Over the Wire
TAPPI
Weekly Spotlight
International Paper, Memphis, Tenn., USA, and Dogwood Alliance, a southern U.S. forest conservation organization, announced an agreement this past week that will help advance science based forestry improvements in the world's largest paper producing region. The former foes will map forests around I P's southeastern operations to identify whether any endangered forests or high conservation value areas exist. This mapping will help ensure that IP is not sourcing from any endangered forests as per its long-standing company policy and will also identify mutually-agreed upon areas where conservation can be focused. In addition, IP and Dogwood Alliance will work together to discourage the conversion of natural hardwood forests to pine plantations.
This collaboration builds on initiatives recently announced by IP. The first is its membership in the World Wildlife Fund's Global Forest & Trade Network in North America. Additionally, IP announced a $7.5 million five-year project with the National Fish and Wildlife Foundation to restore and conserve forests in the Coastal Carolinas, Cumberland Plateau, and Texas/Arkansas Piney Woods regions. Finally, IP announced an increase in its sourcing of Forest Stewardship Council certified fiber by more than 1.2 million tons during the past five years, and expects to triple that increase by the end of 2014. The company continues to support multiple certification standards as part of its public goal of increasing certified fiber.
"IP has a clear, built-in need to maintain healthy forests; our business creates the economic basis for millions of acres of land to remain as forests over long periods of time," said Teri Shanahan, IP's VP of sustainability. "Engaging with our critics is an important part of our process of continuous improvement. We look forward to working with Dogwood, because it's clear that, although we approach it from markedly different perspectives, they are as passionate about the forests as we are."
"IP's leadership on FSC certification and its recently-announced commitment to fund conservation in regions that have long been a priority for us opened the door for transitioning our formerly adversarial relationship to one of collaboration," said Danna Smith, executive director of Dogwood Alliance. "We are pleased to work with IP on these initiatives, that, when combined with our collaborative effort, set a leadership standard within the southern forest industry."
The collaboration will kick off with a 2013 pilot project to map forests around IP's mill in Riegelwood, N.C. (near Wilmington). After the pilot project, IP and Dogwood Alliance will evaluate the framework used and modify it as necessary with the intent of applying it across additional IP southeastern operations.
This affiliation represents an unprecedented relationship between Dogwood and IP. Dogwood Alliance has been critical of IP in the past, though it has increasingly worked with industry leaders to find innovative business solutions that protect southern forests.
Until this week, IP has not been able to reach agreement with Dogwood Alliance although the company's focus on sustainable forestry practices has led to collaborations with a broad set of stakeholders in the conservation community.
##SHARELINKS##
|
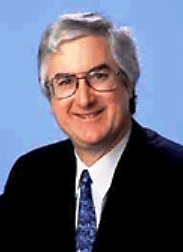 George Weyerhaeuser Jr., a former senior executive of Weyerhaeuser Co., co-founded by his great-great grandfather, died of a heart attack this week at the age of 59, the News Tribune of Tacoma, Wash., USA, reported. Weyerhaeuser suffered a heart attack this past Sunday night while on his boat on Commencement Bay, according the newspaper report.
Weyerhaeuser, whose great-great grandfather, Frederick Weyerhaeuser, co-founded Weyerhaeuser Co., retired from the Federal Way, Wash.-based firm in 2008 and was serving as president of the Thea Foss Waterway Development Authority.
In his 30-year career at Weyerhaeuser Co., Weyerhaeuser served at various times as VP for containerboard, VP of manufacturing for the pulp and paper business, president and CEO of Weyerhaeuser Canada, and SVP of technology, procurement, and transportation.
Weyerhaeuser is survived by his wife, Kathy McGoldrick, and by sons Walker and Corydon, and by his father, George Weyerhaeuser, and his mother Wendy. He also is survived by four sisters and a brother.
##SHARELINKS##
|
Kimberly-Clark Corp., Dallas, Texas, USA, has been ranked No. 18 among the "100 Best Corporate Citizens," the company's fifth straight year in the top 20 on the list published this past week in the current issue of Corporate Responsibility Magazine.
The annual listing credited K-C's strengths in categories such as corporate governance, environment, and human rights. The list ranks K-C as a leader among other consumer packaged-goods companies in the top 100. The complete list is available online.
"For us at Kimberly-Clark, good citizenship means that we are serving our communities by providing essentials for a better life," said Gail Ciccione, VP of sustainability and continuous improvement for K-C. "Citizenship also means that we are achieving our business goals while imparting a culture of environmental stewardship. Consistently winning recognitions like this is only possible when many thousands of K-C employees worldwide do their work while maintaining an underlying focus on sustainability and citizenship."
With this designation, K-C continues a well-established track record as a responsible corporate citizen. K-C recently repeated its designation by Ethisphere Institute as one of the "World's Most Ethical Companies," among multiple other global distinctions received in the past year.
CR Magazine compiles its annual ranking of Best Corporate Citizens based on 298 factors for each company on the Russell 1000 index. Data are gathered from publicly available resources for seven key criteria: climate change, environment, employee relations, finance, governance, human rights, and philanthropy.
##SHARELINKS##
|
Session T1 at PaperCon's Tissue360° Forum, April 29 - May 1, 2013, in Atlanta, Ga., USA, will define, dissect, and analyze the global tissue and hygienic products market, setting the stage for seven intensive technology sessions that follow over the next three days—chemistry, fiber, advanced production systems, water and energy, controls and measurement, yankee dryer, and converting developments. Sponsored by TAPPI's newest print publication, Tissue360° magazine, these eight Tissue Forum sessions provide the most comprehensive exploration of emerging market drivers and technology developments available anywhere for understanding and meeting challenges of the rapidly evolving tissue and hygienic products industry.
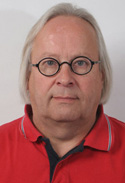 Leading off Session T1, Esko Uutela of RISI (photo left) examines the tissue, towel, and personal hygiene products arena in North America and worldwide in term of current and projected capacities as well as new and emerging trends that will shape markets into the foreseeable future. Lindsay Gervais of Pöyry Management Consulting (photo right) then looks specifically at the critical fiber side of tissue and hygiene products, assessing the decline of recycled fiber quality and availability and the outlook for virgin and other fiber sources, as well as nonwovens resources that will determine the future direction of these product markets.
Uutela notes that the tissue business is booming today after recovering quickly and strongly from the 2009 recession. Globally, tissue consumption approached 32 million metric tpy in 2012 and for the first time exceeded the volume of newsprint. RISI expects the long-term growth to continue at an annual average rate of 4% or slightly above. During the past 10 years, China has been the prime motor for growth in the global paper and board industry, and so also in the tissue business, followed by Latin America, which also has shown strong expansion. In the next 10 years, large emerging markets such as Brazil, Turkey, and Russia will increasingly offer tissue companies new business opportunities.
The North American tissue market is experiencing a new investment boom this year, expected to continue through 2014, Uutela continues. This time the main driver for new projects seems to be the need for ultra and premium grade tissue, partly as a reflection of major retailers' target to upgrade their private label offerings closer to the main brands in quality, although there is a clear trend toward higher quality in the away from home sector as well. "Market growth has flattened, particularly in terms of weight as the product light-weighting trend continues. Competition does not show any signs of alleviation, and it's amazing to see how a growing number of small, independent converters have been able to forge ahead based on their niche products, flexible service, and sub-contracting orders from the big players," Uutela says.
Gervias adds that amidst a backdrop of falling demand for printing and writing paper in mature markets, a key concern for several tissue manufacturers is the availability, quality, and cost of recovered paper. "But at what point does recycled paper become uneconomical compared with other fiber options?" she asks.
In her presentation, Gervais explores the combination of falling yields and rising costs of SOP (sorted office paper) to determine a breakeven cost of manufacture when compared with a virgin fiber furnish. She examines the impacts of this key issue and takes a look at other fiber resources and their future role in tissue manufacturing.
More information about PaperCon 2013 is available online, including online registration. Additional information about the Tissue360° Forum program is also available online
##SHARELINKS##
|
The TAPPI Yankee Dryer Safety and Reliability (YDS&R) Committee will hold its Spring Meeting May 1-2 at the Hyatt Regency in Downtown Atlanta, Ga., USA, during PaperCon 2013. Members and friends are cordially invited to attend this meeting, which is scheduled as follows:
- Work Group Meetings, Wednesday, May 1, Noon – 4:00 p.m.
- Full Committee Meeting, Thursday, May 2, 8:00 a.m. – Noon.
Attendees are asked to register online for these meetings so that we may get an accurate headcount. You may attend one time as a visitor, and thereafter, you must join TAPPI to participate in the committee. If your membership has lapsed, you may renew using the online registration link as well.
More information about the YDS&R committee also is available online, as is Hotel information.
Please email Scott Springmier with any questions, or contact him by phone at +1 404-375-0464.
We look forward to seeing you in Atlanta
##SHARELINKS##
|
The TAPPI Tissue Properties & Manufacturing Course will be held on April 27-28, 2013, in Atlanta, Ga., USA, and co-located with 2013 PaperCon and the Tissue Forum. Both the Tissue Forum and Tissue Properties & Manufacturing Course are being sponsored by TAPPI's Tissue360° magazine.
This is a great opportunity to get the most out of the PaperCon experience. The Tissue Properties & Manufacturing course is designed for those who desire an introductory-to-intermediate level, comprehensive, and structured course on tissue properties, and the effect of manufacturing. This course precedes the Tissue 360° Tissue Forum at PaperCon, and is an excellent educational compliment to these technical sessions.
The course will be particularly helpful to non-technical professionals, technical process engineers, operators, suppliers, converters, and marketers with 0-5 years of experience in tissue manufacturing.
More information about the Tissue Properties & Manufacturing Course is available online.
##SHARELINKS##
|
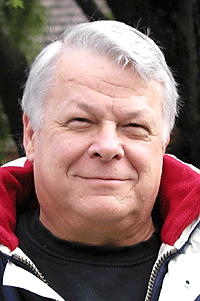 The keynote speaker for the OpEx Maintenance and Reliability Workshop at TAPPI PaperCon 2013 in Atlanta, Ga., USA, on April 30, will be John Yolton with SKF, a highly respected paper industry reliability expert who will explore "The Continuing Journey to Asset Reliability Improvement." As Yolton notes, "with the NAM pulp and paper market contracting, only the most reliable equipment can provide a competitive advantage. Data demonstrates that there is clearly a return on investment for those ‘best' within the pool of competitors."
What do the "best" do to achieve this extra measure of competitiveness? Yolton's presentation will identify and discuss the primary issues associated with the Top 3%, e.g., the "best" and the "rest." "It might surprise you to find that ‘soft' issues play an important and vital role in the transformation and journey from the ‘rest' to the ‘best,'" Yolton says. His presentation includes a case study analysis at Daishowa-Marubeni International's 500,000 metric tpy chemical pulp mill in Canada.
The opening keynote session also includes presentations by Bill Wick of American Industrial Metrology on "A Holistic Approach to Paper Machine Alignment" and Dave Cutnaw of SKF on "Maintenance and Asset Reliability Strategies—Developing a Foundation for Success."
More information about PaperCon 2013 and the OpEx Maintenance and Reliability Workshop, including registration procedures, is available online. Also available online is the 2013 OpEx Workshop program
##SHARELINKS##
|
Market Roundup
U.S. sales of corrugated packaging board picked up in the first quarter of 2013 but are growing slowly, reflecting moderate and inconsistent demand for the consumer products that they contain, industry executives said in a report by MNI, New York, N.Y., USA. Corrugated producers in Texas, Wisconsin, and Philadelphia, Pa., in the MNI report said that orders are growing steadily, particularly from the food and beverage and pharmaceuticals industries, and that demand appears to be stronger than it was in the fourth quarter of 2012.
But one production measure of containerboard—the grades used for making corrugated—suggested volatile demand and uncertainty about the strength of the economic recovery, MNI pointed out.
"I would not say that we are seeing a strong upturn in orders," Jana Harris, president of Harris Packaging Corp., a maker of corrugated and folding-carton packaging in Fort Worth, Texas, was quoted in the MNI report. "We are not convinced that the economic recovery is well established. It is improving but not at a rate that would make us feel comfortable enough to say that it has turned around."
By early April, orders year-to-date were 4% greater than a year earlier, while the dollar value of sales was higher because of a recent price increase, Harris added. The company's biggest orders have come from the food and pharmaceutical industries while there has been a loss from manufacturers of durable goods such as technology and furniture, who have moved their operations overseas.
Most of the company's growth has come from acquiring new "brown box" customers and from more opportunities in retail display, rather than from existing customers, Harris noted. Meanwhile, the 100-employee company is losing some existing customers to lower-priced competitors. "Accounts that we have provided quality product and service and built a strong relationship with over many years are now going out for national bids," Harris said.
According to Scoring Boxes, a newsletter for the packaging industry, shipments of corrugated boxes rose an annual 0.7% in February, the latest month for which data are available. Year-to-date, MNI reported, shipments rose 0.4%, a rate that the publication said reflects moderate growth in the non-durable goods sector. "This steady growth rate is consistent with the slow growth in output of the nation's nondurable goods manufacturing operations which have increased output by 1.2% during the first two months of 2013," the report said.
But there are signs of volatility in demand for packaging, according to the report. It said the amount of containerboard that is not consumed by U.S. corrugators, exported, or held in inventories, was 95% higher in February than the seven-year average for that month. That followed volatile output in the "unidentified" containerboard production in January and December, suggesting customers still lack the confidence to place large orders on a sustained basis, the report said.
Mill inventories of containerboard reflect the same erratic pattern, increasing by 25% in February after declining by a similar margin in January.
At MarquipWardUnited, a Phillips, Wis.-based maker of machinery for the corrugated and folding carton industries, requests for quotes from packaging manufacturers rose 39% in March from February, according to Trish Kempkes, the company's director of global communications. Kempkes said the requests for quotes are likely a response to two new products that are being offered to meet manufacturers' demand for higher energy-efficiency.
In Fort Atkinson, Wis., overall sales at Wisconsin Packaging Corp. are flat so far this year despite increases of up to 12% to the food industry and around 5% to the furniture industry, said President Fred Negus. Orders from the manufacturing industry are strengthening modestly, he said. Still, that's an improvement from the fourth quarter of last year for the company that employs around 65 people and produced some 200 million square feet of packaging material in 2012, he said.
In Hatboro, Pa., a suburb of Philadelphia, Acme Corrugated Box Co. is seeing good growth in orders, continuing the trend of the last six or seven months, said President Bob Cohen in the MNI report.
##SHARELINKS##
|
According to AF&PA's (Washington, D.C., USA) recently released 53rd Annual Survey of Paper, Paperboard, and Pulp Capacity, U.S. paper and paperboard capacity declined 1.6% in 2012, but will hold essentially stable over the next three years (2013 through 2015). Paper and paperboard capacity is slated to decline 0.4% in 2013 but then rise 0.6% in 2014 and 0.2% in 2015. For the entire three-year projection period, paper and paperboard capacity is expected to rise 0.4% at an average annual rate of 0.1%.
Tissue paper and containerboard grades are slated to add capacity during the next three years, while capacities for newsprint and printing and writing paper grades are expected to decline. The survey findings indicate that boxboard capacity will hold essentially stable.
The survey reports U.S. industry capacity data for 2012 through 2015 for all major grades of paper, paperboard, and pulp, based on a comprehensive survey of all U.S. pulp and paper mills. Survey respondents represent about 90% of the U.S industry capacity.
##SHARELINKS##
|
Pulp & Paper
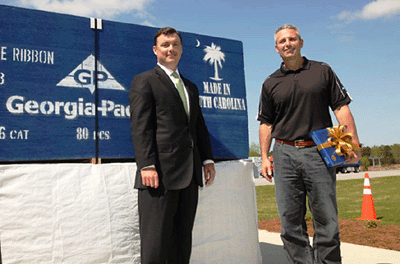 South Carolina government officials joined Georgia-Pacific, Atlanta, Ga., USA, leaders this past week to celebrate the startup of production at the company's oriented strand board (OSB) plant at Clarendon County, S.C., and the 130 new jobs these operations create. Jim Hannan, CEO and president of G-P (on the left in photo), and Bryan Stirling, chief of staff to Governor Nikki Haley, addressed a group of mill employees and officials from state, county, and city government.
"South Carolina is a major part of our focus on growing our building products business," said Hannan. "The investment in our Clarendon County facility makes us well-positioned to grow with our customers as the housing market continues its slow recovery."
Gov. Haley said in a statement that "creating a strong business environment in the state, and as a result a skilled workforce, is a priority for me as governor. The economic ties to manufacturing are a key component in this effort, and partnerships between the State of South Carolina and industry like Georgia-Pacific help South Carolina stay competitive."
The mill was part of a $400 million acquisition of Grant Forest Products in 2010 that also included a plant in Allendale County, S.C., and another plant in Englehart, Ont., Canada. G-P spent an additional $30 million to complete construction on the Clarendon facility in 2011, and in 2012 announced plans to start up operations this year.
G-P, which is a wholly-owned subsidiary of Koch Industries, headquartered in Wichita, Kan., has seven manufacturing facilities in South Carolina directly employing approximately 1,400 people. These jobs, combined with those created by other Koch companies in the state, employ more than 2,000 people directly and support nearly 7,500 South Carolina jobs overall with total compensation of $384 million annually.
##SHARELINKS##
|
White Martins, the Brazil-based subsidiary of Praxair Inc, has started up a new air separation plant in the state of Mato Grosso, in Brazil's Midwest region. As part of a long-term contract, Praxair will supply Eldorado Celulose e Papel's single-line pulp mill, which will be the largest in the world.
The new air separation unit will have the capacity to produce 220 metric tpd of oxygen, nitrogen, and argon. Oxygen is a critical component in Eldorado's manufacturing process. Oxygen delignification, used in the pulp bleaching process, reduces active chlorine requirements, providing significant operating cost advantages and environmental benefits. The plant will also supply local merchant liquid customers in the Brazilian Midwest and in the neighboring state of Sao Paulo in markets such as petrochemicals, metals, and healthcare.
"This is Praxair's fifth plant in this region, which further enhances our production and distribution capabilities," said Domingos Bulus, president of White Martins. "We look forward to playing an important role in Eldorado's ongoing growth and contributing to the industrial and economic development of this region."
Eldorado Brasil is a Brazilian company that officially opened in December 2012 and is the world's largest single line pulp mill. The company whose main shareholder is J&F has the capacity to produce 1.5 million metric tpy of bleached eucalyptus pulp. Production is mostly targeted to export markets for paper producers including North America, Europe, and Asia, as well as to Brazilian customers.
##SHARELINKS##
|
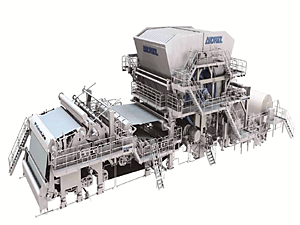 Shandong Sun Paper, China, has ordered from Andritz, Graz, Austria, two tissue machines with steel yankees for the production of high quality facial and toilet paper. The machines will be installed at the Yanzhou mill, Shandong province.
The first ANDRITZ machine is scheduled to start up in May 2014 and the second at the beginning of 2015. With these orders, Shandong Sun Paper is entering the tissue business.
The new PrimeLineTM W8 tissue machines are designed for speeds of 2,000 m/min, with a paper width of 5.62 meters. Each machine will be equipped with a PrimeFlow two-layer headbox including dilution control, a PrimeDry Steel Yankee with a diameter of 18 ft., and a PrimeDry ReEvaporation HeatRecovery system. The scope of supply also includes a stock preparation plant and the automation system with DCS (distributed control system) and QCS (quality control system).
According to Ying Guangdong, VP and chief engineer of Shandong Sun Paper, this investment is part of an expansion program to become one of the five largest tissue producers in China within the next 10 years.
##SHARELINKS##
|
Wepa Lucca, Italy, a member of the Germany-based Wepa Group, has sold its Piano della Rocca tissue mill in Italy to Italian tissue company Roto-cart, according to a report this week by EUWID Pulp & Paper, Germany. Closing of the deal is expected by the end of this month (April 2013). Financial details were not disclosed.
Piano della Rocca is one of the two tissue mills in the Lucca province that had been put on sale in 2012 as a part of Wepa's capacity restructuring programme in Italy. Piano della Rocca runs one machine with an installed capacity of 29,000 metric tpy of tissue and employs 33 people. The Fabbriche di Vallico tissue mill has a capacity of 18,000 metric tpy and is still up for sale. It has been idled since the middle of last year, with some 25 employees temporarily laid off.
Italian trade unions Fistel-Cisl and Slc-Cgil, EUWID reports, are accusing Wepa of not respecting terms and conditions of the reorganisation plan negotiated in late 2011. In addition to the 46 lay-offs agreed upon in 2011, the company recently announced plans to cut 70 more jobs, a spokesperson for Fistel-Cisl said.
Furthermore, a complaint against the company has been filed with the Labour Court in Lucca, as Wepa was undermining union rights and freedoms, trade unions reported. Wepa said the company was implementing the restructuring plan signed in 2011, but declined to comment further on what it called an ongoing issue, according to EUWID.
##SHARELINKS##
|
Containerboard/Packaging
Ahlstrom, Helsinki, Finland, reports that it has completed the earlier announced EUR 7 million investments at its Stenay plant in France. With the investment, the plant successfully expanded its product portfolio of one-side coated papers for metalized labels and flexible packaging.
The grades produced on Stenay's PM 3 now span from 50 to 160 gsm. These coated papers can be used for metalized beer labels and flexible packaging applications such as biscuits, sweets, coffee bags, pharmacy, pet food bag outer liners, tea envelopes, tobacco pouches, and as bundle wraps for yoghurt pots.
"By lowering the weight of a paper used for metalized labels, flexible packaging, and other graphics and industrial applications, Ahlstrom responds to the need for lighter papers to reduce the weight of packaging and labels and consequently lower their environmental footprint," said Daniele Borlatto, EVP, Label and Processing.
With the investment, Ahlstrom offers additional benefits to its customers, such as improved performance during the converting process. The Stenay plant is part of Ahlstrom's Label and Processing Business Area, which operates a total of six production sites in France, Germany, Italy, and Brazil.
##SHARELINKS##
|
Kartonsan Karton Sanayi ve Ticaret A.S., Izmit, Turkey, will upgrade its No. 2 board machine and related stock preparation systems, thus increasing duplex and triplex board production from 100,000 to 160,000 metric tpy. The upgrade will be handled by Andritz, Graz, Austria. Startup is scheduled for the second quarter of 2014.
Andritz's scope of supply includes:
- Upgrade of the board machine (design speed of 450 m/min at a paper width at the reel of 3,650 mm), including a PrimeFlow SW headbox with dilution control, rebuild of the fourdrinier wire and press sections with a PrimePress X shoe press, a new hood and air system, and rebuild of the pre- and after-dryer, hard calendar, and coating sections
- Rebuild of the deinking line for white ledger (capacity: 140 metric tpd)
- Upgrade of the backlayer line with deinking flotation unit and thickener disc filter for an additional white ledger capacity of 85 metric tpd
- Rebuild of the existing old corrugated containers/mixed waste line with a capacity of 380 metric tpd
- Broke pulper adjustment and new broke thickener
- Three primary and two secondary screens for the four layer approach system and a dilution water screen
- Engineering, supervision, commissioning, startup, training, and spare and wear part packages for the entire equipment supply.
##SHARELINKS##
|
MeadWestvaco Corp. (MWV), Richmond, Va., USA, this week was named recipient of Walmart's "Responsibility Award for Total Health and Wellness," recognizing MWV's development of the Shellpak® Renew medication adherence solution. Shellpak Renew was launched in June 2012 to provide an improved and more sustainable medication adherence package for prescription medicines.
Shellpak Renew was developed based on feedback from pharmacists and patients. The outer carton is made of MWV's Natralock®, an environmentally-friendly, paperboard-based solution that maximizes the use of recyclable materials and is tear-resistant for a high level of child resistance. The new sustainable and easy-to-use Shellpak Renew is 40% smaller and 30% lighter than the original Shellpak, and eliminates the use of plastic. This enhances the sustainability profile, minimizes pharmacy shelf space, and improves convenience for patients. To improve adherence, Shellpak Renew includes an integrated calendar for patients to track their doses of medication.
"The evolution of Shellpak Renew exemplifies our research-based approach to innovation, working closely with customers and patients to directly address their needs," said Bruce Thomas, president of MWV Healthcare. "With Shellpak Renew, we combine three key benefits: an adherence-enhancing medication package that is child resistant and also senior friendly, and that maximizes the use of recyclable material. We are honored to be the recipient of the Responsibility Award and excited about our work with Walmart to continue making adherence-enhancing packaging available to patients."
##SHARELINKS##
|
Nonwovens
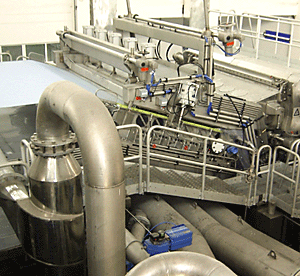 In the future, paper machine manufacturer Voith Paper, Germany, and nonwovens expert Trützschler, Germany, will work together to offer a complete production line for the manufacturing of wet laid and hydroentangled nonwovens. The aim of the cooperation is the joint development and marketing of innovative and economical production equipment.
"We are certain that this partnership will enable us to offer convincing machine concepts," says Marc Wolpers, sales director of Trützschler Nonwovens & Man-Made Fibers. "By providing common solutions, we can meet the market requirements in a much better and faster way than we ever could by acting independently".
With its HydroFormer (photo), Voith Paper contributes the core component to the cooperation. It has been specifically optimized for the formation of wet-laid nonwovens and, with more than 70 successful installations, gained worldwide acceptance. Due to its expertise, Voith also offers support regarding stock and water systems, press concepts, fabrics, and calenders.
In the bonding area, the know-how from Trützschler is applied. Web bonding is performed downstream of the former with the help of the well-known AquaJet, a leading solution in the field of hydroentanglement. In this field, Trützschler Nonwovens can draw on extensive experience from more than 100 projects.
As expert for complete production lines for the nonwovens industry, Trützschler is also responsible for drying and winding within the framework of the joint project.
"This cooperation allows us to offer our customers a complete line ranging from wet laying, bonding, to drying and winding," adds Dr. Klaus Afflerbach, responsible for special machines within Voith Paper. "The combination of two wet processes in the form of HydroFormer and AquaJet results in a high-quality web that is of interest to manufacturers of cleaning cloths throughout the world."
Trützschler, founded in 1888, is one of the world's leading textile machinery manufacturers with more than 2,800 employees. The traditional family-owned company specializes in machines, installations, and accessories for the spinning preparation, nonwovens, and man-made fiber industry. Trützschler Nonwovens is part of Trützschler Nonwovens & Man-Made Fibers and was created through the merger of Fleissner, Erko, and Bastian companies.
##SHARELINKS##
|
New Products
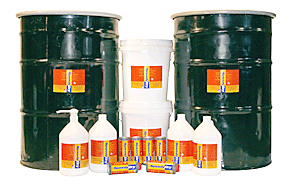 Printers have been using a high performance ink drying additive by SpeedyDry –Genesis Inc., Burlington,N.C., USA, since 2005 to cut ink drying time by 75% or more without negatively affecting print quality or ink properties such as tone reproduction and tack, while also improving rub resistance. Tests conducted by the Graphics Arts Technical Foundation and elsewhere showing dramatic decreases in ink drying time have now been augmented by a series of more recent tests showing that SpeedyDry also helps prevent migration of mineral oils and other potential printing ink contaminants, allowing various types of packaging board to be used for food packaging without special barrier coatings or treatments.
Tightening regulations in North America, Europe, and elsewhere in the world during the past several years have spawned new barrier coating technologies that add significant costs to paperboards used for food packaging. Some of these coating also interfere with normal ink drying times, further raising costs and slowing print delivery schedules, as well as creating print quality problems. By accelerating cross linking reactions that normally occur in ink during drying, SpeedyDry dramatically steps up ink set time and thus reduces the opportunity for penetration of mineral oils through the board, possibly contaminating packaged foodstuffs.
SpeedyDry, which works well with almost all types of ink, attaches itself to the pigment and varnishes in the ink and then attaches to the substrate. Its properties create a chemical reaction that allows drying from top to bottom and side to side at the same time. It not only speeds drying times up to 75% in some applications, it also enhances ink gloss and increases adhesion of the ink on most hard to print substrates, including various plastics, while increasing rub resistance and eliminating chalking.
A series of migration tests conducted over the past several years show that results are acceptable with SpeedyDry at up to 20% of the ink mixture using various food packaging substrates including polyboard and recycled SBS (solid bleached sulfate) boards, as well as most recently (this past February) using Metsä Board's 240 gram Simcote coated folding boxboard.
The polyboard and SBS tests for fatty acid migration were conducted by ink supplier INX International at its R&D labs in Chicago. The inks were run under normal manufacturing conditions by a major packaging printer, and the migration testing used the approved fatty foods simulant of 95% ethanol in water at 40oC for 10 days. Gas chromatography testing with several meat and vegetable products then showed that both fatty acids and fatty acid esters remained well below the 6 ppm requirements of most national and international regulations.
The most recent testing by ISEGA in Germany (which also conducted earlier tests on the SpeedyDry product itself, showing it may be used safely as an ink dryer catalyst with food packaging) evaluated for hard water (cobalt and manganese) migration as well as mineral oil migration. ISEGA is one of only a few labs in the world that can do hard water (heavy metals) migration testing. The mineral oil testing included both the MOSH (paraffinic, naphthenic mineral oil hydrocarbons) and MOAH (aromatic mineral oil hydrocarbons) types.
In regard to cobalt, gas chromatography results showed that migration with all samples was lower than 0.05 mg/kg of foodstuff, and that the transfer onto dry foodstuffs would be significantly lower. Manganese in all samples ranged from 0.75 – 0.25 mg/kg (level of non-detectable) of foodstuff. The migration of mineral oils in all samples tested was well below the draft German regulation (No. 1935/2004, art. 3) of 0.6 mg/kg MOSH and 0.15 mg/kg MOAH.
The ISEGA tests show that the tested board grades printed using up to 20% SpeedyDry in the ink are well within current German regulations (which meet or are more stringent than most other country regulations for mineral oil migration) and may be used for food packaging. Further, ISEGA notes that food packaging materials printed with SpeedyDry may come into direct contact with dry, non-fatty foodstuffs on their non-printed sides. Contact with the non-lacquered side with fatty foodstuffs is also allowed.
More information about Speedy Dry is available online or by calling 1-336-261-0170.
##SHARELINKS##
|
Under the brand name XelorexTM, BASF, Ludwigshafen, Germany, has launched a solution for the production of paper and board. The new BASF brand of multifunctional 4-in-1 wet-end chemistry responds to the diverse challenges the paper industry is facing these days. As the company notes, whether it involves a reduction of complexity in production, a higher stability of operations, a boost for productivity, or an improved cost-efficiency, "a broad range of needs are addressed by applying only a single product of the Xelorex product family."
Dr. Uwe Liebelt, president of BASF's Paper Chemicals Division, says that "we want to serve the paper industry with solutions, not just chemicals. With Xelorex, we offer an innovative chemistry that significantly improves various performance parameters in papermaking while reducing the total cost of operation. For our customers this represents a real competitive advantage."
Xelorex reduces complexity in the wet-end through its 4-in-1 functionality. It enables papermakers to achieve and improve the effects of retention, drainage, fixation, and strength with just one product of the product family. Further, it has the potential of replacing other wet-end chemicals up to an extent of 100%. Application of Xelorex also leads to proven enhancements of a variety of dry strength parameters. This can mean a 10%–30% improvement in this area, depending on the basis weight and the paper grade, BASF explains.
Applying Xelorex, customers also gain clear improvements in stability of operations, BASF continues. The outstanding improvement of the initial wet web strength (IWWS) reduces the number of breaks and this way improves productivity. In addition, Xelorex provides enhancements of a variety of dry strength parameters, which is particularly important in the production of packaging paper and board.
Manufacturers of both packaging and graphical papers benefit from the additional productivity increases that Xelorex yields, the company says. The improved IWWS, less stickies, and clean water circuits lead to a higher efficiency due to less downtime. The reduced draw also permits a mill to run machines at significantly increased speeds, another booster of productivity, if needed.
Finally, BASF points out, Xelorex means an improved cost-efficiency for papermakers as it targets a variety of cost drivers in the papermaking process. Through its powerful dry strength performance, expensive long fibers can be replaced with lower-cost short fibers. It also enables the increased use of recycled fibers. Additionally, Xelorex supports an increased filler loading, as it leads to a better integration of filler particles into the paper web. The increased filler loading means a cheaper way of replacing fiber material and improving printing properties and also helps to save steam since less fiber needs to be dried. Overall, specific fixed costs are diluted without compromising on the quality of paper and board.
Introduction of the brand and the new Xelorex portfolio starts in Europe and will be gradually extended to the regions of Asia Pacific and North and South America.
##SHARELINKS##
|
Fox River Fiber, DePere, Wis., USA, has introduced Fox Pure brand of FDA compliant pulp for environmentally conscious companies. Fox River Fiber is one of the nation's only suppliers of FDA-grade recycled pulp.
"The cleanliness of our Fox Pure brand of pulp makes it food-safe and appropriate for applications such as cup stock and other food packaging," said Ted Heimerman, business manager at Fox River Fiber. "As more consumers make environmental responsibility part of their buying decision, food and beverage producers are demanding access to recycled pulp that meets the FDA's food safety requirements. Fox River Fiber's Fox Pure is becoming the trusted brand in the marketplace."
Fox River Fiber also uses 100% of the byproducts generated by its proprietary deinking process for beneficial purposes such as animal bedding, and lawn and garden care products. Fox River Fiber is a privately owned company that develops and uses leading-edge technology to provide customers with high quality deinked pulp.
##SHARELINKS##
|
People
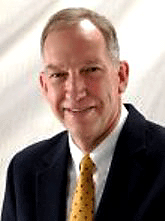 Port Townsend Paper Corp., Port Townsend, Wash., USA, has named Robert P. Hagan, long time member of PIMA and current PIMA executive council chair, its new president, effective May 1. Hagan, a 35-year veteran of the paper and packaging industry, will assume all financial, operational, and external communications responsibilities, according to Dale Stahl, the company's executive chairman to whom Hagan will report.
Roger Loney, who served as president since 2008, announced his resignation as president last month to return to the East Coast, and is remaining in Port Townsend to help Hagan with a "quick and seamless transition of company leadership," Stahl said.
Hagan has been working as VP, operations at Zilkha Biomass Energy/Fuels in Houston, Texas, for the past year. He has managed six different mills during his 35-year career, including RockTenn's Solvay mill in New York, the Hodge mill in Louisiana, and the Stevenson Mill in Alabama. He holds a B.S. degree in pulp and paper technology from the University of Washington, and a M.S. degree from the Institute of Paper Science and Technology in Atlanta, Ga.
Port Townsend Paper is owned by Port Townsend Holdings, which is owned and operated by GoldenTree Asset Management, a New York–based equity investment firm.
##SHARELINKS##
|
Xerium, Raleigh, N.C., USA, this week announced that Mike Bly has been hired to fill its newly created position of EVP of Global Human Resources. Bly will be responsible for all of Xerium's human resources—wage plans, benefit plans, insurance, union contracts, incentive plans, personal goals and objectives, human resource management systems, and career planning.
According to President and CEO Harold Bevis, "Xerium has two objectives with this move. First, we want to instill stronger pay-for-performance regimens across all people and processes. Xerium has begun a multi-year journey to create an enterprise that sets and meets its commitments to shareholders, customers, and employees. The markets that Xerium serves have fundamentally changed in the past few years and we must change our human resource approaches to compete and win in this environment.
"Second, we need to establish more contemporary regimens within the human resource function itself. Many of our current habits are outdated and need to be brought up to contemporary standards. We have a big opportunity to leverage our scale better, simplify our network of activities, and organize and group common areas of work. This organizational move will enable that to happen naturally. All human resource personnel will report to Mike with dotted line reporting to the regional presidents."
Bly has 28 years of experience leading human resource and manufacturing functions, quality, supply chain, lean manufacturing, materials optimization and substitution, standardized manufacturing systems, per unit cost reduction, customer service, and M&A operational integrations. He formerly was VP of human resources for Bevis at Pliant Corp., and most recently was VP of human resources at Berry Plastics (acquired Pliant Corp. in 2009), where he had responsibility for the Flexible Packaging Division's human resource function.
##SHARELINKS##
|
Susanna Ottila was elected a member of Metsä Tissue's (Finland) board of directors at the company's recent Annual General Meeting of 2013. Ottila works as a marketing director in the frozen pastry division of a Finnish bakery company, VAASAN Oy.
The following members were also re-elected to the board of directors: Kari Jordan, Jozef Antosik, Hannu Anttila, Martti Asunta, Arto Hiltunen, Juhani Järvi, and Tuomo Lähdesmäki. Metsä Tissue's board of directors consists of eight members.
##SHARELINKS##
|
TAPPI News
2013 NCSU Alumni and Friends Golf Tournament
Register Today!
Date: Friday, April 26, 2013
Location: NC State's Lonnie Poole Golf Course
Format: Four Person Superball
Cost: $100 per player
(Fee includes golf cart, range balls, lunch, refreshments, tee gift and a PGA Golf Management student as a personal forecaddie for your group)
AM Round Times
Check-in - 7am; Shotgun Start - 8 a.m
.PM Round Times
Check-in - 12pm; Shotgun Start - 1:30 p.m.
Proceeds support scholarships and other enrichment activities for students.
Sponsored by NC State Natural Resources Foundation Inc.
##SHARELINKS##
|
It's time to tighten up plans to attend the Total Pump Training course being held at the TAPPI Training Facility in metro Atlanta, Ga., USA, for three days, May 1-3, 2013. This is an invaluable course for anyone in the pump and piping system industries.
The Total Pump Training course offers a comprehensive look at common pump applications and is taught by a recognized industry expert who can answer any questions about how system changes can alter pump operation and the best way to respond to system modifications.
Learn the important fundamentals of pumps, about positive displacement pumps, hydraulics selection and curves, advanced hydraulics considerations, sealing systems, installation, troubleshooting, repair, and more.
Earn 2.0 CEUs or 20 Professional Development hours, and carry back with you two indispensable manuals and even greater confidence.
Register online before seats fill.
##SHARELINKS##
|
Early Bird Registration rates for this course have been extended to May 1. Register today to save over $650 off the normal registration rate. Don't miss the best educational and learning opportunity of the year - the 2013 TAPPI Corrugated Press Hands-on Maintenance Workshop, May 7-8, at the Global Equipment USA Warehouse in Skokie, Ill., USA.
This unique course offers both classroom and indispensable hands-on maintenance training for corrugated industry plant managers and supervisors, engineers, maintenance teams, and machine operators.
Over the course of two days, you will learn from our team of instructors led by course chair Tom Pearce, Pearce Corrugated Consulting, and actively participate in more than eight hours of hands-on training.
Students will acquire practical knowledge and experience while conducting maintenance procedures on the facility floor, and interact with real-world machinery. You will be able to view first-hand the solutions to common problems and techniques to improve quality, efficiency, and reduce future downtime at your plant.
Because the attendance will be limited to the first 18 people that register, you will have ample time to have your individual and specific questions answered by our instructors. You could pour over all of the how-to manuals available and still not retain this level and quality of working knowledge.
After successfully completing this course, participants should be able to:
- Learn to use the basic tools to mechanically audit and troubleshoot a press
- Learn press audit procedures for process centering, better quality products, and increased productivity
- Attendees will understand presentation anilox roll selection, Press "fingerprinting", inks & substrates, quality defects & cause(s).
To learn more about this course and why you should attend, go the course website.
##SHARELINKS##
|
The popular Paper Machine Operations Course is returning to the TAPPI Training Facility on May 21-23, 2013. This course has proven to be one of the best ways to get a good overview of paper mill operations.
Led by Jim Atkins and a team of instructors, this course will provide participants with an improved understanding of the overall paper machine operation. Fundamental understanding of fiber properties and the way the mechanical components function on the paper machine will give the participant the tools needed to more quickly troubleshoot operational problems and improve paper machine operations and product quality.
Go to the course website to learn more and to reserve your space in this upcoming course.
This course in NOT intended for employees of tissue companies. Those interested in learning about tissue may be more interested in the TAPPI Tissue Runnability Course.
##SHARELINKS##
|
For a very short time, TAPPI is offering a 10% discount on your registration to the IDCON Reliability and Maintenance Management course taking place in Raleigh, N.C., USA, on April 22-26. This is a rare opportunity to take this exceptional course for less and to make your operations more productive and efficient. But, act on this offer now to save more than $250 with only a few seats remaining.
For this course, IDCON has taken its FOUR key seminars and combined them into ONE to give your frontline organization the kick-start needed to build and support good work processes.
Stop the wrench from getting into smoother operations. Register to secure your access to these premier training courses with IDCON.
##SHARELINKS##
|
Register by May 11 to save for one of the 25 seats in the popular TAPPI Introduction to Wet End Chemistry course.
Three industry-known instructors are focusing the three-day curriculum, June 11-13, 2013, on innovative wet end chemistry principals and foundations designed to help you reach higher yield, improve confidence in the use of papermaking chemicals, and to better troubleshoot.
View the Workshop Schedule to see the specific topics covered.
This introductory- to intermediate-level course is designed for those in pulp and paper manufacturing facilities with job responsibilities, such as chemical and process engineers, mill superintendents, research and development engineers, technology and chief chemists, R&D vice presidents, process and quality control technicians, and suppliers involved with the wet end processes.
##SHARELINKS##
|
Spring has arrived (hopefully) and the Miami University Student TAPPI will welcome the sun back to Oxford by heading to the Indian Ridge Golf Club for our annual Golf Outing!
This event is the primary fundraiser for the Miami TAPPI chapter and the funds raised help to provide students the opportunity to attend various industry conferences and hold on-campus meetings throughout the year.
Over the past year, Miami's Student TAPPI has done some exciting things. We took a record number of students to North Carolina for the Student Summit and had a great time! Closer to home, we started a student run mentoring program for underclassmen. Upperclassmen are available to answer any questions, from what an internship is like to what classes to take. The future holds opportunities for more students to get involved with the opening of new positions on the executive board.
The annual golf outing is an opportunity for industry professionals and students to meet and interact in a relaxed atmosphere while helping to raise money for the student chapter. Last year's outing was very successful and we are hoping to have even better success this year.
If for whatever reason you are unable to attend but would still like to support Student TAPPI, donations would be greatly appreciated.
If you have sponsored TAPPI in previous years, we thank you greatly. If not, we hope to gain your sponsorship for this event! .
We hope to hear from you soon and see you on the green! Please see the golf outing flyer for details.
For more information please contact Sophia Singer, (513)-604-9006
##SHARELINKS##
|
Fact: the current economy has affected many schools' endowment funds, resulting in decreased support of student scholarships.
But here's the good news: TAPPI has a scholarship to offer. You have a chance to apply for some green (funds to pay tuition, etc.) to fund a satisfying green career. The Cullison scholarship is available for graduate and undergraduate students with an interest in the pulp, paper, converting, and packaging industries.
William L. Cullison Memorial Scholarship.
What this message means to you:
- If you're a student, here is a great way to apply for financial assistance for the 2013-2014 school year.
- The deadline for the Cullison scholarship is May 1, 2013. Mark your calendar now to allow yourself time to create an application that reflects the hard work you've been investing in your career.
- If you are affiliated with a college or university, share this with your students or other staffers who work with students. They will be glad you did!
- If you're in the industry, perhaps you know of students worthy of scholarship assistance with their education, please pass this information along.
##SHARELINKS##
|
Congratulations to Kenneth Kildahl from the University of Minnesota and Aislinn Brackman from the State University of New York – ESF. They are winners of the 2013 Outstanding Student Chapter Member Award. This is perhaps the most prestigious award TAPPI offers to a student chapter member.
Ulrike Tschirner, Faculty Advisor at the University of Minnesota notes that "due to Kenneth's influence, our Student Chapter is the most active we have had in years. He has recruited a large number of new members and initiated several activities such as fundraising through selling coffee mugs or handmade paper, and three large (and successful) grant applications. The grants were a group effort, but he clearly took the lead. Through these efforts we were able to send 12 members to the TAPPI PIMA Student Summit this year.
Aislinn Brackman worked as a senior marketing coordinator at King & King Architects in Syracuse while taking classes part time at Onondaga Community College. A co-worker suggested to her the papermaking program at SUNY-ESF. As she learned more about the program she was excited about the possibility of going into such a specialized field with excellent scholarships and almost guaranteed job placement after graduation. Aislinn is involved in many organizations on campus. She is the outgoing president of the Undergraduate Student Association and treasurer of Papyrus Club, a member of the Empire Forester, ESF's yearbook, and AXS, ESF's honor society. Her scholarly activities allowed her to interact with many members of the campus' administration and faculty and serve as a representative of the PBE program. She also helped make the paper and bioprocess engineering program more visible to the student campus community, many of who have had no idea that Walters Hall even existed.
We are pleased to recognize these two deserving students.
##SHARELINKS##
|
Handbook for Pulp and Paper Technologists (The Smook Book) Third Edition
By Gary A. Smook
This best-selling text provides an introduction to the entire technology of pulp and paper manufacture. The book features 27 chapters covering all aspects of pulping and papermaking. Hundreds of illustrations, charts, and tables help the reader grasp the concepts being presented. The third edition features additional material on secondary fiber recovery and utilization, mechanical pulping, kraft pulping and bleaching, and papermaking.
Handbook for Pulp & Paper Technologists
View the Table of Contents
Product code: 0202SMOOK
Member Price: $56.00
Non-Member Price: $75.00
##SHARELINKS##
|
Don't Miss PaperCon!
In just a few short weeks, the industry will gather for a record-breaking event: PaperCon 2013, April 27-May 1 at the Hyatt Regency Downtown, Atlanta, Ga., USA. More than 1,500 CEOs, mill managers, superintendents, scientists, process engineers, and suppliers are expected and pre-conference registration indicates this will be the largest PaperCon ever.
You still have time to register online. In addition, you can see who is attending.
Don't miss the industry's most important event for 2013. With the multi-track program and co-located events, PaperCon lets you customize your learning and networking experience to best fit your professional needs. Bring back ideas and innovation that will help you be more effective and efficient.
Learn more about the multifaceted PaperCon Program:
See you in Atlanta!
##SHARELINKS##
|
The Introduction to Traditional and Emerging Printing Technology Course will be co-located at the 2013 PaperCon Conference, April 27-29, 2013, in Atlanta, Ga., USA.
This is an introductory course on printing methods and applications, designed for those who need to understand print quality, attend print trials, trouble shoot print problems or are generally new to printing operations. It will be taught by printing experts from TAPPI's Coating and Graphic Arts Division and is an excellent complement to the Coating Program at PaperCon.
As an added bonus, the course will include a tour of Hewlett-Packard's new state-of-the art facility where production laser and inkjet presses will be demonstrated.
Course attendees may also join the Coating and Graphic Arts Opening Session where printing visionary Frank Romano is giving the keynote address. Learn more and register online.
##SHARELINKS##
|
The launch of this successful conference series, produced by the Recycling Today and Smithers Pira, in co-operation with China TAPI, into Asia provides a unique opportunity for companies in North America, Europe, and the rest of the world to meet buyers in the Asian market.
The full program for Paper Recycling Conference Asia launching on May 30-31, 2013, has been announced. Highlights include the opening keynote address - The role of recyclables in China's Economic Resurgence, presented by Professor Wang, Ministry of Environmental Protection, China; An Overview of Macro-Economic Trends Impacting Asia's Recovered Paper Industry from Sally Sun, Deloitte China, and an exclusive One-on-One Interview with Ross Li, Lee & Man.
Save 20% on a ticket to attend by using the code CD20TAP!
Attendees will hear from other key speakers on the agenda, including; Randy Kim, Ekman Recycling; Henri Vermeulen, Smurfit Kappa Group; Niu Qingmin, Jiangsu Paper Association; Yoshimitsu Tanaka, Kaneko, and more, on recovered paper supply, infrastructure, and quality issues and challenges.
"We're excited about launching a Paper Recycling Conference in Asia, particularly as Asian demand continues to represent the major growth area for recovered paper. Since this inaugural event replicates the design of our existing events' list to attract merchants, brokers, suppliers of recovered fiber, and mills from around the globe, it's sure to represent a unique and powerful opportunity for the world's suppliers and consumers of recovered paper to meet," Jim Keefe, EVP and group publisher, Recycling Today, said.
More information about the inaugural Paper Recycling Conference is available online.
##SHARELINKS##
|
Nominations for the major TAPPI 2014 awards are due by August 1, 2013. The awards that may be presented in the upcoming year are:
Gunnar Nicholson Gold Medal Award - The Association's highest technical honor may be presented annually to recognize an individual or individuals for preeminent scientific and engineering achievements of proven commercial benefit to the world's pulp, paper, board, and forest products industries and the other industries that TAPPI serves.
Herman L. Joachim Distinguished Service Award - The Association's highest award for service may be presented annually to recognize leadership and service that have significantly and demonstrably contributed to the advancement of the Association.
Paul W. Magnabosco Outstanding Local Section Member Award - The highest honor for Local Sections may be presented annually to recognize an individual for outstanding leadership and exceptional service to one or more Local Sections, which have resulted in significant and demonstrable benefits to the Local Section members.
TAPPI Fellow - TAPPI Fellows are individuals who have been members of TAPPI for not less than 10 years prior to the nomination, and who have contributed meritorious service to the Association and/or the paper and related industries. Retiring members of the TAPPI Board of Directors become Fellows automatically at the end of their term.
The TAPPI Awards and Honors page has links to these awards that will show the qualifications required and links to the nomination forms that must be completed. You may submit all nomination forms by email to standards@tappi.org, or you may fax them to the attention of the awards department at +1-770-446-6947, or send them by mail to TAPPI, Awards Department, 15 Technology Parkway South, Peachtree Corners, GA 30092, USA.
##SHARELINKS##
|
The TAPPI Centennial Celebration will be a multi-year long series of outreach events and educational offerings showcasing the proud history and promising future of the global pulp, paper, packaging, and related industries. This once-in-a-lifetime event will expand public awareness, foster further connection, and provide outstanding opportunities for collaboration, growth, and investment in our future for all of those involved. Goals for the TAPPI Centennial Celebration are:
- To honor TAPPI's 100 years of connection, education, and advancement as a foundation for the sustainable success of our members, our industries, and the world we share
- To recognize the achievements of those who built our industry and to inspire those who seek to build its future
- To celebrate the contributions and innovations of the global pulp, paper, and packaging industries to human culture, commerce, health, and social advancement
- To sustain the industry and support its growth, vitality, and future through the TAPPI Foundation.
We invite you to be a part of this momentous event. The sooner you join us the more opportunities there are for recognition of your company, its products, and key innovations. Keep in mind that an early commitment allows you to spread your investment over multiple years' budgets.
For more information on sponsorship and volunteer opportunities please contact dbell@tappi.org.
The sponsorship prospectus can be downloaded online.
##SHARELINKS##
|
Member Mike Haas is a strong proponent of education and considers his long association with TAPPI to be a key ingredient in a successful career. He says that TAPPI has always served as a "fantastic learning resource" that has consistently offered him opportunities to hone leadership skills.
But it is not just the opportunity to engage in scientific and scholarly pursuits through TAPPI that Mike says brings great personal and professional rewards. It is the chance to mentor and serve as an advocate for future leaders in the industry, and it is for this reason that he urges fellow professionals to support the pulp and paper schools in their areas. "Get involved, serve as a mentor, create excitement about careers in our industry," he says.
Mike knows personally of what he speaks. As a young student at Miami University, he says he learned first-hand "how rewarding and fun TAPPI membership could be." It was the encouragement of TAPPI members like Fellow Dick Elliott that convinced him joining TAPPI was an important cog in the wheel of professional success. He presented his first TAPPI paper at a pulping conference in Toronto and there was no looking back.
Find out more by reading this month's Member Spotlight.
Spotlight participants are recommended by fellow members and staff. If you would like to nominate a member, just send his or her name (or names) to MemberSpotlight@tappi.org. We will forward a Spotlight Questionnaire to fill out and return.
We look forward to seeing you in the Spotlight!
##SHARELINKS##
|
The packaging industry continually seeks innovative solutions to make their products more sustainable and, at the same time, cost-effective. Further, the Consumer Packaged Goods companies seek to deliver enhanced consumer experience through improved package performance, which may be achieved through improved material properties. Cellulose nanofibers, cast as composite films, provide excellent barrier to oxygen and water vapor.
At TAPPI's upcoming International Conference on Nanotechnology for Renewable Materials this June, researchers from around the world will share their latest findings on the use of cellulose-derived nanomaterials to improve functional properties, targeted for packaging applications. Dr. Tamal Ghosh of PepsiCo's Corporate Research (Beverage Packaging), USA, will host a packaging-focused session on Wednesday, June 26.
The Packaging Session showcases three presentations focused on food and beverage packaging applications. A team of researchers from Switzerland will present their work on composite films with layered silicates and nanofibrillated cellulose. Their results will show a 30-fold lower water vapor permeability and 5-fold higher E-modulus compared with commercial base paper. Researchers from Hungary will discuss their work on improved barrier properties of a poly lactic acid (PLA) bottle coated with an invisible layer of cellulose nanocrystalline-chitosan material. An international team of researchers will discuss the promise of fungal chitin as a nanomaterial for the future.
The 8th Annual International Conference on Nanotechnology for Renewable Materials is scheduled for June 24 -27, 2013, in Stockholm, Sweden, at KTH Royal Institute of Stockholm. New reports will present some exciting advances for both within the pulp and paper industry and beyond. The technical program features cellulose nanomaterials in a variety of applications, including:
- Unique and Thin-Film Composites
- Filler and Coating Applications for Different Paper Grades
- Improved Barrier Properties for Packaging Applications
- Cellulose Nanomaterials as Films and Carriers in Medical Applications
- Nanopaper and Iridescent Colored Cellulose Films.
With more than 80 technical presentations, five keynote presentations, and 50 poster presentations, this year's conference is packed with the latest applications of renewable nanomaterials. Watch for additional updates from TAPPI on how nanotechnology, and cellulose nanomaterials, in particular, can be a transformative technology for the pulp and paper industry.
The 8th Annual International Conference on Nanotechnology for Renewable Materials is hosted by TAPPI's International Nanotechnology Division, which strives to collectively advance the responsible and sustainable production and use of renewable nanomaterials.
More information is available online.
##SHARELINKS##
|
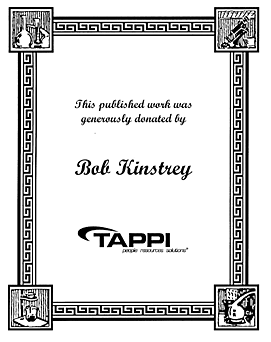
Do you have a history book gathering dust on your shelf? TAPPI's 100th year is coming soon and we are looking for donations to the TAPPI Library. Specifically, we are interested in histories of companies and mills in the paper and packaging industry (both producers and suppliers). Each donated book will have a bookplate in the front cover recognizing the donor. For more information please contact David Bell.
Please send books to:
c\o David Bell
TAPPI
15 Technology Parkway, South
Suite 115
Peachtree Corners, Georgia 30092
##SHARELINKS##
|
The existence of cellulose nanocrystals and cellulose nanofibrils has been known for several decades, yet recent advances in science, particularly in the field of nanotechnology, have revealed that these materials contain unique physical properties, particularly high strength properties. Researchers have been studying how these materials can improve paper properties and will present their latest finding this June 24-27, 2013, in Stockholm, Sweden, at TAPPI's 8th Annual International Conference on Nanotechnology for Renewable Materials at the KTH Royal Institute of Stockholm.
The program for this year's event has been released, and one session will focus on using cellulose nanofibers for improving retention and increasing strength in paper. Researchers from Aalto University in Finland will report on improved flocculation of both precipitated calcium carbonate (PCC) and kaolin with the addition of certain cellulose nanomaterials. Researchers from Papiertechnische Stiftung (PTS) in Heidenau, Germany, will report on the importance of adding fillers, celluloses, and compounding agents in the right order to achieve the best results. Researchers from VTT in Finland will report on ways to increase the strength of paper by using filler particles coated with nanoscale calcium silicate hydrate (CS) structures.
New reports at the conference will present some exciting advances for both within the pulp and paper industry and beyond. The technical program features cellulose nanomaterials in a variety of applications, including:
- Unique and Thin-Film Composites
- Filler and Coating Applications for Different Paper Grades
- Improved Barrier Properties for Packaging Applications
- Cellulose Nanomaterials as Films and Carriers in Medical Applications
- Nanopaper and Iridescent Colored Cellulose Films.
With more than 80 technical presentations, five keynote presentations, and 50 poster presentations, this year's conference is packed with the latest applications of renewable nanomaterials.
Watch for additional updates from TAPPI on how nanotechnology, and cellulose nanomaterials in particular, can be a transformative technology for the pulp and paper industry.
The 8th Annual International Conference on Nanotechnolgy for Renewable Materials is hosted by TAPPI's International Nanotechnology Division, which strives to collectively advance the responsible and sustainable production and use of renewable nanomaterials. More information is available online.
##SHARELINKS##
|
With more than 80 technical presentations and 50 posters, the 2013 TAPPI International Conference on Nanotechnology for Renewable Materials is packed with the latest applications of renewable nanomaterials.
The conference will take place June 24-27, 2013, at the KTH Royal Institute of Technology in Stockholm, Sweden. Register by April 29 for the best rates!
This year's conference features keynote presentations that focus on the steps needed to deploy emerging nanotechnologies into the bioeconomy. Hear from these recognized global leaders:
- "Small World, Large Impact: Driving a Materials Revolution through Nanotechnolgy" Arthur Carty, executive director and research professor in the Department of Chemistry, Waterloo Institute for Nanotechnology, University of Waterloo, special adviser to the president on international science and technology collaboration
- "Towards High-Value Applications of Nanocellulose: A Player an Patent Landscape Approach" Katja Salmenkivi, Pöyry Management Consulting
- "Key Considerations for Successful Technology Transfer of Nanocellulose" Martha Marrapese, Keller and Heckman, USA
- "Life Cycle Considerations of Nanomaterials: Possibilities for Evaluating the Environmental Impact of Renewable Nanomaterials" David Lazarevic, Division of Environmental Strategies Research and the Divsion of Industrial Ecology, KTH
- "Nanosafety Research and Legislation in European Union: Future Activities" Tom van Teunenbroek, ministry of infrastructure and environment, The Netherlands
Sponsorship Opportunities are available.
Looking for Additional Nanotechnology Events?
Check out the TAPPI Flexible Packabing Symposium: New Technologies, preceding the ICE USA Exposition on April 8 at the Orange County Convention Center in Orlando, Fla. Sessions include Innovations in Nanocomposites, Innovations in Barrier, and Brand Launch, Shelf Appeal, and Authentication. Learn more.
##SHARELINKS##
|
The Bleaching of Pulp, Fifth Edition
By Alan W. Rudie and Peter Hart
Previous editions of The Bleaching of Pulp have provided comprehensive information on the technology used to bleach wood pulps. The 5th edition will continue this tradition as the premiere industry text on bleaching technologies but will be more focused on the modern industrial processes with less emphasis on fundamental science. New or more comprehensive sections are included on elemental chlorine free bleaching, enzymes, acid treatments for hexeneuronic acids, control of mineral scale, and multi-stage modeling as used to optimize bleaching among multiple stages.
Item Number: 0101R331 • List Price: $232 • Member Price: $155
Handbook for Pulp and Paper Technologists
(The Smook Book) Third Edition
By: Gary A. Smook
This best-selling text provides an introduction to the entire technology of pulp and paper manufacture. The book features 27 chapters covering all aspects of pulping and papermaking. Hundreds of illustrations, charts, and tables help the reader grasp the concepts being presented. The third edition features additional material on secondary fiber recovery and utilization, mechanical pulping, kraft pulping and bleaching, and papermaking. 2002. 425 pages, hard cover.
Item Number: 0202SMOOK • List Price : $75 • Member Price: $56
Troubleshooting the Papermaking Process
By: By Jerome M. Gess and Paul H. Wilson
This book takes the reader through the process of making paper, pointing out where interruptions can occur and where elements that are added to the system can cause problems in that part or subsequent parts of the papermaking process. The aim of this book is to give papermakers and those involved in the papermaking process the information required to allow them to understand how to track down and solve problems at their source rather than where the problems surface.
Item Number: 0101R298 •List Price: $161• Member Price: $106
Paper Machine Quality Control Systems - Vol. 1: Measurement Systems and Product Variability
By: Quality Control Systems Education Common Interest Group of the Process Control Division
This book describes in detail the measurement technology used in Quality Controls Systems (QCS). Individual chapters are devoted to the five most prevalent QCS measurements (basis weight, moisture, caliper, ash, and color) in the paper industry. Each of these chapters covers the physical principles involved in each measurement, sensor designs, various methods of implementation, and influence factors. A somewhat lighter coverage is given to 10 other QCS measurements that do not have such a broad installation base. Common issues that impact all sensors are explained, including how sensor performance is measured and reported, the impact of scanning process, filtering, scanner designs and construction, and sensor calibration and correlation. Statistical methods are covered in depth from discrete one-dimensional variability to multi-dimensional variability. Guidance is provided for using these statistical methods to locate the sources of variability in the paper process.
Item Number: 0101R328•List Price: $205• Member Price: $135
The Corrugated Containers Manufacturing Process
By: Jody A. Brittain, Stephen R. Perkins, and Philip G. Schnell
This comprehensive textbook describes the entire process of manufacturing corrugated containers. In addition to detailed explanations, the book also features practical troubleshooting tips, and a discussion of common problems and solutions within each major section. Seven detailed chapters cover the following topics:
- Paper and the Papermaking Process
- Steam
- Corrugating Adhesives
- Singleface Operations
- Doublebacker Process
- Combined Board
- Converting.
This textbook is designed to provide in-depth explanations and information for professionals working in all areas of the corrugated containers industry.
Item Number: 0101R281•List Price: $185•Member Price: $37
##SHARELINKS##
|
The Pulp and Paper Manufacturers Association (PPMA) has launched its first-ever Best Place to Work Award. The award is open to all companies in the forest products industry and will look not only at corporate life but also look at how employees feel about their work environments.
In conjunction with Majority Opinion Research Group, PPMA has started taking nominations for this award and will continue to accept nominations through July 1, 2013.
"This award is an exciting opportunity for PPMA to honor great companies. As an association that serves HR professionals, we know the value of the making your company a great place to work," said PPMA President Joe Thibaudeau, employee relations manager - Procter & Gamble - Green Bay, Wis., USA.
The award will be presented to the winner at the annual PPMA conference on October 23-25, 2013, in Milwaukee, Wis., USA. The winner will have the chance to speak with conference attendees about what makes his or her company the "Best Place to Work."
PPMA is a nonprofit association built around a community comprised of executives, managers, and human resource professionals from the pulp and paper industry. For its members, PPMA serves as a primary source of information on labor settlements and current human resource issues, governmenta,l and related operational issues.
To nominate your company for the Best Place to Work Award, use the online form.
##SHARELINKS##
|
The Pulp and Paper Safety Association (PPSA) will host its 70th Annual Safety and Health Conference - "The Human Element of Safety," June 9-12, 2013 in Williamsburg, Va., USA.
At the conference, presenters will address how human behavior will proactively help prevent, detect, and control events before they occur. Professionals from across the country know the importance of safety and attendees will hear from 18 speakers who will show the impact of addressing the human impact on safety. The conference will feature updates from OSHA, member company case studies, and PPSA's popular legal update.
Among the confirmed speakers are representatives from MeadWestvaco, Weyerhaeuser Co., Domtar, Safe Start, International Paper, REM Safety Consulting, Michael Best & Friedrich Law Firm, Training Logic, Change Management Consulting, and BushCo.
PPSA is a non-profit, non-political, international organization, devoted to the countinuous improvement of safety throughout all aspects of the paper industry. From forest products to paper mills, to converting plants, to recycle collections centers, our membership is grouped by category to ensure a fair and appropriate basis for comparison.
Registration is currently open for this event. More information is available online.
##SHARELINKS##
|
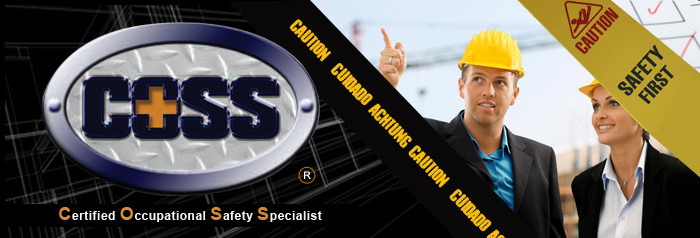
Are you ready to go further, faster in your safety career? The Certified Occupational Safety Specialist (COSS) class can take you there.
The COSS Class is Unique
Not only will you learn how to read and understand the OSHA 1910 and 1926 CFRs and help your company avoid OSHA citations that cost millions of dollars, but more importantly, by learning how to work safely on a job site, you can teach your company how to lower fatalities and near misses. Almost 47% of COSS graduates responding to our survey indicate that, since taking COSS, their company's injury rate and/or OSHA recordables have decreased by as much as 25% and others attest to as much as a 100% decrease!
Request a Course Outline & Syllabus for more information.
The class also addresses the psychology of safety, the true cost of an accident, hazard recognition, how to start up a health and safety program, behavior based safety, system safety, and much more!
What Will You Receive?
Upon successfully completing the class, you will obtain your national Certified Occupational Safety Specialist (COSS) designation, your OSHA 10-hr. card of completion in construction, and your OSHA 10-hr. card of completion in general industry.
National Program Recognitions
COSS is currently one of only 37 programs in the world recongnized and accredited by the American Petroleum Institute (API). In addition, the certifying body for construction education for colleges, universties and technical/trade schools, American Council for Construction Education (ACCE), has also recongnized our program. COSS is the only non-degree program to receive this national endorsement. Lastly, COSS has been established as a mandatory course for students in the Construction Management Program at Louisiana State University.
Program Content
The program consists of 40 hr. of hands on, face-to-face learning, which is delivered by an Authorized OSHA outreach trainer in both construction and general industry. Case studies and workshops are used extensively to bring learning objectives into focus. Guest speaker from areas such as OSHA and other governmental agencies are used to enhance the learning experience. Student presentations, daily quizzes, practical reviews, and a comprehensive final exam will allow you to demonstrate your competency.
Prerequisites
The only prerequisite for the COSS class is you must have a high school diploma or equivalent. In each class, we tend to have a mix of non-experienced, first time safety persons, as well as safety professionals who have been in the safety field for 20+ years. But, we have learned that regardless of the numbers of years of experience you have in safety, everyone leaves the COSS class with a wealth of knowledge!
Visit the COSS website for FAQs, testimonials and a list of clients that have taken COSS.
Register now.
If you would like more information on the COSS program, contact Beth Gordon at 877-610-2677
##SHARELINKS##
|
|
|