 |
|
Weekly Spotlight
Economic activity in the U.S. manufacturing sector expanded in February for the third consecutive month, and the overall economy grew for the 45th consecutive month, say the nation's supply executives in the latest Manufacturing ISM (Institute of Supply Management) Report On Business®
Learn More...
|
Session T1 at PaperCon's Tissue360³ Forum, April 29 - May 1, 2013, in Atlanta, Ga., USA, will define, dissect, and analyze the global tissue and hygienic products market, setting the stage for seven intensive technology sessions that follow over the next three days
Learn More...
|
Nippon Paper Industries Co., Japan, reports that it will build new verification and production facilities for cellulose nanofibers at its Iwakuni pulp mill in Japan
Learn More...
|
The National Association of Printing Ink Manufacturers (NAPIM), Peachtree Corners, Ga., USA, is offering a special webinar on March 19, from 2:00 to 4:00 p.m., to provide an overview of the regulation of printing inks in the U.S. and the European Union (EU)
Learn More...
|
International Paper, Memphis, Tenn., USA, has again been named No. 1 company in the Forest and Paper Products sector, according to Fortune magazine's annual report of "America's Most Admired Companies."
Learn More...
|
Brussels, Belgium-based duomedia reports that it conducted a survey in the fourth quarter of 2012 to gain insight from key consultants in the graphic arts industry
Learn More...
|
TAPPI's 2013 Tissue Properties and Manufacturing Course, to be held in conjunction with PaperCon 2013, covers the fundamentals of manufacturing and provides an excellent overview of this dynamic market segment
Learn More...
|
The OpEx Maintenance and Reliability Workshop at TAPPI PaperCon 2013 in Atlanta, Ga., USA, on April 30, will include a special joint session with the Recycled Paper Trade Association (RPTA) that explores Operator Driven Reliability (ODR) from an up-close, mill case-study perspective
Learn More...
|
Below is the latest listing of job openings in the TAPPI Career Center.
Learn More...
|
Market Roundup
Total U.S. printing and writing (P&W) paper shipments in January were down 3% from January 2012
Learn More...
|
Total U.S. kraft paper shipments in January were 140,500 tons, an increase of 19% compared with the prior month
Learn More...
|
Pulp & Paper
The United Steelworkers Union (USW), Pittsburgh, Pa., USA, this week said that proposed state legislation to end Maryland's biofuel credit could increase pollution and fuel costs, suppress development of renewable fuels, and lead to massive job losses
Learn More...
|
Consumers for Paper Options, Washington, D.C., USA, a coalition of individuals and organizations advocating for the right to paper-based communications, has applauded a new congressional resolution to protect access to paper-based options for government services and information
Learn More...
|
Cascades, Candiac, Qué., Canada, reports that the expansion of its Tissue Group plant in Lachute, Qué,, has received the LEED® Gold certification
Learn More...
|
Following a comprehensive analysis, Clearwater Paper Corp., Spokane, Wash., USA, this week announced the planned permanent closure of its Thomaston, Ga., tissue converting and distribution facility
Learn More...
|
Ilim Group, Russia, reports that its new paper machine at Koryazhma, Arkhangelsk oblast, made paper for the first time this past Sunday (March 3)
Learn More...
|
International Forest Products Limited (Interfor), Vancouver, B.C., Canada, has completed the acquisition of Rayonier''s (Jacksonville, Fla., USA) Wood Products Business in the U.S. South, headquartered in Baxley, Ga.
Learn More...
|
Containerboard/Packaging
A. Merati & C. Cartiera di Laveno, Laveno, Italy, has successfully started up a paperboard machine rebuilt by Andritz, Graz, Austria
Learn More...
|
The Europac Group, Madrid, Spain, has acquired a corrugated board factory in Caradec, France, for EUR 21.7 million, expected to become effective March 1
Learn More...
|
Nonwovens
A new version of Fibertect®, a nonwoven decontamination wipe created by researchers at Texas Tech University, Lubbock, Texas, USA, has proved itself more viable at cleaning up a nerve chemical surrogate than the decontamination substance currently used by the U.S. Department of Defense (DoD), which is currently being phased out
Learn More...
|
|
New Products
Brennan Industries Inc., Cleveland, Ohio, USA, has expanded its product lines by introducing new compression-end instrumentation valves
Learn More...
|
Hahnemuehle, Germany, announced this week that Hahnemuehle Photo is a new product line consisting of two resin-coated papers for photographic inkjet printing
Learn More...
|
Published Pricing
Lecta, France, reports that it will continue implementing the announced price increase of 5% to 6% on its CWF paper in all channels and markets justified by the high level prices of main raw materials, transport, and energy
Learn More...
|
Metsä Board, Finland, is raising the prices of all Kemiart white-top kraftliner grades by EUR 50 per metric ton
Learn More...
|
Nippon Paper Industries Co., Japan, this week announced price increases for printing paper in the domestic market to all of its agencies
Learn More...
|
Södra, Sweden, has raised the price of its softwood pulp to $860 and hardwood pulp to $820 per metric ton in Europe, effective March 1
Learn More...
|
The Newark Group, Cranford, N.J., USA, this week announced a $40 per ton price increase on all coated grades of recycled paperboard effective with shipments on or after April 2
Learn More...
|
People
Sappi Limited, Johannesburg, South Africa, this week announced that Robert J. DeKoch has joined the board as an independent non-executive director beginning March 1
Learn More...
|
TAPPI News
TAPPI's Annual Business Meeting will be held on March 12 via teleconference.
Learn More...
|
The Herman Joachim Distinguished Service Award, to be presented to Kinstrey at PaperCon 2013 in Atlanta, is the highest honor TAPPI can bestow upon an individual for exemplary leadership that has significantly contributed to the advancement of the Association.
Learn More...
|
Webinar set for Match 13 is focued on Increasing Paper Machine Agility with a Novel Grade Change Concept.
Learn More...
|
This active member recommends volunteering as one way to give back.
Learn More...
|
TAPPI has partnered with PPSA to bring you the best safety practices in the industry.
Learn More...
|
Organized by tissue experts, this comprehensive technical forum will cover all aspects of tissuemaking.
Learn More...
|
The TAPPI Tissue Properties & Manufacturing Course will be held on April 27-28, 2013, in Atlanta, Ga., USA, co-located with PaperCon 2013 and the Tissue Forum.
Learn More...
|
The TAPPI International Best practices on the Corrugator Seminar will be held April 9-11 in conjunction with SinoCorrugated 2013 in Shanghai, China.
Learn More...
|
NETInc Innovative Nonwovens Conference in April to focus on innovation.
Learn More...
|
W more than 130 diagrams and photographs, this book is available to TAPPI members for a $29.00 discount off the list price.
Learn More...
|
TAPPI's Shipping, Receiving and Warehousing Workshop Focuses on Reducing Roll Damage
Learn More...
|
David Schirmer, Vice President and General Manager, Hearst Enterprises, will Keynote SRW Workshop this April.
Learn More...
|
Strengthen your understanding of the corrugating process and linerboard and medium performance properties and manufacture with TAPPI's Linerboard Medium & Corrugated Box Manufacture Course, April 15-16, at the Holiday Inn in Neenah, Wis., USA.
Learn More...
|
April 16-18, 2013 - Join industry veteran Dick Target, founder of On Target Consultants, as he helps attendees identify and address downtime issues and develop a better understanding of machine calibration and how to maintain proper board caliper during the converting process.
Learn More...
|
PaperCon will feature Executive Panel with leaders from International Paper, NewPage, Verso, and Soundview.
Learn More...
|
PaperCon 2013 to feature session focusing on effective labor/management teams that yield positive business results.
Learn More...
|
Expand your knowledge, improve your personal network, and learn ways to generate innovation at PaperCon.
Learn More...
|
Highly regarded industry leaders to speak on April 29 at Papercon '13 in Atlanta, Ga., USA.
Learn More...
|
Introductory course on printing methods and applications is designed for those who need to understand print quality, attend print trials, trouble shoot print problems, or are generally new to printing operations.
Learn More...
|
One of TAPPI's most exciting new products, the laminated and wall-sized 2013 Pulp & Paper "Mills of the World" Map, is now available through TAPPI Press with a twenty dollar discount for members.
Learn More...
|
This book takes the reader through the process of making paper, pointing out where interruptions can occur and where elements added to the system can cause problems in that part or subsequent parts of the papermaking process.
Learn More...
|
Register now for the class where you will learn to understand OSHA, avoiding citations that could cost millions of dollars. Teach your company how to lower fatalities and near-misses.
Learn More...
|
|
Find us on Facebook
Network with us on LinkedIn
Follow us on Twitter
|
Weekly Spotlight
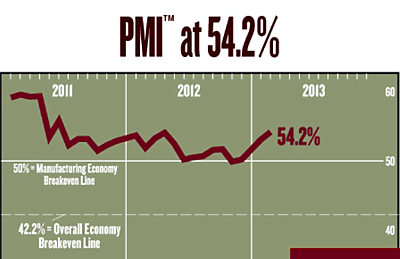 Economic activity in the U.S. manufacturing sector expanded in February for the third consecutive month, and the overall economy grew for the 45th consecutive month, say the nation's supply executives in the latest Manufacturing ISM (Institute of Supply Management) Report On Business®. The report was issued this week by the ISM Manufacturing Business Survey Committee, Tempe, Ariz., USA.
The PMI registered 54.2%, an increase of 1.1 percentage points from January's reading of 53.1%, indicating expansion in manufacturing for the third consecutive month. This month's reading reflects the highest PMI since June 2011, when the index registered 55.8%. The New Orders Index registered 57.8%, an increase of 4.5% over January's reading of 53.3%, indicating growth in new orders for the second consecutive month. As was the case in January, all five of the PMIs component indexes—new orders, production, employment, supplier deliveries, and inventories—registered in positive territory in February. In addition, the Backlog of Orders, Exports, and Imports Indexes all grew in February relative to January.
Of the 18 manufacturing industries, 15 are reporting growth in February in the following order: Apparel, Leather and Allied Products; Miscellaneous Manufacturing; Paper Products; Electrical Equipment, Appliances and Components; Plastics and Rubber Products; Fabricated Metal Products; Furniture and Related Products; Petroleum and Coal Products; Wood Products; Printing and Related Support Activities; Transportation Equipment; Nonmetallic Mineral Products; Food, Beverage, and Tobacco Products; Machinery; and Primary Metals. The three industries reporting contraction in February are: Textile Mills; Computer and Electronic Products; and Chemical Products.
The 15 industries reporting growth in new orders in February (in order) are: Apparel, Leather, and Allied Products; Furniture and Related Products; Miscellaneous Manufacturing; Paper Products; Machinery; Nonmetallic Mineral Products; Fabricated Metal Products; Transportation Equipment; Plastics and Rubber Products; Primary Metals; Electrical Equipment, Appliances and Components; Food, Beverage, and Tobacco Products; Computer and Electronic Products; Chemical Products; and Petroleum and Coal Products. The only industry reporting a decrease in new orders during February is Wood Products.
ISM's Production Index registered 57.6% in February, which is an increase of 4 percentage points when compared with the 53.6% reported in January. This indicates growth in production for the sixth consecutive month. An index above 51.2%, over time, is generally consistent with an increase in the Federal Reserve Board's Industrial Production figures.
The 13 industries reporting growth in production during the month of February (in order) are: Wood Products; Paper Products; Electrical Equipment, Appliances and Components; Miscellaneous Manufacturing; Primary Metals; Apparel, Leather, and Allied Products; Printing and Related Support Activities; Fabricated Metal Products; Transportation Equipment; Plastics and Rubber Products; Food, Beverage, and Tobacco Products; Computer and Electronic Products; and Machinery. The four industries reporting a decrease in production in February are: Textile Mills; Petroleum and Coal Products; Chemical Products; and Furniture and Related Products.
ISM's Employment Index registered 52.6% in February, which is 1.4 percentage points lower than the 54% reported in January. This month's reading indicates growth in employment for the 41st consecutive month. An Employment Index above 50.5%, over time, is generally consistent with an increase in the Bureau of Labor Statistics (BLS) data on manufacturing employment.
Of the 18 manufacturing industries, 10 reported growth in employment in February in the following order: Petroleum and Coal Products; Apparel, Leather, and Allied Products; Paper Products; Printing and Related Support Activities; Furniture and Related Products; Electrical Equipment, Appliances and Components; Miscellaneous Manufacturing; Plastics and Rubber Products; Fabricated Metal Products; and Primary Metals. The five industries reporting a decrease in employment in February are: Chemical Products; Transportation Equipment; Computer and Electronic Products; Machinery; and Wood Products.
The Inventories Index registered 51.5% in February, which is 0.5 percentage point higher than the 51% in January. This month's reading indicates that respondents are reporting that inventories are growing in February for the second consecutive month. An Inventories Index greater than 42.7%, over time, is generally consistent with expansion in the Bureau of Economic Analysis' (BEA) figures on overall manufacturing inventories (in chained 2000 dollars).
The nine industries reporting higher inventories in February (in order) are: Apparel, Leather, and Allied Products; Wood Products; Plastics and Rubber Products; Petroleum and Coal Products; Transportation Equipment; Miscellaneous Manufacturing; Chemical Products; Fabricated Metal Products; and Food, Beverage, and Tobacco Products. The six industries reporting decreases in inventories in February (in order) are: Textile Mills; Primary Metals; Furniture and Related Products; Paper Products; Computer and Electronic Products; and Nonmetallic Mineral Products.
The full text version of the Manufacturing ISM Report on Business is available online.
Back To Top
|
Session T1 at PaperCon's Tissue360° Forum, April 29 - May 1, 2013, in Atlanta, Ga., USA, will define, dissect, and analyze the global tissue and hygienic products market, setting the stage for seven intensive technology sessions that follow over the next three days—chemistry, fiber, advanced production systems, water and energy, controls and measurement, yankee dryer, and converting developments. Sponsored by TAPPI's newest print publication, Tissue360° magazine, these eight Tissue Forum sessions provide the most comprehensive exploration of emerging market drivers and technology developments available anywhere for understanding and meeting challenges of the rapidly evolving tissue and hygienic products industry.
Leading off Session T1, Esko Uutela of RISI examines the tissue, towel, and personal hygiene products arena in North America and worldwide in term of current and projected capacities as well new and emerging trends that will shape markets into the foreseeable future. Lindsay Gervais of Pöyry Management Consulting then looks specifically at the critical fiber side of tissue and hygiene products, assessing the decline of recycled fiber quality and availability and the outlook for virgin and other fiber sources, as well as nonwovens resources that will determine the future direction of these product markets.
Uutela notes that the tissue business is booming today after recovering quickly and strongly from the 2009 recession. Globally, tissue consumption approached 32 million metric tpy in 2012 and for the first time exceeded the volume of newsprint. RISI expects the long-term growth to continue at an annual average rate of 4% or slightly above. During the past 10 years, China has been the prime motor for growth in the global paper and board industry, and so also in the tissue business, followed by Latin America, which also has shown strong expansion. In the next 10 years, large emerging markets such as Brazil, Turkey, and Russia will increasingly offer tissue companies new business opportunities.
The North American tissue market is experiencing a new investment boom this year, expected to continue through 2014, Uutela continues. This time the main driver for new projects seems to be the need for ultra and premium grade tissue, partly as a reflection of major retailers' target to upgrade their private label offerings closer to the main brands in quality, although there is a clear trend toward higher quality in the away from home sector as well. "Market growth has flattened, particularly in terms of weight as the product light-weighting trend continues. Competition does not show any signs of alleviation, and it's amazing to see how a growing number of small, independent converters have been able to forge ahead based on their niche products, flexible service, and sub-contracting orders from the big players," Uutela says.
Gervias adds that amidst a backdrop of falling demand for printing and writing paper in mature markets, a key concern for several tissue manufacturers is the availability, quality, and cost of recovered paper. "But at what point does recycled paper become uneconomical compared with other fiber options?" she asks.
In her presentation, Gervais explores the combination of falling yields and rising costs of SOP (sorted office paper) to determine a breakeven cost of manufacture when compared with a virgin fiber furnish. She examines the impacts of this key issue and takes a look at other fiber resources and their future role in tissue manufacturing.
More information about PaperCon 2013 is available online, including online registration. Additional information about the Tissue360° Forum program http://www.papercon.org/pdf/TissueProgram.pdf is also available online.
Back To Top
|
Nippon Paper Industries Co., Japan, reports that it will build new verification and production facilities for cellulose nanofibers at its Iwakuni pulp mill in Japan. The cellulose nanofiber will use pulp as a raw material.
Cellulose nanofibers are materials obtained by breaking plant fibers (pulp) down to the nano-order level, several orders of magnitude smaller than a micron. They provide excellent features. The elasticity is as high as that of aramid fibers known for high intense fiber. They stretch well, similar to glass, as temperature changes. They provide high barrier performance to gas, including oxygen. Also, because they come from plant fibers, they are characterized by a low environmental footprint in production and disposal, as well as light weight. Cellulose nanofibers are expected to find many applications, such as reinforcements, thickeners, and gas barrier materials.
The new verification and production facility for cellulose nanofibers will have an annual production capacity of 30 or more metric tons, and will start production this October. The facilities will make it easy to disintegrate pulp by implementing prior treatment chemically.
The basic development for this has already been conducted in a project called "Research and Development of Nanodevices for Practical Utilization of Nanotechnology" at the New Energy and Industrial Technology Development Organization (NEDO). The new facilities will be Japan's first full-fledged facilities producing cellulose nanofibers by chemical treatment.
Back To Top
|
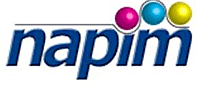 The National Association of Printing Ink Manufacturers (NAPIM), Peachtree Corners, Ga., USA, is offering a special webinar on March 19, from 2:00 to 4:00 p.m., to provide an overview of the regulation of printing inks in the U.S. and the European Union (EU). Presenters, Mitzi Ng Clark and Catherine R. Nielsen of Keller and Heckman LLP, will address the various forms of customer assurance, and how to respond to requests in this regard.
The webinar is free to NAPIM members and $25 for nonmembers. Registration is available online.
Participants will learn the "basics" of how printing inks are regulated in the U.S. and EU. Focus will be given to unique issues faced by the printing ink industry, and better understanding customer assurance questions as they relate to printing inks. This webinar should be of interest to ink formulators, research personnel, technical support personnel, sales people, and regulatory compliance personnel.
After the webinar, participants should be able to identify various approaches to establishing regulatory compliance of printing ink components in the U.S. and Europe, including application of the functional barrier doctrine, identify legislation and guidance impacting the compliance and safety of printing inks used in the EU, and prepare letters of assurance regarding the regulatory status of printing inks. Overall, participants will better understand letters of assurance received from suppliers concerning the FDA and EU status of printing components.
Registration is required to participate in this webinar.
Back To Top
|
International Paper, Memphis, Tenn., USA, has again been named No. 1 company in the Forest and Paper Products sector, according to Fortune magazine's annual report of "America's Most Admired Companies." This is IP's tenth time in the past 11 years to top the Fortune list within this category. Out of the nine key attributes on which companies are judged, IP took the top spot in seven within its industry. Those categories included people management, quality of management, financial soundness, quality of products and services, global competitiveness, use of corporate assets, and innovation.
"This is well-deserved recognition and a reflection of International Paper's 68,000 talented employees around the globe," said John Faraci, chairman and CEO. "Managing through an uneven global economy while continuing to generate solid results is what good execution is all about. Congratulations to all of our employees."
IP has manufacturing operations in North America, Europe, Latin America, Russia, Asia, and North Africa. Its businesses include industrial and consumer packaging and uncoated papers, complemented by xpedx, the company's North American distribution company. The company employs some 68,000 people and is located in more than 24 countries. Its net sales for 2012 were $28 billion.
Back To Top
|
Brussels, Belgium-based duomedia reports that it conducted a survey in the fourth quarter of 2012 to gain insight from key consultants in the graphic arts industry. The results of this international survey, duomedia notes, make it absolutely clear that "print must adapt" to continue to play a crucial role in the communications mix. Print professionals and influencers from 10 countries shared their opinions on how print will evolve in the digital age.
Lutt Willems, partner at duomedia, explains that the survey "provides an accurate snapshot of the status of the print industry. By soliciting the opinions of professionals and influencers from around the globe, we can help print houses identify the most important areas of focus to drive revenue and to ensure that print remains a highly effective component of the cross-media communication mix."
Many survey respondents identified the need for print houses to adopt a new strategy. They urged printers to go beyond being just a supplier, and to work more closely with customers and brands to establish themselves as value-added service providers in the marketing and communication supply chain.
Eddy Hagen, director and trend-watcher at VIGC (Flemish organization for Graphic Communication), says that "print houses need to change their mindset and focus on offering solutions and services rather than selling products. A marketing manager doesn't need a printed brochure, he needs a solution to convey his message to his (potential) customers. Identifying the real needs of their customers will lead to new and interesting offerings. I recently spotted a simple but very effective example of this solutions-oriented mindset: a printer solved the number one issue of a small winery—missed sales—by simply changing the layout of the label. A small change with a big impact. Of course, a change in mindset means investing time and resource. But it's well worth the effort if it means your company is seen as a high-value link in the marketing and product development chain rather than as just a supplier of printed paper or of printed packaging. This industry will evolve from a product industry to a solutions and services industry."
Many survey respondents flagged the growing trend for short-run, on-demand work, which is being facilitated by advances in digital printing technology. High volume printing will decrease over time as more print is produced on demand.
A perfect example of why short-run, on-demand work is proving so popular are school books. It doesn't make economic sense to hold on to thousands of copies when it's highly likely they'll need updating before too long. With digital, the school can print as many copies as they need, when they need them, and be able to update content as needed to keep educational materials as relevant as possible.
Respondents highlighted that there are growth opportunities in producing products to which people attach a new function, an added value or an emotional value, such as photos.
Ed Boogaard, freelance journalist in the printing industry, believes some people will always value print over digital: "For example, for many people, printed photos hold a special place. Looking back at pictures on a laptop just isn't the same as seeing them in an album or photo book. Also magazines will become more and more functional for people, especially with the trend towards short run printing."
Whether you are talking about magazines, commercial print, or packaging, QR Codes, personalized URLs, or augmented reality, there are a variety of ways to make print interactive and blend it more seamlessly with digital communications strategies, duomedia points out.
According to Cary Sherburne, senior editor at What They Think, "printers view digital alternatives to print as a threat and worry about cannibalization of their printing business. The truth is, this cannibalization will continue to happen, with them or without them. Making print interactive will extend the life and value of print, and it's not that hard to do. Additionally, adding value by supplementing a printed brochure with a tablet or smartphone app that overlays rich content such as audio, video, and more, can add high margin revenue streams and increase customer loyalty."
Those surveyed predicted that while commercial print volume will continue falling, the opposite is true for packaging and label printing. As one respondent summed up, "no matter how much digital evolves, you can't download an ice cream. You're always going to need packaging."
But with environmentalists pushing for ever-smaller packaging, does this mean a smaller market? Not necessarily, according to one respondent. "You only have to look at Easter eggs to see how packaging has shrunk. But this doesn't spell the end for packaging printers—it just means there's more emphasis on creative packaging. Packaging designers and producers can add value to brands' products by producing creative, attractive packaging, despite having a much smaller ‘canvas' to work on."
According to the survey, sustainability will become even more important, with brands using their green credentials to glean a competitive edge. To this end, respondents suggested that all companies operating in paper-based industries should be more vocal in communicating their sustainability accreditations and initiatives, particularly as digital-based companies will come under greater environmental scrutiny in the future than they are under today.
Back To Top
|
TAPPI's 2013 Tissue Properties and Manufacturing Course, to be held in conjunction with PaperCon 2013, covers the fundamentals of manufacturing and provides an excellent overview of this dynamic market segment. The two-day course will be held on April 27-28, 2013 in Atlanta, Ga., USA, and precedes PaperCon and the Tissue360° Forum.
"Tissue manufacturing is technically innovative and rapidly growing and the Tissue Course provides an excellent overview of manufacturing operations, equipment, and tissue sheet properties," notes Larry N. Montague, TAPPI president and CEO. "Course participants will be able to also take advantage of the Tissue360° Forum and all of the networking opportunities available during PaperCon."
This course is designed for those who desire an introductory-to-intermediate level, comprehensive, and structured course on tissue properties, and the effect of manufacturing processes on them. It provides an excellent educational compliment to the Tissue360° Forum sessions. Attendees will learn about a wide range of key topics including: tissue properties and tests; stock prep and refining; chemicals (wet end and yankee); wet end operations; TAD and yankee drying; creping; calendaring; and converting.
The Tissue360° Forum and PaperCon 2013 feature the industry's largest technical program in addition to a number of special events, seminars, and tracks on a wide range of topics and industry segments, numerous networking opportunities, keynote presentations, and a trade show exhibit.
Back To Top
|
The OpEx Maintenance and Reliability Workshop at TAPPI PaperCon 2013 in Atlanta, Ga., USA, on April 30, will include a special joint session with the Recycled Paper Trade Association (RPTA) that explores Operator Driven Reliability (ODR) from an up-close, mill case-study perspective. During this session, Christer Idhammar with IDCON examines what has been tried with ODR, who's succeeded, what's failed, and why—all based on mill case study results.
Also during the joint session, Tony Kenneson-Adams of RockTenn will look in-depth at how his Solvay recycled containerboard mill in Syracuse, N.Y., set up its ODR program and the pitfalls they experienced along the way. Rounding out the joint OpEx/RPTA session, Jim Davis of Performance Consultants Associates illustrates how to effectively support ODR programs by building "The Perfect Maintenance Storeroom."
More information about PaperCon 2013 and the OpEx Maintenance and Reliability Workshop, including registration procedures, is available online. Also available online is the 2013 OpEx Workshop program.
Back To Top
|
Below is the latest listing of job openings in the TAPPI Career Center. The current listing includes job openings for a variety of positions including process engineers, power and recovery assistant superintendent, chief engineer, executive director, production manager, sales manager, production manager, mill manager, engineering intern, and R&D manager. Current, specific job openings at companies and locations in the TAPPI Career Center include:
Employer |
Title |
Location |
BASF The Chemical Co. |
Process Engineer-Kaolin |
Mcintyre, Ga. |
BASF The Chemical Co. |
Development Scientist |
Gordon, Ga. |
Boise Inc. |
Maintenance Manager |
Salt Lake City, Utah |
Boise Inc. |
Power & Rec. Assist. Super. |
Wallula, Wash. |
Confidential |
R&D Manager |
Albany, N.Y. |
Fajar Paper |
Mill Manager |
Indonesia |
Fajar Paper |
Production Manager |
Indonesia |
Fajar Paper |
Chief Engineer |
Indonesia |
Kadant Johnson |
Process Engineer |
Lenoir City, Tenn. |
Longview Fibre |
Project Engineering Manager |
Longview, Wash. |
MeadWestVaco |
Human Resources Mgr-Mill Ops. |
Cottonton, Ala. |
Michelman |
Global Tech. Mgr.-Paper Coatings |
Cincinnati, Ohio |
NCR Corporation |
Chem. Eng./P&P-Paper Coatings |
Georgia |
Norpac-Weyerhaeuser |
Engineering Internship |
Longview, Wash. |
Total Lubri. Mgt./Colfax Fluid Hand. |
Territory Sales Manager |
SE USA |
Washington P&P Foundation |
Executive Director |
Seattle, Wash. |
More information about these jobs is available online.
Back To Top
|
Market Roundup
Total U.S. printing and writing (P&W) paper shipments in January were down 3% from January 2012, according to the AF&PA (Washington, D.C., USA) January 2013 Printing-Writing Paper Report released this week. Additional key findings of the report include:
- January shipments of coated free sheet (CFS) papers in the U.S. increased by 5% compared with January 2012, the third year-over-year increase in the past four months
- Uncoated free sheet (UFS) papers shipments of 766,300 tons in January were 3% below the same period last year
- January uncoated mechanical (UM) paper shipments decreased 10% compared with January 2012
- January shipments of coated mechanical (CM) decreased 9%, compared with January 2012, to 255,900 tons.
Back To Top
|
Total U.S. kraft paper shipments in January were 140,500 tons, an increase of 19% compared with the prior month, AF&PA, Washington, D.C., USA, reports in its January 2013 Kraft Paper Report issued this week. Bleached kraft paper shipments increased year-over-year 17%, and unbleached kraft paper shipments increased 7% year-over-year.
As a result, total kraft paper shipments begin the year 9% higher than 2012. Total month-end inventory decreased 14% to 73,500 tons this month compared with December 2012 month-end inventories.
Back To Top
|
Pulp & Paper
The United Steelworkers Union (USW), Pittsburgh, Pa., USA, this week said that proposed state legislation to end Maryland's biofuel credit could increase pollution and fuel costs, suppress development of renewable fuels, and lead to massive job losses. Maryland House Bill 1102 and Senate Bill 684, if passed, USW notes, would redefine renewable energy to exclude "black liquor"—a byproduct of the pulping process in the manufacture of paper—as a biofuel. This would eliminate the payments that paper companies currently receive from Maryland utilities for selling renewable-energy credits to them.
Maryland adopted a renewable energy law in 2005 that requires utilities to buy certain minimum percentages of their electricity from renewable sources. Washington, D.C. has a virtually identical law known as the renewable portfolio standard law.
As USW explains, paper companies use the spent pulping liquor, which includes bark and unused wood chips leftover from the pulping process, as fuel so that the material does not go into landfills or water. This biomass fuel is carbon-neutral because the trees that are planted for every tree brought into a mill absorb more carbon dioxide than the mill emits when it uses this biofuel, USW adds, noting that, unlike other industries, the paper sector relies more on renewable fuel to reduce its dependency on fossil fuels, and this helps the U.S. in its overall goal to reduce its carbon imprint and dependence on other nations for fuel.
"If the fuel credit is taken away, it will change the economics of fuel use at our mill," said USW Local 676 President Greg Harvey, who is a recovery boiler operator at the NewPage paper mill in Luke, Md. "It will make the use of coal more economical and the use of carbon-neutral biofuel less attractive. What this would mean is more use of coal and less use of biofuel—a renewable resource—at our mill, which would increase net carbon emissions in Maryland."
Currently, wind energy is getting the majority of Maryland's renewable fuel credits, and keeping biomass-based sources in Tier 1 works to keep prices of renewable fuel low. But if this legislation passes and biofuels are moved to Tier II, there will be fewer renewable energy credits available and they will likely cost more. The end result is higher renewable fuel costs for consumers.
Moving biofuels to Tier II also would suppress the development of renewable fuels since it would reduce the likelihood that Maryland companies would work to increase the state's reliance on this renewable resource, USW points out.
"In addition to sending a bad message about carbon-neutral, renewable biofuel, HB 1102 and SB 684 send a bad message about jobs in western Maryland," Harvey said. "Right now there are close to 800 union members working at my mill and about 1,000 people total work there. This is 1,000 people, in a part of our state where the overall economy is not in good shape right now, who can support their families and local businesses.
"Eliminating the payments to paper companies for their renewable fuel would likely harm my mill. Unfair imports from Asia caused two of our paper machines to close and more than 500 employees to lose their jobs. The trade pressure was eased because our union, along with my company's help, was able to get the federal government to intervene, but trade and market pressures continue to be severe. Our area cannot withstand more layoffs," Harvey emphasized.
Harvey testified on Tuesday of this week (March 5) before the Maryland Senate Finance Committee about SB 684. His testimony can be read online. Today (March 7) he is testifying before the Maryland House Economic Matters Committee on HB 1102. This testimony is also available online.
Back To Top
|
Consumers for Paper Options, Washington, D.C., USA, a coalition of individuals and organizations advocating for the right to paper-based communications, has applauded a new congressional resolution to protect access to paper-based options for government services and information. This bipartisan resolution (H. Res. 97), introduced in the U.S. House of Representatives by Reps. Sean Duffy (R-Wis.) and Mike Michaud (D-Maine), seeks to reverse recent federal initiatives to completely eliminate paper-based information and services, such as Social Security checks and earnings statements, savings bonds, and income tax forms.
Federal agencies have been forcing Americans to go "paperless" without public comment or Congressional oversight, despite the fact that millions of Americans cannot access information in electronic formats and cybersecurity threats are on the rise. The Duffy-Michaud resolution seeks to bring these agency decisions under Congressional review, while directing the federal government to ensure that Americans receive paper information and services, unless they specifically choose electronic-only.
"Federal efforts to eliminate paper-based services and information are disenfranchising millions of Americans, including senior citizens, lower income Americans, and those who are concerned about cyber-threats," said John Runyan, executive director of Consumers for Paper Options. "More than 30 million American households lack Internet access both at home and at work, and yet our government expects all citizens to e-file tax forms, manage their finances online, and purchase savings bonds electronically."
Runyan further noted that "it's time for Congress to step in and protect equal and appropriate information access for all Americans. We are pleased to see Reps. Duffy and Michaud leading the charge to make federal agencies accountable for their decisions, and to defend the right for Americans to receive government information in whatever means they choose. The federal government has a duty to serve every citizen, regardless of which side of the digital divide they inhabit."
More information about Consumers for Paper Options is available online.
Back To Top
|
Cascades, Candiac, Qué., Canada, reports that the expansion of its Tissue Group plant in Lachute, Qué,, has received the LEED® Gold certification. The plant is the first paper manufacturing facility to obtain LEED-NC (new construction) certification in the Canadian paper industry.
The 6,800 sq. meter expansion project of the Lachute plant received the Gold level of LEED certification due to Cascades' continuous efforts to reduce its ecological footprint. The project was recognized for its exemplary performance regarding:
- The reduction of its drinking water consumption, evaluated at 46.57%
- The use of regional materials, with 47.08% of costs used for the purchase of materials produced and extracted locally
- The presence of certified wood, accounting for 96.36% of total cost for materials.
"Congratulations to Cascades Tissue Group - Lachute for this LEED Gold certification. Buildings that are sustainable and respectful of the environment have become an exemplary practice in the building industry, but the manufacturing sector is lagging behind. I congratulate Cascades Tissue Group for its determination in working towards the preservation of the environment and the well-being of Canada," said Thomas Mueller, president and CEO of the Canada Green Building Council (CaGBC), the organization behind the certification.
The project was also acknowledged because it offers a 58% reduction in energy costs, when compared with a Canadian reference building. The CaGBC applauded the fact that 86.6% of the construction waste was diverted from landfill.
"We are honored to receive this certification, which reflects our numerous efforts to protect the environment and to make sustainable development a priority," added Alain Lemaire, president and CEO of Cascades. "The new plant expansion not only meets the strict standards set by the LEED-NC rating system, but also helps to sustain the local economy, while respecting the building's more than 100-year-old heritage and its contribution to the community."
Cascades Tissue Group, a division of Cascades ULC, is the fourth largest manufacturer of tissue paper in North America. Founded in 1964, Cascades produces, converts and markets packaging and tissue products that are composed mainly of recycled fiber. The company employs more than 12,000 men and women who work in more than 100 units located in North America and Europe.
Back To Top
|
Following a comprehensive analysis, Clearwater Paper Corp., Spokane, Wash., USA, this week announced the planned permanent closure of its Thomaston, Ga., tissue converting and distribution facility. The gradual shutdown of converting equipment will occur on a schedule throughout the year, with some operations running into the first quarter of 2014, affecting a total of 150 employees.
"This has been a difficult decision—one where the company reviewed many scenarios and alternatives to closing the plant," said Tom Colgrove, president of Clearwater Paper's consumer products division. "We have concluded that consolidating regional converting and permanently closing Thomaston was the solution to best serve the needs of our southeastern customers and improve the overall logistics of our national manufacturing network."
Displaced Thomaston employees will be given an opportunity to apply for open positions at other Clearwater Paper facilities. In addition, the company is offering separation and incentive pay for employees who remain at Thomaston until their established final day of work. Also, the company is working closely with West Central Georgia Private Industries Council and the Economic Development Division at the Southern Crescent Technical College to assist with career transition services where needed.
Clearwater Paper will integrate most of the equipment from Thomaston in its facilities at Oklahoma City, Okla., and Shelby, N.C.
"Our goal is to provide jobs where possible to our valued employees who are willing to relocate," said Colgrove. "Where the company cannot do that, Clearwater Paper wants to ensure we are doing as much as we can to help affected employees through this difficult transition."
The company expects the total impact of non-recurring exit-related costs to be approximately $6 - $7 million, of which approximately $4 - $5 million will be incurred this year. The cost savings benefits resulting from the equipment relocation and converting facility optimization, which are part of the company's previously announced cost savings programs, are expected to be fully realized beginning in the fourth quarter of 2014.
Back To Top
|
Ilim Group, Russia, reports that its new paper machine at Koryazhma, Arkhangelsk oblast, made paper for the first time this past Sunday (March 3). During the coming weeks, Ilim Group's specialists, supported by experts from International Paper, Memphis, Tenn., USA, its partner in the Koryazhma mill, and representatives of equipment suppliers, will be working together to bring the machine up to full production, and help it meet all of the product quality parameters. New office and offset paper being produced on the new machine will soon enter the Russian market.
The Big Koryazhma project, with an investment of $270 million, involved construction of a new paper machine, installation of an off-machine coater, installation of cut-size and folio sheeters, construction of a precipitated calcium carbonate (PCC) plant, and implementation of infrastructure projects. Construction of the new paper machine in Koryazhma started in the summer of 2011 at the production site of Ilim Group Branch in Koryazhma.
As a result of the project, Russia's most advanced state-of-the-art paper machine has started operations and will produce more than 150,000 metric tpy of office paper. This summer the company will start producing 70,000 metric tpy of coated paper, making Ilim Group Russia's first and only producer of this product.
Back To Top
|
International Forest Products Limited (Interfor), Vancouver, B.C., Canada, has completed the acquisition of Rayonier's (Jacksonville, Fla., USA) Wood Products Business in the U.S. South, headquartered in Baxley, Ga. The $80 million acquisition includes three sawmills in Baxley, Swainsboro, and Eatonton, Ga., with a combined annual capacity of 360 million board feet of southern pine dimension lumber. As part of the transaction, Interfor agreed to hire all of the business' current employees.
"The acquisition of Rayonier''s Wood Products Business is a significant strategic move for Interfor," said Duncan Davies, Interfor''s president and CEO. "In addition to providing a footprint in the U.S. South, the acquisition increases Interfor's annual production capacity to more than 2 billion board feet and broadens our product base to include Southern Yellow Pine. I would like to thank the people involved from both Rayonier and Interfor who worked so hard to complete this transaction in such a short period of time," said Davies. "We are looking forward to working with Rayonier to build mutual value as we move ahead."
Back To Top
|
Containerboard/Packaging
A. Merati & C. Cartiera di Laveno, Laveno, Italy, has successfully started up a paperboard machine rebuilt by Andritz, Graz, Austria. Due to the rebuild, the mechanical properties of the board have been improved and the output has been increased, the company reports.
To increase the capacity, Andritz widened the complete wet section, containing the PrimeForm fourdrinier former and PrimePress X shoe press section, by 800 mm. The order included supervision of the wet end rebuild, installation of new framing, rolls, and components for the fourdrinier and the first press, as well as widening of the headbox.
In a second phase, the existing dandy roll will be replaced by a new Andritz PrimeForm HB hybrid former to improve the visual appearance of the board as well as the profiles. The new components have a design speed of 700 m/min at a width at reel of 3,350 mm. Startup is scheduled for this August.
"Our positive experience with Andritz during the successful startup of the shoe press three years ago was decisive for the award of this challenging order for expansion of the wet section," explains Marco Filauro, managing director of A. Merati & C. Cartiera di Laveno. With a production capacity of approximately 400 metric tpd, the Italian family-owned company ranks among Europe's leading core board manufacturers.
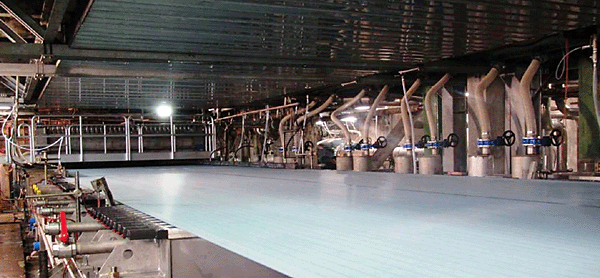
Back To Top
|
The Europac Group, Madrid, Spain, has acquired a corrugated board factory in Caradec, France, for EUR 21.7 million, expected to become effective March 1. The facility produces 100 million cubic meters of recycled corrugated board per year and consumes 60,000 metric tpy of paper. The deal will enable the Europac group to step up board production in France by 28% and to increase its vertical integration. With this acquisition, the degree of integration between paper and board in the French market will rise from 67% to 88%.
José Miguel Isidro, chairman of the Europac Group, said that "this acquisition falls under the umbrella of the Group's strategic targets for the French market, where we command a share of the packaging segment of 7.4%".
The factory is located in Brittany and its integration into the Europac Group's organizational structure will consolidate the company's position in Western France, which represents one-third of the French packaging market.
This transaction follows the acquisition of SCA Packaging by DS Smith, which the European anti-trust authorities had made conditional upon the sale of the Caradec corrugated board factory in Western France, among others.
The integration of this facility into the Europac Group will enable the company to consolidate its position as a benchmark supplier to the France market, Europe's third-largest market by sales volumes and Europac's largest. The deal will extend the company's sales reach in Brittany and boost cooperation with French and international customers.
The Europac Group entered the French market in 2008. It currently produces 280,000 metric tons of recycled paper and 360 million cubic meters of corrugated board annually. Accordingly, the addition of this new facility will boost board production to 460 million cubic meters per year, making Europac the fourth-largest packaging producer in France.
Back To Top
|
Nonwovens
A new version of Fibertect®, a nonwoven decontamination wipe created by researchers at Texas Tech University, Lubbock, Texas, USA, has proved itself more viable at cleaning up a nerve chemical surrogate than the decontamination substance currently used by the U.S. Department of Defense (DoD), which is currently being phased out. Seshadri Ramkumar, lead investigator on the project and inventor of Fibertect, said that when compared with the powdered decontaminant called M-291, the all-cotton version of nonwoven wipe paired with an activated carbon center cleaned up not only the chemical surrogate to the nerve gas soman, but also adsorbed its vapors five times better.
The results were published in the peer-reviewed Journal of Engineered Fibers & Fabrics, by INDA – Association of the Nonwoven Fabrics Industry. Experiments in the research were conducted by Utkarsh Sata, a co-investigator on the project.
"The basic structure is still Fibertect," Ramkumar said. "This is an improved reiteration of Fibertect. This is just two nonwoven cotton layers with the carbon in between. The cotton composite takes liquid up very quickly and can adsorb vapors more efficiently than the powdered decontaminant."
Part of the added benefit of this new Fibertect is that it contains biodegradable cotton, Ramkumar said. A problem with the powdery form is that it leaves dirty residue.
"That is why the U.S. Department of Defense wants to get away from the powdery form," he said. "Fibertect is a fabric. It is skin-friendly. When it comes to adsorbing the surrogate nerve agent's vapors, it just works better. So the powdered decontaminant will be phased out."
In 2005, Ramkumar and his team at the Institute of Environmental and Human Health (TIEHH) at Texas Tech studied the absorbent capabilities of cotton to create the Fibertect wipe that can adsorb and neutralize gases and liquids that might be used in chemical warfare.
"Fibertect contributes to our national security and helps with the safety of our first responders," Sata said.
The process to make Fibertect has received a patent and has been validated for use as a low-cost decontamination wipe for the U.S. military and the Department of Homeland Security. Also, the wipe's qualities were re-engineered to create a better absorbent material to pick up the oil slicks inundating Gulf Coast beaches following the Deepwater Horizon disaster in 2010.
Ron Kendall, a co-investigator on the project, said the creation of Fibertect began as a need to develop a decontamination wipe system for the human skin, which was a top priority for the Pentagon at the time. This has resulted now in the invention of Fibertect, a patent, and now commercialization.
"The powdered form is very difficult to handle and to apply toward decontamination purposes," Kendall said. "And it is so much easier to handle and apply toward decontamination needs than M-291 carbon system. We're learning more and more of absorption capabilities of cotton-carbon composite."
Other researchers included Eugene Wilusz of the U.S. Army Natick Soldier RD&E Center, Steve Mlynarek of the University of South Florida, and Gopal Coimbatore of Texas Tech. The research was funded in part by DoD, Cotton Inc., the International Cotton Research Center, Texas Department of Agriculture, Cotton Foundation, and The CH Foundation.
A copy of the research is available online.
Back To Top
|
New Products
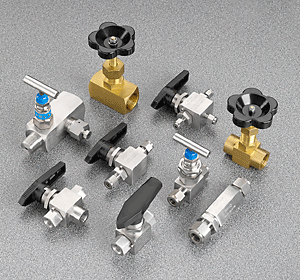 Brennan Industries Inc., Cleveland, Ohio, USA, has expanded its product lines by introducing new compression-end instrumentation valves. The new valves are available with single or double ferrule-style tube fittings and are tested for quality prior to leaving the factory. The new offerings include:
- NVB Series Ball Valves ranging in size from 1/8- to 3/4-in., available in either 316 SS or brass construction. These valves can have two- or three-way configurations and are rated to 3,000 psi.
- NVN-2200 and NVN-2300 Series Screwed Bonnet Needle Valves ranging in size from 1/8- to 1-in., available with either metal-to-metal or soft-seat stem types. The 316 SS valves are rated to 6,000 psi and the brass valves are rated to 3,000 psi.
- NVN-2000 and NVN-2100 Series Integral Bonnet Needle Valves ranging in size from 1/8- to 1-in. with metal-to-metal stem types with "V" stem tip form. The 316 SS valves are rated to 6,000 psi and the brass valves are rated to 3,000 psi.
- NVC Series Check Valves ranging in size from 1/8- to 1-in. with O-ring seat seals. The 316 SS valves are rated to 6,000 psi and the brass valves are rated to 3,000 psi.
"Brennan instrumentation valves are constructed and tested to provide the quality products that our customers expect," said Bill Jarrell, vice president of marketing and operations. "The variety of size and material options make it easier to select the right valve for the job."
More information is available online.
Back To Top
|
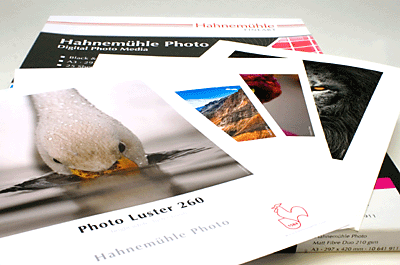 Hahnemuehle, Germany, announced this week that Hahnemuehle Photo is a new product line consisting of two resin-coated papers for photographic inkjet printing. Both are bright white with an extremely large color gamut, and the 290 gsm weight makes it more durable and substantial than other photographic inkjet papers while staying very competitive in price, the company notes. The Hahnemuehle Photo line offers a cost-effective way to produce color and black and white images that are both durable and fade resistant, it adds. The two papers are:
- Photo Luster 290 gsm—bright white, smooth, luster surface with a pearlescent sheen
- Photo Glossy 290 gsm—bright white, super smooth surface, high gloss for a vivid image result.
Both surfaces will be available in 8.5 in. by 11 in., 11 in. by 17 in., 13 in. by 19 in., and 17 in. by 22 in. cut sheets, 25 per box. Both surfaces will be available in 17 in. by 100 ft., 24 in. by 100 ft., and 44 in. by 100 ft. rolls.
Hahnemuehle FineArt GmbH has been producing paper since 1584, thus being one of Germany's oldest paper manufacturers. In addition to the production of traditional artist papers, Hahnemuehle today focuses on producing refined papers for the digital print as well as on the development and production of technical specialty papers for industry and research. The company has some 150 employees worldwide.
Back To Top
|
Published Pricing
Lecta, France, the second largest European coated woodfree (CWF) paper producer, made up of Condat, Cartiere del Garda, and Torraspapel, reports that it will continue implementing the announced price increase of 5% to 6% on its CWF paper in all channels and markets justified by the high level prices of main raw materials, transport, and energy. The company adds that further price increases will be needed this year to recover the minimum profitability that would guarantee quality and service levels. Lecta notes that its sales teams are at its customer's disposal to provide them with any information they may require.
Lecta competes in three businesses. The first Lecta business, and by far the most important, is the manufacture of coated fine paper, with current production capacity of about 1,410,000 tons. The second business is the manufacture of about 200,000 tons of specialty paper and 100,000 tons of base paper. Third, Lecta is a distributor of paper in Iberia, France, and Argentina where it sells around 470,000 tons.
Back To Top
|
Metsä Board, Finland, is raising the prices of all Kemiart white-top kraftliner grades by EUR 50 per metric ton in Europe, the Middle East, and Africa. The price hikes become effective for deliveries beginning April 8.
The company notes that the price increase is needed to counter the effects of a continued rise in production costs.
Back To Top
|
Nippon Paper Industries Co., Japan, this week announced price increases for printing paper in the domestic market to all of its agencies. Products subject to price revisions include woodfree paper, coated woodfree paper, lightweight coated paper, and ultra lightweight coated paper. The increase will be a minimum of 15 Yen/Kg, effective with shipments beginning April 21.
According to Nippon, imported paper volume increased rapidly after the Great East Japan Earthquake, and the fall of the market price continued to drop. Based on rapid earnings deterioration, the company decided that the price had to be corrected to a sustainable level.
Back To Top
|
Södra, Sweden, has raised the price of its softwood pulp to $860 and hardwood pulp to $820 per metric ton in Europe, effective March 1. Seasonal improvement, together with maintenance shutdowns, will improve the market balance further in the spring, the company noted.
Södra is organized into four business areas—Södra Skog (timber raw products, forestry services), Södra Timber (wood products), Södra Cell (paper pulp), Södra Interiör (interior wood products).
Back To Top
|
The Newark Group, Cranford, N.J., USA, this week announced a $40 per ton price increase on all coated grades of recycled paperboard effective with shipments on or after April 2. "The increase is necessary due to the escalating costs of raw materials, freight, and energy," said Raymond Vargo Jr., VP of Sales, Newark Paperboard Mills.
The Newark Group is an integrated producer of 100% recycled paperboard and paperboard products in the U.S. and Canada. The company employs more than 1,500 people and owns 34 facilities.
Back To Top
|
People
Sappi Limited, Johannesburg, South Africa, this week announced that Robert J. DeKoch has joined the board as an independent non-executive director beginning March 1. DeKoch is currently the president and COO of The Boldt Co. in Appleton, Wis., USA.
Prior to joining The Boldt Co., DeKoch served as a production manager and mill manager as well as VP of manufacturing for Appleton Papers (USA). He also served inter alia as technical director of Consolidated Papers (USA).
Dr Danie Cronje, Sappi chairman, said that "Bob DeKoch brings a wealth of experience regarding leadership as well as lean manufacturing to the board. His broad industry experience will also contribute to the board's deliberations. We are pleased to welcome him to the Sappi board."
Back To Top
|
Travels with Larry
What's in your hometown?
I have adopted nine cities in my career in this industry, but my hometown was and remains to be Memphis, Tenn., USA. My town is blessed to have a lot of well know jewels as well as some, not-so-much in the spotlight. Memphis is no stranger to our great industry with the likes of International Paper, Verso Paper, Buckeye, Buckman, Cascades Tissue Group, and Georgia Pacific to name a few.
Recently, I received some bad news that one if my second cousins was spending some time in Le Bonheur Children's Hospital in Memphis. I called and spoke to his dad, my first cousin, to check on them. When I discovered they would be in there for several days, I decided to send a goodie basket to cheer them up a bit and to let them know I was thinking about them.
I went online to search for baskets in the Memphis area. This one store kept popping up, Bella Vita, is located in Collierville, Tenn., a town located right outside of Memphis. Although they had some great choices, I was looking for some snacks, balloons, flowers, and a stuffed animal for this specific occasion.
I did however go on Bella Vita's website and discovered some very unique, creative gifts from several local and regional artists. In addition to all types of products, they also carry many "reclaimed items" that are turned into art. I could not help but notice that several items were made from recycled wood and paper. Curiosity got the best of me and I had to see this place for myself the next time I was in the area. The first thing that caught my eye was the display in the window.
They have Flowers, made from packaging materials contained in the boxes that are shipped to their store, and get this, they are attached to stands made from recycled pallets. For you that know me, I am not a real flowery kind of guy, but this was really cool.
I went inside the store and met the owner, Stephanie Singley, as well as Laurie Losorwith, the artist who made the paper flowers (posing with her creation in the photo at left). They gave their permission for me to take a few photos and tell our readers about this small piece of how our industry touches people's lives in ways we probably never think of.
They also had some "rewind candles" made from old wine bottles that have been cut down to hold candles scented with your favorite wine (not a lot to do with paper but I thought they were cool).
So the next time you think our industry is not creative, just remember that there are those who consider our products a true work of art.
More information about Bella Vita is available online.
More information about TAPPI is also available online.
There are two types of people in this world, TAPPI members and those who should be.
Until next time....................
Larry
Back To Top
|
TAPPI News
TAPPI Annual Business Meeting /Teleconference
TAPPI Headquarters
15 Technology Parkway S., Suite 115
Peachtree Corners, Ga., 30092 USA
March 12, 2013
1:00 pm - 1:30 pm EST
As a corporation, TAPPI must hold an annual Business Meeting. That meeting will be held March 12, 2013, via teleconference. Any interested TAPPI member may join us for a brief report on association business -- Larry N. Montague, TAPPI president and CEO
1. Opening Remarks/Antitrust Reminder - Norman Marsolan, TAPPI Board chair
This call will be held in accordance with TAPPI's Antitrust Policy and Procedures.
TAPPI's aim is to promote research and education, and to arrange for the collection, dissemination, and interchange of technical concepts and information in fields of interest to its members. TAPPI is not intended to, and may not, play any role in the competitive decisions of its members or their employees, or in any way restrict competition among companies.
2. Financial Report - Larry Montague, TAPPI president and CEO
3. Board Transition - Norman Marsolan, TAPPI Board chair, Tom Garland, TAPPI Board vice chair
4. Adjourn - Norman Marsolan, TAPPI Board chair
Please contact Mary Beth Cornell, +1 770-209-7210, for more information, including the teleconference number and password.
Back To Top
|
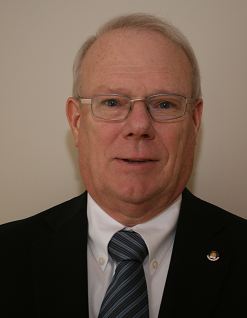
Robert Kinstrey, director, Pulp and Paper Consultancy for Jacobs, has been named recipient of TAPPI's 2013 Herman Joachim Distinguished Service Award. The Award is the highest honor the Association can bestow upon an individual for exemplary leadership that has significantly contributed to the advancement of the Association. It will be presented at the PaperCon 2013 Conference Awards Dinner, Tuesday, April 30, 2013.
"By virtue of the outstanding leadership he has demonstrated in a number of senior positions, Robert Kinstrey has provided great benefit to the Association and its members," according to Larry N. Montague, president and CEO of TAPPI. "During a long and distinguished career, he's led by example and has been an inspiration to everyone he's worked with. I am pleased to be able to honor his outstanding record of service with this prestigious award."
Kinstrey is a TAPPI Fellow and has been an active participant and leader in TAPPI and PIMA for many years. He has served in a wide range of senior roles including TAPPI Foundation Trustee and the TAPPI Board of Directors. He has made or written more than 90 presentations and articles published in numerous industry publications. Kinstrey is a member of the Syracuse Pulp & Paper Foundation where he's served on the Board of Directors and as foundation president. he was awarded the 2008 PIMA/CPBIS Management Excellence Award.
Back To Top
|
Special TAPPI webinar on March 13 provides inside preview of PaperCon 2013 in Atlanta, Ga., USA, April 27 - May 1
Webinar
Increasing Paper Machine Agility with a Novel Grade Change Concept
Wednesday, March 13, 2013 - 12:00pm - 1:00pm EST
Register to attend.
A narrow grade mix and long grade runs were once common. Not today. Most machine make a wider set of products with many grade changes. A new grade transition concept makes such machines more competitive by increasing the stability and agility of the line. Unlike traditional programs, the new grade change concept replies on normal quality controls to move the machine from one grade to the next, quickly and smoothly in a closed loop. Learn more.
Back To Top
|
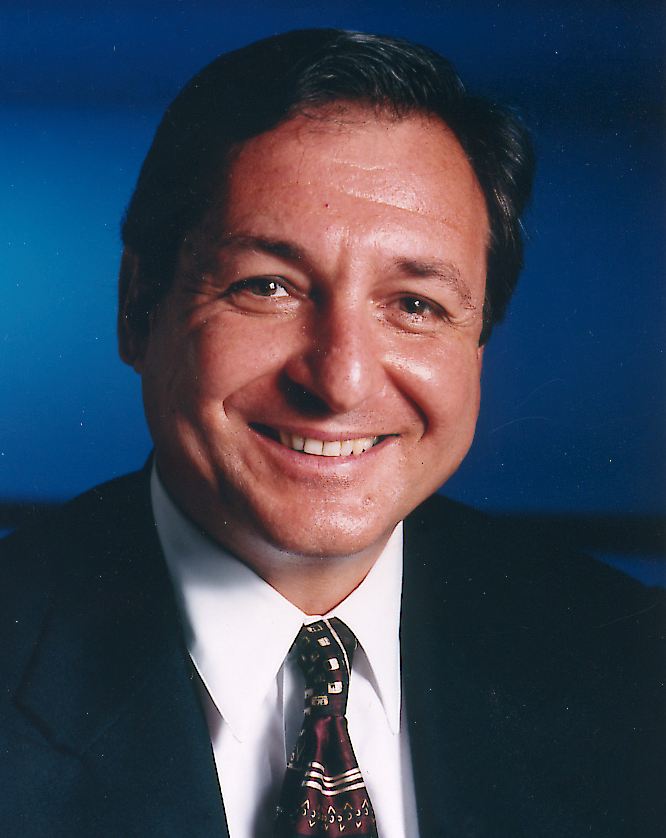
TAPPI member Nick Triantafillopoulos, Ph.D., says he believes strongly in one's "ethical obligation to give back through service," especially to an organization that has played a pivotal role in your career. That's why he has been an active member since 1981 when he was just beginning his pulp and paper career path and eager to make a difference in the industry he loves. "Membership has meant an opportunity to develop not only technical and leadership skills, but also a network of technical experts and friends." This tight-knit relationship with his profession and TAPPI is still going strong.
"Part of engaging in TAPPI is the opportunity to play a leadership role in volunteerism," he said. Besides teaching training courses, organizing symposia, progressing through committee chairs, writing a division newsletter, and editing articles for TAPPI Journal, Nick says helping to execute change in the volunteer programs taught him the inherent challenges and satisfaction of seeing a new, morphed organization created. Find out more by reading this month's Member Spotlight.
Spotlight participants are recommended by fellow members and staff. If you would like to nominate a member just send his or her name (or names) to MemberSpotlight@tappi.org. We will forward a Spotlight Questionnaire to fill out and return.
We look forward to seeing you in the Spotlight!
Back To Top
|
The TAPPI - PPSA Safety Management Leadership course is designed to build leadership commitment and engagement for a culture of safety excellence. This partnership with the Pulp & Paper Safety Association brings you the best safety practices in the industry.
The Safety Management Leadership Course will be held April 10-11, 2013, at the TAPPI Training Facility in Peachtree Corners, near Atlanta, Ga., USA.
This course delivers curriculum to help you learn the fundamentals of record-keeping, incident investigation, risk management, cultivating a safety culture, managing change safely, and measuring performance. Take a look at the expert panel of instructors. The course is designed for anyone that is involved in workplace safety.
Course registration is limited to only 20 participants, so please register today at the course website. TAPPI and PPSA members save, and early registration discounts are available.
Back To Top
|
Tissue360 Forum @ PaperCon 2013
Monday, April 29 - Wednesday, May 1
Atlanta, Ga., USA
TAPPI's new Tissue publication, Tissue360o magazine, and TAPPI tissue experts have organized Tissue360 Forum, a comprehensive technical forum covering all aspects of tissuemaking. You will hear about the latest tissue technology, market trends, and pick-up some runnability/operational tips. The program is open to all full PaperCon registrants.
Program Overview:
Hygenic Products Market Overview
Session Chairs: Ken Patrick, Tissue360o
Chemistry Solutions for Tissue Making
Session Chair: Gary Furman, Nalco
Water and Energy Strategies for Tissue
Session Chair: Tom Jenn, Kimberly-Clark
Premium Tissue Manufacturing Technologies
Session Chair: Soren Eriksson, Metso
Tissue Controls and Measurement
Session Chair: Rene Naranjo, AstenJohnson
Yankee Reliability (CEUs provided)
Session Chair: Al Coons, Clearwater Paper
Converting Efficiencies
Session Chair: Kevin Brennan, Ashland Water Technologies
See the full Tissue360 Forum program.
PaperCon will take place April 27 through May 1, 2013 in Atlanta, Ga., USA. Designed by industry professionals, PaperCon brings together CEOs, mill managers, superintendents, scientsits, process engineers, and suppliers for the largest pulp and paper technical program in the world. No other such event provides such a comprehensive program, networking opportunites, and trade fair among such a distinguished group of industry leaders.
Learn more about PaperCon 2013.
Back To Top
|
The TAPPI Tissue Properties & Manufacturing Course will be held on April 27-28, 2013 in Atlanta, Ga., co-located with PaperCon 2013 and the Tissue Forum. This is a great opportunity to get the most out of your conference experience. This Tissue Properties course is designed for those who desire an introductory-to-intermediate level, comprehensive, and structured course on tissue properties and the effect of manufacturing. The course precedes the Tissue Forum at PaperCon 2013 and is an excellent educational component to these technical sessions.
This course will be particularly helpful to non-technical professionals, technical process engineers, operators, suppliers, converters and marketers with 0-5 years of experience in tissue manufacturing. Go to the course website to learn more.
Back To Top
|
The TAPPI International Best Practices on the Corrugator Seminar will be held April 9-11, 2013, in conjunction with SinoCorrugated 2013 in Shanghai, China. The three-day course features an in-depth technical program designed to teach participants about each element in the corrugating process and how to improve box plant operations and box quality.
The Best Practices on the Corrugator Seminar is an introductory to intermediate level course that teaches participants how to understand each element in the corrugating process and how to run each component with optimum settings for peak performance to increase productivity, improve quality, and minimize waste. Both old and new equipment will be covered. Participants will also develop an understanding of the critical properties of the raw materials that are vital to guarantee acceptable quality board.
Among the key topics to be addressed are: theory of corrugated board production and solutions to common operational problems; distinguishing key features of paperboard/starch adhesive and how to control warp; operating the corrugated production line; controlling and minimizing downtime; maximizing production line efficiency and maintaining quality standards.
Find out more about the Corrugator Best Practices Seminar.
Back To Top
|
The NETInc Innovative Nonwovens Conference, April 29-May1, 2013, in Atlanta, Ga., USA, is the only technical conference developed by engineers and technologists to help you understand the innovation behind the science and how it impacts the world.
Program topics include: Nanotechnology, Binders and Additives, Building Sciences, Health Care and Medical Applications for Nonwovens, Manufacturing Technology, Process Management Technology, and an Intro to Nonwovens Tutorial.
With several focused tracks, NETInc offers peer reviewed papers, expert speakers, and exclusive networking opportunities. NETInc participants can also enjoy the full PaperCon program and exhibits, Tissue360 Forum, RPTA P-T Seminar and the OpEx Reliability Workshop with their registration.
Learn more about NETInc.
Back To Top
|
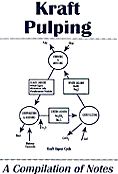
Edited by: A. Mimms, M.J. Kocurek, J.A. Pyatte, and E.E. Wright
Liberally illustrated with more than 130 diagrams and photographs, this book includes basic formulas and diagrams to explain the structure of wood, variables affecting the quality and handling of wood chips, pulping chemistry and equipment, the pulping process, and black liquor recovery. It includes a glossary of frequently used terms. Kraft Pulping.
View the Table of Contents
Preview Sample Pages
Product code: 0101R171
Member Price: $58.00
Non-Member Price: $87.00
Back To Top
|
Paper Roll Damage Expensive?
Attend TAPPI's SRW Workshop this April and be a part of this dedicated group of mills, carriers, warehouses and printers as they collaborate to reduce in-transit damage to rolls of paper.
The Shipping, Receiving and Warehousing Workshop is an affordable working meeting with presentations and collaborative discussions, engaging keynote speakers, and great opportunities for networking. It's something you can't afford to miss.
Why attend?
- Keynote Presentation by Dave Schirmer, Vice President and General Manager of Hearst Enterprises responsible for paper procurement for divisions of The Hearst Corporation.
- Presentations provided by experts from the class 1 railroads, intermodal providers, warehouses, shippers and dunnage manufacturers with extensive experience and practical background knowledge.
- Practical information sharing by all parties in the paper manufacturing supply chain in an interactive environment
- Excellent networking opportunity - paper buyers, paper companies, carriers, securing / damage prevention specialists, block and bracing manufacturers, safety experts - all under one roof.
Learn more about the Shipping, Receiving and Warehousing Workshop.
Back To Top
|
David Schirmer, Vice President and General Manager of Hearst Enterprises will Keynote at Tappi's Shipping Receiving and Warehousing Workshop this April in Nashville. Schirmer is responsible for paper procurement for divisions of Hearst Corp. including Hearst Magazines and Hearst Newspapers and is one of principles of Newsprint Purchasing LLC.
Tappi's SRW Workshop, taking place April 9-10, focuses on reducing in-transit paper roll damage through collaborative discussions and best practices. Learn more about SRW.
Back To Top
|
Strengthen your understanding of the corrugating process, and linerboard and medium performance properties and manufacture with TAPPI's Linerboard Medium & Corrugated Box Manufacture Course, April 15-16, at the Holiday Inn in Neenah, Wis., USA.
With an emphasis on helping attendees improve corrugating box performance and runnability, this popular introductory to intermediate level course is ideal for process engineers and operators in linerboard and medium manufacturing facilities and corrugating and converting plants.
Instructors Michael J. Kocurek, Professor Emeritus, of Paper Science & Engineering at North Carolina State University, and Jon Porter, Senior Trainer / Process Specialist for Fosber America will address:
- The Corrugated Session (1/2 day) will cover how to achieve the strongest bond and highest quality combinerboard. You'll learn about (1) the equipment, (2) starch, (3) corrugated process technology, and (4) importance of linerboard and medium properties and runnability.
- The Properties and Testing of Liner and Medium session (1/2 day) covers the tests, what they mean, and how the properties of the board affect the tests.
- The Pulp and Paper Mill Operations session (1 day) will cover the technology of the pulp and papermaking processes, and how they affect the quality, properties, tests, and runnability of the liner and medium.
View the proposed course schedule.
Register by March 15 to take advantage of the Early Bird registration discount. Join TAPPI or renew your membership for the best rates!
Back To Top
|
The TAPPI Troubleshooting "Flexos" and "Die Cutters" Sustain Board Caliper & Improve Printing Course is scheduled for April 16-18, 2013, in Neenah, Wis., USA. Join industry veteran Dick Target, founder of On Target Consultants, as he helps attendees identify and address downtime issues and develop a better understanding of machine calibration and how to maintain proper board caliper during the converting process.
Target will use an easy to understand format to help attendees improve the basic manufacturing process. Topics will include: methods to minimize caliper loss in the converting process; one-box set-up techniques; and waste reduction techniques. View the course schedule.
Take advantage of the Early Bird Registration discount before March 16. Join TAPPI or renew your membership for the best rates!
Back To Top
|
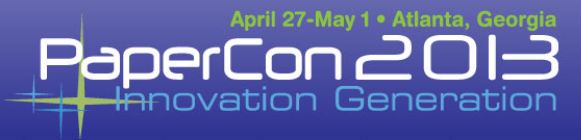
The highly-regarded Executive Panel on Monday, April 29, will illuminate how industry leaders are thinking and driving innovation in their companies.
See who's speaking.
Designed by industry professionals, PaperCon (April 27 - May 1 in Atlanta, Ga., USA) will bring together CEOs, mill managers, superintendents, scientists, process engineers, and suppliers for the largest pulp and paper technical program in the world. No other event provides such a comprehensive program with networking opportunities and trade fair among such a distinguished group of industry leaders.
Back To Top
|
PaperCon Session: Insights into Effective Labor/Management Relationships
Organized by PPMA and PIMA
Monday, April 29, 2013 - 1:30-3:00pm
Many companies have embraced innovative processes for managing labor-management relationships. These processes result in better communication, more effective problem solving, and alignment around shared business goals. Attend this session at PaperCon, part of the PIMA Management Program, and hear examples of effective labor/management teams that yield positive business results. Panelists will share first-person testimonials and stories of challenge, frustration, and success.
Moderator:
Roger Hagan, Zilkha Biomass Energy
Panelists:
Steve Myers, mill manager, Thilmany Paper, Kaukauna, Wis.
Peter Tantalo, operations manager, RockTenn Solvay, Syracuse, N.Y.
Mike Rayome, director, human resources, Graphic Packaging, Wausau, Wis.
Karl Christianson, mill manager, RockTenn, Stevenson, Ala.
PaperCon will take place April 27 through May 1, 2013, in Atlanta, Ga, USA. Designed by industry professionals, PaperCon brings together CEOs, mill managers, superintendents, scientists, process engineers, and suppliers for the largest pulp and paper technical program in the world. No other event provides such a comprehensive program, networking opportunities, and trade fair among such a distinguished group of industry leaders.
Learn more about PaperCon 2013.
Back To Top
|
PaperCon Programs Now Available
Customize your learning and networking experience at PaperCon to best fit your professional needs. Bring back ideas, innovation that will help you be more effective and efficient.
Papermakers program will give you everything you need to know about paper machine performance evaluations, running mill trials, and product certification.
Eight peer-reviewed Coating sessions focus on scientific developments and practical tips. Highlighs include opacity enhancement with Ti02 and advancements in barrier coating.
PIMA Management sessions provide excellent insight for mill managers, production managers, and executives. This year's sessions will help you develop effective labor/management relationships and show you how to motivate today's employees.
The Tissue360 Forum provides a comprehensive peer-reviewed technical program unlike any other. You will learn about fiber, water, and energy savings, the latest softness and strength additives, and forming concepts.
The OpEx Reliability Workshop will help you improve reliability and maintenance in your mill. Operator driven reliability, alignment, education, and mill processes will be addressed by leading reliability experts.
The Young Professionals Program (YP) offers those new to the industry an unbelievable opportunity to gain basic industry knowledge and meet experienced industry leaders.
Back To Top
|
The highly regarded panel on Monday, April 29, will illuminate how industry leaders are thinking and driving innovation within their companies.
See who's speaking.
Designed by industry professionals, PaperCon will bring together CEOs, mill managers, superintendents, scientists, process engineers, and suppliers for the largest pulp and paper technical program in the world. No other event provides such a comprehensive program, networking opportunities, and trade fair among such a distinguished group of industry leaders.
Back To Top
|
The Introduction to Traditional and Emerging Printing Technology Course will be co-located at the 2013 PaperCon Conference, April 27-29, 2013, in Atlanta, Ga., USA.
This is an introductory course on printing methods and applications, designed for those who need to understand print quality, attend print trials, trouble shoot print problems or are generally new to printing operations. It will be taught by printing experts from TAPPI's Coating and Graphic Arts Division and is an excellent complement to the Coating Program at PaperCon.
As an added bonus, the course will include a tour of Hewlett-Packard's new state-of-the art facility where production laser and inkjet presses will be demonstrated.
Course attendees may also join the Coating and Graphic Arts Opening Session where printing visionary Frank Romano is giving the keynote address. Learn more and register online.
Back To Top
|
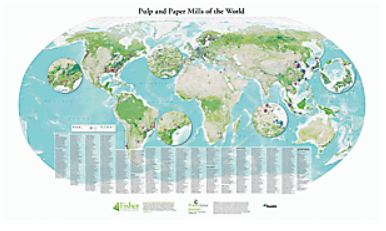
One of TAPPI's most exciting new products is the wall-sized, laminated 2013 Pulp & Paper "Mills of the World" Map.
A winning combination of high quality print and paper stock along with brilliant colors makes this the perfect map to frame and hang in your office. The "Mills of the World" map features include:
- Every mill in the world producing 50 tpd or more
- Major greenfield projects
- Design elements showing mill characteristics, forest cover, and typography
- 3 ft. x 5 ft. (or 0.99 x 1.5 meters) .
Each map will be shipped in a protective tube, ready for display.
Don't miss out on this popular item. Order your Pulp & Paper "Mills of the World" Map today.
Product code: 12PPMAP
Member Price: $299.00
Non-Member Price: $319.00
Back To Top
|
By: Jerome M. Gess and Paul H. Wilson
This book takes the reader through the process of making paper, pointing out where interruptions can occur and where elements added to the system can cause problems in that part or subsequent parts of the papermaking process. The aim of this book is to give papermakers and those involved in the papermaking process the information required to allow them to understand how to track down and solve problems at their source rather than where the problems surface.
Troubleshooting the Papermaking Process.
View the Table of Contents.
Product Code: 0101R298
Member Price: $106.00
Non-member Price: $161.00
Back To Top
|
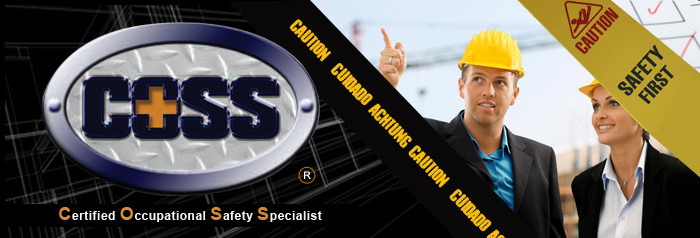
Are you ready to go further, faster in your safety career? The Certified Occupational Safety Specialist (COSS) class can take you there.
The COSS Class is Unique
Not only will you learn how to read and understand the OSHA 1910 and 1926 CFRs and help your company avoid OSHA citations that cost millions of dollars, but more importantly, by learning how to work safely on a job site, you can teach your company how to lower fatalities and near misses. Almost 47% of COSS graduates responding to our survey indicate that, since taking COSS, their company's injury rate and/or OSHA recordables have decreased by as much as 25% and others attest to as much as a 100% decrease!
Request a Course Outline & Syllabus for more information.
The class also addresses the psychology of safety, the true cost of an accident, hazard recognition, how to start up a health and safety program, behavior based safety, system safety, and much more!
What Will You Receive?
Upon successfully completing the class, you will obtain your national Certified Occupational Safety Specialist (COSS) designation, your OSHA 10-hr. card of completion in construction, and your OSHA 10-hr. card of completion in general industry.
National Program Recognitions
COSS is currently one of only 37 programs in the world recongnized and accredited by the American Petroleum Institute (API). In addition, the certifying body for construction education for colleges, universties and technical/trade schools, American Council for Construction Education (ACCE), has also recongnized our program. COSS is the only non-degree program to receive this national endorsement. Lastly, COSS has been established as a mandatory course for students in the Construction Management Program at Louisiana State University.
Program Content
The program consists of 40 hr. of hands on, face-to-face learning, which is delivered by an Authorized OSHA outreach trainer in both construction and general industry. Case studies and workshops are used extensively to bring learning objectives into focus. Guest speaker from areas such as OSHA and other governmental agencies are used to enhance the learning experience. Student presentations, daily quizzes, practical reviews, and a comprehensive final exam will allow you to demonstrate your competency.
Prerequisites
The only prerequisite for the COSS class is you must have a high school diploma or equivalent. In each class, we tend to have a mix of non-experienced, first time safety persons, as well as safety professionals who have been in the safety field for 20+ years. But, we have learned that regardless of the numbers of years of experience you have in safety, everyone leaves the COSS class with a wealth of knowledge!
Visit the COSS website for FAQs, testimonials and a list of clients that have taken COSS.
Register now.
If you would like more information on the COSS program, contact Beth Gordon at 877-610-2677
Back To Top
|
|
|
TAPPI Over the Wire | 15 Technology Pkwy. S. | Norcross, GA 30092 USA | Voice: 770.446.1400 | Fax: 770.446.6947
|
 |