Over the Wire
TAPPI
Weekly Spotlight
The U.K. paper recycling rate in 2011 increased by nearly 5% over 2010, according to figures released this past week by the U.K.-based Confederation of Paper Industries (CPI). The rise from 75.1% in 2010 to 78.7% last year ensures that the U.K. surpasses the target set in the revised European Declaration on Paper Recycling (2011 - 2015) to "maintain current high levels in countries where it already reached levels of above 70%."
However, CPI sounded a note of caution by highlighting that the rise in the recycling rate could be attributed more to a decrease in paper consumption than a significant increase in the amount of paper collected for recycling.
Stuart Pohler, CPI Recovered Paper Sector manager, said that "while the increase in the recycling rate is welcomed in principle, it is important to qualify the apparent performance improvement. U.K. collection of used recovered paper in 2011 was just over 8 million metric tons, an increase of 0.4% over 2010, whereas consumption of paper and board products that entered the U.K. waste stream fell by 4.2% compared with 2010."".
"With lower volumes available for collection, and only a modest increase in tonnage collected for recycling from existing sources, ensuring recycling performance is maintained in the future will mean additional sources will be required. This will have a significant knock-on effect for cost and quality control for collectors, and may become increasingly difficult if demand from global paper mills falls, further suppressing collectors income," Pohler explained.
##SHARELINKS##
|
All major trade associations representing the forestry sector in Indonesia have together launched a declaration outlining eight practical steps required to be undertaken by industry, stakeholders, and international trade partners to achieve world-class timber production and trade standards through implementation of the Wood Legality and Verification System (SVLK), according to a report by the Asia Pulp & Paper Group (APP), Jakarta, Indonesia.
The declaration was recently agreed at a formal ceremony in Jakarta during the Second High Level Market Dialogue 2012. The introduction of SVLK in Indonesia will ensure that only wood products verified as legal will enter the market. At the event, the forestry associations pledged to fully support the government of Indonesia's efforts to:
1. Engage with all stakeholders from across the forest industry's multi-layer supply chains to help finalize and implement full SVLK compliance
2. Encourage an examination of the desirability of adopting a phased approach to SVLK implementation across the industry to ensure a successful transition to full compliance of all companies, thereby mitigating possible production, trade, and market disruption
3. Assist small to medium sized companies, companies operating in remote areas, and community based companies to be fully SVLK compliant in line with the government of Indonesia's sustainable forestry development plan
4. Work with foreign countries to build and strengthen an efficient mechanism to promote legal wood products and avoid unnecessary administrative and financial impact on verified legal Indonesian timber and timber-based producers
5. Encourage foreign countries to ensure consistency of policy application, encourage national public procurement policies to prioritize verified legal products, and to support the introduction of the same high standards across the private sector
6. Communicate and promote SVLK to global stakeholders consistently as the highest standard to verify legality and as the foundation for the sustainable forest management certification scheme in Indonesia (PHPL/SFM)
7. Encourage a reciprocal responsibility on the part of VPA partners and also the wider international community to ensure only wood products that are verified as legal enter the market
8. Seek active participation in process to implement the VPA, such as the Indonesia/EU Joint Participatory Committee.
Trade associations present at the signing of the declaration were: GPEI (Indonesian Exporters Association), MPI (Indonesian Forestry Community), APHI (Association of Indonesian Forest Concessionaires), APKINDO (The Indonesian Wood Panel Association), ISWA (The Indonesia Sawmill & Woodworking Association), APKI (The Indonesian Pulp & Paper Association), and ASMINDO (The Indonesian Furniture Industry & Handicraft Association).
SVLK is Indonesia's chain of custody certification program, enacted in 2009. It ensures that wood products exported from the country are legal and traceable to verified points of origin. SVLK is designed to ensure that the industry will only receive and process timber from legal sources according to the regulations of Indonesia. The regulations cover aspects of licensing, harvesting, transporting, and processing for the industry. SVLK is a key step in the effort to achieve full Sustainable Forest Management (SFM) certification.
##SHARELINKS##
|
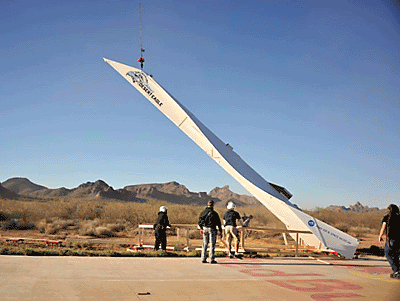 A giant paper airplane soared for some 10 seconds at 3,000 ft above Arizona, USA, this past week before tail stress caused it to plummet and crash into a crumpled mass on the desert floor. The 45-ft long, 800-lb paper giant, with a 24-ft wide wingspan, was made of rigid, corrugated graphic board. Based on a model by a young contest-winner, it was the result of the Pima Air & Space Museum's Giant Paper Airplane Project. The museum's project was designed to entice youngsters like 12-year-old contest-winner Arturo Valdenegro of Tucson, Ariz., to learn more about aviation and engineering.
Dubbed Arturo's Desert Eagle, the plane was attached to a chain and lifted by helicopter to a height of 2,703 feet and released, whereupon it soared at speeds of around 98 mph. The flight lasted about as long as the Wright brothers' first successful flight at Kitty Hawk, N.C., in 1903. The flight of Arturo's Desert Eagle might have lasted longer if the team had been able to release it at between 4,000 and 5,000 ft as originally planned. But wind conditions in the area forced the helicopter to let it go more than 1,000 ft lower than the target altitude.
While it was based on Valdenegro's design, the paper plane was actually designed by Art Thompson, an aviation engineer who was part of the team that engineered and constructed the Northrup-Grumman's B-2 stealth bomber for the U.S Air Force.
"For several shining moments, our huge, beautiful, silly, hubristic 45-foot paper airplane soared," museum spokesman Tim Vimmerstedt wrote on the project's website.
##SHARELINKS##
|
Today's procurement professional is challenged to provide more bottom-line business value while globalization, rising raw material and transportation costs, and supply chain dynamics present increasing pressures on current practices. The Procurement Forum at PaperCon 2012, a new addition this year, will focus on providing procurement and sourcing professionals in the pulp and paper industry with information to help support these new and challenging demands. Topics will address best practices and emerging trends in procuring consumables, chemicals, energy, and mechanical parts.
The first session of the Procurement Form, Procurement Organizational Effectiveness, will begin with Greg Anderson from Accenture reporting on Accenture's recent research on high performing procurement organizations. He will review the three key dimensions of procurement mastery: strategy, supplier relationship management, and sourcing and category management. The three key enablers—requisition to pay, technology, and workforce and organization—will also be addressed. Attendees will then hear from two paper manufacturers. Glen Sanders, director-sourcing with Verso Paper Corp., and Jim Thomas, corporate VP of purchasing with Domtar, will each provide a brief overview of their current purchasing philosophies. Jason Caldwell, manager commodity chemicals for RockTenn, will moderate the session.
The second session of the Procurement Forum is Emerging Trends in Procurement. Greg Anderson from Accenture will open this session to review Accenture's research on where procurement leaders need to focus over the next five years. Diane Palmquist, VP manufacturing industry solutions for GT Nexus, will share perspectives on her company's cloud-based collaboration platform for global trade and logistics. As sustainability is a growing factor in procurement, Emilio Tenuta, director of sustainability for Nalco, will share insights on how other industries integrate sustainable procurement practices. This session will be moderated by Manoj Sujanani, Ph.D., director, procurement for Sappi Fine Paper North America.
The Procurement Forum takes place on Monday, April 23, 2012 from 1:30 PM to 5:00 PM at the Sheraton New Orleans. Participation in the Procurement Forum is included with all PaperCon registrations. There is still time to register, so don't miss this one-of-a-kind event for procurement professionals.
More details about the PaperCon 2012 program, exhibition, workshops and seminars, including the Procurement Forum, special events, and registration, are available online, along with information about travel and accommodations.
##SHARELINKS##
|
TAPPI's two-day (April 23 - 24) OpEx Reliability Seminar being co-located with PaperCon 2012, April 22 - 25, in New Orleans, La., USA, features a total of seven full sessions on Monday and Tuesday. On Monday from 1:30 p.m. until 3:00 p.m., Tor Idhammar of IDCON and Ian McKinnon of Reliability Solutions take a close up look at progress that has been made in the reliability arena and what can be done to keep the ball rolling in that direction.
Idhammar's presentation, titled "The Journey toward World Class Maintenance: Why Some Reach It and Most Do Not," examines persistent obstacles to progress in the maintenance and reliability function and how to possible overcome them and move forward. McKinnon explores success mills are having by combining reliability systems, processes, and precision skills to deliver exceptional results. Together, these two presentations serve as both an industry report card and a detailed analysis of potential paths toward improvement. .
More details about the PaperCon 2012 program, exhibition, workshops and seminars, including the OpEx (Operating Excellence) Seminar, special events, and registration, are available online, along with information about travel and accommodations.
##SHARELINKS##
|
North Carolina State University, Raleigh, N.C., USA, has announced the opening of a position for program director of recruiting and industry relations, Paper Science and Engineering Program, College of Natural Resources. The program director will report to the executive director for development and college relations, College of Natural Resources, with a dotted line responsibility to the department head, Forest Biomaterials. The program director will be located within the Forest Biomaterials department.
The successful candidate for program director will have the following qualifications:
- A B.S. or B.A. degree; a MS is preferred
- An energetic personality; very good written and oral communication skills
- A self starter with good organizational skills
- The ability to prioritize work, operate independently, and to multitask
- Skills in or the ability to develop web-based recruiting materials, including text, photos, blogs, social media, and video content
- Knowledge of the pulp and paper industry, or some other allied manufacturing industry is highly desirable.
The program director of recruiting, development, and industry relations will have three primary responsibility areas:
- Recruiting – student relations
- Develop and implement a successful recruiting program for in-state, out-of-state, and on-campus prospects
- Provide ongoing student support programs to achieve student retention objectives
- Support student professional development training programs within the department.
- Alumni – donor relations
- Using the Advance database, develop and maintain Alumni contact information and Individual donor information
- Develop and provide appropriate Stewardship to Alumni and Individual donors through personal contact, semi-annual newsletter, and appropriate social media.
- Industry outreach
- Promote and grow Pulp and Paper Foundation membership through timely communication with corporate members and potential new members
- Direct and coordinate with Pulp and Paper Foundation president, board, and committees to:
- organize and manage Annual Meeting, including publishing the Annual Report -
- schedule other appropriate meetings -
- solicit and collect Corporate Membership dues
- encourage Corporate Members and industry supporters to provide student internship opportunities
##SHARELINKS##
|
Market Roundup
Total U.S. printing and writing (P&W) paper shipments increased 2% in February compared with February 2011, according to AF&PA's (Washington, D.C., USA) February 2012 Printing-Writing Paper Report released this past week. Three of the four major P&W grades posted increases compared with last February, and the one decrease is the smallest since April 2011.
U.S. purchases (shipments + imports – exports) of P&W papers decreased slightly less than 1% in February. Total P&W paper inventory levels also decreased slightly less than 1% compared with January 2012.
Some highlights from the additional findings are:
- Coated mechanical (CM) paper shipments increased 4% year-over-year, the largest such increase since September 2010
- Uncoated mechanical (UM) paper shipments decrease by the smallest year-over-year change since April 2011, which was the start of the recent declines that came on the heels of 15 consecutive months of year-over-year increases
- Shipments of uncoated free sheet (UFS) papers increased year-over-year for just the second time in the past 20 months
- Shipments of coated free sheet (CFS) papers increased year-over-year for the first time in the past 15 months.
##SHARELINKS##
|
Vietnam has topped Australia as the world's largest supplier of wood chips to pulp mills in Asia. In 2011, Vietnam exported 5.4 million metric tons, triple that in 2007, according to the Wood Resource Quarterly (WRQ), Seattle, Wash., USA. The good news for wood chip exporters in both Vietnam and Australia has been the steady increase in demand for hardwood chips from China, WRQ notes.
Wood chip trade flows in the Pacific Rim have changed substantially the past five years. Vietnam, Chile, Thailand, and Uruguay have all been increasing their shipments of chips, while Australia and South Africa have been losing their market share as fiber suppliers to the pulp mills in Japan, China, Taiwan, and South Korea.
Exports of hardwood chips from Australia fell 8% in the second half of 2011 compared with the first half, making 2011 the slowest year for chip exports since 2000, WRQ reported. Japan was a major importer of wood chips from Australia for many years, but shipments fell almost 30% in 2011 compared with 2010, reducing Australia's market share.
The good news, mentioned above, is that Australian chip shipments to China picked up during 2011. Total exports reached a record high of almost 700,000 metric ton, which was up 12% from 2010 and more than three times as much as five years ago. With the expansion of pulp capacity in China, it could be expected that Australian exports to China will continue to increase.
There is, however, a substantial difference in the average value for chips going to China compared with chips for pulp mills in Japan. In 2011, the premium for Japan-bound chips was almost $60 per metric ton.
Australia has been the largest wood chip supplier in the world for almost 20 years, but in 2011 Vietnam overtook this role with shipments accounting for about 20% of globally traded chips. Exports of Eucalyptus and Acacia wood chips from Vietnam have increased at a phenomenal pace the past 10 years. In 2001, the country exported only 400,000 metric tons of wood chips. In 2011, a new record of 5.4 million metric tons was reached. Last year's shipments were 36% higher than the previous years and a tripling from 2007.
The biggest boost to the establishment of fast-growing hardwood plantations and chipping facilities in Vietnam has been the expanding pulp industry in neighboring China. With limited domestic resources in China, the country will continue to rely on neighbors to supply wood raw-material in the future.
##SHARELINKS##
|
U.S. containerboard production increased 6.0% over the same month last year, according to AF&PA's February 2012 U. S. Containerboard Statistics Report released this past week. Production was down, losing 5.5% compared with January 2012. However, the month-over-month average daily production increased by 1.1%. The containerboard operating rate for February 2012 gained 1.0% over January 2012, increasing from 95.2% to 96.2%.
Additional key findings from the report include:
- Linerboard production was up 6.5%
- Corrugating medium production also saw an increase.
##SHARELINKS##
|
Pulp & Paper
Canfor, Vancouver, B.C., Canada, this week reported that it has completed the previously announced acquisition of Tembec Industries' southern British Columbia interior wood products assets consisting of the Elko and Canal Flats sawmills and approximately 1.1 million cubic meters of combined Crown, private land, and contract annual allowable cut. The transaction includes a long term residual fiber supply agreement for Tembec's Skookumchuck mill.
"Canfor is pleased to welcome the former Tembec employees into the Canfor family and is looking forward to continuing the development of strong community and First Nations relationships," said Don Kayne, president and CEO of Canfor. "This acquisition strengthens Canfor's fiber position in British Columbia while meeting the increasing needs of our highly valued global customers."
The additional sawmill production will add approximately 420 million board ft to Canfor's annual capacity, bringing its total capacity to more than 5 billion board ft. Canfor intends to make capital investments in excess of $50 million in the southern British Columbia mill facilities over the next few years.
##SHARELINKS##
|
A product that helps tissue makers optimize production is the first result of a strategic partnership between Nalco, Naperville, Ill., USA, an Ecolab Co. (Saint Paul, Minn.), and SKF, Göteborg, Sweden, a global supplier of bearings, seals, mechatronics, and lubrication systems. The Nalco Early Warning Chatter Detection (EWCD) system provides tissue machine operators the ability to detect potentially harmful vibrations that can result in doctor blade chatter.
"The combination of the knowledge of two leading companies in their respective areas of expertise has created a solution to help tissue manufacturers optimize their production," said Scott Morris, SKF global marketing manager, Pulp and Paper. "Our customers are asking for suppliers to work together to provide more advanced solutions, and we're delivering."
Keys to the effectiveness of the system are Nalco's approach to early chatter detection through analysis of various parameters, an easy-to-use graphic user interface, and best-in-class online monitoring technology from SKF. Nalco's EWCD system is designed specifically for the creping application and has an intuitive, user-friendly operator interface.
In addition to its critical early warning purpose, the technology can provide additional insight regarding coating stability on the yankee dryer, thus allowing improved troubleshooting for other creping problems. Ongoing pilot projects already have resulted in successful "saves," proving the value and reliability of the system.
"Nalco is extremely excited to bring EWCD technology to tissue and towel manufacturers as an extension of our world-class offering, coupling chemistry, automation, technical expertise, and now real-time monitoring of the creping process," said Chris Futral, Nalco global strategic business leader for Tissue and Towel Grades. "With the SKF partnership in our offering bundle, we have expanded the programs we can provide to our customers along with our process and tissue machine expertise to help drive quality improvements and efficiency in the tissue and towel marketplace."
##SHARELINKS##
|
Norske Skog, Lysaker, Norway, has agreed to sell its Bio Bio newsprint mill in Chile to Group BO, a consortium of Chilean investors, for $56 million. Group BO plans to continue producing newsprint at the mill.
The divestment is a part of Norke Skog's strategy to improve its cash flow and financial position. "We are very pleased to be able to sell the Chilean operations to an industrial player with long-term plans for the mill," noted Sven Ombudstvedt, president and CEO of Norske Skog.
The Bio Bio mill has a total newsprint production capacity of approximately 125 000 metric tpy. It is one of only four newsprint mills in South America.
The investors participating in Group BO are already partners in BO Packaging, one of the leading companies in the Chilean and Peruvian packaging business. The investor consortium is headed by the Pathfinder Group, former owners of Masisa, and has interests in packaging, glass products, building products, agribusiness, and real estate.
Closing of the transaction is expected to take place in the second quarter of this year.
##SHARELINKS##
|
SCA, Stockholm, Sweden, reports that the privatization of Everbeauty under Taiwanese law has been completed, and as a result, the agreement for SCA to acquire Everbeauty has now been signed by both parties.
On February 25, SCA announced that it had delivered a binding offer to acquire Everbeauty, an Asian personal care products company with sales in China, Taiwan, and Southeast Asia. The company produces and markets baby diapers and incontinence care products with strong brands such as Dr P for incontinence care products and Sealer for baby diapers.
Following the signing of the sale and purchase agreement by the parties, the process will continue towards completing the acquisition, which will include seeking approvals and clearances from relevant authorities in Taiwan. Closing of the deal is expected to take place this summer.
##SHARELINKS##
|
Tembec has awarded to Pöyry, Finland, the detail engineering and procurement assistance support contract for a C$190 million investment to upgrade its specialty cellulose (dissolving pulp) mill in Temiscaming, Que., Canada. Installation of a new waste liquor recovery boiler and turbo generator will increase the mill's annual green electricity production by up to 40 MW and reduce sulfur dioxide emissions by 70%. The boiler is expected to be operational in December 2013, followed by the turbo-generator in May 2014.
Pöyry's assignment includes project management and detail engineering design for all disciplines. The project will be executed by Pöyry's office in Montreal, Que. The contract value is C$7.2 million (EUR 5.5 million).
##SHARELINKS##
|
Norway-based Viken Skog has agreed to acquire Norske Skog's (Lysaker, Norway) Follum, Norway, mill site. Viken Skog reportedly has "ambitious, future plans" for the Follum site.
After the decision to close the mill at Follum, Norske Skog says it worked to find relevant stakeholders to create new activities on the site. Norske Skog considers it a good solution that others can now take over the further development.
"Norske Skog is very pleased that Viken Skog will now take over the work to create new activities at Follum. It has been important for us to find a buyer with ambitions for the future, with support from the Buskerud County Council, Ringerike Municipality Council, and regional businesses, and not least from the trade unions at Follum. I wish Viken Skog and the Ringerike region luck with the exciting development work," says Norske Skog President and CEO Sven Ombudstvedt.
As Norske Skog explains, Viken Skog will develop a new, future-oriented forest-based industry cluster at Follum. The location and the existing infrastructure, in the heart of Norway's richest forest areas, make Follum a natural center for an offensive strategy. It will be a milestone for the Ringerike region that Follum will now become a center for sustainable development of environmentally friendly products from the forest. "We have had good cooperation with the Ministry of Trade and Industry in the process of forging our long-term industrial plans. We now expect the government to implement measures to promote innovation and research in forest-based industries, to contribute to the huge effort we now face," said Managing Director Ragnhild Borchgrevink.
The net sales proceeds are in the order of NOK 60 million. The acquisition will take place in the second quarter of this year, and includes Norske Skog Follum AS and Follum Industripark AS, as well as all properties related to the mill site, including Årbogen. Norske Skog will disassemble and retain parts of the technical production equipment, discontinuing production at Follum on Friday, March 30.
Sale of the Follum site will generate a total accounting gain in the order of NOK 30 million, according to Norske Skogn. This will be recognized in the first quarter of this year.
##SHARELINKS##
|
Containerboard/Packaging
Dart Container Corp., Mason, Mich., USA, will acquire Solo Cup Co., Lake Forest, Ill., in a transaction valued at approximately $1 billion. Both companies are in the consumer and foodservice disposable packaging business. The transaction, subject to regulatory approval, is expected to close by the third quarter of this year.
"Our acquisition of Solo will allow us to provide even greater value to our customers in the future," said Dart Container CEO Robert C. Dart. "It will enable customers to purchase a wider range of products, made from a greater variety of materials with varying functional and environmental attributes—all from a single vendor. Both companies have an extensive history in the industry and will bring together valuable experience, traditions, and complementary, high-quality products."
Robert M. Korzenski, CEO, Solo Cup Co., noted that "Solo has made great strides over the past several years in improving its operating efficiency, information systems, and the caliber of the talent within the organization. Dart's leadership team has shown a high level of respect for what Solo has accomplished and I believe we are putting the company in the right hands to succeed and grow going forward."
Dart added that "Dart Container's acquisition of Solo will accelerate the progress Solo has made to improve its levels of service and customer support. We will use our expertise in running a successful, efficient, reliable, and service-oriented company to create an organization that blends the best of both Dart and Solo for the benefit of our customers." According to Dart, a top priority is bringing together the talents and skills of employees from both organizations to ensure that customers continue to receive exceptionally reliable service.
"These are two companies with strong histories of innovation and quality that have invested in the industry and in their customers," said Robert L. Hulseman, chairman emeritus, Solo Cup Co. "I am very proud of this company's contributions to the foodservice packaging industry and extremely pleased that many of Solo's dedicated employees will have the opportunity to continue making a difference for our customers. This is a positive outcome for everyone involved."
Solo is majority-owned by the family of its founder, Leo J. Hulseman, and is also a portfolio company of Vestar Capital Partners IV, L.P. Dart Container is a privately owned company founded by William A. Dart. The integrated organization will be a private company known as Dart Container Corp. Dart expects to continue offering Products under the Solo brand, including the iconic red Solo cup.
##SHARELINKS##
|
Huhtamaki, Oyj, Espoo, Finland, has agreed to acquire Josco (Holdings) Ltd., a manufacturer and distributor of paper and plastic disposable packaging products headquartered in Hong Kong and with manufacturing in China, for a debt free purchase price of EUR 67 million. With the acquisition, Huhtamaki continues to implement its strategy of quality growth and significantly strengthens its position as a global provider of foodservice packaging products. The transaction is expected to be finalized in April.
"I am extremely pleased to announce this acquisition," said Jukka Moisio, CEO of Huhtamäki Oyj. "It further strengthens our leading position in the fast growing Asian markets, particularly in China. Many of our global customers are investing heavily to grow in China, and now we are better resourced to help them grow."
Privately owned Josco is a producer of paper and plastic disposable packaging products in China and Hong Kong. The company also has significant exports to Europe, the U.S., and Australia. Its net sales in 2011 were approximately EUR 70 million and it employs some 1,350 people. The company is strategically located in China with two manufacturing units (Guangzhou and Shandong) and two distribution centers (Shanghai and Beijing). It also has sales operations in Hong Kong.
"With Josco we are able to create a superior service platform for foodservice customers in Asia," says Eric Le Lay, EVP, Foodservice Europe-Asia-Oceania. "Josco's strategic locations in China, its complementary product range, and strong network of suppliers are a perfect strategic fit to our existing foodservice business in Asia."
Jukka Moisio, CEO of Huhtamäki Oyj, noted that "Huhtamaki began packaging businesses in Asia in 1984 with paper cup manufacturing. Now in 2012 with the Josco acquisition, the Group will have altogether 12 manufacturing units in Asia, including seven flexible packaging plants across Asia and the newly started films unit in Thailand. Huhtamaki will employ approximately 4,400 people in Asia and approximately 15% of the Group's net sales in 2012 are expected to come from Asia. With such excellent positions we are ready to participate in the growth of the region."
##SHARELINKS##
|
RockTenn, Norcross, Ga., USA, this past week celebrated the grand opening of its new Marion, N.C., folding carton facility. The plant produces consumer packaging for a variety of products.
"Last summer, Governor Perdue joined us to announce the expansion of our operations here in Marion," said Mike Kiepura, RockTenn president, Consumer Packaging. "Today, it's just as exciting to be back in North Carolina to see the culmination of everyone's hard work and to open a new facility that will provide our customers with innovative, value-added products."
RockTenn has already invested almost $25 million in the new Marion facility. The plant, which completes its first full month of production on March 31, plans to add a total of 124 jobs with an average annual wage that is 10% more than current average for McDowell County. The hiring process is already underway and interested parties are encouraged to contact the Employment Security Commission of McDowell County.
"We would like to extend our thanks to all of the dedicated people at the city, county, state, and other associations that made today possible," said Steve Harrell, GM of the Marion plant. "Our goal is to continue to be the low-cost provider of folding cartons in the selected value-added markets that Marion targets, and this expansion allows us to focus on achieving that goal while better serving our customers."
In North Carolina, RockTenn has folding carton facilities in Marion, Claremont, and Conover, and its Merchandising displays business is headquartered in Winston-Salem. A total of almost 1,500 full-time and 1,800 part-time RockTenn employees call North Carolina home.
##SHARELINKS##
|
New Products
NewPage Corp., Miamisburg, Ohio, USA, this week introduced its 40 lb. (65 gsm) EcoPoint™, a new wet strength label paper offering environmental and performance advantages for the bottled water, juice, and soft drink industries. EcoPoint 40 lb. provides a notable source reduction advantage to beverage producers, with up to a 7% reduction in label paper usage compared with traditional 43 lb. (70 gsm) bottle label papers, and is designed for optimal performance in continuous roll fed labeling operations as well as cut-and-stack labeling machines.
As a new lighter weight label paper, EcoPoint 40 lb allows label printers to supply more labels per shipment to beverage bottling operations, effectively reducing both shipment frequency and storage of finished goods. Bottling line productivity also increases as more labels can be stocked in labeling equipment, resulting in longer continuous bottling runs with fewer changeovers.
EcoPoint 40 lb. joins the broader range of label papers from NewPage for beverage markets that includes DuraPoint™, ProPoint™ and LithoPoint™ product brands. In addition, NewPage manufactures specialty papers used in flexible packaging, technical, and pressure-sensitive labeling applications.
##SHARELINKS##
|
Tetra Pak, Switzerland, has unveiled four new features for its carton packaging portfolio, aimed at strengthening the environmental attributes of several of its leading products. The features, a separable top for the Tetra Evero™ Aseptic and three renewable polyethylene (PE) caps made from plant-based sources, are part of Tetra Pak's commitment to develop sustainable packaging solutions for environmentally conscious consumers, the company notes.
In partnership with Braskem, Brazil's largest petrochemical company, Tetra Pak was the first company in the global carton packaging industry to use green PE caps made from sugar cane derivatives. The new caps represent another step in the company's plans to offer packaging made entirely from renewable material.
Since July 2011, Nestle Brazil has been packing two of its milk bands (Ninho and Molico) in Tetra Brik Aseptic packages using the green PE StreamCap™ 1000. Based on this successful trial, Tetra Pak has now launched the green alternatives of another three caps, DreamCap™ 26, LightCap™ 30, and Helicap™ 27. The green caps will be distinguished from the original caps by a leaf logo that will be carried on the cap.
Following the successful launch of the Tetra Evero Aseptic, the world's first aseptic carton bottle for white milk, Tetra Pak has developed the additional functionality of a separable top. The Tetra Evero Aseptic Separable Top has a perforation in the carton board that allows the separating of a polyethylene top from the carton sleeve, making it easy for consumers to separate the top and carton sleeve and recycle them separately. The new package is entirely recyclable and made from FSC certified paperboard.
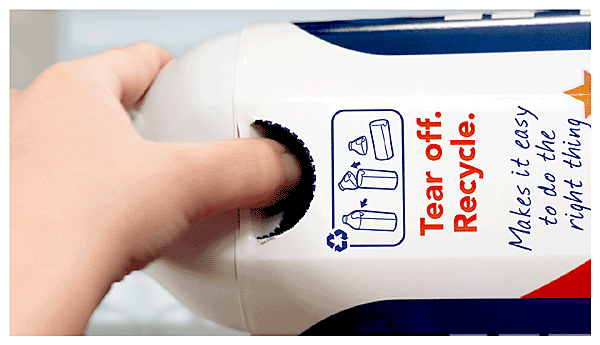
##SHARELINKS##
|
Published Pricing
Caraustar Industries Inc., Atlanta, Ga., USA, will increase prices for all of its uncoated recycled board (URB) mill converted products—pasted or laminated, sheeted, cut to size, rounded corners, and other specialty operations or packaging. The increase will be up to $40 per ton, depending on the actual requirements, and will be effective with shipments on or after April 23.
Caraustar is one of North America's largest integrated manufacturers of 100% recycled paperboard and converted paperboard products. The company serves the four principal recycled boxboard product end-use markets: tubes and cores, folding cartons, gypsum facing paper, and specialty paperboard products.
##SHARELINKS##
|
Södra, Sweden, is raising the price of its northern bleached softwood kraft (NBSK) pulp. The new price of $870 per metric ton becomes effective with shipments beginning April 1, or as contracts permit.
Södra employs some 4,000 people. The company's four business areas produce sawn and planed timber goods, interior products, paper pulp, and biofuel.
##SHARELINKS##
|
Suzano Pulp and Paper, Brazil, will increase the price for its bleached eucalyptus pulp (BEK) sold in Asia by $30 per metric ton, according to a RISI report. The new BEK price increases to $670 per metric ton beginning with shipments on April 1, or as contracts allow.
##SHARELINKS##
|
Energy
Virent, Madison, Wis., USA, and Virdia, Redwood City, Calif., formerly HCL CleanTech, this week reported to have successfully converted cellulosic pine tree sugars to drop-in hydrocarbon fuels within the BIRD Energy project, a joint program funded by the U.S. Department of Energy (DOE), the Israeli Ministry of National Infrastructure, and the BIRD Foundation. The project, which commenced in January 2011, successfully demonstrated that Virdia's deconstruction process generated high-quality sugars from cellulosic biomass, which were converted to fuel via Virent's BioForming® process.
Virent used Virdia's biomass-derived sugars to produce gasoline and jet fuel, the latter being sent to the U.S. Air Force Research Laboratory (AFRL) for analysis where it passed rigorous testing. Tim Edwards of the Fuels Branch of the AFRL said that "this fuel passed the most stringent specification tests we could throw at it (such as thermal stability) under some conditions where conventional jet fuels would fail. This fuel is definitely worth further evaluation."
"While Virent's BioForming process has previously generated fuels and chemicals from sugars in cellulosic biomass," said Virent Co-Founder and CTO Dr. Randy Cortright, "the high-quality sugars generated from pine trees using Virdia's process leveraged Virent's conversion process, establishing a viable route to drop-in hydrocarbons from biomass."
Philippe Lavielle, Virdia CEO, noted that "passing the AFRL's arduous test requirements for jet fuel further substantiates the superior value proposition of the advanced carbohydrates that Virdia is introducing. As demonstrated by the BIRD Energy project results, Virdia's CASE™ (Cold Acid Solvent Extraction) process can deliver the high-purity, cost-effective cellulosic sugars needed as the primary raw material for jet fuels and other applications. We are pleased to work with Virent to prove that the value of cellulosic biomass can be unlocked."
Virdia's CASE process encompasses a sequence of proprietary extraction and separation operations. Originally developed around the Bergius process (concentrated hydrochloric acid hydrolysis of biomass), the CASE process achieves the highest yields in the industry, and produces high purity fractions of sugars and lignin. Its low temperature and low pressure hydrolysis coupled with its closed loops of acid recovery and solvent extraction establish it as one of the most economical and environmentally sustainable processes.
Virent's BioForming platform utilizes a novel combination of catalytic processes to convert water-soluble oxygenated hydrocarbons derived from biomass to non-oxygenated hydrocarbons that can be used as drop-in compounds in gasoline, jet fuel, and diesel fuel. Virent's BioForming platform catalysts and reactor systems are similar to those found in today's petroleum oil refineries and petrochemical complexes.
##SHARELINKS##
|
People
Kimberly-Clark Corp., Dallas, Texas, USA, this week announced two key executive promotions. Christian Brickman, currently president of Kimberly-Clark Professional, has been elected president of Kimberly-Clark International, and is succeeding Bob Black, who is leaving to pursue opportunities outside the organization. Elane Stock, SVP and chief strategy officer for Kimberly-Clark, has been elected president of Kimberly-Clark Professional, succeeding Brickman. .
"We have a great team in place to drive our business plan strategies across the globe," said Chairman and CEO Thomas J. Falk. "Chris and Elane are strong leaders with excellent track records. Chris brings tremendous experience and success into his K-C International role and will continue to drive the expansion of our international business. Elane's general management and strategy experience make her the ideal successor to expand on our Kimberly-Clark Professional business aspiration to create exceptional workplaces."
Brickman joined K-C in 2008 and has led the Kimberly-Clark Professional business since 2010. Previously, he successfully guided the company through its ongoing strategic planning process and the evolution of its current Global Business Plan. Prior to joining the company, he served as a principal at McKinsey and Company. Earlier in his career, he was president and CEO of Whitlock Packaging, the largest U.S. specialty beverage packaging company, and was VP and GM of Latin America for Guinness Brewing Worldwide.
Stock joined K-C in 2010 and has served as its chief strategy officer since she joined the company. Prior to joining K-C, she served as national VP at the American Cancer Society, and was previously GM of Georgia Pacific's Color Box business. She has also held progressive management positions at McKinsey and Company both in the U.S. and Ireland.
Brickman and Stock will continue to report to Falk.
##SHARELINKS##
|
Michelman, Cincinnatti, Ohio, USA, has hired Steven Wong as managing director of Asia Pacific. Wong will be responsible for managing Michelman's Asian strategy across all of the company's industry segments in accordance with its global strategy.
According to Steven Shifman, president and CEO at Michelman, "years ago, we made a strategic commitment to creating and growing our presence in the Asian region. Over the past two years in particular, we have made great strides in adding people resources, leadership resources, global practices, and investment to support our growing business in the region. The addition of Steven Wong to our team continues that trend and we feel fortunate to have added someone of his caliber."
In his newly created position, Wong will report directly to Shifman, and will work closely with the company's global Executive Leadership Team. He will be heavily involved with Michelman's global supply chain, finance, and commercial development teams with a focus on the Asian region.
Wong brings 11 years of experience with Honeywell Corp. and most recently three years with Tennant as the managing director/GM of Asia Pacific. In his career, he has been involved in technical and commercial development, operations and general management. He also has a broad academic background with an MBA in marketing from the University of Leicester, in the U.K., an MSc in polymer science and technology from Victoria University of Manchester, Institute of Science & Technology, also in the U.K., and various other academic accomplishments.
##SHARELINKS##
|
Södra, Sweden, reports that (l-r in the photo below) Klara Helstad, Ulf Edman, Magnus Olsson, and Stefan Sandberg are taking new positions within the company, now that Urban Eriksson, president of Södra Interiör, and Per Braconier, director of communications, have decided to leave Södra. The changes will become effective May 15.
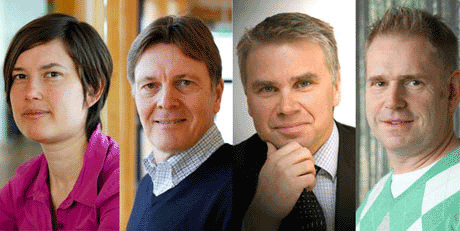
Braconier, will be leaving Södra to take a new position as director of communications for the Swedish Forest Industries Federation. He has worked for Södra since 2005, joining the company from Dagens Industri. Helstad, who was recently appointed sustainability director, will be taking over from Braconier, serving as director for sustainability and communication. She has a Doctor of Forestry and, prior to taking on this position, worked as the environmental and quality manager at Södra Skog.
Edman, currently president of Södra Cell International, will be taking over as president of Södra Interiör from Eriksson, who will be starting up a consultancy after he leaves the company July 1. Edman has worked for Södra since 1997, when he was employed as director of marketing for Södra Cell. Prior to that, he was CEO of MoDo Paper Ltd in the U.K.
Olsson, currently plant manager at Södra Cell Mörrum will be the new president of Södra Cell International. He joined Södra in 2006 after working as the CEO of Stora Enso Nymölla.
Sandberg will become the new plant manager for Södra Cell Mörrum. He is currently head of HR at Södra Timber, and was formerly head of HR and head of purchasing at Södra Cell Värö. He joined Södra in 2003.
##SHARELINKS##
|
TAPPI News
The renewable chemicals industry is gathering next week at the Renewable Chemicals Live Conference 2012, which will be held April 2, 2012 at the Capital Hilton Hotel in Washington, DC. See the growing list of registered companies on the event website.
Produced by TAPPI and Biofuels Digest, this conference is co-located with the Advanced Biofuels Leadership Conference which spans from April 3 – 5, 2012.
Renewable Chemicals Live features the top leadership in renewable chemicals, plastics and bio-based materials, featuring C-level presentations on finance, scale-up, R&D, policy and global trends.
The combination of Renewable Chemicals Live and the Advanced Biofuels Leadership Conference will provide four days of "can't miss content" - get the most for your time and money by attending both!
Learn more
##SHARELINKS##
|
Attend the Shipping, Receiving and Warehousing Workshop, in Nashville, April 2-4, 2012, and learn new ways to improve your bottom line. Be a part of this dedicated group of mills, carriers, warehouses and printers as they collaborate to reduce in-transit damage to rolls of paper at this premier forum for industry leading paper shippers.
This is truly a practical, interactive and collaborative shipping and receiving workshop put on by industry professionals, for industry professionals - all parties of the supply chain - to address common issues and concerns relating to damage and damage prevention in the paper industry. It's an excellent networking opportunity - paper buyers, paper companies, carriers, securing / damage prevention specialists, block and bracing manufacturers, safety experts all under one roof. Learn more about TAPPI's Shipping, Receiving and Warehousing Workshop.
##SHARELINKS##
|
PaperCon Discounted Registration available until March 30
Register now for best rates to attend this important industry event, April 22-25 in New Orleans.
PaperCon is where CEOs, mill managers, superintendents, scientists, process engineers and suppliers gather to learn and network. Program tracks include Papermakers, Coating and Graphic Arts and PIMA Management. The PaperCon program also features: Inside and outside the box: Optimizing paperboard grades , the Sustainability Forum , an Executive Panel Discussion , a Young Professional Program , Coating 101 Course and other practical workshops and seminars and features the largest PaperCon exhibit ever. Bonus Sessions (open to all PaperCon registrants) Control Systems 2012: The first USA appearance for this highly-rated biannual conference. RPTA Production-Technical Seminar , the OpEx Reliability Seminar .
In addition, PaperCon 2012 will feature two Keynote Speakers: Jeffrey Hayzlett , Bestselling Author, Global Business Celebrity and Sometime Cowboy will address the crowd on Monday, April 23 in the Opening Session and Lisa Bauer Lotto, M.S., Director, Environmental and Sustainability Programs, Green Bay Packaging Inc., will kick-off the Coating program during a special session on Sunday, April 22. Learn more about PaperCon
##SHARELINKS##
|
Nominations for the major TAPPI 2013 awards are due by August 1, 2012.
The awards that may be presented in the upcoming year are:
Gunnar Nicholson Gold Medal Award - The Association's highest technical honor may be presented annually to recognize an individual or individuals for preeminent scientific and engineering achievements of proven commercial benefit to the world's pulp, paper, board, and forest products industries and the other industries that TAPPI serves.
Herman L. Joachim Distinguished Service Award - The Association's highest award for service, may be presented annually to recognize leadership and service which have significantly and demonstrably contributed to the advancement of the Association.
Paul W. Magnabosco Outstanding Local Section Member Award – The highest honor for Local Sections may be presented annually to recognize an individual for outstanding leadership and exceptional service to one or more Local Sections, which have resulted in significant and demonstrable benefits to the Local Section members.
TAPPI Fellow - TAPPI Fellows are Individuals who have been members of TAPPI for not less than 10 years prior to the nomination, and who have contributed meritorious service to the Association and/or the paper and related industries. Retiring members of the TAPPI Board of Directors become Fellows automatically at the end of their term.
The TAPPI Awards and Honors page has links to these awards which will show the qualifications required and links to the nomination forms that must be completed. You may submit all nomination forms by email to standards@tappi.org, or you may fax them to the attention of the awards department at +1-770-446-6947, or send by mail to TAPPI, Awards Department, 15 Technology Parkway South, Norcross, GA 30092, USA.
##SHARELINKS##
|
Engineers involved in paper making wet end chemistry will want to mark June 4-6 on the calendar. The 2012 TAPPI Introduction to Wet-End Chemistry course takes place soon at TAPPI headquarters in Norcross, Georgia, USA. This course will help you get up to speed on the latest technology and terminology you need for optimum papermaking performance.
Instructors for this course know that cost savings is ultimately your mark for a strong finish, so they focus the 3-day interactive training on innovative wet-end chemistry principals and the use of additives to change or create new paper products.
Through case studies, break-out sessions and networking with others in the course, you'll learn how to: · Implement new technology into your mill's wet-end process to reach higher efficiency and yield consistent, quality products ·
Use chemicals and other additives to change or create new products and maximize machine capacity ·
Put the brakes on machine downtime and off-specification products ·
Make better judgments on selection and use of papermaking chemicals ·
Better troubleshoot problems on the paper machines ·
Get up to speed on the challenges papermakers face due to changing fiber qualities, regulations and competitive pressures
View the Workshop Schedule to see the specific topics covered.
This introductory- to intermediate-level course is designed for those in pulp and paper manufacturing facilities with job responsibilities, such as chemical and process engineers, mill superintendents, research and development engineers, technology and chief chemists, R&D vice presidents, process and quality control technicians and suppliers involved with the wet end processes.
##SHARELINKS##
|
Registration is underway now for the TAPPI Hands-On Workshop for Pulp and Paper Basics June 4-8, 2012 at North Carolina State University in Raleigh, North Carolina, USA.
Register here to reserve your seat. The number of students in the course will be limited in size - to 32 - for maximum effectiveness and registrations will be accepted in the order they are received.
If you're wondering whether this course is right for you, it probably is! It's an essential course that teaches the basic concepts in pulp and paper manufacturing and is designed for anyone wanting to improve their role in operations. Learn more.
This workshop is especially beneficial for:
- New process engineers, manufacturing operators and technicians who want to understand more fully how raw materials are processed into products
- Individuals who wish to broaden their knowledge of the processes through basic laboratory and pilot paper machine experiences •
- Sales and service personnel, machine operators, and maintenance personnel who need to better appreciate paper machine operations by conducting a pilot paper machine trial
- Individuals who have completed TAPPI's Introduction to Pulp and Paper course and who want to benefit from the laboratory and pilot plant experiences
Previous participants said:
"The information was detailed and easily understood by both engineers and non-engineers. I will definitely suggest the course to others."
"This is an excellent course; providing an intense overview of the entire papermaking process."
Workshop Materials: Participants will receive a course notebook and CD with approximately 400 pages of reference materials.
Earn CEUs: You'll earn 3.7 continuing education credits at the completion of this June 4-8 course. It's a lovely time to be in North Carolina.
##SHARELINKS##
|
Pigments for Paper
Robert W. Hagemeyer, Editor
John E. O'Shea, Task Group Chairman
This comprehensive text covers all aspects of pigments for paper. This unique book can serve as an introductory text as well as a practical reference. Well-respected industry experts who are specialists in their area wrote each of the twelve chapters. This text provides the most current information on different ingredients, describing what they do and how they perform. It is a valuable reference tool for everyone involved in paper coating. Pigments for Paper
View the Table of Contents
Product code: 0102B062
Member Price: $103.00
Non-Member Price: $155.00
##SHARELINKS##
|
Join the World's Process Control Experts in New Orleans
The 15th Control Systems Conference will bring together the world's preeminent experts in pulp and paper process measurement, control and systems engineering. The exceptional program emphasizes both practical implementation and leading research.
Control Systems 2012 will be held April 22-25 in conjunction with TAPPI's PaperCon 2012, the largest pulp and paper technical program in the world and Control Systems 2012 attendees have access to the PaperCon Sessions and Trade Fair. Discounted registration is available through March 30.
Keynote Address: "What's Hidden in your Data? Sensor-Fusion and Signal Processing for Process and Performance Monitoring" - Sirish L. Shah, Department of Chemical and Materials Engineering, University of Alberta
Topics include:
- Web Imaging and Inspections ·
- Millwide Applications
- Paper Machine Optimization and Grade Change
- Paper Machine CD Applications
- Sheet Quality Measurement
- Pulp Mill Sensors
- Pulp Mill Controls
- Diagnostics and Analysis
- Process Control New Technology Showcase
Learn more about the Control Systems 2012 program.
##SHARELINKS##
|
Make the most out of your time at PaperCon by attending one or more of these workshops or seminars. Additional registration is required for each.
Essentials of Market Pulp Course
Wednesday, April 25
Instructor: Alan F. Button, PhD, World of Market Pulp
Gain a broad understanding of current pulp trends in the global marketplace, understand the unique nature of pulps through the study of a large cross-section of samples from all over the world, and initiate a simple, efficient evaluation process for smart pulp selection. Learn more.
Coating 101 Course
Saturday and Sunday, April 21-22
Taught by TAPPI coating experts from both the supplier and manufacturing backgrounds, this course is designed for commercial professionals needing a technical knowledge base, professionals new to the paper industry, young professionals that are recent graduates or new to coating, or professionals new to coating who've spent their career in other parts of the paper industry. Learn more.
Eliminating Cost while Enhancing Customer Value
Sunday, April 21
Instructor: Christopher W. Miller, PhD, NPDP, President, Innovation Focus, Inc.
A customer-centered and creative approach to value analysis (the Unilever approach), this one-day workshop will help you unleash the power of your organization. Learn to design a customer-centered cost reduction project; facilitate an effective cost reduction effort; and how to select tools and techniques that will help you and your team be more customer-centered. Learn more.
Stickies Workshop Sunday
April 21
Instructor: Dr. Mahendra Doshi, Editor, TAPPI Journal and Progress in Paper Recycling Designed for engineers, scientists and technicians who want to a better understanding of stickies and related issues, anyone working in recycling mills, using recycled pulp or supplying equipment, chemicals or recovered paper to recycled mills will greatly benefit from attending. Learn more.
##SHARELINKS##
|
This information-packed volume provides practical, industrially focused approaches to operational issues, and includes a first-ever, complete examination of the ongoing environmental and staging changes that occurred after the discontinuation of chlorine usage in 1996. Written to assist production engineers, supervisors and scientists find quick solutions to today's immediate problems, The Bleaching of Pulp (5th Edition) is designed to help both novice and seasoned professionals quickly understand a wide range of operational issues
Authors Alan W. Rudie, Ph.D., and Peter W. Hart, Ph.D., have delivered the industry's premier text on bleaching technologies. Pre-order your copy today and pay only $110, a savings of more than 50% off the May release list price of $232 (TAPPI members: $155). Or, contact TAPPI's Member Connection or call, +1 800 332-8686 (US), 1 800 446-9431(Canada), or +1 770 446-1400 (Worldwide).
But hurry, this offer ends April 30th!
##SHARELINKS##
|
2012 Pulp and Paper Manufacturers Association Annual Meeting in May The Pulp and Paper Manufacturers Association (PPMA) Annual Meeting and Conference will be held May 9-11, 2012 at the Intercontinental Hotel in Milwaukee, Wisconsin. PPMA provides human resource information to the pulp, paper, converting and allied industries. The meeting includes a program of expert speakers covering topics such as labor law, training and health care, extensive networking opportunities and updates on key industry research including an annual salary survey.
"The 2012 Annual Meeting will provide attendees with helpful information that can be used to improve business performance, including results from our annual salary surveys and other human resource information," notes PPMA Executive Director, Dick Kendall. "In addition, we have a strong speaker line-up including David Scheible, CEO of Graphic Packaging, who will share his views and insights on how to sustain results in a tough economic and business climate."
The theme of this year's conference is "On the Anvil." Key topics that will be covered include: how to discuss and implement a labor/management committee to help efficiency; update on current health care discussions across the U.S.; current labor law developments; OSHA rules and their impact on union and non-union operations. In addition, a review of how to use the National Network for Pulp and Paper Technology Training (NPT2) training resource will be provided.
A wide range of key trends in the industry will be addressed by an outstanding program of speakers including: David Scheible, CEO, Graphic Packaging International; Dan Murphy, Labor Law Expert; Dennis Smith, Secretary of the Department of Health Services; Daniel Van Wychen, Commissioner, Federal Mediation and Conciliation Service (FMCS); T.J. Murphy, Executive Director, NPT2, Mike Lies, Partner at Seyfarth Shaw LLP, Professor Emeritus C.Y. Allen and Eric Hobbs, partner at Michael Best & Friedrich Law Firm.
##SHARELINKS##
|
|
|