Over the Wire
TAPPI
Weekly Spotlight
VTT Technical Research Centre of Finland has published a study on the carbon footprint and other environmental impacts of newspapers, magazines, photo books, books, and advertising leaflets. The case studies were based on a life cycle assessment that followed print products from cradle to grave—fiber supply, paper production, printing, transport, use, and recycling and waste management.
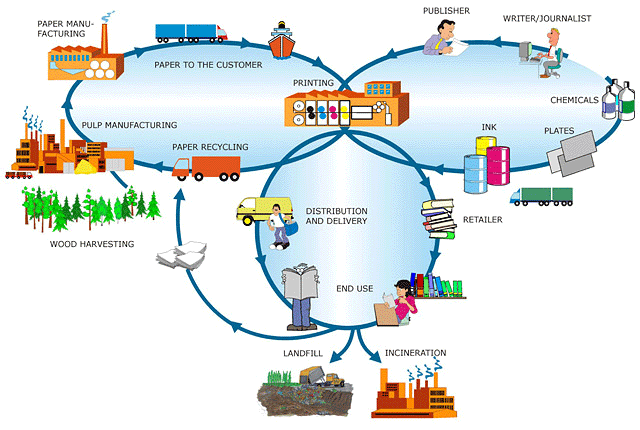
The VTT study showed that greenhouse gas emissions produced by a single newspaper during its entire life cycle correspond to a car journey of approximately one kilometer. The carbon footprint of a book bought from a store is equivalent to the greenhouse gas emissions of a car journey of approximately 7 kilometers. The research gives information about the environmental impacts' magnitude related to products of the print products' group.
The carbon footprint of newspapers mostly comprises emissions caused by the electricity and heat production required for making the product as well as greenhouse gas emissions resulting from transport. In addition, methane is produced as a result of the decomposition of newspapers deposited in landfill sites.
Emissions resulting from the use of purchased electricity in paper production and printing are responsible for approximately 50% of the carbon footprint of a typical Finnish newspaper. If all of the purchased electricity required for the production of newspapers constituted what is known as "green electricity," such as wind power or hydropower, the carbon footprint of a typical Finnish newspaper would drop by approximately 40%.
The carbon footprint of an annual volume of daily newspapers amounts to approximately 75 kg of carbon dioxide equivalents and that of a single newspaper to approximately 210 g. The carbon footprint of an annual volume of daily newspapers is equivalent to the greenhouse gas emissions of a car journey of 456 kilometers.
The carbon footprint of an annual volume of weekly magazines is equivalent to the greenhouse gas emissions of a journey of 45 kilometers by a car. Based on the assumptions made in the study, the greenhouse gas emissions produced over the entire life cycle of a single magazine are therefore equivalent to a car journey of approximately one kilometer.
The carbon footprint of a book is equivalent to the greenhouse gas emissions of a journey of about 7 kilometers by car. According to calculations, the carbon that remains bound to a printed paper product such as a book reduces after five years the carbon footprint caused by the production stage by approximately 5%. After 100 years, the drop is approximately 75%. In the study, the life cycle of books was followed from the sourcing of raw materials to the retailer's warehouse. The last stage of the life cycle (recycling and waste management) was excluded from the examination.
The contribution of newspapers, books, and other paper products to the climate impacts of consumption by Finnish households in 2005 was small (approximately 1%). The biggest climate impacts of consumption by Finnish households were attributable to housing (28%), food products (16%), and transport (13%).
More information about this study is available online.
##SHARELINKS##
|
International Paper Co., Memphis, Tenn., USA, is hosting the 2011 Coins 4 Kids 5K Run and Walk, to be held April 2, beginning at 8:30 a.m., at IP's global headquarters, 6400 Poplar Ave., in Memphis. Early registration is $18 and members of the Memphis Runners Track Club get a $1 discount. Registration is available online http://www.coins4kids.com and race-day registration will be available for $25 on April 2, beginning at 7:00 a.m. at the race site.
In conjunction with the Coins 4 Kids Run and Walk, the event will include a kid's Peanut Butter & Jelly (PB&J) Fun Run to support The Memphis Food Bank. In lieu of a registration fee, children are asked to donate a jar of peanut butter and/or jelly to enter the PB&J Run. This race is open to children ages 12 and younger and begins at 9:45 a.m.
All of the race proceeds benefit Coins 4 Kids, an award-winning school feeding program launched in 2004 as a partnership between IP and the World Food Programme, the world's largest humanitarian agency. For $0.25 per day or $50 per year, school children who would otherwise go hungry are provided food in school each day. Annually, gifts from the company, IP employees, friends, and the International Paper Foundation provide meals in school for more than 72,000 school children in poverty-stricken areas of Nairobi, Kenya.
"IP will always support the communities where our employees live and work," said Patty Neuhoff, president of the International Paper Foundation. "Coins 4 Kids gives us an avenue to continue our corporate responsibility around the globe."
Awards will go to the top male and female overall winners, male and female masters winners, and the top three finishers in each of the following age groups: 10 and under, 11-14, 15-19, 20-24, 25-29, 30-34, 35-39, 40-44, 45-49, 50-54, 55-59, 60-64, 65-69, and 70 and over.
##SHARELINKS##
|
The latest listing of job openings in the TAPPI Career Center reflect a growing need for engineers and technical specialists, together with increased listings in all areas as the U.S. and global pulp, paper, and forest products recovery continues. Current job openings in the TAPPI Career Center include:
Knowlton Technologies, LLC |
Technical Service Manager |
Georgia Pacific |
ASSET AVAILABILITY LEADER |
Dart Container Corporation |
Senior Materials Engineer #270 |
Kimberly-Clark Corporation |
Electrical Engineer II/III |
Kimberly-Clark Corporation |
Process Engineer II/III/IV and Sr. |
Kimberly-Clark Corporation |
Mechanical Engineer II/III/IV |
Econotech Services |
Pulping and Bleaching Manager |
Pratt Industries (USA), Inc. |
Assistant Paper Machine Superintendent |
Primary Manufacturing |
Maintenance Manager |
CORPAK, Inc. |
Corrugator Operator / Single Facer Operator |
More information about these jobs is available online.
##SHARELINKS##
|
Market Roundup
Total U.S. printing and writing (P&W) paper shipments decreased 6% in February compared with February 2010, according to the AF&PA (Washington, D.C., USA) February 2011 Printing-Writing Paper Report, All four major P&W paper grades posted decreases compared with last February. U.S. purchases (shipments + imports - exports) of P&W papers also decreased 6% in February. Total P&W paper inventory levels increased 2% compared with January 2011.
Some points of interest from the report include:
- Uncoated free sheet (UFS) inventory increased m/m for the fifth consecutive month
- The y/y decrease of coated free sheet (CFS) shipments ended a streak of increases at 15 consecutive months
- Purchases of coated mechanical (CM) decreased y/y for the sixth consecutive month
- Uncoated mechanical (UM) y/y shipments declined for the second month.
##SHARELINKS##
|
February Pulp and Paper Products Council pulp figures this past week came in slightly weaker than expected, "but supply/demand remains balanced in our view," reports Mark Wilde, senior analyst with Deutsche Bank. Total shipments decreased by 1.6% Y/Y. The overall inventory level rose by 1 day m/m (+1 day for softwood, +2 days for hardwood). "We attribute some of the weakness to North America, where shipments declined 9.6% y/y to 557,000 metric tons, with weather-related issues likely impacting volumes. Looking ahead, we don't expect such a sharp rate of decline to continue over the remainder of the year. Additionally, we are mindful of the month–to–month volatility in these numbers." Wilde said.
"A tale of two pulp grades?" Wilde asks. Hardwood fundamentals are still weaker than that of softwood, he notes. For February, China hardwood shipments were down 30.4% y/y to 219,000 metric tons and North America fell 17.4% y/y to 208,000 metric tons. The softwood market remained relatively stable with overall shipments up 2.8% y/y. In contrast with hardwood, y/y improvement was driven by China, where shipments were up 14.9% to 325,000 metric tons. This continued strength helped to offset weakness in North America, where softwood shipments declined 5.7% y/y, Wilde says.
The data are marginally supportive of recent $30/metric ton price hike announcements for softwood pulp slated for April 1, Wilde explains. "Despite the two-day increase in hardwood inventories, we believe the recently announced $30 BEK hike will be successfully implemented considering that overall pulp inventories were basically flat, softwood prices are rising, and some of the shipment weakness in February may have resulted from weather conditions and/or month-to-month demand volatility. Our expectation is still that pulp demand/supply will remain relatively balanced in the months ahead," he notes.
##SHARELINKS##
|
Markets Research Company Wilde also reports that "we're receiving reports of Asian companies raising paper and paperboard prices, pointing to supply constraints. Elsewhere, consumer goods companies and their packaging suppliers are expressing concern about potentially-contaminated Japanese fiber." The upshot?--pressure on non-Japanese OCC, Wilde says.
##SHARELINKS##
|
Pulp & Paper
Clearwater Paper Corp., Spokane, Wash., USA, this week selected Metso, Helsinki, Finland, to supply its new through-air-dried (TAD) tissue machine to be located at the company's previously announced Shelby, N.C., tissue converting and distribution facility. The new production and distribution capabilities of the Shelby facility will increase the company's ultra and premium offerings to existing U.S. Southern and East Coast customers and create new opportunities to expand the company's private label consumer tissue business to other retail grocery chains in the region.
Construction of the first phase — converting and warehouse areas of the facility — is on schedule and the company expects to begin converting production at the facility in the second half of 2011. The new Metso paper machine is expected to begin production during the second half of 2012.
"We chose an industry staple, a proven supplier, a machine used by many tissue companies around the world," said Brian Hoaglund, expansion project leader for Clearwater Paper. "Our team looked at all of the leading suppliers, but in the end we were most comfortable with Metso, due to their excellent engineering and quality end-product as well as top notch customer service."
Metso's machine will comprise a complete tissue production line with stock preparation equipment and an Advantage ThruAir 200 TAD tissue machine including an OptiFlo II TIS multi-layer headbox, Thru-Air dryers and air system, and an Advantage WetDust dust management system. The production line will also feature Metso's Advantage SoftReel-B belted reel technology. The production line will be optimized to produce ultra TAD quality tissue and towel products at high speed and efficiency.
Clearwater produces quality consumer tissue, away-from-home tissue, hard roll tissue, machine glazed tissue, bleached paperboard, pulp, and wood products at 14 manufacturing locations in the U.S. and Canada. It is a premier supplier of private label tissue to major retailers and wholesale distributors. The company also produces bleached paperboard, and has some 3,800 employees.
##SHARELINKS##
|
Domtar Corp., Montreal, Que., Canada, this week announced that, no later than July 1, it will permanently shutdown one of four paper machines at its Ashdown, Ark., USA, pulp and paper mill. This will reduce Domtar's annual uncoated freesheet paper production capacity by approximately 125,000 short tons. The mill's workforce will be reduced by approximately 110 employees.
Following the shutdown, the Ashdown mill will continue to operate three fiber lines, a pulp dryer, and three paper machines, and employ approximately 940 people. The mill will have an annual production capacity of approximately 810,000 metric tons of pulp and some 780,000 short tons of paper.
"Domtar is committed to keeping a balance between its supply and its customer demand. Because secular demand decline in North America continues, we must permanently reduce our uncoated freesheet paper production capacity," said John D. Williams, president and CEO of Domtar. "I want to thank affected employees for their efforts, and recognize all Domtar Ashdown mill employees for their hard work and continued focus on safety," added Williams.
The closure will result in an aggregate pre-tax charge to earnings of approximately $80 million, which includes an estimated $77 million in non-cash charges relating to the accelerated depreciation of the carrying amounts of manufacturing equipment and the write-off of related spare parts and $3 million related to other costs. Of the estimated total pre-tax charge of $80 million, $6 million is expected to be recognized in the first quarter of 2011 and $74 million is expected to be incurred in the second quarter of 2011.
##SHARELINKS##
|
International Paper Co., Memphis, Tenn., reported this week that it has agreed to purchase approximately 53.5% of the outstanding shares of Andhra Pradesh Paper Mills (APPM) of India for some $257 million in cash. In addition, IP agreed to a $62 million non-compete payment to the sellers, L.N. Bangur and related family members and affiliates.
Pursuant to Indian securities law, IP will also launch a mandatory public tender offer to acquire up to an additional 21.5% of the outstanding shares of APPM for approximately $104 million in cash. IP anticipates acquiring up to 75% of APPM's outstanding shares through these two transactions.
Once completed, the transaction will position IP as the first global paper and packaging company with a significant position in India's fast growing economy. APP has annual sales of approximately $160 million.
"APPM is an established and highly respected company in India, and is an excellent platform for IP to grow with the Indian paper and packaging markets," said John Faraci, chairman and CEO of IP. "Both APPM and the India paper and packaging industry are growing at substantial rates, and we believe that IP's global operations and technical expertise can accelerate that growth and create value for customers as well as IP and APPM shareholders."
L.N. Bangur, executive chairman, Bangur Group, noted that "we have built a strong business in India, and the next phase of growth requires a different set of resources and capabilities. IP is the right company to take the business forward and deepen maturity of the sector in India."
APPM is one of the leading integrated paper manufacturers in India, with two mills having a combined capacity of about 250,000 metric tpy of uncoated freesheet paper. The existing management team and 2,500 employees of APPM will continue to operate the business, supplemented by additional IP leadership and technical resources.
The share purchase and public tender are expected to be completed as early as the third quarter, subject to regulatory and other approvals, including the Security and Exchange Board of India (SEBI), the Reserve Bank of India (RBI), and, if applicable, the Competition Commission of India.
##SHARELINKS##
|
Kunshan APT Coldwater Technology Manufacturing and Coldwater Group, Atlanta, Ga., USA, reported this week that they will begin construction of a new Eco Friendly Green Factory in Kunshan China with a floor space of 4,000 sq. meters. The Green factory will be home to Kunshan APT Coldwater where Coldwater's suction roll seal strips are processed for most paper mills in the Chinese market.
In addition to the KAPTCO factory, the facility will have eight mini green factory spaces to lease out to companies that have a focus on providing sustainable solutions. The eco factory will use the latest environmentally friendly technologies such as solar heat for hot water, geothermal for heating and cooling of the building, sustainable building materials, green roofing, sky lights, and light tunnels for natural lighting, rain water collection and reuse, building orientation optimization, and reuse of recycled materials.
##SHARELINKS##
|
Mitsubishi Paper Mills, Tokyo, Japan, this week updated damages caused by the March 11 earthquake and tsunami. The company says that six employees were injured and three production sites were damaged.
The company's Hachinohe mill (Hachinohe city, Aomori prefecture) has stopped operations. The Tsunami flooded the ground floor of the mill and the electrical system was severely damaged. Damage to the buildings and the paper machines were rather mild. Based on the above situation, resumption of operations are planned as follows :
- From the end of April: one by one startup of power plants (recovery of utility generation facility)
- From mid-May: one by one startup of paper machines and coaters (seven paper machines and three coaters).
To contribute to a nationwide power shortage, the company is negotiating with the relevant ministries, Aomori prefecture, and Tohoku Electric Power to supply some power to Tohoku Electric Power from the mill's power plant as soon as it resumes.
Damage at the Kitakami Division facilities (Kitakami HiTech Paper Co., Kitakami City, Iwate Prefecture) is relatively minor, and the hygienic paper production facilities were restarted March 21. Despite some concern about the shortage of certain raw materials, from the beginning of April, the pulp plant, the paper machine, and the resin coaters will be started up stepwise.
Damage at the Shirakawa mill (Nishigou, Nishishirakawa County, Fukushima Prefecture) is also minimal and the stock finishing process was started up March 18. From March 23 on, it is expected to recover fully including two paper machines, though it may take more time to reach full capacity production due to the shortage of heavy oil supply.
The product inventory at the Hachinohe mill was flooded by the tsunami and damaged by the earthquake. The total damage of the inventory is still under investigation. Inventories in the company's warehouses in the Kitakami, Sendai, and Kanto area were also damaged by the earthquake. However, the damage was minor and limited. The impact on earnings is still being investigated and will be reported separately.
##SHARELINKS##
|
For the fourth year in a row, Mohawk Fine Papers, Cohoes, N.Y., USA, has been named a winner of the annual Progressive Manufacturing 100 Awards, which recognize the top 100 manufacturing companies from around the world that have achieved significant breakthroughs in innovation, in the use of advanced technologies, and in the effective management of their businesses. An independent blue-ribbon panel -- including leading manufacturing researchers and analysts, academics, and manufacturing executives -- recognized Mohawk for its innovation in the Business Model Mastery award category.
"The Progressive Manufacturing 100 Award is in recognition of the development of a cloud-based service-oriented architecture that enables the rapid and dynamic formation of business partnerships to deliver a unique portfolio of products and services to our customers," says Paul Stamas, VP of information technology at Mohawk.
In collaboration with Syracuse University and Liaison Technologies, Mohawk developed a cloud-based, service-oriented architecture designed to enable interoperability with business partners and cloud-based business applications. The company has leveraged this solution to effectively integrate its business processes with its customers, logistics providers, and manufacturing partners.
In addition to Mohawk, this year's Progressive Manufacturing 100 winners include: Boeing, Caterpillar, Chevron, Coca-Cola, Dow Chemical, Ford, IBM, General Motors, Honeywell, Kodak, L'Oreal, Lockheed Martin, Motorola, Nestle, and Porsche.
##SHARELINKS##
|
The AF&PA, Washington, D.C., USA, this week announced its 2011 Recycling Award winners, recognizing some of the work being done by businesses, communities, and schools across the country to recover paper for recycling. In 2010, 63.5% of paper consumed in the U.S. was recovered for recycling, up slightly from 63.4% in 2009. Paper recovery for recycling has increased by 77% since 1990.
The 2011 winners were:
- Business Leadership Award – MGM Resorts International, Las Vegas, Nev. This company operates a portfolio of destination resort brands including Bellagio, MGM Grand, Mandalay Bay, and The Mirage. Proving that luxury and sustainability can co-exist, the corporation's 60,000 employees recovered 10,913 tons of paper and paper-based packaging from their operations in 2010. ·
- Community Recycling Award – Onondaga County Resource Recovery Agency, Onondaga, N.Y. With the leadership of the OCRRA, the 450,000 residents of Onondaga County recovered 165,000 tons of paper and paper-based packaging in 2010. Curbside collection, drop-off locations, and annual shredding and book recycling events are promoted through a comprehensive education and outreach program that incorporates multi-media advertising, newsletters, emails, and Facebook fan pages. ·
- School Recycling Award – Purdy High School, Purdy, Mo. This high school's recycling program in Southwest Missouri was initiated in 2005, with a dual goal of providing a service to the community and raising funds for the Spanish Club. Just five years later, this self-sustaining program successfully recovered 26 tons of paper (77 lb per student) while providing rigorous academic integration and education for the community at large.
##SHARELINKS##
|
Sappi Fine Paper's Stockstadt mill in Germany has ordered a modern metsoDNA control system for the Metso/Valmet winder type JR 1000 that was delivered to the mill in 1992. The system upgrade will enable adapting production line No. 2 at the Stockstadt mill to constantly changing market requirements.
To adjust to the increasingly stringent safety requirements and bring the JR 1000 winder to the newest level of safety engineering, modifications will also be made in the winder's safety devices and its surroundings. The rebuild is planned for this summer and fall.
##SHARELINKS##
|
Syktyvkar Tissue Group has ordered a rebuild of PM 2 tissue line at its mill in the Republic of Komi in Russia. The first stage of the rebuild, to be handled by Metso of Finland, is scheduled to be completed at the end of this year. The value of the order will not be disclosed.
Metso will rebuild the PM 1 tissue line to be of the Advantage DCT 100 type, similar to the mill's PM 2 tissue line built by Metso. Metso's delivery will in the first stage comprise a Metso deinking line with stock preparation equipment, an Advantage DCT 100 former section including an OptiFlo II TIS headbox, a press section, an Advantage AirCap hood, and a reel. The delivery will also include Metso QCS and DCS systems.
The 2.7-m-wide PM 1 tissue machine is designed for a speed of 1,600 m/min and the line for a daily production of 75 tons of tissue.
##SHARELINKS##
|
Syassky Pulp and Paper, St. Petersburg, Russia, reports that it has ordered a new tissue line from Italian manufacturer Toscotec to be installed at the company's mill in Syasstroy, Russia. The new machine will replace the mill's existing PM 2.
Syassky PPM, one of the oldest and important pulp and paper mill in the USSR period, was founded in 1928, with the unique aim to cover the needs of the domestic market. Actually, Syassky is one of the most modern enterprises of the northwest Russian region and the only tissue producer in this area with integrated production, having an in-line pulp mill, tissue production (PM 2, PM3, PM 5), and converting, as well as packaging facilities.
The new Toscotec AHEAD 1.5M crescent former machine consists in a single layer headbox, single press configuration TT SPR 1050, a 3,660-mm-dia steel yankee dryer TT SYD 12 ft., and a renewed reel TT REEL-P. The scope of supply also includes upgrading of the existing stock preparation plant, approach flow system, gas heated hood, steam and condensate system, as well as the electrification and control system. Engineering and services (erection supervision, commissioning, and startup assistance and training) complete the Toscotec package. Machine speed will be up to 1,400 m/min with a trim width of 4,200 mm, for a daily production of 125 tons.
Syassky PPM's manufacturing facilities have the following annual production capacity:
- Bleached softwood sulfite pulp, 120,000 metric tpy
- Chemi-thermomechanical pulp, 100,000 metric tpy
- Tissue paper, 71,000 metric tpy
- Lignosulfonate liquid, 200,000 metric tpy
- Fodder yeas, 4,000 metric tpy
- Toilet Paper, 280 million rolls
- Paper napkins, 20 million packs
- Roller towels, 15 million rolls.
The main tissue brand produced by Syassky is Myagky Znak that in 2010, according to AC Nielsen Market Research, has reached a 21% market share in the Moscow and St. Petersburg regions. During the past two years, the company has conducted a major investment program that resulted in the startup of new converting lines, packaging lines, and of a new Toscotec TT Wind-H winder that successfully came on-stream in September 2010.
##SHARELINKS##
|
Containerboard/Packaging
Lombard Investments, San Francisco, Calif., reports that it has sold its 23% stake in paper packaging manufacturer S Pack & Print Public Co. of Thailand to Oji Paper Co., realizing a 3.5x return. Oji Paper, founded in 1873 and based in Chuo-ku, Tokyo, is Japan's leading paper packaging and related product manufacturer.
Lombard notes that it invested in the then privately held S Pack through its Thailand Equity Fund to facilitate financial restructuring, a subsequent IPO, and expansion. During Lombard's holding period, the company built a strong market position that benefited from Thailand's growing export trade.
Established in 1982, S Pack has grown steadily to become one of Thailand's leading paper packaging companies, operating factories in Had Yai District, Songkhla Province, and Bangkok. S Pack provides high grade commercial printing and corrugated box services and products for multinational companies, including producers of latex gloves, consumer electronics, and convenience food and airlines.
##SHARELINKS##
|
Papier und Kartonfabrik Varel, Germany, reports that it is pushing forward with the revamp of its PM 4. The machine is being reconstructed to expand the mill's product portfolio with white testliner and kraftliner substitute qualities. Some of the newly installed components of PM 4 are already in operation or startup is imminent.
With a new starch preparation plant, the mill will be able to activate starch enzymatically. This process is more eco-friendly, since the usage of chemical substances is not necessary, the company explains. Also, the cumulative energy balance is significantly better compared with the thermochemical method, it adds, noting that the new starch preparation plant was put in operation at the beginning of this year.
A new indoor crane with a lift capacity of 80 metric tons was installed several weeks ago. This crane will lift all components to their final position during the time of revamp, beginning in April. Thereafter this crane will be used for tambour lifts as well as for maintenance jobs.
A newly designed 90-m³ D-pulper is set to startup at the end of April. This unit will supply pulp to PM 4-line 1.
All revamp measures are being carried out during the mill's regular manufacturing schedule, which underscores the complexity of the project and capability of the project teams, the company points out.
##SHARELINKS##
|
The Paperboard Packaging Council (PPC) on May 17 - 18 will host its first Folding Carton Boot Camp workshop for the year at PPC headquarters in Springfield, Mass., USA. The Folding Carton Boot Camp, PPC notes, "is ideal for anyone new to carton construction (even if not new to the industry) as well as non-plant personnel with limited experience outside of a single plant operation.
PPC explained that the program mirrors the packaging production process, moving from how paper is made to inks and coatings, prepress, CAD, layout, graphics, presses, tooling, embossing, stamping, stripping, finishing, gluing, windowing, and automatic packaging equipment. Participants are awarded a certificate of achievement at the end of the session.
"Boot Camp is a fantastic opportunity for employees unfamiliar with the complete boxmaking process," says PPC's president Ben Markens. "Each time we've hosted this event, company leaders tell us the experience was invaluable in creating and maintaining a more well-rounded and informed staff."
The Folding Carton Boot Camp is open to both PPC members and non-members. More information and registration is available online.
##SHARELINKS##
|
Published Pricing
Botnia, Finland, will increase its pulp prices in Europe beginning April 1. The company's new prices are $1,010/metric ton for softwood pulp (NBSK), and $880/metric ton for bleached birch sulfate pulp. All prices are CIF Botnia's usual ports. Other terms remain as agreed.
##SHARELINKS##
|
Södra Cell, Växjö, Sweden, this week announced a $30/metric ton increase for its softwood pulp. The new price, effective April 1, is $1,010/metric ton. Södra is the world's third largest supplier of market pulp. The company operates five pulp mills (three in Sweden and two in Norway) with a total capacity of 2.1 million metric tpy, of which just over 100,000 tons is mechanical pulp (CTMP) and the rest bleached kraft pulp. The company makes pulp from softwood and hardwood, including eucalyptus. Softwood pulp makes up 80% of its total production and hardwood pulp the remaining 20%.
##SHARELINKS##
|
The Newark Group, Cranford, N.J., USA, reports that effective April 11 its Paperboard Products division will implement the following fuel surcharges per shipment to a customer's dock:
- 0 - 24 miles, $25 ·
- 25 - 74 miles, $80 ·
- 75 - 124 miles, $130 ·
- 125 - 174 miles, $180 ·
- 175 - 224 miles, $235 ·
- 225 miles or more, $290.
The company attributes the surcharges to a rapid escalation of diesel fuel prices, and says they are calculated on a base cost of $3.14/gal, which is the U.S. Energy Information Administration's average diesel price for the month of November 2010.
##SHARELINKS##
|
People
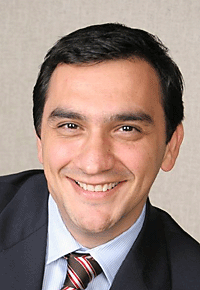 Stora Enso, Helsinki, Finland, has appointed Juan Carlos Bueno to head the company's operations in Latin America and serve as a member of the Group Executive Team, effective April 1. Bueno is a native Colombian and has worked for DuPont in various positions since 1992. For the past several years he has been VP, leading the DuPont Agricultural Products business in Brazil. He has some 20 years of experience in finance, sales, marketing, and general business management.
Nils Grafström, for the past eight years head of Stora Enso Latin America, will retire as previously planned in June 2011.
"We welcome Juan Carlos Bueno to the Stora Enso team with high expectations. He will bring us a combination of solid business experience and totally new insights into Latin America. Throughout his career Juan Carlos has demonstrated strong strategic and operational capabilities in the changing economic and market conditions, not only in Latin America but also in Europe and North America," said Stora Enso CEO Jouko Karvinen.
##SHARELINKS##
|
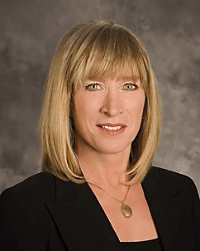 MeadWestvaco Corp., Richmond, Va., USA, this week reported that it has selected Diane Teer the new president of the company's food packaging business. Teer will lead profitable growth strategies, including building strong partnerships with food customers and driving "shopper ready" solutions across retail grocery channels. She brings considerable experience in launching disruptive new consumer packaged goods products and actively aligning business segments to new and changing company values and growth strategies.
Teer most recently served as president of World Kitchen LLC, where she led the North America division as well as global innovation for brands such as Pyrex, Corelle, Corningware, and Chicago Cutlery. Prior to World Kitchen, she held leadership positions in Frozen and Culinary Foods at Conagra Foods during her four year tenure. While there, she oversaw brands including Banquet, Marie Callender's, and Healthy Choice as part of the $2 billion frozen foods business, and provided strategic oversight for all dedicated functional areas and plants. She also spent nine years at The Campell Soup Co. as VP and GM of the Beverage division and as president of the New Growth division, VP of Red & White Soups, and VP Marketing for the Canadian division. Prior to Campbell Soup, she led marketing efforts at The Nabob Coffee Co. and the integration of its brands into Kraft's portfolio following the acquisition by Kraft Canada.
##SHARELINKS##
|
Travels with Larry
Can you name one corrugated converting facility that nearly tripled its sales over the past 5-6 years in what some have called the worst economy since the Great Depression? By the way, this growth did not come through plant consolidations or through big national account business.
It came from a 125,000-square-foot plant in Raleigh that was built in 1982, with 62 employees (11 temporary) and purchased by Pratt Industries in 1992. The plant is one of Pratt Industries Converting Division locations. Pratt is made up of 6 different divisions in the United States: Recycled, Mill, Corrugated, Converting, Display and Clean Energy.
My visit to Pratt began with a call to TAPPI member Roger Dooley of Stafford Cutting Dies, which supplies rotary and flatbed cutting dies as well as other tooling and training to the corrugated industry
I asked Roger, who's been with Stafford for 5 years, if he had some time to meet with me during my recent visits to North Carolina. He said that he could do better than that and asked me if I would like to tour one of his favorite customer's plants – the Pratt facility. Stafford, which was formed in 1991, has steadily added new capacity and equipment nearly every year since then. They have experienced sales growth of 30% over the past 2 years and currently employ 56 people. They already have 6 new hires in 2011.
Now back to Pratt. What a great group of people. They spent a great deal of time with me showing me around and telling me about the Pratt philosophy. Mike Keepers, General Manager, Jeff Bunner, Sales Manager, Brandt Gunther, Designer, Scott Strong, Technical Representative/Design and Tracy Stallings, Production Manager, all made me feel right at home during my visit. It is very easy to see why their business has grown so much with their Can-Do attitudes.
Mike Keepers shared the following about this plant: "Our service and quality are what set us apart. We've found our niche and focus on what we're good at. We don't try to be all things to all people. For instance we have the unique ability to manufacture a 2"x2"x2" blank to make a 6" box - one of the many different sizes we get out the door on a daily basis. We also offer 72-hour turn around as well as next-day releases. Plus, we use our own mills for 95% of our paper, and have narrowed our basis weights and can meet ECT with lighter grades. But the bottom line is our people. They really do make the difference. You cannot forget that your internal people are as important as the external people you deal with on a regular basis. This is something the entire Pratt company believes in. I'm proud to be a part of a Family Train that is on the right track and ahead of the curve."
For more information about Pratt go to www.prattindustries.com
For more information about Stafford go to www.gostafford.com
There are two types of people in our industry, TAPPI members and those who should be.
Until next time............ Larry
##SHARELINKS##
|
TAPPI News
Three world-renown course instructors are coming together April 30 for "Essentials of Market Pulp" before the Papercon 2011 convention to address the questions they encounter in their fields.
"In seminars and my interactions with paper mills, I've found considerable interest in all species of softwoods and for what each is best suited. Acacia, both Acacia Mangium and Acacia Cassacarpa, and cold-weather-resistant Eucalyptus (E.Nitens, E.Dunii) have gained particular attention. In this course, we will discuss these pulp selections, as well as species for specific use, such as Black Spruce, for example, found to be best suited for premium facial tissue; Douglas Fir for towelling; and White Spruce for fast response to refining."
- Dave Hillman, Course Instructor and Pulp Expert
View the Proposed Course Schedule to see the day's curriculum. You will learn how to:
- Demonstrate knowledge of a comprehensive overview of the global market pulp industry, pulp categories, supply and demand influences, regional pulps and trends in the market
- Describe how market pulps have transitioned over time, exhibit knowledge of the range and differing characteristics of market pulps
- Identify the characteristics of the fiber sources used to make market pulp, the common defects and factors influencing pulp quality
- Strengthen your understanding of pulp testing principles, test methods and pulp/paper relationships
- Understand the range of pulps available, rank them for particular paper applications and describe best practices for maximizing value from market pulps
Register before April 1 and save!
##SHARELINKS##
|
Several paper company members of the SRW committee are interested in forming a Mill Working Group to focus on streamlining roll damage definitions, claims and reporting throughout the industry. Specifically, the Mill Working Group would:
• Define damage classifications (transit wrinkle, edge, water)
• Create a roll handling workbook
• Report damage on a monthly basis (lbs lost per damage type)
• Review reporting and create industry action plans based on findings.
One outcome is that mills could submit data to a confidential TAPPI database so that industry trends and benchmarking on roll damage could be possible. Several mills are already interested. If you are interested or would like more information please contact Scott Springmier. An organizational meeting is planned during TAPPI's 2011 SRW Workshop in Nashville, TN on April 12-13.
##SHARELINKS##
|
Shipping damage is a challenge for most mills. TAPPI's Shipping Receiving and Warehousing Workshop tackles the root causes and brings you up to date with the latest in paper mill logistics. It's not too late to attend this affordable two-day workshop, April 12-13 in Nashville, TN.
Program highlights:
• DDCT (Damaged Defective Car Tracking) Project Update
• Verso Success Story - Claims Reduction
• Warehouse Tutorial: Handling Paper Rolls In Today's Environment
• qMetrixtm Pilot Project Results
• Claims Tutorial
• Membership Special - register for SRW and join TAPPI at a 60% savings!
See the full program.
##SHARELINKS##
|
A successful consultant is generally busy doing ONE thing -- consulting with clients to help them improve their business. The one thing that a consultant is generally NOT doing at the same time is promoting and selling their services to new clients. For independent consultants, it often proves difficult to perform both roles - a service provider and a business development person - at the same time.
There are three effective ways that a consultant like yourself can grow your business in this type of situation:
1. Narrow Your Focus - You can't be 'everything to everybody', so narrow your focus to a core industry segment so that you can be the best in that business area.
2. Talk "Dollars & Sense" - Develop a strong message that communicates a clear value proposition(s) that a prospective client can derive from engaging you as a consultant. Ideally, this 'value proposition' should be monetized in a way that makes sense to a C-Level executive.
3. Be Where Your Customers Are - Clearly identify the best, most cost-effective method(s) for reaching your target client prospects. Find opportunities to put your message 'in front' of your prospective clients, when you can't be there yourself.
At TAPPI, we have created a unique marketing opportunity for our industry consultants -- independent consultants just like you.
The TAPPI Consulting Council (TCC) puts participating consultants 'front and center' with their core audience -- when they are looking for consulting services. This service leverages a small participating fee in order to create an expanded marketing effort that rivals the 'big consulting shops'.
Let TAPPI help you market your services, while you are busy providing those services to your existing customers.
We invite you to learn more about this unique service. Contact Kristi Ledbetter at TAPPI today to get more information about the TCC at (770) 209-7319.
And if you are an independent consultant, be sure to ask for more information about the upcoming TCC Consultant Workshop that will be held in Atlanta, Ga., on April 26.
##SHARELINKS##
TAPPI is offering a two-part webinar series on
Recycled Content Certification on
Wednesday, April 13 and
Wednesday, April 20 - both at 1 p.m. EST. One registration provides your entry into both online presentations where you can learn how to better interpret the standards of recycled content and how you can use it to its best marketing advantage!
Recycled Content has become increasingly meaningful in operations and the need for clarity in certification has become more important. As many of you might have experienced, problems can arise when there's too much room for interpretation, but there are many sets of standards to scrutinize. So, what do you do?
Eric Taub and Andrew Keenan of Verus Carbon Neutral will discuss:
- Making sense of the paper industry's primary standards, the differences between each;
- How to utilize the standards to your specific marketing advantage; and
- Properly defining recycled content for your products.
Pricing -- TAPPI Member Rate $10 TAPPI Non-Member Rate $174
Special Membership Offer
Non-members of TAPPI will become members ($160 toward membership and $14 for access to this webinar).
This webinar has limited capacity. Register now for your online access to this valuable content.
##SHARELINKS##
|
The Pulp and Paper Safety Association (PPSA) will hold its 68th Annual Safety & Health Conference at the Hyatt Regency in San Antonio, Texas, on June 19-22, 2011.
Program highlights:
• Meet and make valuable safety contacts within Forest Products Industry
• Hear first hand from companies like yours with outstanding safety records
• Find out what the latest OSHA activity and direction is
• Learn new accident avoidance techniques
• Learn about new industry specific training programs
• Find out what is on the cutting edge and currently available from safety suppliers
• Learn from both the positive and negative experiences of others in our industry
For more information download the conference program or visit the website.
##SHARELINKS##
|
PaperCon's Sustainability Forum to highlight the latest developments in this rapidly evolving field during this one-day event.
Attend PaperCon's Sustainability Forum and discover the latest developments and trends directly from our industry's sustainability leaders - and learn what the future holds in this rapidly evolving field.
The Sustainability Forum, taking place Wednesday, May 4, 8 a.m. to 5 p.m. will:
Focus on the "Science Behind Sustainability" - providing a venue for technically based discussions on sustainability and reviewing the basics of sustainability grounded in science - from providing definitions and interpretations of existing/proposed standards and certifications, to sharing best practices, impacts and assessment of sustainability drivers.
Share Knowledge Among Paper Manufacturers and Their Customers - and created a technically-focused learning environment for the paper/packaging industry and its suppliers - and bring togehter end users, technical marketers, paper merchants and buyers to enhance their knowledge about paper sustainability.
Share and Leverage Best Practices and Lessons Learned - enhancing overall industry advancement in sustainability by sharing experiences and initiatives with product development, manufacturing improvements and customer relations.
Bring Industry Issues to the Forefront - providing a forum to gather industry opinions and develop industry consensus (as appropriate) on sustainability issues and drivers to enhance the industry's performance.
Learn more about the Sustainability Forum and PaperCon, taking place May 1-4, 2011 in Covington, Ky., (Greater Cincinnati area).
##SHARELINKS##
|
TAPPI's OpEx Maintenance Seminar: Operating Excellence through Advanced Asset Management is an important two-day seminar, taking place May 2-3 during PaperCon 2011. It is designed for mill maintenance and reliability supervisors who are interested in bringing the latest reliability techniques and best practices back to their mill. Organized by TAPPI's Asset Management Committee, speakers include mill personnel, consultants and suppliers.
Attendees will bring practical ideas back to their mill; meet and network with world class asset management experts and suppliers; and attend a roundtable of maintenance superintendants from TAPPI's Ohio Local Section. Up-to-date program information is available.
Learn more about this event and all PaperCon has to offer.
##SHARELINKS##
|
PaperCon's one-day Tissue Forum on May 3 will give you a perspective on business and market trends through peer-reviewed papers on the latest technical innovations, and safety and reliability best practices for yankee dryers. Highlights include...
Tissue Market Overview
State of the Tissue Industry-2011 and Onwards with speakers from Poyry Management Consulting USA, Inc., Procter & Gamble, and Kimberly-Clark
Modeling and Simulation of the Crepeing Process
Paper Towel Absorptive Properties
New Polymers for Wet Strength-An Academic Perspective
Yankee Dryer Safety and Reliability-Panel Discussion
TAPPI Subcommittees address steam and condensate systems, air systems, cast iron dryer maintenance and inspections, and reducing chatter.
Tissue Forming Systems-Panel Discussion
Consistency Measurement and Control in a Tissue Mill–The Often-Neglected Parameter
Modeling of Crescent Former Dewatering
Learn more about PaperCon, May 1-4, 2011 in Covington, Kentucky (Greater Cincinnati area) and the one-day Tissue Forum.
##SHARELINKS##
"What appears to be a sloppy or meaningless use of words may well be a completely correct use of words to convey sloppy or meaningless ideas."
-- An anonymous diplomat, quoted by Sir Ernest Gowers in "The Complete Plain Words"
##SHARELINKS##
|
|