 |
|
Weekly Spotlight
Injection of carbon dioxide (CO2) has begun at a site in southeastern Washington to test deep geologic storage
Learn More...
|
Asia Pulp & Paper Group (APP) Singapore, reports that its PT Pabrik Kertas Tjiwi Kimia Tbk and PT Pindo Deli pulp and paper mills have completed the acquisition of a 70.58% share (each 35.29%) in PT. OKI Pulp & Paper Mills
Learn More...
|
OfficeMax Inc., Naperville, Ill., USA, and Office Depot Inc., Boca Raton, Fla., this week provided an update on the integration planning process and expected annual cost-saving synergies related to the companies' proposed merger
Learn More...
|
The 2013 TAPPI PEERS Conference in Green Bay, Wis., USA, September 15-18, focuses on advances and emerging developments in the kraft pulping and bleaching arena as well as the chemical recovery island
Learn More...
|
Below is the latest listing of job openings in the TAPPI Career Center
Learn More...
|
Market Roundup
Total U.S. printing and writing (P&W) paper shipments were down 7% compared with June 2012, with total inventory levels increasing 4% from May
Learn More...
|
In recent years, the huge demand for dissolving pulp has prompted many companies to build new dissolving pulp projects, leading to a rapid increase in dissolving pulp production capacity
Learn More...
|
In 2012, world consumption of kaolin had recovered to almost 23 million metric tons, compared with less than 20 million metric tons during the global economic downturn of 2008/09
Learn More...
|
The global market for folding cartons is growing by 5.1% annually, and will reach $184 billion by 2018
Learn More...
|
Pulp & Paper
Buckman, Memphis, Tenn., USA, this week announced the formation of a new company, Buckman North America, under which the current Buckman Canada and Buckman U.S. organizations will be brought together into a single operation
Learn More...
|
The new line will have a maximum production capacity of 110 metric tpd
Learn More...
|
Voith Paper FRS' ongoing advancement of fabric technology was the key factor in K-C's selection of Voith for the award
Learn More...
|
Weyerhaeuser Co., Federal Way, Wash., USA, has completed the acquisition of Longview Timber from affiliates of Brookfield Asset Management
Learn More...
|
Weyerhaeuser Co., Federal Way, Wash., USA, has published its tenth annual sustainability report
Learn More...
|
Containerboard/Packaging
Pratt Industries, Conyers, Ga., USA, this week reported that its Conyers mill has made its 6 millionth ton of 100% recycled paper
Learn More...
|
Rengo Co., Japan, has begun construction to renew a containerboard (linerboard) machine at its consolidated subsidiary Marusan Paper Mfg. Co. in Japan
Learn More...
|
Smurfit Kappa Group, Ireland, has completed refinancing of its existing senior secured credit facility with a new five-year unsecured relationship bank facility
Learn More...
|
|
New Products
Dura-Fibre, Menasha, Wis., USA, reports that many of its folding carton substrates, including Forte, Eclipse, and Blanc, now feature a kraft liner that provides enhanced wet durability, quality, and consistency
Learn More...
|
Eaglewood Technologies, Minneapolis, Minn., USA, makers of Sani-Blast™ Anilox Roll Cleaning Systems, has begun a partnership with corrugated machinery supplier, The Haire Group, to offer the Sani-Blast Anilox Roll Cleaning systems
Learn More...
|
NewPage Corp., Miamisburg, Ohio, this week announced Anthem® Plus™, a new, economy coated paper designed to perform in virtually every print application
Learn More...
|
People
Asia Packaging Group Inc. China, reports that Brian Birmingham, VP and director of the company, has resigned
Learn More...
|
Ferragina reports to Debabrata Mukherjee, President and CEO, Finch Paper
Learn More...
|
Darlene Kober has joined Hexacomb, Buffalo Grove, Ill., USA, a Boise company, as director of global marketing and strategy
Learn More...
|
Mario Gosselin, CEO of Kruger Products L.P., Mississauga, Ont., Canada, this week announced that Rob Latter has been named corporate VP, Away From Home (AFH) Division and Strategic Planning
Learn More...
|
TAPPI News
Pre-registration closes this Friday for this ground-breaking workshop taking place August 6-7 in Kalamazoo, MI.
Learn More...
|
Being an active member means creating a network that spans the globe.
Learn More...
|
The TAPPI/PPSA Safety Management Leadership Course will be held August 26-27 in Metro Atlanta, Ga., USA. This course sold out in 2012 and course registration is limited to 30 participants.
Learn More...
|
Nineteen publications offered at only 1 penny (plus shipping). Order now while supplies last. This event will not last long.
Learn More...
|
"The Production and Applications of Cellulose Nanomaterials" is the latest TAPPI Press product to broaden industry knowledge regarding who is researching nano technologies as well as leads on successful applications.
Learn More...
|
August 13th is the annual golf outing at Mid-Vallee Country Club in De Pere, Wis. August 27th PIMA will hold it's Golf Outing at Grand View Lodge of Pequot Lakes, Minn.
Learn More...
|
With only 25 seats left, register now to reserve your spot.
Learn More...
|
The TAPPI International Research Management Committee requests nominations to be submitted for the Research and Development Technical Award and the William H. Aiken Prize by August 31.
Learn More...
|
The TAPPI Improving Paper Machine Performance Course, August 20-22, will allow students to see real world examples of paper mills that have made major improvements in overall efficiency by implementing many small improvements across their operation.
Learn More...
|
The schedule for this course, September 17-18, is packed into just two efficiently planned days so that participants get loads of skill and experience without much time away from their own operations.
Learn More...
|
The 2014 PLACE Technical Program Team is actively seeking technical presentations, panels, tutorials, roundtables and case studies from the packaging and academic community to be presented at the conference.
Learn More...
|
Authors presenting papers at conferences, experts with significant industry findings, and students or professors reporting academic research − any authors performing relevant industry research − are encouraged to submit their manuscripts.
Learn More...
|
Anyone working in the nanomaterials field, or needing to understand the production and standards of the field, will want to add the soon-to-be-published "Production and Applications of Cellulose Nanomaterials" to their reference material.
Learn More...
|
The Building Sciences Committee Fall Meeting will be September 18-20 at The Hilton Marco Island Beach Resort in Marco Island, Fla.
Learn More...
|
September event also co-located with Research Forum on Recycling and International Bioenergy and Bioproducts Conference.
Learn More...
|
Opportunity for engineers, scientists, and technicians who want to get a handle on one of the difficult contaminants in paper recycling - stickies.
Learn More...
|
Make plans to attend the only industry event dedicated to advancing biorefineries in the forest products industry.
Learn More...
|
TAPPI CorrExpo 2013, October 7-9, will be held at the JW Marriott in Indianapolis, Ind., USA, and will feature the classic golf tournment as well as an evening gala at the Indianapolis Motor Speedway.
Learn More...
|
Join more than 7,000 TAPPI members across the world with 650-plus years of industry experience.
Learn More...
|
This once-in-a-lifetime event will expand public awareness, foster further connection, and provide outstanding opportunities for collaboration, growth, and investment in our future for all of those involved.
Learn More...
|
As TAPPI's 100th year approaches, we are looking for donations to the TAPPI Library.
Learn More...
|
|
Find us on Facebook
Network with us on LinkedIn
Follow us on Twitter
|
Weekly Spotlight
Injection of carbon dioxide (CO2) has begun at a site in southeastern Washington to test deep geologic storage. Batelle, Columbus, Ohio, USA, researchers based at the group's Pacific Northwest National Laboratory in Richland, Wash., are injecting 1,000 tons of CO2 one-half mile underground to see if the greenhouse gas can be stored safely and permanently in ancient basalt flows.
Boise Inc. teamed with Battelle, which operates PNNL for the U.S. Department of Energy, and Praxair, Inc., Danbury, Conn., to conduct the CO2 injection phase of the pilot project. Injection is occurring on Boise property (Wallula, Wash., pulp and paper mill) in deep basalt—the same massive ancient lava flows that underlie major portions of Washington, Oregon, and Idaho. The joint research is conducted under the Big Sky Carbon Sequestration Partnership, which is led by Montana State University and funded by DOE and a consortium of industrial partners. It is one of seven regional partnerships throughout the U.S. aimed at finding safe and economical ways to permanently store the nation's greenhouse gas emissions.
"We have been conducting laboratory tests on basalts from the region for several years that have conclusively demonstrated the unique geochemical nature of basalts to quickly react with CO2 and form carbonate minerals or solid rock, the safest and most permanent form for storage in the subsurface," said Battelle project manager Pete McGrail. "However convincing the laboratory data may be, proving the same processes operate deep underground can only be done by conducting a successful field demonstration. We have taken the very first steps to do that here in Wallula."
During the next two to three weeks, Battelle scientists will work with Praxair technicians to inject into porous layers of basalt CO2 that has been compressed into a liquid-like state. Thick and impermeable layers of rock above these porous layers will act as barriers or seals to prevent the CO2 from travelling vertically upward.
During the next 14 months, fluid samples will be extracted from the injection well. Scientists will look for changes in chemical composition in comparison with baseline data compiled prior to injection. Scientists will also compare results to predictions made using PNNL's supercomputer. At the end of the monitoring period, rock samples will be taken from the well. They are expected to exhibit the formation of limestone crystals as a result of CO2 reacting with minerals in the basalt.
The Boise pulp and paper mill, located in the Columbia Basin between the Tri-Cities and Walla Walla, Wash., sits atop dozens of volcanic lava flows, extending down 8,000 feet or more. Like a stack of pancakes, these geologic layers were formed as volcanic lava flowed and cooled, one on top of the other. In 2009, an injection well was drilled at the site confirming that basalt flows located immediately above and below the injection zone were nearly impermeable. Additional research conducted at the site in late 2012 indicated that the location is well suited for the pilot test.
"Boise is pleased to have worked with Battelle in recent years and to be a partner for this research that advances the science of geologic carbon sequestration," said Rich Garber, Boise environmental director. "At Boise Inc., we believe wisely using energy and resources is good for business and for our environment. Through various other means, we've reduced our greenhouse gas emissions 27% since 2004 at our manufacturing facilities. This collaborative effort with Battelle is an additional opportunity for us to build on that progress and demonstrate our commitment toward continuous environmental improvement. "
According to recent DOE estimates, the U.S. and portions of Canada have enough potential capacity in geologic formations to store as much as 900 years of CO2 emissions. If the Wallula demonstration is successful, basalt flows in many parts of the world may serve as storage locations to store CO2 emissions from a variety of industrial facilities.
"Boise has been a fantastic partner and there is no question that this field research could not have been done without their unwavering support," said McGrail.
The demonstration is approximately 80% funded through DOE's National Energy Technology Laboratory. To date, approximately, $12 million has been committed to the pilot project. Other contributors include Schlumberger, Royal Dutch Shell, Boise Inc., and Portland General Electric.
In the photo, Praxair technicians make adjustments to the CO2 piping. The injection well itself is in the foreground, left.
Back To Top
|
Asia Pulp & Paper Group (APP) Singapore, reports that its PT Pabrik Kertas Tjiwi Kimia Tbk and PT Pindo Deli pulp and paper mills have completed the acquisition of a 70.58% share (each 35.29%) in PT. OKI Pulp & Paper Mills, a company currently developing a pulp and paper mill in South Sumatra, Indonesia. The new mill will be situated on 2,600 hectares in Ogan Komiring Ilir in Palembang, South Sumatra, with an additional 200 hectares for the development of a port. Civil works are starting this year, with the first phase of commercial production expected to begin in 2016. The new mill is expected to produce around 2 million air-dried metric tpy.
PT OKI Pulp & Paper Mills will use the most advanced environmental technology and standards available, APP notes. Clean and self sufficient energy generated from the pulp production process and wood bark gasification will power the mill. The new facility also plans to comply with the European Union's standards for Integrated Pollution and Prevention Control (IPCC).
Some 10,000 direct and indirect jobs will be provided by the new mill, with the objective of employing a largely South Sumatran workforce. Local job creation and economic development is a top priority for the province. PT OKI Pulp & Paper Mills will only use plantation wood for its raw material.
Aida Greenbury, director of sustainability at APP, said that "expansion of our production capacity is essential if we are to continue to meet customer demand and to further strengthen Indonesia's presence in global trade. Working together with its sister companies, local government, and other stakeholders, this new mill will continue to uphold and implement APP's Sustainability Roadmap Vision 2020 and our commitments to No-Deforestation. It will ensure that we can achieve sustainable economic development in South Sumatra, respect community rights, provide employment, and ensure that forest biodiversity is protected, across our entire supply chain."
The APP Group is one of the world's largest vertically integrated pulp and paper companies, with an annual combined pulp, paper, and converting products capacity of more than 19 million metric tons. APP-Indonesia and APP-China currently market their products in more than 120 countries across six continents. The majority of APP's production facilities are Chain-of-Custody certified by SVLK, LEI, and PEFC.
Back To Top
|
OfficeMax Inc., Naperville, Ill., USA, and Office Depot Inc., Boca Raton, Fla., this week provided an update on the integration planning process and expected annual cost-saving synergies related to the companies' proposed merger. The two companies had agreed to a merger this past February, and then on July 10, stockholders of both companies approved the merger. The transaction is expected to close by the end of this year.
The integration planning process has made significant progress since being launched in May:
- An Integration Management Office (IMO) has been established to guide day-to-day integration design and planning, ensure interdependencies and risks are identified, and make certain that mitigation plans are developed. The IMO has created an overall integration methodology and schedule, with clear governance guidelines.
- Twelve integration planning teams, co-led by senior leaders of both companies, have been formed with the goal of ensuring business continuity, customer and talent retention, and synergy attainment. These teams have completed team charters, identified Day One priorities and action plans, and developed detailed work plans for their functional areas. These teams are in the process of identifying the critical initiatives to execute after closing in order to deliver the expected synergies and begin integrating the companies, identifying best practices within the respective companies, and designing an operating model and organizational structure for the combined company.
- Five integration platform teams have been established and are executing detailed work plans to support the IMO and integration planning teams with project management, synergy development, communications, change management, and talent management.
- This collective integration team, comprised of more than 150 seasoned leaders from both companies and with the support of a dedicated BCG team, has extensive industry and functional expertise, broad experience in the design and development of efficiency capture programs, and integration planning expertise for mergers of varying scale.
Based on their integration planning work to date, the companies reaffirmed confidence in their ability to realize $400-$600 million of total annual cost synergies by the end of the third year following the close of the merger, with synergies categorized as follows:
- Purchasing Efficiencies: An estimated total of $130-$200 million in synergies are expected to come from purchasing efficiencies related to the combined cost of goods sold, including vendor optimization, and SKU harmonization.
- Supply Chain: Approximately $70-$100 million in estimated synergies are expected to result from combining the North American supply chains. The companies believe that supply chain network optimization, along with transportation and delivery efficiencies, will generate these significant savings.
- Advertising and Marketing: The companies estimate savings in the range of $70-$100 million from advertising and marketing efficiencies. A substantial amount of these savings are expected to result from reducing duplicative efforts in weekly inserts, media and catalogs.
- Selling, General and Administrative: An estimated $130-$200 million in savings is expected to result from sales and support function efficiencies and standardization of processes.
The companies believe approximately one third of the $400-$600 million range of synergies are achievable in the first year following the close of the merger. The companies also reiterated their expectation to incur approximately $350-450 million in one-time costs, including transaction expenses, and approximately $200 million in capital investment to achieve the cost synergies.
Back To Top
|
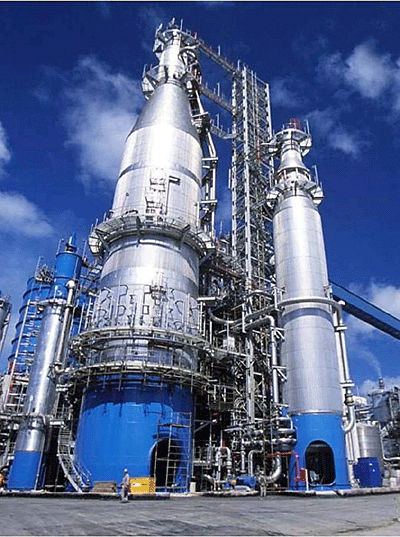 The 2013 TAPPI PEERS Conference in Green Bay, Wis., USA, September 15-18, focuses on advances and emerging developments in the kraft pulping and bleaching arena as well as the chemical recovery island. From the chemical pulp mill operating floor viewpoint, a series of sessions explore methods and approaches for improving and automating digester performance for a variety of grades and feedstock under a combination of conditions.
On Monday, September 16, Session S2 on Advances in Kraft Pulping, begins with a presentation on Nippon Paper's (Japan) electrolytic oxidation method to produce polysulfide (PS) liquor from white liquor, and demonstrates how the PS liquor was integrated into the mill's kraft pulping process to boost yield. The electrolytic process produces highly concentrated PS liquor at the anode and pure sodium hydroxide as well as hydrogen at the cathode. Nippon shows that the process is especially suitable for modified cooking, such as MCC or ITC in which the cooking liquor is split and charged into the multistage of a digester. PS liquor from the anode is added at the initial cooking stage with anthraquinone, and untreated white liquor is added at the additional stage. Sodium hydroxide derived from the cathode is used as the alkaline source for an oxygen delignification process instead of oxidized white liquor.
The second paper in Session S2 explores the optimization of batch and continuous cooking using alkali measurements and controls as well as kappa and residual alkali measurement-based feedback controls. As illustrated in this presentation, new developments in cooking—such as several alkali addition points and circulations—complicate process control and also mean new challenges for the measurement of pulp properties. At the same time, there are a lot of different disturbances present—wood age, density, chip size, white liquor concentration, etc. The paper introduces a control technology that goes beyond optimizing the temperature and alkali profile, and compares the actual measured profile to a "reference" profile, that allows conclusions about what is the original disturbance source (wood age, chip size, etc.) and makes a correcting action based on that. Multiple mill case studies are reviewed in this presentation.
The third presentation in Session S2 looks at factors important for continuous digester chip column movement and presents the results from a digester conversion at the BillerudKorsnäs Gävle mill in Sweden. As explained in this paper, most continuous digesters are 30 to 50 years old and in many cases production has been increased by 50% to 100%. In some cases, the kappa target and/or wood specie has also been changed. These digesters no longer operate under the conditions they originally were designed for. To produce pulp, the chip column must be moving, and this has become one of the most important tasks for the operator. As illustrated by the Gävle mill case study, the chip column movement in a two-vessel hydraulic digester can be improved by converting the digester to a two-vessel steam/liquor phase digester.
Other sessions at 2013 PEERS examine several additional breakthrough enhancements to chemical pulp production, including chlorine dioxide bleaching and oxygen and ozone reinforced bleaching technologies. These and other subjects covered at PEERS will be examined in subsequent issues of Over the Wire.
More information on the 2013 PEERS Conference, and more information on the International Bioenergy and Bioproducts Conference being held September 18-20 in conjunction with PEERS, are available online.
Back To Top
|
Below is the latest listing of job openings in the TAPPI Career Center. The current listing includes job openings for a variety of positions including project manager, senior development engineer, reliability manager, design assistant, and manager of laboratory, development, and quality. Current, specific job openings at companies and locations in the TAPPI Career Center include:
Employer |
Title |
Location |
AMEC |
Project Manager |
Tucker, Ga. |
Confidential |
Sr. Development Engineer |
New Hampshire |
Graphic Packaging International |
Sr. Reliability/Planning Engineer |
Georgia |
Homasote Co. |
Mgr. Lab, Development, Quality |
West Trenton, N.J. |
Rand-Whitney Containerboard |
Reliability Manager |
Montville, Conn. |
RockTenn Merchandising Displays |
Design Assistant |
Bentonville, Ark. |
More information about these jobs is available online.
Back To Top
|
Market Roundup
Total U.S. printing and writing (P&W) paper shipments were down 7% compared with June 2012, with total inventory levels increasing 4% from May, according to the AF&PA (Washington, D.C., USA) June 2013 Printing-Writing Paper Report issued this past week. Other key findings include:
- June shipments of coated free sheet (CFS) papers decreased 4% compared with June 2012, with year-to-date CFS shipments down less than 1% compared with 2012. U.S. imports of CFS papers increased 7% year-over-year in May.
- Uncoated free sheet (UFS) paper shipments decreased 3% year-over-year in June. For the year, shipments are down 4% in 2013. Imports of UFS in May increased 6% compared with May 2012, with exports of UFS up 5%.
- June uncoated mechanical (UM) paper shipments decreased 16% compared with June 2012, with year-over-year imports through May up 1%. UM exports are up 12% in 2013 compared with the first five months of 2012.
- Coated mechanical (CM) shipments in June decreased 16% compared with June 2012. Shipments of CM are down 13% for the year, with imports down 3% year-over-year in May.
Back To Top
|
In recent years, the huge demand for dissolving pulp has prompted many companies to build new dissolving pulp projects, leading to a rapid increase in dissolving pulp production capacity. This has particularly been true in China. According to a new report added to the Research and Markets (Dublin, Ireland) portfolio, titled " Research and Forecast of China Dissolving Pulp Market, 2013 - 2011 by 2012, the production capacity of dissolving pulp in China had reached 937,500 tons, up 57% compared with 2011. But during 2012, the output of dissolving pulp in China was only about 335,000 tons, with the operating rate declining to 35.7% by the end of that year.
The major use of dissolving pulp downstream is the production of viscose fiber. China is the world largest production base of viscose fiber and the output of viscose fiber in China accounted for about 62% of total global output in 2012. In future years, the output of viscose fiber in China is expected to continue growing at about a 10% rate, further spurring the increase of demand for dissolving pulp.
Research and Forecast of China Dissolving Pulp Market, 2013-2017 mainly analyzes the Chinese domestic market status quo and major enterprise operating conditions in the dissolving pulp industry. It also analyses the future of the dissolving pulp industry.
Back To Top
|
In 2012, world consumption of kaolin had recovered to almost 23 million metric tons, according to a new report on the industry by Roskill Information Services, London, England, compared with less than 20 million metric tons during the global economic downturn of 2008/09 when demand for kaolin weakened. Consumption is concentrated in Asia (36%), Europe (30%), and North America (24%), and differences in regional rates of growth will continue to reshape the industry. By 2017, Asia is forecast to account for 39% of total demand, followed by Europe (28%), and North America (23%).
The largest market for kaolin is as an extender or filler, mainly in paper and paint, but also in rubber, plastics, and adhesives/sealants. Other important markets are in ceramics, fiberglass, and refractories. In addition, significant amounts of unprocessed kaolin are used in some applications, particularly ceramics. The relative importance of the two major markets for kaolin is forecast to change, with paper remaining the largest market but its share falling to 36% in 2017, compared with 39% in 2012, while ceramics grows to 31%, up from 29%, according to the Roskill report.
Asian production of paper grew by an average of more than 5% per year during the past decade to become the largest of any region, the report continues. Production elsewhere grew by less than 2% per year and declined in North America. Global paper and board production is forecast to rise by 2.5% per year to 2017, but Roskill expects demand for minerals to rise at a higher rate, especially in regions such as Asia where pulp costs are high. Much of the rise in demand will be for calcium carbonate rather than kaolin, however. Demand for kaolin in paper is therefore forecast to grow by an average of only around 1% per year to 2017.
Output of kaolin in Europe has recovered since 2009, despite capacity closures in the U.K., one of the main centers of production within the region. Production in North America has been declining because of competition with calcium carbonate and imports from Brazil. This has led to industry consolidation. IMin of the U.S. bought Huber's kaolin division to form KaMin in 2008 and later acquired CADAM of Brazil. Imerys bought PPSA in 2010 followed by Itatex in 2012 and is now in the process of buying Goonvean's kaolin operations in the U.K.
In Asia, production has been stimulated by rising regional demand for paper and ceramics and is now the second largest of any region. Output in the Middle East has risen to supply the expanding regional ceramics industry while in South America, production is export driven and closely linked to consumption by the global paper market.
Roskill's analysis shows capacity is currently sufficient to meet expected demand in most regions, meaning few new operations or expansions are expected. The main exception is China where capacity could increase by at least 0.7 million metric tpy by the end of 2013. A new operation will also reach full operating capacity in the U.S. in 2014. Energy is a significant proportion of the overall cost of producing kaolin. The fall in U.S. natural gas prices may make producers in that country more competitive and lead to a rise in exports. This may have a negative impact on producers elsewhere, particularly those that supply paper grades.
More information about this report is available online.
Back To Top
|
The global market for folding cartons is growing by 5.1% annually, and will reach $184 billion by 2018, according to a new study by U.K.-based Smithers Pira. Market growth will be led by increased demand for health care products, cigarettes, dry foods, and frozen/chilled foods, especially in the emerging economies.
The Future of Folding Cartons to 2018 outlines the shape of the industry globally by end-use sector, region, and country, through extensive primary research. With strategic forecasts to 2018, plus details of key market drivers and opportunities, it analyzes major drivers and trends shaping the industry, and provides exclusive exploration of end-use markets and current and future worldwide demand.
Three key technologies that will result in added value in the folding carton market between 2013 and 2018 are retail-ready packs (mainly in microflute), anti-counterfeit systems, and barrier coating technologies. Retail-ready packaging is a growing trend among retailers striving to reduce their costs and comes in the form of corrugated/microflute systems, rigid plastic, and some rigid board products. Anti-counterfeit technology used in folding carton applications is expected to almost double with high growth expected, especially in the health care sector. Developments in water-based coatings, nano-materials, bio-polymers, and antimicrobial compounds are leading the growth for barrier coatings.
According to Smithers Pira, a global trend towards smaller packs will be offset by an increase in demand for single serve portion packs. Smaller packs tend to use more total packaging material than the larger packs they replace, for the same volume of packed product.
The need for continual brand differentiation in the crowded marketplace is the impetus of growing demand for innovation in printing methods, with an increase in such technologies as QR codes, holographic images, Fresnel lenses, and other 3D devices. The technological developments in printed electronics are bringing the development of smart packaging closer to fruition as costs are decreasing.
The following graph shows the top 10 end use markets for folding cartons in 2012:
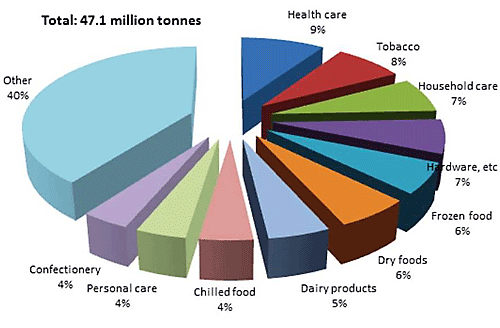
Consumer electronics continue to offer great opportunities for folding cartons and microflute packs with the continued global growth in demand for mobile phones, tablets, and other personal devices.
The health care sector, accounting for nearly 10% of the folding cartons demand, will see a call for the development of smart packs able to provide a system for monitoring patient medication. The level of counterfeit goods, and the health threats these products pose, is stimulating demand for sophisticated track-and-trace systems in the form of either 1D barcodes, 2D barcodes, or RFID systems.
Global demand for convenience foods and the development of niche markets such as low calorie products are growth opportunities for both the dry and frozen foods sectors. In the confectionery market, perceived over-packaging has been a focus of consumer discontent, leading to considerable innovation in the packaging of seasonal products such as Easter eggs and Christmas gift packs.
According to the report, personal care market has shown a rapid recovery from the global recession and growth is being stimulated by the use of technology in the form of social media, mobile commerce, and in-store digital technologies, targeting the tech-savvy young consumer. Eco-friendly brands are gaining prominence and demand for innovating printing techniques such as Fresnel lenses is growing.
Globally, cartonboard production grew by 1.3% in 2012 to reach a total of 42.5 million metric tons, valued at $37.3 billion, with more than half of this volume located in the Asia-Pacific sector. The top five producers of cartonboard constituted almost 16% of the total volume in 2012, with the top 10 making up over a quarter. The 20 largest producers accounted for 40% of the market. Total volume of converted folding carton grew by more than 1% to reach 47.4 million metric tons in 2012, with 55% of this emanating in the Asia-Pacific sector. The five largest cartonboard converters make up almost 7% of this somewhat fragmented market, while the 10 largest converters accounted for more than 9% of the volume in 2012.
Back To Top
|
Pulp & Paper
Buckman, Memphis, Tenn., USA, this week announced the formation of a new company, Buckman North America, under which the current Buckman Canada and Buckman U.S. organizations will be brought together into a single operation. The new company will begin operating immediately and will be based out of Buckman's global headquarters in Memphis. The company will also maintain operations at the current Buckman Canada location in Vaudreuil-Dorion, a suburb of Montreal.
Jim Doan, will serve as president of Buckman North America, and Pete Tchouros will serve as GM of operations for the new company.
"When fully operational, this new Buckman North America structure will give Buckman associates in Canada and the U.S. increased access to technical knowledge, encourage sharing of best practices, and enhance abilities to serve our customers," said Doan. The transformation to Buckman North America will be seamless from a customer perspective, with no business interruption, Doan added.
The creation of Buckman North America follows similar organizational changes made around the world as a part of the OneBuckman global business model that is focused on maximizing efficiency, synergy, and customer responsiveness that result in a stronger company poised for continued growth. This new geographic organization is similar to the structure of most of Buckman's customers.
With the creation of Buckman North America, Buckman now has six geographically organized operating companies focused on customer needs around the world.
Back To Top
|
Grigiskes AB, Lithuania, has ordered from Toscotec, Italy, a new tissue line. The new line will have a maximum production capacity of 110 metric tpd. Grigiskes is Lithuania's only producer of tissue products, having worked in this type of business for 190 years. The company is a leading regional player in pulp and paper, packaging, and wood industries, employing around 900 people, with a yearly turnover of some EUR 84 million.
The new Toscotec's line includes an AHEAD-1.5S crescent former tissue machine with a single-layer headbox, single press configuration, a steel yankee dryer (TT SYD-15FT), machine auxiliaries including vacuum pumps, stock preparation plant for virgin pulp, and electrification and control system. Milltech, a Toscotec associate, also will be involved in the project, providing a natural gas heated hood with three stages of heat recovery, machine dust and mist removal system, and a hall ventilation system. A two-unwind-stand tissue slitter-rewinder (TT WIND-M) and an automatic roll handling system complete the supply.
The machine design speed is 1,900 m/min. with a net web width of 2,750 mm. The project will be managed by Toscotec on an EPC (engineering and procurement) basis.
Grigiskes has been in operation since 1823, when the first paper mill was founded in Kuckuriskes that later was incorporated into the Grigiskes Group. Over many years, the company expanded and grew into the biggest pulp and paper producer in the Baltic Region. Today, Grigiskes Paper Mill is a private company belonging to the Grigiskes AB Group, operating three paper machines with an annual tissue paper capacity of 28,000 metric tons.
Grigiskes owns the brands called Grite and Grite Professional. Today, Grite is a well known brand not only in the Lithuanian market, but in all of the surrounding countries as well. Grite has a wide variety of consumer hygienic paper and away-from-home products, including toilet paper, towels, napkins, handkerchiefs, folded towels, wiping paper, etc. With a market share of 41% for toilet paper and 33% for kitchen towels in Lithuania, this company exports more than 60% of production to 22 countries worldwide.
In early 2011, the company had modernized the dry section of existing TM 5 with the installation of a Toscotec steel yankee dryer (TT SYD-4200MM). The project was successful, with 25% energy savings and 40% capacity increase. The good cooperation between the two companies has driven the decision to continue with this new order.
Back To Top
|
Kimberly-Clark Corp., Dallas, Texas, USA, has named Voith Paper Fabric & Roll Systems (FRS), Wilson, N.C., "2012 Supplier of the Year." Voith Paper FRS' ongoing advancement of fabric technology was the key factor in K-C's selection of Voith for the award. Voith also supports K-C with a Total Roll Management program and tissue cylinder service.
"Voith Paper Fabric & Roll Systems is part of a very elite group by being selected as one of Kimberly-Clark's top seven suppliers around the globe," said Cynthia Dautrich, global procurement officer for K-C. "Voith serves as an exemplary model of what Kimberly-Clark values in supplier performance and is helping provide a framework to develop and implement best practices."
A Global Supplier Criterion was followed to identify, evaluate, and select K-C's top vendors from its 75,000 global vendors that demonstrate above and beyond compliance of reliable on-time delivery, quality performance, sustainability, and innovation, among other factors.
"We're honored to receive this award from Kimberly-Clark, one of our highly valued customers," said John Fox, SVP at Voith Paper FRS. "It's gratifying to be recognized and to know that our products and services truly help advance our customers' position in the market."
In the photo,(l-r) of Voith Paper FRS receiving the K-C award are: Jerry Baker, VP Family Care R&E, K-C; David Buchanan, VP Sales, Voith Paper FRS; Cory Riehl, Tissue Product manager, Voith Paper FRS; Mark Buthman, CFO, K-C; John Fox, SVP, Voith Paper FRS; Tom Falk, CEO, K-C; Antony Morton, Specialty Products R&D manager, Voith Paper FRS; Bill He, VP Strategic Sourcing, K-C; Cynthia Dautrich, chief procurement officer, K-C; and Scott Prentice, global procurement category director, K-C
Back To Top
|
Weyerhaeuser Co., Federal Way, Wash., USA, has completed the acquisition of Longview Timber from affiliates of Brookfield Asset Management. The acquisition includes approximately 645,000 acres of high-quality timberlands in Washington and Oregon, which expand Weyerhaeuser's timber holdings in the Pacific Northwest by 33% to approximately 2.6 million acres. The transaction increases the total amount of U.S. timberlands Weyerhaeuser owns or controls to approximately 6.6 million acres.
"This acquisition is a truly unique opportunity for us to grow our high-value timberlands assets west of the Cascade Mountains," said Dan Fulton, president and CEO. "This region provides excellent soil and climate conditions for growing Douglas fir, which is a preferred species for many of our customers. We intend to leverage our silviculture, infrastructure, logistics, and marketing expertise to realize the full potential of these lands, which are highly complementary to our existing ownership in the area."
Weyerhaeuser owns or controls approximately 6.6 million acres of timberlands, primarily in the U.S., and manages another 14 million acres under long-term licenses in Canada. It also is one of the largest manufacturers of wood and cellulose fibers products, and develops real estate, primarily as a builder of single-family homes.
Back To Top
|
Weyerhaeuser Co., Federal Way, Wash., USA, has published its tenth annual sustainability report. The online report details the company's performance in 2012 and demonstrates its progress against more than 40 specific targets it will accomplish by 2020. The company's commitments, goals, and targets are organized under three sustainability pillars—performance, people, and planet.
A few highlights of Weyerhaeuser's 2012 sustainability achievements include:
- A 19% reduction in water use since 2007 in the company's Cellulose Fibers business
- A 28% reduction in greenhouse gas emissions since 2000, demonstrating solid progress toward the company's 2020 goal of a 40% reduction
- A 9% reduction in solid waste sent to landfills since 2010, which nearly meets the company's 2020 goal of a 10% reduction
- An average Home Energy Rating System score of 70 for the company's homebuilding businesses, indicating its homes are generally 30% more energy efficient than the HERS reference home
- More than 50% total shareholder return for the year
- A new Eco+ Innovation program, which tracks revenue and investments that show significant improvement in Weyerhaeuser's environmental performance or that enable substitution of renewable energy and materials for non-renewables
- Continued safety excellence, with a recordable incident rate of less than one
- A new Leadership Development Framework designed to strengthen the company's leadership pipeline and bench
- A $4 million investment of cash donations, in-kind giving and employee time spent in support of Weyerhaeuser's operating communities
- The launch of a successful Employee Volunteer of the Quarter program that celebrates Weyerhaeuser employees who make a significant impact in their communities through volunteerism.
Weyerhaeuser was also the recipient of more than 20 third-party awards and recognitions in 2012 and early 2013. For the second year in a row, the company was included on the Dow Jones Sustainability World Index, and it was also named one of Corporate Responsibility Magazine's 100 Best Corporate Citizens and one of the World's Most Ethical Companies by Ethisphere Institute.
Back To Top
|
Containerboard/Packaging
Pratt Industries, Conyers, Ga., USA, this week reported that its Conyers mill has made its 6 millionth ton of 100% recycled paper. The Conyers facility, the first Pratt-built mill in the U.S., reached the landmark number on July 24, some 18 years after startup. Ironically, the 6 millionth ton was 26-lb.—as was the first ton back in 1995.
Since then, the mill notes, its recycling has saved the equivalent of more than 100 million trees and prevented 480 million truck loads of discarded paper from possibly going to landfill.
Pratt CEO Brian McPheely extended a company-wide "well done" to the Conyers team. "This is another great day for both Pratt Industries and all of the people who have worked at the mill over the years," he said. "Congratulations to you all. Wow! More than 6 million tons of paper—well done and thank you!"
Mill manager Allen Bowdler echoed those sentiments, saying the milestone was a tribute to hard work and dedication. "This type of achievement is a reflection of the dedication and effort put forth by all of the Pratt Paper 12 team members, past and present," he said. "It's my honor to have been part of this team and I couldn't be more proud of all those who contributed."
More information about the 6 millionth ton at Conyers is available online.
Just a month ago, Conyers' sister mill in New York City celebrated the production of its 5 millionth ton. More information about this achievement is also available online.
Back To Top
|
Rengo Co., Japan, has begun construction to renew a containerboard (linerboard) machine at its consolidated subsidiary Marusan Paper Mfg. Co. in Japan. Marusan Paper, Rengo Group's production center for containerboard in the Tohoku region, currently produces about 20,000 metric tons of containerboard per month using two paper machines—PM 6 for linerboard and PM 7 for corrugating medium.
PM 6, installed in 1973, was damaged during the Great East Japan Earthquake in March 2011 and, the company explains, has become difficult to respond to recent needs for lightweight containerboard. For that reason, Rengo decided to renew PM 6 to serve the current needs of the market, and to further improve product quality while striving to conserve energy and resources. A groundbreaking ceremony was held July 19, and operation of the machine is scheduled to start in January 2015.
This renewal is intended to ensure Marusan Paper Mfg.'s continued growth. It is also aimed at enhancing the Rengo Group's containerboard supply system in the Eastern Japan region and improving mid- and long-term performance by further strengthening the integrated production system from containerboard to corrugated packaging.
Back To Top
|
Smurfit Kappa Group, Ireland, has completed refinancing of its existing senior secured credit facility with a new five-year unsecured relationship bank facility. In connection with the refinancing, the collateral securing the obligations under the Group's various outstanding senior notes and debentures has also been released and the senior notes and debentures are therefore now unsecured. The transition of the capital structure from secured to unsecured reflects the re-positioning of SKG's credit profile from leveraged to corporate.
The new EUR 1.375 billion, five-year facility includes a EUR 750 million term loan with a margin of 2.25% and a EUR 625 million revolving credit facility with a margin of 2.00%, reduced from margins of 3.75% and 3.25% respectively.
The Group expects cash interest savings from the refinancing will be approximately EUR 13 million per annum and the transaction will be immediately earnings accretive. There will be a one-off exceptional cost of approximately EUR 16 million arising from the accelerated amortization of unamortized deferred debt issue costs related to the existing facility.
The transaction was initially launched at EUR 1.100 billion and was upsized to EUR 1.375 billion following a substantial oversubscription. A total of 22 banks, all of whom are SKG relationship banks, have committed to the new facility.
In addition to the new senior facility, SKG has put in place a five-year trade receivables securitization program of up to EUR 175 million utilizing the Group's receivables in Austria, Belgium, Italy, and the Netherlands. The program, which has been arranged by Rabobank and carries a margin of 1.70%, will complement the Group's existing EUR 250 million securitization program.
Back To Top
|
New Products
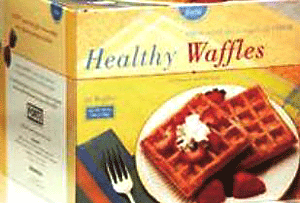 Dura-Fibre, Menasha, Wis., USA, reports that many of its folding carton substrates, including Forte, Eclipse, and Blanc, now feature a kraft liner that provides enhanced wet durability, quality, and consistency. The company explains that for the folding carton industry, freeze/thaw applications are particularly challenging, as moisture can cause packaging to lose its integrity and warp or tear.
Dura-Fibre's heavy weight folding carton substrates combine the natural kraft liner with a superior print surface for excellent printability, stiffness, and tear and internal strength properties. These combinations of boards laminated together provide for superior freeze/thaw packaging applications, Dura-Fibre notes.
Compared with corrugated materials, these folding carton substrates provide improved refrigerator freeze/thaw for indirect food contact. As the company points out, corrugated materials have difficulty holding up through multiple cycles of freeze/thaw due to air trapped in the flutes. The trapped air begins to break down the flutes and glue, causing performance of the carton to fail. Dura-Fibre's substrates combine a natural kraft liner with a superior print surface for excellent printability, stiffness, and tear and internal strength properties—holding up after multiple freeze/thaw cycles.
Back To Top
|
Eaglewood Technologies, Minneapolis, Minn., USA, makers of Sani-Blast™ Anilox Roll Cleaning Systems, has begun a partnership with corrugated machinery supplier, The Haire Group, to offer the Sani-Blast Anilox Roll Cleaning systems. The Sani-Blast systems clean rolls on-press or off-press with a proprietary blend of Arm and Hammer baking soda.
According to Pete Mulheran, president of Eaglewood Technologies, "the Haire Group is a leader in equipment sales to the corrugated industry and understands the importance of maintaining clean anilox to eliminate variables in the print process. The partnership is a perfect fit for Eaglewood Technologies. Our Sani- Blast system demonstrated such great results at one of their customers' that it has already resulted in a sale."
Ken Andersen, Haire's new machinery product manager, added, "the symmetry between our two companies only enhances the complementary benefit of the Sani-Blast system's design, and I believe our customers will embrace Eaglewood Technology's proven results and continued support. We foresee a long and mutually beneficial partnership as we move forward together."
Back To Top
|
NewPage Corp., Miamisburg, Ohio, this week announced Anthem® Plus™, a new, economy coated paper designed to perform in virtually every print application. Anthem Plus is 90 brightness with a pure blue-white shade, and is available in gloss, dull, and matte finishes ranging from 60 lb. text to 110 lb. cover.
Anthem Plus is stocked in press-ready mini skids and cartons for maximum efficiencies. It is chain-of-custody certified to the Forest Stewardship Council (FSC), the Sustainable Forestry Initiative (SFI), and the Programme for the Endorsement of Forest Certification (PEFC) to support sustainable forestry practices
"Customers including merchants, printers, and end users have been asking for a simplified economy sheet offering from NewPage with 90 brightness, a competitive price, good on-press performance, and breadth and depth of inventory," said Jeff Pfister, commercial marketing manager, economy sheets for NewPage. "So we listened to our customers and we went to work developing an improved product and service offering that meets or exceeds all expectations. The result is Anthem Plus."
Until now, NewPage offered multiple economy sheet brands with different attribute packages and value propositions. These brands included Anthem, Fortune, and Gusto. With the introduction of Anthem Plus, the company will be discontinuing Fortune and Gusto coated sheets.
"Last year, we made a major shift at our customers' request with the introduction of Sterling® Premium," stated Steven DeVoe, VP of marketing for NewPage. "Sterling Premium shifted the definition of premium grades to reflect the times, delivering a better option for customers looking for premium print performance. Now we bring our customers another shift in our grade offering with the introduction of Anthem Plus. No other coated paper producer currently offers the breadth and depth of this product and service line-up, and we are excited about the potential to continue to grow and evolve with our customers."
Back To Top
|
People
Asia Packaging Group Inc. China, reports that Brian Birmingham, VP and director of the company, has resigned. Wenge Hong, president and CEO, said that "we would like to thank Brian for his contribution to Asia Packaging and wish him all the best in his future endeavors."
Asia Packaging Group, through its wholly-owned subsidiaries in the People's Republic of China, provides packaging products and services to the food, pharmaceutical, and retail industries in China.
Back To Top
|
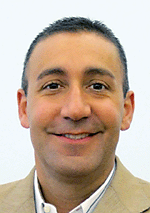 Finch Paper, Glens Falls, N.Y., has appointed Rob Ferragina national sales director. Ferragina reports to Debabrata Mukherjee, President and CEO, Finch Paper.
As National Sales Director, Ferragina leads a team of sales executives in the opaque, text and cover, and digital paper markets. His extensive experience in premium, white paper sales complements Finch's product portfolio, the company noted. He will also work closely with Sheldon Spicer, national sales director—corporate accounts, and Philip Hart, director of commercial operations to develop a diversified portfolio of products and services to meet the changing needs of the marketplace.
Ferragina has more than 15 years of industry experience in Metro New York, most recently with Mohawk as regional sales manager, northeast, with responsibility for sales from Maine to Virginia. He has also represented Fox River and Fraser in his career. Ferragina holds a Master of Administrative Science from Fairleigh Dickinson University and Master of Arts in History from Monmouth University.
Back To Top
|
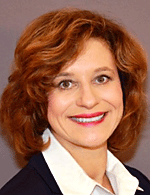 Darlene Kober has joined Hexacomb, Buffalo Grove, Ill., USA, a Boise company, as director of global marketing and strategy. Kober has more than 20 years of experience with multinational manufacturing corporations serving diverse industries such as packaging, specialty industrial products, medical devices and chemicals. She has held marketing and sales roles of increasing responsibility at Baxter Healthcare, Danaher Corp., Morton International, and Air Products and Chemicals.
Most recently, Kober was director, global marketing for Baxter Healthcare where she reshaped business unit strategy and initiated an acquisition that brought state-of-the-art technology to customers. Previously, she led marketing efforts for industrial coding and marking leader Videojet Technologies, a division of Danaher Corp.
Kober holds a Master of Business Administration in marketing and strategy from the Kellogg School of Management at Northwestern University and a Bachelor of Science in chemical engineering from Bucknell University. She is active in the Chicago chapter of the Business Marketing Association, serving on the Education Committee to elevate the focus of business-to-business marketing within MBA marketing curriculums.
Hexacomb is a producer of paper-based protective packaging and display boards. It has nine production facilities in North America and three in Europe.
Back To Top
|
Mario Gosselin, CEO of Kruger Products L.P., Mississauga, Ont., Canada, this week announced that Rob Latter has been named corporate VP, Away From Home (AFH) Division and Strategic Planning. In his new role, Latter is responsible for maintaining the company's dominance in the Canadian marketplace as well as strategically growing its presence in the U.S. The AFH Division represents a significant growth opportunity for Kruger Products and is well poised for future expansion.
"The segments we serve are dynamic and as the market leader in our industry, our customers increasingly look to us to help alleviate their evolving challenges," says Rob Latter. "With my team, I intend to navigate these challenges and strengthen our distributor and customer relationships, while continuing to grow our business in new directions."
Latter first joined Kruger Inc. in 1997 as sales manager for the Kruger Packaging Division. Over the next number of years, he proved invaluable to the company, and in 2001 assumed the role of VP, AFH Division, where he drove his team to bolster its market dominance in Canada. He remained in this role before returning to the Packaging business as VP in 2007.
Latter holds a bachelors degree in Business Administration from Concordia University and is the outgoing president of the Canadian Corrugated Containerboard Association. He takes an active role in the company's corporate social responsibility initiatives, including support of its long-time beneficiaries Friends of We Care and Ronald McDonald House Charities.
Back To Top
|
TAPPI News
Aug 6-7, 2013
Western Michigan University, Kalamazoo, MI
Pre-registration closes tomorrow, Friday, August 2 for the ground-breaking workshop Building Electronics on Paper – Why, How & Who at Western Michigan University in Kalamazoo, MI.
Join us on August 6-7, 2013 along with companies such as Appvion, Brother International, Cambridge Display Technology, DuPont, EMD Chemicals, Gentex, Goss, Kellogg's, Kodak, Konica, Jabil, MeadWestvaco, Sappi, Verso Paper, and others to hear and discuss advancements and challenges in building electronics on paper substrates.
Paper can take on incredible properties when combined with new nanomaterials, some very capable of holding the strict geometries demanded by electronic circuitry. Meanwhile, electronic-conducting materials are being developed that hold their shape and transfer electrons at acceptable rates for many applications.
Paper 360° is the media sponsor and TAPPI members receive a substantial registration discount. Use discount code: PAPER360.
Join us as we explore applications that can take advantage of these new capabilities and where paper and electronics become compatible. Gain an understanding of the processes and methodologies being created by a wide range of enterprising companies and research institutes, starting with our host, the Center for the Advancement of Printed Electronics (CAPE) at Western Michigan University.
This workshop is close to reaching its maximum participants. Register now to ensure your attendance and access to the networking dinner.
See workshop details and register today.
Back To Top
|
TAPPI member Hideki Fujiwara, Ph.D., has hit a lot of high notes in his long and illustrious career in the pulp and paper industry. Not the least of which occurred as a result of his nearly three decades of membership, including being the first member from Asia to be honored with the Charles W. Engelhard Coating and Graphics Arts Division award.
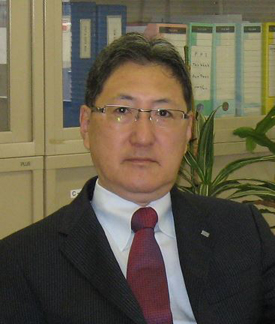 Dr. Fujiwara, who retired in June after 38 years in the industry, spent the majority of his career with Nippon Paper, serving in a variety of managerial positions. He credits his active involvement in TAPPI with providing ample opportunities not only to receive, but to share technical ideas and innovations with other professionals from around the world. Membership helped broaden his view of the forest products industry, and he notes that "joining TAPPI was the very first step to being a real professional in this field."
Find out more by reading this month's Member Spotlight. Spotlight participants are recommended by fellow members and staff. If you would like to nominate members, just send their name (or names) to MemberSpotlight@tappi.org. We will forward a Spotlight Questionnaire to fill out and return.
We look forward to seeing you in the Spotlight!
Back To Top
|
The Safety Management Leadership Course, August 26-27 in Metro Atlanta, Ga., USA, places a particular focus on leadership training, including incorporating a safe environment into workforce training and work expectations. Key safety topics are covered by the course, including:
- Safety Fundamentals / Modern Safety Management Principles
- OSHA Record Keeping and Medical Management
- Incident Investigation
- Safe Behavior and Choices
- Safety Culture
- Measuring Safety Performance
- Hazard Recognition
- Safety Walk-throughs, Observations, and Messaging
- Managing Change Safely
- Effective Safety Communication.
See more listed on the course schedule.
Meet the instructors.
Register for the Webinar Preview.
Tuesday, August 6 ♦ 1:00 p.m. EST ♦ 45 min.
This course is designed for anyone involved in workplace safety, including:
- Training and HR
- Safety Supervisors
- Team/Project Leaders
- Plant Managers
- Frontline Supervisors
- Safety Committees.
A special discount is offered for TAPPI and PPSA members. Register by July 26 for savings off the regular course rate.
TAPPI will award 1.3 CEUs to those who complete this course.
Back To Top
|
These 19 publications are all available for just one penny for a limited time during the month of August.
This offer will expire August 25.
The World In 2015: Four Possible Scenarios
Edited by: Stuart Sharp, chairman, The TAPPI Futurists
TAPPI Futurists explore issues that may affect the world and the paper industry in 2015. Four possible scenarios are presented based on expert opinion, scanning and monitoring, and extrapolation of trends. Each scenario is a description of the way the paper industry and the world may look 15 years from now, depending on the effects of various trends and issues. The book provides an opportunity for readers to think about the future and to plan and position themselves and their companies for what the future might hold.
The TAPPI Futurists is a group of TAPPI members whose purpose is to develop a long-term view of the paper industry to assist the Association in long range planning. This book was developed to provide a framework for readers to think strategically about the future. The book represents views and opinions of individuals from all segments of the pulp and paper industry, including manufacturers, suppliers, and customers. In addition, the Futurists worked with five non-paper industry companies to ensure that the scenarios would give a broad-based global view of the possible world 15 years from now.
Item Number: 0101R307
Process Engineering Design Criteria Handbook: Pulp and Paper Normal Design Criteria
Edited by: Thomas L. Abrams
This report presents design criteria guidelines important for existing mill modifications and for new mill proper design. A project of the Process Engineering Committee of TAPPI's Engineering Division, this comprehensive text features normal design criteria for kraft, TPM, and groundwood mills and includes everything from mill site preparation through paper production. Designed to benefit process, chemical, civil, electrical, mechanical, instrument, and construction engineers in mills or consulting firms, this report is sure to be a valuable addition to all engineering libraries.
Item Number: 0101R262
Industrial Environmental Control Pulp and Paper Industry, Second Edition, (Spanish)
By: A. M. Springer
Now in Spanish.
This classic text is a comprehensive reference on pollution control in the pulp and paper industry. It was written to promote further implementation of cost-effective environmental control by the pulp and paper industry. The Spanish version includes 18 chapters.
Item Number: 0102B056S
Pigments for Paper
Edited by: Robert W. Hagemeyer
Task Group Chairman: John E. O'Shea
This comprehensive text covers all aspects of pigments for paper. This unique book can serve as an introductory text as well as a practical reference. Well-respected industry experts who are specialists in their area wrote each of the12 chapters. This text provides the most current information on different ingredients, describing what they do and how they perform. It is a valuable reference tool for everyone involved in paper coating.
Item Number: 0102B062
Setting the Industry Technology Agenda
Edited by: Gerard Closset
Discover the innovative ideas proposed by Summit participants to meet the industry's greatest challenges. This text provides a summary of the Forest Products Industry's technology needs as identified by the participants of the 2001 Forest, Wood and Paper Industry Technology Summit. During this Summit, more than 130 leading experts from industry, supplier and service providers, government, and academia worked to identify, define, and analyze gaps in current technology and knowledge and then propose bold, breakthrough approaches to fill those gaps and meet the greatest needs and priorities of the industry. The book presents a compendium of those critically important technology needs, prioritized and aligned with the new industry technology strategy, including:
- Sustainable forest productivity
- Recycling
- Process automation
- Fiber engineering
- Process improvement/breakthrough technologies
- Ttechnologically advanced workforce
- Environmental performance
- Energy performance
- Nnew forest-based materials
- Wood products.
Reading this book is a must for anyone wishing to understand the needs and the direction of technology development for the industry. The book also features an Agenda 2020 retrospective and concludes with a discussion of the industry's path forward.
Item Number: 0101R307
Remember, this offer expires August 25, 2013.
Back To Top
|
Editor Mike Postek says, "Preparing this book has been an interesting process... we never thought there would be such an overwhelming response to our request....this book demonstrates that CNM are here to stay ....and will be an important component of the future economy.
"Having a document such as this at hand is extremely important as an information and marketing tool to inform administrators and decision makers about the future potential value of cellulose nanomaterials.
"Cellulose nanomaterials have not gained the level of interest they deserve because there has been a dearth of good education and marketing materials. This book should fill that need."
Anyone working in the nanomaterials field, or needing to understand the production and standards of the field, will want to add this volume to your reference material.
This new book includes:
- A collection of more than 100 two- to three-page summaries on recently completed and on-going research with these high strength materials
- A list of who's-who of research as well as leads on successful applications
- Topics on subjects such as production and modification, composites, other applications, modeling, and standards
- Special Feature: Actual Cellulose Nanocrystals included within the overcoat varnish of the cover.
Back To Top
|
This is a reminder that there will be two great golfing opportunities from Lake States TAPPI / North Central PIMA this summer.
August 13th is the annual golf outing at Mid-Vallee Country Club in De Pere, Wis. An afternoon shotgun scramble golf outing is planned with dinner to follow. Prizes will be awarded and individual pin events will be held. Proceeds help fund scholarships for local TAPPI and PIMA programs. Register online before August 9th .
August 27th PIMA will hold it's Golf Outing at Grand View Lodge of Pequot Lakes, Minn. The shotgun scramble starts at 9:30 a.m. Box lunch is included, with cocktail hour to follow. Net proceeds go to Lake States TAPPI/ North Central PIMA's Scholarship Fund. Details now available and registration is open.
Back To Top
|
The 2013 TAPPI Linerboard/Medium Manufacture Course, August 13-15 at the TAPPI Training Room, in Peachtree Corners, Ga., USA, is designed to help increase your understanding of linerboard and medium performance properties and manufacturing to improve corrugated box performance and runnability.
This intermediate-level course is ideal for process engineers and operators in linerboard and medium manufacturing facilities and converting plants with a more intermediate background. For those participants who require an overview background on pulp and papermaking technology, there will be an optional one day Introduction to P&P on Monday afternoon, August 12, prior to the beginning of the main course on Tuesday. This supplemental session is intended for corrugators, new P&P mill and supplier personnel, and those without exposure to pulp and paper operations.
If you are looking to increase your understanding of linerboard and medium performance properties and how they are achieved, build your confidence in interacting more knowledgeably within the mill with suppliers and with corrugators, and improve manufacturing operations to produce a more competitive product, then this course is for you.
There are only 25 seats available for this course. Register now to reserve your spot.
Back To Top
|
The TAPPI International Research Management Committee requests nominations be submitted for the Research and Development Technical Award and the William H. Aiken Prize.
The award is given for outstanding accomplishments or contributions that have advanced the technology of the paper and related industries in the field of research and development. The nomination should contain:
- A summary of the nominee's technical achievements
- The impact and relevance of the research on industry
- Education, work history
- Examples of the impact that they have had on others
- Other pertinent activity such as involvement in TAPPI.
The $500 prize is funded by an endowment from the estate of William H. Aiken, TAPPI president in 1967-1968 and vice president of technology for the former Union Camp Corp. at the time of his death in 1974. Dr. Aiken also won the TAPPI Gold Medal, the association's highest honor, in 1971. Nominations for the Research and Development Technical Award and the William H. Aiken Prize should be submitted by August 31, 2013, to Colleen Walker, cwalker@tappi.org at TAPPI, 15 Technology Parkway South, Peachtree Corners, Ga. 30092, USA, or fax +1 770-446-6947.
Back To Top
|
Your business can potentially save millions implementing improvements to paper machine performance and reliability.
The TAPPI Improving Paper Machine Performance Course, August 20-22, in Peachtree Corners (Metro Atlanta), Ga., USA., will allow students to see real world examples of paper mills that have made major improvements in overall efficiency by implementing many small improvements across their operation.
Jim Atkins will lead you through a real mill improvement project and show you how you can do the same thing in your mill. Dick Reese will show you how to make big savings in energy costs by correcting problems that often require little or no capital expenditures. Chuck Klass will teach you how to evaluate size press and coating operations to get the most out of what you have. And Ken Hill will give you the tools you need to evaluate and benchmark dryer systems, so you can correct problems and dry more paper.
This is an advanced level course. Students who complete this course will know everything required to save their company millions of dollars through paper machine performance improvements.
Learn more about this course.
Register online.
Back To Top
|
Registration is now open for the 2013 TAPPI Corrugated Press Hands-On Maintenance Workshop, September 17-18 at the Global Equipment USA Warehouse in Skokie, Ill., USA.
This unique course gives you an unprecedented opportunity to get hands-on training on how to audit converting machines. With only 18 seats available, you will have ample opportunity to get your questions answered by instructors Tom Pearce (Pearce Corrugated Consulting), John Bingham (Pamarco), Jim Wegemer (INXinc), Chuck Bobeldyk (Mark-Maker Co.), Randy Kesselring (MarquipWardUnited), as well as representatives from Global Equipment. The schedule for this course is packed into just two efficiently planned days so that participants get loads of skill and experience without much time away from their own operations.
Who should attend?
This Intermediate-level course offers indispensable hands-on maintenance training for corrugated industry plant managers and supervisors, engineers, maintenance teams, and machine operators.
You could pour over all of the how-to manuals available and still not retain this level and quality of working knowledge. Completing this workshop will enable you to:
- Use the basic tools to mechanically audit and troubleshoot a press
- Understand press audit procedures for process centering, better quality products, and increased productivity
- Discuss anilox roll selection, press "fingerprinting," inks and substrates, quality defects amd cause(s), and scoring.
Register by August 16 and join TAPPI or renew your membership to receive the best rates.
Back To Top
|
There's still time to be part of the program at the 2014 TAPPI PLACE Conference, May 12-14, 2014, at the Sawgrass Marriott Hotel in Ponte Vedra, Fla., USA. The 2014 PLACE Technical Program Team is actively seeking technical presentations, panels, tutorials, roundtables, and case studies from the packaging and academic community to be presented at the conference.
View the Call for Abstracts.
Interested in being a session chair or know someone who would be a great presenter? Extended abstracts will be accepted anytime before September 6, 2013. Space is limited so submit now! Final papers will be due on or before March 17, 2014.
The 2014 PLACE Conference is the premier North American event for the flexible packaging industry and will have something for the whole supply chain including suppliers, converters, extruders, retailers, and brand owners. This event not only offers top notch technical presentations but also allows ample opportunity for networking with your peers. Visit the event website for additional conference information.
Back To Top
|
TAPPI invites submissions of basic and applied research articles, communications, and technical reviews to TAPPI Journal, the world recognized peer-reviewed research publication. TAPPI is the leading association for the worldwide pulp, paper, packaging, tissue, nonwovens, and converting industries, with more than 7,000 members globally.
Authors presenting papers at conferences, experts with significant industry findings, and students or professors reporting academic research − any authors performing relevant industry research − are encouraged to submit their manuscripts.
Why submit your work to TAPPI Journal?
High visibility: Publishing in TJ makes your work accessible to professionals, libraries, and the global academic community through TAPPI's robust communications network.
TJ electronic issue: Distributed to thousands of TAPPI members every month, TJ features abstracts, full papers, author notes, and more.
Print compendium: Members also receive TJ's annual print compendium, a bookshelf reference volume containing abstracts of every paper published that year. The compendium is distributed to more than 250 libraries, industry organizations, and academic institutions around the world.
Paper360°: Summaries of select TJ papers appear in Paper360°, TAPPI's bi-monthly magazine with a global circulation of more than 40,000.
Online library: Papers published in TJ become part of TAPPI's e-Library available online. Searchable by subject and author name, the e-Library allows worldwide access to abstracts and downloadable full papers.
Indexing: Every issue of TJ is indexed by Thomson-Reuters, the world's leading citation index for academic research.
Career enhancement: Our stringent peer-review process and distinguished Editorial Board have made TAPPI Journal a well-respected, commonly referenced source of the best industry research for more than 60 years. TJ publication is an excellent way to gain attention from colleagues, peers, and current or future employers.
Author-focused process: Editorial Board members carefully marshal every paper submitted, based on area of expertise; TJ peer reviewers are selected for their proven subject knowledge. These experienced professionals – most of whom are TJ authors themselves – work with authors to ensure that papers meet TJ's high standards and are presented clearly and accurately.
Easy to submit: Papers may be submitted by email to Jeff Wells at TAPPI. Complete author guidelines are available online. (Please note: Papers must be submitted by the author; TAPPI Conference papers are NOT automatically reviewed for TJ publication.)
We look forward to receiving your work!
Back To Top
|
The soon-to-be-published, "Production and Applications of Cellulose Nanomaterials" is the latest TAPPI Press product to broaden the industry knowledge regarding who is researching nano technologies as well as leads on successful applications.
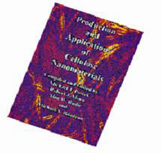 Anyone working in the nanomaterials field, or needing to understand the production and standards of the field, will want to add this volume to their reference material. Cellulose nano-crystals and cellulose nano-fibrils have been known for 20-50 years, but recent research suggesting very high strength properties and other unique physical properties have generated extensive interest in these materials.
Pre-order your copy today and save!
This new book will include:
- A collection of two to three page summaries on recently completed and on-going research with these high strength materials
- A list of who's-who of research as well as leads on successful applications
- Topics on subjects such as production and modification, composites, other applications, modeling, and standards.
- Special feature: Actual cellulose nanocrystals included within the overcoat varnish of the cover.
Pre-order Price:
Member: $149
Nonmember: $149
After July 15:
Member: $189
Nonmember: $259
Product code: 0101R332
Back To Top
|
Make plans to attend the 2013 Building Sciences Committee Fall Meeting September 18-20.
The Building Sciences Committee has designed a strong technical program for production managers and engineers to provide firsthand knowledge to improve their fiberglass mat process with practical production-targeted papers.
This year's program will include papers on: Process Variation Reduction, Glass Sizing Basics; Burner Safety and Efficiency; Biological Treatment Case Study, Operator and Mechanical Training to Enhance Operational Effectiveness; IT Systems to Manage Roll Goods and Reduce Waste.
We are pleased that Tim Worms of 3M will return by popular demand to present his updated Roofing Market Overview and Forecast.
The meeting will be held at The Hilton Marco Island Beach Resort in Marco Island, Fla. USA. TAPPI has negotiated a very economical room rate of $109.00 per night per guest. This rate is good for TAPPI members for stays of any length from Wednesday, September 18, through Sunday, September 22. Group dinners Wednesday and Thursday evenings will provide opportunities to meet other manufacturing personnel and suppliers, and their cost is included in the cost of the meeting. These will be excellent networking opportunities.
Thursday's afternoon recreational activity (also included in the registration price) is a choice of golf, coastal fishing, or an afternoon at the spa. Non-registered spouses and guests are welcome to participate in the activities and dinners for the following costs: $60 per dinner and $95 for golf, fishing, or the spa treatment. They do not have to pay the conference registration fee.
Click here for additional meeting information.
Back To Top
|
The 2013 TAPPI PEERS Conference, September 15-18, in Green Bay, Wis., USA, has announced the detailed technical program focusing on sustainable manufacturing and other pressing business and technical questions faced by pulp and paper companies as they manage raw materials, assets, regulatory requirements, and production assets. Register now and save.
In addition to the peer-reviewed technical program, Keynote Speaker Robert Feeser, SVP of Packaging with MWV, will share his insights on the day-to-day challenges he faces as he oversees the company's primary mill-based manufacturing businesses in the U.S. and Brazil. PEERS will also offer exclusive networking opportunities and insight into new technologies that can help you optimize your mill operations.
For 2013, PEERS will be co-located with the 10th Research Forum on Recycling and the International Bioenergy and Bioproducts Conference, creating a value-added opportunity for you to expand your learning, networking, and resources by attending all three events.
Learn more about the TAPPI PEERS Conference.
Back To Top
|
Don't miss out on your chance to attend the Process Control of Stickies Workshop, taking place just before the TAPPI PEERS Conference.
Organized by Dr. Mahendra Doshi, current TAPPI JOURNAL Editorial Board Member and Founding Editor of Progress in Paper Recycling, the workshop will be held from 7:30 a.m. to 4:30 p.m. on Sunday, September 15.
The international workshop is designed for engineers, scientists, and technicians who want to get a handle on one of the difficult contaminants in paper recycling - stickies. The workshop will benefit anyone using recycled pulps, working in recycling mills, or affiliated with companies supplying equipment, chemicals, and recovered papers to the recycling industry.
Problems caused by stickies cost millions of dollars to the industry. As indicated above, experts from around the world together with highly experienced speakers from mills offer an excellent overview for managing and controlling stickies. If you could just save one hour of paper machine downtime it would pay for the workshop many times over.
Learn more about this important workshop.
Don't miss this golden opportunity to learn about stickies related issues at this one-day international workshop.
Registration Cost:
$295/member; $345/non-member (on or before August 16); or $345 (if registered after August 16).
Back To Top
|
Now's the time to make your plans to attend IBBC, September 18-20 in Green Bay, Wis., USA.
As the only industry event dedicated to advancing biorefineries in the forest products industry, International Bioenergy and Bioproducts Conference (IBBC) offers you a fresh look at biomass utilization. Sessions focusing on biomass supply and demand, biochemical and thermochemical conversion technologies, conversion pathways, and economic assessments – along with a Keynote Presentation from Linda A. Beltz, Ph.D., NPDP, Director, Technology Partnerships at Weyerhaeuser – can help you determine how to integrate these technologies into your mill.
For 2013, IBBC will be co-located with the TAPPI PEERS Conference, and the 10th Research Forum on Recycling, creating a value-added opportunity for participants to expand their learning, networking, and resources by attending both events. Offered just after IBBC, TAPPI's Biorefinery Course, can deepen your understanding of biorefinery strategies and emerging technologies and their design/implementation in a business strategy.
Learn more about IBBC.
Register by August 16 for best rates!
Back To Top
|
TAPPI CorrExpo 2013, October 7-9 at the JW Marriott in Indianapolis, Ind, USA,. is your one-stop pitstop to fuel your networking and relationship building needs.
Take advantage of these high-octane opportunities:
View the full program to fast track your CorrExpo experience.
Back To Top
|
As TAPPI is getting ready to celebrate its 100th Year Anniversary in 2015, we were wondering how much industry expertise we have in this great group of professionals.
So, we decided to post a discussion question on our TAPPI Social Media outlets. We asked, "How many years of paper and/or packaging experience do you have?"
Who knew such a simple question would have such an impressive response.
With more than 7,000 TAPPI members, all over the world, we have counted 650-plus years of industry experience! And that's just counting the first 30 people who have responded. Now you probably can't find that anywhere else . So why don't you join us?
From those "born" into the industry to third generation professionals. From paper to packaging, to sustainability, environment, tissue, converters, and consulting. This TAPPI network has something for everyone.
Become a part of this unique community of paper and packaging professionals, and add your expertise to our group, and network with others to learn something new.
Visit our website to learn more today!
Back To Top
|
The TAPPI Centennial Celebration will be a multi-year long series of outreach events and educational offerings showcasing the proud history and promising future of the global pulp, paper, packaging, and related industries. This once-in-a-lifetime event will expand public awareness, foster further connection, and provide outstanding opportunities for collaboration, growth, and investment in our future for all of those involved. Goals for the TAPPI Centennial Celebration are:
- To honor TAPPI's 100 years of connection, education, and advancement as a foundation for the sustainable success of our members, our industries, and the world we share
- To recognize the achievements of those who built our industry and to inspire those who seek to build its future
- To celebrate the contributions and innovations of the global pulp, paper, and packaging industries to human culture, commerce, health, and social advancement
- To sustain the industry and support its growth, vitality, and future through the TAPPI Foundation.
We invite you to be a part of this momentous event. The sooner you join us the more opportunities there are for recognition of your company, its products, and key innovations. Keep in mind that an early commitment allows you to spread your investment over multiple years' budgets.
For more information on sponsorship and volunteer opportunities please contact dbell@tappi.org.
The sponsorship prospectus can be downloaded online.
Back To Top
|
Do you have a history book gathering dust on your shelf? TAPPI's 100th year is coming soon and we are looking for donations to the TAPPI Library. Specifically, we are interested in histories of companies and mills in the paper and packaging industry (both producers and suppliers). Each donated book will have a bookplate in the front cover recognizing the donor. For more information please contact David Bell.
Please send books to:
c\o David Bell
TAPPI
15 Technology Parkway, South
Suite 115
Peachtree Corners, Georgia 30092
Back To Top
|
|
|
TAPPI Over the Wire | 15 Technology Pkwy. S. | Norcross, GA 30092 USA | Voice: 770.446.1400 | Fax: 770.446.6947
|
 |