Over the Wire
TAPPI
Weekly Spotlight
International Paper (IP), Memphis, Tenn., USA, this week announced that it has reached two agreements to sell three U.S containerboard mills to satisfy the company's obligations in its February 2012 settlement agreement with the U.S. Department of Justice. Under the terms of the DOJ settlement agreement, entered into in connection with the company's acquisition of Temple-Inland, IP agreed to divest the following mills:
- The former Temple-Inland mill in Ontario, Calif.
- The former Temple-Inland mill in New Johnsonville, Tenn.
- The IP mill in Oxnard (Hueneme), Calif.
After conducting a robust auction process, IP has entered into agreements for the sale of the New Johnsonville mill to Hood Companies, and for the sale of the Ontario and Hueneme mills to New-Indy Containerboard, a newly formed joint venture of The Kraft Group and Schwarz Partners.
"We are pleased to have reached these agreements within the timeline established in our settlement with the DOJ," said Chairman and CEO John Faraci. "The purchasers are experienced operators in the paper, forest products, and packaging industries, and we look forward to working with them to close these transactions in a timely manner."
The Kraft Group and Schwarz Partners said in a joint statement this week that "we have been working together in the paper and packaging industry for decades and we have never been more optimistic about the direction of the industry than we are currently. This investment represents a generational commitment by both families to the industry."
Hood Companies said in a statement that "the mill represents a key strategic growth platform within Hood's holdings. We view the New Johnsonville mill as an exceptional asset with an outstanding management team and employee group. We look forward to the long term opportunities that this acquisition creates for the New Johnsonville employees and Hood Companies."
Each divestiture is subject to certain closing conditions, including DOJ approval, and must be closed within the time periods prescribed by the DOJ settlement agreement.
##SHARELINKS##
|
The recent news that the U.S. Environmental Protection Agency (EPA) will regulate logging roads with state-managed best management practices (BMPs) instead of federal permits is encouraging, but much more work remains to provide long-term legal certainty to forest landowners, Washington timber leaders said his week.
A recent Ninth Circuit Court of Appeals decision reclassified logging roads as "point sources" of water pollution, requiring industrial discharge permits typically applied to factories and sewage plants, for each drainage pipe or rain-water ditch on tens of thousands of miles of logging roads across the West. The EPA said the state-based system of forest practices is the best way to regulate forest roads and protect water quality.
In Washington, the state-managed BMP approach has resulted over the last decade in large forest landowners improving 18,700 miles of logging roads and opening 4,700 passages for fish and 2,600 miles of fish habitat. Even as one of the worst recessions in memory has squeezed forest owners, 2011 was a highly productive year for environmental restoration. They removed 1,000 fish passage barriers and 900 miles of fish habitat, according to a state report released last month.
"Forest owners in Washington remain committed to environmental stewardship, even in the midst of unprecedented economic hardship," said Mark Doumit, executive director of the Washington Forest Protection Association, Olympia, Wash. "Their success shows why BMPs not only work but exceed the environmental protection in a federal permitting system."
Along with the success of the state regulations and the EPA's decision, Congress has demonstrated support for the state-based approach by approving legislation last year that temporarily prevented the Ninth Circuit ruling from taking effect, but it expires in September.
Additionally, the Solicitor General (SG) recently filed a brief with the Supreme Court, which is considering whether to review the Ninth Circuit's ruling. Even though the SG agreed that the Ninth Circuit was wrong, the SG argued that the Court should not review the Ninth Circuit's decision because EPA and Congress are best able to resolve the issue.
Despite this wide support for the state-based approach, including the EPA's decision, there could be significant problems ahead, timber leaders say. The Ninth Circuit ruling reclassifying logging roads as "point sources" of water pollution will take effect on September 30 unless the legislation is made permanent. This means forest landowners across the West could still be subject to a flurry of third-party lawsuits, and legal uncertainty, no matter what the EPA does.
For Washington forest owners to have certainty, either the U.S. Supreme Court must take the Ninth Circuit case, or failing that, Congress must approve a permanent stay of the Ninth Circuit ruling. The Supreme Court is expected to make its decision on whether to take the case later this month.
"Forest landowners are already strained financially by one of the worst housing markets in history," Doumit said. "For them to succeed, they need to have a permanent solution regarding how our country's logging roads will be regulated. The EPA's decision is a positive step, but there are still a lot of questions that need to be answered. The bottom line is the need for long-term certainty."
##SHARELINKS##
|
Economic activity in the U.S. manufacturing sector expanded in May for the 34th consecutive month, and the overall economy grew for the 36th consecutive month, according to the nation's supply executives in the latest Manufacturing ISM Report on Business. The report was issued this week by Bradley J. Holcomb, CPSM, CPSD, chair of the Institute for Supply Management Manufacturing Business Survey Committee, Tempe, Ariz., USA.
The PMI registered 53.5%, a modest decrease of 1.3 percentage points from April's reading of 54.8%, indicating expansion in the manufacturing sector for the 34th consecutive month. The New Orders Index continued its growth trend for the 37th consecutive month, registering 60.1% in May. This represents an increase of 1.9 percentage points from April and also the highest level recorded by the index since April 2011. The Prices Index for raw materials fell to 47.5% in May, dropping 13.5 percentage points from April, indicating lower prices for the first time since December 2011. Comments from the panel generally reflect stable-to-strong orders, with sales showing steady improvement over the first five months of 2012.
Of the 18 manufacturing industries, 13 are reporting growth in May, in the following order: Nonmetallic Mineral Products; Furniture and Related Products; Apparel, Leather, and Allied Products; Miscellaneous Manufacturing; Primary Metals; Electrical Equipment, Appliances and Components; Fabricated Metal Products; Machinery; Textile Mills; Paper Products; Computer and Electronic Products; Printing and Related Support Activities; and Chemical Products. The four industries reporting contraction in May are: Plastics and Rubber Products; Petroleum and Coal Products; Food, Beverage, and Tobacco Products; and Transportation Equipment.
A PMI in excess of 42.6% over a period of time generally indicates an expansion of the overall economy. Therefore, the PMI at 53.5% in May indicates growth for the 36th consecutive month in the overall economy, as well as expansion in the manufacturing sector for the 34th consecutive month. Holcomb noted that "the past relationship between the PMI and the overall economy indicates that the average PMI for January through May (53.6%) corresponds to a 3.7% increase in real gross domestic product (GDP). In addition, if the PMI for May (53.5%) is annualized, it also corresponds to a 3.7% increase in real GDP annually."
The 13 industries reporting growth in new orders in May (listed in order) are: Furniture and Related Products; Apparel, Leather, and Allied Products; Nonmetallic Mineral Products; Miscellaneous Manufacturing; Fabricated Metal Products; Wood Products; Electrical Equipment, Appliances, and Components; Primary Metals; Printing and Related Support Activities; Paper Products; Computer and Electronic Products; Machinery; and Chemical Products. The three industries reporting a decrease in new orders during May are: Plastics and Rubber Products; Food, Beverage, and Tobacco Products; and Transportation Equipment.
ISM's Production Index registered 55.6% in May, a decrease of 5.4 percentage points when compared with the 61% reported in April. This indicates growth for the 36th consecutive month. An index above 51.2% over time is generally consistent with an increase in the Federal Reserve Board's Industrial Production figures.
The 14 industries reporting growth in production during the month of May (listed in order) are: Furniture and Related Products; Apparel, Leather, and Allied Products; Nonmetallic Mineral Products; Textile Mills; Fabricated Metal Products; Printing and Related Support Activities; Paper Products; Primary Metals; Machinery; Computer and Electronic Products; Plastics and Rubber Products; Electrical Equipment, Appliances, and Components; Miscellaneous Manufacturing; and Transportation Equipment. The two industries reporting a decrease in production in May are: Food, Beverage, and Tobacco Products; and Chemical Products.
ISM's Employment Index registered 56.9% in May, which is 0.4 percentage point lower than the 57.3% reported in April. This is the 32nd consecutive month of growth in the Employment Index. An Employment Index above 50.5% over time is generally consistent with an increase in the Bureau of Labor Statistics (BLS) data on manufacturing employment.
Of the 18 manufacturing industries,13 reported growth in employment in May in the following order: Apparel, Leather, and Allied Products; Nonmetallic Mineral Products; Textile Mills; Primary Metals; Furniture and Related Products; Machinery; Fabricated Metal Products; Transportation Equipment; Electrical Equipment, Appliances and Components; Miscellaneous Manufacturing; Computer and Electronic Products; Paper Products; and Chemical Products. The two industries reporting a decrease in employment in May are Wood Products and Food, Beverage, and Tobacco Products.
The full text version of the Report is available online.
##SHARELINKS##
|
Global manufacturing executives, cautiously optimistic about the business outlook for the next two years, remain focused on cost management and operational efficiency initiatives but are turning their attention to investing in innovation and value-added services to drive growth, according to a new survey report from KPMG International, Detroit, Mich., USA. According to KPMG's 2012 Global Manufacturing Outlook: Fostering Growth through Innovation, which polled 241 senior, global manufacturing executives – including 50 from the U.S. – 75% of respondents are optimistic about their business outlook over the next 12 to 24 months. The U.S. is expected to lead the growth, according to 40% of global respondents, followed by China, India, Brazil, and Germany.
Despite their optimism, executives, especially those based in the U.S., identify top-line growth (58% U.S.; 41% global) and bottom-line growth (62% U.S.; 43% global) as main priorities for their organizations. Other areas of focus are improved productivity/efficiency and increased competitiveness.
"Manufacturers may be optimistic about the business environment over the next few years, but they are challenged with continued price volatility on cost inputs, risk in the supply chain, and uncertain demand," said Jeff Dobbs, KPMG's global head of Diversified Industrials and a partner in the U.S. firm. "As such, companies must continue to seek opportunities to optimize business operations and squeeze costs out of the process to maximize revenue and profits."
In fact, 62% of respondents say their companies are doing what is typically done in low-growth periods: improving process efficiency and refocusing the business on its core offerings and capabilities. More than 50% say they are eliminating unprofitable product lines and markets.
KPMG's Dobbs points out that manufacturers are doing more than just scaling back, they are looking to the spur growth opportunities through new product development and value-added service offerings.
Forty-four percent of U.S. executives and 36% of global executives indicate that their companies will increase investment in innovation and research and development. And, the overwhelming majority of global respondents (72%) believe that 'transformational innovation' is either in full swing or will be so in 12 - 24 months, with U.S. respondents leading in the view (84%) that the innovation wave is or will be well under way within the period.
"After several years spent cutting costs, many manufacturers realize that they can't afford to sit back and wait. They must deploy capital to develop the products that could give them a competitive advantage," Dobbs said.
Innovation is not going to happen in isolation according to the survey findings, but increasingly in collaborative arrangements with suppliers, customers, and partner companies over the next 12 -24 months. Just over 60% of respondents globally said they will work with customers for customized product development and with suppliers for product design.
For more information, contact Manuel Goncalves at mdgoncalves@kpmg.com.
##SHARELINKS##
|
Smithers Pira, Falmouth, Maine, USA, in partnership again with TAPPI, Norcross, Ga., has announced the Fourth Annual Specialty Papers Conference, scheduled for November 7 - 8 at the Hyatt Rosemont in Rosemont, Ill. This year's program will focus on markets and trends in specialties and pulp, packaging and printing advances, perspectives from paper makers, and new developments in coatings, fibers, and equipment.
Specialty Papers 2012 will be shaped by an esteemed advisory board of paper industry leaders including: David Bell, VP corporate relations, TAPPI; Chuck Klass, president, Klass Associates Inc.; Tom Rodencal, president, Rodencal Paper Consulting Inc.; Steve Rosenberg, senior director, business development and innovation, Neenah Paper Technical Products Business; Steve Ottone, technical service manager, Mallard Creek Polymers; Dr. Frank Adamsky, market development manager, Daikin; Frank Perkowski, president, Business Development Advisory; and David B. Cutler, senior process engineer, Domtar Inc.
"After a successful year in Europe, we are excited to have our Specialty Papers conference return to North America. This event has proven itself to be a must-attend for anyone in the paper industry, and the 2012 program will cover a wealth of new topics," said Barbara Fowler, conference director at Smithers Pira. "For example, for the first time ever, we have paper mills presenting about the new technologies they are developing for specialty grades and how they have bounced back from difficult economic times and global trends."
Bell added that "we're very pleased to announce that the conference program will include presentations from members of the Functional Paper Society from Japan. Professor Hiroshi Inagaki will provide an overview of the Society's research over the past 50 years and his views for future research. Other members will discuss advanced synthetic fibers for papermaking and nanocellulose fiber for barrier coatings. Other key speakers include David Fortin, economist – Fiber, RISI, speaking on the "Outlook for the World Pulp Market" and "Barrier Coatings for Packaging and Printing" by Frank Adamsky, Daikin America."
##SHARELINKS##
|
Sappi Fine Paper North America (SFPNA), Boston, Mass., USA, this week announced the 10 gold winners of its 15th North American Printers of the Year awards for 2011-2012. Culled from a field of approximately 2,000 entries, the 10 gold winners will now compete for the Sappi International Printers of the Year Award global competition.
Each of the gold winning printers will receive $20,000 to support marketing and brand initiatives, as well as entry into the 2013 Sappi International Printers of the Year awards. A list of the gold winners in each category is available online.
"Sappi is devoted to delivering the highest quality product to our clients, and in turn we recognize the value of quality printing to the continued vitality of print as a communication medium," said Jennifer Miller, EVP Coated Business, SFPNA. "For print to remain relevant, it needs to be approached in innovative ways, and our printing community must continue to share its best work. This is the mission behind our long-standing Printers of the Year competition and we are honored to showcase the exemplary craftsmanship submitted by our 2012 gold winners."
To ensure the highest possible standards and integrity, Lauren Elliot, principal of Wicked Good Print Production based in San Francisco, Calif., Bill Garno, director of Rochester Institute of Technology's (RIT) Printing Applications Laboratory (PAL), Malcolm Keif, professor in the Graphic Communication Department at Cal Poly, and, Ken Lantz, director of operations for Euro RSCG Life LMP in New York, served as the panel of judges.
##SHARELINKS##
|
Below is the latest listing of job openings in the TAPPI Career Center. The current listing includes electrical and control engineers, service technician, technical specialist, and safety and plant managers in the U.S. pulp and paper industry. Current, specific job openings at companies and locations in the TAPPI Career Center include:
Employer |
Title |
City |
Longview Fibre |
Electrical Engineers |
Longview, Wash. |
BASF, The Chemical Co. |
Tech Spec. (Paper/Board Coating) |
Charlotte, N.C. |
RockTenn |
Division Safety Manager |
Norcross, Ga. |
BTG Americas |
Service Technician |
Alabama |
Burriws Paper Corp. |
Tech. Asst. Plant Mgr. |
Pickens, Miss. |
FPInnovations |
Control Eng., Dev & Applications |
Vancouver, B.C |
More information about these jobs is available online.
##SHARELINKS##
|
Market Roundup
During the next five years, recovered paper demand, particularly in fiber-poor regions such as China and India, will continue to grow. At the same time, supply coming from North America and Europe will be flat or even diminish, creating a shortage that will keep prices high. These findings recently published in the Outlook for Global Recovered Paper Markets, were announced this week by RISI, Boston, Mass., USA.
"Worldwide recovered paper demand has grown by 45% in the past 10 years, with China increasingly becoming one of the largest consumers," said Kurt Schaefer, VP of Fiber at RISI. "To truly understand the demand-side, we needed to better understand China's ability to meet its own recovered paper needs. So as part of the Outlook for Global Recovered Paper Markets, we have included an extensive analysis of China's export rates and its domestic collection system."
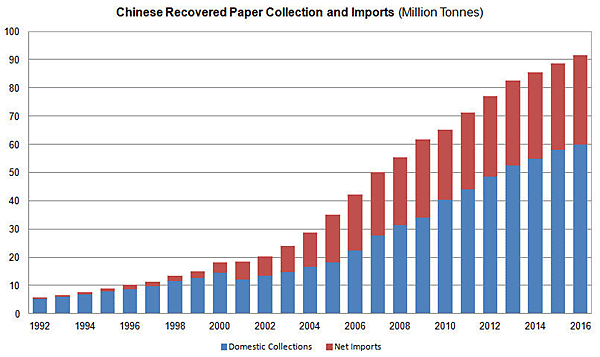
While efforts by the Chinese government and papermakers have bolstered domestic collection, they are not enough to catch up with the country's demand (see above graph). Imports from North America and Europe continue to play an important role, but those supplies are shrinking as demand for graphic papers in the developed world continues to decline.
The report provides a historical analysis and five-year forecast of the global recovered paper sector, spanning 25 years, from 1994 - 2016.
##SHARELINKS##
|
According AF&PA's (Washington, D.C., USA) recently released April 2012 U.S. Recovered Fiber Monthly Report, total U.S. industry consumption of recovered paper in April was 2.48 million tons, 4% lower than March 2012. Year-to-date consumption in 2012 is 3% lower than during the same period last year.
U.S. exports of recovered paper increased 7% in March compared with February, with increases mainly seen in mixed and corrugated. Year-to-date exports of recovered paper in 2012 are 3% higher than during the same period in 2011.
##SHARELINKS##
|
Pulp & Paper
Canfor Pulp Products Inc., Vancouver, B.C., Canada, reports that production at the Canfor Pulp Limited Partnership's Northwood pulp mill has been curtailed to investigate a failure in one of its two recovery boilers. There were no injuries reported in the incident but the No. 1 recovery boiler has been shutdown to determine the cause of the malfunction. As a result, only one of the two production lines at the mill is currently operating.
The cost of repair and the duration of curtailment cannot be reliably determined until a detailed inspection of the facility is completed. However, based on a preliminary review, it is estimated that the curtailment will last for at least three weeks, with an estimated 25,000 metric ton reduction in NBSK pulp production.
To mitigate the impact of the incident, management intends to continue operation of the second production line at the mill and will advance certain mill maintenance activities previously scheduled to be performed during a planned mill shutdown in September. Production at the Partnership's Intercontinental Pulp Mill and Prince George Pulp and Paper Mill is not affected by the curtailment at Northwood.
Due to mitigation efforts by the company, including property damage and business interruption insurance coverage, the curtailment is not expected to have a material impact on the financial condition of the company or the Partnership.
##SHARELINKS##
|
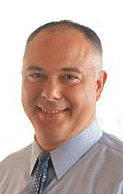 Glatfelter, York, Pa., USA, SVP and CFO John P. Jacunski this week was named 2012 Chief Financial Officer of the Year by Central Penn Business Journal. The program honors financial executives who contribute to Central Pennsylvania's economic growth and stability.
Jacunski was the top winner in the large public company category and was honored along with representatives from small and large private companies as well as non-profit organizations. Judges for the Central Penn Business Journal's annual award considered three criteria for each nominee, including career achievements, impact of contribution, and leadership in other areas of management.
"John has long been regarded as a leader by his colleagues and peers in the investment and financial community, who tout his integrity and ethical character," said Dante C. Parrini, Glatfelter chairman and CEO. "We feel fortunate to have John on our team as he embodies all of our core values—integrity, financial discipline, mutual respect, customer focus, environmental responsibility, and social responsibility."
During Jacunski's tenure as CFO, Glatfelter has doubled in size through successful acquisitions in 2006 and 2007 as well as its most recent and largest acquisition in 2010. Under his financial leadership, the company has significantly reduced debt, increased cash flow, and achieved an 18.2% total shareholder return in 2011, significantly outperforming the Russell 2000 and S&P 500. He also extends his leadership outside of the workplace, supporting St. Leo the Great Parish and helping to raise funds for pediatric cancer research and support.
Glatfelter is a global producer of specialty papers and fiber-based engineered materials. U.S. operations include facilities in Spring Grove, Pa., and Chillicothe and Fremont, Ohio. International operations include facilities in Canada, Germany, France, the U.K., and the Philippines, a representative office in China, and a sales and distribution office in Russia. Glatfelter's sales approximate $1.6 billion annually.
##SHARELINKS##
|
Klabin, Brazil, plans to purchase a new paper machine for sack kraft paper production at its Correia Pinto mill that will have a production capacity of 80,000 metric tpy. The new capacity, aimed at the growing industrial bags market, is scheduled to come online in the fourth quarter of 2013.
The new machine, manufactured in Brazil, will consume the surplus of pulp at Correia Pinto, as well as paper trims generated by mills in Santa Catarina State. Capital expenditures will total approximately BRL 220 million (about EUR 88 million). As a result, Klabin will attain a production capacity of 213,000 metric tpy of sack kraft paper in 2014.
##SHARELINKS##
|
SCA, Stockholm, Sweden, this week completed the acquisition of the Asian hygiene products company Everbeauty. The deal strengthens SCA's market and brand positions in one of the Group's prioritized growth regions. The purchase price for the deal amounts to approximately SEK 1.9 billion ($290 million) on a debt-free basis.
Everbeauty produces, markets, and distributes baby diapers and incontinence care products under its strong brand names Sealer and Dr P, respectively, in China, Taiwan, and parts of Southeast Asia.
The finalizing of the transaction follows approvals and clearances by the relevant Taiwanese authorities.
##SHARELINKS##
|
Shandong Chenming Paper, Shanghai, China, reportedly has shutdown a 30,000 metric tpy paper mill in Hulunbeir City, in the Inner Mongolia autonomous region. The site, operated by Hailar Chenming Paper, ceased production at the end of May. The mill has several small paper machines producing low quality tissue and uncoated fine paper, all which will be permanently retired.
The action is in line with China's efforts to shutdown old and small paper and board making machinery. The government recently announced it would force the closure of old pulp and paper equipment with a combined capacity of 9.7 million metric tpy across the country by the end of this year, according to a RISI report. Each province will have a specific target, and provide a detailed list of machines to be closed soon. Hailar Chenming has been put on this year's closure list by the Inner Mongolian authorities.
##SHARELINKS##
|
Södra Cell, Sweden, has decided to implement two energy investments at Södra Cell Värö in Sweden. The investments will include a new lime kiln and a new pelletizing plant. "These investments will allow us to further improve energy efficiency at Värö, while at the same time creating profitable processing of our members' wood," said Gunilla Saltin, acting CEO of the Södra Group and president of Södra Cell.
A new lime kiln will help reduce the consumption of oil and bark, using biofuel in the form of wood powder instead. The lime kiln will allow lime to be reused in pulp production. The existing lime kiln at Värö does not have sufficient capacity to manage sustainably the lime production needed at the mill.
This project also includes construction of a completely new pelletizing plant that will supply biofuel to both external customers and the new lime kiln. The raw material for the pelletizing plant will come from Södra Timber's sawmill in Värö. Raising production at the new sawmill will also increase volumes of sawdust and planer shavings. The investment will allow these byproducts to be turned into a biofuel with a high energy content suitable for sale, but can also be used as a fuel in the new lime kiln. The two investments decided upon form part of the efforts to take advantage of the benefits of scale available at Värö.
"At Värö, we have access to raw materials in the form of shavings and the energy to dry the shavings to form pellets. This means that everything is in place to provide cost-effective production of a highly processed biofuel," Saltin added.
The new lime kiln and pelletizing plant will be commissioned in late 2013.
##SHARELINKS##
|
UPM Raflatac, Finland, will acquire the business operations of Gascogne Laminates Switzerland SA. The parties have agreed not to disclose the purchase price. The closing of the acquisition is subject to regulatory approvals.
Gascogne Laminates Switzerland is the labelstock business of Gascogne Group, a major player in the French wood industry. Gascogne's labelstock operations' sales totaled EUR 44 million in 2011. The company employs approximately 110 people in its factory in Martigny, Switzerland.
"UPM Raflatac in Europe has focused in the past years especially in growth in special labelstock products. Gascogne Laminates has a strong and long-standing brand in this product area in Europe and through this acquisition we are proud to add those capabilities to our product platform. As a result of this transaction, customers will enjoy stronger specialty offering available through UPM Raflatac's extensive distribution network," says Tapio Kolunsarka, SVP, Europe, Middle-East and Africa.
UPM Raflatac, part of UPM's Engineered Materials business group, is a major global supplier of self-adhesive label materials.
##SHARELINKS##
|
Voith, Germany, reports that its new, free-of-charge ScreenFitNavigator online benchmark test offers all paper manufacturers the chance to check the energy efficiency of their fine screening (slot screening) in the stock preparation area. Just a few weeks after the launch of the tool, many paper manufacturers from all over the world had performed the online test and received a quick and nonbinding energy assessment of their fine screening system. As well as English and German, the Navigator is now also available in Chinese.
For the analysis, system operators only need to input into the website a few parameters and the focus of their screening quality program. The analysis is done instantly and returned in the form of a PDF document that is sent via email. If potential is found in the quick test, Voith provides a more detailed analysis. Dedicated experts (ScreenFit doctors) can then work out a specific program for improvement after comprehensive measurements.
##SHARELINKS##
|
Zellstoff Pöls AG, Austria, has ordered from Andritz, Graz, Austria, a new PrimeLine plant for production of specialty paper. The new paper machine (5.4 meter width, 80,000 metric tpy capacity; up to 1,000 m/min design speed) will produce very high-strength paper grades used primarily for shopping bags, high-grade medical packaging, and food packaging. Startup is scheduled for the end of 2013.
The Andtitz scope of supply includes the stock preparation plant, an approach flow system, the complete PrimeLine fourdrinier paper machine, a high-precision steel Yankee to increase drying rates (6.5 meter dia.), a calender, and the automation systems.
With this investment, Zellstoff Pöls is extending its existing paper production capacities at the Pöls mill. The company is the largest manufacturer of ECF sulfate pulp from bleached softwood in Central and Southeast Europe.
##SHARELINKS##
|
Containerboard/Packaging
Demand for corrugated and paperboard boxes in the U.S. is projected to exceed $36 billion in 2016. Gains will be driven by an overall strengthening of the U.S. economy following the 2007-2009 recession, according to a new report by Reportlinker.com, New York, N.Y., USA, titled U.S. Corrugated and Paperboard Boxes Market.
Through 2016, growth will benefit from expanded food, beverage, and durable goods output, as well as from a rebound in construction spending, which will stimulate demand for goods and materials used in construction applications. Advances will also reflect a trend toward more expensive boxes such as corrugated types, folding cartons that offer high-quality graphics and printing, and boxes that are retail- or shelf-ready, the report notes.
Corrugated and solid fiber boxes will post the fastest shipment gains through 2016, a result of their position as the shipping container of choice for a broad array of durable and nondurable goods. Though folding carton shipments will increase more slowly due to competition from other packaging formats, growth will accelerate from the performance of the 2006-2011 period based on improved manufacturing output in food and beverages in light of a strengthening economy. Good opportunities are also anticipated in such markets as chemicals and pharmaceuticals, and foodservice and carryout food.
Set-up box shipments are expected to continue their long-term decline due to their higher cost relative to other box types and surging levels of imports from countries (such as China) with lower labor costs. Nonetheless, overall demand will benefit from the entrenched position of set-up boxes as upscale packaging for premium confectionery products and fragrances.
Food and beverages represent the largest single market for corrugated and paperboard boxes, accounting for 50% of total demand in 2011. The beverage and frozen food segments are expected to post the fastest gains, with sugar and confectionery, and grain mill product uses expected to increase more slowly. Despite sustainability efforts aimed at reducing excess packaging by eliminating boxes and cartons or reducing the amount of paperboard used in food and beverage cartons, continued high oil prices and the good environmental profile of paper based packaging will support ongoing use of boxes in the vast food and beverage market.
The durable goods and nonmanufacturing markets are expected to post above average gains through 2016, supported by a recovery in the broader economy. Moreover, a rebound in construction expenditures will drive demand for household appliances, furniture, and other durable goods, as well as related boxes. The continuing popularity of online shopping will propel healthy gains for corrugated boxes used in the fulfillment of Internet sales.
Paperboard demand will rebound from the declines of the 2006 - 2011 period as output in the manufacturing sector improves. However, volume growth will be restrained by heightened use of lighter weight, high-performance containerboard in light of sustainability and cost control efforts. Among other materials used in boxes, above average growth for inks will be driven by trends favoring boxes with high-quality graphics. Healthy prospects are also expected for wax-free alternative coatings, which can provide the moisture resistance of conventional wax-coated boxes while being fully recyclable.
##SHARELINKS##
|
Billerud Finland Oy's acquisition of UPM's packaging paper operations at Pietarsaari and Tervasaari in Finland is now completed. Billerud Finland Oy is a wholly owned subsidiary of Billerud AB., Sweden. The purchase price is around EUR 130 million.
The acquired operation was consolidated as of June 1, and was included in Billerud's Packaging and Specialty Paper business area.
In the January - June 2012 interim report, sales of the Billerud Group's market pulp will continue to be reported as a separate business area—Market Pulp. As of July 1, market pulp sales will not be reported separately but will be included in the Packaging and Specialty Paper business area.
Financial pro forma information will be published in the January - June 2012 interim report.
In 2011, the acquired operations' sales amounted to approximately EUR 220 million, and EBITDA was approximately EUR 18 million (pro forma).
The transaction is financed through half cash and cash equivalents, half through raising loans within existing credit frameworks. The impact of the acquisition on Billerud's net debt/equity ratio will be +24 percentage points.
##SHARELINKS##
|
Cascades Inc., Kingsey Falls, Que., Canada, this week reported that a significant majority of employees at its Norampac containerboard mill in Trenton, Ont., Canada, has voted in favor of its final offer, and thus it will not proceed with closure of the facility as previously planned and announced in April.
"We are satisfied to be able to finally reach an agreement with the union and the employees in Trenton. By keeping the mill open, we are saving 130 jobs in this community and avoiding significant financial losses for the local forest industry. The challenges faced by this mill are by no means over. However, reaching this agreement with our employees is a vital pre-condition, and we can now concentrate on identifying an action plan for achieving long-term viability." said Marc-André Dépin, president and CEO at Norampac.
The Norampac–Trenton facility produces corrugating medium with an annual production capacity of 150,000 metric tons.
Founded in 1964, Cascades produces, converts, and markets packaging and tissue products composed mainly of recycled fibers. The company employs close to 12,000 men and women, who work in more than 100 units in North America and Europe.
##SHARELINKS##
|
MeadWestvaco Corp., Richmond, Va., USA, this week announced that it is acquiring AARDEX Group SA, Switzerland, a pioneer in the design and use of electronic medication event monitoring systems and applications designed to measure, analyze, and manage patient adherence in clinical drug trials.
"This acquisition builds on MWV's long-standing commitment and scientific approach to showing medication packaging's impact as an important adherence intervention," said Bruce Thomas, president, MWV Healthcare and SVP, Global Innovation. "We recognize the critical global need to create packaging solutions that address the issue of medication non-adherence. With the acquisition of AARDEX Group, MWV will now be able to provide customers with a complete range of packaging, data analysis, and service solutions that address non-adherence to medications, from phase II clinical trials all the way through commercialization."
AARDEX Group is led by scientists Dr. Bernard Vrijens and Dr. John Urquhart, who pioneered electronic medication event monitoring, now widely recognized as the gold-standard method for compiling patients' drug dosing histories during clinical trials. A small microcircuit, integrated into the drug package, records the time and date of each opening of the package. This technology has been employed in over 500 clinical research studies conducted by leading universities, public and private research organizations, and numerous research-based pharmaceutical companies.
With the acquisition of AARDEX Group, MWV adds the Medication Event Monitoring Systems (MEMS®) Cap for bottles to its portfolio of adherence-enhancing package designs that currently includes Cerepak®, Helping Hand®, Dosepak®, Dosepak Express®, Med-Easy® and Shellpak® solid oral dose solutions. These packaging solutions have had a positive effect on patient adherence in clinical trials and commercial settings by eliminating double-dosing or omission of dosing.
The AARDEX Group management team will remain in place and the team of 12 employees will become MWV employees. Dr. Bernard Vrijens will serve as managing director, AARDEX, and will engage more broadly with pharmaceutical customers and prospects around adherence strategies in drug development and life-cycle management. Dr. John Urquhart will continue to work in the new organization as Senior Scientific Advisor.
##SHARELINKS##
|
SCA Packaging Munksund AB, Sweden, has contracted with Metso, Finland, to rebuild the white top kraftliner machine at its Piteå mill in Sweden. The rebuilt production line will be fully operational during 2013. The value of the order was not disclosed.
The main target of the rebuild is to increase the share of the production of value-added white top kraftliner products. As a result of the rebuild, SCA Packaging Munksund will be able to increase its total annual white top kraftliner production from the current level of 110,000 metric tons to 165,000 metric tons and the total kraftliner production from today's 360,000 metric tons to 415,000 metric tons.
"The investment in the rebuild facilitates increased production of white top kraftliner, a strong specialty paper for the corrugated board industry that is experiencing a high growth rate. The investment is in line with the company's strategy, which is to increase production and sales of products and services with a higher degree of refinement that add value to our customers," said Jan Johansson, president and CEO of SCA.
Metso's delivery will include a rebuild of the approach flow system, headbox, forming, press, and dryer sections, as well as of the board machine ventilation system.
The 7.01-meter-wide (wire) PM 1 produces white top kraftliner in the basis weight range of 115 - 200 gsm and unbleached kraftliner in the range of 170 - 440 gsm at the design speed of 1,100 m/min.
SCA is a global hygiene and paper company that develops and produces personal care products, tissue, packaging solutions, publication papers, and solid-wood products. The company's sales in 2011 amounted to EUR 11.7 billion and it has approximately 44,000 employees.
##SHARELINKS##
|
New Products
AstenJohnson, Charleston, S.C., USA, this week announced the newly formed Paperchine Quantum Solutions (PQS). This new engineering, analytical services, and consultancy company will offer a unique range of diagnostic and technical expertise to help papermakers improve machine efficiency and performance.
Paperchine Quantum Solutions will function as an independent business and will be led by VP Jean Pierre Bouchard. According to Bouchard, "today's paper mill is running with fewer resources than in the past, but the need to remain globally competitive is stronger than ever. AstenJohnson is a trusted resource among paper mill personnel when it comes to problem solving, data analysis, training, and other high end services. With PQS, we are harnessing the knowledge and experiences of our people to give papermakers a dedicated addition to their current workforce."
PQS will focus its efforts in four key areas, including: ·
- Audits that examine all facets of the paper machine, from stock approach through winding, to evaluate mechanical, hydraulic, and structural conditions as well as process capability ·
- Process improvement and optimization using on and off-line data analysis, diagnostic, and statistical tools to provide machine operators with the forward-looking process information necessary to increase overall equipment efficiency ·
- Engineering services to support customers in defining and planning capital investments needed to achieve productivity and quality objectives ·
- Education services on papermaking, statistical process control, and Lean and Six Sigma protocols that give novice and seasoned papermakers the opportunity to expand their skills and expertise.
PQS will draw on the knowledge capital of both Paperchine and AstenJohnson, allowing papermakers to take advantage of a wealth of papermaking and engineering knowledge and capabilities.
AstenJohnson employs approximately 2,000 associates worldwide and manufactures paper machine clothing, filaments, and filtration fabrics in addition to the products and equipment manufactured by Paperchine.
##SHARELINKS##
|
People
The Newark Group, Cranford, N.J., USA, reports that it has expanded its product development team with the additions of Michael Meuli and David Guelzow as New Business Development Managers for the converting divisions of Newark BCI and Newark Paperboard Products. Meuli, a LEAN-certified executive who is also a Six Sigma black belt, brings experience from companies including Kimberly-Clark. Guelzow brings strategic business development experience with a focus on primary and secondary packaging markets. A third specialist will join The Newark Group in July.
##SHARELINKS##
|
PaperlinX, Australia, this week announced that James Orr, EGM Corporate Affairs and company secretary, is to leave the company at the end of June. Michelle Wong will take on the role of company secretary, reporting to Wayne Johnston who takes on the responsibility as EGM Corporate Services in addition to his role as deputy CFO.
Global Marketing and HR functions are to be disbanded, with ongoing functions transferred to the operating divisions. The corporate office in Milton Keynes, Australia, is to close. The CEO and CFO will move to the U.K. Northampton offices.
Total corporate costs in FY 2013 are expected to be approximately A$12.5 million, a 35% reduction on prior year and less than 0.4% of projected turnover. Commenting on the changes, Toby Marchant, CEO, said that "minimizing corporate overheads is a key element of the strategic review, and these changes are a next step."
##SHARELINKS##
|
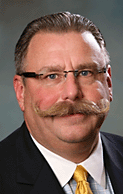 Mohawk, Cohoes, N.Y., USA, has named George William Wurtz III to its board of directors. Wurtz is currently CEO and president of WinCup Inc., a manufacturer and distributor of a broad line of disposable foodservice products.
With a 25-year history in the manufacturing of paper and packaging products, Wurtz held executive positions with Georgia-Pacific Corp., Fort James Corp., and James River Corp. before joining WinCup. He retired as an officer of G-P in 2006 after serving in several executive management positions including president of paper, bleached board, and kraft operations. Prior to that, he worked for Fort James and James River, holding executive management positions in operations, logistics, procurement, and manufacturing planning.
"George brings more than 25 years of experience and success in the paper industry, and with that comes a perspective that is invaluable to the board and to our business. We are looking forward to George's contributions as we continue to advance our products and evolve our company," said Thomas D. O'Connor Jr., chairman and CEO, Mohawk.
##SHARELINKS##
|
TAPPI News
Later this month, June 21 - 22, Portland will host the 2012 TAPPI Paper Machine Drives Short Course. This one-and-a-half-day course will be conveniently held in conjunction with the IEEE Pulp and Paper Technical Conference.
Paper Machine Drives Course attendees will acquire a complete understanding of the selection, operation, and maintenance of paper machine drives as well as troubleshooting skills to reduce downtime and machine failure.
The Paper Machine Drives Course is taught by experienced industry experts who will lead not only classroom training but also team activities and problem solving exercises. This is your opportunity to get specific and individual questions answered directly. After completing this course you will be able to increase production volume capabilities to speed up operations and know how to upgrade and select new paper drives.
The Paper Machine Drives Course takes place Thursday, June 21 through Noon on Friday, June 22 in Portland, Ore., USA.
For additional information and to save your seat please visit the course website.
##SHARELINKS##
|
The 2012 Gulf Coast TAPPI Local Section Annual Meeting will be held June 14 – 17, 2012, at the Seascape Resort in Destin, Fla., USA.
Join us on Thursday, June 14, for the Best Reliability and Maintenance Practices Workshop, from 1:00 - 5:00 p.m. This is a one-day workshop sponsored by Gulf Coast TAPPI and IDCON.
There is no registration fee for this event. However, event staffers request that you register early so that there will be an accurate head-count for our attendees to be properly accommodated.
Course Instructor: Christer Idhammer – IDCON.
Join us on Friday, June 15, for the Reliability and Safety Working Together technical sessions that include the following topics:
- The Big Five to Stay Alive (Lockout Tagout Test, Line Break, Confined Space, Hotwork , Fall Protection)
- TAPPISAFE is Changing Safety Orientation for the Industry
- Six Sigma – Bad Actor Identification Project
- Safety & Reliability ... Similar Behaviors, Terrific Results
- The Manufacturer's Approach to Winder Safety
- 'LOCKOUT: How to Improve and Take It to the Next Level
- SAFETY & OSHA VPP - Because When It Comes to Safety, Failure is Not an Option
- Using Infrared Imaging to Troubleshoot Equipment and Processes
- A Basic Planning Bucket List
- Carrier Rope Reliability Improvement
- A Roundtable Discussion with Christer Idhammer.
Full event information is available online .
##SHARELINKS##
|
Join us on Tuesday, August 14, 2012, at the Mid-Valley Country Club in De Pere, Wis., USA. An afternoon shotgun scramble golf outing is planned with dinner to follow.
Your participation will help fund scholarships for local TAPPI and PIMA programs.
Multiple Prizes will be awarded and individual pin events will be held.
Those submitting registration with their fee, postmarked by August 9, will be assigned holes on a first-come, first-serve basis. Later registrations will be assigned as space is available. Foursome sponsors and all singles will be notified of their hole assignment at the course on the day of the event.
Check-in registration will be at the main entrance of the golf course club house. Golf clubs will be unloaded, tagged, and placed on golf carts for your assigned hole.
Beverage carts will also be available throughout the day on a cash basis. Lunch will be provided prior to tee-off, with the standard fine cuisine of brats, hamburgers, and beverage.
If you have any questions about this event, please contact Chris Wolslegel.
##SHARELINKS##
|
The TAPPI International Research Management Committee requests that nominations be submitted for the William H. Aiken Prize for Research and Development. The award is given for outstanding accomplishments and/or contributions that have advanced the technology of paper and related industries in the R&D field.
The $500 prize is funded by an endowment from the estate of William H. Aiken, TAPPI President in 1967 - 1968, and VP of Technology for the former Union Camp Corp. at the time of his death in 1974. Dr. Aiken won the TAPPI Gold Medal, the association's highest honor, in 1971.
Nominations should be sent to David Bell (DBell@TAPPI.org) TAPPI Headquarters,15 Technology Parkway South, Norcross, Ga. 30092, USA, or by fax (+1 770-446-6947).
The deadline for nominations for the William H. Aiken Prize for Research and Development Award is August 1, 2012.
The nomination should contain a summary of the nominee's technical achievements, impact on the industry and peers, personal data (such as education and work history), and information of other pertinent activity (such as TAPPI activities).
##SHARELINKS##
|
This information-packed volume provides practical, industry-focused approaches to operational issues, and includes a first-ever, complete examination of the ongoing environmental and staging changes that occurred after the discontinuation of chlorine usage in 1996.
Bleaching of Pulp, 5th Edition is written to assist production engineers, supervisors, and scientists find quick solutions to today's immediate challenges in modern bleaching. The text is also designed to help both novice and seasoned professionals quickly understand a wide range of operational issues.
Authors: Alan W. Rudie, Ph.D., and Peter W. Hart, Ph.D.
Together they have delivered the industry's premier text on bleaching technologies.
Thanks to strong pre-ordering, TAPPI has extended this special pricing into late June.
Order your copy of Bleaching of Pulp, 5th Edition today and pay only $110. This is a savings of more than 50% off of the June release list price of $232 (TAPPI members: $155).
For more information contact TAPPI's Member Connection by email (MemberConnection@TAPPI.org). You can also call +1 800 332-8686 (USA), +1 800 446-9431 (Canada), or +1 770 446-1400 (Worldwide).
June's special order-price: $110
TAPPI Member price : $155
List Price: $232
Remember, this offer ends on exactly June 28!
##SHARELINKS##
|
The 2012 TAPPI Linerboard/Medium Manufacture Course,
August 7 - 9, 2012, at the TAPPI Training Facility, in Norcross, Ga.,
USA, is designed to help increase your understanding of linerboard and
medium performance properties and manufacturing to improve corrugated
box performance and runnability. This intermediate-level course is ideal
for process engineers and operators in linerboard and medium
manufacturing facilities and converting plants with a more intermediate
background.
For those participants who require an overview background on pulp and
papermaking technology, there will be an optional one-half day Introduction to P&P
on Monday afternoon, August 6, prior to the beginning of the main
course on Tuesday. This supplemental session is intended for
corrugators, new pulp and paper mill and supplier personnel, and those
without exposure to pulp and paper operations.
If you are looking to increase your understanding of linerboard and
medium performance properties and how they are achieved, build your
confidence in interacting more knowledgeably within the mill with
suppliers and with corrugators; and improve manufacturing operations to
produce a more competitive product, then this course is for you!
Only 25 seats are available for this course. Will you be one of the lucky ones? Register now.
##SHARELINKS##
|
TAPPI and the Pulp and Paper Safety Paper Association (PPSA) have announced a new course focusing on Safety Leadership and Modern Safety Management Principles. The 2012 TAPPI/PPSA Safety Leadership Course, to be held at TAPPI Headquarters, August 15 - 16, in Norcross, Ga., USA, brings the best practices in safety to the paper and packaging industry. A special focus will be placed on leadership commitment and engagement in cultivating a culture of safety excellence.
"Participants in the course will be able to understand the fundamentals of safety and safety management principles including: recordkeeping, incident investigation, safety culture, managing change safely, understanding safety behavior, risk management, and measuring performance," notes Matthew Kanneberg, RockTenn, course chairman.
The course is designed for anyone who takes on a leadership role in safety, including human resources, training, safety supervisors, team leaders, plant managers, project leaders, frontline supervisors, and safety committee participants.
A range of key topics are covered by the course, including: Safety Fundamentals / Modern Safety Management Principles; OSHA Recordkeeping and Medical Management; Incident Investigation; Safe Behavior and Choices; Safety Culture; Measuring Safety Performance; Hazard Recognition; Safety Walkthroughs, Observations and Messaging; Managing Change Safely; and Effective Safety Communication.
More information about the 2012 TAPPI/PPSA Safety Leadership Course is available online.
##SHARELINKS##
|
The Empire State TAPPI and New York-Canadian PIMA Local Section invites you to join them on June 21, 2012, for the 2012 Transformational Technologies Conference in Glenn Falls.
The event will be held at the Queensbury Hotel in Glens Falls, N.Y., USA.
Phil Jones, director of Disruptive Technologies with Imerys and co-chair of the Nanotechnology Task Force for the Agenda 2020 Technology Alliance, will speak on Materials of the Twenty First Century.
Phil also is vice chair of TAPPI's Nanotechnology Steering Committee. This group produced the "Rethink Trees" video, created to raise the awareness about the opportunities of nano-cellulose. The video is avialable online.
Also featured at this year's event, are Charlie Pound, manager-Forming Systems at Kadant Solutions, Brandon Meyer and Matt Bryer from Albany International, and Bob Belair from Metso.
Complete event information and registration details are available online.
##SHARELINKS##
|
Interested in nanotechnology but can't bear to wade through detailed technical reports?
Individual reports on nanotechnology by research and marketing firms as well as governmental agencies are comprehensive and insightful. But they can also be tedious to read, expensive to procure, and generally unknown to non-experts interested in nanotechnology.
Offering a reader-friendly and affordable alternative to these options, Nanotechnology: Health and Environmental Risks introduces risk analysis as a tool for responsible environmental decision making in nanotechnology development. The text provides examples of past, present, and future technologies that demonstrate the need for and benefits of evaluating the risks of nanotechnology.
Access the most up-to-date and relevant information on the impact of Nanotechnology on our health and surroundings.
After outlining the steps of risk analysis, this book examines the opportunity costs inherent in present day nanotechnology development. It then introduces life cycle analysis, examining the toxicology of nanoscale materials, and the known impacts of specific nanoscale materials on human beings.
The text also covers environmental impacts and exposure, followed by chapters on the state-of-the-art tools that adapt life cycle thinking into risk analysis for nanotechnology. The final chapters describe current practices for managing the hazards and risks of nanoscale materials and explore the numerous international efforts that address the risks, science, and policies of nanotechnology.
Learn to recognize and overcome the risks involving nanotechnology. With full-color images and insights into the key health and environmental aspects of nanotechnology, this resource shows how risk analysis can play an important role in creating a sustainable future for nanotechnology.
Product code: 11NANOENV
Member Price: $42.00
Non-Member Price: $52.00
##SHARELINKS##
|
The 2012 TAPPI PEERS Conference, October 14 - 17 in Savannah, Ga., USA, is designed to answer the most pressing business and technical questions faced by pulp and paper companies as they manage raw materials, assets, regulatory requirements, and production assets. Learn more about the PEERS Technical Program
In addition to the in-depth, peer-reviewed technical program, keynote speaker Don Roberts, vice chairman of CIBC World Markets, will offer a global business perspective. PEERS will also offer exclusive networking opportunities and insight into new technologies that can help you optimize your mill operations.
The TAPPI PEERS Conference will be co-located with the International Bioenergy and Bioproducts Conference, creating a value-added opportunity for you to expand your learning, networking, and resources by attending both events.
Exhibit and Sponsorship opportunities also are available. Contact Shane Holt by email at TAPPIPEERS@naylor.com or by phone at 800.369.6220, ext. 3345.
##SHARELINKS##
|
TAPPI's International Bioenergy and Bioproducts Conference, October 17-19, 2012 in Savannah, Ga., will include a tour to Herty Advanced Materials Development Center the morning of Wednesday, October 17. Chartered by the State of Georgia, Herty has leveraged its industry-proven laboratory and pilot capabilities to execute its strategic plan that includes significant emphasis in the biopower and biofuels areas. Herty's focus is on feedstock with current impact of more than $1.5 billion in alternative energy commercialization projects. Herty provides a hub location needed for rapid cost-effective development of biomass resources for energy production. Learn more about Herty and this tour.
IBBC will focus on technical advancements and commercialization of bioconversion technologies that leverage the forest products manufacturing infrastructure. Learn more about IBBC and see the entire technical program.
IBBC will also feature Keynote Speakers:
- Paul Spindler, VP of Technology at Catchligh
- John B. chairman and CEO, Buckeye Technologies Inc.
In addition, IBBC will include technical presentations, expert panels, case studies, and reports from projects that address:
- Feedstock and harvesting improvements to increase yield and quality of biomass
- Bioelectricity using combined heat and power (CHP)
- Bioconversion technologies for wood and biomass
- Production of chemicals and transportation fuels fromwood and biomass
- Policies and incentives for bioconversion projects'
IBBC will be co-located with the TAPPI PEERS Conference, creating a value-added opportunity for participants to expand their learning, networking and resources by attending both events.
##SHARELINKS##
|
Authors: Wei-Hong Zhong and Bin Li, Jo Anne Shatkin, Russell G. Maguire, Vivian T. Dang, Gwen M. Gross, and Michael C. Richey
A comprehensive account of how nanomaterials are synthesized and processed, this book presents the theory and technology of introducing nano-based materials as value-added elements into product manufacturing. The book explains the fundamentals of vapor, liquid, solid phase, and biosystem-assisted nanoparticle syntheses, with sufficient analysis of each method to permit decisions on which is most productive, energy efficient, and safe. The text then confronts the problems of scaling up from lab-based syntheses to manufacturing and demonstrates how nanomaterials on the shop floor require new protocols of quality assurance and employee and environmental protection. The book concludes with case studies of individuals who endeavored to commercialize nanotechnologies for higher-volume production.
Nano Science and Nano Materials: Synthesis, Manufacturing, and Industry Impacts.
Product code: 12NSNM
Member Price: $129.00
Non-Member Price: $149.00
##SHARELINKS##
|
The Nonwovens Engineers and Technologists Division (NET) of TAPPI will co-locate its annual Innovative Nonwovens Conference (NETInc) next year with PaperCon 2013, April 28 - May 1 in Atlanta, Ga., USA.. The NETInc technical conference is a unique event developed by engineers and technologists to cover the latest market and technical developments and innovations in the global nonwovens industry.
"Co-location of the NETInc Conference at PaperCon 2013, the pulp and paper industry's largest event and most comprehensive technical conference, will provide attendees an expanded range of options to network and learn the latest cutting edge technical content," notes TAPPI President and CEO Larry N. Montague. "The nonwovens industry is a dynamic, rapidly growing segment of our industry that encompasses a wide range of raw materials, applications, and market segments, and it employs some of the most innovative technology in the industry. We're excited about the synergy provided by having these two industry leading events located in one venue."
NETInc offers peer reviewed papers, expert speakers, and exclusive networking opportunities. A comprehensive technical program covers a wide range of products, innovative technologies, and topics including market trends, raw materials, fibers, and processing used in an array of applications including absorbent products, medical applications, building science, and many others.
TAPPI's NET Division covers the global nonwovens business and includes members and nonwovens experts from diverse markets and disciplines. It covers materials, equipment, and processes for the manufacture and use of nonwovens. The division's technical committees sponsor courses, conference sessions, roundtables, and TAPPI PRESS products, as well as networking and problem-solving opportunities.
##SHARELINKS##
|
Wet End Chemistry is the eleventh of 15 CD-ROMs in the Making Pulp and Paper CD-ROM Series. Through this highly interactive, self-paced CD-ROM, participants learn wet end chemistry terms, concepts, and processes.
Learning outcomes:
After completing the Wet End Chemistry CD-ROM, participants should be able to:
- Understand the reasons why papermakers use wet end additives in paper
- Describe commonly used functional additives
- Describe commonly used process additives.
Benefits for Everyone
The series is designed for anyone who would benefit from a working knowledge of the pulping and papermaking process, including:
- Paper machine operators
- Process and product engineers
- Sales and technical support staff
- New employees
- Students.
It will also be beneficial to experienced production or technical employees who need a more thorough understanding of a specific area of the operation, especially for cross-training purposes. New employees of chemical and equipment suppliers and paper industry consultants will also benefit from this series.
The complete set of all 15 Making Pulp and Paper CD-ROMs are also available.
Product code: MPP-11
Member Price: $78.00
Non-Member Price: $119.00
##SHARELINKS##
|
The Extrusion Coating Manual, Fourth Edition is now available through TAPPI Press.
Edited by: Thomas Bezigian
This comprehensive volume details all aspects of extrusion coating. The book will be a valuable training tool for new employees and a useful reference for everyone involved in extrusion coating. It includes information on classic materials and troubleshooting techniques as well as the latest materials and machine designs available anywhere in the world today.
Completely revised and updated, the fourth edition contains the work of more than 30 well-known industry experts.
View the Table of Contents
Product code: 0102B065
Member Price: $93.00
Non-Member Price: $140.00
##SHARELINKS##
|
Martin A. Hubbe and Kasy King
This handbook provides cost-saving strategies associated with the use of chemical additives during the manufacture of paper. Topics include:
- Loss of materials (i.e. "yield" of the papermaking process)
- Production rate issues
- Downtime
- Inefficient use of functional additives
- Process-enhancing additives and their control
- Strategies to reduce the amount of fibers required to make a paper product
- Strategies to reduce the amount of energy to make paper.
A glossary of terms and a brief introduction to selected principles of capital budgeting are provided as appendices.
This book is ideal for paper machine process engineers/scientists, paper machine superintendents, paper mill management, chemical supplier technical staff, product development engineers, paper mill consultants, and technical staff from allied industries, e.g. process control equipment, papermaking machinery, and environmental services.
Cost Saving Strategies in Papermaking Chemistry
View the Forward and Table of Contents
Product code: 0101R325
Member Price: $150.00
Non-Member Price: $215.00
##SHARELINKS##
|
Tension Control
Kee-Huyn Shinn, Ph.D.
This volume provides a thorough study of the longitudinal dynamics and tension control of web handling systems. Critical web handling problems that can be related to improper tension control include wrinkle, slack, breakage, lateral movement, and poor roll quality. This valuable text is the only reference currently available devoted entirely to tension control.
Tension Control
View the Table of Contents
Product code: 0101R275
Member Price: $50.00
Non-Member Price: $75.00
##SHARELINKS##
|
|
|