Over the Wire
TAPPI
Weekly Spotlight
Smurfit Kappa Group (SKG), Ireland, one of the world's largest integrated manufacturers of paper-based packaging products with operations in Europe and Latin America, will acquire U.K.-based Orange County Container Group (OCCG) for a total cash consideration of $340 million (EUR 260 million). OCCG is a private corrugated and containerboard manufacturer with operations in Northern Mexico and the Southern U.S. It employs 2,800 people (2,000 of whom are employed in Mexico and 800 in the U.S.), and is expected to generate $53 million of EBITDA for the full year 2012. OCCG's strong strategic fit with SKG's existing businesses is expected to deliver at least $14 million of synergies by the end of year two.
The $340 million cash consideration will be funded from the Group's existing cash resources. The transaction is expected to be completed in the fourth quarter of this year, subject to customary completion conditions and regulatory approval.
OCCG produces, markets, and sells high graphics and conventional corrugated containers, as well as point-of-purchase displays. It operates eight main packaging facilities in Mexico, including two box plants, three sheet plants, and three fulfillment centers, along with seven distribution centers in Mexico. It also has two packaging facilities in the southern part of the U.S., consisting of one box and one sheet plant. The Dallas, Texas, mill produces 290,000 metric tpy of recycled containerboard on two paper machines. The company operates seven wholly owned recycling centers in Texas, Oklahoma, and Arkansas, which is a significant strategic resource and provides security of supply of recovered paper for the mill and of containerboard for the corrugated operations.
The business has well maintained and well invested assets following a capital investment program of more than $85 million in the past four years. The gross assets of the business being acquired are approximately $325 million, and the profit before tax in 2011 was $6.3 million.
The transaction delivers a range of strategic and financial benefits for SKG including:
- Further strengthens SKG's position in higher growth markets
- SKG's containerboard and corrugated Mexican business includes three paper machines and nine box plants with containerboard production of approximately 295,000 metric tpy and corrugated shipments of 500 million square meters for the 12 months to June 2012
- Complements SKG's Mexican business with limited customer or geographic overlap
- Provides SKG with a pro-forma total market share of approximately 17% of the Mexican market
- Enhanced geographic diversity, with SKG's non-European exposure expected to increase from 23% to 26% of Group EBITDA
- OCCG's integrated model provides security of supply and consistency of service to packaging customers – particularly under-pinned by a substantial level of "grip" on recovered paper supply
- OCCG comprises well invested assets and well run businesses delivering strong growth
- Synergy benefits of at least $14 million expected within two years
- Pro-Forma FY 2012 multiple of 6.4x before synergies (5.1x after synergies)
- Expected returns for SKG shareholders are attractive – earnings accretive on completion
- Transaction funded through SKG's existing cash resources
- SKG's 2012 year-end net debt to EBITDA multiple post completion is expected to be well within the Group's stated target of less than three times.
SKG, a producer of recycled containerboard in Europe, notes that the transfer of some of its European recycled containerboard production experience and expertise will enhance the efficiency and production capability of OCCG's mill.
##SHARELINKS##
|
The Association of Suppliers to the Paper Industry (ASPI), Norcross, Ga., USA, has named Mike Edwards, Domtar's SVP, Pulp and Paper Manufacturing, as its 2012 ASPI Excellence in Leadership recipient. Edwards was presented the award at ASPI's Fall 2012 Customer Alignment Meeting with Domtar last week in Charlotte, N.C.
ASPI's Excellence in Leadership Award honors leaders in the pulp and paper industry that have demonstrated exceptional and inspiring leadership. Nominations are made by ASPI members, and voted on by the ASPI Board of Directors. Members specifically commended Edwards on his strategic partnerships with suppliers to improve operational efficiencies at Domtar's mills
"ASPI is extremely pleased to honor Mike Edwards with this award," said ASPI President Carl Howe, VP Sales with Kadant Paperline. "Mike's reputation as an outstanding leader is widely recognized in the pulp and paper industry, particularly in the supplier community. ASPI welcomes this opportunity to formally recognize Mike and his achievements."
John D. Williams, Domtar president and CEO, added that "we're delighted that Mike has been recognized by his peers for his longstanding leadership in the industry. This award couldn't go to a more deserving recipient."
Edwards is responsible for all pulp and paper manufacturing as well as converting operations at Domtar. His career in the pulp and paper industry spans more than 48 years. He started his career in 1963 in Scotland and immigrated to Canada in 1981, working in various pulp and paper positions. In 1997 he moved to the U.S. He was previously VP, Fine Paper Manufacturing at Weyerhaeuser Co., which he joined in 1994 and where he held various management positions in pulp and paper operations.
Edwards has previously been chairman of the North Carolina External Affairs Council (2001-2007) and a member of the board of the North Carolina State Pulp and Paper Foundation (2002-2009) and the Governor's Business Council of North Carolina for Management and Development. In the early 1990s, he was chairman and director of the Ontario Pulp and Paper Makers Association.
ASPI is the leading association of companies that supply products and/or services to the pulp, paper, and board industry. Member participation consists primarily of CEOs, owners, and senior management executives. ASPI's mission is to assist its member supplier companies in providing increased economic benefits to their customers through collective knowledge, initiatives, and efforts.
More information about ASPI is available online, or by contacting Colleen Walker, director of member relations.
In the photo below are (l-r) ASPI President Carl Howe (VP Sales, Kadant Paperline), Mike Edwards (Sr. VP, Pulp and Paper Manufacturing, Domtar), ASPI Board Member Peter Collins (VP, Andritz), and ASPI Past President Bob Gallo (President, Voith Paper North America).
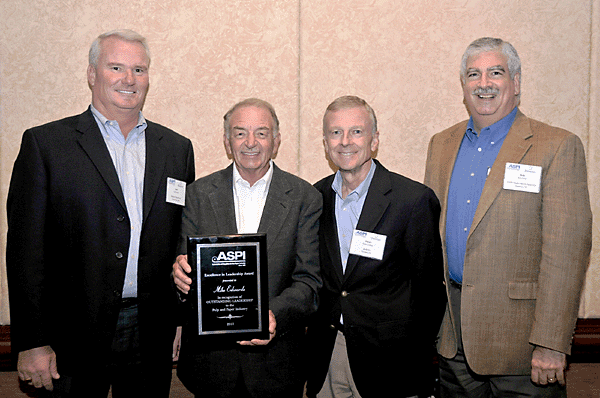
##SHARELINKS##
|
Domtar Corp., Montreal, Que., Canada, has announced the launching of an interactive, educational website known as The Forest Academy. The tool, introduced a few months ago, has reached a milestone of 25,000 visitors. The Forest Academy builds on Domtar's original youth education website "Tree World" that had been developed in the 1990s. It provides elementary school students with fun, informative games about trees, and forest ecology,
"We're thrilled that teachers and parents are finding the new site to be a useful and engaging learning tool," noted Pascal Bossé, Domtar VP of communications and investor relations. "We put a lot of effort into creating the site's top quality educational content, but the flash programming of the games is what makes it fun for adults and kids to learn, and what makes The Forest Academy so unique."
In addition to the games, teachers will find a faculty manual with a wealth of information about trees and forest ecology. More information is available online.
##SHARELINKS##
|
The Procter & Gamble Co., Cincinnati, Ohio, USA, has recognized paper machine clothing supplier Albany International Corp., Rochester, N.H., as a "Business Partner of the Year." Of P&G's more than 75,000 suppliers and agencies, only eight received this highest honor, with Albany International achieving this recognition for the second consecutive year. In addition, the company has received four consecutive Excellence Awards from P&G.
Daniel Halftermeyer, president of Albany's Global Machine Clothing business, said that "to receive this prestigious honor from P&G for a second consecutive year underscores the dedicated customer focus of the entire Albany team. From the manufacturing floor to R&D, from planning to technical, all of our employees are aligned to support our customers in achieving business excellence."
The company became a supplier to P&G in 1957 and the current partnership was formalized in 1991. Albany International is an exclusive supplier to a proprietary process related to the production of the P&G Charmin®, Bounty®, and Puffs® brands.
##SHARELINKS##
|
TAPPI and the Christian Brothers University Packaging Department, Memphis, Tenn., USA, will host a driving range fundraising event at the new Vantage Point Golf Center in Cordova, Tenn., on October 22, from 5:30 p.m. – 9:30 p.m. The event will raise money for scholarships for CBU packaging students. Information on how to participate is available online. Sponsorship opportunities are available.
Prizes are all for a great cause:
- Get a Hole-In-One and WIN A TOYOTA 4RUNNER from Wolfchase Toyota
- Team & Individual Events
- Longest Drive
- Nearest the pin
- Silent Auction
- Golf Trivia
- And much, much, more....
Single Player—$35 ea.,
Teams of Four—$120
Med. Bucket of Balls, Food, & Beverages
Please pass this along to those in your organization that might like to play or sponsor.
##SHARELINKS##
|
Below is the latest listing of job openings in the TAPPI Career Center. http://careers.tappi.org/ The current listing includes job openings for a variety of positions, including product marketing manager, maintenance manager, fiber scientist, technical services manager, director of operations, coating scientist, process engineer, electrical engineer, fiberline specialist, and customer service representative. Current, specific job openings at companies and locations in the TAPPI Career Center include:
Employer |
Title |
Location |
Albarrie Environ. Services |
Product Mkt. Mgr. (Liq. Filtration Media) |
|
Armstrong World Industries |
Maintenance Manager |
Pennsylvania |
Boise Inc. |
Sr. Scientist- Fiber |
Wallula, Wash. |
Catalyst Paper |
Manager, Technical Services |
Powell River, B.C. |
Confidential |
Technical Services Manager |
Columbus, Ohio |
Confidential |
Coatings Scientist |
Columbus, Ohio |
First Quality Enterprises |
Director of Operations |
Lock Haven, Pa. |
GL&V USA |
Sr. Process Eng.- Fiberline Specialist |
Nashua, N.H. |
New-Indy Containerboard |
Process Engineer |
Ontario, Calif. |
SCA Americas |
Electrical Engineer |
|
SCA Americas |
Process Optimization Manager |
|
UPM Kymmene |
Customer Service Representative |
Westmont, Ill. |
More information about these jobs is available online.
##SHARELINKS##
|
Market Roundup
The U.S. paper and paperboard market had total revenue of $63.6 billion in 2011, representing a compound annual rate of change (CARC) of -2.7% between 2007 and 2011, according to a new report by Research and Markets, Dublin, Ireland, titled Paper and Paperboard in the United States. Market consumption volumes decreased with a CARC of -4% between 2007-2011, to reach a total of 74.6 million metric tons in 2011, the report notes.
The performance of the market is forecast to decline further but with a slower pace, with an anticipated CARC of -0.1% for the five-year period 2011 - 2016, which is expected to drive the market to a value of $63.3 billion by the end of 2016.
More information about Paper and Paperboard in the United States is available online.
##SHARELINKS##
|
In 2007, China imported wood chips from only three countries—Vietnam, Indonesia, and Australia, who together shipped 1.1 million metric tons throughout the year. With the fast expansion of the pulp industry in China, the country is rapidly growing its need for wood fiber. Domestic supplies have proven inadequate, so the list of supplying countries has expanded from three to eight during the past 12 months, according to the Wood Resource Quarterly ( WRQ), Seattle, Wash., USA.
Two of the three chip-exporting countries in Latin America, Chile and Brazil, sent the first vessels with eucalyptus chips since 2006 in the third quarter of last year. The total volume exported from the two countries in 2011 was 100,000 metric tons, and during the first seven months of this year, 76,000 metric tons have been shipped, a majority from Chile. Wood chips from Latin America still accounted for only 3% of all hardwood chips imported to China in the 2Q/12, and these chips were among the costliest chips landing in the country, WRQ notes.
So, although Chinese pulp mills will be in search of additional wood fiber in the coming years, it is not likely that either Chile or Brazil will be major competitors to countries in closer proximity to China, including Vietnam, Thailand, Indonesia, and Australia. Chile most likely will continue to ship a majority of its chips to Japan, where its chips are more competitively priced with other supplying countries.
During the first six months of 2012, Chile was the largest supplier of hardwood chips to Japanese pulp mills, followed closely by Australia. Chile's market share in this market has gone from 17% five years ago to 27% in the first half of 2012. With chips from Chile being less costly than Australian chips delivered to Japan, there will continue to be opportunities for Chile to gain market share in the Japanese chip market in the coming year.
More information is available online.
##SHARELINKS##
|
Total U.S. printing and writing (P&W) paper shipments decreased 5% in August compared with August 2011, according to the AF&PA, Washington, D.C., USA, August 2012 Printing-Writing Paper Report issued this week. All four major P&W paper grades posted single-digit decreases compared with last August.
U.S. purchases of P&W papers also decreased, down 6% in August. Total P&W paper inventory levels decreased 5% from last month, primarily due to double-digit decreases in mechanical-grade paper inventories. Additional key findings include:
- Shipments of coated freesheet papers decreased year-over-year, but August shipments reached the highest level since October 2011
- Shipments of uncoated freesheet papers were down year-over-year, the sixth consecutive single-digit year-over-year decrease
- Uncoated mechanical paper inventories dropped sharply
- The inventory of coated mechanical papers also dropped and hit the lowest point since December 2007.
##SHARELINKS##
|
Total U.S. boxboard production decreased by 0.8% compared with August 2011, but increased 2.2% from last month, according to the AF&PA (Washington, D.C., USA) August 2012 U.S. Paperboard Report released this past week. Unbleached kraft boxboard production decreased over the same month last year and decreased compared with last month.
Total solid bleached boxboard and liner production increased compared with August 2011 and increased compared with last month, the new report notes. The production of recycled boxboard increased compared with August 2011 and increased compared with last month.
##SHARELINKS##
|
U.S. containerboard production in August rose 2.2% over July 2012 and was flat compared with the same month last year, according to the newly released AF&PA (Washington, D.C., USA) August 2012 U.S. Containerboard Statistics Report. The month-over-month average daily production increased 2.2%. The containerboard operating rate for August 2012 gained 2.1 points over July 2012, from 95.4% to 97.5%.
##SHARELINKS##
|
Total U.S. kraft paper shipments were 133,000 tons in August, a decrease of 3.6% compared with the prior month, AF&PA, Washington, D.C., USA, reported in its August 2012 Kraft Paper Sector Report published this past week. Total inventory was 77,800 tons in August. Both unbleached and bleached kraft shipments decreased year-over-year.
##SHARELINKS##
|
Total U.S. paper industry consumption of recovered paper in August was 2.56 million tons, 6% higher than July 2012, AF&PA, Washington, D.C., USA, reported in its August 2012 U.S. Recovered Fiber Monthly Report issued last Friday. Year-to-date total consumption in 2012 is 4% lower than during the same period last year.
U.S. exports of recovered paper, as reported by the U.S. Census Bureau, increased 5% in July compared with June, led by a 14% increase in mixed papers exports. Year-to-date exports of recovered paper in 2012 are 6% lower than during the same period in 2011.
##SHARELINKS##
|
Pulp & Paper
AkzoNobel, the Netherlands, reports that its Pulp and Performance Chemicals business (formerly Eka Chemicals), in a move to optimize its European supply chain for paper chemicals, will consolidate its manufacturing in Europe. This will include closure of the company's sizing chemicals plants in Trollhättan and Borås, Sweden.
"These efficiency-enhancing measures position us well to meet demand within the segment," said Jay Hunsberger, director, Paper Chemicals Sales and Marketing. "Our remaining plants in Europe will allow us to stay competitive and serve our European customers with products that create value for them."
The difficult market and global economic conditions make the current situation in Europe unsustainable, the company noted. It added that the consolidation actions are necessary to remain competitive in this product line, and will ensure that AkzoNobel continues to be a strong supplier to its key customers in Europe.
##SHARELINKS##
|
U.K.-based H.I.G. Europe, the European arm of global private equity firm H.I.G. Capital, Miami, Fla., USA, this week announced that it has simultaneously acquired ARMetallizing (ARM), a Belgium-based European producer of metalized paper, from Ackermans & van Haaren, and Vacumet Paper, a Massachusetts-based U.S. producer of metalized paper, from Scholle Corp. The combined group will be a global market leader in metalized paper for use in the beverage and consumer packaged goods markets.
The group's metalized paper is currently used as base paper in premium beer labels, spirit labels, food packaging, and consumer product packaging. With revenues in excess of EUR 120 million, the group will supply clients globally from three manufacturing facilities in Belgium, Italy, and the U.S. and will be led by ARM CEO Paul Van Emmerick and CFO Martin Raeymakers, who will retain a significant shareholding in the business.
##SHARELINKS##
|
Metsä Tissue Corp., Espoo, Finland, part of Metsä Group and a European tissue and cooking paper products supplier, this week said that it will update its organization. As a first step, the Management Team will be restructured. The new roles and responsibilities will become effective December 1.
"With this change we will reduce complexity as well as clarify roles and responsibilities. Given the regional character of the tissue business, this move will strengthen our organization regionally and bring decision-making closer to our customers," Mika Joukio, CEO of Metsä Tissue, said. "The new organizational structure will support our ambition to improve profitability, stay agile, and ensure a strong platform for future growth," he added.
The Management Team of Metsä Tissue will consist of the following persons:
- Mika Joukio, CEO
- Mariusz Jedrzejewski, SVP, Tissue, Central Eastern Europe
- Jori Sahlsten, SVP, Tissue, North Eastern Europe
- Mark Watkins, SVP, Tissue, Scandinavia
- Christoph Zeiler, SVP, Tissue, Western Europe
- Juha Tilli, SVP, Baking & Cooking
- Markus Holm, CFO
- Ghita Jansson-Kiuru, SVP, Human Resources
- Hubert Schönbein, SVP, Brand Marketing and International Sales
- Lars Warvne, SVP, Technology.
##SHARELINKS##
|
Metsä Tissue, Finland, Metsä Group's tissue and cooking paper business, this week reported that it will begin personnel reductions at its Finnish units. The reductions will involve white-collar personnel, excluding frontline sales teams. Some 150 employees will be involved in the process and the maximum headcount reduction is not expected to exceed 40. Metsä Tissue's Finnish offices are based in Espoo and Mänttä.
"Increasing competition and continuous tightening of EU regulation pose additional challenges for Metsä Tissue. Additionally, the Finnish government's stricter national adaptation of EU directives concerning areas such as waste taxation and landfill regulations is a major threat to our competitiveness. By restructuring and reorganizing our operations, we aim to secure our future competitiveness in the growing tissue and cooking paper market," said Metsä Tissue's CEO Mika Joukio.
##SHARELINKS##
|
Mondi, South Africa, has partnered with Finland-based Tieto and Metso to increase the efficiency and profitability of pulp and paper production at its Syktyvkar Mill in Russia. Tieto and Metso provide the mill advanced control and optimization systems for its fiberlines. By improving overall operation of the fiberline, Mondi will boost the yield, chemical consumption, and production capacity of Syktyvkar's three lines, leading to significant reductions in operating costs and improving productivity.
Process areas for the advanced control and optimization system at Syktyvkar include its three continuous digesters, three brownstock washing lines, two oxygen delignification lines, and two bleach plants. The Tieto part, Tieto Integrated Paper Solution TIPS, applications include budgeting, order entry, production, and process and quality management integrated into mill-level reporting.
The flexible optimization options from Metso for each application are continuous digester, washing optimizer, oxygen delignification optimizer, and bleaching optimizer. Coordinating these various applications maximizes the overall benefit for Mondi for fiberline optimization. These applications join the almost four hundred pulping and recovery advanced control applications Metso has installed globally.
The Mondi Group is an integrated packaging and business paper producer with operations in 28 countries and around 23,400 employees. Tieto is an IT service company in Northern Europe, with about 18,000 employees.
##SHARELINKS##
|
The government of Nova Scotia reportedly has reached a new agreement to reopen the shuttered NewPage Port Hawkesbury paper mill, one day after a Canadian company's bid to buy the mill collapsed. The revised deal is with Pacific West Commercial Corp., Vancouver, B.C., Canada, which has offered $33 million for the 50-year-old, shuttered newsprint and coated papers mill.
The agreement means that money the provincial government had spent in an effort to restart the mill, which originally opened in 1962, could be repaid in as little as 12 years. This includes a $124.5 million aid package announced last month and $36.8 million the government has spent so far to keep the mill in a so-called "hot idle state" to be able to quickly resume operations. The $124.5 funding package included $66.5 million in loans, $40 million of which would have been repayable. The other $26.5 million would be forgiven if certain criteria including wage targets were met.
Pacific West Commercial said it plans to begin producing paper in early October. The mill shut down last September, throwing some 600 people out of work and affecting another 400 forestry contractors. At the time, NewPage cited the high Canadian dollar and increased rates for shipping and electricity as the reasons for its closure.
"Many people have worked extremely hard to arrive at this moment, and we will all continue to work hard together over the coming years to ensure that Port Hawkesbury remains the highest quality, most competitive paper mill of its kind in North America," company president Ron Stern said. The company has promised to rehire about 300 workers and operate one of the mill's two paper machines.
##SHARELINKS##
|
Suzano Papel e Celulose S.A., Sao Paulo, Brazil, is performing market analysis supporting the installation of a biomass-fired boiler in its Mucuri Pulp Mill (Bahia, Brazil). The study is expected to be completed at the beginning of 2013. The total investment cost of the project is estimated to be $14.82 million (30 million Brazilian reais).
The new boiler will burn biomass as its primary fuel and will provide steam to the industrial process. It will have a capacity to produce 340,000 lb/hr, and the manufacturer will be Brazilian CBC Industrias Pesadas S.A. Infrastructure construction is expected to begin in the first quarter of 2014, and the boiler is scheduled to be operational during the second quarter of 2015.
Mucuri Pulp Mill currently produces 1 million metric tpy of bleached eucalyptus pulp per year. The facility is also equipped with a 240 MW powerhouse that provides energy for the mill's self-consumption, with the excess being sold to the national grid. Approximately 950 people work at the facility.
Suzano Pulp and Paper is a forestry-based company that produces eucalyptus pulp and paper in Latin America. The company has been active in the pulp and paper industry for 87 years, with global operations in approximately 80 countries. It currently has five mills: Suzano, Rio Verde, Embu and Limeira (Sao Paulo), and Mucuri (Bahia State). The company's operations are divided into three business units—forestry, pulp, and paper.
##SHARELINKS##
|
Containerboard/Packaging
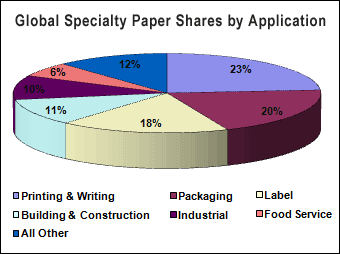 Changes in consumer preferences, rising petrochemical costs, and increasing government regulation have caused consumer products companies to look for alternatives to plastic-based packaging. Paper-based specialty packaging is helping to meet that demand and is creating new growth and investment opportunities for paper producers, according to the new Specialty Packaging Papers Special Market Analysis Study from RISI, Boston, Mass., USA.
"Not only is there opportunity for manufacturers who are already producing packaging paper grades, but producers of graphic papers could also benefit," said Michael Jones, director of packaging - mill intelligence at RISI.
"Graphic paper manufacturers producing printing and writing grades are facing significant market headwinds as demand for those grades continues to decline. The specialty market offers them an opportunity to improve machine utilization rates and create new revenue streams," Jones continued.
More information about the study is available online.
##SHARELINKS##
|
Fujian Liansheng Paper Co., Longhai, Zhangzhou City, Fujian Province, China, has ordered from Andritz, Graz, Austria, a stock preparation system for its new board machine. Startup is scheduled for the end of 2013. The new board machine will produce 600,000 metric tpy of coated board and white top test liner.
Andritz will supply:
- A 250 metric tpd virgin fiber line (northern bleached kraft pulp/leaf bleached kraft pulp, northern unbleached kraft pulp) for the top ply
- A 350 metric tpd OMG/MOW/old books line (old magazines/mixed office waste) for the under top ply
- Components for the 1,300 metric tpd mixed waste line for the filler ply
- A 260 metric tpd ONP line (old newsprint pulp) for the back ply
- A sludge dewatering system and reject treatment components for the recycled fiber lines
- A four-layer paper machine approach system
- A save-all disc filter
- An under-the-machine pulper system (all-in-all eight pulping/slushing units)
- Basic engineering, supervision of erection, commissioning, startup and training, as well as spare and wear part packages for the entire equipment supply.
##SHARELINKS##
|
Metsä Board, Finland, reports that it can now provide more folding boxboard in sheets for customers. Two sheet cutters at its Äänekoski, Finland, mill are now dedicated to providing extra sheeting capacity, initially 70,000 metric tpy, but with further potential for growth.
The Ӓänekoski sheeting plant will process some of the increased folding boxboard capacity at the mill, following the board machine rebuild completed earlier this year, and partially replace outsourced sheeting. The Äänekoski mill's products, Carta Integra and Carta Solida, are designed for high quality packaging and graphics.
"We recognize the growth in demand for our sheeted folding boxboard and as a result have developed our operations at both Äänekoski and Gohrsmühle," says Markku Romano, responsible for cartonboard sales in Europe and MEA.
The Gohrsmühle mill in Germany will open a new Express Board service center for all Metsä Board's folding boxboard grades near the end of this month. The sheeting capacity at Gohrsmühle will be 60,000 metric tpy with the potential for future expansion.
Direct mill orders are recommended to customers who know their product specification and volume well in advance of delivery. Express Board Service, the company notes, is ideal for orders with short delivery lead times and for smaller orders. Customers wishing to take advantage of the new sheeting services should contact their local Metsä Board Sales or Customer Service representative.
##SHARELINKS##
|
In response to strong growth and positive market forecasts for the packaging market, Sappi Fine Paper Europe, Bruissles, Belgium, said that it has begun the process of converting its Alfeld Mill in Germany to exclusively produce one-sided coated paper for packaging, labels, and technical applications. The project will take 12 months to complete. At the same time, Sappi will actively manage its graphic paper capacity by transferring the current coated paper production of the Alfeld Mill to other Sappi Mills in Europe in close consultation with these customers. This action will further improve Sappi's cost position in coated woodfree paper in Europe and elsewhere.
The strong growth and improved margins in this market are due to the growth in the demand for paper packaging and a lack of standardization; high degree of customization; and the long qualification times imposed by customers, Sappi notes. The company also has been successful in the development of innovative and sustainable solutions for this market in close cooperation with end-use customers and converters.
Commenting on the conversion, Sappi Fine Paper Europe CEO Berry Wiersum said that "our decision is in line with the Sappi group strategy to invest in higher growth and higher margin businesses. In addition, it will further improve Sappi's cost position in coated woodfree paper in Europe and elsewhere."
The decision will entail the conversion of paper machine 2 (PM 2) from producing 150,000 metric tpy of coated fine paper to producing 135,000 metric tpy of specialty paper. Paper machines 1, 3, 4, and 5 at the Alfeld Mill already produce jointly 165,000 metric tpy of specialty paper and board.
Once the conversion is complete, the Alfeld Mill will benefit from increased margins, improved quality, increased efficiencies on raw material consumption, and an optimized fixed cost profile. The mill will become the biggest and lowest cost producer of these one-sided coated specialty grades globally, with the converted PM 2 being the fastest and most productive specialty machine in the world. The PM 2 product range will focus on one-sided coated grades from 40–180 gsm for packaging, technical purposes, liner, and label applications.
##SHARELINKS##
|
Sonoco Recycling, a unit of Sonoco, Hartsville, S.C., USA, and one of the largest packaging recyclers in North America, has completed a $2 million upgrade at its Onslow County, N.C., materials recovery facility (MRF). The upgrades will allow the MRF to process a higher volume of recyclables.
With locations and expertise worldwide, Sonoco Recycling annually collects more than 3 million tons of old corrugated containers, various grades of paper, metals, and plastics. Currently, Sonoco Recycling operates six MRFs and serves more than 125 communities in which curbside-collected residential and commercial materials are processed. The company also provides recycling programs that identify waste reduction opportunities for many of the largest consumer product companies in the U.S.
"Onslow County is one of the premier coastal counties of North Carolina and environmental stewardship has always been of the utmost importance," said Scott Bost, solid waste director, Onslow County. "With that in mind, we are extremely pleased to partner with Sonoco Recycling to provide long-term recycling capabilities to the citizens of the Onslow County area. Sonoco Recycling's expertise and many years of experience in the recycling industry will continue to move the county forward with efficient and sustainable waste management."
Ray Howard, GM, Sonoco Recycling, agrees. "In the year that we've been here, we've found the Onslow community to be very progressive in the areas of sustainability and recycling. We are excited to provide them with expanded recycling capabilities and help the county continue to move forward in these areas."
In addition to new equipment, the company also added an education room, and has been providing tours to approximately three classes of students per week. Currently, the tours are open to students of all ages, including first grade through high school seniors."
##SHARELINKS##
|
New Products
Voith, Germany, has launched its newly-developed Revolution press felt for board and packaging paper machines. Along with increased drying performance, Voith notes that Revolution ensures shorter startup phases, energy savings, and consistent quality characteristics over its entire service life.
The key innovation of Revolution is its structure, which has a special polymer layer, according to Voith. The felt can thus control the flow of water before, during, and after passage through the nip. This allows it to dewater better and contaminate less. The dry content is higher by up to 2% than with a conventional felt. The self-cleaning effect also helps to ensure that felt performance remains the same over its entire service life.
Voith further points out that paper produced with the aid of Revolution has especially good surface characteristics due to the larger contact surface with the paper or board web, adding that practical testing confirmed that the new felt allows substantially shorter startup times. From the beginning, it says, the level of nip dewatering is very high. Revolution thus has a positive effect on energy balance.
##SHARELINKS##
|
Published Pricing
Koehler Paper Group, Germany, announced this week that it will increase prices for its carbonless paper. The price increases, which have been implemented in Europe and Latin America already in June, are now to be applied in South Africa as well.
Prices for reels and sheets will go up by 6% for shipments from mid-November onwards. The company attributes the increase to ongoing cost increases for raw materials, energy, wages, and transportation.
##SHARELINKS##
|
Metsä Fibre, Finland, will increase the price of Botnia Nordic Pine (northern bleached softwood kraft) in Europe, effective October 1. The new price will be $790 per metric ton, CIF Metsä Fibre's usual European ports.
Metsä Fibre is a global producer of softwood pulp for paper, board, and tissue producers in Europe and the Far East.
##SHARELINKS##
|
People
Ashland Inc., Covington, Ky., USA, this week announced that Janice J. Teal, Ph.D., former group VP and chief scientific officer for Avon Products Inc., has been elected to the company's board of directors. With her election, the Ashland board now has 11 directors.
Dr. Teal brings 28 years of leadership and scientific research experience to Ashland's board. Prior to her retirement from Avon in 2010, she led the company's global research and development team of chemists and scientists, with responsibility for the development and support of Avon's worldwide product lines. Before that, she served as VP of the Avon Skin Care Laboratories, where she led the bioscience research and skin care teams that ultimately led to the growth of the Anew Skin Care brand to more than $1 billion in sales. She had additional responsibility for development of Avon's vitamin and nutritional lines.
Dr. Teal joined Avon in 1982 as a program leader in toxicology and built Avon's first pharmacokinetics and cell culture laboratories. She earned a Ph.D. in pharmacology from Emory University and served as a Research Fellow in toxicology at New York University. She previously served on the board of directors of Arch Chemicals, which was acquired last year by Lonza Group Ltd. In addition to serving on the Ashland board, she is a trustee of Dominican College.
Ashland provides specialty chemicals, technologies, and insights in a wide variety of markets and applications, including tissue and towel, architectural coatings, automotive, construction, energy, food and beverage, personal care, pharmaceutical, and water treatment. The company operates through four commercial units: Ashland Specialty Ingredients, Ashland Water Technologies, Ashland Performance Materials, and Ashland Consumer Markets.
##SHARELINKS##
|
The World Containerboard Organisation (WCO), Brussels, Belgium, has elected James B. Porter, president of Norcross, Ga., USA,-based RockTenn, to its board of directors. Porter joined the WCO Board on September 15 for a two- year term.
Michael Harwood, WCO president, said that "we are indeed fortunate to have Jim Porter join the distinguished leadership on the WCO Board of Directors. His knowledge and active involvement in all aspects of the containerboard industry are respected and admired by producers and containerboard users around the world. Jim Porter is a tireless champion of this global industry and we are privileged to have his remarkable insight and input on the WCO Board."
The World Containerboard Organisation was founded in 2000 with the purpose of promoting the collection and publication of statistics and other data within the global containerboard industry, and to improve internal and external communications through services and activities that support and supplement those provided by national and regional trade associations.
##SHARELINKS##
|
TAPPI News
SuperCorrExpo, Oct.1-4, 2012, in Atlanta, Ga., USA, is your one-stop shop for all things corrugated. In addition to the nearly 300 exhibitors on the show floor, you can also take advantage of the pre-conference workshops, the joint TAPPI/AICC conference program featuring six keynote presentations and eight multi-track workshops, as well as countless networking opportunities like the Welcome Reception at 200 Peachtree on Sunday, September 30.
And, just added to the jam-packed program, there is now a Folding Carton Workshop sponsored by PIRA. Join Strategic Consultant Dr. Graham Moore on Thursday, October 4, as he provides an overview of the carton board sector and insight into the value added innovations that are attracting attention in the carton board market and increasing the functionality of the products. A separate registration is required for this workshop.
See for yourself why SuperCorrExpo is One Week. One Conference. One Can't Miss Event!
Register today!
##SHARELINKS##
|
New Program Addition: Safety Training Session (Session 13 led by Matthew Kanneberg, RockTenn) an interactive training session sponsored by the Pulp and Paper Safety Association exploring the four (4) stages of safety learning and help participants identify their current organizational safety level. This analysis will identify actions needed to support an injury free team from planning through implementation to delivering safe solutions throughout the organization.
PEERS is a "must attend" event for anyone seeking to make their mill run more efficiently. The Pulping Program focuses on ways to improve kraft pulping to afford pulps that are more uniform in quality and to afford higher pulp yields. The Engineering Program has added a focused one-day session focusing on OpEx Maintenance and Reliability. The Environmental Program will address the challenges and costs involved in keeping up with the regulations of the U.S. paper industry. The Recycling Program brings together experts from around the world to present new technological breakthroughs related to fractional pulping, absorption deinking and electrostatic deinking. Keynote Speaker Don Roberts will discuss why the pulp and paper industry should be open to change by presenting a case study in commercializing an emerging bio-energy technology and the key success factors as part of the Sustainability Program.
Your investment of time and money will go far with the full program of both educational and career networking opportunities presented at PEERS 2012.
PEERS is co-located with IBBC, the only conference that is dedicated to examining applications of biorefineries in the pulp and paper industry - offering you a deeper analysis of technology and economics in commercializing biorefineries. See the Full Program.
##SHARELINKS##
|
Attend this FREE TAPPI Webinar!
Process Control: Combat Process Disturbances and Interactions
Time: 12:00 p.m. to 1:00 p.m. EST
Monday, October 10, 2012
Learn how to employ new tools to easily assess the effects of interactions and disturbances on your process (the models) and how to use these to break or eliminate loop interactions and the effects of disturbances. Appropriate for managers, process engineers, and process control engineers.
Register to attend
This webinar is presented by TAPPI's Process Control Division and was selected as the best Process Control Paper at PaperCon 2011.
Participants will receive a 25% discount on Paper Machine Quality Control Systems - Volume 1: Measurement Systems and Product Variability by the Quality Control Systems Education Common Interest Group of the Process Control Division.
##SHARELINKS##
|
If you've ever wanted to feel more confident in working with important financial information at your mill, understanding the costs of running operations, or perhaps in putting the financial structure behind an idea, this course is for you.
The Financial and Strategic Analysis Workshop for Pulp & Paper and Related Industries is taught by instructors with decades of leadership in the business operations of the pulp and paper industry.
North Carolina State University and TAPPI have partnered to offer this exceptional course scheduled for October 3-5, 2012, in Raleigh, N.C., USA.
You'll learn both basic and sophisticated tools to help you analyze and manage important financial information with more confidence.
Understand the critical role of reinvesting in pulp and paper mill assets to ensure long-term survival and prosperity
- Study basics of capital budgeting, cost of capital (cost of debt and cost of equity), and financial indicators to allow you to use these tools to build financial analyses and sell your ideas, products, and services
- Appreciate the importance of cost structure and how you can increase your competitive advantage by managing your costs
- Explain in financial terms the impact of your operation, research, new technique, or new product
- Build an entire financial analysis from the ground up
- Learn the basics for strategic planning and decision making.
Learn more about the instructors and curriculum with this printable schedule.
##SHARELINKS##
|
The Corrugated Containers Manufacturing Process
Authors: Jody A. Brittain, Stephen R. Perkins, and Philip G. Schnell
This comprehensive textbook describes the entire process of manufacturing corrugated containers. In addition to detailed explanations, the book also features practical troubleshooting tips and a discussion of common problems and solutions within each major section. Seven detailed chapters cover the following topics:
- Paper and the Papermaking Process
- Steam
- Corrugating Adhesives
- Singleface Operations
- Doublebacker Process
- Combined Board
- Converting.
This textbook is designed to provide in-depth explanations and information for professionals working in all areas of the corrugated containers industry.
Product Code: 0101R281
Member Price: $37.00
Non-Member Price: $185.00
##SHARELINKS##
|
Join us at this new lovely golf center near Memphis, Tenn., USA to hit a bucket of balls and enjoy food and fellowship at our Driving Range Fundraiser. Proceeds will support scholarships at Christian Brothers University Packaging Program.
The event will be held in Cordova, Tennessee on October 22 from 5:30 - 9:30pm.
Prizes all for a great cause!
- Team & Individual Events
- Longest Drive
- Nearest the pin
- Silent Auction
- Golf Trivia
- And much, much more...
Visit www.tappi.org/CBUFundraiser for more information and to learn about sponsorship opportunities.
##SHARELINKS##
|
This text, edited by Carlton W. Dence and Douglas W. Reeve, covers fundamentals and processes from the chemical composition of pulp to the technology, production, and the environmental impact of bleaching. Designed as both a textbook and a reference book, Pulp Bleaching: Principles and Practice explains what bleaching is, why pulp is bleached, and how bleaching is done.
The book also features discussions on several "hot topics" in pulp bleaching, including elemental chlorine free bleaching, totally chlorine free bleaching, enzyme assisted bleaching, and bleaching of recycled fiber. In addition, the book is key-word indexed and each chapter contains extensive references.
Pulp Bleaching: Principles and Practice
Product code: 0102B061
Member Price: $124.00
Non-Member Price: $186.00
##SHARELINKS##
|
Are you someone who could benefit from an overview of the entire pulping and paper-making process?
If so, The 2012 TAPPI Hands-On Workshop for Pulp and Paper Basics might be the perfect course for you to learn about the fundamental processes and operations of the pulping and paper-making industry. This year's workshop runs from October 1-5 at North Carolina State University in Raleigh, North Carolina, USA. Reserve your place now so that you can:
- Find out how different processes affect paper properties
- Perform hands-on laboratory experiments to support your understanding of the process
- Run a pilot plant paper machine
- Solidify your knowledge from close interaction with professors in small, interactive groups
Be among the first 32 people to register for this five-day workshop, and you will gain an invaluable overview of pulping, bleaching, chemical recovery, recycling, paper-making and converting. You'll receive course notes, an accompanying CD-ROM, and your own polo shirt. You will also have the opportunity to earn 3.7 CEUs.
This workshop is ideal for new process engineers, manufacturing operators and technicians, sales and service personnel, machine operators, and maintenance personnel. Everyone who wants a better understanding of the basic operation of the pulp and paper business will benefit from this course.
This course typically fills quickly, so don't wait long.
We look forward to seeing you in Raleigh this October!
##SHARELINKS##
|
Biomass Subcommittee Hosts Webinar Featuring Biomass Modeling Tool
As the competition for biomass increases, there is a growing need to more rigorously understand and predict supply availability, sustainability, and economic feasibility of biomass sources. This is true for existing pulp mills as well as new biorefineries.
TAPPI's Biomass Supply, Handling & Handling Subcommittee is hosting a webinar for their next subcommittee meeting featuring a new modeling tool available from Enegis: Biomass Energy Analytical Model (BEAM). BEAM can assess biomass energy availability, including transport options and delivery costs, modeling resources from field/forest, through processing, to determining demand - providing a geographic quantification, storage, and densification options as well as transportation analysis.
The model has a 30 meters resolution for the lower 48 states, and currently carries about 50 species and commodities as it performs analysis with costs of net energy and net carbon carried forward at all modeling steps. BEAM can conduct assessments on a site-specific, regional, or national-scale. Focus on residuals, consistent with the American Council on Renewable Energy (ACORE) proposed definition of biomass, has been run in a number of cases including mark to market. BEAM was originally developed for the Federal Energy Management Program.
Please come join us for the next subcommittee meeting and this presentation on Tuesday, October 9th from 1:00-2:00 PM.Subcommittee Chair Bob Hurter and Vice-Chair Bill Fuller will provide an update on subcommittee activities.
Webinar Registration
- This webinar is free to all who are interested!. Click here to register for this one-of-a-kind opportunity to learn about cutting-edge technology and commercial strategies as it relates to new business opportunities in the biomass sector.
##SHARELINKS##
|
TAPPI's International Bioenergy and BioProducts Conference, October 17-19, 2012 in Savannah, Ga., USA will focus on advancements and commercialization of bioconversions that leverage the forest products manufacturing infrastructure, providing you with a deeper analysis of the technology and economics involved in commercializing biorefineries. Click here to learn more about the IBBC full technical program.
Keynote Speakers:
- Paul Spindler, VP of Technology at Catchlight
- John B. Crowe, Chairman and CEO, Buckeye Technologies, Inc.
In addition, IBBC will include technical presentations, expert panels, case studies, and reports from projects that address:
- Feedstock and harvesting improvements to increase yield and quality of biomass
- Bioconversion technologies for wood and biomass
- Production of chemicals and transportation fuels from wood and biomass
- Commercial bioenergy products using woody biomass
- Tools for evaluating bioenergy projects.
IBBC will be co-located with the TAPPI PEERS Conference, creating a value-added opportunity for participants to expand their learning, networking, and resources by attending both events.
Exhibit and Sponsorship opportunities are available. Contact Shane Holt via e-mail or at 800.369.6220, ext. 3345 for more information.
##SHARELINKS##
|
The 2012 TAPPI Internatioal Bioenergy & Bioproducts Conference, taking place October 17-19 in Savannah, Ga., USA, offers you a deeper analysis of technology and economics in commercializing biorefineries. IBBC is the only event dedicated to advancing biorefineries in the forest products industry. Hear the latest on biomass development, as well as the thermochemical and biochemical-based technologies that can be profitably integrated into pulp mills.
Please note that discounted registration for IBBC has been extended to September 21. In addition, discounted hotel rooms at the host hotel, the Savannah Marriott Riverside, are available on a first-come, first-serve basis through September 21.
Program Highlights:
Session 4: Bioenergy Policy: Three Perspectives
Panel Moderator: Steve Betzler - Paper Segment Leader, Minnesota Power
Wednesday, October 17, 2012 - 4:00-5:30pm
Panel Themes: What role can government policies play in the development of bioenergy in the forest products industry in North America? Come and hear three policy experts assess recent bioenergy policy impacts and discuss future priorities for Canadian and US policies. Panelists include representatives of two forest industry public policy organizations (FPAC and AF&PA) and a representative of a major industrial forestland owner. A timely topic for the election seasons in North America...
Panelists:
Catherine Cobden - Executive VP, Forest Products Association of Canada
Mike Jostrom - Director Renewable Resources, Plum Creek
Paul Noe - Vice President for Public Policy, American Forest & Paper Association
Learn more about IBBC.
Click here to see the entire program.
##SHARELINKS##
|
Gain a better understanding of kraft pulping operations and the effect of process on quality.
An encore, one-day presentation of the popular Intro to Kraft Pulping Workshop will be held in conjunction with the 2012 TAPPI PEERS Conference, October 14-17 in Savannah, Ga., USA. This workshop, held on Saturday, October 13, will be lead by Dr. Michael J. Kocurek, Professor Emeritus of Paper Science and Engineering at North Carolina State University.
The Intro to Kraft Pulping Workshop is a condensed version of the pulping portion of the full course. The overall course objective is to give participants increased understanding of kraft pulping operations, awareness of how one part of the process affects other operations, and the effect of processes on kraft pulp quality.
Learn more about this workshop.
Pulp and Paper Companies Get Discounted Registration!
TAPPI offers a discounted registration to pulp and paper mills and their corporate offices to attend the PEERS Conference. Bring an unlimited number from your mill or office to visit for one day, one hour, or just to drop in and see the Trade Fair! Learn more.
Register Now for PEERS and Save!
The 2012 TAPPI PEERS Conference will be co-located with the International Bioenergy and Bioproducts Conference, creating a value-added opportunity for you to expand your learning, networking and resources by attending both events.
See you in Savannah!
##SHARELINKS##
|
Operating Excellence (OpEx) Maintenance and Reliability Seminar at PEERS
This is a first-time program for the 2012 TAPPI PEERS Conference.
Maintenance and reliability continue to be critical to the efficient operation of pulp and paper mills worldwide, just behind fiber and labor as top production cost factors.
This one-day seminar explores the latest reliability strategies today's mills are implementing to stay in-tune and competitive under progressively lean operating conditions.
The OpEx Maintenance and Reliability Track, included in your PEERS registration at no extra cost, is part of the Engineering Program.
If you are only interested in attending the OpEx Track, select the Single Day PEERS Registration for Thursday, October 18. This year's PEERS Conference includes a full program of educational opportunities for maintenance and reliability personnel, including:
- Sunday, Oct. 14: Fixed Equipment Maintenance Optimization System Course (Additional Fee)
- Monday, Oct. 15 - Wednesday, Oct. 17: Corrosion & Materials Engineering Track
- Thursday, Oct. 18: OpEx Maintenance and Reliability Track.
In addition, 2012 TAPPI PEERS Conference, October 14-17 in Savannah, Ga., features a detailed technical program. Five programming tracks of peer-reviewed sessions, Pulping, Engineering, Environmental, Recycling and Sustainability, will answer the most pressing business and technical questions faced by pulp and paper companies as they manage raw materials, assets, regulatory requirements and production assets.
Register now and save.
The 2012 TAPPI PEERS Conference will be co-located with the 2012 International Bioenergy and Bioproducts Conference, creating a value-added opportunity for you to expand your learning, networking, and resources by attending both events.
See you in Savannah!
##SHARELINKS##
|
Attend the Fixed Equipment Maintenance Optimization System Workshop (FEMOS)
Sunday, October 14, 2012; 8:00 a.m. - 5:00 p.m.
Mills annually spend millions of dollars inspecting, repairing, and recovering from unexpected leaks in boiler tubes, tanks, pressure vessels, exposed and buried pipes, stacks, bleach towers, etc. – learn how to substantially reduce those costs! Corrosion Probe Inc.'s FEMOS Workshop training shows maintenance staff how to rationally manage the mechanical (containment) integrity of all types of fixed equipment with a simple, rigorous system utilizing comparable disciplines and procedures promoted by vendors specializing in maintenance of rotating equipment.
What will you learn?
The workshop teaches attendees how to implement a mill-specific program by using a transparent and disciplined process to systematically design the right inspection plan for each major piece of fixed equipment based on its materials of construction, present condition and service conditions. The basic concept employs proven, high-value practices from refining and petrochemical industries for risk-based inspection, customizing inspection plans to possible damage mechanisms and using fitness-for-service engineering assessments to define damage limits.
Who is leading the workshop?
Corrosion Probe Inc.'s experienced and renowned TAPPI participants Dave Bennett, David Crowe, and Doug Sherman, will train up to 20 people in a one-day (6-hour) workshop. Training is presented so attendees can use their new knowledge to immediately implement FEMOS at their mill. Many working examples are provided and students are invited to bring their mill's costliest fixed equipment inspection/ maintenance concern for case analysis.
The workshop takes place just before the TAPPI PEERS and IBBC conferences so those attending the FEMOS workshop can also attend these important events.
Learn more about PEERS 2012...
##SHARELINKS##
|
Why Whitewater Filtration Systems Fail
Time: 12:00 p.m. to 1:00 p.m. EST
Wednesday, November 14, 2012
This free webinar from TAPPI addresses why whitewater filtration systems are often problematic and in some instances fail completely. The presentation will explain why filtration systems fail under certain conditions and offers the best solutions to improve the overall reliability of the process.
Attendees will learn:
- Significance of process variation on equipment performance
- The negative cost impact associated with poor system performance
- New sensor technology that is making the system "visible"
- Cutting-edge strategies to manage the process variation
- How to develop a "roadmap' for system optimization.
Learn more and register
##SHARELINKS##
|
On Nov. 7-9, 2012, TAPPI will conduct its Tissue Runnability Course in Neenah, Wi., USA.
This special course is being taught by technical experts in each area of the machine from wet end operations through creping and process control. The experienced, highly qualified faculty for this course will provide a thorough understanding of the entire tissue making process and current best practices in each area.
Wednesday's (November 7) classes will focus on stock preparation and wet end operations, while Tuesday's (November 8) classes cover pressing, drying, and doctoring. Wednesday (November 9) classes examine technologies and latest developments in hoods, TAD (through-air drying), and other dynamics of the tissue machine dry end,
The 2012 TAPPI Tissue Runnability Course is designed for process engineers, machine supervisors, and reliability professionals who have to maximize uptime and saleable production. It is also an excellent tutorial for suppliers who support tissue making customers. It will help attendees:
- Improve tissue quality and consistency
- Understand contributors to waste and downtime
- Learn reliability and maintenance best practices
- Diagnose and troubleshoot problems quickly.
After successfully completing this course, attendees will specifically be able to:
- Diagnose the impact of recycled furnishes on tissue properties
- Make changes to wet-end chemistry to improve machine operations
- Improve cleaning and conditioning of fabrics
- Troubleshoot runnability problems in the press, Yankee, and creping systems
- Identify improvement opportunities on the dry end
- Pinpoint productivity opportunities in Yankee steam, coating, and hood systems.
TAPPI will award CEU credits to participants who attend at least 80% of the educational sessions and complete a final program evaluation.
The 2012 Tissue Runnabilitry Course includes advanced process instruction. If you are looking for an introductory-intermediate tissue course, consider the upcoming 2012 Tissue Properties and Manufacturing Course at TAPPI Headquarters in Norcross, Ga., USA, on August 15-16.
Attendance for the 2012 TAPPI Tissue Runnability Course is limited, so please register today at the course website.
##SHARELINKS##
|
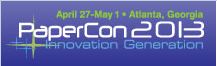
A Call for Papers has been issued for PaperCon 2013. Theme is "Innovation Generation."
After record attendance in 2012, PaperCon will again bring together CEOs, mill managers, superintendents, scientists, process engineers, and suppliers for the largest pulp and paper technical program in the world. The event will take place April 27 to May 1 in Atlanta, Ga., USA. Learn more about PaperCon 2013.
For 2013, PaperCon is pleased to welcome the Tissue360 Forum, NETInc (Innovative Nonwovens Conference), RPTA (Recycled Paperboard Technical Association) P-T Seminar and the OpEx Reliability Workshop. Each of these events is open to full PaperCon registrants and papers in these areas are welcome.
Calls for Papers and Posters have been issued. The conference theme is Innovation Generation, and authors are encouraged to include this within their papers. Topics under consideration include mill management, papermaking, coating, tissue, nonwovens, and recycled paperboard. Paper company personnel, suppliers, academics, and students are strongly encouraged to submit their ideas for papers, posters, or roundtable discussions.
Papermakers Program:
The Papermakers Program encourages topics on paper machine performance evaluations, papermaking fundamentals, product/process optimization, recycled paperboard, tissue making (Tissue360 Forum), and the RPTA P-T Seminar. The deadline for submission of abstracts is November 20, 2012. Abstracts for panel discussions and roundtables are welcome. See Papermakers Program Call for Papers.
Coating and Graphic Arts Program:
The Coating and Graphic Arts Program will focus on The Future of Print and its Demands on Paper and Coatings. The deadline for extended abstracts for this program is Oct. 16, 2012. See the Coating and Graphic Arts Program Call for Papers.
All abstracts must be submitted using TAPPI's Speaker Management System for consideration by the TAPPI and RPTA program committees.
##SHARELINKS##
|
Frank Romano to Keynote at PaperCon 2013
Frank Romano, Professor Emeritus, Rochester Institute of Technology, will Keynote at Papercon 2013 on Sunday, April 21. Focusing on "Innovation and the Future of Print," Romano will kick-off PaperCon's Coating and Graphic Arts Program.
Romano's career has spanned an impressive 53 years in the printing and publishing industries. Many know him as the editor of the International Paper "Pocket Pal" for 30 years, or have read one of the thousands of articles he has written. He is the author of 52 books, including the 10,000-term Encyclopedia of Graphic Communications (with Richard Romano), the standard reference in the field.
Learn more about Romano.
PaperCon 2013 will take place April 27 through May 1 in Atlanta, Ga., USA. Designed by industry professionals, PaperCon brings together CEOs, mill managers, superintendents, scientists, process engineers and suppliers for the largest pulp and paper technical program in the world. No other event provides such a comprehensive program, networking opportunities, and trade fair among such a distinguished group of industry leaders.
Learn more about PaperCon 2013.
Registration information, including special mill reservation deals, are now available at the PaperCon website.
##SHARELINKS##
|
The 20 volumes of Papermaking Science and Technology bookseries cover the entire paper manufacturing process from wood raw material to end product, providing a basis for university-level education, for updating training courses, and as handbooks for the industry. The bookseries has been updated and second editions are now available. TAPPI members can place an order by contacting The Finnish Paper Engineers' Association. Please contact Mary Anne Cauthen, Member Group Coordinator, at +1.770.209.7352 or by e-mail at MCauthen@TAPPI.org
These books can be purchased individually or as a set.
This 20 volume set includes:
- Volume 1 - Economics of the Pulp and Paper Industry
- Volume 2 - Forest Resources and Sustainable Management
- Volume 3 - Forest Products Chemistry
- Volume 4 - Papermaking Chemistry
- Volume 5 - Mechanical Pulping
- Volume 6, part 1 - Chemical Pulping Part 1, Fiber Chemistry and Technology
- Volume 6, part 2 - Chemical Pulping Part 2, Recovery of Chemicals and Energy
- Volume 7 - Recycled Fiber and Deinking
- Volume 8 - Papermaking Part 1, Stock Preparation and Wet End
- Volume 9 - Papermaking Part 2, Drying
- Volume 10 - Papermaking Part 3, Finishing
- Volume 11 - Pigment Coating and Surface Sizing of Paper
- Volume 12 - Paper and Paperboard Converting
- Volume 13 - Print Media - Principles, Processes, and Quality
- Volume 14 - Process and Maintenance Management
- Volume 15 - Materials, Corrosion Prevention and Maintenance
- Volume 16 - Paper Physics
- Volume 17 - Pulp and Paper Testing
- Volume 18 - Paper and Board Grades
- Volume 19 - Environmental Management and Control
- Volume 20 - Biorefining of Forest Resources
##SHARELINKS##
|
 Member Jay Kaplan has been associated with TAPPI since 1994 when he was living in the Chicago area working for Stone Container. But it wasn't until years later that he finally took full personal advantage of all the benefits inherent in TAPPI membership, "the industry's best resource for technical support and information on emerging technologies and cutting edge science."
Having been mentored early in his career by serveral long-time TAPPI members, Jay says their influence set the groundwork for his future involvement. Through the years he has practiced in numerous meetings and shows at both the local and national level, and is now very involved in SuperCorrExpo, the largest tradeshow in the western hemisphere catering to the corrugated industry. "It's through events like these that you form and nurture professional relationships that help drive sustainable business improvements that may not have been achieved as quickly or at all without the common ground and opportunity that TAPPI provides."
Jay also believes this exposure to emerging technologies, technical expertise, and experts from outside his own company have played an integral role in his professional growth. Now serving as the Manager for Learning an Organizational Development for Corrugated Packaging at RockTenn, he says that use of TAPPI's website, the eLibrary, technical support, and industry news are all important elements to stay on the cutting edge of your career. And, furthermore, Jay puts his actions where his words are. Not content to just tell his peers and fellow employees about the benefits of membership, he recently brought a new group of new and future production managers to TAPPI's headquarters in Norcross, Ga., USA, for a tour and afternoon of learning. "I believe they left feeling a lot more informed about what our industry has to offer," he said.
To read more about Jay's professional accomplishments and personal interests, be sure to visit this month's Member Spotlight page.
##SHARELINKS##
|
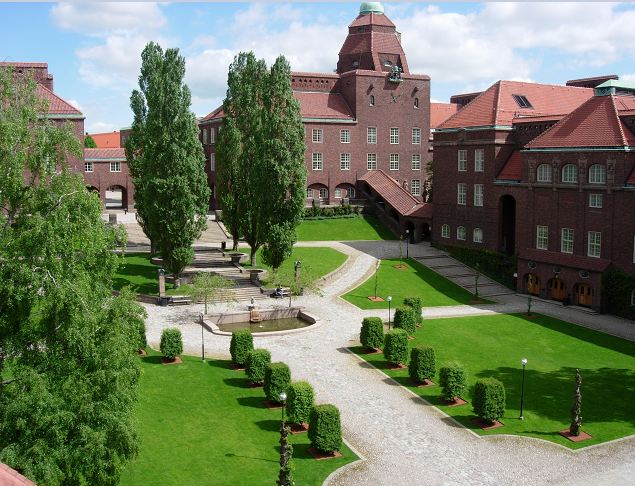 The 2013 TAPPI International Conference on Nanotechnology for Renewable Materials will be held July 24-27, 2013, on the KTH Royal Institute of Technology campus in Stockholm, Sweden. Industry experts, scientists, health and safety specialists, legal and government policy makers, as well as the field's leading researchers will discuss the latest in nanotechnology research and development.
The 2013 Technical Program Committee has issued a Call for Papers inviting contributions from participants working in research, development, and deployment of renewable nanomaterials.
Abstracts are due by December 3, 2012.
##SHARELINKS##
|
Make your plans now to join a host of professionals from industry, universities and research institutes at the 14th TAPPI European PLACE Conference, which will be held May 6-8, 2013, at the Swissotel in Dresden, Germany.
The Call for Papers is now officially open. Submit your abstract and take an active role in this not-to-miss event!
##SHARELINKS##
|
|
|