 |
|
Weekly Spotlight
Domtar Corp., Montréal, Qué., Canada, this week reported that it will sell its Ariva business in the U.S. to privately-held Central National-Gottesman Inc
Learn More...
|
KapStone Paper and Packaging Corp., Northbrook, Ill., USA, this week reported that it has completed the stock purchase of Longview Fibre Paper and Packaging, Inc., Longview, Wash.
Learn More...
|
Stora Enso, Helsinki, Finland, has decided to invest EUR 32 million in building a world-class biorefinery at Sunila Mill in Finland, which will reduce carbon dioxide emissions of the mill by replacing up to 90% of natural gas by lignin extracted from the black liquor
Learn More...
|
Resolute Forest Products Inc., Montréal, Qué., Canada, has offered the municipality of Lac-Mégantic a significant volume of lumber to help rebuild the downtown core that was devastated by the recent train derailment and explosion
Learn More...
|
Georgia-Pacific, Atlanta, Ga., USA, this past week completed the acquisition of the Temple-Inland Building Products assets from International Paper Co., Memphis, Tenn., after receiving clearance from the Department of Justice under the Hart-Scott-Rodino merger review process
Learn More...
|
Market Roundup
Total U.S. boxboard production this past June increased by 0.7% compared with June 2012, but decreased 0.3% from May
Learn More...
|
Total U.S. kraft paper shipments were 131,400 tons in June, an increase of 2.3% compared with the prior month
Learn More...
|
Containerboard production in the U.S in June fell 2.2% from May 2013, but rose 3.8% over the same month last year
Learn More...
|
Pulp & Paper
BillerudKorsnäs, Solna, Sweden, this week reported that it is already half way toward realizing its synergy target, following the merger of Billerud and Korsnäs earlier this year
Learn More...
|
Boise Cascade Co., Boise, Idaho, USA, has agreed to purchase Wood Resources LLC's (Shelton, Wash.) Southeast operations, which include Chester Wood Products and Moncure Plywood
Learn More...
|
The new line will have a maximum production capacity of 110 metric tpd
Learn More...
|
Kemira, Finland, has completed the expansion of its hydrogen peroxide plant in Fray Bentos, Uruguay
Learn More...
|
Oji Papéis Especiais, Brazil, has ordered from Voith (Germany) a new lubrication system for suction roll sealing strips – HydroSeal
Learn More...
|
UPM, Helsinki, Finland, reports that it is proceeding with the schedule announced in January 2013 to find buyers for itsDocelles paper mill and its Aigrefeuille further processing mill in France
Learn More...
|
Containerboard/Packaging
James Cropper Plc, U.K., this week unveiled a new facility to recycle disposable coffee cups as high-quality paper products
Learn More...
|
SiHai Paper Co, Fuzhou, JiangXi province in China, has ordered from SinoCPMC (China), and PMT Italia (Italy) a new linerboard machine
Learn More...
|
Stora Enso, Helsinki, Finland, reports that it has received project approval for its integrated pulp and board project in Guangxi, southern China, from the Chinese National Development and Reform Commission (NDRC)
Learn More...
|
Thimm Display, Wörrstadt, Rhineland-Palatinate, Germany, has taken over the operations of Hohendahl Wellkarton GmbH, Essen, Germany
Learn More...
|
|
New Products
Brennen Industries Inc., Cleveland, Ohio, USA, an international supplier of hydraulic fittings and adapters, has introduced a new instrumentation catalog for its complete line of instrumentation fittings
Learn More...
|
To minimize downtime, ROTEX, Cincinnati, Ohio, USA, announced that it is now offering Express Part Service, ensuring that all in-stock parts orders received by 1:30 p.m. ET, Monday through Friday, will receive same-day shipping from strategic distribution centers located worldwide
Learn More...
|
Toyota Material handling, USA Inc. (TMHU), Irvine, Calif., USA, this week unveiled its new 8-Series lift trucks designed to meet applications associated with the pulp and paper industry
Learn More...
|
Verso Paper Corp., Memphis, Tenn., USA, has launched a new pharmaceutical insert grade known as VersoRx™
Learn More...
|
West Salem Machinery, Salem, Ore., USA, this week announced a new screening design called the Waterfall™ Disc Screen
Learn More...
|
People
Precision Roll Grinders, Allentown, Pa., USA, has named Chad Bailey account manager, serving customers in the Ohio, Indiana, and Michigan territory
Learn More...
|
Sonoco, Hartsville, S.C., USA, this week announced that Harry A. Cockrell has been elected to its board of directors
Learn More...
|
Timo Salonen, CFO and a long-term member of the executive team of Huhtamaki Group, Espoo, Finland, has decided to leave the company at his own request
Learn More...
|
Weyerhaeuser Co., Federal Way, Wash., USA, reports that its board of directors has elected Devin Stockfish corporate secretary for the company
Learn More...
|
He will be part of Södra's group executive team, reporting to CEO and Group President Lars Idermark
Learn More...
|
TAPPI News
Larry N. Montague, TAPPI president and CEO, has been named to the 2013 RISI Power List of the most influential leaders in the global pulp and paper industry.
Learn More...
|
Nominations for the major TAPPI 2014 awards are due by August 1, 2013.
Learn More...
|
The TAPPI/PPSA Safety Management Leadership Course will be held August 26-27 in Metro Atlanta, Ga., USA. This course sold out in 2012 and course registration is limited to 30 participants.
Learn More...
|
The 2014 PLACE Technical Program Team is actively seeking technical presentations, panels, tutorials, roundtables and case studies from the packaging and academic community to be presented at this year's conference. Extended abstracts will be accepted anytime before August 1.
Learn More...
|
IEEE Spectrum author and noted researcher Dr. Andrew Steckl will provide the opening presentation at the upcoming "Building Electronics on Paper" Workshop August 6-7.
Learn More...
|
August 13th is the annual golf outing at Mid-Vallee Country Club in De Pere, Wis. August 27th PIMA will hold it's Golf Outing at Grand View Lodge of Pequot Lakes, Minn.
Learn More...
|
This 1.5-day combination of demonstrations, presentations, and networking features industry and academic experts explaining the dynamics of printing electronic circuitry on paper.
Learn More...
|
With only 25 seats left, register now to reserve your spot.
Learn More...
|
The TAPPI International Research Management Committee requests nominations to be submitted for the Research and Development Technical Award and the William H. Aiken Prize by August 31.
Learn More...
|
The TAPPI Improving Paper Machine Performance Course, August 20-22, will allow students to see real world examples of paper mills that have made major improvements in overall efficiency by implementing many small improvements across their operation.
Learn More...
|
The schedule for this course, September 17-18, is packed into just two efficiently planned days so that participants get loads of skill and experience without much time away from their own operations.
Learn More...
|
Authors presenting papers at conferences, experts with significant industry findings, and students or professors reporting academic research − any authors performing relevant industry research − are encouraged to submit their manuscripts.
Learn More...
|
Anyone working in the nanomaterials field, or needing to understand the production and standards of the field, will want to add the soon-to-be-published "Production and Applications of Cellulose Nanomaterials" to their reference material.
Learn More...
|
The Building Sciences Committee Fall Meeting will be September 18-20 at The Hilton Marco Island Beach Resort in Marco Island, Fla.
Learn More...
|
Join more than 7,000 TAPPI members across the world with 650-plus years of industry experience.
Learn More...
|
September event also co-located with Research Forum on Recycling and International Bioenergy and Bioproducts Conference.
Learn More...
|
TAPPI CorrExpo 2013, October 7-9, will be held at the JW Marriott in Indianapolis, Ind., USA, and will feature the classic golf tournment as well as an evening gala at the Indianapolis Motor Speedway.
Learn More...
|
This once-in-a-lifetime event will expand public awareness, foster further connection, and provide outstanding opportunities for collaboration, growth, and investment in our future for all of those involved.
Learn More...
|
As TAPPI's 100th year approaches, we are looking for donations to the TAPPI Library.
Learn More...
|
|
Find us on Facebook
Network with us on LinkedIn
Follow us on Twitter
|
Weekly Spotlight
Domtar Corp., Montréal, Qué., Canada, this week reported that it will sell its Ariva business in the U.S. to privately-held Central National-Gottesman Inc., Purchase, N.Y. Ariva, Covington, Ky., is a network of strategically located paper and printing supplies distribution facilities. The business will be integrated into Lindenmeyr Munroe, a division of Central National-Gottesman. The transaction is expected to close at the end of this month, subject to customary closing conditions.
"Our employees' efforts to adjust to a rapidly changing printing industry are commendable and I am appreciative of their dedication over the years," said John D. Williams, president and CEO of Domtar. "Today's decision to rationalize and sell the business represents the best alternative for our shareholders and the agreement with Lindenmeyr, a well-established and long-time valued business partner of Domtar, will assure business continuity for customers. Lindenmeyr has committed to quickly assess its business requirements and this will provide employment opportunities for Ariva's employees."
In a subsequent transaction that Domtar is not party to, immediately following the closing of the sale, Central National-Gottesman has agreed to sell the U.S. Midwest portion of the Ariva business to The Millcraft Paper Co. a family-run paper merchant based in Cleveland, Ohio.
Ariva has approximately 400 employees in the U.S. It operates from 15 locations in the U.S. across eight states in the Northeast and Midwest regions. Domtar will take proper measures to assist the employees affected by the transaction in accordance with its policies.
Ariva's Canadian operations are not affected by the transaction. The Canadian operations will be consolidated into Domtar's Pulp and Paper Division as they had been historically, upon closing of the transaction.
Domtar produces a wide variety of fiber-based products including communication papers, specialty and packaging papers, and absorbent hygiene products. The foundation of its business is a network of world class wood fiber converting assets that produce paper grade, fluff, and specialty pulps. The majority of its pulp production is consumed internally to manufacture paper and consumer products. Domtar is the largest integrated marketer of uncoated freesheet paper in North America. It also produces a complete line of incontinence care products as well as baby diapers. The company employs approximately 9,800 people.
Central National-Gottesman is an international marketer of pulp and paper. The company has sales offices in 28 U.S. cities and 23 countries worldwide. It operates several divisions, including its U.S. Distribution Division, the largest independent paper merchant in the U.S., comprised of Lindenmeyr, Spicers Paper, Inc., Kelly Paper Co., and Central National, a global provider of pulp, paper, and packaging. The company's sales of pulp and paper exceed $4 billion annually.
Back To Top
|
KapStone Paper and Packaging Corp., Northbrook, Ill., USA, this week reported that it has completed the stock purchase of Longview Fibre Paper and Packaging, Inc., Longview, Wash. Longview is a producer of containerboard, lightweight high performance multiwall paper, specialty kraft papers, and corrugated products. The company employs about 1,800 people.
"Today we are welcoming Longview's team as the newest members of KapStone," said Roger W. Stone, chairman and CEO. "The Longview team orchestrated a transformation that is truly, in my experience, the most amazing that I've actually ever seen in my 55 years in the industry. We're thrilled and delighted to officially have them with us."
Matt Kaplan, KapStone's president and COO, noted that "Longview continues to demonstrate its excellence by delivering outstanding results. In the second quarter, Longview's revenues and adjusted EBITDA of $228 million and $49 million, respectively, yielded an adjusted EBITDA margin of 20.7%, one of the best in the industry. Even more notable was that they achieved these results despite incurring $4.3 million of expense for their once every five year planned mill maintenance outage performed in April. June was particularly strong as adjusted EBITDA for the month exceeded $19 million benefitting from the partial implementation in the quarter of the $50 per ton containerboard and associated box price increases."
Funding for the acquisition came from borrowings under the $1.675 billion amended and restated senior secured credit facility led by Bank of America, Barclays Bank, and Well Fargo Bank. The amended facility now consists of Term Loan A-1 of $805 million maturing over five years, Term Loan A-2 of $470 million maturing over seven years with 1% amortization in each of the first six years with the remaining principal due at the end of year seven, and a $400 million revolving credit facility. The initial blended interest rate will be 2.6% as determined from the LIBOR based pricing grid, and the rate is subject to change over the life of the loans as LIBOR rates and KapStone's debt to EBITDA ratio change.
Under the terms of Longview's existing $480 million, 8% senior secured notes, current note holders will be notified shortly regarding redemption of the notes, including a 4% change of control penalty. The redemption is expected to take 30 days.
KapStone is a producer of containerboard, unbleached kraft paper products, and corrugated products. The company operates four paper mills and 22 converting plants throughout the U.S. It employs some 4,500 people.
Back To Top
|
Stora Enso, Helsinki, Finland, has decided to invest EUR 32 million in building a world-class biorefinery at Sunila Mill in Finland, which will reduce carbon dioxide emissions of the mill by replacing up to 90% of natural gas by lignin extracted from the black liquor. This will be the first step towards a new business selling lignin to external customers. It will enable global specialty chemical and high-tech material customers to replace fossil raw materials with renewable alternatives. Stora Enso is developing new applications in which lignin provides added value as a natural polymer.
"The investment in Sunila Mill will accelerate Stora Enso's transformation into a renewable materials company. The first applications will be in, for example, the building, construction, and automotive sectors, where lignin offers sustainable alternatives for phenols in plywood glues and other wood-based panels, and polyols used in foams. Other applications are also under development, thus creating a solid platform for growth for sustainable alternatives to fossil-based products," says Juan Bueno, EVP, Stora Enso Biomaterials Division.
The investment includes a lignin extraction plant and dryer, lignin dust burners in the lime kilns, and a packing line. Production is scheduled to start up during the first quarter of 2015. The investment is expected to generate annual sales of EUR 80 million in 2017 and over time clearly exceed Stora Enso's ROCE target of 13%. The technology also has the potential for future scalability at other Group pulp mills.
Sunila Mill has an annual capacity of 370,000 metric tons of softwood pulp. The mill employs approximately 230 people.
Back To Top
|
Resolute Forest Products Inc., Montréal, Qué., Canada, has offered the municipality of Lac-Mégantic a significant volume of lumber to help rebuild the downtown core that was devastated by the recent train derailment and explosion. The lumber is valued at C$50,000, and Resolute will work with its partners and the municipality to identify specific projects.
In a letter to Lac-Mégantic Mayor Colette Roy-Laroche, Richard Garneau, president and CEO of Resolute Forest Products, announced the donation to the community for the reconstruction of public and community buildings.
"Despite the days that have passed since this terrible tragedy, we still have difficulty finding the right words and gestures to express our compassion and support for the people of Lac-Mégantic," Garneau said. "As a large company in Québec, we believe we have an important role to play in assisting the community during this difficult time. The people of Lac-Mégantic are in our thoughts."
Resolute has more than 5,000 employees in Québec and more than 8,000 in North America. The company owns or operates more than 40 pulp and paper mills and wood products facilities in the U.S., Canada, and South Korea, and power generation assets in Canada.
Back To Top
|
Georgia-Pacific, Atlanta, Ga., USA, this past week completed the acquisition of the Temple-Inland Building Products assets from International Paper Co., Memphis, Tenn., after receiving clearance from the Department of Justice under the Hart-Scott-Rodino merger review process. The purchase price was $710 million.
The acquisition includes 15 U.S. facilities (five solid wood mills, four particleboard plants, one medium-density fiberboard plant, one fiberboard plant, and four gypsum wallboard plants) with more than 1,800 employees across eight states, including Alabama, Arkansas, Georgia, Louisiana, Oklahoma, Pennsylvania, Tennessee, and Texas. Teams at these facilities manufacture fiberboard, gypsum products, lumber, medium density fiberboard (MDF), and particleboard.
"With the sale final, we are eager to combine our assets into one building products business," said Mark Luetters, EVP–building products. "Temple-Inland brings high-quality assets with teams of talented employees, and we look forward to combining best practices so that we will continue to improve our ability to serve key customers. We highly value our employees and the communities where we operate, and we are committed to a smooth transition."
John Faraci, chairman and CEO, noted that "we are pleased to have closed on this transaction and I would like to acknowledge and thank all of the employees on the building products team for their continued dedication to their customers, safety, and business results during this transition period. We wish the group well in the years ahead."
Back To Top
|
Market Roundup
Total U.S. boxboard production this past June increased by 0.7% compared with June 2012, but decreased 0.3% from May, according to the AF&PA, Washington, D.C., USA, June 2013 Paperboard Statistics Report released this past week. Unbleached kraft boxboard production increased over the same month last year but decreased compared with last month. Total solid bleached boxboard and liner production increased compared with June 2012 and increased compared with last month.
The production of U.S. recycled boxboard increased compared with June 2012 but decreased compared with last month.
Back To Top
|
Total U.S. kraft paper shipments were 131,400 tons in June, an increase of 2.3% compared with the prior month, as reported by the AF&PA (Washington D.C., USA) in its June 2013 Kraft Paper Sector Report. Bleached kraft paper shipments increased year-over-year 5.7%, and the 2.8% year-over-year decline in unbleached kraft paper shipments were enough to bring overall kraft paper shipments down 1.5% year-over-year.
Total month-end inventory increased 0.7% to 71, 200 tons in June 2013 compared with May 2013 month-end inventories.
Back To Top
|
Containerboard production in the U.S in June fell 2.2% from May 2013, but rose 3.8% over the same month last year, according to the AF&PA (Washington, D.C., USA) June 2013 U.S. Containerboard Statistics Report published this week. The month-over-month average daily production increased 1.1%.
The containerboard operating rate for June 2013 gained one point from May 2013, from 98% to 99%.
Back To Top
|
Pulp & Paper
BillerudKorsnäs, Solna, Sweden, this week reported that it is already half way toward realizing its synergy target, following the merger of Billerud and Korsnäs earlier this year. The company says it is increasing value in the form of brand-strengthening, productivity-boosting, and environment-enhancing packaging solutions. Among the top global producers of primary fiber-based packaging paper, the company has annual sales of around SEK 20 billion.
Updating performance during the second quarter of this year, CEO Per Lindberg said that "we continue to focus on integration and to create the new BillerudKorsnäs. I am therefore first and foremost very pleased to see that we have realized synergies corresponding to an annual pace of approximately SEK 260 million, which takes us almost half way to our target of SEK 530 million. This means that integration is making good progress. We have also received approval from the EU Commission to sell PM 2 in Gävle to SwedPaper and we expect closing on August 1, thus fulfilling the formal requirements from the authorities concerning our acquisition of Korsnäs.
As reported earlier, the company's adjusted operating profit for the second quarter of SEK 318 million fell short of expectations primarily due to startup problems after the rebuild of the board machine KM 5 in Frövi. The cost for the rebuild became almost SEK 50 million higher than expected, but the company noted that it is not uncommon that this happens in connection with such a large remodeling. "We now have created a platform for higher capacity and increased quality. I am also pleased to see that production now has stabilized and is in line with expectations," Lindberg said.
"We have noted varying market conditions during the second quarter. In short, the European demand in some segments is still treading water, which in combination with overcapacity is putting pressure on some European segments. We will therefore actively pursue sales outside of Europe in the medium-to-long-term.
"During the quarter, our new communication platform was launched. We view ourselves as challengers, where we challenge conventional packaging for a sustainable future. Our target remains to deliver smarter packaging, both through better materials as well as better solutions. Smarter packaging adds value at every step of the value chain; attracting consumers, increasing productivity, lowering cost of transportation, reducing waste, and not the least lowering environmental impact.
"We therefore continue to be very optimistic about the future prospects for BillerudKorsnäs. We will share more of our views at our Capital Markets Day planned for November 14 in Stockholm," Lindberg concluded.
Back To Top
|
Boise Cascade Co., Boise, Idaho, USA, has agreed to purchase Wood Resources LLC's (Shelton, Wash.) Southeast operations, which include Chester Wood Products and Moncure Plywood. The sale is expected to be completed in the third quarter.
Chester Wood Products, based in Chester, S.C., produces softwood plywood panels and veneer for a variety of end markets. Moncure Plywood, based in Moncure, N.C., is a flexible specialty plywood mill that produces both hardwood and softwood panels.
In 2004, Wood Resources, an operating unit of Greenwich, Conn.-based Atlas Holdings LLC, acquired Chester and Moncure from Weyerhaeuser Corp. amid uncertainty about both mills' futures in an industry undergoing significant consolidation.
Back To Top
|
Grigiskes AB, Lithuania, has ordered from Toscotec, Italy, a new tissue line. The new line will have a maximum production capacity of 110 metric tpd.
Grigiskes is Lithuania's only producer of tissue products, having worked in this type of business for 190 years. The company is a leading regional player in pulp and paper, packaging, and wood industries, employing around 900 people, with a yearly turnover of some EUR 84 million.
The new Toscotec's line includes an AHEAD-1.5S crescent former tissue machine with a single-layer headbox, single press configuration, a steel yankee dryer (TT SYD-15FT), machine auxiliaries including vacuum pumps, stock preparation plant for virgin pulp, and electrification and control system. Milltech, a Toscotec associate, also will be involved in the project, providing a natural gas heated hood with three stages of heat recovery, machine dust and mist removal system, and a hall ventilation system. A two-unwind-stand tissue slitter-rewinder (TT WIND-M) and an automatic roll handling system complete the supply.
The machine design speed is 1,900 m/min. with a net web width of 2,750 mm. The project will be managed by Toscotec on an EPC (engineering and procurement) basis.
Grigiskes has been in operation since 1823, when the first paper mill was founded in Kuckuriskes that later was incorporated into the Grigiskes Group. Over many years, the company expanded and grew into the biggest pulp and paper producer in the Baltic Region. Today, Grigiskes Paper Mill is a private company belonging to the Grigiskes AB Group, operating three paper machines with an annual tissue paper capacity of 28,000 metric tons.
Grigiskes owns the brands called Grite and Grite Professional. Today, Grite is a well known brand not only in the Lithuanian market, but in all of the surrounding countries as well. Grite has a wide variety of consumer hygienic paper and away-from-home products, including toilet paper, towels, napkins, handkerchiefs, folded towels, wiping paper, etc. With a market share of 41% for toilet paper and 33% for kitchen towels in Lithuania, this company exports more than 60% of production to 22 countries worldwide.
In early 2011, the company had modernized the dry section of existing TM 5 with the installation of a Toscotec steel yankee dryer (TT SYD-4200MM). The project was successful, with 25% energy savings and 40% capacity increase. The good cooperation between the two companies has driven the decision to continue with this new order.
Back To Top
|
Kemira, Finland, has completed the expansion of its hydrogen peroxide plant in Fray Bentos, Uruguay. Hydrogen peroxide is produced in one of the most modern chemical islands built and operated by Kemira since 2007. The expansion was planned since the beginning of the operation in 2005, and the project was carried out from April 2012 to June 2013.
"We finalized the expansion in the planned schedule and the capacity was increased by 65%, which allows us to serve the growing demand of the product in the regional pulp market," said Pedro Cirillo, director of Kemira Uruguay.
"This investment is well aligned with Kemira's strategy to grow in pulp chemicals, in South America," Hilton Casas, president of the Region South America, noted.
Back To Top
|
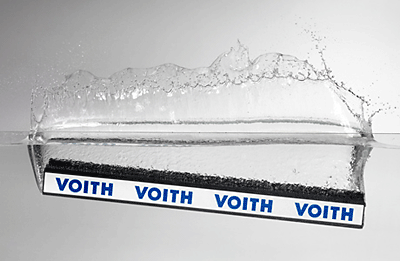 Oji Papéis Especiais, Brazil, has ordered from Voith (Germany) a new lubrication system for suction roll sealing strips – HydroSeal. The HydroSeal system prevents sheet rewetting and drastically reduces water consumption.
Operating in Piracicaba, in the state of São Paulo, Oji's specialty paper mill produces nearly 120,000 metric tpy of thermal paper, carbonless copy paper, and coated paper. The new HydroSeal is expected to become operational in mid-September. Once it is installed, the HydroSeal will allow a considerable decrease in water consumption, as well as a performance improvement in the transfer suction roll operating between the second and third press of the Oji PM 2.
HydroSeal replaces current conventional seals and lubricating showers installed in suction rolls in favor of a more efficient seal system that distributes the lubricant film more evenly over the entire width of the sealing strip, Voith explains. The system thus enables a significant decrease in the amount of water consumed while also minimizing sheet rewetting, which in turn improves the CD moisture profile. This system will allow paper manufacturers to disable conventional shower systems regardless of the suction roll type or manufacturer.
The sealing strip system with integrated water supply enables significant savings, and in some cases may also provide for drive power savings. Trials carried out in Germany demonstrate that by using HydroSeal, papermakers can achieve yearly savings of some EUR 100,000, since water and energy consumption can be reduced by up to 87% and 9% respectively.
As shown in the photo, with the HydroSeal, lubricating water is distributed continuously over the entire width of the sealing strip and thus allows its surface to continuously be covered with a homogeneous film of lubricating water. The efficient feed substantially reduces the amount of lubricating water required. Moreover, this new design prevents remoistening of the paper web and also improves the CD moisture profile.
Since its recent release, nine HydroSeal systems have been sold worldwide, including the one to Oji Papéis Especiais.
With a yearly production capacity of 120,000 metric tons of paper, Oji is a Brazilian and Latin-American leader in the specialty paper segment (thermal and carbonless copy paper), as well as a pioneer in online machine coated paper production. The Oji Paper Group was founded in Japan in 1873, and currently employs more than 26,000 people.
More information about sealing strips with integrated lubrication is available online.
Back To Top
|
UPM, Helsinki, Finland, reports that it is proceeding with the schedule announced in January 2013 to find buyers for itsDocelles paper mill and its Aigrefeuille further processing mill in France. The company has received a conditional offer for the Aigrefeuille mill, but is still working with interested parties to develop a credible offer for the Docelles mill.
"According to the legal process, the Aigrefeuille conditional offer will now be submitted to employee information and consultation. We expect to finalize the process by mid-September," said Anssi Klinga, SVP, UPM Timber.
"As for the UPM Docelles mill, UPM has been conducting an active search for a buyer that could offer a credible future for the mill. Unfortunately the general economic climate in Europe is not favoring our process and it is very challenging to attract investors to new initiatives," Jyrki Ovaska, president of the UPM Paper Business Group, noted.
UPM will continue the sales processes, and at the same time will initiate an employee information and consultation process with the Central Workers' Council of UPM France on two alternatives, i.e. the sale or permanent closure of the two mills. The consultation process will also include functional streamlining measures in France.
UPM said that it is continuing to work closely with the stakeholders to find the best possible solutions for all sites and employees concerned. The mills will continue production until the employee consultation has been concluded. Customer deliveries are not expected to be impacted.
The plan of sale or other exit of the UPM Docelles mill as well as the functional streamlining were originally announced this past January 17. It is part of UPM's plan to adjust its graphic paper capacity and support operations to match the declining demand in Europe.
UPM's plan to sell the Aigrefeuille mill, also announced January 17, follows its 2012 renewed Timber business strategy. UPM develops its sawmills closely integrated with its pulp and paper mills.
Back To Top
|
Containerboard/Packaging
James Cropper Plc, U.K., this week unveiled a new facility to recycle disposable coffee cups as high-quality paper products. The new plant will allow Kendal, England-based James Cropper to recycle 1 billion coffee cups a year to produce packaging and shopping bags for luxury brands such as fashion company Fendi SpA. The facility was formally opened by Queen Elizabeth II in a visit to Cumbria, a non-metropolitan county in northwestern England where the new plant is located.
"Rather than having to buy pulp from overseas, we built this plant to have our own supply," Chairman Mark Cropper said. "We can be more stable in our cost base."
The technology to separate plastic coating from paper fiber may stop 40% of 2.5 billion paper cups from going to landfills or being burned each year in the U.K., the company said. The system may lead to opportunities in parts of the U.S. where packaging products must have a proportion of recycled inputs.
"It's really important for our luxury business that we now have this technology in place," Cropper said. "We can meet the recycling-content need with no decline in quality."
James Cropper exports to more than 50 countries and papermaking accounts for about 70% of its revenue.
Back To Top
|
SiHai Paper Co, Fuzhou, JiangXi province in China, has ordered from SinoCPMC (China), and PMT Italia (Italy) a new linerboard machine. China Paper Machinery Corp., part of the Sinolight Corp., selected PMT Italia as its partner to supply the new liner machine.
PMT Italia will supply the dilution headbox ÆGO™ Stream S, the shoe press ÆGO™FLX Shoe, ÆGO™FLX Counter Roll, as well as additional engineering related to other parts. CPMC will engineer the remaining parts of the project and manufacture them at its new plant in China.
PMT and CPMC have assigned a specific team made by Italian and Chinese engineers to work together with SiHia Paper papermakers.
The project consist of a Greenfield, 6.2 meter machine to produce test liner and fluting from recycled fibers. Paper machine startup is scheduled for the second quarter of 2014.
Back To Top
|
Stora Enso, Helsinki, Finland, reports that it has received project approval for its integrated pulp and board project in Guangxi, southern China, from the Chinese National Development and Reform Commission (NDRC). To benefit from the growing consumer demand for hygienic and high quality consumer board more rapidly, Stora Enso has, together with its local partner and supported by key customers, revised the investment schedule and will start by building a consumer board machine to be operational in the beginning of 2016. Construction of the previously announced pulp mill will be started after the board machine has been completed.
"The revised two-phase schedule, starting with the board machine and related industrial investments, will enable us through our customers to access the Chinese consumer market with an accelerated timetable. The revised investment schedule will cut the mid-term three-year capital expenditure requirements by half, as capital will be committed for the pulp mill only when the board machine is already generating cash flow," says Mats Nordlander, head of Stora Enso's Renewable Packaging Division.
Capital expenditure for the first phase of the project is estimated to be approximately EUR 760 million, including EUR 590 million for industry and EUR 170 million for plantation operations. The current capital expenditure estimate is approximately EUR 90 million in 2013, EUR 300 million in 2014, EUR 300 million in 2015, and EUR 70 million in 2016 or soon after. The project is expected to clearly exceed Stora Enso's ROCE target of 13%.
"Delaying construction of the pulp mill will also give us an additional three years to build up our fiber base and sustainable plantation operations in harmony with the local communities and with the support of all stakeholders. We will not be acquiring new land for eucalyptus plantations before we have solved the existing challenges concerning land leasing. We will continue our efforts together with the local communities to seek fair distribution of income from our operations.
"The new timetable fully supports Stora Enso's transformation from a European pulp and paper company into a renewable materials company focusing on growth markets. We are very excited to have a solid plan for finally going forward with the investment, which will produce sustainable and hygienic food packaging solutions for Chinese consumers," Nordlander concludes.
Back To Top
|
Thimm Display, Wörrstadt, Rhineland-Palatinate, Germany, has taken over the operations of Hohendahl Wellkarton GmbH, Essen, Germany. Beginning September 1, business activities at the Essen site will be conducted under the name of Hohendahl Display GmbH. Both Thimm Display and Hohendahl develop and manufacture advertising and product display units as well as decorations for branded goods for the retail sector. Through the Essen site, Thimm Display (with 246 employees and an annual turnover of EUR 33 million) is expanding its market presence in western and northern Germany and in the adjacent export markets. Hohendahl in Essen has 80 employees and recorded a turnover of EUR 13 million in 2012. Thimm Display is a business division of the Northeim, Germany-based Thimm Group.
Founded in 1949, Thimm is a family-owned business and one of the leading system suppliers of corrugated cardboard transportation and sales packaging, high-quality sales displays, multi-material packaging, and packaging-related services in the European market. Around 2,200 employees at 13 sites in Germany, Czech Republic, Romania, Poland, and Austria generated an annual turnover of EUR 431.2 million in 2012.
Back To Top
|
New Products
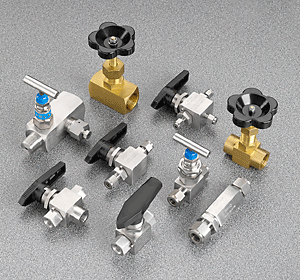 Brennen Industries Inc., Cleveland, Ohio, USA, an international supplier of hydraulic fittings and adapters, has introduced a new instrumentation catalog for its complete line of instrumentation fittings. The new catalog has all Brennan instrumentation tube fittings and their specifications in one place and includes tubing selection guides, tube-working pressure tables, sizing charts, and other helpful information for selecting the right fittings for each application. Brennan instrumentation tube fittings provide leak-proof, torque-free seals at all tubing connections and eliminate leaks in instrumentation, process, pneumatic, hydraulic, gas, and other tubing systems.
"Brennan instrumentation fittings are constructed and tested to provide the quality products that our customers expect," said Bill Jarrell, VP of marketing and operations, Brennan Industries. "The new category-specific catalog makes it faster and easier to make the right selections."
Brennan's complete line of instrumentation fittings includes plugs, nuts, back and front ferrule, connectors, unions, reducers, caps, and several other styles.
The catalog is available online.
Back To Top
|
To minimize downtime, ROTEX, Cincinnati, Ohio, USA, announced that it is now offering Express Part Service, ensuring that all in-stock parts orders received by 1:30 p.m. ET, Monday through Friday, will receive same-day shipping from strategic distribution centers located worldwide. Parts included in this service range from mesh cleaning balls, connector sleeves, to screen tension clips.
ROTEX offers genuine OEM parts, noting that this ensures optimal screening performance and prevents machine failure caused by sub-standard, generic replacement parts. All parts including screens and fabricated items (such as top covers and screen frames) are specifically engineered for ROTEX screeners and their unique applications, increasing equipment life and operating efficiency.
For after-our emergencies, ROTEX offers a staffed 24-hr Emergency Parts Line (513-591-5375). ROTEX'S staff of parts and services professionals is available to answer any screener related question by phone at the phone number above or by email. Rotex experts are also on-hand for on-site technical and operation training and service, as well as for online operation and maintenance training.
In addition to Express Parts Service, ROTEX offers machine refurbishment and rebuild services for upgrading existing ROTEX machinery or as a lower cost alternative to purchasing a brand-new screener. Refurbishment services include a thorough multi-point inspection of all machine components, an accurate cost estimator prior to starting work, replacement or reconditioning of all major machine components, and upgrades with the latest screening technologies.
More information about the ROTEX Express Parts Service, or any other ROTEX product or service offering is available online.
Back To Top
|
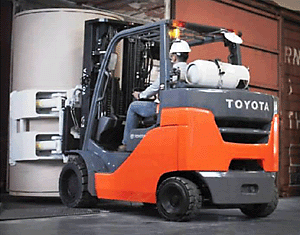 Toyota Material handling, USA Inc. (TMHU), Irvine, Calif., USA, this week unveiled its new 8-Series lift trucks designed to meet applications associated with the pulp and paper industry. The new lift trucks, which offer 8,000 – 15,500 lb lifting capacities, also include a new 12,000 lb standard counterweight, box car and paper roll special option. Powering the new lift trucks is a newly designed 3.7-liter, 4-cylinder engine built by Toyota Industries Corp.
The new 8-Series standard, box car, and paper roll models offer several features specific to the paper handling industry. To meet the paper industry's need for damage-free roll handling with maximum efficiency, factory-installed paper roll clamps are available in a wide range of configurations to handle multiple diameters, weights, and types of paper. To ensure proper operation, a clamp release interlock system built into the control valve works to help prevent accidental activation of the release lever. In addition, an automatic clamp leveling feature allows the operator to quickly level the clamp vertical to the paper roll with the touch of a button.
Toyota's paper roll special model offers a shortened wheelbase, load distance, and right angle stacking. These dimensional changes make the paper roll special lift truck more nimble and compact to maneuver in and out of the tight spots found inside of rail cars and in confined work environments around paper mills. The new 8-Series paper roll special counterweight is built with a cast iron enclosure specially shaped to reduce paper roll contact. This design modification provides a number of lift truck benefits including: better weight distribution, a lower center of gravity, and improved truck stability.
A number of improvements increase the lift truck's cooling performance to keep the engine running at optimal temperatures, including integrating an externally mounted hydraulic oil cooler, increasing the radiator size by 55% to provide a larger cooling surface for heat dissipation, a larger diameter cooling fan, and developing a cast iron rear frame that creates a wind tunnel effect to optimize heat extraction from the engine compartment. Additionally, a new engine protection system works to automatically reduce the engine's output if the coolant temperature rises to potentially damaging levels. Fully stamped steel plate side panels, plate-iron front tire fenders, and water-resistant electrical connectors are all designed to increase productivity when working in adverse weather conditions and corrosive applications. An accumulator option significantly reduces shock loading which, in turn, works to increase the life of mast and attachment components and lower the likelihood of product damage associated with poor warehouse floor conditions, Toyota notes.
The 8-Series' gas engine is 20% more fuel efficient than the previous V6 engine used. Also, in designing the 8-Series lift truck line, ergonomic improvements were made to the floor space, entry step, operator seat, curvilinear overhead guard, and LPG tank bracket. Newly designed operator assist grips accommodate operators of all sizes, while a four-way adjustable full suspension seat with anti-cinch seat belt mechanism allows operators to choose their ideal position to work comfortably. The new lift trucks also feature Toyota's System of Active Stability™ (SAS), which helps reduce the likelihood of lateral and longitudinal tip-overs. In addition, a standard technician programmable travel speed control system allows plant managers to limit the top speed of the truck without reducing performance of the hydraulic functions.
More information is available online.
Back To Top
|
Verso Paper Corp., Memphis, Tenn., USA, has launched a new pharmaceutical insert grade known as VersoRx™. The new product offering, engineered to deliver high print fidelity and sheeting and folding performance, is an addition to Verso's specialty papers product portfolio.
"Our introduction of VersoRx pharmaceutical inserts is a great example of our continued focus in the specialty papers market segment," says Mike Weinhold, Verso's SVP of sales, marketing, and product development. "By adding the VersoRx products to our portfolio, we have enhanced the wide range of product solutions that Verso offers converters, printers, and end-users."
Available in 27 lb, 30 lb, and 35 lb basis weights, VersoRx pharmaceutical inserts are produced on the No. 1 paper machine at Verso's mill in Bucksport, Maine. "The No. 1 paper machine at Bucksport plays a key role in Verso's plan to diversify its product line and expand in the specialty papers market segment," Weinhold explains. "Thanks to the expertise and ingenuity of our manufacturing team and to strategic investments made at the Bucksport mill, we are pleased to announce this important, new commercial component of our product diversification plan. The VersoRx products are integral to the success of our diversification efforts, both now and in the future," he says.
More information on VersoRx pharmaceutical inserts or other Verso products is available online.
Back To Top
|
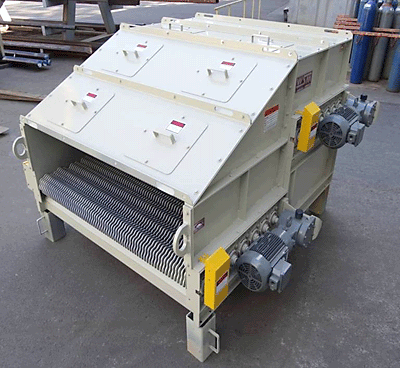 West Salem Machinery, Salem, Ore., USA, this week announced a new screening design called the Waterfall™ Disc Screen. The new arrangement utilizes two or more screening decks that agitate and tumble the mat of material being screened as it falls from level to level. This tumbling movement is similar to a waterfall in that the mat is blended as it falls and fine particles that were in the upper portion now have a chance to be screened on the lower deck.
To make this possible, West Salem developed a disc screen shaft manufacturing method that creates a tighter spacing between the discs, allowing the chipped or hogged materials to be sorted by size (thickness and length), but at a smaller dimension than in the past. Dust, dirt, and fine particles pass between the discs, while desirable and acceptable materials are retained above. This concentrates the fines and dirt so that they can be diverted from the process, or they can be re-screened to recover the maximum amount of organic material.
In particleboard manufacture where dryer efficiency and pellet properties are so dependent on material thickness and size, the Waterfall Disc Screen has an important role to play in sorting the sawdust and fine particles for optimum performance, often in combination with vibratory or shaker screens also manufactured and supplied by West Salem Machinery.
The Waterfall Disc Screen design is available for processing a variety of materials, including wood products, agricultural waste products, and any granular organic material where fines and dust are a problem. The welded discs are fixed to a sturdy tubular shaft, with large journals and bearings supporting and driving them from outside of the dust-proof screen frame. The modular nature of this arrangement makes it easy to combine different sections, and to use different disc spacing on each of the levels to target specific material fractions, if that is needed by the process.
As shown in the photo, the Waterfall Disc Screen has a dust proof housing complete with access doors for viewing the screen in action. For maintenance, the bolted covers are removed and the shafts are easily accessible. Internal chuting matches up with the collection chutes below. A common conveyor can be used to collect all of the fines removed, or separate conveyors can catch each of the screening deck's fines independently.
More information is available online.
Back To Top
|
People
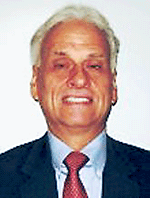 Precision Roll Grinders, Allentown, Pa., USA, has named Chad Bailey account manager, serving customers in the Ohio, Indiana, and Michigan territory. Bailey has held positions including director of marketing at FTH Maintenance Solutions & Constructors, sales and marketing manager at Sterling Boiler, and mechanical and regional sales manager at Haynes International.
Bailey will be based out of PRG's Lewisport, Ky., facility.
Back To Top
|
Sonoco, Hartsville, S.C., USA, this week announced that Harry A. Cockrell has been elected to its board of directors. Cockrell is managing director of Pacific Tiger Group Ltd, a Hong Kong-based privately held investment enterprise with a wide range of businesses and assets across the Asia/Pacific region. The group's investments include real estate and property development, packaging products and services, food processing and distribution, petroleum distribution, convenience store operations, biotechnology/medical technology, and information technology including multimedia and web-based services.
"We're extremely pleased to have Harry join Sonoco's board," said Harris E. DeLoach Jr., executive chairman. "In addition to being a long-time partner with Sonoco Asia businesses, Harry has a wealth of business and investment experience in growing Asia/Pacific markets."
Cockrell holds a B.A. degree in Asian studies from Seton Hall University and an M.B.A. from the Thunderbird School of Global Management where he serves as a trustee. He is a director of Pathfinder Investment Holdings Corp., a Philippines real estate management group. He is a former director of Hanesbrands Inc., and former investment committee member of Asian Infrastructure Fund. Earlier in his career, he was director of corporate banking for the National Commercial Bank of Saudi Arabia and was a banking advisor for Middle Eastern and Asian interests.
With Cockrell's election, Sonoco has 12 board members. He assumes the board seat vacated by John H. Mullen III, who retired having reached the age of 72, the mandatory retirement age of members of the board. Mullen retired on June 15, 2013, after serving on the Sonoco Board since 2002.
Back To Top
|
Timo Salonen, CFO and a long-term member of the executive team of Huhtamaki Group, Espoo, Finland, has decided to leave the company at his own request. "I would like to take the opportunity to thank Timo for his long service with the company and contribution to the Group's current success, as well as wish him all the best in his future challenges," said Jukka Moisio, CEO.
Also, Thomas Geust has been appointed director, finance and a member of the Group Executive Team, reporting to Moisio, as of October 1. He joins Huhtamaki from ABB Group, where his latest position was global controller for the business unit Marine & Cranes in Switzerland. Prior to ABB, Geust has worked in various financial positions in Schneider Electric, Lexel Group, and KPMG.
With these changes, the company's Group Executive Team currently includes:
- Jukka Moisio (chairman), CEO
- Thomas Geust, director, finance (effective October 1)
- Sari Lindholm, SVP, human resources
- Clay Dunn, EVP, North America
- Suresh Gupta, EVP, flexible packaging
- Olli Koponen, EVP, molded fiber
- Eric Le Lay, EVP, foodservice Europe-Asia-Oceania
- Peter Wahsner, EVP, films.
Back To Top
|
Weyerhaeuser Co., Federal Way, Wash., USA, reports that its board of directors has elected Devin Stockfish corporate secretary for the company. The appointment became effective July 1. Stockfish will continue to serve as assistant general counsel and his practice includes corporate governance, securities law compliance, mergers and acquisitions, and corporate finance matters.
Stockfish succeeds Claire Grace, who will remain assistant general counsel until her planned retirement on August 16. Grace was Weyerhaeuser's corporate secretary from 2000 to June 30, 2013.
Before joining Weyerhaeuser, Stockfish was VP and associate general counsel at Univar Inc. where he focused on mergers and acquisitions, corporate governance, and securities law. Prior to Univar, he was an attorney in the securities and corporate law group at Starbucks Corp. and practiced corporate law at K&L Gates. He received a Juris Doctorate from Columbia Law School and holds a Bachelor of Science degree in mechanical engineering from the University of Colorado.
Grace joined Weyerhaeuser in 1997, became corporate secretary and assistant general counsel in 2000, and was named a VP in 2007. She has been a securities lawyer since 1986, focusing on corporate securities and finance, compliance with securities laws, public disclosure, mergers and acquisitions, international transactions, corporate law, and contract law. Prior to joining Weyerhaeuser, Grace was VP and associate counsel at Washington Mutual Bank, a securities and finance lawyer with Perkins Coie, and served as administrative law clerk to Judge Eugene Wright, U.S. Court of Appeals, Ninth Circuit.
Back To Top
|
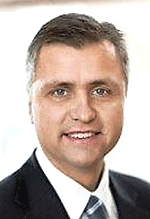 Christer Thörn has been appointed the new HR director of Södra, Sweden. He will be part of Södra's group executive team, reporting to CEO and Group President Lars Idermark.
Thörn was previously employed as an HR director and head of TQM at listed group PartnerTech. He has previously worked in the Armed Forces and in various personnel manager roles at Tetra Pak, and as head of production at Distansapoteket in Hässleholm.
Thörn has broad managerial and leadership experience from his time with the armed forces, and he has extensive HR experience from both Tetra Pak and PartnerTech. He will be taking over responsibility for the group's HR function in the autumn from Carina Olson, who will be continuing in her position as CFO.
Back To Top
|
TAPPI News
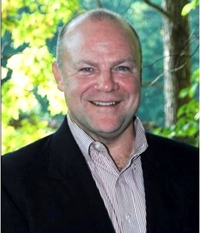 Larry N. Montague, TAPPI president and CEO, has been named to the 2013 RISI Power List of the most influential leaders in the global pulp and paper industry. The sixth annual list is selected by the RISI/PPI Magazine editorial staff and recognizes individuals having the greatest influence on the global industry in the past year.
"TAPPI has been able to reinvent itself and better serve the industry under Larry's leadership and vision," said Tom Garland, chair, TAPPI board of directors, and president-Packaging, Quad Graphics. "He was instrumental in transforming a failing association that had posted financial losses for 11 years into a financially healthy organization with growing membership. He implemented a team-based approach that led to a change in culture that cut expenses, strengthened member benefits, and developed new market opportunities."
"RISI's Power List includes many highly respected leaders and executives from all sectors of the global industry and I'm honored to be included," said Montague. "The nomination reflects the tireless hard work of the many TAPPI members and TAPPI staff that are essential to our success. It's through their efforts that we have been able to expand into new areas, grow membership, and enhance the value of the products and services we provide to our members. I would like to express my sincere thanks for their efforts."
In nominating Montague the magazine's editors recognized his leadership at TAPPI, which has experienced a resurgence following the long industry downturn, noting improved attendance at the PaperCon conference, growing popularity of the exhibit, and TAPPI's involvement with current issues such as nanotechnology, the bio sector, and industry safety.
Prior to becoming TAPPI's president and CEO in 2006, Montague worked for 27 years in paper industry sales and management, most recently as VP of sales and marketing for The Newark Group, a producer of recycled paperboard and paperboard products. He began his career in the industry with Boise Cascade Corp. before joining the Republic Group Inc. where he held senior management positions including GM of the Corrugated Container Division and GM and VP of sales and marketing at Republic Recycling.
RISI provides news, prices, forecasts, and analysis on the global forest products industry, including pulp and paper, tissue, wood products, and timber. RISI also publishes PPI Magazine and other publications and industry conferences.
Back To Top
|
Nominations for the major TAPPI 2014 awards are due by August 1. The awards that may be presented in the upcoming year are:
Gunnar Nicholson Gold Medal Award - The Association's highest technical honor may be presented annually to recognize an individual or individuals for preeminent scientific and engineering achievements of proven commercial benefit to the world's pulp, paper, board, and forest products industries and the other industries that TAPPI serves.
Herman L. Joachim Distinguished Service Award - The Association's highest award for service may be presented annually to recognize leadership and service that have significantly and demonstrably contributed to the advancement of the Association.
Paul W. Magnabosco Outstanding Local Section Member Award - The highest honor for Local Sections may be presented annually to recognize an individual for outstanding leadership and exceptional service to one or more Local Sections, which have resulted in significant and demonstrable benefits to the Local Section members.
TAPPI Fellow - TAPPI Fellows are individuals who have been members of TAPPI for not less than 10 years prior to the nomination, and who have contributed meritorious service to the Association and/or the paper and related industries. Retiring members of the TAPPI Board of Directors become Fellows automatically at the end of their term.
The TAPPI Awards and Honors page has links to these awards that will show the qualifications required and links to the nomination forms that must be completed. You may submit all nomination forms by email to standards@tappi.org, or you may fax them to the attention of the awards department at +1-770-446-6947, or send them by mail to TAPPI, Awards Department, 15 Technology Parkway South, Peachtree Corners, GA 30092, USA.
Back To Top
|
The Safety Management Leadership Course, August 26-27 in Metro Atlanta, Ga., USA, places a particular focus on leadership training, including incorporating a safe environment into workforce training and work expectations. Key safety topics are covered by the course, including:
- Safety Fundamentals / Modern Safety Management Principles
- OSHA Record Keeping and Medical Management
- Incident Investigation
- Safe Behavior and Choices
- Safety Culture
- Measuring Safety Performance
- Hazard Recognition
- Safety Walk-throughs, Observations, and Messaging
- Managing Change Safely
- Effective Safety Communication.
See more listed on the course schedule.
Meet the instructors.
Register for the Webinar Preview.
Tuesday, August 6 ♦ 1:00 p.m. EST ♦ 45 min.
This course is designed for anyone involved in workplace safety, including:
- Training and HR
- Safety Supervisors
- Team/Project Leaders
- Plant Managers
- Frontline Supervisors
- Safety Committees.
A special discount is offered for TAPPI and PPSA members. Register by July 26 for savings off the regular course rate.
TAPPI will award 1.3 CEUs to those who complete this course.
Back To Top
|
The 2014 PLACE Technical Program Team is actively seeking technical presentations, panels, tutorials, roundtables, and case studies from the packaging and academic community to be presented at this year's conference. Interested in being a session chair or know someone who would be a great presenter? Extended abstracts will be accepted anytime before August 1. Space is limited so submit now! Final papers will be due on or before March 17, 2014.
View the list of suggested topics and an extended abstract example.
The 2014 PLACE Conference is the premier North American event for the flexible packaging industry and will have something for the whole supply chain, including suppliers, converters, extruders, retailers, and brand owners.
Join us for this comprehensive event with more targeted content, topic variety, and program ideas than ever before. This event will use traditional content delivery methods like primers/tutorials, panel discussions, and interactive content delivery methods.
Submission Deadline is August 1, 2013.
Feel free to contact Kristi Ledbetter if you have any additional questions.
Kristi Ledbetter
Converting Division Manager
TAPPI
15 Technology Parkway South
Peachtree Corners, GA 30092
Phone: 770-209-7319
Fax: 770-446-6947
Back To Top
|
IEEE Spectrum author and noted researcher Dr. Andrew Steckl will provide the opening presentation at the upcoming Building Electronics on Paper Workshop, August 6-7 at Western Michigan University in Kalamazoo, MI., USA. Based at the University of Cincinnati, Dr. Steckl revealed the following in the IEEE magazine about paper as a substrate for displays and microfluidic systems:
- With the right set of additives and manufacturing processes, paper can take on a seemingly endless range of properties. It can be made hydrophilic or hydrophobic, porous or watertight, opaque or nearly transparent, delicate or strong, coarse or about as smooth as glass.
- It is possible to fabricate reliable pixels on coated paper with switching times as short as 10 milliseconds - nearly suitable for video. Paper-based displays using electrowetting might be ideal for smart labels on packages that could, for example, show videos about how the product is to be used, or for displays containing vital information for soldiers in the field—that can be rapidly destroyed if necessary.
- Researchers are now trying to develop a general class of paper-based microfluidic systems that can be adapted to make a variety of different tests, for such tasks as monitoring liver function or diagnosing tuberculosis. If done right, these tests could be compact, self-contained, and extremely affordable.
Join Dr. Steckl and subject matter experts from the Kellogg Company, DuPont Electronics, Rutgers University, and others will share results of their research and product development at the FlexTech Workshop, co-hosted by Western Michigan University (WMU). Workshop sponsors include FujiFilm Dimatix and Paper360.
See the full agenda on the event website.
Paper 360° is the media sponsor and TAPPI members receive a substantial registration discount. Use the discount code: PAPER360. Register today.
Prior to the workshop, registrants will benefit from a 1/2 day of hands-on demos at WMU's Center for the Advancement of Printed Electronics, which features labs dedicated to inkjet, screen, rotogravure, and flexographic printing.
Back To Top
|
This is a reminder that there will be two great golfing opportunities from Lake States TAPPI / North Central PIMA this summer.
August 13th is the annual golf outing at Mid-Vallee Country Club in De Pere, Wis. An afternoon shotgun scramble golf outing is planned with dinner to follow. Prizes will be awarded and individual pin events will be held. Proceeds help fund scholarships for local TAPPI and PIMA programs. Register online before August 9th .
August 27th PIMA will hold it's Golf Outing at Grand View Lodge of Pequot Lakes, Minn. The shotgun scramble starts at 9:30 a.m. Box lunch is included, with cocktail hour to follow. Net proceeds go to Lake States TAPPI/ North Central PIMA's Scholarship Fund. Details now available and registration is open.
Back To Top
|
DuPont and Kellogg's are among the featured companies presenting at FlexTech Alliance's upcoming workshop "Building Electronics on Paper – Why, How & Who" on August 6-7 at Western Michigan University in Kalamazoo, Mich., USA. This 1.5-day combination of demonstrations, presentations, and networking features industry and academic experts explaining the dynamics of printing electronic circuitry on paper. See the full list of speakers.
Paper 360° is the media sponsor and TAPPI members receive a substantial registration discount. Toward the end of the registration process, enter this code PAPER360 in the "Discount Code" field and click "Apply" to receive the $149 workshop price.
Valuable market insights will be presented, including a keynote from Kellogg's Corporation on smart packaging, while DuPont will explain its experience with printed electronic materials. Other presentations include paper as a novel platform, paper–based touch pads, thermal printing, and paper-based printed circuit boards (PCBs).
Registrants will benefit from the ½ day of hands-on demos at WMU's Center for the Advancement of Printed Electronics (CAPE), which features labs dedicated to inkjet, screen, rotogravure, and flexographic printing. DuPont, Mitsubishi Inks, NovaCentrix, and WMU will provide experts to conduct the demos and explain fabrication methods.
By attending this workshop, registrants will learn:
- Why paper is an important substrate for printed electronics
- What applications are of interest to end users
- Challenges in developing and accepting new printed electronics technology
- Recent advancements in corporate and university labs that are enabling printed electronics on papers in all of its forms.
Click here for registration and workshop details.
Back To Top
|
The 2013 TAPPI Linerboard/Medium Manufacture Course, August 13-15 at the TAPPI Training Room, in Peachtree Corners, Ga., USA, is designed to help increase your understanding of linerboard and medium performance properties and manufacturing to improve corrugated box performance and runnability.
This intermediate-level course is ideal for process engineers and operators in linerboard and medium manufacturing facilities and converting plants with a more intermediate background. For those participants who require an overview background on pulp and papermaking technology, there will be an optional one day Introduction to P&P on Monday afternoon, August 12, prior to the beginning of the main course on Tuesday. This supplemental session is intended for corrugators, new P&P mill and supplier personnel, and those without exposure to pulp and paper operations.
If you are looking to increase your understanding of linerboard and medium performance properties and how they are achieved, build your confidence in interacting more knowledgeably within the mill with suppliers and with corrugators, and improve manufacturing operations to produce a more competitive product, then this course is for you.
There are only 25 seats available for this course. Register now to reserve your spot.
Back To Top
|
The TAPPI International Research Management Committee requests nominations be submitted for the Research and Development Technical Award and the William H. Aiken Prize.
The award is given for outstanding accomplishments or contributions that have advanced the technology of the paper and related industries in the field of research and development. The nomination should contain:
- A summary of the nominee's technical achievements
- The impact and relevance of the research on industry
- Education, work history
- Examples of the impact that they have had on others
- Other pertinent activity such as involvement in TAPPI.
The $500 prize is funded by an endowment from the estate of William H. Aiken, TAPPI president in 1967-1968 and vice president of technology for the former Union Camp Corp. at the time of his death in 1974. Dr. Aiken also won the TAPPI Gold Medal, the association's highest honor, in 1971. Nominations for the Research and Development Technical Award and the William H. Aiken Prize should be submitted by August 31, 2013, to Colleen Walker, cwalker@tappi.org at TAPPI, 15 Technology Parkway South, Peachtree Corners, Ga. 30092, USA, or fax +1 770-446-6947.
Back To Top
|
Your business can potentially save millions implementing improvements to paper machine performance and reliability.
The TAPPI Improving Paper Machine Performance Course, August 20-22, in Peachtree Corners (Metro Atlanta), Ga., USA., will allow students to see real world examples of paper mills that have made major improvements in overall efficiency by implementing many small improvements across their operation.
Jim Atkins will lead you through a real mill improvement project and show you how you can do the same thing in your mill. Dick Reese will show you how to make big savings in energy costs by correcting problems that often require little or no capital expenditures. Chuck Klass will teach you how to evaluate size press and coating operations to get the most out of what you have. And Ken Hill will give you the tools you need to evaluate and benchmark dryer systems, so you can correct problems and dry more paper.
This is an advanced level course. Students who complete this course will know everything required to save their company millions of dollars through paper machine performance improvements.
Learn more about this course.
Register online.
Back To Top
|
Registration is now open for the 2013 TAPPI Corrugated Press Hands-On Maintenance Workshop, September 17-18 at the Global Equipment USA Warehouse in Skokie, Ill., USA.
This unique course gives you an unprecedented opportunity to get hands-on training on how to audit converting machines. With only 18 seats available, you will have ample opportunity to get your questions answered by instructors Tom Pearce (Pearce Corrugated Consulting), John Bingham (Pamarco), Jim Wegemer (INXinc), Chuck Bobeldyk (Mark-Maker Co.), Randy Kesselring (MarquipWardUnited), as well as representatives from Global Equipment. The schedule for this course is packed into just two efficiently planned days so that participants get loads of skill and experience without much time away from their own operations.
Who should attend?
This Intermediate-level course offers indispensable hands-on maintenance training for corrugated industry plant managers and supervisors, engineers, maintenance teams, and machine operators.
You could pour over all of the how-to manuals available and still not retain this level and quality of working knowledge. Completing this workshop will enable you to:
- Use the basic tools to mechanically audit and troubleshoot a press
- Understand press audit procedures for process centering, better quality products, and increased productivity
- Discuss anilox roll selection, press "fingerprinting," inks and substrates, quality defects amd cause(s), and scoring.
Register by August 16 and join TAPPI or renew your membership to receive the best rates.
Back To Top
|
TAPPI invites submissions of basic and applied research articles, communications, and technical reviews to TAPPI Journal, the world recognized peer-reviewed research publication. TAPPI is the leading association for the worldwide pulp, paper, packaging, tissue, nonwovens, and converting industries, with more than 7,000 members globally.
Authors presenting papers at conferences, experts with significant industry findings, and students or professors reporting academic research − any authors performing relevant industry research − are encouraged to submit their manuscripts.
Why submit your work to TAPPI Journal?
High visibility: Publishing in TJ makes your work accessible to professionals, libraries, and the global academic community through TAPPI's robust communications network.
TJ electronic issue: Distributed to thousands of TAPPI members every month, TJ features abstracts, full papers, author notes, and more.
Print compendium: Members also receive TJ's annual print compendium, a bookshelf reference volume containing abstracts of every paper published that year. The compendium is distributed to more than 250 libraries, industry organizations, and academic institutions around the world.
Paper360°: Summaries of select TJ papers appear in Paper360°, TAPPI's bi-monthly magazine with a global circulation of more than 40,000.
Online library: Papers published in TJ become part of TAPPI's e-Library available online. Searchable by subject and author name, the e-Library allows worldwide access to abstracts and downloadable full papers.
Indexing: Every issue of TJ is indexed by Thomson-Reuters, the world's leading citation index for academic research.
Career enhancement: Our stringent peer-review process and distinguished Editorial Board have made TAPPI Journal a well-respected, commonly referenced source of the best industry research for more than 60 years. TJ publication is an excellent way to gain attention from colleagues, peers, and current or future employers.
Author-focused process: Editorial Board members carefully marshal every paper submitted, based on area of expertise; TJ peer reviewers are selected for their proven subject knowledge. These experienced professionals – most of whom are TJ authors themselves – work with authors to ensure that papers meet TJ's high standards and are presented clearly and accurately.
Easy to submit: Papers may be submitted by email to Jeff Wells at TAPPI. Complete author guidelines are available online. (Please note: Papers must be submitted by the author; TAPPI Conference papers are NOT automatically reviewed for TJ publication.)
We look forward to receiving your work!
Back To Top
|
The soon-to-be-published, "Production and Applications of Cellulose Nanomaterials" is the latest TAPPI Press product to broaden the industry knowledge regarding who is researching nano technologies as well as leads on successful applications.
Anyone working in the nanomaterials field, or needing to understand the production and standards of the field, will want to add this volume to their reference material. Cellulose nano-crystals and cellulose nano-fibrils have been known for 20-50 years, but recent research suggesting very high strength properties and other unique physical properties have generated extensive interest in these materials.
Pre-order your copy today and save!
This new book will include:
- A collection of two to three page summaries on recently completed and on-going research with these high strength materials
- A list of who's-who of research as well as leads on successful applications
- Topics on subjects such as production and modification, composites, other applications, modeling, and standards.
- Special feature: Actual cellulose nanocrystals included within the overcoat varnish of the cover.
Pre-order Price:
Member: $149
Nonmember: $149
After July 15:
Member: $189
Nonmember: $259
Product code: 0101R332
Back To Top
|
Make plans to attend the 2013 Building Sciences Committee Fall Meeting September 18-20.
The Building Sciences Committee has designed a strong technical program for production managers and engineers to provide firsthand knowledge to improve their fiberglass mat process with practical production-targeted papers.
This year's program will include papers on: Process Variation Reduction, Glass Sizing Basics; Burner Safety and Efficiency; Biological Treatment Case Study, Operator and Mechanical Training to Enhance Operational Effectiveness; IT Systems to Manage Roll Goods and Reduce Waste.
We are pleased that Tim Worms of 3M will return by popular demand to present his updated Roofing Market Overview and Forecast.
The meeting will be held at The Hilton Marco Island Beach Resort in Marco Island, Fla. USA. TAPPI has negotiated a very economical room rate of $109.00 per night per guest. This rate is good for TAPPI members for stays of any length from Wednesday, September 18, through Sunday, September 22. Group dinners Wednesday and Thursday evenings will provide opportunities to meet other manufacturing personnel and suppliers, and their cost is included in the cost of the meeting. These will be excellent networking opportunities.
Thursday's afternoon recreational activity (also included in the registration price) is a choice of golf, coastal fishing, or an afternoon at the spa. Non-registered spouses and guests are welcome to participate in the activities and dinners for the following costs: $60 per dinner and $95 for golf, fishing, or the spa treatment. They do not have to pay the conference registration fee.
Click here for additional meeting information.
Back To Top
|
As TAPPI is getting ready to celebrate its 100th Year Anniversary in 2015, we were wondering how much industry expertise we have in this great group of professionals.
So, we decided to post a discussion question on our TAPPI Social Media outlets. We asked, "How many years of paper and/or packaging experience do you have?"
Who knew such a simple question would have such an impressive response.
With more than 7,000 TAPPI members, all over the world, we have counted 650-plus years of industry experience! And that's just counting the first 30 people who have responded. Now you probably can't find that anywhere else . So why don't you join us?
From those "born" into the industry to third generation professionals. From paper to packaging, to sustainability, environment, tissue, converters, and consulting. This TAPPI network has something for everyone.
Become a part of this unique community of paper and packaging professionals, and add your expertise to our group, and network with others to learn something new.
Visit our website to learn more today!
Back To Top
|
The 2013 TAPPI PEERS Conference, September 15-18, in Green Bay, Wis., USA, has announced the detailed technical program focusing on sustainable manufacturing and other pressing business and technical questions faced by pulp and paper companies as they manage raw materials, assets, regulatory requirements, and production assets. Register now and save.
In addition to the peer-reviewed technical program, Keynote Speaker Robert Feeser, SVP of Packaging with MWV, will share his insights on the day-to-day challenges he faces as he oversees the company's primary mill-based manufacturing businesses in the U.S. and Brazil. PEERS will also offer exclusive networking opportunities and insight into new technologies that can help you optimize your mill operations.
For 2013, PEERS will be co-located with the 10th Research Forum on Recycling and the International Bioenergy and Bioproducts Conference, creating a value-added opportunity for you to expand your learning, networking, and resources by attending all three events.
Learn more about the TAPPI PEERS Conference.
Back To Top
|
TAPPI CorrExpo 2013, October 7-9 at the JW Marriott in Indianapolis, Ind, USA,. is your one-stop pitstop to fuel your networking and relationship building needs.
Take advantage of these high-octane opportunities:
View the full program to fast track your CorrExpo experience.
Back To Top
|
The TAPPI Centennial Celebration will be a multi-year long series of outreach events and educational offerings showcasing the proud history and promising future of the global pulp, paper, packaging, and related industries. This once-in-a-lifetime event will expand public awareness, foster further connection, and provide outstanding opportunities for collaboration, growth, and investment in our future for all of those involved. Goals for the TAPPI Centennial Celebration are:
- To honor TAPPI's 100 years of connection, education, and advancement as a foundation for the sustainable success of our members, our industries, and the world we share
- To recognize the achievements of those who built our industry and to inspire those who seek to build its future
- To celebrate the contributions and innovations of the global pulp, paper, and packaging industries to human culture, commerce, health, and social advancement
- To sustain the industry and support its growth, vitality, and future through the TAPPI Foundation.
We invite you to be a part of this momentous event. The sooner you join us the more opportunities there are for recognition of your company, its products, and key innovations. Keep in mind that an early commitment allows you to spread your investment over multiple years' budgets.
For more information on sponsorship and volunteer opportunities please contact dbell@tappi.org.
The sponsorship prospectus can be downloaded online.
Back To Top
|
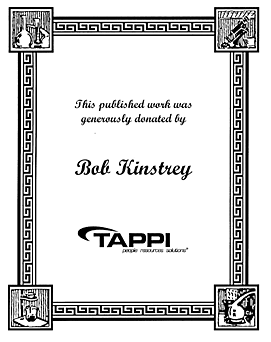
Do you have a history book gathering dust on your shelf? TAPPI's 100th year is coming soon and we are looking for donations to the TAPPI Library. Specifically, we are interested in histories of companies and mills in the paper and packaging industry (both producers and suppliers). Each donated book will have a bookplate in the front cover recognizing the donor. For more information please contact David Bell.
Please send books to:
c\o David Bell
TAPPI
15 Technology Parkway, South
Suite 115
Peachtree Corners, Georgia 30092
Back To Top
|
|
|
TAPPI Over the Wire | 15 Technology Pkwy. S. | Norcross, GA 30092 USA | Voice: 770.446.1400 | Fax: 770.446.6947
|
 |