L.C. Paper 1881 Overhauling Dry End of PM 2 Tissue Machine in Spain
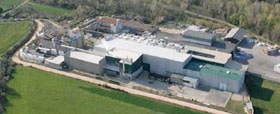
L.C. Paper 1881, Spain, has ordered from Toscotec, Italy (and its associate Milltech), a major dry-end rebuild of its SA PM 2 tissue machine in Besalu, Catalunya, Spain. Startup of the rebuilt machine is scheduled for the second quarter of 2014.
LC Paper was formed in 1881 during the Industrial Revolution and is now well regarded for its production of niche tissue products with two tissue machines (PM 2 and PM 3), annually producing 45,000 metric tons of tissue for the Away from Home (AfH) market The company’s main product—OnePly® tissue paper—is produced on PM 3, a 2.8 m crescent former machine, from virgin pulp, while PM 2, a 3.3 m fourdrinier yankee machine, produces a variety of tissue papers from 100% recycled paper.
The range of PM 2’s products includes Table 72 (37 gsm) and Exterkraft (50 gsm) tissue. The products are certified by the ISO 14001 European policy and the Ecolabel tag, both of them ensuring extraordinary attention to the environment. LC Paper is also well recognized in the European tissue market for its attention to energy reduction and its leadership in cogeneration applications.
In 1993, the company started up a new cogeneration plant. It was the first plant with a diesel engine of 6.5 MW in Spain, which was expanded in 1999 with a second 6 MW engine.
In 2009 LC Paper launched PM 3 with a patented process that uses gases from the cogeneration plant to dry the tissue paper by means of an innovative hood provided by Milltech. In 2011, the first diesel engine was sold and in 2012 LC paper installed a new gas engine. Some 6 MW of this energy will be used for feeding the new hood by Milltech on PM 2, further decreasing energy consumption.
Toscotec's delivery includes a major rebuild of the PM 2 dry end and press section, which will be replaced with a TT DOES (Drying Optimization for Energy Saving) package. This features a double press solution with a rebuild of the felt run, a new TT SYD-15FT yankee dryer with doctoring system, and a Duo-system yankee hood, a SMART eMT type from Milltech. The wet end hood is a burner feeding type, while the dry end hood can be fed either by cogeneration gases or conventional burner (normally with COG switched off).
Exhaust gases are used to generate two stages of steam (high and low pressure) through steam generators, in addition to the heat recovery to pre-heat the make-up and combustion air. Maximum drying production with a machine trim width at the reel of 3,050 mm will be 130 tpd. With this, PM 2’s consumption will be lower than1,350 kWh/ton.
According to LC Paper CEO Joan Vila, the investment will allow the company to improve its competitiveness. "After a detailed analysis of our project, we decided to again choose Milltech and Toscotec because of the innovative solution they were able to introduce, which aligns with LC Paper’s business philosophy, and also due to the previous positive experience we had with PM 3," he said.
TAPPI
http://tappi.org/