Over the Wire
TAPPI
Weekly Spotlight
Wausau Paper, Mosinee, Wis., USA, reports that it has signed a non-binding Letter of Intent to sell its specialty paper business to a new company (NewCo) to be formed and controlled by investment funds sponsored by KPS Capital Partners L.P., New York, N.Y., USA. KPS is a private equity firm with significant experience in the paper industry and in completion of complex corporate carve-outs.
The specialty business, Wausau's biggest source of revenue in 2011, makes paper and paperboard for food packaging, labels, and writing papers. Selling the specialty paper business will allow the company to focus resources on its tissue business. Last month, Wausau announced that it would shut down its specialty paper mill in Brainerd, Minn., in the second quarter of this year. The company sold its print and color paper brands last year.
KPS also has signed a non-binding Letter of Intent to acquire another company and combine it with the specialty paper business within NewCo. Wausau has the option to have an initial ownership position in NewCo of up to 25%, with the opportunity to earn up to an additional 5% interest upon NewCo reaching certain performance thresholds.
Key highlights of the transaction are as follows:
- NewCo will acquire the assets of Wausau's Rhinelander and Mosinee (see photo above) mills in Wisconsin; the assets of Wausau's Brainerd mill are not included in the transaction
- The transaction requires that the United Steelworkers ratify new collective bargaining agreements with NewCo (see article below)
- Wausau will retain legacy defined benefit pension and post-retirement liabilities related to the businesses being sold to NewCo
- The initial cash purchase price will be approximately $130 million, subject to KPS' confirmatory due diligence and adjustments for the ultimate treatment of certain transaction related liabilities and customary post closing adjustments.
Hank Newell, president and CEO of Wausau Paper said that "we are pleased to have signed this letter of intent with KPS, which will provide proven operations and management leadership for the paper business along with new opportunities to expand its product offerings and market reach. This announcement represents an important step in the strategic repositioning of Wausau Paper, narrowing our focus on our Tissue business and creating additional value for shareholders."
The ultimate transaction is subject to acceptable confirmatory due diligence, ratification of new collective bargaining agreements and satisfactory completion of effects bargaining, required regulatory clearances, final negotiation, and board approval of the definitive agreements and certain other customary contingencies to closing, including third party financing.
Wausau expects to finalize the transaction in the second quarter of this year.
##SHARELINKS##
|
The United Steelworkers Union (USW), Pittsburgh, Pa., USA, said that it views "with interest and cautious optimism" the announcement earlier this week that Wausau Paper will potentially sell its Mosinee and Rhinelander mills and other non-disclosed assets to KPS Capital Partners (see article above). USW Locals 01778 and 2-15 represent workers at the Rhinelander mill. USW Locals 2-221 and 2-316 represent workers at the Mosinee mill.
The transaction requires that the USW ratify new collective bargaining agreements with the new company.
Wausau signed a non-binding Letter of Intent to sell its specialty paper business to a new company that will be formed and controlled by investment funds sponsored by KPS Capital Partners L.P. KPS also signed a non-binding Letter of Intent to acquire a second company to establish a new specialty paper business. This new company will acquire the assets of Wausau's Rhinelander and Mosinee mills provided it acquires the second company.
"The specialty sector of the paper industry has lagged other sectors in terms of strategic consolidation, and deserves a renewed focus," said USW International VP Jon Geenen, who oversees the USW's paper sector. "The sector produces paper for many stable markets today, and given the right attention is poised to capture even more opportunity in advanced and evolving technical markets."
Geenen added that "we are anxious to engage in a discussion that will position the new company and its employees for long-term success and operational viability. We have had a long-term relationship with KPS, and have successfully worked with the company on numerous acquisitions that have resulted in the creation of thriving businesses. We appreciate KPS's constructive approach to doing business."
USW District 2 Director Michael Bolton said that "Wisconsin's paper industry and its skilled workers have been the centerpiece of Wisconsin's economy. It is encouraging to see renewed interest and investment in the kind of advanced manufacturing facilities that the Rhinelander and Mosinee mills represent."
Local 2-15 President Dennis Meyer noted that "our members are committed to the ongoing success of these plants. In many cases we are third and fourth generation paper workers. We know the potential of these plants and look forward to showing that to KPS."
The USW has 850,000 members in the U.S., Canada, and the Caribbean. It represents workers employed in paper, metals, rubber, chemicals, oil refining, atomic energy, and the service sector.
##SHARELINKS##
|
Domtar Corp., Montreal, Que., Canada, one of the largest producers and distributors of paper in North America, has agreed to acquire Xerox's paper and print media products business in the U.S. and Canada.
"The Xerox brand is well regarded in the paper markets it serves," said John D. Williams, Domtar's president and CEO. "This deal brings together Xerox's branded papers with Domtar's already comprehensive paper offering and will allow us to better serve our customers."
While Xerox does not manufacture paper, the company has long distributed through its brand name a broad range of coated and uncoated papers and specialty print media including business forms as well as carbonless and wide-format paper. This business will now become part of Domtar's pulp and paper segment, and Domtar will market and distribute Xerox-branded paper and print media.
"As Xerox broadens its business to focus more on services and innovative document technology, we saw an opportunity for our paper business clients to be better served by a leader in the industry," said Frank Edmonds, SVP, Xerox Global Paper and Supplies Distribution Group. "It's an across-the-board win. Xerox benefits through a trademark licensing agreement with Domtar; Domtar adds a well-regarded brand to its portfolio; and our respective clients get a simplified, 'one-stop' experience through Domtar's extensive offerings and distribution network."
Xerox will continue to manufacture, sell, and support its broad range of consumables, such as toner and ink, and Xerox Replacement Cartridges. The transaction is expected to close in the second quarter of this year, subject to customary closing conditions.
##SHARELINKS##
|
Tembec Inc., Montreal, Que., Canada, this week announced that it will sell its NBSK (northern bleached softwood kraft) pulp mill and related assets and liabilities in Skookumchuck, B.C., Canada, to Paper Excellence Canada Holdings Corp. for $89 million, which includes working capital. Closing of the transaction is expected to occur in the second calendar quarter of this year.
"This transaction supports the continuing transformation of the company and the reshaping of its business portfolio," said Tembec President and CEO James Lopez.
Tembec acquired the Skookumchuck pulp mill in 1999 as part of the acquisition of Crestbrook Forest Industries Ltd. The mill, where 290 employees currently work, started up in 1968. Its pulp is shipped to North American and Asian customers, primarily for tissue applications.
Tembec is a producer of forest products—lumber, pulp, paper, and specialty cellulose—with principal operations in Canada and France. It has some 3,700 employees and annual sales of approximately $2 billion.
##SHARELINKS##
|
TAPPI's newest publication, Tissue360° magazine, and TAPPI tissue experts have organized a comprehensive technical forum for PaperCon 2013 in Atlanta, Ga., USA, April 28 – May 1. Covering all aspects of tissue making, the Tissue Forum includes eight information- and data-packed sessions beginning Monday afternoon and continuing through Wednesday morning of PaperCon. The program is open to all full PaperCon registrants.
The Forum's eight sessions focus on tissue and hygiene product market trends and developments, the latest chemical, fiber, water, energy, control, and converting technologies, and explore new and emerging production technologies, with a special full-session look at yankee dryer issues and concerns. All material presented at Tissue Forum has been carefully selected and reviewed by TAPPI members with extensive tissue expertise, and most of the presentations include a written paper.
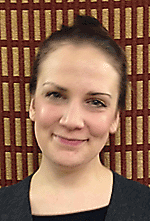 In Session T1 beginning after lunch on Monday, Esko Uutela of RISI (photo on right) presents a data-rich analysis of the global tissue business in North America. Complementing Uutela's presentation, Lindsay Gervais of Poyry International (photo on left) examines the fiber side of the tissue industry with a detailed report on cost, quality, and sustainability issues in the global tissue arena. Session T2 on Monday afternoon covers "Chemistry Solutions for Tissue Making" with a paper by Yuping Luo of Kemira Chemicals that examines the newest generation of wet strength resins for towel grades, and a close-up look at approaches to evaluating and enhancing softness by Timothy Patterson of Ashland Water technologies.
Session T3 on Tuesday morning examines "Fiber Usage and Supply for Tissue" from four different fiber type perspectives. Fernando Pescatori Silva of Eldorado Brasil updates attendees on eucalyptus fibers. Xuejun Zou of FPInnovations provides a current overview of softwood kraft pulps for tissue making, and Medwick Byrd of North Carolina State University looks at nonwood raw materials as a possible fiber source for tissue and specialty products. The recycled fiber sourcing side is covered by Dave Anderson of SCA. Leading up to lunch, Session T4 explores "Water and Energy Strategies for Tissue," with presentations by Thomas Jenn of Kimberly-Clark on conducting tissue machine audits to reduce fiber losses and improve pulp yield, maximizing post pressure roll solids with advanced press fabric structures by Roger Banks of AstenJohnson, and engineering effective void volume in tissue production by Glen Harvey of Xerium Technologies.
Session T5 begins Tuesday afternoon with a focus on Premium Tissue Manufacturing Technologies. Dennis Jewitt of Metso Paper discusses advanced technologies for structured tissue products, Roberto Zane of Voith Paper explores premium tissue technologies that are enhancing the conventional tissue world, and tissue consultant Ed Graf reports on "air dried tissue" (ADT), an alternative to TAD and similar technologies. Session T6, completing Tuesday afternoon, provides a special review and analysis of the latest tissue control techniques. Doeung Choi of Ashland Water Technologies examines the use of process simulation in structured tissue and towel making, John Feola of Cristini North America presents a roundup of the latest process control tools to boost tissue machine performance, and Richard Falcoff of Alicona Corp. looks at 3D optical micro-measurement technology to quantify surface roughness with ISO traceable Sa values.
Wrapping up the Forum on Wednesday morning, Session T7 (CEU's provided) focuses directly on "Yankee Reliability," beginning with a presentation by Clive Butler of PMT on diagnosing surface chatter. Sam Archer of Nalco then looks more closely at the impact of chatter on yankee surface reliability, Jerry Vandoros of Kadant covers yankee doctor considerations for improving safety and reliability, and John Yolton of SKF explores reliability best practices in the global tissue industry. Session T8 on "Converting Efficiencies" features presentations by John Cork of Ibis International on process air filtration for tissue converting and Karl Hilden of Papertech on solving tissue production and converting problems using event capturing camera systems. Completing the Forum's final session on Wednesday morning, Futura analyzes key factors for enhanced converting performance.
More information about PaperCon 2013 and the Tissue360° Tissue Forum is available online, including online registration and the Tissue Forum program.
##SHARELINKS##
|
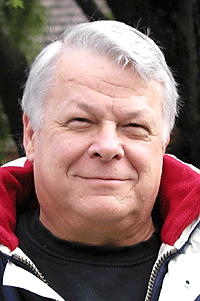 The keynote speaker for the OpEx Maintenance and Reliability Workshop at TAPPI PaperCon 2013 in Atlanta, Ga., USA, on April 30, will be John Yolton with SKF, a highly respected paper industry reliability expert who will explore "The Continuing Journey to Asset Reliability Improvement." As Yolton notes, "with the NAM pulp and paper market contracting, only the most reliable equipment can provide a competitive advantage. Data demonstrates that there is clearly a return on investment for those ‘best' within the pool of competitors."
What do the "best" do to achieve this extra measure of competitiveness? Yolton's presentation will identify and discuss the primary issues associated with the Top 3%, e.g., the "best" and the "rest." "It might surprise you to find that ‘soft' issues play an important and vital role in the transformation and journey from the ‘rest' to the ‘best,'" Yolton says. His presentation includes a case study analysis at Daishowa-Marubeni International's 500,000 metric tpy chemical pulp mill in Canada.
The opening keynote session also includes presentations by Bill Wick of American Industrial Metrology on "A Holistic Approach to Paper Machine Alignment" and Dave Cutnaw of SKF on "Maintenance and Asset Reliability Strategies—Developing a Foundation for Success."
More information about PaperCon 2013 and the OpEx Maintenance and Reliability Workshop, including registration procedures, is available online. Also available online is the 2013 OpEx Workshop program.
##SHARELINKS##
|
The TAPPI Tissue Properties & Manufacturing Course will be held on April 27-28, 2013, in Atlanta, Ga., USA, and co-located with 2013 PaperCon and the Tissue Forum. Both the Tissue Forum and Tissue Properties & Manufacturing Course are being sponsored by TAPPI's Tissue360° magazine.
This is a great opportunity to get the most out of your conference experience. The Tissue Properties course is designed for those who desire an introductory-to-intermediate level, comprehensive, and structured course on tissue properties, and the effect of manufacturing. This course precedes the Tissue 360° Forum at PaperCon, and is an excellent educational compliment to these technical sessions.
The course will be particularly helpful to non-technical professionals, technical process engineers, operators, suppliers, converters, and marketers with 0-5 years of experience in tissue manufacturing.
More information about the Tissue Properties & Manufacturing Course is available online.
##SHARELINKS##
|
The U.S. Supreme Court has overturned the U.S. Ninth Circuit Court's decision in the case of Georgia-Pacific Wes, Inc. vs NEDC, Sup. Ct. No. 11-347, commonly referred to as the "forest roads" case. In a ruling announced this past week, the decision overturns a 2011 ruling by a three-judge panel of the Ninth Circuit Court that reversed 35 years of regulation governing management of rainwater runoff from forest roads.
Originally, the Ninth Circuit Court had rejected the Environmental Protection Agency's longstanding interpretation of the Clean Water Act and would have required forest road operators in the states under its jurisdiction to obtain Clean Water Act discharge permits for ditches, drains, and culverts that channel rain runoff from their roads ― treating rain runoff from forest roads used for logging the same as industrial sources.
"The court's ruling is a significant victory for the 2.5 million people and thousands of local economies that depend on forest products for their livelihood," said Mike Adams, G-P's SVP of sourcing and fiber supply. "Today's decision helps protect jobs and ensures that regulating forest roads through state forestry best management practices continues as the most environmentally responsible way to oversee management of the nation's forest roads.
"By overturning the Ninth Circuit, the Supreme Court has helped keep private and public resources focused on implementing state forestry best management practices, which are sensitive to local conditions, rather than requiring costly permitting that likely would have resulted in wasteful litigation without serving the environment or the economy. We are pleased the Supreme Court recognized the serious errors in the Ninth Circuit's ruling," Adams said.
The case has been closely watched not only by the forest products industry, but also by other impacted industries, with numerous groups banding together to file 15 amicus briefs, including a brief filed by 31 state attorney generals supporting G-P's position.
Timothy Bishop, the lead appellate attorney for the forestry industry, said that "during the course of the lawsuit, EPA adopted a new regulation that reiterated its intention that forest road discharges should be regulated at the state level and not by federal permitting. Because the court's decision today means that new rule is legally unassailable, it brings certainty to the industry nationwide on this important issue of environmental protection."
##SHARELINKS##
|
Market Roundup
Total printing and writing (P&W) paper shipments in the U.S. were down 12% from February 2012, according to the February 2013 Printing-Writing Paper Report published this week by the AF&PA, Washington, D.C., USA. Additional key findings of the report are:
- February shipments of coated free sheet (CFS) papers decreased 5% compared with February 2012, with year-to-date CFS shipments up less than 1% relative to 2012
- Uncoated free sheet (UFS) papers shipments of 701,700 tons in February were 10% below the same period last year, with imports increasing 14% year-over-year in January
- February uncoated mechanical (UM) paper shipments decreased 22% compared with February 2012
- February shipments of coated mechanical (CM) decreased 20%, compared with February 2012, to 218,900 tons, the lowest total since before 1995.
##SHARELINKS##
|
China's hunger for wood was less acute in 2012 than the previous year, according to the Wood Resource Quarterly (WRQ), Seattle, Wash., USA. In particular, importation of softwood logs fell substantially from the record levels of 2011. Importation of lumber was also lower in 2012, but the decline was much less than that of logs. The biggest change in wood imports between 2011 and 2012 was the sharp decline of Russian logs crossing the Chinese border and the reduced lumber volumes from the U.S. lumber entering Chinese ports.
North America is a major supplier of softwood products to China, with the market share for logs and lumber in January 2013 accounting for 26% and 53%, respectively. In 2012, Canada and the U.S. exported logs and lumber valued at 2.1 billion dollars, which was down 17% from 2011. Despite the decline in shipments last year, it was still the second highest level on record and more than four times the level just three years earlier, WRQ notes.
Sawmills in British Columbia have become the largest suppliers of lumber to China in recent years, surpassing Russia in 2010. The value of Canadian shipments was about $1.1 billion in both 2011 and 2012, and the value is likely to be higher in 2013. Just five years ago, less than $100 million worth of lumber was shipped to China. This new market has become increasingly important for many sawmills in Western Canada, which historically have shipped most of their production to the U.S. market. Five years ago, about 10% of the export volumes from the province were destined for China. This share had gone up to 32% in 2012. The still unanswered question is how sawmills in this region will choose to allocate their production in the coming years when lumber demand is expected to increase in the U.S., WRQ reports.
Log exports from the Western U.S. to China have jumped ten-fold the past five years, which has had a major impact on the coastal log market in the states of Washington and Oregon. Despite relatively low production levels in the industry the past five years, saw log prices in the fourth quarter of 2012 were about 60% higher than in 2009, according to the North American Wood Fiber Review. This development coincides with the period when log exports to China expanded rapidly. Although lumber price increases are good news for sawmills in the Western states during 2012 and early 2013, the bad news is that the log prices are increasing as well.
##SHARELINKS##
|
Total U.S. kraft paper shipments were 119,000 tons, a decrease of 15% compared with the prior month, the AF&PA (Washington, D.C., USA) reported in its February 2013 Kraft Paper Sector Report this week. Bleached kraft paper shipments increased year-over-year 13% while unbleached kraft paper shipments decreased 13% year-over-year.
As a result, total kraft paper shipments are down slightly less than 1% compared with the first two months of 2012. Total month-end inventory decreased 3% to 71,300 tons this month compared with January 2013 month-end inventories.
##SHARELINKS##
|
Pulp & Paper
Catalyst Paper, Richmond, B.C., Canada, reports that it has completed the sale of its approximately 50% interest in Powell River Energy Inc. and Powell River Energy Limited Partnership to Powell River Energy Trust, a Brookfield Renewable Energy affiliate, for $33 million . Approximately $12.7 million of the net proceeds of the sale will be distributed to certain unsecured creditors of Catalyst pursuant to its plan of arrangement under the Companies' Creditors Arrangement Act of Canada. The company will offer to purchase a portion of its Floating Rate Senior Secured Notes with the balance of the net proceeds.
Catalyst Paper produces diverse specialty mechanical printing papers, newsprint, and pulp. Its customers include retailers, publishers, and commercial printers in North America, Latin America, the Pacific Rim, and Europe. With three mills located in British Columbia, Catalyst has a combined annual production capacity of 1.5 million metric tons.
##SHARELINKS##
|
Joining an ambitious campaign to encourage reading, Domtar Corp., Montreal, Que., Canada, this week announced it will sponsor World Book Night U.S. The effort will distribute 500,000 free books at thousands of locations across the U.S. on April 23.
World Book Night will rely on 25,000 volunteer book lovers, including Domtar staff at two dozen facilities. They will personally hand out specially printed copies of a wide range of books to people who either don't read frequently or don't have the means or access to printed books.
Domtar's PAPERbecause campaign will also help spread the word about World Book Night by advertising in media such as The New York Times, Forbes, Fortune, Bloomberg BusinessWeek, Smithsonian, and The Week, and Time. Domtar's commitment comes as part of its award-winning PAPERbecause campaign that showcases paper's sustainability and enduring value in a digital age.
"World Book Night is a reminder that paper is personal, purposeful, and sustainable, and we're proud to support it" said Paige Goff , Domtar's VP of Sustainable Business and Brand Management. "Domtar believes in the power and joy of the simple act of reading a printed book, and this is a great way for us to give back to readers around the country."
World Book Night U.S. Executived Director Carl Lennertz added that "we chose a variety of books about different subjects so that everyone can find something appealing, no matter where they live, what their age, what their backgrounds are, or what interests them the most. We're thrilled that Domtar will be working with us and helping get people connected with books they will love to read."
##SHARELINKS##
|
International Paper, Memphis, Tenn., USA, has joined the Global Forest & Trade Network in North America (GFTN), one of World Wildlife Fund (WWF)'s initiatives focused on eliminating illegal logging and promoting environmentally and socially responsible forest management. IP joins a network of more than 200 companies and communities around the globe committed to the responsible forest management and sourcing of forest products.
"We have long been committed to responsible forestry everywhere we operate, and collaborating with WWF is an excellent way to demonstrate and grow that commitment," said Teri Shanahan, IP's VP, Sustainability.
The initial scope of IP's participation in GFTN will encompass fiber sourced for the company's North American and Brazilian mills, representing more than two thirds of its global fiber volume.
"By joining GFTN and increasing its sourcing of credibly certified fiber, International Paper—as the world's largest paper and packaging company—can use its purchasing power to drive improvements in responsible forestry around the globe," said Suzanne Apple, VP of Business and Industry for WWF. "This kind of leadership is critical to conserving the places and species we are working so hard to protect."
In the U.S., IP has increased its sourcing of Forest Stewardship Council certified fiber by more than 1.2 million tons over the past five years, and expects to triple that increase by the end of 2014. While IP supports multiple certification standards, the company has developed a highly successful model for increasing its supply of FSC-certified fiber in the Southeastern U.S. In Brazil, IP's operations source approximately 75% of its pulpwood from FSC-certified sources.
As a GFTN participant, IP will release an updated global fiber sourcing policy. The company announced a set of voluntary goals in 2012, including one focused on increasing third-party certified wood fiber by 15% by 2020. Participation in GFTN aligns well with this goal, as the company implements an action plan toward achieving its 2020 target. In addition, IP will support WWF's efforts to protect forests, holding particular value for their biodiversity, landscape, and socio-economic benefits.
##SHARELINKS##
|
Metso, Finland, reports that it is considering the possible separation of its Pulp, Paper, and Power businesses into a new company. The company's current Mining and Construction and Automation businesses would remain in the current company after the potential separation. The contemplated transaction would help the two companies capitalize on their strengths in their respective markets faster and more efficiently, Metso notes.
Jukka Viinanen, Metso's chairman, said that the company has developed its businesses purposefully during the past years to the point where entering the next stage of development would be smoother as separate companies. "Both of them are strong global businesses with well-established positions in their customer industries. By separating the two, we would seek to accelerate strategy implementation, as clearer business structures would increase the focus and ambition of the two companies with distinct growth strategies. The board also believes that both companies would be seen as attractive investments, which has the potential to increase value for our shareholders."
Matti Kähkönen, president and CEO, added that "developing Mining, Construction, and Automation and Pulp, Paper, and Power businesses separately would help the already strong two entities to fully realize their potential. This would in turn benefit our customers and personnel through more focused management, superior competence development, and customer services, and through enabling both companies to cultivate their technology and services offering that would match their goals perfectly,"
The Metso Board aims to finalize the study process and announce further details about the possible separation by the end of the second quarter of 2013.
Although no decisions have been taken, the separation, if carried out, would likely be by means of a demerger (i.e. partial demerger as defined in the Finnish Companies Act), after which the Mining, Construction, and Automation businesses would remain with Metso, whereas Pulp, Paper, and Power businesses would constitute the new company, which would nitially have the same ownership structure as Metso and would be totally independent from it without any cross-ownership between Metso and the new company. This strategy study will be headed by Kähkönen.
If implemented, the demerger would leave Metso shareholders' ownership in the company unchanged. In addition, Metso shareholders would receive shares in the new company as demerger consideration in proportion to their shareholding in Metso. The demerger and listing of the new company's shares would be expected to take place before the end of this year.
##SHARELINKS##
|
Pope Resources, Poulsbo, Wash., USA, together with the State of Washington's Department of Ecology this week announced that they have agreed on the scope for the final portion of the environmental clean-up effort in and around Port Gamble Bay, a process that began in 2002. Pope Resources and the Department of Ecology will sign a consent decree, which is a legally binding agreement that will lay out how the remaining clean-up of contaminated in-water sediments will be designed and carried out.
The agreement, which was reached after lengthy negotiations, includes:
- Removal of about 2,000 creosote pilings
- Excavation of intertidal areas and dredging of wood waste from the bottom of Port Gamble Bay
- Installation of a sand-cap of up to 4 ft in specific locations in Port Gamble Bay
- Removal of all existing docks and overwater structures on and around the former Pope & Talbot Port Gamble mill site by the fall of 2015.
The clean-up effort, which will likely take a few years to complete, is estimated to cost $17 million. This cost will be shared by Pope Resources and the Washington State Department of Natural Resources (DNR), the other Potentially Liable Party as determined by the Department of Ecology. The agreement between the Department of Ecology and Pope Resources opens the way for the company and DNR to engage in discussions regarding how costs for the clean-up effort will be shared.
As part of the clean-up agreement, Ecology will allocate $2.0 million for the removal of Pope Resources' sewer outfall that drains into Hood Canal and will also contribute about $2.0 million to assist in the acquisition of Pope Resources' nearly 500-acre "Shoreline Block," which contains nearly two miles of shoreline on Port Gamble Bay. The Kitsap Forest & Bay Coalition has been working to obtain grants to acquire this $4.6 million property for conservation.
The negotiations between Pope Resources and the Department of Ecology also included extensive discussions on a voluntary Natural Resource Damages (NRD) assessment entailing restoration projects on and around the former Pope & Talbot mill site. These discussions were not conclusive and the parties agreed to end negotiations. A separate process to determine any potential NRD liability will be forthcoming.
As part of its effort to redevelop the historic town of Port Gamble, Pope Resources is preparing an application to build a new community dock to serve the town and local community. As part of this application, the company wanted to delay the removal of two small docks used by current mill site tenants as mitigation for the new dock. The company has agreed to remove these docks as part of the clean-up effort, but to stage the timing of the removal to 2015. By phasing the removal of these docks within the broader clean-up effort, the company will be able to apply for advanced mitigation credit as part of its new dock application.
##SHARELINKS##
|
SCA, Sweden, has ordered from ABB, Zurich, Switzerland, an upgrade of the paper quality control system for production line LWC4 at its Ortviken paper mill in Sweden. The project scope includes a number of new functions and measurement scanners for the paper quality control process as well as integration of the new functions in the existing operator environment. The upgrading project represents the final step of integrating the entire control in one single operator environment in the paper line.
The new quality control system, System 800xA QCS with six operator stations, will be integrated in a virtualized server as well as in the existing operator environment for DCS and drive systems. SCA Ortviken is one of the first paper mills to use ABB's technology for virtual operator stations, which provides lower system maintenance and energy use since fewer hardware units are needed to do the work that previously required one computer for each operator.
The order also includes replacement of the older measurement scanners with the Network Platform, including latest technology such as the moisture measurements meter HPIR and the optical thickness meter Optical Caliper. Multivariable CD Control (MCD) is used for profile control, which enables control decisions based on the most important paper quality aspects in every situation. The new system will be commissioned in late May of this year.
SCA Ortviken is one of the largest paper mills in Sweden with four paper machines and an annual output of 510,000 metric tons of lightweight coated (LWC) paper and 380,000 metric tons of uncoated paper.
##SHARELINKS##
|
The Sofidel Group, Italy, reports that it has invested more than EUR 25 million to date to achieve a target it set together with the World Wildlife Fund (WWF) of reducing the Group's carbon dioxide emissions 26% by 2020. The steps taken range from increased use of renewable energy sources to improving the efficiency of plant and equipment and investment in co-generation plants.
The investments are:
- 2008: EUR 3 million to install a 300 kWp photovoltaic array at the Delicarta Paper Mill, avoiding 225 tons of carbon dioxide emissions per annum
- 2009: EUR 1.5 million for rebuilding work on the hydroelectric power generating plant at the Fibrocellulosa plant (Lucca, Italy), avoiding approx. 350 tons of carbon dioxide emissions per annum
- 2009: EUR 200,000 for repair work on the supply channel for the hydroelectric plant at the Werra Papier plant (Wernhausen, Germany), avoiding 150 tons of carbon dioxide emissions per annum
- 2009/2010: EUR 900,000 for secondary interventions focused on energy and water saving (Delipapier Fr; Fibrocellulosa; Papyros; Soffass Cartiera; THP; Werra; Delipapier De; Delicarta Valdottavo; Delicarta Porcari; Cartiera di Monfalcone)
- 2010: EUR 2.5 million to install a 554 kWp photovoltaic array integrated into the roof of the Soffass converting plant, situated in Porcari (Lucca, Italy), avoiding 255 tons of carbon dioxide emissions per annum
- 2010: EUR 2.1 million to install a 778 kWp photovoltaic array partially integrated into the roof of the Delicarta converting plant in Porcari (Lucca, Italy), avoiding 420 tons of carbon dioxide emissions per annum
- 2010: for a total expenditure of EUR 300,000, Sofidel installed 350 LED lamps to replace old neon or other types of lighting, avoiding 110 tons of carbon dioxide emissions per annum
- 2010: EUR 7 million to construct a new generation gas turbine at the Delitissue plant (Ciechanov, Poland) which will enable carbon dioxide emissions to be reduced by around 16,000 tons per annum
- 2011: EUR1.6 million for secondary interventions focused on energy and water saving (Comceh; Soffass paper mill; Sofidel U.K.; Swedish Tissue).
- 2012: EUR 5.350 million to install two photovoltaic arrays for Delicarta paper mill and Soffass Converting, both located in Porcari (Lucca, Italy) capable of approximately 1956 kW and an annual production estimated at approximately 1,975,000 kWh
- 2012: EUR 1.780 million for interventions focused on energy saving (Soffass paper mill; Soffass Converting; Delicarta paper mill; Delicarta Tassignano; Delitissue; Ibertissue; Werra Papier; THG, Papyros; Sofidel U.K.; Swedish Tissue.
##SHARELINKS##
|
Containerboard/Packaging
U.S. February containerboard production fell 10.2% from January 2012 and 1.7% less than the same month last year, as reported by AF&PA (Washington, D.C., USA) in its February 2013 U. S. Containerboard Statistics Report published this week. However, the month-over-month average daily production decreased just 0.5%.
The containerboard operating rate for February 2013 lost 0.5 points compared with January 2012, decreasing from 97.1% to 96.6%.
##SHARELINKS##
|
Total U.S. boxboard production in February decreased by 1.9% compared with February 2012 and decreased 5.6% from last month, according to the AF&PA (Washington, D.C., USA) February 2013 U.S. Paperboard Report released this past week. Unbleached kraft boxboard production decreased over the same month last year and decreased compared with last month.
Total solid bleached boxboard and liner production decreased compared with February 2012 and decreased compared with last month. The production of recycled boxboard decreased compared with February 2012 and decreased compared with last month.
##SHARELINKS##
|
Mondi, South Africa, has ordered environmental upgrades from Andritz (Graz, Austria) for its mills in Slovakia, Sweden, and the Czech Republic. The orders are part of Mondi's program to increase energy efficiency and environmental protection.
For Mondi SCP, Ružomberok, Slovakia, Andritz will deliver a High Energy Recovery Boiler (HERB). In terms of its power-to-heat ratio, the new boiler will be one of the most efficient recovery boilers in the world. It will replace an existing boiler, increase the mill's electricity production significantly, provide conditions for operation with a minimized amount of fossil fuels, and will also enable an increase of pulp production.
The delivery also includes an evaporation plant retrofit. The evaporator will represent the latest technology including seven-effect heat economy, enhanced internal condensate purification, and 85% black liquor concentration. Startup of the boiler and the rebuilt evaporation plant is scheduled for the end of 2014.
At Mondi's Dynäs mill in Väja, Sweden, two existing lime kilns will be replaced by a new Andritz lime kiln. Based on its LimeFlash technology, operating costs will be reduced due to lower fuel consumption. Startup is planned for the fourth quarter of 2013.
For Mondi's Štětí, Czech Republic, mill, Andritz will build a packaging paper machine (PM 7) to produce various amounts of bleached kraft grades. PM 7 will start up in the latter part of 2014. In addition, the mill's PM 5 will receive an upgrade of its dryer section this October.
##SHARELINKS##
|
Siam Kraft Industry Co. (SGP Paper) has ordered a stock preparation system from Andritz (Graz, Austria) for its new PM 16 corrugated board plant located in Ratchaburi, Thailand. Startup is scheduled for the fourth quarter of 2014.
Andritz's scope of supply includes the complete stock preparation system—a drum pulping line with a capacity of 1,200 metric tpd based on 100% Local old corrugated container (LOCC) and a state-of-the-art reject handling system.
SCG Paper is a producer of packaging papers. Its total capacity, produced on 14 lines in Thailand, Vietnam, and the Philippines, amounts to approximately 1.9 million metric tpy of packaging paper that is certified to international environmental standards.
##SHARELINKS##
|
The Newark Group, Cranford, N.J., USA, this week announced that SCS Global Services, an independent auditor, has completed its audit on all six Newark Paperboard Mills. The mills are now FSC (Forest Stewardship Council) chain-of-custody certified.
"This is a significant enhancement for The Newark Group," said Raymond M. Vargo Jr., VP of sales, Newark Paperboard Mills. He added that "FSC is the gold standard of forest management and we are proud of this achievement. It is also a valuable resource for our vendors and customers."
The six Newark Group FSC certified mills are Mobile Paperboard, Newark America, Ohio Paperboard, Newark Pacific Paperboard, California Paperboard, and Wisconsin Paperboard.
"We have worked hard to obtain FSC Chain-of-Custody Certification," said Marc Hingsbergen, Newark Sustainability Manager. "Even a self-sustaining recycled paperboard company like Newark is always searching for additional ways to lower the carbon footprint within our mills through continuous improvement practices." The Newark Group employs more than 1,500 people and owns or manages 34 facilities.
##SHARELINKS##
|
New Products
Tembec, Montreal, Que., Canada, this week officially launched its Kallima Coated Cover C2S 14 pt - the latest extension of its line of bleached paperboard products. This new product release, Tembec notes, stems from its continuous investment in research and development operations.
Tembec point out that with the new 14 pt caliper coated two-side cover grade, printers can benefit from savings of up to 20% due to Kallima's basis weight advantage achieved through its unique high-bulk, low-density construction. Kallima's on-press reliability, visual performance, and savings potential make it ideal for business cards, post cards, direct mail, POP displays, advertising collateral, and pocket folders.
Kallima Coated Cover C2S 14 pt is available in rolls and sheets (skids only), and is fully compatible with post press production effects such as die cutting, UV and aqueous coating, folding, scoring, embossing, debossing, and foil stamping. It is FSC-certified and available with 10% recycled content upon request. The company is currently taking pre-orders for deliveries in late April.
Tembec is a producer of lumber, pulp, paper, and specialty cellulose. Its principal operations are in Canada and France. The company has some 3,700 employees and annual sales of approximately $2 billion.
##SHARELINKS##
|
People
Cascades President and CEO Alain Lemaire this week announced that he will be passing his company positions to Mario Plourde, currently COO of the company. The transfer will take place on May 9, following a two-year transition period. Lemaire also indicated that he will continue to serve as chairman of the board of directors.
"Of course, I will continue to support Mario in his daily activities, and I also intend to remain involved with the company, returning to my original passion by putting my technical skills to use in the various groups," Lemaire said. His brothers Bernard and Laurent will also remain active, continuing to serve on the board and the executive committee, and participating in the company's strategic planning.
"In February 2011, we announced the nomination of Mario Plourde to the position of COO. He belongs to the new generation of competent and dedicated leaders at Cascades, and he is a true believer in our values. At the same time, we announced the beginning of a transition process that would ensure a sound business succession. We had a plan, and we carried it out. After nearly 10 years at the head of the company, my brothers and I feel it is time to pass on the torch and make room for the younger generation," Lemaire said.
Plourde commented that "today, I'd like to thank Bernard, Laurent, and Alain for the trust they are placing in me," said Plourde. "It is a real honor to take over the reins of the company they have built with their own hands, and that has become one of the most admired businesses in the province. I am looking forward to perpetuating the values of the company, and taking the torch they have carried for close to 50 years. I want Cascades employees to know that they can count on me to be there, and that I am fully committed and dedicated to the company. In these challenging economic times, it is more important than ever to remain unified, stay the course, and build an increasingly efficient business."
Since his arrival at Cascades in 1985, Plourde has occupied various positions including controller, plant manager, and general manager. In 1997, he was appointed president and COO of the Specialty Products Group, and was president of this group from 2000 to 2010.
##SHARELINKS##
|
Resolute Forest Products Inc., Montreal, Que., Canada, reports that its board of directors has nominated Michel P. Desbiens and Jennifer C. Dolan to stand for election as new board members. Desbiens and Dolan will join seven other current members of the board standing for re-election at Resolute's upcoming annual meeting of stockholders on May 16.
Richard B. Evans, currently the company's non-executive chairman, has determined that he will retire and not stand for re-election. The board has recommended Bradley P. Martin, a current member, to serve as Resolute's new (non-executive) chairman, and Alain Rhéaume, also a current member, as lead director.
Desbiens is a forest products industry veteran and an accomplished business leader. He has been an independent consultant since 2000, advising a number of clients in the forest products industry, during which time he served briefly as Quebecor World Inc.'s CEO (international) and CEO for part of 2002 and 2003. He had been president and CEO of Donohue Inc. since 1994 when it was acquired by Abitibi-Consolidated Inc. (a predecessor entity of Resolute) in 2000, after which he served briefly as its chairman and a special advisor. Before then, he held a number of executive positions with Donohue, Domtar Inc., Chapelle d'Arblay paper mill, and Abitibi-Price Inc. (a predecessor entity of Resolute). Desbiens is a mechanical engineer. He currently serves on the board of Rogers Sugar Inc.
Dolan retired from The New York Times Co. in 2012 after a 33-year career, the last 10 of which she spent as VP of forest products, where she managed paper procurement and oversaw its equity investments in two paper mills, including as a member of the board of Donohue Malbaie Inc., a joint venture with the company. Before then, she held a number of executive and senior finance roles. Dolan is a certified public accountant, and a member of the American Institute of Certified Public Accountants.
Martin currently serves as VP for strategic investments with Fairfax Financial Holdings Limited. He previously served as its VP and COO and corporate secretary. Before joining Fairfax, he was a partner with Torys LLP, a leading Canadian business law firm, specializing in mergers and acquisitions and securities laws. Martin currently serves as chairman of Ridley Inc. and Imvescor Restaurant Group Inc., and as a member of the board of The Brick Ltd. Rhéaume is founder and managing partner of Trio Capital Inc. Before then, he was EVP and president of Fido, a subsidiary of Rogers Wireless Communications Inc., a role he assumed when Microcell Telecommunications Inc. was acquired by Rogers.
Rhéaume was president and COO and previously served as CFO of Microcell. He has served as associate deputy minister of finance and deputy minister of finance in the provincial government of Quebec.. Rhéaume currently serves as a board member of the Canadian Public Accountability Board, the Canadian Investors Protection Fund, Boralex Inc., and Redline Communications Group Inc.
##SHARELINKS##
|
The Washington Pulp and Paper Foundation (WPPF), Seattle, Wash., USA, this week announced that Michael A. Roberts has been hired as its next executive director. He will officially take on his new role beginning April 1.
Roberts is a 1969/71 graduate of the University of Washington with BS/MS degrees in chemical engineering. He has spent more than 40 years as a professional in the pulp and paper and allied industries, and he has been active in WPPF for more than 20 years. He and his wife Barb, also a UW graduate, have two grown children and three granddaughters.
The purpose of the WPPF is to attract excellent students to Bioresource Science & Engineering (BSE), and thus provide the industry and its allied industries with a pipeline of highly qualified technical graduates who understand and are dedicated to the industry. Bioresource Science & Engineering, formerly called Paper Science & Engineering (PSE), was established in the School of Forest Resources as a degree program at the University of Washington in 1965. WPPF, a not for profit organization, was incorporated in 1968.
##SHARELINKS##
|
TAPPI News
Register for NETInc by Saturday, March 30, and save more than 25% off registration rates. NETInc is the perfect forum for industry and academic researchers and professionals from the nonwovens and affiliated industries to make connections that support both career and industry growth.
Your registration also gives you access to these events:
Tissue 360 Forum
RPTA-PT Seminar
OpEx Reliability Workshop
##SHARELINKS##
|
PIMA has organized an IT track at PaperCon to explain the latest tools for high speed network and traffic isolation approaches, security considerations, and data integration techniques. Chaired by Paul Stecher, SVP and CIO, RockTenn, the session's speakers include several mill IT experts and systems providers.
Learn more about these sessions and PaperCon's PIMA Management Program.
Register before March 30 for best rates!
Special Mill Registration: For one flat fee, pulp, paper, and tissue mills can bring an unlimited number of employees to PaperCon. Learn more.
##SHARELINKS##
|
Fact: the current economy has affected many schools' endowment funds, resulting in decreased support of student scholarships.
But here's the good news: TAPPI has a scholarship to offer. You have a chance to apply for some green (funds to pay tuition, etc.) to fund a satisfying green career. The Cullison scholarship is available for graduate and undergraduate students with an interest in the pulp, paper, converting, and packaging industries.
William L. Cullison Memorial Scholarship.
What this message means to you:
- If you're a student, here is a great way to apply for financial assistance for the 2013-2014 school year.
- The deadline for the Cullison scholarship is May 1, 2013. Mark your calendar now to allow yourself time to create an application that reflects the hard work you've been investing in your career.
- If you are affiliated with a college or university, share this with your students or other staffers who work with students. They will be glad you did!
- If you're in the industry, perhaps you know of students worthy of scholarship assistance with their education, please pass this information along.
##SHARELINKS##
|
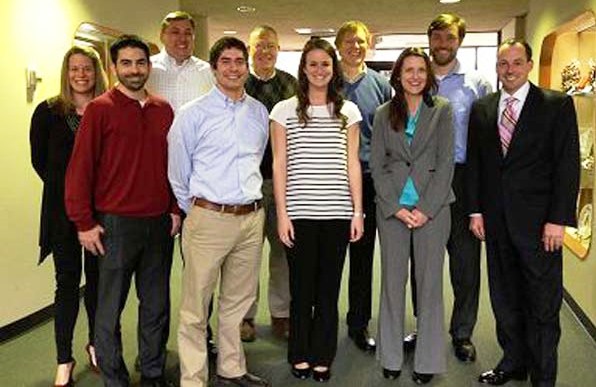 The TAPPI Team, along with experienced volunteer Richard Reese, with Dick Reese and Associates Inc., met Tuesday to discuss the history of the Speaker Management System with the software developer & President of EnSync Corporation, Mark Jones. An all day meeting was conducted to review Volunteer feedback, brainstorm ideas on ways to improve our member experience and on a process to implement new updates that will help improve the collection and processing of conference materials.
We are always looking for ways to improve, and welcome your feedback and suggestions on our current process. Please contact Ashley Anthony (770-209-7284; aanthony@tappi.org) or Ben Hopper (770-209-7243; bhopper@tappi.org) with any comments.
##SHARELINKS##
|
On March 20, young paper industry professionals met at TAPPI to give feedback on their needs and how to best structure the newly fomed TAPPI Young Professionals Committee. Sarah Muzzy from O'Neil Inc. volunteered to chair the committee and John Vanderklok from AstenJohnson will be the vice chair.
Muzzy said that "I am looking forward to working with the Young Professionals Committee. I think there are many wonderful opportunities to make the Young Professionals a strong and meaningful group of TAPPI. I am glad that there are others that share the vision and drive to help this group take shape".
The committee decided to start with four core interest areas: Programming and New Technology, Networking and Local Sections, YP Awards and Recognition, and YP Ambassadors that will focus on committee development and student connections. In addition to the leadership listed above, Austin Sickle from Stickle Steam agreed to chair the Networking interest area and Andrew Reep from Ashland agreed to chair the Programming and New Technology interest area.
TAPPI has purchased s new communities module for tappi.org and hopes to have it functional by early April. The communities module will imrpove the member online experience and add new functionality for sharing information. The Young Professional committee will act as beta testers for this new software so that it can be rolled out to all TAPPI members.
##SHARELINKS##
|
The Pulp and Paper Manufacturers Association (PPMA) has launched its first-ever Best Place to Work Award. The award is open to all companies in the forest products industry and will look not only at corporate life but also look at how employees feel about their work environments.
In conjunction with Majority Opinion Research Group, PPMA has started taking nominations for this award and will continue to accept nominations through July 1, 2013.
"This award is an exciting opportunity for PPMA to honor great companies. As an association that serves HR professionals, we know the value of the making your company a great place to work," said PPMA President Joe Thibaudeau, employee relations manager - Procter & Gamble - Green Bay, Wis., USA.
The award will be presented to the winner at the annual PPMA conference on October 23-25, 2013, in Milwaukee, Wis., USA. The winner will have the chance to speak with conference attendees about what makes his or her company the "Best Place to Work."
PPMA is a nonprofit association built around a community comprised of executives, managers, and human resource professionals from the pulp and paper industry. For its members, PPMA serves as a primary source of information on labor settlements and current human resource issues, governmenta,l and related operational issues.
To nominate your company for the Best Place to Work Award, use the online form.
##SHARELINKS##
|
The Pulp and Paper Safety Association (PPSA) will host its 70th Annual Safety and Health Conference - "The Human Element of Safety," June 9-12, 2013 in Williamsburg, Va., USA.
At the conference, presenters will address how human behavior will proactively help prevent, detect, and control events before they occur. Professionals from across the country know the importance of safety and attendees will hear from 18 speakers who will show the impact of addressing the human impact on safety. The conference will feature updates from OSHA, member company case studies, and PPSA's popular legal update.
Among the confirmed speakers are representatives from MeadWestvaco, Weyerhaeuser Co., Domtar, Safe Start, International Paper, REM Safety Consulting, Michael Best & Friedrich Law Firm, Training Logic, Change Management Consulting, and BushCo.
PPSA is a non-profit, non-political, international organization, devoted to the countinuous improvement of safety throughout all aspects of the paper industry. From forest products to paper mills, to converting plants, to recycle collections centers, our membership is grouped by category to ensure a fair and appropriate basis for comparison.
Registration is currently open for this event. More information is available online.
##SHARELINKS##
|
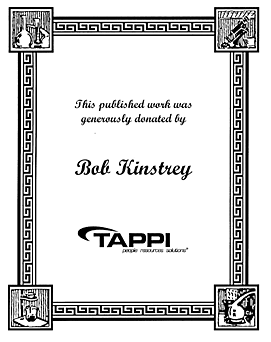
Do you have a history book gathering dust on your shelf? TAPPI's 100th year is coming soon and we are looking for donations to the TAPPI Library. Specifically, we are interested in histories of companies and mills in the paper and packaging industry (both producers and suppliers). Each donated book will have a bookplate in the front cover recognizing the donor. For more information please contact David Bell.
Please send books to:
c\o David Bell
TAPPI
15 Technology Parkway, South
Suite 115
Peachtree Corners, Georgia 30092
##SHARELINKS##
|
Nominations for the major TAPPI 2014 awards are due by August 1, 2013. The awards that may be presented in the upcoming year are:
Gunnar Nicholson Gold Medal Award - The Association's highest technical honor may be presented annually to recognize an individual or individuals for preeminent scientific and engineering achievements of proven commercial benefit to the world's pulp, paper, board, and forest products industries and the other industries that TAPPI serves.
Herman L. Joachim Distinguished Service Award - The Association's highest award for service may be presented annually to recognize leadership and service that have significantly and demonstrably contributed to the advancement of the Association.
Paul W. Magnabosco Outstanding Local Section Member Award - The highest honor for Local Sections may be presented annually to recognize an individual for outstanding leadership and exceptional service to one or more Local Sections, which have resulted in significant and demonstrable benefits to the Local Section members.
TAPPI Fellow - TAPPI Fellows are individuals who have been members of TAPPI for not less than 10 years prior to the nomination, and who have contributed meritorious service to the Association and/or the paper and related industries. Retiring members of the TAPPI Board of Directors become Fellows automatically at the end of their term.
The TAPPI Awards and Honors page has links to these awards that will show the qualifications required and links to the nomination forms that must be completed. You may submit all nomination forms by email to standards@tappi.org, or you may fax them to the attention of the awards department at +1-770-446-6947, or send them by mail to TAPPI, Awards Department, 15 Technology Parkway South, Peachtree Corners, GA 30092, USA.
##SHARELINKS##
|
The TAPPI - PPSA Safety Management Leadership course is designed to build leadership commitment and engagement for a culture of safety excellence. This partnership with the Pulp & Paper Safety Association brings you the best safety practices in the industry.
The Safety Management Leadership Course will be held April 10-11, 2013, at the TAPPI Training Facility in Peachtree Corners, near Atlanta, Ga., USA.
This course delivers curriculum to help you learn the fundamentals of record-keeping, incident investigation, risk management, cultivating a safety culture, managing change safely, and measuring performance. Take a look at the expert panel of instructors. The course is designed for anyone that is involved in workplace safety.
Course registration is limited to only 20 participants, so please register today at the course website. TAPPI and PPSA members save, and early registration discounts are available.
##SHARELINKS##
|
Tissue360 Forum @ PaperCon 2013
Monday, April 29 - Wednesday, May 1
Atlanta, Ga., USA
TAPPI's new Tissue publication, Tissue360o magazine, and TAPPI tissue experts have organized Tissue360 Forum, a comprehensive technical forum covering all aspects of tissuemaking. You will hear about the latest tissue technology, market trends, and pick-up some runnability/operational tips. The program is open to all full PaperCon registrants.
Program Overview:
Hygenic Products Market Overview
Session Chairs: Ken Patrick, Tissue360o
Chemistry Solutions for Tissue Making
Session Chair: Gary Furman, Nalco
Water and Energy Strategies for Tissue
Session Chair: Tom Jenn, Kimberly-Clark
Premium Tissue Manufacturing Technologies
Session Chair: Soren Eriksson, Metso
Tissue Controls and Measurement
Session Chair: Rene Naranjo, AstenJohnson
Yankee Reliability (CEUs provided)
Session Chair: Al Coons, Clearwater Paper
Converting Efficiencies
Session Chair: Kevin Brennan, Ashland Water Technologies
See the full Tissue360 Forum program.
PaperCon will take place April 27 through May 1, 2013 in Atlanta, Ga., USA. Designed by industry professionals, PaperCon brings together CEOs, mill managers, superintendents, scientsits, process engineers, and suppliers for the largest pulp and paper technical program in the world. No other such event provides such a comprehensive program, networking opportunites, and trade fair among such a distinguished group of industry leaders.
Learn more about PaperCon 2013.
##SHARELINKS##
|
The TAPPI Tissue Properties & Manufacturing Course will be held on April 27-28, 2013 in Atlanta, Ga., co-located with PaperCon 2013 and the Tissue Forum. This is a great opportunity to get the most out of your conference experience. This Tissue Properties course is designed for those who desire an introductory-to-intermediate level, comprehensive, and structured course on tissue properties and the effect of manufacturing. The course precedes the Tissue Forum at PaperCon 2013 and is an excellent educational component to these technical sessions.
This course will be particularly helpful to non-technical professionals, technical process engineers, operators, suppliers, converters and marketers with 0-5 years of experience in tissue manufacturing. Go to the course website to learn more.
##SHARELINKS##
|
PaperCon, April 27 - May 1 in Atlanta,Ga., USA, will include two focused, peer-reviewed sessions within the PIMA Management Program that examine recent developments and usage techniques in Information Technology (IT).
Session M6: "Traditional DCS and IT Converge: How to Position Yourself to Take Full Advantage of the Opportunities," chaired by Paul Stecher, SVP and CIO, RockTenn, is geared to DCS control engineers, superintendents, and IT support, and will focus on high speed network and traffic isolation approaches, security considerations, and the latest data integration techniques.
Session M8: "Using Industry Proven Software Tools to Drive Mill Efficiencies", chaired by Jim Pigott, MAJIQ, will include three presentations: "Integrating Forecasting to Costing in Dollars and Sense" presented by David Pawelke, MAJIQ; "Thoughts on Paper: Connecting the Supply Chain" presented by Jim Black, OSI Soft; and "Vertically Integrated Real-time Costing for Pulp and Paper Mills," presented by Fredric Karlsson, Enterprise Performance Solutions.
Learn more about these sessions and the PIMA Mangement Program at PaperCon.
Learn more about PaperCon 2013.
##SHARELINKS##
|
Introduction to Nonwovens Tutorial
Monday, April 29
3:30 - 5:00pm EST
This tutorial will be led by Behnam Pourdehimi, executive director of the Nonwovens Institute at North Carolina State University.
As far as business segments that are growing and vibrant, the Nonwovens industry certainly meets those criteria. But Nonwovens means different things to different people. The Nonwovens Institute at North Carolina State University will share an insightful tutorial about the industry, what it includes, which areas are mature, and which are growing.
This tutorial is part of the NETInc Innovative Nonwovens Conference, April 29 - May 1, in Atlanta, Ga., USA. This is the only technical conference developed by engineers and technologists to help you understand the innovation behind the science and how it impacts the market. Learn more about NETInc.
##SHARELINKS##
|
With more than 80 technical presentations and 50 posters, the 2013 TAPPI International Conference on Nanotechnology for Renewable Materials is packed with the latest applications of renewable nanomaterials.
The conference will take place June 24-27, 2013, at the KTH Royal Institute of Technology in Stockholm, Sweden. Register by April 29 for the best rates!
This year's conference features keynote presentations that focus on the steps needed to deploy emerging nanotechnologies into the bioeconomy. Hear from these recognized global leaders:
- "Small World, Large Impact: Driving a Materials Revolution through Nanotechnolgy" Arthur Carty, executive director and research professor in the Department of Chemistry, Waterloo Institute for Nanotechnology, University of Waterloo, special adviser to the president on international science and technology collaboration
- "Towards High-Value Applications of Nanocellulose: A Player an Patent Landscape Approach" Katja Salmenkivi, Pöyry Management Consulting
- "Key Considerations for Successful Technology Transfer of Nanocellulose" Martha Marrapese, Keller and Heckman, USA
- "Life Cycle Considerations of Nanomaterials: Possibilities for Evaluating the Environmental Impact of Renewable Nanomaterials" David Lazarevic, Division of Environmental Strategies Research and the Divsion of Industrial Ecology, KTH
- "Nanosafety Research and Legislation in European Union: Future Activities" Tom van Teunenbroek, ministry of infrastructure and environment, The Netherlands
Sponsorship Opportunities are available.
Looking for Additional Nanotechnology Events?
Check out the TAPPI Flexible Packabing Symposium: New Technologies, preceding the ICE USA Exposition on April 8 at the Orange County Convention Center in Orlando, Fla. Sessions include Innovations in Nanocomposites, Innovations in Barrier, and Brand Launch, Shelf Appeal, and Authentication. Learn more.
##SHARELINKS##
|
The NETInc Innovative Nonwovens Conference, April 29 - May 1, 2013, in Atlanta, Ga., USA, is the only technical conference developed by engineers and technologists to help you understand the innovation behind the science and how it impacts the world.
Program topics include: Nanotechnology, Binders and Additives, Building Sciences, Health Care and Medical Applications for Nonwovens, Manufacturing Technology, Process Management Technology, and an Intro to Nonwovens Tutorial.
With several focused tracks, NETInc offers peer reviewed papers, expert speakers, and exclusive networking opportunities. NETInc participants can also enjoy the full PaperCon program and exhibits, Tissue360 Forum, RPTA P-T Seminar and the OpEx Reliability Workshop with their registration.
Learn more about NETInc.
##SHARELINKS##
|
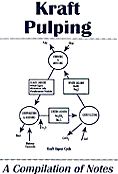
Edited by: A. Mimms, M.J. Kocurek, J.A. Pyatte, and E.E. Wright
Liberally illustrated with more than 130 diagrams and photographs, this book includes basic formulas and diagrams to explain the structure of wood, variables affecting the quality and handling of wood chips, pulping chemistry and equipment, the pulping process, and black liquor recovery. It includes a glossary of frequently used terms. Kraft Pulping.
View the Table of Contents
Preview Sample Pages
Product code: 0101R171
Member Price: $58.00
Non-Member Price: $87.00
##SHARELINKS##
|
Strengthen your understanding of the corrugating process, and linerboard and medium performance properties and manufacture with TAPPI's Linerboard Medium & Corrugated Box Manufacture Course, April 15-16, at the Holiday Inn in Neenah, Wis., USA.
With an emphasis on helping attendees improve corrugating box performance and runnability, this popular introductory to intermediate level course is ideal for process engineers and operators in linerboard and medium manufacturing facilities and corrugating and converting plants.
Instructors Michael J. Kocurek, Professor Emeritus, of Paper Science & Engineering at North Carolina State University, and Jon Porter, Senior Trainer / Process Specialist for Fosber America will address:
- The Corrugated Session (1/2 day) will cover how to achieve the strongest bond and highest quality combinerboard. You'll learn about (1) the equipment, (2) starch, (3) corrugated process technology, and (4) importance of linerboard and medium properties and runnability.
- The Properties and Testing of Liner and Medium session (1/2 day) covers the tests, what they mean, and how the properties of the board affect the tests.
- The Pulp and Paper Mill Operations session (1 day) will cover the technology of the pulp and papermaking processes, and how they affect the quality, properties, tests, and runnability of the liner and medium.
View the proposed course schedule.
Register by March 15 to take advantage of the Early Bird registration discount. Join TAPPI or renew your membership for the best rates!
##SHARELINKS##
|
Guidelines for the Safe Operation of Steam Heated Paper Machine Dryers
Edited by Steven P. Fusco
This is a guide to the safe operation and maintenance of steam heated paper machine dryers. The Steam Heated Dryer Subcommittee of the TAPPI Engineering Division's Maintenance and Mechanical Engineering Committee prepared this report. The report includes details on dryer construction, operation, and safety guidelines. It also features a glossary, a reference list, and conversion factors for SI units.
Guidelines for the Safe Operation of Steam Heated Paper Machine Dryers.
View the Table of Contents.
Product Code: 0101R250
TAPPI Member Price: $37.00
Non-Member Price: $54.00
##SHARELINKS##
|
PaperCon Session: Insights into Effective Labor/Management Relationships
Organized by PPMA and PIMA
Monday, April 29, 2013 - 1:30-3:00pm
Many companies have embraced innovative processes for managing labor-management relationships. These processes result in better communication, more effective problem solving, and alignment around shared business goals. Attend this session at PaperCon, part of the PIMA Management Program, and hear examples of effective labor/management teams that yield positive business results. Panelists will share first-person testimonials and stories of challenge, frustration, and success.
Moderator:
Roger Hagan, Zilkha Biomass Energy
Panelists:
Steve Myers, mill manager, Thilmany Paper, Kaukauna, Wis.
Peter Tantalo, operations manager, RockTenn Solvay, Syracuse, N.Y.
Mike Rayome, director, human resources, Graphic Packaging, Wausau, Wis.
Karl Christianson, mill manager, RockTenn, Stevenson, Ala.
PaperCon will take place April 27 through May 1, 2013, in Atlanta, Ga, USA. Designed by industry professionals, PaperCon brings together CEOs, mill managers, superintendents, scientists, process engineers, and suppliers for the largest pulp and paper technical program in the world. No other event provides such a comprehensive program, networking opportunities, and trade fair among such a distinguished group of industry leaders.
Learn more about PaperCon 2013.
##SHARELINKS##
|
The Introduction to Traditional and Emerging Printing Technology Course will be co-located at the 2013 PaperCon Conference, April 27-29, 2013, in Atlanta, Ga., USA.
This is an introductory course on printing methods and applications, designed for those who need to understand print quality, attend print trials, trouble shoot print problems or are generally new to printing operations. It will be taught by printing experts from TAPPI's Coating and Graphic Arts Division and is an excellent complement to the Coating Program at PaperCon.
As an added bonus, the course will include a tour of Hewlett-Packard's new state-of-the art facility where production laser and inkjet presses will be demonstrated.
Course attendees may also join the Coating and Graphic Arts Opening Session where printing visionary Frank Romano is giving the keynote address. Learn more and register online.
##SHARELINKS##
|
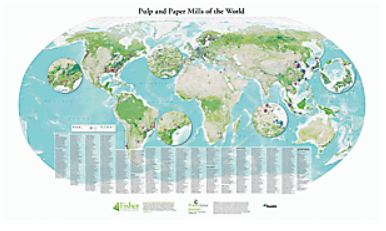
One of TAPPI's most exciting new products is the wall-sized, laminated 2013 Pulp & Paper "Mills of the World" Map.
A winning combination of high quality print and paper stock along with brilliant colors makes this the perfect map to frame and hang in your office. The "Mills of the World" map features include:
- Every mill in the world producing 50 tpd or more
- Major greenfield projects
- Design elements showing mill characteristics, forest cover, and typography
- 3 ft. x 5 ft. (or 0.99 x 1.5 meters) .
Each map will be shipped in a protective tube, ready for display.
Don't miss out on this popular item. Order your Pulp & Paper "Mills of the World" Map today.
Product code: 12PPMAP
Member Price: $299.00
Non-Member Price: $319.00
##SHARELINKS##
|
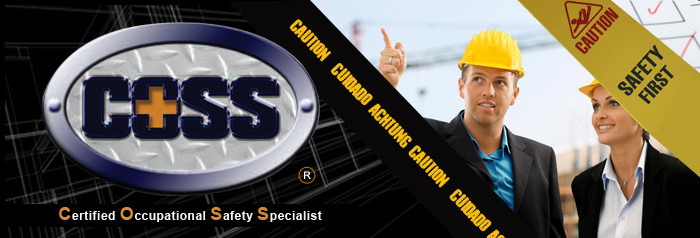
Are you ready to go further, faster in your safety career? The Certified Occupational Safety Specialist (COSS) class can take you there.
The COSS Class is Unique
Not only will you learn how to read and understand the OSHA 1910 and 1926 CFRs and help your company avoid OSHA citations that cost millions of dollars, but more importantly, by learning how to work safely on a job site, you can teach your company how to lower fatalities and near misses. Almost 47% of COSS graduates responding to our survey indicate that, since taking COSS, their company's injury rate and/or OSHA recordables have decreased by as much as 25% and others attest to as much as a 100% decrease!
Request a Course Outline & Syllabus for more information.
The class also addresses the psychology of safety, the true cost of an accident, hazard recognition, how to start up a health and safety program, behavior based safety, system safety, and much more!
What Will You Receive?
Upon successfully completing the class, you will obtain your national Certified Occupational Safety Specialist (COSS) designation, your OSHA 10-hr. card of completion in construction, and your OSHA 10-hr. card of completion in general industry.
National Program Recognitions
COSS is currently one of only 37 programs in the world recongnized and accredited by the American Petroleum Institute (API). In addition, the certifying body for construction education for colleges, universties and technical/trade schools, American Council for Construction Education (ACCE), has also recongnized our program. COSS is the only non-degree program to receive this national endorsement. Lastly, COSS has been established as a mandatory course for students in the Construction Management Program at Louisiana State University.
Program Content
The program consists of 40 hr. of hands on, face-to-face learning, which is delivered by an Authorized OSHA outreach trainer in both construction and general industry. Case studies and workshops are used extensively to bring learning objectives into focus. Guest speaker from areas such as OSHA and other governmental agencies are used to enhance the learning experience. Student presentations, daily quizzes, practical reviews, and a comprehensive final exam will allow you to demonstrate your competency.
Prerequisites
The only prerequisite for the COSS class is you must have a high school diploma or equivalent. In each class, we tend to have a mix of non-experienced, first time safety persons, as well as safety professionals who have been in the safety field for 20+ years. But, we have learned that regardless of the numbers of years of experience you have in safety, everyone leaves the COSS class with a wealth of knowledge!
Visit the COSS website for FAQs, testimonials and a list of clients that have taken COSS.
Register now.
If you would like more information on the COSS program, contact Beth Gordon at 877-610-2677
##SHARELINKS##
|
|
|