Over the Wire
TAPPI
Weekly Spotlight
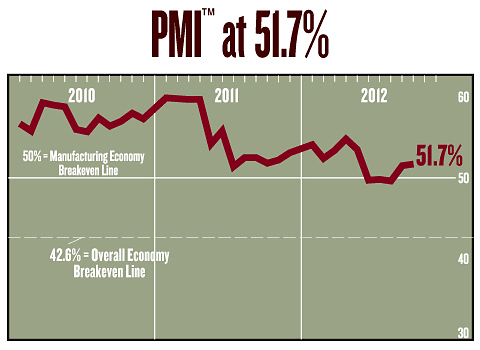 Economic activity in the U.S. manufacturing sector expanded in October for the second consecutive month following three months of slight contraction, and the overall economy grew for the 41st consecutive month, say the nation's supply executives in the latest Manufacturing ISM Report On Business. The report was issued this week by Bradley J. Holcomb, chair of the Institute for Supply Management's Manufacturing Business Survey Committee, Tempe, Ariz., USA.
According to the report, the PMI™ registered 51.7%, an increase of 0.2 percentage point from September's reading of 51.5%, indicating growth in manufacturing at a slightly faster rate. The New Orders Index registered 54.2%, an increase of 1.9 percentage points from September, indicating growth in new orders for the second consecutive month. The Production Index registered 52.4%, an increase of 2.9 percentage points, indicating growth in production following two months of contraction. The Employment Index registered 52.1%, a decrease of 2.6 percentage points, and the Prices Index registered 55%, reflecting a decrease of 3 percentage points. Comments from the panel this month reflect continued concern over a fragile global economy and soft orders across several manufacturing sectors.
Of the 18 manufacturing industries, eight are reporting growth in October in the following order: Petroleum and Coal Products; Furniture and Related Products; Apparel, Leather, and Allied Products; Paper Products; Miscellaneous Manufacturing; Food, Beverage, and Tobacco Products; Plastics and Rubber Products; and Chemical Products. The eight industries reporting contraction in October (listed in order) are: Primary Metals; Wood Products; Machinery; Fabricated Metal Products; Transportation Equipment; Electrical Equipment, Appliances and Components; Computer and Electronic Products; and Nonmetallic Mineral Products.
The five industries reporting growth in new orders in October are: Furniture and Related Products; Food, Beverage, and Tobacco Products; Paper Products; Computer and Electronic Products; and Miscellaneous Manufacturing. The eight industries reporting a decrease in new orders during October (listed in order) are: Primary Metals; Wood Products; Machinery; Electrical Equipment, Appliances and Components; Transportation Equipment; Chemical Products; Nonmetallic Mineral Products; and Apparel, Leather, and Allied Products.
The six industries reporting growth in production during the month of October (listed in order) are: Furniture and Related Products; Apparel, Leather and Allied Products; Paper Products; Petroleum and Coal Products; Computer and Electronic Products; and Miscellaneous Manufacturing. The seven industries reporting a decrease in production in October (listed in order) are: Primary Metals; Machinery; Wood Products; Plastics and Rubber Products; Transportation Equipment; Food, Beverage, and Tobacco Products; and Nonmetallic Mineral Products.
Of the 18 manufacturing industries, eight reported growth in employment in October in the following order: Apparel, Leather, and Allied Products; Petroleum and Coal Products; Food, Beverage, and Tobacco Products; Paper Products; Miscellaneous Manufacturing; Chemical Products; Transportation Equipment; and Primary Metals. The six industries reporting a decrease in employment in October (listed in order) are: Nonmetallic Mineral Products; Plastics and Rubber Products; Electrical Equipment, Appliances and Components; Fabricated Metal Products; Compute rand Electronic Products; and Wood Products.
Of the 18 manufacturing industries, eight reported paying increased prices during the month of October in the following order: Furniture and Related Products; Food, Beverage, and Tobacco Products; Apparel, Leather, and Allied Products; Nonmetallic Mineral Products; Miscellaneous Manufacturing; Plastics and Rubber Products; Chemical Products; and Transportation Equipment. The four industries reporting paying lower prices during October are: Primary Metals; Machinery; Computer and Electronic Products; and Petroleum and Coal Products.
The five industries reporting growth in new export orders in October are: Wood Products; Nonmetallic Mineral Products; Fabricated Metal Products; Food, Beverage, and Tobacco Products; and Computer and Electronic Products. The eight industries reporting a decrease in new export orders during October (listed in order) are: Transportation Equipment; Chemical Products; Primary Metals; Electrical Equipment, Appliances, and Components; Machinery; Miscellaneous Manufacturing; Paper Products; and Apparel, Leather, and Allied Products.
The five industries reporting growth in imports during the month of October are: Petroleum and Coal Products; Plastics and Rubber Products; Computer and Electronic Products; Food, Beverage, and Tobacco Products; and Fabricated Metal Products. The eight industries reporting a decrease in imports during October (listed in order) are: Wood Products; Nonmetallic Mineral Products; Primary Metals; Paper Products; Transportation Equipment; Machinery; Chemical Products; and Apparel, Leather, and Allied Products.
The full text version of the Manufacturing ISM Report on Business is available online.
##SHARELINKS##
|
Minas Basin Pulp and Power Co., Hantsport, Nova Scotia, a producer of recycled paperboard, reports that it will cease operations in December, putting some 135 workers out of work. Last year the company said that it hoped a restructuring of operations and changes to pricing would make the Hantsport operations sustainable. However, the company notified employees this past week that "after several years of challenge, the board of Scotia Investments Ltd. has concluded that it is time to recognize the mill is at the end of its cycle, Long-term sustainability cannot be achieved."
Minas Basin was founded in 1927, producing a single product—groundwood pulp. It added paperboard capacity in 1946. Currently, the mill produces 100% recycled paperboard products, including linerboard and coreboard, and has a production capacity of 100,000 metric tpy. The mill's 110 in. fourdrinier machine operates at 1,500 fpm, producing two-ply lightweight high performance and regular linerboard.
The company cited challenges in the marketplace, competition from plants using newer and more efficient technology, and rising operating costs as key factors in its decision. In a letter to employees, the company said that while 135 people will lose their jobs, more than 40 employees will be moved to other companies within Scotia Investments. Those companies include CKF Inc., a paper plate manufacturer also located in Hantsport, a town of 1,160.
The letter also said that the company would begin working immediately with the remaining employees to find alternative options and support them through this transition and mill closure. It further noted that the company is not seeking any government assistance and would fulfill its employment obligations, including the pension plan.
Robert Patzelt, Scotia Investments' VP of corporate development, said pouring more money into such a small mill just wouldn't make sense. "Additional money from the government would be inadequate to overcome those structural and economic challenges, he said in an interview with the Canadian Press. "In this instance, you would have to build a new mill and it would have to be huge and it would have to be located somewhere else," Patzelt said.
The former NewPage Port Hawkesbury paper mill in Point Tupper, N.S., shut down in September 2011, but resumed operations last month under the new name Port Hawkesbury Paper, with roughly half the workers it once employed, after the provincial government announced a $124.5-million assistance package. In June, Montreal-based Resolute Forest Products announced closure of the Bowater paper mill in Brooklyn, N.S., throwing 320 people out of work. That came despite a $50-million government offer to the company, $23.75 million of which was spent to buy land.
##SHARELINKS##
|
Orchids Paper Products Co., Pryor, Okla., USA, was recently named to the Forbes 2012 list of the "100 Best Small Companies in America." The Company ranks No. 70 in its first appearance on the list. To qualify as a "100 Best Small Companies" candidate, a company must be publicly traded for at least a year, generate annual revenue between $5 million and $1 billion, and have a stock price higher than $5 a share. Rankings are based on earnings growth, sales growth, and return on equity in the past 12 months and over five years, as well as stock performance versus each company's peer group.
"We are honored to be named by Forbes as one of the best small companies in America. This award, which recognizes our success for both the past year and over the last five-year period, is a testament to our team's continued commitment to providing innovative, high quality products to our customers that provide a great value proposition to the consumer. We are optimistic that Orchids is positioned for continued success in the future," said Robert Snyder, president and CEO.
Orchids Paper Products is an integrated manufacturer of tissue paper products serving the at-home private label consumer market. From its operations in northeast Oklahoma, the company produces a full line of tissue products, including paper towels, bathroom tissue, and paper napkins, to serve the value through premium quality market segments. The company provides these products to retail chains throughout the U.S.
##SHARELINKS##
|
Ashland Inc., Wilmington, Del., USA, was named Best Chemical Supplier of the Year for the Pulp and Paper segment by the Brazilian Pulp & Paper Association (ABTCP) at its recent annual awards. Flavio Parrilha Martins, commercial leader paper, Brazil, accepted the award on behalf of Ashland Water Technologies.
This award was the result of a survey conducted among the pulp and paper companies in Brazil, which gave Ashland the winning endorsement. Ashland was chosen by many pulp and paper companies for its innovative products, technical support, and problem-solving skills.
"Ashland has been a leading supplier of specialty chemicals to the Brazilian pulp and paper industry for many years and we are delighted to receive this award from ABTCP," said Wanderley Flosi Filho, commercial director, Ashland Water Technologies, Latin America. "This award is excellent recognition from the industry and a proof that, with good chemistry great things happen."
ABTCP held its 45rd Pulp and Paper International Congress and Exhibition last month at the Transamérica ExpoCenter in Sao Paulo. There were more than 6,000 attendees from many countries around the world who took part in this three-day convention.
Ashland Water Technologies is a global producer of papermaking chemicals and a specialty chemical supplier to the pulp, mining, food and beverage, paper, chemical processing, general manufacturing, institutional, and municipal markets.
##SHARELINKS##
|
Several Christian Brothers University (CBU), Memphis, Tenn., USA, students, faculty, and staff participated in the recent TAPPI-CBU Driving Range Fundraiser at the new Vantage Point Golf Center in Cordova, Tenn. The event raised a $2,500 scholarship fund for CBU packaging students.
In the photo below are (l-r) Larry Montague (president and CEO of TAPPI), Adam Thornton, Alvin Siow, Phyo Aung, Rhett Jordan, Shawn Breckenridge, Evan Edwards, Mallory Harvey, Palacio Giovanti, Lauren Harrett, and Dr. Pong Malasri (CBU Packaging Department chair).
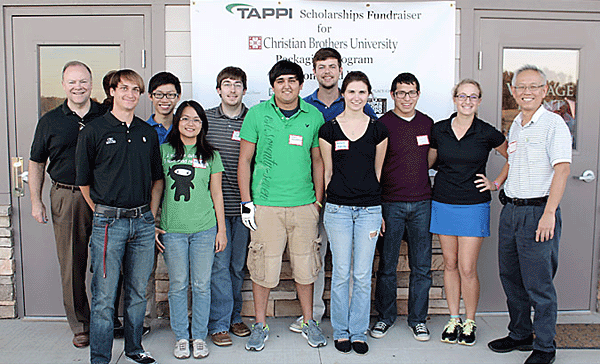
##SHARELINKS##
|
The 2012 NAPIM/NPIRI Technical Conference recently marked its 56th successful year at the Eaglewood Resort and Spa in Itasca, Ill., USA. This year's conference was attended by 140-plus ink manufacturers and suppliers and featured short courses, tabletop exhibits/supplier spotlights, and cutting edge technical and regulatory presentations. This year's conference also featured the Open Board and Annual Awards Dinner, which was attended by more than 150 people.
Jon Graunke of INX International received the 2012 Technical Achievement Award and Rick Krause of BASF Corp. was honored with the TAM Service Award. More information about these awards is available online.
The NPIRI Lecture Series awards, sponsored by Lawter Inc., were also presented at the Open Board/Awards Dinner at this year's conference. The first place winning paper was presented by Charlie Hsu of BASF in the Wednesday morning session. Gene Cassidy of Lawter International presented the first place prize to Charlie Hsu and Rick Grandke of BASF Corp. The second place award was presented to Matt Carroll of Evonik Corp.
##SHARELINKS##
|
Below is the latest listing of job openings in the TAPPI Career Center. The current listing includes job openings for a variety of positions, including technical sales reps, process and electrical engineers, engineering intern, research specialist, and manager of technical services. Current, specific job openings at companies and locations in the TAPPI Career Center include:
Employer |
Title |
City |
Albany International |
Design/App. Eng. Press Fabrics |
St Stephen, S.C. |
BASF, The Chemical Co. |
Technical Sales Rep Sr II |
Spokane/E. Washington |
BASF, The Chemical Co. |
Technical Sales Rep Sr II |
South of Atlanta, Ga. |
BASF, The Chemical Co. |
Technical Sales Rep Sr II |
Eastern Pa. |
BASF, The Chemical Co. |
Technical Sales Rep Sr II |
Upstate, N.Y. |
Boise Inc |
Paper Production Engineer |
Wallula, Wash. |
Boise, Inc |
Process Control Staff Engineer |
Boise, Id. |
Canfor Pulp |
Paper Mach. Specialist, Specialty Paper |
Prince George, B.C., Canada |
Catalyst Paper |
Manager, Technical Services |
Powell River, B.C ., Canada |
Catalyst Paper |
Engineer, Electrical Maintenance |
Crofton, B.C., Canada |
Confidential |
Process Engineer |
Denver, Colo. |
FM Global |
Senior Research Specialist |
Massachusetts |
Norpac-Weyerhaeuser |
Eng. Internship-Norpac/Weyerhaeuser |
Longview, Wash. |
Pactiv |
Principal Engineer |
Pennsylvania |
More information about these jobs is available online.
##SHARELINKS##
|
Market Roundup
Total U.S. pulp and paper industry consumption of recovered paper in September was 2.36 million tons, 8% lower than August 2012, according to the AF&PA (Washington, D.C., USA) September 2012 U.S. Recovered Fiber Monthly Report. Year-to-date total consumption in 2012 is 4% lower than during the same period last year.
U.S. exports of recovered paper, as reported by the U.S. Census Bureau, decreased 4% in August compared with July, led by a drop in mixed papers exports that fell after a very strong July. Year-to-date exports of recovered paper in 2012 are 6.5% lower than during the same period in 2011.
##SHARELINKS##
|
Pulp mills and sawmills in Brazil became more competitive in 2012, mostly thanks to a weakening Brazilian real, according to Wood Resources Quarterly ( WRQ), Seattle, Wash., USA. Pine sawlog prices in Brazil, in U.S. dollar terms, fell 22% in just one year, and prices in the 2Q/12 have been at a level below where they were just before the financial crisis that hit in 2008, WRQ notes. In the local currency, on the other hand, prices have actually increased steadily and in the 2Q/12 were at their highest levels in more than four years.
Domestic demand for wood products has been a key driver for the higher log costs. In 2010 and 2011, the local lumber market was strong because of major investments in the housing construction sector in Brazil, WRQ continues. This market slowed in 2012, and instead, lumber and plywood exports have slowly picked up steam as those sectors have benefited from the weakening Brazilian real and the Brazilian forest industry became more competitive in the international market.
With the real expected to continue to stay weak against the U.S. dollar, market participants are hoping for increased exports of lumber, plywood, and value-added products in the coming months. If this scenario actually comes to fruition, demand for sawlogs may go up and log prices will likely move up in both real and dollar terms. Although Brazilian pulplog prices have not changed much in the local currency, they have fallen dramatically in U.S. dollar terms as the real weakened this past year. Eucalyptus pulplog prices in the 2Q/12 were down 28% from the same quarter in 2011, while pine pulplog prices declined 26% from a year ago, according to the WRQ.
The recent dramatic price reductions of pulpwood have had the result that wood costs for Brazilian pulp mills now are among the lowest of all regions tracked by the WRQ, compared with a year ago when wood fiber costs in Brazil were above the Global Wood Fiber Price Indices (SFPI and HFPI). Since wood fiber costs accounted for about 70% of the production costs for pulp mills in Brazil in the 2Q/12, the substantial reduction in pulpwood prices has made the country's pulp mills more competitive in 2012 relative to other pulp producers around the world.
More information is available online.
##SHARELINKS##
|
Ilim Group, Russia, reports that during the first nine months of 2012, its mills in northwestern Russia and in Siberia manufactured 1,928,000 metric tons of pulp and paper products, which is slightly more than for the same period last year. The output of market pulp reached 1,224,000 tons, which is a 2% growth against last year.
Ilim's market containerboard production totaled 525,000 metric tons, 2% less than in the first nine months of 2011. Paper production rose 5%, reaching 179,000 metric tons. OAO Ilim Gofra, corrugated box business of Ilim Group in the Leningrad Oblast, increased its production volumes by 4.5% to reach 94,248,000 square meters of corrugated products.
##SHARELINKS##
|
Pulp & Paper
Arctic Paper S.A., Poland, yesterday (November 7) announced a public offer to acquire all shares in Rottneros AB, Sweden, a non-integrated and customized supplier of paper pulp. Rottneros' board of directors has unanimously recommended the offer.
The combined group will be a European producer of bulky book paper, graphic fine paper, and pulp for paper producers. In addition, it will remain a significant supplier of market pulp. The combined group will have a good balance between pulp production and consumption in the fine paper mills and will thus be less volatile than the two companies as stand-alone entities, Arctic Paper notes. It will have four fine paper mills and two pulp mills.
Arctic Paper does not anticipate any material effects of the implementation of the offer for Rottneros' business or employees, including employment conditions and employment levels at locations where Rottneros currently conducts business.
Until the completion of the offer, Rottneros and Arctic Paper will operate as two independent listed companies with their current boards and management teams, respectively.
Arctic Paper has its roots in the Swedish Trebruk AB group, established in 1990 with Munkedal as one of the mills. Over time, Arctic Paper has expanded geographically to become the second-largest European producer of bulky book paper and one of Europe's leading producers of fine graphic paper. Arctic Paper is a major purchaser of paper pulp, from which it produces numerous types of paper for printing houses, paper distributors, book and magazine publishing houses, and the advertising industry.
The group's paper mills are located in Sweden (Grycksbo and Munkedal), Poland (Kostrzyn nad Odra), and Germany (Mochenwangen), with a total annual production capacity of more than 800,000 metric tons of paper. Through 15 wholly-owned sales and distribution companies, Arctic Paper has access to all European markets. In 2011, the company employed close to 1,600 people and its consolidated sales revenue amounted to PLN 2,527 million (SEK 5,551 million).
Rottneros operates two pulp mills in Sweden, the Rottneros Mill (first photo below) and the Vallvik Mill (second photo below), with a total annual production capacity of approximately 400,000 metric tons. In 2011, Rottneros employed around 300 people and its consolidated sales revenue amounted to SEK 1,513 million (PLN 689 million).
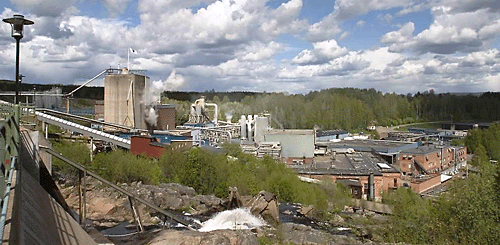
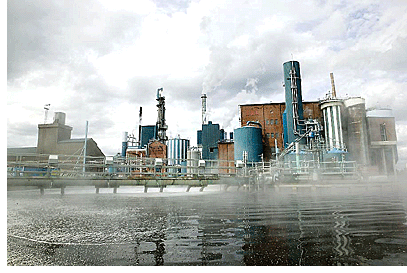
##SHARELINKS##
|
PaperlinX Ltd., Australia, this week confirmed that it has completed the sale of its operations in Slovakia, Hungary, Slovenia, Croatia, and Serbia to Heinzel Group's (Vienna, Austria) subsidiary Europapier Group. In the transaction, Europapier International AG took control of all shares in Budapest Papir Kft., Bratislavska Papierenska Spolocnost s.r.o., Alpe Papir Trgovina na debelo d.o.o., Adria Papir d.o.o., and Dunav Papir d.o.o., effective November 1.
Europapier received clearance from competition authorities in each of the five countries without any restrictions, as expected. Europapier management says it intends to combine the strength of both enterprises in these markets and to utilize all potential synergies by merging businesses into one strong organization per country.
Europapier Group employs about 770 people and has an annual sales volume of around 445,000 metric tons. The Heinzel Group, which is united under the Heinzel Holding umbrella, ranks with its subsidiaries Zellstoff Pöls AG (Austria) and AS Estonian Cell (Estonia) among the largest producers of market pulp in central and eastern Europe. The Group's trading division includes Wilfried Heinzel AG, a globally active pulp and paper trading company, and Europapier International, a leading paper merchant in the CEE region.
##SHARELINKS##
|
International Paper, Memphis, Tenn., USA, announced this week that it will donate more than 8,100 acres of land, which includes the Bussey Brake and Wham Brake reservoirs, to the Louisiana Department of Wildlife and Fisheries (LDWF). The total donation is valued at $7.8 million-plus. The fresh water reservoirs located near Bastrop, La., in Morehouse Parish are popular recreational sites.
"This donation by International Paper will preserve these reservoirs for future generations to come for the citizens of Louisiana," said Tommy Joseph, International Paper SVP. "We are excited to be able to make this announcement today."
LDWF Secretary Robert Barham added that "preserving fish and game habitat for public use is a key component in the department's conservation mission. IP's generous donation falls right in line with our public access initiatives."
Bussey Brake, a 2,600-acre fresh water reservoir, was constructed in the mid-1950s by IP to serve as an alternative water source for the Louisiana Mill. IP owned 620 acres of the reservoir site with the remaining balance under leases with third parties. Under terms of the donation, the leases will be transferred to LDWF.
LDWF plans for Bussey Brake include a complete renovation of the reservoir's fish population. The impoundment will be drained and allowed to dry completely. The current fish population will be removed and the reservoir stocked with popular game fish including bass, bream, catfish, and crappie. Once re-stocked, the reservoir will be monitored and managed with recreational fisheries a priority. The renovation process will take three to five years to achieve success and the resulting fish population, once established, would self-sustain as healthy fisheries for several decades.
Wham Brake was also constructed in the 1950s on IP lands though a joint effort with the U.S. Army Corp of Engineers. The 5,550-acre reservoir will become part of the (21,948 acre) LDWF's Russell-Sage Wildlife Management Area, providing preservation of wildlife habitat for future generations. LDWF will partner with Ducks Unlimited to initiate a hydrologic survey of Wham Brake to determine a management strategy for this vitally important waterfowl area. Planned site improvements include better hunter access through additional boat launches and parking areas, improved water delivery systems, and more uniform moist soil management units creating added acres of waterfowl habitat.
##SHARELINKS##
|
Resolute Forest Products, Montreal, Que., Canada, this week reported that it will permanently shut down paper machine No. 10 at its Laurentide mill in Shawinigan, Que. The company noted that the permanent shutdown comes after an "important drop in demand and an increase in market capacity of the paper grade produced on machine No. 10."
The Laurentide mill, which currently has 388 employees, produces more than 350,000 metric tpy of commercial printing papers with two machines. Machine No. 10, which produces 125,000 metric tpy, will cease production on November 26, eliminating nearly 111 jobs. The shutdown will not affect paper machine No. 11, which has a production capacity of nearly 225,000 metric tpy.
The company said that it is aware of the impacts this decision will have on the employees concerned and their families and will work with union representatives and the governments to mitigate these impacts with a focus on retirement. "Management intends to make sure that all of the employees affected receive the necessary support, in compliance with the relevant collective agreement terms, and that as many employees as possible are reassigned to other company facilities," Resolute stated.
Resolute President and CEO Richard Garneau noted that market demand and capacity, the strong Canadian dollar, rising freight and fuel costs, and the continuing high cost of fiber also factored into management's decision. "Resolute must prove that it is profitable with mills that perform well, which forces us to improve our competitive edge by focusing on our best assets and cutting costs. This is a major challenge and we are confident that we, with our employees, will be able to meet it."
Resolute Forest Products is a producer of newsprint, commercial printing papers, market pulp, and wood products. The company owns or operates 22 pulp and paper mills and 22 wood products facilities in the U.S., Canada, and South Korea.
##SHARELINKS##
|
Sappi, South Africa, will use automated process valves supplied by Metso, Finland, in its fiberline expansion at the Ngodwana mill. In this project, called Go-Cell, the existing fiberline is being expanded to produce chemical (specialized) cellulose, also known as dissolving pulp. In total, more than 700 automated valves will be delivered during the final quarter of 2012, and the mill startup is scheduled for early 2013.
Metso will provide all of the automated on-off and control valves with intelligent Profibus positioners for the new fiberline, and for upgraded process areas in evaporation, recausticizing, and ash leaching. The delivery includes valves in stainless steel, duplex stainless steel, titanium, SMO, and ceramic material in sizes from DN25 to DN500. All valves are equipped with pneumatic cylinder actuators and intelligent positioners or limit switches. The delivery also includes Neles metal-seated ball valves, segment and triple eccentric Neldisc butterfly valves, as well as Jamesbury soft-seated ball valves.
In addition to typical process valves, Metso will also supply specially designed high-consistency valves for the fiberline as well as capping and discharge valves for six batch digesters for the cooking plant. All of these high-performance solutions will support the mill's goals of increased efficiency and reduced energy consumption.
The expanded fiberline will produce 210, 000 metric tpy of chemical (specialized) cellulose, which is widely used in the textile, pharmaceutical, and food industries. Sappi is the global leader in chemical (specialized) cellulose production.
##SHARELINKS##
|
S.A. Industrias Celulosa Aragonesa (SAICA), reports that it has successfully started up a fibrous reject compacting line at its El Burgo de Ebro mill in Saragossa, Spain. The three new Andritz (Graz, Austria) Reject Compactors are part of an existing waste-to-power line and have a total capacity to process 500 metric tons of wet rejects per day. The wet rejects consist of various fiber residues and plastics produced in a recycled fiber processing line at the mill, which is used in the production of industrial grades of paper.
By removing the water and compacting the rejects, the heating value of the rejects is improved and SAICA obtains a higher electricity output from its power boiler and turbine-generator.
##SHARELINKS##
|
SCA, Stockholm, Sweden, plans to gradually reduce and eventually stop the production of newsprint on its PM 2 at the Ortviken mill. As CEO Jan Johansson notes, the machine (installed in 1952) is not being shut down as a direct result of market conditions, but rather as part of an internal process as the company is concentrating on production with the modernized PM 5 and on the new paper grade.
SCA plans to use PM 2 for some time as a test machine and then eventually wants to shut it down for good. This was scheduled to happen soon, but Johansson did not give a firm timeline.
PM 2 has a capacity of 135,000 metric tpy of newsprint and improved newsprint. PM 5, which was the focus of the upgrading work in Ortviken, now produces standard newsprint, improved newsprint, and the new mechanical uncoated paper GraphoInvent, with an annual capacity of 255,000 metric tons. The Ortviken mill has four paper machines with a combined capacity of 900,000 metric tpy of publication papers.
##SHARELINKS##
|
SCA, Stockholm, Sweden, at a capital markets day (CMD) in Stockholm this week, reported that to further strengthen profitability in its hygiene operations, measures are being taken to decrease costs and improve efficiency. The company's target for return on capital employed (ROCE) has been adjusted from 13% to 15% for tissue and for forest products from 11% to being the top quartile of the sector.
The integration of SCA's European tissue operations acquired from Georgia-Pacific is progressing in line with or better than planned, and is expected to provide EUR 125 million in annual cost synergies, with the full effect occurring after three years, the company reports.
"Our efficiency program from 2011 goes according to plan and to date we have achieved more than half of the expected annual savings of EUR 80 million. A new efficiency program has been initiated within the hygiene operations to further reduce costs and increase productivity. It will provide annual cost savings of some EUR 300 million, with full impact in 2015. About 1,500 employees are affected and costs are expected to be some EUR 100 million," Jan Johansson, president and CEO, said.
During the past year, SCA notes that it completed a number of major acquisitions and divestments that strengthened the company and focused operations on hygiene and forest products. The hygiene operations currently account for 80% of SCA's sales, with the majority in Europe, but with increasing exposure to emerging markets, both via organic growth and acquisitions. Increasing disposable income in emerging markets offers continuing favorable conditions for growth in the hygiene operations, SCA adds.
##SHARELINKS##
|
Södra's Mörrum mill in Sweden this week received the second order for a large Metso (Finland) Kappa Q analyzer unit. The delivered analyzer replaces Mörrum's retiring Metso Kappa analyzers after a long service of more than 15 years. The new analyzer includes the online kappa and brightness measurements and, as a new feature to the previous ones, online fiber and shives measurements.
During their lifecycle, the replaced analyzers at the Mörrum mill carried out some 4.5 million measurements. After well over a decade's usage of two kappa analyzers and a brightness analyzer, the mill decided to gradually replace the old analyzers with recently released Metso Kappa Q technology.
The Mörrum mill has several other Metso analyzers and sensor installations, such as alkali analyzers in the caustification plant and different versions of Cormec and Polarox inline-measurements of pulp brightness and residual chemicals.
Södra Cell Mörrum annually produces 360,000 metric tons of paper pulp, of which 87% is exported.
##SHARELINKS##
|
Containerboard/Packaging
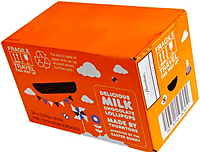 More packaging, not less packaging, could help the environment—by reducing the amount of food waste going to landfill, according to the U.K.-based Confederation of Paper Industries (CPI) Corrugated Sector. Around 7 million metric tons of edible food ends up in landfill in the U.K. each year at a staggering cost to household budgets, the economy, and the environment, CPI notes, adding that it is "pleased to confirm that the packaging industry is playing its part in reducing waste with significant investment in preventive steps such as providing easier opening solutions, clearer date labelling, and smaller pack sizes."
CPI also points to figures released by The Industry Council for Packaging and the Environment (INCPEN) on energy consumption in the food supply chain. INCPEN's research shows that primary and secondary packaging makes up just 10% of the total energy used in feeding one person for a week (Table for One, an INCPEN report on energy usage in the food supply chain), compared with 51% in the production stages and 31% for home storage and cooking.
Corrugated packaging is playing a pivotal role in supply chain sustainability by ensuring that more food reaches the consumer's table as safely and efficiently as possible. Corrugated producers have invested heavily in moving from a brown box for goods in transit to a three-in-one shelf ready packaging solution comprising product protection, an advertising platform, and merchandiser, CPI says. The advantages that corrugated is bringing to the supply chain are a result of continued investment in printing techniques, allowing greater product presentation on outer packaging, which is proving a big hit with retailers, it adds.
Packaging materials to combat food waste are also being developed, with some supermarkets trialling corrugated board that utilizes an ethylene-absorbing agent to slow down fruit and vegetable ripening to help them stay fresher for longer. CPI's Director of Packaging Andy Barnetson says that corrugated packaging's protective qualities are supporting the food industry's sustainability goals by keeping products fresher for longer, whereas reducing packaging could increase food waste. "Diverting waste from landfill sites is very important," he points out. "The corrugated industry is proud to use and promote a sustainable and renewable material, more than 80% of which is recycled, saving an area of board the size of Greater London from landfill every four months.
"Packaging helps to protect food in transit as well as preserve its freshness on arrival at the retailer," Barnetson continues. It also uses far less energy in the supply chain than the production and cooking processes. By preventing food from going off, it is saving far more in resources than those used in the packaging itself. The best environmental solution can be more packaging rather than less. To suggest that more packaging for food could be beneficial for the environment might bring howls of protest from the green lobby, but surely in a world where billions of people are at risk of hunger, saving from landfill as much of this most basic of human needs as possible, is crucial."
##SHARELINKS##
|
KapStone Paper and Packaging Corp., has ordered from PMT Italia, Italy, an upgrade of No. 3 paper machine at its North Charleston, S.C., USA, mill. The scope of the rebuild, planned for a first quarter 2014 startup, includes replacement of the existing 6.2 meter press section and extension of the first dryer section.
PMT will supply a new single ÆGO™FLX SHOE module with mated ÆGO™FLX ROLL as part of the new press configuration. The project is expected to improve the capability and efficiency of No. 3 paper machine in producing ultra high performance (UPL) lightweight linerboard grades.
PMT will also supply startup and commissioning services. This is the second shoe press project for PMT in North America.
##SHARELINKS##
|
Sonoco, Hartsville, S.C., USA, reports that its retail point-of-purchase display and packaging business won two of the top awards at the inaugural Retail Innovation Fair presented by the Wake Forest University Center for Retail Innovation. Sonoco received the Best Consumer Engagement Award and the People's Choice Award at the CVS Caremark-sponsored event, which was themed "Marketing to an Aging Population." The event showcased the latest retail marketing ideas for engaging today's senior shoppers and attracted exhibitors, sponsors, and attendees representing many of the best-known names in retail.
"There's a silver tsunami coming as the Baby Boomer population becomes seniors," said Professor Roger Beahm, executive director of the Center for Retail Innovation. "As the size of this demographic grows, so do the retail marketing opportunities."
Sonoco presented its award-winning exhibit in a "total store solution" format, integrating a mix of in-store promotional packaging and merchandising displays to highlight industry best practices for marketing to seniors. The CVS Caremark Best Consumer Engagement Award was chosen by a panel of CVS executives, while the People's Choice Award was voted on by event attendees.
"Our retail display and packaging team does an outstanding job helping our customers maximize their in-store branding and sales opportunities," said Jeff Tomaszewski, division VP and GM, Sonoco Display and Packaging. "To receive further validation for our expertise in marketing, to seniors in particular, is extremely gratifying."
##SHARELINKS##
|
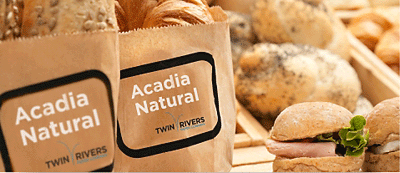 Twin Rivers Paper Co., South Portland, Maine, USA, a producer of lightweight specialty packaging, label, and publishing papers, with operations in Maine and New Brunswick, N.S., Canada, reports that it is answering the market need for more environmentally-responsible packaging by expanding its Acadia® Natural portfolio to include basis weight offerings as low as 18 lb and up to 50 lb. Acadia Natural, a fully recyclable and compostable packaging paper, is made from unbleached pulp and offers an environmentally-friendly alternative for packaging applications such as bread bags, carry-out bags, fast-food sandwich wraps, french fry bags, and basket liners.
"The demand for sustainable packaging is growing and Twin Rivers is well-positioned to meet this demand with both our portfolio and our ability to co-develop products tailored to the unique needs of the packaging market. By broadening our product offering, we are able to support lightweight initiatives as well as serve a broader set of end-use applications," says Dave Deger, director of Business Development and Marketing.
Twin Rives points out that "Acadia Natural is an ideal solution for food service, retail-food applications, and quick serve restaurants. It offers excellent runnability, printability, sustainability, and FDA-compliance, while available in both a standard and an oil and grease-resistant option up to kit 7."
##SHARELINKS##
|
New Products
Garlock Rubber Technologies (GRT), Paragould, Ark., USA, reports that it has nearly doubled the weight of individual, bulk-haulage conveyor belts it can produce. The company manufactures these conveyor belts for a wide range of industries, including pulp and paper.
"With the recent acquisition of a larger crane, we now have the capability to produce belts weighing up to 25 tons," said Jeff Phillips, GRT sales manager. "That means we can run longer segments—72 in. wide and, depending on construction, up to 1,500 ft in length. Previously, our lifting capacity was limited to 15 tons, which for longer belts required splicing, a difficult and not particularly desirable process. By keeping our 15-ton crane in place, we have also been able to reduce set up and loading times in our finishing and shipping areas."
Manufactured by R & M Material Handling Inc., the new crane was installed in early October. It features wireless radio controls, integrated load cell readout, and standard safety features required by OSHA.
##SHARELINKS##
|
Published Pricing
Ashland Water Technologies, Schaffhausen, Switzerland, a commercial unit of Ashland Inc., reports that it will increase prices for its portfolio of polyacrylamide and polyacrylate chemistries sold in Europe by a minimum of 5% to 10%, or as contracts allow. The price increases become effective immediately.
"Steep cost escalation for critical raw materials, energy, and transportation make these increases necessary. We will continue to work in partnership with our customers to help mitigate these increases," said Charles Robinson, VP, StreamLink Specialty Chemicals, Ashland Water Technologies. "Responding to changing market conditions enables us to continue our industry-leading product support and deliver value to our customers."
Ashland Water Technologies is a global producer of polyacrylamide polymers, technical superabsorbents, and polyacrylate specialties used in papermaking, municipal water treatment, mining, oilfield applications, and various industrial market segments. Its process, utility, and functional chemistries are used to improve operational efficiencies, enhance product quality, protect plant assets, and help ensure environmental compliance.
##SHARELINKS##
|
People
FutureMark Paper Group, Westport, Conn., USA, has named paper industry veteran Paul E. Bradshaw VP of sales and marketing for the group's uncoated paper products. FutureMark's 100% recycled uncoated printing and packaging papers, made at the group's plant in Manistique, Mich., are used by "sustainability-minded companies" such as Houghton Mifflin Harcourt, JPMorgan Chase, L.L. Bean, and McDonald's, the company notes.
Bradshaw will direct all aspects of sales and marketing for FutureMark uncoated products, which include printing and writing grades such as Future Book™ UC, Future Mystique™, and Future Office™, and packaging papers such as Future Bag™, and Future Pack™. Bradshaw will also spearhead FutureMark's continued expansion into high-end publication paper markets, including book and digital papers.
"Having Paul join the FutureMark team is a boon for our business," said FutureMark Paper Group President and CEO Steve Silver. "Paul has proven experience building market-leading positions in high-end publication and digital papers. His deep expertise and relationships in our customer markets will generate many new opportunities for FutureMark with companies that value the environmental benefits of our 100% recycled uncoated papers."
Bradshaw previously served as the SVP for publishing papers at Appleton Coated LLC, overseeing relationships with major publishing customers and leading the company's entry into coated inkjet papers. He had held various sales and management positions at Appleton Coated and its predecessor companies since 1988.
##SHARELINKS##
|
Andrea K. Tarbox, CFO of KapStone Paper and Packaging Corp., Northbrook, Ill., USA, has been awarded 2012 Chicago CFO of the year by the Financial Executives International (FEI) Chicago Chapter. Chicago CFO of the Year Awards are presented to senior financial leaders and recognize exceptional performance of financial professionals in their roles as corporate stewards in five categories—large public company, mid-size public company, large private company, mid-size private company, and not-for-profit organizations.
Tarbox, winner in the mid-size public company category, said that "I consider this a KapStone win. I am fortunate to have an extraordinary team that was adventurous enough to join the fledgling company and then to execute brilliantly in its areas of expertise."
Roger Stone, KapStone's chairman and CEO, noted that "in many ways, Andrea is in a class all by herself. She joined KapStone when it was in formation and she was our only financial employee. She quickly recruited and built a talented and effective organization. As the company grew, she integrated our acquisitions and created a cohesive, committed, and motivated group."
Tarbox joined the company in 2006. KapStone has since grown from $0 in revenue to its current annual run-rate of well over $1 billion. Tarbox's previous career includes financial positions of increasing responsibility in several global companies including Gartner, British Petroleum, and Fortune Brands. Her career began with Ernst & Young. Andrea earned a B.A. in psychology from Connecticut College and an MBA from the University of Rhode Island.
##SHARELINKS##
|
TAPPI News
One of TAPPI's highest rated and best-attended courses, the Kraft Recovery Course, is scheduled for January 7-10, 2013 in St. Petersburg, Florida, USA. The intermediate-level course covers every phase of the complex kraft pulp mill recovery process and is designed for those new to the recovery area and the industry, as well as technical staff looking to better understand the process in order to take back new ideas to improve mill operations.
"The kraft recovery process is a fundamental reason that kraft pulping is the most widely used chemical pulping processes in the world and used to produce a large number of bleached and unbleached products," notes Course Chairman Honghi Tran, "The recovery process is highly complex and composed of many different unit operations and technologies. This course, taught by world-renowned experts in their field, provides attendees an excellent review of each part of the process, as well as the opportunity to interact with experts in each area to have their specific questions addressed."
The Kraft Recovery Course is taught by an internationally recognized faculty composed of 15 experts who delve into each key area. Course Chairman Honghi Tran is Professor, the Frank Dottori Chair in Pulp and Paper Engineering, and the Director of the Pulp & Paper Centre, University of Toronto. Honghi was named a TAPPI Fellow in 2000.
The TAPPI Kraft Recovery Course provides practical day-to-day information in both traditional workshops and in team-based training sessions that will provide attendees with information on how to improve production efficiency, minimize operating costs and reduce environmental impact. Among the many topics covered are recausticizing, lime kiln operations, black liquor evaporation, recovery boiler operations, corrosion, energy optimization and energy and cost reduction. The course is one of TAPPI's most popular and highly rated technical courses.
The TAPPI Introduction to Pulp and Paper Technology Course is co-located with the Kraft Recovery Course. This introductory course is designed for anyone new to the industry or those needing a better understanding of mill-wide operations. The course covers the entire papermaking process from raw materials and the wood yard through pulping, papermaking and finishing operations. Attendees will learn about the pulp and paper industry's products from industry experts, and will gain knowledge that will help them increase their contribution to improving mill operations.
Register before December 6th and you can save more than $900!
##SHARELINKS##
|

The premier issue of NANO360, the only newsletter dedicated to global developments in nanotechnology from renewable and sustainable materials, has been launched by TAPPI. NANO360, the official newsletter of TAPPI's International Nanotechnology Division, will cover news, resources, research, and technology of nanocellulose and other renewable materials.
"The global market for products using nanotechnology could reach an estimated $1 trillion by 2015 with wood products potentially accounting for 20%," notes TAPPI President & CEO Larry N. Montague. "TAPPI's Nanotechnology Division serves as a platform for helping this growing industry respond to the rapidly changing field of nanotechnology, especially as commercialization develops. NANO360 will be a key resource for professionals interested in all aspects of this fast-paced field."
"NANO360 will keep you up to speed on all that is going on in this dynamic industry by highlighting new research, publications, reports, and events going on around the world in sustainable nanotechnology," comments Division Chair Sean Ireland, Verso Paper Corp. "Our focus will be on nanocellulose, but not exclusively, and we welcome and encourage contributions from others working with renewable materials."
A range of topics and types of information will be covered including: nanocellulose and other nanomaterial research, newly published reports, new peer-reviewed publications, resources such as peer-approved databases, Nanotechnology Division activities, websites, and other tools and global nanocellulose news.
The mission of TAPPI's International Nanotechnology Division is to serve as the leading global forum for the community of individuals, organizations, and institutions seeking to collectively advance the responsible and sustainable production and use of renewable nanomaterials.
Contact: Nano360@tappi.org
##SHARELINKS##
|

If you're planning a career in the pulp and paper (or packaging) industry, this event will put you on the cutting-edge of some groundbreaking technology.
Make plans now to attend the 2013 TAPPI-PIMA Student Summit, January 19-31, 2013, in Raleigh, N.C., USA.
This is a rare opportunity for advanced undergraduate and graduate students to meet face-to-face with industry leaders and gain valuable information on what forces are shaping the industry today - plus the added bonus of the inside track on employment and career development.
Program Session Topics:
- Mock Interview Session/Resume Critique
- Myth vs. Fact of the Industry
- Voith Fabrics Presentation
- Printed Electronics
- Future of Carbohydrates
- Career Path Panel: Grad School vs. Job
- BioEnergy
- Project Management.
The 2013 TAPPI-PIMA Student Summit includes:
- An Engineering Competition
- Networking and a Career Fair
- Scavenger Hunt
- Multiple Tours of Industry Facilities
- Interviews with Hiring Companies.
Sponsorships are available. For more information, contact David Bell.
##SHARELINKS##
|
More than 60 entries were received for the CorrPak Competition held recently at TAPPI/AICC SuperCorrExpo, Atlanta, Ga., USA, October 1-4. Open to all corrugated manufacturers worldwide, the competition is held on even years and features entries in two main categories: Structure and Printing. The CorrPak Competition is open to all corrugated manufacturers worldwide. TAPPI's Corrugated Packaging Division sponsors this distinguished event to select and recognize the finest commercially produced corrugated package products manufactured between Aug. 1, 2010, and Aug. 1, 2012.
Beginning this year, and continuing for the next decade, the coveted Attendees Favorite Award will be presented in honor of George G. Maltenfort. Dr. Maltenfort was a highly respected, long-time member of TAPPI who made innumerable contributions to the industry. He distinguished himself in advancing pulp, paper, and converting technologies particularly in the corrugated shipping containers arena. Dr Maltenfort published 50-plus works for TAPPI and served on numerous TAPPI boards and committees relating to corrugated containers and served with other international organizations as well.
The "Corrbie" is awarded for Best in Show. This year the Corrbie for Structure was awarded to Ardent Displays & Packaging for its Martha Stewart Home Office Standee entry. The Corrbie in Printing was presented to RockTenn Fresno for their Lemon Bin Sleeve entry. Arvco Container Corp. won the Attendees Favorite in Structure for its Rear Window Suspension Pack. RockTenn MD Adams won the Attendees Favorite in Printing for its Point Special packaging.
The complete list of winners can be found on the TAPPI Corrugated Division website.
##SHARELINKS##
|
Towel and Tissue Papermaking is the last of the 15 CD-ROMs in the Making Pulp and Making Paper CD-ROM Series. Through this highly interactive, self-paced CD-ROM, participants learn towel and tissue papermaking terms, concepts, and processes.
Learning outcomes
After completing the Towel and Tissue Papermaking CD-ROM, participants should be able to:
- Explain how the manufacturing of towel and tissue grades is different from other grades of paper
- Describe the different types of tissue formers
- Explain the TAD process and its advantages and disadvantages.
Benefits for Everyone
The series is designed for anyone who would benefit from a working knowledge of the pulping and papermaking process, including:
- Paper machine operators
- Process and product engineers
- Sales and technical support staff
- New employees
- Students.
It will also be beneficial to experienced production or technical employees who need a more thorough understanding of a specific area of the operation, especially for cross-training purposes. New employees of chemical and equipment suppliers and paper industry consultants will also benefit from this series.
The complete set of 15 Making Pulp and Paper CD-ROMs
is also available.
Product code: MPP-15
Member Price: $78.00
Non-member Price: $119.00
##SHARELINKS##
|
TAPPI's 2012 Nominating Committee presents a slate of candidates for two officer and three director positions on the TAPPI Board. The candidates are: chair, Thomas J. Garland; vice chair, Chris Luettgen, Kimberly-Clark; and directors, Daniel D. Cappell (AstenJohnson), Kirt J. Cuevas (International Paper), and Robert A. Feeser (MeadWestvaco Corp.).
Voting begins December 1.
Per the TAPPI Bylaws, members of the organization have until November 1 to review the slate.
More information about the slate and election process is available online.
##SHARELINKS##
|
TAPPI's Corrugated Packaging Division members have elected three individuals to serve on the Division's Corrugated Packaging Council, the governing body for the Division. The Corrugated Packaging Council gives TAPPI suggested direction on strategic development and planning for projects and products for the corrugated division. It is made up of eight appointed members from the major integrated companies and independents, the chair of the two TAPPI technical committees, and four elected positions that each serve a three-year term. The balance of the council includes the division chair, vice chair, and past chair.
Newly elected members include: Paul Hrubesky, Fosber America; John Kohl, Harper/Love Adhesives; and Steve Woodard, ARC International. Their term will run through the corrugated packaging division conference in 2015.
##SHARELINKS##
|

Registration is now open for the TAPPI Introduction to Pulp and Paper Technology Course scheduled for January 7-10, 2013 in St.Petersburg, Fla., USA.
This is one of TAPPI's longest running courses. Why is this course one of our most popular?
Intro to Pulp and Paper Technology is unique in that it provides information on how each individual part of a paper mill influences another. This course allows you to understand how materials, pulping, and paper-making processes affect paper and board properties. You will also be delivered a broad overview of pulping and paper-making technology, including the entire pulping and paper-making process from raw materials and wood prep. to pulping and mill operations.
Four Reasons to attend Intro to Pulp and Paper Technology:
- Course pre-surveys will ensure this course meets attendees individual needs
- You will have networking opportunities during hourly breaks
- This course measures up the MOST training content in the SHORTEST amount of time
- You get the instruction of Dr. Michael Kocurek and can learn from his 45 years of experience on this topic.
Who benefits?
- Pulp and paper company employees - new technical/operating staff, operators, non-technical personnel, chemical and direct equipment suppliers, technical service professionals, and sales people.
This course is taught by Dr. Michael J. Kocurek, Professor Emeritus, Paper Science & Engineering at North Carolina State University. Dr. Kocurek is one of the world's most recognized educators in the field of pulp and paper industry science.
##SHARELINKS##
|
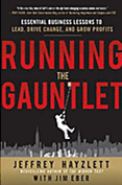
By: Jeffrey Hayzlett
Running The Gauntlet is a rough-and-tumble guide for running and driving change through the business gauntlet. The book divides into three parts that parallel the three parts of change that every business leader must face: Getting Ready, Getting Going, and Creating and Sustaining Momentum.
In each section, Hayzlett shows business leaders and owners how to develop the necessary mental, emotional, and (yes) physical toughness they must have for smart, strategic, and lasting change. Through this book, Hayzlett will force leaders to really get up in their own businesses – to take them over from the inside and drive change – gaining customers and profits in the process.
Readers will be able to efficiently assess what kind of change their business needs and then summon the vision, courage, and passion to enact it.
View the Table of Contents and Preview.
Hard cover. 256 pages.
Member Price: $26.00
Item #: 11RUNN
##SHARELINKS##
|
The Tissue360 Forum, organized by TAPPI tissue experts in conjunction with Tissue360 magazine, will be held April 29 - May 1, 2013 at PaperCon 2013 in Atlanta, Ga., USA. The forum will cover a wide range of tissue manufacturing and converting technologies and market trends. PaperCon 2013 will be the pulp and paper industry's largest technical conference and trade show.
"The inclusion of the Tissue360 Forum at PaperCon 2013 will add comprehensive coverage of this dynamic segment to the industry's best technical program," notes TAPPI President and CEO Larry Montague. "The forum will provide business insights and peer-reviewed technical papers covering developments in one of the industry's most rapidly growing and technically innovative grade sectors."
Tissue360 Forum topics will include an overview of hygienic product market drivers, raw material usage and supply, wet and dry end additives, latest hybrid tissue making technology and runnability/operational tips. All material will be selected and peer reviewed by TAPPI members with tissue expertise. The program is open to all full PaperCon registrants. An invitation to Present at the Tissue360 Forum has been issued. Industry professionals interested in presenting a paper, panel, roundtable, or poster on any of these topics should submit an abstract no later than November 20, 2012.
PaperCon brings together CEOs, mill managers, superintendents, scientists, process engineers, and suppliers for the largest pulp and paper technical program in the world. No other event provides such a comprehensive program, networking opportunities and trade fair among such a distinguished group of industry leaders.
##SHARELINKS##
|
Why Whitewater Filtration Systems Fail
Time: 12:00 p.m. to 1:00 p.m. EST
Wednesday, November 14, 2012
This free webinar from TAPPI addresses why whitewater filtration systems are often problematic and in some instances fail completely. The presentation will explain why filtration systems fail under certain conditions and offers the best solutions to improve the overall reliability of the process.
Attendees will learn:
- Significance of process variation on equipment performance
- The negative cost impact associated with poor system performance
- New sensor technology that is making the system "visible"
- Cutting-edge strategies to manage the process variation
- How to develop a "roadmap' for system optimization.
Learn more and register
##SHARELINKS##
|
This November, if you want to learn how to improve mill efficiency, effectiveness, and reduce overall maintenance costs over time, these two courses are for you!
Attendees will learn:
- How to improve reliability and maintenance practices at your mill
- Implementation of the best practices for successful scheduling and process planning
- How to tie cause and effect together and apply logical thought processes to arrive at the core of your problem
- How to bring root cause analysis into your day-to-day reliability management process.
Maintenance Planning, Scheduling, and Reliability Training
Date: November 12-14
Covers:
- Results-oriented reliability and maintenance
- Successful planning and scheduling
- Best-practice business process
- Work identification/request initiation
- Setting work priorities, handling backlog
- Planning: What and How
- Scheduling: Who and When
- Work execution and improvement
- The impact of maintenance inventory management on performance
- Organizing for efficient management
- Aligning objectives for purchasing, storeroom, and maintenance managers
- Record materials data
- Integration of materials management with plant reliability
- Inventory management basics
- Determining what to stock
- Managing obsolete stock
- Knowing what parts should be inventoried.
Root Cause Problem Elimination Training
Date: November 15-16
Covers:
- RCPE in an industrial setting
- Well-known root cause investigations
- RCPE examples for IDCON's experience
- Basic beliefs for RCPE
- Drawing the "How-Can Diagram"
- Hands-on experience
- Finding and prioritizing problems
- Creative and critical thinking
- Root cause and logical thinking
- The RCPE process
- Triggers to perform RCPE
- Problem definition
- Possible causes
- Selecting most likely cause
- Verifying selected cause
- Identifying solutions
- Final exercises.
With your registration, you also get:
- IDCON's 215-page Practical Maintenance Planning and Scheduling Manual ($145 value)
- IDCON's Reliability Based Spare Parts and Materials Management Book ($49 value)
- Class notes and exercises
- Full examples on USB stick.
Begin solving problems at your facility by participating in one or both of these important, time and money-saving courses.
One flight takes you to both training sessions in beautiful Raleigh, N.C., USA.
##SHARELINKS##
|
The 360° Leader by Dr. John C. Maxwell
People who desire to lead from the middle of organizations face unique challenges. They are often held back by myths that prevent them from developing their influence. Dr. Maxwell, one of the globe's most trusted leadership mentors, debunks the myths, shows you how to overcome the challenges, and teaches you the skills you need to become a "360° leader."
If you have found yourself trying to lead from the middle of the organization, as the vast majority of professionals do, then you need Maxwell's insights. You have a unique opportunity to exercise influence in all directions-up (to the boss), across (among your peers), and down (to those you lead).
The good news is that your influence is greater than you know. Practice the disciplines of 360° leadership and the opportunities will be endless... for your organization, for your career, and for your life.
View the Table of Contents and Preview.
Member Price: $25.00
Press Item #: 12LEAD
##SHARELINKS##
|
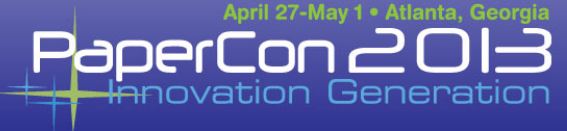

Joel Weldon, one of the most sought after corporate speakers in North America, will provide the keynote address on Monday, April 29 at PaperCon 2013. Weldon is an award winning speaker renowned for his well-researched, informative, and engaging presentations. At PaperCon, Weldon will be addressing "Innovation Generation," how industries like paper can adapt to changing consumer habits and cost containment pressures.
Weldon has been an idea consultant, sales trainer, and executive speech coach for many of the world's leading organizations and businesses for well over three decades. He's widely known as one of North America's most highly respected and sought-after corporate speakers. His presentations are known for effectively and specifically addressing each audience and their unique business and industry challenges, fears, risks, and opportunities.
Weldon is one of an elite group of speakers to have earned all four of the highest honors in the speaking profession. They include induction into the Speakers Hall of Fame, the coveted Communication & Leadership Award, The Golden Gavel, "for his profound impact on corporate America," and in 2006 being named "Legend of the Speaking Profession." He turned down a four-year college scholarship because he thought he wasn't "smart enough" to go to college. A former construction worker, he's living proof that human potential can be tapped, and your entire life transformed, when even one good idea is presented, accepted and acted upon.
PaperCon 2013 will feature the world's largest paper industry technical program. It has been expanded to include both tissue and nonwovens programs in 2013. PaperCon takes place April 27 through May 1, 2013, in Atlanta, Ga., USA.
Learn more about PaperCon.
##SHARELINKS##
|
Papers are still being accepted for the Appita 2013 Technical and Industry Innovations programs. This year, as an added bonus, a special speakers rate will apply. Papers can be on any subject of relevance to forestry, pulp, paper, print, or packaging.
The Call for Papers deadline is November 9.
You are invited to submit an extended abstract on topics relevant to the industry, including but not limited to:
- Forestry and wood products
- Sustainability
- Bioresources, bioenergy, and cogeneration
- Resource assessment and management
- Paper and board manufacturing
- Efficiency and process improvement
- Safety
- Lean manufacturing
- Pulping and bleaching.
For additional details and registration information contact Appita 2013 Conference organizers.
##SHARELINKS##
|
This text, edited by Carlton W. Dence and Douglas W. Reeve, covers fundamentals and processes from the chemical composition of pulp to the technology, production, and the environmental impact of bleaching. Designed as both a textbook and a reference book, Pulp Bleaching: Principles and Practice explains what bleaching is, why pulp is bleached, and how bleaching is done.
The book also features discussions on several "hot topics" in pulp bleaching, including elemental chlorine free bleaching, totally chlorine free bleaching, enzyme assisted bleaching, and bleaching of recycled fiber. In addition, the book is key-word indexed and each chapter contains extensive references.
Pulp Bleaching: Principles and Practice
Product code: 0102B061
Member Price: $124.00
Non-Member Price: $186.00
##SHARELINKS##
|
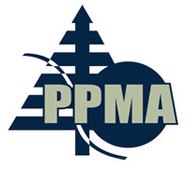
The Pulp and Paper Manufacturers Association's (PPMA) new website (ppmausa.com) offers access to labor contracts, salary data, surveys, and other human resource related material.
"The look and feel of the PPMA website has remained unchanged for several years," said Dick Kendall, executive director for PPMA. "We have now revamped the site to be more user-friendly and to provide industry information to our members."
PPMA members have access to a treasure trove of valuable information such as a labor database of information regarding union contracts, a 'library' of current labor agreements (union contracts), and custom survey results on a variety of topics tabulated by PPMA at the request of members.
PPMA supplies human resource services to the pulp, paper, converting, and allied industries. Its membership includes union and non-union facilities involved in producing and converting products allied with the paper industry.
Media Contact: Dick Kendall, executive director, dkendall@ppmausa.com, 920-731-4994.
##SHARELINKS##
|
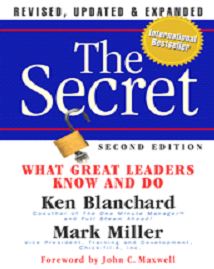
The Secret, Second Edition
What Great Leaders Know and Do
By: Ken Blanchard & Mark Miller
- Uses the popular "business fable" format that Ken pioneered
- Explains the five essential practices exhibited by the best leaders and provides practical ideas on how to make these a reality in your life.
At one time or another, everyone in a position of authority-whether in a multinational corporation or a local volunteer group-wonders what the key to great leadership is. And who better to answer that question than the team of Ken Blanchard, whose books on leadership have sold over 20 million copies, and Mark Miller, who worked his way up from line worker to vice president of one of the largest fast-food chains in the country. In The Secret, Blanchard and Miller use the uniquely accessible "business fable" format that Blanchard pioneered to get at the heart of what makes a leader truly able to inspire and motivate people. Debbie Brewster, recently promoted and struggling, finds herself about to lose her job due to poor performance. In an attempt to save her career, she enrolls in a new mentoring program offered by her company. Much to her surprise, Debbie finds her mentor is none other than Jeff Brown, the president of the company. Debbie decides that she is going to ask her new mentor the one question she feels she desperately needs answered: "What is the secret of great leaders?" Jeff's immediate answer-that great leaders serve their followers-completely flummoxes Debbie. Over the next 18 months, Jeff helps Debbie discover and explore five fundamental ways that leaders lead through service.
The Secret puts what Blanchard and Miller have learned about leadership in a form that anyone can easily understand, embrace, and pursue. It is a book that will benefit not only those who read it, but also the organizations they work in an the people who look to them for guidance.
The second edition includes revised and updated content including:
- A new foreword by John Maxwell
- A new resource section in the back matter summarizing key learning points
- A greater focus on the book's primary focus: servant leadership
- A more humanized protagonist
- Numerous other minor renovations throughout.
Ken Blanchard, coauthor of The One Minute Manager, the bestselling business book of all time!
Item #: 12SECRET
View the Table of Contents and Preview.
Member Price: $23.00
##SHARELINKS##
|
The 20 volumes of Papermaking Science and Technology bookseries cover the entire paper manufacturing process from wood raw material to end product, providing a basis for university-level education, for updating training courses, and as handbooks for the industry. The bookseries has been updated and second editions are now available. TAPPI members can place an order by contacting The Finnish Paper Engineers' Association. Please contact Mary Anne Cauthen, Member Group Coordinator, at +1.770.209.7352 or by e-mail at MCauthen@TAPPI.org
These books can be purchased individually or as a set.
This 20 volume set includes:
- Volume 1 - Economics of the Pulp and Paper Industry
- Volume 2 - Forest Resources and Sustainable Management
- Volume 3 - Forest Products Chemistry
- Volume 4 - Papermaking Chemistry
- Volume 5 - Mechanical Pulping
- Volume 6, part 1 - Chemical Pulping Part 1, Fiber Chemistry and Technology
- Volume 6, part 2 - Chemical Pulping Part 2, Recovery of Chemicals and Energy
- Volume 7 - Recycled Fiber and Deinking
- Volume 8 - Papermaking Part 1, Stock Preparation and Wet End
- Volume 9 - Papermaking Part 2, Drying
- Volume 10 - Papermaking Part 3, Finishing
- Volume 11 - Pigment Coating and Surface Sizing of Paper
- Volume 12 - Paper and Paperboard Converting
- Volume 13 - Print Media - Principles, Processes, and Quality
- Volume 14 - Process and Maintenance Management
- Volume 15 - Materials, Corrosion Prevention and Maintenance
- Volume 16 - Paper Physics
- Volume 17 - Pulp and Paper Testing
- Volume 18 - Paper and Board Grades
- Volume 19 - Environmental Management and Control
- Volume 20 - Biorefining of Forest Resources
##SHARELINKS##
|
The International Mechanical Pulping Conference, sponsored by PI, TAPPI, PAPTAC, SPCI and PTF, will be held on June 3-5, 2014, in Helsinki, Finland. IMPC 2014 is a major part of PulPaper, one of the world's most premier pulp and paper exhibitions, coinciding with the 100th anniversary of PI, the Paper Engineers' Association.
The Conference Program Committee invites you to submit papers on the following topics:
- Energy saving in Mechanical Pulping process
- New applications and innovations
- Raw materials in Mechanical Pulping
- Advanced Mechanical Pulping technologies e.g.
- Process control and simulation
- Bleaching
- Water management and effluent treatment
5. Mill operations update e.g.
- Production cost saving technologies (energy and chemicals)
- Improving mechanical pulping business potential
6. Mechanical pulps in paper and board.
Authors interested in presenting a paper or a poster on these topics should submit an extended abstract (˜500 words) to impc2014@vtt.fi. Abstracts are due by February 28, 2013. Authors will be notified of acceptance by May 31, 2013 and final manuscripts are due March 31, 2014.
If you have any questions, please contact Sari Liukkonen, Chair of the Program Committee at +358 40 586 0384, or by e-mail at impc2014@vtt.fi.
##SHARELINKS##
|
Make your plans now to join a host of professionals from industry, universities and research institutes at the 14th TAPPI European PLACE Conference, which will be held May 6-8, 2013, at the Swissotel in Dresden, Germany.
The Call for Papers is now officially open. Submit your abstract and take an active role in this not-to-miss event!
##SHARELINKS##
|
|
|