Toscotec Delivers Tadvision® Machine to Latin America.
Print this Article | Send to Colleague
Toscotec has delivered a TADVISION® machine to a confidential customer in Latin America, as part of a major turnkey supply contract. Toscotec supplied the TAD plant as a turnkey delivery. Toscotec has delivered a TADVISION® machine to a confidential customer in Latin America, as part of a major turnkey supply contract. Toscotec supplied the TAD plant as a turnkey delivery.
The machine is equipped with a two-layer TT Headbox ML-T with dilution system, a second generation TT SYD and gas-heated TAD air system, with a high level of energy recovery. It features a trim width of 2,750 mm and has a production capacity of more than 27,000 tpy. The supply includes the stock preparation equipment and accessories, Toscotec’s patented TT SAF (Short Approach Flow), the fiber recovery and water system, the dust and mist removal systems, the vacuum system, the electric and control system, the distributed control system (DCS) for the complete plant and the quality control system (QCS).
The turnkey scope also comprises the compressed air system, the bridge crane, a complete pulp bales handling system, an online shaft puller, the roll handling and wrapping systems and the hall ventilation system.
As part of the service package, Toscotec will also provide the detailed mill engineering, the erection, commissioning and test runs and start-up assistance.
In June, the Italian manufacturer had presented its newly redesigned TADVISION® machine at iT’s Tissue, in Lucca, Italy. With this new design, Toscotec builds on the experience of its TAD machine that came online in the US in 2004 and takes it further to obtain superior bulk and absorbency, higher production and energy efficiency. The TAD section is composed of three coated TAD drums, featuring an optimized airflow, which contributes to cutting consumption down to 4.5-5.5 MWh/ton, from the consumption of current TAD machines estimated in the range of 6.0-7.5 MWh/ton.
Toscotec’s project manager Pier Paolo Brunazzi says, “Thanks to the successful cooperation of the two teams, we worked out an erection schedule that could accommodate the requirements of the mill, based on the civil works’ progress. As a rule, on our turnkeys we have the flexibility to adapt to the changing needs of the mill, in order to advance towards our common goal. One of the main challenges we faced during the engineering phase of the project was the altitude of the mill, which stands at approximately 2,500 m above sea level. Such a high altitude inevitably affects the electric and vacuum plants, because the air is more rarefied. The advanced design of the new TADVISION® significantly reduces the overall consumption and improves efficiency. Starting from that, we had to go the extra mile and optimize the use of energy, because of the altitude factor. We are happy with the outcome of this effort, and expect to see very good results on site.”
Installation of the new plant began in September and will continue into the second quarter of 2019. Start-up is scheduled for June 2019.
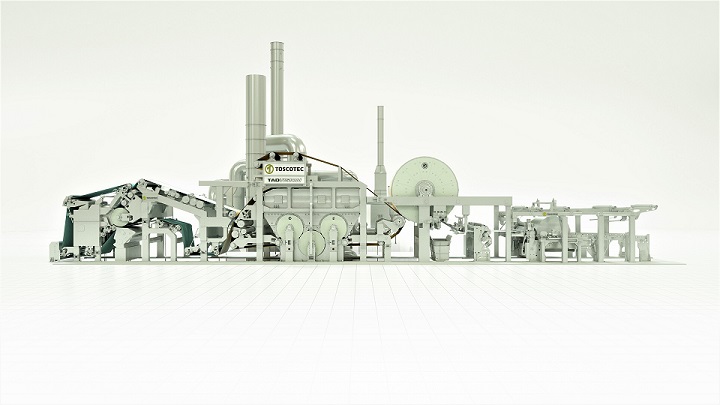 Back to Tissue360 Newsletter |
|
|