New Tools Help Tissue Makers Manage Strength, Reduce Cost, Optimize Runnability
Print this article | Send to Colleague
By Pascal Rivard, applications project manager, Tissue/Towel - Ashland Inc.
Achieving strength targets required for finished product specifications have traditionally required the use of expensive long fiber (softwood), increased refining that significantly drives up energy costs, or the use of standard dry strength chemicals. For grades that utilize recycled fiber, these challenges can be even more daunting. Finally, fiber type, refining, and strength chemistry must all be balanced to ensure optimal machine runnability.
Considering these challenges, Ashland recently introduced two new Hercobond™ enzyme-based products specifically designed for recycle and virgin grades. Key features of these products include:
- Improved performance versus traditional dry strength chemistries such as GPAM, liquid starch, or other commercially available enzyme products
- Unique mechanism and mode of action
- Superior shelf life and product stability
- Overdosing and/or prolonged exposure of the product-in-use has no negative impact on fiber quality or machine runnability. (compared with other enzyme products, not starch or GPAM).
- Proven commercially, these products have demonstrated the following benefits:
- Improved strength
- Fiber substitution such as replacing SWK by HWK or recycled pulp
- Lower refining input (energy savings by improving drainage)
- Reduce traditional strength additive usage
- Better fines management (improved retentions)
- Lower polymer cost
- Speed-up machine
- Lower dusting
- Enhanced sheet properties
- Improved softness; more flexible fibers
- Increased bulk with lower refiner input.
Case Study – Hercobond 8800 – Recycle Fiber
A Northern U.S. mill producing consumer bath and napkin grades using up to 100% recycle furnish was unable to meet strength requirements on a critical napkin grade. Ultimately, an additional 8% basis weight as well as a standard GPAM dry strength was required to achieve the test. Partnering with Ashland, the mill switched to Hercobond™ 8800 to meet its strength target and the following benefits:
- Fiber savings due to return to normal basis weight
- Lower cost in use of chemical required
- Reduced energy as a result of the lower basis weight.
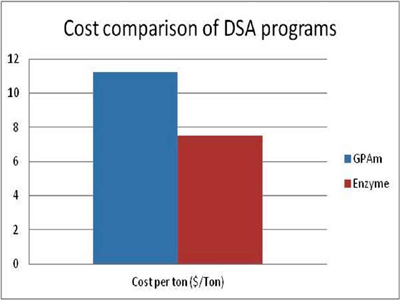
Case History- Hercobond 8900 -Virgin Fiber
A Southern U.S. virgin consumer tissue manufacturer needed to increase production of its light dry crepe asset. Sheet strength and stretch were limiting factors negating the ability to speed up the reel without getting into sheet breaks. With the use of Hercobond 8900, sheet strength improved and stretch was increased by 20%, allowing the operators to reduce refining energy, speed up the reel (90 fpm), and increase overall production.
About the Author
Pascal Rivard has 17 years of paper chemistry experience in both sales and applications roles. He is a member of TAPPI and PAPTAC.

|
|