PrimeLinetex – A New Machine "Above All Expectations"
Print this Article | Send to Colleague
The new Andritz tissue machine, PrimeLineTEX, has been developed for the production of textured tissue. It enables up to 50 percent energy savings compared with TAD systems and even up to 25 percent fiber savings compared with dry crepe. As for further operating cost reductions the concept has only one fabric instead of two used in competing designs.The new Andritz tissue machine, PrimeLineTEX, has been developed for the production of textured tissue. It enables up to 50 percent energy savings compared with TAD systems and even up to 25 percent fiber savings compared with dry crepe. As for further operating cost reductions the concept has only one fabric instead of two used in competing designs.
Klaus Gissing, director, PrimeLineTIAC and Air & Energy Systems, and Carlos Gallo, director of technology, R&D and start-up – Tissue Machines, Tissue & Drying, at Andritz, explain the benefits of the PrimeLineTEX.
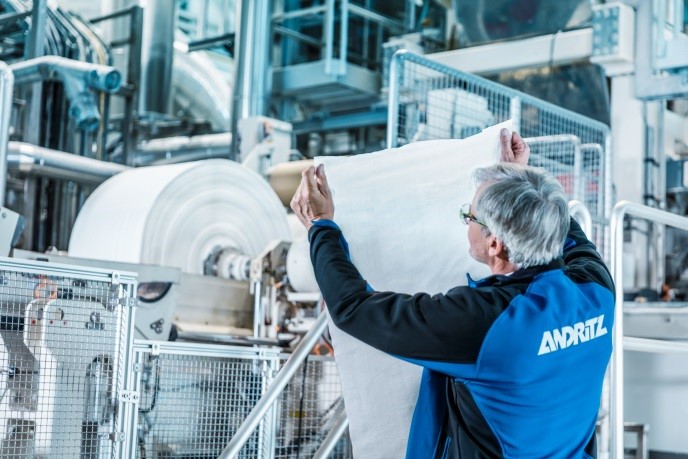 The PrimeLineTEX delivers a quality close to structured (TAD) tissue
Can you describe why the PrimeLineTEX machine concept was created and why it is of such significance to the tissue industry?
Klaus Gissing: Before we started the R&D on this project, we carried out an extensive market survey in order to better understand the needs of our customers worldwide and gain a deeper insight into their work, particularly regarding machine operation. The results of the survey showed a high demand for premium tissue quality produced at lower operating costs and for a machine that can produce a wide range of products.
Carlos Gallo: The consumption of tissue is growing continuously, and there is a market trend towards the use of higher quality products. For many years, TAD technology was almost the only option available to produce higher quality tissue, but the technology involves high energy consumption. PrimeLineTEX is the Andritz alternative for this market, producing paper with quality very close to TAD and requiring much less energy.
Can you tell us individually about the main advantages of the PrimeLineTEX?
Gissing: In regard to quality, the tissue being produced by the new machine is very close to TAD, especially in its bulk and absorbency.
In terms of fiber savings, compared with a European 4-ply toilet tissue produced on a dry crepe machine, we are achieving a 25-percent fiber saving, which is even above all of our own expectations. This will help our customers to significantly reduce their costs.
The energy consumption is perhaps one of the most important advantages of the new machine, where we are using 50% less energy when compared to TAD machines. We are able to do this because the PrimeLineTEX concept creates pressed and structured tissue. Due to pressing before structuring and drying, the energy consumption is less than 50% of TAD dried tissue. The structure comes from a rush sheet transfer from the shoe press belt to the structured fabric.
Gallo: Also, when it comes to investment costs, the PrimeLineTEX is a more simple solution compared to TAD and other alternatives in the market and it requires less installation space.
Can you explain in more depth about the swing ability of the PrimeLineTEX to switch from textured to dry crepe? And also why it only requires one fabric as opposed to the usual two?
Gissing: The PrimeLineTEX concept is unique on the market when it comes to swing mode. This concept uses the shoe press belt as transfer belt, where other concepts have a separate transfer belt. This is a huge advantage in terms of maintenance and rebuild time, and the switch from one grade to another can be done in less than one day.
Gallo: The PrimeLineTEX concept is actually quite simple, based on well-known dry crepe machine sections such as the crescent former and a drying section with a Yankee. It requires only one additional fabric, so the rebuild from TEX to dry crepe and vice versa is much simpler than other technologies on the market.
Can you tell us how the new research center in Graz enabled Andritz to make this new tissue machine concept happen?
Gissing: Our research center in Graz has put us in a very favorable position as we have all the facilities we need in place there, including a purpose-built pilot machine. In the case of the PrimeLineTEX, we focused our R&D work on the two most important areas: the shoe press concept for pressing and sheet transfer on belt, and the pick-up and rush transfer from belt to structured fabric. The PrimeLineTIAC in Graz has given us the real ability and freedom to be as imaginative and innovative as we need to be.
Gallo: The PrimeLineTIAC was a key factor in the development of the new machine concept. It was possible to test and verify the theoretical ideas and make the necessary changes. Also, customers can now see the new technology in operation and be more confident about the results if they decide to order a commercial installation.
Another advantage is that customers have the opportunity to run trials on the PrimeLineTEX concept using their own furnish and reproducing the conditions they have in their own mills. The paper produced can then be shipped and further converted into final products to be market-tested.
Any technical parameters, for example width, speed and weights?
Gissing: The PrimeLineTEX can be delivered for single width and double width with a production of 100 to 200 metric tpd and a machine speed up to 1,600 m/min. Can you tell us about any customer feedback you have had on the PrimeLineTEX so far?
Gissing: The feedback we have received up to now was extremely positive. Customers like the very simple concept compared to others on the market and are impressed with the wide product range. PrimeLineTEX is bridging the gap between dry crepe tissue and TAD. In the trials we conducted, we could clearly see that customers are looking closely at PrimeLineTEX in comparison to other concepts.
Anything else you can reveal about what ANDRITZ is working on next at TIAC?
Gissing: A quick glimpse at our R&D plan will tell you that energy saving and sustainability have the highest priority. Needless to say, energy-saving concepts for TAD and fiber development for tissue are both on our list of upcoming projects.
Gallo: Andritz is also developing further in the direction of IIoT. We have our own IIoT solution, Metris, installed at our pilot plant, and we are already supplying solutions for many customers worldwide.
|
|
Textured tissue rolls produced at the ANDRITZ pilot plant in Graz, Austria Back to Tissue360 Newsletter |
|
|