Over the Wire
TAPPI
Weekly Spotlight
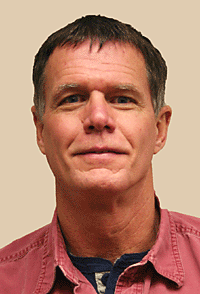 The Papermaking Track at TAPPI's PaperCon 2012 event in New Orleans, La., USA, April 22 -25, features a very special paper industry success story—the company-wide transformation of Longview Fibre Paper and Packaging, Longview, Wash. Focused on the key role that operations training is playing in rebuilding Longview Fibre into a high performance company and an attractive investment for its owners, Bruce Warrick, operations training manager (photo on right), will detail how the mill has completely overhauled operator training from a highly informal, hit-or-miss process to a performance-based, results-driven program.
In the past, training for operations employees at Longview Fibre was done in a very informal manner, by supervisors and co-workers on the job. There were few standards or checklists, and mastery of skills was not a prerequisite for advancement—seniority was the only criteria. The trainer simply told the employee from memory what needed to be done, and the employee was expected to remember what was needed. There was no formal process to establish training timelines, track progress, or demonstrate competencies learned as a result of the training. Now all of that has changed.
The new operations training program launched in April 2010 includes consistent structure and delivery across all departments. The current curriculum consists of 86 unique training plans, each tied to a specific operating position. All employees in a particular job get the same training. The program now supports the company's core values of people, self-improvement, speed to action, and accountability, and is serving as a key lever in the company's effort to change its organizational culture from one of entitlement to one of empowerment and high performance. Operators are becoming more proactive and engaged in their jobs, resulting in improved efficiency and productivity.
Duncan and Peterson's presentation explains how the company selected the team that designed the new training program, and provides detailed insight into how it is structured. The entire program is delivered through a learning management system (LMS) and involves a blend of on-line learning, classroom training, and on-the-job training (OJT). Training plans include objectives, task lists for identification and location of equipment and systems, quizzes requiring a 100% score, references and resources such as manuals, work instructions (SOP), pictures, drawings, and purchased computer based learning modules. The OJT, or hands-on training, requires that the trainee be evaluated with a series of pre-determined, manager-scored field tests as a part of the qualification process. Electronic delivery through the LMS also improves basic computer skills as a side benefit for many of the mill's employees.
The training timeline includes completion of the training material online, field tests to demonstrate ability, progress checks to validate learning and provide teaching opportunities, and a scored qualification board review. Additionally, a standardized process was developed for scheduling and tracking of all trainees, progress checks and board reviews, including documentation and metrics. Each trainee is scheduled for training, receives orientation on training plan use, and is then scheduled for progress checks at set intervals.
Time to qualify depends on the position. Qualification is accomplished through panel interviews called qualification board reviews. A panel of managers asks pre-developed questions of the trainee, using a 0-5 scoring system. A minimum score of 90% is required for qualification. Emphasis is placed not just on how to do things, but on why. Post qualification expectations and follow-up with managers is required and a program for refresher opportunities is currently in the implementation phase.
The approach has proved to be so successful at the paper mill, that Longview Fibre will be rolling it out to the company's container plants this year.
More information about therPapermaking program keynote presentation as well as all program tracts and events at PaperCon 2012 is available online.
##SHARELINKS##
|
The Institute of Paper Chemistry Foundation (IPCF, Atlanta, Ga., USA, awarded prizes this week to three winners of the Georgia Tech Research and Innovation Conference in the forest bioeconomy category. The IPCF's successor, the Institute of Paper Science and Technology, is one of Georgia Tech's 12 strategic theme area research centers.
A $10,000 prize went to Jie Wu, who won the innovation prize in the category for his project, "Highly-Scattering, Nanostructured Optical Coatings for Sustainable Paper and Paperboard Products." The Foundation also awarded $5,000 prizes for poster presentations to Yan Li for "Microstructure-based evaluation of material fracture toughness" and to John Copeland for "Interactions of Biomass Molecules with Heterogeneous Catalysts in Aqueous and Vacuum Environments."
The prizes were selected from among some 400 competition entries, of which a third was submitted in the forest bioeconomy category.
Professor Sujit Banerjee presented the awards on behalf of the Foundation. "The Institute of Paper Chemistry Foundation congratulates all participants in the competition," Dr. Banerjee commented. "I am personally pleased to award these prizes. Congratulations for a job well done."
IPST Associate Director Marko Hakovirta led the introduction of the new forest bioeconomy category in the GTRIC competition and also congratulated the winners.
The Institute of Paper Chemistry Foundation supports the research mission of IPST as well as advancing the Paper Science and Engineering educational program at Georgia Tech.
##SHARELINKS##
|
Domtar Corp., Montreal, Que., Canada, reports that it has collaborated with Hatch Show Print®, Nashville, Tenn., USA., to create a limited edition poster that supports AIGA's "Design for Good" initiative—an effort to recognize and support pro bono social engagement design projects.
The "Good Design Still Matters" poster is part of Domtar's commitment to graphic communications and its "Paper Because" campaign that showcases the importance of paper in our daily lives. "The 'Good Design Still Matters' limited edition poster is a special project for Domtar, because this single printed piece embodies so much of what the 'Paper Because' campaign is all about," said Lewis Fix, VP of Sustainable Business and Brand Management at Domtar. "Domtar had the chance to work directly with Hatch Show Print, a legendary letterpress printer that traces its roots back to 1879, on a project that will help support the efforts of today's graphic design professionals to make the world a better place."
As part of the "Good Design Still Matters" project, Domtar is making a cash donation to the AIGA's "Design for Good" initiative. The company will also distribute copies of the limited edition poster—which is printed on Domtar's Cougar Natural 80 lb. cover stock—to graphic designers attending the HOW Conference in Boston June 21 - 25.
Hatch Show Print is one of the oldest working letterpress shops in the U.S. Throughout its history, the company created iconic posters for vaudeville and circus performers; auto races, boat races and rodeos; and a range of musical acts that include Johnny Cash, Garth Brooks, Elvis, B.B. King, and the Rolling Stones. Hatch Show Print is part of the Country Music Hall of Fame® and Museum. It has thousands of historic pieces of type and woodblock art that it still uses (often on Domtar's Cougar paper) to produce approximately 600 letterpress jobs annually on hand-powered roller presses.
"The Hatch Brothers are quoted as saying that 'Advertising without posters is like fishing without worms'," said Jim Sherraden, manager of Hatch Show Print. "We firmly believe good design is more powerful than ever, and a project like this that brings a printed poster together with a great cause is proof."
"'Design for Good' is more than just pro bono design projects. It is a broader movement to encourage and enable designers to bring their creative problem solving to the assistance of their communities as they approach community and social problems," according to Richard Grefé, executive director of AIGA. "'Design for Good' offers a means for creative professionals to play a central role among concerned citizens, demonstrating their commitment, talent and leadership to power change in ways that are important to others in their communities."
##SHARELINKS##
|
Metsä Tissue, Espoo, Finland, has been awarded a grant of more than EUR 400,000 by the European Commission as part of its Sustainable Industry Low Carbon (SILC) Scheme. Metsä Tissue is participating in the scheme with its Sustainable Low Carbon Tissue Manufacturing Project.
The project's main target is to analyze and develop concepts for the optimization of heat recovery systems at all tissue paper mills operated by Metsä Tissue. The mills will adopt the template successfully established at two German mills in 2009-2010. The project is part of the company's Tissue 20 project, which aims to implement energy-saving actions to achieve a combined saving equal to 20% of the company's 2007-level energy consumption by the end of this year.
Metsä Tissue's project was one of only two projects to pass all of the strict thresholds defined by the European Commission. The Commission confirms that the requirements were extremely strict to assure the quality of the accepted projects.
"This grant enables us to radically speed up the project realization time," says Rudi Staszewski, project manager and energy efficiency coordinator at Metsä Tissue.
"The forthcoming efficiency improvements are important steps mitigating climate change. This grant will give us an extra boost, enabling us to channel more resources into the valuable energy efficiency work being done at Metsä Tissue," confirms Jarkko Kaplin, VP, Purchasing and Energy at Metsä Tissue.
Metsä Tissue will publish project results and will consult other companies and organizations on themes related to energy efficiency. The final report will be published at the end of the project.
##SHARELINKS##
|
The Nonwovens Cooperative Research Center at North Carolina State University, Raleigh, N.C., USA, has announced two upcoming short courses. The first is the Nonwoven Fabric Property Development and Characterization short course, taking place March 12 – 15. This course surveys a broad range of fabric properties, how they are developed in the process, and how they are measured. Most of the common conventional methods are covered with an emphasis on imaging technology and how it can be used to predict fabric behavior.
The second short course is Meltblowing and Spunbonding Fundamentals, April 9 – 13. This course covers polymer requirements, fundamentals of fiber formation, fabric formation, and surveys bonding technologies, A full day is spent in the pilot facility demonstrating responses to the most important process variables.
More information http://www.nonwovensinstitute.com/education.cfm is available online.
##SHARELINKS##
|
Below is the latest listing of job openings in the TAPPI Career Center. The current listing includes a variety of technical specialist and paper mill operations positions, as well as sales representative openings and engineers. Current, specific job openings at companies and locations in the TAPPI Career Center include:
Employer |
Title |
Location |
RockTenn |
Safety Manager |
West Point, Va., Mill |
Filcon America |
Technical Sales Rep |
Southeastern USA |
Metso |
Product Mgr, PM Clothing |
|
GL&V USA |
Field Service Rep, Pulping |
Southwestern U.S. |
Confidential |
Steam Chief - Alberta Newsprint |
Whitecourt, AB |
Lydall Filtration/Separation |
Development Engineer |
Rochester, N.H. |
Rayonier |
Area Manager, Pulp Machine |
Fernandina Beach, Fla. |
Global Paper Industry Supplier |
Product Mgr - Chemical Pulping |
Cincinnati, Oh. |
Global Paper Industry Supplier |
(Senior) Application Engineer |
Cincinnati, Oh. |
Glatfelter |
Enterprise Mfg Applications Mgr |
Spring Grove, Pa./Chillicothe, Oh. |
Cognex |
Paper Industry Sales Engineer |
Near Major U.S. Airport |
Confidential |
Chemical Sales/Support |
Southeast U.S. |
Confidential |
Specialty Chemical Sales Agent |
Western Canada |
Burrows Paper Corp. |
Operations Specialist III |
Pickens, Miss. |
Burrows Paper Corp. |
Quality Manager |
Lyonsdale/Pickens, Miss. |
More information about these jobs is available online.
##SHARELINKS##
|
Market Roundup
Referring to it as the possible build-up of a "pulp tidal wave," Mark Wilde, senior analyst with Deutsche Bank, points to two recently announced chemical pulp expansion projects—Aauco's plans to build a new 1.3 million metric tpy pulp mill in southern Chile with a late-2015 startup, and Asia Pulp & Paper's reported plans to build the world's largest pulp line (2 million metric tpy) in South Sumatra with a 2017 startup. Several new pulp mills, he adds, are planned for Latin America during the next three years.
##SHARELINKS##
|
In the global wastepaper arena, "China is back in the game," Wilde says, noting that The Official Board Market reports that Chinese buyers have returned to the wastepaper markets and are triggering a rebound in prices. Old corrugated container (OCC) prices are up $10 - $15/ton in early February, he says, pointing out that recycled paperboard mills could be facing margin pressures by the second quarter of this year.
##SHARELINKS##
|
"It was great while it lasted," Wilde says about the two-year run-up in North American kraft paper prices that he says is now over. Kraft paper markets have weakened and prices are falling, he notes, pointing out that January prices fell $20 - $30/ton in extensible and bag grades.
"With December prices falling ˜$30/ton m/m, producers appear to have given up the October price increase of $50 - $60/ton. In the natural multiwall grade, January estimated prices slipped $10/ton to $1,010 - $1,020/ton. The key issue is weakness in Europe and its ripple effect on domestic supply/demand balance," Wilde says.
##SHARELINKS##
|
North American newsprint prices are stable, but demand remains weak, Wilde reports, adding that 30-lb East Coast newsprint estimated prices were flat at $640/metric ton in January. While demand is weak from a cyclical standpoint, secular pressures remain intense. According to the Newspaper Association of America, estimated U.S. newsprint consumption fell 21.5% y/y in December (2011 -17% y/y), he explains.
Wilde notes that White Birch has permanently closed its 550,000 metric tpy Stadacona newsprint mill in Quebec City, Que., Canada, after failing to reach a labor agreement with the union members. On the west coast, Catalyst Paper is in the midst of a financial restructuring.
##SHARELINKS##
|
Pulp & Paper
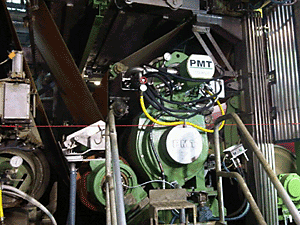 Cartiera del Chiese S.p.A, Italy, this past week reported to have started up a PMT Italia (Pinerolo, Italy) Smartnip shoe press at its Montichiari Mill in Italy. The shoe press was selected to optimize the production of smooth and semi-extensible sack kraft paper, with the goal of increasing production and improving quality. Also, in this specific mill application, the modularity and compactness of the Smartnip press was a key factor in using this kind of technology in the press section rebuild, while improving geometry of the first dryer group.
The paper machine was restarted with the Smartnip on January 16 and is currently in its optimization phase. PMT notes that, due to its flexibility, the Smartnip will achieve the right balance among dry content after press, density, porosity, and other typical sack kraft peculiarities.
##SHARELINKS##
|
Corner Brook Pulp and Paper, Corner Brook, Newfoundland and Labrador, a mill owned by Montreal, Que., Canada-based Kruger Inc, reports that it has started implementing a previously announced rightsizing plan as part of the company's strategy to improve its competitiveness. This past week, the company met with union executives to announce the immediate layoff of nine employees, as well as a gradual reduction of 33 additional positions and four vacancies that will not be filled.
This announcement is the first step in an ongoing process to reduce labor costs. For the mill to survive and be competitive, the company says, it must rank within the first quartile of the industry. To achieve this goal, it must reduce its workforce accordingly. Therefore, the company notes that it will reassess its manning needs in the coming weeks and months to make further labor force adjustments.
The company says it will make every effort to minimize the impact of its rightsizing process on employees and their families.
Founded in 1904, Kruger produces publication papers, tissue, lumber, and other wood products, corrugated cartons, green and renewable energy, and wines and spirits. In Canada, the company operates facilities in Quebec, Ontario, British Columbia, and Newfoundland and Labrador. It also has facilities in the U.S.
##SHARELINKS##
|
Georgia-Pacific, Atlanta, Ga., USA, has accepted SCA's (Stockholm, Sweden) binding offer to acquire G-P's European tissue operations, following consultations with appropriate works councils. The process will continue towards finalizing the acquisition, including approvals by relevant competition authorities and further local consultations processes. As a result, a sales and purchase agreement has been signed by both parties.
SCA had announced this past November 10 that it has made the binding offer to acquire G-P's European tissue operations. G-P has a well-established presence in Europe in both Away-from-Home (AFH) and consumer (At-Home) tissue products. The company's products are in particular marketed with the well-known Lutus brand.
G-P's European tissue operations have approximately 5,000 employees and 15 production sites in seven countries. Sales in 2010 amounted to EUR 1.25 billion (SEK 11.9 billion).
##SHARELINKS##
|
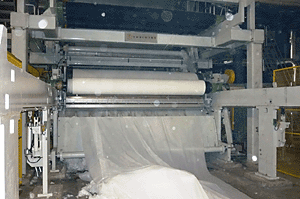 Ningxia Bauhinia Paper Co., Yinchuan, China, has started up on-schedule a new Toscotec (Italy) Ahead 1.5M tissue line. Ningxia Bauhinia was founded in 1989 and is part of the Ningxia Zijinghua Group. The company started as a township enterprise and with this new tissue line investment, has increased its annual production capacity up to 100.000 tpy. The company has 2,000 employees and ranks among the Top 10 tissue producers in China.
The Toscotec supply included an Ahead 1.5M crescent former tissue machine with a single-layer headbox and a double press configuration, a 15-ft steel yankee dryer (TT SYD 15FT), a Milltech steam heated hood, machine auxiliaries, approach flow system, electrification, and control system. Maximum machine speed is 1,500 m/min, with a net trim width of 3,450 mm.
The startup curve was very smooth, the mill reports, noting that the machine reached a stable speed of 1,300 m/min a few days after startup, with a 13 gsm product, despite difficult outside weather conditions (-20°C temperature).
##SHARELINKS##
|
Stora Enso, Helsinki, Finland, reports that its Printing and Reading Business Area plans to increase its cost competitiveness by restructuring coated magazine paper operations at the Corbehem Mill in France, Veitsiluoto Mill in Finland, and Kabel Mill in Germany. The plans will reduce annual costs by some EUR 48 million, with the full impact achieved from the third quarter of 2013 onwards. The restructuring also includes investments in the Corbehem, Veitsiluoto, and Kabel mills totaling EUR 18 million.
The proposed restructuring measures would reduce the number of employees in coated magazine paper operations by up to 110. All of the actions would be completed by the end of 2012. Stora Enso will record a cash provision of approximately EUR 5 million and a fixed asset write-down of approximately EUR 1 million in the Printing and Reading segment as a non-recurring item in the first quarter results.
"The operating environment in coated magazine paper has remained challenging. The plans announced today would respond to these challenges by improving cost efficiency and productivity. The planned streamlining of coated magazine paper operations, including investments in quality, productivity, and energy saving, would enable us to better meet customer and market expectations, and improve profitability," said Juha Vanhainen, EVP, Stora Enso Printing and Reading Business Area.
The outcome of the plans, the company notes, will depend on the result of the local co-determination procedures. Stora Enso would work in cooperation with the local communities to help affected personnel to find new employment opportunities, and all job openings in other Stora Enso units would be available to those affected.
##SHARELINKS##
|
Stora Enso, Helsinki, Finland, says that it also plans to increase further the efficiency and flexibility of its local maintenance operations in Sweden by restructuring and changing the processes. The planned restructuring measures would reduce the workforce by approximately 130 employees in maintenance operations in Sweden.
The planned restructuring involves the company's Hylte, Skoghall, Skutskar, Fors, and Kvarnsveden mills. Altogether, approximately 800 personnel are employed in maintenance at these units.
The restructuring measures would reduce annual costs by approximately EUR 21 million, starting gradually from late 2012 onwards, the company notes. Stora Enso will record a cash provision of EUR 6 million in the Renewable Packaging segment and EUR 4 million in the Printing and Reading segment as a non-recurring item in the first quarter of 2012 results.
"To safeguard our competitiveness, we need to stay on the path of improvements in costs and productivity, and also flexibility. We are therefore planning to increase the efficiency of our local maintenance operations," says Mats Nordlander, EVP, Renewable Packaging and Country Manager, Sweden.
All decisions will be taken only after the local co-determination negotiations have been concluded. Stora Enso would make every effort in co-operation with local communities to help the affected personnel find new employment opportunities, and all job openings in other Stora Enso units would be available to those affected.
##SHARELINKS##
|
AkzoNobel, the Netherlands, reports that it is planning to invest EUR 80 million in the construction of a new pulp chemical island facility in Brazil. The plant, operated by the company's Pulp and Paper Chemicals business, Eka Chemicals, will supply the Suzano Maranhão pulp mill. This is AkzoNobel's second largest investment in Brazil in the past 12 months.
"This 15-year agreement emphasizes the importance of high growth markets for AkzoNobel and will help drive the company's medium-term strategy of doubling revenue in Brazil to EUR.5 billion," said Rob Frohn, AkzoNobel Executive Committee member responsible for Specialty Chemicals.
The investment will involve supplying, storing, and handling all chemicals for the 1.5 million ton per year pulp mill, which is being constructed in Imperatriz, Maranhão, Brazil. The mill is expected to come on stream in the last quarter of 2013.
"We are very proud to have been awarded this project; it underlines the value our Chemical Island concept brings to our customers," said Pulp and Paper Chemicals GM Ruud Joosten. "The future demand for pulp and paper in Latin America and China is forecast to increase substantially over the next decade and these investments ensure that we are part of that growth."
Commenting on the agreement, Ernesto Pousada, COO at Suzano Papel e Celulose, said that "Eka Chemicals is a long and reliable partner to Suzano Papel e Celulose. Through this deal, we are ensuring our plant will use the latest and most sustainable chemicals available, something that has been key for us."
The new facility expands AkzoNobel's pulp and paper activities in Brazil. The business already runs Chemical Islands, as well as other production units, on several customer sites. It also operates bleaching and paper chemical plants in Jacareí, Rio de Janeiro, Três Lagoas, and Jundiaí.
##SHARELINKS##
|
Buckman, Memphis, Tenn., USA, this week announced that it has been selected as a Hay Group Insight's (HGI) High Performing Company for 2011. To be selected for this recognition, companies must score in the top two-thirds of engagement and enablement within HGI's normative database, as well as exceed industry averages on the majority of financial indicators.
According to HGI, Buckman's results are on average 5% above the high performing benchmarks in the HGI databases. Specifically, the report indicated that Buckman is an ethical and socially responsible company, has a clear sense of direction and strong leadership, treats its associates with respect, and offers learning and development opportunities. The report also noted that quality and customer focus are clearly priorities at Buckman, and that Buckman fosters a culture that supports teamwork and collaboration. As a result, according to the report, employee engagement levels are strong and most employees intend to stay for the long-run.
"At Buckman, we are always looking for opportunities to measure our performance against our peer group and against the best companies in the world," said Chip Westbrook, VP of Global Human Resources at Buckman. "We participated in the Hay Group process because of the things that they measure, the benchmarking they provide, and the insight they can give us on key elements of our associate engagement and overall sustainability."
Among the specific measurement areas in the report are scores in 15 different dimensions, with sub-categories within each dimension. The dimensions are clear and promising direction, quality and customer focus, confidence in leaders, associate engagement, authority and empowerment, principles of highly effective teamwork, respect and recognition, collaboration, associate enablement, performance management, work/structure/process, development opportunities, training, resources, and pay/benefits.
##SHARELINKS##
|
Containerboard/Packaging
Caraustar Industries, Atlanta, Ga., USA, one of North America's largest producers of uncoated recycled boxboard (URB), reports that it achieved certification in the Forest Stewardship Council (FSC) Chain of Custody Standard for the following mills: Austell Boxboard Mill No. 2 (Austell, Ga.), Carotell Paperboard (Taylors, S.C.), Cincinnati Paperboard (Cincinnati, Ohio), and Tacoma Paperboard (Tacoma, Wash.). Other Caraustar mills receiving certification earlier include Austell Boxboard Mill No. 1 and Sweetwater Paperboard.
The six certified Caraustar URB mills all produce a 100% recycled paperboard product that is used in various applications, including folding cartons, tubes and cores, gypsum facing papers, and specialty paperboard products. These mills, and now all Caraustar URB mills, have also received certification to the Sustainable Forestry Initiative (SFI) Chain of Custody Standard.
##SHARELINKS##
|
Shareholders of U.K.-based packaging group DS Smith Plc last Friday (February 3) approved the company's proposal to acquire SCA's (Stockholm, Sweden) packaging operations, excluding the two kraftliner mills in Sweden. The transaction remains subject, among other things, to antitrust clearance from the European Commission. Closing is expected during the second quarter.
Regarding the French part of the packaging operations, DS Smith has made a formal offer to acquire this business. This process is subject to an information and consultation procedure with the relevant works councils and will be treated separately.
##SHARELINKS##
|
Jiangmen Xinghui Paper Mill Co., China, has selected PMT Italia (Pinerolo, Italy) as a key supplier for its new "white line chip board" machine project to be installed at a mill in the Jiangmen, Guangdong province of China, near the town of Shuangshui. Startup is scheduled for the end of 2013.
PMT Italia will supply technological paper machine sections like the four M4 headboxes, of which one will have dilution control, a shoe press, and a winder. The new PM 1 board machine will be designed to produce white line chip board in the range of 230 to 500 gsm at a speed of 650 m/min. Trim width at the reel will be 4.360 mm, and the machine will have a forecast output of 300.000 metric tpy. .
The scope of supply includes the control and automation systems of the related paper machine sections to be integrated into the main MCS, together with erection supervision, commissioning, and startup services.
##SHARELINKS##
|
RockTenn Co., Norcross, Ga., USA, this week announced that it intends to redeem $300,000,000 of its 9 1/4% Senior Notes due 2016 March 2016 Notes), representing all of the March 2016 Notes outstanding. The redemption will be made in accordance with the terms of the indenture governing the March 2016 Notes and the terms of the notice of redemption.
Rock-Tenn expects the March 2016 Notes to be redeemed on March 15 (Redemption Date) at a redemption price equal to 104.625% of the principal amount of the March 2016 Notes, plus the accrued and unpaid interest, if any, to but excluding the Redemption Date.
A notice of redemption is being mailed to all registered holders of the March 2016 Notes. Copies of the notice of redemption may be obtained from HSBC Bank USA, National Association by calling 212-525-1404.
RockTenn, with net sales of $10 billion, has some 26,000 employees. The company operates facilities in the U.S., Canada, Mexico, Chile, Argentina, and China.
##SHARELINKS##
|
Tetra Pak, Switzerland, this week inaugurated its new packaging material factory in Finland. The factory, located in the town of Imatra, with a planned capacity of 500 million packages per year, will expand Tetra Pak's gable top capacity for Northern Europe.
The laminated paperboard used to produce the packaging material comes from the Imatra paper mills only six km from the location of the new factory. The short distance helps reduce carbon dioxide emissions for the transportation of paperboard to the factory.
The new factory's production facilities are expected to be ISO 14001 certified during Quarter 1 of 2013, and plans are underway to implement World Class Manufacturing (WCM) practices at the plant. ISO 14001 is an environmental management system standard, and WCM is a tool to help drive and visualize improvements in various areas, including cost, efficiency, competence, maintenance, availability, quality, safety, and environment.
##SHARELINKS##
|
New Products
Resolute Forest Products, Montreal, Que., Canada, this week unveiled its Align™ family of high brightness, environmentally responsible papers that can be used as alternatives to chemical pulp coated and uncoated free sheet in most commercial printing applications. Typical free sheet papers are designed for brightness and use more trees and chemicals than are needed for most print applications, according to Resolute.
Align papers are made with up to 50% less wood fiber, Resolute notes, and have a smaller environmental footprint than traditional offset papers, including some containing recycled content. By delivering higher opacity and bulk at a lower basis weight than traditional free sheet, Align also helps reduce paper, postage, and transportation costs, the company adds.
"For several years, Resolute has seen growing demand for high-quality, eco-conscious papers that can reduce print costs," said Richard Garneau, president and CEO. "With our Align papers, customers can reduce fiber consumption and save money without sacrificing quality in their printed products. Align makes sense for their budgets and the environment."
Resolute also points out that traditional offset papers are designed to deliver both brightness and longevity, but at a premium price. With Align, it says, "value-conscious customers can choose from a range of bright, opaque, high-bulk papers that are designed to meet their specific needs."
More information about Resolute's Align papers, as well as how to order samples, is available online.
##SHARELINKS##
|
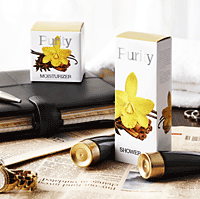 Stora Enso Renewable Packaging, Finland, a supplier of premium boards for packaging cosmetics, fragrances, personal care products, and luxury products, has launched enhanced versions of the Performa White, Performa Bright, and Performa Cream carton boards. Thanks to several technical innovations made at Stora Enso Fors Mill in Sweden, these boards now come with enhanced smoothness, strength, and visual appearance.
"By listening to both printers and brand owners, we focused our development work of the Performa boards on the key properties of strength and printability. This input from our customers was combined with the capabilities of the rebuilt board machine," says Eva Lundqvist, product manager at Fors Mill. "The printability has improved considerably, thanks to the board's enhanced coating and smoothness. Increased strength has had a positive effect on the board's runnability and overall performance."
With its improved smoothness and better visual appearance, Performa White is a suitable choice for the demanding segment of cosmetics and beauty care packaging. It is also compatible for use in rotogravure printing, which requires a high-quality printing surface.
##SHARELINKS##
|
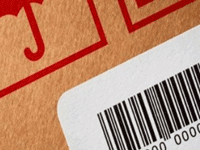 Twin Rivers Paper Co., South Portland, Maine, USA, a producer of lightweight specialty label, packaging, and publishing papers, announced that its Alliance® TT (Thermal Transfer) product is now available in 40 lb. This newly designed 40 lb basis weight (24x36/500) broadens the company's label product offering. Twin Rivers' label portfolio includes release liner, C1S wet strength, thermal transfer, and specialty base stock.
Alliance TT, with its Flexo (flood coat) and thermal transfer ribbon printability as well as aesthetics properties, eliminates many of the hassles that converters encounter when picking a thermal transfer label. With its specialized coating and surface smoothness, the product can deliver high quality images across a wide range of ribbon combinations. Its high brightness combined with its blue-white shade provides a print contrast for better bar code readability, the company points out. The addition of 40 lb Alliance TT allows converters to get more units out of a roll.
Twin Rivers Paper Co. has operations in New Brunswick, Maine, and Québec (Canada).
##SHARELINKS##
|
Energy
International technology Group Andritz, Graz, Austria, through its U.S. subsidiary Andritz Inc., Roswell, Ga., reports that it is collaborating with ZeaChem Inc., Lakewood, Colo., on the production of cellulosic biofuels and bio-based chemicals by providing the technology for a continuous biomass pre-treatment pilot plant. ZeaChem is a developer of biorefineries for the conversion of renewable biomass into sustainable fuels and chemicals.
The partnership between the two organizations is the culmination of several years of cooperative work focused on the production of cellulosic biofuels. The Andritz technology will be installed at ZeaChem's new 250,000 gpy biorefining facility in Boardman, Ore.
The Andritz technology will be used to convert various cellulosic feedstocks, including poplar trees and agricultural residues, into low-cost sugars. These cellulosic sugars will be used by ZeaChem to enable the production of sustainable and economical advanced biofuels and bio-based chemicals. Cellulosic ethanol production at the ZeaChem biorefinery will begin this year and the product portfolio of the biorefinery will be expanded for the production of bio-based jet and diesel fuels beginning in 2013.
The pilot plant system includes an Andritz cooking reactor with continuous steam explosion technology. Andritz filter press technology will be used to wash the steam-exploded biomass.
##SHARELINKS##
|
The American National Standards Institute (ANSI), New York, N.Y., USA, coordinator of the U.S. standards and conformity assessment system, is playing a key role in the national push for a robust, reliable, and interoperable smart grid for the U.S. Ranking among the Obama Administration's top priorities for the nation, the smart grid is a planned nationwide network that integrates information and communication technologies, enabling two-way flows of energy and communications to deliver electricity efficiently, reliably, and securely.
Taking the next step forward in the grid's development, the Smart Grid Interoperability Panel (SGIP), a joint effort of the National Institute of Standards and Technology (NIST), Gaithersburg, Md., and the private sector, recently released version 2.0 of the testing and certification framework for the North American electric power industry. Developed with input from ANSI, the framework lays out a plan to enhance the quality of secure and interoperable smart grid products and significantly reduce their installation cost in the smart grid.
The Interoperability Process Reference Manual (IPRM) details processes and procedures for increasing market confidence in products through testing and certification, especially third-party assessment services providing quality assurance to purchasing organizations.
As the first U.S. signatory to the International Accreditation Forum (IAF) Multilateral Recognition Arrangement (MLA) for product certification, ANSI has committed to support the implementation of the IPRM Framework as an internationally recognized accrediting organization.
ANSI accreditation offers a formal, third-party process for review and recognition of certification programs. The international standard General requirements for bodies operating product certification systems forms the cornerstone of ANSI's accreditaton process for product certification programs.
##SHARELINKS##
|
People
Crane & Co., Dalton, Mass., USA, has appointed Rachel V. Ivey VP, Creative and Product Development. Ivey will lead the creative direction of the company's consumer division.
"Crane & Co. is at an exciting juncture as we are in the process of evolving the company to the next stage of its development. Rachel brings the creative edge to our already exemplary leadership team," said Anil Jagtiani, president, Consumer Division, Crane & Co. "We know that Rachel will drive innovation while honoring our incredible heritage, and we're proud to have her onboard."
With more than 15 years of experience, Ivey brings extensive design experience and a strong understanding of brand identity to Crane & Co. Before joining Crane, she served as the Creative Director of Color and Trend for Walmart, overseeing expansion of the communication of color and trend throughout the business. Previously, she was head designer at Williams Sonoma where she established the design direction and sensibility for which the brand is known today. She began her career in interiors with The Gap Inc., as part of a product team for the Banana Republic Home Division.
"I am excited to be working with such an iconic brand known for its superior quality and exquisite craftsmanship. It's an incredible opportunity to modernize and update the brand's unique aesthetic," said Ivey. "I'm very much looking forward to helping to grow the brand in all dimensions."
Since 1801, Crane & Co. has been a producer of 100% cotton quality paper for personalized notes, business stationary, wedding invitations, birth announcements, calling cards, and more. The seventh-generation family-owned business has produced the paper for U.S. currency since 1879, and manufactures products used in banknote security and industrial applications.
##SHARELINKS##
|
Ola Hildingsson has been elected as a new member of the board of directors at Södra Cell, Sweden. Hildingsson holds a Master of Science in Forestry and has extensive experience in the forestry industry, including working as a manager for what was at that time the Billerud Uddeholm sawmill and as CEO for SCA Timber AB. Hildingsson currently is CEO of Domsjö Fabriker, a position which he will be leaving on March 1..
Södra Cell AB is one of the largest pulp manufacturers in the world, producing 2.1 million metric tpy. The company operates three mills in Sweden and two in Norway. Its main product is long-fiber paper pulp, but it also manufactures textile pulp (dissolving pulp) and the new composite material DuraPulp. Södra Cell is also a supplier of green energy in the form of electricity, biofuel, and district heating.
##SHARELINKS##
|
Systec Conveyors, Indianapolis, Ind., USA, has named Alberto Spallino regional sales manager for the Central U.S. as well as Ontario, Canada. Spallino is based out of Toledo, Ohio.
With more than 15 years of sales experience, seven years of which are in the corrugated Industry and more than 10 years selling conveyors, Spallino is a seasoned veteran to complement the growing sales team at Systec, the company notes.
##SHARELINKS##
|
TAPPI News
Leading up to the Sustainability Forum at PaperCon in April, a series of webinars are planned to help manufacturers and customers better understand key issues around sustainability. Participate in these seminars, and attend PaperCon's Sustainability Forum to assure you have the most up-to-date knowledge of this dynamic and important topic.
How to Deal with Misleading Environmental Claims Related to Print and Paper
February 27, 11:00 am
Facilitated by: Phil Riebel, President and COO, Two Sides U.S., Inc.
Cost: There is no cost to participate, but you must register to attend.
Register for this webinar
Many corporations are promoting electronic communications (ex: e-billing) as a more environmentally-friendly method of communication, and in doing such they are spreading erroneous facts and messages about print and paper. As a result, the public is being flooded with messages that portray print and paper as a "bad" product with "destructive" environmental impacts relative to other communication methods. This presentation will outline some of the unique environmental and social features of print and paper products which make it a sustainable way of communicating. The (often ignored) environmental and social impacts of electronic communications will also be reviewed, as well as environmental marketing rules and guidelines that companies should respect when making environmental claims (ex: US Federal Trade Commission Green Guides). Print and electronic media will co-exist for many decades and we need to reduce the environmental impacts of both. It's not a question of one versus the other, but rather which combination is the most sustainable. The initiatives taken by Two Sides to challenge misleading claims will also be presented.
Learn more and make plans to participate.
Additional webinar in the series:
A Global Sustainability Perspective
March 12, 2012 at 11:00am EST - Facilitated by: Avrim Lazar, FPAC
Register in advance for this webinar
A Comparison of the FSC and SFI Forest Certification Standards
Took place on January 30. Listen to a recording.
PaperCon 2012 will take place April 22-25, 2012 in New Orleans, Louisiana, and will focus on "Growing the Future"; leveraging renewable, recyclable raw materials and developing human capital to ensure value for customers, long-term sustainability for shareholders, and a future for our peers.
##SHARELINKS##
|
Book your hotel now for PaperCon 2012 in New Orleans
PaperCon 2012 will be held at the Sheraton New Orleans. A limited amount of discounted rooms are available at both the Sheraton and the nearby Omni Royal Crescent Hotel. TAPPI has negotiated special rates at both hotels that includes complimentary internet in your guest room and other perks. You don't want to miss out; rooms outside our block may be much more expensive and will not include special offers. If you utilize a travel agent or company travel department, please have them book you in the TAPPI block. Take a moment to register and reserve your discounted hotel room for this "must attend" event.
What is PaperCon? Designed by industry professionals, PaperCon brings together CEOs, mill managers, superintendents, scientists, process engineers and suppliers for the largest pulp and paper technical program in the world. No other event provides such a comprehensive program, networking opportunities and exhibit among such a distinguished group of industry leaders.
Why attend PaperCon? For 2012, PaperCon is about "Growing the Future", leveraging renewable, recyclable raw materials and developing human capital to ensure value for customers, long-term sustainability for shareholders, and a future for our peers. Located in the heart of the Southern USA pulp and papermaking region, New Orleans, PaperCon sessions will highlight today's dynamic packaging grades.
Learn more about PaperCon.
##SHARELINKS##
|
TAPPI and PIMA are pleased to announce the selection of James A. Rubright, Chairman and Chief Executive Officer of RockTenn, as the association's 2012 Executive of the Year. RockTenn, based in Norcross, Georgia, is a leading North American producer of corrugated and consumer packaging and recycling solutions. The award is PIMA's highest honor and is bestowed on senior-level executives in the pulp, paper or converting industries for excellence in management and outstanding contributions to the industry as a whole. Rubright will receive his award on April 23 during the opening session of TAPPI's PaperCon 2012 in New Orleans, where he will also participate in an Executive Panel.
"Throughout his career James Rubright has exemplified the strong leadership skills, vision and integrity required for success in a globally competitive business like the pulp and paper industry. His accomplishments as a leader and his many contributions to the industry make him an outstanding choice as PIMA Executive of the Year," said Larry N. Montague, TAPPI President and CEO. "Most recently his leadership helped RockTenn deliver consistently solid earnings during the major Smurfit-Stone acquisition. Both competitors and independent converters have responded positively to the acquisition which has brought RockTenn to a new level in the industry as one of the largest, most respected and profitable integrated paperboard and packaging companies in North America."
Rubright has served as RockTenn's CEO since October 1999 and Chairman of the Board since January 2000. The Smurfit-Stone merger in 2011 vaulted RockTenn into the position of No. 2 paperboard packaging producer in the U.S., behind International Paper Co. Before joining RockTenn, he served as Executive Vice President of Sonat Inc., a diversified energy company headquartered in Birmingham, Alabama. He is a director of AGL Resources, Inc., an energy company, and Forestar Real Estate Group, Inc., a real estate and natural resources company. He lives in Atlanta, Georgia with his wife, Mary, and their two boys, who are the youngest of his six children. Rubright was RISI's 2008 and 2011 North American Forest Products CEO of the Year and named Global CEO of Year by PPI in 2009.
##SHARELINKS##
|
The 2012 TAPPI PEERS Conference, October 14-17 in Savannah, Georgia, has announced the Call for Papers. PEERS is the perfect forum for paper industry professionals both to acquire practical operating insights and to network with industry peers in technical sessions, tutorials, round tables, new technology sessions and workshops.
Topics suggested for the 2012 technical program are as follows:
- Fiber and Pulping
- Mill Operations and Engineering
- Steam and Power
- Recycling
- Environmental Management and Regulation
- Sustainability
- Abstracts on other topics are welcome.
Learn more.
Authors interested in presenting a paper should upload their extended abstract to TAPPI's Speaker Management System by March 9, 2012.
Authors will be notified of acceptance by April 20, 2012 and must provide a full text manuscript by July 20, 2012.
For more information please contact Craig McKinney, TAPPI Program Manager at +1.770.209.7294
##SHARELINKS##
|
An Invitation to Present has been announced for TAPPI's 2012 International Bioenergy and Bioproducts Conference (IBBC), October 17-19, 2012 in Savannah, Georgia.
IBBC will focus on technical advancements and commercialization of bioconversion technologies that leverage the forest products manufacturing infrastructure and will include technical presentations, expert panels, case studies, and reports from projects that address:
- Feedstock and harvesting improvements to increase yield and quality of biomass
- Bioelectricity using combined heat and power (CHP)
- Bioconversion technologies for wood and biomass
- Production of chemicals and transportation fuels from wood and biomass ·
- Policies and incentives for bioconversion projects
Presentations are sought in the following areas:
Advances in Technology: strong technical papers with a focus on presenting new findings
- Biomass Supply & Demand
- Advances in Conversion Pathways
- Biomass Harvesting & Preparation
- Advances in Bioproducts
Commercialization Activities: case studies and updates from pilot scale, commercial, and pre-commercial operations
- Biorefineries
- Repurposing the Traditional Pulp and Paper Mill
- Harvesting and Preparation
- Technical Economic Analyses
- Commercial Collaborations for Enabling Technologies
- Project Deployment Issues
Impacts of Policies and Incentives: analysis of existing or proposed bioconversion policies at State, Provincial or Federal levels
- Public policy proposals
- Pulp/paper incentives that support bioconversion progress
- Assessing common ground between pulp/paper and agricultural bioconversion policies
Limited space is available for poster presentations.
Abstract Submission Information:
Authors interesting in presenting a paper should upload their abstract to the TAPPI's Speaker Management System
Abstract Requirements: Abstracts should be no more than 200 words.
Submission Deadline: March 9, 2012
Presentations Deadline: September 17, 2012 Authors will be notified of acceptance by April 20, 2012.
OTHER OPPORTUNITIES TO PRESENT
2012 PEERs Conference
October 14-17, 2012
(Being held in conjunction with IBBC)
For more information, visit our website.
##SHARELINKS##
|
Attend the "How To" Conference for Operations and Maintenance Professionals
The 24th Pulp and Paper Reliability and Maintenance Conference will be held March 12-15, 2012 in Raleigh, NC. The goal of this conference is to continue to be the marketplace for Reliability and Maintenance solutions for the pulp and paper industry. And it promises to provide an arsenal of improvement solutions to help your plant improve financial performance and survive long term.
Since its inception in 1986, the Pulp and Paper Reliability and Maintenance Conference has developed a devoted following of Reliability and Maintenance professionals representing Operations, Maintenance, Stores and Engineering. Over 400 speakers have shared their knowledge and experiences along with over 3,000 conference delegates. Learn more about this conference and register to attend at the TAPPI conference page.
##SHARELINKS##
|
CALL FOR NOMINATIONS
JOHANNES A. VAN DEN AKKER PRIZE FOR PAPER PHYSICS
The Johannes A. Van den Akker Prize recognizes outstanding written publications in the field of paper physics. The Prize is awarded by TAPPI Paper Physics Committee, and funded from an endowment established and administered by the Institute of Paper Science and Technology. It was established in the year 2000 to honor the distinguished research and teaching contributions of J. A. Van den Akker, a long time faculty member of the Institute of Paper Science and Technology and TAPPI Gold Medalist.
The Van den Akker Prize for Paper Physics is awarded annually to the author[s] of the best paper published in the area of fiber and paper physics during the preceding calendar year. It is intended to recognize publications that make a significant contribution to the field of paper physics. The award consists of a $2500 honorarium (split between authors of multiple papers) and award medal(s).
Papers in the area of paper physics that are published in archival journals or conference proceedings will be considered for this award. Nominations of outstanding papers for award consideration are solicited each year from members of the TAPPI Paper Physics Committee, journal editors, conference proceedings editors, and other paper scientists active in the area of paper physics.
Nominations for the 2012 Johannes A. Van den Akker Prize should be sent to Ramin Farnood, Chair of the Paper Physics Honors and Awards Committee:
Professor Ramin Farnood
Department of Chemical Engineering and Applied Chemistry
University of Toronto 200 College Street Toronto, Ontario, Canada M5S 3E5
ramin.farnood@utoronto.ca
Nominated publications should have appeared in print during the 2011 calendar year. Nomination packets should arrive on or before April 1, 2012, and consist of a copy of the publication and a short cover letter (1-2 pages), which expounds on the major contributions of the paper. Electronic submissions are encouraged. The Paper Physics Honors and Awards Committee will select a panel of experts to judge the nominated papers and select the winner. The award will be presented at the 2012 International Paper Physics Conference held June 10-14, 2012 in Stockholm.
##SHARELINKS##
|
Bring the excitement of papermaking home with you by purchasing a papermaking kit. These kits are hand constructed for the express purpose of providing you with a home version of the papermaking experience. Every kit includes the following:
Cotton pulp linters - Drying Sheets (felt) – Vat - Mold and Deckle- Couching sheets (paper)- Easy to follow directions
Product code: 08PAPERKIT
Member Price: $45.00
Non-Member Price: $61.00
##SHARELINKS##
|
66TH APPITA ANNUAL CONFERENCE & EXHIBITION
The APPITA Conference and Exhibition is the premier event for the pulp and paper industry in Australia and New Zealand.
The 2012 Conference theme will explore opportunities and techniques to drive performance, productivity and profits in a clean energy economy. The conference offers a well balanced program of technical presentations and workshops, management forums and networking opportunities. Hear from international and local experts on the latest technologies and techniques to drive productivity and profits. The opportunity to network with peers is one of the most valuable aspects of the conference.
Visit our website for further information about Appita membership.
View registration Form
SPECIAL OFFER FOR PULP & PAPER MANUFACTURERS!
Mill Package Registration
For one flat fee of $5665, pulp and paper manufacturing sites and their corporate offices can register an unlimited number of employees to attend the 66th Appita Annual Conference & Exhibition. The special Mill Package Registration offers great flexibility. Attend one session, one day or the entire conference! To qualify for the special Mill Package rate, employees must work together at the same mill location or corporate head office.
##SHARELINKS##
|
December 4, 1921 - February 1, 2012
Earll Church passed away peacefully in Sarasota, Florida on February 1st, 2012. Earll was a resident of Sarasota from 1982. He is survived by his loving wife Eunice Church, sons David, Douglas (Barbara), and grandchildren Jennie Church, Jeffrey Church, and Sara Nicholson (Rob).
He was a graduate of Onondaga Valley Academy H.S. in Syracuse, N.Y. and was Salutatorian of his class in 1939. He also received a B.S. degree in 1943 from the State University College of Forestry at Syracuse, N.Y. (now known as SUNY College of Environmental Science and Forestry). In 1957 he earned a Ph.D. in Physical Chemistry from Syracuse University. He was a member of the engineering honor society Tau Beta Pi.
Earll worked as a chemist in industry and was a professor at Temple University in Philadelphia. He was then a professor at the State University College of Forestry at Syracuse for over 10 years. He worked for 25 years for ITT Rayonier in New York, N.Y. and Stamford, Connecticut as a Director of Technical Service and Product Development, and later Corporate Planning. He concluded his career with ITT Rayonier as the Liason Manager between the B.C. Forest Products Company and ITT Rayonier in Vancouver, British Columbia, Canada. Earll was active in TAPPI, the leading association for the worldwide pulp, paper, packaging and converting industries for many years.
After retiring, Earll settled in Sarasota, Florida. In his spare time Earll had a passion for his family, photography, gardening, electronic and automotive building and repairs, fine woodworking, golf, boating, fishing and bridge. A Memorial Service will take place at the Church of the Palms Friday, February 10 at 3:00 pm, with a reception to follow.
##SHARELINKS##
|
|
|