 |
|
Weekly Spotlight
Sofidel, Italy, a producer of paper for hygiene and domestic use, reports that it has met its five-year target to reduce CO2 emissions by 11%, a target that was set in 2008 when the company joined WWF's international Climate Savers program
Learn More...
|
Kimberly-Clark, Dallas, Texas, USA, maker of bath tissue Cottonelle, says it is looking to open the door on bathroom conversation, adding that "toilet talk is about to go mainstream."
Learn More...
|
The nova-Institute, Berlin, Germany, has published a paper on agricultural feedstock use in industrial applications shedding light on the controversial public debate surrounding the industrial use of food crops or so-called first generation feedstock
Learn More...
|
With the completed acquisition of Longview Timber's approximately 645,000 acres of forestland in Washington state and Oregon in July, Weyerhaeuser Co., Federal Way, Wash., now owns or manages approximately 20.5 million acres of forestland in the U.S. and Canada
Learn More...
|
The American Forest & Paper Association (AF&PA), Washington, D.C., USA, is moving to the Capital's East End this November
Learn More...
|
This fall, TAPPI is providing a unique opportunity for North American suppliers to exhibit at the 2013 China International Paper Technology Exhibition and Conference (CIPTE)
Learn More...
|
Below is the latest listing of job openings in the TAPPI Career Center
Learn More...
|
Market Roundup
World demand for corrugated boxes will rise 4.2% per year to 234 billion square meters in 2017, according to a new report by the Freedonia Group, Cleveland, Ohio, USA
Learn More...
|
Pulp & Paper
Glatfelter, York, Pa., USA, this week reported that it has completed a preliminary assessment of the damage resulting from an August 7 fire at its facility in Gatineau, Canada
Learn More...
|
Fortress Paper Ltd., Vancouver, B.C., Canada, reports that the high pressure water pump at its Fortress Specialty Cellulose (FSC) mill was reinstalled on July 12, and the cogeneration facility operated for 20 days before being shut down due to pump failure
Learn More...
|
Taishan Gypsum, Foshan, China, has ordered from Andritz, Graz, Austria, a FibreFlow drum pulper to be installed at its paper mill in Tai'an City, Shandong province, China
Learn More...
|
During the past three years, EcoPlanet Bamboo, Chicago, Ill., USA, says that it has driven the development of commercial plantations of non invasive tropical clumping bamboo around one core pillar—to "set in stone the benchmarks and framework for the industrialization of bamboo as an alternative fiber in a way that addresses issues of social and environmental concern."
Learn More...
|
Jari Celulose, Papel e Embalagens, Brazil, plans to restart its pulp mill in Monte Dourado in the Brazilian state of Pará at the beginning of 2014, according to a report this week by EUWID Pulp and Paper, Germany
Learn More...
|
Minerals Technologies Inc., New York, N.Y., USA, has signed an agreement for a 14,000-metric ton satellite precipitated calcium carbonate (PCC) plant in Europe
Learn More...
|
Orient Paper Inc., Boading, China, has announced the sale of land use rights for its headquarters compound
Learn More...
|
The closure will remain in effect until the operating areas receive adequate rainfall and the temperatures improve.
Learn More...
|
Containerboard/Packaging
Productora de Papel, SA de CV (Propasa), Mexico, has begun producing containerboard on its rebuilt PM 3
Learn More...
|
Rengo Co., Kita-ku, Osaka, Japan, has acquired a 75% stake in TCG Rengo Subang (M) Sdn. Bhd., a wholly-owned subsidiary of its overseas joint venture company Thai Containers Group Co., Thailand
Learn More...
|
Summer Industries, Welcome, N.C., USA, a producer of spiral wound paper tubes, cores, and cans made from 100% recycled paperboard, this week announced the opening of a plant in Neenah, Wis.
Learn More...
|
The specialty chemicals group ALTANA, Wesel, Germany, has acquired the specialty coatings business of Henkel
Learn More...
|
|
New Products
This smaller, more discreet medication adherence package is designed to meet patient and pharmacist needs by enabling greater patient portability and improving pharmacy efficiency
Learn More...
|
Voith, Germany, reports that it is expanding its clothing portfolio for pulp production with a further-developed press fabric
Learn More...
|
People
Glatfelter, York, Pa., USA, has hired Brian E. Janki as VP and GM of its Specialty Papers Business Unit (SPBU), effective yesterday, August 14
Learn More...
|
Weyerhaeuser Co., Federal Way, Wash., has appointed Jeanne M. Hillman VP and chief accounting officer for the company
Learn More...
|
TAPPI News
PIMA hosted webinar is set for August 20 at 11 a.m. EDT.
Learn More...
|
Special $100 savings for the 25th Pulp and Paper Reliability and Maintenance Conference expires in a few days. Register now.
Learn More...
|
Share your experiences with a company's products or services with your peers in the industry, and enter for a chance to win a seven-night trip to Hawaii.
Learn More...
|
The TAPPI/PPSA Safety Management Leadership Course will be held August 26-27 in Metro Atlanta, Ga., USA. This course sold out in 2012 and course registration is limited to 30 participants.
Learn More...
|
August 27th PIMA will hold it's Golf Outing at Grand View Lodge of Pequot Lakes, Minn.
Learn More...
|
Being an active member means creating a network that spans the globe.
Learn More...
|
Nineteen publications offered at only 1 penny (plus shipping). Order now while supplies last. This event will not last long.
Learn More...
|
"The Production and Applications of Cellulose Nanomaterials" is the latest TAPPI Press product to broaden industry knowledge regarding who is researching nano technologies as well as leads on successful applications.
Learn More...
|
First, second, and third place prizes were awarded at this year's Nanotechnology and Renewable Materials conference held June 24-27.
Learn More...
The TAPPI International Research Management Committee requests nominations to be submitted for the Research and Development Technical Award and the William H. Aiken Prize by August 31.
Learn More...
|
The schedule for this course, September 17-18, is packed into just two efficiently planned days so that participants get loads of skill and experience without much time away from their own operations.
Learn More...
|
The 2014 PLACE Technical Program Team is actively seeking technical presentations, panels, tutorials, roundtables and case studies from the packaging and academic community to be presented at the conference.
Learn More...
|
The BSC, September 18-20, 2013, has designed a strong technical program for production managers and engineers in the fiberglass mat industry.
Learn More...
|
Authors presenting papers at conferences, experts with significant industry findings, and students or professors reporting academic research − any authors performing relevant industry research − are encouraged to submit their manuscripts.
Learn More...
|
Anyone working in the nanomaterials field, or needing to understand the production and standards of the field, will want to add the soon-to-be-published "Production and Applications of Cellulose Nanomaterials" to their reference material.
Learn More...
|
The Building Sciences Committee Fall Meeting will be September 18-20 at The Hilton Marco Island Beach Resort in Marco Island, Fla.
Learn More...
|
September event also co-located with Research Forum on Recycling and International Bioenergy and Bioproducts Conference.
Learn More...
|
Register today for the Root Cause Problem Elimination Training Course in Raleigh, NC, USA Oct. 8-10 and save an additional 10 percent with TAPPI.
Learn More...
|
Opportunity for engineers, scientists, and technicians who want to get a handle on one of the difficult contaminants in paper recycling - stickies.
Learn More...
|
Make plans to attend the only industry event dedicated to advancing biorefineries in the forest products industry.
Learn More...
|
The Mitsubishi Heavy Industries Corrugated Scholarship has been awarded to Michelle Blood of N.C. State University. The award will be officially announced during the 2013 CorrExpo Conference, October 7-9, 2013, in Indianapolis, Ind., USA.
Learn More...
|
TAPPI CorrExpo 2013, October 7-9, will be held at the JW Marriott in Indianapolis, Ind., USA, and will feature the classic golf tournment as well as an evening gala at the Indianapolis Motor Speedway.
Learn More...
|
Foundations of Leadership Excellence, Oct. 22-24, 2013, is focused on the fundamentals of leadership and management skills for emerging leaders, high-potentials, and area operating managers and other technical professionals.
Learn More...
|
Tighten-up plans to attend the Piping System Training courses planned for two locations coming this fall, October 2-3, in Chicago, Ill., and October 23-24 in Houston, Texas.
Learn More...
|
Join more than 7,000 TAPPI members across the world with 650-plus years of industry experience.
Learn More...
|
This once-in-a-lifetime event will expand public awareness, foster further connection, and provide outstanding opportunities for collaboration, growth, and investment in our future for all of those involved.
Learn More...
|
As TAPPI's 100th year approaches, we are looking for donations to the TAPPI Library.
Learn More...
|
|
Find us on Facebook
Network with us on LinkedIn
Follow us on Twitter
|
Weekly Spotlight
Sofidel, Italy, a producer of paper for hygiene and domestic use, reports that it has met its five-year target to reduce CO2 emissions by 11%, a target that was set in 2008 when the company joined WWF's international Climate Savers program. Sofidel is the only Italian company and the first worldwide in the tissue sector to sign up to WWF's Climate Savers program, which encourages companies to play a leading role in fighting climate change by pledging to reduce their greenhouse gases on a voluntary basis.
To meet its target, over a five-year period Sofidel has invested more than EUR 25 million in renewable sources (photovoltaic and hydro-electric), cogeneration (combined production of electricity and steam), and improvement works to increase energy efficiency (e.g., LED lighting).
Today the emissions produced by Sofidel's companies that were active in 2007 have been reduced by 11.1% (approximately 186,000 metric tons, roughly equal to the amount of emissions made by 150,000 Italian families of four in one year for their electricity consumption). Regarding specific emissions (emissions set against the amount of paper produced), Sofidel has recorded a reduction of 14.4%. Not only has the company met its environmental targets, these results are also significant because at the same time, Sofidel has been able to consolidate its position on the market, becoming the second largest player in Europe in the tissue sector.
"Meeting WWF's Climate Savers objective while at the same time significantly strengthening the company's position is proof that economic and environmental sustainability can go hand in hand. Reducing its CO2 emissions is just one of Sofidel's efforts to curb its environmental impact and to underpin a more general commitment: do more with less. Results obtained so far make us more determined to consider sustainability as a central lever for innovation and competitive consolidation," said Luigi Lazzareschi, CEO of the Sofidel Group.
In collaboration with WWF, Sofidel aims to consolidate its commitment to reducing emissions by 2020 and to extend these objectives to its newly-acquired plants in Europe and the U.S. The company's reduction in CO2 emissions is part of a wider commitment to sustainability that also sees the Group environmentally active in terms of responsible sourcing of raw materials (cellulose) and in limiting the use of water in the production cycle.
For its involvement in WWF's Climate Savers program, Sofidel was given the Award of Excellence within the framework of the Tuscany Eco-efficient Awards 2009-2010 by the Tuscany Region. It also received a special mention for the best environmental initiative at the Sodalitas Social Award 2012 by Fondazione Sodalitas.
Back To Top
|
Kimberly-Clark, Dallas, Texas, USA, maker of bath tissue Cottonelle, says it is looking to open the door on bathroom conversation, adding that "toilet talk is about to go mainstream." Cottonelle wants to get North Americans "talking about their bums and on the road to a better way to clean ‘down there' by using the Cottonelle Clean Routine—combining dry toilet paper and flushable wipes for a cleaner, fresher experience."
With the help of London-based immersive journalist, Cherry Healey, Cottonelle is helping consumers to "open up" about their bathroom behaviors and "makeover" their old toileting routine. And with a sleek, newly designed dispenser for Cottonelle Flushable Cleansing Cloths, Healey is set to start the conversation this week.
Unfortunately, since bathroom habits are not something that people regularly talk about, many people don't know that there is a better way to feel clean and fresh than just using toilet paper alone, Cottnelle says. According to a recent survey, it adds, one third of Americans find "wiping your bum" to be the most taboo topic likely because more than 50% say they were raised not to discuss what happens behind the bathroom door. However, it seems America is ready to open the door to this topic since 80% say they would be comfortable talking about bathroom habits with others.
"These things can be embarrassing subjects, but that's why I'm here...so we come out from behind the bathroom door to talk about it!" Healey explains. The commercial program launches this week with Healey leading the conversation on bathroom habits. Integrated marketing efforts span across media placements, retail and shopper marketing, public relations, digital, and advertising to drive awareness and encourage consumers to "Talk about Your Bum" on- and off-line.
As a documentary filmmaker, Healey isn't afraid to talk about things that others may shy away from, Cottonelle notes, adding that her humor and charm have helped people open up to her about all kinds of "taboo"-yet-common experiences—from sex to childbirth. As a user of the Cottonelle Care Routine herself, she'll combine her professional and personal experience to talk to everybody, everywhere about their bums, and how they can use the Cottonelle Care Routine to be ready...for anything.
Ironically, Cottonelle reports, while some people are hesitant to talk about bathroom habits, "many of us have a habit of talking while in the bathroom." More than 60% talk on the phone and nearly 40% email while on the toilet. Cottonelle says that it knows all too well that bathroom habits aren't discussed as often as they should be. "As progressive as our society has become, we know that most consumers are not discussing the details of their bathroom routine," says Mike Haley, Cottonelle marketing director. "That's why we're teaming up with documentary filmmaker Healey to start this conversation about using dry and moist and help people open up and understand that there's a better way to feel clean and fresh in the bathroom versus dry alone."
The goal of K-C's latest campaign with Healey is for the Cottonelle Care Routine to become a regular bathroom habit, so much so that having wipes on hand become part of bathroom etiquette. Right now, the company says,most Americans agree that not wiping off the seat (94%), forgetting to flush (92%), and not refilling toilet paper (74%) are offensive bathroom behaviors. One quarter (25%) of Americans agree that not having flushable wipes is offensive but that number could increase as more people adopt the routine.
More information about the campaign is available online.
Back To Top
|
The nova-Institute, Berlin, Germany, has published a paper on agricultural feedstock use in industrial applications shedding light on the controversial public debate surrounding the industrial use of food crops or so-called first generation feedstock. The core finding asserts that efficiency and sustainability assessed on a case-by-case basis should be the sole criteria in judging the choice of feedstock used. The institute further stresses that the real issue is land availability for growing biomass for different purposes.
The paper refers to studies asserting that, even after satisfying food demand of a rapidly growing world population, enough arable land would remain available for purposes other than food production. The best usage of these areas is achieved by considering the land-efficiency of different crops. Studies show that many food crops are more land-efficient than non-food crops. According to the paper, they require less land to produce the same amount of e.g. fermentable sugar (commonly used in biotechnology processes) than non-food crops or so-called second generation feedstock, e.g. lignocelluloses.
"Efficiency and sustainability should be the leading criteria when selecting renewable feedstock for industrial purposes, such as the production of bioplastics," said Hasso von Pogrell, managing director of European Bioplastics, embracing the paper as a welcome contribution to the discussion. "If the industry was to neglect the use of first generation feedstock at this point in time, it would do a disservice to society and the environment," he added. "In addition to being currently more efficient, the use of food-crops for industrial purposes has the major advantage that, in times of food crisis, these crops could be reallocated to food use".
European Bioplastics is in favor of promoting the use of second or even third generation feedstock for industrial purposes. However, as long as food crops continue in many cases to represent the most efficient feedstock by far, discrediting their use would be misguided and a step in the wrong direction in achieving the European Commission sustainability targets. "This often very emotional discussion needs to be steered into a more fact based direction," von Pogrell continued. "Only 2% of the global agricultural area is actually used to grow feedstock for material production and only 0.006% is used in the production of bioplastics, compared with 98% used for food, feed, and as pastures," he concluded.
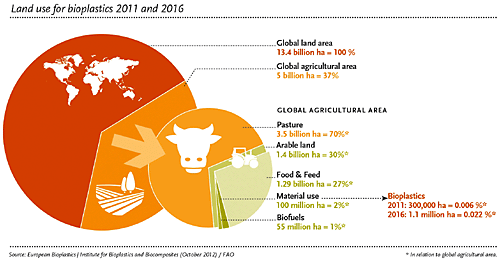
These findings echo the conclusion of a study recently published by the World Bank, according to which an increase in food prices is largely influenced by the oil price. Biofuels and, by extension, bioplastics play a negligible factor here. The study looked at food commodities such as corn, wheat, rice, soybeans, and palm oil and compared commodity prices to energy prices, exchange rates, interest rates, inflation, income and a stocks-to-use ratio to determine which of these drivers had the most impact on food prices.
The full nova-Institute paper Food or Non-Food: Which agricultural feedstocks are best for industrial uses? is available online.
Back To Top
|
With the completed acquisition of Longview Timber's approximately 645,000 acres of forestland in Washington state and Oregon in July, Weyerhaeuser Co., Federal Way, Wash., now owns or manages approximately 20.5 million acres of forestland in the U.S. and Canada. The latest acquisition makes Weyerhaeuser one of North America's—and the world's—largest private sustainable forestry operations.
"Weyerhaeuser is dedicated to industry leadership in forest stewardship and sustainability, and we will continue that leadership as we bring the recently acquired Longview Timber operations into our portfolio," said Tom Gideon, Weyerhaeuser's EVP of Timberlands. "All of Weyerhaeuser's North American forests will continue to be certified to the Sustainable Forestry Initiative standard, which ensures that our forest management practices meet a broad spectrum of social, economic, and environmental requirements."
Kathy Abusow, president and CEO of the Sustainable Forestry Initiative, explained that "by successfully achieving independent, third-party certification of its lands to the SFI standard, Weyerhaeuser has demonstrated a strong commitment to responsible forestry and to the communities that depend on a variety of forest benefits."
Gideon added that "we achieved 100% certification in our North American operations several years ago, and this year we also achieved full certification for our forests in Uruguay. It's a standard we've set for all of our operations. And while we're proud of our accomplishments, we continue to focus on continuous improvement as one of the world's preeminent sustainability leaders."
Back To Top
|
The American Forest & Paper Association (AF&PA), Washington, D.C., USA, is moving to the Capital's East End this November. Construction officially begins this week on the association's new office space at 1101 K Street NW.
"As one of the top 10 manufacturing sectors in the U.S., we need to be constantly engaged with policymakers and regulators, and our new location will enhance our ability to do that," said AF&PA President and CEO Donna Harman.
With nearly 30,000 sq. ft. of space in the East End neighborhood just steps from the new CityCenterDC complex, AF&PA's new, more central location helps position the association to better meet its members' advocacy needs on Capitol Hill.
"We're excited to make the move into a modern office space in a preeminent D.C. location," said Harman. "The association's history dates back more than 100 years, and this move demonstrates that our industry is as strong as ever."
Back To Top
|
This fall, TAPPI is providing a unique opportunity for North American suppliers to exhibit at the 2013 China International Paper Technology Exhibition and Conference (CIPTE). This is the largest pulp and paper exhibit in China, and will be held September 23-25, 2013.
TAPPI has held several 9 m2 booths for exhibitors from North America. The exhibit cost is less than $1,500. Please reply this week or the booth space will be released.
More information is available online.
Back To Top
|
Below is the latest listing of job openings in the TAPPI Career Center. The current listing includes job openings for a variety of positions including quality supervisor, project manager, senior development engineer, design assistant, and product manager. Current, specific job openings at companies and locations in the TAPPI Career Center include:
Employer |
Title |
City |
AMEC |
Project Manager |
Tucker, Ga. |
Confidential |
Sr. Development Engineer |
New Hampshire |
GL&V USA |
Product Manager |
New Hampshire |
Homasote Co. |
Mgr. Lab, Development, and Quality |
West Trenton, N.J. |
MeadWestVaco |
R&D Researcher - Paper Science |
Virginia |
P.H. Glatfelter |
Direct Materials Sourcing Specialist |
York, Pa. |
RockTenn |
Displays Design Assistant |
Bentonville, Ark. |
Suddekor LLC |
Quality Supervisor |
E. Longmeadow, Mass. |
More information about these jobs is available online.
Back To Top
|
Market Roundup
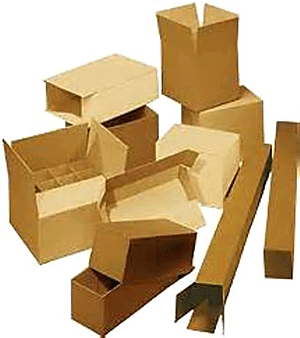 World demand for corrugated boxes will rise 4.2% per year to 234 billion square meters in 2017, according to a new report by the Freedonia Group, Cleveland, Ohio, USA. The fastest growth will occur in developing areas, especially in the Asia/Pacific and Africa/Mideast regions. Food and beverages will remain the leading market for corrugated boxes in 2017, accounting for 43% of global demand, while the nonfood, nondurables segment will grow the fastest.
The new study analyzes the 190.7 billion square meter world box industry, and presents historical demand data for 2002, 2007, and 2012, and forecasts for 2017 and 2022 by raw material (e.g., containerboard, adhesives, inks, waxes), market (e.g., food and beverage, nonfood nondurables), world region, and for 27 major countries.
The study also considers market environment factors, details industry structure, evaluates company market share, and profiles 33 industry players, including International Paper, Smurfit Kappa, and Rock-Tenn.
According to the report, advances will represent a notable acceleration from the 2007-2012 period, in which most developed world markets in North America and Western Europe experienced sluggish increases—or even declines—in corrugated box demand. Going forward, gains will be driven by an improved economic outlook as these regions continue to recover from the global economic downturn.
As economies strengthen, demand for manufactured goods will increase as a matter of course, stimulating sales of related packaging like corrugated boxes. The continued expansion of the electronic shopping market will drive heightened requirements for corrugated boxes used in the fulfillment of such sales. Advances will also be fueled by the expanded food, beverage, and durable goods output, while rising construction spending will stimulate demand for goods and materials (and their related boxes) used in construction applications.
Opportunities are also anticipated for retail-ready, or shelf-ready, corrugated box packaging, which is increasingly demanded by retailers as a means of controlling labor costs. Retail-ready corrugated boxes are designed to enable products to be placed on store shelves with minimal preparation. Such boxes tend to incorporate clean tearing features that allow the boxes to be converted from shipping containers into display trays without the use of box knives.
The Asia/Pacific region will remain the largest and fastest-growing outlet for corrugated boxes through 2017. Gains will continue to be driven by the large market in China; although slowing from the double digit growth seen during the 2002-2012 period, the country will post strong gains going forward. Corrugated box demand in the region will also benefit from healthy gains in countries such as India and Vietnam, although subpar increases in the Japanese market will temper this to some extent. Above average growth is also forecast for Central and South America and in the Africa/Mideast regions, areas in which corrugated demand per capita is below the world average. Although North America and Western Europe will post below-average gains, corrugated box demand in these markets will rebound from 2007-2012 declines.
Demand for containerboard, the primary raw material for corrugated boxes, will also accelerate from the slow growth of the 2007-2012 period. However, volume growth will be restrained by the heightened use of lighter weight, high performance containerboard in light of sustainability and cost control efforts. North America and Western Europe will also see demand improve from the declines of the 2007-2012 period, with both regions continuing to be net exporters of containerboard. The Asia/Pacific region will remain the leading market for containerboard with strong growth in demand anticipated for China, India, Indonesia, and Vietnam. However, although containerboard production is expected to outpace demand, the region will remain a net importer of containerboard.
In both the Africa/Mideast and Central and South America regions, containerboard production will expand faster than demand, although both markets will remain net importers. Containerboard demand in Eastern Europe is expected to expand at an average pace.
More information is available online.
Back To Top
|
Pulp & Paper
Glatfelter, York, Pa., USA, this week reported that it has completed a preliminary assessment of the damage resulting from an August 7 fire at its facility in Gatineau, Canada. The fire partially damaged one of the two airlaid lines at the facility. There were no injuries or environmental impact. The damaged airlaid line is expected to be down approximately two to four weeks.
The finishing and shipping operations were not impacted by the incident and shipment of customer orders resumed within 24 hr. Due to capacity available at Glatfelter's other airlaid facility in Germany, the company expects this incident will have a modest impact on third quarter shipments, reducing them by approximately 600 to 1,000 metric tons. The company is working with customers to minimize the impact of this interruption.
An assessment of the costs for the impact of inventory loss, equipment damage, and clean up is underway. Based on its preliminary assessment, the company expects no significant financial impact from this incident as it is expected to be covered by insurance, subject to a deductible of $750,000. However, there may be an impact on third quarter results due to lower shipments and the timing of recognizing the business interruption portion of the insurance recovery under the applicable accounting standards.
The Gatineau mill produces absorbent nonwoven materials on two airlaid machines for the feminine hygiene and specialty wipes markets. Approximately 265 Glatfelter employees work in this mill.
Glatfelter's U.S. operations include facilities in Spring Grove, Pa, and Chillicothe and Fremont, Ohio. International operations include facilities in Canada, Germany, France, the U.K, and the Philippines, a representative office in China, and a sales and distribution office in Russia.
Back To Top
|
Fortress Paper Ltd., Vancouver, B.C., Canada, reports that the high pressure water pump at its Fortress Specialty Cellulose (FSC) mill was reinstalled on July 12, and the cogeneration facility operated for 20 days before being shut down due to pump failure. The back-up high pressure water pump was then installed on August 5, and its operation was again unsustainable due to inadequate repairs. The company has already placed an order with another supplier for a high pressure water pump that is expected to arrive in approximately four weeks for installation.
Despite these setbacks, the FSC mill completed all major testing of equipment during the operating period. The facility successfully completed 18 and 24 MWH output testing. The company anticipates completing the final 100 hr. test as soon as the new pump is installed and tested. Fortress expects the cogeneration facility will be delivering power to the Hydro Quebec grid at the contractual rate within 24 hr. of completing the test.
Chad Wasilenkoff, CEO of Fortress Paper, noted that "although the performance of the repair by the supplier of the pump has been disappointing, we are pleased that we were able to complete all major testing of equipment. The company will proceed with an alternate pump supplier to complete the final 100 hr. test before delivering power to the Hydro Quebec grid and ultimately reducing our production costs."
Back To Top
|
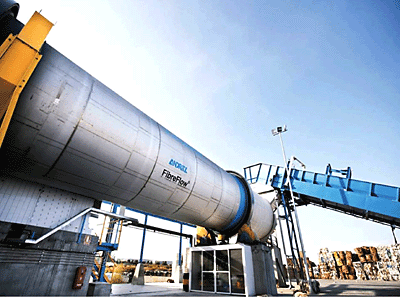 Taishan Gypsum, Foshan, China, has ordered from Andritz, Graz, Austria, a FibreFlow drum pulper to be installed at its paper mill in Tai'an City, Shandong province, China. The mill produces high-quality mask paper for gypsum board. Startup is scheduled for March 2014.
Low energy consumption, exceptionally high availability, and low operating costs of the FibreFlow system (capacity of 800 metric tpd) were decisive factors in the award of this order. Andritz's scope of supply also includes engineering, erection work supervision, startup, training, as well as a spare and wear parts package.
The raw material treated by Taishan Gypsum consists of one-half LOCC (local old corrugated containers) and one-half AOCC (American old corrugated containers). The Andritz FibreFlow drum pulper is used for pulping all kinds of recycled paper grades—slushing of paper and separation of contaminants are handled in a single unit.
Taishan Gypsum is a producer of high-quality gypsum board and frame series for interior decoration. The company, with a production capacity of 1.2 billion square meters of gypsum board per year, serves the domestic market and also exports to countries such as the United Arab Emirates, Indonesia, India, and Russia.
Back To Top
|
During the past three years, EcoPlanet Bamboo, Chicago, Ill., USA, says that it has driven the development of commercial plantations of non invasive tropical clumping bamboo around one core pillar—to "set in stone the benchmarks and framework for the industrialization of bamboo as an alternative fiber in a way that addresses issues of social and environmental concern." The company's recently concluded first phase of growth, the strategically located reforestation of approximately 10,000 acres of highly degraded land, in some of the poorest and least developed regions of Central America and Southern Africa, was focused on being demonstrative.
Being demonstrative has included proving that bamboo could be successfully produced at a commercial scale across different species and climates from both seed and tissue culture plantlets, proving that climate change benefits (accredited by the Verified Carbon Standard), as well as biodiversity and social co-benefits (accredited by the Climate, Community, Biodiversity Alliance) could be achieved, and ultimately proving that bamboo could be produced in a truly sustainable manner through the early acquisition of FSC Forest Management certification for the Rio Siquia and Rio Kama plantations.
EcoPlanet further notes that, in addition to these certifications, its plantations have received independent accreditation from a range of institutions, from the World Bank to the World Wildlife Fund (WWF). Such accreditation demonstrates that a for-profit company can earn strong financial returns in a sustainable and transparent way, while positively impacting the lives of the poor, improving the environment, and protecting the planet, the company emphasizes. EcoPlanet adds that it is hopeful this success will set a new global benchmark for the industrialization of bamboo.
With this framework strongly in place to guide the development of each new plantation, EcoPlanet has set its sights on a second phase of growth–achieving the reforestation of 1 million acres of highly degraded land into fully functioning commercial bamboo forests, with a focus on Southeast Asia, Brazil, and Africa. Split into manageable operations of 25,000 – 100,000 acres, these are to be dedicated plantations; each one co-developed alongside timber dependent manufacturing companies within strategic locations globally, providing them the ability to create a long-term competitive price advantage, secure supply, and a meeting of each entity's sustainability goals, the company explains.
"While our achievements to date are still a long way from our 1,000,000 acre goal, they have proved not only that we can, but that we are committed to industrializing bamboo in a way that benefits the local community, is environmentally positive, and enables the feedstock security that multinational corporations require to ultimately move away from unsustainable logging practices, and make the switch to an alternative fiber," says Troy Wiseman, CEO of EcoPlanet Bamboo Group.
Back To Top
|
Jari Celulose, Papel e Embalagens, Brazil, plans to restart its pulp mill in Monte Dourado in the Brazilian state of Pará at the beginning of 2014, according to a report this week by EUWID Pulp and Paper, Germany. The mill will be converted to dissolving pulp production instead of paper pulp. The project reportedly has already begun.
Production of bleached eucalyptus pulp at the 410,000 metric tpy mill in Northern Brazil was idled in early January of this year reportedly due to technical problems and competitive disadvantages in the hardwood pulp market. EUWID notes that the company's management then examined different product options.
According to EUDID, the Brazilian newspaper Valor Economico reported that the company's rebuilt facility would have an annual capacity of 240,000 - 250,000 metric tpy of dissolving pulp. The investment will be $80 muillion to $100 million, with the Brazilian development bank BNDES (Banco Nacional de Desenvolvimento Economico e Social) providing credit that partly covers these costs.
Back To Top
|
Minerals Technologies Inc., New York, N.Y., USA, has signed an agreement for a 14,000-metric ton satellite precipitated calcium carbonate (PCC) plant in Europe. The satellite facility, which will produce PCC as a filler pigment, will become operational in the fourth quarter of 2014.
"We are very pleased to have come to an agreement for a satellite PCC plant at a paper mill in Europe, for an established paper company that wished to remain unnamed for competitive reasons," said Robert S. Wetherbee, CEO of Minerals Technologies. "This facility will be our eleventh in Europe to deliver our PCC filling technology, which provides savings to papermakers by replacing higher-cost fiber."
PCC is a specialty pigment for filling and coating high-quality fine papers. In 1986, Minerals Technologies originated the satellite concept for making and delivering PCC on-site at paper mills and the concept was a major factor in revolutionizing papermaking in North America. Today, the company has more than 55 satellite plants in operation or under construction around the world
Back To Top
|
Orient Paper Inc., Boading, China, has announced the sale of land use rights for its headquarters compound. The compound includes the company's office building, all industrial-use buildings, and three employee dormitories located on Juli Road in Xushui County, Hebei Province, to Hebei Fangsheng Real Estate Development Co. for approximately $8.23 million in cash.
In 2012, governmental authorities in Xushui County, where Orient's headquarters compound is located, approved a new urban development plan covering properties occupied by several entities, including the company, that had previously been zoned for industrial use. Under this development plan, these properties were re-zoned for residential use only. Since the development plan was announced, the company has evaluated its options to determine the most effective and least disruptive way to comply with the plan's requirements.
Among alternatives investigated were having the company establish a land development subsidiary to develop the headquarters compound by itself, attempting to solicit proposals from real estate development companies that might be prepared to purchase the headquarters compound from the company and convert the land and buildings to residential use, and surrendering the company's land use rights to the local government.
After this investigation and analysis of the various options available to the company, at its meeting this past week, the board determined that the proposal of Hebei Fangsheng was the most attractive of the available alternatives and directed officers of the company to proceed with the Transaction.
The sale price of the headquarters compound's industrial land use rights is approximately $2.79 million, as determined by the valuation from a government designated appraisal, which was 3.35% higher than a second independent appraisal commissioned by the company. The sale price per acre is also 28% higher than the unit price that the company paid for the industrial land use rights for a piece of land right across the street from the company's main manufacturing plant in the Xushui County in April 2012.
In addition to the sale of the land use rights, the sale also includes the industrial buildings and the dormitories located within the headquarters compound. The sale prices of the Industrial buildings and dormitories are approximately $1.15 million and $4.29 million respectively. An appraisal obtained by the company put the value at $0.4 million.
Gross profit resulting from the sale is approximately $740,000, and net gain for Orient Paper was approximately $345,000 from the overall transaction after payment of applicable taxes and fees. The net proceeds from the sale were approximately $7.84 million, which are expected to fund the company's household and tissue paper business expansion.
In connection with the sale, Hebei Fangsheng agrees to lease the Industrial Buildings back to Orient Paper at an annual rental of RMB 1 million, or approximately $162,000, for a term of up to three years, while the company prepares to relocate its offices and the digital photo paper operations currently located in the headquarters compound.
As the relocation from Juli Road is mandatory, the sale allows Orient Paper to continue its operations in the current location for a maximum of three years while looking for a new location.
Back To Top
|
Weyerhaeuser Co., Federal Way, Wash., USA, announced this past week that, effective immediately, the Weyerhaeuser tree farms in the counties of Chelan, Clark, Cowlitz, Kittitas, Klickitat, and Skamania will be closed to public access due to the extreme forest fire danger. The closure will remain in effect until the operating areas receive adequate rainfall and the temperatures improve.
The company has also placed a number of limitations on its remaining tree farms in Washington and is considering additional closures if the forest fire danger continues to increase in the coming weeks.
Visitors planning a trip to Weyerhaeuser forestlands in Washington are reminded to call the company's statewide, toll-free telephone number before heading out to the woods. The Weyerhaeuser Hunter and Recreational Use Hotline number for Washington is 866-636-6351. The same information can also be accessed online
Back To Top
|
Containerboard/Packaging
Productora de Papel, SA de CV (Propasa), Mexico, has begun producing containerboard on its rebuilt PM 3. With the machine rebuilt by Voith, Germany, Propasa aims to increase production by up to 25%, producing nearly 500 metric tpd of board, while improving the final quality of its product.
The project's first part included the supply of a MasterJet Pro F/B headbox with ModuleJet II dilution control as well as the rebuild of the forming section, including a DuoShake that allows for greater homogeneity in the paper web formation. The reel and winder were also modernized. In a second step, the machine's dryer section was rebuilt. The second phase included the addition of two dryer sections to the machine, thereby increasing its speed.
Propasa also utilized Voith's basic engineering services for the machine's steam and condensate, lubrication, ventilation, and vacuum systems.
Shortly after startup, the machine was producing saleable board and there was a visible improvement in product quality. With this outcome, the company says it has taken an important step towards consolidating the group's growth in highly competitive markets such as Mexico and the U.S.
Propasa has been operating for more than 70 years, dedicated to the production of coated cardboard and liner, corrugated medium, and white top liner. In recent years, the company has expanded its production capacity with sales to markets in Mexico, the U.S., and Central America.
Back To Top
|
Rengo Co., Kita-ku, Osaka, Japan, has acquired a 75% stake in TCG Rengo Subang (M) Sdn. Bhd., a wholly-owned subsidiary of its overseas joint venture company Thai Containers Group Co., Thailand. Industrialization centering on the manufacturing industry has been underway in Malaysia since 1970, with the active introduction of foreign capital. With the promotion of Malaysia's long-term plan, Vision 2020, which aims for Malaysia to become one of the world's developed nations by 2020, the company expects a stable increase in demand for corrugated packaging.
The corrugated packaging business in Malaysia and other countries in Southeast Asia is an important strategic focus for overseas operations of the Rengo Group, which defines itself as a "general packaging industry," and aims to expand its operations globally in the same manner as Japan. Rengo says it will continue to work to further enhance its corrugated packaging supply system in the region.
Back To Top
|
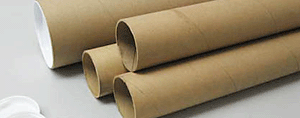 Summer Industries, Welcome, N.C., USA, a producer of spiral wound paper tubes, cores, and cans made from 100% recycled paperboard, this week announced the opening of a plant in Neenah, Wis. The new facility marks the sixth plant opening in just 12 years for Summer Industries, and produces paperboard tubes and cores on lines designed and built in-house. Summer Industries also has plants in Florida, Mississippi, New York, and North Carolina.
The Neenah plant represents an investment of more than $1.5 million, and will create some 20 new manufacturing jobs when the plant is in full operation. Fox Valley industry veterans Peter Emenecker, GM, and Scott Meyer, operations manager, comprise the leadership team of the new facility.
"We were fortunate to attract top industry talent to lead the Neenah operation." said VP Anthony Patterson, "Peter and Scott are men of character, with a commitment to excellence in whatever they undertake. They understand this market, and have a proven track record for growing the business. This makes them a perfect fit to bring the CORE VALUES™ of Summer Industries to the Fox Valley."
Peter Emenecker added that "Summer Industries is among the most respected and successful companies in our industry, with a proprietary manufacturing platform beyond anything we've seen before. Scott and I are excited to combine this with our deep knowledge of the local market and common commitment to world class service."
Back To Top
|
The specialty chemicals group ALTANA, Wesel, Germany, has acquired the specialty coatings business of Henkel. The products are sold under the brand names MiraFoil and Miracure and are mainly supplied to the packaging industry in North America. The business generated sales of around $15 million in 2012.
Within the ALTANA group, the business will be integrated into ACTEGA Kelstar Inc. in the U.S. and into ACTEGA Terra GmbH in Germany, both belonging to the ACTEGA Coatings & Sealants division. "By acquiring the specialty coatings business of Henkel we are continuing to execute our North American growth strategy consistently and focus on innovative specialty chemicals," ALTANA CEO Dr. Matthias L. Wolfgruber, said.
The technologies are acquired by way of an asset deal and include effect and overprint coatings curing under ultraviolet radiation and electron beam. MiraFoil coatings are an environmentally responsible alternative to foil board laminating and hot foil stamping while reportedly being equally brilliant to foil. They can be applied to precise areas, thus reducing waste and shortening lead times, ALTANA notes. Miracure coatings provide a range of matte, gloss, satin, and silicone coatings for conventional printing processes, creating visual appearance such as glow-in-the-dark or dimensional texture.
"With the specialty coatings business of Henkel we are expanding our product portfolio by two highly innovative and sustainable product families," Dr. Roland Peter, president Division ACTEGA Coatings & Sealants, said. "Hence, we will be able to offer our customers even better solutions that are tailor-made to their needs."
Back To Top
|
New Products
MeadWestvaco Corp. (MWV), Richmond, Va., USA, has introduced Shellpak® Renew with Optilock™ technology. This smaller, more discreet medication adherence package is designed to meet patient and pharmacist needs by enabling greater patient portability and improving pharmacy efficiency. The package features an advanced locking mechanism for the highest level of child resistance (F=1) in a significantly reduced package size. It is 23% smaller than the original Shellpak Renew, while still accommodating the same medications. The package will launch at Walmart pharmacies this summer with medications from Mylan, a generics and specialty pharmaceutical company. Additional medications will follow later this year through MWV.
"Walmart is committed to developing scalable, accessible solutions to improve patient adherence to medication," said Sandy Kinsey, VP, Pharmacy Merchandising for Walmart Stores. "We are proud to offer Shellpak Renew with Optilock technology and are excited about the new, smaller package size, which many of our patients requested."
Shellpak Renew with Optilock technology features a calendared blister and space for patient educational information, which is shown to improve patient adherence to medications. The decreased package size provides a more convenient way for patients to access and carry their medications, while also making dispensing medications quicker and easier for pharmacists.
Mylan Pharmaceuticals is working with Walmart to offer 11 SKUs packaged in the new Shellpak.
The package's outer carton is made of MWV's Natralock®, a paperboard-based packaging solution that maximizes the use of recyclable materials and minimizes waste. The secure, tear-resistant carton does not require paper backing on the foil blister, making pill expression easy. In addition, the package contains enhanced adherence features, including a smooth-slide blister for easy medication access and color-coded spine labels to help distinguish among medications.
Back To Top
|
Voith, Germany, reports that it is expanding its clothing portfolio for pulp production with a further-developed press fabric, Voith already delivers entire pulp drying machines, from the headbox and the innovative vertical dryer section to the cross-cutter and bale packing. The forming fabrics and roll covers from Voith are now supplemented by the further-developed CellFlex VMax press fabric.
Along with roll covers such as SolarFlow or MegaFlow, Voith also offers a broad range of different press fabrics for pulp production. The CellFlex VMax press fabric has been developed to provide a particularly long-lasting and continuous dewatering capacity. CellFlex VMax press fabrics are already in use worldwide.
With the expanded portfolio, Voith now offers pulp producers forming fabrics, press fabrics, and roll covers from a single source. More information is available online.
Back To Top
|
People
Glatfelter, York, Pa., USA, has hired Brian E. Janki as VP and GM of its Specialty Papers Business Unit (SPBU), effective yesterday, August 14. Janki has overall P&L responsibility for SPBU and leads the development and implementation of strategies and tactical plans for this business unit.
In making this announcement, Dante C. Parrini, chairman and CEO, said that "Brian is a global leader who has a demonstrated track record of success in building high-performing teams, improving business performance, delivering results, and leading change. We look forward to his leadership and expertise as we welcome him to Glatfelter's senior executive team."
Janki has diverse leadership experiences that include assignments in Asia Pacific, Latin America, and North America. He comes to Glatfelter having most recently served as VP and GM, Rigid Industrial Packaging and Services for Greif. He worked for Greif for 12 years in a variety of progressive leadership assignments including P&L leadership of two business units, global responsibility for supply chain and sourcing, and transformational assignments including global oversight of the implementation of the Greif Business System.
Prior to working at Greif, Janki served in supply chain and general business consultant roles with IBM Global Services, The ProAction Group, and Ernst & Young. He graduated with a Bachelor of Science in Business Administration, Finance, and Accounting, from Ohio State University. His executive development includes leadership and general management programs with the Fuqua School of Business, Duke University, and the Ross School of Business at the University of Michigan.
Back To Top
|
Weyerhaeuser Co., Federal Way, Wash., has appointed Jeanne M. Hillman VP and chief accounting officer for the company. Hillman succeeds Jerald W. Richards, who recently resigned from his position to become CFO at Potlatch Corp (see article below).
"Jeanne is an experienced leader with tremendous financial expertise," said Patty Bedient, EVP and CFO. "The knowledge she gained supporting our businesses for the past three years will serve her well as she expands her role to include the responsibilities of this critical position for the company.
"Jerry has been an outstanding member of the Weyerhaeuser team, and while we are sorry to see him go, we wish him the very best in his new role," Bedient added.
Hillman was Weyerhaeuser's VP and controller for operations since 2010. Prior to that role, she served as the company's VP and chief accounting officer from 2006 to 2010. Hillman joined the company in 1984 and has held various finance positions with the company. Before joining Weyerhaeuser, she was employed by Ernst & Young LLP. She is a CPA in the state of Washington.
Back To Top
|
TAPPI News
The PIMA Executive Council is hosting a free informational webinar on TAPPISAFE—the innovative contractor safety orientation program. Help bring your contractor partners home safe while reducing your cost for training.
TAPPISAFE is now being implemented at 14 mills, including IP, RockTenn, Graphic Packaging, and Domtar locations.
The free webinar is scheduled for Tuesday, August 20, at 11 a.m. EDT.
Back To Top
|
Make your plans to attend this annual networking conference, September 9-12, 2013, in Raleigh, N.C., USA.
Sponsored by IDCON and Metso, this conference offers:
- Leading industry keynote speakers
- Insightful presentations
- Technical information
- Solutions to improve reliability
- Techniques to impact the bottom line.
Register through TAPPI by August 10 to snag that benefit savings.
Back To Top
|
TAPPI is pleased to announce the new business reviews section on its buyers guide. Now you have the opportunity to share your experiences with a company's products or services with your peers in the industry.
Write a review to be entered for a chance to win airfare and seven nights at a luxury resort hotel in Hawaii.
What are the benefits of writing a review?
- 7 of 10 people read reviews before making a purchase
- 51% of buyers trust strangers' opinions over friends, family, and trusted business advisors
- Consumers trust online reviews and other consumer feedback 12 times more than marketing messages from businesses
- Local business reviews are read by 85% of consumers
- Reviews not only give consumers the ability to share their opinions about the products or services they buy, but it also offers businesses a way to evaluate and track what people are saying about them
- Good reviews lead to more purchases, and negative reviews allow marketers to make adjustments to products and show their willingness to work with their consumers (both the consumer and the brand benefit from these opinions).
Back To Top
|
The Safety Management Leadership Course, August 26-27 in Metro Atlanta, Ga., USA, places a particular focus on leadership training, including incorporating a safe environment into workforce training and work expectations. Key safety topics are covered by the course, including:
- Safety Fundamentals / Modern Safety Management Principles
- OSHA Record Keeping and Medical Management
- Incident Investigation
- Safe Behavior and Choices
- Safety Culture
- Measuring Safety Performance
- Hazard Recognition
- Safety Walk-throughs, Observations, and Messaging
- Managing Change Safely
- Effective Safety Communication.
See more listed on the course schedule.
Meet the instructors.
Register for the Webinar Preview.
Tuesday, August 6 ♦ 1:00 p.m. EST ♦ 45 min.
This course is designed for anyone involved in workplace safety, including:
- Training and HR
- Safety Supervisors
- Team/Project Leaders
- Plant Managers
- Frontline Supervisors
- Safety Committees.
A special discount is offered for TAPPI and PPSA members. Register by July 26 for savings off the regular course rate.
TAPPI will award 1.3 CEUs to those who complete this course.
Back To Top
|
August 27th PIMA will hold it's Golf Outing at Grand View Lodge of Pequot Lakes, Minn. The shotgun scramble starts at 9:30 a.m. Box lunch is included, with cocktail hour to follow. Net proceeds go to Lake States TAPPI/ North Central PIMA's Scholarship Fund. Details now available and registration is open.
Back To Top
|
TAPPI member Hideki Fujiwara, Ph.D., has hit a lot of high notes in his long and illustrious career in the pulp and paper industry. Not the least of which occurred as a result of his nearly three decades of membership, including being the first member from Asia to be honored with the Charles W. Engelhard Coating and Graphics Arts Division award.
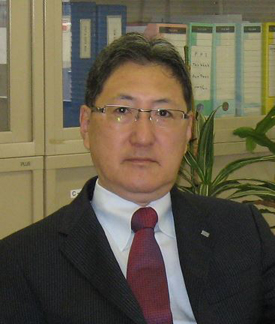 Dr. Fujiwara, who retired in June after 38 years in the industry, spent the majority of his career with Nippon Paper, serving in a variety of managerial positions. He credits his active involvement in TAPPI with providing ample opportunities not only to receive, but to share technical ideas and innovations with other professionals from around the world. Membership helped broaden his view of the forest products industry, and he notes that "joining TAPPI was the very first step to being a real professional in this field."
Find out more by reading this month's Member Spotlight. Spotlight participants are recommended by fellow members and staff. If you would like to nominate members, just send their name (or names) to MemberSpotlight@tappi.org. We will forward a Spotlight Questionnaire to fill out and return.
We look forward to seeing you in the Spotlight!
Back To Top
|
These 19 publications are all available for just one penny for a limited time during the month of August.
This offer will expire August 25.
The World In 2015: Four Possible Scenarios
Edited by: Stuart Sharp, chairman, The TAPPI Futurists
TAPPI Futurists explore issues that may affect the world and the paper industry in 2015. Four possible scenarios are presented based on expert opinion, scanning and monitoring, and extrapolation of trends. Each scenario is a description of the way the paper industry and the world may look 15 years from now, depending on the effects of various trends and issues. The book provides an opportunity for readers to think about the future and to plan and position themselves and their companies for what the future might hold.
The TAPPI Futurists is a group of TAPPI members whose purpose is to develop a long-term view of the paper industry to assist the Association in long range planning. This book was developed to provide a framework for readers to think strategically about the future. The book represents views and opinions of individuals from all segments of the pulp and paper industry, including manufacturers, suppliers, and customers. In addition, the Futurists worked with five non-paper industry companies to ensure that the scenarios would give a broad-based global view of the possible world 15 years from now.
Item Number: 0101R307
Process Engineering Design Criteria Handbook: Pulp and Paper Normal Design Criteria
Edited by: Thomas L. Abrams
This report presents design criteria guidelines important for existing mill modifications and for new mill proper design. A project of the Process Engineering Committee of TAPPI's Engineering Division, this comprehensive text features normal design criteria for kraft, TPM, and groundwood mills and includes everything from mill site preparation through paper production. Designed to benefit process, chemical, civil, electrical, mechanical, instrument, and construction engineers in mills or consulting firms, this report is sure to be a valuable addition to all engineering libraries.
Item Number: 0101R262
Industrial Environmental Control Pulp and Paper Industry, Second Edition, (Spanish)
By: A. M. Springer
Now in Spanish.
This classic text is a comprehensive reference on pollution control in the pulp and paper industry. It was written to promote further implementation of cost-effective environmental control by the pulp and paper industry. The Spanish version includes 18 chapters.
Item Number: 0102B056S
Pigments for Paper
Edited by: Robert W. Hagemeyer
Task Group Chairman: John E. O'Shea
This comprehensive text covers all aspects of pigments for paper. This unique book can serve as an introductory text as well as a practical reference. Well-respected industry experts who are specialists in their area wrote each of the12 chapters. This text provides the most current information on different ingredients, describing what they do and how they perform. It is a valuable reference tool for everyone involved in paper coating.
Item Number: 0102B062
Setting the Industry Technology Agenda
Edited by: Gerard Closset
Discover the innovative ideas proposed by Summit participants to meet the industry's greatest challenges. This text provides a summary of the Forest Products Industry's technology needs as identified by the participants of the 2001 Forest, Wood and Paper Industry Technology Summit. During this Summit, more than 130 leading experts from industry, supplier and service providers, government, and academia worked to identify, define, and analyze gaps in current technology and knowledge and then propose bold, breakthrough approaches to fill those gaps and meet the greatest needs and priorities of the industry. The book presents a compendium of those critically important technology needs, prioritized and aligned with the new industry technology strategy, including:
- Sustainable forest productivity
- Recycling
- Process automation
- Fiber engineering
- Process improvement/breakthrough technologies
- Ttechnologically advanced workforce
- Environmental performance
- Energy performance
- Nnew forest-based materials
- Wood products.
Reading this book is a must for anyone wishing to understand the needs and the direction of technology development for the industry. The book also features an Agenda 2020 retrospective and concludes with a discussion of the industry's path forward.
Item Number: 0101R307
Remember, this offer expires August 25, 2013.
Back To Top
|
Editor Mike Postek says, "Preparing this book has been an interesting process... we never thought there would be such an overwhelming response to our request....this book demonstrates that CNM are here to stay ....and will be an important component of the future economy.
"Having a document such as this at hand is extremely important as an information and marketing tool to inform administrators and decision makers about the future potential value of cellulose nanomaterials.
"Cellulose nanomaterials have not gained the level of interest they deserve because there has been a dearth of good education and marketing materials. This book should fill that need."
Anyone working in the nanomaterials field, or needing to understand the production and standards of the field, will want to add this volume to your reference material.
This new book includes:
- A collection of more than 100 two- to three-page summaries on recently completed and on-going research with these high strength materials
- A list of who's-who of research as well as leads on successful applications
- Topics on subjects such as production and modification, composites, other applications, modeling, and standards
- Special Feature: Actual Cellulose Nanocrystals included within the overcoat varnish of the cover.
Back To Top
|
Christina Shultz, Royal Institute of Technology (Sweden), Virginie Bigand, Grenoble INP Pagora (France), and Assya Boujemaoui, KTH Royal Institute of Technology (Sweden) were all named winners of the student poster competition at the 2013 TAPPI International Conference on Nanotechnology for Renewable Materials. The conference was held June 24- 27 at the KTH Royal Institute in Sweden. The student poster competition was graciously sponsored by Verso Paper Corp, Memphis, Tenn., USA.
"I would like to congratulate Christana Schultz, Virginie Bigand, and Assya Boujemaoui for being named poster winners for this year's TAPPI Nanotechnology Conference," said Larry N. Montague, TAPPI president and CEO. "They were selected from a group of more than 40 conference posters and their outstanding presentations highlighted some very innovative applications for nanotechnology based on renewable materials."
The first place poster was by Schütz from the Royal Institute of Technology's Department of Materials and Environmental Chemistry who presented "Carbon Aerogels from Bacterial Nanocellulose as Anodes for Lithium Ion Battery." Second place was awarded to Bigand for "Use of Different Quality of MFC for Producing Controlled Release Films." Poster winners receive certificates of recognition and first place receives a cash prize. Posters were reviewed by a team of judges, who evaluated the objective of the work, experimental plan, layout, and presentation of results, and conclusions.
The winners were recognized at the conference dinner gala event, which featured a keynote address by Derek Gray of McGill University, winner of the prestigious Marcus Wallenberg prize, and held at the world renowned Vasa maritime museum.
Back To Top
The TAPPI International Research Management Committee requests nominations be submitted for the Research and Development Technical Award and the William H. Aiken Prize.
The award is given for outstanding accomplishments or contributions that have advanced the technology of the paper and related industries in the field of research and development. The nomination should contain:
- A summary of the nominee's technical achievements
- The impact and relevance of the research on industry
- Education, work history
- Examples of the impact that they have had on others
- Other pertinent activity such as involvement in TAPPI.
The $500 prize is funded by an endowment from the estate of William H. Aiken, TAPPI president in 1967-1968 and vice president of technology for the former Union Camp Corp. at the time of his death in 1974. Dr. Aiken also won the TAPPI Gold Medal, the association's highest honor, in 1971. Nominations for the Research and Development Technical Award and the William H. Aiken Prize should be submitted by August 31, 2013, to Colleen Walker, cwalker@tappi.org at TAPPI, 15 Technology Parkway South, Peachtree Corners, Ga. 30092, USA, or fax +1 770-446-6947.
Back To Top
|
Registration is now open for the 2013 TAPPI Corrugated Press Hands-On Maintenance Workshop, September 17-18 at the Global Equipment USA Warehouse in Skokie, Ill., USA.
This unique course gives you an unprecedented opportunity to get hands-on training on how to audit converting machines. With only 18 seats available, you will have ample opportunity to get your questions answered by instructors Tom Pearce (Pearce Corrugated Consulting), John Bingham (Pamarco), Jim Wegemer (INXinc), Chuck Bobeldyk (Mark-Maker Co.), Randy Kesselring (MarquipWardUnited), as well as representatives from Global Equipment. The schedule for this course is packed into just two efficiently planned days so that participants get loads of skill and experience without much time away from their own operations.
Who should attend?
This Intermediate-level course offers indispensable hands-on maintenance training for corrugated industry plant managers and supervisors, engineers, maintenance teams, and machine operators.
You could pour over all of the how-to manuals available and still not retain this level and quality of working knowledge. Completing this workshop will enable you to:
- Use the basic tools to mechanically audit and troubleshoot a press
- Understand press audit procedures for process centering, better quality products, and increased productivity
- Discuss anilox roll selection, press "fingerprinting," inks and substrates, quality defects amd cause(s), and scoring.
Register by August 16 and join TAPPI or renew your membership to receive the best rates.
Back To Top
|
There's still time to be part of the program at the 2014 TAPPI PLACE Conference, May 12-14, 2014, at the Sawgrass Marriott Hotel in Ponte Vedra, Fla., USA. The 2014 PLACE Technical Program Team is actively seeking technical presentations, panels, tutorials, roundtables, and case studies from the packaging and academic community to be presented at the conference.
View the Call for Abstracts.
Interested in being a session chair or know someone who would be a great presenter? Extended abstracts will be accepted anytime before September 6, 2013. Space is limited so submit now! Final papers will be due on or before March 17, 2014.
The 2014 PLACE Conference is the premier North American event for the flexible packaging industry and will have something for the whole supply chain including suppliers, converters, extruders, retailers, and brand owners. This event not only offers top notch technical presentations but also allows ample opportunity for networking with your peers. Visit the event website for additional conference information.
Back To Top
|
The 2013 Building Science Committee Technical Program will include papers on: Process Variation Reduction, Glass Sizing Basics; Burner Safety and Efficiency; Biological Treatment Case Study; Operator and Mechanical Training to Enhance Operational Effectiveness; and IT Systems to Manage Roll Goods and Reduce Waste.
This year's program will focus on aiding production managers and engineers in the fiberglass mat industry. Attendees will get the first-hand knowledge needed to improve their mat processes with production-targeted papers.
These topics and more will be covered in the comprehensive technical program. Tim Worms, of 3M's Industrial Mineral Products Division, is returning by popular demand to present his outlook for housing starts and the roofing forecast for this year. Kirby Erickson, of GAF, will discuss critical safety issues to be aware of as you seek to implement new efficiency and pollution requirements in curing ovens. In addition he will provide an example of how mistakes led to a massive oven explosion and what was implemented to address burner safety going forward. Charles Black, of Charles Black & Associates, will ask if your training dollars are being spent wisely and provide case studies showing how strong training programs can have a positive impact on your company's bottom line. Blaine Krause, of Nalco, will offer case studies on microbial control including its impact on operations, monitoring, control, and examples of newer technology.
The meeting will be held September 18-20 at The Hilton Marco Island Beach Resort in Marco Island, Florida, USA. Meeting registration includes the full conference program, the Building Sciences Committee Meeting, and ample opportunities for networking with other manufacturing personnel and suppliers. Thursday afternoon's activity is a choice of golf, backwater fishing, or a relaxing spa treatment. Group dinners are included in the cost of registration for Wednesday and Thursday evenings at some of the area's finest restaurants. Non-registered spouses and guests are welcome to participate in the activities and dinners for the following costs: $60 per dinner and $95 for golf, fishing, or the spa treatment. They do not have to pay the conference registration fee.
Companies participating as sponsors include ESP, GAF, Georgia-Pacific Chemical, Malarkey Roofing, Momentive Specialty Chemicals, Nalco, PPG, Albany International, Xerium, Ineos, Mallard Creek Polymers, and Majiq. Opportunities to sponsor with this select group of companies are still available and your company will receive special recognition throughout the meeting.
You do not want to miss out on this opportunity to stay abreast of current market trends, new and emerging product/process technical developments, and regulatory issues that are or will be impacting our industries.
For full meeting information including the conference agenda and program summaries, please visit the meeting website today.
Back To Top
|
TAPPI invites submissions of basic and applied research articles, communications, and technical reviews to TAPPI Journal, the world recognized peer-reviewed research publication. TAPPI is the leading association for the worldwide pulp, paper, packaging, tissue, nonwovens, and converting industries, with more than 7,000 members globally.
Authors presenting papers at conferences, experts with significant industry findings, and students or professors reporting academic research − any authors performing relevant industry research − are encouraged to submit their manuscripts.
Why submit your work to TAPPI Journal?
High visibility: Publishing in TJ makes your work accessible to professionals, libraries, and the global academic community through TAPPI's robust communications network.
TJ electronic issue: Distributed to thousands of TAPPI members every month, TJ features abstracts, full papers, author notes, and more.
Print compendium: Members also receive TJ's annual print compendium, a bookshelf reference volume containing abstracts of every paper published that year. The compendium is distributed to more than 250 libraries, industry organizations, and academic institutions around the world.
Paper360°: Summaries of select TJ papers appear in Paper360°, TAPPI's bi-monthly magazine with a global circulation of more than 40,000.
Online library: Papers published in TJ become part of TAPPI's e-Library available online. Searchable by subject and author name, the e-Library allows worldwide access to abstracts and downloadable full papers.
Indexing: Every issue of TJ is indexed by Thomson-Reuters, the world's leading citation index for academic research.
Career enhancement: Our stringent peer-review process and distinguished Editorial Board have made TAPPI Journal a well-respected, commonly referenced source of the best industry research for more than 60 years. TJ publication is an excellent way to gain attention from colleagues, peers, and current or future employers.
Author-focused process: Editorial Board members carefully marshal every paper submitted, based on area of expertise; TJ peer reviewers are selected for their proven subject knowledge. These experienced professionals – most of whom are TJ authors themselves – work with authors to ensure that papers meet TJ's high standards and are presented clearly and accurately.
Easy to submit: Papers may be submitted by email to Jeff Wells at TAPPI. Complete author guidelines are available online. (Please note: Papers must be submitted by the author; TAPPI Conference papers are NOT automatically reviewed for TJ publication.)
We look forward to receiving your work!
Back To Top
|
The soon-to-be-published, "Production and Applications of Cellulose Nanomaterials" is the latest TAPPI Press product to broaden the industry knowledge regarding who is researching nano technologies as well as leads on successful applications.
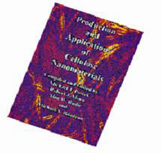 Anyone working in the nanomaterials field, or needing to understand the production and standards of the field, will want to add this volume to their reference material. Cellulose nano-crystals and cellulose nano-fibrils have been known for 20-50 years, but recent research suggesting very high strength properties and other unique physical properties have generated extensive interest in these materials.
Pre-order your copy today and save!
This new book will include:
- A collection of two to three page summaries on recently completed and on-going research with these high strength materials
- A list of who's-who of research as well as leads on successful applications
- Topics on subjects such as production and modification, composites, other applications, modeling, and standards.
- Special feature: Actual cellulose nanocrystals included within the overcoat varnish of the cover.
Pre-order Price:
Member: $149
Nonmember: $149
After July 15:
Member: $189
Nonmember: $259
Product code: 0101R332
Back To Top
|
Make plans to attend the 2013 Building Sciences Committee Fall Meeting September 18-20.
The Building Sciences Committee has designed a strong technical program for production managers and engineers to provide firsthand knowledge to improve their fiberglass mat process with practical production-targeted papers.
This year's program will include papers on: Process Variation Reduction, Glass Sizing Basics; Burner Safety and Efficiency; Biological Treatment Case Study, Operator and Mechanical Training to Enhance Operational Effectiveness; IT Systems to Manage Roll Goods and Reduce Waste.
We are pleased that Tim Worms of 3M will return by popular demand to present his updated Roofing Market Overview and Forecast.
The meeting will be held at The Hilton Marco Island Beach Resort in Marco Island, Fla. USA. TAPPI has negotiated a very economical room rate of $109.00 per night per guest. This rate is good for TAPPI members for stays of any length from Wednesday, September 18, through Sunday, September 22. Group dinners Wednesday and Thursday evenings will provide opportunities to meet other manufacturing personnel and suppliers, and their cost is included in the cost of the meeting. These will be excellent networking opportunities.
Thursday's afternoon recreational activity (also included in the registration price) is a choice of golf, coastal fishing, or an afternoon at the spa. Non-registered spouses and guests are welcome to participate in the activities and dinners for the following costs: $60 per dinner and $95 for golf, fishing, or the spa treatment. They do not have to pay the conference registration fee.
Click here for additional meeting information.
Back To Top
|
The 2013 TAPPI PEERS Conference, September 15-18, in Green Bay, Wis., USA, has announced the detailed technical program focusing on sustainable manufacturing and other pressing business and technical questions faced by pulp and paper companies as they manage raw materials, assets, regulatory requirements, and production assets. Register now and save.
In addition to the peer-reviewed technical program, Keynote Speaker Robert Feeser, SVP of Packaging with MWV, will share his insights on the day-to-day challenges he faces as he oversees the company's primary mill-based manufacturing businesses in the U.S. and Brazil. PEERS will also offer exclusive networking opportunities and insight into new technologies that can help you optimize your mill operations.
For 2013, PEERS will be co-located with the 10th Research Forum on Recycling and the International Bioenergy and Bioproducts Conference, creating a value-added opportunity for you to expand your learning, networking, and resources by attending all three events.
Learn more about the TAPPI PEERS Conference.
Back To Top
|
TAPPI is offering a 10% discount on registration for the Root Cause Problem Elimination Training Course taking place in Raleigh, N.C, USA, on October 8-10, 2013. If you register soon, you can save more than $250 with only a few seats remaining.
IDCON's Root Cause Problem Elimination Seminar focuses on eradicating problems. We all have problems, right? At least in your operations, let this training help you get to the source of problems.
You'll learn how to tie cause and effect together and apply logical thought processes to arrive at the problem's core. You'll learn how to use the "How-Can Diagram" to bring root cause analysis into your day-to-day reliability management process, and do it cost effectively!
This expanded course will focus on outlining basic mechanical engineering stress/strain fundamentals, metallurgy, and engineering design, which are typically necessary in the development of possible root cause(s) for mechanical failures.
You'll learn how to use predictive maintenance tools correctly to provide a mechanism for root-cause analysis initiation and eventual elimination of repeat failures.
Register today to secure your access to these premier training courses with IDCON.
Back To Top
|
Don't miss out on your chance to attend the Process Control of Stickies Workshop, taking place just before the TAPPI PEERS Conference.
Organized by Dr. Mahendra Doshi, current TAPPI JOURNAL Editorial Board Member and Founding Editor of Progress in Paper Recycling, the workshop will be held from 7:30 a.m. to 4:30 p.m. on Sunday, September 15.
The international workshop is designed for engineers, scientists, and technicians who want to get a handle on one of the difficult contaminants in paper recycling - stickies. The workshop will benefit anyone using recycled pulps, working in recycling mills, or affiliated with companies supplying equipment, chemicals, and recovered papers to the recycling industry.
Problems caused by stickies cost millions of dollars to the industry. As indicated above, experts from around the world together with highly experienced speakers from mills offer an excellent overview for managing and controlling stickies. If you could just save one hour of paper machine downtime it would pay for the workshop many times over.
Learn more about this important workshop.
Don't miss this golden opportunity to learn about stickies related issues at this one-day international workshop.
Registration Cost:
$295/member; $345/non-member (on or before August 16); or $345 (if registered after August 16).
Back To Top
|
Now's the time to make your plans to attend IBBC, September 18-20 in Green Bay, Wis., USA.
As the only industry event dedicated to advancing biorefineries in the forest products industry, International Bioenergy and Bioproducts Conference (IBBC) offers you a fresh look at biomass utilization. Sessions focusing on biomass supply and demand, biochemical and thermochemical conversion technologies, conversion pathways, and economic assessments – along with a Keynote Presentation from Linda A. Beltz, Ph.D., NPDP, Director, Technology Partnerships at Weyerhaeuser – can help you determine how to integrate these technologies into your mill.
For 2013, IBBC will be co-located with the TAPPI PEERS Conference, and the 10th Research Forum on Recycling, creating a value-added opportunity for participants to expand their learning, networking, and resources by attending both events. Offered just after IBBC, TAPPI's Biorefinery Course, can deepen your understanding of biorefinery strategies and emerging technologies and their design/implementation in a business strategy.
Learn more about IBBC.
Register by August 16 for best rates!
Back To Top
|
The TAPPI Corrugated Packaging Division's Mitsubishi Heavy Industries Corrugated Scholarship has been awarded to Michelle Blood of N.C. State University. The award will be officially announced during the 2013 CorrExpo Conference, October 7-9, 2013, in Indianapolis, Ind., USA.
"The corrugated packaging industry requires outstanding young science and engineering professionals to pursue a career in the pulp and paper industry in order for the industry to continue to innovate and prosper," comments Larry N. Montague, TAPPI president and CEO. "Michelle Blood is simply a great example of the type of future leader our industry needs to be successful and we are very pleased to provide this scholarship to support her as she works towards her undergraduate degree."
Blood is a fifth-year student at N.C. State University studying Paper Science and Engineering and Chemical Engineering. She currently serves as VP of the TAPPI Student Chapter. Her work experience includes: two co-op rotations at Packaging Corporation of America in Valdosta, Ga.; the process engineering group with Rayonier Performance Fibers in Jesup, Ga.; and Technical Sales Intern for Ashland in Rockingham, N.C. and Bennettsville, S.C. She recently returned from a two-week trip to China with faculty and students from the Paper Science program at N.C. State.
The Corrugated Packaging Division established its scholarship program to encourage talented science and engineering students to pursue careers in the corrugated containers industry and to utilize their talents in advancing the science and technology of papermaking.
Back To Top
|
TAPPI CorrExpo 2013, October 7-9 at the JW Marriott in Indianapolis, Ind, USA,. is your one-stop pitstop to fuel your networking and relationship building needs.
Take advantage of these high-octane opportunities:
View the full program to fast track your CorrExpo experience.
Back To Top
|
The Foundations of Leadership Excellence Course is the only leadership course specifically focused on the paper and packaging industry.
Foundations of Leadership Excellence explains the fundamentals of leadership and management skills for emerging leaders, high-potentials, area operating managers, and other technical professionals. This three-day session takes place Oct. 22 - 24, 2013, at the TAPPI Training Facility in Metro Atlanta, Ga., USA.
This course will sell out at 25 participants.
The instructors for this course have approximately 100 years of combined experience in leadership, management, and human resource roles within the pulp and paper industry.
Course curriculum covers industry specific, real-world scenarios. Participants will develop personal leadership skills through the use of influence. They will learn to impact organizations from a 360 degree perspective and how to address the challenges of team building, accountability, performance management, and other critical factors of organizational success.
Back To Top
|
Piping System Training is a course anyone in the piping system industry can use. This course provides real-world practical knowledge for junior engineers, is a good refresher course for senior engineers, and helps operations and maintenance supervisors, design and process engineers, and operators and maintenance personnel better understand how piping systems operate.
This course provides the foundation of piping terminology, mathematics, and the underlying concepts and principles that determine the performance of individual piping system elements and the system as a whole. Piping System Training places an emphasis on understanding the relationship between components that make up the piping system.
Visit the course website to find more information and register.
Earn 1.6 CEUs and carry back with you two indispensable manuals as well as greater confidence in your work.
Back To Top
|
As TAPPI is getting ready to celebrate its 100th Year Anniversary in 2015, we were wondering how much industry expertise we have in this great group of professionals.
So, we decided to post a discussion question on our TAPPI Social Media outlets. We asked, "How many years of paper and/or packaging experience do you have?"
Who knew such a simple question would have such an impressive response.
With more than 7,000 TAPPI members, all over the world, we have counted 650-plus years of industry experience! And that's just counting the first 30 people who have responded. Now you probably can't find that anywhere else . So why don't you join us?
From those "born" into the industry to third generation professionals. From paper to packaging, to sustainability, environment, tissue, converters, and consulting. This TAPPI network has something for everyone.
Become a part of this unique community of paper and packaging professionals, and add your expertise to our group, and network with others to learn something new.
Visit our website to learn more today!
Back To Top
|
The TAPPI Centennial Celebration will be a multi-year long series of outreach events and educational offerings showcasing the proud history and promising future of the global pulp, paper, packaging, and related industries. This once-in-a-lifetime event will expand public awareness, foster further connection, and provide outstanding opportunities for collaboration, growth, and investment in our future for all of those involved. Goals for the TAPPI Centennial Celebration are:
- To honor TAPPI's 100 years of connection, education, and advancement as a foundation for the sustainable success of our members, our industries, and the world we share
- To recognize the achievements of those who built our industry and to inspire those who seek to build its future
- To celebrate the contributions and innovations of the global pulp, paper, and packaging industries to human culture, commerce, health, and social advancement
- To sustain the industry and support its growth, vitality, and future through the TAPPI Foundation.
We invite you to be a part of this momentous event. The sooner you join us the more opportunities there are for recognition of your company, its products, and key innovations. Keep in mind that an early commitment allows you to spread your investment over multiple years' budgets.
For more information on sponsorship and volunteer opportunities please contact dbell@tappi.org.
The sponsorship prospectus can be downloaded online.
Back To Top
|
Do you have a history book gathering dust on your shelf? TAPPI's 100th year is coming soon and we are looking for donations to the TAPPI Library. Specifically, we are interested in histories of companies and mills in the paper and packaging industry (both producers and suppliers). Each donated book will have a bookplate in the front cover recognizing the donor. For more information please contact David Bell.
Please send books to:
c\o David Bell
TAPPI
15 Technology Parkway, South
Suite 115
Peachtree Corners, Georgia 30092
Back To Top
|
|
|
TAPPI Over the Wire | 15 Technology Pkwy. S. | Norcross, GA 30092 USA | Voice: 770.446.1400 | Fax: 770.446.6947
|
 |