability of paper."
The Arbor Day Foundation is providing a variety of saplings suitable for different regions of the country for the discounted price of $1 each (50-tree minimum order). Any company interested in participating should place orders online no later than April 1.
For ideas on how to implement this unique educational program, anyone is welcome to download a free program guide that includes lesson plans, classroom questions, planting tips, fun facts, and sample forms.
In the photo, students plant saplings in pre-constructed paperboard boxes at the 2012 TICCIT program, under the supervision of the staff of PPC member Frankston Packaging of Southlake, Texas.
Back To Top
|
Rigid Containers Ltd., U.K., part of the VPK Group, this past week reported that it will open a new corrugated packaging facility in England, its third one in that country. The 200,000 sq ft site in Wellington, Somerset, will allow the company to serve its customer base in the southwest of England.
"We will open the site as a distribution hub in early April," said Richard Coward, managing director. "Packaging manufacture will be handled at our Desborough and Selby factories and then transported to Wellington in bulk loads. Customers can then call off by batch, meaning we can offer a true just-in-time service for the southwest."
Coward added that "it is our intention to install a range of converting machines during 2013. During the year, a balanced line-up of converting machines will be installed that will enable Rigid to provide a full product range including cases, die cut containers, and multi point glued products. This will involve both equipment bought specifically for the new site and machine transfers from our Selby and Desborough operation as we replace them with new models as part of our investment plans here in the U.K."
The new site will be a multi-million pound investment entirely funded by the Group. The distribution hub will create between 30 and 40 new jobs for the area immediately and is seen as a positive move by the local council. As the hub then transforms into a manufacturing plant by the middle of the summer, it is expected that dozens of new jobs will also be created.
Coward noted that the range of machines Rigid plans to install at Wellington means it can offer a broad range of packaging styles, printed in up to four colors. "We anticipate that our new four color flexo folder gluer will be fitted with dryers, meaning we can print on the highest quality papers in the industry, which is particularly relevant for shelf ready packaging applications."
Back To Top
|
New Products
Fruitapeel, a U.K.-based manufacturer of own-label and branded juices and smoothies, has partnered with Elopak to launch the U.K.'s first gable top carton aseptic filling line for Juice. "UK producers have traditionally had to go abroad to fill aseptic juices in gable top cartons. This increases costs, logistics, and carbon footprints," says Fruitapeel Managing Director Terry Haigh. "The Elopak technology enables British-based production for the first time."
An Elopak S-PS80 High Aseptic filling machine will be installed at Fruitapeel's manufacturing site in Llantrisant, Wales, next month. The machine will fill aseptic juices and smoothies in 1 liter, 750 ml, and 500 ml Pure-Pak® cartons.
"This machine enables the production of longer-life chilled juices, creating the opportunity for smaller retailers to produce own-label," explains Haigh. "Current systems only allow for large volumes with short shelf-life, leading to high wastage and logistical nightmares. Elopak's S-PS80 machine has increased speeds of 40% compared with existing chilled lines. In addition, the post filling cap application for the Pure-Twist® cap offers added quality and integrity benefits—increasing shelf life. This machine will open up new markets for U.K. retail."
By the end of March, production will begin with the co-packing of Cracker Drinks juices and smoothies—all previously produced in Germany. "Logistical, cost and environmental benefits are now uniquely available for those U.K. brands and retailers choosing gable top cartons for chilled, ESL, and aseptic juices," Haigh concludes.
Back To Top
|
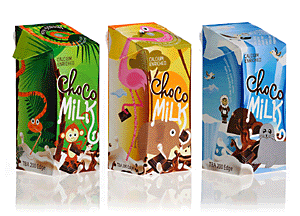 Tetra Pak, Lausanne, Switzerland, this week announced new developments to its packaging solutions portfolio. The developments are aimed at delivering faster response times for customers in meeting changing consumer needs, while minimizing packaging equipment investment.
The company is launching One-Step Opening (OSO) for the Tetra Evero Aseptic, the world's first aseptic carton bottle for ambient white milk. OSO offers double safety features due to the tamper evidence ring and a neck membrane that is removed by twisting the cap. In addition to these safety features, the Tetra Evero Aseptic with OSO enables customers to offer an easy to open, handle, and pour-from-carton bottle.
Tetra Pak's new TBA/19 Retrofitability Kit allows customers to transform the package shape and base area on the same machine platform, a world first in the aseptic carton packaging industry. Customers with the TBA/19 filling machine for 200 Slim, 250 Base, and 125 Slim will soon be able to retrofit their existing filling lines, enabling them to produce the new Tetra Brik Aseptic 200 and 250 Edge (see photo). For those with this machine who are not yet ready to invest in the Tetra Pak® A3/Compact Flex filling machine, this solution provides the option of producing these packages for a fraction of the cost. In addition, the retrofitability kit takes less time to install than a new machine, which means products get to market faster, the company notes.
The new Tetra Pak A3/Speed filling machine is now available for Tetra Prisma Aseptic 200 and 250 portion packs. The Tetra Pak A3/Speed iLine is the fastest line available from Tetra Pak, with a maximum production capacity of 24,000 portion packs per hour.
Back To Top
|
Published Pricing
Metsä Fibre, Finland, has announced a new price for its Botnia Nordic Pine (Northern Bleached Softwood Kraft) in Europe, effective March 1, until further notice. The new price is $860 per metric ton, CIF Metsä Fibre's usual European ports. Other terms remain as agreed.
Metsä Group manufactures market pulp at six mills in Finland and Sweden. The combined annual capacity of production units in Husum, Joutseno, Kaskinen, Kemi, Rauma, and Äänekoski is 3.4 million metric tons. The company's product family includes four types of pulp—Botnia Nordic Pine (a long-fiber softwood pulp), Botnia Nordic Birch (a short-fiber hardwood pulp), Botnia Nordic Strong (a reinforcement pulp), and Botnia High Yield (a BCTMP pulp). This year it will introduce two new pulp grades based on a polysulfide manufacturing method—Botnia Nordic Pine+ and Botnia Nordic Strong+.
Back To Top
|
PaperWorks Industries Inc. (PWI), Philadelphia, Pa., USA, this week announced price increase of $40 per ton for all MasterWorks grades of coated recycled boxboard, and $25 per ton for MasterWorks URB+ uncoated recycled boxboard. The increases become effective with shipments beginning March 25. The company notes that the increase is necessary to recover escalating costs including raw materials, energy, chemicals, transportation, benefits, and other expenses.
Founded in 2008, PWI is an integrated, full-service packaging provider. It produces specialized folding cartons, serving clients across North America from 10 facilities. Its Paperboard Group produces approximately 300,000 tons of 100% recycled paperboard annually for a variety of end uses and further specializes in the cutting and distribution of all paper types according to specific customer needs. The company has more than 1,600 employees in 17 North American locations, with annual sales exceeding $600 million.
Back To Top
|
Sappi Fine Paper Europe, Brussels, Belgium, will increase its prices for all coated fine paper sheets and reels by 5% - 7%, effective April 1. The company notes that after correcting its prices for coated fine paper to some extent during the first quarter of this year, following the significant fall in prices during the last months of 2012, the continuing rise in input costs means that current profitability "has by no means reached acceptable levels.
"While we expect industry demand to improve from the low levels in the beginning of the year, the unprecedented rise in input costs (pulp, chemicals, and transport costs) entirely outstrips the benefits from our price improvements and cost reduction programs so far. As a result Sappi is obliged to raise its prices for coated fine papers for the second time this year, since current price levels are unsustainably low," the company explains.
The company adds that if market conditions indicate that production downtime needs to be taken at its coated mills during this time, it "will not hesitate to do so, since the overwhelming priority is to get the business back to a sustainable profitability level."
Back To Top
|
People
Western Forest Products Inc., Vancouver, B.C., Canada, has appointed Don Demens president and CEO, effective immediately. Dominic Gammiero will continue his role as chairman of the board.
Demens was appointed president of the company in July 2012 and has held numerous strategic roles at Western including, COO and SVP, Sales and Manufacturing. He has more than 25 years of coastal forest industry experience.
"I am very pleased that Don has accepted these additional responsibilities," said Gammiero. "He was instrumental in helping us turn around the business and his knowledge of our industry has been critical in defining our long-term strategy at Western. The board is confident his leadership will continue to strengthen Western''s position as a globally competitive forest products business."
Back To Top
|
Travels with Larry
Okay here we go again.
Two questions:
- What is the name of the highest spot in Delaware?
- What is the elevation of this aforementioned spot? Put you're reading glasses on and see for yourself as VP-Operations for TAPPI, Eric Fletty, highlights these for us (photo).
Our trek to Wilmington, Del., although extremely interesting was not to find the answer to this burning question. Our visit was in response to an invitation by a 30-year TAPPI member who has served on at least seven committees, and is also the recipient of at least five TAPPI awards—Senior Group Leader for Ashland Water Technologies, Frank Sutman.
Wilmington is the home to Hercules legacy business. In 2006 the lab in Jacksonville, Fla., was relocated to Wilmington. Just three years later, the group from Boonton, N.J., was also relocated to Wilmington.
Today this campus is home to about 500 Ashland employees whom I bet know Frank by name. After spending all day touring their facilities, I asked Frank if he was running for Mayor of Ashland. Everyone seem to know his name and he theirs. This reminded me of the old sitcom Cheers. Remember Norm? Everyone seemed to know his name.
This global division of Ashland is known as Ashland Water Technologies (AWT). Folks, I don't have to tell you how important water is to our industry and our lives in general. We must continue to utilize this God given resource as the precious gift that it is. There is a French proverb that says: Fish discover water last. The very thing that sustains them, they do not even have a concept of it until it is gone.
This is, has been, and continues to be a very important topic.
Ashland has implemented a theme and lifestyle known as Responsible Care™, which includes:
- A global management system to deliver excellence in environmental health, safety, and performance
- Employee involvement at every level of the organization
- Continual improvement toward Ashland's Responsible Care goals.
Responsible Care goals:
- Operate with zero incidents
- Achieve 100% compliance
- Reduce environmental, health and safety impact.
Ashland has approximately 15,000 employees worldwide (50% are outside of North America). The company's $8.2 billion of annual sales (47% outside of North America in more than 100 countries) is broken down into four commercial units:
- Ashland Specialty Ingredients - 35%
- Ashland Water Technologies - 21% and $1.7 billion in sales (Paper Process Additives, Paper Functional Additives, and Utility Water Treatment Chemicals)
- Ashland Consumer Markets - 25%
- Ashland Performance Materials -19%.
Worldwide, Ashland has 100 manufacturing sites, 17 R&D centers, and ranks either No. 1 or No. 2 in the four primary categories that they serve.
AWT's sales by product category are: Paper Process-27%, Utility Water-34%, and Paper Functional 44%. Its percentage of sales by geography is not what I expected, with 45% coming from North America. The balance is broken down as follows: Asia Pacific-12%, Latin America/Other-9%, Europe-34%.
AWT's Technology Deployment takes two routes, short- and long-term projects. The customer application laboratories focus on short term solutions for customer problems while 66% of their research effort focuses on basic R&D for more long term, strategic product development. In addition, the company has Fast Track laboratories that are more short-term opportunist such as product reformulations with new raw materials.
Two thirds of AWT's R&D supports the pulp and paper industry. The R&D task is to develop Game Changers with specific market focus in pulp, tissue and towel, printing and writing paper, and packaging.
In addition to a facility tour, Frank set up two group meetings for us with employees who were both current TAPPI members and those who should be. The first meeting had approximately 50 people in attendance and four or five on the phone. This meeting was for the specific purpose of letting people know exactly what TAPPI is all about and how they can better utilize TAPPI to advance their careers. Meeting number two was set up for a smaller focus group of 10-15 people to drill down on how TAPPI is doing and how TAPPI can improve our products and services.
I have to tell you that I was thrilled with not only the attendance of both meetings but the input that we received concerning multiple topics. We left these meetings with a list of take-a-ways as well as some new volunteers who want to help us kick off our new Tissue Division.
Our photographer had a little trouble getting everyone in, so shown above are just a few of the great Ashland people we met during our visit.
We were very happy that we had the opportunity to visit Ashland, which has been a sustaining member for 21 years.
There are two types of people in our industry—TAPPI Members and those who should be.
More information about Ashland is available online.
More information about TAPPI is also available online.
Until next time..................
Larry
Back To Top
|
TAPPI News
Congratulations to TAPPI's new Board of Directors: Robert A. Feeser (MeadWestvaco), Kirt Cuevas (International Paper), and Daniel D. Cappel (Asten Johnson). Elected to begin a three-year term in March 2013, they will join Thomas J. Garland and Chris Luettgen, who will serve as TAPPI chair and TAPPI vice chair, respectively.
Fesser (right) is SVP of MeadWestvaco (MWV) and is responsible for the company's global food packaging business, and all of MWV's business operations in Asia Pacific. He has a long and distinguished career, including responsibility for mill-based manufacturing businesses in the U.S. and in Brazil, and a number of sales, marketing, and management roles during his 25 years with MWV.
Cappell (left) is president and CEO of Asten Johnson. He started at Asten in 1984 as a technical service engineer before moving into senior management at Asten, which later became Asten Johnson.
Cuevas (right) is VP of manufacturing for International Paper's Printing and Communications Papers and is responsible for all manufacturing operations. He has held leadership positions in the company's Technology organization as well as the Industrial Packaging, Consumer Packaging, and Papers divisions. He joined the company in 1983 and has more than 29 years of manufacturing experience.
Fesser, Cappell, and Cuevas will join the following directors who will continue to serve on the TAPPI Board of Directors: Michael Exner, Markku A. Karlsson (VTT Technical Research Centre of Finland), Sandra L. LeBarron (Finch Paper LLC), Steven Shifman (Michelman Inc.), Robert A. Snyder (Orchids Paper Products Co.) and Clayton Teague.
Back To Top
|
TAPPI Annual Business Meeting /Teleconference
TAPPI Headquarters
15 Technology Parkway S., Suite 115
Peachtree Corners, Ga., 30092 USA
March 12, 2013
1:00 pm - 1:30 pm EST
As a corporation, TAPPI must hold an annual Business Meeting. That meeting will be held March 12, 2013, via teleconference. Any interested TAPPI member may join us for a brief report on association business -- Larry N. Montague, TAPPI president and CEO
1. Opening Remarks/Antitrust Reminder - Norman Marsolan, TAPPI Board chair
This call will be held in accordance with TAPPI's Antitrust Policy and Procedures.
TAPPI's aim is to promote research and education, and to arrange for the collection, dissemination, and interchange of technical concepts and information in fields of interest to its members. TAPPI is not intended to, and may not, play any role in the competitive decisions of its members or their employees, or in any way restrict competition among companies.
2. Financial Report - Larry Montague, TAPPI president and CEO
3. Board Transition - Norman Marsolan, TAPPI Board chair, Tom Garland, TAPPI Board vice chair
4. Adjourn - Norman Marsolan, TAPPI Board chair
Please contact Mary Beth Cornell, +1 770-209-7210, for more information, including the teleconference number and password.
Back To Top
|
Special TAPPI webinar on March 13 provides inside preview of PaperCon 2013 in Atlanta, Ga., USA, April 27 - May 1
Webinar
Increasing Paper Machine Agility with a Novel Grade Change Concept
Wednesday, March 13, 2013 - 12:00pm - 1:00pm EST
Register to attend.
A narrow grade mix and long grade runs were once common. Not today. Most machine make a wider set of products with many grade changes. A new grade transition concept makes such machines more competitive by increasing the stability and agility of the line. Unlike traditional programs, the new grade change concept replies on normal quality controls to move the machine from one grade to the next, quickly and smoothly in a closed loop. Learn more.
Back To Top
|
Overview of Tissue Manufacturing for Softness and Bulk Webinar
Wednesday, March 6, 2013 - 12:00 pm - 1:00 pm EST
This introductory level webinar will give you an overview of basic manufacturing factors, terminology, and operations that will affect and contribute to softness and bulk.
Topics will include:
- The Basic Components of Softness
- Fiber Raw Materials
- Chemical Additives
- Refining
- Tissue Formingand Pressing
- Yankee and Through-Air-Drying (TAD)
- Creping Operations
- Calendering and Converting.
This is a free webinar, but you must register to attend.
Back To Top
|
The TAPPI - PPSA Safety Management Leadership course is designed to build leadership commitment and engagement for a culture of safety excellence. This partnership with the Pulp & Paper Safety Association brings you the best safety practices in the industry.
The Safety Management Leadership Course will be held April 10-11, 2013, at the TAPPI Training Facility in Peachtree Corners, near Atlanta, Ga., USA.
This course delivers curriculum to help you learn the fundamentals of record-keeping, incident investigation, risk management, cultivating a safety culture, managing change safely, and measuring performance. Take a look at the expert panel of instructors. The course is designed for anyone that is involved in workplace safety.
Course registration is limited to only 20 participants, so please register today at the course website. TAPPI and PPSA members save, and early registration discounts are available.
Back To Top
|
Tissue360 Forum @ PaperCon 2013
Monday, April 29 - Wednesday, May 1
Atlanta, Ga., USA
TAPPI's new Tissue publication, Tissue360o magazine, and TAPPI tissue experts have organized Tissue360 Forum, a comprehensive technical forum covering all aspects of tissuemaking. You will hear about the latest tissue technology, market trends, and pick-up some runnability/operational tips. The program is open to all full PaperCon registrants.
Program Overview:
Hygenic Products Market Overview
Session Chairs: Ken Patrick, Tissue360o
Chemistry Solutions for Tissue Making
Session Chair: Gary Furman, Nalco
Water and Energy Strategies for Tissue
Session Chair: Tom Jenn, Kimberly-Clark
Premium Tissue Manufacturing Technologies
Session Chair: Soren Eriksson, Metso
Tissue Controls and Measurement
Session Chair: Rene Naranjo, AstenJohnson
Yankee Reliability (CEUs provided)
Session Chair: Al Coons, Clearwater Paper
Converting Efficiencies
Session Chair: Kevin Brennan, Ashland Water Technologies
See the full Tissue360 Forum program.
PaperCon will take place April 27 through May 1, 2013 in Atlanta, Ga., USA. Designed by industry professionals, PaperCon brings together CEOs, mill managers, superintendents, scientsits, process engineers, and suppliers for the largest pulp and paper technical program in the world. No other such event provides such a comprehensive program, networking opportunites, and trade fair among such a distinguished group of industry leaders.
Learn more about PaperCon 2013.
Back To Top
|
The TAPPI Tissue Properties & Manufacturing Course will be held on April 27-28, 2013 in Atlanta, Ga., co-located with PaperCon 2013 and the Tissue Forum. This is a great opportunity to get the most out of your conference experience. This Tissue Properties course is designed for those who desire an introductory-to-intermediate level, comprehensive, and structured course on tissue properties and the effect of manufacturing. The course precedes the Tissue Forum at PaperCon 2013 and is an excellent educational component to these technical sessions.
This course will be particularly helpful to non-technical professionals, technical process engineers, operators, suppliers, converters and marketers with 0-5 years of experience in tissue manufacturing. Go to the course website to learn more.
Back To Top
|
The TAPPI International Best Practices on the Corrugator Seminar will be held April 9-11, 2013, in conjunction with SinoCorrugated 2013 in Shanghai, China. The three-day course features an in-depth technical program designed to teach participants about each element in the corrugating process and how to improve box plant operations and box quality.
The Best Practices on the Corrugator Seminar is an introductory to intermediate level course that teaches participants how to understand each element in the corrugating process and how to run each component with optimum settings for peak performance to increase productivity, improve quality, and minimize waste. Both old and new equipment will be covered. Participants will also develop an understanding of the critical properties of the raw materials that are vital to guarantee acceptable quality board.
Among the key topics to be addressed are: theory of corrugated board production and solutions to common operational problems; distinguishing key features of paperboard/starch adhesive and how to control warp; operating the corrugated production line; controlling and minimizing downtime; maximizing production line efficiency and maintaining quality standards.
Find out more about the Corrugator Best Practices Seminar.
Back To Top
|
The NETInc Innovative Nonwovens Conference, April 29-May1, 2013, in Atlanta, Ga., USA, is the only technical conference developed by engineers and technologists to help you understand the innovation behind the science and how it impacts the world.
Program topics include: Nanotechnology, Binders and Additives, Building Sciences, Health Care and Medical Applications for Nonwovens, Manufacturing Technology, Process Management Technology, and an Intro to Nonwovens Tutorial.
With several focused tracks, NETInc offers peer reviewed papers, expert speakers, and exclusive networking opportunities. NETInc participants can also enjoy the full PaperCon program and exhibits, Tissue360 Forum, RPTA P-T Seminar and the OpEx Reliability Workshop with their registration.
Learn more about NETInc.
Back To Top
|
Paper Roll Damage Expensive?
Attend TAPPI's SRW Workshop this April and be a part of this dedicated group of mills, carriers, warehouses and printers as they collaborate to reduce in-transit damage to rolls of paper.
The Shipping, Receiving and Warehousing Workshop is an affordable working meeting with presentations and collaborative discussions, engaging keynote speakers, and great opportunities for networking. It's something you can't afford to miss.
Why attend?
- Keynote Presentation by Dave Schirmer, Vice President and General Manager of Hearst Enterprises responsible for paper procurement for divisions of The Hearst Corporation.
- Presentations provided by experts from the class 1 railroads, intermodal providers, warehouses, shippers and dunnage manufacturers with extensive experience and practical background knowledge.
- Practical information sharing by all parties in the paper manufacturing supply chain in an interactive environment
- Excellent networking opportunity - paper buyers, paper companies, carriers, securing / damage prevention specialists, block and bracing manufacturers, safety experts - all under one roof.
Learn more about the Shipping, Receiving and Warehousing Workshop.
Back To Top
|
David Schirmer, Vice President and General Manager of Hearst Enterprises will Keynote at Tappi's Shipping Receiving and Warehousing Workshop this April in Nashville. Schirmer is responsible for paper procurement for divisions of Hearst Corp. including Hearst Magazines and Hearst Newspapers and is one of principles of Newsprint Purchasing LLC.
Tappi's SRW Workshop, taking place April 9-10, focuses on reducing in-transit paper roll damage through collaborative discussions and best practices. Learn more about SRW.
Back To Top
|
Strengthen your understanding of the corrugating process, and linerboard and medium performance properties and manufacture with TAPPI's Linerboard Medium & Corrugated Box Manufacture Course, April 15-16, at the Holiday Inn in Neenah, Wis., USA.
With an emphasis on helping attendees improve corrugating box performance and runnability, this popular introductory to intermediate level course is ideal for process engineers and operators in linerboard and medium manufacturing facilities and corrugating and converting plants.
Instructors Michael J. Kocurek, Professor Emeritus, of Paper Science & Engineering at North Carolina State University, and Jon Porter, Senior Trainer / Process Specialist for Fosber America will address:
- The Corrugated Session (1/2 day) will cover how to achieve the strongest bond and highest quality combinerboard. You'll learn about (1) the equipment, (2) starch, (3) corrugated process technology, and (4) importance of linerboard and medium properties and runnability.
- The Properties and Testing of Liner and Medium session (1/2 day) covers the tests, what they mean, and how the properties of the board affect the tests.
- The Pulp and Paper Mill Operations session (1 day) will cover the technology of the pulp and papermaking processes, and how they affect the quality, properties, tests, and runnability of the liner and medium.
View the proposed course schedule.
Register by March 15 to take advantage of the Early Bird registration discount. Join TAPPI or renew your membership for the best rates!
Back To Top
|
The TAPPI Troubleshooting "Flexos" and "Die Cutters" Sustain Board Caliper & Improve Printing Course is scheduled for April 16-18, 2013, in Neenah, Wis., USA. Join industry veteran Dick Target, founder of On Target Consultants, as he helps attendees identify and address downtime issues and develop a better understanding of machine calibration and how to maintain proper board caliper during the converting process.
Target will use an easy to understand format to help attendees improve the basic manufacturing process. Topics will include: methods to minimize caliper loss in the converting process; one-box set-up techniques; and waste reduction techniques. View the course schedule.
Take advantage of the Early Bird Registration discount before March 16. Join TAPPI or renew your membership for the best rates!
Back To Top
|
TAPPI and NCSU are partnered again for the first of three introductory level courses for industry professionals that cover the entire pulping and papermaking process.
The 2013 Hands-On Workshop for Pulp and Paper Basics takes place March 4-8 at North Carolina state University in Raleigh, N.C., USA.
This workshop fills to capacity quickly, so reserve your place now so that you can:
- Find out how different processes affect paper properties
- Perform hands-on laboratory experiments to support your understanding of the process
- Run a pilot plant paper machine
- Solidify your knowledge from close interaction with professionals in small, interactive groups.
Be among the first 32 people to register for this five-day workshop, and you'll gain an invaluable overview of pulping, bleaching, chemical recovery, recycling, papermaking, and converting. You'll receive course notes, a CD, a polo shirt, and 3.7 CEUs!
This workshop is ideal for new process engineers, manufacturing operators and technicians, sales and service personnel, machine operators, and maintenance personnel -- everyone who wants a better understanding of the pulp and paper business.
Don't wait too long to register for the March 4-8 workshop. Two additional courses are being offered at NCSU in June and October for those who aren't able to attend the first event.
Back To Top
|
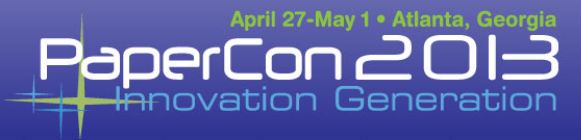
The highly-regarded Executive Panel on Monday, April 29, will illuminate how industry leaders are thinking and driving innovation in their companies.
See who's speaking.
Designed by industry professionals, PaperCon (April 27 - May 1 in Atlanta, Ga., USA) will bring together CEOs, mill managers, superintendents, scientists, process engineers, and suppliers for the largest pulp and paper technical program in the world. No other event provides such a comprehensive program with networking opportunities and trade fair among such a distinguished group of industry leaders.
Back To Top
|
PaperCon Session: Insights into Effective Labor/Management Relationships
Organized by PPMA and PIMA
Monday, April 29, 2013 - 1:30-3:00pm
Many companies have embraced innovative processes for managing labor-management relationships. These processes result in better communication, more effective problem solving, and alignment around shared business goals. Attend this session at PaperCon, part of the PIMA Management Program, and hear examples of effective labor/management teams that yield positive business results. Panelists will share first-person testimonials and stories of challenge, frustration, and success.
Moderator:
Roger Hagan, Zilkha Biomass Energy
Panelists:
Steve Myers, mill manager, Thilmany Paper, Kaukauna, Wis.
Peter Tantalo, operations manager, RockTenn Solvay, Syracuse, N.Y.
Mike Rayome, director, human resources, Graphic Packaging, Wausau, Wis.
Karl Christianson, mill manager, RockTenn, Stevenson, Ala.
PaperCon will take place April 27 through May 1, 2013, in Atlanta, Ga, USA. Designed by industry professionals, PaperCon brings together CEOs, mill managers, superintendents, scientists, process engineers, and suppliers for the largest pulp and paper technical program in the world. No other event provides such a comprehensive program, networking opportunities, and trade fair among such a distinguished group of industry leaders.
Learn more about PaperCon 2013.
Back To Top
|
PaperCon Programs Now Available
Customize your learning and networking experience at PaperCon to best fit your professional needs. Bring back ideas, innovation that will help you be more effective and efficient.
Papermakers program will give you everything you need to know about paper machine performance evaluations, running mill trials, and product certification.
Eight peer-reviewed Coating sessions focus on scientific developments and practical tips. Highlighs include opacity enhancement with Ti02 and advancements in barrier coating.
PIMA Management sessions provide excellent insight for mill managers, production managers, and executives. This year's sessions will help you develop effective labor/management relationships and show you how to motivate today's employees.
The Tissue360 Forum provides a comprehensive peer-reviewed technical program unlike any other. You will learn about fiber, water, and energy savings, the latest softness and strength additives, and forming concepts.
The OpEx Reliability Workshop will help you improve reliability and maintenance in your mill. Operator driven reliability, alignment, education, and mill processes will be addressed by leading reliability experts.
The Young Professionals Program (YP) offers those new to the industry an unbelievable opportunity to gain basic industry knowledge and meet experienced industry leaders.
Back To Top
|
The highly regarded panel on Monday, April 29, will illuminate how industry leaders are thinking and driving innovation within their companies.
See who's speaking.
Designed by industry professionals, PaperCon will bring together CEOs, mill managers, superintendents, scientists, process engineers, and suppliers for the largest pulp and paper technical program in the world. No other event provides such a comprehensive program, networking opportunities, and trade fair among such a distinguished group of industry leaders.
Back To Top
|
The Introduction to Traditional and Emerging Printing Technology Course will be co-located at the 2013 PaperCon Conference, April 27-29, 2013, in Atlanta, Ga., USA.
This is an introductory course on printing methods and applications, designed for those who need to understand print quality, attend print trials, trouble shoot print problems or are generally new to printing operations. It will be taught by printing experts from TAPPI's Coating and Graphic Arts Division and is an excellent complement to the Coating Program at PaperCon.
As an added bonus, the course will include a tour of Hewlett-Packard's new state-of-the art facility where production laser and inkjet presses will be demonstrated.
Course attendees may also join the Coating and Graphic Arts Opening Session where printing visionary Frank Romano is giving the keynote address. Learn more and register online.
Back To Top
|
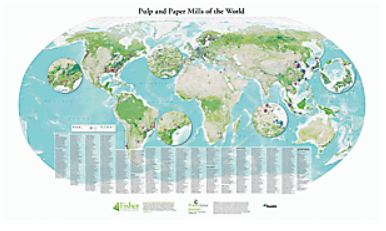
One of TAPPI's most exciting new products is the wall-sized, laminated 2013 Pulp & Paper "Mills of the World" Map.
A winning combination of high quality print and paper stock along with brilliant colors makes this the perfect map to frame and hang in your office. The "Mills of the World" map features include:
- Every mill in the world producing 50 tpd or more
- Major greenfield projects
- Design elements showing mill characteristics, forest cover, and typography
- 3 ft. x 5 ft. (or 0.99 x 1.5 meters) .
Each map will be shipped in a protective tube, ready for display.
Don't miss out on this popular item. Order your Pulp & Paper "Mills of the World" Map today.
Product code: 12PPMAP
Member Price: $299.00
Non-Member Price: $319.00
Back To Top
|
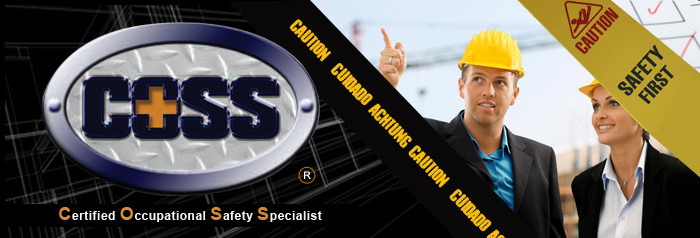
Are you ready to go further, faster in your safety career? The Certified Occupational Safety Specialist (COSS) class can take you there.
The COSS Class is Unique
Not only will you learn how to read and understand the OSHA 1910 and 1926 CFRs and help your company avoid OSHA citations that cost millions of dollars, but more importantly, by learning how to work safely on a job site, you can teach your company how to lower fatalities and near misses. Almost 47% of COSS graduates responding to our survey indicate that, since taking COSS, their company's injury rate and/or OSHA recordables have decreased by as much as 25% and others attest to as much as a 100% decrease!
Request a Course Outline & Syllabus for more information.
The class also addresses the psychology of safety, the true cost of an accident, hazard recognition, how to start up a health and safety program, behavior based safety, system safety, and much more!
What Will You Receive?
Upon successfully completing the class, you will obtain your national Certified Occupational Safety Specialist (COSS) designation, your OSHA 10-hr. card of completion in construction, and your OSHA 10-hr. card of completion in general industry.
National Program Recognitions
COSS is currently one of only 37 programs in the world recongnized and accredited by the American Petroleum Institute (API). In addition, the certifying body for construction education for colleges, universties and technical/trade schools, American Council for Construction Education (ACCE), has also recongnized our program. COSS is the only non-degree program to receive this national endorsement. Lastly, COSS has been established as a mandatory course for students in the Construction Management Program at Louisiana State University.
Program Content
The program consists of 40 hr. of hands on, face-to-face learning, which is delivered by an Authorized OSHA outreach trainer in both construction and general industry. Case studies and workshops are used extensively to bring learning objectives into focus. Guest speaker from areas such as OSHA and other governmental agencies are used to enhance the learning experience. Student presentations, daily quizzes, practical reviews, and a comprehensive final exam will allow you to demonstrate your competency.
Prerequisites
The only prerequisite for the COSS class is you must have a high school diploma or equivalent. In each class, we tend to have a mix of non-experienced, first time safety persons, as well as safety professionals who have been in the safety field for 20+ years. But, we have learned that regardless of the numbers of years of experience you have in safety, everyone leaves the COSS class with a wealth of knowledge!
Visit the COSS website for FAQs, testimonials and a list of clients that have taken COSS.
Register now.
If you would like more information on the COSS program, contact Beth Gordon at 877-610-2677
Back To Top
|
A Call for Papers is underway for these three co-located events:
The 2013 TAPPI PEERS Conference, September 15-18, 2013 in Green Bay, Wi., USA has announced the Call for papers. PEERS is the perfect forum for paper industry professionals both to acquire practical operating insights and to network with industry peers in technical sessions, tutorials, round tables, new technlogy sessions and workshops. Suggested topics and more information now available. Deadline for abstracts is March 1, 2013.
An Invitation to Present has been announced for TAPPI's 2013 International Bioenergy and Bioproducts Conference (IBBC), September 18-20, 2013 Green Bay, Wi., USA. IBBC is the only event dedicated to advancing biorefineries in the forst product industries, and for the first time will be ehld in the Midwest, providing an expanded focus on activities in Wisconsin and surrounding areas. Suggested topics and more information now available. Deadline for abstracts is March 1, 2013.
The International Program Committee for the 10th Research Forum on Recycling announces an Invitation to Present at the 2013 event, September 16-18, 2013 in Green Bay, Wi., USA. Research engineers, scientists, and practitioners are encouraged to submit presentation proposals on all aspects of recycling technologies and operations. Submissions describing both basic and applied research results will be considered. This year's event will provide participants an extraordinary opportunity to hear about the latest in recycling research, discuss mill operation issues, network with peers, and identify future research needs of the recycling community. Deadline for abstracts is March 1, 2013. Learn more.
Back To Top
|
By: Jerome M. Gess and Paul H. Wilson
This book takes the reader through the process of making paper, pointing out where interruptions can occur and where elements added to the system can cause problems in that part or subsequent parts of the papermaking process. The aim of this book is to give papermakers and those involved in the papermaking process the information required to allow them to understand how to track down and solve problems at their source rather than where the problems surface.
Troubleshooting the Papermaking Process.
View the Table of Contents.
Product Code: 0101R298
Member Price: $106.00
Non-member Price: $161.00
Back To Top
|
|
|
TAPPI Over the Wire | 15 Technology Pkwy. S. | Norcross, GA 30092 USA | Voice: 770.446.1400 | Fax: 770.446.6947
|
 |