Over the Wire
TAPPI
Weekly Spotlight
KapStone Paper and Packaging Corp., Northbrook, Ill., USA, will acquire the stock of Longview Fibre Paper and Packaging, Longview, Wash., from Brookfield Capital Partners II, a private equity fund managed by Brookfield Asset Management Inc. in a cash-free, debt-free transaction for $1.025 billion in cash and subject to certain post-closing adjustments. Closing of the acquisition, expected to occur this summer, is subject to a number of customary conditions, including regulatory review.
Longview is a producer of containerboard, lightweight high performance multiwall paper, specialty kraft papers, and corrugated containers, located in the U.S. Pacific Northwest region. Longview's operations include a mill in Longview, Wash., equipped with five paper machines that produce 1.15 million tons of containerboard and kraft paper annually. In 2012, Longview generated $831 million in net sales and $118 million of EBITDA. In the first quarter of 2013, Longview's net sales were $217 million, generating $42 million of EBITDA.
Chairman and CEO of KapStone, Roger W. Stone, said that "acquiring Longview is an outstanding opportunity for numerous reasons. The acquisition immediately adds value for our shareholders by increasing earnings and generating very strong free cash flow. The deal is accretive to our bottom-line from Day 1. Our balance sheet, which was strong going into this transaction, remains strong after the acquisition. The combined company is expected to deliver substantial free cash flow in the first year, allowing KapStone to quickly de-lever. This acquisition will increase our exposure to the highly desirable containerboard segment. It also broadens our kraft paper line and makes KapStone a global producer of high performance, extensible multiwall paper, a grade that is growing at about 4% per year."
Matt Kaplan, president and COO of KapStone, added that "we look forward to having the Longview team join KapStone. Their track record is very impressive and over the past several years, Longview has increased productivity, benefitted from increased demand for containerboard and extensible kraft paper, and experienced declining wood costs. We anticipate synergies of approximately $10 million within the first 18 months."
Hugh Sutcliffe, managing partner of Brookfield, noted that "I would like to thank all of the people at Longview who have contributed toward building a safe and successful business and I am confident that this success will continue with KapStone."
Randy Nebel, president of Longview, said that "we are excited to be part of the KapStone family. It's a great opportunity for our customers and employees. Our product lines complement each other and provide us with a national presence in corrugated containers. We thank Brookfield for the support they have given us."
KapStone Paper and Packaging Corp. is a producer of unbleached kraft paper and corrugated products. The company is the parent company of KapStone Kraft Paper Corp. and KapStone Container Corp., which includes three paper mills and 15 converting plants across the Eastern and Midwestern U.S. The company employs approximately 2,700 people.
##SHARELINKS##
|
Kruger Products L.P, Canada, has started up a new TAD (through-air-dry) tissue machine at its Memphis, Tenn., USA, mill. The company recently held a dedication ceremony at the facility, during which Joseph Kruger II, chairman and CEO of Kruger Inc., and Mario Gosselin, CEO of Kruger Products, welcomed several distinguished guests, including Tennessee Governor Bill Haslam, Tennessee Commissioner of Economic and Community Development, Bill Hagerty, and several elected officials and members of local organizations.
This $316 million project included construction of a new building and a TAD machine, which is among the industry's most advanced technologies for the production of premium quality tissue. TAD technology produces tissue with high bulk and softness, as well as strength and absorption.
Completion of the project required more than 1 million person-hours over a period of 14 months. More than 100 new employees were hired for the new production line, bringing the overall employee count to 485 at the Memphis facility, which is the largest industrial building in the state of Tennessee.
The Kruger Products Memphis mill produces the White Cloud products, a range of tissue products sold exclusively at Walmart in the U.S.
In the photo below (l-r) are: Reid Dulberger, chief economic development officer for Memphis/Shelby County; David A. Spraley, EVP and COO; Mario Gosselin, CEO of Kruger Products; Vinny Borello, president and CEO, Boys and Girls Club of Greater Memphis; Mark H. Luttrell Jr., mayor of Shelby County; Bill Haslam, Tennessee governor; Joseph Kruger II, chairman of the board and CEO, Kruger Inc.; Bill Hagerty, Tennessee commissioner of economic and community development; A C Wharton, mayor of Memphis; Dan Clarahan, VP, U.S. business expansion, Kruger Products L.P.; Donald Cayouette, EVP, Kruger Inc.; and Jean-Yves Ouellet, VP, major projects, Kruger Inc.
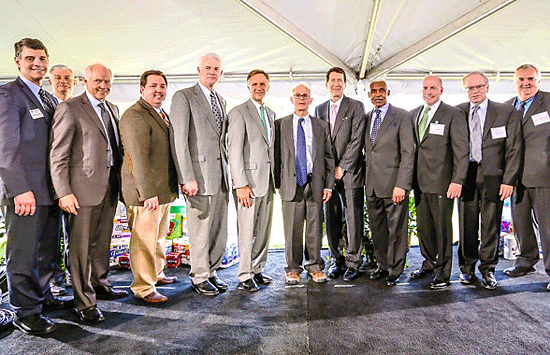
##SHARELINKS##
|
Klabin, São Paulo, Brazil, this week reported that it will build a new pulp mill in the city of Ortigueira, in the State of Paraná, Brazil, with the capacity to produce 1.5 million metric tpy of pulp, of which 1.1 million metric tpy will be hardwood pulp and 400,000 metric tpy will be softwood pulp. The new mill project is known as "Project Puma."
The company believes that Project Puma differs from other ongoing pulp projects in its flexibility to produce two types of fiber at the same mill and for enabling the supply of fluff pulp to the Brazilian market (fluff pulp is currently imported). Additionally, it will be possible to obtain a lower cost in the production of the two fibers, as well as to benefit from excellent inbound and outbound logistics and to produce 144 MW of surplus energy, the company notes.
Klabin currently owns 107,000 hectares of planted forest with pine and eucalyptus that will ensure wood supply for the new mill. The average distance between the forests and the plant is 74 km, ensuring competitiveness and low cost of wood transportation. Transportation of part of the mill's production will be made through railroad to the port of Paranaguá (State of Paraná).
The implementation of Project Puma, which is expected to begin on the 1Q 2016, represents an important step for Klabin, in light of the significant increase of its production capacity, which will not only supply pulp markets, but will also enable future expansions in packaging paper machines, as well as provide operational gains and positive impacts in its financial results.
As previously disclosed, the company's management had been conducting negotiations with investors to implement Project Puma through the establishment of a new company that would be called Klabin Celulose, which would receive the company's contribution of 107,000 hectares of planted forests in the State of Paraná, as well as financial resources from investors, while preserving majority control by the company. Under this structure, investors would have the right to withdraw from Klabin Celulose within a certain period, under conditions pre-established by contract.
Although implementation of Project Puma through Klabin Celulose is feasible and in the company's interest, management believes that development of the project directly by Klabin will better address the interests of the company and its shareholders.
##SHARELINKS##
|
This past week at the Royal Ontario Museum in Toronto, Ont., Canada, Alain Lemaire, executive chairman of the board at Cascades, Kingsey Falls, Que., Canada, was named "Greenest CEO in Canada," a recognition initiated by Corporate Knights, an organization specialized in the promotion of good corporate practices in terms of social responsibility. The award, given for the first time, was presented to Lemaire before more than 500 guests gathered as part of Corporate Knight's 12th annual gala that reveals and honors Canada's best 50 corporate citizens.
Cascades produces, converts, and markets packaging and tissue products that are composed mainly of recycled fibers. The company employs more than 12,000 employees who work in more than 100 production units across North America and Europe.
The candidacy of the person who co-founded Cascades and who lead the company for nearly 10 years, taking over from his brothers Bernard and Laurent, was unanimous among the jury members. The jury was made up of leaders from Canada's five most recognized environmental organizations: Équiterre, the David Suzuki Foundation, World Wildlife Fund-Canada, Nature Conservancy of Canada, and the Pembina Institute.
According to Toby Heaps, president of Corporate Knights, "the jury recognized in Alain Lemaire a man who has a number of environmental achievements to his credit. Among these, the ongoing concern to prioritize recycled fibers over virgin wood fibers as a raw material; the development of strategic partnerships to offer Cascade's expertise, namely in energy efficiency and in the management of waste materials; and lastly, the continued willingness to improve the company's results with regard to water and energy consumption."
Lemaire said that "this recognition is an exceptional way to conclude my experience as head of the family business that we founded close to 50 years ago. I am also honored to be the first recipient of this prestigious award. I would like to congratulate the other nominees and thank the members of the jury, but also to salute Corporate Knight's initiative for having created this award. Corporate leaders are often recognized for their management style and economic achievements, but rarely for their environmental accomplishments."
##SHARELINKS##
|
The Paper Industry International Hall of Fame's membership roster will expand to 117 on October 3 with the induction of six more paper industry notables who have been chosen as the 19th anniversary induction class. Walter Brecht, Charles N. Egan, Waldemar Jensen, Sverker Martin-Löf, Sven Axel Rydholm, and Theodore H. Wegner will join 111 previous members of the Paper Hall of Fame during induction ceremonies at the Radisson Paper Valley Hotel in Appleton, Wis., USA.
The Paper Industry International Hall of Fame recognizes individuals who, through their inventions initiative and efforts, have built or improved paper and allied industries worldwide. Each of the six inductees is being recognized in one or more categories, including Academic, Entrepreneur/Builder, Leadership, Research & Development, and Technology. Inductees are from the U.S., Finland, Germany, and Sweden.
Brecht (deceased), Darmstadt, Germany, was a professor in Paper Science and Technology at Technische Universität Darmstadt where he had a pivotal role in the training of Masters and PH.D. students for the Central European pulp and paper industry. Egan (deceased), Green Bay, Wis., USA, was an entrepreneur, builder, and innovative leader who put together Little Rapids Corp. (LRC) and is the primary reason why LRC not only survived as an independent, family-held paper company but continues to thrive with strong niche positions in attractive and growing end use markets.
Jensen (deceased), Helsinki, Finland, was a professor at Åbo Akademi University who later became CEO of The Finnish Pulp and Paper Research Institute (KCL). His research work at Åbo Akademi University was instrumental in the development of birch pulp as a significant component of the pulp and paper industry in Finland. Martin-Löf, Stockholm, Sweden, is one of Sweden's most renowned industrialists, who has played a key role in a number of Swedish Industries, not the least being pulp and paper.
Rydholm (deceased), Saffle, Sweden, was the global authority on pulping processes and pulp qualities of his time. Wegner, Madison, Wis., USA, has been the assistant director at the USDA Forest Service, Forest Products Laboratory for the past 24 years, overseeing an $8-10 million per year pulping and papermaking research program. He was also instrumental in the start of TAPPI's Nanotechnology Division in 2012.
The 19th annual ceremony will begin with a reception at 5 p.m. on Thursday, October 3, 2013, followed by dinner at 6:30 and the ceremony at 8 p.m. Attendees also will have the opportunity to witness the hanging of the commemorative plaques at the Paper Industry International Hall of Fame within the Paper Discovery Center located at 425 W. Water St., along the Fox River in Appleton, in the historic Atlas Paper Mill.
Reservations for the induction event can be made through the Paper Industry International Hall of Fame office at 920-380-7491.
##SHARELINKS##
|
Following a successful partnership last year, Georgia-Pacific, Atlanta, Ga., USA, the maker of Brawny® paper towels, this past week launched its second national campaign to support Wounded Warrior Project (WWP) and honor the strength of Wounded Warriors. WWP is a national organization dedicated to honoring and empowering Wounded Warriors as they recover and transition back to civilian life.
As part of the "Inner Strength" campaign, the Brawny brand is making a direct donation of $250,000 to WWP to benefit Wounded Warriors and their families. To raise further awareness for the cause, Brawny paper towels will donate an additional $1, up to $350,000, for every individual who:
The Brawny "Inner Strength" initiative will continue through December 31, and features an integrated marketing campaign with television advertising, social media, in-store signage, live events and digital advertising, as well as special Brawny paper towel packaging highlighting Wounded Warrior stories at participating retailers.
"It's been a privilege to stand strong alongside Wounded Warrior Project through our ongoing partnership," said Lanier Thomas, director of marketing, Brawny. "Brawny as a brand has always admired strength. The physical, mental and emotional wounds of these warriors take a tremendous amount of strength to overcome, and we're proud to support such a worthy cause. With help from our consumers, we can make a difference for those men and women in uniform who have already given so much."
Donations raised from the campaign will benefit a variety of programs and services WWP offers to ease Wounded Warriors' transitions back to civilian life. WWP serves veterans and service members who incurred physical or mental injuries, illnesses, or wounds, co-incident to their military service on or after Sept. 11, 2001. Their programs are uniquely structured to nurture the mind and body, and encourage economic empowerment and engagement.
"This nation's newest generation of wounded veterans have incredible stories of strength and Wounded Warrior Project is thankful to companies like Georgia-Pacific for bringing those stories to the forefront," said Jonathan Sullivan, Development EVP, Wounded Warrior Project. "It's through partnerships with Georgia-Pacific and the Brawny 'Inner Strength' campaign that we are able to inch closer to our vision of fostering the most successful, well-adjusted generation of wounded service members in our nation's history."
More information on the campaign, Brawny paper towels, or to see how you can get involved is available online. More information on WWP or to make a direct donation to the organization is also available online.
##SHARELINKS##
|
National Envelope, Frisco, Texas, the largest private U.S. envelope maker, sought bankruptcy protection for the second time in three years this week as cost cuts failed to keep pace with the decline in mail usage. According to a Reuters news report, the company blamed its struggles in part on its supply agreement with International Paper Co., which prevented it from reducing costs as sharply as its competitors. The company makes 37 billion envelopes a year and employs 1,600 people.
NE Opco Inc., which does business as National Envelope, said in court documents it had retained PricewaterhouseCoopers to help it find a buyer of its assets. So far, 18 potential buyers have signed non-disclosure agreements and it expects a "spirited" bidding process.
Money from the sale of National Envelope's assets would go to repaying its debts, which include $148.3 million in secured debt and about $20 million in trade debt, according to documents filed this week with the U.S. Bankruptcy Court in Wilmington, Del.
National Envelope filed for bankruptcy in 2010 and was sold to an affiliate of the Gores Group private equity firm for $150 million along with the assumption of debt.
##SHARELINKS##
|
Now an established event during London Pulp Week, this year's BWPA (British Wood Pulp Association) and Hawkins Wright Symposium moves to the historic Freemasons Hall in London, one of the finest Art Deco buildings in England. The event is scheduled for Thursday, November 14, from 8:30 a.m. – 12:30 p.m,, followed by lunch. The registration fee is £305 (VAT included).
This year's program includes:
- Diego Iscaro, IHS Global Insight
- The Global Economic Outlook
- João Cordeiro, Jaakko Pöyry
- Pulp Wood Supply Trends in Asia and Latin America
- Hani Nuqul, Nuqul Group
- Tissue: Prospects in the MENA Markets
- Heikki Vappula, UPM
- Pulp Production and Bioenergy - Strategic Opportunity or Risk?
- Oliver Lansdell, Hawkins Wright
- The Outlook for Market Pulp.
For more information email Amanda Marcus or phone at: +44 (0) 7802449144.
##SHARELINKS##
|
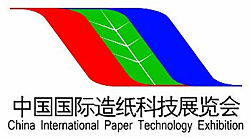 TAPPI has reserved exhibit space in the prestigious China International Paper Expo and Conference (CIPTE) to be held Sept. 23-25, 2013, in the National Agriculture Exhibition Center (New Hall), Beijing. The Expo is attended by more than 6,000 highly qualified buyers, mill employees, and others from China and around the world. Space is very affordable ($1,450 for a 36 m2 booth), but limited.
The goal of this conference is to:
- Promote the development of China's paper industry
- Display technical achievements of the paper industry
- Provide a communication platform for the enterprises of paper and relative industries.
This exhibit is attended by pulp and paper professionals from across China and the Pacific Rim. If you are interested, you must book your booth by July 1.
More information is available online.
##SHARELINKS##
|
Market Roundup
In 2012, 91% (29 million tons) of corrugated packaging used in the U.S. was successfully recovered for recycling, maintaining its top position as the most-recycled packaging material. Recovery for recycling has increased steadily since 1993, when 54.5% of old corrugated containers (OCC) was recycled. Recovery is also helped by the widespread access to community paper and paper-based packaging recycling programs. According to the AF&P's (Washington, D.C.) Community Survey, 87% (268 million) of the U.S. population has access to curbside or drop-off recycling programs.
Of the 91% of corrugated that was recovered in 2012, more than 50% was used to make new containerboard. An additional 12% was used to make recycled paperboard, and more than 34% was exported.
Where OCC Goes |
|
000 tons |
% |
Containerboard |
14,588 |
50.1 |
Recycled Paperboard |
3,510 |
12.0 |
Packaging & Industrial |
484 |
1.7 |
Tissue |
224 |
0.9 |
Newsprint |
0 |
0 |
Other |
251 |
0.9 |
Net Exports |
10,007 |
34.6 |
Total |
29,134 |
100 |
Source: AF&PA |
According to the most recent data available from the U.S. Environmental Protection Agency (EPA) report, Municipal Solid Waste in the United States; 2010 Facts and Figures, the corrugated and paper-based packaging industries set the standard for recovering products from the solid waste management stream.
The table below reflects data drawn from the EPA report and compares recovery rates for several major packaging materials. The data show that corrugated and paper-based packaging have the highest recovery rates among these major commodities.
Packaging Category |
Recovery Rates (2010) |
Percent change in discarded tonnage (1990-2010) |
Corrugated |
85% |
-65% |
Paper-Based Packaging |
71.3% |
-47% |
Aluminum |
35.8% |
+37% |
Glass |
33.4% |
-32% |
Plastics |
13.5% |
+78% |
Source: Municipal Solid Waste in the United States; 2010 Facts and Figures |
The corrugated industry continues to support the increased OCC recovery for recycling by:
- Modernizing equipment and technology so that OCC can be used at the manufacturing facilities
- Supporting business, community, and school recycling programs
- Developing a repulpability/recyclability standard protocol for corrugated boxes treated for moisture resistance.
More information about paper and corrugated recycling is available online. More information.about corrugated packaging's life-cycle studies and sustainability is also available online.
The Corrugated Packaging Alliance (CPA) is a corrugated industry initiative, jointly sponsored by the AF&PA, the Association of Independent Corrugated Converters (AICC), the Fibre Box Association (FBA), and TAPPI. Its mission is to foster growth and profitability of corrugated in applications where it can be demonstrated, based on credible and persuasive evidence, that corrugated should be the packaging material of choice; and to provide a coordinated industry focus that effectively acts on industry matters that cannot be accomplished by individual members. CPA members include corrugated manufacturers and converters throughout North America.
##SHARELINKS##
|
China's hunger for wood was less acute in 2012 than in the previous year. In particular, importation of softwood logs fell substantially from the record levels of 2011. Importation of lumber was also lower in 2012, but the decline was much less than that of logs. The biggest changes in log and lumber imports between 2011 and 2012 were the sharp decline of Russian log volumes crossing the Chinese border and the reduced lumber shipments from the U.S. to Chinese ports, as reported by the Wood Resource Quarterly (WRQ), Seattle, Wash., USA. During the first four months of 2013, import volumes of both logs and lumber picked up and were 12% and 19% higher, respectively, than in the 1Q/12.
The housing sector, a major consumer of imported lumber, has been strong in early 2013, and prices for new houses in 70 cities rose on average by more than 4% in April, up from 3.1% in March, 2013, according to national statistics. So far this year, the housing construction sector has outperformed the manufacturing, trade, investment, and personal consumption sectors.
North America is a major supplier of softwood products to China, with the market share for lumber and logs in the 1Q/13 accounting for 51% and 23%, respectively. In 2012, Canada and the U.S. exported logs and lumber valued at just over $3 billion, which was down 23% from 2011. During the first four months of this year, the import value for softwood logs and lumber from North America totaled $940 million dollars, an increase of more than 30% from the same period in 2012.
New Zealand's log-exporting companies continue to expand their presence in China. In 2012, New Zealand was the only country that expanded shipments when total Chinese log imports fell by 15%. Russia has for many years been the major log supplier to China, but in the 1Q/13, Russia and New Zealand both had a market share of close to 33% after year-over-year shipments were up almost 50% from New Zealand and down by 18% from Russia, according to the WRQ.
The biggest change in the Chinese buyers' sourcing of lumber has been the doubling of importation from Chile and the almost tripling in shipments from Sweden and Finland. Although these three countries still account for less than 10% of all imports, it is likely that their presence in China will expand in the coming years.
More information is available online.
##SHARELINKS##
|
Brazil has a large amount of biomass stock available. Last year, the country accounted for more than 20 billion MWh of power generation through biomass, according to a new report titled Biomass Industry in Brazil, which Research and Markets, Dublin, Ireland, has now added to its offering. Brazil's lush green forests spread over 6.3 million hectares of land, which basically consists of pine and eucalyptus, has set the country with abundance in biomass feedstock. Hydroelectric power and natural gas dominate Brazil's electricity generation capacity.
Brazil's total installed renewable power capacity was 14 GW in 2011, including the key renewable sectors—ethanol, biomass, and small hydroelectric power leading the country's renewable power supply. Historically, hydroelectric power has dominated Brazil's electricity supply, with more than 80% of electricity being fed into the grid.
Brazil's most abundant biomass feedstock is sugarcane, according to the report, which makes cogeneration the most viable biomass technology for installation across the country. Brazil has abundant forest residues, which can be used as a source for electricity generation in that country. Currently, the majority of Brazil's sugarcane is grown in the northeast region around Sao Paulo.
Surplus electricity generated from the existing sugar factories in Brazil is fed to the power grid. Biomass power plant size is often driven by biomass availability in close proximity as transport costs of the (bulky) fuel play a key factor in the plant's economics. It has to be noted, however, that rail and especially shipping on waterways can reduce transport costs significantly, which has led to a global biomass market, the report points out.
##SHARELINKS##
|
Pulp & Paper
Twin Rivers Paper Co., Madawaska, Maine, USA, a producer of specialty packaging, label, and publishing papers, this week announced that Atlas Holdings and Blue Wolf Capital Partners completed the acquisition of a controlling interest in the company. Twin Rivers also announced the formation of a new board of directors and leadership team that are turning their attention to building a growing, profitable business and creating long-term value.
Adam Blumenthal, managing partner of Blue Wolf, Tim Fazio, managing partner of Atlas Holdings, and new Twin Rivers' CEO Tim Lowe join existing board members in setting the strategic direction for the company. Joining Lowe on the new executive team for Twin Rivers are Wayne Gosse, CFO, Jean-Pierre Grenon, VP of forestry and sawmill operations, and Adam Levy, chief restructuring officer.
"We are turning our attention to building a growing, profitable business," said Lowe. "We are focused on bringing new resources, operational expertise, and a commitment to the future of the business."
The new management team brings many decades of leadership experience in the forest products industry. Lowe and Gosse previously led the successful operational and financial turnaround of Northern Resources Nova Scotia Corp., an integrated forest products company in Pictou, Nova Scotia. Before their work at Northern, Lowe held multiple operational positions at Domtar, including GM of the Woodlands, Maine pulp mill. Gosse held multiple finance positions at Neenah Paper and Kimberly Clark. Prior to joining Twin Rivers, Grenon has had a distinguished career, leading forestry operations at Domtar, Donohue, and as an independent industry consultant. Adam has 20 years' leadership experience in business transformations, including carve-outs, growth situations, and turnarounds, working throughout the U.S. and Canada. He has worked with companies ranging from $100 million to $1 billion in revenue in a wide range of industries.
Twin Rivers, with facilities in Edmundston, N.B., Canada, Plaster Rock, N.B., and Madawaska, has been a vital economic engine for the region for more than 80 years, producing specialty papers and lumber for a variety of markets. The new leadership team will build upon the existing foundation with a view to improving market focus and increasing profitability. The company is committed to investing capital to achieve these goals. The key pillars of the strategy include:
- Ensuring exceptional manufacturing capability in lightweight papers and expanding specialty markets
- Operating more efficiently and safely
- Expanding sawmill operation and lowering wood costs
- Local management and committed ownership.
"We welcome the early support received from employees, union leaders, community stakeholders, and government partners to collaborate on a successful business strategy," said Lowe. "We begin the transition today with a 12- to 18-month plan to ensure Twin Rivers can compete and thrive long-term in the extremely competitive forest products industry."
##SHARELINKS##
|
Australian Paper has signed a multi-year agreement with Metso, Finland, to manage maintenance operations at its Maryvale Mill in Victoria, Australia. Metso will manage all maintenance systems and procedures at the mill and be responsible for optimizing maintenance costs and developing maintenance quality. The agreement became effective June 1. The value of the agreement was not disclosed.
The Maryvale Mill has three pulp lines, five papermaking machines, an ECF bleach plant, pulp lapping machine, finishing facility, and a wastepaper processing plant. The objective of the agreement with Metso is to achieve world-class maintenance standards at the Maryvale Mill. Metso will assist Australian Paper with the skills development of maintenance staff and employees, as well as with improved planning and productivity. Metso's mill maintenance model optimizes the use of Total Productive Maintenance (TPM), Metso's streamlined reliability centered maintenance (Applied RCM), and condition-based maintenance. The model ensures the highest possible equipment efficiency and cost optimization.
"We are pleased to announce Metso will be our Alliance partner to work with Australian Paper to achieve world-class maintenance," says Jim Henneberry, CEO, Australian Paper. "Metso is a world-class maintenance supplier and original equipment manufacturer to the pulp and paper industry globally. Its significant worldwide expertise and professionalism will greatly benefit our operations at Maryvale."
Australian Paper is Australia's largest producer of fine papers for print and office applications, and also produces high-quality packaging papers. Australian Paper employs more than 1,400 Australians and supplies more than 500,000 metric tpy of product within Australia and around the world. The company is part of Nippon Paper Group that consists of approximately 180 affiliates and related companies. The Maryvale Mill is Australia's largest integrated fine paper and packaging papers complex.
##SHARELINKS##
|
Double A, Prachinburi, Thailand, reportedly has restarted production at the Alizay fine paper mill in Northern France. According to a report by Euwid Pulp and Paper, Germany, the company said this week that the first paper roll had been produced. A spokesman explained that production was currently in a test phase and would be increased step by step. Double A plans to start full activity on the French market beginning in the fourth quarter of this year.
"The Alizay mill will be the foundation for our expansion in Europe," Thirawit Leetavorn, Double A's senior EVP, was quoted in the Euwid report, adding that the company would be focusing on the production of its Double A brand.
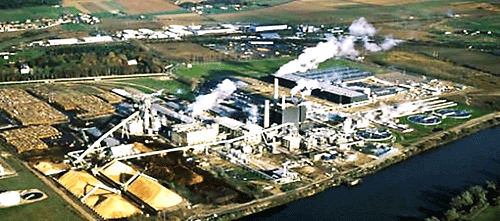
The Alizay mill has an annual production capacity of 300,000 metric tpy of uncoated woodfree paper. Double A said it would produce the paper brands Double A, Smart Copy, Hi-Plus, and Smartist. The company will use its own hardwood pulp from Thailand for production of the KHAN-NA brand. In February of this year, Double A had said that it would continue producing recycled paper at Alizay, and also bring back the Evolve brand.
The company did not give details on the number of employees currently at Alizay, but local media report that 150 people have been hired. Double A had announced at the beginning of the year that it would employ 200 people at the site.
Paper production in Alizay had been permanently idled since early 2012 when Metsä Board, Finland, closed the facilities. Double A acquired the operations earlier this year.
##SHARELINKS##
|
Buckeye Technologies Inc., Memphis, Tenn., USA, this week reported that Georgia-Pacific, Atlanta, Ga., has received a request for additional information and documentary material (the Second Request) regarding the nonwovens business in connection with the review by the U.S. Federal Trade Commission (FTC) and Antitrust Division of the U.S. Department of Justice of the Premerger Notification and Report Form initially filed by G-P on May 7, 2013, relating to its proposed acquisition of Buckeye. The effect of the Second Request is to extend the waiting period under the Hart-Scott Rodino Antitrust Improvements Act, which was scheduled to expire at 11:59 p.m., New York City time, on June 10, to 11:59 p.m., New York City time, on the date upon which the applicable waiting period expires after substantial compliance by G-P with the Second Request, unless such waiting period is earlier terminated.
G-P and Buckeye note that they will continue to work with the FTC and the Antitrust Division during the course of their review to respond to any inquiries, including the Second Request, as expeditiously as possible. In practice, complying with requests for additional information or material, including the Second Request, can take a significant amount of time.
##SHARELINKS##
|
Mercer International Inc., New York, N.Y., USA, this week announced that, during the current quarter, its Celgar mill (near Castlegar in British Columbia, Canada) took its annual scheduled major maintenance shutdown. As a result of a combination of a lightning strike at the mill and equipment and execution issues, the shutdown, which was planned for 11 days, took 15 days instead.
Also, Mercer reports, startup of the mill was slower than budgeted. The shutdown and slower startup resulted in a loss of approximately 30,300 air-dried metric tons (admt) of NBSK (northern bleached softwood kraft) pulp production (of which approximately 14,300 admt were unplanned) and a consequential loss of energy production. Mercer currently estimates that the Celgar mill's shutdown will have an overall negative impact of approximately EUR 11 million to its operating income in its second quarter of 2013 results, compared with its first quarter 2013 results.
Jimmy Lee, president and chairman, said that "we believe the issues with this recent shutdown were isolated and the mill is performing well and operating at pre-shutdown levels." He concluded: "We believe our current inventory levels are adequate and anticipate no material customer issues from this event."
Mercer's Celgar mill produces approximately 520,000 admt annually. It is one of the largest and most modern kraft pulp mills in North America.
##SHARELINKS##
|
At Steinbeis Papier GmbH, Glückstadt, Germany, the existing AP3 primary flotation system was recently upgraded to Voith (Germany) LowEnergyFlotation (LEF) Technology. Due to the rebuild, energy savings of 37% have been achieved at the flotation pumps, while flotation quality remained constant regarding the degree of whiteness, dirt specks and fiber loss.
In the course of the rebuild to LEF technology, the flotation cell injectors and the flotation pumps were improved in terms of hydrodynamics and dimensioned for optimum efficiency. The existing injectors were replaced by LEF injectors, and the flotation pumps were equipped with new LEF impellers. Contractually agreed measurements of the energy consumption before and after the rebuild confirmed the energy savings promised by Voith, which was also documented in a report.
The rebuild is part of an extensive, ambitious energy efficiency program of Steinbeis Papier GmbH. "As a sustainable company in the recycled paper industry, we want to take full advantage of all production possibilities to reduce energy consumption," said Dr. Michael Hunold, production manager at Steinbeis Papier.
##SHARELINKS##
|
Syktyvkar Tissue Group, Russia, has placed an order with Kadant Lamort SAS, Vitry-le-François, France, a subsidiary of Kadant Inc., Westford, Maine, USA, for a turnkey deinked pulping (DIP) line to be installed at Syktyvkar Tissue Group's greenfield site in Semibratovo, located in the Yaroslavsky region of Russia. The new recycled fiber DIP line will have a capacity of 110 bone-dry metric tons per day and will feature Kadant's compact concept deinking line. With startup of this new tissue mill in Semibratovo, Syktyvkar Tissue Group will become the largest producer of tissue in Russia.
"The selection of Kadant to supply our complete DIP line at our new facility in Semibratovo was based on our strong relationship and positive experiences following the successful startup of Kadant's DIP line at our flagship mill in Syktyvkar," said Mark Reznik, managing partner of Syktyvkar Tissue Group.
"We were pleased to once again be selected by one of Russia's most innovative and forward thinking tissue producers to supply the new DIP line for the Semibratovo project," said Alain Serres, president of Kadant Lamort. "The ongoing collaboration between Syktyvkar Tissue Group and Kadant has continued to strengthen and we look forward to working together with Syktyvkar on future tissue projects."
Kadant's compact concept deinking line features the latest advanced technology for the production of tissue, enabling the mill to operate with low energy consumption and maintain a small installation footprint, minimizing the total investment in buildings and annual operating costs. The compact DIP line will include the power-saving Helisoft™ pulper rotor, the all-in-one ScreenOne™ pressure screen, the new MAK-C™ deinking cell, and the DNT™ stock washer. In addition, the FibreWall™ screen cylinder is included with the ScreenOne system to maximize screening efficiency and the water treatment plant will use Kadant's pioneering Poseidon technology.
##SHARELINKS##
|
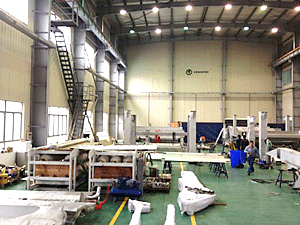 To keep pace with rapid growth in the Asia Pacific tissue market, Toscotec S.p.A., Italy, reports that it has successfully established its Chinese subsidiary, Toscotec Paper Machine (Shanghai) Co. Toscotec says it is proud to be able to contribute to the Chinese economy by employing local young engineers and highly qualified personnel for the construction of state-of-the-art machinery.
The new company, a Wholly Owned Foreign Enterprise (WOFE), is approximately a 40 min. drive from Shanghai downtown and 20 min. from Pudong international airport, in the Gaohang district of Shanghai. It has a total covered area of 1,500 m² dedicated to paper machine manufacturing and commercial offices.
Toscotec Shanghai's mission is to become a benchmark for tissue technology in the Asia Pacific region, to provide the best service level to its customers and strengthen the company's presence in one of the world's most significant and fastest growing markets.
With a skilled team of permanent engineers from both Italy and China, Toscotec Shanghai is now in a position to manufacture and deliver tissue paper machines to its clients. The Shanghai service team will be able to provide a full range of services such as mill site surveys, fast delivery of spare parts, and mill staff training.
Already active in the Asian market since early 2000, Toscotec S.p.A. has developed a strong commercial network in the Far East in recent years with the result that today 14 tissue machines have successfully started up for Chinese clients and an additional 15 are to be started up in 2014.
Alessandro Mennucci, CEO of Toscotec Italy, noted that "this startup, together with our existing commercial network, brings Toscotec closer to our Asian clients, wherever they are located."
##SHARELINKS##
|
UPM, Helsinki, Finland, and Renmatix Inc., King of Prussia, Pa., USA, have entered into a non-exclusive joint development agreement (JDA) in the area of biochemicals. Under terms of the JDA, both companies will further develop Renmatix's water-based Plantrose™ process to convert woody biomass into low-cost sugar intermediates for subsequent downstream processing into biochemicals. Offering cost-competitive bio-alternatives for select petrochemicals on an industrial scale is the long term goal of this initiative.
"We are very excited about this truly collaborative endeavor. It combines UPM's core competencies in sustainable sourcing and efficient industrial processing of wood, with Renmatix's unique conversion technology," noted Michael Duetsch, director of Biochemicals, at UPM. "Access to second generation, lignocellulosic sugars through a process that uses almost no consumables is a crucial factor in Plantrose technology's attractiveness."
The Plantrose process employs water at very high temperatures and pressures to breakdown biomass through supercritical hydrolysis. Under such conditions water can act as both a powerful solvent and catalyst, creating rapid reactions.
"We believe this pioneering approach leads to real cost advantages over conventional methods. Our growing relationship with UPM gives Renmatix an opportunity to support them expanding the Biofore story," said Mike Hamilton, CEO of Renmatix. "Renmatix, as a U.S.-based technology provider, takes great pride in working with global companies across the emerging bio-value chains. It reinforces the demand that exists for licensing Plantrose technology as the bridge between sustainable sources of upstream biomass, and downstream manufacturing of biochemicals and fuels."
"The joint development agreement with Renmatix is another milestone in the implementation of our biochemicals strategy and UPM's Biofore vision. The cooperation further strengthens our position as the frontrunner in the innovation-driven integration of bio and forest industries," Juuso Konttinen, VP of UPM, added.
UPM consists of three business groups: Energy and Pulp, Paper, and Engineered Materials. The Group employs some 22,000 people, and has operations in 67 countries, with production units in 17 countries. UPM's annual sales exceed EUR 10 billion.
##SHARELINKS##
|
Containerboard/Packaging
China's packaging industry is forecast to reach a total output value of RMB1.824 trillion in 2016, with a compound annual growth rate of 8.0% in 2013-2016, according to a new report being offered by Research and Markets, Dublin, Ireland, titled China Packaging Industry Report, 2013-2016. In China, packaging industry segments mainly refer to paper packaging, plastic packaging, metal packaging, glass packaging, package printing and packaging machinery, of which, paper packaging accounts for a large proportion of the market size (33%), followed by plastic packaging (31%) and package printing (15%).
Among all market segments, paper packaging materials enjoy advantages such as wide source, light weight, population-free, good workability, and low cost. In 2008-2012, China's paper and paperboard container industry witnessed compound annual growth rates of 17.27% and 24.86% in operating revenue and total profit, respectively. Despite light weight and good formability, plastic packaging is difficult to be degraded, therefore, environmentally friendly plastic packaging materials such as PVDC and EVOH with high barrier property and easy degradability will usher in a large market space in the future.
In 2012, influenced by the slowdown in downstream demand for paper packaging and plastic packaging, China's metal packaging container industry experienced better development than other market segments, with operating revenue and total profit up 14.02% and 18.63% year-over-year, respectively (6.51% and 12.83% for paper packaging; 7.96% and 2.03% for plastic packaging during the same period). The same year, revenue from metal packaging enterprises also performed well.
##SHARELINKS##
|
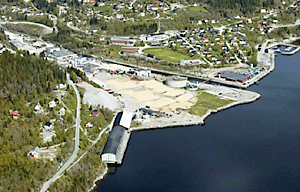 Mayr-Melnhof Karton, Vienna, Austria, has agreed to acquire Södra's Follafoss, Norway pulp mill for an undisclosed amount. In 2012, Södra Cell decided to divest the Follafoss pulp mill. Production at the mill ceased at the end of October/beginning of November 2012. Discussions about selling the mill got under way just before Christmas, a declaration of intent was issued at the end of December, and an agreement has now been reached with Mayr Melnhof Karton.
Södra's pulp mill in Follafoss produces CTMP (chemi-thermomechanical pulp) and has a capacity of just over 100,000 metric tpy.
The Mayr-Melnhof Group, headquartered in Vienna, is the largest producer of coated recycled cardboard, with a growing position in virgin fiber-based board as well as the leading European manufacturer of folding cartons.
##SHARELINKS##
|
Pactiv LLC, Lake Forest, Ill., USA, has launched a new website designed to enhance site usability and product search capabilities (available even on a mobile device). The site is completely reorganized and has a simplified, modern look, Pactiv notes. Visitors can quickly learn more about the company's history, including company and product history, industry awards, and what it's like to be an employee.
The site boasts enhanced product search functionality. "Gone are the days of flipping through a static brochure—instead, the interactive search tool allows for a broad exploration, casting the net as wide as a product category, market channel, or application. It also caters to those who know exactly what they want by refining the search based on specific attributes (from material type to color to temperature to capacity," the company points out.
The new site will continue to be updated with additional products and photographs, and in coming months it will be translated into different languages.
Pactiv is one of the largest manufacturers and distributors of food packaging and foodservice products, supplying packers, processors, supermarkets, restaurants, institutions, and foodservice outlets around the world. It has more than 11,000 employees at more than 50 manufacturing plants, mixing centers and distribution centers.
##SHARELINKS##
|
New Products
Wausau Paper, Mosinee, Wis., USA, this past week launched its new Green Seal certified, DublNature® line of premium, plush, cloth-like towel and tissue products utilizing 100% recycled fiber on the company's recently completed ATMOS technology-enabled paper machine at Harrodsburg, Ky. DublNature products, the company notes, "provide exceptional softness, strength, absorbency, and brightness, and are well suited to a wide range of applications. They are targeted at businesses and institutions seeking the finest quality while supporting ‘green' purchasing initiatives."
Henry C. Newell, president and CEO, said that "the launch of our new DublNature line of products represents a milestone in capitalizing on a first-of-a-kind technology investment, the largest capital investment in the history of our company. Like our engineering and construction team, who delivered our Harrodsburg paper machine under budget, our product design, papermaking, converting and marketing teams are to be congratulated for delivering the new DublNature product family on a much-accelerated timeline."
Matthew L. Urmanski, SVP, Tissue, added that "a significant amount of credit also goes to our highly engaged network of distributors. As our partners, these distributors have played a key role in our assessment of the market opportunity for a broader expression of premium towel and tissue products in the away-from-home market and in the product design process itself. The excitement that exists within our distributor community for these distinctive DublNature products is evident in their positive reactions, as is the anticipation that exists for the launch of our ultimate premium brand Artisan later this year."
##SHARELINKS##
|
People
Ilim Group, Russia, has appointed Ekaterina Serebrenikova chief managing director of human resources. Serebrenikova previously served as HR director for International Paper, Russia. Before that she was with such companies as Motorola and EMC.
Evgeny Dymkin, who until now worked as chief managing director of human resources for the Ilim Group, is leaving the company to assume a senior management position for International Paper, EMEA, headquartered in Brussels, Belgium.
##SHARELINKS##
|
Kelheim Fibres GmbH, Germany, named Sebastian Basel business manager of Specialty Papers. Stefan Meier will succeed Basel as commercial manager of New Business.
Meiier's counterpart on the R&D side—as technical manager of New Business--remains Dr. Philipp Wimmer, who has been part of Kelheim's team since November 2010.
##SHARELINKS##
|
Stora Enso Group, Finland, has appointed Treasurer Jyrki Tammivuori acting CFO, effective July 1. As announced in April, the current CFO, Karl-Henrik Sundström, will head the company's new Printing and Living Division, combining the current Printing and Reading Business Area and Building and Living Business Area beginning in July.
The process of recruiting a new CFO is advancing, Stora Enso reports.
##SHARELINKS##
|
TAPPI News
The Pulp and Paper Safety Association (PPSA) will award John Sunderland, of Buckeye Technology, the first ever PPSA Distinguished Service Award. The PPSA Distinguished Service Award was established in 2013 to recognize Sunderland for his voluntary leadership and service and will be awarded to anyone who has performed outstanding service to the association.
"We were honored to be able to present John with this award. He has shown a dedication for this association and has helped us through challenging times," said Pete Masias and Monty Batchelor, PPSA Awards Committee and Board of Directors members.
Sunderland has served on the PPSA Board of Directors for a number of years and in that time he took an association that was heading for financial disaster and stepped in to provide the needed administration that literally saved the association. It is that dedication to PPSA that allows PPSA to remain the most respected safety association in the pulp and paper industry.
The award will be given to Sunderland at the 70th Annual Health and Safety Conference in Williamsburg, Va. Registration is currently open for this event. More information is available online.
The Pulp & Paper Safety Association is a non-profit, non-political, international organization, devoted to the continuous improvement of safety throughout all aspects of the paper industry. From forest products to paper mills, to converting plants, to recycle collection centers, our membership is grouped by category to ensure a fair and appropriate basis for comparison.
##SHARELINKS##
|
Free Webinar: "Providing Operator Training to the Workforce"
The Pulp and Paper Manufacturers Association is proud to offer a free webinar on June 19: "Providing Operator Training to the Workforce of the Future."
The one-hour informational webinar will be presented by NPT2, the National Network of Pulp and Paper Training Technology. NPT2 was created under a National Science Foundation grant to provide training to your workforce with the skills needed to operate equipment, produce quality product, and to understand the technical aspects of their assignment, so that employees are truly engaged in and understand their work.
The webinar will cover various methods of operator training, including the more advanced educational training used by the paper industry around the world; introduction to the newest and most advanced curriculum of e-learning available, developed by industry experts; and how mills can customize learning.
The webinar will be facilitated by Michael J. Kocurek, PhD, Professor Emeritus, Paper Science & Engineering, North Carolina State University, and the Director of NPT2 at Alabama Southern.
The webinar, sponsored by the National Science Foundation and hosted by Alabama Southern, will begin at 11:00 a.m. est. and will appeal to human resource professionals, operations and manufacturing employees, process engineers, and others needing to stay current on operational training issues. To participate, please register online.
The pulp and paper industry is currently facing a serious shortage of trained workers who understand both what happens and why things happen. The crisis is dramatic due to ongoing retirement of a generation of seasoned workers who represent decades of experience. This is a challenge to the industry--but also an opportunity to train and create a more technologically advanced workforce.
This webinar will segue into the one-day Operator Training Workshop, sponsored by the National Science Foundation and Alabama Southern, in Thomasville, Ala., on July 18. (see article below titled Operator Training Conference and Workshop Set for July 18 at Alabama Southern).
##SHARELINKS##
|
The 2014 PLACE Technical Program Team is actively seeking technical presentations, panels, tutorials, roundtables, and case studies from the packaging and academic community to be presented at this year's conference. Interested in being a session chair or know someone who would be a great presenter? Extended abstracts will be accepted anytime before August 1. Space is limited so submit now! Final papers will be due on or before March 17, 2014.
View the list of suggested topics and an extended abstract example.
The 2014 PLACE Conference is the premier North American event for the flexible packaging industry and will have something for the whole supply chain, including suppliers, converters, extruders, retailers, and brand owners.
Join us for this comprehensive event with more targeted content, topic variety, and program ideas than ever before. This event will use traditional content delivery methods like primers/tutorials, panel discussions, and interactive content delivery methods.
Submission Deadline is August 1, 2013.
Feel free to contact Kristi Ledbetter if you have any additional questions.
Kristi Ledbetter
Converting Division Manager
TAPPI
15 Technology Parkway South
Peachtree Corners, GA 30092
Phone: 770-209-7319
Fax: 770-446-6947
##SHARELINKS##
|
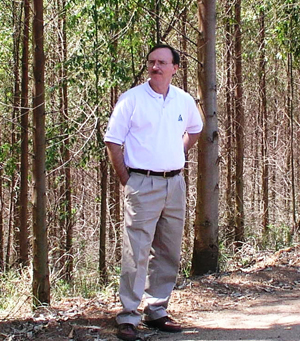 What do buggy whips and TAPPI membership have in common? If you ask member Jim Atkins, he'll tell you it is change – revolutionary, fast-moving, and ever constant change. But that's where the similarities end.
To keep ahead of the advances occurring every day in our industry, you need to have an advantage," Jim says, "and the best place to jump in with both feet is with membership in TAPPI." And, Jim talks from experience. He's been a member since 1975, joining shortly after receiving his degree in Chemistry from the University of North Carolina. For him, being prepared has been the best way to turn change into opportunity. "Embracing change is key to future success. You can continue to make buggy whips or you can embrace the opportunities that change offers." And TAPPI, he says, is the best way to do that.
Find out more by reading this month's Member Spotlight. Spotlight participants are recommended by fellow members and staff. If you would like to nominate a member just send their name (or names) to MemberSpotlight@tappi.org. We will forward a spotlight questionnaire to fill out and return.
We look forward to seeing you in the Spotlight!
##SHARELINKS##
|
As TAPPI is getting ready to celebrate its 100th Year Anniversary in 2015, we were wondering how much industry expertise we have in this great group of professionals.
So, we decided to post a discussion question on our TAPPI Social Media outlets. We asked, "How many years of paper and/or packaging experience do you have?"
Who knew such a simple question would have such an impressive response.
With more than 7,000 TAPPI members, all over the world, we have counted 650-plus years of industry experience! Now you probably can't find that anywhere else . So why don't you join us?
From those "born" into the industry to third generation professionals. From paper to packaging, to sustainability, environment, tissue, converters, and consulting. This TAPPI network has something for everyone.
Become a part of this unique community of paper and packaging professionals, and add your expertise to our group, and network with others to learn something new.
Visit our website to learn more today!
##SHARELINKS##
|
The Lake States TAPPI/North Central PIMA golf outing will take place August 13.
For more information, see the event announcement.
This year's kick-off Golf Outing is being held at Mid-Vallee Country Club in De Pere, Wis..An afternoon shotgun scramble golf outing is planned with dinner to follow. Prizes will be awarded and individual pin events will be held.
Those submitting their registration with their fee, postmarked by August 9, will be assigned holes on a first-come, first-served basis. Later registrations will be assigned as space is available. Foursome sponsors and all singles will be notified of their hole assignment at the course on the day of the event.
##SHARELINKS##
|
The TAPPI Best Practices on the Corrugator Course, June 25-27 at the TAPPI Training Center in Peachtree Corners, Ga., USA.
Top 10 Reasons to Register for TAPPI's Best Practices on the Corrugator Course:
#10 Gain the knowledge you need to troubleshoot most operational problems.
#9 Learn how you can maintain quality while reaching maximum corrugator speeds.
#8 Network with peers to find solutions to your quality issues.
#7 See on-site videos of conditions producing defects and how they can be resolved.
#6 Learn from industry-renown instructors Tom Pearce, Pearce Corrugated Consulting; Dan Dyson, Vice President of Production for Avista Solutions International, Inc.; Jon Porter, Senior Instructor/Process Specialist, Fosber America; Robin A. Sommers, Engineering Manager, Donahue & Associates; and Peter Snyder, National Account Salesman, Harper/Love Adhesive.
#5 Bring your defects to the experts—and to your colleagues in the room—to get guidance on how to overcome your production problems.
#4 Find out how you can get the maximum yield of boxes from the paperboard consumed.
#3 Take home new ideas and operational methods to improve production.
#2 Analyze your mill's specific problems with course instructors and explore possible solutions.
And the Number 1 reason why you should register for the 2013 TAPPI Best Practices on the Corrugator Course is...
With all of these great reasons, how can you not afford to?
Last year's course sold out, so here's your chance to attend. If you work with a corrugator, this is your opportunity to learn how to:
- Increase productivity and improve quality
- Reduce excess waste
- Adopt the "Centerline Process" to achieve a product that is consistent on every shift
- Maintain quality while reaching maximum corrugator speeds
- Get the maximum yield of boxes from the paperboard consumed
- Troubleshoot the most common operational problems
- Recognize critical properties of paperboard, starch, adhesive, and how to control warp.
What to Bring with You: Your questions and issues related to corrugator operations and samples of your defects.
What You'll Take Home: New ideas and operational methods to improve production.
Want to know more? Here's the Proposed Course Schedule.
Put June 25-27 on your calendar and register now to lock in your participation before seats fill.
##SHARELINKS##
|
The soon-to-be-published, "Production and Applications of Cellulose Nanomaterials" is the latest TAPPI Press product to broaden the industry knowledge regarding who is researching nano technologies as well as leads on successful applications.
Anyone working in the nanomaterials field, or needing to understand the production and standards of the field, will want to add this volume to their reference material.
Pre-order your copy today and save!
This new book will include:
- A collection of two to three page summaries on recently completed and on-going research with these high strength materials
- A list of who's-who of research as well as leads on successful applications
- Topics on subjects such as production and modification, composites, other applications, modeling, and standards.
- Special feature: Actual cellulose nanocrystals included within the overcoat varnish of the cover.
##SHARELINKS##
|
The existence of cellulose nanocrystals and cellulose nanofibrils has been known for several decades, yet recent advances in science, particularly in the field of nanotechnology, have revealed that these materials contain unique physical properties, particularly high strength properties. Researchers have been studying how these materials can improve paper properties and will present their latest finding this June 24-27 in Stockholm, Sweden, at TAPPI's 8th Annual International Conference on Nanotechnology for Renewable Materials at the KTH Royal Institute of Stockholm.
The program for this year's event has been released, and one session will focus on using cellulose nanofibers for improving retention and increasing strength in paper. Researchers from Aalto University in Finland will report on improved flocculation of both precipitated calcium carbonate (PCC) and kaolin with the addition of certain cellulose nanomaterials. Researchers from Papiertechnische Stiftung (PTS) in Heidenau, Germany, will report on the importance of adding fillers, celluloses, and compounding agents in the right order to achieve the best results. Researchers from VTT in Finland will report on ways to increase the strength of paper by using filler particles coated with nanoscale calcium silicate hydrate (CS) structures.
New reports at the conference will present some exciting advances for both within the pulp and paper industry and beyond. The technical program features cellulose nanomaterials in a variety of applications, including:
- Unique and Thin-Film Composites
- Filler and Coating Applications for Different Paper Grades
- Improved Barrier Properties for Packaging Applications
- Cellulose Nanomaterials as Films and Carriers in Medical Applications
- Nanopaper and Iridescent Colored Cellulose Films.
With more than 80 technical presentations, five keynote presentations, and 50 poster presentations, this year's conference is packed with the latest applications of renewable nanomaterials.
Watch for additional updates from TAPPI on how nanotechnology, and cellulose nanomaterials in particular, can be a transformative technology for the pulp and paper industry.
The 8th Annual International Conference on Nanotechnolgy for Renewable Materials is hosted by TAPPI's International Nanotechnology Division, which strives to collectively advance the responsible and sustainable production and use of renewable nanomaterials. More information is available online.
##SHARELINKS##
|
Paper Machine Wet Press Manual, Fourth Edition
Edited by: Richard A. Reese
Paper Machine Wet Press Manual provides an introduction to wet pressing technology in the paper industry and includes information on practical press section considerations on paper machines. The book provides an overview of press section equipment and key factors in optimizing press section performance. In addition, checklists are included to evaluate press section performance.
The book will be particularly useful to paper company personnel including paper machine superintendents, foremen, paper machine operators, process engineers, etc. Employees of suppliers to the paper industry involved in supplying press section equipment and evaluating press section performance will also find the book beneficial. The Paper Machine Wet Press Manual, Fourth Edition is a project of the Water Removal Committee of TAPPI's Engineering Division.
Item Number: 0102B042 • List Price: $124 • Tappi Member: $83
Starch and Starch Products for Wet End Application
By: Hans W. Maurer
Starch and Starch Products for Wet End Applications is a complement to Maurer's previous book, Starch and Starch Products in Surface Sizing and Paper Coating. His new book, Starch and Starch Products for Wet End Application, addresses issues in the preparation and application of starch and starch products for use in the wet stages of the papermaking process. This publication covers a wide range of subjects in starch utilization, ranging from the preparation of specific starch products to their use in papermaking for flocculation, retention, drainage, strength, and sizing control. Environmental issues in the use of starch and analytical procedures for starch analysis and charge characterization are also addressed.
Item Number: 0101R319 • List Price: $185 • Tappi Member: $125
E-BOOKS COMING SOON
Roll and Web Defect Terminology - E-Book
By: Jerome M. Gess and Paul H. Wilson
This book takes the reader through the process of making paper, pointing out where interruptions can occur and where elements that are added to the system can cause problems in that part or subsequent parts of the papermaking process. The aim of this book is to give papermakers and those involved in the papermaking process the information required to allow them to understand how to track down and solve problems at their source rather than where the problems surface.
Paper Machine Quality Control Systems - Volume 1: Measurement Systems and Product Variability - E-Book
By: Quality Control Systems Education Common Interest Group of the Process Control Division
This book describes in detail the measurement technology used in Quality Controls Systems (QCS). Individual chapters are devoted to the five most prevalent QCS measurements (basis weight, moisture, caliper, ash, and color) in the paper industry. Each of these chapters covers the physical principles involved in each measurement, sensor designs, various methods of implementation, and influence factors. A somewhat lighter coverage is given to 10 other QCS measurements that do not have such a broad installation base. Common issues that impact all sensors are explained, including how sensor performance is measured and reported, the impact of scanning processes, filtering, scanner designs and construction, and sensor calibration and correlation. Statistical methods are covered in depth from discrete one-dimensional variability to multi-dimensional variability. Guidance is provided for using these statistical methods to locate the sources of variability in the paper process. This book was written by the Quality Control Systems Education Common Interest Group of the Process Control Division.
COMING SOON IN PRINT
Production and Applications of Cellulose Nanomaterials
By: Alan W. Rudie, USDA Forest Service, Forest Products Laboratory,
Michael A. Postek, National Institute of Standards and Technology,
Robert J. Moon, USDA Frost Service, Forest Products Laboratory,
Michael A. Bilodeau, University of Maine
Cellulose nanocrystals and cellulose nanofibrils have been known for upwards of 50 years, but recent research suggesting very high strength properties and other unique physical properties have generated extensive interest in these materials. The book will be a collection of summaries on recently completed and on-going research with these high strength materials. This book will highlight cutting-edge research as well as leads on successful applications. Topics will include: production and modification, composites, other applications, modeling, and standards.
##SHARELINKS##
|
The Pulp and Paper Manufacturers Association (PPMA) has launched its first-ever Best Place to Work Award. The award is open to all companies in the forest products industry and will look not only at corporate life but also look at how employees feel about their work environments.
In conjunction with Majority Opinion Research Group, PPMA has started taking nominations for this award and will continue to accept nominations through July 1.
"This award is an exciting opportunity for PPMA to honor great companies. As an association that serves HR professionals, we know the value of the making your company a great place to work," said PPMA President Joe Thibaudeau, employee relations manager - Procter & Gamble - Green Bay, Wis., USA.
The award will be presented to the winner at the annual PPMA conference on October 23-25, 2013, in Milwaukee, Wis., USA. The winner will have the chance to speak with conference attendees about what makes his or her company the "Best Place to Work."
PPMA is a nonprofit association built around a community comprised of executives, managers, and human resource professionals from the pulp and paper industry. For its members, PPMA serves as a primary source of information on labor settlements and current human resource issues, governmenta,l and related operational issues.
To nominate your company for the Best Place to Work Award, use the online form.
##SHARELINKS##
|
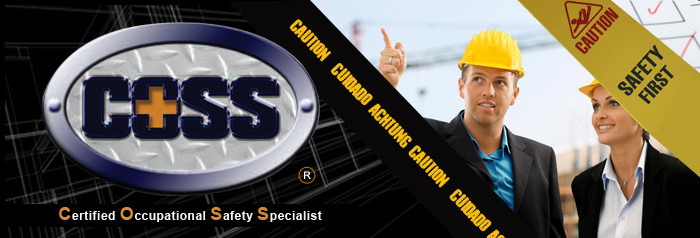
Are you ready to go further, faster in your safety career? The Certified Occupational Safety Specialist (COSS) class can take you there.
Your opportunity to attend the highly reputable
Certified Occupational Safety Specialist (COSS) Course
is coming July 15-19, at the TAPPI Training Facility in metro Atlanta, Ga., USA.
Not only will you learn how to read and understand the OSHA 1910 and 1926 CFRs and help your company avoid OSHA citations that cost millions of dollars, but more importantly, by learning how to work safely on a job site, you can teach your company how to lower fatalities and near misses. Almost 47% of COSS graduates responding to our survey indicate that, since taking COSS, their company's injury rate and/or OSHA recordables have decreased by as much as 25% and others attest to as much as a 100% decrease!
Request a Course Outline & Syllabus for more information.
COSS curriculum is updated every year for the highest integrity of accuracy because safety rules and OSHA standards are often changing. The cost of this nationally-known program is minimal if you compare it with the potential cost of even one accident.
This course is designed for all job levels so that anyone can become a leader in safety management on the job. COSS instructors are Authorized OSHA Outreach Trainers, a highly complex level of commitment - meaning these trainers are passionate about safety. You'll learn from the best in the profession. This class also addresses the psychology of safety, the true cost of an accident, hazard recognition, how to start up a health and safety program, behavior based safety, system safety, and much more!
What Will You Receive?
Upon successfully completing the class, you will obtain your national Certified Occupational Safety Specialist (COSS) designation, your OSHA 10-hr. card of completion in construction, and your OSHA 10-hr. card of completion in general industry.
National Program Recognitions
COSS is currently one of only 37 programs in the world recongnized and accredited by the American Petroleum Institute (API). In addition, the certifying body for construction education for colleges, universties and technical/trade schools, American Council for Construction Education (ACCE), has also recongnized our program. COSS is the only non-degree program to receive this national endorsement. Lastly, COSS has been established as a mandatory course for students in the Construction Management Program at Louisiana State University.
Program Content
The program consists of 40 hr. of hands on, face-to-face learning, which is delivered by an Authorized OSHA outreach trainer in both construction and general industry. Case studies and workshops are used extensively to bring learning objectives into focus. Guest speaker from areas such as OSHA and other governmental agencies are used to enhance the learning experience. Student presentations, daily quizzes, practical reviews, and a comprehensive final exam will allow you to demonstrate your competency.
Prerequisites
The only prerequisite for the COSS class is you must have a high school diploma or equivalent. In each class, we tend to have a mix of non-experienced, first time safety persons, as well as safety professionals who have been in the safety field for 20+ years. But, we have learned that regardless of the numbers of years of experience you have in safety, everyone leaves the COSS class with a wealth of knowledge!
Visit the COSS website for FAQs, testimonials and a list of clients that have taken COSS.
Register now.
If you would like more information on the COSS program, contact Beth Gordon at 877-610-2677.
##SHARELINKS##
|
Alabama Southern will host a one-day-only Operator Training Conference & Workshop. This complimentary event, funded by the National Science Foundation (NSF) in conjunction with NPT2, will help HR professional and mill leaders add value to their existing operator training programs and provide practical advice on how to create a more competitive and better trained workforce.
Date: Friday, July 18
Location: Alabama Southern, Thomasville, Ala.
Time: 8:00 a.m.- 3:00 p.m CST
Discover new tools, learn best practices, and better equip your operator workforce. For more details or to register for the event, please contact Martha Wynn by email or by phone at 334.637.3194.
##SHARELINKS##
|
Nominations for the major TAPPI 2014 awards are due by August 1. The awards that may be presented in the upcoming year are:
Gunnar Nicholson Gold Medal Award - The Association's highest technical honor may be presented annually to recognize an individual or individuals for preeminent scientific and engineering achievements of proven commercial benefit to the world's pulp, paper, board, and forest products industries and the other industries that TAPPI serves.
Herman L. Joachim Distinguished Service Award - The Association's highest award for service may be presented annually to recognize leadership and service that have significantly and demonstrably contributed to the advancement of the Association.
Paul W. Magnabosco Outstanding Local Section Member Award - The highest honor for Local Sections may be presented annually to recognize an individual for outstanding leadership and exceptional service to one or more Local Sections, which have resulted in significant and demonstrable benefits to the Local Section members.
TAPPI Fellow - TAPPI Fellows are individuals who have been members of TAPPI for not less than 10 years prior to the nomination, and who have contributed meritorious service to the Association and/or the paper and related industries. Retiring members of the TAPPI Board of Directors become Fellows automatically at the end of their term.
The TAPPI Awards and Honors page has links to these awards that will show the qualifications required and links to the nomination forms that must be completed. You may submit all nomination forms by email to standards@tappi.org, or you may fax them to the attention of the awards department at +1-770-446-6947, or send them by mail to TAPPI, Awards Department, 15 Technology Parkway South, Peachtree Corners, GA 30092, USA.
##SHARELINKS##
|
The TAPPI Introduction to Kraft Pulping and Bleaching Course is coming August 5-6, 2013, at the TAPPI Training Facility.
This course is efficiently and expertly planned and taught by one of the world's most recognized educators in the pulp and paper industry, Dr. Michael Kocurek, Emeritus Professor, North Carolina State University. In just two days, you'll gain a valuable overview of kraft operations that would normally take nearly 15 days in other, more comprehensive training.
The TAPPI Introduction to Kraft Pulping and Bleaching Course is designed to:
- Expand overall understanding of kraft pulp mill operations
- Broaden awareness of how one part of the process affects other operations
- Demonstrate the affect of processes on kraft pulp quality
- Build confidence for better interaction among experienced process engineers and operators
- Help you troubleshoot product quality problems.
Participants will learn specifically about:
- Wood and fiber raw materials
- Preparation of wood and chips for pulping
- Preparation of white liquor
- Pulping terminology, pulp properties, and tests
- Batch and continuous cooking
- Kraft pulping chemical reactions
- Pulping variables and effects on properties
- Trends in kraft pulping and bleaching
- Brown stock washing
- Screening and cleaning
- Bleaching and oxygen delignification
- The pulp mill biorefinery.
Who Should Attend?
This course is ideal for anyone new to the kraft pulping process, particularly process engineers and operators.
Learning Outcomes
After successfully completing the course, participants should be able to:
- Describe and define kraft pulp mill processes, equipment, operating variables, and terminology, in order to increase ability to improve operations and pulp quality
- Recognize how one part of the process affects other operations, in order to increase awareness of thinking on a mill wide scale
- Interpret how the process variables affect pulp quality, in order to improve pulp quality and troubleshoot variations in quality
- Extend awareness of the complex environmental challenges associated with kraft pulp production.
Please register soon. Only 25 seats are available for this course to ensure the most beneficial interaction among attendees and the instructor.
##SHARELINKS##
|
The 2013 TAPPI PEERS Conference, September 15-18, in Green Bay, Wis., USA, has announced the detailed technical program focusing on sustainable manufacturing and other pressing business and technical questions faced by pulp and paper companies as they manage raw materials, assets, regulatory requirements, and production assets. Register now and save.
In addition to the peer-reviewed technical program, Keynote Speaker Robert Feeser, SVP of Packaging with MWV, will share his insights on the day-to-day challenges he faces as he oversees the company's primary mill-based manufacturing businesses in the U.S. and Brazil. PEERS will also offer exclusive networking opportunities and insight into new technologies that can help you optimize your mill operations.
For 2013, PEERS will be co-located with the 10th Research Forum on Recycling and the International Bioenergy and Bioproducts Conference, creating a value-added opportunity for you to expand your learning, networking, and resources by attending all three events.
Learn more about the TAPPI PEERS Conference.
##SHARELINKS##
|
The 2013 TAPPI Linerboard/Medium Manufacture Course, August 13-15 at the TAPPI Training Room, in Peachtree Corners, Ga., USA, is designed to help increase your understanding of linerboard and medium performance properties and manufacturing to improve corrugated box performance and runnability.
This intermediate-level course is ideal for process engineers and operators in linerboard and medium manufacturing facilities and converting plants with a more intermediate background. For those participants who require an overview background on pulp and papermaking technology, there will be an optional one day Introduction to P&P on Monday afternoon, August 12, prior to the beginning of the main course on Tuesday. This supplemental session is intended for corrugators, new P&P mill and supplier personnel, and those without exposure to pulp and paper operations.
If you are looking to increase your understanding of linerboard and medium performance properties and how they are achieved, build your confidence in interacting more knowledgeably within the mill with suppliers and with corrugators, and improve manufacturing operations to produce a more competitive product, then this course is for you.
There are only 25 seats are available for this course. Register now to reserve your spot.
##SHARELINKS##
|
The corrugated packaging and converting industry is heading for Indianapolis, Ind., USA, October 7-9, 2013, for TAPPI CorrExpo 2013. The JW Marriott is the waypoint where ideas turn into innovation. Join your colleagues to take advantage of highly-sought-after speakers, seminars, workshops, exhibits, and programs you don't want to miss:
- There will be two keynote presentations - Bob Chapman, CEO and chairman of Barry-Wehmiller, and Alexander Toeldte, president and CEO of Boise Inc.
- Extensive networking and sales opportunities on the sold-out exhibit floor
- Training and insight from the best in the industry
- A cutting-edge technology showcase exhibit of innovative trends and design
- Opportunity for one-on-one meetings with top-level attendees
- Problem solving with industry experts
- Numerous special events, including a welcome reception, golf tournament, gala at the Indianapolis Motor Speedway, and spouse/guest program
- Eye-opener sessions tackling timely topics affecting box plants today, with plenty of time for questions and interaction with the speakers
- Complimentary workshops on Wednesday afternoon for all registered exhibit visitors.
View the full program to see what's in store for you this October.
Register today.
##SHARELINKS##
|
The TAPPI Centennial Celebration will be a multi-year long series of outreach events and educational offerings showcasing the proud history and promising future of the global pulp, paper, packaging, and related industries. This once-in-a-lifetime event will expand public awareness, foster further connection, and provide outstanding opportunities for collaboration, growth, and investment in our future for all of those involved. Goals for the TAPPI Centennial Celebration are:
- To honor TAPPI's 100 years of connection, education, and advancement as a foundation for the sustainable success of our members, our industries, and the world we share
- To recognize the achievements of those who built our industry and to inspire those who seek to build its future
- To celebrate the contributions and innovations of the global pulp, paper, and packaging industries to human culture, commerce, health, and social advancement
- To sustain the industry and support its growth, vitality, and future through the TAPPI Foundation.
We invite you to be a part of this momentous event. The sooner you join us the more opportunities there are for recognition of your company, its products, and key innovations. Keep in mind that an early commitment allows you to spread your investment over multiple years' budgets.
For more information on sponsorship and volunteer opportunities please contact dbell@tappi.org.
The sponsorship prospectus can be downloaded online.
##SHARELINKS##
|
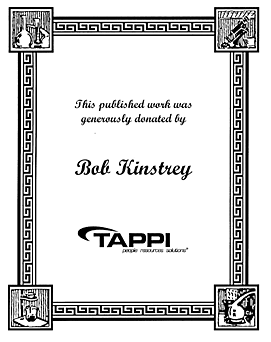
Do you have a history book gathering dust on your shelf? TAPPI's 100th year is coming soon and we are looking for donations to the TAPPI Library. Specifically, we are interested in histories of companies and mills in the paper and packaging industry (both producers and suppliers). Each donated book will have a bookplate in the front cover recognizing the donor. For more information please contact David Bell.
Please send books to:
c\o David Bell
TAPPI
15 Technology Parkway, South
Suite 115
Peachtree Corners, Georgia 30092
##SHARELINKS##
|
|
|