 |
|
Weekly Spotlight
The transaction was valued at approximately $1.5 billion, including debt.
Learn More...
|
Company releases newest brochure in its popular "Ed" series that has been delivering educational tips and advice on printing techniques, new technologies, and sustainability topics for more than a decade.
Learn More...
|
Company wants to celebrate its 50 years of existence by providing a meaningful and long-lasting legacy to inhabitants of the Kingsey Falls region in Québec, Canada.
Learn More...
|
Session on Tuesday, September 17 examines pulping and bleaching for specific paper grades, with reports on some of the industry's latest approaches to cooking and bleaching of kraftliner, newsprint, and other printing and writing paper grades.
Learn More...
|
Conference, set for Sept. 30–Oct. 3, 2013, at the Grand Hyatt Denver, Denver, Colo., USA, is a one-of-a-kind technical event for professionals in the nonwoven/engineered fabric industry.
Learn More...
|
Market Roundup
North American lightweight coated (LWC), No. 5 – 40 lb, prices averaged $875 per ton in July, up $5 from June.
Learn More...
|
Containerboard output last month (July) increased 4.1% over June 2013 and 5.3% over the same month last year.
Learn More...
|
Pulp & Paper
Coldwater will continue to operate the Rock Hill, S.C., facility and all employees are being retained.
Learn More...
|
ABB will provide Hengan Group with drives for eight papermaking machines and complete solutions for drives and automation control systems for the 300,000 metric tpy carton paper production line of Lee & Man Paper.
Learn More...
|
JV partners will construct a 45,000-metric tpy satellite precipitated calcium carbonate (PCC) plant at Jindaxing Paper's papermaking facility in Guangxi Province, China.
Learn More...
|
Mill in Point Tupper, Nova Scotia, this week held an open house at the facility to celebrate its upcoming first anniversary.
Learn More...
|
Delivery will include an upgrade to the Metso DNA control system and an upgrade to the Metso IQ quality control system, including a non-nuclear Metso IQ Fiber Weight Measurement, and related comprehensive product training.
Learn More...
|
Shutdown of the 400,000 metric tpy softwood and hardwood pulp mill had been planned for this past spring, but was postponed several times to improve conditions for a possible sale of the mill.
Learn More...
|
The new dedicated starch products website allows current and future customers to explore a range of high-quality products for whatever they make.
Learn More...
|
New structure will consist of UPM Biorefining, UPM Energy, UPM Raflatac, UPM Paper Asia, UPM Paper Europe, and UPM Plywood.
Learn More...
|
Company will re-start production on its Trus Joist® TJI® joists and Microllam® LVL lines in Evergreen, Ala., USA, effective immediately.
Learn More...
|
Containerboard/Packaging
New microsite contains searchable customer service content and recycling resources, as well as access to a variety of devices, including mobile phones and tablets.
Learn More...
|
Company completes the installation of a reconstructed paper machine at the joint venture Mayak-Vega mill in the Penza region of Russia.
Learn More...
|
Carton boxes will be made using TGP's palm pulp kraft liner technology.
Learn More...
|
Nanotechnology
The 2013 Agenda 2020/Forest Service/University Consortium on Cellulose Nanotechnology Meeting will be held at Oak Ridge National Laboratory (ORNL), in Oak Ridge, Tenn., USA, October 29-30
Learn More...
|
|
New Products
Three intuitive product categories are standard, premium, and super premium, with streamlined packaging that places the most important product information front and center and a color system for easy identification.
Learn More...
|
New solution runs entirely and securely inside of a web browser so that users can connect to other InTouch applications at anytime from anywhere, using any mobile device.
Learn More...
|
HydraBan 410 not only has high water resistance, but also oil and grease resistance, while HydraBan 420 is a versatile and economical new coating that is easy-to-run with or without dilution.
Learn More...
|
RH04FG offers high initial tack, securely affixing labels to all fruits and vegetables while increasing automated labeling accuracy.
Learn More...
|
New insulated shipping solution ensures proper refrigerated temperature control for diagnostic kits, blood samples, and other diagnostic specimens.
Learn More...
|
Self-contained, compact system provides automatic control of spray nozzles to ensure uniform and accurate placement of the sprayed solution with minimal waste.
Learn More...
|
Published Pricing
Company will increase the price of its Botnia Nordic Pine NBSK in Europe and the price of Botnia Nordic Pine and Botnia Nordic Strong NBSK pulps in China.
Learn More...
|
People
Holm will be responsible for managing AF&PA's scientific research and identifying research opportunities across the forest products industry.
Learn More...
|
Kevin Braun, replaces Richard Zoulek, who has left the company.
Learn More...
|
Company's board has confirmed several appointments to its Group Executive Team as part of an effort to ensure prompt implementation of profitability improvement and growth plans.
Learn More...
|
TAPPI News
The corrugated packaging industry is heading to Indianapolis, Ind., USA, October 7-9 for TAPPI's CorrExpo 2013. You must register by September 1 to take advantage of CorrExpo's Early Bird Registration Rate.
Learn More...
|
It's not too late to make plans to attend this annual networking conference, September 9-12, 2013 in Raleigh, North Carolina, USA.
Learn More...
|
Ohio TAPPI will sponsor this summer's golf outing at Heatherwoode Golf Club on Thursday, September 5.
Learn More...
|
Gulf Coast TAPPI will host its Fall Meeting on September 11-13 at the Auburn University Conference Center.
Learn More...
|
The schedule for this course, September 17-18, is packed into just two efficiently planned days so that participants get loads of skill and experience without much time away from their own operations.
Learn More...
|
Share your experiences with a company's products or services with your peers in the industry, and enter for a chance to win a seven-night trip to Hawaii.
Learn More...
|
TAPPI will exhibit at the 2013 PACK EXPO, September 23-25 in Las Vegas, Nev., USA.
Learn More...
|
Don't miss out on your chance to present at the largest program for the pulp and paper industry.
Learn More...
|
Being an active member means creating a network that spans the globe.
Learn More...
|
The 2014 PLACE Technical Program Team is actively seeking technical presentations, panels, tutorials, roundtables and case studies from the packaging and academic community to be presented at the conference.
Learn More...
|
The BSC, September 18-20, 2013, has designed a strong technical program for production managers and engineers in the fiberglass mat industry.
Learn More...
|
September event also co-located with Research Forum on Recycling and International Bioenergy and Bioproducts Conference.
Learn More...
|
Register today for the Root Cause Problem Elimination Training Course in Raleigh, NC, USA Oct. 8-10 and save an additional 10 percent with TAPPI.
Learn More...
|
IDCON's Results Oriented Reliability and Maintenance Management Seminar, October 22, in Seattle, Wash., USA will help attendees learn how to build and sustain successful reliability and maintenance improvements.
Learn More...
|
Opportunity for engineers, scientists, and technicians who want to get a handle on one of the difficult contaminants in paper recycling - stickies.
Learn More...
|
Make plans to attend the only industry event dedicated to advancing biorefineries in the forest products industry.
Learn More...
|
Foundations of Leadership Excellence, Oct. 22-24, 2013, is focused on the fundamentals of leadership and management skills for emerging leaders, high-potentials, and area operating managers and other technical professionals.
Learn More...
|
Tighten-up plans to attend the Piping System Training courses planned for two locations coming this fall, October 2-3, in Chicago, Ill., and October 23-24 in Houston, Texas.
Learn More...
|
Join more than 7,000 TAPPI members across the world with 650-plus years of industry experience.
Learn More...
|
This once-in-a-lifetime event will expand public awareness, foster further connection, and provide outstanding opportunities for collaboration, growth, and investment in our future for all of those involved.
Learn More...
|
As TAPPI's 100th year approaches, we are looking for donations to the TAPPI Library.
Learn More...
|
|
Find us on Facebook
Network with us on LinkedIn
Follow us on Twitter
|
Weekly Spotlight
Georgia-Pacific LLC (G-P), Atlanta, Ga., USA, has completed the previously announced merger with Buckeye Technologies Inc. (BKI), Memphis, Tenn. Under the merger agreement, all outstanding shares of BKI's common stock were converted into the right to receive $37.50 per share, net to the holder in cash, without interest, subject to any withholding of taxes required by applicable law. The transaction was valued at approximately $1.5 billion, including debt.
As a result of the merger, G-P acquired all of the outstanding stock of BKI, including ownership of its five manufacturing facilities, global sales offices, and headquarters. Employees of BKI (approximately 1,200) are now employees of G-P, as Buckeye becomes a wholly owned subsidiary.
"We are excited to finalize the acquisition," said John Crowe, BKI's chairman and CEO. "This combination will be very good for a lot of people. Many Buckeye employees will have more opportunities, customers will have more options, community members will continue to have a company with a record of contributing in communities where they operate, and, of course, shareholders get a very nice return."
Jim Hannan, CEO and president of G-P, added that "we are very pleased to welcome the talented Buckeye employees to our company. They, along with Buckeye Technologies' assets, innovation capabilities, advanced technologies, and specialty fibers and nonwovens businesses, provide a significant platform for continued growth and success for our cellulose and consumer products businesses."
As a result of the merger, BKI's common stock will no longer be listed on the New York Stock Exchange or any other securities exchange.
Back To Top
|
NewPage Corp., Miamisburg, Ohio, USA, this week announced the release of Ed #15: Interactive Print, the newest brochure in its popular "Ed" series that has been delivering educational tips and advice on printing techniques, new technologies, and sustainability topics relevant to customers and other stakeholders for more than a decade.
"Ed #15 showcases paper as the original interactive communication medium," says Steven DeVoe, VP, marketing for NewPage. "Paper keeps getting better, finding new ways to connect, not just to a particular audience, but also to other media. With new browser technologies, print has become a uniquely effective gateway to video, websites, e-catalogs, and other information through smart devices. Printed communication is more vital than ever. It's vibrant and highly effective—reaching millions and selling billions."
Julie Davis, senior marketing communications manager for NewPage, adds that "paper has a unique ability to get the reader to participate. You open it, touch it, fold it, pull it, even smell it—and it creates something real, something dimensional and, even more important, something memorable. In Ed #15, customers can see Ed come to life for the first time on the cover of the brochure through Layar® technology, an augmented reality platform that displays videos on your smartphone without ever leaving the printed piece."
DeVoe notes that "print is always coming up with new ways—including Quick Response (QR) codes, Short Message Service (SMS) technology, video-inprint, and browser apps like Layar—to team up with digital media to convert readers into active shoppers and buyers. In Ed #15, you'll learn about the ever-expanding ways paper is interacting with readers and other media to get the word out."
NewPage owns paper mills in Kentucky, Maine, Maryland, Michigan, Minnesota, and Wisconsin, with a total annual production capacity of some 3.5 million tons of paper. The company's portfolio includes coated, supercalendered, and specialty papers.
Back To Top
|
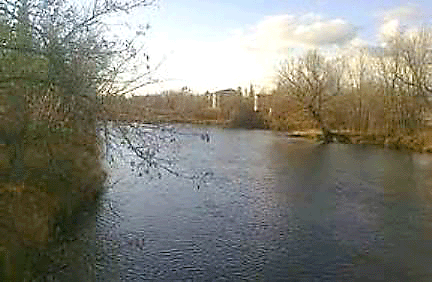 Cascades Inc., Kingsey Falls, Qué, Canada, will celebrate its 50th anniversary in 2014, and will highlight the occasion by opening a new footbridge over the Nicolet River in the community of Kingsey Falls. The announcement was made this week by Laurent Lemaire, the company's executive vice-chairman of the board, together with his brother Alain, executive chairman of the board, and Mario Plourde, president and CEO.
In collaboration with the municipality, the company wants to celebrate its 50 years of existence by providing a meaningful and long-lasting legacy to the inhabitants of the region. The footbridge, made of recovered materials, will serve as a symbolic link between the company's "rich past and its promising future," the company notes.
"We are very close to the people in this region. They adopted us, supported us, and helped make Cascades a success. Without them, none of what we accomplished would have been possible. The footbridge is our way of showing the community our appreciation," explained Laurent Lemaire, the man behind the project.
The structure will add to the quality of life in Kingsey Falls, providing citizens with safe passage across the river on foot or by bicycle, and a unique meeting place with an exceptional view of the river. Sixty-six meters long, the bridge will span the Nicolet River, linking the municipal park with attractions in Parc Marie-Victorin, promoting tourism in the region.
"As an artist, I drew my inspiration for the project from the company's history and my passion for working with recycled materials," said Florent Cousineau, the artist chosen to design the footbridge.
The work began several days ago, and will continue on into the fall. The Lemaire brothers and Plourde have launched an invitation to the public for the inauguration of this new—and not so new—footbridge that will take place in the spring of 2014.
A sod-turning ceremony took place this past Monday, August 26, with Cascades executives and numerous local dignitaries on-hand.
Back To Top
|
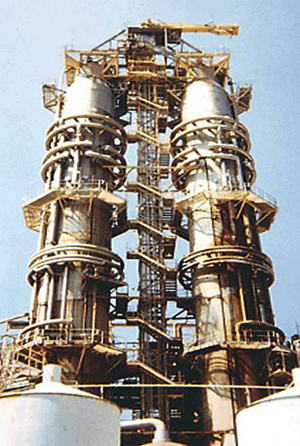 The 2013 TAPPI PEERS Conference in Green Bay, Wis., USA, September 15-18, focuses on advances and emerging developments in the kraft pulping and bleaching arena as well as the chemical recovery island. In the pulp bleaching area, Session 14 on Tuesday, September 17, from 10:30 a.m. – noon, examines pulping and bleaching for specific paper grades, with reports on some of the industry's latest approaches to cooking and bleaching of kraftliner, newsprint, and other printing and writing paper grades.
In the first of three papers in this session, Stefan Antonsson of Metso Sweden AB makes a "Comparison of Cooking Technologies for Production of Softwood Kraftliner Pulp." As Antonsson notes, for many years pulping development for kraftliner has been limited, possibly due to corrugated board standards in many countries having specified basis weight and not strength demands on the corrugated board. With the modifications of Item 222/Rule 41, the situation in the U.S. has changed. Recently, Antonsson says, a new cooking technology has been developed enabling defibration of softwood pulps at considerably higher kappa number with low reject content. Pulp quality as a function of kappa number has been evaluated for this new cooking technology compared with pulp produced using a conventional kraftliner cooking technology. Lower H-factor demands and increased strength, measured as tensile energy absorption, were the most important differences found between the two cooking systems in this study, Antonsson points out.
In the second paper of Session 14, Sankaralingam Pichandi of Tamilnadu Newsprint and Papers examines Casuarina pulp bleaching. Pichandi details how Tamilnadu was able to improve pulp bleachability without affecting pulp strength properties, optical properties, or physical properties, while improving effluent characteristics.
In the session's third presentation, Douglas Reid of AkzoNobel reports on "The Contribution of Pulp Brightness and Optical Brightening Agents to Paper Whiteness." As Reid explains, the desired optical properties of a paper can be achieved through a variety of tools: pulp brightness, optical brightening agents, dyes, or filler qualities. "In this work, we explore the interaction between pulp brightness levels and optical brightening agents (OBA) addition on paper whiteness. Papers were prepared using eucalyptus and softwood kraft pulps bleached to three different brightness levels. The addition of OBA was evaluated as a wet-end only application and as a wet-end/size press application. We found that the initial brightness of the pulp furnish sets the limit for whiteness level achievable with OBA during papermaking. Additionally, in this work, we surveyed the optical properties of a range of commercially available papers. We also evaluated the economics of pulp brightness and OBA addition to show how these two variables can be balanced," Reid says.
Back To Top
|
The INDA (Association of the Nonwovens Fabrics Industry) RISE (Research Innovation and Science for Engineered Fabrics) conference, Sept. 30–Oct. 3, 2013, at the Grand Hyatt Denver, Denver, Colo., USA, is a one-of-a-kind technical event for professionals in the nonwoven/engineered fabric industry who scout for new ideas, new technology, new materials, and new applications to grow their business.
RISE 2013 will provide an array of mind-expanding industry relevant topics that will keep business growth professionals on the leading edge of thought leadership.
More information about the RISE program, speakers, hotel, and registration is available online.
Back To Top
|
Market Roundup
North American lightweight coated (LWC), No. 5 – 40 lb, prices averaged $875 per ton in July, up $5 from June, according to Mark Wilde, senior analyst with Deutsche Bank. LWC prices ranged from $680 to $1,240 per ton.
Coated free sheet (No. 3 rolls – 60 lb.) prices averaged $950 per ton in July, an increase of $5 per ton from June. CFS prices ranged from $720 to 1,100 per ton in July
.
Uncoated free sheet (20 lb. – Repro Bond) prices averaged $1,015 per ton last month, which was flat compared with June. UCFS prices varied from $650 to $1,200 per ton in July, Wilde noted.
Back To Top
|
U.S. Containerboard production last month (July) increased 4.1% over June 2013 and 5.3% over the same month last year, as reported by AF&PA (Washington, D.C., USA) in its recently released July 2013 U.S. Containerboard Statistics Report. The month-over-month average daily production increased 0.7%.
The containerboard operating rate for July 2013 dropped 0.4 points from June 2013, from 99% to 98.6%.
Back To Top
|
Pulp & Paper
![]() 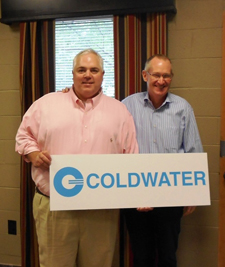 Coldwater Group Inc, Atlanta, Ga., USA, has acquired BladePro of Rock Hill, S.C. Coldwater will continue to operate the Rock Hill facility and all employees are being retained.
BladePro is a manufacturer of doctor blades for the paper industry. BladePro President Joe Christopher has joined Coldwater as manager of all doctor blade business from Coldwater's U.S. operations.
"We are very pleased to have Joe and BladePro join Coldwater. Joe's customer oriented service philosophy fits very well with our culture. This acquisition builds on our R&E Kirwin Ltd. acquisition last year in the U.K., as we continue to build the most reliable one-stop source for paper machine consumables to the global paper industry," said David Withers, president of Coldwater Group.
"Coldwater is a good fit for us. We operate very similar service driven manufacturing businesses with the flexibility to meet our customer's needs. We plan to keep doing what we've been doing, but now have more resources to expand our business," Christopher added.
In the photo are Joe Christopher, president of BladePro (left), and David Withers, president of Coldwater.
Back To Top
|
ABB, Ireland, this week reported that it has finalized two deals in the papermaking industry, providing China-based Hengan International Group and Guangdong Lee & Man Paper Manufacturing with high-efficient drives and automation control products to help them achieve efficient and stable operation. According to the agreements, ABB will provide Hengan Group with drives for eight papermaking machines, and complete solutions for drives and automation control systems for the 300,000 metric tpy carton paper production line of Lee & Man Paper.
.
Hengan Group is one of the largest manufacturers of hygiene products in China. It has maintained a partnership with ABB since 1996. ABB's drives, process control systems, motor control systems, and power distribution systems account for 80% of all electric and automation systems used by Hengan Group's 17 papermaking machines. Lee & Man Paper is a top global carton producer. Since 1991, all of its electric and automation systems for 12 papermaking machines and three pulp mills have been solely provided by ABB.
Erik Oja, head of Process Automation Division, ABB North Asia and China, said that "China is the world's largest papermaker, but the industry is currently undergoing structural adjustments and transformation. ABB is a leading supplier in the global pulping and papermaking industry with the most complete automation, instruments, and electrical devices. We are proud to lead the development of automation technologies in the global Pulp & Paper market. ABB will continue to uphold its "In China and for China" strategy and contribute to the sustainable development of the industry by providing innovative technologies and leading solutions to help Chinese papermakers achieve industrial modernization."
Back To Top
|
Minerals Technologies Inc., New York, N.Y., USA, has entered into a joint venture agreement with Nanning Jindaxing Paper Industry Co. for the construction of a 45,000-metric tpy satellite precipitated calcium carbonate (PCC) plant at Jindaxing Paper's papermaking facility in Guangxi Province, China. Jindaxing Paper, a privately owned paper company, is a producer of uncoated free sheet papers.
The satellite facility, which will produce PCC as a filler pigment for Jindaxing Paper, will become operational in the fourth quarter of 2014.
"We are pleased to provide our PCC to an emerging paper company like Jindaxing Paper," said Robert S. Wetherbee, CEO of Minerals Technologies. "This agreement, our third in China within the last year, confirms the momentum of our geographic expansion strategy, and brings the number of satellite plants we have in China to six. It should also be noted that Minerals Technologies' cost-saving, FulFill® high-filler technology was a differentiator in obtaining the contract with Jindaxing Paper, and represents our commitment to bring our best technology to all our customers as soon as possible."
PCC is a specialty pigment for filling and coating high-quality paper. By substituting PCC for more expensive wood fiber, customers are able to produce brighter, higher quality paper at lower cost. In 1986, Minerals Technologies originated the satellite concept for making and delivering PCC on-site at paper mills and the concept was a major factor in revolutionizing papermaking in North America, the company notes. Today Minerals Technologies has 59 satellite plants in operation or under construction around the world.
Back To Top
|
The Port Hawkesbury Paper mill in Point Tupper, Nova Scotia, this week held an open house at the facility to celebrate its upcoming first anniversary. The Stern Group acquired the mill from NewPage in September 2012. New owner Ron Stern reports that the mill is now turning a small profit, according to Canada's CTV News.
Stern told reporters at the event that the mill's profit is "not very big." He added that "as a matter of fact, it is pretty skinny and it's nowhere near where we need to get to for a sound future, but it is a big deal to be able to say we're operating profitably."
Only one of the mill's two production lines reopened, and only about half the staff was brought back. "We would have liked to have 600 jobs, but there's 300 jobs, with good incomes," said Port Hawkesbury Mayor Billy Joe MacLean. "Full-time work with a future, I guess we couldn't hope for anything better than that."
According to a report by ForestTalk.Com, Stern said that it is likely the mill's older newsprint machine will soon be sold off. The company has operated only the mill's newer supercalenderd paper machine since starting back up. Mill officials have said there isn't enough fiber available in Nova Scotia to operate the older paper machine, and the company is not willing to go to the expense of importing fiber as the mill's previous operator, NewPage Port Hawkesbury, did, ForestTalk.com added.
"We're here for the long haul," says Stern. "I'll tell you that right now, we're committed to this place. We're stubborn and together, with the people in this mill, we'll move heaven and earth to make this mill succeed."
Back To Top
|
The Sofidel Group, Italy, has placed an order with Metso, Finland, to upgrade the automation of tissue machine 1 and water treatment at its Délipapier mill in Frouard, France. The delivery will include an upgrade to the Metso DNA control system and an upgrade to the Metso IQ quality control system, including a non-nuclear Metso IQ Fiber Weight Measurement, and related comprehensive product training.
According to François Lecomte, Délipapier Paper Mill director, "this significant upgrade will enhance productivity, allowing Délipapier to bring better quality to its customers, especially for the flagship brands of Sopalin and Le Trèfle in France along with Lotus and Moltonel in Benelux."
The upgrade will be implemented using innovative virtualization technology, which aims at delivering more flexible datacenters to reduce costs thanks to server consolidation. This solution will significantly reduce the number of computers normally required for an upgrade and thus decrease both the purchase cost of computers and cabinets, and the operating expenses of such devices, together with the space needed to install them.
Metso notes that virtualization allows it to deliver efficient remote support and maintenance of the control system over its entire lifecycle. Patch deployment, server maintenance, software compatibility and further upgrades can all be executed more efficiently.
The project is scheduled to be completed in October. The value of the order will not be disclosed.
Back To Top
|
Södra. Sweden, permanently shuttered its Tofte chemical pulp mill in Norway on August 25. A spokesperson for the Swedish pulp manufacturer told EUWID Pulp and Paper, Germany, that shutdown of the 400,000 metric tpy softwood and hardwood pulp mill had been planned for this past spring, but was postponed several times to improve conditions for a possible sale of the mill.
Södra's decision to close the mill was based on "long-term difficulties with achieving profitability at the plant," as announced early last month. The company said then that It was not possible to turn the tide despite extensive measures being implemented. A process began in late 2012 with a view to finding a buyer. However, the discussions proved fruitless, and thus the mill has been permanently closed. Some 280 staff members at the mill were affected.
The mill at Tofte was purchased by Södra in 2000. Its production capacity amounts to 400 000 metric tons of chemical paper pulp. The factory employs 280 staff.
The company had decided to part with the Tofte mill due to permanent problems to achieve adequate returns. Södra took over the Tofte and Folla pulp mills from Norske Skog in 2000. Last January, Södra sold the 105,000 tpy CTMP Folla pulp mill to the Austrian cartonboard producer Mayr-Melnhof.
Following the closure of the Tofte pulp mill, Södra is withdrawing from pulp operations in Norway, EUWID notes. The company now runs three Swedish pulp mills in Mönsterås, Värö, and Mörrum with a total pulp output capacity of 1.6 million metric tpy.
Back To Top
|
Tate & Lyle, U.K., reports that it has launched a new Global Industrial Starches website. The new dedicated starch products website allows current and future customers to explore a range of high-quality products for whatever they make—paper, corrugated, adhesives, building materials, laundry, or other products.
Tate & Lyle is a global provider of ingredients and solutions to the papermaking, food, beverage, and other industries. More information about the company and its products and services is available online.
Back To Top
|
UPM, Helsinki, Finland, this week reported that it will implement a new business structure to "drive clear change in profitability." The company also will seek to simplify and further develop its business portfolio
.
UPM's new structure will consist of the following Business Areas and reporting segments: UPM Biorefining, UPM Energy, UPM Raflatac, UPM Paper Asia, UPM Paper Europe, and UPM Plywood. Forests and wood procurement will be reported in Other operations. The new structure will be valid as of November 1.
The new Paper Business Areas will be located at the centers of their markets. UPM Paper Asia will be headquartered in Shanghai, China, and UPM Paper Europe in Augsburg, Germany. The Group Head Office will remain in Helsinki, Finland.
"Changes in management structure (see People Section below) will sharpen the targets and required actions for each business. We will address the competitive challenge in mature European businesses and drive profitable growth outside of Europe and in biorefining. The new management structure will also increase transparency of the company performance," said Jussi Pesonen, president and CEO of UPM. "We are determined to change UPM. We will also seek to simplify our business portfolio and uncover the value of our assets. These opportunities will be explored in parallel with the profitability improvement and growth initiatives and may involve changes in ownership structures," he added.
The current Business Group structure, established at the end of 2008, will be discontinued.
"Within the Business Group structure, we have created commercial platforms and market driven business organizations for Energy and Pulp. We have also achieved profitability turnaround in Timber and Plywood businesses, and restructured our European label business. Now these are healthy UPM businesses each in their own right," Personen noted. "Although the Paper Business Group has been able to improve efficiency and managed change and integration processes professionally, we now need to move into a more simple and scalable structure to improve performance further," he pointed out.
In regard to the simplified business structure, UPM has identified actions with an overall profit improvement impact of EUR 200 million in its existing businesses. Each business will implement a profit improvement program with simplified business model and variable and fixed cost savings. These planned actions do not include additional capacity closures at this time.
Profit improvement includes the remaining part of the EUR 90 million savings announced this past January, as well as further actions resulting from the new business structure and consequent profit improvement programs.
UPM said that it will follow and update the progress of the program in its quarterly reporting. The full impact of the program is expected to materialize by the end of 2014, as compared with the Q2/2013 results.
Pesonen said that since 2007 UPM's Energy, Pulp, Label, and Asian Paper businesses have grown by 43% in the top line. "These businesses have been not only growing but also profitable and enjoy positive long term fundamentals. Biofuels, woodfree specialty papers in China, and continued growth in UPM Raflatac will provide top line growth for UPM in the coming years. In addition, we have identified opportunities to expand production in our existing pulp mills. With these development initiatives we are targeting additional EBITDA contribution of EUR 200 million when in full operation."
The total investment requirement in these projects is EUR 680 million, including the earlier announced EUR 540 million in the Changshu paper machine and Lappeenranta biorefinery. EUR 60 million has already been invested, and the total remaining capital expenditure in the coming three years would be EUR 620 million.
Back To Top
|
Weyerhaeuser, Federal Way, Wash., USA, reports that it will re-start production on its Trus Joist® TJI® joists and Microllam® LVL lines in Evergreen, Ala., USA, effective immediately. The company will be investing capital in the engineered lumber products facility after a four-year closure due to previously weak wood products demand in North America. It also plans to hire 100 new employees at the facility by the end of 2014. Robert (Bob) Doll has been selected as plant manager and will be on site beginning August 30.
"Customer demand for engineered wood products has improved over the last year and our Evergreen facility is the ideal location to add production capacity of our Trus Joist® TJI® Joists and Microllam® LVL building products," said Jan Marrs, manufacturing manager for Weyerhaeuser Engineered Lumber Products. "With our markets improving and positive support from both the state and local community, we are looking forward to re-starting this facility."
The Evergreen Trus Joist facility was acquired by Weyerhaeuser in 2000 and has an estimated annual production of 2 million cubic feet of Microllam LVL and 120 million lineal feet of TJI Joists.
In Alabama, Weyerhaeuser also operates a lumber manufacturing facility in Millport, a Nursery Tree Improvement Center in Camden, and it sustainably manages more than 547,000 acres of timberland in 23 counties.
Back To Top
|
Containerboard/Packaging
Sonoco Recycling LLC, a unit of Sonoco, Hartsville, S.C., USA, one of the largest packaging recyclers in North America, this week announced the launch of a new microsite that provides visitors with searchable customer service content and recycling resources, as well as access on a variety of devices, including mobile phones and tablets. The new website includes a convenient contact form that allows visitors to request information from the company quickly and easily, a new locations database where visitors can more easily identify Sonoco Recycling facilities near them, more expansive use of video (including the Education page where visitors can learn how recycling works with the Remarkable Recyclables, an animated video), and a home page that regularly rotates content, providing visitors with a prominent space to quickly learn about available services and resources or news announcements.
"Our new microsite makes it easier for customers to find us and the information on recycling they need, whether they are a municipality, CPG, government agency, or a grocery store chain," said Ray Howard , GM, Sonoco Recycling. "Additionally, the site provides a platform where we can share educational assets for teachers and parents, such as the Remarkable Recyclables video, which teaches kids about what happens to materials after they're placed in the recycle bin, or our Green Steps curriculum for environmental education."
The new site also features a services launch pad, which is a list of the top industries and markets that Sonoco Recycling serves, with direct links to full breakdowns of services offered, making it easier for potential and existing customers to find content relevant to them. A database-driven event calendar allows website visitors to quickly see all upcoming events, including trade shows, recycling drives, and educational events.
Sonoco Recycling annually collects nearly 3 million tons of old corrugated containers, various grades of paper, metals, and plastics. In addition, company experts provide secure, reliable, and innovative recycling solutions to residential and commercial customers. Currently, Sonoco Recycling operates five material recovery facilities (MRFs) and serves nearly 150 communities in which curbside-collected residential and commercial materials are processed.
Back To Top
|
Papcel, Litovel, the Czech Republic, reports that it has completed the installation of a reconstructed paper machine at the joint venture Mayak-Vega mill in the Penza region of Russia. The 2,600 mm-wide at the reel) machine will produce containerboard fluting and testliners. It has a production capacity of 70,000 metric tpy and an operating speed of 700 m/min.
The 11,000 sq. meter main building has been constructed, network engineering is completed, and the automation system has been installed, according to Papcel. Startup of the machine is set for the beginning of September. The Papcel project reportedly is valued at EUR 22.7 million.
The machine is reconstructed from a unit dismantled at Alce in Italy beginning in August 2011. It may also be used to produce a plasterboard in the future.
Back To Top
|
Thai Gorilla Pulp Ltd. (TGP), Rayong, Thailand, reports that it has received an order for several million in-flight boxes from Thai Airways International Public Co. The carton boxes will be made using TGP's palm pulp kraft liner technology.
TGP CEO Ryosuke Tanaka noted that "last year our company received the Environmental Award by the governor of Bangkok, and now we welcome Thai Airways as a new customer. Being recognized by a prestigious company such as Thai Airways is not only a major step forward for our business, but it also shows that highly innovative companies are accepted in Thailand. Being green, environmental, and sustainable does not necessarily mean more expensive. We continue to focus on achieving our goal to protect the rainforests and forests of our earth."
In 2008 (when it was founded), TGP, a 100% subsidiary of Pulp GreenTech Holding AG in Liechtenstein, invented and since has continuously improved pulping technology using palm oil waste—the Empty Fruit Bunch (EFB). Since 2008, TGP has successfully developed methods to convert Palm Oil EFB into paper and paperboard products.
Back To Top
|
Nanotechnology
The 2013 Agenda 2020/Forest Service/University Consortium on Cellulose Nanotechnology Meeting will be held at Oak Ridge National Laboratory (ORNL), in Oak Ridge, Tenn., USA, October 29-30. Because the meeting is being held at ORNL, security clearances need to be obtained to get on site. Names of all attendees are needed at least four weeks prior to the meeting. Non-U.S. citizens can attend but need the full four weeks to make it through security checks (please send registration information no later than September 27).
As part of the meeting—in addition to hearing about all of the research program accomplishments and plans from the Agenda 2020/Forest Service/University Consortium—ORNL and NIST staff will also make presentations on the cellulose nanomaterial projects that they have underway. ORNL has also arranged for a more in-depth tour of its facilities to see capabilities that fit with nanocellulose interests. Included on the tour are:
- The Spallation Neutron Source (combined with the Center for Nanophase Materials Science or CNMS)
- BioEnergy Science Center, and High Temperature Materials Laboratory (HTML).
Information about the Spallation Neutron Source, Center for Nanophase Materials Science, and the BioEnergy Science Center is available online.
The registration fee will be $45 to cover the costs of lunches and breaks. For information on registering, email, telephone, or fax Jane Kohlman at USDA Forest Service, Forest Products Laboratory, Madison, Wis., Tel: 608.231-9479; Fax 608.231-9567.
Make lodging reservations at the DoubleTree by Hilton Hotel Oak Ridge–Knoxville, 215 S. Illinois Ave., Oak Ridge, TN 37830; Phone: 865-481-2468. Reservations can also be made online. The group room rate is $91/night + tax. The block of rooms will be held until October 9.
Back To Top
|
New Products
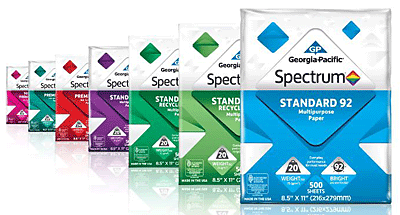 To simplify paper purchasing for businesses, Georgia-Pacific, Atlanta, Ga., USA, says that it is re-launching its Spectrum® brand of business communication papers in three intuitive product categories—standard, premium, and super premium—with streamlined packaging that places the most important product information front and center and a color system for easy identification.
"At Georgia-Pacific, we listen to our customers," said Bob Hieronymus, VP, uncoated free sheet category, Georgia-Pacific Communication Papers. "Our research showed that business users place importance on streamlining their purchasing processes and simplifying the paper selection decision. At the same time they do not want to sacrifice quality or value in the paper they use. Spectrum papers are now grouped into three categories with simplified product names that quickly communicate product quality and help make the paper choice easier for different printing applications."
Based on a paper's weight, the three product tiers help facilitate quick decisions by corporate purchasing professionals and end users:
- Standard – In a basic weight for everyday office needs, these multipurpose papers are ideal for printing copies, drafts, and emails. They are available in 92 and 96 bright options along with 30% and 100% recycled content options.
- Premium – These inkjet and laser papers have extra thickness that helps reports, flyers, and important documents look appealing and feel durable. Both 92 and 96 bright options are available in this category.
- Super Premium – New to the G-P Spectrum paper offering, this inkjet and laser paper is the thickest, brightest, and smoothest of the three paper categories for documents that really need to stand out—like presentations and brochures.
Most of the Spectrum paper cartons feature a new EZ Access™ carton design, which allows for easier access to the carton contents while providing a more aesthetically appealing storage option in office applications.
More information on the new product packaging tools for refining and simplifying paper decisions is available online
Back To Top
|
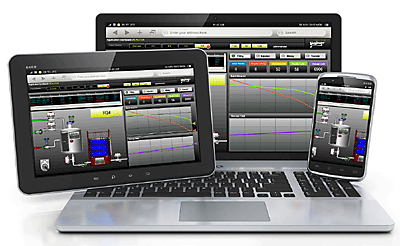 Invensys, Houston, Texas, USA, has released its Wonderware InTouch Access Anywhere software solution for accessing plant-floor data. The new solution runs entirely and securely inside of a web browser so that users can connect to other InTouch applications at anytime from anywhere, using any mobile device, including Microsoft Surface tablets, iPads, iPhones, Androids, and others. The software also supports Macintosh and Linux-based computer systems, as well as Microsoft Windows PCs and laptops. And because users are not required to install any software on their mobile device, the offering is easy to deploy, manage, and maintain.
"This new offering complements Invensys' broader mobile strategy to provide and improve real-time visualization, collaboration, and execution at multiple levels of an organization," according to Craig Resnick, VP, ARC Advisory Group. "Along with delivering mobile solutions for reporting, decision-support, dashboards, workflow, and workforce execution, this new offering also brings HMI visualization capabilities to mobile devices. These capabilities extend the company's operations management software portfolio by providing plant operators and other key individuals with modern process optimization tools, regardless of their location or the task being performed, and in real time."
InTouch Access Anywhere software is the newest capability in the company's progressive suite of mobility solutions, which now includes workflow, reporting, analytics, visualization, maintenance management, operator training, data gathering, and procedure management. In 2010, Invensys released its IntelaTrac offering, a mobile reporting and decision support system that enables workflow, data collection, and general task management. In 2011, the company released its SmartGlance solution, an industrial reporting application that delivers secure, on-demand access to rich, graphical reports from any operations data source via mobile devices. In 2012, Invensys released its Work Tasks mobile offering, enabling plant personnel, regardless of their location, to respond immediately to assigned work tasks via the company's ArchestrA Workflow software.
Back To Top
|
Michelman, Cincinnati, Ohio, USA, has introduced two additions to its line of HydraBan® water resistant coatings for converters of paper and corrugated. New HydraBan 410 not only has high water resistance, but also oil and grease resistance.
HydraBan 420 is a versatile and economical new coating that is easy-to-run with or without dilution, and can be applied inline on the corrugator from the wet or dry end, with a rod or blade coater, or offline. It can also be applied by flexo.
Back To Top
|
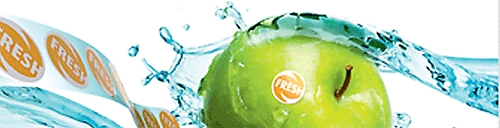 UPM Raflatac, Mills River, N.C., USA, has launched RH04FG, a hotmelt adhesive approved by the U.S. FDA for direct contact with fruit and vegetable skin. RH04FG offers high initial tack, securely affixing labels to all fruits and vegetables while increasing automated labeling accuracy.
Currently, this adhesive is paired with Foodgloss OBA, an FDA-approved lightweight glossy paper that is optical brightening agent-free. "We're pleased to offer a unique fruit and vegetable labeling solution that goes the extra mile to increase customer confidence," says Jean-Marc Borel, Specials Business director, Americas. "Both the facestock and adhesive meet tough FDA requirements for direct contact with raw fruits and vegetables."
Foodgloss OBA and RH04FG meet FDA requirements 21 CFR 176.170 and 176.180 for facestocks and 21 CFR 175.125(b)(2) for adhesives.
Back To Top
|
Sonoco ThermoSafe, Arlington, Heights, Ill., USA, a unit of Sonoco, has launched its new Envoy Diagnostic insulated shipping solution to ensure proper refrigerated temperature control for diagnostic kits, blood samples, and other diagnostic specimens.
The Envoy Diagnostic product line features the two-day Envoy shipper combined with one of five available diagnostic kits. The system provides the necessary components used in UN DOT, IATA, and USPS certifications for shipping specimens and infectious substances. The entire Envoy Diagnostic series gives consistent 2- to 8-degree Celsius temperature control while exposed to the real-world ISCsilver® ambient profile, which is representative of the ambient conditions diagnostic specimens are typically exposed to during shipment.
"To better target new disease indications and markers, the diagnostic market has been increasing its research and development efforts, as well as performing more tests," said Marianne Hoonakker-Kelly, market manager, Sonoco ThermoSafe. "To better serve this market, we've combined two of our well known product lines; the Envoy Shipper and our Sonoco ThermoSafe Diagnostic Kits. The pairing of these two products allows our customers to receive a complete solution to ensure the thermal integrity of the diagnostic specimens with the lowest total cost solution."
Back To Top
|
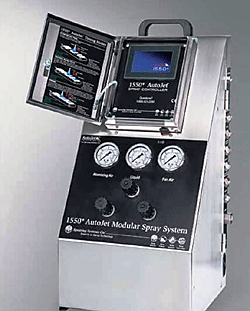 Spraying Systems Co., Wheaton, Ill., USA, this week announced that the next generation of its AutoJet Model 1550 Modular Spray System is now available. Designated as the Model 1550+, this self-contained, compact system provides automatic control of spray nozzles to ensure uniform and accurate placement of the sprayed solution with minimal waste. The system is ideal for coating, marking, and lubricating operations.
The AutoJet Model 1550+ Modular Spray System operates electrically- and pneumatically-actuated spray nozzles. When used with Spraying Systems Co.'s hydraulic PulsaJet® automatic nozzles, Pulse Width Modulated (PWM) flow control is possible. Automatic adjustment of flow rate based on line speed, nearly instantaneous adjustment of flow rate, and the ability to maintain low flow rates with larger spray orifices to reduce clogging are just a few of the benefits of PWM flow control.
An easy-to-use touch screen, new timing modes, and a food-contact version are among the enhancements to the system.
Back To Top
|
Published Pricing
Metsä Fibre, Finland, reports that it will increase the price of its Botnia Nordic Pine NBSK (northern bleached softwood kraft) in Europe, effective September 1. The new price will be $880 per metric ton, CIF Metsä Fibre's frequently used European ports of destination. All other terms and conditions remain unchanged.
The company also said that it will increase the price of Botnia Nordic Pine and Botnia Nordic Strong NBSK pulps in China, effective September 1. The new price of Botnia Nordic Pine is $710 per metric ton and the price of Botnia Nordic Strong is $720 per metric ton. All other terms and conditions remain unchanged.
Back To Top
|
People
The American Forest & Paper Association (AF&PA), Washington, D.C., USA, has selected Stewart Holm as chief scientist. Holm will be responsible for managing AF&PA's scientific research and identifying research opportunities across the forest products industry.
"We are excited to have Stewart on board to develop and implement a comprehensive science and research strategy in support of AF&PA's policy objectives. His management of key programs in product stewardship, chemical safety and toxicology, coupled with his knowledge of the forest products industry, make him a great addition to AF&PA," said AF&PA President and CEO Donna Harman.
Holm has provided expert scientific oversight, guidance, and strategic thinking to multi-national corporations related to public policy issues before the U.S. Environmental Protection Agency, Occupational Safety and Health Administration, and the Food and Drug Administration. He holds a Bachelor of Arts in chemistry and biology from Drury University and a Master of Science in oceanography from the Florida Institute of Technology.
Back To Top
|
PPG Industries, Pittsburgh, Pa., USA, this week announced that Kevin Braun has been appointed VP of industrial coatings, Americas, effective immediately, replacing Richard Zoulek, who has left the company. Braun was most recently appointed VP, global raw materials and Americas purchasing.
"Kevin is a superb leader who combines excellent product and manufacturing experience with a keen awareness of the industry and market trends," said Viktor Sekmakas, PPG EVP
.
Braun, who joined PPG in 1991, also has served as PPG's GM, silica products, and GM, architectural coatings, Australia/New Zealand. Previously, he held roles of increasing commercial responsibility in industrial coatings, fiber glass, and architectural coatings in the U.S. He holds a Bachelor of Science in industrial engineering from the University of Pittsburgh and a Master of Business Administration from Capital University.
Back To Top
|
To ensure prompt implementation of profitability improvement and growth plans (see article in Pulp & Paper section above), UPM, Helsinki, Finland, says that its board of directors has confirmed several appointments to its Group Executive Team. The appointments are:
Heikki Vappula has been appointed EVP, UPM Biorefining, which consists of pulp, timber, and biofuels businesses. It has an annual capacity of 3.2 million metric tons of pulp, produced by four pulp mills in Finland and Uruguay, plantation operations, four sawmills in Finland and one in Austria, and a biodiesel plant under construction in Lappeenranta, Finland. In H1 2013, sales of the business was EUR 1,044 million and EBITDA EUR 234 million. Heikki is currently president for UPM's Energy and Pulp Business Group.
Tapio Korpeinen has been appointed EVP, UPM Energy, which operates in power generation and physical and derivatives trading. The business assets consist of UPM's hydro power assets in Finland and shareholdings in energy companies, with total electricity generation capacity of 1,721 MW. In H1 2013, sales of the business was EUR 242 million and EBITDA EUR 106 million. Tapio will also continue in his current role as the CFO, including responsibilities for Finance and Control, Treasury, Investor Relations, IT, Sourcing, and Real Estate.
Tapio Kolunsarka has been appointed EVP, UPM Raflatac as of September 1. Kolunsarka, a new member of the Group Executive Team, is currently SVP, UPM Raflatac, Emea. His predecessor, Jussi Vanhanen, is leaving the company of his own initiative to pursue a long-standing personal project as well as to act as management adviser in one of the leading consulting companies. UPM Raflatac manufactures self-adhesive label materials for product and information labeling. In H1 2013, sales of the business was EUR 608 million and EBITDA EUR 54 million
Kim Poulsen has been appointed EVP, UPM Paper Asia. UPM Paper Asia consists of UPM Changshu paper mill in China and label paper operations in Tervasaari and Jämsänkoski mills in Finland. In H1 2013, sales of the business was EUR 557 million and EBITDA EUR 84 million. The production capacity of UPM Paper Asia is 1.5 million metric tpy of fine and label papers. Poulsen is currently EVP, Paper Business Asia Pacific and Corporate Relations.
Bernd Eikens has been appointed EVP, UPM Paper Europe. Eikens, a new member of the Group Executive Team, is currently SVP, Supply Chain, UPM Paper Business Group. UPM Paper Europe produces magazine paper, newsprint, and fine paper in 19 paper mills in Europe and North America. In H1 2013, sales of the business was EUR 2,730 million and EBITDA EUR 66 million. The production capacity of UPM Paper Europe is 10.3 million metric tpy of magazine, newsprint, and fine papers.
Mika Sillanpää has been appointed EVP, UPM Plywood. Sillanpää, a new member of the Group Executive Team, is currently SVP, Plywood. UPM Plywood is capable of producing approximately one million cubic meters per year of plywood and veneer products in Finland, Russia, and Estonia. In H1 2013, sales of the business was EUR 219 million and EBITDA EUR 21 million.
Kari Ståhlberg has been appointed EVP, Strategy. A new member of the Group Executive Team, he is currently SVP, Corporate Strategy.
Jyrki Ovaska has been appointed EVP, Technology, responsible for R&D, Investment Management, wood plastic composite unit UPM Profi, and New Business Development. Ovaska is currently president of UPM's Paper Business Group.
Hartmut Wurster EVP, Technology, will retire after 12 years at UPM and 31 years of service in the industry. In addition to his main responsibilities, his active contribution in the German stakeholder relations has been invaluable, the company notes.
Pirkko Harrela, currently EVP, Corporate Communications, has been appointed EVP, Stakeholder Relations, including responsibilities for Corporate Communications, Brand Management, Environmental Affairs, Corporate Relations, and Responsibility.
All members of the Group Executive Team report to the president and CEO. Unless otherwise noted, the appointments are valid as of November 1.
Back To Top
|
TAPPI News
The corrugated packaging industry is heading to Indianapolis, Ind., USA, for TAPPI's CorrExpo 2013. Join your colleagues on October 7-9 and don't miss out on this year's activities, including:
- Keynote presentations by industry leaders Bob Chapman, CEO and chairman of Barry-Wehmiller and Alexander Toeldte, president and CEO - Boise Inc.
- Pre-Conference Workshops. On Sunday and Monday, Dick Target, On Target Consultants, will present "Flexo and Rotary Diecutters Calibration Workshop (Sustain Board Caliper and Printing Capabilities)." On Monday, Steve Farm and Ron Bridges, Partners, Genesis Performance Partners LLC will present "The Essentials of Successful Leadership." Separate registration is required for these workshops.
- Eye Opener Sessions kicking off at 7:00 a.m. on Tuesday and Wednesday with 90-min. presentations tackling timely topics affecting box plants today, with plenty of time for questions and interaction with the speakers. Topics covered include: Management/Planning, Printing, Energy Management, and Paper Savings. Want to attend more than one? Don't worry, the sessions will be repeated on Wednesday.
- Evening Gala at the Indianapolis Motor Speedway Museum sponsored by Alliance Machine Systems LLC and AG Stacker on Tuesday. The museum is situated in the center of the famed oval and is home to a collection vintage and present-day racing automobiles, the Borg Warner Trophy, and legendary photos. In addition to dining, you and your colleagues will be treated to a lap around the famed track in one of the track's mini buses.
- Cutting edge technology on the Trade Show Floor Tuesday and Wednesday afternoons. Fast track your exhibit experience by reviewing the list of exhibitors prior to arriving at CorrExpo.
This is a reminder that you must register by September 1 to take advantage of CorrExpo's Early Bird Registration Rate!
Back To Top
|
You can still get involved, build contacts and learn at the 25th Pulp and Paper Reliability and Maintenance Conference – a popular "how-to" event held expressly for operations and maintenance professionals in the industry. This event will take place September 9-12 in Raleigh, North Carolina, USA.
Sponsored by IDCON and Metso, this conference offers:
- Leading industry keynote speakersInsightful presentations
- Technical information
- Solutions to improve reliability
- Techniques to impact the bottom line.
Find out more and register online.
Back To Top
|
Gulf Coast TAPPI Local Section will host its Fall Meeting in partnership with the Alabama Pulp and Paper Council and Auburn Pulp & Paper Foundation, September 11-13. The meeting will be held at the Auburn University Hotel & Conference Center.
More information is available at the meeting website.
Back To Top
|
Registration is now open for the 2013 TAPPI Corrugated Press Hands-On Maintenance Workshop, September 17-18 at the Global Equipment USA Warehouse in Skokie, Ill., USA.
This unique course gives you an unprecedented opportunity to get hands-on training on how to audit converting machines. With only 18 seats available, you will have ample opportunity to get your questions answered by instructors Tom Pearce (Pearce Corrugated Consulting), John Bingham (Pamarco), Jim Wegemer (INXinc), Chuck Bobeldyk (Mark-Maker Co.), Randy Kesselring (MarquipWardUnited), as well as representatives from Global Equipment. The schedule for this course is packed into just two efficiently planned days so that participants get loads of skill and experience without much time away from their own operations.
Who should attend?
This Intermediate-level course offers indispensable hands-on maintenance training for corrugated industry plant managers and supervisors, engineers, maintenance teams, and machine operators.
You could pour over all of the how-to manuals available and still not retain this level and quality of working knowledge. Completing this workshop will enable you to:
- Use the basic tools to mechanically audit and troubleshoot a press
- Understand press audit procedures for process centering, better quality products, and increased productivity
- Discuss anilox roll selection, press "fingerprinting," inks and substrates, quality defects amd cause(s), and scoring.
Register and join TAPPI or renew your membership to receive the best rates.
Back To Top
|
TAPPI is pleased to announce the new business reviews section on its buyers guide. Now you have the opportunity to share your experiences with a company's products or services with your peers in the industry.
Write a review to be entered for a chance to win airfare and seven nights at a luxury resort hotel in Hawaii.
What are the benefits of writing a review?
- 7 of 10 people read reviews before making a purchase
- 51% of buyers trust strangers' opinions over friends, family, and trusted business advisors
- Consumers trust online reviews and other consumer feedback 12 times more than marketing messages from businesses
- Local business reviews are read by 85% of consumers
- Reviews not only give consumers the ability to share their opinions about the products or services they buy, but it also offers businesses a way to evaluate and track what people are saying about them
- Good reviews lead to more purchases, and negative reviews allow marketers to make adjustments to products and show their willingness to work with their consumers (both the consumer and the brand benefit from these opinions).
Back To Top
|
As part of a partnership agreement with PMMI, the Association for Processing and Packaging Technologies, TAPPI will exhibit at the 2013 PACK EXPO. PACK EXPO, Sept. 23-25, 2013, in Las Vegas, Nev., USA, is North America's largest packaging and processing trade show.
"TAPPI is excited about our partnership with PMMI and our participation in PACK EXPO," notes Larry N. Montague, TAPPI president and CEO. "Packaging is a major part of our industry and as an exhibitor at an industry leading trade show we will have the opportunity to interact with professionals from many aspects of the business and showcase TAPPI's member services and industry information products related to both our PLACE Division and Corrugated Division"
Sponsored by PMMI, PACK EXPO provides a comprehensive showcase of packaging and processing technology for more than 26,000 packaging and processing professionals and 1,700-plus exhibitors. The three-day event includes the latest developments in new materials, containers, package design, food safety, and sustainability. The exhibit covers a full range of vertical markets of consumer packaged goods companies.
Back To Top
|
Calls for Papers have been issued for PaperCon 2014.
After a record attendance in 2013, PaperCon will again bring together CEOs, mill managers, superintendents, scientists, process engineers, and suppliers for the largest pulp and paper technical program in the world. The event will take place April 27-30, 2014, in Nashville, Tenn., USA. Learn more about PaperCon 2014.
For 2014, PaperCon is once again co-located with the Tissue360° Forum, NETInc (Innovative Nonwovens Conference), RPTA (Recycled Paperboard Technical Association) P-T Seminar, and the OpEx Reliability Workshop. Each of these events is open to full PaperCon registrants and papers in these areas are welcome.
Calls for Papers and Posters have been issued. The conference theme is In Tune for Stability, Agility, and Profitability, and authors are encouraged to include this within their papers.
Papermakers Program:
The Papermakers Program encourages topics on paper machine upgrades, product development, stability, agility, and fluid fundamentals, and recycled paperboard. The deadline for submission of abstracts is Nov. 10, 2013. Abstracts for panel discussions and roundtables are welcome. See Papermakers Program Call for Papers.
Coating and Graphic Arts Program:
The Coating and Graphic Arts Program will focus on The Future of Print and its Demands on Paper and Coatings. The deadline for extended abstracts for this program is October 16, 2013. See the Coating and Graphic Arts Program Call for Papers.
All abstracts must be submitted using TAPPI's Speaker Management System for consideration by the TAPPI and RPTA program committees.
Back To Top
|
TAPPI member Hideki Fujiwara, Ph.D., has hit a lot of high notes in his long and illustrious career in the pulp and paper industry. Not the least of which occurred as a result of his nearly three decades of membership, including being the first member from Asia to be honored with the Charles W. Engelhard Coating and Graphics Arts Division award.
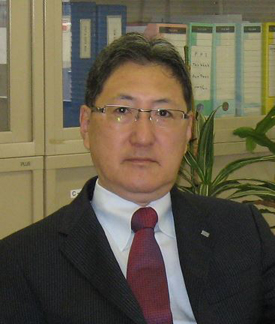 Dr. Fujiwara, who retired in June after 38 years in the industry, spent the majority of his career with Nippon Paper, serving in a variety of managerial positions. He credits his active involvement in TAPPI with providing ample opportunities not only to receive, but to share technical ideas and innovations with other professionals from around the world. Membership helped broaden his view of the forest products industry, and he notes that "joining TAPPI was the very first step to being a real professional in this field."
Find out more by reading this month's Member Spotlight. Spotlight participants are recommended by fellow members and staff. If you would like to nominate members, just send their name (or names) to MemberSpotlight@tappi.org. We will forward a Spotlight Questionnaire to fill out and return.
We look forward to seeing you in the Spotlight!
Back To Top
|
There's still time to be part of the program at the 2014 TAPPI PLACE Conference, May 12-14, 2014, at the Sawgrass Marriott Hotel in Ponte Vedra, Fla., USA. The 2014 PLACE Technical Program Team is actively seeking technical presentations, panels, tutorials, roundtables, and case studies from the packaging and academic community to be presented at the conference.
View the Call for Abstracts.
Interested in being a session chair or know someone who would be a great presenter? Extended abstracts will be accepted anytime before September 6, 2013. Space is limited so submit now! Final papers will be due on or before March 17, 2014.
The 2014 PLACE Conference is the premier North American event for the flexible packaging industry and will have something for the whole supply chain including suppliers, converters, extruders, retailers, and brand owners. This event not only offers top notch technical presentations but also allows ample opportunity for networking with your peers. Visit the event website for additional conference information.
Back To Top
|
The 2013 Building Science Committee Technical Program will include papers on: Process Variation Reduction, Glass Sizing Basics; Burner Safety and Efficiency; Biological Treatment Case Study; Operator and Mechanical Training to Enhance Operational Effectiveness; and IT Systems to Manage Roll Goods and Reduce Waste.
This year's program will focus on aiding production managers and engineers in the fiberglass mat industry. Attendees will get the first-hand knowledge needed to improve their mat processes with production-targeted papers.
These topics and more will be covered in the comprehensive technical program. Tim Worms, of 3M's Industrial Mineral Products Division, is returning by popular demand to present his outlook for housing starts and the roofing forecast for this year. Kirby Erickson, of GAF, will discuss critical safety issues to be aware of as you seek to implement new efficiency and pollution requirements in curing ovens. In addition he will provide an example of how mistakes led to a massive oven explosion and what was implemented to address burner safety going forward. Charles Black, of Charles Black & Associates, will ask if your training dollars are being spent wisely and provide case studies showing how strong training programs can have a positive impact on your company's bottom line. Blaine Krause, of Nalco, will offer case studies on microbial control including its impact on operations, monitoring, control, and examples of newer technology.
The meeting will be held September 18-20 at The Hilton Marco Island Beach Resort in Marco Island, Florida, USA. Meeting registration includes the full conference program, the Building Sciences Committee Meeting, and ample opportunities for networking with other manufacturing personnel and suppliers. Thursday afternoon's activity is a choice of golf, backwater fishing, or a relaxing spa treatment. Group dinners are included in the cost of registration for Wednesday and Thursday evenings at some of the area's finest restaurants. Non-registered spouses and guests are welcome to participate in the activities and dinners for the following costs: $60 per dinner and $95 for golf, fishing, or the spa treatment. They do not have to pay the conference registration fee.
Companies participating as sponsors include ESP, GAF, Georgia-Pacific Chemical, Malarkey Roofing, Momentive Specialty Chemicals, Nalco, PPG, Albany International, Xerium, Ineos, Mallard Creek Polymers, and Majiq. Opportunities to sponsor with this select group of companies are still available and your company will receive special recognition throughout the meeting.
You do not want to miss out on this opportunity to stay abreast of current market trends, new and emerging product/process technical developments, and regulatory issues that are or will be impacting our industries.
For full meeting information including the conference agenda and program summaries, please visit the meeting website today.
Back To Top
|
The 2013 TAPPI PEERS Conference, September 15-18, in Green Bay, Wis., USA, has announced the detailed technical program focusing on sustainable manufacturing and other pressing business and technical questions faced by pulp and paper companies as they manage raw materials, assets, regulatory requirements, and production assets. Register now and save.
In addition to the peer-reviewed technical program, Keynote Speaker Robert Feeser, SVP of Packaging with MWV, will share his insights on the day-to-day challenges he faces as he oversees the company's primary mill-based manufacturing businesses in the U.S. and Brazil. PEERS will also offer exclusive networking opportunities and insight into new technologies that can help you optimize your mill operations.
For 2013, PEERS will be co-located with the 10th Research Forum on Recycling and the International Bioenergy and Bioproducts Conference, creating a value-added opportunity for you to expand your learning, networking, and resources by attending all three events.
Learn more about the TAPPI PEERS Conference.
Back To Top
|
TAPPI is offering a 10% discount on registration for the Root Cause Problem Elimination Training Course taking place in Raleigh, N.C, USA, on October 8-10, 2013. If you register soon, you can save more than $250 with only a few seats remaining.
IDCON's Root Cause Problem Elimination Seminar focuses on eradicating problems. We all have problems, right? At least in your operations, let this training help you get to the source of problems.
You'll learn how to tie cause and effect together and apply logical thought processes to arrive at the problem's core. You'll learn how to use the "How-Can Diagram" to bring root cause analysis into your day-to-day reliability management process, and do it cost effectively!
This expanded course will focus on outlining basic mechanical engineering stress/strain fundamentals, metallurgy, and engineering design, which are typically necessary in the development of possible root cause(s) for mechanical failures.
You'll learn how to use predictive maintenance tools correctly to provide a mechanism for root-cause analysis initiation and eventual elimination of repeat failures.
Register today to secure your access to these premier training courses with IDCON.
Back To Top
|
One of the year's most important maintenance training courses will be held in Seattle, Wash., USA, on Oct. 22, 2013.
IDCON's Results Oriented Reliability and Maintenance Management Seminar will help those who attend learn how to build and sustain successful reliability and maintenance improvements.
Topics covered include:
- Common improvement obstacles
- How to measure reliability
- Best practices in the maintenance system
- Understanding your tools
- Creating a culture of reliability
- Building partnerships
- Understanding key performance indicators
- Setting a vision and plan of action.
This seminar has been delivered to hundreds of companies to start or improve their manufacturing organization's improvement initiatives and is consistently rated a "best" presentation at conferences world-wide.
If you register soon, you can still save more than $250 with only a few seats remaining.
A special discount on IDCON Courses is available for those who register through TAPPI.
Back To Top
|
Don't miss out on your chance to attend the Process Control of Stickies Workshop, taking place just before the TAPPI PEERS Conference.
Organized by Dr. Mahendra Doshi, current TAPPI JOURNAL Editorial Board Member and Founding Editor of Progress in Paper Recycling, the workshop will be held from 7:30 a.m. to 4:30 p.m. on Sunday, September 15.
The international workshop is designed for engineers, scientists, and technicians who want to get a handle on one of the difficult contaminants in paper recycling - stickies. The workshop will benefit anyone using recycled pulps, working in recycling mills, or affiliated with companies supplying equipment, chemicals, and recovered papers to the recycling industry.
Problems caused by stickies cost millions of dollars to the industry. As indicated above, experts from around the world together with highly experienced speakers from mills offer an excellent overview for managing and controlling stickies. If you could just save one hour of paper machine downtime it would pay for the workshop many times over.
Learn more about this important workshop.
Don't miss this golden opportunity to learn about stickies related issues at this one-day international workshop.
Registration Cost:
$295/member; $345/non-member (on or before August 16); or $345 (if registered after August 16).
Back To Top
|
Now's the time to make your plans to attend IBBC, September 18-20 in Green Bay, Wis., USA.
As the only industry event dedicated to advancing biorefineries in the forest products industry, International Bioenergy and Bioproducts Conference (IBBC) offers you a fresh look at biomass utilization. Sessions focusing on biomass supply and demand, biochemical and thermochemical conversion technologies, conversion pathways, and economic assessments – along with a Keynote Presentation from Linda A. Beltz, Ph.D., NPDP, Director, Technology Partnerships at Weyerhaeuser – can help you determine how to integrate these technologies into your mill.
For 2013, IBBC will be co-located with the TAPPI PEERS Conference, and the 10th Research Forum on Recycling, creating a value-added opportunity for participants to expand their learning, networking, and resources by attending both events. Offered just after IBBC, TAPPI's Biorefinery Course, can deepen your understanding of biorefinery strategies and emerging technologies and their design/implementation in a business strategy.
Learn more about IBBC.
Register by August 16 for best rates!
Back To Top
|
The Foundations of Leadership Excellence Course is the only leadership course specifically focused on the paper and packaging industry.
Foundations of Leadership Excellence explains the fundamentals of leadership and management skills for emerging leaders, high-potentials, area operating managers, and other technical professionals. This three-day session takes place Oct. 22 - 24, 2013, at the TAPPI Training Facility in Metro Atlanta, Ga., USA.
This course will sell out at 25 participants.
The instructors for this course have approximately 100 years of combined experience in leadership, management, and human resource roles within the pulp and paper industry.
Course curriculum covers industry specific, real-world scenarios. Participants will develop personal leadership skills through the use of influence. They will learn to impact organizations from a 360 degree perspective and how to address the challenges of team building, accountability, performance management, and other critical factors of organizational success.
Back To Top
|
Piping System Training is a course anyone in the piping system industry can use. This course provides real-world practical knowledge for junior engineers, is a good refresher course for senior engineers, and helps operations and maintenance supervisors, design and process engineers, and operators and maintenance personnel better understand how piping systems operate.
Attend Piping System Training courses planned for two locations coming this fall:
- October 2-3 in Chicago, IL
- October 23-24 in Houston, TX
This course provides the foundation of piping terminology, mathematics, and the underlying concepts and principles that determine the performance of individual piping system elements and the system as a whole. Piping System Training places an emphasis on understanding the relationship between components that make up the piping system.
Visit the course website to find more information and register.
Earn 1.6 CEUs and carry back with you two indispensable manuals as well as greater confidence in your work.
Back To Top
|
As TAPPI is getting ready to celebrate its 100th Year Anniversary in 2015, we were wondering how much industry expertise we have in this great group of professionals.
So, we decided to post a discussion question on our TAPPI Social Media outlets. We asked, "How many years of paper and/or packaging experience do you have?"
Who knew such a simple question would have such an impressive response.
With more than 7,000 TAPPI members, all over the world, we have counted 650-plus years of industry experience! And that's just counting the first 30 people who have responded. Now you probably can't find that anywhere else . So why don't you join us?
From those "born" into the industry to third generation professionals. From paper to packaging, to sustainability, environment, tissue, converters, and consulting. This TAPPI network has something for everyone.
Become a part of this unique community of paper and packaging professionals, and add your expertise to our group, and network with others to learn something new.
Visit our website to learn more today!
Back To Top
|
The TAPPI Centennial Celebration will be a multi-year long series of outreach events and educational offerings showcasing the proud history and promising future of the global pulp, paper, packaging, and related industries. This once-in-a-lifetime event will expand public awareness, foster further connection, and provide outstanding opportunities for collaboration, growth, and investment in our future for all of those involved. Goals for the TAPPI Centennial Celebration are:
- To honor TAPPI's 100 years of connection, education, and advancement as a foundation for the sustainable success of our members, our industries, and the world we share
- To recognize the achievements of those who built our industry and to inspire those who seek to build its future
- To celebrate the contributions and innovations of the global pulp, paper, and packaging industries to human culture, commerce, health, and social advancement
- To sustain the industry and support its growth, vitality, and future through the TAPPI Foundation.
We invite you to be a part of this momentous event. The sooner you join us the more opportunities there are for recognition of your company, its products, and key innovations. Keep in mind that an early commitment allows you to spread your investment over multiple years' budgets.
For more information on sponsorship and volunteer opportunities please contact dbell@tappi.org.
The sponsorship prospectus can be downloaded online.
Back To Top
|
Do you have a history book gathering dust on your shelf? TAPPI's 100th year is coming soon and we are looking for donations to the TAPPI Library. Specifically, we are interested in histories of companies and mills in the paper and packaging industry (both producers and suppliers). Each donated book will have a bookplate in the front cover recognizing the donor. For more information please contact David Bell.
Please send books to:
c\o David Bell
TAPPI
15 Technology Parkway, South
Suite 115
Peachtree Corners, Georgia 30092
Back To Top
|
|
|
TAPPI Over the Wire | 15 Technology Pkwy. S. | Norcross, GA 30092 USA | Voice: 770.446.1400 | Fax: 770.446.6947
|
 |