Over the Wire
TAPPI
Weekly Spotlight
The University of Maine Pulp and Paper Foundation, Orono, Maine, USA, has established a new annual award that recognizes a UMaine employee who supports the pulp and paper industry through research, innovative student recruitment, or teaching that inspires current engineering students. The new award will bear the name of its first recipient--long-time UMaine chemical engineering professor Joseph Genco, an exemplary scholar who personifies all three of the award criteria
In announcing the award and presenting it to Genco at this year's foundation meeting, foundation president Barbara Hamilton noted Genco's impact on the industry and those who work in it. Some 130 industry representatives, students, and former students responded affirmatively to Hamilton's request that those influenced by Genco join him at the podium to share in the award, to be called the Joseph M. Genco Award.
Genco thanked the group, the university, and the foundation, noting that he has enjoyed his time working with the industry and that he has benefited from that association. The award comes with a $1,000 stipend and $2,500 for the recipient to use for research, related travel, or graduate student support. Genco immediately returned the stipend to the foundation to be used for its Helen Horner Genco Scholarship.
##SHARELINKS##
|
The Maine Forest Products Council, Augusta, Maine, USA, this week recognized Verso Paper Corp., Memphis Tenn., with its "Manufacturer of the Year" award. Verso operates mills in Jay and Bucksport, Maine.
James Cote of the Maine Forest Products Council said that "Verso was chosen for this award because of their outstanding progress in manufacturing innovation, their fantastic record of corporate citizenship, and their dedication to a stronger, more robust forest products industry here in Maine."
Verso employs more than 1,500 people at the Androscoggin Mill in Jay and the Bucksport Mill. The company also supports four to five times that many workers indirectly through contracted jobs and other community efforts.
"We are thrilled to be recognized for the work we are doing because it means others are now noticing what we have known all along," Androscoggin Mill Manager Marc Connor said. "We are proud of our ability to survive in this difficult economy," Connor added. "We believe it is a testament to our commitment to Maine and to being responsible pulp and paper makers. Only using wood from sustainable forests, being environmentally responsible, and committed to our communities has been key for us."
Verso is committed to investing capital for upgrades and improvements, especially in the wood-processing areas of both mills, the company noted in a release, adding that "once completed, the upgrades should result in significant water conservation and ever-increasing environmental improvements." Verso also has invested in energy production, resulting in its two mills generating about 20% of the electricity the state uses.
##SHARELINKS##
|
Terry McAuliffe, a leader in politics, business, and the promotion of green energy, will deliver the keynote address at the TAPPI PEERS Conference and the Research Forum on Recycling, October 17 - 20 in Norfolk, Va., USA. McAuliffe is chairman of Greentech Automotive (GTA), established to carry out his vision that "no green technology is truly green unless it is affordably green."
McAuliffe is also an active investor in and developer of renewable energy companies and projects. He is involved in a next generation fuel cell company, a wind project in the southwest, and is currently investigating the repurposing of shuttered paper mills for bioenergy production. In his keynote speech, McAuliffe will share how his vision applies to the pulp and paper industry and the future of renewable energy.
##SHARELINKS##
|
The Water Sustainability Forum 2010, Oct. 13-14 in Chicago, Ill., USA, at the Hyatt McCormick Hotel, is tightly focused on the new water economy in today's business and industry. It examines the right steps to intelligently manage water and explores how to find solutions for 2011 environmental and financial goals.
Hosted by World Wildlife Fund (WWF), Alliance for Water Stewardship, Water Innovation Alliance, Ernst & Young, McKinsey & Company, and Nalco Company, this new Forum will provide the tools needed to take action, including:
- Impact and opportunity of impending 2012 global water standards
- Water use risk—reinventing corporate practices
- How to move from water and energy strategies to implementation
- How others have succeeded—case histories and lessons learned in water management
- Emerging technologies and best practices in water conservation.
The mill and plant histories presented at Forum are the very best, most recent operating floor studies and best practices from the most well-known multinational corporations. They look closely at practical steps these facilities have taken to shrink their water footprint and innovatively use water, whether in the form of new management practices, plant and process changes, or installing new technologies.
A pre-Forum workshop on Day 1 (October 13), titled "The Water Energy Nexus," analyzes energy costs of water movement, heating, cooling, treatment, and disposal, cost benefits for driving water management and efficiency, and leveraging green incentives and tax credits. Also on Day 1, Speakers and attendees will be treated to a special networking reception at Chicago's Field Museum to experience the Climate Change Exhibit, which uncovers natural evidence for climate change and examines its impact on our atmosphere, oceans, land, and societies. Participants can also contribute to the creation of a Water Energy Nexus white paper, and will receive contributing credit in the paper, as well as an advanced copy of the finished document.
More information is available online, along with registration forms and instructions.
##SHARELINKS##
|
Market Roundup
For the tenth straight month, U.S. containerboard production rose over the same month a year ago and posted the highest production amount since August 2008. According to AF&PA's (Washington, D.C., USA) U.S. Containerboard Statistics Report for August 2010 released this week, total production saw an increase of 195,400 tons or 7.0% compared with August 2009 and rose slightly (0.9%) over July 2010.
The month-over-month average daily production reflected a similar change. Year-to-date 2010 production has increased 9.4% over 2009. The containerboard operating rate for August 2010 rose 10.8 points over August 2009 to 98.9%. Additional key findings from the report include: ·
- Linerboard production was highest since August 2008
- Medium production shows growth over same month last year.
##SHARELINKS##
|
Total U.S. kraft paper shipments in August 2010 were 136,200 tons, an increase of 7.5% compared with August 2009, and July 2010, according to the AF&PA's (Washington, D.C., USA) August 2010 Kraft Paper Sector Report released this week.
Total year-to-date shipments rose 15.1% over last year. Total inventory was up 2.8% from last month. Additional key findings from the report cover total unbleached kraft shipments and total bleached kraft shipments.
##SHARELINKS##
|
Anemic housing construction—and the resulting impacts on lumber demand—delayed the expected recovery of pine sawtimber prices this year. Despite the apparent delay in recovery, several states, and end markets for pulpwood, show signs of resiliency, according to Forisk Consulting, Athens, Ga., USA. Forisk this week released a mid-year update of its 10-year, state-by-state forecast for pine sawtimber and pulpwood stumpage in the U.S .South.
South-wide, Forisk's update indicates pine sawtimber prices will be 6.4% lower in 2011 than expected six months ago. Results vary across states, with Alabama, Arkansas, Georgia, and South Carolina best positioned to rebound quickly as lumber demand strengthens. According to Forest Economist Dr. Tim Sydor, "expectations for key macroeconomic factors—such as GDP and housing starts—have, frankly, proved to be way off-base. GDP grew faster than expected, but housing starts are expected to remain 30% below 2009 projections. As a result we've adjusted our forecast of U.S. softwood lumber consumption downward by 6.3 billion board feet for 2010. Lower lumber demand means lower stumpage prices, and pine sawtimber prices in the South have been revised downward by nearly $1 per ton for the year."
Forisk's president, Dr. Brooks Mendell, agrees that 2010 is a "bridge" year and emphasizes to investors the benefits of patiently following local markets. "Robust local markets, with capitalized mills and resilient loggers and wood suppliers, pay dividends to their investors through faster recoveries."
Pulpwood demand, relative to sawtimber, is distinct for the complexity of its end-use markets. "We follow several factors that have push-and-pull effects on pulpwood demand and stumpage prices," says Dr. Sydor. "For instance, while a housing recovery lifts demand for pulpwood from oriented strand board (OSB) producers, it decreases demand for roundwood through increased residual chip flows from lumber mills."
Forisk projects that 9.6% of pulpwood demand across the South will come from new bioenergy facilities. "Bioenergy and OSB end-use markets drive any growth in pulpwood demand over the next 10 years," says Dr. Sydor.
More information is available online (click "Stumpage Price Forecasts").
##SHARELINKS##
|
Pulp & Paper
AbitibiBowater, Montreal, Que., Canada, this week received approval for its plan of reorganization from unsecured creditors under the Companies' Creditors Arrangement Act (CCAA) in Canada. The plan of reorganization received overwhelming support from its unsecured creditors both in dollar amount of claims and in number of claim holders who voted on the plan, the company notes.
Having obtained the requisite votes in each class, except with respect to Bowater Canada Finance Corp. (BCFC), a special purpose company subsidiary with no operating assets, AbitibiBowater will seek a sanction order in respect of its CCAA plan other than in respect of BCFC, which is excluded from the CCAA plan. The company says it does not believe that the exclusion of BCFC will affect the timing of its sanction hearing by the Canadian Court, nor does it expect it will materially delay its emergence from creditor protection slated for this fall.
Voting tabulations on the plan of reorganization under Chapter 11 of the U.S. Bankruptcy Code are expected on September 20. The company will provide further information when the results become available.
"We appreciate the support given by the significant majority of our creditors under the CCAA process for our plan of reorganization," stated David J. Paterson, president and CEO. "We are confident our restructuring efforts have created a stronger foundation for a more sustainable and competitive company. We look forward to completing the restructuring process and emerging from creditor protection this fall."
The sanction hearing under the CCAA process is scheduled to occur on September 20, in the Quebec Superior Court and the confirmation hearing under the Chapter 11 process is scheduled to start on September 24, in the U.S. Bankruptcy Court in Delaware.
##SHARELINKS##
|
Domtar Corp., Montreal, Que., Canada, and The Nature Conservancy this week announced that they have partnered to help private landowners maintain and sustainably manage their forested land through a program called Working Woodlands. The Nature Conservancy will cooperate with Working Woodlands landowners to develop sustainable forest management plans that are certified by the Forest Stewardship Council (FSC).
In addition to generating FSC certified forest products, the certified lands are also managed to help reduce greenhouse gas emissions and ensure that more carbon is stored in the forest. The Conservancy then works with Blue Source, a global greenhouse gas offset developer, to market and sell the landowners' forest carbon credits. In return, landowners agree to manage the forest sustainably for at least 60 years.
"Working Woodlands is an innovative approach to help forest owners manage their properties for ecological health, productivity, and better economic return," said Lewis Fix, Domtar VP, Brand Management and Sustainable Product Development. "The program marks the first time private landowners can gain access to markets that will help them sustain healthy, diverse, rich forests. We are excited to team with The Nature Conservancy and help show how proper forestry practices lead to sustainable and renewable paper and wood products that consumers can feel good about using."
This marks the latest effort by Domtar to help better manage forests. As a founding member of the Canadian Boreal Leadership Council, Domtar joined forces in 2003 with First Nations communities, environmental groups, and other resource companies to help sustain the Canadian boreal forest region. A few years later, Domtar transferred 15 square miles of land in the Eastern Townships region of Quebec and sold 20,000 acres in New York's Adirondack Mountains to The Nature Conservancy. This year, the company contributed to preserving an additional 2,011 acres of wetlands in the Eastern Townships region with a land transfer to Ducks Unlimited Canada, a non-profit organization dedicated to the conservation of wetlands.
The Nature Conservancy and Blue Source launched Working Woodlands in December 2009, and the program has already attracted interest from landowners whose total holdings exceed 10,000 acres. Additionally, the Conservancy has certified its own Pennsylvania forest properties under FSC, and has led efforts globally to promote forest certification and carbon trading as incentives for conservation.
Under the pilot program with The Nature Conservancy, Domtar will donate $30,000 over the next two years to help enroll a total of 20,000 acres in Working Woodlands. At least 4,000 acres are expected to be from owners of small plots of forested land near Domtar's Johnsonburg paper mill in Central Pennsylvania, but the impact could be far more extensive. Domtar and The Nature Conservancy said the pilot program may also expand to areas surrounding Domtar's mills in the southeastern U.S.
##SHARELINKS##
|
NewPage Corp., Miamisburg, Ohio, USA, this week announced the upload of a new "On Paper" sustainability series podcast featuring Anders Hildeman of IKEA, the Netherlands. As global forestry manager for IKEA, Hildeman discusses the importance of responsible forestry management and the role IKEA plays through numerous associations to preserve forestlands worldwide.
The podcast can be downloaded online, as well as more than 30 previous episodes on topics such as supply chain management, zero waste, and green business strategies,
IKEA, a global home furnishings company with more than 300 stores in 37 countries, sources wood from close to 50 different countries to supply materials for their range of home furnishings products. "Wood is the soul of IKEA products," Hildeman says.
In 1993, IKEA became a member of the Forest Stewardship Council (FSC). Explaining the importance of FSC to IKEA, Hildeman says that "the reason we've promoted and worked closely with the Forest Stewardship Council is that it allows stakeholder input to deciding the criteria for {forest} management. It's really not up to IKEA to decide how people should be managing their forests, but we would like to see major stakeholders agree on how they should be managed."
Today, IKEA, along with NewPage and 10 other business and world leaders, is a founding member of the Forest Legality Alliance, an international initiative designed to reduce trade in illegally harvested forest products, increase transparency in forest product supply chains, and support global supply chain efforts to deliver legal wood and paper. The Alliance is currently developing a risk assessment tool that will help companies evaluate the risk of purchasing illegally harvested forest products, including paper and wood.
The "On Paper" Podcast Series is an ongoing dialogue that provides a platform for professionals to share how their organizations implement sustainable practices. With dozens of episodes featuring representatives from the most innovative of corporate America, across a variety of industries, "On Paper" has garnered more than one million downloads.
##SHARELINKS##
|
International Paper, Memphis, Tenn., USA, announced this week that it is making a $650 million voluntary contribution to its U.S. pension fund. In July, IP made a voluntary contribution of $500 million to the fund, which brings the year-to-date contribution total to $1.15 billion.
"These contributions to the U.S. pension fund help fulfill our long-term funding requirements and will reduce our future pension expense," said Robert Hunkeler, VP of investments.
IP has manufacturing operations in North America, Europe, Latin America, Russia, Asia, and North Africa. Its businesses include uncoated papers, industrial and consumer packaging, and distribution. The company employs about 60,000 people in more than 20 countries and serves customers worldwide. Net sales in 2009 were more than $23 billion.
##SHARELINKS##
|
Innventia, a Stockholm, Sweden-based research institute, is continuing to revolutionize the paper business. Its research work has now produced a new method that will result in a stronger paper with lower production costs and reduced raw materials consumption. This dream scenario has now become a reality for many companies in the paper business, Innventia notes.
"For a paper mill that produces 450,000 metric tpy of the new paper, this technology means an annual savings of approximately 120 million Swedish kronor," says Daniel Söderberg, research manager and initiator at Innventia and the person behind the previous work.
The Aq-Vane technique is derived from the aircraft industry. It deals with the separation of fiber layers before they are joined together to form the paper. "This technique uses a thin layer of water to stabilize the fiber layers and consequently form an even flow while they are being joined together. This prevents the layers from blending with each other. This means that it is now possible to keep the layers separate as well as to control the precise properties that are wanted in a paper," Söderberg says.
For a product such as the IKEA catalogue, approximately 200 million copies of which are distributed each year, this means enormous savings, Innventia points out. For the papermaking industry as a whole, this implies a savings in billions of kronor. "We've tailor-made a new kind of uncoated paper, which is the same type as that used in the IKEA catalogues. By putting finer fibers in the surface and coarse fibers in the middle of the paper we're able to save up to 10% in costs on fiber raw materials and energy," Söderberg explains.
Earlier this summer, Innventia began leading BoostEff, an EU project with a total budget of EUR 11 million, to demonstrate the industrial and economical potential of the method. Using Aq-vane, with its possibilities for advanced dosage, Innventia, in collaboration with Finland's Stora Enso, is developing the kind of paper that is used in catalogues and magazines.
"This project also signifies a completely new way of working," says Söderberg. "The starting point in the project is three existing industrial production units, one of which belongs to Stora Enso. Using these, the possibilities of the new technique, together with existing techniques, are being adapted to demonstrate the potential product and the production process involved. The results from the project are going to be used as a basis for three investment projects involving technical specifications and economical results.
The Aq-vane technique has the potential to generate increased profits based on the form of savings in the fiber raw materials and energy.
"Within BoostEff several companies and institutes from around Europe are collaborating with us at Innventia," Söderberg continues. "When the project comes to an end in 2013, the technology will also be available to the rest of the industry, giving the opportunity of an increased profitability and, most of all, an improved paper."
##SHARELINKS##
|
OfficeMax, Naperville, Ill., USA, and E&I Cooperative Purchasing (E&I), the largest higher education purchasing consortium in North America, this week announced a new five-year contract for office supplies. The contract allows E&I members to take advantage of an enhanced program including reductions in overall pricing, an expanded list of core program items tailored for each participating member, and an expanded selection of office supplies, print services, technology solutions, furniture, asset disposition, and a closed-loop paper system. A special Early Adopter incentive rebate will be offered to E&I members who sign on to the program by year-end 2010, and the agreement features aggressive ongoing rebates based on volume and service package.
"OfficeMax provides a range of competitive and reliable purchasing options for higher education institutions at a time when the cost savings really matter the most," said Tom Fitzgerald, CEO of E&I. "We are excited about the many enhancements available through this new agreement and we look forward to continuing to deliver increased savings opportunities to our members."
##SHARELINKS##
|
Tembec, Temiscaming, Que., Canada, will permanently close its newsprint mill in Pine Falls, Manitoba, Canada. The mill has been indefinitely idled due to a labor dispute on Sept. 1, 2009. After examining a full range of options, the company initiated a sales process for the mill in early January 2010. This sales process has proved unsuccessful. After a thorough analysis of the situation, the company concluded that the permanent closure of the facility was the only viable option. Approximately 230 employees will be affected.
"Although not an easy decision to make, the structural decline of the newsprint market and the cost structure of the mill prompted such a decision," said Chris Black, Tembec's executive VP and president, Paper Group. "The company intends to act in a manner that will ensure that employees receive their severance pay in accordance with the collective agreement."
As a result of this announcement, a net charge of approximately $8 million related to the closure will be recorded in the quarter ending September 25.
##SHARELINKS##
|
West Fraser Timber Co., Vancouver, B.C., Canada, this week announced a new $125 million capital spending program that will focus on expanding and upgrading various solid wood operations in Alberta, the U.S. South, and the British Columbia interior. The program is expected to be carried out over the next 18 months.
Hank Ketcham, West Fraser's chairman, president, and CEO, said that "as a result of our strong balance sheet, we are able to begin making significant capital improvements to our facilities to keep them at the forefront of technology and efficiency."
West Fraser is an integrated wood products company producing lumber, wood chips, LVL, MDF, plywood, pulp, and newsprint. The company has operations in western Canada and the southern U.S.
##SHARELINKS##
|
Containerboard/Packaging
Cascades Inc., Kingsey Falls, Qué., Canada, a producer, converter, and marketer of packaging and tissue products composed mainly of recycled fibers, has received confirmation from the U.S. Environmental Protection Agency (EPA) that its American mills have been accepted as Energy Star partners. By becoming Energy Star partners, Cascades' mills in the U.S. will carry their energy consumption efforts one step further. Using tools provided by the EPA, they will be able to measure and compare their performance more accurately, optimize their action plan for reducing energy consumption, and draw inspiration from the winning strategies adopted by other Energy Star partners to further improve performance.
"Cascades is a pioneer in sustainable development and, as such, strives to constantly reduce its environmental footprint, Alain Lemaire, president and CEO of Cascades, said. "This position involves, among other things, reducing energy consumption in our mills and, where possible, using clean, renewable energy sources." Moreover, Cascades is the only North American papermaker to employ a team of energy efficiency specialists. Last year, that experienced team enabled Cascades to cut the intensity of its greenhouse gas emissions by 3% compared with the previous year.
Founded in 1964, Cascades employs nearly 12,500 people who work in some 100 production units located in North America and in Europe.
##SHARELINKS##
|
Tetra Pak, Lausanne, Switzerland, reports that it will begin supplying carton packages in Switzerland with the Forest Stewardship Council (FSC) label. Starting with a range of packages for Coop stores later this month, Tetra Pak plans to offer around 340 million FSC-labeled packages to Swiss customers next year, representing around 60% of its annual sales in this market.
Currently, only 5% of the global forest stocks are FSC certified, and Tetra Pak says that it is working with its partners to support an increase in supply. The world's first FSC-labeled liquid food cartons were introduced in the U.K. in 2007. Since then, Tetra Pak has introduced more than 2.3 billion through 2009.
##SHARELINKS##
|
New Products
European-based Sonoco-Alcore S.a.r.l, a wholly owned subsidiary of Sonoco, Hartsville, S.C., USA, reports that it is introducing several new products at the PacTec Exhibition next week in Helsinki, Finland. Among the new products that will be featured are Intellicore radio frequency identification (RFID) enabled paper cores for roll tracking in the paper industry, Dricore rain-resistant paperboard cores for the agricultural industry, and FirmaLoad carriers, environmentally responsible paperboard pallets for transporting bulk bags.
Water-resistant properties allow the DriCore paperboard core to be stored outside for up to 20 days without sacrificing core strength or stability, Sonoco notes. The Intellicore paper roll utilizes RFID technology to enable automatic paper roll inventory tracking from initial production all the way through to consumption. It allows manufacturers to monitor and streamline production in real time, minimizes buffer stocks and working capital, and ensures accurate order fulfillment. The Firmaload carrier is an environmentally friendly paperboard product used in the FIBC industry as a more efficient and effective means of transporting big bags. The FirmaLoad carrier saves on cost, space and freight versus wooden pallets.
A number of other new products include the M-Core a high-performance paper mill core for the printing industry, the Printex core for the textile industry, and a range of products for all served industries.
##SHARELINKS##
|
Published Pricing
RockTenn, Norcross, Ga., USA this week a $35 per ton price increase on all grades of uncoated recycled paperboard. The price increases are effective with shipments beginning October 18.
RockTenn is a North American manufacturer of paperboard, containerboard, and consumer and corrugated packaging, with annual net sales of approximately $3 billion. With 10,000 employees, the company operates facilities in the U.S., Canada, Mexico, Chile, and Argentina.
##SHARELINKS##
|
Sonoco, Hartsville, S.C., USA, will increase prices in the U.S. and Canada for all uncoated recycled paperboard grades by $35 per ton, effective with shipments beginning October 11, according to Jim Bowen, SVP, Primary Materials Group.
Sonoco is a $3.6 billion global manufacturer of industrial and consumer products and a provider of packaging services, with more than 300 operations in 35 countries, serving customers in some 85 nations.
##SHARELINKS##
|
Caraustar Industries, Atlanta, Ga., USA, also reported this past week that it will increase prices by $35 per ton on all uncoated recycled paperboard grades produced by its mills. The increase will become effective with orders placed on and after September 27.
In a letter to customers, Caraustar pledged that its mills will continue to operate efficiently, and service customer needs effectively during this time of rising raw material costs.
##SHARELINKS##
|
The Newark Group, Cranford, N.J., USA, reports that its Paperboard Mill Division will also increase the ice of all uncoated grades of recycled paperboard by $30 per ton. The increase becomes effective with shipments beginning October 4.
##SHARELINKS##
|
Sustainability
Sonoco, Hartsville, S.C., USA, for the second year in a row has been selected to join the Dow Jones Sustainability World Index (DJSI World), which is made up of the leading global companies in terms of economic performance, environmental stewardship, and social responsibility. Dow Jones Sustainability Indexes are determined following an annual review by SAM, an investment boutique focused on sustainability investing, together with Dow Jones Indexes.
Following SAM's largest global analysis of corporate sustainability leadership, 48 companies will join DJSI World, while 46 firms will be deleted, resulting in a total of 318 index components. All changes will become effective with the opening of equity markets on September 20. The DJSI follows a best-in-class approach and includes sustainability leaders from each industry on a global and regional level.
The annual review of the DJSI family is based on a thorough analysis of corporate sustainability efforts, assessing issues such as corporate governance, risk management, climate change mitigation, supply chain standards, and branding. It accounts for general as well as industry specific sustainability criteria for each of the 57 sectors defined according to the Industry Classification Benchmark (ICB).
Harris E. DeLoach Jr., chairman, president and CEO, pointed out that Sonoco's selection to DJSI World for 2010/2011 was the result of a significant improvement in its ranking in a number of economic, environmental stewardship, and social responsibility factors. "Overall, the company's 2010 score improved 14% from 2009, which reinforces the progress we're making in all of our global operations. In addition, the company received best-in-class marks in our industry for advancements in product stewardship, climate strategy, customer relationship management, code of conduct, and stakeholder engagement."
##SHARELINKS##
|
Energy
The U.S. Department of Energy (DOE), Washington, D.C., USA, this past week announced the award of up to $16.5 million for two major research and development cost-share initiatives that will support the expansion of renewable fuels production. Under the first initiative, DOE will invest up to $12 million over three years in four projects that will employ pyrolysis, the heating of biomass in the absence of oxygen to create a bio-based oily liquid called bio-oil. The projects will explore a variety of catalytic processes to upgrade this bio-oil into so-called "drop-in" biofuels—advanced biofuels that are compatible with the existing fueling infrastructure.
Drop-in biofuels may include a bio-based crude oil substitute that could be processed in existing refineries, as well as bio-based versions of gasoline, diesel fuel, and jet fuel that can be handled the same way as their petroleum-based counterparts. For example, the Gas Technology Institute will test wood, corn stover, and an aquatic plant in an automated, integrated pilot facility that converts biomass directly into gasoline and diesel fuel.
Under the second initiative, DOE will provide up to $4.5 million to three projects focused on developing sustainable methods of biomass crop production. The projects will design, model, and implement biomass production systems across different regions of the country while looking at factors such as how plants impact soil erosion and water quality, quantifying the environmental impacts of different strategies for producing energy crops and using crop residues. The projects will also provide insight into where to locate bioenergy crops within a landscape to maximize their potential positive impacts.
Under this initiative, a team led by North Carolina State University will examine sites in Alabama, Mississippi, and North Carolina and will investigate biomass production options that are compatible with forest management, with a focus on the intercropping of pine and switchgrass. Meanwhile, the University of Minnesota and Purdue University will focus on energy crops in the Mississippi River watershed and watersheds in the Upper Midwest, respectively.
Switchgrass (shown in the photo below) will be studied by North Carolina State University to determine if it can be sustainably grown in close proximity to pine trees.
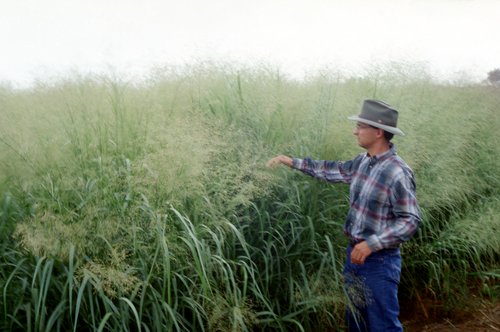
##SHARELINKS##
|
People
Rayonier, Jacksonville, Fla., USA, this past week announced that Paul G. Boynton has been elected president and COO by the company's board of directors, effective October 1. Boynton will report to Lee M. Thomas, chairman and CEO.
Boynton will be responsible for all of Rayonier's operating businesses. He will maintain oversight for Rayonier's Forest Resources business, which sustainably manages nearly 2.5 million acres of timberland in the U.S. and New Zealand, and for the Real Estate business, which manages the thousands of acres of land with potential for commercial, residential, conservation, or recreational uses. Boynton will also resume responsibility for the company's global Performance Fibers business.
Boynton joined the company in 1999 and currently serves as EVP, Forest Resources and Real Estate. Prior to that, he was SVP, Performance Fibers and Wood Products. He holds a Bachelor of Science in mechanical engineering from Iowa State University, a Master of Business Administration from the University of Iowa, and graduated from the Harvard University Graduate School of Business Advanced Management Program.
"Paul's strong track record and leadership experience in each of our three core businesses make him uniquely qualified to assume overall operational responsibility," commented Thomas. "I look forward to working with Paul as we execute our strategy to maximize value from a growing timberland base and to produce the world's highest quality cellulose products."
##SHARELINKS##
|
TAPPI News
A direct lightning strike on TAPPI offices in late August has affected the telephone and voicemail systems. We are taking corrective action and our evaluation indicates that a total system replacement is required and should be completed early November. Please bear with us as it will take a few weeks to correct the current shortcoming and implement a new solution to better serve you.
In the meantime, if you are calling TAPPI, you may not be able to leave a voicemail or it may cut-off in mid message. If you experience this difficulty, please either send an e-mail to memberconnection@tappi.org or call Member Connection number toll free at 800-332-8686 (U.S.) or 800-446-9431 (Canada). If busy, please use +1 770-209-7212.
We apologize for any inconvenience and thank you for your understanding while we find creative ways to meet your ongoing needs.
##SHARELINKS##
|
You still have time to join the legions of corrugated industry professionals heading to the TAPPI-AICC Corrugated Week 2010 event in Baltimore, Md., the week of October 4-8.
If you haven't registered yet, stop what you're doing now and go to the Registration Page so you won't miss, among the many activities, the outstanding Technical Program planned.
TAPPI Conference Keynotes
The cornerstones of the TAPPI Conference are two exceptional keynote speakers and the strong presence of other featured presenters.
Dennis D. Mehiel, president and Chief Operating Officer of U.S. Corrugated Inc., one of today's most dynamic and progressive companies in the industry, offers his keynote presentation, "Keeping it Simple: How We Achieved Success in the Box Business and How You Can, Too" on Tuesday, October 5.
John L. Knudsen, newly appointed Senior Vice President for Supply Chain and Board Sales for Smurfit-Stone Container, shares his experiences and insights from more than 24 years of experience in sales and operations management in the packaging industry with, "The New Smurfit-Stone: Positioned for Long-Term Profitability," on Wednesday, October 6.
TAPPI Sessions
Packaging safety, sustainability, quality and color consistency are more than familiar buzzwords – they're critical issues for today's corrugators and the focus of the TAPPI Sessions held October 5-6.
Safety Focus: With a new president in office, a new Director of Labor, and a new head of OSHA, there are sure to be changes in federal policies and procedures that will impact the entire industry. To find out how new regulations will affect your business, attend the Safety Focus 2010 presentation by Marc Freedman, executive director of labor law policy at the U.S. Chamber of Commerce. Freedman is responsible for developing and advocating the Chamber's response to OSHA matters and other labor and workplace issues. Freedman has appeared on various media outlets and testified before Congress on behalf of the U.S. Chamber.
Sustainability and Renewability: Moderator Michael Schaepe, Cargill, will lead a panel presentation on Sustainability and Renewability. Several speakers are scheduled, including Cynthia Forsch, Eco-Logic Strategies, who will address "What the retail grocery industry expects from Corrugated." Another speaker, Mike McLeod of Temple Inland, will discuss "Using Corrugated as Reusable Containers." For years, McLeod has observed the processes of use, return and costs of returnable plastic containers (RPCs), and he plans to underscore the use of control systems to accurately forecast packaging needs based on cycle times and conducting accurate cost analysis on RPC assets. McLeod also plans to address market observations, namely in the automotive industry, where corrugated lost share to other packaging options, and where new products can open doors and opportunities.
Color Consistency: This session highlights the change in the industry from producing pleasing (subjective) color to producing measured (objective) color with featured speaker, Axel Kling, Print Quality Assurance Manager at The Coca-Cola Company, Atlanta. Kling is expected to cover topics related to market trends and needs related to color, as well as packaging expectations. With reported revenue of US$31 billion dollars in 2009 and product sales in more than 200 countries around the world, Coca-Cola is a juggernaut company known for its attention to packaging and market concerns; Kling's presentation offers packaging pros a rare opportunity to gain valuable insight from a major player.
Quality Assurance: Food packaging expert, Rod Wheeler of AIB, presents "Understanding the Food Safety Enhancement Act and How It Specifically Relates to Protecting Packaging from the Threat of Terrorism." Wheeler is a homeland security and facility defense expert for AIB, and a crime analyst for the Fox News Channel. He'll discuss the importance of packaging to homeland security – a concern he says is often overlooked, even within the industry. Mike Freeman, Loma Systems, will share his expertise on "Implications of Metal Detection in Food and Corrugated Packaging."
The TAPPI Corrugated Conference takes place as part of the TAPPI-AICC-sponsored Corrugated Week, which includes a sold-out Trade Show and Exhibit at the Baltimore Hilton Hotel featuring nearly 150 exhibitors, plus many other special events. Learn more at www.corrugatedweek.org.
##SHARELINKS##
|
Formerly known as TAPPI Engineering, Pulping and Environmental Conference, registration for TAPPI PEERS Conference and the 9th Annual Research Forum on Recycling is discounted until September 20. To accommodate tight budgets, one registration fee will allow attendees to access both conferences taking place October 17-20, 2010 in Norfolk, Virginia. Register now for best rates!
TAPPI PEERS Conference is designed to answer the most pressing business and technical questions faced by pulp and paper companies as they manage raw materials, assets, regulatory requirements and production assets. With several focused tracks and more than 40 sessions, PEERS offers peer-reviewed papers, expert speakers, exclusive networking opportunities and new technologies that can help mills optimize operations.
The 9th Annual Research Forum on Recycling, running in conjunction with the PEERS Conference will continue its history of highlighting cutting-edge research results from around the world and will offer extraordinary opportunities for professional development and personal growth.
These events will also include training workshops, a mill tour (focused on recycling), Hot Topic Breakfast, a New Product Showcase, a Trade Fair, networking events, a spouse/guest program, a dinner cruise, and a 5K Fun Run. Learn more.
##SHARELINKS##
|
BioPro Expo & Marketplace, the largest biomass conference in the Southeast, will be held on March 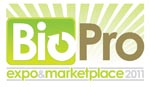 14-16, 2011, at the Atlanta Hilton in Atlanta, Georgia, USA. The conference will benefit farmers, dedicated energy crop producers, local and state governments, wood waste producers, and manufacturers.
BioPro Expo & Marketplace 2011 includes a new Marketplace. This expanded feature of the conference allows for a more extensive presentation of the ‘near term' biomass technologies that the attendees are wanting to learn more about.
In addition, the 5th Annual International Bioenergy & Bioproducts Conference (IBBC) will be held at the same time as the BioPro Expo & Marketplace event. IBBC is the only event that focuses on deploying wood-based biorefineries and using forest products industry resources.
To register and for more information: Visit www.bioproexpo.org.
##SHARELINKS##
|
A Call for Papers or Posters has been issued for the Papermaking Program at PaperCon 2011 being held May 1-4, 2011, in Covington, Kentucky, USA.
The deadline for submission of titles and abstracts for technical papers, posters as well as for panel sessions and roundtables is November 15, 2010.
Paper company personnel, suppliers, students and academics are strongly encouraged to submit abstracts, as TAPPI is interested in providing a forum for new concepts and speakers.
See the full list of recommended topics and submittal details and learn more about PaperCon 2011.
##SHARELINKS##
|
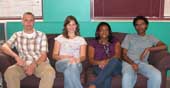 On a recent visit to the IPST Student Chapter at Georgia Tech, TAPPI Staff members David Bell and Simona Marcellus had the opportunity to sit down and talk with several members of this growing chapter. The students agreed that their greatest needs were more networking opportunities with industry and jobs when they graduate. They are enthusiastic about having industry professionals speak to their chapter members on these topics. The chapter officers are pictured here.
The chapter has been reinvigorated by IPST's new director and faculty advisor, Norman F. Marsolan, and they are focused on recruiting new members and finding new ways to actively participate in TAPPI. They have also started to develop a new website and are exploring a presence through social media channels.
TAPPI student chapters conduct fundraising events to cover their operational costs and travel expenses to TAPPI conferences and events. If you are interested in helping the IPST student chapter, please contact their president Mikhail Levit or David Bell if you'd like more information on other TAPPI Student Chapters.
##SHARELINKS##
|
Join us at the Empire Room, NYS Fairgrounds, Syracuse, New York, on September 28 where Empire State TAPPI – New York/Canadian PIMA will co-host with Central NYWEA a program entitled "Sustainable Wastewater Treatment."
This program will have something for everyone. There will be no charge for mill personnel, and for other attendees the charge will be $125. Speakers have been lined up to discuss treatment plant operations, latex coating treatment and intelligent process control. We will have a presentation on the Rock Tenn Solvay mill followed by a tour. In addition, we will have tabletop exhibits during the breaks. Exhibit spaces are still available. Contact: Phil Dorsey, pdorsey@smpe.com or 585-624-4490.
Click here for details of the program and registration information.
##SHARELINKS##
|
After a VERY successful spring meeting of TAPPI's Ohio Local Section, our follow-up meeting will be held at Appleton Papers on Friday, October 15, 2010. We will present a technical seminar on Energy Management in the Paper Industry.
Admission is $25 for TAPPI members who pre-register before October 1; this also guarantees you a lunch! Admission will be $40 at the door. For non-TAPPI members, the meeting fee is $50. As always, students are free.
For additional information as well as registration contact information, click here.
##SHARELINKS##
|
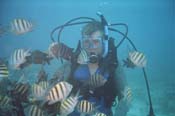 Stepping into the Member Spotlight this month is Richard "Rick" Croker, active member since 1975. As Director of Technical Services for Georgia-Pacific Containerboard LLC, Rick is responsible for setting all product specifications for the company's containerboard mills.
A two-time past Chairman of a TAPPI local section, Rick has also served as Chairman of several committees, taught numerous courses around the world, published 20 technical papers and co-authored 12 TIPs for TAPPI's Corrugated Packing Division. An avid scuba diver, he was also a PADI instructor for more than 18 years and firmly believes that teaching enables lifelong learning.
Spotlight participants are often recommended by fellow members and staff. If you would like to nominate a member (or even yourself!) just send their name (or names) to MemberSpotlight@tappi.org. We will forward a Spotlight Questionnaire to fill out and return.
We look forward to seeing you in the Spotlight!
##SHARELINKS##
|
The 2010 TAPPI Nominating Committee announces the 2011 TAPPI Board Slate. Nominees and their respective positions are:
Chair – Norman Marsolan - Director IPST and Chemical Engineering Professor of the Practice, Georgia Tech IPST@GA Tech
Vice Chair – Thomas J. Garland - President and CEO, PaperWorks Industries Inc.
Directors –
• Sandra L. Le Barron, Director of Environmental, Health and Safety, Finch Papers
• Markku A. Karlsson, Senior Vice President of Technology, UPM-Kymmene Corporation
• Bob Snyder, President and CEO, Orchids Paper Products
Returning Directors
Davide R. Friedman, General Mills Inc., 2009-2011
Robert J. Gallo, Voith, 2010-2012
Jeff Hamilton, Sappi Fine Paper North America, 2010-2012
Chris Luettgen, Kimberly-Clark, 2010-2012
Thomas E. Rodencal, Rodencal Paper Consulting Inc., 2009-2011
Gary M. Scott, State University of New York, 2009-2011
Larry N. Montague, President and CEO, TAPPI
Other Nominations
Per TAPPI's Bylaws, the Association's membership has until November 1, 2010, to submit other nominations to the President and CEO of TAPPI, Larry N. Montague at lmontague@tappi.org. Such nominations must be signed by at least one percent of the voting members, and each voting member may sign for only one such nomination. Each such nomination must be accepted in writing by the nominee.
The name of each such nominee so submitted, signed and accepted shall be placed on the election ballot. The election ballot shall give voters the options of voting for or against the entire slate or for or against the individual candidate(s) for each position. Elections will begin December 1, 2010, and conclude January 15, 2011. Contact Mary Beth Cornell, + 1 770-209-7210 or mcornell@tappi.org with questions.
Retiring Officers and Directors
Jeffrey J. Siegel, Mica Corporation(Chair)
Vincent Newberry, Mondi Akrosil, LLC
Nicki S. Slusser, International Paper
2010 Nominating Committee
Chair
Mark R. McCollister, Paperchine Inc.
Members
Kathy Buckman Gibson, Buckman
Scott Frasca, RohmNova
Charlie Hodges, Port Townsend Paper
Asko Hyttinen, Strategy First
Norman F. Marsolan (non-voting), IPST @ GA Tech
Larry N. Montague, TAPPI
Jeff Pallini, Fosber
Gerry Ring, University of Wisconsin--Stevens Point
Barb Russell, Sonoco
##SHARELINKS##
|
"You have no control over what the other guy does. You only have control over what you do." A. J. Kitt (1968 - ), world champion skier
##SHARELINKS##
|
|
|