Over the Wire
TAPPI
Weekly Spotlight
Domtar Corp., Montreal, Que., Canada, is extending its PAPERbecause campaign with a series of new print ads that show why paper still plays a vital role in everything from today's business meetings to educating tomorrow's business leaders. The print ads will begin this month in leading paper, graphic design, and printing trade publications.
The campaign will expand in the first quarter to include prominent consumer publications such as Fast Company, National Geographic, and The New York Times. The print campaign shows how using paper responsibly makes sense in our homes and professional lives, and how it's also an environmentally sound choice. The print ads will join a series of videos and banner ads appearing on a variety of websites.
"The PAPERbecause print campaign gives Domtar a platform to show how paper, a sustainable, renewable, and recyclable product, fits so nicely into our lives," said Lewis Fix, VP of Sustainable Business and Brand Management at Domtar. "Domtar is a leader in sustainable paper production, and we promote the responsible use of paper. PAPERbecause reminds people of why paper is so vital today."
Since Domtar unveiled the PAPERbecause campaign last year, there has been substantial support from paper industry, printing, graphic design, and marketing partners. Many have picked up elements of the campaign and provided significant exposure on websites, in catalogs, at conferences, and other outlets.
"PAPERbecause demonstrates that paper is sustainable, personal, and purposeful. It's easier to learn on paper, senior executives prefer print versus online information, people make purchases as a result of direct mail, and paper is one of the most recycled products on the planet—more than 63% of paper gets recycled," noted Fix. "That's a pretty exciting story about a product that has been in use for more than 2,000 years."
##SHARELINKS##
|
If you prefer to read from paper instead of an electronic screen, you're not alone. According to a recent survey commissioned by Two Sides, an international non-profit organization created to promote the responsible production, use, and sustainability of print and paper, 70% of Americans, including 69% of 18- to 24-year-olds, say they prefer to read print and paper communications than reading off a screen.
Two Sides commissioned Ipsos, a global market research company, to conduct the multi-country survey in September 2011. U.S. results included 500 respondents classified by age and gender.
Most of those surveyed also believe that paper records are more sustainable than electronic record storage (68%) and that paper is more pleasant to handle and touch than other media (67%). But survey results also show that many Americans still have misconceptions about the environmental impacts of print and paper.
"Even though most Americans still prefer print over electronic communications, they also have misconceptions about the effects of paper-based communications on the environment," says Two Sides President Phil Riebel. "In fact, print and paper have a great environmental story to tell, and Two Sides is committed to setting the record straight using factual information from well-known, credible sources."
The Two Sides survey indicates a majority of respondents are concerned about the effect of print and paper production on forests and believe that there is a connection between the loss of tropical rainforests and the manufacture of paper, but data from a variety of sources show these beliefs to be unfounded.
"Authoritative sources like the U.S. Forest Service, the United Nations Food and Agriculture Organization, and others report that the amount of forestland in the U.S. has remained nearly the same over the last century at about 750 million acres, and the major cause of global deforestation is not papermaking, but the conversion of tropical rainforests to agricultural land," Riebel says.
While 96% of survey respondents said they believe recyclability is a sign of environmentally responsible products, most significantly underestimated the amount of U.S. paper that's actually recycled each year. "Most people think the U.S. paper recycling rate is between 20% and 40%," Riebel explains, "but American Forest and Paper Association data show that more than 63% of all paper used in the U.S. in 2010 was recycled. According to the U.S. Environmental Protection Agency, that's more than any other commodity, including plastics, glass, and metals. The industry has set a goal to exceed 70% of all paper recovered for recycling by 2020."
The survey also found that more than half of the respondents believe that electronic communications are a more environmentally friendly way to read books, magazines, and mail. "That's another myth that has been perpetuated by financial institutions, utilities, and other organizations that are trying to save money by encouraging consumers to go green by going paperless," Riebel says. "The fact is that both electronic and paper-based communications have an environmental footprint, and making both smaller is the right environmental choice."
Earlier this month, Two Sides launched its U.S. website, as a resource for consumers, the media, and others who are looking for a trustworthy resource for factual information on the environmental sustainability of print and paper. The website offers a "myths and facts" section that dispels many of the common misconceptions about the medium's environmental impacts, including citations from authoritative sources with links to original source documents.
For more information about Two Sides, please contact Phil Riebel at 1-855-896-7433 or pnr@twosides.info, or visit the Two Sides website.
##SHARELINKS##
|
Sustainability, carbon footprint, and green initiatives are among the hottest topics in the tissue business today. Customers and consumers, retailers and distributors, governments and NGOs, buyers, and sellers are all focusing more attention on this area. And many industry-leading tissue companies are putting enormous efforts into improving all aspects of the sustainability profile of their products and processes, both now and for the future.
To examine these questions and issues in detail, the Tissue World Americas Conference, March 20 - 23 in Miami Beach, Fla., USA, has assembled a world-class panel of speakers for in-depth group discussions. The panel includes, among others:
- Kimberly-Clark
- Greenpeace
- SCA North America
- FSC – Forest Stewardship Council
- Cascades Tissue
- EcoLogo.
The panel discussion is part of an extensive conference program for Tissue World Americas, the most complete event for the North and South American tissue business. In addition to the panel, the four-days of meeting sessions include some 40 other experts presenting information and solutions covering:
- Market sessions on the supply/demand outlook for tissue markets in the Americas
- Fiber supply outlook for tissue making
- Technical sessions covering all aspects of tissue making
- Yankee Dryer Summit on safety, operational, and reliability issues.
The Yankee Dryer Summit, organized by Tissue World and TAPPI, is planned for Tuesday, March 20. It will share practical and non-commercial solutions to common issues that relate directly to the bottom line. Summit organizers note that one applied idea from the yankee sessions will pay for the conference many times over.
TAPPI has also scheduled its bi-annual Yankee Dryer Safety and Reliabilitry Committee meeting for Monday, March 19, at the convention center, courtesy of Tissue World. Committee members and guests in town for Tissue World are welcome to attend. To ensure that you are part of this "must attend" tissue industry event, conference organizers strongly encourage registration today. Attendance at the tradeshow of vendors is free of charge, while attendance at the conference meeting sessions is subject to a registration fee. To get the cheaper "early bird" conference registration fee, sign-up online today.
##SHARELINKS##
|
Co-produced with Biofuels Digest, TAPPI's 2012 Renewable Chemicals Live conference will be held at the Capital Hilton Hotel in Washington, D.C., USA, April 2 - 5. This year, Renewable Chemicals Live has been co-located with The Advanced Biofuels Leadership Conference (ABLC) and has up to four days of "can't miss content." To get the most for their time and money, attendees are encouraged to participate in both events.
Day 1 of the Renewable Chemicals Live conference features the top leadership in renewable chemicals, plastics, and bio-based materials. The program features C-level presentations on finance, scale-up, R&D, policy, and global trends. More information about the Day 1 program is available online.
Conducted on Day 2, the Forest Biorefinery Workshop is intended for forest industry and non-forest industry professionals involved in or impacted by the emerging bio-economy, and who seek to understand better the perspective and priorities of the emerging forest industry commitment to the biorefinery. Executive management, including especially strategy planners as well as product development/technical experts in the bioenergy and renewable chemicals sectors, will be particularly interested in this course. More information about the workshop is available online.
Organized by Biofuels Digest, ABLC is the biggest gathering of advanced biofuels CEOs and senior leadership in North America. More than 40 CEOs will give presentations, including 15 of the 20 hottest companies in bioenergy. More information about the ABLC is also available online.
Professionals in the renewable chemicals and biofuels industries should attend these co-located events to help attract financing for a project, develop partners for feedstock, processing technology, and off take, and develop strategic partners and investors. The events are designed to assist attendees in finding new customers and networking with senior policymakers, as well as assessing the latest trends in advanced biofuels and benchmarking against the competition.
##SHARELINKS##
|
Mercer International Inc., New York, N.Y., USA, has announced a new project (Project Blue Mill) to increase production and efficiency through debottlenecking initiatives, including the installation of an additional 40 MW steam turbine at its Stendal, Germany, mill. The debottlenecking which, among other things, requires the new turbine to enhance and efficiently utilize steam production, is designed to increase the mill's annual pulp production capacity by 30,000 a.d. metric tpy to approximately 675,000 a.d. metric tpy. The new turbine is also expected to initially produce an additional 109,000 MWh of surplus renewable energy for sale at premium pricing.
"We are very pleased with this project," said Jimmy Lee, president and CEO. "The project allows us to maximize value from the wood that we process at Stendal, increase production and efficiency, provide a backup generator on the first turbine, reduce energy costs during maintenance periods, and expand power generation. We currently expect the project, in addition to enhancing mill operating results, to deliver approximately EUR 7.5 million ($9.8 million) of additional annual power revenues."
Lee added that "the project is in line with our group's overall focus on enhancing revenues from the production of green energy and other by-products at all of our mills. We believe that our generation and sale of surplus renewable energy and by-products give Mercer a competitive energy advantage over less efficient mills and provide us with a stable revenue source unrelated to pulp pricing. Based on our overall 2011 production and sales, after giving effect to Project Blue Mill, on a consolidated basis, we currently expect Mercer will produce about 760,000 MWh of annual surplus renewable green energy and generate approximately EUR 65.5 million ($84.5 million) of associated revenues there-from. Since our energy production is a by-product of our pulp production process, there are minimal incremental costs and our surplus energy sales are highly profitable."
Project Blue Mill will require approximately EUR 40.0 million in capital expenditures over about 21 months. The project is eligible for EUR 12.0 million of non-refundable German government grants and the Stendal mill has secured a new EUR 17.0 million, five-year amortizing secured term debt facility, of which 80% will be government guaranteed. The facility is non-recourse to Mercer. The balance of the project will be funded through operating cash flow of the Stendal mill and up to an aggregate of EUR 8.0 million in pro-rata shareholder loans from Mercer and its minority partner. Project Blue Mill is currently designed to be completed and start to generate power revenues in or about September 2013.
The Stendal mill is a state-of-the-art, single-line NBSK pulp mill with a current annual pulp production capacity of approximately 645,000 a.d. metric tons.
##SHARELINKS##
|
Sappi Fine Paper North America, Boston, Mass., USA, this week released the sixth episode in its humorous online video series, Flo Channel: Off Register™. The latest episode, "Paper Claim," makes fun of the laborious process of filling out a paper claim. Off Register is based on real-life experiences of printers and captures some of the funnier, more absurd aspects of being on press, which many people involved in the print process can relate to or find entertaining.
In "Paper Claim," actors from Second City Improv deliver another hilarious episode, as they labor over the seemingly endless list of questions that come from an actual paper claim. "Sappi realizes that no one enjoys filling out a paper claim, so we figured, why not poke fun at the undertaking," says Patti Groh, director, Marketing Communications, Sappi Fine Paper North America. "The Off Register series continues to be a hit among our customers and we're planning to build on this energy with more episodes planned for the future."
Sappi's Off Register not only shares hilarious stories of printing, it also invites the public to share in the fun. The series celebrates the quirks of print production, the personalities people must contend with in the process, and the desire to produce good work despite uncontrollable variables. Sappi continues to invite printers to share their own "war stories" for future episodes. Story ideas can also be submitted online.
##SHARELINKS##
|
A new report from Dovetail Partners, a Minneapolis, Minn., USA-based non-profit, examines the carbon cycle and the storage of carbon. This report starts from square one in understanding the building blocks of carbon science and the policy impacts.
Carbon is a basic chemical component of all living organisms and many non-living substances. Carbon exists in plants, soils, the air, people, buildings, and many other things.
The places where carbon is stored are called "carbon pools." The largest such pools are the oceans, the land and vegetation, and the atmosphere. When a pool gains more carbon than it loses over a period of time, it is called a "carbon sink." Carbon is continually cycled between various "carbon pools" and "carbon sinks."
"When it comes to understanding the problem posed by fossil-fuels, what it boils down to is that for millions of years fossil carbon was captured and stored in the earth, and today there is no natural mechanism for either capturing the full amount of carbon released through its burning, or for restoring that carbon to the carbon pool where it originated. The net effect is an increase in greenhouse gases in the atmosphere," Dr. Jim Bowyer, lead author on the report, explains.
Forests, on the other hand, both emit and absorb carbon in a two-way flow. Biogenic carbon is captured and stored in plants, trees, soils, and other renewable materials. This natural carbon cycle is ongoing, balanced, and a result of the fundamental principles of renewable materials.
"The carbon storage and re-capture differences between renewable and non-renewable materials are dramatic. These differences are sometimes overlooked or discounted in discussions of environmental policy," reports Bowyer.
More information is available online, as is access to the full report.
##SHARELINKS##
|
James W. Johnston and Cornel Hagiopol, Ph. D., two Georgia-Pacific Chemicals (Atlanta, Ga., USA) employees, have recently authored a comprehensive review of the papermaking process. Written from the chemist's perspective, The Chemistry of Modern Papermaking is intended to supply researchers, developers, and end-users with updated information on the literature of papermaking chemistry.
Supported by more than 3,000 references of patents and scientific articles covering 150 years of published literature and enhanced by the authors' industrial experience, the book encompasses and covers the state of science for all facets of papermaking chemistry including retention aids, temporary and permanent wet-strength agents, dry strength resins, internal sizing chemicals, creping additives, and softeners.
"Georgia-Pacific Chemicals supported the development of this book as a resource for industry, as well as academia," said Robert McDonald, paper chemicals business manager for GP Chemicals. "It illustrates the depth of knowledge and resources available at GP Chemicals and we are proud of the years of extensive work Jim and Cornel put into its preparation."
Johnston, paper chemicals research and development manager at GP Chemicals, guides technology development strategy and execution and manages intellectual property as well as product and project resources. He is a graduate of Syracuse University and SUNY ESF Chemical Engineering and Paper Science and Engineering Program.
Hagiopol, a research scientist, received his PhD in macromolecular chemistry from Polytechnic University in Romania and is an expert in polymer chemistry. He holds more than 20 patents.
More information on The Chemistry of Modern Papermaking is available online.
##SHARELINKS##
|
Market Roundup
Earlier this month, Deutsche Bank surveyed North American paper and packaging executives regarding their outlook for 2012, receiving 125 responses. According to senior analyst Mark Wilde, these responses provide clues regarding trade expectations for prices, costs, volumes, capital spending and profitability in 2012. Once again, participants were asked "what is Wall Street Missing?" as well as opinions regarding the "best managed" companies in the industry. Packaging Corp. of America took the top spot in the survey for the fourth straight year, Wilde reports. However, this year, they shared the top spot with RockTenn, he adds.
Modest Volume Expectations in 2012
The expected range for box volumes is flat to up 2% y/y, Wilde says. The outlook for market pulp is more cautious, with most respondents expecting volumes to be flat y/y. In the paperboard grades, the general expectation appears to be for volumes to be flat to up 1% y/y. "As we would have expected, printing and writing grades are expected to remain weak. In fact, a number of participants indicated that the accelerated decline in demand for these papers is a big concern," Wilde notes.
Expectation for Rising Costs
Most expect input costs (with the exception of natural gas) to increase from current levels, Wilde continues. The trade appears relatively optimistic about prices for wood products and paperboard grades. There was no clear message regarding market pulp and kraft paper prices, with nearly the same number of participants predicting increases, as decreases. "Given the pessimism about printing and writing volumes, it is not surprising that most respondents believe that newsprint, uncoated free sheet, and coated paper prices will decline," Wilde points out.
Digging Deeper on Containerboard and Boxes
Expectations for box demand in December and January were on average in the +1 - 2% y/y range, with January anticipated to be a bit better than December. Demand is still considered the "most important" driver of containerboard and box prices. The U.S. dollar and exports ranked lowest in importance this year. "Looking at the year ahead, 44% of our respondents believe containerboard and box prices will rise in 2012. Among our coverage, this would be most positive for RockTenn, International Paper, Packaging Corp., and KapStone. Boise also has exposure to containerboard," Wilde explains.
##SHARELINKS##
|
North American softwood pulp markets remain weak and prices slipped $20/metric ton m/m in January, Wilde reports. Hardwood markets appear to be close to a bottom—prices were flat m/m in January. U.S. NBSK (northern bleached softwood kraft) fell $20/metric ton to $870/metric ton in January. Spot prices at $600 - $650/metric ton (-$25/metric ton m/m in January) remain well below list price levels. At current spot levels, prices appear to be at/below mill cash-cost levels.
"This is apt to be among the issues behind news that the 350,000 metric tpy Terrace Bay, Ont., Canada, mill won't be restarting as planned," Wilde says. Other key issues, he adds, include: (1) sluggish pulp demand in Europe (No. 1 global market), (2) soft paper demand in developed countries, and (3) higher inventories. The fluff pulp market is also weak with prices down ˜$35/metric ton m/m in January.
##SHARELINKS##
|
U.S. uncoated free sheet (UFS) demand is a bit soft and prices remain under pressure, Wilde says. According to PPPC, he reports, preliminary December shipments were -4.7% y/y (2011 -3.2% y/y). The December operating rate was 83% (2011 = 88%). December 20-lb repro bond estimated prices fell $10/ton m/m to $1,055 - $1,105/ton, -1.4% y/y. Current prices are ˜$30/ton below August levels.
"While 50-lb estimated offset prices were flat at $920 - $940/ton in December, reports suggest that transaction prices are still under pressure. Producers continue to reduce capacity. Wausau recently announced the permanent closure of its 173,000 tpy non-integrated UFS mill in Brokaw, Wis.," Wilde says.
##SHARELINKS##
|
Uncoated mechanical (UM) demand remains weak and prices are also under pressure, Wilde continues. According to PPPC, he notes, preliminary December shipments were -19.6% y/y (November -14.6% y/y and 2011 -9.9% y/y).
Producers have been shuttering capacity, including Newpage's 360,000 tpy PM 2 at Port Hawkesbury, N.S., Canada, and Verso Paper's 103,000 tpy unit at Sartell, Minn., USA. Port Hawkesbury's new owner, Stern Partners, recently hinted that production could resume by late-Spring. December 35-lb estimated offset prices fell $5/ton to $680 - $710/ton and SC-A fell $23/ton to $820 - $860/ton, according to Wilde.
##SHARELINKS##
|
Total printing and writing (P&W) paper shipments decreased 7% in December compared with December 2010, according to AF&PA's (Washington, D.C., USA) December 2011 Printing-Writing Paper Report released this week. All four major P&W paper grades posted decreases compared with last December.
U.S. purchases (shipments + imports – exports) of P&W papers decreased 5% in December. Total P&W paper inventory levels increased 6% compared with November 2011.
Some points of interest from the report include:
- Exports of uncoated free sheet (UFS) increased year-over-year for the fourth time in the past six months
- Shipments of coated free sheet (CFS) decreased year-over-year for the thirteenth consecutive month, following 13 consecutive months of year-over-year increases
- Coated mechanical (CM) shipments decreased for the ninth consecutive month
- Uncoated mechanical (UM) shipments decreased year-over-year for the ninth consecutive month, following 15 consecutive months of year-over-year increases.
##SHARELINKS##
|
Wood chip exports from Latin America are on track to reach a record high of almost eight million tons in 2011, reports the Wood Resource Quarterly ( WRQ), Seattle, Wash., USA. This would be an increase of 7% from last year and of almost 60% higher than in 2006. Chile is by far the biggest exporter, accounting for two-thirds of the total shipments from the continent, while Brazil and Uruguay both account for about 16% each. In 2011, Chile was the world's second largest supplier of hardwood chips after Vietnam. Latin America's hardwood chip export volumes accounted for approximately 50% of globally traded wood chips, a share that has grown from 34% five years ago.
Historically, between 80% and 90% of the exported wood chips from Latin America have been destined for Japanese pulp mills, but there has been a diversification of consumers over the past few years. Although shipments to Japan have gone up by more than 30% from 2006, the share of total exports has declined and is currently around 70%.
The biggest change from five years ago is that pulp mills in Europe have been buying much higher volumes of eucalyptus chips, particularly from Chile and Uruguay. In 2011, total shipments to Europe reached almost 1.7 million metric tons, which was slightly lower than 2010 but more than a doubling from 2009, according to the WRQ.
The three major importing countries in Europe are Spain, Portugal, and Norway. In addition, there also have been a few shipments to Finnish and Swedish pulp mills during the past few years.
New destinations for Eucalyptus chips from Latin America during the past five years include Morocco, Turkey, and China. There are expectations that Chile will increase its shipments to China in the coming years because of higher demand from new pulp mills in the country.
##SHARELINKS##
|
Pulp & Paper
Catalyst Paper Corp., Richmond, B.C., Canada, reported this week that, in accordance with an interim order from the British Columbia Superior Court, a hearing is scheduled to be held on February 3 in regard to its previously announced recapitalization transaction. Also in February, full details of the recapitalization agreement and the transaction will be provided in a management information circular to be distributed to shareholders, holders of its 11% senior secured notes due 2016, and holders of its 7 3/8% senior notes due 2014.
Implementation of the plan of arrangement under the CBCA is subject to approval by not less than 66⅔% of the votes cast by holders of each of the senior secured notes and the senior notes at meetings to be held to consider the arrangement, the approval of the Supreme Court of British Columbia, and receipt of all necessary regulatory and stock exchange approvals. In addition, the agreement is subject to termination if a new labor agreement with all union locals at the company's Canadian mills has not been ratified by January 31.
Copies of the court documents are available on SEDAR, EDGAR, and the company's web page. Investors who have questions about the recapitalization may contact Nancy Turner of Perella Weinberg Partners, the financial advisor for Catalyst Paper, at 415-671-4550.
Catalyst Paper produces specialty mechanical printing papers, newsprint, and pulp at four mills in British Columbia and Arizona. The company has a combined annual production capacity of 1.9 million metric tons.
##SHARELINKS##
|
AbitibiBowater, doing business as Resolute Forest Products, Montreal, Que., Canada, has extended to February 13 the expiry date for its offer to acquire all of the issued and outstanding common shares of Fibrek Inc. The extension will allow the Canadian Competition Bureau to complete its review of the proposed acquisition following its request for supplementary information and the Bureau de révision et décision (Québec) to hear Resolute's application for an order to cease trade the Fibrek shareholder rights plan (the "tactical poison pill").
"A supplementary information request is a normal part of the regulatory process," said Richard Garneau, president and CEO. "We will continue to work with the Canadian competition authority and provide it with the responsive information. We're pleased to see that more than 57% of Fibrek shares have been tendered as of January 20. The success of our bid should be up to shareholders, unimpeded by management entrenchment maneuvers like the tactical poison pill."
According to Resolute, Fibrek shareholders should consider the following factors in making their decision to accept the offer:
- The offer represents a substantial premium to Fibrek's pre-announcement trading price
- The offer is not subject to any financing condition
- Fibrek shareholders have the opportunity to exchange their shares of Fibrek, which had been thinly traded through to the date the offer was announced
- Resolute is uniquely positioned to integrate Fibrek into its existing operations
- Fibrek shareholders who become Resolute shareholders will own shares in a company that:
- is financially stronger
- has a diversified asset and product base
- is determined to continue improving the competitive position of its mills by focusing on cost optimization
- maintains a prudent capital structure, with a ratio of long-term debt to the past 12 months adjusted EBITDA of 1.3x as of the end of the third quarter of 2011.
The offer, which Resolute is making together with RFP Acquisition Inc., a wholly-owned subsidiary, is more fully described in the offer circular and other ancillary documentation the company filed this past December 15, on the Canadian Securities Administrators' SEDAR website, as amended by notice of variation on January 9 and on January 20.
The offer will expire at 5:00 p.m. EST on February 13, unless it is extended or withdrawn by Resolute. As of the close of market on January 20, approximately 74.25 million common shares of Fibrek had been tendered to the offer, representing approximately 57.1% of the outstanding common shares.
##SHARELINKS##
|
U.K.-based DS Smith Paper Ltd has ordered from ABB, Zurich, Switzerland, an extensive automation upgrade at its Kemsley Mill in Sittingbourne, Kent, England. The new systems will help the mill produce a greater diversity of high quality paper products.
The order includes an upgrade of the mill's PM 3 automation and drives systems, including a new quality control system (QCS), upgraded and expanded distributed control system (DCS), and upgraded and expanded drive system, as well as a new Web Imaging Solution (WIS). All of the systems will be integrated with the existing System 800xA.
The mill's Advant QCS will be upgraded to an 800xA with two new Network Platforms and an Air Water Spray. The drives upgrade includes new ACS800 drives and AC800M controllers. One of the existing DCS Advant controllers will be upgraded to an AC800M and integrated into the system.
The new QCS will help improve product quality on PM 3, while it increases production and reduces costs. ABB's System 800xA DCS will provide a solid platform for the mill's integrated process operation. The upgraded ABB drives will deliver fast startups and benefits over the equipment lifecycle that include increased productivity, improved quality, and energy savings, while the new WIS (see photo below) will give the mill a state-of-the-art tool for identifying web defects and managing visual uniformity.
The Kemsley Mill is rebuilding PM 3 to produce highest quality linerboard and white-top liner grades. The new systems will be ready for startup in June 2012.
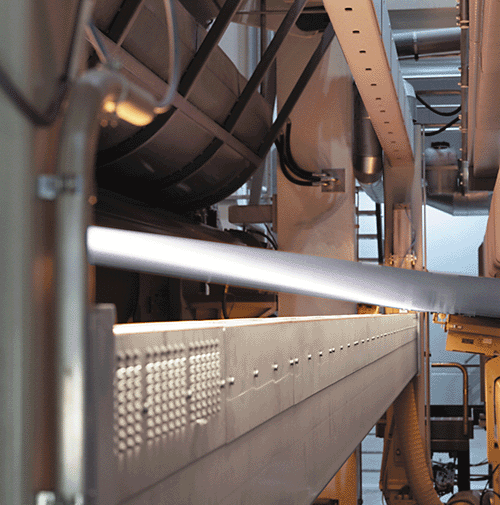
##SHARELINKS##
|
Nippon Paper Group, Japan, reports that it will shutdown production facilities at its Iwakuni Mill (Japan) of Nippon Paper Crecia Co., Ltd., "to cope with severe conditions in the household paper products business." These facilities account for about 15% of Nippon Paper Crecia's entire production capacity. Transferring products produced at the Iwakuni Mill to Kyoto and other mills in Japan will raise the operation ratio of production facilities to 90% or above.
By shutting down production at Iwanuni, Nippon Paper Crecia says it intends to reduce fixed costs and enhance production efficiency, thereby strengthening the competence of its household paper products business. After shutting down the production facilities, the Iwakuni Mill will be converted to a logistics center, aimed at strengthening functions and covering the Chugoku, Shikoku, and Kyushu regions.
##SHARELINKS##
|
Sappi Fine Paper North America, Boston, Mass., USA, this week announced that Rick Dwyer and Mike Haws have been appointed new managing directors of the Cloquet Mill in Cloquet, Minn., and Somerset Mill in Skowhegan, Maine, respectively. As managing directors, each will be responsible for overseeing the safety performance, productivity, and cost management of the integrated pulp and coated fine paper mills.
Sappi also announced the appointment of Mike Schultz as managing director of the previously announced, upcoming $170 million capital project to convert Cloquet's pulp mill from hardwood kraft pulp to produce chemical cellulose, the largest capital investment in Cloquet since the 1990s.
"We are very excited to announce the appointments of Rick Dwyer and Mike Haws as managing directors of our Cloquet and Somerset Mills and Mike Schultz as managing director of the pulp mill conversion," said John Donahue, VP of manufacturing, Sappi Fine Paper North America. "Dwyer, Haws, and Schultz bring an expertise and leadership that is critical to operating our world-class coated fine paper and pulp mills safely and sustainably. Managing a large-scale manufacturing site like Cloquet and Somerset is no easy task. I am confident our mills, under their direction, will maintain the highest standard of performance," Donahue added.
Dwyer brings more than 34 years of paper industry experience to his new role as managing director of the Cloquet Mill. In his new position, he will continue to support the mill on quality and operating improvements. Most recently, he played an important role in the work leading to the Sappi Limited Board's approval of the Cloquet Mill's upcoming capital project on chemical cellulose. Prior to this project, he served as managing director of the Muskegon Mill. Before joining Sappi, Dwyer held positions at International Paper and Fox River Paper.
For the upcoming conversion of Cloquet's pulp mill to chemical cellulose, Dwyer will work closely with Schultz. With more than 20 years of experience at the Cloquet Mill, including his previous roles as managing director and pulp production manager, Schultz brings extensive experience in pulping and project leadership to this initiative.
Haws joins Sappi Fine Paper North America as managing director of the Somerset Mill with more than 26 years of experience in the paper industry. Previously, he served as VP of operations at Verso Paper's Bucksport Mill during which the mill notably improved its safety and paper machine performance. His experience includes serving as manager of operational services at IP's Jay Mill and holding manufacturing roles with Champion International and St. Regis Paper.
Haws' predecessor, Fred Oettinger, will be retiring from Sappi at the end of this month after a 36-year career in the paper industry, of which he spent the past five years running the Somerset pulp and paper mill. Under Oettinger's leadership, the Somerset Mill increased paper machine operational efficiency and successfully rebuilt the wet end of PM 1. He was also responsible for significantly reducing the mill's dependence on oil and rebuilding the recovery boiler, which resulted in significant energy and pulp production improvements.
##SHARELINKS##
|
Containerboard/Packaging
The largest end-user segment of corrugated boxes in North America is the food and beverage industry, accounting for 51% of shipments in 2010. These shipments to the food industry will continue to increase at an average annual rate of 2.4% from 2012 – 2016. The expansions and contractions among 21 end-use markets for corrugated are published in a new study by RISI, Brussels, Belgium, titled U.S. Corrugated Box End-Use Markets: Analysis and Forecast through 2016.
Demand for corrugated boxes traditionally fluctuates with the growth of a wide range of consumer products industries—including both durable and non-durable manufactured goods, the report notes. Thus trends in corrugated shipments can often be explained by general macroeconomic conditions such as changes in real GDP, consumer spending, international trade, and industrial production, factors that affect manufactured goods markets. Following economic trends from 2002 - 2011, corrugated box shipments declined at an average annual rate of 0.6%. However, in 2010 corrugated box shipments rebounded, reflecting the resilience of the broader U.S. economy - increasing 3.6% over 2009 to reach 357 billion sq. ft.—valued at more than $24 billion.
Looking forward, the study finds that retail and packaging trends will play a significant role in determining shipment trends. Opportunities for corrugated in the food and beverage segment will abound as Walmart and other 'big box' retailers remain committed to increasing stocking efficiency and the use of sustainable packaging materials such as corrugated packaging. Corrugated packaging is 100% recyclable, made from renewable resources and is cost-effective to transport and stock produce, meat, and other food products.
Within the food and beverage end-use category, the study finds that beverages, fresh fruit and vegetables, and dairy will see the largest future shipment growth. "This is opening up opportunities for mini-flute corrugated," explains Ken Waghorne, RISI's VP, Paper Packaging, "potentially taking share from markets traditionally dominated by folding cartons."
##SHARELINKS##
|
U.S. containerboard prices have remained stable during the seasonally slower winter months, reports Mark Wilde, senior analyst with Deutsche Bank. At the same time, he adds, domestic demand appears modestly positive.
OCC (old corrugated container) costs have stabilized at a relatively high level and have begun increasing. Fourth quarter export prices were a bit weaker-than-expected, but appear to be bottoming. "Although we're still forecasting a $40 - $45/ton y/y drop in domestic containerboard prices in FY12, recent data points make us a bit more positive on containerboard prices for FY12. If the trend continues, we may need to review our estimates not only for domestic prices not falling, but also for any potential of a price hike attempt," Wilde says
According to data released by AF&PA (Washington, D.C., USA), December production was up 0.8% y/y and the operating rate fell to 93.6% from 96.5% in November.
##SHARELINKS##
|
OCC (old corrugated container) prices appear to have stabilized and are beginning to move higher, Wilde continues, noting that in the past four months, domestic OCC fell $58/ton. January domestic OCC was essentially flat, up $2/ton m/m to $123/ton, he says. Export OCC demand, he adds, has improved in the past two to three weeks and prices are rebounding, up $15 - $20/ton m/m to $170 - $180/ton FAS to China/Asia.
"We view this as positive for containerboard producers as high OCC prices translate into higher global containerboard costs. At the same time, improving OCC demand is typically an indicator of strength in the global containerboard market," Wilde says.
##SHARELINKS##
|
Papier- und Kartonfabrik Varel, Germany, reports that it has started up steam turbine 9, significantly boosting the mill's power generation efficiency. Steam turbine no. 9 has an output of 13.9 MW and substitutes/replaces power generation from steam turbines No. 1 and 2. Both of these turbines were taken out of regular operation, but are still available as reserve capacity.
Main steam to the turbine is at 480°C and 80 bars, exiting at 170°C and 6 bars. Compared with previous installations, energy efficiency has been improved by 25%, which significantly reduces specific carbon dioxide emissions.
The new turbine's weight is 25 metric tons and the generators weigh 45 metric tons. Together with the gear box and auxiliary aggregates, total weight of the unit is approximately 100 metric tons. "Integration of such a complex segment into a running power plant was a major logistical challenge, which our staff of energy division and others involved passed with great success," the company noted.
Papier- und Kartonfabrik Varel produces paper and board from 100% wastepaper and is one of the top producers of paper and board packaging in Europe.
##SHARELINKS##
|
New Products
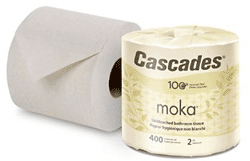 Cascades Tissue Group, Waterford, N.Y., USA, this week launched its Moka™ 100% recycled, unbleached bathroom tissue, a first-of-its-kind product available to the Away-from-Home market in late August. Beige in appearance, Cascades Moka offers commercial purchasers high hygienic qualities and softness while significantly reducing the environmental impact associated with manufacturing a highly common, yet also single-use product. In addition to eliminating chemical whitening, Cascades' value-added tissue product is made of a pulp mix with 100% recycled fiber, 80% of which is post-consumer material and 20% is recovered corrugated boxes. The product is also offset with 100% Green-e certified renewable wind electricity, saving 2,500 lb. of carbon dioxide emissions for each ton produced, Cascades notes.
A detailed life cycle analysis of Moka undertaken by the company revealed a reduction in overall environmental impact of at least 25% compared with Cascades' 100% recycled fiber bathroom tissue, which has been regarded as a highly sustainable tissue but includes a chlorine-free whitening process for aesthetics.
"Beige is the new green, at least as it relates to towel and tissue," said Cascades Tissue Group CEO Suzanne Blanchet, who personally conceived and championed Moka bath tissue's development. "The last several years have brought about countless habit changes meant to preserve the environment. The quality of this bath tissue hasn't been sacrificed one bit, so adjusting to a new color seems like a small step to take for even greater sustainability."
Cascades Tissue Group has 17 mills in North America, including 10 in the U.S.
##SHARELINKS##
|
People
Thomas J. Garland resigned Tuesday of this week as president and CEO of PaperWorks Industries Inc., Philadelphia, Pa., USA. As the company's first fulltime chief executive, Garland provided the company with leadership through its growth phase from shortly after its founding in late 2008 to the present.
The company reports that a search for a new president and CEO has been initiated and it is anticipated that the position will be filled in the next 90 days. In the meantime, Richard LeBlanc will step into the role on an interim basis. LeBlanc is a seasoned executive with almost 30 years of experience in managing and driving strategic, operational, and financial outcomes.
Founded in 2008, PaperWorks Industries is an integrated, full-service packaging provider. The company's Packaging Division produces specialized folding cartons, with facilities in the U.S. and Canada. Its Paperboard Division produces approximately 300,000 tons of 100% recycled paperboard every year for a variety of end uses, largely concentrated in consumer products. The company has nearly 1,700 employees at 17 North American locations and annual sales in excess of $600 million.
##SHARELINKS##
|
Glatfelter, York, Pa., USA, has appointed Michael L. Korniczky VP, general counsel, and corporate secretary, effective immediately. Korniczky most recently served as the chief administrative officer, general counsel, and secretary for Graham Packaging Co., a $2.8 billion global producer of custom blow-molded plastic containers. Previously he served as assistant general counsel at Crown Holdings Inc.
"I am pleased to welcome Michael to our senior executive team and look forward to his contributions as we work to create value for the company and our shareholders," said Dante C. Parrini, chairman and CEO. "His background in providing strategic leadership and direction to global businesses with substantial international operations fits well with our global growth strategies in fiber-based engineered materials."
##SHARELINKS##
|
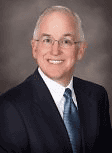 NewPage, Miamisburg, Ohio, USA, announced that James C. Tyrone has accepted the role of EVP, Commercial Operations and Business Development, effective February 1. He will report to George F. Martin, president and CEO.
Effective with Tyrone's return, the Sales and Marketing, Order Management, and Strategy groups will be realigned under his direction. Barry Nelson, SVP, Sales and Marketing, will report directly to Tyrone and retain his current roles and responsibilities, as will Linda McClinchy, VP, Order Management, and Curtis Short, VP, Strategy.
Tyrone was most recently with Appleton Papers, where since 2010 he served as SVP responsible for Appleton's thermal paper business unit and oversight of the company's paper manufacturing operations. He started his paper industry career with The Mead Corp. in 1990, serving in a variety of roles. When Mead and Westvaco merged, Tyrone was SVP of Sales and Marketing, a role he continued when NewPage started in May 2005. Before Mead, he worked for seven years as a senior manager for McKinsey & Co.
NewPage operates paper mills in Kentucky, Maine, Maryland, Michigan, Minnesota, and Wisconsin, with a total annual production capacity of some 3.5 million tons of paper. The company's product portfolio includes coated, specialty, supercalendered, and uncoated papers.
##SHARELINKS##
|
TAPPI News
Leading up to the Sustainability Forum at PaperCon in April, a series of webinars are planned to help manufacturers and customers better understand key issues around sustainability. The first in this series reviews the updated FSC and SFI standards.
A Comparison of the FSC and SFI Forest Certification Standards
January 30, 11:00 am
Facilitated by: Katie Fernholz, Dovetail Partners
Free to attend, but you must register.
The Forest Stewardship Council (FSC) and Sustainable Forestry Initiative (SFI) standards offer two approaches to forest management certification. Both programs recently updated their standards for forest certification auditing in the United States. This webinar will review the FSC and SFI standards and some of their key differences. The information from this discussion will be helpful to land managers that are audited to these standards as well as to manufacturers and customers interested in understanding the requirements behind these eco-labels.
Learn more and make plans to participate.
Additional webinars in the series:
How to deal with misleading environmental claims related to print and paper?
February 27, 2012 at 11:00am EST - Facilitated by: Phil Riebel, President and COO, Two Sides U.S., Inc.
March 12, 2012 at 11:00am EST - Facilitated by: Avrim Lazar, FPAC
PaperCon 2012 will take place April 22-25, 2012 in New Orleans, Louisiana, and will focus on "Growing the Future"; leveraging renewable, recyclable raw materials and developing human capital to ensure value for customers, long-term sustainability for shareholders, and a future for our peers.
##SHARELINKS##
|
TAPPI OpEx Reliability Seminar at PaperCon 2012
Monday and Tuesday, April 23-24
8:30am - 5:00pm
Maintenance and reliability are critical to efficient mill operations - and just behind fiber and labor as top cost factors. Attend the two-day OpEx Reliability Seminar during PaperCon and learn the latest reliability strategies that mills are implementing to stay competitive.
Program topics include:
- Progress in Reliability
- Mill Systems and Equipment Optimization
- Reducing Downtime/Cutting Costs
- Maintenance/Reliability Training · Reliability Panel Discussion
- Fixed Equipment Maintenance Optimization (FEMOS)
Learn more about the OpEx Reliability Seminar.
Learn more about PaperCon
##SHARELINKS##
|
Growing the Division – A Message from the Nanotechnology Division Chairman
Hello fellow nanophiles!
I am excited to be the chairman of TAPPI's new International Nanotechnology Division, and I look forward to sharing with you regular updates on some projects that are in development, as well as exciting new opportunities to get involved and help this Division grow. There are many opportunities to get involved, and member benefits include our E-library, Standards, Event & Education Discounts, access to the Membership Directory, and much more. Visit the Nano website for more information and how to join.
The mission of the International Nanotechnology Division is to serve as the leading global forum for the community of individuals, organizations and institutions seeking to collectively advance the responsible and sustainable production and use of renewable nanomaterials. Please consider getting involved!
Although TAPPI's Nanotechnology Division is new, it is already very active. The Division will take the lead in guiding and overseeing the development of the Roadmap for Nanocellulose Standards. Many of our colleagues have already been hard at work and produced a draft this fall. The Division has created the INSCC (International Nanotechnology Standards Coordination Committee) to formalize this activity. This committee will work on creating proposals for new Standards or test methods that will be submitted to TAPPI, ISO, and other standards development organizations. The Division is also represented in the ISO TC 229 US TAG membership group.
The "Rethink Trees" video, a video created to raise awareness about the opportunity for nanocellulose, has also been completed, and is available for download and distribution. Please visit this website and spread the word about all of the benefits of using nanotechnology.
Planning for the 2012 Conference has also begun. More information can be found at TAPPI Nano website. Please contact Raine Hyde if you are interested in getting more involved with the conference.
Finally, The Division has also created 3 new "teams":
The Technical Team, which will focus on the Annual Conference, Symposiums, and Courses, is being lead by Robert Moon, USDA Forest Service and Yaman Boluk, University of Alberta.
The Marketing & Promotions Team, which will explore Campus Outreach (University Outreach & Student Chapter development), Industry trends (Knowledge needs), Membership (recruitment and retention), and Industry Outreach (collaboration, awareness), is being lead by John Cowie, Agenda 2020 and Professor Bruce Lyne, Royal Institute of Technology And the
Product Resources & Development Team, which will delve into Press & Publications (books, manuals, newsletter, web content), Standards & TIP Development (ISO TC229), and Education (Webinars, other needs), is being lead by Mike Bilodeau, University of Maine and one other co-chair yet to be determined.
Don't forget to visit TAPPI's Nano webiste for more information and how to join.
Until next time,
Sean Ireland
TAPPI International Nanotechnology Division Chairman
##SHARELINKS##
|
Comprehensive Book on Papermaking Chemistry Now Available
James W. Johnston and Cornel Hagiopol, Ph. D., two Georgia-Pacific (GP) Chemicals employees, have recently authored a comprehensive review of the papermaking process. Written from the chemist's perspective, The Chemistry of Modern Papermaking is intended to supply researchers, developers and end-users with updated information on the literature of papermaking chemistry.
Supported by more than 3000 references of patents and scientific articles covering 150 years of published literature and enhanced by the authors' industrial experience, the book encompasses and covers the state of science for all facets of papermaking chemistry including retention aids, temporary and permanent wet-strength agents, dry strength resins, internal sizing chemicals, creping additives and softeners.
"Georgia-Pacific Chemicals supported the development of this book as a resource for industry, as well as academia," said Robert McDonald, paper chemicals business manager for GP Chemicals. "It illustrates the depth of knowledge and resources available at GP Chemicals and we are proud of the years of extensive work Jim and Cornel put into its preparation."
Johnston, paper chemicals research & development manager at GP Chemicals, guides technology development strategy and execution and manages intellectual property as well as product and project resources. He is a graduate of Syracuse University and SUNY ESF Chemical Engineering and Paper Science and Engineering Program.
Hagiopol, a research scientist, received his PhD in macromolecular chemistry from Polytechnic University in Romania and is an expert in polymer chemistry. He holds more than 20 patents.
According to the publisher, CRC Press, a respected publisher of scientific and technical work, "The Chemistry of Modern Papermaking focuses on the chemistry behind each application, on what has been done, and on what can be done." -
To view excerpts of an interview with the authors, please visit the Georgia-Pacific TV channel. For more information on The Chemistry of Modern Papermaking.
The Chemistry of Modern Papermaking is available from TAPPI PRESS.
##SHARELINKS##
|
An Invitation to Present has been announced for TAPPI's 2012 International Bioenergy and Bioproducts Conference (IBBC), October 17-19, 2012 in Savannah, Georgia.
IBBC will focus on technical advancements and commercialization of bioconversion technologies that leverage the forest products manufacturing infrastructure and will include technical presentations, expert panels, case studies, and reports from projects that address:
- Feedstock and harvesting improvements to increase yield and quality of biomass
- Bioelectricity using combined heat and power (CHP)
- Bioconversion technologies for wood and biomass
- Production of chemicals and transportation fuels from wood and biomass
- Policies and incentives for bioconversion projects
Presentations are sought in the following areas:
Advances in Technology: strong technical papers with a focus on presenting new findings
- Biomass Supply & Demand
- Advances in Conversion Pathways
- Biomass Harvesting & Preparation
- Advances in Bioproducts
Commercialization Activities: case studies and updates from pilot scale, commercial, and pre-commercial operations
- Biorefineries
- Repurposing the Traditional Pulp and Paper Mill
- Harvesting and Preparation ·
- Technical Economic Analyses ·
- Commercial Collaborations for Enabling Technologies
- Project Deployment Issues
Impacts of Policies and Incentives: analysis of existing or proposed bioconversion policies at State, Provincial or Federal levels
- Public policy proposals
- Pulp/paper incentives that support bioconversion progress
- Assessing common ground between pulp/paper and agricultural bioconversion policies
Limited space is available for poster presentations.
Abstract Submission Information:
Authors interesting in presenting a paper should upload their abstract to the TAPPI's Speaker Management System .
Abstract Requirements: Abstracts should be no more than 200 words.
Submission Deadline: March 9, 2012
Presentations Deadline: September 17, 2012
Authors will be notified of acceptance by April 20, 2012.
##SHARELINKS##
|
TAPPI Advanced Coating Fundamentals Symposium Abstracts Deadline Extended
Organizers of the 12th TAPPI Advanced Coating Fundamentals Symposium have extended the deadline for abstracts to February 14, 2012. View the call for papers and posters.
This is a forum for academics and technologists to present their fundamental research findings and leading-edge developments related to the coating of paper substrates and the printing and converting of these products.
The symposium, September 10-12, 2012 in Atlanta, Georgia, will be co-located with the 16th International Coating Science and Technology Symposium (September 9-12, 2012), providing attendees and presenters with expanded learning and networking opportunities. Abstracts for full papers or posters will be accepted.
##SHARELINKS##
|
Experts Invited to Participate in Cellulose Nanotechnology Terminology Standard Development
January 19, 2012
An initial draft has been prepared for the first cellulose nanomaterial standard: TAPPI WI 3021: Standard Terms and Their Definition for Cellulose Nanomaterials. This standard shall establish and define standard terms for cellulose nanomaterials, the different types of cellulose nanomaterials and the hierarchical structure of cellulose nanomaterial terms.
If you would like to review and comment on this initial draft, please contact World Nieh at wnieh@fs.fed.us or 703-605-4197. World will provide you with a copy of the draft and a comment review form. All comments are due by January 31, 2012.
Once a formal draft has been prepared, the official balloting process will begin. If you are interested in participating in this process, you will need to join the Standard Spcific Interest Group (SSIG). If you would like to join the Standard Specific Interest Group (SSIG) for this standard, and receive a ballot for voting when it is available, please notify the Standards Department at standards@tappi.org or by fax at +1-770-446-6947 no later than January 31, 2012. Please reference WI 3021 in your communication.
##SHARELINKS##
|
|
|