Over the Wire
TAPPI
Weekly Spotlight
Buckeye Technologies Inc, Memphis, Tenn., USA, reports that during a special stockholders' meeting this past week its stockholders approved the Agreement and Plan of Merger, dated April 23, 2013, by Georgia-Pacific, GP Cellulose Group (purchaser), and Buckeye. More than 84% of the total outstanding shares of Buckeye common stock eligible to vote as of July 8 were voted in favor of adopting the merger agreement.
Buckeye stockholders also approved the non-binding advisory proposal regarding merger-related compensation with a vote of more than 83% of the total outstanding shares of Buckeye common stock eligible to vote as of the July 8 record date.
On closing of the transaction, Buckeye will become an indirect, wholly-owned subsidiary of Georgia-Pacific, and Buckeye stockholders (other than Buckeye stockholders who have properly exercised rights of appraisal) will receive $37.50 in cash, without interest and subject to any withholding of taxes for each share of Buckeye common stock owned at the time of the transaction's closing.
Consummation of transaction remains subject to the expiration or termination of the waiting period under the Hart-Scott-Rodino Antitrust Improvements Act of 1976, along with the satisfaction of other customary closing conditions.
##SHARELINKS##
|
Weakening cost competitiveness and shifts in global demand from developed markets to emerging markets are expected to force manufacturers in the Nordic nations of Denmark, Finland, Norway, and Sweden to cut around 200,000 production jobs over the next five to seven years unless the region acts decisively, according to a new report by The Boston Consulting Group (BCG), Boston, Mass., USA. The report, titled Revitalizing Nordic Manufacturing: Why Decisive Action Is Needed Now, warns that such continued erosion of manufacturing—a foundation of Nordic economies since World War II—would have significant economic consequences. The region has already lost nearly 1 million production jobs, a decline of 40% since 1980.
Further job losses could exacerbate already high unemployment among Nordic youth and weaken the future competitiveness of key Nordic manufacturing industries—such as wood products, electronics, machinery, and transportation equipment—the report says. Nordic service industries would suffer, too, because many services jobs are connected to manufacturing.
"Manufacturing has historically been a critical driver of economic growth, employment, and healthy trade balances in the Nordic economies," says BCG partner Andreas Alsén, a coauthor of the report. "Urgent policy action is required on a number of fronts to keep the region's competitiveness from eroding further."
The biggest challenges for Nordic manufacturing are relatively high labor costs, explains the report, which elaborates on research previously released in Denmark and Sweden. Despite rapid wage increases in emerging markets, average manufacturing labor costs remain 80% to 90% lower in China and Eastern Europe. Average manufacturing labor costs in Germany are around 20% lower than in the Nordic region, while in the U.S. they are around 40% lower.
"Because Nordic wages are also projected to keep rising for the rest of this decade, the cost gap with emerging markets is unlikely to shrink enough to improve the region's competitiveness in the near term," explains coauthor Ian Colotla, who leads BCG's Operations practice in Denmark. "And the cost gap with Germany and the U.S. is likely to widen."
An aging workforce that will likely lead to a future talent shortage and rigid labor rules in three out of four Nordic countries also undermine Nordic competitiveness. According to the Global Competitiveness Report 2012-2013 by the World Economic Forum, Sweden, Norway, and Finland rank in the bottom twentieth percentile of 144 countries in terms of flexibility in setting wages. Sweden and Norway also rank in the bottom twentieth percentile in hiring and firing practices. Denmark is the exception because of its flexible labor rules.
The combination of factory downsizings with labor rules that encourage older employees to hold onto their jobs as long as possible effectively excludes young Nordic workers from the manufacturing workforce.
"Many companies, particularly small and midsize enterprises, avoid new permanent hiring unless absolutely necessary," says Børge Kristoffersen, a BCG partner based in Oslo. "Instead, they are hiring offshore." Partly as a consequence, the average age of Nordic workers is rising steadily. "If today's youth can't get entry-level jobs now, Nordic industries could face shortages of trained labor in the future as veteran workers retire," Kristoffersen explains.
A shift in global demand from developed markets to emerging markets—especially in Asia—increases incentives for Nordic manufacturers to relocate production. Consumption of manufactured goods in mature European economies is flat, for example, while in China it has been rising dramatically. Relatively high corporate taxes and regulatory costs also discourage investment in manufacturing capacity in Nordic economies.
Despite these handicaps, Nordic economies still have many advantages that can be leveraged. Each of the four economies ranks among the top 15 nations in the World Economic Forum's Global Competitiveness Index and scores high in international rankings of education quality, political stability, and ease of doing business. Sweden, Denmark, and Finland are also among the world's biggest spenders on research and development as a percentage of GDP.
The BCG report urges Nordic policymakers, private industry, and labor organizations to craft a "new deal" to strengthen manufacturing. The region should ensure that wage levels remain competitive, lower corporate tax rates, invest more in skills training, and improve programs to translate public investments in R&D into innovative products and new industries. Governments should also increase support for small enterprises to help them develop into the globally competitive manufacturers of the future.
"By taking decisive action now, the region can also ensure that manufacturing will remain a powerful contributor to future economic growth and job creation," says Pekka Vanne, a partner based in Helsinki who leads BCG's Industrial Goods practice in the Nordic region.
More information about the report is available online.
##SHARELINKS##
|
Scott Adams, director of sales for 3C Software, Atlanta, Ga., USA, recently visited TAPPI in Peachtree Corners, Ga., to discuss the new PIMA IT Committee. For more than 20 years, 3C Software has provided pulp and paper customers a modeling solution that delivers standard and actual grade costing by paper machine, grade run and reel specific analysis, recipe management, expense allocations, rate build-ups, and forward-looking planning tools.
In the photo below (l-r) are Amanda Thomas, TAPPI, Scott Adams, 3C Software, and Scott Springmier, TAPPI.
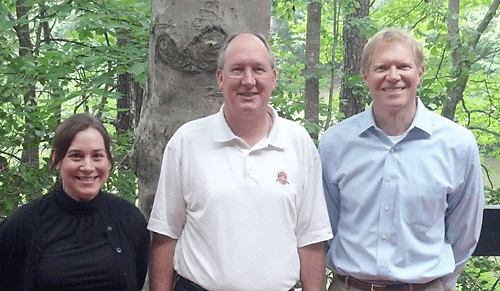
##SHARELINKS##
|
 The 2013 TAPPI PEERS Conference in Green Bay, Wis., USA, September 15-18, focuses on advances and emerging developments in the kraft pulping and bleaching arena as well as the chemical recovery island. In the pulp bleaching area, Session 11 on Tuesday, September 17, from 8:30 a.m. – 10 a.m., looks at new approaches with oxygen and ozone and explores results some mills are experiencing.
In the first of two papers in this session, Niclas Andersson of BTG Instruments examines a new sensor tool and control concept that measures the concentration of dissolved lignin in the filtrate portion of pulp suspensions using a unique principle based on optical measurement. A key characteristic of the sensor is the ability to perform the measurement even in the present of pulp fibers, and also that it is pre-calibrated. The sensor has two major applications, partly related—improving efficiency in washing stages, and optimizing chemical charges.
As Andersson explains, pulp washers are critical unit operations that seldom bottleneck production, especially in lines running much above nominal production. At the same time, there is a large optimization potential in finding the balance between using excess of wash liquor, thus directly increasing the energy need in evaporation, and achieving a sufficient purity level of washed pulp going to the bleaching process. Inline probes for conductivity and occasionally refractive index are sometimes used to control washers. Both principles suffer from not measuring the critical dissolved lignin component.
Chemical charging control, Andersson notes, can be optimized taking not only washed fiber kappa but also the dissolved lignin into account. Results from several mill trials have shown that the contribution from dissolved lignin in the filtrate portion of the pulp is up to 30% of the total bleach load (i.e. fiber kappa and filtrate kappa combined) in the bleach plant inlet, and even more up-stream in the fiberline. Hence, chemical savings can be achieved taking this component into account, compared with only measuring the washed fiber kappa.
In the second paper of the oxygen and ozone bleaching session, Brendan Van Wyk with Xylem looks at what he calls "The A to Z Upgrade in Eucalyptus Pulp Bleaching." Van Wyk explains that eucalyptus pulp bleaching was modernized in the 1990s with the industry's conversion to ECF bleaching and the discovery of the high content of hexenuronic acids (HexA) in eucalyptus pulp. Today the use of acid hydrolysis for HexA removal is becoming a common practice and is carried out in the first bleaching stage of sequences such as DHT-EOP-D-P and A/D-EOP-D-P for eucalyptus pulp. However, he says, the needs to lower operating costs and comply with ever stricter ecological regulations still drives the pulp and paper industry to improve on traditional ECF bleaching.
Ozone bleaching, Van Wyk continues, has successfully proved to be an economical and sustainable technology and can be widely implemented to treat the high HexA content found in eucalyptus pulp. The competitive operating costs of Z-ECF bleaching with ozone results not only from the replacement of chlorine dioxide and hydrogen peroxide by ozone but also the opportunity to increase bleach plant closure and therefore extend the use of oxidized white liquor in place of caustic soda. Moreover, such a practice also reduces operating and investment costs in the effluent treatment plant. Nevertheless, the ozone bleaching alternative is still, from time to time, put aside during the discussions for mega pulp mill projects, Van Wyk says. The estimated savings in bleaching chemicals are not always seen as significant enough to justify the risk of implementing "green technology."
Van Wyk's paper describes a new way of using ozone—the combination of a hot acid stage A in front of an ozone stage Z. There is clear industrial evidence, he says, that maximum efficiency from the chemical cost viewpoint is achieved through an A-Z combination, since the acidic extraction of HexA is intelligently complemented with more selective ozone delignification. Extensive lab studies and the optimization work carried out in the four mills running such a process demonstrates that the difference is significant enough to overwhelm the ECF status quo and result in a new breakthrough in eucalyptus pulp, Van Wyk concludes.
More information on the 2013 PEERS Conference, and more information on the International Bioenergy and Bioproducts Conference being held September 18-20 in conjunction with PEERS are available online.
##SHARELINKS##
|
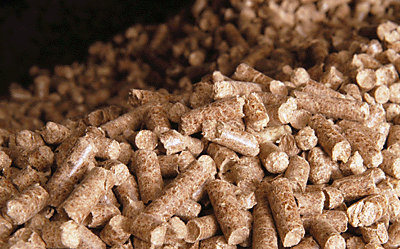 The Northwest Advanced Renewables Alliance (NARA), initiated in 2011, is an example of a new approach to establish sustainable production of bioenergy and bioproducts. Linda A. Beltz, Ph.D., NPDP, director, Technology Partnerships for Weyerhaeuser, will present NARA: Public Private Partnerships to Advance the Forest Products Industry at TAPPI's International Bioenergy and Bioproducts Conference, Sept. 18-20, 2013, in Green Bay, Wis., USA.
Discounted registration has been extended to tomorrow, Friday, August 23, so there is still time to take advantage of discounted registration rates and hear more about NARA.
NARA is a public-private partnership between companies, universities, and other organizations to develop jet fuel and co-products from forest-based feedstocks. Weyerhaeuser announced its engagement with NARA as a subcontractor to support investigations into feedstock development, including sustainable production, cost-effective use of under-utilized harvest material, and conversion of lignin into value-added products. Weyerhaeuser also contributes to NARA in team leadership and development of Phase and Gate processes.
NARA's supply chain approach provides a platform for integration with the traditional forest products industry, which has been evaluating forest biorefineries and the production of energy, fuels, and chemicals from biomass for many years. Using bio-based wood materials instead of fossil fuels for aviation fuel and valuable co-products seems like a great idea, but there has been limited commercial success. NARA's public-private partnership is a new, promising approach to successful commercial development.
Learn more about NARA's progress to date, and the latest in advancing biorefineries in the forest products industry at IBBC 2013. With eight, single-track sessions, you will also be able to learn the latest developments in forest-based biorefineries. Build your relationships with key decision makers at the ample networking opportunities both on the exhibit floor and the conference dinner and receptions.
Come a few days early and also attend the PEERS Conference, TAPPI's leading event for those involved in mill pulping operations, engineering projects, and environmental processes. The sustainability program at PEERS looks at fiber issues, industry innovation, and responsible supply chain issues. Also included is the 10th Research Forum on Recycling.
Following IBBC, you can continue your professional development by attending the TAPPI Biorefinery Course. Spend two days with a team of experts and your peers to learn about advanced biorefinery fundamentals, setting biorefinery strategy, and biorefinery techno-economics and case studies.
##SHARELINKS##
|
From the Experts
Wisconsin news outlets have been highlighting results of a newly released 10-year economic study commissioned by the Wisconsin Economic Development Corp. (WEDC). According to reports and the WEDC web site, pulp and paper manufacturing has dropped from first to third among Wisconsin businesses The full study is available online. This study looks into some of the possible reasons why paper is becoming less significant in Wisconsin.
At one time, Wisconsin was a top producer of pulp and paper in the U.S. Today, Southern States like Georgia, Alabama, and Louisiana have overtaken Wisconsin (see Figure 1).
The industry is shifting to wider and faster machines to feed the large 96 million ton U.S. paper demand. These new machine investments are being made in states with raw materials, proximity to population centers (the market), tax-friendly environment for business and individuals, and an amenable labor force.
Wisconsin's machine base is becoming less competitive as expansions of new, more productive machines move into states like Georgia. Wisconsin now ranks 31st in production rate per inch of width where Georgia ranks 8th. The end result is a distinct cost disadvantage, with Wisconsin ranked 31st lowest in cost per ton compared with Georgia which is 14th. So, why is this?
Wisconsin has the wood raw material base, but is at a disadvantage in other key drivers. Georgia is the largest producing state in 2013. A fact table on the WEDC web site shows that compared with Wisconsin, Georgia has lower corporate tax rates (6.0% versus 7.9%), lower personal income tax top bracket ($7,000 versus $232,640), a lower Unemployment Insurance Tax Rate (2.62% versus 3.6% for new employers), and Georgia prohibits union security agreements while Wisconsin protects them. Another key driver is population demographics. The population is shifting to southern states and their increasingly concentrated markets, leaving Wisconsin with a transportation disadvantage.
Reduced reliance on printed media is another important dynamic impacting Wisconsin's paper industry. The digital age is taking its toll on paper use across the country. U.S. paper production demand in some key segments has been falling off for the last five years (see Figure 2).
Some grades like packaging are experiencing steady performance while consumer driven tissue and towel has steady growth tied to population. Wisconsin's problem becomes apparent when looking at the same 10-year trend for the state. Wisconsin is experiencing drop offs across all grades with the possible exception of packaging (see Figure 3).
Losses in printing and writing is the most profound as smaller and older machines lose competitiveness in a shrinking market. Grades like tissue and towel and specialties are growing slowly on a national base but trending down in Wisconsin. Even packaging, which is experiencing solid growth nationally, is barely holding rates in Wisconsin. An improving economy nationally may help soften the blow to Wisconsin's paper business, but it will likely take a dramatic change in the state's business environment to stabilize or reverse the declining trend.
About the Author
Bill Burns is a senior consultant at Fisher International Inc. and can be contacted at bburns@fisher.com. The source for market data and analyses in this article is FisherSolve™, which describes the assets, capacity, and costs of every pulp and paper mill in the world making 50 tpd or more. More information about FisherSolve is available online.
##SHARELINKS##
|
Market Roundup
Total U.S. boxboard production increased by 1.6% compared with July 2012, and increased 0.4% from last month, according to the AF&PA, Washington, D.C., USA, July 2013 U.S. Paperboard Report released this week. Unbleached kraft boxboard production decreased from the same month last year, and decreased compared with June 2013. Total solid bleached boxboard and liner production increased compared with July 2012, but decreased compared with last month.
The production of recycled boxboard increased compared with July 2012, and increased when compared with last month.
##SHARELINKS##
|
Growing demand for paper in China has not only forced the country to import large volumes of pulp to supply the country's paper machines, but also resulted in investments in new pulp production within China, according to the Wood Resource Quarterly (WRQ), Seattle, Wash., USA. Because of a lack of competitively priced wood fiber in China, the two pulp companies with the largest pulp mills in the country, Asia Pacific Resources International Ltd (APRIL) and Asia Pulp and Paper (APP), are procuring much of their wood fiber needs from out-of-country sources. As a consequence, importation of wood chips to China has surged the past few years.
In just five years, China's import value for wood chips has increased from $180 million dollars in 2008 to $1.3 billion dollars in 2012. This year the estimated import value could be close to 1.5 billion dollars, according the WRQ.
It was only been a matter of time for China to become the largest importer of hardwood chips in the world. In the second quarter of this year, China surpassed Japan with the record importation of almost 2.4 million cubic meters of chips.
Although there have been sporadic shipments of chips from Latin America, Malaysia, and South Africa during 2012 and 2013, there are really only four countries that have been supplying China with wood fiber the past few years. Those countries are Australia, Indonesia, Thailand, and Vietnam, with Vietnam accounting for more than half of the total import volume.
Another interesting development is that the average cost of imported wood chips has declined by almost 6% from the second quarter of 2012 to the second quarter of 2013, WRQ reports. The biggest price decline has been in Australian chips, which have fallen more than 11% in one year. Because of this price drop, in the second quarter of this year, Australia exported its highest quarterly volume to China since 2010.
With continued plans to expand domestic pulp manufacturing in China, it can be expected that shipments of wood chips, both softwood and hardwood, is going to increase in the coming years, WRQ says.
More information is available online.
##SHARELINKS##
|
North American lightweight coated (LWC), No. 5 – 40 lb, prices averaged $875 per ton in July, up $5 from June, according to Make Wilde, senior analyst with Deutsche Bank. LWC prices ranged from $680 to $1,240 per ton.
Coated free sheet (No. 3 rolls – 60 lb.) prices averaged $950 per ton in July, an increase of $5 per ton from June. CFS prices ranged from $720 to 1,100 per ton in July.
Uncoated free sheet (20 lb. – Repro Bond) prices averaged $1,015 per ton last month, which was flat compared with June. UCFS prices varied from $650 to $1,200 per ton in July, Wilde noted.
##SHARELINKS##
|
Sweden's paper and paperboard production fell by 6.2% to 2.7 million metric tons in the second quarter of this year compared with the second quarter of 2012. Newsprint output continues to decrease, falling by 20%. Printing paper fell by 5%, and other paper and paperboard grades decreased by 2%, according to a Swedish Forest Agency report issued this past week.
Comparing the first half of 2013 with 2012, Sweden's paper production decreased by 4.3% and wood pulp production dropped by 2.5%.
Production of wood pulp in Sweden decreased by 4.4% to 2.9 million metric tons in the second quarter of 2013 compared with the same quarter in 2012. Production of kraft pulp fell by 3% in the second quarter of this year compared with the same quarter of last year.
##SHARELINKS##
|
According to the AF&PA (Washington, D.C., USA) July 2013 Kraft Paper Report published this week, U.S. kraft paper shipments in July were 135,500 tons, an increase of 3.1% compared with the prior month. Bleached kraft paper shipments increased year-over-year 11.4%, but the 4.8% year-over-year decline in unbleached kraft paper shipments was enough to bring overall kraft paper shipments down 2.7% year-over-year.
Total month-end inventory increased 2.5% to 73,000 tons this month compared with June 2013 month-end inventories.
##SHARELINKS##
|
The price of North American NBSK (northern bleached softwood kraft) market pulp in July was $950 per metric ton, which was flat compared with June 2013, according to Mark Wilde, senior analyst with Deutsche Bank. Wilde noted that NBSK market pulp prices in July ranged from $600 to $1,100 per metric ton in North America.
##SHARELINKS##
|
U.S. Containerboard production increased 4.1% over June 2013 and 5.3% over the same month last year, as reported by AF&PA (Washington, D.C., USA) in its July 2013 U.S. Containerboard Statistics Report released this week. The month-over-month average daily production increased 0.7%.
The containerboard operating rate for July 2013 dropped 0.4 points from June 2013, from 99% to 98.6%.
##SHARELINKS##
|
Pulp & Paper
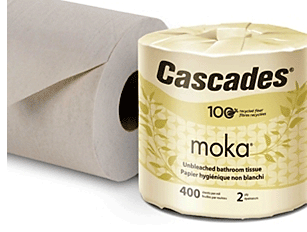 Cascades Tissue Group, Candiac, Que., Canada, reports that its Moka® 100% recycled, unbleached bathroom tissue has been honored with a bronze Stevie Award in the International Business Awards (IBA). Honored in the "Best New Product or Service of the Year—Business-to-Business Products" category, the commercial tissue, with its beige color, was praised for offering "uncompromised softness and hygiene qualities with a recipe that significantly reduces environmental impact."
Suzanne Blanchet, Cascades Tissue Group CEO, said that "our Cascades Moka bathroom tissue is a true example of what innovation and care for the environment can bring to a marketplace hungry for products that are kind to the environment. Practicing sustainability is in our DNA at Cascades and guides everything we do."
Cascades will receive its award on October 14 at a gala event in the W Hotel in Barcelona, Spain. This is the second time in recent years that a Cascades product has won a Stevie Award. Cascades Antibacterial won a 2011 Stevie Award for Best New Product in the Health Category.
Cascades Tissue Group is the fourth largest producer of tissue paper in North America. Founded in 1964, the company produces, converts, and markets packaging and tissue products that are composed mainly of recycled fiber. The company employs more than 12,000 people who work in more than 100 units throughout North America and Europe.
##SHARELINKS##
|
Rentech, Inc., Los Angeles, Calif., USA, this week reported that a subsidiary of the company has closed the sale of approximately 450 acres in Natchez, Miss., to Adams County, Miss., for proceeds of approximately $9 million. D. Hunt Ramsbottom, president and CEO of Rentech, said that "the sale of the Natchez site is consistent with our stated intention to dispose of our non-core alternative energy related assets."
Ramsbottom added that "we remain focused on the significant opportunities within our newly launched wood fiber processing business as well as growth in our nitrogen fertilizer business."
Rentech owns and operates wood fiber processing and nitrogen fertilizer manufacturing businesses. The wood fiber processing business consists of wood chipping services and the production and sale of wood chips, through a wholly-owned Georgia-based subsidiary, Fulghum Fibres Inc., and the development of wood pellet production facilities. Rentech also owns the intellectual property, including patents, pilot, and demonstration data, and engineering designs for a number of clean energy technologies designed to produce certified synthetic fuels and renewable power when integrated with third-party technologies.
##SHARELINKS##
|
Parteks Paper Co., Turkey, has ordered from Toscotec, Lucca, Italy, a new tissue line to be installed at its mill in Kayseri, capital of the same district in the Central Anatolian region. The line will be started up in the first half of 2014.
The delivery, based on an intensive energy-saving concept, includes the approach flow featuring Toscotec technology TT SAF®, broke line, a MODULO-PLUS tissue machine with single-layer headbox, single press configuration, and a Toscotec steel yankee dryer TT SYD-12FT. The supply will also include an electrification and controls package, tissue machine auxiliaries such as a natural gas heated hood, and the steam and condensate system provided by Toscotec associate Milltech. A two-unwind-stands Toscotec rewinder TT WIND-P will complete the package.
With a width of 2,85 meters and a design speed of 1,600 m/min, the new production line will produce 75 metric tpd of high-quality facial, toilet, and towel grades, despite the fact that the mill is located 1,050 meters above sea level. The new Toscotec project will be focused on reduced energy consumptions, use of selected raw materials in the manufacturing process, recovery and re-usage of process water, low emissions (noise and pollutants), and green energy adoption with the steel yankee dryer technology.
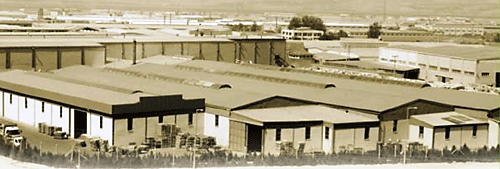
Parteks is a fully integrated producer of tissue paper for at-home and away-from-home markets, corrugated containerboard, and fluting papers. The existing mill that houses the TM 1 tissue machine (started up in 2007) and the PM 1 fluting machine and corrugating line covers an area of 100,000 square meters. The mill's converting facility for tissue is nearby.
Parteks' tissue paper is produced with recycled paper and virgin pulp. Panda and Senta are tissue brands produced by Parteks.
##SHARELINKS##
|
Thiele Kaolin Co., Sandersville, Ga., USA, was presented three safety awards at the 2013 Georgia Mining Association conference. All three of the awards were granted on a basis of length of work completed without a lost time accident. The Avant-Ennis Mine and mill was recognized for having worked 12 years and 2 months, Hobbs Clay Mine for having worked 4 years and 10 months, and Reedy Creek Division Plant for having worked 4 years and 4 months accident free.
Thiele notes that these awards are a "testament" to the company's safety oriented culture, "made possible by the focused employees and management personnel that strive to maintain an injury free workplace."
Thiele mines, processes, blends, and delivers a full spectrum of kaolin coating and filler pigments tailored to meet the specific needs of its customers.
##SHARELINKS##
|
Verso Paper Corp., Memphis, Tenn., USA, reports that its common stock price has fallen below the New York Stock Exchange's continued listing standard. The NYSE notified the company that the average closing price of Verso's common stock must be at least $1.00 over a consecutive 30 trading-day period. As of August 14, the date of the NYSE notice, the average closing price of Verso's common stock over the past 30 trading days was $0.97 per share.
To maintain its NYSE listing, Verso has until February 14, 2014, which is six months from the date of the NYSE notice, to bring the closing share price and the average closing share price of its common stock back above $1.00. Verso has notified the NYSE that it intends to cure the share price deficiency. During the cure period, Verso's common stock will continue to be traded on the NYSE, subject to Verso's compliance with other NYSE continued listing requirements.
Separately, and as previously disclosed, Verso has appealed the NYSE staff's determination to delist its common stock due to the company's failure to satisfy the NYSE's continued listing standard requiring that it have an average market capitalization of at least $75 million over a consecutive 30 trading-day period. The review committee of the NYSE's board of directors currently is scheduled to hear Verso's appeal on September 10.
##SHARELINKS##
|
Xerium Technologies Inc., Youngsville, N.C., USA, announced plans to build a new, high-end press felt plant near Shanghai, China. The greenfield plant will employ the industry's most advanced press felt manufacturing technology capable of supplying the highest quality products for the most demanding machines in the region, Xerium noted.
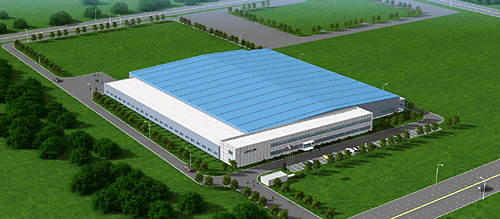
Production at the new plant is expected to begin by the first quarter of 2015. Xerium said that its decision to build a new machine clothing plant in China is based on several important business reasons:
- The company's sales in Asia are growing differentially higher than in other parts of the world and third party market estimates are for these consumption rates to continue for a long time.
- There is strong customer preference for the company's high-end press felt products in Asia, especially in tissue. Today, the company supplies products to the region from 21 of its global plants.
- Xerium is committed to reducing its overall cost structure by repositioning its manufacturing footprint in low cost countries. The company already is expanding its current operations in Mexico, Brazil, and China. This investment will be another step forward in that direction and the building plant site is being designed to accommodate future expansions to further lower Xerium's cost structure materially.
- This new plant enables quick turns for customers with short lead time and emergency coverage requirements.
The company will fund the investment from its normal cash flow and capital structure and Xerium's overall capital spending will be substantially similar to previous estimates.
"This new low-cost, high-tech plant in China is another big step forward for Xerium," said Harold Bevis, Xerium's president and CEO. "This state-of-the-art facility will produce the most advanced press felts in the world and its quality processes are being modeled after our plant in Gloggnitz, Austria, which will create one of the best press felt facilities in the world. It will be a big advancement for our Chinese customers specifically as it will allow Xerium, for the first time ever, to provide quick in-county press felt service to the largest pulp, paper, and board market in the world. This new facility will immediately become our lowest cost plant and strengthen our global manufacturing base. Several options exist for the next steps in the China plant evolution, but no decisions have been made yet. We will do one phase at a time in a high-quality, low-cost manner and build from there."
##SHARELINKS##
|
Zhejiang Jingxing Paper, China, has ordered from Andritz, Graz, Austria, two new tissue machines with steel yankee dryers for its mill in Pinghu city, Zhejiang Province. The two new machines will produce high-quality facial and toilet paper. Startup of the machines is scheduled for the end of 2014 and mid-2015, respectively.
Zhejiang Jingxing Paper is one of Asia's largest linerboard producers and is now entering the tissue business.

The tissue machines, both of the type PrimeLineST, are designed to operate at speeds up to 1,900 m/min and produce paper at a width of 2.85 meters. They will be equipped with 18-ft.-dia. PrimeDry steel yankees with head insulation. The steel yankees, in combination with a steam-heated hood, enable high drying capacity at minimal energy consumption.
##SHARELINKS##
|
Containerboard/Packaging
Evergreen Packaging, Memphis, Tenn., USA, this week launched the fall 2013 Made by Milk Carton Construction Contest, themed "Transportation." Schools across the U.S. can win up to $5,000 by having classroom teams design and construct creations made from empty school milk cartons, which students save from their school lunches. The deadline for submissions is November 15.
Evergreen Packaging notes that the Made by Milk program underscores its commitment to promote milk consumption and carton recycling among school-aged children," said Katie Lewis, associate marketing manager. "The contest encourages students to be creative and work together to design and construct transportation-themed projects out of cartons. It's also a hands-on exercise on how cartons can be reused and recycled instead of thrown away."
Evergreen Packaging produces gable-top cartons in North America. Since the 2012 inception of the Made by Milk contest, the company has awarded cash prizes to 20 winning schools across the country.
Students in grades 1–12 are eligible for the Made by Milk contest. To enter, classroom teams are required to collect a minimum of 100 empty milk cartons to use in their carton creations, and write a 200-word essay about how their school will utilize the prize money.
Winning categories include:
- Grand Prize – $5,000
- People's Choice Award – $2,500
- Elementary Winners (3 total) – $1,500
- Middle School Winners (3 total) – $1,500
- High School Winners (3 total) – $1,500.
More details on the Transportation theme, rules, and photos of previous winning creations are available online.
##SHARELINKS##
|
Papcel, Litovel, the Czech Republic, reports that it has completed the installation of a reconstructed paper machine at the joint venture Mayak-Vega mill in the Penza region of Russia. The 2,600 mm-wide at the reel) machine will produce containerboard fluting and testliners. It has a production capacity of 70,000 metric tpy and an operating speed of 700 m/min.
The 11,000 sq. meter main building has been constructed, network engineering is completed, and the automation system has been installed, according to Papcel. Startup of the machine is set for the beginning of September. The Papcel project reportedly is valued at EUR 22.7 million.
The machine is reconstructed from a unit dismantled at Alce in Italy beginning in August 2011. It may also be used to produce a plasterboard in the future.
##SHARELINKS##
|
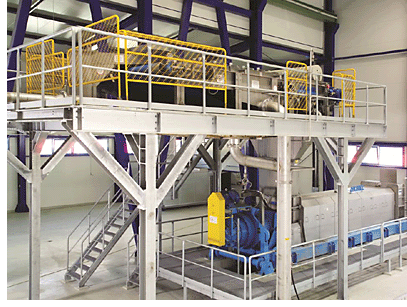 Stora Enso, Finland, has ordered from Andritz, Graz, Austria, a new sludge dewatering line for thickening and dewatering of fibrous sludges at its board mill in Skoghall, Sweden. With a capacity of up to 750,000 metric tpy, Skoghall is one of the world's largest producers of liquid packaging board. Startup of the new plant is scheduled for April 2014.
The order includes a gravity table and a sludge screw press to process up to 50 metric tons of mixed sludge per day, thus significantly increasing the capacity of the existing sludge dewatering plants. The sludge to be dewatered consists of a mixture of fibrous and biological sludges, as well as chemical sludges from the mill's CTMP line. Andritz notes that the sludge screw press dewaters the mixed sludge to the highest possible dryness that can be achieved today by mechanical means.
To meet new process requirements resulting from the plant extension, Stora Enso's order also includes the rebuild of an existing Andritz belt press supplied in 1989. Due to the higher final dryness achieved through the dewatering lines in the future, Stora Enso Skoghall will be able to feed a higher amount of dewatered sludge to the power boiler and operate it with greater energy efficiency.
##SHARELINKS##
|
Zumbiel Packaging, Hebron, Ky., USA, has joined the U.S. EPA's Green Power Partnership (GPP). The Cincinnati-area paperboard packaging company has committed to purchase 5% of its electricity from renewable sources to reduce the environmental impact of its operations.
As part of the GPP, Zumbiel purchased Renewable Energy Certificates (RECs) for wind energy. Shifting 5% of its use to sustainable wind energy will avoid approximately 544 tons of CO2 emissions annually—the equivalent of taking 103 passenger cars off of U.S. roads. The GPP program is only one part of the sustainability plan for Zumbiel Packaging, which has been a member of the EPA's Energy Star program since 2008.
The U.S. Green Power Partnership is a voluntary program that seeks to offset carbon emissions by increasing the use of renewable sources of energy. Participating companies purchase a portion of their energy from renewable sources. Using renewable sources helps companies reduce their carbon footprint, stabilize their energy costs, and support the continued development of the renewable energy industry.
"The Green Power Partnership is a natural fit for our business and environmental priorities," says Tom Zumbiel, marketing director. "By purchasing wind power, Zumbiel Packaging is able to engage with our local community on environmental issues, do our part to protect the environment, and take a leadership position in supporting a sustainable future."
As one of the largest independent paperboard packaging companies in the U.S., Zumbiel has provided a wide range of innovative packaging solutions to clients in the beverage, food, and general consumer product markets for 170 years.
##SHARELINKS##
|
Nanotechnology
The 2013 Agenda 2020/Forest Service/University Consortium on Cellulose Nanotechnology Meeting will be held at Oak Ridge National Laboratory (ORNL), in Oak Ridge, Tenn., USA, October 29-30. Because the meeting is being held at ORNL, security clearances need to be obtained to get on site. Names of all attendees are needed at least four weeks prior to the meeting. Non-U.S. citizens can attend but need the full four weeks to make it through security checks (please send registration information no later than September 27).
As part of the meeting—in addition to hearing about all of the research program accomplishments and plans from the Agenda 2020/Forest Service/University Consortium—ORNL and NIST staff will also make presentations on the cellulose nanomaterial projects that they have underway. ORNL has also arranged for a more in-depth tour of its facilities to see capabilities that fit with nanocellulose interests. Included on the tour are:
- The Spallation Neutron Source (combined with the Center for Nanophase Materials Science or CNMS)
- BioEnergy Science Center, and High Temperature Materials Laboratory (HTML).
Information about the Spallation Neutron Source, Center for Nanophase Materials Science, and the BioEnergy Science Center is available online.
The registration fee will be $45 to cover the costs of lunches and breaks. For information on registering, email, telephone, or fax Jane Kohlman at USDA Forest Service, Forest Products Laboratory, Madison, Wis., Tel: 608.231-9479; Fax 608.231-9567.
Make lodging reservations at the DoubleTree by Hilton Hotel Oak Ridge–Knoxville, 215 S. Illinois Ave., Oak Ridge, TN 37830; Phone: 865-481-2468. Reservations can also be made online. The group room rate is $91/night + tax. The block of rooms will be held until October 9.
##SHARELINKS##
|
New Products
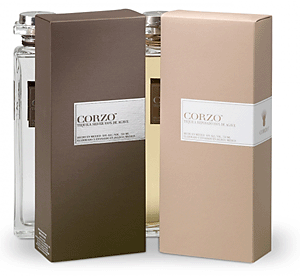 FiberMark, Brattleboro, Vt., USA, has announced a new portfolio of folding carton products specifically engineered to meet rigorous design demands of the upscale spirits packaging market. The dyed-through board materials offer deep color saturation that eliminates white edges in the finished product. FiberMark's manufacturing process ensures color consistency from lot- to-lot, which as FiberMark emphasizes, is a "must for high-end brands."
FiberMark's Premium Board Portfolio Includes:
- Grafton® – Premium board with an uncoated vellum finish
- Dorset® – Premium board with a matte pigment-coated finish
- Metal-X™ and Shimmer™ (K-Series) – Luxury board products with decorative coatings.
The new packaging boards are available in a wide variety of custom colors, including custom color duplex solutions, a wide variety of embossed patterns, and are all FSC certified, made in the USA, and include recycled content. Available in three calipers (12 pt, 18 pt, and 26 pt), the premium and luxury boards are strong and durable while providing a stylish, refined alternative to white SBS, FiberMark notes.
The company further points out that with excellent scoring, folding, and gluing properties and high resistance to cracking and scuffing, the boards are not only ideal for folding carton applications but are also well-suited for complimentary branding projects such as hang tags, special event invitations, and other corporate collateral materials.
More information is available online.
##SHARELINKS##
|
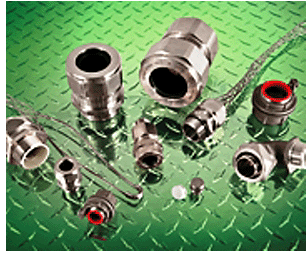 Remke, Wheeling, Ill., USA, has introduced an expanded family of corrosion-resistant stainless steel (CRSS) connectors. In sizes up to 3 in., the expanded family of CRSS Connectors includes standard cord connectors, liquid-tight conduit fittings, water-tight conduit hubs, jacketed metal clad cable connectors, and ventilation plugs. Custom stainless steel connectors in small or large quantities are also available.
Remke notes that its CRSS Connectors provide durability against corrosion, harsh climatic conditions, harmful environmental influences, and high humidity. The CRSS connectors are also recommended for use in wash downs or high moisture environments.
Features of the expanded connectors include:
- More sizes in stock of standard Type 304 stainless steel cord connectors with Type 316 available upon request (rated NEMA 4, 4X and 12)
- Seven conduit sizes in stock of Type 304 stainless steel liquid-tight conduit fittings rated IP 68 and NEMA 4X
- A complete offering of custom stainless steel connectors in small or large quantities (not available elsewhere)—custom products, specials, adaptations, and variations available to all customers
- More sizes and styles in stock of Type 316 stainless steel watertight conduit hubs that are rated NEMA 4, 4X, and 12
- More type 304 stainless steel jacketed metal clad cable connectors in stock with Type 316 available upon request
- Stainless steel ventilation plugs with three thread sizes in stock that are rated IP 69K (additional thread sizes and permeability levels available on request).
More information about the family of corrosion resistant stainless steel connectors is available online.
##SHARELINKS##
|
Voith, Germany, reports that it has reworked and further developed the technology behind its VariFlex two-drum winder. Along with simplified operation, special attention was paid to ensure robust safety technology. The winders up to 7 meters wide and with a roll diameter of 2,100 mm are the first components to come onto the market.
The Voith VariFlex winder is based on the two-drum concept. The roll set is wound in a roll bed formed by two winder drums. With the compact new VariFlex line, Voith has further developed its VariFlex S, M, and L two-drum winders and simplified their control technology.
It is primarily the roll geometry, the roll arrangement, and if applicable the covers that are important for the high productivity and consistent quality of the two-drum winder, Voith notes. Properly combined, they ensure high speeds, a reliable web run, good roll geometry, and reliable handling of large roll diameters as well. Depending on the requirements and design, production speeds of up to 3,000 m/min are possible without any problem, Voith says.
The modularly structured VariFlex was designed for a broad range of applications and due to different roll and cover combinations allows configurations for numerous paper grades. While new paper machines from Voith are already delivered with a winder, the new VariFlex was designed in particular for replacements or rebuilds on existing machines, which requires only very short shutdown and optimization times.
Since VariFlex is directly delivered with all drives included, Voith points out that customers benefit from fewer interfaces and especially short commissioning and system optimization timeframes. The specifically developed elastic covers for the winder drums, ElaGrip and ElaCare, ensure flawless winding quality even for demanding paper grades, according to Voith. Together with the VariPlus and VariTop single-drum winders, VariFlex covers the entire range of winders for all paper grades and characteristics.
##SHARELINKS##
|
Published Pricing
Ashland Water Technologies (AWT), Wilmington, Del., USA, a commercial unit of Ashland Inc., this week announced a 5% to 12% global price increase effective immediately, or as contracts allow, varying by country and product. Both business units, Pulp & Paper and Industrial Water Treatment, will implement these increases on most products within its portfolio around the world.
"Inflationary pressures associated with energy, transportation, and labor, combined with cost escalation in regulatory compliance and raw materials, make these increases necessary. We will continue to work in partnership with our customers to help mitigate these increases," said John Schumann, VP, Industrial Water.
Charles Robinson, VP, Pulp & Paper, added that "this action is necessary to continue to provide industry-leading product support and value to our customers."
##SHARELINKS##
|
People
Catalyst Paper, Richmond, B.C., Canada, has appointed Joe Nemeth president and CEO. Nemeth is an experienced pulp and paper industry executive bringing 30 years of background to his new role at Catalyst. His appointment is effective October 1.
Nemeth has held executive positions in sales, marketing, and operations and was, most recently, president and CEO of Canada-based Canfor Pulp. His leadership achievements include best of peer group financial performance, negotiation and oversight of major business and strategic development initiatives, and continuous improvement in operations, cost, and organizational management.
"Mr. Nemeth 's knowledge of the marketplace and his experience in the operational side of the pulp and paper process are well-matched with our requirements and will ensure the necessary momentum to keep pace with the very competitive global paper industry," said Catalyst Board Chairman and Interim CEO Leslie T. Lederer.
Nemeth holds an MBA from the University of Western Ontario and a Bachelor of Forestry from the University of British Columbia. He is a director of Fortress Paper Ltd. Born and raised in coastal British Columbia, Nemeth and his family make their home in the greater Vancouver region.
Catalyst Paper produces specialty mechanical printing papers, newsprint, and pulp. With three mills in British Columbia, Catalyst has a combined annual production capacity of 1.5 million metric tons.
##SHARELINKS##
|
Markku Honkasalo, LL.M., eMBA, has been appointed CFO of Valmet Corp. (pending Metso EGM approval and registration of the demerger). He will start in his new position on September 2, and will report to President and CEO Pasi Laine.
Honkasalo has previously worked as CFO, Rautaruukki Corp., and director, administration, legal, and HR at Myllykoski Corp. Prior to his career in industry, Honkasalo held a variety of positions in the banking sector.
As of January 2014, Metso's Pulp, Paper, and Power business is scheduled to begin operating as Valmet Corp., an independent, listed company.
##SHARELINKS##
|
SCA, Stockholm, Sweden, reports that Carl-Axel Olsson, group treasurer, will retire August 31. Johan Rydin has been appointed as his successor. Rydin has been employed by SCA Treasury since 1988 and will begin his new position on September 1.
SCA is a global hygiene and forest products company that develops and produces personal care, tissue, and forest products. It is the world's third-largest supplier of tissue. The company's sales are conducted in some 100 countries under brands including TENA and Tork, and regional brands, such as Lotus, Libresse, Tempo, and Libero.
##SHARELINKS##
|
Weyerhaeuser Co., Federal Way, Wash., USA, this week announced several changes to its senior management team. Larry Burrows, SVP, Wood Products, will retire on October 31. Cathy Slater has been named SVP, Oriented Strand Board, Engineered Lumber Products and Distribution, effective immediately. Adrian Blocker has been named SVP, Lumber, effective immediately. Weyerhaeuser also announced the retirement of Miles Drake, CTO and SVP Research and Development. Effective immediately, the company's R&D organization will report directly to Shaker Chandrasekaran, SVP, Cellulose Fibers.
Burrows has been Weyerhaeuser's SVP, Wood Products, since October 2010, and served as president of Weyerhaeuser Real Estate Co. from 2008 to 2010. Prior to those roles, he held various leadership positions at Winchester Homes Inc., a subsidiary of WRECO, including president and EVP.
Slater brings more than 25 years of forest industry experience to her new role, including leadership positions in the company's Cellulose Fibers and Wood Products businesses. She has been Weyerhaeuser's VP, Oriented Strand Board since 2011. Prior to that, she held leadership roles in the company's Wood Products segment, including VP for both engineered wood products manufacturing and veneer technologies. Before joining the Wood Products team, she held positions in the company's Cellulose Fibers business, including leadership roles at the Flint River and Port Wentworth, Ga., pulp mills, and leadership oversight for the company's operations in Alberta, which included the pulp, timberlands, OSB, lumber, and engineered lumber.
Blocker brings more than 30 years of experience to his new role, including forestland management, fiber procurement, consumer packaging, and wood products manufacturing of lumber, plywood, and laminated veneer lumber. He joined Weyerhaeuser in May 2013 as VP, Lumber, and prior to that served as CEO of the Wood Products Council and chairman. During his paper industry career, Blocker has held leadership positions at West Fraser, International Paper, and Champion International, focused on forest management, fiber procurement, consumer packaging, strategic planning, business development, and manufacturing.
Both Slater and Blocker will report to Doyle Simons, president and CEO.
Drake has been Weyerhaeuser's SVP, Research and Development, and CTO since 2006. Prior to joining the company, he was VP, Research and Development and CTO of Air Products and Chemicals Inc. from 2001 to 2006 and held numerous other leadership positions with that company from 1986 to 2001.
Chandrasekaran has been Weyerhaeuser's SVP, Cellulose Fibers, since 2006. Prior to that, he was VP, Manufacturing, Cellulose Fibers, VP and mill manager at the Kamloops, British Columbia, Cellulose Fibers mill, and VP and mill manager at the Kingsport, Tenn., paper mill. He joined Weyerhaeuser in 2002 with the company's acquisition of Willamette Industries.
##SHARELINKS##
|
TAPPI News
The Safety Management Leadership Course, August 26-27 in Metro Atlanta, Ga., USA, places a particular focus on leadership training, including incorporating a safe environment into workforce training and work expectations. Key safety topics are covered by the course, including:
- Safety Fundamentals / Modern Safety Management Principles
- OSHA Record Keeping and Medical Management
- Incident Investigation
- Safe Behavior and Choices
- Safety Culture
- Measuring Safety Performance
- Hazard Recognition
- Safety Walk-throughs, Observations, and Messaging
- Managing Change Safely
- Effective Safety Communication.
See more listed on the course schedule.
Meet the instructors.
Register for the Webinar Preview.
Tuesday, August 6 ♦ 1:00 p.m. EST ♦ 45 min.
This course is designed for anyone involved in workplace safety, including:
- Training and HR
- Safety Supervisors
- Team/Project Leaders
- Plant Managers
- Frontline Supervisors
- Safety Committees.
A special discount is offered for TAPPI and PPSA members. Register by July 26 for savings off the regular course rate.
TAPPI will award 1.3 CEUs to those who complete this course.
##SHARELINKS##
|
August 27th PIMA will hold it's Golf Outing at Grand View Lodge of Pequot Lakes, Minn. The shotgun scramble starts at 9:30 a.m. Box lunch is included, with cocktail hour to follow. Net proceeds go to Lake States TAPPI/ North Central PIMA's Scholarship Fund. Details now available and registration is open.
##SHARELINKS##
|
TAPPI will be performing its fiscal year-end inventory counting starting August 27. As a result, we will not be processing TAPPI Press orders from August 27 through August 30. Orders received during this time will be shipped in the order they have been received, starting September 3. All normal payment processing will resume on September 3.
We apologize in advance for any inconvenience and thank you for your patience. This process allows us to better serve our members.
##SHARELINKS##
|
The TAPPI International Research Management Committee requests nominations be submitted for the Research and Development Technical Award and the William H. Aiken Prize.
The award is given for outstanding accomplishments or contributions that have advanced the technology of the paper and related industries in the field of research and development. The nomination should contain:
- A summary of the nominee's technical achievements
- The impact and relevance of the research on industry
- Education, work history
- Examples of the impact that they have had on others
- Other pertinent activity such as involvement in TAPPI.
The $500 prize is funded by an endowment from the estate of William H. Aiken, TAPPI president in 1967-1968 and vice president of technology for the former Union Camp Corp. at the time of his death in 1974. Dr. Aiken also won the TAPPI Gold Medal, the association's highest honor, in 1971. Nominations for the Research and Development Technical Award and the William H. Aiken Prize should be submitted by August 31, 2013, to Colleen Walker, cwalker@tappi.org at TAPPI, 15 Technology Parkway South, Peachtree Corners, Ga. 30092, USA, or fax +1 770-446-6947.
##SHARELINKS##
|
Ohio TAPPI Local Section is sponsoring the Miami Valley Paper Industry & Suppliers Golf Outing at Heatherwoode Golf Club on Thursday, September 5. There will be a 1:30 p.m. Shotgun Start plus dinner and prizes afterward. The cost per foursome is $275.00. Suppliers are encouraged to bring raffle and door prizes.
For more information contact Judy Mann at 513-705-2060, or Sam Flannery at 513-702-4480.
##SHARELINKS##
|
A new TAPPI student chapter has been formed at Virginia Tech in Blacksburg, Va., USA. TAPPI student chapters are located on many college campuses that have curricula relevant to the forestry and pulp and paper industries. They offer students an opportunity to meet their peers, interact with future employers, tour facilities, and advance their knowledge of the industry.
"Our packaging program has really taken off over the past two years and the number of students declaring a major or minor in packaging science has surged to new levels," notes Young T. Kim, assistant professor of Practice, Packaging Systems, and Design, Department of Sustainable Biomaterials at Virginia Tech. "Two years ago we only had a handful of students in the department, so we are very excited about the level of interest we now have in our programs. Packaging is a major industry and employer and our packaging science program will result in many new scientists and engineers considering the packaging industry as a career."
Virginia Polytechnic Institute and State University (Virginia Tech), a land grant university, offers 215 undergraduate and graduate degree programs and has more than 32,000 students. The Packaging Science program offers several options including a major and minor covering packaging systems and design.
##SHARELINKS##
|
Gulf Coast TAPPI Local Section will host its Fall Meeting in partnership with the Alabama Pulp and Paper Council and Auburn Pulp & Paper Foundation, September 11-13. The meeting will be held at the Auburn University Hotel & Conference Center.
More information is available at the meeting website.
##SHARELINKS##
|
Registration is now open for the 2013 TAPPI Corrugated Press Hands-On Maintenance Workshop, September 17-18 at the Global Equipment USA Warehouse in Skokie, Ill., USA.
This unique course gives you an unprecedented opportunity to get hands-on training on how to audit converting machines. With only 18 seats available, you will have ample opportunity to get your questions answered by instructors Tom Pearce (Pearce Corrugated Consulting), John Bingham (Pamarco), Jim Wegemer (INXinc), Chuck Bobeldyk (Mark-Maker Co.), Randy Kesselring (MarquipWardUnited), as well as representatives from Global Equipment. The schedule for this course is packed into just two efficiently planned days so that participants get loads of skill and experience without much time away from their own operations.
Who should attend?
This Intermediate-level course offers indispensable hands-on maintenance training for corrugated industry plant managers and supervisors, engineers, maintenance teams, and machine operators.
You could pour over all of the how-to manuals available and still not retain this level and quality of working knowledge. Completing this workshop will enable you to:
- Use the basic tools to mechanically audit and troubleshoot a press
- Understand press audit procedures for process centering, better quality products, and increased productivity
- Discuss anilox roll selection, press "fingerprinting," inks and substrates, quality defects amd cause(s), and scoring.
Register by August 16 and join TAPPI or renew your membership to receive the best rates.
##SHARELINKS##
|
Marion Keyes led Bailey Controls and earned dozens of patents over the course of his career.
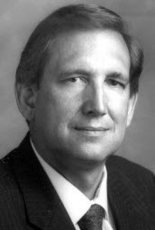 Keyes was born and raised in Bellingham, Wash., USA. He earned his bachelor's degree in chemical engineering at Stanford University, a master's in electrical engineering from the University of Illinois, and a master's of business administration from Baldwin-Wallace College.
He worked as an engineer for Ketchikan Pulp in Alaska, where he met his future wife Loretta. Keyes became engineering director for the controls division of Beloit Corp. in Wisconsin, then GM of Taylor Instruments' new digital systems business in Rochester, N.Y. In 1975, he became VP of engineering at the Wickliffe headquarters of what was then Bailey Meter, a leader in control products and systems for industry. Five years later, at age 42, he became Bailey's president and COO. He expanded sales overseas and designed an early computerized control system called Network 90.
In 1985, Keyes became VP and group executive of Bailey's parent company, Babcock & Wilcox, and an officer of that company's parent, McDermott International Inc. During these years he kept working and living in a home he'd built with his family in Moreland Hills. Marion rejoined Bailey as president and chief executive from 1989 to 1991. He then founded and chaired DCOM Corp. in Mentor, which made computers and peripheral systems. He moved to St. Louis in 1993 and served as VP of Emerson until retiring in 2010.
Keyes wrote two technical books and about 150 articles. He lectured at several schools, including at Oxford University in England. He had about 50 U.S. patents as well as 75 foreign patents. In 1984, the Cleveland world Trade Association named him International Businessman of the Year for "strong leadership in directing Bailey's expanding participation in world trade." He has also been honored by several other groups, including the Academy of Science in the Soviet Union, the Process Automation Hall of Fame, the Ohio Academy of Science, and TAPPI.
Keyes was president of the Boy Scouts of America's Northeast Ohio Council, Northern Ohio chairman of a United Cerebral Palsy telethon, grand master of ceremonies for the Kappa Sigma fraternity, and a trustee of Baldwin-Wallace. He belonged to Canterbury Golf Club, the Clevelander Club, and the Bluecoats.
He is survived by his wife, one of their three sons, and all six of their grandchildren. Ambruster Chapel in St. Louis handled his arrangements.
##SHARELINKS##
|
TAPPI is pleased to announce the new business reviews section on its buyers guide. Now you have the opportunity to share your experiences with a company's products or services with your peers in the industry.
Write a review to be entered for a chance to win airfare and seven nights at a luxury resort hotel in Hawaii.
What are the benefits of writing a review?
- 7 of 10 people read reviews before making a purchase
- 51% of buyers trust strangers' opinions over friends, family, and trusted business advisors
- Consumers trust online reviews and other consumer feedback 12 times more than marketing messages from businesses
- Local business reviews are read by 85% of consumers
- Reviews not only give consumers the ability to share their opinions about the products or services they buy, but it also offers businesses a way to evaluate and track what people are saying about them
- Good reviews lead to more purchases, and negative reviews allow marketers to make adjustments to products and show their willingness to work with their consumers (both the consumer and the brand benefit from these opinions).
##SHARELINKS##
|
As part of a partnership agreement with PMMI, the Association for Processing and Packaging Technologies, TAPPI will exhibit at the 2013 PACK EXPO. PACK EXPO, Sept. 23-25, 2013, in Las Vegas, Nev., USA, is North America's largest packaging and processing trade show.
"TAPPI is excited about our partnership with PMMI and our participation in PACK EXPO," notes Larry N. Montague, TAPPI president and CEO. "Packaging is a major part of our industry and as an exhibitor at an industry leading trade show we will have the opportunity to interact with professionals from many aspects of the business and showcase TAPPI's member services and industry information products related to both our PLACE Division and Corrugated Division"
Sponsored by PMMI, PACK EXPO provides a comprehensive showcase of packaging and processing technology for more than 26,000 packaging and processing professionals and 1,700-plus exhibitors. The three-day event includes the latest developments in new materials, containers, package design, food safety, and sustainability. The exhibit covers a full range of vertical markets of consumer packaged goods companies.
##SHARELINKS##
|
Calls for Papers have been issued for PaperCon 2014.
After a record attendance in 2013, PaperCon will again bring together CEOs, mill managers, superintendents, scientists, process engineers, and suppliers for the largest pulp and paper technical program in the world. The event will take place April 27-30, 2014, in Nashville, Tenn., USA. Learn more about PaperCon 2014.
For 2014, PaperCon is once again co-located with the Tissue360° Forum, NETInc (Innovative Nonwovens Conference), RPTA (Recycled Paperboard Technical Association) P-T Seminar, and the OpEx Reliability Workshop. Each of these events is open to full PaperCon registrants and papers in these areas are welcome.
Calls for Papers and Posters have been issued. The conference theme is In Tune for Stability, Agility, and Profitability, and authors are encouraged to include this within their papers.
Papermakers Program:
The Papermakers Program encourages topics on paper machine upgrades, product development, stability, agility, and fluid fundamentals, and recycled paperboard. The deadline for submission of abstracts is Nov. 10, 2013. Abstracts for panel discussions and roundtables are welcome. See Papermakers Program Call for Papers.
Coating and Graphic Arts Program:
The Coating and Graphic Arts Program will focus on The Future of Print and its Demands on Paper and Coatings. The deadline for extended abstracts for this program is October 16, 2013. See the Coating and Graphic Arts Program Call for Papers.
All abstracts must be submitted using TAPPI's Speaker Management System for consideration by the TAPPI and RPTA program committees.
##SHARELINKS##
|
TAPPI member Hideki Fujiwara, Ph.D., has hit a lot of high notes in his long and illustrious career in the pulp and paper industry. Not the least of which occurred as a result of his nearly three decades of membership, including being the first member from Asia to be honored with the Charles W. Engelhard Coating and Graphics Arts Division award.
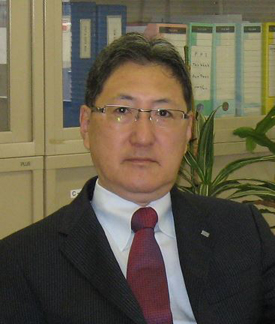 Dr. Fujiwara, who retired in June after 38 years in the industry, spent the majority of his career with Nippon Paper, serving in a variety of managerial positions. He credits his active involvement in TAPPI with providing ample opportunities not only to receive, but to share technical ideas and innovations with other professionals from around the world. Membership helped broaden his view of the forest products industry, and he notes that "joining TAPPI was the very first step to being a real professional in this field."
Find out more by reading this month's Member Spotlight. Spotlight participants are recommended by fellow members and staff. If you would like to nominate members, just send their name (or names) to MemberSpotlight@tappi.org. We will forward a Spotlight Questionnaire to fill out and return.
We look forward to seeing you in the Spotlight!
##SHARELINKS##
|
There's still time to be part of the program at the 2014 TAPPI PLACE Conference, May 12-14, 2014, at the Sawgrass Marriott Hotel in Ponte Vedra, Fla., USA. The 2014 PLACE Technical Program Team is actively seeking technical presentations, panels, tutorials, roundtables, and case studies from the packaging and academic community to be presented at the conference.
View the Call for Abstracts.
Interested in being a session chair or know someone who would be a great presenter? Extended abstracts will be accepted anytime before September 6, 2013. Space is limited so submit now! Final papers will be due on or before March 17, 2014.
The 2014 PLACE Conference is the premier North American event for the flexible packaging industry and will have something for the whole supply chain including suppliers, converters, extruders, retailers, and brand owners. This event not only offers top notch technical presentations but also allows ample opportunity for networking with your peers. Visit the event website for additional conference information.
##SHARELINKS##
|
The 2013 Building Science Committee Technical Program will include papers on: Process Variation Reduction, Glass Sizing Basics; Burner Safety and Efficiency; Biological Treatment Case Study; Operator and Mechanical Training to Enhance Operational Effectiveness; and IT Systems to Manage Roll Goods and Reduce Waste.
This year's program will focus on aiding production managers and engineers in the fiberglass mat industry. Attendees will get the first-hand knowledge needed to improve their mat processes with production-targeted papers.
These topics and more will be covered in the comprehensive technical program. Tim Worms, of 3M's Industrial Mineral Products Division, is returning by popular demand to present his outlook for housing starts and the roofing forecast for this year. Kirby Erickson, of GAF, will discuss critical safety issues to be aware of as you seek to implement new efficiency and pollution requirements in curing ovens. In addition he will provide an example of how mistakes led to a massive oven explosion and what was implemented to address burner safety going forward. Charles Black, of Charles Black & Associates, will ask if your training dollars are being spent wisely and provide case studies showing how strong training programs can have a positive impact on your company's bottom line. Blaine Krause, of Nalco, will offer case studies on microbial control including its impact on operations, monitoring, control, and examples of newer technology.
The meeting will be held September 18-20 at The Hilton Marco Island Beach Resort in Marco Island, Florida, USA. Meeting registration includes the full conference program, the Building Sciences Committee Meeting, and ample opportunities for networking with other manufacturing personnel and suppliers. Thursday afternoon's activity is a choice of golf, backwater fishing, or a relaxing spa treatment. Group dinners are included in the cost of registration for Wednesday and Thursday evenings at some of the area's finest restaurants. Non-registered spouses and guests are welcome to participate in the activities and dinners for the following costs: $60 per dinner and $95 for golf, fishing, or the spa treatment. They do not have to pay the conference registration fee.
Companies participating as sponsors include ESP, GAF, Georgia-Pacific Chemical, Malarkey Roofing, Momentive Specialty Chemicals, Nalco, PPG, Albany International, Xerium, Ineos, Mallard Creek Polymers, and Majiq. Opportunities to sponsor with this select group of companies are still available and your company will receive special recognition throughout the meeting.
You do not want to miss out on this opportunity to stay abreast of current market trends, new and emerging product/process technical developments, and regulatory issues that are or will be impacting our industries.
For full meeting information including the conference agenda and program summaries, please visit the meeting website today.
##SHARELINKS##
|
The 2013 TAPPI PEERS Conference, September 15-18, in Green Bay, Wis., USA, has announced the detailed technical program focusing on sustainable manufacturing and other pressing business and technical questions faced by pulp and paper companies as they manage raw materials, assets, regulatory requirements, and production assets. Register now and save.
In addition to the peer-reviewed technical program, Keynote Speaker Robert Feeser, SVP of Packaging with MWV, will share his insights on the day-to-day challenges he faces as he oversees the company's primary mill-based manufacturing businesses in the U.S. and Brazil. PEERS will also offer exclusive networking opportunities and insight into new technologies that can help you optimize your mill operations.
For 2013, PEERS will be co-located with the 10th Research Forum on Recycling and the International Bioenergy and Bioproducts Conference, creating a value-added opportunity for you to expand your learning, networking, and resources by attending all three events.
Learn more about the TAPPI PEERS Conference.
##SHARELINKS##
|
TAPPI is offering a 10% discount on registration for the Root Cause Problem Elimination Training Course taking place in Raleigh, N.C, USA, on October 8-10, 2013. If you register soon, you can save more than $250 with only a few seats remaining.
IDCON's Root Cause Problem Elimination Seminar focuses on eradicating problems. We all have problems, right? At least in your operations, let this training help you get to the source of problems.
You'll learn how to tie cause and effect together and apply logical thought processes to arrive at the problem's core. You'll learn how to use the "How-Can Diagram" to bring root cause analysis into your day-to-day reliability management process, and do it cost effectively!
This expanded course will focus on outlining basic mechanical engineering stress/strain fundamentals, metallurgy, and engineering design, which are typically necessary in the development of possible root cause(s) for mechanical failures.
You'll learn how to use predictive maintenance tools correctly to provide a mechanism for root-cause analysis initiation and eventual elimination of repeat failures.
Register today to secure your access to these premier training courses with IDCON.
##SHARELINKS##
|
Don't miss out on your chance to attend the Process Control of Stickies Workshop, taking place just before the TAPPI PEERS Conference.
Organized by Dr. Mahendra Doshi, current TAPPI JOURNAL Editorial Board Member and Founding Editor of Progress in Paper Recycling, the workshop will be held from 7:30 a.m. to 4:30 p.m. on Sunday, September 15.
The international workshop is designed for engineers, scientists, and technicians who want to get a handle on one of the difficult contaminants in paper recycling - stickies. The workshop will benefit anyone using recycled pulps, working in recycling mills, or affiliated with companies supplying equipment, chemicals, and recovered papers to the recycling industry.
Problems caused by stickies cost millions of dollars to the industry. As indicated above, experts from around the world together with highly experienced speakers from mills offer an excellent overview for managing and controlling stickies. If you could just save one hour of paper machine downtime it would pay for the workshop many times over.
Learn more about this important workshop.
Don't miss this golden opportunity to learn about stickies related issues at this one-day international workshop.
Registration Cost:
$295/member; $345/non-member (on or before August 16); or $345 (if registered after August 16).
##SHARELINKS##
|
Now's the time to make your plans to attend IBBC, September 18-20 in Green Bay, Wis., USA.
As the only industry event dedicated to advancing biorefineries in the forest products industry, International Bioenergy and Bioproducts Conference (IBBC) offers you a fresh look at biomass utilization. Sessions focusing on biomass supply and demand, biochemical and thermochemical conversion technologies, conversion pathways, and economic assessments – along with a Keynote Presentation from Linda A. Beltz, Ph.D., NPDP, Director, Technology Partnerships at Weyerhaeuser – can help you determine how to integrate these technologies into your mill.
For 2013, IBBC will be co-located with the TAPPI PEERS Conference, and the 10th Research Forum on Recycling, creating a value-added opportunity for participants to expand their learning, networking, and resources by attending both events. Offered just after IBBC, TAPPI's Biorefinery Course, can deepen your understanding of biorefinery strategies and emerging technologies and their design/implementation in a business strategy.
Learn more about IBBC.
Register by August 16 for best rates!
##SHARELINKS##
|
TAPPI CorrExpo 2013, October 7-9 at the JW Marriott in Indianapolis, Ind, USA,. is your one-stop pitstop to fuel your networking and relationship building needs.
Take advantage of these high-octane opportunities:
View the full program to fast track your CorrExpo experience.
##SHARELINKS##
|
The Foundations of Leadership Excellence Course is the only leadership course specifically focused on the paper and packaging industry.
Foundations of Leadership Excellence explains the fundamentals of leadership and management skills for emerging leaders, high-potentials, area operating managers, and other technical professionals. This three-day session takes place Oct. 22 - 24, 2013, at the TAPPI Training Facility in Metro Atlanta, Ga., USA.
This course will sell out at 25 participants.
The instructors for this course have approximately 100 years of combined experience in leadership, management, and human resource roles within the pulp and paper industry.
Course curriculum covers industry specific, real-world scenarios. Participants will develop personal leadership skills through the use of influence. They will learn to impact organizations from a 360 degree perspective and how to address the challenges of team building, accountability, performance management, and other critical factors of organizational success.
##SHARELINKS##
|
Piping System Training is a course anyone in the piping system industry can use. This course provides real-world practical knowledge for junior engineers, is a good refresher course for senior engineers, and helps operations and maintenance supervisors, design and process engineers, and operators and maintenance personnel better understand how piping systems operate.
This course provides the foundation of piping terminology, mathematics, and the underlying concepts and principles that determine the performance of individual piping system elements and the system as a whole. Piping System Training places an emphasis on understanding the relationship between components that make up the piping system.
Visit the course website to find more information and register.
Earn 1.6 CEUs and carry back with you two indispensable manuals as well as greater confidence in your work.
##SHARELINKS##
|
As TAPPI is getting ready to celebrate its 100th Year Anniversary in 2015, we were wondering how much industry expertise we have in this great group of professionals.
So, we decided to post a discussion question on our TAPPI Social Media outlets. We asked, "How many years of paper and/or packaging experience do you have?"
Who knew such a simple question would have such an impressive response.
With more than 7,000 TAPPI members, all over the world, we have counted 650-plus years of industry experience! And that's just counting the first 30 people who have responded. Now you probably can't find that anywhere else . So why don't you join us?
From those "born" into the industry to third generation professionals. From paper to packaging, to sustainability, environment, tissue, converters, and consulting. This TAPPI network has something for everyone.
Become a part of this unique community of paper and packaging professionals, and add your expertise to our group, and network with others to learn something new.
Visit our website to learn more today!
##SHARELINKS##
|
The TAPPI Centennial Celebration will be a multi-year long series of outreach events and educational offerings showcasing the proud history and promising future of the global pulp, paper, packaging, and related industries. This once-in-a-lifetime event will expand public awareness, foster further connection, and provide outstanding opportunities for collaboration, growth, and investment in our future for all of those involved. Goals for the TAPPI Centennial Celebration are:
- To honor TAPPI's 100 years of connection, education, and advancement as a foundation for the sustainable success of our members, our industries, and the world we share
- To recognize the achievements of those who built our industry and to inspire those who seek to build its future
- To celebrate the contributions and innovations of the global pulp, paper, and packaging industries to human culture, commerce, health, and social advancement
- To sustain the industry and support its growth, vitality, and future through the TAPPI Foundation.
We invite you to be a part of this momentous event. The sooner you join us the more opportunities there are for recognition of your company, its products, and key innovations. Keep in mind that an early commitment allows you to spread your investment over multiple years' budgets.
For more information on sponsorship and volunteer opportunities please contact dbell@tappi.org.
The sponsorship prospectus can be downloaded online.
##SHARELINKS##
|
Do you have a history book gathering dust on your shelf? TAPPI's 100th year is coming soon and we are looking for donations to the TAPPI Library. Specifically, we are interested in histories of companies and mills in the paper and packaging industry (both producers and suppliers). Each donated book will have a bookplate in the front cover recognizing the donor. For more information please contact David Bell.
Please send books to:
c\o David Bell
TAPPI
15 Technology Parkway, South
Suite 115
Peachtree Corners, Georgia 30092
##SHARELINKS##
|
|
|