Over the Wire
TAPPI
Weekly Spotlight
Boise Inc., Boise, Id., USA, has chosen the location of the next urban park developed by Project UP in Baltimore, Md. Funded through sales of Boise ASPEN® Recycled Papers, Project UP works to transform distressed urban spaces into vibrant community parks in partnership with Alliance for Community Trees (ACTrees).
"Boise is excited to be contributing to the beautification of such a historic area of Baltimore," said Terry Stepney, Boise brand manager. The future park site is a one-acre corner lot that has been cleared of 12 abandoned row homes. "This unique and highly visible area represents an opportunity to bring a public green space to what is currently a reminder of less prosperous times for the community," Terry said.
Project UP and ACTrees will coordinate the park development with local non-profits, Parks & People Foundation, as well as Humanim Inc. "So many partners in Baltimore understand the urgent need for green space to help enhance the city's infrastructure, watershed, and community health. We're thrilled to work with local organizations to create a valuable new resource for this neighborhood," said Carrie Gallagher, ACTrees executive director.
This project will be the second for Project UP. Founded in 2011, Project UP completed its first park in Indianapolis, Ind., with more than 100 trees and plants, a walkway, and public benches. More than 70 volunteers gathered for a community planting day on Sept. 24, 2011, and Mayor Gregory Ballard of Indianapolis declared the day 'Project UP Day'. In addition, Project UP sponsored National NeighborWoods Month, a program led by ACTrees that celebrates greener communities nationwide with hundreds of tree planting projects throughout the month of October. Project UP will continue to be a sponsor of National NeighborWoods Month for 2012.
##SHARELINKS##
|
U.S. manufacturing grew in April at the strongest rate in 10 months, easing concerns the economy had lost momentum at the start of the second quarter, according to a Reuters news report this week. The Institute for Supply Management (ISM), New York, N.Y., USA, reported this past Tuesday that its index of national factory activity rose to 54.8 from 53.4 in March. The figure bested expectations for a decline to 53.0 and came in above the top end of forecasts in a Reuters poll. A reading below 50 indicates contraction in the manufacturing sector, while a number above 50 means expansion.
"The view on the economy has swung from optimism to pessimism of late and this could bring us back to the middle," Nick Bennenbroek, head of FX Strategy for North America at Wells Fargo, was quoted in the Reuters report. "ISM suggests there's no real reason to get too concerned about the path of the U.S. economy at this point," he added.
ISM's gauge of employment also rose to its highest since June, to 57.3 from 56.1. The forward-looking new orders component racked up its best reading in a year at 58.2, up from 54.5.
The strong labor figure comes ahead of the larger government nonfarm payrolls report due tomorrow (Friday, May 4), which is forecast to show the economy added 170,000 jobs last month, including 22,000 manufacturing positions. The ISM report was in contrast to some regional manufacturing reports, including Chicago this past Monday, that had showed the rate of growth slowed last month. It also bucked the trend of recent data that suggested the economy lost some steam as the second quarter got under way, highlighting the bumpy nature of the recovery, Reuters noted.
The economy grew at a 2.2% rate in the first quarter, a step back from the 3% pace logged in the final months of 2011.
Construction spending edged up 0.1% to an annual rate of $808.07 billion, according to the Commerce Department, after a revised 1.4% drop in February. Economists polled by Reuters had expected construction spending to rise 0.5%.
##SHARELINKS##
|
Scotland-based Tullis Russell Papermakers and RWE npower renewable recently flew three local students to Finland on a special, all-expenses-paid exchange visit. The student trainees, all from Adam Smith College with various campuses across the county of Fife in Scotland, were selected to work with cutting-edge technology at Metso Power facilities in Tampere, Southern Finland, that will be used with a boiler system Metso is constructing to power RWE npower renewables' £200 million state-of the-art biomass plant at its Markinch site in Scotland. The new plant will supply all of Tullis Russell's steam and electricity requirements, reducing the paper mill's fossil fuel carbon dioxide emissions by some 250,000 metric tons per year.
The students spent a week with Metso Power experts. They were briefed on the boiler's automation systems and given the opportunity to get hands-on experience with the technology by assisting with a program of tests. The trip for the three NC Electrical installation (pre-apprenticeship) students formed part of their second work placement at the biomass plant. The boiler is a key component to the successful implementation of the power plant, and the student's involvement helped to provide them with a greater insight into the industry and the pioneering technology being used at the power plant.
Peter Wilson, project manager, from RWE npower renewables said that "Metso Power is a global supplier of sustainable technology, and the manufacture of the boiler and gas cleaning systems are at the heart of the biomass plant. The three lads have shown great enthusiasm throughout their time with both ourselves and Tullis Russell, and we would like to thank Metso Power for giving them the opportunity to see first-hand how the control systems are put together."
Metso's Peter Anson noted that "the student's attitude about the work throughout the week was excellent; they were very keen to learn and applied themselves well to the tasks. We have since sent all three testimonials that they will be able to take with them into their working lives. All three are a credit to Adam Smith College, and we are delighted to have been able to help facilitate this visit for them."
The three students—Michael Wilson (17) and Jamie Forrest (21) from Glenrothes, and Kieran Finnegan (17) from Leven—have successfully completed block two of their work placement, with the final block due to commence in May. All have rotated between the new biomass plant and Tullis Russell's papermaking facility, ensuring they get a wide range of skills and experience throughout their time.
The Biomass Combined Heat and Power (CHP) plant is scheduled to be fully operational in mid-2013, creating up to 40 permanent jobs at the plant and at the offsite fuel processing plant at Cardenden. During construction, more than 400 temporary jobs have been created. I
In the photo below (l-r) are Tony Dawson from RWE npower renewables, Metso's Peter Anson, and the three students: Jamie Forest, Michael Alexander Wilson, and Kieron James Finnegan. Metso's Tiina Kaunisto is pictured at the front
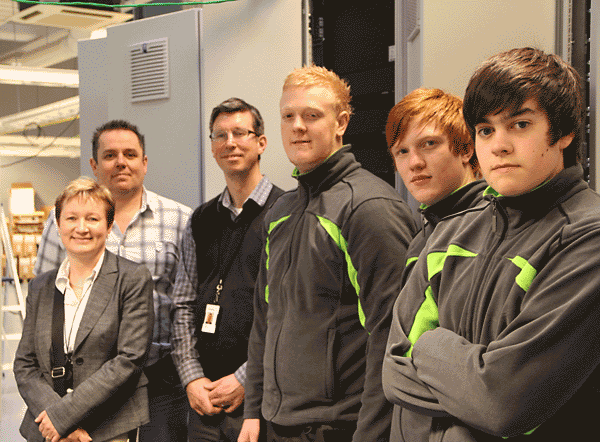
##SHARELINKS##
|
Market Roundup
During the past decade, China's fast expanding economy and boom in housing starts lifted the country to being the world's largest importer of sawlogs and the second largest importer of softwood lumber, after the U.S., according to the Wood Resource Quarterly ( WRQ), Seattle, Wash., USA. China has increased the importation of logs and lumber practically every year for more than 10 years, with lumber imports in 2011 being 15 times higher than in 2001 and log imports being up three-fold from 10 years ago.
The total value of China's imported logs and lumber increased from $630 million dollars in 2001 to almost $8 billion dollars last year. This constant upward trend in importation came to a halt in late 2011 when construction activities slowed and inventories of logs and lumber at many Chinese ports reached very high levels. As a result of lower demand for wood products, softwood log import volumes during the first three months of 2012 were down 11% from the same period last year, WRQ notes.
Log shipments from the two largest supplying countries, Russia and New Zealand, have declined by 16% and 17%, respectively, from a year ago. However, not all log suppliers to China have been hit by the reduced log demand in the country. Both Canada and the U.S. have increased exports dramatically the past few years, and this trend continued into the first quarter of 2012, when exports from Western Canada were up 23% from 1Q/11 and U.S. shipments were 2% higher than in early 2011.
North American log exporters have gained considerable market shares since 2009 when about 1 million cubic meters of softwood logs were shipped, which accounted for only 5% of the total imports to China. In 2011, the volume reached a new high of 7.1 million cubic meters, which was 22% of all imported logs to the country last year, WRQ reports. Softwood lumber imports have shown a similar trend to that of logs, it adds. In 1Q/12, North American softwood lumber accounted for as much as 55% of all imports, up from only 25% in 2007.
China is likely to continue to rely heavily on North America for particularly lumber but also increasingly for logs over the next few years. When the U.S. housing market, and as a consequence, lumber demand, eventually improve, available wood supply will tighten and costs for logs and lumber are likely to go up. This expected scenario may change how China sources logs and lumber in the future, WRQ says.
##SHARELINKS##
|
There is some encouraging news for pulp producers, reports Mark Wilde, senior analyst with Deutsche Bank. Global pulp shipments in March were off 3.8%, mainly on lower volumes to Europe and North America, he notes, adding that Chinese demand remained very strong. The "good news?" Inventories on a "days-of-supply" basis dipped two days for softwood (29 days) and one day for hardwood (34 days), Wilde says.
##SHARELINKS##
|
Pulp & Paper
Atlas Holdings, Greenwich, Conn., USA, has acquired Elmwood Park, N.J.-based Marcal Paper Mills, a tissue and paper products manufacturer and distributor, and renamed it Soundview Paper Co. Soundview will continue the mill's production of towel and tissue products for the at-home and away-from-home markets in North America. Located 15 miles northwest of New York City, Soundview's operations encompass more than 1 million sq ft of manufacturing and storage facilities on its 30-acre site. Operations include a manufacturing facility with fully integrated deinking, towel, tissue, napkin, and facial production and converting capabilities, as well as separate storage facilities for housing finished goods and parent rolls.
"We plan to focus on superior customer service and product excellence by building on the quality of our people, our equipment, our papermaking skills, and our core brand, Marcal," said George Wurtz, CEO of Soundview Paper Co. "Soundview's leadership team is comprised of industry veterans with unparalleled experience in the tissue business. With the strong focus and high standards of this team, Soundview is well-positioned to transform this business, better serving our customers." Wurtz's paper industry background includes EVP at Georgia-Pacific.
"We are excited about the acquisition of Marcal by Soundview," said Tim Fazio, managing partner at Atlas Holdings. "Soundview fits well with our core investment strategy of investing in and revitalizing businesses that are critical to the markets they serve. The Soundview employees have unmatched tissue industry experience and are a welcome addition to the Atlas family.
"While there are certainly challenges inherent to running a successful manufacturing business in New Jersey, we believe New Jersey's pro-growth policies create an environment in which we can save and eventually grow this important business," Fazio added.
Atlas Holdings owns and operates more than 70 facilities with nearly 8,500 employees worldwide. Its businesses are engaged in a broad spectrum of industries, including pulp, paper, and tissue manufacturing, food and agriculture, wood products and building materials, packaging, capital equipment, and industrial and business services.
##SHARELINKS##
|
Canfor Corp., Vancouver, B.C., Canada, this week announced that it will proceed with capital improvement projects totaling some $40 million at its sawmill facilities in the Kootenay region of British Columbia. These investments represent the first major component of a multi-year capital investment program aimed at enhancing productivity and cost performance in the company's Southern Interior mill facilities.
The announced investments are focused on the Radium Sawmill in the community of Hot Springs, B.C. Approximately $38.5 million will be invested in a new planer facility, the installation of a biomass energy system, and modifications to the existing sawmill. The balance will be invested at the company's Canal Flats sawmill to improve drying capacity.
The Radium mill project will begin this month, with startup expected in the fourth quarter.
##SHARELINKS##
|
For the second time in recent weeks, Catalyst Paper, Richmond B.C., Canada, has changed the date for meetings of its secured and unsecured creditors to consider the plan of arrangement under the Companies' Creditors Arrangement Act of Canada. The date has now been moved form May 2 to May 15, allowing additional time for Catalyst to consider feedback from its trade and other creditors and to advance discussions to gain further support for the restructuring.
"We are taking the additional time to work through a very complicated process and to ensure the many interests involved are fully considered. We are continuing our efforts to bring a consensual deal to a satisfactory conclusion," said Kevin J. Clarke, president and CEO. The court date to sanction and approve the plan of arrangement has also been rescheduled from May 7 to May 18.
##SHARELINKS##
|
Andritz, Graz, Austria, reports that it has successfully started up the steel yankee and headbox supplied to a customer in Indonesia for a new MG paper machine. With a shell length of 7.4 m, this steel yankee is currently the longest of the world, Andritz notes.
In addition to the PrimeDry Steel Yankee and the headbox, Andritz also delivered core components for the approach system and the dilution water control equipment.
The headbox (PrimeFlow SW) has been newly developed for the use on fourdrinier wires and hybrid formers. With this technology, the step diffuser and the lamella nozzle generate micro-turbulence to obtain optimum formation and evenness of the sheet. Andritz adds that the mechanical design, manufacturing precision, and dilution water system (PrimeProFiler F) guarantee excellent cross-direction profile.
##SHARELINKS##
|
JSC Arkhangelsk Pulp and Paper Mill (APPM), Russia, has ordered from Andritz, Graz, Austria, equipment for a new semi-chemical pulp line for its Novodvinsk mill in Russia. The green liquor cooking and washing technology by Andritz will improve the fiber quality and reduce effluents, as well as lower production costs. Startup is scheduled for the second quarter of 2014.
The scope of supply includes the chip washing system, the cooking plant with continuous steam-phase digester, flat disc refiners, washers, screw presses, electrical equipment, and instrumentation and control systems. The new plant will use birch and aspen as the raw material to produce 1,000 metric tpd of fluting and testliner pulp grades, doubling the mill's current capacity.
##SHARELINKS##
|
Mercer International Inc., New York, N.Y., USA, reports that its offer for all of the common shares of Fibrek Inc. expired on April 27. The Offer was conditioned upon, among other things, at least 50.1% of the outstanding Fibrek Shares, on a fully-diluted basis, having been tendered there-under, which was not met as of the Expiry Time. Accordingly, Mercer and MERC Acquisition Inc. will not acquire any Fibrek Shares that were tendered under the offer.
The company adds that the support agreement between Mercer and Fibrek dated February 9, 2012, as amended, has thus been terminated. All Fibrek Shares that were previously tendered under the offer and not withdrawn will be returned promptly.
##SHARELINKS##
|
Saigon Paper Corp. one of the leading Vietnamese producers of tissue and board, has started up a new Andritz (Graz, Austria) tissue machine. With a speed of 1,650 m/min, the 2,850 mm wide PrimeLineCOMPACT tissue machine has an annual production capacity of 25,000 metric tons.
The Andritz scope of supply included the complete tissue machine, from stock preparation to the finished reel (including automation), as a modularized plant that is easy to configure, install, and operate, as well as a PrimeDry steel yankee (3.66 m dia.) that is used to enable high production capacity and high operational safety.
##SHARELINKS##
|
Tembec, Canada, has ordered from Andritz, Graz, Austria, a new SulfitePower boiler plant for its Témiscaming, Qué., pulp mill. Startup is scheduled for the final quarter of 2013.
For this order, Andritz Energy & Environment (AE&E) will provide the boiler pressure part and steel structures, liquor and gas burners, fan, air preheater, air and flue gas ducts, and the soot blower. In the power boiler plant, 78.5 metric tons of liquor will be burned and 222 metric tons of high-pressure steam will be produced per hour. A turbine with an output of 50 MW will generate energy that will be supplied to the public grid as green electricity. Ammonium bisulfite will be recovered in a subsequent flue gas cleaning plant.
With this environmentally friendly investment and the additional revenue from the sale of electricity, Tembec is safeguarding its location in Témiscaming in the long term, the company notes.
##SHARELINKS##
|
UPM, Finland, has awarded a contract for detail engineering on its biorefinery project at Lappeenranta, Finland, to Pöyry's Industry business group. The parties have agreed not to disclose the value of the assignment.
Finland-based Pöyry's engineering assignment includes services for civil and plant engineering, project control, procurement, document management, and industrial safety. The services will be carried out during 2012 - 2014.
The Lappeenranta Biorefinery is UPM's first step in its strategy towards being a key player in advanced biofuels production and therefore a vital part of UPM's Biofore strategy.
##SHARELINKS##
|
Containerboard/Packaging
Cascades Inc., Kingsey Falls, Qué., Canada, this week announced the consolidation of its corrugated product plants in its Norampac division in Ontario, Canada. The consolidation translates into an investment totaling in excess of $30 million in the Vaughan, St. Mary's, Etobicoke, and Belleville plants, and the closure of the North York and Peterborough units, as well as the OCD plant in Mississauga.
"The purpose of this restructuring is to optimize productivity in our corrugated product plants in Ontario and enhance customer service. These steps are in line with our regional development strategy, which includes the recent acquisition of three Bird Packaging plants," explained Marc-André Dépin, president and CEO of Norampac.
As part of the strategic plan set in motion by Cascades, this consolidation aims to improve the group's profitability in an increasingly competitive market. This decision is another step in a series of initiatives taken over the past years that seek to modernize the company's assets. With this goal in mind, Cascades announced in June 2011, the construction of Greenpac Mill LLC, a lightweight containerboard mill located in Niagara Falls, N.Y., USA.
With this investment of more than $30 million, Norampac aims to modernize manufacturing equipment in the four Ontario plants and increase production capacity, profitability, as well as productivity.
"We are investing for the future by taking the necessary measures to strengthen our leadership in the market and demonstrate our commitment to our clients," Dépin said. "The Vaughan, St. Mary's, Etobicoke, and Belleville plants have the ideal infrastructure in which to incorporate new equipment with cutting edge technology, ranking them among the most competitive in Canada. These investments will enable us to provide clients with a wider variety of packaging products, increase the speed of execution, and improve the quality of our products and services," he added.
In a competitive packaging market, which is strongly influenced by the strength of the Canadian dollar and enhanced competition from U.S. manufacturers, Norampac has no choice but to reduce its operating costs through the closure of three corrugated product plants in Ontario, the company noted.
"The decision to close the OCD, North York, and Peterborough plants can be explained by a decrease in demand in the Canadian and North American corrugated products industry dating back to the beginning of the recession, as well as the large number of Norampac converting plants in Ontario. These factors, combined with adverse economic conditions, have forced us to restructure our assets to be more competitive," Dépin noted. The three operating units are scheduled to close at the end of 2012.
The OCD, North York, and Peterborough plants are specialized in converting corrugated products. In preparation for the closures, production from these plants will gradually be redirected to other Norampac converting plants in the province, which will continue to supply the plants' clients with the same quality and services. Many of the 200 employees from the three plants will have the opportunity to transfer to other Norampac plants in Ontario.
"As was the case in Québec in 2010 and in the northeast of the U.S. in 2011, the consolidation of our Norampac operations in Ontario, to which we are adding significant investments to modernize our facilities, will allow us to optimize our assets in this region and improve Cascades' performance," Dépin said.
##SHARELINKS##
|
M-real, Finland, has now changed its name to Metsä Board, following the decision at the company's annual meeting last month.
Metsä Board is part of the Metsä Group (earlier Metsäliitto Group) of Finland, and the parent company is Metsäliitto Cooperative. Metsäliitto is owned by 125,000 Finnish forest owners. The new name and identity give Metsä Group a common identity to strengthen its visibility in the market, the company notes.
"Over recent years we have worked hard to transform from a paper company to a profitable paperboard company," said Mikko Helander, CEO of Metsä Board. "Our structural transformation is at a stage where we want to communicate it with the new company name, Metsä Board."
Metsä Board is made up of two business areas—Paperboard and Paper and Pulp.
##SHARELINKS##
|
MeadWestvaco Corp., Richmond, Va., USA, this week announced the final exchange ratio for the spin-off and subsequent merger of its Consumer & Office Products Business with ACCO Brands Corp. In addition to retaining the shares of MeadWestvaco common stock they currently own, MeadWestvaco stockholders will receive .32986547 shares of ACCO Brands common stock for each share of MeadWestvaco common stock they owned of record as of April 24.
No fractional shares of ACCO Brands Corp. will be issued; MeadWestvaco stockholders will receive cash in lieu of any fractional shares. The spin-off and merger became effective May 1. Following the merger, ACCO Brands common stock will trade under the ticker "ACCO" on the NYSE.
##SHARELINKS##
|
SCA, Stockholm, Sweden, reports that it has accepted UK-based DS Smith's formal offer to acquire its packaging operations in France, following consultations with appropriate works councils. As a result, a sale and purchase agreement has been signed by both parties.
SCA had announced this past January that its packaging operations, excluding two kraftliner mills in Sweden, would be sold to DS Smith. The agreed purchase price totals EUR 1.7 billion on a debt free basis. Closing of the transaction is expected to take place in the second quarter.
##SHARELINKS##
|
UPM Raflatac, Finland, has begun full-scale production at its new specialty products factory in Fletcher, N.C., USA, providing the company with narrow-web coating capabilities and capacity to develop specialty labelstock solutions for demanding end-uses. The company noted that the facility also allows it to deliver on a promise of becoming a full product line supplier to its diverse industry customer base,
The specialty products factory will supply labelstock products for end-uses such as security, pharmaceutical, food, tire, and durables labeling and ultra removable applications. It also will provide coat-to-order services and run small orders. This factory is located just a few miles from UPM Raflatac's existing labelstock manufacturing facility in Mills River, N.C., allowing the company to streamline its logistics processes, accelerating production and order delivery.
"With our new label solutions center, UPM Raflatac achieves its vision of offering a full range of standard Prime, VIP, and Specials products to our customers," says Jouko Lähepelto, SVP, Americas & Asia Pacific. "We can now provide labelstock converters with the industry know-how and production tools they need to supply specialty products to market-leading brand owners."
UPM Raflatac, part of UPM's Engineered Materials business group, is a global supplier of self-adhesive label materials. UPM Raflatac has a global service network consisting of 13 factories on six continents and a broad network of sales offices and slitting and distribution terminals worldwide.
##SHARELINKS##
|
New Products
Sentinel Bioactive Paper Network funded researchers at McMaster University, Hamilton, Ont., Canada, have developed a rapid testing method using a simple paper strip that can detect E. coli in recreational water within minutes, according to a report this week by TKX Inc. The new tool reportedly can close the gap between outbreak and detection, improving public safety globally.
Scientists have created and validated the viability of the test strip, which can detect potentially harmful concentrations of E. coli in water quickly and simply, with much greater accuracy than existing portable technology, TKX reports. The work is described in a paper published online in the journal Analytical and Bioanalytical Chemistry.
The Natural Sciences and Engineering Research Council of Canada (NSERC) funds Sentinel Bioactive Paper Network, a strategic research network that spans Canada and is based at McMaster University. Several dozen researchers are involved in its initiatives to detect, repel, and deactivate air, water, or food-borne pathogens to improve human health and safety.
The new strips are coated with chemicals that react to the bacteria, and are printed using inkjet technology similar to that found in standard desktop printers. Within 30 min. of sampling, the paper changes color to indicate the presence of E. coli, with colors coded to represent different forms and concentrations of the bacteria.
Field testing of the prototype strips is planned or under way in Canada and across the globe, in regions where untreated water poses particular health hazards. The results of these studies will help to refine the test strips and may lead to strips that are sensitive enough to tell whether water is safe enough to drink.
The next stage of pre-commercial development of the test strips is already funded by NSERC through a Phase I Idea to Innovation grant. Commercialization of a final product could take as little as two to three years.
More information is available online.
##SHARELINKS##
|
Published Pricing
Billerud, Solna, Sweden, this past week announced that it will increase the price of sack and kraft paper. The EUR 80 per metric ton increase will become effective with shipments beginning June 1.
Billerud produces packaging and specialty papers, packaging boards, and market pulp. It operates three pulp and paper mills in Sweden (Gruvön, Karlsborg, and Skärblacka) and one in Beetham, U.K.
##SHARELINKS##
|
Mondi, U.K., will increase the price for its unbleached and bleached sack kraft grades in Europe by 8% to 10%, effective with deliveries beginning June 1. Also, prices for Mondi Europe's overseas markets will be increased to bring them back to the same levels as in 2011, the company noted.
Mondi has operations in Europe, Russia, and South Africa, and employs some 23,400 people in 28 countries.
##SHARELINKS##
|
People
TimberWest Forest Corp., Vancouver, B.C., USA, has appointed Brian E. Frank president and CEO, effective May 2. Frank comes to TimberWest with an extensive background in the natural resources industry at the executive level, most recently as chief executive of Global Oil Europe and Finance for BP in London, England. He has also recently held the positions of president, BP Energy Co. in Houston, Texas, and president and CEO of BP Canada Energy Co. in Calgary, Alberta. Frank also spent 10 years at Natural Resources Canada in Ottawa and has the benefit of extensive private and public sector experience.
Frank replaces Bev Park who served as Interim president and CEO following the sale of TimberWest to private owners in 2011.
##SHARELINKS##
|
TAPPI News
Registration rates for the 2012 TAPPI International Conference on Nanotechnology for Renewable Materials are due to increase on May 7.
Register this week to take advantage of the discounted rates.
The conference, June 4-7, 2012 at the Hyatt Regency Montreal in beautiful Montreal, Que., Canada, will feature 28 sessions under the theme of Brining New Dimension to Sustainable Business Solutions.
Registration for this not-to-miss event includes a tour of CelluForce, the world's first NanoCrystalline Cellulose (NCC) plant located in Windsor, Que., on Monday, June 4, 2012. In addition, if you are one of the first 100 people to register, you will enjoy dinner at Vieux-Port Steak House followed by Cirque Du Soleil's Amaluna on Wednesday, June 6.
View the Conference Brochure or learn more about the conference including registration information online.
##SHARELINKS##
|
If you haven't yet registered for the TAPPI Introduction to Wet End Chemistry Course, you can still take advantage of the early registration savings through May 7. But, don't wait too long. Seating is limited.
This course is the only one of its kind in the world -- and is taught by three highly respected experts in paper chemistry who will help you understand how wet end additives can differentiate your products. Bring your team up to speed on the latest technology and terminology in this important process in papermaking.
2012 TAPPI Introduction to Wet-End Chemistry- June 4-6, 2012
Norcross, Ga. USA
This unique training program offers an in-depth focus on chemical additives and what you can and can't do to help you save costs, increase machine efficiency and product better paper products. Participants will learn how to:
- Implement new wet end technology to reach higher efficiency and consistent, quality products
- Use additives to improve or create new products
- Reduce downtime and off-spec production
- Make better judgments on selection and use of chemicals
- Troubleshoot problems and optimize performance
- Respond quickly to changing fiber qualities, regulations, and competitive pressures.
View the entire curriculum planned in the Course Schedule.
TAPPI will award 1.7 Continuing Education Units (CEUs) for completion of the curriculum.
##SHARELINKS##
|
Reintroduced in 2010, TAPPI is pleased to bring back this essential--and popular--program for paper professionals. Plan to attend this course being held in Appleton, Wis., May 15 - 17.
This course, designed for new as well as experienced personnel, helps attendees learn how to improve the quality of their product, diminish waste, and increase output. Machine supervisors, technical resources, lead operators and technical personnel, project engineers, and suppliers can all benefit from this course, which is being led by industry-recognized instructors.
To learn more about this course and register, go to the event website.
##SHARELINKS##
|
Unfortunately the learning curve is not sympathetic when it comes to implementing a new idea-to-launch process and, with a failed implementation, key support necessary to ensure operational success is lost forever!.
Ensure that you and your team will be successful launching a new, or sustaining an existing idea-to-launch process, by attending this companion program to our world-renowned "Winning at New Products" seminar."
Join us and leave ready to implement and sustain, with full confidence, your new product innovation process.
May 15-16 in Philadelphia, Pa., USA, Stage-Gate International is hosting Implementing and Sustaining Your Idea-to-Launch Innovation Process, an action packed, hands-on, two day seminar that will help you and your team:
- Accelerate implementation and adoption of your process
- Avoid the most common and easy-to- make, but hard-to-correct, implementation mistakes.
Why attend? Because research shows that a high-quality product development process increases new product success by almost 40%.
The Stage-Gate process provides an operational roadmap that takes a new product from concept to launch, using a decision-based approach to maximize effectiveness and efficiency. When properly designed and implemented, it has been shown to be a key factor for ensuring innovation success.
Created to ensure successful implementation of the Stage-Gate® process, Implementing and Sustaining Your Idea-to-Launch Process introduces you and your team to a structured implementation process that has been used by hundreds of the world's leading companies.
This seminar will teach you and your team how to:
- Accelerate adoption of your process
- Select the right approach for your organization
- Assess your organization's innovation change readiness
- Sustain a new and existing innovation process.
Learn More: Download Brochure
Lever Your TAPPI Membership to Receive 10% OFF the Registration Fee – Use Code TAP11
##SHARELINKS##
|
The Extrusion Coating Manual, Fourth Edition is now available through TAPPI Press.
Edited by: Thomas Bezigian
This comprehensive volume details all aspects of extrusion coating. The book will be a valuable training tool for new employees and a useful reference for everyone involved in extrusion coating. It includes information on classic materials and troubleshooting techniques as well as the latest materials and machine designs available anywhere in the world today.
Completely revised and updated, the fourth edition contains the work of more than 30 well-known industry experts.
View the Table of Contents
Product code: 0102B065
Member Price: $93.00
Non-Member Price: $140.00
##SHARELINKS##
|
2012 Pulp and Paper Manufacturers Association Annual Meeting in May The Pulp and Paper Manufacturers Association (PPMA) Annual Meeting and Conference will be held May 9-11, 2012 at the Intercontinental Hotel in Milwaukee, Wisconsin. PPMA provides human resource information to the pulp, paper, converting and allied industries. The meeting includes a program of expert speakers covering topics such as labor law, training and health care, extensive networking opportunities and updates on key industry research including an annual salary survey.
"The 2012 Annual Meeting will provide attendees with helpful information that can be used to improve business performance, including results from our annual salary surveys and other human resource information," notes PPMA Executive Director, Dick Kendall. "In addition, we have a strong speaker line-up including David Scheible, CEO of Graphic Packaging, who will share his views and insights on how to sustain results in a tough economic and business climate."
The theme of this year's conference is "On the Anvil." Key topics that will be covered include: how to discuss and implement a labor/management committee to help efficiency; update on current health care discussions across the U.S.; current labor law developments; OSHA rules and their impact on union and non-union operations. In addition, a review of how to use the National Network for Pulp and Paper Technology Training (NPT2) training resource will be provided.
A wide range of key trends in the industry will be addressed by an outstanding program of speakers including: David Scheible, CEO, Graphic Packaging International; Dan Murphy, Labor Law Expert; Dennis Smith, Secretary of the Department of Health Services; Daniel Van Wychen, Commissioner, Federal Mediation and Conciliation Service (FMCS); T.J. Murphy, Executive Director, NPT2, Mike Lies, Partner at Seyfarth Shaw LLP, Professor Emeritus C.Y. Allen and Eric Hobbs, partner at Michael Best & Friedrich Law Firm.
##SHARELINKS##
|
Dr. John Mitchell McEwen, 94, was a long-time member of TAPPI and one of the association's longest serving members. He became active in TAPPI beginning in 1941, and served as its president in 1965 and 1966. He was honored as a TAPPI Fellow in 1968. Dr. McEwen played a role in the pulp and paper industry's major transformation that began prior to World War II and continues today with the technologically advanced processes, equipment, and systems used in modern mills and plants around the world.
Following graduation from Ohio State University with a degree in chemical engineering in 1939, Dr. McEwen served as an army reserve officer. He was called to duty before Pearl Harbor and served almost five years as lieutenant, captain, and major in the U.S. Army Corps of Engineers. After the war, he completed his Ph.D. in pulp and paper science at the Institute of Paper Chemistry in Appleton, Wis.
In 1947, Dr. McEwen joined Weyerhaeuser Co. and did technical work in the company's Pulp Division in Longview, Wash., and Everett, Wash. He later managed pulp and paper mills and served as area manager in both Everett and Springfield, Ore. He subsequently served as Weyerhaeuser International VP for Europe, Middle East, and Africa, while living in Brussels, Belgium. After returning to the U.S., he was named regional VP for Southwest Washington. After 30 years with Weyerhaeuser, he retired in 1977.
Dr. McEwen served on the boards of a number of non-profit organizations in Everett, Springfield, and Longview. After retirement, he helped start Community Home Health and Hospice in Longview and served as its president until he moved to Redmond, Wash., in 1992. He married his wife Isabel in 1942.
He is survived by daughters Irene McEwen and Marie McEwen of Redmond, and Judy Richardson of Scottsdale, Ariz. He is also survived by a granddaughter Marcy J. Harrington and her husband Ed of Seattle, Wash., and their daughters Madeline and Heidi.
##SHARELINKS##
|
Members who would like to nominate a candidate for TAPPI's 2013 Board of Directors election should submit a nomination datasheet available online. The candidates must be TAPPI members.
Nominations should be submitted no later than May 15, 2012, by email to mcornell@tappi.org or by mail to Mary Beth Cornell, TAPPI, 15 Technology Parkway South, Norcross, GA 30092 USA +1 770 209-7210.
Thank you,
Jeffrey Siegel, TAPPI Nominating Committee Chair
##SHARELINKS##
|
If there is one time in your professional career when TAPPI membership should be of maximum value to you, it is when you're just getting started in the industry. You need to know how other companies are tackling the problems which have been assigned to you. Your performance depends so much on your staying up to date on the latest advances reported in the technical literature. You need to sharpen your skills in dealing with people since you're new in the role of a supervisor. You need TAPPI courses and the specialized seminars a professional society like TAPPI can offer to keep you current. You need a broader perspective.
Then why, excluding student members, is the median age of new TAPPI members in the mid-30s? Why do many college graduates entering the industry wait roughly 10 years before they join the Association? Several reasons are given. They can't afford the dues. Their employers should pay those dues. They can always read someone else's copy of TAPPI Journal or Paper360°. They aren't allowed to travel to TAPPI meetings. They're too busy. The benefits of TAPPI membership and of continuing education aren't self-evident.
After several years in industry, they'll seek such opportunities to promote their own professional and leadership skills. They'll recognize the opportunities TAPPI provides to work cooperatively on industry-wide technical problems. But the opportunities of those early years will have been lost forever. This is the reason why TAPPI has a less expensive membership option for industry professionals less than 29 years of age. This is also why TAPPI has started a young professionals committee to focus in on specific needs of recent graduates. So pass this along to the younger members of your team and get them involved in TAPPI now!
More information about the TAPPI Young Professionals Committee is available online.
##SHARELINKS##
|
Engineers involved in papermaking wet end chemistry will want to mark June 4 - 6 on their calendars. The 2012 TAPPI Introduction to Wet-End Chemistry course takes place during these three days at TAPPI headquarters in Norcross, Ga., USA.
This course will help you get up to speed on the latest technology and terminology you need for optimum papermaking performance. Instructors for this course know that cost savings is ultimately your mark for a strong finish, so they focus the three-day interactive training on innovative wet end chemistry principals and the use of additives to change or create new paper products.
Through case studies, break-out sessions, and networking with others in the course, you'll learn how to:
- Implement new technology into your mill's wet-end process to reach higher efficiency and yield consistent, quality products
- Use chemicals and other additives to change or create new products and maximize machine capacity
- Put the brakes on machine downtime and off-specification products
- Make better judgments on selection and use of papermaking chemicals
- Better troubleshoot problems on paper machines
- Get up to speed on the challenges papermakers face due to changing fiber qualities, regulations, and competitive pressures.
View the Workshop Schedule to see specific topics covered.
This introductory- to intermediate-level course is designed for those in pulp and paper manufacturing facilities with job responsibilities, such as chemical and process engineers, mill superintendents, research and development engineers, technology and chief chemists, R&D VPs, process and quality control technicians, and suppliers involved with the wet end processes.
##SHARELINKS##
|
Get an overview of the entire pulping and papermaking process and run a pilot plant paper machine! It's all a first-hand experience at the TAPPI Hands-on Workshop for Pulp and Paper Basics. This course is coming up soon, June 4 - 8, 2012, at North Carolina State University in Raleigh, N.C., USA.
Register to reserve your seat.
The number of students in the course will be limited in size to ensure the best interaction among attendees and instructors during the workshop.
If you're wondering whether this course is right for you, it probably is! It's an essential course that teaches the basic concepts in pulp and paper manufacturing and is designed for anyone wanting to improve their role in operations.
Learn more.
Participants will receive a course notebook and CD with approximately 400 pg of reference materials.
Earn CEUs: You'll earn 3.7 continuing education credits at the completion of this June 4 - 8 course. It's a lovely time to be in North Carolina.
##SHARELINKS##
|
Have you ordered your copy of the The Bleaching of Pulp (5th Edition) yet? There's still time to receive up to 50% off the list price if you order before April 30.
Order Online Now
Still undecided? Take a moment to preview the Table of Contents, Introduction, and chapter on Oxygen Delignification. We're confident you – and your company – will find this newest edition to be well worth the investment.
And we're not alone in that assessment. Here is what colleague and contributing editor Brian N. Brogdon, Ph.D., of FutureBridge Consulting and Training LLC, had to say:
"Readers of The Bleaching of Pulp (5th Edition) will be able to easily examine the holistic philosophical approaches to bleach sequence design in a single reference. The environmental aspects of bleaching section has been completely revamped to cover U.S. and Canadian regulations of bleach plant air and water emissions enacted in the late 1990s, as well as the literature assessing and interpreting the impact of emissions from modern bleach sequences on aquatic life. It also contains an encyclopedic chapter on the safe storage, handling, and standardized hazard labeling of most common chemicals employed in bleaching, and I highly recommend it to process engineers, R&D personnel, equipment and chemical supplier vendors, and consultants whom are actively involved in bleach plants."
What are you waiting for? Order your copy today at the incredible pre-order price of $110, a savings of more than 50% off the May release list price of $232 (TAPPI members: $155). Or, contact TAPPI's Member Connection at memberconnection@tappi.org +1 800 332-8686 (U.S.), 1 800 446-9431(Canada), or +1 770 446-1400 (Worldwide).
But hurry, pre-order pricing ends April 30!
##SHARELINKS##
|
Tension Control
Kee-Huyn Shinn, Ph.D.
This volume provides a thorough study of the longitudinal dynamics and tension control of web handling systems. Critical web handling problems that can be related to improper tension control include wrinkle, slack, breakage, lateral movement, and poor roll quality. This valuable text is the only reference currently available devoted entirely to tension control.
Tension Control
View the Table of Contents
Product code: 0101R275
Member Price: $50.00
Non-Member Price: $75.00
##SHARELINKS##
|
The awards that may be presented in the upcoming year are:
Gunnar Nicholson Gold Medal Award - The Association's highest technical honor may be presented annually to recognize an individual or individuals for preeminent scientific and engineering achievements of proven commercial benefit to the world's pulp, paper, board, and forest products industries and the other industries that TAPPI serves.
Herman L. Joachim Distinguished Service Award - The Association's highest award for service, may be presented annually to recognize leadership and service which have significantly and demonstrably contributed to the advancement of the Association.
Paul W. Magnabosco Outstanding Local Section Member Award – The highest honor for Local Sections may be presented annually to recognize an individual for outstanding leadership and exceptional service to one or more Local Sections, which have resulted in significant and demonstrable benefits to the Local Section members.
TAPPI Fellow - TAPPI Fellows are Individuals who have been members of TAPPI for not less than 10 years prior to the nomination, and who have contributed meritorious service to the Association and/or the paper and related industries. Retiring members of the TAPPI Board of Directors become Fellows automatically at the end of their term.
The TAPPI Awards and Honors page has links to these awards which will show the qualifications required and links to the nomination forms that must be completed. You may submit all nomination forms by email to standards@tappi.org, or you may fax them to the attention of the awards department at +1-770-446-6947, or send by mail to TAPPI, Awards Department, 15 Technology Parkway South, Norcross, GA 30092, USA.
##SHARELINKS##
|
Martin A. Hubbe and Kasy King
This handbook provides cost-saving strategies associated with the use of chemical additives during the manufacture of paper. Topics include:
- Loss of materials (i.e. "yield" of the papermaking process)
- Production rate issues
- Downtime
- Inefficient use of functional additives
- Process-enhancing additives and their control
- Strategies to reduce the amount of fibers required to make a paper product
- Strategies to reduce the amount of energy to make paper.
A glossary of terms and a brief introduction to selected principles of capital budgeting are provided as appendices.
This book is ideal for paper machine process engineers/scientists, paper machine superintendents, paper mill management, chemical supplier technical staff, product development engineers, paper mill consultants, and technical staff from allied industries, e.g. process control equipment, papermaking machinery, and environmental services.
Cost Saving Strategies in Papermaking Chemistry
View the Forward and Table of Contents
Product code: 0101R325
Member Price: $150.00
Non-Member Price: $215.00
##SHARELINKS##
|
|
|